(19) |
 |
|
(11) |
EP 2 466 144 B1 |
(12) |
EUROPÄISCHE PATENTSCHRIFT |
(45) |
Hinweis auf die Patenterteilung: |
|
20.02.2013 Patentblatt 2013/08 |
(22) |
Anmeldetag: 16.12.2010 |
|
(51) |
Internationale Patentklassifikation (IPC):
|
|
(54) |
Vorrichtung zum Verdichten eines Prozessgases
Device for compressing a process gas
Dispositif pour comprimer un gaz de procédé
|
(84) |
Benannte Vertragsstaaten: |
|
AL AT BE BG CH CY CZ DE DK EE ES FI FR GB GR HR HU IE IS IT LI LT LU LV MC MK MT NL
NO PL PT RO RS SE SI SK SM TR |
(43) |
Veröffentlichungstag der Anmeldung: |
|
20.06.2012 Patentblatt 2012/25 |
(73) |
Patentinhaber: FIMA Maschinenbau GmbH |
|
74423 Obersontheim (DE) |
|
(72) |
Erfinder: |
|
- Schmid, Joachim
74599 Wallhausen (DE)
|
(74) |
Vertreter: Hössle Patentanwälte Partnerschaft |
|
Postfach 10 23 38 70019 Stuttgart 70019 Stuttgart (DE) |
(56) |
Entgegenhaltungen: :
|
|
|
|
|
|
|
|
Anmerkung: Innerhalb von neun Monaten nach der Bekanntmachung des Hinweises auf die
Erteilung des europäischen Patents kann jedermann beim Europäischen Patentamt gegen
das erteilte europäischen Patent Einspruch einlegen. Der Einspruch ist schriftlich
einzureichen und zu begründen. Er gilt erst als eingelegt, wenn die Einspruchsgebühr
entrichtet worden ist. (Art. 99(1) Europäisches Patentübereinkommen). |
[0001] Die vorliegende Erfindung betrifft eine Vorrichtung zum Verdichten eines Prozessgases.
[0002] Vorrichtungen zum Verdichten von Prozessgasen sind bekannt. So offenbart bspw. die
WO 2009/034006 eine Verdichtereinheit bestehend aus einem Antriebsmotor und einem ein- oder mehrstufigen
Turboverdichter, wobei der Antriebsmotor und der Verdichter in einem nach außen gasdichten
Gehäuse angeordnet sind. Da der Bereich des integrierten Antriebsmotors mindestens
dem gleichen Druck wie der Ansaugbereich des Verdichters ausgesetzt ist, ist zur Vermeidung
von durch erhöhte Gasdichte im Antriebsmotor entstehenden nachteiligen Auswirkungen
zwischen dem Bereich des Antriebsmotors und des Verdichters eine Dichtung angeordnet.
Darüber hinaus ist eine zusätzliche Verdichtereinheit vorgesehen, die das in den Bereich
des Antriebsmotors strömende Gas zurück in den Bereich des Verdichters fördert. Derartige
Verdichtereinheiten werden insbesondere bei der Verdichtung von Erdgas eingesetzt.
[0003] Ein Verdichter ähnlichen Typs ist aus der
DE 200 11 217 U1 bekannt. Der dort beschriebene Verdichter ist ebenfalls in einem nach außen gasdichten
Gehäuse gemeinsam mit dem Antriebsmotor angeordnet. Zwischen Verdichter und Antriebsmotor
ist eine Dichtung vorgesehen, die soweit durchlässig ist, um Prozessgas, das nach
der ersten Verdichterstufe entnommen und zur Kühlung in den Antriebsmotor eingeleitet
wird, wieder in den Verdichterbereich durchzulassen.
[0004] Aus der
EP 1 577 561 A1 ist ein Rotationskompressor mit einem aufwendigen doppelten Dichtgaskreislauf bekannt,
bei dem dem Kompressor Prozessgas entnommen und über die beiden Dichtgaskreisläufe
zusammen mit einem weiteren Dichtungs- oder Puffergas den zwischen den beiden Wellenlagern
der Antriebswelle und dem Kompressor angeordneten aufwendigen Labyrinth-Gasdichtungen
zugeführt wird. Aus den Gasdichtungen entweichendes Gas wird abgeführt, entweder in
die Atmosphäre oder zu einer Fackel. Auch dieser Kompressor wird zur Erdgasverdichtung
eingesetzt.
[0005] Ein weiterer Kompressor mit den Merkmalen des Oberbegriffs von Anspruch 1 ist bspw.
aus der
FR 2 528 127 bekannt (nächstliegender Stand der Technik).
[0006] Die bekannten Kompressoren sind nicht in Bereichen einsetzbar, in denen es auf eine
hohe Reinheit des Prozessgases ankommt und das Prozessgas zur Vermeidung von Verunreinigungen
somit auf keinen Fall mit dem Inneren des Motorbereichs in Kontakt gelangen darf.
[0007] Um einen gewünschten hohen Wirkungsgrad und eine hohe Energieeffizienz zu erzielen
sowie auch kleine Fördermengen bei hohen Drücken zu verdichten, werden Hochleistungsantriebe
mit magnetgelagerten Wellen verwendet, die mit sehr hohen Drehzahlen arbeiten. Bei
Verwendung angepasster Laufrad-Durchmesser der Verdichter sind Umdrehungen von 60.000
bis 80.000 U/min möglich. Ein derartiger Antrieb unterliegt jedoch hohen Betriebsanforderungen,
insb. dahingehend, dass das Innere des Motorgehäuses stabilen Druck-/Temperaturverhältnissen
unterliegen muss und keine lagerbelastenden Fremdpartikel eindringen dürfen. So dürfen
z.B. bei einer Verdichtung von Feinstpartikel aus bzw. mit Silicium enthaltenden Prozessgases
keine derartigen Siliciumpartikel in den Motorraum eindringen, da diese eine Beschädigung
der Wellenlager verursachen könnten. Auch muss ein Druckanstieg im Motorraum vermieden
werden, und insbesondere muss vermieden werden, dass die Betriebsbedingungen im Motorraum
einen für das im Motorraum befindliche Gas transkritischen Zustand annehmen.
