(19) |
 |
|
(11) |
EP 2 420 616 B1 |
(12) |
EUROPÄISCHE PATENTSCHRIFT |
(45) |
Hinweis auf die Patenterteilung: |
|
03.10.2012 Patentblatt 2012/40 |
(22) |
Anmeldetag: 13.07.2011 |
|
(51) |
Internationale Patentklassifikation (IPC):
|
|
(54) |
Verfahren und Anlage zur Aufbereitung von Holz für die Herstellung mitteldichter Faserplatten
Method and assembly for preparing wood for the production of medium thickness fibre
boards
Procédé et installation de traitement du bois pour la fabrication de panneaux de fibres
d'épaisseur moyenne
|
(84) |
Benannte Vertragsstaaten: |
|
AL AT BE BG CH CY CZ DE DK EE ES FI FR GB GR HR HU IE IS IT LI LT LU LV MC MK MT NL
NO PL PT RO RS SE SI SK SM TR |
(30) |
Priorität: |
18.08.2010 DE 102010034763
|
(43) |
Veröffentlichungstag der Anmeldung: |
|
22.02.2012 Patentblatt 2012/08 |
(73) |
Patentinhaber: Kronotec AG |
|
6006 Luzern (CH) |
|
(72) |
Erfinder: |
|
- Obst-Lück, Peter
16909 Zaatzke (DE)
|
(74) |
Vertreter: Rehmann, Thorsten et al |
|
Gramm, Lins & Partner GbR
Theodor-Heuss-Strasse 1 38122 Braunschweig 38122 Braunschweig (DE) |
(56) |
Entgegenhaltungen: :
EP-A1- 0 979 895 WO-A2-2009/134764 DE-A1- 19 515 734 JP-A- 2004 285 533
|
EP-A2- 0 826 471 DE-A1- 10 347 052 DE-A1- 19 746 383
|
|
|
|
|
|
|
|
|
Anmerkung: Innerhalb von neun Monaten nach der Bekanntmachung des Hinweises auf die
Erteilung des europäischen Patents kann jedermann beim Europäischen Patentamt gegen
das erteilte europäischen Patent Einspruch einlegen. Der Einspruch ist schriftlich
einzureichen und zu begründen. Er gilt erst als eingelegt, wenn die Einspruchsgebühr
entrichtet worden ist. (Art. 99(1) Europäisches Patentübereinkommen). |
[0001] Die Erfindung betrifft ein Verfahren und eine Anlage zur Aufbereitung von Holz für
die Herstellung von mitteldichten Faserplatten (MDF), bei dem zunächst Hackschnitzel
erzeugt werden, die anschließend in einen Bunker transportiert und dort mittels Heißdampfs
vorgekocht werden. Aus dem Bunker werden die Hackschnitzel mittels einer Stopfschnecke
in einen Kocher gefördert, wobei sie beim Passieren der Stopfschnecke entwässert werden.
Im Kocher werden die Hackschnitzel anschließend mittels Heißdampfs aufgeschlossen.
Die aufgeschlossenen Hackschnitzel werden aus dem Kocher ausgefördert und in einen
Refiner gegeben, wo sie zu Holzfasern zerfasert werden. Die noch nassen Holzfasern
werden anschließend beleimt und einem Trockner zugeführt, in dem sie mittels Heißgas
getrocknet werden. Die trockenen Holzfasern werden dann einer Streuvorrichtung zugeführt,
mittels der die Fasern zu einem Kuchen gestreut werden, der anschließend unter hohem
Druck und hoher Temperatur zu einer Faserplatte gewünschter Dicke verpresst wird.
[0002] Ein solches Verfahren ist beispielsweise aus der
DE 197 46 383 A1 bekannt.
[0003] Aus der
WO 2009/134764 A2 ist ein Verfahren zur Herstellung eines Cellulose- oder Lignocellulosematerials für
die Papierherstellung bekannt, bei dem das Rohmaterial mit ionisierender Strahlung
behandelt wird, um so das Molekulargewicht des Rohstoffs zu beeinflussen und die Eigenschaften
des fertigen Papiers zu verbessern.
