Background of the Invention
[0001] Normal air diffusion reduces tire pressure over time. The natural state of tires
is under inflated. Accordingly, drivers must repeatedly act to maintain tire pressures
or they will see reduced fuel economy, tire life and reduced vehicle braking and handling
performance. Tire Pressure Monitoring Systems have been proposed to warn drivers when
tire pressure is significantly low. Such systems, however, remain dependant upon the
driver taking remedial action when warned to re-inflate a tire to recommended pressure.
It is a desirable, therefore, to incorporate an air maintenance feature within a tire
that will re-inflate the tire in order to compensate for any reduction in tire pressure
over time without the need for driver intervention.
Summary of the Invention
[0002] The invention relates to a method of providing a passageway in a tire in accordance
with claim 1 and to a coated filament in accordance with claim 12.
[0003] Dependent claims refer to preferred embodiments of the invention.
[0004] In one aspect of the invention, the method in accordance with the invention may be
a method of constructing a tire, the method comprising: constructing a coated filament,
the coated filament constructed by coating a filament with a coating material, the
coating material comprising at least one diene based elastomer and heat expandable
thermoplastic resin particles containing therein a liquid or solid capable of generating
a gas upon vaporization, decomposition, or a chemical reaction under heating; encasing
the coated filament into containment within an uncured or pre-cured flexible tire
component; building a green tire from tire components including the uncured or pre-cured
flexible tire component and the encased coated filament; curing the green tire including
the flexible tire component containing the coated filament; removing the filament
from the cured flexible tire component to leave within the flexible tire component
a substantially unobstructed air passageway.
[0005] In one aspect of the invention, the flexible tire component may be an uncured flexible
tire component.
[0006] In another aspect of the invention, the flexible tire component may be a pre-cured
flexible tire component.
[0007] The flexible tire component may be a tire sidewall component, a tire tread component,
a tire chafer component, or a tire apex component.
[0008] In one aspect of the invention, the coated filament may extend between an air inlet
and an air outlet cavity in the uncured or pre-cured flexible tire component.
[0009] In one aspect of the invention, the method may further comprise removing the filament
axially from the cured flexible tire component by means of drawing a free end of the
filament.
[0010] In one aspect of the invention, the method may further comprise inserting a temporary
air inlet assembly into an air inlet cavity prior to curing the green tire; and inserting
a temporary air outlet assembly into an air outlet cavity prior to curing the green
tire; and removing the temporary air inlet assembly and the temporary air outlet assembly
after curing the green tire.
[0011] In one aspect of the invention, the temporary air inlet assembly may be a procured
temporary air inlet assembly and the temporary air outlet assembly may be a procured
temporary air outlet assembly.
[0012] In one aspect of the invention, the method may include extending the air outlet assembly
through a tire sidewall into communication with a tire cavity.
[0013] In one aspect of the invention, the method may include extending the air outlet assembly
through a tire sidewall into air flow communication between the unobstructed air passageway
and a tire cavity.
[0014] In one aspect of the invention, the method may include encasing the coated filament
into a containment with the uncured or pre-cured flexible tire component by: forming
a channel into the uncured or pre-cured flexible tire component defined by channel
sidewalls and a channel bottom wall; inserting the coated filament into the channel;
and collapsing a flexible channel sidewall over the coated filament.
[0015] In one aspect of the invention, the forming a channel into the uncured or pre-cured
flexible tire component may be by extruding the uncured flexible tire component with
the channel formed therein.
[0016] In another preferred aspect of the invention, a coated filament comprising a filament
and a coating material coating the filament is disclosed. The coating material comprises
at least one diene based elastomer and heat expandable thermoplastic resin particles
containing therein a liquid or a solid capable of generating a gas upon vaporization,
decomposition, or a chemical reaction under heating.
[0017] In one aspect of the invention, the filament may be a polyamide filament, a polyester
filament, or a poly(vinyl alcohol) filament.
[0018] In one aspect of the invention, the thermoplastic resin particles may be (meth)acrylonitrile
polymer particles or copolymer particles preferably having a high content of (meth)acrylonitrile.
[0019] In one aspect of the invention, the liquid or solid capable of generating a gas upon
vaporization, decomposition, or a chemical reaction under heating may be a hydrocarbon
such as n-pentane, isopentane, neopentane, butane, isobutane, hexane, and petroleum
ether; a chlorinated hydrocarbon such as methyl chloride, methylene chloride, dichloroethylene,
trichloroethane, and trichloroethylene; or azodicarbonamide, dinitrosopentamethylene-tetramine,
azobisisobutyronitrile, a toluenesulfonyl hydrazide derivative, or aromatic succinyl
hydrazide.
Definitions
[0020] "Axial" and "axially" means lines or directions that are parallel to the axis of
rotation of the tire.
[0021] "Chafer" is a strip of material placed around the outside of a tire bead to protect
the cord plies from wearing and cutting against the rim and distribute the flexing
above the rim.
[0022] "Circumferential" means lines or directions extending along the perimeter of the
surface of the annular tread perpendicular to the axial direction.
[0023] "Equatorial Centerplane (CP)" means the plane perpendicular to the tire's axis of
rotation and passing through the center of the tread.
[0024] "Footprint" means the contact patch or area of contact of the tire tread with a flat
surface at zero speed and under normal load and pressure.
[0025] "Peristaltic" means operating by means of wave-like contractions that propel contained
matter, such as air, along tubular pathways.
[0026] "Radial" and "radially" means directions radially toward or away from the axis of
rotation of the tire.
Brief Description of the Drawings
[0027] The invention will be described by way of example and with reference to the accompanying
drawings in which:
FIG. 1 is a detail view of the filament die.
FIG. 2 is a perspective view of a basic filament extruder and conveyor.
FIG. 3 is a detail of a chafer die.
FIG. 4 is a perspective view of a basic chafer strip extruder and conveyor.
FIG. 5 is a dimensioned sectioned view of the filament.
FIG. 6 is a dimensioned sectioned view of extruded chafer strip.
FIGS. 7A through 7C are detailed views showing the filament being coated with a rubber
composition according to the present invention.
FIG. 8 is a detail view of the chafer strip with punched hole locations.
FIG. 9 is an enlarged perspective view of the coated filament being assembled into
the chafer strip.
FIGS. 10A through 10C are sectioned views showing the coated filament and the chafer
strip assembly.
FIG. 11A is a perspective view of a tire build up drum with assembled 180 degree filament/chafer
strip being applied, with a normal chafer strip placement on opposite ends.
FIG. 11B is a perspective view of a tire build up drum with a normal 180 degree chafer
strip being placed abutting the 180 degree filament/chafer strip.
FIG. 12 is a perspective front view of a formed green tire showing inlet and outlet
locations with the coated filament extending from openings and the tire ready for
core forming devices.