[0008] Darüber hinaus ist es auch stets ein Bestreben, einen Prozessgasschwund zu minimieren,
insbesondere bei der Verarbeitung wertvoller und hochreiner Gase.
[0009] Die Verwendung bekannter Dichtungen wie Feststoffdichtungen und Fremdgasfluiddichtungen
scheidet aus, da diese stets mit Verunreinigungen des Prozessgases und damit einhergehenden
Reinigung oder Verlust verbunden sind.
[0010] Es ist daher ein Anliegen, einerseits eine Kontaminierung des Prozessgases mit Partikeln
aus dem Motorraum zu vermeiden, und andererseits eine Beeinträchtigung der Betriebsbedingungen
(Druck, Temperatur, Fremdpartikel) im Motorraum durch Prozessgas zu unterbinden.
[0011] Aus diesem Grunde wird erfindungsgemäß eine Vorrichtung zum Verdichten eines Prozessgases
mit den Merkmalen des Anspruchs 1 vorgeschlagen.
[0012] Die erfindungsgemäße Vorrichtung zum Verdichten eines Prozessgases (im folgenden
kurz Verdichtungsvorrichtung genannte) umfasst mindestens eine Verdichtereinheit sowie
einen in einem Motorgehäuse angeordneten Antriebsmotor. Der Antriebsmotor weist eine
Antriebswelle zum Antreiben der mindestens einen Verdichtereinheit aufweist. Des weiteren
ist erfindungsgemäß eine sogenannte gasdynamische Barriere vorgesehen, die im Bereich
der Antriebswelle zwischen der Verdichtereinheit und dem Motorgehäuse angeordnet ist.
Unter gasdynamischer Barriere ist eine Anordnung zu verstehen, die zur Vermeidung
von Eindringen von Prozessgas in das Motorgehäuse eine unter Ausnutzung der spezifischen
Gasdynamik der Verdichtungsvorrichtung erzeugte Barriere oder Schwelle für das an
einem Antriebswellendurchtritt aus dem Verdichtergehäuse durchtretende Prozessgas
darstellt. Die gasdynamische Barriere ist eine aus einem spezifischen Druckprofil
bestehende Gasbarriere, wobei das Druckprofil den sogenannten P-N-P-Effekt nutzt,
d.h. in der Mitte der Barriereanordnung herrscht der niedrigste Druck. Auf die erfindungsgemäße
Verdichtungsvorrichtung übertragen bedeutet dies, dass zwischen dem Verdichtergehäuse
und dem Motorgehäuse zwei Zonen vorzusehen sind, von denen die zum Verdichtergehäuse
weisende (verdichterseitige) Zone einen höheren Druck aufweist als die zum Motorgehäuse
weisende (antriebseitige) Zone, die wiederum einen niedrigeren Druck aufweist, als
in dem Motorgehäuse herrscht.
[0013] Die gasdynamische Barriere der Erfindung dient somit zur Vermeidung eines Durchtritts
von Prozessgas in das Motorgehäuse (32). Hierzu umfasst die gasdynamische Barriere
zwei Zonen (41, 43), nämlich eine zu dem Verdichtergehäuse weisende erste Zone (verdichterseitige
oder laufradseitige Zone) mit einem Druck, der höher ist als ein Druck einer zu dem
Motorgehäuse weisenden zweiten Zone (antriebseitige oder lagerseitige Zone), deren
Druck wiederum kleiner ist als ein Druck in dem Motorgehäuse.
[0014] Die Bildung der Zonen kann durch geeignete Maßnahmen erfolgen, bspw. mittels Gasdrosseleinrichtungen
o. dgl., die eine Drosselung bzw. Minderung des Gasflusses entlang der Antriebswelle
bewirken. Zwischen den Gasdrosseleinrichtungen o. d.gl. entstehen die entsprechenden
Zonen (oder auch Kammern). Die Gasdrosseleinrichtungen o. dgl. Können ringförmig um
die Antriebswelle angeordnet sein.
[0015] Die Druckfestlegung in der verdichterseitigen ersten Zone bzw. Kammer kann durch
Verbinden mit einer Druckausgleichsleitung erfolgen, die das Druckniveau der ersten
Zone auf das Niveau eines stromaufwärts einer Ansaugöffnung der Verdichtereinheit
herrschenden Prozessgas-Druckes bringt. Die Druckfestlegung in der antriebseitigen
zweiten Zone bzw. Kammer kann durch Verbinden mit einer Absaugvorrichtung erfolgen,
die das Druckniveau der zweiten Zone auf ein Druckniveau bringt, das etwas unter dem
Druckniveau im Innern des Motorgehäuses liegt.
[0016] Die Verdichtungsvorrichtung der Erfindung kann zwei Verdichtereinheiten umfassen.
Diese können in Reihe geschaltet sein. Sie können an einem gleichen Ende der Antriebswelle
oder jeweils an den gegenüberliegenden Enden der Antriebswelle angeordnet sein. Jeder
Verdichtereinheit ist eine erfindungsgemäße gasdynamische Barriere zugeordnet. Die
verdichterseitigen Kammern der beiden gasdynamischen Barrieren können (über eine gemeinsame
Leitung) miteinander verbunden sein. Die antriebseitigen Kammern der beiden gasdynamischen
Barrieren können (über eine gemeinsame Leitung) miteinander verbunden sein.
[0017] Weitere Vorteile und Ausgestaltungen der Erfindung ergeben sich aus der Beschreibung
und der beiliegenden Zeichnung.
