TECHNICAL FIELD
[0001] The present invention relates to a glow plug used for preheating of a diesel engine
and the like, and a heating device.
BACKGROUND ART
[0002] As a glow plug used for preheating or the like a diesel engine in general, there
has been known a glow plug which has the sheath heater structure. The sheath heater
structure is formed by sealing a heating resistor made of an alloy containing chromium
(Cr), aluminum (Al) or the like in addition to iron (Fe) and nickel (Ni) which are
main components, together with insulation powder, in the inside of a tube which is
made of an alloy containing iron (Fe) and nickel (Ni) as main components and is formed
in a cylindrical shape with a closed front end.
[0003] Recently, to realize the further reduction of emission or the like, there has been
a demand for the further elevation of a temperature in the inside of a combustion
chamber. To satisfy this demand, heat may be generated by a glow plug at a higher
temperature (for example, setting a temperature of a surface of a tube to 1150°C or
more). However, since the temperature difference between a temperature of a surface
of the tube and a temperature of the heating resistor is approximately 300°C, to heat
the glow plug at a higher temperature, it is necessary to heat the heating resistor
at an extremely high temperature (for example, 1450°C or more). However, a melting
point of a conventionally-used alloy containing Fe and Ni as main components is around
1500°C. Accordingly, when the heating resistor is heated up to the above-mentioned
extremely high temperature, there is a possibility of giving rise to a drawback such
as melting of the heating resistor.
[0004] In view of the above, to realize the enhancement of heat resistance, a heating resistor
may be made of tungsten (W) or molybdenum (Mo) which has a high melting point (see
patent document 1 and the like, for example).
Prior art document
Patent document
SUMMARY OF THE INVENTION
Problems that the Invention is to Solve
[0006] However, W and Mo have a property that these components are extremely likely to be
oxidized and hence, W or Mo reacts with oxygen present inside the tube thus giving
rise to a possibility that the heating resistor is rapidly degraded.
[0007] Further, to realize the heat generation of the glow plug at a higher temperature,
it is necessary to enhance durability of the tube per se besides durability of heating
resistor. However, Fe and Ni are likely to be oxidized under high temperature and
hence, there exists a possibility that the tube made of an alloy which does not sufficiently
contain Al or Cr while containing Fe and Ni as main components cannot have sufficient
durability.
[0008] The present invention has been made under such circumstances, and it is an object
of the present invention to provide a glow plug which has a heating resistor made
of a metal material which contains W or Mo as a main component, wherein durability
of both the heating resistor and a tube can be enhanced so that the heat generation
at a higher temperature can be realized over a long period, a manufacturing method
of the glow plug, and a heating device provided with the glow plug.
Means for Solving the Problems
[0009] Hereinafter, the respective constitutions suitable for achieving the above-mentioned
object are explained in accordance with paragraphs. The manner of operation and advantageous
effects peculiar to the corresponding constitutions are described when necessary.
Constitution 1
[0010] A heating device having this constitution includes:
a glow plug which has a heating resistor thus constituting a heating part; and
a energization control device which is configured to adjust electric power to be supplied
to the heating resistor, and is capable of controlling the heat generation of the
heating resistor by adjusting the electric power to be supplied, wherein
the energization control device supplies the electric power to the heating resistor
such that a temperature of the heating part is elevated to 1000°C from a normal temperature
within 3 seconds,
the glow plug includes;
a cylindrical tube which has a closed front end portion and constitutes the heating
part in a state where the heating resistor is inserted into the inside of the tube;
and
a seal portion which is provided at a rear-end-side opening of the tube and brings
the inside of the tube into a sealed state,
the heating resistor is made of a metal material containing W or Mo as a main component,
and
the tube is made of an alloy containing 0.5 mass% or more and 5.0 mass% or less of
Al and 20 mass% or more and 40 mass% or less of Cr.
[0011] Here, "heating part" means the tube into which the heating resistor is inserted.
However, a portion of a surface of the tube where a temperature becomes the highest
due to the energization of the heating resistor may be employed as a portion corresponding
to "heating part".
[0012] According to the above-mentioned constitution 1, the heating resistor is made of
the metal material which contains W or Mo having a high melting point as a main component
and hence, the heating resistor having excellent heat resistance can be realized.
[0013] On the other hand, as described previously, there exists a possibility that oxidation
resistance is lowered due to the use of W or Mo. According to the above-mentioned
constitution 1, however, the tube contains 0.5 mass% or more of Al and 20 mass% or
more of Cr. Accordingly, at the time of heat generation, Al or Cr which is more likely
to be oxidized than W or Mo functions as an oxygen getter element and hence, an oxide
film made of Al
2O
3 or Cr
2O
3 is formed on an inner peripheral surface of the tube. Since the inside of the tube
is in a sealed state, an oxygen partial pressure inside the tube can be effectively
lowered. As a result, the oxidation of the heating resistor containing W or Mo as
a main component can be more surely prevented.
[0014] Further, by allowing the tube to contain a predetermined quantity or more of Al or
Cr, an oxide film made of Al
2O
3 or Cr
2O
3 can be formed on an outer surface of the tube over a broad range. The intrusion of
oxygen into the inside of the tube can be more surely suppressed due to the oxide
film and hence, the oxidation resistance of the tube can be enhanced. Further, the
content of Al or Cr is set sufficiently large and hence, even when peeling-off or
cracks occur in the oxide film due to thermal stress caused by the repetition of a
thermal cycle, the oxide film can be formed again more surely and over a longer period.
[0015] As described above, according to the above-mentioned constitution 1, by allowing
the tube to contain a predetermined quantity or more of Al or Cr, the oxidation of
the heating resistor made of W, Mo or the like can be effectively prevented, the heating
resistor can sufficiently exhibit the excellent heat resistance which W or Mo possesses,
and the tube can maintain the excellent oxidation resistance for a long period. As
a result, durability of both the heating resistor and the tube can be remarkably enhanced
whereby the glow plug can realize the heat generation at a higher temperature over
a long period.
[0016] Further, according to the above-mentioned constitution 1, the energization control
device supplies the electric power to the heating resistor such that the temperature
of the surface of the tube (heating part) is elevated to 1000°C from the normal temperature
within 3 seconds. By heating the tube rapidly in this manner, thermal stress applied
to the tube can be increased. Accordingly, an oxide film made of Al
2O
3 or Cr
2O
3 formed on the inner peripheral surface of the tube can be easily broken and hence,
a non-oxidized metal surface is likely to be exposed from the oxide film on the inner
peripheral surface of the tube. Due to the new oxidation of Al or Cr contained in
the metal surface, an oxygen partial pressure inside the tube can be further reduced
thus preventing the oxidation of the heating resistor made of W or the like extremely
effectively.
[0017] When an Al content in the tube exceeds 5.0 mass% or a Cr content in the tube exceeds
40 mass%, there exists a possibility that workability of the tube is lowered. Accordingly,
it is preferable to set the Al content to 5.0 mass% or less and the Cr content to
40 mass% or less.
Constitution 2
[0018] The heating device having this constitution is, in the above-mentioned constitution
1, characterized in that an average value of normal-temperature resistance at a portion
of the heating resistor between a front end of the heating resistor and a position
6 mm away from the front end toward a rear end of the heating resistor along a center
axis of the tube is set larger than an average value of the normal-temperature resistance
of the whole heating resistor.
[0019] Here, "an average value of normal-temperature resistance at a portion of the heating
resistor between a front end of the heating resistor and a position 6 mm away from
the front end toward a rear end of the heating resistor along a center axis of the
tube" means a value obtained by dividing the normal-temperature resistance at the
portion of the heating resistor between the front end of the heating resistor and
the position 6 mm away from the front end toward the rear end of the heating resistor
along the center axis of the tube (front-end-side heating body) by a length of the
front-end-side heating body along the center axis of the tube (that is, the normal-temperature
resistance of the front-end-side heating body per unit length along the center axis
of the tube). Further, "average value of the normal-temperature resistance of the
whole heating resistor" means a value obtained by dividing the normal-temperature
resistance of the whole heating resistor by a length of the heating resistor along
the center axis of the tube (that is, normal-temperature resistance of the heating
resistor per unit length along the center axis of the tube) (same definition being
applicable hereinafter).
[0020] In a state where a glow plug is assembled to an internal combustion engine, in general,
a portion of the tube between a front end and a position approximately 4 mm away from
the front end toward a rear end (hereinafter referred to as "exposed portion") is
arranged in the inside of the combustion chamber by projecting into a combustion chamber
from an inner wall of the combustion chamber. Accordingly, the temperature of the
exposed portion is likely to become higher at the time of heat generation compared
to other portions of the tube around which constitutional parts of the internal combustion
engine are positioned. Further, the temperature of the exposed portion is more rapidly
elevated compared to other portions of the tube, and the exposed portion is also rapidly
cooled and hence, the exposed portion is likely to be subjected to a sudden temperature
change. Accordingly, at the time of supplying electric power to the heating resistor,
by particularly elevating the temperature of the exposed portion, the temperature
of the tube can be elevated higher, and it is possible to cause a rapid temperature
change in the tube. By setting the temperature of the tube higher or by causing the
rapid temperature change in the tube, thermal stress which occurs in the tube can
be further increased and hence, an oxide film made of Al
2O
3 or Cr
2O
3 formed on an inner peripheral surface of the tube can be more easily broken. As a
result, an oxidation prevention effect of the heating resistor by the above-mentioned
constitution 1 can be further enhanced.
[0021] In view of the above-mentioned point, according to the above-mentioned constitution
2, the average value of the normal-temperature resistance at the portion of the heating
resistor between the front end of the heating resistor and the position 6 mm away
from the front end toward the rear end of the heating resistor along the center axis
of the tube (front-end-side heating body) is set larger than the average value of
the normal-temperature resistance of the whole heating resistor. By setting the average
value of the normal-temperature resistance of the front-end-side heating body larger
than the average value of the normal-temperature resistance of the whole heating resistor,
the temperature of a portion of the tube at the position approximately 2 mm away from
the front end toward the rear end (that is, a center portion of the exposed portion
and an area around the center portion) can be positively elevated. Accordingly, due
to the above-mentioned constitution 2, the temperature of the tube can be elevated
higher, and it is also possible to cause a rapid temperature change in the tube. As
a result, thermal stress which is generated in the tube can be further increased leading
to the further enhancement of an oxidation prevention effect of the heating resistor.
[0022] Further, to rapidly elevate the temperature in the combustion chamber, it is desirable
to particularly elevate the temperature of the exposed portion. Accordingly, the above-mentioned
constitution 2 has significance also in this respect.
Constitution 3
[0023] The heating device having this constitution is, in the above-mentioned constitution
1 or 2, characterized in that the heating resistor is formed into a coil shape, a
wire diameter of the heating resistor is 0.2 mm or more, and
an average pitch of a portion of the heating resistor between the front end of the
heating resistor and the position 6 mm away from the front end toward the rear end
of the heating resistor along the center axis of the tube is set smaller than an average
pitch of a portion of the heating resistor positioned on a more rear end side than
the position 6 mm away from the front end toward the rear end of the heating resistor
along the center axis of the tube by 0.9 mm or more.