FIG. 13A is an enlarged sectioned view showing the inlet cavity and the coated filament
ready for placement of the inlet core device.
FIG. 13B is an enlarged sectioned view showing the outlet cavity and the coated filament
ready for placement of the outlet core device.
FIG. 14A is a top perspective view showing a first embodiment outlet core assembly
with screw punch attached.
FIG. 14B is a bottom perspective view showing the outlet core assembly with screw
punch removed and the nut attached.
FIG. 14C is a top exploded view of the outlet core assembly showing top/bottom core
halves and mounting screw with the screw punch and hold down nut.
FIG. 14D is a bottom exploded view of FIG. 14C.
FIG. 15A is a top perspective view of a first embodiment inlet core assembly.
FIG. 15B is a top exploded view of the inlet core assembly showing top/bottom core
halves and magnetic inserts.
FIG. 15C is a bottom exploded view of FIG. 15B.
FIG. 16A is a threaded elbow and valve housing assembly.
FIG. 16B is an exploded view of FIG. 16A showing the elbow, valve housing and Lee
valve.
FIG. 17A shows an alternative embodiment of threaded elbow and one-way valve assembly.
FIG. 17B is an exploded view of FIG. 17A showing the elbow valve housing with air
passage ways and membrane cover.
FIG. 18A is an enlarged sectioned view showing the inlet bottom core being inserted
into the cavity under the coated filament and the chafer groove re-opened to allow
room of the conical end of the inlet core to be fully seated into cavity.
FIG. 18B is an enlarged sectioned view showing the inlet bottom core fully inserted
into the cavity and the coated filament being trimmed to length.
FIG. 18C is an enlarged sectioned view showing the inlet top core ready for placement
into the cavity.
FIG. 18D is an enlarged section view showing the inlet core assembly fully assembled
into cavity.
FIG. 18E is an enlarged section view showing the inlet core assembly held in place
with thin rubber patches is ready for curing.
FIG. 19A is an enlarged sectioned view showing the outlet bottom core unit being inserted
into the cavity under the coated filament and the punch forced through the tire wall
into the cavity chamber with the chafer groove re-opened to allow room for the conical
end of the outlet core bottom unit to be fully seated into cavity.
FIG. 19B is an enlarged sectioned view of the bottom outlet core unit fully seated
into the cavity.
FIG. 19C is an enlarged sectioned view from cavity side showing the screw punch fully
inserted through the tire wall.
FIG. 19D is an enlarged sectioned view of the screw punch removed from the outlet
bottom core half component with the nut attached to thread shaft.
FIG. 19E is an enlarged sectioned view showing the nut fully attached to the outlet
bottom core shaft.
FIG. 19F is an enlarged sectioned view of the coated filament cut to length at the
outlet bottom core strip cavity.
FIG. 19G is an enlarged sectioned view of the outlet top core component placed into
the cavity and screwed into place.
FIG. 19H is an enlarged sectioned view showing the outlet core halves and screw fully
assembled.
FIG. 19I is an enlarged sectioned view showing the conical end of outlet core assembly
covered with a rubber patch.
FIG. 20 is a side view of a tire showing the inlet and outlet core locations before
curing.
FIG. 21A is a section view taken from FIG. 20 showing the inlet core location.
FIG. 21B is an enlarged view of the inlet core taken from FIG. 21A.
FIG. 22A is a section view taken from FIG. 20 showing the outlet core.
FIG. 22B is an enlarged view of the outlet core taken from FIG. 22A.
FIG. 23 is an enlarged sectioned view showing the inlet core halves being removed
after curing.
FIG. 24 is an enlarged sectioned view showing the nut removed from the outlet core
threaded shaft.
FIG. 25 is an exploded view of the outlet core halves disassembled and removed from
the sidewall cavity.
FIG. 26 is a side elevation showing the coated filament removed from the tire sidewall.
Detailed Description of Example Embodiments of the Invention
[0028] As an embodiment of the invention, there is disclosed a method of constructing a
tire, comprising:
constructing a coated filament, the coated filament constructed by coating a filament
with a coating material, the coating material comprising at least one diene based
elastomer and heat expandable thermoplastic resin particles containing therein a liquid
or solid capable of generating a gas upon vaporization, decomposition, or a chemical
reaction under heating;
encasing the coated filament into containment within an uncured or pre-cured flexible
tire component;
building a green tire from tire components including the uncured or pre-cured flexible
tire component and the encased coated filament;
curing the green tire including the flexible tire component containing the coated
filament;
removing the filament from the cured flexible tire component to leave within the flexible
tire component a substantially unobstructed air passageway.
[0029] In one embodiment, the coated filament extends between an air inlet and an air outlet
cavity in the uncured or pre-cured flexible tire component.
[0030] In one embodiment, the method further comprises removing the filament axially from
the cured flexible tire component by means of drawing a free end of the filament.
[0031] In one embodiment, the method further comprises inserting a temporary air inlet assembly
into an air inlet cavity prior to curing the green tire; and inserting a temporary
air outlet assembly into an air outlet cavity prior to curing the green tire; and
removing the temporary air inlet assembly and the temporary air outlet assembly after
curing the green tire.
[0032] In one embodiment, the temporary air inlet assembly is a procured temporary air inlet
assembly and wherein the temporary air outlet assembly is a procured temporary air
outlet assembly.
[0033] In one embodiment, the method further comprises extending the air outlet assembly
through a tire sidewall into communication with a tire cavity.
[0034] In one embodiment, the method further comprises extending the air outlet assembly
through a tire sidewall into air flow communication between the unobstructed air passageway
and a tire cavity.
[0035] In one embodiment, the method further comprises encasing the coated filament into
a containment with the uncured or pre-cured flexible tire component by:
forming a channel into the uncured or pre-cured flexible tire component defined by
channel sidewalls and a channel bottom wall;
inserting the coated filament into the channel; and
collapsing a flexible channel sidewall over the coated filament.
[0036] In one embodiment, forming a channel into the uncured or pre-cured flexible tire
component is by extruding the uncured flexible tire component with the channel formed
therein.
[0037] There is further disclosed a coated filament comprising a filament and a coating
material coating the filament, the coating material comprising at least one diene
based elastomer and heat expandable thermoplastic resin particles containing therein
a liquid or a solid capable of generating a gas upon vaporization, decomposition,
or a chemical reaction under heating.