[0018] Es versteht sich, dass die voranstehend genannten und die nachstehend noch zu erläuterten
Merkmale nicht nur in der jeweils angegebenen Kombination, sondern auch in anderen
Kombinationen oder in Alleinstellung verwendbar sind, ohne den Rahmen der vorliegenden
Erfindung zu verlassen.
[0019] Die Erfindung ist anhand eines Ausführungsbeispiels in der Zeichnung schematisch
dargestellt und wird im folgenden unter Bezugnahme auf die Zeichnung ausführlich beschrieben.
- Figur 1
- zeigt in schematischer Blockbilddarstellung eine erfindungsgemäße Vorrichtung zum
Verdichten eines Prozessgases.
- Figur 2
- zeigt in vergrößertem Ausschnitt eine erfindungsgemäße gasdynamische Barriere der
Vorrichtung zum Verdichten eines Prozessgases der Figur 1.
Figur 1 zeigt in schematischer Blockbilddarstellung eine erfindungsgemäße Vorrichtung
zum Verdichten eines Prozessgases, im folgenden kurz Verdichtungsvorrichtung 10 genannt.
[0020] Die Verdichtungsvorrichtung 10 umfasst eine erste Verdichtereinheit 12.1 mit einem
in einem Gehäuse 14.1 angeordneten Laufrad 16.1. Die Verdichtungsvorrichtung 10 umfasst
des weiteren eine zweite Verdichtereinheit 12.2, die ebenfalls ein in einem Gehäuse
14.2 angeordnetes Laufrad 16.2 aufweist.
[0021] Die beiden Verdichtereinheiten 12.1 und 12.2 sind derart angeordnet, dass zwischen
ihnen ein in einem hermetisch oder halbhermetisch gasdichten Motorgehäuse 32 angeordneter
Antriebsmotor 30 zu liegen kommt. Der Antriebsmotor 30 treibt eine Welle 36 an, die
mittels Lagern 34 drehgelagert ist. Der Antriebsmotor ist von im wesentlichen bekannter
Bauweise und aus diesem Grunde lediglich stark schematisch dargestellt. Die Lager
34 sind bspw. radiale Magnetlager.
[0022] Ein erstes Ende 36.1 der Welle 36 ist antriebsfest mit dem Laufrad 16.1 der ersten
Verdichtereinheit 12.1 verbunden, und ein zweites Ende 36.2 der Welle 36 ist antriebsfest
mit dem Laufrad 16.2 der zweiten Verdichtereinheit 12.2 verbunden.
[0023] Die beiden Verdichtereinheiten 12.1, 12.2 sind im Sinne einer zweistufigen Verdichtung
miteinander in Reihe geschaltet, d.h. über eine Zufuhr- bzw. Speiseleitung L1 einer
Ansaugöffnung 18.1 der ersten Verdichtereinheit 12.1 zugeführtes Prozessgas wird nach
dem erststufigen Verdichten über eine an eine Austrittsöffnung 20.1 der ersten Verdichtereinheit
12.1 angeschlossene Verbindungsleitung L2 einer Ansaugöffnung 18.2 der zweiten Verdichtereinheit
12.2 für das zweitstufige Verdichten zugeführt.
[0024] Im Bereich des Übertritts zwischen dem Motorgehäuse 32 und den Gehäusen 14.1., 14.2
der beiden Verdichtereinheiten 12.1, 12.2 ist erfindungsgemäß jeweils eine sogenannte
gasdynamische Barriere GB.1, GB.2 vorgesehen. Eine erste gasdynamische Barriere GB.1
ist zwischen dem Motorgehäuse 32 und dem Gehäuse 14.1 der ersten Verdichtereinheit
12.1 im Bereich des ersten Endes 36.1 der Welle 36 angeordnet, und die zweite gasdynamische
Barriere GB.2 ist zwischen dem Motorgehäuse 32 und dem Gehäuse 14.2 der zweiten Verdichtereinheit
12.2 im Bereich des zweiten Endes 36.2 der Welle 36 angeordnet. In dem dargestellten
Ausführungsbeispiel sind die gasdynamischen Barrieren GB.1 und GB.2 jeweils in einem
Wellenmantelgehäuse 38.1 bzw. 38.2 angeordnet, das der Ummantelung der Antriebswelle
36 im Bereich zwischen Motorgehäuse 32 und Verdichtergehäuse 14 dient.
[0025] Jede der gasdynamischen Barrieren GB.1, GB.2 umfasst drei um die Welle 36 in deren
Endbereichen 36.1, 36.2 angeordnete Gasdrosseleinrichtungen 40, 42, 44 (zur besseren
Erkennbarkeit in Figur 2 im Ausschnitt vergrößert für die erste gasdynamische Barriere
GB.1). Der Aufbau der gasdynamischen Barriere ist am Beispiel einer Barriere erläutert.
Für die beiden in der Verdichtungsvorrichtung 10 der Figur 1 verwendeten, spiegelsymmetrisch
angeordneten gasdynamischen Barrieren GB.1 und GB.2 sind jeweils die verwendeten Bezugszeichen
mit dem Suffix ".1" bzw. ".2" versehen.
[0026] Die Gasdrosseleinrichtungen 40, 42, 44 definieren jeweils paarweise zwischen benachbarten
Gasdrosseleinrichtungen 40, 42, und 42, 44 liegende Kammern 41 und 43. Die in Richtung
des Laufrads 16 angeordnete Gasdrosseleinrichtung 40 (verdichterseitige bzw. laufradseitige
Gasdrosseleinrichtung) bildet mit der ihr benachbarten mittigen Drosseleinrichtung
42 eine erste, laufradseitige Kammer 41. Die in Richtung des Antriebsmotors 30 und
dessen Wellenlager 34 angeordnete Gasdrosseleinrichtung 44 (lagerseitige bzw. antriebseitige
Gasdrosseleinrichtung) bildet mit der mittigen Drosseleinrichtung 42 eine zweite,
lagerseitige Kammer 43. Die Kammern 41, 43 sind stark schematisch dargestellt und
sind in der Praxis so ausgeführt, dass durch eine Gasdrosseleinrichtung gelangtes
Prozessgas in der Kammer gesammelt und abgeführt werden kann. Hierzu ist der ersten,
laufradseitigen Kammer 41 eine erste Abführleitung L4 zugeordnet, und der zweiten,
lagerseitigen Kammer 43 eine zweite Abführleitung L5 zugeordnet. Bei der ersten Abführleitung
L4 handelt es sich - wie nachstehend noch beschrieben - um eine Druckausgleichsleitung.
