BACKGROUND OF THE INVENTION
Field of the Invention
[0001] The present invention relates to a plate cleaning agent for a lithographic printing
plate, more particularly to an emulsified plate cleaning agent, and even more particularly
to an emulsified plate cleaning agent used for a lithographic printing plate obtained
by platemaking from a photopolymerizable lithographic printing plate precursor provided
with an oxygen-blocking protective layer. In addition, the present invention relates
to a plate surface treatment method for a lithographic printing plate that uses this
emulsified plate cleaning agent.
Description of the Related Art
[0002] In general, lithographic printing plates typically comprise an oleophilic image area
that is ink receptive during the printing process and a hydrophilic nonimage area
that is fountain solution receptive during the printing process. Lithographic printing
plates utilize the fact that water and oil of mutually repel to generate a difference
in ink adherence to the surface of the lithographic printing plate by using the oleophilic
image areas of the lithographic printing plate as ink receptive areas and the hydrophilic
nonimage areas as a fountain solution receptive areas (areas not receptive to ink),
thereby causing ink to only adhere to the image areas, followed by transferring the
ink to a printed substrate such as paper. In lithographic printing, the nonimage areas
are dampened with the fountain solution, the surface chemical difference between the
image areas and the nonimage areas is enlarged, and ink repulsion between the nonimage
areas and ink receptivity of the image areas are increased. Thus, if the hydrophilicity
of the nonimage areas of a lithographic printing plate is impaired for some reason,
ink frequently adheres to that region resulting in the occurrence of so-called "scumming",
while conversely as a result of other components adhering to the image portion, the
ink is unable to adhere thereto, thereby preventing an increase in the image density
of the printed matter.
[0003] In the case hydrophilicity has been impaired and there is increased susceptibility
to scumming, or in the case ink no longer adheres to the image areas, plate surface
treatment is typically carried out on the lithographic printing plate using a plate
cleaning agent in order to correct these problems and restore the hydrophilicity of
the nonimage areas and the adherence of the image areas. In the past, various plate
cleaning agents for lithographic printing plates have been proposed (see, for example,
Japanese Patent Application Publication No.
H11-288104 and Japanese Patent Application Publication No.
2007-45055).
[0004] On the other hand, from the viewpoint of lithographic printing plates, lithographic
printing plate precursors (PS plates) have heretofore been widely used that are obtained
by providing an oleophilic photosensitive resin (image recording layer) on a hydrophilic
support. A lithographic printing plate is obtained by platemaking this type of lithographic
printing plate precursor using a method consisting of exposing the lithographic printing
plate precursor through an original image such as a lith film, followed by allowing
the areas serving as the image areas of the image recording layer to remain while
dissolving and removing other unwanted areas of the image recording layer with an
alkaline developing solution or organic solvent to expose the surface of the hydrophilic
support and form nonimage areas.
[0005] Digitization technology, consisting of electronically processing, accumulating and
outputting image information with a computer, has become widespread in recent years,
and various new image output methods have come to be used practically in accommodation
of this digitization technology. Accompanying this, computer-to-plate (CTP) technology
has attracted attention for use in directly producing lithographic printing plates
without using a lith film by carrying digitized image information with highly convergent
radiant rays of light in the manner of laser light, and exposing a lithographic printing
plate precursor by scanning with the light.
[0006] Photopolymerizable lithographic printing plate precursors have been proposed as an
example of a lithographic printing plate precursor for CTP as described above. Since
a polymerization initiator (compound that initiates and promotes polymerization of
a compound having polymerizable unsaturated groups by generating radicals with the
energy of light, heat or both) is typically used in photopolymerizable lithographic
printing plate precursors, an oxygen-blocking protective layer is normally provided
on the image recording layer to improve polymerization efficiency by inhibiting the
loss of radicals caused by oxygen in the air. Polyvinyl alcohol is a well-known example
of a component of this protective layer. In addition, the containing of fine particles
of inorganic substances in the oxygen-blocking protective layer has also been proposed
(see, for example, Japanese Patent Application Publication No.
2005-119273).
[0007] Inorganic compounds used in this type of oxygen-blocking protective layer partially
remain on the surface of the image areas after developing, and due to their own hydrophilicity
and/or hydrophilic components in the foundation solution being adsorbed onto the surface
of the inorganic compounds, adequate ink receptivity of the surface of the image areas
is lost during printing, and as a result thereof, the problem of defective ink adherence
occurs in which the ink concentration on printed matter decreases. The problem of
ink failing to adhere to the image region during printing is referred to as blinding.
On the other hand, when scumming occurs during printing, there is the problem of increased
likelihood of blinding when treatment is carried out with a plate cleaning agent,
and so-called uneven wiping may occur when unevenness occurs in the adherence of ink
as a result of treating with a plate cleaning agent.
[0008] With the foregoing in view, a plate cleaning agent is required that can be used favorably
without causing problems such as blinding or uneven wiping on a lithographic printing
plate obtained by platemaking from a photopolymerizable lithographic printing plate
precursor provided with an oxygen-blocking protective layer, and particularly an oxygen-blocking
protective layer containing inorganic fine particles.
DISCLOSURE OF THE INVENTION
Problem to be solved by the Invention
[0009] An object of the present invention is to provide a plate cleaning agent capable of
favorably treating a plate surface without causing blinding in a lithographic printing
plate obtained by platemaking from a photopolymerizable lithographic printing plate
precursor provided with an oxygen-blocking protective layer, and particularly an oxygen-blocking
protective layer containing inorganic fine particles.
Means to Solve the Problem
[0010] As a result of conducting extensive studies to achieve the above object, the inventors
of the present invention found that the type and amount of cation in a plate cleaning
agent is involved in the occurrence of blinding, and accordingly, plate cleaning treatment
can be favorably carried out while inhibiting the occurrence of blinding without causing
uneven adherence of ink in an image areas by selecting a specific mode for the cation
in the plate cleaning agent, thereby leading to completion of the present invention.
[0011] Thus, the present invention is an emulsified plate cleaning agent for a lithographic
printing plate used on a lithographic printing plate obtained by platemaking from
a photopolymerizable photographic printing plate precursor provided with an oxygen-blocking
protective layer, wherein the total cation content of a contained salt based on the
total weight of the plate cleaning agent is 0.5% by weight or more, and 30% by weight
or more of the cations are at least one type selected from the group consisting of
potassium, cesium and rubidium based on the weight of all cations. Here, a salt includes
salts in the manner of organic salts and inorganic salts, as well as hydroxides.
[0012] In a preferred embodiment of the present invention, the emulsified plate cleaning
agent for a lithographic printing plate is used in a lithographic printing plate obtained
by platemaking from a photopolymerizable lithographic printing plate precursor in
which the oxygen-blocking protective layer contains inorganic fine particles.
[0013] Moreover, the present invention is directed to a plate surface treatment method for
a lithographic printing plate that comprises cleaning a lithographic printing plate,
obtained by platemaking from a photopolymerizable lithographic printing plate precursor
provided with an oxygen-blocking protective layer, with the above-mentioned emulsified
plate cleaning agent for a lithographic printing plate. In particular, the plate surface
treatment method of the present invention is suitable for treating a lithographic
printing plate obtained by platemaking from a photopolymerizable lithographic printing
plate precursor provided with an oxygen-blocking protective layer containing inorganic
fine particles.
Effect of the Invention
[0014] According to the emulsified plate cleaning agent of the present invention, scum removal
ability is demonstrated against various types of scumming in nonimage areas and defective
ink adherence and uneven wiping are prevented from occurring in image areas in a lithographic
printing plate obtained by platemaking from a photopolymerizable lithographic printing
plate precursor provided with an oxygen-blocking protective layer.
[0015] According to the emulsified plate cleaning agent of the present invention, high-quality
printed matter can be provided by carrying out favorable plate cleaning treatment
on a lithographic printing plate obtained by platemaking from a photopolymerizable
lithographic printing plate precursor provided with an oxygen-blocking protective
layer, and particularly an oxygen-blocking protective layer containing inorganic fine
particles.
Mode for Carrying Out the Invention
[0016] A salt that provides a cation is contained as a component thereof in the emulsified
plate cleaning agent for a lithographic printing plate of the present invention. Salts
in the manner of organic salts and inorganic salts as well as hydroxides and the like
are included in the salt that provides a cation used in the present invention, and
any of normal salts, acid salt, basic salts, double salts or complex salts and the
like are included. The salt that provides a cation used in the present invention can
be selected from known salts and hydroxides for use as a component in the plate cleaning
agent for a lithographic printing plate. The emulsified plate cleaning agent for a
lithographic printing plate of the present invention is required to contain at least
one type of cation originating in the above-mentioned salt selected from potassium
(K), cesium (Cs) and rubidium (Rb). Namely, the emulsified plate cleaning agent for
a lithographic printing plate of the present invention is required to contain a salt
that provides at least one type of cation at least selected from the group consisting
of potassium, cesium and rubidium. Furthermore, a cation originating in a salt contained
in the emulsified plate cleaning agent for a lithographic printing plate of the present
invention does not include a cation originating in the water used to prepare the plate
cleaning agent.
[0017] The content of all cations originating in the contained salt of the emulsified plate
cleaning agent for a lithographic printing plate of the present invention is 0.5%
by weight or more, preferably 1.0% by weight or more and typically 10% by weight or
less based on the total weight thereof, and 30% by weight or more of the cations are
at least one type of cation selected from the group consisting of potassium, cesium
and rubidium based on the weight of all cations.
[0018] All cations originating in the salt contained in the emulsified plate cleaning agent
for a lithographic printing plate of the present invention may be at least one type
of cation selected from the group consisting of potassium, cesium and rubidium.
[0019] As an example of the composition thereof, the emulsified plate cleaning agent for
a lithographic printing plate of the present invention can be composed of an aqueous
phase containing (1) a water-soluble polymer compound, (2) at least one type of compound
selected from the group consisting of phosphoric acid, polyphosphoric acid and salts
thereof such as alkaline metal salts, organic phosphonic acid and salts thereof, (3)
nitric acid and/or nitrates, (4) sulfuric acid, sulfates and/or bisulfates, (5) water,
and an oily phase containing (6) a hydrocarbon-based solvent having a dissolving action
on ink. The emulsified plate cleaning agent for a lithographic printing plate of the
present invention can also contain (7) a surfactant, (8) a wetting agent, (9) a thixotropic
agent, and (10) a pH adjuster as necessary. A preservative, disinfectant or colorant
and the like may also be added to the plate cleaning agent of the present invention
in addition to the above-mentioned components.