[0038] With reference to FIGS. 1, 2, 3, 4, 5 and 6, a polymer filament 58 is formed by means
of die 48 having a profiled orifice 50 therethrough. The orifice is elongate and generally
lens shaped in section with the extruded strip 58 of like sectional geometry. The
lens shape may have a dimension of, by way of example, 2.7 mm length D2 x 0.5 mm at
D1. While the preferred composition of the strip 58 is a polymer, other materials
such as cable may be used if desired. The die 48 is affixed to a basic extruder of
conventional configuration and deposits a formed filament 58 on a conveyer belt moved
by drive roller 56. The filament 58 may be wound on a spool (not shown) for further
processing and will be shown. As shown in FIGS. 3 and 4, a chafer strip 70 is formed
by extrusion die 60 affixed to extruder 66 and deposited on roller 68. The die 60
is formed having along a chafer forming opening 62 along a bottom side and a downward
projection finger 64 projecting into the opening 62. FIG. 6 shows a sectioned view
of the extruded chafer strip. As seen, the strip 70 widens in section from a low width
or thinner end region 72 to a stepped wider or thicker region 74 to a wider or thicker
opposite region 88. The die finger 64 forms an incut, arching chafer channel or tube
80 extending the length of the chafer strip, defined by channel sidewalls 82, 84 and
bottom wall 86. The channel is open initially as shown at 90. The chafer strip dimensions
may be varied to suit the particular tire sizing needs and the tire construction characteristics
desired.
[0039] The chafer tube or channel 80, as best seen in section from FIG. 6, is defined by
tube sidewalls 82, 84 that angle inwardly from top to bottom to a bottom channel wall
86. The channel 80, formed within a thicker side 88 of the chafer strip is accordingly
open at upper opening 90. The channel 80 formed within the chafer is as a result at
an acute angle 6. As shown in FIGS. 7A through 7C, the filament 58 is enveloped within
a coating 92 formed of rubber composition as will be described in more detail later
herein. The coating 92 is folded over the filament 58 to form an overlap seam 94 to
enclose the filament 58 and forms therewith a coated filament 104. The coated filament
104, as explained following, will be used to form peristaltic tube within a green
tire during green tire construction.
[0040] The general purpose of coated filament 104 is to form within a green tire component,
such as chafer 28, a core air passageway which, once the filament is removed, forms
a peristaltic tube integrally within and enclosed by the tire component. The angled
groove 80 is formed within the chafer strip as a slot, with the lips 82, 84 in a close
opposed relationship. The groove 80 is then opened to receive the coated filament
104 by an elastic spreading apart of groove lips 82, 84. Thereafter, the coated filament
104 is positioned downward into the groove 80 until reaching a position adjacent to
the bottom wall 86. A release of the lips 82, 84 causes the lips to elastic resume
their close opposed original orientation. The lips 82, 84 are then stitched together
in a rolling operation wherein a roller (not shown) presses the lips 82, 84 into the
closed orientation shown in FIGS. 6 and 8 and become entrapped within the chafer strip
by a folding over the chafer strip over the top as seen in FIG. 10C. The angle θ of
the channel 80 with respect to a bottom surface of the chafer strip enables a complete
capture of the coated filament 104 within the tire component, chafer 28, entirely
surrounded by the chafer strip material composition.
[0041] With reference to FIGS. 8, 9, 10A through 10C and 7B, the channel 80 is destined
to become the tube component to a peristaltic pump assembly within the tire chafer
70 and generally extends from chafer strip end 96 to end 98. The chafer is cut at
a given length depending on the pump length that is desired when the tire is cured.
Formed within each end of the chafer by a punching operation or cutting operation
are enlarged diameter circular holes 100, 102. The holes 100, 102 are adjacent the
ends of the channel 80 and are sized to accommodate receipt of peristaltic pump inlet
and outlet devices (not shown). The lips 82,84 of the chafer channel 80 are pulled
apart The coated filament 104 is inserted at direction arrow 110 into the channel
80 as shown in FIGS. 10A through 10C until adjacent and contacting the lower wall
86 of the channel 80. Thereupon, the coated filament 104 is enclosed by the chafer
by a folding over of the chafer lip flap 82 in direction 112. The channel 80 is thus
closed and subsequently stitched in the closed position by a pair of pressure contact
rollers (not shown). So enclosed, the coated filament 104 will preserve the geometry
of the channel 80 from green tire build until after tire cure when the coated filament
104 is removed. The coated filament 104 is dimensioned such that ends 106, 108 extend
free from the chafer strip 70 and the chafer strip channel 80, and extend a distance
beyond the punched holes 100, 102 at opposite ends of the chafer strip.
[0042] Referring to FIGS. 11A, 11B and 12, a conventional green tire building station is
depicted to include a build drum 116 rotational about an axial support 118. The chafer
strip 70 containing coated filament 104 and an opposite chafer strip 122 that does
not incorporate a coated filament 104 are positioned along opposite sides of the build
drum 116 in direction 124 in an initial 180 degree chafer build-up. The chafer strip
70 is thus combined with a normal chafer strip 126 length to complete the circumference.
The second strip 126 is applied to the building drum in alignment with and abutting
strip 70 as shown in FIG. 11B to complete a 360 degree chafer construction on the
drum. The opposite side of the drum receives two 180 degree normal strips 122 in abutment
to complete the chafer build on that side. It will be noted that the chafer strip
70 contains the coated filament while the abutting strip 126 does not. However, if
desired, both of the chafer strips 70, 126 as well as one or both of the strips 122
may be configured to contain a coated filament 104 to create a 360 degree peristaltic
pump tube on one side or both sides of the green tire. For the purpose of explanation,
the embodiment shown creates a pumping tube of 180 degree extent in one chafer component
only. In FIG. 11B it will be noted that chafer strip 126 is configured to complement
the construction of strip 70 shown in FIGS. 8 and 9. Circular punch holes 100, 102
are at opposite ends of the complementary strip 126. When abutted against the strip
70, the punch holes 100, 102 create 180 degree opposite cavities 132, 134 as seen
in FIGS. 13A and 13B.
[0043] The free end 106 for the purpose of explanation will hereafter be referred to as
the "outlet end portion" of the coated filament 104 extending through the outlet cavity
134; and the free end 108 the "inlet end portion" of the coated filament 104 extending
through the circular inlet cavity 132. FIG. 12 illustrates the 180 degree extension
of the coated filament 104 and FIGS. 13A,13B show the relative location of the coated
filament 104 to the lower tire bead and apex components. FIG. 13A shows the inlet
cavity 132 and coated filament 104 ready for placement of a temporary inlet core device
and FIG. 13B shows the outlet cavity 134 ready for placement of a temporary outlet
core device.
