FIELD OF THE INVENTION
[0001] This invention concerns reducing deposit formation in a centrifuge system in a trunk
piston diesel engine.
BACKGROUND OF THE INVENTION
[0002] Trunk piston diesel engines are used in marine, power generation and rail traction
applications and may have a rated speed of between 300 and 1000 rpm. In trunk piston
diesel engines, a single lubricant composition is used for crankcase and cylinder
lubrication. All major moving parts of the engine, i.e. the main and big end bearings,
camshaft and valve gear, are lubricated by a pumped circulation system. The cylinder
liners are lubricated partially by splash lubrication and partially by oil from the
circulation system which finds its way to the cylinder wall through holes in the piston
skirt via the connecting rod and gudgeon pin.
[0003] Trunk piston diesel engines use a centrifuge system to remove contaminants such as,
for example, soot or water, from the lubricant composition. The centrifuge system
relies on the use of a sealing medium that is heavier than the lubricant. The sealing
medium is generally water. When the lubricant composition passes through the centrifuge
system, it comes into contact with the water. The lubricant therefore needs to be
capable of shedding the water and remaining stable in the presence of water. If the
lubricant is unable to shed the water, the water builds up in the lubricant forming
an emulsion, which leads to deposits building up in the centrifuge system and prevents
the centrifuge system from working properly. The centrifuge system normally operates
at temperatures of less than 100°C, such as less than 95°C, e.g. around 90°C.
[0004] Traditional trunk piston diesel engine lubricant compositions have a total base number
of 30-40. However, the recent development of trunk piston diesel engines having very
low oil consumption has resulted in lubricant formulators increasing the total base
number up to, for example, 50-60. Unfortunately, this increase in total base number
affects the ability of the lubricant composition to shed any contamination with the
sealing medium used in the centrifuge systems, resulting in deposits building up in
the centrifuge system.
[0005] The aim of the present invention is to provide for the reduction of deposit formation
in a centrifuge system in a trunk piston diesel engine.
[0006] US-A-2008/0287329 Al ("'329") describes a lubricant oil for a marine four-stroke engine that includes
1 to 20 % by weight of at least one polyisobutylene. '329 states that the increase
of viscosity of such lubricant oils is slowed down. However, '329 makes no mention
of the above-mentioned deposit formation problem in the centrifuge of trunk piston
engines.
SUMMARY OF THE INVENTION
[0007] It is now found that a polyisobutylene additive in a trunk piston engine oil lubricant
enables the above deposit formation to be overcome.
[0008] Thus, the present invention provides the use of a polyisobutylene of number-average
molecular weight in the range of 400 to 8000, such as 1,300 to 2,225, and having a
kinematic viscosity at 100°C in the range of 50 to 50,000, such as 630 to 2,500, mm
2/sec, as an additive constituting 1-25 mass % of a trunk piston diesel engine lubricant
composition to reduce deposit formation in a centrifuge in a trunk piston diesel engine
when the composition is lubricating the engine during its operation.
[0009] Preferably, the trunk piston diesel engine lubricant composition contains little
or no brightstock. Preferably, the trunk piston diesel engine lubricant composition
is substantially free of brightstock. Even more preferably, the trunk piston diesel
engine lubricant composition contains no brightstock.
[0010] In this specification, the following words and expressions, if and when used, have
the meanings ascribed below:
"active ingredients" or "(a.i.)" refers to additive material that is not diluent or
solvent;
"comprising" or any cognate word specifies the presence of stated features, steps,
or integers or components, but does not preclude the presence or addition of one or
more other features, steps, integers, components or groups thereof; the expressions
"consists of" or "consists essentially of" or cognates may be embraced within "comprises"
or cognates, wherein "consists essentially of" permits inclusion of substances not
materially affecting the characteristics of the composition to which it applies;
"major amount" means 50 mass % or more of a composition;
"minor amount" means less than 50 mass % of a composition;
"TBN" means total base number as measured by ASTM D2896.
[0011] Furthermore in this specification, if and when used:
"calcium content" is as measured by ASTM 4951;
"phosphorus content" is as measured by ASTM D5185;
"sulphated ash content" is as measured by ASTM D874;
"sulphur content" is as measured by ASTM D2622;
"KV 100" means kinematic viscosity at 100°C as measured by ASTM D445.