[0020] Specific examples of the water-soluble polymer compound of (1) include natural substances
and their modified forms, such as dextrin, cyclodextrin, alginates, fibrin derivatives
(such as carboxymethyl cellulose, carboxyethyl cellulose, hydroxyethyl cellulose and
methyl cellulose), gum arabic or soybean polysaccharides, and synthetic products such
as polyvinyl alcohol and derivatives thereof, polyvinylpyrrolidone, polyacrylamide
and copolymers thereof, acrylic acid copolymers, vinyl methyl ether/maleic anhydride
copolymers, vinyl acetate/maleic anhydride copolymers or styrene/maleic anhydride
copolymers.
[0021] Examples of polysaccharides extracted from soybeans that have the ability to form
a film include water-soluble soybean polysaccharides. Water-soluble soybean polysaccharides
contain constituent sugars such as rhamnose, fucose, arabinose, xylose, galactose,
glucose or uronic acid, and the average molecular weight thereof is 50,000 to 1,000,000.
The content of water-soluble soybean polysaccharide in the plate cleaning agent of
the present invention is suitably within the range of 0.5% by weight to 20% by weight
and preferably 1% by weight to 10% by weight. The water-soluble soybean polysaccharide
is used in the form of a homogeneous aqueous solution by dissolving in water or warm
water at 50°C or lower. A production method for this type of water-soluble soybean
polysaccharide is described in Japanese Patent Application Publication No.
H5-32701. In addition, an example of a commercially available product of the water-soluble
soybean polysaccharide is Soyafib-S-LN (Fuji Oil Co., Ltd.) and the like. A soybean
polysaccharide having a viscosity of a 10% by weight aqueous solution thereof (25°C)
within the range of 5 cp to 100 cp is preferably used as a water-soluble soybean polysaccharide
able to be used in the present invention.
[0022] These substances can be used alone or as a mixture, and in order to allow the plate
cleaning agent to have a preferable viscosity range (about 100 cps to 1000 cps), their
amount used is suitably 1% by weight to 24% by weight, and can be more preferably
selected from the range of 3% by weight to 20% by weight based on the total weight
of the plate cleaning agent.
[0023] Examples of the component (2) include phosphoric acid, sodium phosphate, potassium
phosphate, lithium phosphate, pyrophosphoric acid, sodium pyrophosphate, potassium
pyrophosphate, lithium pyrophosphate, triphosphoric acid, sodium triphosphate, potassium
triphosphate, lithium triphosphate, tetraphosphoric acid, sodium tetraphosphate, potassium
tetraphosphate, lithium tetraphosphate, metaphosphoric acid, sodium metaphosphate,
potassium metaphosphate, lithium metaphosphate, trimetaphosphoric acid, sodium trimetaphosphate,
potassium trimetaphosphate, lithium trimetaphosphate, hexametaphosphoric acid, sodium
hexametaphosphate, potassium hexametaphosphate, lithium hexametaphosphate, methylene
diphosphonic acid, 1-hydroxyethane-1,1-disulfonic acid, nitrilotrisphosphonic acid,
N-carboxymethyl-N,N-di(methylenephosphonic acid), hexamethylenediamine-tetra(methylenephosphonic
acid), ethylenediamine-tetra(methylenephosphonic acid) diethylenetriamine-penta(methylenephosphonic
acid), N,N-di(carboxymethyl)-N-methylenephosphonic acid, N-(2-hydroxyethyl)-N,N-di(methylenephosphonic
acid), N-hydroxymethyl-N,N',N'-ethylenediaminetris(methylenephosphonic acid), N-hydroxyethyl-N',N'-diethylethylenediamine-N,N,N',N'-tetra(methylenephosphonic
acid), di(2-hydroxypropylene)triamine penta(methylenephosphonic acid), and tri(2-hydroxypropylene)
tetraaminehexa(methylenephosphonic acid) and the like. These compounds can also be
acquired as commercially available products, and are commercially available as, for
example, the Dequest series available from Monsanto Chemical Company or the Wayplex
series available from the Wayland Chemical Division of the Philip A. Hant Chemical
Corp. The above-mentioned compounds can be used alone or two or more types can be
used in combination, and are contained within the range of 0.1% by weight to 15% by
weight and more preferably within the range of 0.5% by weight to 10% by weight based
on the total weight of the plate cleaning agent according to the present invention.
[0024] Examples of the nitric acid and/or nitrates of component (3) used in the present
invention include, in addition to nitric acid, nitrates in the form of metal salts
of nitric acid, in the manner of zinc nitrate, cobalt nitrate, magnesium nitrate,
sodium nitrate, potassium nitrate, nickel nitrate, bismuth nitrate, tin nitrate, strontium
nitrate, cesium nitrate, rubidium nitrate and cerium nitrate, as well as ammonium
nitrate. The usage range of the nitric acid and/or water-soluble nitric acid metal
salt used in the present invention is 0.1% by weight to 10% by weight, and more preferably
0.5% by weight to 5% by weight, based on the total weight of the plate cleaning agent.
[0025] Examples of the sulfuric acid, sulfates and/or bisulfates of component (4) used in
the present invention include, in addition to sulfuric acid, sulfates or bisulfates
such as sodium sulfate, potassium sulfate, cesium sulfate, rubidium sulfate or aluminum
sulfate. Bisulfates are represented by the general formula M(HSO
4)
n (wherein, M represents a metal and n indicates the valence of M), and examples thereof
include strontium bisulfate, potassium bisulfate, calcium bisulfate, thallium bisulfate,
sodium bisulfate, lead bisulfate, bismuth bisulfate, magnesium bisulfate and rhodium
bisulfate. These compounds can be used alone or two or more types can be used in combination,
and are contained within a range of 0.01% by weight to 5% by weight, and more preferably
0.1% by weight to 3% by weight, based on the total weight of the plate cleaning agent
according to the present invention.
[0026] Although the remaining component of the aqueous phase of the plate cleaning agent
of the present invention is water, the amount thereof is suitably 45% by weight to
85% by weight, and more preferably 50% by weight to 80% by weight, based on the total
weight of the plate cleaning agent of the present invention.
[0027] On the other hand, the hydrocarbon-based solvent of component (6) can be used concurrently
in the oily phase of the plate cleaning agent of the present invention. A petroleum
residue normally used to clean printing ink having a boiling point of 120°C to 350°C
is particularly useful for use as the component (6). Specific examples of such hydrocarbon-based
solvents include products manufactured by Nippon Petrochemicals Co., Ltd. consisting
of Cleansol (volatile oil), dry solvent, A solvent, K solvent, mineral spirit A and
Hiarom 25 having melting points of 150°C to 200°C, insecticide solvent, fog solvent
and non-sulfur solvent having boiling points of 200°C to 250°C, and no. 3 solvent,
no. 4 solvent, no. 5 solvent, no. 6 solvent and no. 7 solvent having boiling points
of 250°C to 300°C, as well as tall oil fatty acid ester, Swasol (aromatic-based, high
boiling point solvent, Maruzen Petrochemical Co., Ltd.), Exxsol (Exxon Chemical Japan,
Ltd.) and Exxol (naphthene-based solvent, ExxonMobil Corp.). The usage range of these
hydrocarbon-based solvents is suitably 1% by weight to 50% by weight, and more preferably
5% by weight to 35% by weight, based on the total weight of the plate cleaning agent.
[0028] Since component (6) is not miscible with the water of component (5), it is used in
an adequately mixed and dispersed state at the time of use. It is useful to add the
surfactant of component (7) for the purpose of enhancing dispersion stability at this
time. Surfactants able to be used in the present invention consist of anionic surfactants
and nonionic surfactants.
[0029] Examples of anionic surfactants include fatty acid salts, abietic acid salts, hydroxyalkanesulfonic
acid salts, alkanesulfonic acid salts, dialkylsulfosuccinic acid salts, linear alkylbenzenesulfonic
acid salts, branched alkylbenzenesulfonic acid salts, alkylnaphthalenesulfonic acid
salts, alkylphenoxypolyoxyethylene propylsulfonic acid salts, polyoxyethylene alkyl
sulfophenyl ether salts, sodium N-methyl-N-oleyltaurate, disodium N-alkylsulfosuccinate
monoamide, petroleum sulfonic acid salts, sulfated castor oil, sulfated beef tallow,
sulfuric acid ester salts of fatty acid alkyl esters, alkyl sulfate ester salts, polyoxyethylene
alkyl ether sulfate ester salts, fatty acid monoglyceride sulfate ester salts, polyoxyethylene
alkyl phenyl ether sulfate ester salts, polyoxyethylene styryl phenyl ether sulfate
ester salts, alkyl phosphate ester salts, polyoxyethylene alkyl ether phosphate ester
salts, polyoxyethylene alkyl phenyl ether phosphate ester salts, partially saponified
styrene-maleic anhydride copolymers, partially saponified olefin-maleic anhydride
copolymers, naphthalene sulfonate formalin condensates and the like. Among these,
dialkylsulfosuccinic acid salts, alkyl sulfate esters and alkylbenzenesulfonic acid
salts are used particularly preferably.
[0030] In addition, examples of nonionic surfactants include polyoxyethylene alkyl ethers,
polyoxyethylene alkyl phenyl ethers, polyoxyethylene polystyryl phenyl ethers, polyoxyethylene
polyoxypropylene alkyl ethers, glycerin fatty acid partial esters, sorbitan fatty
acid partial esters, pentaerythritol fatty acid partial esters, propylene glycol mono
fatty acid esters, sucrose fatty acid partial esters, polyoxyethylene sorbitan fatty
acid partial esters, polyoxyethylene sorbitol fatty acid partial esters, polyethylene
glycol fatty acid esters, polyglycerin fatty acid partial esters, polyoxyethylated
castor oil, polyoxyethylene glycerin fatty acid partial esters, fatty acid diethanolamides,
N,N-bis-2-hydroxyalkylamines, polyoxyethylene alkylamines, triethanolamine fatty acid
esters, trialkylamine oxides and the like. Among these, sorbitan fatty acid partial
esters, polyoxyethylated castor oil ethers, polyoxyethylene alkyl ethers, polyoxyethylene
alkyl phenyl ethers and polyoxyethylene-polyoxypropylene block polymers are used preferably.