[0024] Here, "average pitch" means, in a cross section which includes the center axis (coil
axis) of the heating resistor, an average of a distance (pitch) between the centers
of cross sections of neighboring heating resistors along the center axis (coil axis)
(the same definition being applicable hereinafter).
[0025] According to the above-mentioned constitution 3, the average pitch at the portion
of the heating resistor between the front end and the position 6 mm away from the
front end toward the rear end (front-end-side heating body) is set smaller than the
average pitch at the portion of the heating resistor positioned on the more rear end
side than the portion of the heating resistor 6 mm away from the front end (rear-end-side
heating body) by 0.9 mm or more. Accordingly, without making the front-end-side heating
body excessively thin (by maintaining a wire diameter of the heating resistor to 0.
2 mm or more), the average value of the normal-temperature resistance of the front-end-side
heating body can be set sufficiently large compared to the average value of the normal-temperature
resistance of the whole heating resistor. That is, according to the above-mentioned
constitution 3, it is possible to further rapidly elevate the temperature of the exposed
portion while sufficiently maintaining mechanical strength of the heating resistor.
As a result, an oxidation prevention effect of the heating resistor can be further
enhanced.
[0026] Further, it is unnecessary to make the front-end-side heating body excessively thin
and hence, the heating resistor can be manufactured relatively easily thus preventing
lowering of productivity more reliably.
Constitution 4
[0027] The heating device having this constitution is, in any one of the above-mentioned
constitutions 1 to 3, characterized in that the glow plug includes insulation powder
which is filled in the tube and around the periphery of the heating resistor, and
the insulation powder is powder which contains magnesium oxide (MgO) as a main component.
[0028] According to the above-mentioned constitution 4, since MgO which exhibits excellent
thermal conductivity is used as the insulation powder, the thermal conductivity from
the heating resistor to the tube can be enhanced. As a result, it is possible to make
the glow plug (heating part) generate heat at a higher temperature without excessively
elevating a temperature of the heating resistor.
[0029] Further, since the temperature of the tube (heating part) can be set higher, thermal
stress applied to the tube can be further increased whereby an oxide film made of
Al
2O
3 or Cr
2O
3 formed on the inner peripheral surface of the tube can be more easily broken. Accordingly,
an unoxidized metal surface is more likely to be exposed on the inner peripheral surface
of the tube and hence, an oxygen partial pressure inside the tube can be lowered more
effectively due to the oxidation of Al or Cr contained in the metal surface.
[0030] Further, while MgO is likely to form a composite oxide between MgO and Al
2O
3 or Cr
2O
3 formed on the inner peripheral surface of the tube, the composite oxide is extremely
coarse compared to an oxide film made of Al
2O
3 or the like. Accordingly, Al or Cr contained in the tube and oxygen present inside
the tube more easily react with each other and hence, an oxygen partial pressure inside
the tube can be further lowered.
[0031] Due to a synergistic action of favorable heat conductivity which is property that
MgO possesses and property of MgO that MgO easily forms a composite oxide with Al
2O
3 or the like, an oxygen partial pressure inside the tube can be reduced extremely
effectively. As a result, durability of the heating resistor can be further enhanced
whereby the heat generation at a higher temperature can be realized over a further
prolonged period with respect to the glow plug.
Constitution 5
[0032] The heating device having this constitution is, in any one of the above-mentioned
constitutions 1 to 4, characterized in that the seal portion is made of a material
having oxygen permeability of 2.0×10
-9 (cm
3·cm/sec·cm
2·cmHg) or less.
[0033] According to the above-mentioned constitution 5, the oxygen permeability of the seal
portion is set to a sufficiently small value of 2.0×10
-9 or less. Accordingly, it is possible to effectively prevent the intrusion of oxygen
into the inside of the tube without excessively increasing a thickness of the seal
portion.
Constitution 6
[0034] The heating device having this constitution is, in any one of the above-mentioned
constitutions 1 to 5, characterized in that a front end portion of the heating resistor
is joined to a front end portion of the tube, and
the front end portion of the tube does not contain W, but contains Cr whose content
is equal to or more than a content of Cr in the metal material.
[0035] The metal material used for forming the heating resistor may contain Cr or may not
contain Cr.
[0036] There has been known a glow
plug where a front end portion of a heating resistor is joined to a front end portion
of a tube. Here, as a technique for joining the heating resistor to the tube, there
has been known a technique in which the heating resistor is inserted into the tube
with the front end portion in an open state, and the front end portion of the tube
and the front end portion of the heating resistor are welded to each other while closing
the front end portion of the tube by arc welding or the like. When the heating resistor
which contains W as a main component is joined to the front end portion of the tube
using this technique, there exists a possibility that the front end portion of the
tube may contain W. When the front end portion (particularly outer surface) of the
tube contains W, W is rapidly oxidized so that there exists a possibility that the
tube is broken.
[0037] In this respect, according to the above-mentioned constitution 6, the front end portion
of the tube is formed such that the front end portion does not contain W, but contains
Cr whose content is equal to or more than the content of Cr in the heating resistor
(the heating resistor may not contain Cr). Accordingly, the occurrence of the above-mentioned
drawback attributed to the containing of W can be prevented, and an oxide film made
of Cr
2O
3 can be more surely formed on a surface of the front end portion of the tube due to
contained Cr. As a result, it is possible to realize the sufficiently excellent durability
at the front end portion of the tube thus preventing breaking of the tube more reliably.
[0038] In realizing the above-mentioned constitution 6 while joining the front end portion
of the tube and the front end portion of the heating resistor by the above-mentioned
technique, it is possible to name a technique where, for example, a metal piece which
contains Cr while not containing W is welded to the front end portion of the heating
resistor in advance, and the metal piece and the front end portion of the tube are
welded to each other.
Constitution 7
[0039] A glow plug having this constitution includes:
a cylindrical tube with a closed front end portion;
a heating resistor which is inserted into the inside of the tube; and
a seal portion which is formed on a rear-end-side opening of the tube and seals the
inside of the tube, wherein
the heating resistor is made of a metal material containing W or Mo as a main component,
and
the tube is made of an alloy containing 0.5 mass% or more and 5.0 mass% or less of
Al and 20 mass% or more and 40 mass% or less of Cr.
[0040] According to the above-mentioned constitution 7, basically, the manner of operation
and advantageous effects substantially equal to the manner of operation and the advantageous
effects of the above-mentioned constitution 1 can be acquired. That is, by allowing
the tube to contain a predetermined quantity or more of Al or Cr, oxidation of the
heating resistor made of W, Mo or the like can be effectively prevented whereby the
heating resistor can sufficiently exhibit excellent heat resistance which W or Mo
possesses, and the tube can maintain excellent oxidation resistance over a long period.
As a result, durability of both the heating resistor and the tube can be remarkably
enhanced whereby the heat generation of the glow plug at a higher temperature can
be realized over a long period.
Constitution 8
[0041] The glow plug having this constitution is, in the above-mentioned constitution 7,
characterized in that an average value of normal-temperature resistance at a portion
of the heating resistor between a front end of the heating resistor and a position
6 mm away from the front end toward a rear end of the heating resistor along a center
axis of the tube is set larger than an average value of the normal-temperature resistance
of the whole heating resistor.
[0042] According to the above-mentioned constitution 8, basically, the manner of operation
and advantageous effects substantially equal to the manner of operation and advantageous
effects of the above-mentioned constitution 2 can be acquired.
Constitution 9
[0043] The glow plug having this constitution is, in the above-mentioned constitution 7
or 8, characterized in that the heating resistor is formed into a coil shape, a wire
diameter of the heating resistor is 0.2 mm or more, and
an average pitch of a portion of the heating resistor between the front end of the
heating resistor and the position 6 mm away from the front end toward the rear end
of the heating resistor along the center axis of the tube is set smaller than an average
pitch of a portion of the heating resistor positioned on a more rear end side than
the position 6 mm away from the front end toward the rear end of the heating resistor
along the center axis of the tube by 0.9 mm or more.
[0044] According to the above-mentioned constitution 9, basically, the manner of operation
and advantageous effects substantially equal to the manner of operation and advantageous
effects of the above-mentioned constitution 3 can be acquired.
Constitution 10
[0045] The glow plug having this constitution is, in any one of the above-mentioned constitutions
7 to 9, characterized in that the glow plug includes insulation powder which is filled
in the tube and around the periphery of the heating resistor, and
the insulation powder is powder which contains MgO as a main component.
[0046] According to the above-mentioned constitution 10, basically, the manner of operation
and advantageous effects substantially equal to the manner of operation and the advantageous
effects of the above-mentioned constitution 4 can be acquired.
Constitution 11
[0047] The glow plug having this constitution is, in any one of the above-mentioned constitutions
7 to 10, characterized in that the seal portion is made of a material having oxygen
permeability of 2.0×10
-9 (cm
3·cm/sec·cm
2·cmHg) or less.
[0048] According to the above-mentioned constitution 11, basically, the manner of operation
and advantageous effects substantially equal to the manner of operation and the advantageous
effects of the above-mentioned constitution 5 can be acquired.
Constitution 12
[0049] The glow plug having this constitution is, in any one of the above-mentioned constitutions
7 to 11, characterized in that a front end portion of the heating resistor is joined
to a front end portion of the tube, and
the front end portion of the tube does not contain W, but contains Cr whose content
is equal to or more than a content of Cr in the metal material.
[0050] According to the above-mentioned constitution 12, basically, the manner of operation
and advantageous effects substantially equal to the manner of operation and the advantageous
effects of the above-mentioned constitution 6 can be acquired.
Constitution 13
[0051] A method of manufacturing a glow plug according to this constitution, which includes:
a cylindrical tube with a closed front end portion; a heating resistor which is inserted
into the inside of the tube; and a seal portion which is formed on a rear-end-side
opening of the tube and seals the inside of the tube, the method of manufacturing
a glow plug including the steps of:
arranging the heating resistor made of a metal material containing W or Mo as a main
component in the tube which is made of an alloy containing 0.5 mass% or more and 5.0
mass% or less of Al and 20 mass% or more and 40 mass% or less of Cr;
sealing the inside of the tube by forming the seal portion on the rear-end-side opening
of the tube; and
heating an outer surface of the tube after the sealing step.
[0052] According to the above-mentioned constitution 13, the outer surface of the tube is
heated in the heating step after the sealing step and hence, it is possible to allow
Al or Cr in the inside of the tube to positively react with oxygen present inside
the tube prior to the material of the heating resistor. As a result, an oxygen partial
pressure inside the tube can be further lowered while suppressing the oxidation of
the heating resistor thus further enhancing durability of the heating resistor.
[0053] Here, when a heating temperature of the outer surface of the tube is excessively
low or when a heating time is excessively short, there exists a possibility that oxidation
of Al or Cr in the tube is not sufficiently promoted. Further, when the heating temperature
is excessively high or when the heating time is excessively long, there also exists
a possibility that the seal portion is broken. Accordingly, to prevent the breaking
of the seal portion while promoting the oxidation of Al or Cr more surely, it is preferable
to set the heating temperature to 700°C or more and 1300°C or less and the heating
time to 1 second or more and 60 seconds or less. It is more preferable to set the
heating temperature to 800°C or more and 1300°C or less and the heating time to 3
seconds or more and 30 seconds or less.