[0004] Die
DE 195 15 734 A1 offenbart ein Verfahren zur Herstellung von Holzfasern, bei dem zur Plastifizierung
der holzeigenen Bindemittel und zur Erweichung der Holzfasern Sattdampf verwendet
wird, dem in einem Kreislaufprozess ungesättigter Heißdampf zugesetzt wird. Dabei
kann ein Teilvolumenstrom von überhitztem Heißdampf einem Hacker zugeführt werden
und dort zur Vorwärmung der Hackschnitzel dienen.
[0005] Die
EP 0 826 471 A2 beschreibt ein Verfahren zur Aufbereitung von Faserplattenabfällen, bei dem die Zerfaserung
der Abfälle nach einer drucklosen Wärmebehandlung in einem flüssigen Medium und anschließender
Druckbehandlung durch Dampfexpansion erfolgt. Die drucklose Wärmebehandlung in einem
flüssigen Medium kann dabei in einer mit Prozesswasser gefüllten Koch-Transportschnecke
erfolgen.
[0006] Beim Einsatz von Wald- oder Restholz ist die Entrindung von hoher Bedeutung hinsichtlich
der späteren Plattenqualität. Je intensiver die Rinde entfernt wird, desto heller
in der Farbe wird später die Platte und desto problemloser lässt sie sich lackieren
bzw. beschichten. Für eine kontinuierliche Entrindung werden in der Regel Rotorenentrinder
verwendet. Um ein zu rasches Austrocknen des Holzes zu verhindern, erfolgt die Entrindung
möglichst unmittelbar vor der Holzaufbereitung bzw. ist Bestandteil des kontinuierlichen
Prozessablaufes. In der ersten Stufe der Zerfaserung wird das Holz vorbereitet, in
dem es sortiert und gereinigt wird. Eine Verwendung von Metallsuchgeräten verhindert
eine Beschädigung der Werkzeuge und erhöht die Standzeiten. Das so gereinigte Holz
wird dann einem Scheiben- oder Trommelhacker zugeführt in dem der Baumstamm dann zu
Hackschnitzeln verarbeitet wird. Die erzielbare Hackschnitzellänge ist bei Trommelhackern
direkt abhängig von der Vorschubgeschwindigkeit und umgekehrt proportional der Rotordrehzahl
und der Messeranzahl. Bei der späteren Zerfaserung bereitet feuchtes Holz an sich
keine Schwierigkeiten, sondern allenfalls bei der nachfolgenden Trocknung. Trockenes
Holz hingegen ist aufgrund des damit verbundenen höheren Staub- bzw. Feingutanfalls
für den Zerfaserungsvorgang sehr ungünstig.
[0008] Die für die Zerfaserung und Trocknung der Hackschnitzel benötigte Energie richtet
sich nach diskreten Merkmalen bzw. Eigenschaften und wird über diese auch gesteuert.
Diese Energie wird in verschiedenen Prozessschritten zugeführt. Beim Vordämpfen der
Hackschnitzel in dem Bunker, beim elektrischen Befüllen des Kochers mittels der Stopfschnecke,
beim Entwässern der Hackschnitzel in einem Entwässerungsrohr, in Form von Heißdampf
beim Kochen, anschließend in elektrischer Form im Refiner beim Zerfasern und schließlich
durch Trocknung mittels heißer Gase.
[0009] Hauptenergieträger ist neben der elektrischen Energie Heißdampf. Durch die Erzeugung
aus gereinigtem Wasser und in Folge des für die Verdampfung benötigten Energieaufwandes
ist Heißdampf sehr teuer. Aggregate für die Dampferzeugung sind konstruktiv aufwendig
gestaltet und ebenfalls kostenintensiv. Verluste in Folge von Undichtigkeiten, Temperaturgefällen
und Restwärme des Kondensates sind extrem hoch, und bei der Entspannung von Dampf
entsteht Kondensat als Abwasser.