Two or more types of these surfactants may be used concurrently. Although there are
no particular limitations on the amount of surfactant used, a preferable range is
0.5% by weight to 10% by weight based on the total weight of the plate cleaning agent.
[0031] In addition to the above-mentioned components, one type or two or more types of wetting
agents (component (8)) are useful for imparting favorable spreading characteristics
to the plate cleaning agent, suppressing drying and imparting favorable usage appropriateness.
Suitable wetting agents are compounds represented by the general formula: HO-(R-O)
n-H (wherein, R represents C
mH
2m (m = 2 to 6), and n represents 1 to 500). Specific examples of preferable compounds
include ethylene glycol, propylene glycol, butylene glycol, pentanediol, hexylene
glycol, diethylene glycol, triethylene glycol, tetraethylene glycol, polyethylene
glycol, dipropylene glycol and tripropylene glycol, while glycerin, sorbitol and pentaerythritol
are useful as other wetting agents. The amount of wetting agent used is typically
within the range of 0.5% by weight to 10% by weight, and more preferably within the
range of 1% by weight to 5% by weight, based on the total weight of the plate cleaning
agent.
[0032] The thixotropic agent of component (9) improves work properties when treating a plate
surface with a sponge and the like by lowering viscosity of the liquid with dynamic
pressure and raising viscosity when still. Examples of suitable thixotropic agents
include finely powdered silicic acid, pumice, calcium carbonate, zeolite and the like.
The amount used is suitably within the range of 0.5% by weight to 10% by weight, and
preferably within the range of 1% by weight to 7% by weight, based on the total weight
of the plate cleaning agent.
[0033] The plate cleaning agent of the present invention is preferably adjusted to be acidic,
and more specifically, to a pH range of 1.0 to 4.0, preferably to a pH range of 1.5
to 4.0, and more preferably to a pH range of 1.5 to 3.0. ApH adjuster (component (10))
can be used to adjust to these pH ranges. Examples of pH adjusters that can be used
include phosphoric acid, nitric acid, sulfuric acid, phosphorous acid and organic
carboxylic acids such as citric acid, acetic acid, malonic acid, tartaric acid, malic
acid, lactic acid, levulinic acid, butyric acid, maleic acid or picolinic acid. In
addition, bases in the form of metal hydroxides such as hydroxides of alkaline metals
or alkaline earth metals may also be used concurrently. Examples of such metal hydroxides
include sodium hydroxide, potassium hydroxide, lithium hydroxide, rubidium hydroxide,
cesium hydroxide, beryllium hydroxide, magnesium hydroxide, calcium hydroxide and
barium hydroxide.
[0034] In addition to the above-mentioned components, preservatives (disinfectants), colorants
and the like can also be added. Examples of preservatives include phenol or derivatives
thereof, formalin, imidazole derivatives, sodium dihydroacetate, 4-isothiazolin-3-one
derivatives, benzisothiazolin-3-one derivatives, benzotriazole derivatives, amidine-guanidine
derivatives, pyridine quaternary ammonium salts, quinoline-guanidine derivatives,
diazine, triazole derivatives, oxazole, oxazine derivatives and bromonitroalcohol-based
preservatives such as 2-bromo-2-nitropropane-1,3-diol. The preferable amount of preservative
added is an amount that stably demonstrates efficacy against bacteria, molds, yeast
and the like, is typically added at roughly 0.01% by weight to 3% by weight based
on the total weight of the plate cleaning agent, and two or more types of preservatives
are preferably used concurrently so as to be effective against various molds and bacteria.
The colorant is used to impart visual contrast by imparting a desired color tone to
the plate cleaning agent of the present invention, and can be selected from a wide
range of dyes. Particularly preferable examples of colorants used include blue, violet
and red colorants. Specific examples include crystal violet, safranin, brilliant blue,
malachite green and acid rhodamine B. The amount used is suitably 0.0001% by weight
to 0.1% by weight, and more preferably within the range of 0.0003% by weight to 0.05%
by weight, based on the total weight of the plate cleaning agent.
[0035] The emulsified plate cleaning agent for a lithographic printing plate of the present
invention can be produced in accordance with ordinary methods as a typical emulsified
O/W type or W/O type of emulsion.
[0036] The emulsified plate cleaning agent for a lithographic printing plate of the present
invention can be preferably used for a lithographic printing plate obtained by platemaking
from a photopolymerizable lithographic printing plate in which is provided an oxygen-blocking
protective layer, and particularly an oxygen-blocking protective layer containing
inorganic fine particles. An example of such a photopolymerizable lithographic printing
plate precursor is described in Japanese Patent Application Publication No.
2005-119273.
[0037] The structure of a photopolymerizable lithographic printing plate precursor able
to be preferably used by the plate cleaning agent of the present invention is that
of a lithographic printing plate precursor having an image recording layer containing
(A) an active light absorber, (B) a polymerization initiator and (C) a polymerizable
compound, and an oxygen-blocking protective layer containing inorganic fine particles,
and particularly inorganic layered compounds, in that order.
[0038] The following provides a brief explanation of the configuration of the above-mentioned
photopolymerizable lithographic printing plate precursor, platemaking process and
printing process.
[Oxygen-Blocking Protective Layer]
[0039] Inorganic fine particles contained in the oxygen-blocking protective layer are classified
into spherical fine particles and layered fine particles.
[Spherical Fine Particles]
[0040] Examples of inorganic spherical fine particles include those of metals and metal
compounds such as oxides, composite oxides, hydroxides, carbonates, sulfates, silicates,
phosphates, nitrides, carbides, sulfides and composite compounds of at least two or
more types thereof, and more specifically, glass, zinc oxide, silica, alumina, zircon
oxide, tin oxide, potassium titanate, strontium titanate, aluminum borate, magnesium
oxide, magnesium borate, aluminum hydroxide, magnesium hydroxide, calcium hydroxide,
titanium hydroxide, basic magnesium sulfate, calcium carbonate, magnesium carbonate,
calcium sulfate, magnesium sulfate, calcium silicate, magnesium silicate, calcium
phosphate, silicon nitride, titanium nitride, aluminum nitride, silicon carbide, titanium
carbide, zinc sulfide and composite compounds of at least two or more types thereof.
Preferable examples include glass, silica, alumina, potassium titanate, strontium
titanate, aluminum borate, magnesium oxide, calcium carbonate, magnesium carbonate,
calcium silicate, magnesium silicate, calcium phosphate and calcium sulfate.
[0041] Preferable examples of silica fine particles include Snowtex 50 (particle size: 0.025
µm), Snowtex O-40 (particle size: 0.025 µm), Snowtex CM (particle size: 0.025 µm),
Snowtex 20L (particle size: 0.045 µm), Snowtex XL (particle size: 0.05 µm), Snowtex
YL (particle size: 0.65 µm), Snowtex ZL (particle size: 0.85 µm), MP1040 (particle
size: 0.1 µm), MP2040 (particle size: 0.2 µm), MP3040 (particle size: 0.3 µm), MP1040
(particle size: 0.1 µm) and MP4540M (particle size: 0.45 µm) manufactured by Nissan
Chemical Industries, Ltd., and Sylysia 310 (particle size: 1.4 µm), Sylysia 320 (particle
size: 1.6 µm), Sylysia 350 (particle size: 1.8 µm), Sylysia 370 (particle size: 3.0
µm), Sylysia 530 (particle size: 1.9 µm), Sylysia 550 (particle size: 2.7 µm), Sylysia
250 (particle size: 2.7 µm) and Sylysia 430 (particle size: 2.5 µm) manufactured by
Fuji Silysia Chemical Ltd.
[0042] Inorganic-organic composite fine particles are also preferable, and preferable examples
thereof include synthetic resin particles and natural polymer particles, preferably
resin particles such as those of acrylic resin, polyethylene, polypropylene, polyethylene
oxide, polypropylene oxide, polyethyleneimine, polystyrene, polyurethane, polyurea,
polyester, polyamide, polyimide, carboxymethyl cellulose, gelatin, starch, chitin,
chitosan and the like, and more preferably composite fine particles in which the surface
of resin particles such as those of acrylic resin, polyethylene, polypropylene or
polystyrene is coated with the above-mentioned inorganic fine particles.
[0043] Among these inorganic spherical fine particles, those in which the inorganic component
is silica (SiO
2) are particularly preferable from the viewpoints of dispersion stability when using
as a coating solution, cost and high coefficient of friction.
[0044] The size of the inorganic spherical fine particles is such that the average particle
size is preferably 0.001 µm to 1 µm, more preferably 0.03 µm to 0.5 µm, and even more
preferably 0.05 µm to 0.2 µm. If the particle size is excessively large, image formation
sensitivity decreases to a considerable decrease in oxygen blocking, and due to the
smaller contact area of the organic fine particles, the effect of increasing the coefficient
of friction is insufficiently obtained resulting in increased susceptibility to shifting.
If the particle size is excessively small, the structure of the inorganic layered
compounds is unable to be disrupted, preventing obtaining of the effect of inhibiting
fogging. Adequate effects with respect to coefficient of friction are unable to be
obtained relative to the amount of spherical fine particles added due to a decrease
in the amount of protrusions from the surface, thereby resulting in the problem of
a lack of balance with image forming performance.
[0045] The above-mentioned average particle size is measured with the centrifugal sedimentation
method using a particle size distribution measuring device (BI-DCP, Brookhaven Instruments).
[0046] The content of the total inorganic spherical fine particle component contained in
the protective layer is preferably 0.1% by weight to 80% by weight, more preferably
1% by weight to 50% by weight, and even more preferably 5% by weight to 30% by weight.
[Inorganic Layered Fine Particles]
[0047] Examples of inorganic layered fine particles include particles in the form of thin
plates, including those belonging to the mica group such as natural mica or synthetic
mica represented by the following general formula: A(B,C)
2-5D
4O
10(OH,F,O)
2 (wherein, A represents K, Na or Ca, B and C represent Fe(II), Fe(III), Mn, Al, Mg
or V, and D represents Si or Al), and talc represented by the formula: 3MgO·4SiO·H
2O, taeniolite, montmorillonite, saponite, hectorite and zirconium phosphate.