BRIEF DESCRIPTION OF THE DRAWINGS
[0054]
Fig. 1 is a block diagram showing the schematic constitution of a heating device;
Fig. 2(a) is a front view with a part broken away of a glow plug, and Fig. 2(b) is
a partially enlarged cross-sectional view of a front end portion of the glow plug;
Fig. 3 is a partially enlarged cross-sectional view for explaining a method of joining
a front end portion of a tube and a front end portion of a heating coil;
Fig. 4 is a partially enlarged cross-sectional view showing the constitution of a
heating coil and the like according to a second embodiment;
Fig. 5 is an enlarged view with a part broken away showing a glow plug and the like
assembled in an internal combustion engine;
Fig. 6 is a partially enlarged cross-sectional view showing the constitution of a
heating coil and the like according to a third embodiment;
Fig. 7(a) and Fig. 7(b) are partially enlarged cross-sectional views showing the constitution
of samples; and
Fig. 8(a) and Fig. 8(b) are partially enlarged cross-sectional views showing the constitution
of samples.
MODE FOR CARRYING OUT THE INVENTION
[0055] Hereinafter, embodiments of the present invention are explained in conjunction with
drawings.
[First embodiment]
[0056] Fig. 1 is a block diagram showing the schematic constitution of a heating device
21 according to the present invention.
[0057] The heating device 21 includes a glow plug 1 and a glow control unit (GCU) 31 which
constitutes an energization control device for controlling the electric power to the
glow plug 1. Although only one glow plug 1 is shown in Fig. 1, a plurality of cylinders
are provided to an actual engine, and the glow plug 1 and a switch 33 described later
are provided corresponding to each cylinder.
[0058] The GCU 31 is operated with electric power supplied from a battery VA, and includes
a microcomputer 32 having a CPU, a ROM, a RAM and the like, and the switch 33 which
turns on or off the electric power supply to the glow plug 1 from the battery VA.
[0059] The energization control executed by the GCU 31 for controlling the electric power
to the glow plug 1 is performed in accordance with a PWM control, and the switch 33
is configured to turn on or off the electric power to the glow plug 1 in accordance
with an instruction from the microcomputer 32.
[0060] Further, in this embodiment, to measure a resistance value of the glow plug 1, the
switch 33 is configured to operate an FET (field effect transistor) having a current
detection function via an NPN-type transistor or the like. In addition to such a constitution,
the microcomputer 32 is connected to a power supply terminal of the glow plug 1 via
a voltage dividing resistor (not shown in the drawing) so that a voltage obtained
by dividing a voltage applied to the glow plug 1 (voltage outputted from the GCU 31)
is inputted to the microcomputer 32. The microcomputer 32 can calculate a voltage
applied to the glow plug 1 based on a voltage inputted to the microcomputer 32. Further,
the microcomputer 32 obtains a resistance value of the glow plug 1 based on the applied
voltage and an electric current which is measured by the switch 33 and flows in the
glow plug 1.
[0061] Further, the microcomputer 32 according to this embodiment is configured to perform
pre-glow energization for rapidly elevating a temperature of the glow plug 1 when
an engine key is turned to an ON position and after-glow energization for maintaining
a temperature of the glow plug 1 at a predetermined temperature for a predetermined
time after the pre-glow power supply.
[0062] In this embodiment, in the pre-glow energization, electric power is supplied to the
glow plug 1 such that a temperature of a surface of a tube 7 of the glow plug 1 (described
later) is elevated to 1000°C from a normal temperature within 3 seconds thus rapidly
elevating a temperature of the glow plug 1 to a predetermined target temperature.
[0063] In this pre-glow energization, by making a curve showing the relationship between
electric power supplied to the glow plug 1 and a lapsed time agree with a preset reference
curve, the temperature of the glow plug 1 is rapidly elevated to the target temperature
without depending on properties of the glow plug 1. To be more specific, using a relational
formula or a table indicative of the above-mentioned preset reference curve, electric
power to be supplied at respective points of time corresponding to times lapsed from
starting the electric power is obtained. A voltage to be applied to the glow plug
1 is obtained based on the relationship between an electric current which flows in
the glow plug 1 and a value of electric power to be supplied at such points of time,
and the voltage to be applied to the glow plug 1 is controlled in accordance with
a PWM control. Accordingly, the electric power is supplied so as to draw the same
curve as the reference curve, and the glow plug 1 generates heat corresponding to
a cumulative amount of electric power supplied until respective points of time in
the course of temperature elevation. Accordingly, when the supply of electric power
along the above-mentioned reference curve is completed, the glow plug 1 reaches the
target temperature at a time set in accordance with the reference curve.
[0064] Further, in the after-glow energization, the supply of electric power to the glow
plug 1 is adjusted such that a surface temperature of the tube 7 becomes an extremely
high temperature of 1150°C or more during a relatively long period (for example, approximately
180 seconds).
[0065] In this after-glow energization, the power supply to the glow plug 1 is controlled
such that a resistance value of the glow plug 1 agrees with a resistance value (target
resistance value) when the temperature of the glow plug 1 is set to a target temperature.
To be more specific, an effective voltage to be applied to the glow plug 1 is calculated
based on the difference between a current resistance value of the glow plug 1 and
a target resistance value of the glow plug 1 in accordance with a PI control, for
example, and a duty ratio is set based on the effective voltage. Since a temperature
of the surface of the tube 7 is maintained at a high temperature of 1150°C or more,
the reduction of emission or the like can be realized at the time of after-glow energization.
[0066] Next, the constitution of the glow plug 1 to which the energization control is applied
by the above-mentioned GCU 31 is explained in detail. As shown in Fig. 2 (a), 2(b),
the glow plug 1 includes a main fitting 2 having a cylindrical shape and a sheath
heater 3 mounted on the main fitting 2.
[0067] The main fitting 2 has an axial hole 4 which penetrates the main fitting 2 in an
axis CL1 direction and, on an outer peripheral surface of the main fitting 2, a threaded
portion 5 for mounting the glow plug 1 on a diesel engine or the like, and a tool
engaging portion 6 having a hexagonal cross section for engagement with a tool such
as a torque wrench are formed.
[0068] The sheath heater 3 is formed as an integral body constituted of the tube 7 and an
intermediate shaft 8 arranged in the axis CL1 direction.
[0069] The tube 7 is a cylindrical tube which is made of a metal material which contains
iron (Fe) or nickel (Ni) as a main component and has a closed front end portion. Further,
in the inside of the tube 7, a heating coil 9 made of a predetermined metal material
(corresponding to "heating resistor" of the present invention) is arranged. A front
end portion of the heating coil 9 is joined to the front end portion of the tube 7
(the metal material for forming the tube 7 and the metal material for forming the
heating coil 9 are described in detail later).
[0070] The tube 7 is configured such that the front end portion of the tube 7 is closed
when the heating coil 9 is joined to the tube 7, while the front end portion of the
tube 7 is in an opened state before the heating coil 9 is joined to the tube 7. In
this embodiment, a metal piece MP (see Fig. 3) described later is welded to the front
end portion of the heating coil 9 in advance and, thereafter, the metal piece MP is
arranged at a front end opening of the tube 7, and the metal piece MP or the like
is melted by arc welding or the like and hence, the front end portion of the tube
7 is closed, and also the front end portion of the heating coil 9 is joined to the
front end portion of the tube 7. Accordingly, a melted portion 7M is formed on the
front end portion of the tube 7.
[0071] In this embodiment, the metal piece MP is made of the same metal material as the
metal material for forming the tube 7. Further, although the tube 7 into which the
heating coil 9 is inserted corresponds to "heating portion" according to the present
invention, a portion of a surface of the tube 7 which acquires the highest temperature
due to the supply of electric power (in this embodiment, a portion of the tube 7 positioned
2 mm away from a front end toward a rear end side of the tube 7) may correspond to
"heating portion".
[0072] Further, insulation powder 10 is filled in the tube 7 and around the heating coil
9. Accordingly, although the heating coil 9 is made electrically conductive with the
tube 7 at the front end thereof, an outer peripheral surface of the heating coil 9
and an inner peripheral surface of the tube 7 are brought into an insulation state
due to the presence of the insulation powder 10 therebetween.
[0073] Further, a rear end of the tube 7 is sealed by an annular seal portion 11 between
the tube 7 and the intermediate shaft 8 thus bringing the inside of the tube 7 into
a sealed state.
[0074] A large-diameter portion 4a is formed on a front end portion of the shaft hole 4,
and a small-diameter portion 4b is formed on a rear end side of the large-diameter
portion 4a. By press-fitting the tube 7 into the small-diameter portion 4b of the
shaft hole 4, the tube 7 is held in a state where the tube 7 projects from a front
end portion of the main fitting 2.
[0075] A front end of the intermediate shaft 8 is inserted into the tube 7 and is electrically
connected with a rear end of the heating coil 9. The intermediate shaft 8 is also
inserted into the shaft hole 4 formed in the main fitting 2. A rear end of the intermediate
shaft 8 projects from a rear end of the main fitting 2, and an O ring 12 made of rubber
or the like, an insulation bushing 13 made of a resin or the like, a pusher ring 14
for preventing the removal of the insulation bushing 13, and a nut 15 for connecting
a power supply cable are fitted on the intermediate shaft 8 in this order at the rear
end portion of the main fitting 2.
[0076] Next, composition of the metal material for forming the heating coil 9, the composition
of the metal material for forming the tube 7 and the like are explained.
[0077] In this embodiment, the heating coil 9 is made of a metal material which contains
tungsten (W) or molybdenum (Mo) as a main component [in this embodiment, pure metal
of W or Mo (pure metal may contain unavoidable impurities)].
[0078] Further, the tube 7 is made of a metal material which contains Ni or Fe as a main
component, and contains 0.5 mass% or more and 5.0 mass% or less of aluminum (Al) and
20 mass% or more and 40 mass% or less of chromium (Cr). In this embodiment, a Cr content
in the tube 7 is set larger than a Cr content in the heating coil 9, and the tube
7 does not contain W.
[0079] The insulation powder 10 is formed of powder which contains magnesium oxide (MgO)
as a main component.
[0080] Further, the seal portion 11 is made of an elastic material having oxygen permeability
of 2.0×10
-9 (cm
3·cm/sec·cm
2·cmHg) or less [for example, ethylene propylene rubber (EPDM rubber), fluoro-rubber
or the like]. A thickness of the seal portion 11 along the axis CL1 direction is set
relatively small (for example, 10 mm or less).
[0081] Further, the melted portion 7M (the front end portion of the tube 7) is formed by
melting of the tube 7 and the metal piece MP which are made of the same material and
hence, the melted portion 7M does not contain W at least in an outer surface thereof.
Further, the melting portion 7M contains Cr whose content is equal to or more than
the content of Cr in a metal material which forms the heating coil 9 (the heating
coil 9 according to this embodiment does not contain Cr).