Bei der zweiten Abführleitung L5 handelt es sich - wie ebenfalls nachstehend beschrieben
- um eine Absaugleitung.
[0027] Die beiden ersten Abführleitungen L4.1 und L4.2 der laufradseitigen Kammern 41.1,
41.2 der beiden gasdynamischen Barrieren GB.1 und GB.2 werden zu einer Rückführleitung
L4 zusammengeführt, die in die Zuführleitung L1 zu der ersten Verdichtereinheit 12.1
im Bereich vor der Ansaugung führt.
[0028] Die beiden zweiten Abführleitungen L5.1 und L5.2 der zweiten Kammern 43.1, 43.2 der
beiden gasdynamischen Barrieren GB.1 und GB.2 werden über eine Absaugvorrichtung 50
zu einer gemeinsamen Abführleitung L5 zusammengeführt, die in einen Bereich vor der
Ansaugöffnung 18.1 der ersten Verdichtereinheit 12.1 führt, der eine geeignete Stelle
zur Rückführung des Prozessgases in den Verdichtungsprozess darstellt. Eine geeignete
Stelle bestimmt der Fachmann nach den Druckverhältnissen. Es handelt sich um eine
Stelle, die in der Regel relativ weit von dem Ansaugbereich der ersten Verdichtereinheit
entfernt ist und an der ein Druck herrscht, der in der Größenordnung des Druckes liegt,
der durch die Absaugvorrichtung 50 bereitgestellt wird. In der Darstellung der Figur
1 ist diese Rückführung am Ende der Rückführleitung L5 gestrichelt und verzweigt dargestellt,
um zu veranschaulichen, dass der Fachmann hier eine Auswahl zwischen mehreren prozessgegebenen
Möglichkeiten hat.
[0029] Im Betrieb der erfindungsgemäßen Verdichtungsvorrichtung herrscht in der Zuführleitung
L1 zu dem Ansaugstutzen 18.1 der ersten Verdichtereinheit 12.1 ein erster Druck P1.
Im Bereich der Ansaugung vor dem Laufrad 16.1 in dem Gehäuse 14.1 der ersten Verdichtereinheit
12.1 herrscht ein zweiter Druck (Ansaugdruck) P2, der leicht über dem ersten Druck
P1 liegt oder gleich dem ersten Druck P1 ist. Nach der Verdichtung der ersten Verdichterstufe
in der ersten Verdichtereinheit 12.1 unterliegt das Prozessgas im Bereich der Auslassöffnung
20.1 der ersten Verdichtereinheit 12.1 einem dritten Druck P3, der über die Verbindungsleitung
L2 auch an dem Ansaugstutzen 18.2 der zweiten Verdichtereinheit 12.2 anliegt. Nach
der Verdichtung der zweiten Verdichterstufe unterliegt das Prozessgas an dem Ausgang
20.2 der zweiten Verdichtereinheit 12.2 einem Zieldruck P4.
[0030] Es gilt somit: P4 > P3 > P2 ≥ P1 (wobei P2 nur wenig größer als P1 ist).
[0031] Die zwischen der ersten, laufradseitigen Kammer 41 jeder gasdynamischen Barriere
und der Zuführleitung L1 angebrachte Druckausgleichsleitung L4 bewirkt, dass in jeder
laufradseitigen Kammer 41.1 und 41.2 jeweils der Druck P1 anliegt. Das Prinzip besteht
also darin, von der laufradseitigen Kammer jeder gasdynamischen Barriere eine Druckausgleichsleitung
zu einem niedrigsten Druckniveau der regulär prozessgasführenden Bereiche der Gesamtvorrichtung
zu legen. Diese "Gasleckage" kann nach Zuführung in die Leitung L1 wieder dem eigentlichen
Prozessgas zugeführt werden. Dies kann - wie in dem Ausführungsbeispiel dargestellt
- in einen Bereich stromaufwärts des Ansaugbereiches der ersten Verdichtereinheit,
aber auch an jeder anderen (von den Druckverhältnissen her) geeigneten Stelle erfolgen.
In der Darstellung des Figur 1 ist an der Stelle der Rückführung des Prozessgases
in die Leitung L1 eine Leitungsverengung angedeutet. Diese Verengung kann sich als
vorteilhaft erweisen, um nach Bernoulli eine Geschwindigkeitserhöhung in diesem Leitungsbereich
zur Verbesserung des Effektes des Druckausgleichs und Prozessgasrückführung zu erzielen.
[0032] In der laufradseitigen ersten Kammer 41 entsteht somit ein Druckniveau P1, das wesentlich
geringer ist, als der Prozessdruck P3 bzw. P4 an dem zugeordneten Laufrad im Bereich
der Wellenenden 36.1, 36.2. (Der Druck an der Rückseite des Laufrades der Verdichtereinheit,
also im Bereich des Wellenendes 36.1 bzw. 36.2 der Antriebswelle 36, liegt in der
Regel zwischen den beiden Drücken im Ansaugbereich und im Austrittsbereich (Druckpaare
P2, P3 im ersten Verdichter bzw. P3, P4 im zweiten Verdichter) und ist somit auf jeden
Fall höher als der Druck P1 in der laufradseitigen ersten Kammer.)