[0048] Examples of natural mica belonging to the above-mentioned mica group include muscovite,
paragonite, phlogopite, biotite and lepidolite. In addition, examples of synthetic
mica include non-swellable mica such as fluor-phlogopite KMg
3(AlSi
3O
10)F
2 or potassium tetrasilicate mica KMg
2.5(Si
4O
10)F
2, and swellable mica such as Na tetrasilicate mica NaMg
2.5(Si
4O
10)F
2, Na or Li taeniolite (Na,Li)Mg
2Li(Si
4O
10)F
2, or montmorillonite-based Na or Li hectorite (Na,Li)
1/8Mg
2/5Li
1/8(Si
4O
10)F
2. Moreover, synthetic smectite is also useful.
[0049] Among the above-mentioned inorganic layered compounds, synthetic inorganic layered
compounds in the form of fluorine-based swellable micas are particularly useful. Namely,
the swellable synthetic micas and swellable clay minerals such as montmorillonite,
saponite, hectorite, bentonite and the like have a layered structure composed of unit
crystal lattice layers having a thickness of about 10 Å to 15 Å, and metal atom substitution
within the lattice is considerably greater than other clay minerals. As a result,
a positive charge deficiency occurs in the lattice layers, and in order to compensate
for this, cations such as Na
+, Ca
2+ or Mg
2+ are adsorbed between the layers. These cations interposed between the layers are
referred to as exchangeable cations, and are exchanged with various cations. In the
case the interlayer cations are Li
+ or Na
+ in particular, bonding between the layered crystal lattices is weak due to the small
ionic radius thereof, causing these layered compounds to be swelled considerably by
water. When shear is applied while in this state, cleavage occurs readily and a stable
sol is formed in water. Bentonite and swellable synthetic micas strongly demonstrate
this tendency making them more useful, and swellable synthetic micas are used particularly
preferably.
[0050] From the viewpoint of controlling diffusion, the shape of the inorganic layered compounds
used is such that the thickness is as thin as possible, and the size of the flat side
is preferably as large as possible provided smoothness of the coated surface and transmission
of active light are not impaired. Thus, the aspect ratio is 20 or more, preferably
100 or more and particularly preferably 200 or more. Furthermore, aspect ratio represents
the ratio of diameter to thickness of the particles, and can be measured from, for
example, a projection of the particles obtained from a micrograph. Greater effects
are obtained the larger the aspect ratio.
[0051] The particle size of the organic layered compounds used is such that the average
diameter is 0.3 µm to 20 µm, preferably 0.5 µm to 10 µm and particularly preferably
1 µm to 5 µm. In addition, the average thickness of the particles is 0.1 µm or less,
preferably 0.05 µm or less and particularly preferably 0.01 µm or less. For example,
among the inorganic layered compounds, the size of a typical compound in the form
of swellable synthetic mica is such that the thickness is 1 nm to 50 nm and the face
size is about 1 µm to 20 µm.
[0052] If particles of an inorganic layered compound having a large aspect ratio in this
manner are contained in the oxygen-blocking protective layer, coated film strength
improves, and since the permeation of oxygen and moisture can be effectively prevented,
deterioration of the oxygen-blocking protective layer caused by deformation and the
like is prevented, and even if stored for a long period of time under conditions of
high humidity, storage stability is superior without demonstrating decreases in image
forming performance in the lithographic printing plate precursor caused by changes
in humidity.
[0053] The content of the inorganic layered compound in the protective layer is preferably
at weight ratio of 5/1 to 1/100 based on the amount of binder used in the protective
layer. In the case of combining the use of several types of inorganic layered compounds,
the total amount of these inorganic layered compounds is preferably within the range
of the above-mentioned weight ratio.
[0054] A binder is preferably used in the oxygen-blocking protective layer along with the
above-mentioned inorganic fine particles.
[0055] There are no particular limitations on the binder provided it facilitates dispersibility
of inorganic fine particles such as layered fine particles and enables the formation
of a uniform film that adheres to the image recording layer, and both water-soluble
polymers and water-insoluble polymers can be suitably selected and used. Specific
examples include water-soluble polymers such as polyvinyl alcohol, modified polyvinyl
alcohol, polyvinylpyrrolidone, polyvinyl imidazole, polyacrylic acid, polyacrylamide,
partially saponified polyvinyl acetate, ethylene-vinyl alcohol copolymer, water-soluble
cellulose derivatives, gelatin, starch derivatives, gum arabic and the like, and polymers
such as polyvinylidene chloride, poly(meth)acrylonitrile, polysulfone, polyvinyl chloride,
polyethylene, polycarbonate, polystyrene, polyamide, cellophane and the like. Two
or more types of these can also be used in combination as necessary.
[0056] Among these, water-soluble polymers are preferable from the viewpoints of ease of
removal of the protective layer remaining on nonimage areas and handling ease during
film formation, with polyvinyl alcohol, polyvinylpyrrolidone, polyvinyl imidazole,
water-soluble acrylic resins such as polyacrylic acid, gelatin, gum arabic and the
like being preferable, and in particular, polyvinyl alcohol, polyvinylpyrrolidone,
gelatin and gum arabic being more preferable from the viewpoints of being able to
be coated using water as a solvent and being easily removed by fountain solution during
printing.
[0057] A portion of the polyvinyl alcohol able to be used in the oxygen-blocking protective
layer may be substituted with an ester, ether or acetal provided a substantial amount
of unsubstituted vinyl alcohol units having the required water solubility are contained.
In addition, a portion may similarly contain other polymer components. Specific examples
of polyvinyl alcohols include those of which 71 mol% to 100 mol% are hydrolyzed that
have a degree of polymerization within the range of 300 to 2400. More specifically,
examples of these include PVA-105, PVA-110, PVA-117, PVA-117H, PVA-120, PVA-124, PVA-124H,
PVA-CS, PVA-CST, PVA-HC, PVA-203, PVA-204, PVA-205, PVA-210, PVA-217, PVA-220, PVA-224,
PVA-217EE, PVA-217E, PVA-220E, PVA-224E, PVA-405, PVA-420, PVA-613 and L-8 manufactured
by Kuraray Co., Ltd. Examples of the above-mentioned copolymers include polyvinyl
acetate chloroacetate or propionate, polyvinylformal, polyvinylacetal and copolymers
thereof of which 88 mol% to 100 mol% are hydrolyzed.
[0058] The above-mentioned inorganic fine particles, such as layered fine particles, are
dispersed in water by a suitable method followed by the preparation of an oxygen-blocking
protective layer coating liquid from this dispersion. Known additives such as surfactants
for improving coatability or water-soluble plasticizers for improving physical properties
of the film can be added to the oxygen-blocking protective layer coating liquid in
addition to the above-mentioned components. The prepared oxygen-blocking protective
layer coating liquid is coated onto an image recording layer provided on a support
followed by drying to form the oxygen-blocking protective layer. Although the coating
solvent can be suitably selected in correlation with the binder, in the case of using
a water-soluble polymer, it is preferable use distilled water or purified water. There
are no particular limitations on the method used to coat the oxygen-blocking protective
layer, and a known method can be applied, such as that described in
U.S. Patent No. 3,458,311 or that described in Japanese Examined Patent Application Publication No.
S55-49729. More specifically, examples of methods used to coat the oxygen-blocking protective
layer include blade coating, air knife coating, gravure coating, roll coating, spray
coating, dip coating, bar coating and the like.
[0059] The coated amount of the oxygen-blocking protective layer in terms of the coated
amount after drying is preferably within the range of 0.01 g/m
2 to 10 g/m
2, more preferably within the range of 0.02 g/m
2 to 3 g/m
2, and most preferably within the range of 0.02 g/m
2 to 1 g/m
2.
Components Comprising Image Recording Layer
[(A) Active Light Absorber]
[0060] The active light absorber is a compound that absorbs light radiated by a exposure
light source, efficiently generates radicals from the polymerization initiator in
a photon mode and/or heat mode, and contributes to improving the sensitivity of the
lithographic printing plate precursor. The active light absorber is preferably an
infrared absorber in the case of imagewise exposure of the lithographic printing plate
precursor with an infrared laser, while a sensitizing dye that absorbs light of a
wavelength of 250 nm to 420 nm is preferable in the case of imagewise exposure of
the lithographic printing plate precursor with an ultraviolet laser for images. The
infrared absorber is preferably a dye or pigment that has an absorption maximum at
a wavelength of 760 nm to 1200 nm. A known infrared absorber can be suitably selected
for this infrared absorber.
[0061] Particularly preferable examples of these dyes include cyanine dyes, squarylium dyes,
pyrylium salts, nickel thiolate complexes and indolenine cyanine dyes. Cyanine dyes
and indolenine cyanine dyes are more preferable.
[0062] These infrared absorbers can be added at a ratio of 0.001% by weight to 50% by weight,
preferably 0.005% by weight to 30% by weight, and particularly preferably 0.01% by
weight to 10% by weight based on the total solid fraction of the image recording layer.
If within these ranges, high sensitivity is obtained without having an undesirable
effect on uniformity or film strength of the image recording layer.
[0063] In addition, a sensitizing dye may also be used, and the sensitizing dye used is
a compound having absorption at a wavelength of 250 nm to 420 nm, specific examples
of which include benzoin, benzoin methyl ether, benzoin ethyl ether, 9-fluorenone,
2-chloro-9-fluorenone, 2-methyl-9-fluorenone, 9-anthrone, 2-bromo-9-anthrone, 2-ethyl-9-anthrone,
9,10-anthraquinone, 2-ethyl-9,10-anthraquinone, 2-t-butyl-9,10-anthraquinone, 2,6-dichloro-9,10-anthraquinone,
xanthone, 2-methylxanthone, 2-methoxyxanthone, thioxanthone, benzyl, dibenzalacetone,
p-(dimethylamino)phenyl styryl ketone, p-(dimethylamino)phenyl p-methyl styryl ketone,
benzophenone, p-(dimethylamino) benzophenone (or Michler's ketone), p-(diethylamino)
benzophenone and benzanthrone.
[0064] These sensitizing dyes can be added preferably at a ratio of 0.1% by weight to 50%
by weight, more preferably 0.5% by weight to 30% by weight and particularly preferably
0.8% by weight to 20% by weight based on the total solid fraction that composes the
image recording layer.