[0044] FIGS. 14A through 14D show a first embodiment of a pre-cure, temporary outlet core
assembly 136 with attached screw punch 138 and replacement nut 140. The temporary
outlet core assembly 136 includes mating bottom half-housing component 142 and a top
half-housing component 144 connecting by means of a coupling screw 160. The bottom
half-housing component 142 has a dependent cylindrical screw threaded sleeve 146;
an upper socket 148 extending downward into the component 142 and communicating with
the upward facing opening of sleeve 146; and a half-protrusion 150 having an axial
half-channel formed to extend across housing 142. The top-half-housing component 144
has a central through bore 154, a half-protrusion housing 156 and a half-channel formed
to extend side to side across an underside of the housing 144. United as shown in
FIGS. 14A and 14B, the two half-housing components 142, 144 are assembled by screw
160 threading bolt 162 down through the bore 154 and into the sleeve 146. So assembled,
the half-protrusion housings 150 and 156 unite as well as the half-channels 152, 158.
In the assembled state, as seen in FIGS. 14A and 14B, the protrusion housings 150,
156 form an outwardly projecting conical tube-coupling protrusion 164 away from the
combined housing halves 142, 144 and defining an axial air passageway channel 165
having a sectional shape and dimension corresponding with the coated filament 104
within chafer strip 126 of the tire.
[0045] The inwardly and outwardly threaded shaft 146 of the temporary outlet core assembly
136 receives and couples with an externally threaded shaft 168 of the screw punch
accessory device 138. As will be explained below, screw punch device 138 will in the
course of peristaltic tube assembly formation be replaced with the threaded collar
or nut 140 as shown in FIG. 14B.
[0046] With reference to FIGS. 15A through 15C, a metallic first embodiment of a precure,
temporary inlet core assembly 170 is shown forming a housing body 174 from which a
conical coupling housing protrusion 172 extends. An axial air passageway through-channel
176 extends through the housing body 174 and the protrusion 172 having a sectional
shape and dimension corresponding with the shape and dimensions of the coated filament
104 within the chafer strip 126 of the green tire. The housing body 175 is formed
by a combination of half-housing 178, 180, each providing a half-coupling protrusion
182, 194, respectively in which a half-channel 184, 196 is formed, respectively. A
central assembly socket 186 extends into the internal underside of half-body 178 and
receives an upright post 188 from the lower half-body 180 to center and register the
two half-bodies together. Three sockets 190 are formed within the lower half-body
180 with each socket receiving a magnetic insert 192. The magnets 192 operate to secure
the metallic half-housings 178 and 180 together.
[0047] Referencing FIGS. 16A and 16B, a threaded elbow and valve housing assembly 198 is
shown for use as a permanent outlet core valve assembly. The housing assembly 198
is formed of a suitable material such as a nylon resin. The assembly 198 includes
an elbow housing 200 having a conical remote end 202 and a cylindrical valve housing
204 affixed to an opposite end. A one-way valve, such as a Lee valve, is housed within
the valve housing 204. An axial air passageway 208 extends through the L-shaped assembly
198 and through the Lee valve seated in-line with the passageway. A Lee valve is a
one-way valve which opens at a prescribed air pressure to allow air to pass and is
commercially available from The Lee Company USA, located at Westbrook, CT, USA.
[0048] FIGS. 17A and 17B show an alternative embodiment of an elbow connector and one-way
post-cure outlet valve assembly 210. A L-shaped elbow connector housing 212 has a
conical forward arm end 214 and an axial passageway 216 that extends through the L-shaped
housing 212. An umbrella-type valve 218 of a type commercially available from MiniValve
International located in Oldenzaal, The Netherlands, attaches to a threaded end of
housing 212 by means of nut 220. The valve 218 has a circumferential array of air
passages 227 that allow the passing of air from the housing of the valve. The valve
218 includes an umbrella stop member 222 having a frustro-conical depending protrusion
224 that fits and locks within a valve central bore 226 and a flexible circular stop
membrane 223. The protrusion 224 of stop member 222 locks into the axial bore 226.
The flexible membrane 223 is in a closed or down position when air pressure on the
membrane is at or greater than a prescribed pressure setting. In the down position,
membrane 223 covers the apertures 227 of the valve body and prevents air from passing.
The membrane 223 moves to an up or open position when the air pressure outside the
membrane falls to a pressure less than the preset pressure setting. In the up or open
position, air can flow from the apertures 227 into the tire cavity.
[0049] FIGS. 18A through 18D represent sequential views showing the installation of the
inlet core assembly embodiment of FIGS. 15A through 15C connecting into the green
tire coated filament 104 after green tire build and prior to curing of the green tire.
In FIG. 18A, the bottom half housing component 180 is inserted into the inlet cavity
132 after the cavity 132 has been enlarged into generally a key shape as indicated
by the scissor representation. The cutting implement opens the chafer strip groove,
still occupied by coated filament 104, to accommodate receipt of the conical half-protrusion
194 of half-housing 180. The tapered end of conical half-protrusion 194 fits into
the chafer channel occupied by coated filament 104 as shown in FIG. 18B, as the coated
filament 104 is position within the half-channel 196 across the housing 180. The extra
length of inlet end portion 108 is cut and removed, whereby positioning a terminal
end of the coated filament 104 within the housing component 180. The upper, outer,
top half-housing component 178 is thereupon assembled over the housing component 180,
as seen in FIG. 18D, capturing the coated filament 104 within the channel formed by
upper and lower half-channels 184, 196. The magnets 192 secure the metallic half-housings
178, 180 together. Rubber patches 228, 230 as seen in FIG. 18D are applied over the
temporary inlet core assembly 170 to secure the assembly in place for the tire cure
cycle. The hollow metallic housings 178, 180 are held together by the magnets. It
will be appreciated that a non-metallic hollow housing may be employed if desired,
such as a hollow housing made of molded plastic, with housing components held together
by locking detent techniques known in the plastic casing art.
[0050] FIGS. 19A through 19I show sequential assembly of the outlet core assembly embodiment
of FIGS. 14A through 14D into the green tire outlet cavity 134 and to the outlet end
portion 106 of the coated filament 104. In FIG. 19A, the bottom half-component 142
is inserted into the cavity 134 after the circular cavity 134 has been enlarged into
a keyhole configuration to accommodate the geometry of the component 142. The screw
punch 138 is pushed through to protrude through tire wall into the tire cavity 20
from the cavity 134 as seen in FIG. 19C. FIG. 19B shows the component 142 fully seated
into the cavity 134, the tapered conical half-protrusion 159 projecting into the chafer
channel occupied by coated filament 104 with the coated filament 104 residing within
half-channel 152. In FIG. 19D and 19E, the screw punch 138 is removed and replaced
by the nut 140 attached to the screw thread 146. In FIG. 19F, the outlet end portion
106 of coated filament 104 is cut to length at the outlet cavity 134 and placement
of the outlet top half-housing 144 over the bottom half-housing 142 within cavity
134. The screw 160 is threaded at 162 into socket 148 to affix both half-housings
142, 144 together as shown in FIGS. 19G and 19H. A rubber patch 234 is affixed over
the outlet core assembly 136 in place for tire cure.