[0082] Next, a manufacturing method of the above-mentioned glow plug 1 is explained. Parts
which are not specified are formed using a conventionally known method.
[0083] Firstly, a resistance heating wire which contains W or Mo as a main component is
formed into a coil shape thus manufacturing the heating coil 9. The cylindrical tube
7 whose front end is not closed is manufactured using a metal material which contains
Ni or Fe as a main component, and contains 0.5 mass% to 5.0 mass% of Al and 20 mass%
to 40 mass% of Cr.
[0084] Next, as shown in Fig. 3, the metal piece MP made of the same metal material as the
metal material for forming the tube 7 is joined to the front end portion of the heating
coil 9 and, thereafter, in an arrangement step, a front end of the intermediate shaft
8 and the heating coil 9 which is integrally formed with the intermediate shaft 8
are arranged in the inside of the cylindrical tube 7. Then, the metal piece MP is
arranged at the front end opening of the tube 7 and, thereafter, the metal piece MP
and the tube 7 are melted by arc welding or the like thus closing the front end portion
of the tube 7 and also joining the front end portion of the tube 7 and the front end
portion of the heating coil 9 to each other.
[0085] Thereafter, the insulation powder 10 is filled in the inside of the tube 7, and
the seal portion 11 is arranged between the rear end opening of the tube 7 and the
intermediate shaft 8 in a sealing step thus sealing the inside of the tube 7. Accordingly,
the tube 7 is integrally formed with the intermediate shaft 8 thus completing the
sheath heater 3. After sealing the inside of the tube 7, swaging may be applied to
the front end portion of the tube 7 thus narrowing a diameter of the front end portion
of the tube 7. Packing density of the insulation powder 10 can be further increased
by applying swaging.
[0086] Finally, the sheath heater 3 formed in the above-mentioned manner is fixed to the
shaft hole 4 formed in the main fitting 2 by press-fitting, and the above-mentioned
O ring 12, insulation bushing 13 and the like are fitted on the intermediate shaft
8 at the rear end portion of the main fitting 2. Accordingly, the above-mentioned
glow plug 1 is acquired.
[0087] In the acquired glow plug 1, preheating for heating the outer surface of the tube
7 may be performed. In preheating, the glow plug 1 is heated by an electric furnace
or a high-frequency heating device for 1 second to 30 seconds until a temperature
of the outer surface of a portion of the tube 7 where the heating coil 9 is positioned
(for example, a range from the front end of the tube 7 to a position 1 mm away from
the front end of the tube 7 toward a rear end side in the axis CL1 direction) becomes
800°C to 1300°C.
[0088] As has been described in detail heretofore, according to this embodiment, the heating
coil 9 is made of the metal material which contains W or Mo having a high melting
point as the main component and hence, the heating coil 9 having excellent heat resistance
can be realized.
[0089] On the other hand, there exists a possibility that oxidation resistance is lowered
due to the use of W or Mo. According to this embodiment, however, the tube 7 contains
0.5 mass% or more of Al and 20 mass% or more of Cr. Accordingly, at the time of heat
generation, Al or Cr which is more likely to be oxidized than W or Mo functions as
an oxygen getter element and hence, an oxide film made of Al
2O
3 or Cr
2O
3 is formed on an inner peripheral surface of the tube 7. Since the inside of the tube
7 is in a sealed state, an oxygen partial pressure inside the tube 7 can be effectively
lowered. As a result, the oxidation of the heating coil 9 containing W or Mo as a
main component can be more surely prevented.
[0090] Further, by allowing the tube 7 to contain a predetermined quantity or more of Al
or Cr, an oxide film made of Al
2O
3 or Cr
2O
3 can be formed on an outer surface of the tube 7 over a broad range. The intrusion
of oxygen into the inside of the tube 7 can be more surely suppressed due to the oxide
film and hence, the oxidation resistance of the tube 7 can be enhanced. Further, the
content of Al or Cr is set sufficiently large and hence, even when peeling-off or
cracks occur in the oxide film due to thermal stress caused by the repetition of a
thermal cycle, the oxide film can be formed again more surely over a longer period.
[0091] As described above, according to this embodiment, by allowing the tube 7 to contain
a predetermined quantity or more of Al or Cr, the oxidation of the heating coil 9
made of W, Mo or the like can be effectively prevented and hence, the heating coil
9 can sufficiently exhibit the excellent heat resistance which W or Mo possesses,
and the tube 7 also can maintain the excellent oxidation resistance for a long period.
As a result, durability of both the heating coil 9 and the tube 7 can be remarkably
enhanced whereby the glow plug 1 can realize the heat generation at a higher temperature
over a long period.
[0092] Further, the GCU 31 supplies electric power to the heating coil 9 such that the temperature
of the surface (heating part) of the tube 7 is elevated from the normal temperature
to 1000°C within 3 seconds and hence, thermal stress applied to the tube 7 can be
increased. Accordingly, an oxide film made of Al
2O
3 or Cr
2O
3 formed on the inner peripheral surface of the tube 7 can be easily broken and hence,
a non-oxidized metal surface is likely to be exposed from the oxide film on the inner
peripheral surface of the tube 7. Due to the new oxidation of Al or Cr contained in
the metal surface, an oxygen partial pressure inside the tube 7 can be further reduced
thus preventing the oxidation of the heating coil 9 made of W or the like extremely
effectively.
[0093] Particularly, in this embodiment, in the after-glow energization, a surface temperature
(heating part) of the tube 7 becomes an extremely high temperature of 1150°C or more,
and this condition makes the heat generation over a long period difficult. However,
due to a synergistic action of the above-mentioned manner of operations and advantageous
effects, the heat generation even at such a high temperature can be realized over
a long period. In other words, the present invention particularly exhibits the significance
when the temperature of the surface (heating part) of the tube 7 becomes an extremely
high temperature of 1150°C or more in the after-glow energization which is performed
for a relatively long period.
[0094] Further, since MgO which exhibits excellent thermal conductivity is used as the
insulation powder 10, the thermal conductivity from the heating coil 9 to the tube
7 can be enhanced. As a result, it is possible to make the glow plug 1 (tube 7) generate
heat at a higher temperature without excessively elevating a temperature of the heating
coil 9.
[0095] Further, since the temperature of the tube 7 can be set higher, thermal stress applied
to the tube 7 can be further increased whereby an oxide film made of Al
2O
3 or Cr
2O
3 formed on the inner peripheral surface of the tube 7 can be more easily broken. Accordingly,
an unoxidized Al or Cr is more likely to be exposed on the inner peripheral surface
of the tube 7 and hence, an oxygen partial pressure inside the tube 7 can be lowered
more effectively.
[0096] Further, while MgO is likely to form a composite oxide between MgO and Al
2O
3 or Cr
2O
3 formed on the inner peripheral surface of the tube 7, the composite oxide is extremely
coarse compared to an oxide film made of Al
2O
3 or the like. Accordingly, Al or Cr contained in the tube 7 and oxygen inside the
tube 7 are more likely to react with each other and hence, an oxygen partial pressure
inside the tube 7 can be further lowered.
[0097] That is, with the use of the metal material which contains MgO as a main component
as the insulation powder 10, favorable heat conductivity which is property that MgO
possesses and property of MgO that Mgo is likely to form a composite oxide with Al
2O
3 or the like synergistically act together and hence, an oxygen partial pressure inside
the tube 7 can be reduced extremely effectively. As a result, durability of the heating
coil 9 can be further enhanced and hence, the glow plug 1 can generate heat at a higher
temperature over a further prolonged period with respect to the glow plug 1.
[0098] Also the oxygen permeability of the material which forms the seal portion 11 is set
to a sufficiently small value of 2.0×10
-9 or less and hence, it is possible to effectively prevent the intrusion of oxygen
into the inside of the tube 7 without excessively increasing a thickness of the seal
portion 11.
[0099] The melted portion 7M (the front end portion of the tube 7) is formed such that the
melted portion 7M does not contain W at least on the outer surface thereof, and contains
Cr whose content is equal to or more than a content of Cr in the metal material which
forms the heating coil 9. Accordingly, the oxidation of the melted portion 7M attributed
to the containing of W can be prevented, and an oxide film made of Cr
2O
3 can be more surely formed on the surface of the front end portion of the tube 7.
As a result, it is possible to realize the sufficiently excellent durability at the
front end portion of the tube 7 thus preventing breaking of the tube 7 more reliably.
[0100] Further, as the material for forming the heating coil 9, in general, there has been
known a material which contains Cr. In this embodiment, the heating coil 9 is made
of pure metal of W or Mo. Accordingly, it is possible to prevent the occurrence of
a state where an oxide film of Cr is formed on a surface of the heating coil 9 so
that contents of the heating coil 9 change resulting in lowering of a resistance value
of the heating coil 9. As a result, durability of the heating coil 9 can be further
enhanced.
[0101] By performing the preheating at the time of manufacturing the glow plug, it is possible
to allow Al or Cr in the inside of the tube 7 to positively react with oxygen present
inside the tube 7 prior to the material of the heating coil 9. As a result, an oxygen
partial pressure inside the tube 7 can be further lowered while suppressing the oxidation
of the heating coil 9 thus further enhancing durability of the heating coil 9.
[Second embodiment]
[0102] Next, the second embodiment is explained by focusing on the difference between the
above-mentioned first embodiment and the second embodiment. In the second embodiment,
as shown in Fig. 4, a wire diameter of a front-end-side coil 49A of a heating coil
49 which is positioned between a front end and a position 6 mm away from the front
end toward a rear end of the heating coil 49 along a center axis CL2 of a tube 47
(agreeing with the axis CL1 in this embodiment) is set smaller than a wire diameter
of a rear-end-side coil 49B of the heating coil 49 positioned at a more rear end side
than the front-end-side coil 49A. To be more specific, a front end portion of the
front-end-side coil 49A is formed such that the wire diameter of the front end portion
of the front-end-side coil 49A is gradually decreased toward a front end side.
[0103] By setting the wire diameter of the front-end-side coil 49A smaller than the wire
diameter of the rear-end-side coil 49B, an average value of normal-temperature resistance
of the front-end-side coil 49A per unit length along the center axis CL2 of the tube
47 is set larger than an average value of normal-temperature resistance of the whole
heating coil 49 per unit length along the center axis CL2. In this manner, by setting
the average value of normal-temperature resistance of the front-end-side coil 49A
larger than the average value of normal-temperature resistance of the whole heating
coil 49, at the time of supplying electric power to the glow plug 1 (heating coil
49) from the battery VA, it is possible to positively elevate a temperature of a portion
X of the tube 47 approximately 2 mm away from a front end of the tube 47 toward a
rear end of the tube 47 and a temperature of an area in the vicinity of the portion
X and hence, the portion X and the area in the vicinity of the portion X can acquire
the highest temperature.
[0104] In a state where the glow plug 1 is mounted on an internal combustion engine EN,
as shown in Fig. 5, generally, a portion 47E of the tube 47 positioned between the
front end of the tube 47 and a position approximately 4 mm away from the front portion
toward the rear end of the tube 47 (hereinafter referred to as "exposed portion")
is arranged in the inside of a combustion chamber ER. Accordingly, it is safe to say
that the portion X is positioned at the approximately center of the exposed portion
47E.