[(B) Polymerization Initiator]
[0065] The polymerization initiator is a compound that initiates and promotes the polymerization
of a compound having polymerizable unsaturated groups by generating radicals using
light energy, heat energy or both. Examples of polymerization initiators that can
be used include known thermal polymerization initiators, compounds having bonds with
weak bond dissociation energy, and photopolymerization initiators.
[0066] Examples of the polymerization initiators as described above include organic halogen
compounds, carbonyl compounds, organic peroxides, azo-type polymerization initiators,
azide compounds, metallocene compounds, hexarylbiimidazole compounds, organic boron
compounds, disulfone compounds, oxime ester compounds, oxime ether compounds and onium
salt compounds.
[0067] The polymerization initiator used preferably has a maximum absorption wavelength
of 400 nm or less, more preferably a maximum absorption wavelength of 360 nm or less,
and most preferably a maximum absorption wavelength of 300 nm or less. The incandescent
stability of the lithographic printing plate precursor is improved by using an absorption
wavelength for the ultraviolet range in this manner.
[0068] These polymerization initiators can be added at a ratio 0.1% by weight to 50% by
weight, preferably 0.5% by weight to 30% by weight and particularly preferably 1%
by weight to 20% by weight based on the total solid fraction composing the image recording
layer. If within these ranges, favorable sensitivity and favorable resistance to scumming
of nonimage areas during printing can be obtained. Only one type of these polymerization
initiators may be used or two or more types may be used in combination. In addition,
these polymerization initiators may be added to the same layer with other components,
or a separate layer may be provided followed by adding the polymerization initiators
thereto.
[(C) Polymerizable Compound]
[0069] The polymerizable compound used in the image recording layer is an addition polymerizable
compound that has at least one ethylenically unsaturated double bond, and is selected
from compounds having at least one, and preferably two, terminal ethylenically unsaturated
bonds. Such groups of compounds are widely known in the pertinent industrial field,
and can be used without any particular limitations thereon. These compounds have a
chemical form of, for example, a monomer, a prepolymer, namely a dimer, trimer or
oligomer, a mixture thereof or a copolymer thereof. Examples of monomers and copolymers
thereof include unsaturated carboxylic acids (such as acrylic acid, methacrylic acid,
itaconic acid, crotonic acid, isocrotonic acid or maleic acid), esters thereof and
amides thereof, and esters of unsaturated carboxylic acids and aliphatic polyvalent
alcohols, and amides of unsaturated carboxylic acids and aliphatic polyvalent amine
compounds, are used preferably. In addition, addition reaction products of unsaturated
carboxylic acid esters or amides having a nucleophilic substituent such as a hydroxyl
group, amino group or mercapto group and monofunctional or polyfunctional isocyanates
or epoxy compounds, as well as dehydration condensation reaction products between
monofunctional or polyfunctional carboxylic acids, are also used preferably. In addition,
addition reaction products of unsaturated carboxylic acid esters or amides having
an electrophilic substituent such as an isocyanate group or epoxy group and monofunctional
or polyfunctional alcohols, amines or thiols, as well as substitution reaction products
between unsaturated carboxylic acid esters or amides having a leaving substituent
such as a halogen group or tosyloxy group and a monofunctional or polyfunctional alcohol,
amines or thiol, are also preferable. In addition, other examples of compounds that
can be used include groups of compounds in which an unsaturated phosphonic acid, styrene
or vinyl ether and the like have been substituted instead of the above-mentioned unsaturated
carboxylic acid.
[0070] Details regarding the manner in which these polymerizable compounds are used, such
as their structure, independent or combined use or amount added, can be set arbitrarily
according to the ultimate performance design of the lithographic printing plate precursor.
These details are set based on, for example, the viewpoints indicated below.
[0071] With respect to sensitivity, a structure having a large number of unsaturated groups
per molecule is preferable, and in many cases, a bifunctional or greater compound
is preferable. In addition, in order to increase the strength of image areas, or in
other words, the cured film, a trifunctional or greater compound is preferable, and
a method that adjusts both sensitivity and strength by combining with the use of that
having a different number of functional groups and different polymerizable groups
(such as an acrylic ester, methacrylic ester, styrene-based compound or vinyl ether-based
compound) is also effective.
[0072] In addition, selection and the manner of use of the polymerizable compound is also
an important factor with respect to compatibility and dispersibility with other components
in the image recording layer (such as a binder polymer, polymerization initiator,
colorant and the like), and for example, compatibility can be improved by using compounds
having low purity or combining the use of two or more types. In addition, a specific
structure can also be selected for the purpose of improving adhesion with the support
or oxygen-blocking protective layer and the like.
[0073] The above-mentioned polymerizable compound is preferably used within the range of
5% by weight to 80% by weight and more preferably 25% by weight to 75% by weight in
the image recording layer. In addition, these may be used alone or two or more types
may be used in combination. In addition, the manner in which the polymerizable compound
is used is such that a suitable structure, incorporation and amount added can be arbitrarily
selected from the viewpoints of the degree of inhibition of polymerization with respect
to oxygen, resolution, fogging, changes in refractive index, surface adhesiveness
and the like, and depending on the case, a layered configuration and coating method
such as undercoating or topcoating can also be carried out.
[Other Components of Image Recording Layer]
[0074] Components other than the above-mentioned components (A), (B) and (C), such as binder
polymers, surfactants, printout agents, polymerization inhibitors (thermal polymerization
inhibitors), higher fatty acid derivatives, plasticizers, inorganic fine particles
or low molecular weight hydrophilic compounds can be contained in the image recording
layer.
[0075] A conventionally known binder polymer can be used without limitation for the binder
polymer, and linear organic polymers capable of forming a film are preferable. Examples
of such binder polymers include acrylic resins, polyvinyl acetal resins, polyurethane
resins, polyurea resins, polyimide resins, polyamide resins, epoxy resins, methacrylic
resins, polystyrene resins, novolac-type phenolic resins, polyester resins, synthetic
rubbers, and natural rubbers.
[0076] A single binder polymer may be used alone or two or more types may be used as a mixture.
The content of the binder polymer is preferably 10% by weight to 90% by weight and
more preferably 20% by weight to 80% by weight based on the total solid fraction of
the image recording layer. If within these ranges, favorable strength of the image
areas and favorable image formability are obtained. In addition, the polymerizable
compound and the binder polymer are preferably used at a weight ratio of 1/9 to 7/3.
[0077] A surfactant can be used in the image recording layer to promote on-press developability
at the start of printing and to improve coated surface properties. Examples of surfactants
include nonionic surfactants, anionic surfactants, cationic surfactants, amphoteric
surfactants, fluorine-based surfactants and the like. The surfactant may be used alone
or two or more types may be used in combination.
[0078] The surfactant can be used alone or two or more types can be used in combination.
The surfactant is preferably contained in the image recording layer at 0.001% by weight
to 10% by weight and more preferably contained at 0.01% by weight to 5% by weight.
[0079] A dye that absorbs strongly in the visible light region can be used as a colorant
in the image recording layer. Specific examples include Oil Yellow #101, Oil Yellow
#103, Oil Pink #312, Oil Green BG, Oil Blue BOS, Oil Blue #603, Oil Black BY, Oil
Black BS, and Oil Black T-505 (the preceding are products of Orient Chemical Industries,
Ltd.), as well as Victoria Pure Blue, Crystal Violet (CI 42555), Methyl Violet (CI
42535), Ethyl Violet, Rhodamine B (CI 145170B), Malachite Green (CI 42000), Methylene
Blue (CI 52015), and the dyes described in Japanese Patent Application Publication
No.
S62-293247. In addition, pigments such as phthalocyanine pigments, azo pigments, carbon black,
titanium oxide and the like can also be used preferably.
[0080] The addition of these colorants is preferable since their use facilitates discrimination
of the image areas from the nonimage areas following image formation. Furthermore,
the colorant is preferably added at a ratio of 0.01% by weight to 10% by weight in
the image recording layer.
[0081] A compound that changes color due to the action of acid or radicals can be added
to the image recording layer of the present invention in order to produce a printout
image. Various types of dyes are effectively used for this compound, examples of which
include diphenylmethane types, triphenylmethane types, thiazine types, oxazine types,
xanthene types, anthraquinone types, iminoquinone types, azo types, azomethine types
and the like.
[0082] A small amount of polymerization inhibitor is preferably added to prevent unwanted
thermal polymerization of the polymerizable compound (C) during production or storage
of the image recording layer.
[0083] Suitable examples of the thermal polymerization inhibitor include hydroquinone, p-methoxyphenol,
di-t-butyl-p-cresol, pyrogallol, t-butylcatechol, benzoquinone, 4,4'-thiobis (3-methyl-6-t-butylphenol),
2,2'-methylenebis(4-methyl-6-t- butylphenol), and N-nitroso-N-phenylhydroxylamine
aluminum salt.
[0084] The thermal polymerization inhibitor is preferably contained at about 0.01% by weight
to about 5% by weight in the image recording layer.
[0085] A higher fatty acid derivative and the like in the manner of behenic acid or behenamide
may be added to the image recording layer to prevent inhibition of polymerization
by oxygen, and may be partitioned on the surface of the image recording layer during
the course of drying after coating. The amount of the higher fatty acid derivative
added is preferably about 0.1% by weight to about 10% by weight based on the total
solid fraction of the image recording layer.
[0086] The image recording layer is formed by preparing a coating liquid by dispersing or
dissolving the above-mentioned constituents in a suitable solvent and then coating
the coating liquid.
[0087] The image recording layer can also be formed by preparing a plurality of coating
liquids in which each of the same or different components are dispersed or dissolved
in the same or different solvent followed by repeatedly coating and drying a plurality
of times. The coated amount (solid fraction) on the image recording layer is preferably
0.3 g/m
2 to 1.5 g/m
2 and more preferably 0.5 g/m
2 to 1.5 g/m
2.
[0088] Various methods can be used for the coating method. Examples of coating methods include
bar coating, spin coating, spray coating, curtain coating, dip coating, air knife
coating, blade coating, roll coating and the like.