[0010] Von dieser Problemstellung ausgehend liegt der Erfindung die Aufgabe zugrunde, eine
Hackschnitzelaufbereitungsanlage auf die Erzeugung weniger Abwasser hin zu optimieren.
Die Anlage soll neben des geringer entstehenden Abwassers zudem ermöglichen, den Gesamtprozess
energetisch zu optimieren und damit die Herstellung von Holzwerkstoffplatten ökologischer
zu gestalten.
[0011] Die Problemlösung erfolgt dadurch, dass bei einem gattungsgemäßen Verfahren die Hackschnitzel
spätestens im Bunker mittels einer Heizung vorgewärmt werden. Hierzu kann der Bunker
oder die Transporteinrichtung, mit der die Hackschnitzel in den Bunker transportiert
werden, mit einer Heizung versehen sein. Entsprechend kann bei einer gattungsgemäßen
Anlage entweder der Bunker oder die Transporteinrichtung mit einer Heizung versehen
sein, und die Hackschnitzel dadurch vorgewärmt werden, bevor sie mit Heißdampf beaufschlagt
werden.
[0012] Die Vorwärmung der Hackschnitzel im Vorratsbunker oder der Transporteinrichtung,
die bevorzugt eine Förderschnecke ist, erfolgt vorzugsweise mittels Mikrowellen oder
mittels Ultraschalls.
[0013] Wenn die Hackschnitzel auf eine Temperatur von 105 bis 110°C vorgewärmt werden, ergibt
sich ein um ca. 50 % verringerter Heißdampfbedarf. Im Kocher werden die Hackschnitzel
bei einer Temperatur von etwa 170°C vorzugsweise für etwa 3,5 Minuten mittels Heißdampfs
aufgeschlossen. Die im Trockner getrockneten Holzfasern können anschließend nochmals
beleimt werden.
[0014] Durch die erfindungsgemäße Lösung entsteht beim Ausquetschen der Hackschnitzel im
Entwässerungsrohr bzw. der Stopfschnecke weniger Abwasser. Mittels der Heizung erfolgt
eine gezielte Erwärmung der Hackschnitzel ohne gravierende Umgebungsverluste, wodurch
anschließend dann auch die Last des Trockners für die Fasern reduziert wird.
[0015] Mit Hilfe einer Zeichnung soll ein Ausführungsbeispiel der Erfindung nachfolgend
näher beschrieben werden. Es zeigt:
- Figur 1 -
- ein Flussdiagramm des Verfahrensablaufs,
- Figur 2 -
- eine schematisierte Darstellung der Anlage zur Durchführung des Verfahrens.
[0016] Die aus dem entrindeten Baumstamm gehackten Hackschnitzel werden über die mit einer
Heizung 1 a versehene Förderschnecke 9 in den Bunker 1 gefördert und während des Transports
auf eine Temperatur von 105 bis 110°C vorgewärmt. Anschließend wird in den Bunker
1 Heißdampf eingegeben, um die Hackschnitzel vorzukochen. Das dabei ausfallende Kondensat
wird als Abwasser A der Abwasseraufbereitung 8 zugeführt. Nach dem Vorkochen werden
die Hackschnitzel über eine Stopfschnecke 2 einem Kocher 3 zugeführt und dabei über
ein hier nicht näher dargestelltes Entwässerungsrohr entwässert. Zum Entwässern der
Hackschnitzel kann, wie in Figur 2 mit dem Sichtpfeil P angedeutet, in der Förderschnecke
zum Bunker 1 hin eine Pressung der Hackschnitzel erfolgen. Das dabei anfallende Abwasser
A wird auch der Abwasseraufbereitung 8 zugeführt. Der Hauptanteil an Kondensat fällt
in der Stoffschnecke 2 an, bevor die Hackschnitzel dem Kocher 3 zugeführt werden.