[0105] As has been described in detail heretofore, according to this second embodiment,
a temperature of the exposed portion 47E of the tube 47 which is more likely to be
elevated and is likely to be subjected to a steep temperature change can be positively
elevated and hence, a temperature of the tube 47 can be elevated higher thus generating
a steep temperature change in the tube 47. Accordingly, thermal stress which occurs
in the tube 47 can be further increased and hence, it is possible to make an oxide
film formed on an inner peripheral surface of the tube 47 more easily broken. As a
result, an oxidation prevention effect of the heating coil 49 can be further enhanced.
[Third embodiment]
[0106] Next, the third embodiment is explained by focusing on the difference between the
above-mentioned second embodiment and the third embodiment. In the second embodiment,
the wire diameter of the front-end-side coil 49A is set smaller than the wire diameter
of the rear-end-side coil 49B for setting the average value of normal-temperature
resistance of the front-end-side coil 49A larger than the average value of normal-temperature
resistance of the whole heating coil 49. On the other hand, in this third embodiment,
as shown in Fig. 6 (heating coil being schematically shown in Fig. 6 to Fig. 8), an
average pitch of a front-end-side coil 59A is set smaller than an average pitch of
a rear-end-side coil 59B by 0.9 mm or more so as to make an average value of normal-temperature
resistance of the front-end-side coil 59A sufficiently larger than an average value
of normal-temperature resistance of a whole heating coil 59 (in the third embodiment,
the average value of normal-temperature resistance of the front-end-side coil 59A
being set twice or more larger than the average value of normal-temperature resistance
of the whole heating coil 59) . Further, in this third embodiment, a wire diameter
of the heating coil 59 is set to 0.2 mm or more, and the heating coil 59 is configured
to have an approximately fixed wire diameter from a front end to a rear end thereof.
[0107] As described above, according to the third embodiment, a temperature of the exposed
portion of the tube 57 can be positively elevated and hence, the further steep temperature
elevation of the tube 57 or the like can be realized. Accordingly, it is possible
to make an oxide film formed on an inner peripheral surface of the tube 57 more easily
broken thus further enhancing an oxidation prevention effect of the heating coil 59.
[0108] Further, in the third embodiment, the front-end-side coil 59A can secure a sufficient
diameter and hence, the heating coil 59 can sufficiently maintain a mechanical strength.
[0109] Still further, it is unnecessary to excessively narrow a diameter of the front-end-side
coil 59A and hence, the heating coil 59 can be manufactured relatively easily thus
surely preventing the lowering of productivity.
[0110] Next, to confirm the manner of operation and advantageous effects brought about by
the above-mentioned embodiment, samples of glow plugs are prepared, wherein each heating
coil is made of Fe-26Cr-7.5Al (PYROMAX), W or Mo and each tube is made of a metal
material which contains Fe or Ni as a main component and varies in a content of Al
or Cr, and a durability evaluation test is carried out with respect to the respective
samples. To summarize the durability evaluation test, it goes as follows. That is,
with respect to each sample, the number of cycles until the breaking of the heating
coil occurs (breaking cycle) is measured by setting the following series of operations
as 1 cycle. Electric power is supplied to each sample for 60 seconds such that a temperature
of a surface (heating part) of the tube is elevated from a normal temperature to 1000°C
within 2 seconds or within 10 seconds, and the tube surface temperature is saturated
at 1150°C or 1200°C and, thereafter, the tube surface is cooled by air for 180 seconds.
Here, the samples whose breaking cycle becomes 10000 cycles or more when the tube
surface temperature is saturated at 1150°C are considered to have the excellent durability
and the evaluation "good" is given to the samples, while the samples whose breaking
cycle becomes less than 10000 cycles when the tube surface temperature is saturated
at 1150°C are considered to have the inferior durability and the evaluation "bad"
is given to the samples. Further, when the tube surface temperature is saturated at
1200°C (that is, under a condition where the heating coil is more liable to be broken),
the samples whose breaking cycle becomes 5000 cycles or more are given the evaluation
"good", while the samples whose breaking cycle becomes less than 5000 cycles are given
the evaluation "bad". With respect to the samples whose tube is broken are given "*"
in a determination column of following Tables 1 to 3.
[0111] Table 1 shows a result of the test with respect to samples where the heating coil
is made of Fe-26Cr-7. 5 Al. Table 2 shows a result of the test with respect to the
samples where the heating coil is made of W. Table 3 shows a result of the test with
respect to the samples where the heating coil is made of Mo. To elevate the tube surface
temperature from a normal temperature to 1000°C within 2 seconds, electric power is
supplied to the sample at 11 V for 2 seconds. To elevate the tube surface temperature
from a normal temperature to 1000°C within 10 seconds, electric power is supplied
to the sample at 4.5 V for 5 seconds and, thereafter, electric power is supplied to
the sample at 7.5 V for 5 seconds. Further, to saturate the tube surface temperature
at 1150°C, electric power is supplied to the sample at 6.5 V for 60 seconds, while
to saturate the tube surface temperature at 1200°C, electric power is supplied to
the sample at 7.5 V for 60 seconds. In all samples, the seal portion is made of fluoro-rubber,
and the tube composition is specified by quantitative analysis in accordance with
EPMA. With respect to the samples where the heating coil is made of Fe-26Cr-7.5 Al,
only a test where the tube surface, temperature is elevated from a normal temperature
to 1000°C within 2 seconds is carried out.
[0112]
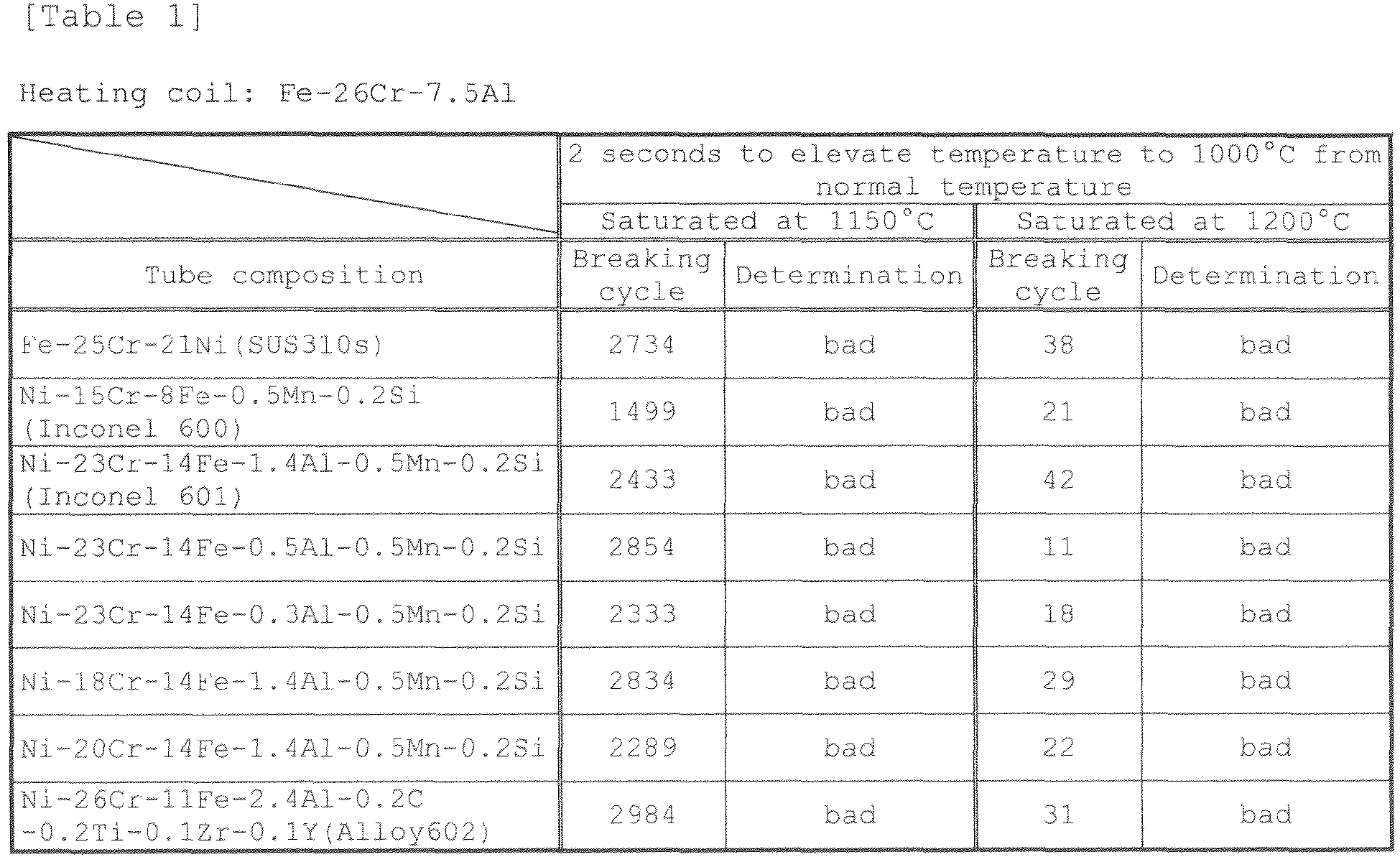
[0113]
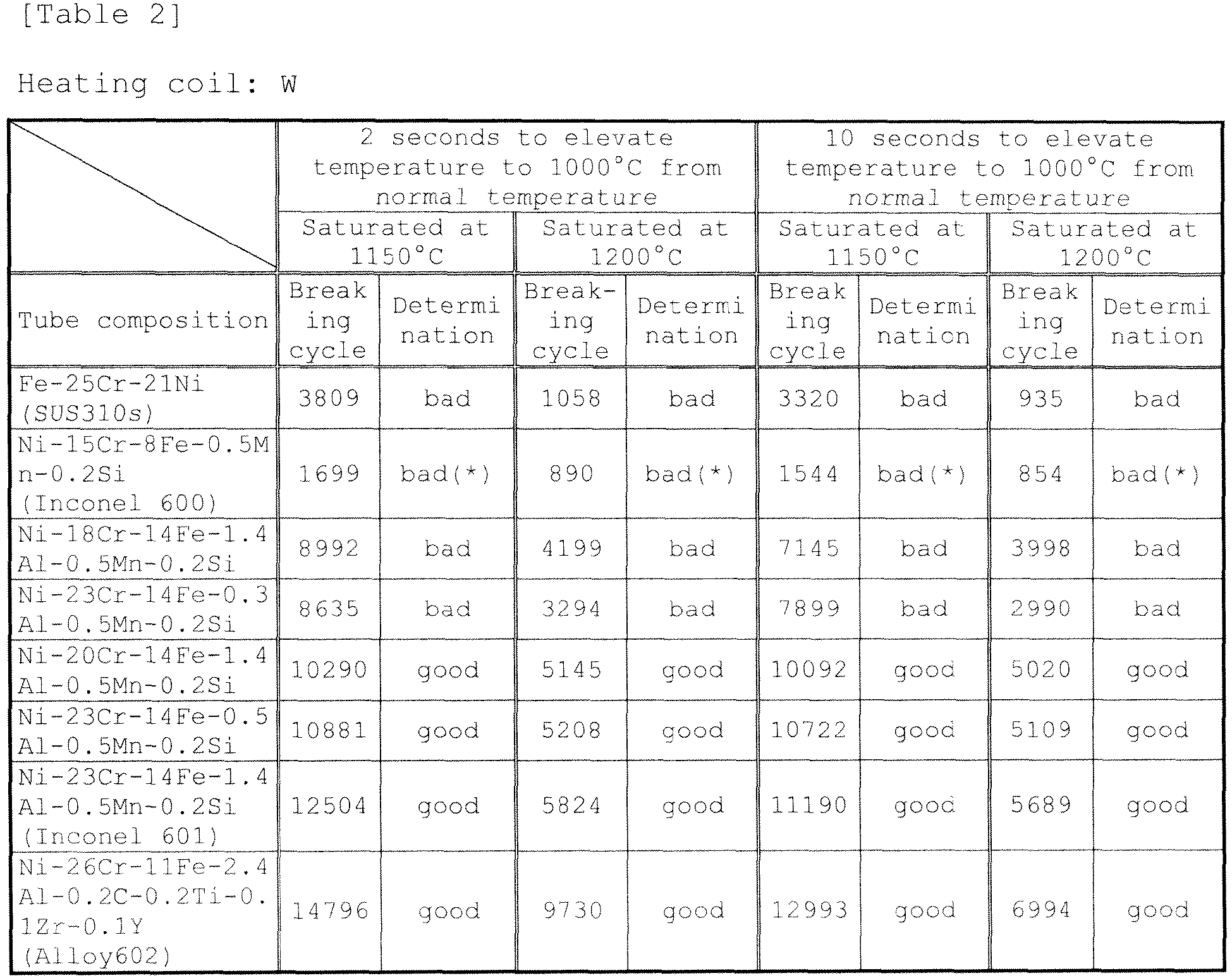
[0114]

[0115] As shown in Table 1, it is found that, with respect to the samples where the heating
coil is made of Fe-26Cr-7.5Al (PYROMAX), the breaking occurs in the heating coil at
an early stage irrespective of the composition of the tube and, particularly, the
heating coil is melted when a temperature of the heating coil is elevated to 1200°C.