[0033] Die Drosselung mittels der Gasdrosseleinrichtungen 40.1, 42.1, 44.1 sowie 40.2, 42.2,
44.2 kann berührungslos ausgeführt sein. Durch die erfindungsgemäße Maßnahme stellt
sich an jedem Wellenende 36.1 und 36.2 der gleiche Druck P1 ein, auch wenn beiden
Wellenenden eine separate Verdichtereinheit zugeordnet ist. Dadurch wird ein Durchströmen
der Antriebseinheit mit Prozessgas verhindert.
[0034] Mit der dritten, antriebseitigen Gasdrosseleinrichtung 44.1, 44.2 und der dadurch
erzeugten antriebseitigen zweiten Kammer 43.1 bzw. 43.2 wird darüber hinaus erreicht,
dass in dem Gehäuse 32 des Antriebsmotors 3 die Betriebsbedingungen stabil gehalten
werden, d.h. es wird erreicht, dass kein hoher Druck, keine hohe Temperatur und keine
Prozesspartikel im Antriebsbereich auftreten können und somit der Betrieb der Antriebseinheit
mit sehr hohen Drehzahlen gewährleistet ist.
[0035] Hierzu wird erfindungsgemäß eine Absaugung der antriebseitigen Kammern 43.1, 43.2
mittels der Absaugvorrichtung 50 vorgesehen. Als Absaugvorrichtung 50 kann jede bekannte
hermetisch dichte Absaugvorrichtung verwendet werden, wie bspw. eine Membranpumpe.
[0036] Abhängig von der Absaugleistung bzw. der Einstellung der Absaugvorrichtung 50 stellt
sich ein (einstellbares) Druckniveau PM' in der lagerseitigen Kammer 43 ein, das leicht
unter dem in der Antriebseinheit selbst herrschenden Druckniveau PM liegt. Die abgesaugte
Gasmenge kann (über die Leitung L5) an einer anderen günstigen Stelle dem Verdichtungsprozess
wieder zugeführt werden. Es gilt somit: PM' < PM « P1`. Das Verhältnis zwischen P1`
und P1 hängt im Endeffekt von der gewählten Absaugleistung ab und davon, an welcher
Stelle die Rückführleitung L5 in den Prozess wieder eingeführt wird. P1' kann somit
größer oder kleiner P1 sein, ist aber stets größer als PM. Wird - wie in der Figur
angedeutet - die Rückführleitung in einen Bereich mit Druck P1 geführt, dann ist P1`
> P1. Außerdem gilt entsprechend der Einstellung der Absaugung: PM > P0 (P0: Umgebungsdruck,
ca. 1 bar).
[0037] Typische Größenordnungen für die angegebenen Drücke in dem dargestellten Ausführungsbeispiel
sind bspw. ca. 29 bis 30 bar für P1, 30 bar für P2, 70 bar für P3, 140 bar für P4
sowie 1,5 bar für PM, 1,3 bar für PM' und 27,1 bar für P1'. Es ist jedoch zu betonen,
dass diese Druckangaben lediglich ein mögliches Ausführungsbeispiel betreffen und
ausschließlich zur Veranschaulichung der Funktionsweise der Erfindung dienen. Der
Fachmann kann die Erfindung je nach Anwendungsgebiet mit anderen Druckverhältnissen
umsetzen. Lediglich die Rangfolge der Druckverhältnisse ist maßgeblich.
[0038] Vor Prozessbeginn, d.h. vor dem Starten des Antriebsmotors 30 und der Welle 36, sollten
die gasdynamischen Barrieren GB.1, GB.2 bereits aktiviert sind, d.h. insbesondere
die Absaugvorrichtung 50 sollte eingeschaltet sein. Auch nach Beendigung des Verdichtungsprozesses
sollte ein Nachlauf der gasdynamischen Barrieren vorgesehen sein. Dadurch wird ein
korrektes Funktionieren der gasdynamischen Barrieren gewährleistet. Insbesondere wird
gewährleistet, dass nicht aufgrund eines falschen Druckprofils in den gasdynamischen
Barrieren Prozessgas in den Motorbereich gelangt, oder Gase/Luft mit Partikeln aus
dem Motorbereich in den Verdichterbereich gelangen.
1. vorrichtung zum Verdichten eines Prozessgases (10), mit
- mindestens einer Verdichtereinheit (12.1, 12.2) in einem Verdichtergehäuse (14.1,
14.2),
- einem in einem Motorgehäuse (32) angeordneten Antriebsmotor (30), der eine Antriebswelle
(36) zum Antreiben der mindestens einen Verdichtereinheit (12.1, 12.2) aufweist, und
- einer im Bereich der Antriebswelle (36) zwischen dem Verdichtergehäuse (14.1, 14.2)
und dem Motorgehäuse (32) angeordneten gasdynamischen Barriere (GB),
dadurch gekennzeichnet, dass die gasdynamische Barriere (GB) zur Vermeidung eines Durchtritts von Prozessgas in
das Motorgehäuse (32) zwei kammern (41.1, 41.2, 43.1, 43.2) umfasst, nämlich eine
zu dem Verdichtergehäuse weisende erste kammer (41.1, 41.2) mit, einem Druck (P1),
der höher ist als ein Druck (PM') einer zu dem Motorgehäuse (32) weisenden zweiten
kammer (43.1, 43.2), deren Druck (PM') wiederum kleiner ist als ein Druck (PM) in
dem Motorgehäuse.
2. Vorrichtung (10) nach Anspruch 1, in der die erste und die zweite kammer mittels Gasdrosseleinrichtungen
(40.1, 40.2, 42.1, 42.2, 44.1, 44.2) gebildete Kammern (41.1, 41.2, 43.1, 43.2) sind.