[0051] FIGS. 20, 21A, 21B, 22A and FIG. 22B show the tire with the inlet and outlet temporary
core assemblies in place before curing. As seen, the coated filament 104 enclosed
within a chafer component 28 of the green tire extends 180 degrees between the pre-cure
outlet core assembly 136 and the pre-cure inlet core assembly 170. An enlarged depiction
of the inlet core location is shown in FIG. 21B from section view FIG. 21A and the
outlet core location is shown enlarged in FIG. 22B from the section view of FIG. 22A.
The coated filament 104 resides enclosed within the chafer channel and thereby preserves
the structural integrity of the chafer channel through tire cure. The sectional configuration
of the coated filament 104, as seen, is complementary to chafer channel in which it
is encased surrounded by chafer composition, and thereby maintains the configuration
of the chafer channel throughout tire cure.
[0052] Referring to FIG. 23, the post-cure removal of the half-housings 178, 180 from the
inlet cavity 132 is shown. The cavity 132 is thus opened including a funnel-shaped
cavity portion 233. FIGS. 24 and 25 show the nut 140 removed from the outlet core
threaded shaft 146 to initiate a post-cure removal of the outlet core assembly 136.
The assembly components 142, 144 are removed from the outlet cavity 134, leaving the
cavity 134 including funnel-shaped adjacent cavity portion 237 open. Thereafter, as
shown by FIG. 26 the coated filament 104 is removed from the tire chafer channel,
whereby the chafer channel left by the vacated coated filament 104 becomes an elongate
unobstructed 180 degree air passageway 238 from the inlet cavity 132 to the outlet
cavity 134, wholly integrated within the chafer component 28.
[0053] Removal of the coated filament 104 as indicated in FIG. 26 is shown as a complete
removal of the filament with the associated coating. In fact, while the filament is
entirely removed, in some embodiments at least part of the coating material may remain
adhered to the interior surfaces of the air passageway 238. The amount of coating
material remaining in the air passageway 238 is insufficient to block the passage
of air and the air passageway remains unobstructed and usable for its intended purpose
as a peristaltic tube.
[0054] The green tire component may include both the chafer as well as a tire carcass, tire
sidewall, and tire tread. The green tire component may be uncured, or fully or partially
pre-cured before incorporation into the green tire.
[0055] As inserted into the tire component, the coated filament is constructed of a relatively
thin filament coated with a rubber composition.
[0056] The relatively thin filament is an elongate body of relatively constant cross section.
Suitable cross sections for the filament are not limited, and include circular, oval
and lens. Suitable filaments include those made of metal and polymers. Suitable metals
include steel. Suitable polymers include thermoplastics and silicone rubber.
[0057] Thermoplastics suitable for use as filaments include polyamides, polyesters, and
poly(vinyl alcohols). Included in the polyamides are nylon 6, nylon 66, nylon 612,
among others. Included in the polyesters are polyethylene terephthalate and polyethylene
naphthalate, among others.
[0058] In one embodiment, the filament has a relatively circular cross section. In one embodiment,
the filament has a diameter ranging from 0.5 to 5 mm.
[0059] In one embodment, the filament is a so-called nylon monofilament.
[0060] Referring again to FIGS. 7A, 7B, and 7C, one embodiment is illustrated for coating
filament 58 with coating material 92. Other methods for coating the filament with
the rubber composition include calendaring or extruding the rubber composition onto
the filament.
[0061] The coating material 92 used for coating the filament 58 is a rubber composition
including heat expandable thermoplastic resin particles containing therein a liquid
or solid capable of generating a gas upon vaporization, decomposition, or a chemical
reaction under heating. Use of the rubber composition as the coating material facilitates
removal of the filament 58 from the tire chafer channel to leave air passageway 238
as seen in FIG. 26.
[0062] In one embodiment, the rubber composition includes from 1 to 20 phr of heat expandable
thermoplastic resin particles containing therein a liquid or solid capable of generating
a gas upon vaporization, decomposition, or a chemical reaction under heating. In one
embodiment, the rubber composition includes 5 to 10 phr of heat expandable thermoplastic
resin particles containing therein a liquid or solid capable of generating a gas upon
vaporization, decomposition, or a chemical reaction under heating.
[0063] The heat expandable thermoplastic resin particles contain therein a liquid or solid
which vaporizes, decomposes, or chemically reacts under heat to generate a gas in
a thermoplastic resin. These heat expandable thermoplastic resin particles are heated
to expand at a temperature above the temperature of start of expansion, normally a
temperature of 140 to 190 °C. The gas is sealed inside a shell comprised of the thermoplastic
resin. Therefore, the size of the gas-encompassed thermoplastic resin particles is
preferably 5 to 300 µm, more preferably 10 to 200 µm before expansion.
[0064] Examples of such heat expandable thermoplastic resin particles (unexpanded particles)
are commercially available as the Expancel series from Sweden's Expancel Co. or the
Matsumoto Microsphere series from Matsumoto Yushi-Seiyaku Co.
[0065] The preferable thermoplastic resin comprising the outer shell of the gas-encompassed
thermoplastic resin particles are, for example, those having a temperature of start
of expansion of at least 100 ° C, preferably at least 120 ° C, and a maximum temperature
of expansion of at least 150° C, preferably at least 160 ° C. Examples of such a thermoplastic
resin are a (meth)acrylonitrile polymer or a copolymer having a high content of (meth)acrylonitrile.
As the other monomer (i.e., comonomer) in the case of a copolymer, a halogenated vinyl,
halogenated vinylidene, styrene based monomer, (meth)acrylate based monomer, vinyl
acetate, butadiene, vinyl pyridine, chloroprene, or other monomer may be used. Note
that the above-mentioned thermoplastic resin may be cross-linked by a cross-linking
agent such as divinylbenzene, ethylene glycol di(meth)acrylate, triethylene glycol
di(meth)acrylate, trimethylolpropane tri(meth)acrylate, 1,3-butylene glycol di(meth)acrylate,
ary(meth)acrylate, triacrylformal, and triarylisocyanulate. For the cross-linking
mode, noncross-linking condition is preferable, but partial cross-linking to an extent
not detracting from the properties as the thermoplastic resin is also possible.
[0066] Examples of the liquid or solid capable of generating a gas by vaporization, decomposition,
or chemical reaction under heat are hydrocarbons such as n-pentane, isopentane, neopentane,
butane, isobutane, hexane, and petroleum ether, liquids such as a chlorinated hydrocarbon,
e.g., methyl chloride, methylene chloride, dichloroethylene, trichloroethane, and
trichloroethylene, or solids such as azodicarbonamide, dinitrosopentamethylene-tetramine,
azobisisobutyronitrile, toluenesulfonyl hydrazide derivative, or aromatic succinyl
hydrazide.