It is thought that a melting point of the metal material which forms the heating coil
is relatively low, that is, approximately 1500°C and hence, when the tube surface
temperature is elevated to a high temperature of 1150°C or more, the heating coil
is heated to a temperature around a melting point of the heating coil per se.
[0116] Further, as shown in Table 2 and Table 3, it is also found that, even in a case where
the heating coil is made of W or Mo having a high melting point, when a Al content
or a Cr content in the tube is relatively small, the durability of the heating coil
becomes insufficient. It is thought that this result is brought about by a phenomenon
that the oxidative exhaustion of the heating coil rapidly progresses under a high
temperature due to the property of W and Mo that W and Mo are relatively easily oxidized.
[0117] Further, it is confirmed that, with respect to the sample where the tube is made
of Ni-15Cr-8Fe-0.5Mn-0.2Si (Inconel (registered trademark) 600), the breaking occurs
in the tube. It is thought that the tube does not contain Al and a Cr content in the
tube is relatively small and hence, an oxide film which is formed by oxidation of
Al or Cr is not sufficiently formed on the tube surface whereby the oxidation resistance
of the tube becomes insufficient.
[0118] To the contrary, it is found that the sample where the heating coil is made of W
or Mo, an Al content in the tube is set to 0.5 mass% or more, and a Cr content in
the tube is set to 20 mass% or more exhibits the excellent durability. It is thought
that Al and Cr contained in the tube are oxidized prior to W or Mo in the heating
coil and hence, an oxygen partial pressure in the tube can be lowered thus leading
to the suppression of oxidation of the heating coil, and that an oxide film made of
Al or Cr is sufficiently formed on an outer surface of the tube and hence, the tube
can realize the excellent oxidation resistance which enables the tube to withstand
a high temperature of 1150°C or more over a long period.
[0119] Further, it is confirmed that, particularly, the larger an Al content or a Cr content
in the tube, the more excellent durability the tube can realize.
[0120] Based on the above-mentioned results of the test, it is reasonable to say that, to
enhance the durability of both the heating coil and the tube thus allowing the glow
plug to generate heat at a higher temperature over a long period, it is preferable
to form the heating coil using a metal material which contains W or Mo as a main component,
and to set an Al content in the tube to 0.5 mass% or more and a Cr content in the
tube to 20 mass% or more. Further, to realize the further enhancement of the durability,
it is also desirable to further increase the Al content to 1.4 mass% or more or 2.4
mass% or more and the Cr content to 23 mass% or more or 26 mass% or more. However,
when the Al content exceeds 5.0 mass% or the Cr content exceeds 40 mass%, there exists
a possibility that the workability is deteriorated. Accordingly, it is desirable to
set the Al content to 5.0 mass% or less and the Cr content to 40 mass% or less.
[0121] Next, a plurality of samples of glow plugs are prepared, wherein the heating coil
is made of W or Mo and the tube is made of Ni-26Cr-11Fe-2.4Al-0.2C-0.2Ti-0.1Zr-0.1Y
(Alloy 602). Then, with respect to each sample, the breaking cycle until the breaking
of the heating coil occurs is measured by setting the series of following operations
as 1 cycle. Electric power is supplied to each sample such that a temperature of a
tube surface is elevated from a normal temperature to 1000°C while changing a temperature
elevation time with respect to each sample and, after the tube surface temperature
reaches 1200°C, the tube surface temperature is maintained for 60 seconds and, thereafter,
the tube surface is cooled by air for 180 seconds. Table 4 shows a result of the test
of samples where the heating coil is made of W, and Table 5 shows a result of the
test of samples where the heating coil is made of Mo. In all samples, a seal portion
is made of fluoro-rubber.
[0122]
[Table 4]
Heating coil: W |
1000°C arrival time (s) |
Applied voltage |
Breaking cycle |
2 |
11V2s-7.5V60s-off180s |
9730 |
3 |
11V1s-7.5V60s-off180s |
8592 |
5 |
7.5V65s-off180s |
7349 |
10 |
4.5V5s7.5V65s-off180s |
6994 |
30 |
2V10s-3V10s-4.5V5s -7.5V65s-off180s |
7049 |
[0123]
[Table 5]
Heating coil: Mo |
1000°C arrival time (s) |
Applied voltage |
Breaking cycle |
2 |
11V2s-7.5V60s-off180s |
9204 |
3 |
11V1s-7.5V60s-off180s |
8762 |
5 |
7.5V65s-off180s |
7199 |
10 |
4.5V5s7.5V65s-off180s |
7092 |
30 |
2V10s-3V10s-4.5V5s -7.5V65s-off180s |
6888 |
[0124] As shown in Table 4 and Table 5, it is found that when the temperature elevation
time from a normal temperature to 1000°C exceeds 3 seconds, the breaking cycle becomes
around 7000 cycles, while when the temperature elevation time from the normal temperature
to 1000°C is within 3 seconds, the breaking cycle becomes 8500 cycles or more so that
the glow plug can realize the further excellent durability. It is also confirmed that
when the temperature elevation time from the normal temperature to 1000°C is within
2 seconds, the breaking cycle exceeds 9000 cycles so that the further enhancement
of the durability is realized. It is thought that the shorter the temperature elevation
time, the larger thermal stress applied to the tube becomes and hence, an oxide film
formed on an inner wall of the tube is liable to be broken (that is, unoxidized Al
or Cr is likely to be exposed on an inner surface of the tube) whereby the oxidation
between oxygen present inside the tube and Al or Cr is further promoted thus further
lowering an oxygen partial pressure inside the tube.
[0125] Based on the above-mentioned results of the test, it is reasonable to say that, in
the glow plug where the heating coil is made of a metal material which contains W
or Mo as a main component and the tube is made of a metal material which contains
a predetermined quantity or more of Al or Cr for further enhancement of the durability,
it is preferable to supply electric power such that the tube surface temperature is
elevated from a normal temperature to 1000°C within 3 seconds, and it is more preferable
to supply electric power such that the tube surface temperature is elevated from a
normal temperature to 1000°C within 2 seconds.
[0126] Next, samples of the glow plug are prepared, wherein an insulation powder which is
filled in the tube is made of Mgo, aluminum oxide (Al
2O
3), or silicon nitride (Si
3O
4). Then, with respect to each sample, the breaking cycle until the breaking of the
heating coil occurs is measured by setting the series of following operations as 1
cycle. Electric power is supplied to each sample at 7.5V for 65 seconds (a temperature
of a tube surface is elevated from a normal temperature to 1000°C with 5 minutes)
and, thereafter, the tube surface is cooled by air for 180 seconds. Table 6 shows
a result of the test. Here, in all samples, the heating coil is made of W, and the
tube is made of Ni-23Cr-14Fe-1.4Al-0.5Mn-0.2Si [Inconel (registered trademark) 601],
Alloy 602 or SUS310s. Further, the seal portion is made of fluoro-rubber and, after
the sample is prepared, preheating is applied at 800°C for 30 seconds.
[0127]
[Table 6]
Insulation powder |
Tube composition |
Ni-23Cr-14Fe-1.4Al -0.5Mn-0.2Si (Inconel 601) |
Ni-26Cr-11Fe-2.4Al -0.2C-0.2Ti-0.1Zr-0.1Y (Alloy602) |
Fe-25Cr-21Ni (SUS310s) |
MgO |
7177 |
8850 |
994 |
Al2O3 |
5699 |
6166 |
689 |
Si3N4 |
6722 |
6954 |
933 |
Determination |
good |
good |
bad |
[0128] As shown in Table 6, it is confirmed that, with respect to the sample where the tube
is made of Inconel 601 or Alloy 602, all insulation powders exhibit the excellent
durability. Particularly, it is found that the sample where the insulation powder
is made of MgO exhibits more excellent durability than the samples where the insulation
powder is made of Al
2O
3 or Si
3O
4 . It is thought that, while MgO is likely to form a composite oxide with an oxide
of Al or Cr formed on the inner periphery of the tube, the composite oxide is extremely
coarse and hence, Al or Cr contained in the tube and oxygen present inside the tube
are more likely to react with each other whereby an oxygen partial pressure inside
the tube can be further lowered, and since MgO possesses the excellent heat conductivity
compared to Al
2O
3 or the like, a larger thermal stress is applied to the tube and, as a result, an
oxide film formed on the inner periphery of the tube can be more easily broken whereby
the oxidation between oxygen present inside the tube and Al or Cr contained in the
tube is further promoted or the like.
[0129] Based on the above-mentioned results of the test, from a viewpoint of realizing the
further enhancement of the durability, it is reasonable to say that a material which
contains MgO is preferably used as a main component as the insulation powder.