3. Vorrichtung (10) nach Anspruch 1 oder 2, in der eine Druckausgleichsleitung (L4) vorgesehen
ist, um die erste kammer (41.1, 41.2) auf das Niveau eines stromaufwärts einer Ansaugöffnung
(18.1) der Verdichtereinheit (12.1) herrschenden Prozessgas-Druckes (P1) zu bringen.
4. Vorrichtung (10) nach einem der Ansprüche 1 bis 3, in der eine Absaugvorrichtung (50)
vorgesehen ist, um die zweite kammer (43.1, 43.2) auf ein Druckniveau (PM') zu bringen,
das etwas unter dem in dem Motorgehäuse (32) herrschenden Druck (PM) liegt.
5. Vorrichtung (10) nach einem der Ansprüche 2 bis 4, in der die Gasdrosseleinrichtungen
(40.1, 40.2, 42.1, 42.2), 44.1, 44.2) um die Antriebswelle (36) im Bereich zwischen
Verdichtergehäuse (14.1, 14.2) und Motorgehäuse (32) angeordnet sind.
6. Vorrichtung (10) nach Anspruch 5, in der die Gasdrosseleinrichtungen (40.1, 40.2,
42.1, 42.2, 44.1, 44.2) ringförmig um die Antriebswelle (36) angeordnet sind.
7. Vorrichtung (10) nach einem der Ansprüche 1 bis 6, in der die gasdynamische Barriere
(GB) in einem Wellenmantelgehäuse (38) angeordnet ist.
8. Vorrichtung (10) nach einem der Ansprüche 1 bis 6, die zwei Verdichtereinheiten (12.1,
12.2) mit jeweils zugeordneter gasdynamischer Barriere (GB.1, GB.2) aufweist.
9. Vorrichtung (10) nach Anspruch 8, bei der eine erste Verdichtereinheit (12.1) an einem
ersten Wellenende (36.1) der Antriebswelle (36) und eine zweite Verdichtereinheit
(12.2) an einem zweiten Wellenende (36.2) der Antriebswelle (36) angeordnet ist.
10. Vorrichtung (10) nach Anspruch 8 oder 9, bei der die zwei Verdichtereinheiten (12.1,
12.2) in Reihe geschaltet sind.
11. Vorrichtung (10) nach einem der Ansprüche 1 bis 10, bei der eine Rückführung von Prozessgas
aus der ersten kammer (41.1, 41.2) und/oder aus der zweiten kammer (43.1, 43.2) an
eine geeignete Stelle erfolgt.
12. Vorrichtung (10) nach Anspruch 3, bei der eine Rückführung von Prozessgas aus der
ersten kammer (41.1, 41.2) über die Druckausgleichsleitung (L4) erfohgt.
13. Vorrichtung (10) nach einem der Ansprüche 1 bis 12, bei der eine Aktivierung der gasdynamischen
Barriere (GB) vor Inbetriebnahme der mindestens einen Verdichtereinheit (12.1, 12.2)
erfolgt und/oder eine Inaktivierung der gasdynamischen Barriere (GB) erst nach einer
Plachlaufzeit nach Abschalten der mindestens einen Verdichtereinheit (12.1, 12.2)
erfolgt.
14. Verfahren zum Betrieb einer Vorrichtung zum Verdichten (10) nach einem der Ansprüche
1 bis 13, in dem die gasdynamische Barriere (GB) vor Inbetriebnahme der mindestens
einen Verdichtereinheit (12.1, 12.2) aktiviert wird, und/oder in dem die gasdynamische
Barriere (GB) erst nach einer Nachlaufzeit nach Abschalten der mindestens einen Verdichtereinheit
(12.1, 12.2) inaktiviert wird.
15. Verfahren nach Anspruch 14, in dem das Aktivieren und Inaktivieren durch Einschalten
bzw. Ausschalten einer der zweiten kammer (43.1, 43.2) der gasdynamischen Barriere
(GB) zugeordneten Absaugvorrichtung (50) erfolgt.
1. An apparatus for compressing a process gas (10), comprising
- at least one compressor unit (12.1, 12.2) in a compressor housing (14.1, 14.2);
- a driving motor (30) arranged in a motor housing (32), comprising a driving shaft
(36) for driving the at least one compressor unit (12.1, 12.2); and
- a gas-dynamic barrier (GB) arranged in the region of the driving shaft (36) between
the compressor housing (14.1, 14.2) and the motor housing (32);
characterized in that, in order to prevent a passage of process gas into the motor housing (32), the gas-dynamic
barrier (GB) comprises two chambers (41.1, 41.2, 43.1, 43.2), that is, a first chamber
(41.1, 41.2) facing to the compressor housing and having a pressure (P1) which is
higher than a pressure (PM') of a second chamber (43.1, 43.2) facing to the motor
housing (32), the pressure (PM') of which is in turn smaller than a pressure (PM)
in the motor housing.
2. The apparatus (10) according to claim 1, in which the first and the second chamber
(41.1, 41.2, 43.1, 43.2) are chambers (41.1, 41.2, 43.1, 43.2) formed by means of
gas throttling means (40.1, 40.2, 42.1, 42.2, 44.1, 44.2).
3. The apparatus (10) according to claim 1 or 2, in which a pressure equalization or
compensation conduit (L4) is provided in order to bring the first chamber (41.1, 41.2)
to the level of a process gas pressure (P1) prevailing upstream of an aspirating part
(18.1) of the compressor unit (12.1).
4. The apparatus (10) according to any one of claims 1 to 3, in which a suction apparatus
(15) is provided in order to bring the second chamber (43.1, 43.2) to a pressure level
(PM') which is slightly below the pressure (PM) prevailing in the motor housing (32).
5. The apparatus (10) according to any one of claims 2 to 4, in which the gas throttling
means (40.1, 40.2, 42.1, 42.2, 44.1, 44.2) are arranged around the driving shaft (36)
in the region between the compressor housing (14.1, 14.2) and the motor housing (32).