[0089] There are no particular limitations on the support used in the lithographic printing
plate precursor provided it is in the shape of a dimensionally stable plate. Examples
of materials of the support include paper, plastic-laminated paper (such as polyethylene,
polypropylene, polystyrene and the like), metal plate or sheet (such as aluminum,
zinc, copper and the like), plastic film (such as cellulose diacetate, cellulose triacetate,
cellulose propionate, cellulose butyrate, cellulose acetate butyrate, cellulose nitrate,
polyethylene terephthalate, polyethylene, polystyrene, polypropylene, polycarbonate,
polyvinyl acetal and the like), and paper or plastic film on which any of the above-mentioned
metals has been laminated or vapor-deposited. Preferable examples of the support include
a polyester film and an aluminum sheet. An aluminum sheet is particularly preferable
due to its dimensional stability and comparatively low cost.
[0090] The lithographic printing plate precursor may also be further provided with a backcoating
or undercoating.
[Platemaking and Printing]
[0091] The lithographic printing plate precursor as previously described is imagewise exposed
by exposing through an original image having a line image or halftone image or by
scanning and exposing with a laser according to digital data. Examples of the exposure
light source include a carbon arc lamp, high-pressure mercury lamp, xenon lamp, metal
halide lamp, fluorescent lamp, tungsten lamp, halogen lamp, ultraviolet laser, visible
light laser and infrared laser. A laser is particularly preferable, and examples thereof
include solid-state lasers and semiconductor lasers that emit infrared light at a
wavelength of 760 nm to 1200 nm and semiconductor lasers that emit light at a wavelength
of 250 nm to 420 nm. In the case of using a laser, imagewise scanning and exposure
are preferably carried out in accordance with digital data. In addition, a multibeam
laser device is preferably used to shorten exposure time.
[0092] There are no particular limitations on the method of using the fountain solution
for the lithographic printing plate. After exposing the lithographic printing plate
precursor in the manner described above, the unwanted image recording layer can be
dissolved and removed with a suitable developing solution followed by supplying an
oil-based ink and the fountain solution to the plate surface and printing.
[0093] Alternatively, after having imagewise exposed the lithographic printing plate precursor
as described above with laser light, an oil-based ink and the fountain solution can
be supplied without having to go through any type of development processing step followed
by printing. Namely, a method referred to as on-press development can be employed
in which a lithographic printing plate is obtained by removing nonimage areas while
on the printing press during the course of printing.
[0094] Specific examples of this method include a method in which the lithographic printing
plate precursor is exposed with laser light followed by mounting on the printing press
and printing without going through a development processing step, and a method in
which the lithographic printing plate precursor is mounted on the printing press followed
by exposing with laser light while on the printing press and then printing without
going through a development processing step.
[0095] When printing is carried out by imagewise exposure of the lithographic printing plate
precursor with laser light followed by supplying the fountain solution and oil-based
ink without going through a development processing step such as a wet development
processing step, the image recording layer that has been cured by exposure forms an
oil-based ink receptive area having an oleophilic surface in exposed areas of the
image recording layer. On the other hand, in the unexposed areas, the uncured image
recording layer is removed by being dissolved or dispersed by the supplied fountain
solution and/or oil-based ink, and a hydrophilic surface is exposed in those areas.
As a result, printing begins with the fountain solution component adhered to the exposed
hydrophilic surface and the oil-based ink is taken up by the exposed areas of the
image recording layer. Here, although the fountain solution or the oil-based ink may
be supplied to the plate surface first, the oil-based ink is preferably supplied first
from the viewpoint of preventing the fountain solution from being contaminated by
the unexposed areas of the image recording layer.
[0096] In this manner, the lithographic printing plate precursor is developed on-press on
an offset printing press and is used as is for printing a large number of sheets.
[0097] The emulsified plate cleaning agent for a lithographic printing plate of the present
invention can be used to remove scumming based on causes occurring during platemaking,
during subsequent storage or printing, or in all other stages from platemaking to
printing.
[0098] The emulsified plate cleaning agent for a lithographic printing plate of the present
invention is used by containing in a cloth or sponge and the like, wiping off any
greasy locations or the entire side of the plate, and allowing to stand for about
30 seconds and finally wiping with water.
EXAMPLES
[0099] Although the following provides an explanation of the present invention through examples
thereof, the present invention is not limited to these examples. Furthermore, the
terms "parts" and "percent (%)" refer to parts by weight and percent (%) by weight,
respectively, unless specifically indicated otherwise.
[Preparation of Emulsified Plate Cleaning Agent]
Example 1
[0100] 5 parts by weight of water-soluble soybean polysaccharide were dissolved in 53 parts
by weight of pure water while warming. Next, 2 parts by weight of sodium metaphosphate
were dissolved while stirring followed by the addition of 0.5 parts by weight of sulfuric
acid, 0.5 parts by weight of nitric acid and 3 parts by weight of potassium hydroxide
and mixing to prepare an aqueous phase. Moreover, the pH of the aqueous phase was
adjusted to 2.0 by adding phosphoric acid a little at a time. On the other hand, an
oil phase as prepared by dissolving 15 parts by weight of Swasol 1000, 15 parts by
weight of Exxsol D-40, 2 parts by weight of Pelex OT-P, 1 part by weight of Nonion
OP-80 and 1 part by weight of Paionin D-212. Next, the aqueous phase prepared in the
manner described above was stirred and warmed to adjust to 35°C, then the oil phase
was slowly added dropwize thereto to prepare a dispersion, and then passing through
a homogenizer to fabricate a milky white, emulsified plate cleaning agent.
[0101] The plate cleaning agent obtained in this manner had a pH of 2.0, the same as that
of the aqueous phase.
Examples 2 to 7 and Comparative Examples 1 to 12
[0102] Emulsified plate cleaning agents were fabricated according to the same procedure
as that of the above-mentioned Example 1 with the exception of changing the composition.
[0103] The compositions of the emulsified plate cleaning agents of Examples 1 to 7 and Comparative
Examples 1 to 12 are shown in the following Tables 1 to 3 (units of components: parts
by weight). Furthermore, pH values of each of the emulsified plate cleaning agents,
total amount of cations originating in contained salts (wt%), and the ratio of at
least one type of cation selected from the group consisting of potassium, cesium and
rubidium based on the total amount of cations (wt%) are also shown in the tables.
[Fabrication of Lithographic Printing Plate Precursors]
(1) Fabrication of Support
[0104] Degreasing treatment was carried out for 30 seconds at 50°C using a 10% by weight
aqueous sodium aluminate solution in order to remove the rolling oil on the surface
of a 0.3 mm thick aluminum sheet (material: JIS A 1050). Following degreasing, the
aluminum surface was then grained using three nylon brushes implanted with bristles
having a diameter of 0.3 mm and using an aqueous suspension (specific gravity: 1.1
g/cm
3) of pumice having a median diameter of 25 µm followed by rinsing well with water.
This sheet was then etched by immersion for 9 seconds in a 25% by weight aqueous sodium
hydroxide solution at 45°C then rinsed with water, followed by immersing for 20 seconds
in 20% by weight nitric acid at 60°C and rinsing with water. The amount of etching
of the grained surface at this time was approximately 3 g/m
2.
[0105] Next, continuous electrochemical surface roughening treatment was subsequently carried
out using 60 Hz alternating current voltage. The electrolyte solution was a 1% by
weight aqueous nitric acid solution (containing 0.5% by weight of aluminum ions) and
the liquid temperature was 50°C. The electrochemical surface roughening treatment
was carried out with an alternating current power source waveform using trapezoidal
square wave alternating current with a time required for the current value to go from
zero to peak (TP) of 0.8 msec and a duty ratio of 1:1 and using a carbon electrode
for the counter electrode. Ferrite was used for the auxiliary anode. The current density
was 30 A/dm
2 at the peak current value, and 5% of the current flowing from the power source was
branched to the auxiliary anode. The amount of electricity during nitric acid electrolysis
was 175 C/dm
2 for the time during which the aluminum sheet served as an anode. This was followed
by rinsing by spraying with water.
[0106] Continuing, electrochemical surface roughening treatment was carried out by the same
method as for the nitric acid electrolysis using a 0.5% by weight aqueous hydrochloric
acid solution (contained 0.5% by weight of aluminum ions) for the electrolyte and
using an electrolyte temperature of 50°C and a quantity of electricity for the time
during which the aluminum sheet served as an anode of 50 C/dm
2. This was followed by rinsing by spraying with water.
[0107] Next, a 2.5 g/m
2 direct current anodic oxidation coating was provided on this sheet using 15% by weight
sulfuric acid (containing 0.5% by weight of aluminum ions) for the electrolyte and
using a current density of 15 A/dm
2, followed by rinsing with water and drying to fabricate a support (1).
[0108] Subsequently, in order to ensure hydrophilicity of the nonimage regions, silicate
treatment was carried out to the support (1) for 10 seconds at 60°C using a 2.5% by
weight aqueous #3 sodium silicate solution followed by rinsing with water to obtain
a support (2). The amount of Si adhered to the support was 10 mg/m
2. The center-line average roughness (Ra) of this substrate was 0.51 µm as measured
using a needle having a diameter of 2 µm.
(2) Formation of Undercoat Layer
[0109] Next, an undercoat layer coating liquid (1) described below was coated onto the above-mentioned
support (2) to a dry coating weight of 20 mg/m
2 to fabricate a support having an undercoat layer used in the following experiments.