Im Kocher 3 werden die Hackschnitzel mittels Heißdampfs bei einem Druck von etwa 10
bar und einer Temperatur von etwa 170°C für eine Dauer von etwa 3,5 Minuten aufgeschlossen.
Das dabei anfallende Kondensat A wird ebenfalls der Abwasseraufbereitung 8 zugeführt.
Wenn die Hackschnitzel ausreichend aufgeschlossen sind, werden sie zur Zerfaserung
einem Refiner 4 zugeführt. Auch dabei fällt Kondensat bzw. Abwasser A an, das der
Abwasseraufbereitung 8 zugeführt wird. Die im Refiner 4 gewonnenen Holzfasern werden
in dem noch nassen Zustand an der Stelle L mit einem Klebstoff beleimt und dann einem
Trockner 5 zugeführt, in dem die beleimten Fasern mittels Heißgas bei einer Temperatur
von etwa 160°C auf eine Restfeuchte von etwa 10 - 15% getrocknet werden. Der dabei
entstehende Dampf und/oder entsprechendes Kondensat A wird der Abwasseraufbereitung
8 zugeführt. Die im Trockner 5 getrockneten Fasern werden anschließend zu einer Streuvorrichtung
6 transportiert und bevor sie die Streuvorrichtung 6 erreichen nochmals an der Stelle
L
1 mit einem Leim beleimt. Über die Streuvorrichtung 6 wird auf ein endlos umlaufendes
Transportband ein Faserkuchen gestreut, der dann der Heißpresse 7 zugeführt wird.
In der Heißpresse 7 wird der gestreute Faserkuchen dann zu einer mitteldichten Faserplatte
(MDF) gewünschter Dicke verpresst.
[0017] Die Heizung 1 a im Bunker 1 oder der Förderschnecke 9 ist eine Vorrichtung zur Bestrahlung
der Hackschnitzel mittels Mikrowellen oder mittels Ultraschalls.
Bezugszeichenliste
[0018]
- 1
- Bunker
- 1 a
- Heizung
- 2
- Stopfschnecke
- 3
- Kocher
- 4
- Refiner
- 5
- Trockner
- 6
- Streuvorrichtung
- 7
- Heißpresse
- 8
- Abwasseraufbereitung
- 9
- Förderschnecke/Transporteinrichtung
- A
- Abwasser/Kondensat
- L
- Beleimstelle
- L1
- Beleimstelle
1. Verfahren zur Aufbereitung von Holz, aus dem zunächst Hackschnitzel erzeugt werden,
für die Herstellung von mitteldichten Faserplatten (MDF) mit folgenden Schritten:
a) Transportieren der Hackschnitzel in einen Bunker (1),
b) Vorkochen der Hackschnitzel in dem Bunker (1) mittels Heißdampfs,
c) Austragen und Entwässern der Hackschnitzel aus dem Bunker (1) mittels einer Stopfschnecke
(2) in einen Kocher (3),
d) Aufschließen der Hackschnitzel im Kocher (3) mittels Heißdampfs,
e) Ausfördern der aufgeschlossenen Hackschnitzel in einen Refiner (4) und Zerfasern
der Hackschnitzel zu Holzfasern,
f) Beleimen der nassen Holzfasern und
g) Trocknen der beleimten Holzfasern in einem Trockner (5) mittels Heißgas,
dadurch gekennzeichnet, dass
h) die Hackschnitzel spätestens im Bunker (1) mittels Mikrowellen oder Ultraschalls
vorgewärmt werden.
2. Verfahren nach Anspruch 1, dadurch gekennzeichnet, dass die Hackschnitzel während des Transports in den Bunker (1) mittels Mikrowellen oder
Ultraschalls vorgewärmt werden.
3. Verfahren nach einem der Ansprüche 1 bis 2, dadurch gekennzeichnet, dass die Hackschnitzel auf eine Temperatur von 105 bis 110°C vorgewärmt werden.
4. Verfahren nach Anspruch 3, dadurch gekennzeichnet, dass die Hackschnitzel im Kocher (3) bei einer Temperatur von etwa 170°C für etwa 3,5
Minuten mittels Heißdampfs aufgeschlossen werden.