6. The apparatus (10) according to claim 5, in which the gas throttling means (40.1,
40.2, 42.1, 42.2, 44.1, 44.2) are arranged annularly around the driving shaft (36).
7. The apparatus (10) according to any one of claims 1 to 6, in which the gas-dynamic
barrier (GB) is arranged in a shaft shell housing (38).
8. The apparatus (10) according to any one of claims 1 to 6, comprising two compressor
units (12.1, 12.2) each having an associated gas-dynamic barrier (GB.1, GB.2).
9. The apparatus (10) according to claim 8, in which a first compressor unit (12.1) is
arranged at a first shaft end (36.1) of the driving shaft (36) and a second compressor
(12.2) is arranged at a second shaft end (36.2) of the driving shaft (36).
10. The apparatus (10) according to claim 8 or 9, in which both the compressor units (12.1,
12.2) are serially connected.
11. The apparatus (10) according to any one of claims 1 to 10, in which a recirculation
of process gas from the first chamber (41.1, 41.2) and/or from the second chamber
(43.1, 43.2) is performed at an appropriate location.
12. The apparatus (10) according to claim 3, in which recirculation of process gas from
the first chamber (41.1, 41.2) is performed via the pressure equalization conduit
(L4).
13. The apparatus (10) according to any one of claims 1 to 12, in which an activation
of the gas-dynamic barrier (GB) is performed before starting the at least one compressor
unit (12.1, 12.2), and/or a deactivation of the gas-dynamic barrier (GB) is performed
not until a follow-up time has elapsed after turning off the at least one compressor
unit (12.1, 12.2).
14. A method for operating a compressing apparatus (10) according to any one of claims
1 to 13, in which the gas-dynamic barrier (GB) is activated before starting the at
least one compressor unit (12.1, 12.2), and/or in which the gas-dynamic barrier is
deactivated not until a follow-up time has elapsed after turning off the at least
one compressor unit (12.1, 12.2).
15. The method according to claim 14, in which the activation and deactivation are performed
by turning on and turning off, respectively, a suction apparatus (50) associated to
the second chamber (43.1, 43.2) of the gas-dynamic barrier (GB).
1. Appareil pour comprimer un gaz de procédé (10), comprenant
- au moins une unité de compression (12.1, 12.2) dans un boîtier de compresseur (14.1,
14.2);
- un moteur d'entraînement (30) agencé dans un carter moteur (32), qui comporte un
arbre d'entraînement (36) pour entraîner ladite au moins une unité de compression
(12.1, 12.2); et
- une barrière dynamique vis-à-vis des gaz (GB) agencée dans la région de l'arbre
d'entraînement (36) entre le boîtier de compresseur (14.1, 14.2) et le carter moteur
(32); caractérisé en ce que la barrière dynamique vis-à-vis des gaz (GB), pour éviter une traversée du gaz de
procédé vers le carter moteur (32), comprend deux chambres (41.1, 41.2, 43.1, 43.2),
à savoir une première chambre (41.1, 41.2) tournée vers le boîtier de compresseur
avec une pression (P1) qui est plus élevée qu'une pression (PM') d'une seconde chambre
(43.1, 43.2) tournée vers le carter moteur (32), dont la pression (PM') est à nouveau
inférieure à une pression (PM) dans le carter moteur.
2. Appareil (10) selon la revendication 1, dans lequel la première et la seconde chambre
sont des chambres (41.1, 41.2, 43.1, 43.2) formées au moyen de systèmes d'étranglement
de gaz (40.1, 40.2, 42.1, 42.2, 44.1, 44.2).
3. Appareil (10) selon la revendication 1 ou 2, dans lequel il est prévu un conduit de
compensation de pression (L4) afin d'amener la première chambre (41.1, 41.2) au niveau
d'une pression (P1) du gaz de procédé qui règne en amont d'une ouverture d'aspiration
(18.1) de l'unité de compression (12.1).
4. Appareil (10) selon l'une des revendications 1 à 3, dans lequel il est prévu un dispositif
d'aspiration (50) afin d'amener la seconde chambre (43.1, 43.2) à un niveau de pression
(PM') qui se trouve quelque peu plus bas que la pression (PM) qui règne dans le carter
moteur (32).
5. Appareil (10) selon l'une des revendications 2 à 4, dans lequel les systèmes d'étranglement
de gaz (40.1, 40.2, 42.1, 42.2, 44.1, 44.2) sont agencés autour de l'arbre d'entraînement
(36) dans la région entre le boîtier de compresseur (14.1, 14.2) et le carter moteur
(32).
6. Appareil (10) selon la revendication 5, dans lequel les systèmes d'étranglement de
gaz (40.1, 40.2, 42.1, 42.2, 44.1, 44.2) sont agencés en formant un anneau autour
de l'arbre d'entraînement (36).
7. Appareil (10) selon l'une des revendications 1 à 6, dans lequel la barrière dynamique
vis-à-vis des gaz (GB) est agencée dans un boîtier (38) qui enveloppe l'arbre.
8. Appareil (10) selon l'une des revendications 1 à 4, qui comporte deux unités de compresseur
(12.1, 12.2) avec des barrières dynamiques vis-à-vis des gaz (GB.1, GB.2).
9. Appareil (10) selon la revendication 8, dans lequel une première unité de compresseur
(12.1) est agencée à une première extrémité (36.1) de l'arbre d'entraînement (36)
et une seconde unité de compresseur (12.2) est agencée à une seconde extrémité (36.2)
de l'arbre d'entraînement (36).
10. Appareil (10) selon la revendication 8 ou 9, dans lequel les deux unités de compresseur
(12.1, 12.2) sont branchées en série.
11. Appareil (10) selon l'une des revendications 1 à 10, dans lequel se produit un recyclage
du gaz de procédé provenant de la première chambre (41.1, 41.2) et/ou de la seconde
chambre (43.1, 43.2) à un emplacement approprié.