[0067] The rubber composition includes, in addition to the heat expandable thermoplastic
resin particles containing therein a liquid or solid capable of generating a gas upon
vaporization, decomposition, or a chemical reaction under heating, one or more diene
based elastomers. The phrases "rubber or elastomer containing olefinic unsaturation"
or "diene based elastomer" are equivalent and are intended to include both natural
rubber and its various raw and reclaim forms as well as various synthetic rubbers.
In the description of this invention, the terms "rubber" and "elastomer" may be used
interchangeably, unless otherwise prescribed. The terms "rubber composition," "compounded
rubber" and "rubber compound" are used interchangeably to refer to rubber which has
been blended or mixed with various ingredients and materials and such terms are well
known to those having skill in the rubber mixing or rubber compounding art. Representative
synthetic polymers are the homopolymerization products of butadiene and its homologues
and derivatives, for example, methylbutadiene, dimethylbutadiene and pentadiene as
well as copolymers such as those formed from butadiene or its homologues or derivatives
with other unsaturated monomers. Among the latter are acetylenes, for example, vinyl
acetylene; olefins, for example, isobutylene, which copolymerizes with isoprene to
form butyl rubber; vinyl compounds, for example, acrylic acid, acrylonitrile (which
polymerize with butadiene to form NBR), methacrylic acid and styrene, the latter compound
polymerizing with butadiene to form SBR, as well as vinyl esters and various unsaturated
aldehydes, ketones and ethers, e.g., acrolein, methyl isopropenyl ketone and vinylethyl
ether. Specific examples of synthetic rubbers include neoprene (polychloroprene),
polybutadiene (including cis-1,4-polybutadiene), polyisoprene (including cis-1,4-polyisoprene),
butyl rubber, halobutyl rubber such as chlorobutyl rubber or bromobutyl rubber, styrene/isoprene/butadiene
rubber, copolymers of 1,3-butadiene or isoprene with monomers such as styrene, acrylonitrile
and methyl methacrylate, as well as ethylene/propylene terpolymers, also known as
ethylene/propylene/diene monomer (EPDM), and in particular, ethylene/propylene/ dicyclopentadiene
terpolymers. Additional examples of rubbers which may be used include alkoxy-silyl
end functionalized solution polymerized polymers (SBR, PBR, IBR and SIBR), silicon-coupled
and tin-coupled star-branched polymers. The preferred rubber or elastomers are polyisoprene
(natural or synthetic), polybutadiene and SBR.
[0068] In one aspect the at least one additional rubber is preferably of at least two of
diene based rubbers. For example, a combination of two or more rubbers is preferred
such as cis 1,4-polyisoprene rubber (natural or synthetic, although natural is preferred),
3,4-polyisoprene rubber, styrene/isoprene/butadiene rubber, emulsion and solution
polymerization derived styrene/butadiene rubbers, cis 1,4-polybutadiene rubbers and
emulsion polymerization prepared butadiene/acrylonitrile copolymers.
[0069] In one aspect of this invention, an emulsion polymerization derived styrene/butadiene
(E-SBR) might be used having a relatively conventional styrene content of 20 to 28
percent bound styrene or, for some applications, an E-SBR having a medium to relatively
high bound styrene content, namely, a bound styrene content of 30 to 45 percent.
[0070] By emulsion polymerization prepared E-SBR, it is meant that styrene and 1,3-butadiene
are copolymerized as an aqueous emulsion.
[0071] The bound styrene content can vary, for example, from 5 to 50 percent. In one aspect,
the E-SBR may also contain acrylonitrile to form a terpolymer rubber, as E-SBAR, in
amounts, for example, of 2 to 30 weight percent bound acrylonitrile in the terpolymer.
[0072] Emulsion polymerization prepared styrene/butadiene/acrylonitrile copolymer rubbers
containing 2 to 40 weight percent bound acrylonitrile in the copolymer are also contemplated
as diene based rubbers for use in this invention.
[0073] The solution polymerization prepared SBR (S-SBR) typically has a bound styrene content
in a range of 5 to 50, preferably 9 to 36, percent. The S-SBR can be conveniently
prepared, for example, by organo lithium catalyzation in the presence of an organic
hydrocarbon solvent.
[0074] In one embodiment, cis 1,4-polybutadiene rubber (BR) may be used. Such BR can be
prepared, for example, by organic solution polymerization of 1,3-butadiene. The BR
may be conveniently characterized, for example, by having at least a 90 percent cis
1,4-content.
[0075] The term "phr" as used herein, and according to conventional practice, refers to
"parts by weight of a respective material per 100 parts by weight of rubber, or elastomer."
[0076] The rubber composition may also include up to 70 phr of processing oil. Processing
oil may be included in the rubber composition as extending oil typically used to extend
elastomers. Processing oil may also be included in the rubber composition by addition
of the oil directly during rubber compounding. The processing oil used may include
both extending oil present in the elastomers, and process oil added during compounding.
Suitable process oils include various oils as are known in the art, including aromatic,
paraffinic, naphthenic, vegetable oils, and low PCA oils, such as MES, TDAE, SRAE
and heavy naphthenic oils. Suitable low PCA oils include those having a polycyclic
aromatic content of less than 3 percent by weight as determined by the IP346 method.
Procedures for the IP346 method may be found in
Standard Methods for Analysis & Testing of Petroleum and Related Products and British
Standard 2000 Parts, 2003, 62nd edition, published by the Institute of Petroleum,
United Kingdom.
[0077] The rubber composition may include from 10 to 150 phr of silica. In another embodiment,
from 20 to 80 phr of silica may be used.
[0078] Various commercially available silicas may be used, such as, only for example herein,
silicas commercially available from PPG Industries under the Hi-Sil trademark with
designations 210 and 243; silicas available from Rhodia, with, for example, designations
of Z1165MP and Z165GR and silicas available from Degussa AG with, for example, designations
VN2 and VN3.
[0079] Commonly employed carbon blacks can be used as a conventional filler in an amount
ranging from 10 to 150 phr. In another embodiment, from 20 to 80 phr of carbon black
may be used. Representative examples of such carbon blacks include N110, N121, N134,
N220, N231, N234, N242, N293, N299, N315, N326, N330, N332, N339, N343, N347, N351,
N358, N375, N539, N550, N582, N630, N642, N650, N683, N754, N762, N765, N774, N787,
N907, N908, N990 and N991. These carbon blacks have iodine absorptions ranging from
9 to 145 g/kg and DBP number ranging from 34 to 150 cm
3/100 g.