5. Verfahren nach einem der vorstehenden Ansprüche, dadurch gekennzeichnet, dass die im Trockner (5) getrockneten Holzfasern nochmals beleimt werden.
6. Anlage zur Aufbereitung von Holz-Hackschnitzeln für die Herstellung von mitteldichten
Faserplatten (MDF), mit einem Bunker (1), in dem die Hackschnitzel vorgekocht werden,
einem Kocher (3), in dem die Hackschnitzel mittels Heißdampfs aufgeschlossen werden,
einem Refiner (4), in dem die aufgeschlossenen Hackschnitzel zu Fasern bearbeitet
werden, und einem Trockner (5), in dem die Fasern getrocknet werden, dadurch gekennzeichnet, dass der Bunker (1) mit einer Heizung versehen ist, die eine Einrichtung zur Mikrowellen-
oder Ultraschallbestrahlung ist.
7. Anlage zur Aufbereitung von Holz-Hackschnitzeln für die Herstellung von mitteldichten
Faserplatten (MDF) mit einer Transporteinrichtung (9), mit der die Hackschnitzel in
einen Bunker (1) transportiert werden, in dem die Hackschnitzel mittels Heißdampfs
aufgeschlossen werden, einem Refiner (4), in dem die aufgeschlossenen Hackschnitzel
zu Fasern bearbeitet werden, und einem Trockner (5), in dem die Fasern getrocknet
werden, dadurch gekennzeichnet, dass die Transporteinrichtung (9) mit einer Heizung versehen ist, die eine Einrichtung
zur Mikrowellen- oder Ultraschallbestrahlung (1a) ist.
8. Anlage nach Anspruch 7, dadurch gekennzeichnet, dass die Transporteinrichtung (9) eine Förderschnecke ist.
1. Method for preparing wood used initially to produce wood chips, for the production
of medium density fibreboards (MDF), comprising the following steps:
a) transporting the wood chips into a bunker (1),
b) pre-boiling the wood chips in the bunker (1) by means of hot steam,
c) discharging and dewatering the wood chips from the bunker (1) into a boiling apparatus
(3) by means of a stuffing screw (2),
d) pulping the wood chips in the boiling apparatus (3) by means of hot steam,
e) delivering the pulped wood chips into a refiner (4) and defibrating the wood chips
to form wood fibres,
f) coating the wet wood fibres with glue, and
g) drying the glue-coated wood fibres in a drier (5) by means of hot gas,
characterized in that
h) the wood chips are preheated by means of microwaves or ultrasound at the latest
in the bunker (1).
2. Method according to Claim 1, characterized in that the wood chips are preheated by means of microwaves or ultrasound during transportation
into the bunker (1).
3. Method according to either of Claims 1 and 2, characterized in that the wood chips are preheated to a temperature of 105 to 110°C.
4. Method according to Claim 3, characterized in that the wood chips are pulped in the boiling apparatus (3) at a temperature of approximately
170°C for approximately 3.5 minutes by means of hot steam.
5. Method according to one of the preceding claims, characterized in that the wood fibres dried in the drier (5) are once again coated with glue.
6. Assembly for preparing wood chips for the production of medium density fibreboards
(MDF), comprising a bunker (1) in which the wood chips are pre-boiled, a boiling apparatus
(3) in which the wood chips are pulped by means of hot steam, a refiner (4) in which
the pulped wood chips are processed to form fibres, and a drier (5) in which the fibres
are dried, characterized in that the bunker (1) is provided with a heating means which is a device for microwave or
ultrasound irradiation.
7. Assembly for preparing wood chips for the production of medium density fibreboards
(MDF),comprising a transport device (9) with which the wood chips are transported
into a bunker (1), in which the wood chips are pulped by means of hot steam, a refiner
(4) in which the pulped wood chips are processed to form fibres, and a drier (5) in
which the fibres are dried, characterized in that the transport device (9) is provided with a heating means which is a device for microwave
or ultrasound irradiation (1a).