<Undercoat Layer Coating Liquid (1)>
[0110]
* Undercoat layer compound (1) having structure indicated below |
0.18 g |
* Hydroxyethylimino diacetic acid |
0.10 g |
* Methanol |
55.24 g |
* Water |
6.15 g |
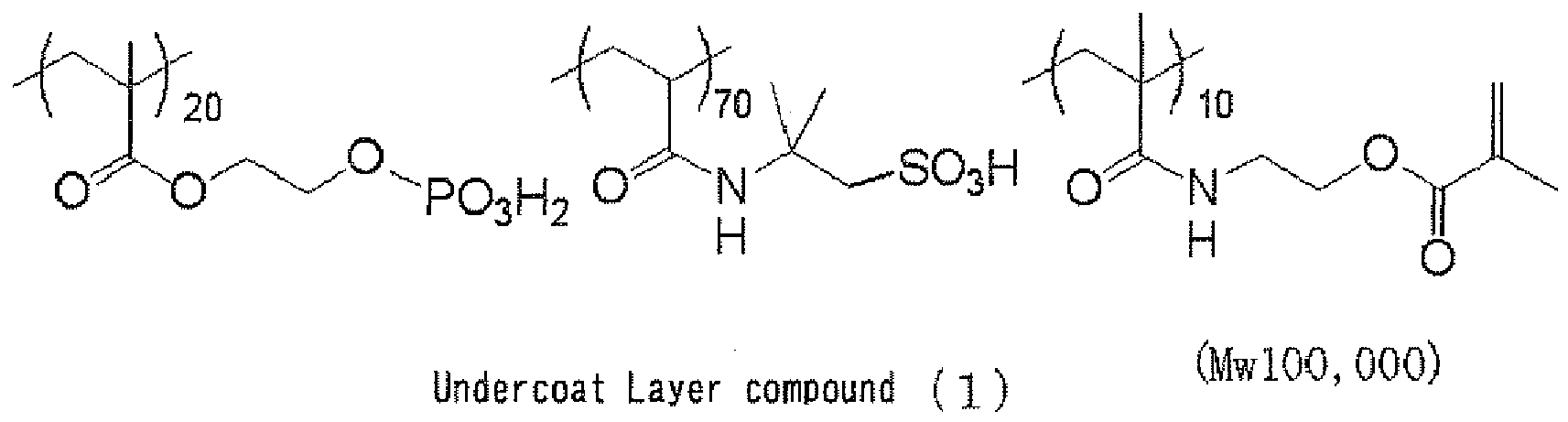
(3) Formation of Image Recording Layer
[0111] An image recording layer coating liquid (1) having the following composition was
bar-coated onto the undercoat layer formed in the manner described above followed
by oven-drying for 60 seconds at 100°C to form an image recording layer having a dry
coating weight of 1.0 g/m
2.
[0112] The image recording layer coating liquid (1) was obtained by mixing and stirring
the following photosensitive liquid (1) with a microgel liquid (1) immediately before
coating.
<Photosensitive Liquid (1)>
[0113]
* Binder polymer (1) (structure below) |
0.240 g |
* Infrared absorbent dye (1) (structure below) |
0.030 g |
* Radical generator (1) (structure below) |
0.162 g |
* Radical polymerizable compound: |
|
Tris(acryloyloxyethyl)isocyanurate |
|
(NK-Ester A-9300, Shin-Nakamura Chemical Co., Ltd.) |
0.192 g |
* Low molecular weight hydrophilic compound: |
|
Tris(2-hydroxyethyl)isocyanurate |
0.062 g |
* Low molecular weight hydrophilic compound (1) |
|
(structure below) |
0.050 g |
* Oleosensitizer: Phosphonium compound (1) |
|
(structure below) |
0.055 g |
* Oleosensitizer: Benzyldimethyloctylammonium·PF6 salt |
0.018 g |
* Oleosensitizer: Ammonium group-containing polymer |
|
(structure below, reduced specific viscosity: 44 cSt/g/ml) |
0.035 g |
* Fluorine-based surfactant (1) (structure below) |
0.008 g |
* 2-butanone |
1.091 g |
* 1-methoxy-2-propanol |
8.609 g |
<Microgel Liquid (1)>
[0114]
* Microgel (1) |
2.640 g |
* Distilled water |
2.425 g |
Synthesis of Microgel (1)
[0116] An oil phase component was prepared by dissolving 10 g of trimethylolpropane/xylene
diisocyanate adduct (today's Mitsui Takeda Chemical Co., Ltd., Takenate D-110N), 3.15
g of pentaerythritol triacrylate (Nippon Kayaku Co., Ltd., SR444), and 0.1 g of Paionin
A-41C (Takemoto Oil & Fat Co., Ltd.) in 17 g of ethyl acetate. 40 g of a 4% by weight
aqueous solution of PVA-205 was prepared for the aqueous phase component. The oil
phase component and aqueous phase component were mixed and emulsified for 10 minutes
at 12,000 rpm using a homogenizer. The resulting emulsion was added to 25 g of distilled
water and stirred for 30 minutes at room temperature and then for 3 hours at 50°C.
The microgel liquid obtained in this manner was diluted with distilled water to a
solid fraction concentration of 15% by weight of use as the above-mentioned microgel
(1). Measurement of the average particle size of the microgel by a light scattering
procedure yielded an average particle size of 0.2 µm.
(4) Formation of Protective Layer
[0117] A protective layer coating liquid (1) having the composition indicated below was
further bar-coated onto the above-mentioned image recording layer followed oven-drying
for 75 seconds at 125°C to form a protective layer having a dry coating weight of
0.15 g/m
2 and obtain a lithographic printing plate precursor.
[0118] Protective Layer Coating Liquid (1)
* Polyvinyl alcohol |
|
(PVA-405, Kuraray Co., Ltd., degree of saponification: 81.5 mol%, degree of polymerization:
500) |
0.16 g |
* Terminal sulfonic acid-modified polyvinyl alcohol |
|
(CKS-50, Nippon Synthetic Chemical Industry Co., Ltd.) |
0.49 g |
* Emalex 710 |
|
(Nihon Emulsion Co., Ltd., surfactant) |
0.13 g |
* Inorganic layered compound dispersion (1) |
22.28 g |
* Colloidal silica MP1040 |
0.30 g |
(Nissan Chemical Industries, Ltd., average particle size: 0.1 µm, 40% by weight aqueous
solution) |
* Ion exchange water |
52 g |
(Preparation of Inorganic Layered Compound Dispersion (1))
[0119] 6.4 g of the synthetic mica Somashif ME-100 (Co-op Chemical Co., Ltd.) were added
to 193.6 g of ion exchange water followed by dispersing to an average particle size
of 3 µm (laser scattering method) using a homogenizer. The aspect ratio of the resulting
dispersed particles was 100 or more.
[0120] Thus, a photopolymerizable lithographic printing plate precursor was obtained in
which an oxygen-blocking protective layer containing an inorganic layered compound
was provided on an image recording layer.
[Testing Methods]
[0121] Platemaking was carried out by on-plate development under the following printing
conditions 1 or 2 using the photopolymerizable lithographic printing plate precursor
obtained in the manner described above, followed by testing the performance of various
types of plate cleaning agents.
<Printing Conditions 1>
[0122] Printing press: Heidelberg MOV (ALCOLOR, fountain solution supply device)
Ink: Environmentally-friendly Non-VOC ink (Toyo Ink Co., Ltd.,
TK NEX NV100 processed red ink)
Fountain solution: PressMax 30.33 fountain solution
(Fuji Hunt Photographic Chemicals Inc.) diluted to 4%
Platemaking conditions: After forming an image of the FM Screen TA FFTA 20 using the
Quantum Thermal Laser Setter manufactured by Creo Co., Ltd., the plate was mounted
on the printing press followed by supplying fountain solution and ink, completing
on-press development and carrying out the printing tests described below.
<Scum Removal>
[0123] The following treatments (1, 2 and 3) were respectively carried out on nonimage areas
of the plate on which on-press development had been completed.
[0124] When printing was resumed, adhesion of ink and scumming occurred on the treated areas.
The various plate cleaning agents were soaked into a sponge, the entire side of the
plate was wiped five times to remove scum after which printing was resumed. The ability
of the plate to recover from scumming was then evaluated.
- 1. Air oxidation scumming: The plate was left for 3 hours in the printing press at
150°C without coating with gum.
- 2. Scratching: Scratches were made while applying a load of 100 g, 200 g or 300 g
to a diamond stylus 4R using a scratch tester (Shinto Scientific Co., Ltd.) followed
by allowing to stand in air for 3 days.
- 3. Oil scumming: 1 g of oleic acid was dissolved in 10 g of mineral spirits followed
by soaking into absorbent cotton and buff drying.
[0125] Recovery from each of the types of scumming 1 to 3 described above was evaluated
according to the criteria indicated below.
1. Removal of air oxidation scumming: Evaluation of removal of scumming for 100 impressions.
[0126] O: Superior
Δ: Somewhat inferior
×: Inferior
2. Scratching: Evaluation of scratching for 100 impressions
[0127] O: Superior
Δ: Somewhat inferior
×: Inferior
3. Oil scumming: Evaluation of removal of soiling for 100 impressions
[0128] O: Superior
Δ: Somewhat inferior
×: Inferior
<Printing Conditions 2>
[0129] Printing press: New DAIYA (Mitsubishi Heavy Industries, Ltd.)
Ink: Printing ink (DIC Graphics Corp., sheet-fed ink,
Fusion G processed red ink)
Fountain solution: PressMax 30.33 fountain solution
(Fuji Hunt Photographic Chemicals Inc.) diluted to 4%
[0130] Platemaking conditions: After forming an image of the FM Screen TA FFTA 20 using
the Quantum Thermal Laser Setter manufactured by Creo Co., Ltd., the plate was mounted
on the printing press followed by supplying fountain solution and ink, completing
on-plate development and carrying out the printing tests described below.
<Ink Adhesion>
[0131] The printing press was stopped after printing 1000 impressions on the plate on which
on-plate development had been completed. The various plate cleaning agents were soaked
into a sponge, the entire side of the plate was wiped five times after which printing
was resumed. Adhesion of ink on solid image areas and halftone image areas during
the time from the start of printing to printing of 2000 impressions was evaluated
according to the following criteria from the viewpoints of the occurrence of uneven
wiping and ink adhesion.
4. Occurrence of uneven wiping: Evaluated as number of impressions from start of printing
to time when uneven wiping no longer occurred
[0132] O: No uneven wiping at start or 50 impressions or less printed until no longer observed
OΔ: 50 to 100 impressions until no longer observed Δ: 100 to 500 impressions until
no longer observed
Δ×: 500 or more impressions until no longer observed
×: Uneven wiping still observed even after printing 2000 impressions
5. Ink adhesion: Evaluation of number of impressions from start of printing
[0133] until ink completely adhered
O: Ink completely adhered in 50 impressions or less
OΔ: Ink completely adhered in 50 to 100 impressions
Δ: Ink completely adhered in 100 to 500 impressions
Δ×: Ink completely adhered in 500 or more impressions
×: Ink not completely adhered even after 2000 impressions
[0134] The test results are described in the following tables.