[0080] Other fillers may be used in the rubber composition including, but not limited to,
particulate fillers including ultra high molecular weight polyethylene (UHMWPE), crosslinked
particulate polymer gels including but not limited to those disclosed in
US-B- 6,242,534;
US-B-6,207,757;
US-B- 6,133,364;
US-B- 6,372,857;
US-B- 5,395,891; or
US-B- 6,127,488, and plasticized starch composite filler including to that disclosed in
US-A- 5,672,639. Such other fillers may be used in an amount ranging from 1 to 30 phr.
[0081] In one embodiment the rubber composition may contain a conventional sulfur containing
organosilicon compound. Examples of suitable sulfur containing organosilicon compounds
are of the formula:
Z-Alk-S
n-Alk-Z I
in which Z' is selected from the group consisting of
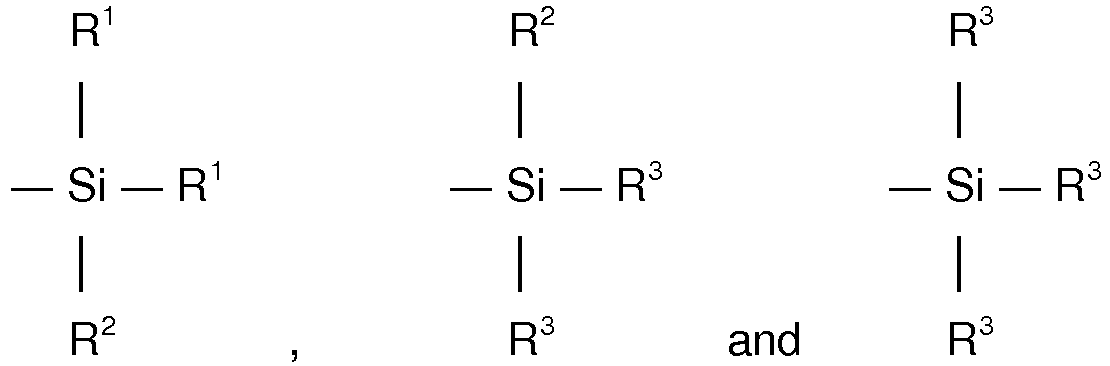
where R
1 is an alkyl group of 1 to 4 carbon atoms, cyclohexyl or phenyl; R
2 and R
3 are alkoxy of 1 to 8 carbon atoms, or cycloalkoxy of 5 to 8 carbon atoms; Alk is
a divalent hydrocarbon of 1 to 18 carbon atoms and n is an integer of 2 to 8.
[0082] In one embodiment, the sulfur containing organosilicon compounds are the 3,3'-bis(trimethoxy
or triethoxy silylpropyl) polysulfides. In one embodiment, the sulfur containing organosilicon
compounds are 3,3'-bis(triethoxysilylpropyl) disulfide and/or 3,3'-bis(triethoxysilylpropyl)
tetrasulfide. Therefore, as to formula I, Z' may be
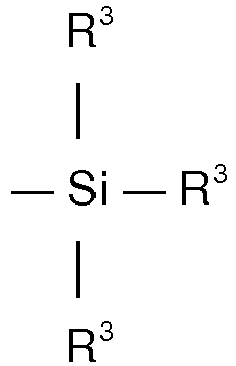
where R
3 is an alkoxy of 2 to 4 carbon atoms, alternatively 2 carbon atoms; alk is a divalent
hydrocarbon of 2 to 4 carbon atoms, alternatively with 3 carbon atoms; and n is an
integer of from 2 to 5, alternatively 2 or 4.
[0083] In another embodiment, suitable sulfur containing organosilicon compounds include
compounds disclosed in
US-B- 6,608,125. In one embodiment, the sulfur containing organosilicon compounds includes 3-(octanoylthio)-1-propyltriethoxysilane,
CH
3(CH
2)
6C(=O) -S-CH
2CH
2CH
2Si(OCH
2CH
3)
3, which is available commercially as NXT™ from Momentive Performance Materials.
[0084] In another embodiment, suitable sulfur containing organosilicon compounds include
those disclosed in
US-A- 2003/0130535. In one embodiment, the sulfur containing organosilicon compound is Si-363 from Degussa.
[0085] The amount of the sulfur containing organosilicon compound in a rubber composition
will vary depending on the level of other additives that are used. Generally speaking,
the amount of the compound will range from 0.5 to 20 phr. In one embodiment, the amount
will range from 1 to 10 phr.
[0086] It is readily understood by those having skill in the art that the rubber composition
would be compounded by methods generally known in the rubber compounding art, such
as mixing the various sulfur-vulcanizable constituent rubbers with various commonly
used additive materials such as, for example, sulfur donors, curing aids, such as
activators and retarders and processing additives, such as oils, resins including
tackifying resins and plasticizers, fillers, pigments, fatty acid, zinc oxide, waxes,
antioxidants and antiozonants and peptizing agents. As known to those skilled in the
art, depending on the intended use of the sulfur vulcanizable and sulfur-vulcanized
material (rubbers), the additives mentioned above are selected and commonly used in
conventional amounts. Representative examples of sulfur donors include elemental sulfur
(free sulfur), an amine disulfide, polymeric polysulfide and sulfur olefin adducts.
In one embodiment, the sulfur-vulcanizing agent is elemental sulfur. The sulfur-vulcanizing
agent may be used in an amount ranging from 0.5 to 8 phr, alternatively with a range
of from 1.5 to 6 phr. Typical amounts of tackifier resins, if used, comprise 0.5 to
10 phr, usually 1 to 5 phr. Typical amounts of processing aids comprise 1 to 50 phr.
Typical amounts of antioxidants comprise 1 to 5 phr. Representative antioxidants may
be, for example, diphenyl-p-phenylenediamine and others, such as, for example, those
disclosed in
The Vanderbilt Rubber Handbook (1978), Pages 344 through 346. Typical amounts of antiozonants comprise 1 to 5 phr. Typical amounts of fatty acids,
if used, which can include stearic acid comprise 0.5 to 3 phr. Typical amounts of
zinc oxide comprise 1 to 5 phr. Typical amounts of waxes comprise 1 to 5 phr. Often
microcrystalline waxes are used. Typical amounts of peptizers comprise 0.1 to 1 phr.
Typical peptizers may be, for example, pentachlorothiophenol and dibenzamidodiphenyl
disulfide.
[0087] Accelerators are used to control the time and/or temperature required for vulcanization
and to improve the properties of the vulcanizate. In one embodiment, a single accelerator
system may be used, i.e., primary accelerator. The primary accelerator(s) may be used
in total amounts ranging from 0.5 to 4, alternatively 0.8 to 1.5, phr. In another
embodiment, combinations of a primary and a secondary accelerator might be used with
the secondary accelerator being used in smaller amounts, such as from 0.05 to 3 phr,
in order to activate and to improve the properties of the vulcanizate. In addition,
delayed action accelerators may be used which are not affected by normal processing
temperatures but produce a satisfactory cure at ordinary vulcanization temperatures.