[0130] Next, samples of the glow plug are prepared, wherein the seal portion is made of
EPDM or fluoro-rubber. Then, with respect to each sample, the breaking cycle until
the breaking of the heating coil occurs is measured by setting the series of following
operations as 1 cycle. Electric power is supplied to each sample at 7.5 V for 65 seconds
(a temperature of a tube surface is elevated from a normal temperature to 1000°C within
5 minutes) and, thereafter, the tube surface is cooled by air for 180 seconds. Table
7 shows a result of the test. Here, the heating coil is made of W, and the tube is
made of Inconel 601 or Alloy 602. Further, a thickness of the seal portion along the
axial direction is set to 10 mm.
[0131]

[0132] As shown in Table 7, it is found that all samples exhibit the excellent durability
and, particularly, the smaller the oxygen permeability of the seal portion, the more
excellent durability the sample can acquire. It is thought that the intrusion of oxygen
into the inside of the tube through the seal portion can be more suppressed.
[0133] Based on the above-mentioned results of the test, to further enhance the durability
of the heating coil, it is reasonable to say that the oxygen permeability of the seal
portion is preferably set to 2.0×10
-9 (cm
3·cm/sec·cm
2·cmHg) or less, and the oxygen permeability is more preferably set to 1.0×10
-9 (cm
3·cm/sec·cm
2·cmHg) or less.
[0134] Next, a plurality of samples of glow plugs are prepared, wherein the heating coil
is made of W and the tube is made of Inconel 601 and, with respect to each sample,
a front end portion of the tube (a portion of the tube ranging from the front end
to a position 1 mm away from the front end) is inserted into an electric furnace thus
preheating the tube at 700°C to 1400°C for 1 second to 60 seconds. Then, with respect
to each sample to which the preheating is applied, the number of cycles until the
breaking of the heating coil occurs (breaking cycle) is measured by setting the series
of following operations as 1 cycle. Electric power is supplied to each sample for
60 seconds such that a temperature of a tube surface is elevated from a normal temperature
to 1000°C within 2 seconds and, at the same time, the tube surface temperature is
saturated at 1200°C (that is, electric power is supplied at 11 V for 2 seconds and,
thereafter, electric power is supplied at 7.5 V for 60 seconds) and, thereafter, the
tube surface is cooled by air for 180 seconds. Table 8 shows a result of the test.
Here, the seal portion is made of fluoro-rubber. Further, in Table 8, as the reference,
the breaking cycle with respect to a sample to which the preheating is not applied
is also shown together with the preheated samples.
[0135]
[Table 8]
Preheating temperature (°C) |
Preheating time (s) |
Breaking cycle |
Determination |
- |
- |
5824 |
Good |
700 |
1 |
6744 |
Good |
30 |
7290 |
Good |
60 |
7582 |
Good |
800 |
1 |
7889 |
Good |
3 |
9234 |
Very good |
10 |
9487 |
Very good |
30 |
9904 |
Very good |
60 |
418 |
Bad |
1300 |
1 |
8654 |
Good |
3 |
9730 |
Very good |
10 |
9779 |
Very good |
30 |
9425 |
Very good |
60 |
599 |
Bad |
1400 |
3 |
875 |
Bad |
[0136] As shown in Table 8, it is found that the durability is extremely lowered with respect
to the samples to which the preheating is applied at 800°C or more for 60 seconds
and the samples to which the preheating is applied at 1400°C. It is thought that this
lowering of durability is brought about by melting of the seal portion due to heating
of the sample for a long time or by the reduction of a thickness of the tube due to
heating of the sample at an extremely high temperature.
[0137] To the contrary, it is found that the sample to which the preheating is applied at
a temperature of 700°C to 1300°C over 1 second to 30 seconds and the sample to which
the preheating is applied at a temperature of 700°C for 60 seconds exhibit the further
excellent durability compared to the sample to which the preheating is not applied.
It is thought that, by heating the tube, Al and Cr contained in the tube positively
react with oxygen inside the tube prior to the heating coil whereby an oxygen partial
pressure inside the tube can be lowered while suppressing the oxidation of the heating
coil as a result.
[0138] Further, particularly, with respect to the sample to which the preheating is applied
at a temperature of 800°C to 1300°C over 3 seconds to 30 seconds, the breaking cycle
exceeds 9000 cycles so that it is confirmed that the sample possesses the extremely
excellent durability.
[0139] Based on the above-mentioned result of the test, it is reasonable to say that it
is preferable to perform the preheating of the front end portion of the tube for realizing
the further enhancement of the durability. Particularly, from a viewpoint of reliably
enhancing the durability, it is more preferable to perform the preheating at a relatively
low temperature of 700°C or less or to perform the preheating at a temperature exceeding
700°C and 1300°C or less over 1 second to 30 seconds, and it is further more preferable
to perform the preheating at a temperature of 800°C or more and 1300°C or less over
3 seconds to 30 seconds.
[0140] Next, a plurality of samples of glow plugs where a wire diameter of the heating coil
is changed to various values are prepared, and while measuring a temperature of a
portion of a tube surface 2 mm away from a front end toward a rear end side (the center
of the exposed portion) by a radiation pyrometer, electric power is supplied to each
sample at 11 V for 2 seconds and, thereafter, electric power is supplied to each sample
at 6 V for 180 seconds. Then, a time which elapses until the temperature of a portion
of the tube 2 mm away from the front end toward the rear end side (measuring object
portion) reaches 1000°C is measured (1000°C arrival time). Here, it is reasonable
to say that, with respect to the sample where the temperature of the measuring object
portion reaches 1000°C within 3 seconds, the temperature of the tube can be easily
rapidly elevated and hence, unoxidized Al or Cr is likely to be exposed on an inner
peripheral surface of the tube whereby the sample is preferable from a viewpoint of
the enhancement of oxidation resistance of the heating coil. Table 9 shows the result
of the test. In all samples, the heating coil is made of Mo, a pitch of the heating
coil is set to a fixed value, an outer diameter of the heating coil is set to 2.5
mm, and the normal-temperature resistance of the whole heating coil is set to 300
mΩ. Further, to set the normal-temperature resistance of the whole heating coil equal
among all samples, a length of the heating coil along an axis of the heating coil
and the number of turns of the heating coil are changed corresponding to a wire diameter
of the heating coil. In Table 9, the length of the heating coil and the number of
turns of the heating coil with respect to each sample are shown together with the
wire diameter and the 1000°C arrival time (s) for reference purposes.
[0141]
[Table 9]
Wire diameter (mm) |
Number of turns of coil |
Length of coil (mm) |
1000°C arrival time (s) |
0.10 |
9 |
3.5 |
1.2 |
0.15 |
18 |
4.5 |
2.0 |
0.20 |
30 |
9 |
3.5 |
0.30 |
60 |
24 |
4.0 |
[0142] As shown in Table 9, it is found that, in the sample where the wire diameter of
the heating coil is set to 0. 15 mm or less, the temperature of the measuring object
portion reaches 1000°C within 3 seconds so that the rapid temperature elevation of
the exposed portion can be easily acquired.
[0143] Next, a plurality of samples of glow plugs are prepared, wherein while a wire diameter
of a portion of the heating coil positioned between a front end and a position 6 mm
away from the front end toward a rear end of the heating coil along the center axis
of the tube (front-end-side coil) is changed, a wire diameter of a portion of the
heating coil which is positioned at a more rear end side than the front-end-side coil
(rear-end-side coil) is set to a fixed value (0.2 mm). A temperature of each sample
is elevated under the above-mentioned energization condition (electric power is supplied
at 11 V for 2 seconds and, thereafter, electric power is supplied at 6 V for 180 seconds).
Then, a time which elapses before the temperature of the measuring object portion
reaches 1000°C is measured. Table 10 shows the result of the test.
[0144] In all samples, the heating coil is made of Mo, an outer diameter of the heating
coil is set to 2.5 mm, a length of the front-end-side coil is set to 6 mm, and a length
of the rear-end-side coil is set to 18 mm. Further, in all samples, the heating coil
is prepared by welding a portion corresponding to the front-end-side coil to a portion
corresponding to the rear-end-side coil. Further, an average pitch of the front-end-side
coil is changed in conformity with the wire diameter of the front-end-side coil so
as to adjust normal-temperature resistance of the front-end-side coil to 150 mΩ. By
also adjusting the normal-temperature resistance of the rear-end-side coil to 150
mΩ, the normal-temperature resistance of the whole heating coil is set to 300 mΩ,
and an average value of the normal-temperature resistance of the whole heating coil
is set to 12.5 mΩ/mm (=300 mΩ/24 mm).
[0145]
[Table 10]
Front end side coil (length: 6 mm) |
Rear end side coil (length: 18 mm) |
Average value of normal temperature resistance of whole heating coil (mΩ/mm) |
1000°C arrival time (s) |
Wire diameter (mm) |
Average value of normal temperature resistance (mΩ/mm) |
Average value of normal temperature resistance (mΩ/mm) |
0.1 |
25.0 |
8.3 |
12.5 |
2 |
0.15 |
25.0 |
8.3 |
12.5 |
2 |
0.2 |
25.0 |
8.3 |
12.5 |
2 |
[0146] As shown in Table 10, in all samples, it is confirmed that the temperature of the
measuring object portion reaches 1000°C within 3 seconds so that the rapid temperature
elevation of the exposed portion can be easily acquired.
[0147] To form the heating coil such that the heating coil possesses sufficient mechanical
strength, it is preferable to set a wire diameter of the heating coil to 2.0 mm or
more. In view of the above, a plurality of samples of glow plugs where an average
value of normal-temperature resistance of the front-end -side coil is changed are
prepared by changing a pitch of the front-end -side coil while setting the wire diameter
of the heating coil to 2.0 mm, and a temperature of each sample is elevated under
the above-mentioned energization condition (electric power is supplied at 11 V for
2 seconds and, thereafter, electric power is supplied at 6 V for 180 seconds). Then,
the evaluation "good" is given to the sample where the temperature of the measuring
object portion reaches 1000°C within 3 seconds as the rapid temperature elevation
of the exposed portion can be easily acquired, while the evaluation "fair" is given
to the sample where the temperature of the measuring object portion does not reach
1000°C within 3 seconds as the temperature elevation of the exposed portion is slightly
difficult. Table 11 shows the result of the test.
[0148] Further, with respect to the samples where a temperature of the measuring object
portion reaches 1000°C within 3 seconds, the number of cycles until the breaking of
the heating coil occurs (breaking cycle) is also measured by setting the series of
following operations as 1 cycle. Electric power is supplied to the sample at 11 V
for 2 seconds and, thereafter, electric power is supplied to the sample at 7.5 V for
180 seconds, and the electric power supply is stopped for 120 seconds. Table 11 also
shows the measured breaking cycles in addition to the above-mentioned result of the
test.