8. Assembly according to Claim 7, characterized in that the transport device (9) is a screw conveyor.
1. Procédé de traitement du bois à partir duquel on fabrique dans un premier temps des
copeaux pour la fabrication de panneaux de fibres de densité moyenne (MDF), comprenant
les étapes suivantes :
a) on transporte les copeaux vers un réservoir (1),
b) on précuit les copeaux dans le réservoir (1) au moyen de vapeur surchauffée,
c) au moyen d'une vis de gavage (2), on défourne hors du réservoir (1) vers un cuiseur
(3) les copeaux et on enlève l'excès d'eau,
d) on désagrège les copeaux dans le cuiseur (3) au moyen de vapeur surchauffée,
e) on extrait les copeaux désagrégés vers une défibreuse (4) et on défibre les copeaux
pour faire des fibres de bois,
f) on encolle les fibres de bois humides, et
g) on sèche les fibres de bois humides dans un sécheur (5) au moyen de gaz chauffé,
caractérisé en ce que
h) l'on préchauffe les copeaux au plus tard dans le réservoir (1), au moyen de micro-ondes
ou d'ultra-sons.
2. Procédé selon la revendication 1, caractérisé en ce que l'on préchauffe les copeaux pendant le transport vers le réservoir (1), au moyen
de micro-ondes ou d'ultra-sons.
3. Procédé selon la revendication 1 ou 2, caractérisé en ce que l'on préchauffe les copeaux à une température allant de 105 à 110°C.
4. Procédé selon la revendication 3, caractérisé en ce qu'au moyen de vapeur surchauffée, on désagrège les copeaux dans le cuiseur (3) à une
température d'environ 170°C pour environ 3,5 minutes.
5. Procédé selon l'une quelconque des revendications précédentes, caractérisé en ce que l'on encolle encore une fois les fibres de bois séchées dans le sécheur (5).
6. Installation pour le traitement de copeaux de bois pour la fabrication de panneaux
de fibres de densité moyenne (MDF), comprenant un réservoir (1) dans lequel les copeaux
sont précuits, un cuiseur (3) dans lequel les copeaux sont désagrégés au moyen de
vapeur surchauffée, une défibreuse (4) dans laquelle les copeaux désagrégés sont travaillés
en fibres, et un sécheur (5) dans lequel les fibres sont séchées, caractérisée en ce que le réservoir (1) est muni d'un chauffage, qui est un dispositif pour l'émission de
micro-ondes ou d'ultra-sons.
7. Installation pour le traitement de copeaux de bois pour la fabrication de panneaux
de fibres de densité moyenne (MDF), comprenant un dispositif de transport (9) à l'aide
duquel on transporte les copeaux dans un réservoir (1) dans lequel les copeaux sont
désagrégés au moyen de vapeur surchauffé, une défibreuse (4) dans laquelle les copeaux
désagrégés sont travaillés en fibres et un sécheur (5) dans lequel les fibres sont
séchées, caractérisée en ce que le dispositif de transport (9) est muni d'un chauffage qui est un dispositif pour
l'émission de micro-ondes ou d'ultra-sons.
8. Installation selon la revendication 7, caractérisée en ce que le dispositif de transport (9) est un transporteur à vis sans fin.