Vulcanization retarders might also be used. Suitable types of accelerators that may
be used in the present invention are amines, disulfides, guanidines, thioureas, thiazoles,
thiurams, sulfenamides, dithiocarbamates and xanthates. In one embodiment, the primary
accelerator is a sulfenamide. If a second accelerator is used, the secondary accelerator
may be a guanidine, dithiocarbamate or thiuram compound.
[0088] The mixing of the rubber composition can be accomplished by methods known to those
having skill in the rubber mixing art. For example, the ingredients are typically
mixed in at least two stages, namely, at least one non-productive stage followed by
a productive mix stage. The final curatives including sulfur-vulcanizing agents are
typically mixed in the final stage which is conventionally called the "productive"
mix stage in which the mixing typically occurs at a temperature, or ultimate temperature,
lower than the mix temperature(s) than the preceding non-productive mix stage(s).
The rubber composition may be subjected to a thermomechanical mixing step. The thermomechanical
mixing step generally comprises a mechanical working in a mixer or extruder for a
period of time suitable in order to produce a rubber temperature between 140°C and
190°C. The appropriate duration of the thermomechanical working varies as a function
of the operating conditions, and the volume and nature of the components. For example,
the thermomechanical working may be from 1 to 20 minutes.
[0089] The rubber composition may be incorporated in a variety of rubber components of the
tire. For example, the rubber component may be a tread (including tread cap and tread
base), sidewall, apex, chafer, sidewall insert, wirecoat or innerliner. In one embodiment,
the component is a tread.
[0090] The pneumatic tire of the present invention may be a race tire, passenger tire, aircraft
tire, agricultural, earthmover, off-the-road or truck tire. In one embodiment, the
tire is a passenger or truck tire. The tire may also be a radial or bias.
[0091] Vulcanization of the pneumatic tire of the present invention is generally carried
out at conventional temperatures ranging from 100°C to 200°C. In one embodiment, the
vulcanization is conducted at temperatures ranging from 110°C to 180°C. Any of the
usual vulcanization processes may be used such as heating in a press or mold, heating
with superheated steam or hot air. Such tires can be built, shaped, molded and cured
by various methods which are known and will be readily apparent to those having skill
in such art.
1. A method of providing a passageway in a tire, the method comprising:
providing a filament (58) coated with a coating material (92), the coating material
(92) comprising at least one diene based elastomer and a material containing therein
a liquid or a solid capable of generating a gas upon vaporization, decomposition,
or a chemical reaction under heating;
encasing the coated filament (104) into containment within an uncured or a pre-cured
flexible tire component (70);
building a green tire from tire components including the uncured or pre-cured flexible
tire component (70) and the encased coated filament (104);
curing the green tire including the flexible tire component (70) containing the coated
filament (104); and
removing the filament (58) from the cured flexible tire component to leave within
the flexible tire component a substantially unobstructed air passageway (80).
2. The method of claim 1 wherein the material containing therein a liquid or a solid
is a thermoplastic resin or is or comprises heat expandable thermoplastic resin particles,
the thermoplastic resin or the heat expandable thermoplastic resin particles containing
therein said liquid or solid capable of generating a gas upon vaporization, decomposition,
or a chemical reaction under heating.
3. The method of claim 1 or 2 wherein the uncured or pre-cured flexible tire component
(70) is a tire carcass component, a tire sidewall component, a tire tread component,
a tire chafer component, or a tire apex component.
4. The method of at least one of the previous claims wherein the coated filament (104)
extends between an air inlet and an air outlet cavity in the uncured or pre-cured
flexible tire component (70).
5. The method of at least one of the previous claims further comprising removing the
filament (58) axially from the cured flexible tire component by means of drawing a
free end of the filament (58).
6. The method of at least one of the previous claims further comprising inserting a temporary
air inlet assembly into an air inlet cavity prior to curing the green tire and/or
inserting a temporary air outlet assembly into an air outlet cavity prior to curing
the green tire; and removing the temporary air inlet assembly and/or the temporary
air outlet assembly after curing the green tire.
7. The method of claim 6 wherein the temporary air inlet assembly is a pre-cured temporary
air inlet assembly and wherein the temporary air outlet assembly is a pre-cured temporary
air outlet assembly.
8. The method of claim 6 or 7, further comprising extending the air outlet assembly through
a tire sidewall into communication with a tire cavity.
9. The method of claim 6, 7 or 8, further comprising extending the air outlet assembly
through a tire sidewall into air flow communication between the unobstructed air passageway
and a tire cavity.
10. The method of at least one of the previous claims further comprising:
encasing the coated filament into a containment with the uncured or pre-cured flexible
tire component by:
forming a channel into the uncured or pre-cured flexible tire component defined by
channel sidewalls and a channel bottom wall;
inserting the coated filament (104) into the channel; and
collapsing a flexible channel sidewall over the coated filament (104).
11. The method of claim 10 wherein forming a channel into the uncured or pre-cured flexible
tire component is by extruding the uncured flexible tire component with the channel
formed therein.
12. A coated filament comprising a filament (58) and a coating material (92) coating the
filament (58), the coating material (92) comprising at least one diene based elastomer
and a material containing therein a liquid or a solid capable of generating a gas
upon vaporization, decomposition, or a chemical reaction under heating.
13. The coated filament of claim 12 wherein the material containing therein a liquid or
a solid is a thermoplastic resin or is or comprises heat expandable thermoplastic
resin particles, the thermoplastic resin or the heat expandable thermoplastic resin
particles containing therein said liquid or solid capable of generating a gas upon
vaporization, decomposition, or a chemical reaction under heating.
14. The coated filament of claim 12 or 13 wherein the filament is a polyamide filament,
a polyester filament, or a poly(vinyl alcohol) filament; and/or wherein the material
or the heat expandable thermoplastic resin particles are (meth)acrylonitrile polymer
particles or copolymer particles preferably having a high content of (meth)acrylonitrile.
15. The coated filament of at least one of the claims 12 to 14 wherein the liquid or solid
capable of generating a gas upon vaporization, decomposition, or a chemical reaction
under heating is a hydrocarbon such as n-pentane, isopentane, neopentane, butane,
isobutane, hexane, and petroleum ether; a chlorinated hydrocarbon such as methyl chloride,
methylene chloride, dichloroethylene, trichloroethane, and trichloroethylene; or azodicarbonamide,
dinitrosopentamethylene-tetramine, azobisisobutyronitrile, a toluenesulfonyl hydrazide
derivative, or aromatic succinyl hydrazide.