[Table 1]
|
Examples |
|
1 |
2 |
3 |
4 |
5 |
6 |
7 |
Aqueous Phase |
Pure Water |
53 |
53 |
53 |
53 |
53 |
53 |
55 |
Water-soluble soybean polysaccharide |
5 |
5 |
5 |
5 |
5 |
5 |
5 |
Sodium metaphosphate |
2 |
2 |
2 |
2 |
2 |
2 |
2 |
Sulfuric acid |
0.5 |
0.5 |
0.5 |
0.5 |
0.5 |
0.5 |
0.15 |
Nitric acid |
0.5 |
0.5 |
0.5 |
0.5 |
0.5 |
0.5 |
0.15 |
Aqueous ammonia |
- |
- |
- |
- |
- |
- |
- |
LiOH |
- |
- |
- |
- |
- |
- |
- |
NaOH |
- |
- |
- |
1 |
1.5 |
2 |
0.35 |
KOH |
3 |
- |
- |
2 |
1.5 |
1 |
1 |
RbOH |
- |
3 |
- |
- |
- |
- |
- |
CsOH |
- |
- |
3 |
- |
- |
- |
- |
Be(OH)2 |
- |
- |
- |
- |
- |
- |
- |
Mg(OH)2 |
- |
- |
- |
- |
- |
- |
- |
Ca(OH)2 |
- |
- |
- |
- |
- |
- |
- |
Ba(OH)2 |
- |
- |
- |
- |
- |
- |
- |
Phosphoric acid |
Added a little at a time to adjust to pH 2.0 |
Oil Phase |
Swasol 1000 |
15 |
- |
- |
7.5 |
- |
15 |
15 |
Swasol 1500 |
- |
15 |
- |
7.5 |
15 |
- |
- |
Swasol 200 |
- |
- |
15 |
- |
- |
- |
- |
Exxsol D-40 |
15 |
- |
- |
7.5 |
- |
- |
- |
Exxsol D-80 |
- |
15 |
- |
7.5 |
- |
- |
- |
Exxsol D-110 |
- |
- |
15 |
- |
15 |
15 |
15 |
Pelex OT-P |
2 |
2 |
2 |
2 |
2 |
2 |
2 |
Nonion OP-80 |
1 |
1 |
1 |
1 |
1 |
1 |
1 |
Paionin OP-212 |
1 |
1 |
1 |
1 |
1 |
1 |
1 |
Total |
100 |
100 |
100 |
100 |
100 |
100 |
100 |
pH Value |
2.0 |
2.0 |
2.0 |
2.0 |
2.0 |
2.0 |
2.0 |
Total cation content (wt%) |
2.61 |
3.03 |
3.18 |
2.49 |
2.43 |
2.38 |
0.77 |
K,Cs,Rb content/total cation content (wt%) |
80.0 |
82.7 |
83.6 |
55.9 |
43.0 |
32.2 |
31.8 |
Test Results |
Air oxidation scumming |
○ |
○ |
○ |
○ |
○ |
○ |
○ |
Scratch recovery |
○ |
○ |
○ |
○ |
○ |
○ |
Δ |
Oil scumming |
○ |
○ |
○ |
○ |
○ |
○ |
○ |
Uneven wiping |
○ |
○ |
○ |
○ |
○ |
○ |
○ |
Ink adhesion |
○ |
○ |
○ |
○ |
○ |
○ |
○ |
[Table 2]
|
Comparative Examples |
|
1 |
2 |
3 |
4 |
5 |
6 |
7 |
Aqueous phase |
Pure Water |
50 |
53 |
53 |
53 |
53 |
53 |
53 |
Water-soluble soybean polysaccharide |
5 |
5 |
5 |
5 |
5 |
5 |
5 |
Sodium metaphosphate |
2 |
2 |
2 |
2 |
2 |
2 |
2 |
Sulfuric acid |
0.5 |
0.5 |
0.5 |
0.5 |
0.5 |
0.5 |
0.5 |
Nitric acid |
0.5 |
0.5 |
0.5 |
0.5 |
0.5 |
0.5 |
0.5 |
Aqueous ammonia |
6 |
- |
- |
- |
- |
- |
- |
LiOH |
- |
3 |
- |
- |
- |
- |
- |
NaOH |
- |
- |
3 |
- |
- |
- |
- |
KOH |
- |
- |
- |
- |
- |
- |
- |
RbOH |
- |
- |
- |
- |
- |
- |
- |
CsOH |
- |
- |
- |
- |
- |
- |
- |
Be(OH)2 |
- |
- |
- |
3 |
- |
- |
- |
Mg(OH)2 |
- |
- |
- |
- |
3 |
- |
- |
Ca(OH)2 |
- |
- |
- |
- |
- |
3 |
- |
Ba(OH)2 |
- |
- |
- |
- |
- |
- |
3 |
Phosphoric acid |
Added a little at a time to adjust to pH 2.0 |
Oil Phase |
Swasol 1000 |
15 |
- |
- |
15 |
- |
- |
15 |
Swasol 1500 |
- |
15 |
- |
- |
15 |
- |
- |
Swasol 200 |
- |
- |
15 |
- |
- |
15 |
- |
Exxsol D-40 |
15 |
- |
- |
15 |
- |
- |
15 |
Exxsol D-80 |
- |
15 |
- |
- |
15 |
- |
- |
Exxsol D-110 |
- |
- |
15 |
- |
- |
15 |
- |
Pelex OT-P |
2 |
2 |
2 |
2 |
2 |
2 |
2 |
Nonion OP-80 |
1 |
1 |
1 |
1 |
1 |
1 |
1 |
Paionin OP-212 |
1 |
1 |
1 |
1 |
1 |
1 |
1 |
Total |
100 |
100 |
100 |
100 |
100 |
100 |
100 |
pH Value |
2.0 |
2.0 |
2.0 |
2.0 |
2.0 |
2.0 |
2.0 |
Total cation content (wt%) |
2.08 |
1.39 |
2.25 |
1.15 |
1.77 |
2.15 |
2.63 |
K,Cs,Rb content/total cation content (wt%) |
0 |
0 |
0 |
0 |
0 |
0 |
0 |
Test Results |
Air oxidation scumming |
○ |
○ |
○ |
Δ |
Δ |
Δ |
Δ |
Scratch recovery |
○ |
○ |
○ |
○ |
○ |
○ |
Δ |
Oil scumming |
○ |
○ |
○ |
Δ |
Δ |
Δ |
Δ |
Uneven wiping |
Δ× |
× |
× |
× |
Δ× |
Δ× |
Δ× |
Ink adhesion |
Δ |
× |
× |
Δ |
Δ× |
Δ× |
Δ× |
[Table 3]
|
Comparative Examples |
|
8 |
9 |
10 |
11 |
12 |
Aqueous phase |
Pure Water |
55 |
57 |
53 |
53 |
53 |
Water-soluble soybean polysaccharide |
5 |
5 |
5 |
5 |
5 |
Sodium metaphosphate |
- |
2 |
2 |
2 |
2 |
Sulfuric acid |
0.04 |
- |
0.5 |
0.2 |
0.08 |
Nitric acid |
0.04 |
- |
0.5 |
0.2 |
0.08 |
Aqueous ammonia |
- |
- |
- |
- |
- |
LiOH |
- |
- |
- |
- |
- |
NaOH |
- |
- |
2.5 |
- |
- |
KOH |
0.1 |
- |
0.5 |
0.5 |
0.2 |
RbOH |
- |
- |
- |
- |
- |
CsOH |
- |
- |
- |
- |
- |
Be(OH)2 |
- |
- |
- |
- |
- |
Mg(OH)2 |
- |
- |
- |
- |
- |
Ca(OH)2 |
- |
- |
- |
- |
- |
Ba(OH)2 |
- |
- |
- |
- |
- |
Phosphoric acid |
Added a little at a time to adjust to pH 2.0 |
Oil Phase |
Swasol 1000 |
15 |
- |
- |
7.5 |
7.5 |
Swasol 1500 |
- |
- |
15 |
7.5 |
7.5 |
Swasol 200 |
- |
15 |
- |
- |
- |
Exxol D-40 |
- |
- |
- |
7.5 |
7.5 |
Exxsol D-80 |
- |
- |
15 |
7.5 |
7.5 |
Exxsol D-110 |
15 |
15 |
- |
- |
- |
Pelex OT-P |
2 |
2 |
2 |
2 |
2 |
Nonion OP-80 |
1 |
1 |
1 |
1 |
1 |
Paionin OP-212 |
1 |
1 |
1 |
1 |
1 |
Total |
100 |
100 |
100 |
100 |
100 |
pH Value |
2.0 |
2.0 |
2.0 |
2.0 |
2.0 |
Total cation content (wt%) |
0.14 |
0.52 |
2.31 |
0.87 |
0.66 |
K,Cs,Rb content/total cation content (wt%) |
49.0 |
0 |
15.9 |
15.1 |
21.0 |
Test Results |
Air oxidation scumming |
Δ |
× |
○ |
Δ |
Δ |
Scratch recovery |
× |
× |
Δ |
Δ |
Δ |
Oil scumming |
× |
× |
○ |
Δ |
Δ |
Uneven wiping |
○ |
Δ |
Δ |
○Δ |
○Δ |
Ink adhesion |
○ |
Δ× |
Δ |
○Δ |
○Δ |
[0135] Furthermore, the components contained in the oil phase were as indicated below.
Swasol 1000 (aromatic, high boiling point solvent, Maruzen Petrochemical Co., Ltd.)
Swasol 1500 (aromatic, high boiling point solvent, Maruzen Petrochemical Co., Ltd.)
Swasol 2000 (aromatic, high boiling point solvent, Maruzen Petrochemical Co., Ltd.)
Exxol D-40 (naphthene-based solvent, Exxon Mobil Corporation)
Exxsol D-80 (naphthene-based solvent, Exxon Mobil Corporation)
Exxsol D-110 (naphthene-based solvent, Exxon Mobil Corporation)
Pelex OT-P (sodium dialkylsulfosuccinate, Kao Corp.)
Active ingredient: 70%
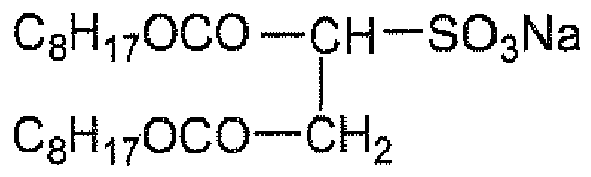
Nonion OP-80 (sorbitan monooleic acid, NOF Corp.)
Paionin D-212 (polyoxyethylene castor oil ether, Takemoto Oil & Fat Co., Ltd.)