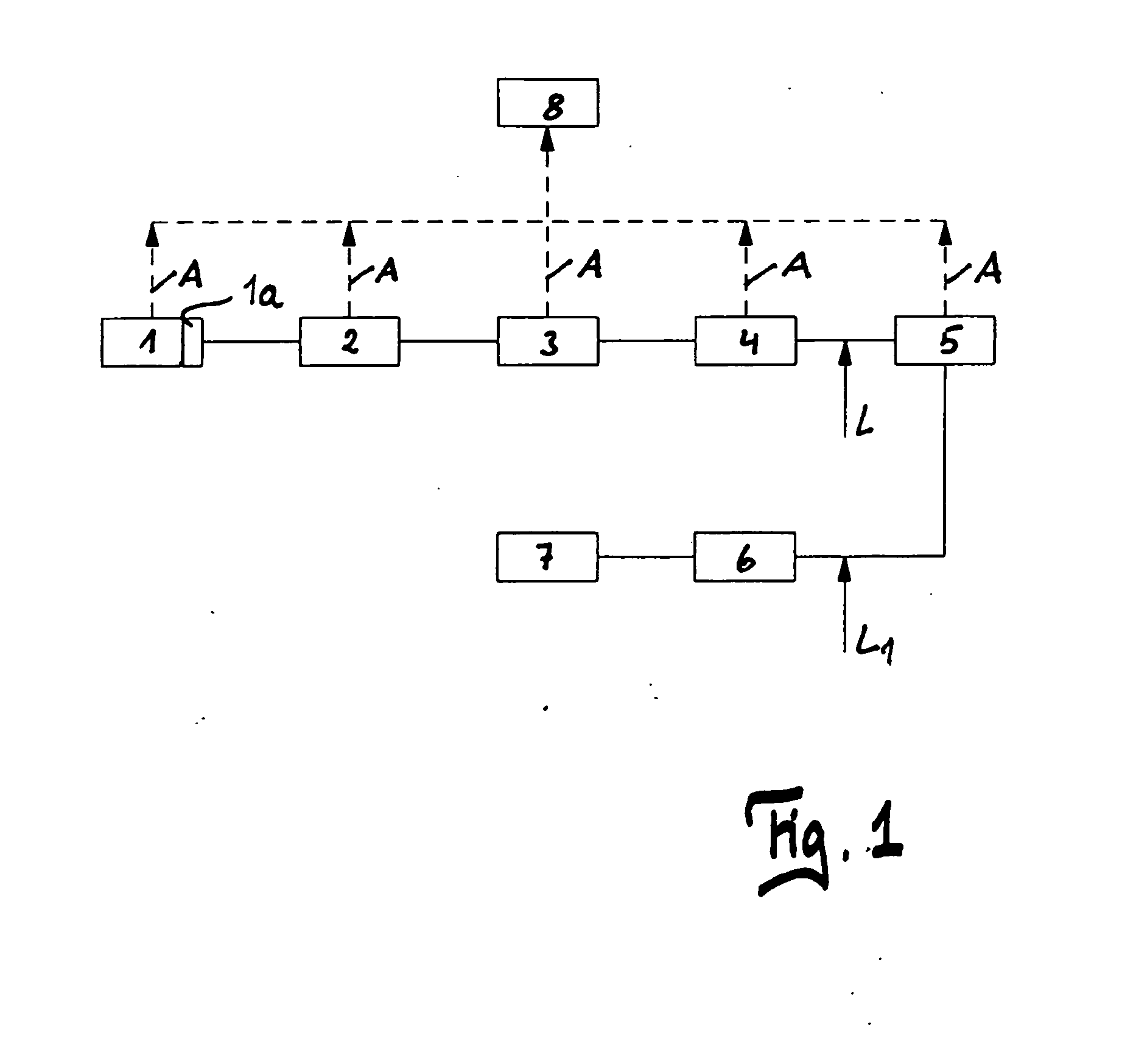
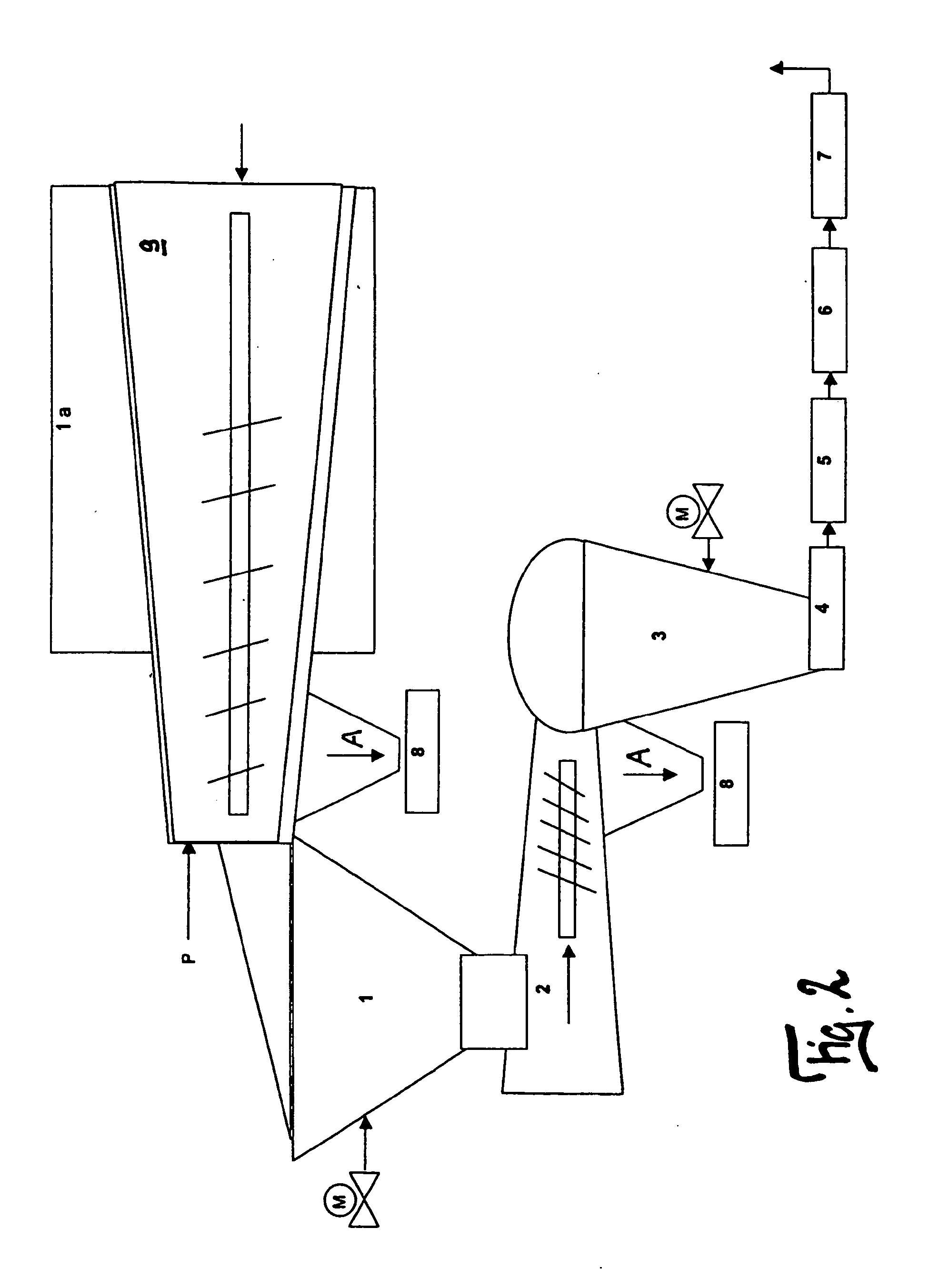
IN DER BESCHREIBUNG AUFGEFÜHRTE DOKUMENTE
Diese Liste der vom Anmelder aufgeführten Dokumente wurde ausschließlich zur Information
des Lesers aufgenommen und ist nicht Bestandteil des europäischen Patentdokumentes.
Sie wurde mit größter Sorgfalt zusammengestellt; das EPA übernimmt jedoch keinerlei
Haftung für etwaige Fehler oder Auslassungen.
In der Beschreibung aufgeführte Patentdokumente
In der Beschreibung aufgeführte Nicht-Patentliteratur
- DEPPE/ERNSTMDF-Mitteldichte FaserplattenDRW-Verlag19960000 [0007]