12. Appareil (10) selon la revendication 3, dans lequel un recyclage du gaz de procédé
provenant de la première chambre (41.1, 41.2) se produit via la conduite de compensation
de pression (L4).
13. Appareil (10) selon l'une des revendications 1 à 12, dans lequel une activation de
la barrière dynamique vis-à-vis des gaz (GB) a lieu avant mise en service de ladite
au moins une unité de compression (12.1, 12.2), et/ou en ce qu'une désactivation de
la barrière dynamique vis-à-vis des gaz (GB) a lieu uniquement après un temps de latence
après coupure de ladite au moins une unité de compression (12.1, 12.2).
14. Procédé pour le fonctionnement d'un appareil pour comprimer (10) selon l'une des revendications
1 à 13, dans lequel la barrière dynamique vis-à-vis des gaz (GB) est activée avant
la mise en service de ladite au moins une unité de compression (12.1, 12.2), et/ou
en ce que la barrière dynamique vis-à-vis des gaz (GB) est désactivée uniquement après
un temps de latence après coupure de ladite au moins une unité de compression (12.1,
12.2).
15. Procédé selon la revendication 14, dans lequel l'activation et la désactivation ont
lieu par enclenchement ou coupure d'un dispositif d'aspiration (50) associé à la seconde
chambre (43.1, 43.2) de la barrière dynamique vis-à-vis des gaz (GB).
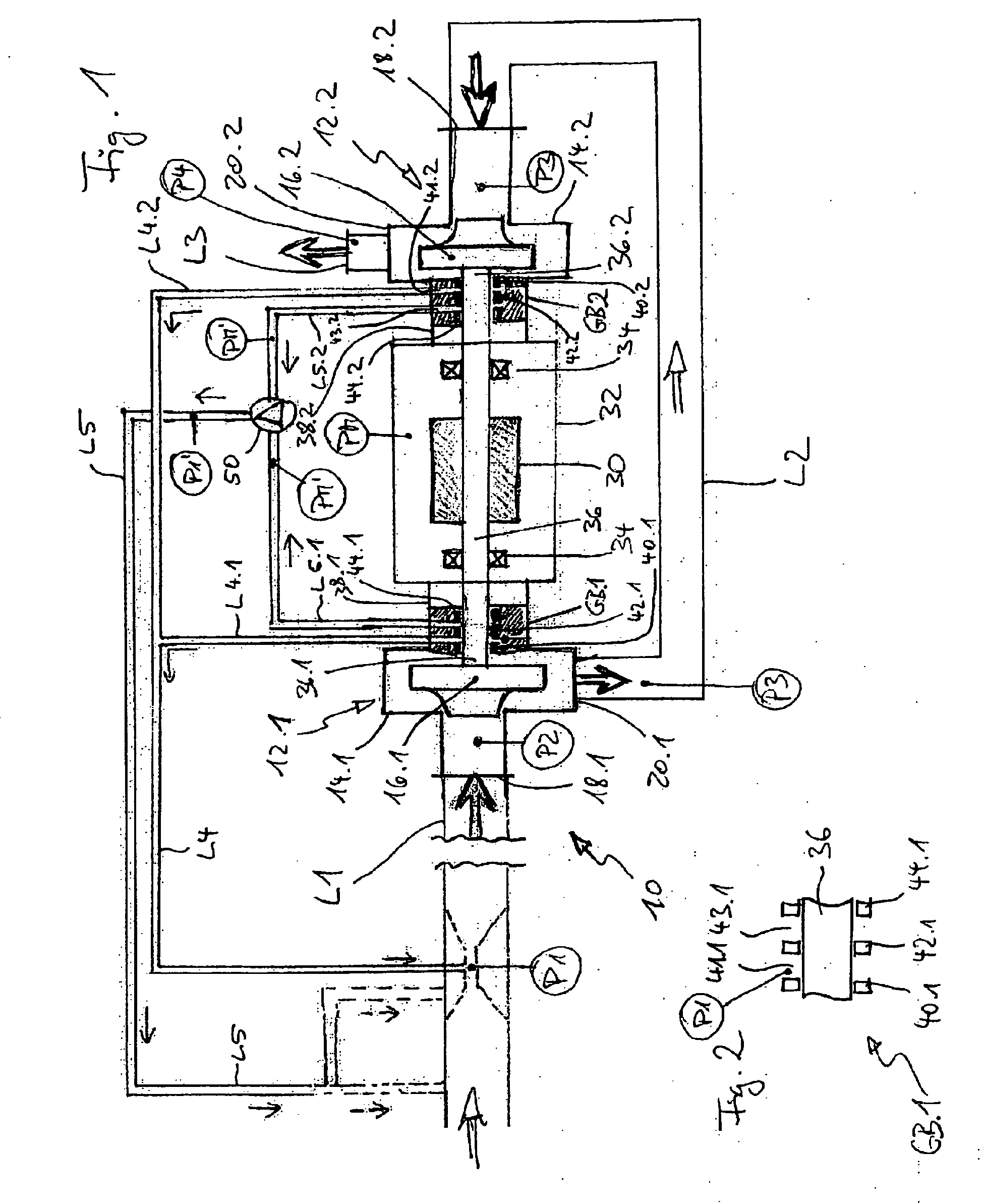
IN DER BESCHREIBUNG AUFGEFÜHRTE DOKUMENTE
Diese Liste der vom Anmelder aufgeführten Dokumente wurde ausschließlich zur Information
des Lesers aufgenommen und ist nicht Bestandteil des europäischen Patentdokumentes.
Sie wurde mit größter Sorgfalt zusammengestellt; das EPA übernimmt jedoch keinerlei
Haftung für etwaige Fehler oder Auslassungen.
In der Beschreibung aufgeführte Patentdokumente