[0149] In all samples, the heating coil is made of Mo and an outer diameter of the heating
coil is set to 2.5 mm. Further, as shown in Fig. 7(a) and Fig. 7(b), in all samples,
a length of the front-end-side coil is set to 6 mm, and a length of the rear-end-side
coil is set to 18 mm. Then, in all samples, the normal-temperature resistance of the
whole heating coil is set to 300 mΩ by also changing the normal-temperature resistance
of the rear-end-side coil by adjusting a pitch of the rear-end-side coil in conformity
with the change of the normal-temperature resistance (pitch) of the front-end-side
coil. Table 11 shows the normal-temperature resistance of the front-end-side coil,
the normal-temperature resistance of the rear-end-side coil, an average pitch of the
front-end-side coil, and an average pitch of the rear-end-side coil along with the
above-mentioned result of the test. The average pitch of the front-end-side coil is
calculated in such a manner that one turn (the frontmost end portion of the heating
coil) adjacent to the front end of the tube is excluded from the front-end-side coil
in calculation.
[0150]
[Table 11]
Front end side coil (length: 6 mm) |
Rear end side coil (length: 18 mm) |
Difference in average pitch |
Average value of normal temperature resistance of whole heating coil (mΩ/mm) |
1000°C arrival time (s) |
Evaluation |
Breaking cycle |
Normal temperature resistance (mΩ) |
Average value of normal temperature resistance (mΩ/mm) |
Average pitch (mm) |
Normal temperature resistance (mΩ) |
Average value of normal temperature resistance (mΩ/mm) |
Average pitch (mm) |
60 |
10.0 |
0.79 |
240 |
13.3 |
0.75 |
-0.04 |
12.5 |
Not reached |
Fair |
Not made |
90 |
15.0 |
0.53 |
210 |
11.7 |
0.86 |
0.33 |
12.5 |
3 |
Good |
8199 |
120 |
20.0 |
0.39 |
180 |
10.0 |
1.00 |
0.61 |
12.5 |
2.5 |
Good |
8912 |
150 |
25.0 |
0.30 |
150 |
8.3 |
1.20 |
0.90 |
12.5 |
2 |
Good |
9481 |
180 |
30.0 |
0.26 |
120 |
6.7 |
1.50 |
1.24 |
12.5 |
2 |
Good |
10221 |
210 |
35.0 |
0.23 |
90 |
5.0 |
2.00 |
1.77 |
12.5 |
2 |
Good |
9893 |
[0151] As shown in Table 11, in the sample where the average value of the normal-temperature
resistance of the front-end-side coil is set larger than the average value of the
normal-temperature resistance of the whole heating coil, the temperature of the measuring
object portion reaches 1000°C within 3 seconds and hence, it is found that the rapid
temperature elevation of the exposed portion can be easily acquired. Further, particularly,
in the sample where the average pitch of the front-end-side coil is set smaller than
the average pitch of the rear-end-side coil by 0.9 mm or more, the temperature of
the measuring object portion reaches 1000°C within 2 seconds and hence, it is found
that the exposed portion exhibits the further excellent rapid temperature elevation
characteristic.
[0152] Further, it is reconfirmed that the shorter the 1000°C arrival time, the more the
durability of the heating coil can be enhanced.
[0153] Next, samples of glow plugs where an average value of normal-temperature resistance
of the whole heating coil is changed are prepared by changing a length L of the rear-end
-side coil while setting both the normal-temperature resistance of the front-end-side
coil and the normal-temperature resistance of the rear-end-side coil to 150 mΩ and
setting the length of the front-end-side coil to 6.0 mm (that is, the average value
of the normal-temperature resistance of the front-end-side coil to a fixed value (25
mΩ/mm)) as shown in Fig. 8 (a) and Fig. 8(b). Then, the temperature of each sample
is elevated under the above-mentioned energization condition (electric power is supplied
at 11 V for 2 seconds and, thereafter, electric power is supplied at 6 V for 180 seconds).
The evaluation "good" is given to the sample where the temperature of the measuring
object portion reaches 1000°C within 3 seconds, and the evaluation "fair" is given
to the sample where the temperature of the measuring object portion does not reach
1000°C within 3 seconds. Table 12 shows the result of the test.
[0154] Further, with respect to the sample which receives the evaluation "good", the number
of cycles until the breaking of the heating coil occurs (breaking cycle) is measured
by setting the series of following operations as 1 cycle. Electric power is supplied
to the sample at 11 V for 2 seconds and, thereafter, electric power is supplied to
the sample at 7.5 V for 180 seconds, and the electric power supply is stopped for
120 seconds. Table 12 also shows the breaking cycles in addition to the above-mentioned
result of the test.
[0155] In all samples, the heating coil is made of W and an outer diameter of the heating
coil is set to 2.5 mm.
[0156]
[Table 12]
Front end side coil (resistance: 150 mΩ) |
Rear end side coil (resistance: 150 mΩ) |
Difference in average pitch |
Average value of normal temperature resistance of whole heating coil (mΩ/mm) |
1000°C arrival-time (s) |
Evaluation |
Breaking cycle |
Length (mm) |
Average value of normal temperature resistance (mΩ/mm) |
Average pitch (mm) |
Length (mm) |
Average value of normal temperature resistance (mΩ/mm) |
Average pitch (mm) |
6 |
25.0 |
0.30 |
4 |
37.5 |
0.27 |
-0.03 |
30.0 |
not reached |
Fair |
not made |
6 |
25.0 |
0.30 |
6 |
25.0 |
0.40 |
0.10 |
25.0 |
3.5 |
Fair |
7677 |
6 |
25.0 |
0.30 |
10 |
15.0 |
0.67 |
0.37 |
18.8 |
3 |
good |
8821 |
6 |
25.0 |
0.30 |
18 |
8.3 |
1.20 |
0.90 |
12.5 |
2 |
good |
9481 |
6 |
25.0 |
0.30 |
25 |
6.0 |
1.67 |
1.37 |
9.7 |
2 |
good |
9928 |
6 |
25.0 |
0.30 |
40 |
3.8 |
2.67 |
2.37 |
6.5 |
2 |
good |
10293 |
[0157] As shown in Table 12, it is reconfirmed that the rapid temperature elevation of the
exposed portion can be easily acquired by setting the average value of the normal-temperature
resistance of the front-end-side coil larger than the average value of the normal-temperature
resistance of the whole heating coil. Further, it is also reconfirmed that the rapid
temperature elevation characteristic of the exposed portion can be further enhanced
by setting the average pitch of the front-end-side coil smaller than the average pitch
of the rear-end-side coil by 0.9 mm or more.
[0158] From the above-mentioned result of the test, it is reasonable to say that, to positively
elevate the temperature of the exposed portion of the tube which is likely to become
high for acquiring the further enhancement of the oxidization resistance of the heating
coil, it is preferable to set the average value of the normal-temperature resistance
of the front-end-side coil larger than the average value of the normal-temperature
resistance of the whole heating coil. Further, it is also reasonable to say that,
to acquire the further enhancement of the oxidization resistance of the heating coil,
it is preferable to set the average pitch of the front-end-side coil smaller than
the average pitch of the rear-end-side coil by 0.9 mm or more.
[0159] The results of the test shown in Table 9 to Table 12 are obtained, as described above,
by supplying electric power at 11 V for 2 seconds and, thereafter, by supplying electric
power at 6 V for 180 seconds. Accordingly, even with respect to the sample on which
the evaluation that the rapid temperature elevation of the exposed portion is slightly
difficult under this energization condition is made, it is possible to set the surface
temperature of the exposed portion to 1000°C or more within 3 seconds by changing
the energization condition. Further, by changing the energization condition and the
constitution of the heating coil, it is also possible to set a surface temperature
of a portion of the tube other than the exposed portion to 1000°C or more within 3
seconds.
[0160] The present invention is not limited to the described content of the above-mentioned
embodiments, and the present invention may be carried out as follows, for example.
It is needless to say that other modifications and variations can be also considered
besides modifications and variations exemplified hereinafter.
[0161] (a) In the above-mentioned embodiments, pure metal of W or Mo is exemplified as the
metal material which forms the heating coil 9. However, the metal material which forms
the heating coil 9 may be an alloy which contains W or Mo as a main component. Accordingly,
the heating coil 9 may be made of a metal material which contains W or Mo as a main
component, and also contains rhenium (Re), thorium oxide (ThO
2)
, Cr or the like. By containing several mass% or more and several tens mass% or less
of Re, the heating coil 9 can sufficiently increase a resistance value thereof thus
realizing a sufficient heat generating performance without excessively narrowing a
diameter thereof (that is, while maintaining durability of the heating coil 9). Further,
by containing several mass% of ThO
2, the heating coil 9 can suppress a grain growth under a high temperature thus further
enhancing durability thereof.
[0162] (b) In the above-mentioned embodiments, the front end portion of the tube 7 and the
front end portion of the heating coil 9 are joined to each other. However, the tube
7 and the heating coil 9 may be configured such that the front end portion of the
tube 7 and the front end portion of the heating coil 9 are not joined to each other.
[0163] (c) In the above-mentioned embodiments, EPDM rubber and fluoro-rubber are exemplified
as the material for forming the seal portion 11. However, the material for forming
the seal portion 11 is not limited to such materials. Accordingly, the seal portion
11 may be made of silicon rubber having some thickness or the seal portion 11 may
be made of a glass material when swaging is not applied to the tube 7.
[0164] (d) In the above-mentioned embodiments, the metal piece MP is made of the material
having the same composition as the material for forming the tube 7. However, the composition
of the metal piece MP is not limited to such composition. Here, to provide the front
end portion of the tube 7 which does not contain W, it is preferable to use the metal
piece MP which does not contain W. Further, as described in the above-mentioned embodiments,
to enhance oxidation resistance of the front end portion of the tube 7 by providing
the front end portion of the tube 7 which contains Cr, it is preferable to provide
the metal piece MP which contains Cr.
[0165] (e) In the above-mentioned embodiments, the insulation powder 10 is made of the metal
material which contains MgO as a main component. However, the insulation powder 10
may be made of a material which contains other metal (for example, Al
2O
3 or Si
3N
4) as a main component.
[0166] (f) A shape or the like of the glow plug 1 is not limited to the above-mentioned
embodiments. For example, with respect to the tube 7, a small-diameter portion may
be formed on the front end portion of the tube 7. Further, the shaft hole 4 formed
in the main fitting 2 may be formed into a straight shape in the axial direction by
eliminating the large-diameter portion 4a of the shaft hole 4, and the tube 7 may
be press-fitted into the shaft hole 4.
[0167] (g) In the above-mentioned embodiments, the intermediate shaft 8 is directly joined
to the rear end of the heating coil 9. However, between the heating coil 9 and the
intermediate shaft 8, it may be possible to provide a coil (a so-called control coil)
which is made of a metal material [for example, a metal material containing Co or
Ni as a main component as represented by a cobalt (Co) -Ni-Fe-based alloy or the like]
different from the metal material for forming the heating coil 9. In this case, during
temperature elevation (at a relatively low temperature), a resistance value of the
control coil is relatively low so that the temperature of the heating coil 9 can be
rapidly elevated, while when the temperature is saturated, the resistance value of
the control coil becomes relatively high so that a electric power supply quantity
to the heating coil 9 is suppressed thus suppressing the excessive temperature elevation
of the heating coil 9.
Explanation of symbols
[0168]
1: |
glow plug |
7: |
tube |
9: |
heating coil (heating resistor) |
10: |
insulation powder |
11: |
seal portion |
21: |
heating device |
31: |
GCU (energization control device) |