[0012] Also, it will be understood that various components used, essential as well as optimal
and customary, may react under conditions of formulation, storage or use and that
the invention also provides the product obtainable or obtained as a result of any
such reaction.
[0013] Further, it is understood that any upper and lower quantity, range and ratio limits
set forth herein may be independently combined.
DETAILED DESCRIPTION OF THE INVENTION
[0014] The features of the invention will now be discussed in more detail below.
OIL OF LUBRICATING VISCOSITY
[0015] The lubricant of composition contains a major proportion of an oil of lubricating
viscosity. Such lubricating oils may range in viscosity from light distillate mineral
oils to heavy lubricating oils. Generally, the viscosity of the oil ranges from 2
to 40, such as 3 to 15, mm
2/sec, as measured at 100°C, and a viscosity index of 80 to 100, such as 90 to 95.
The lubricating oil may comprise greater than 60, typically greater than 70. mass
% of the composition.
[0016] The oil may include 'brightstock' which refers to base oils which are solvent-extracted,
de-asphalted products from vacuum residuum generally having a kinematic viscosity
at 100°C of from 28 to 36 mm
2s
-1. It is, however, preferred that little or no brightstock is included, for example
less than 5, 4, 3, 2 or 1 mass %, based on the mass of the composition. Brightstock
may be completely or substantially absent.
[0017] Natural oils include animal oils and vegetable oils (e.g., castor oil, lard oil);
liquid petroleum oils and hydrorefined, solvent-treated or acid-treated mineral oils
of the paraffinic, naphthenic and mixed paraffinic-naphthenic types. Oils of lubricating
viscosity derived from coal or shale also serve as useful base oils.
[0018] Synthetic lubricating oils include hydrocarbon oils and halo-substituted hydrocarbon
oils such as polymerized and interpolymerized olefins (e.g., polybutylenes, polypropylenes,
propylene-isobutylene copolymers, chlorinated polybutylenes, poly(1-hexenes), poly(1-octenes),
poly(1-decenes)); alkybenzenes (e.g., dodecylbenzenes, tetradecylbenzenes, dinonylbenzenes,
di(2-ethylhexyl)benzenes); polyphenyls (e.g., biphenyls, terphenyls, alkylated polyphenols);
and alkylated diphenyl ethers and alkylated diphenyl sulphides and derivative, analogues
and homologues thereof.
[0019] Alkylene oxide polymers and interpolymers and derivatives thereof where the terminal
hydroxyl groups have been modified by esterification, etherification, etc., constitute
another class of known synthetic lubricating oils. These are exemplified by polyoxyalkylene
polymers prepared by polymerization of ethylene oxide or propylene oxide, and the
alkyl and aryl ethers of polyoxyalkylene polymers (e.g., methyl-polyiso-propylene
glycol ether having a molecular weight of 1000 or diphenyl ether of poly-ethylene
glycol having a molecular weight of 1000 to 1500); and mono- and polycarboxylic esters
thereof, for example, the acetic acid esters, mixed C
3-C
8 fatty acid esters and C
13 oxo acid diester of tetraethylene glycol.
[0020] Another suitable class of synthetic lubricating oils comprises the esters of dicarboxylic
acids (e.g., phthalic acid, succinic acid, alkyl succinic acids and alkenyl succinic
acids, maleic acid, azelaic acid, suberic acid, sebacic acid, fumaric acid, adipic
acid, linoleic acid dimer, malonic acid, alkylmalonic acids, alkenyl malonic acids)
with a variety of alcohols (e.g., butyl alcohol, hexyl alcohol, dodecyl alcohol, 2-ethylhexyl
alcohol, ethylene glycol, diethylene glycol monoether, propylene glycol). Specific
examples of such esters includes dibutyl adipate, di(2-ethylhexyl) sebacate, di-n-hexyl
fumarate, dioctyl sebacate, diisooctyl azelate, diisodecyl azelate, dioctyl phthalate,
didecyl phthalate, dieicosyl sebacate, the 2-ethylhexyl diester of linoleic acid dimer,
and the complex ester formed by reacting one mole of sebacic acid with two moles oftetraethylene
glycol and two moles of 2-ethylhexanoic acid.
[0021] Esters useful as synthetic oils also include those made from C
5 to C
12 monocarboxylic acids and polyols and polyol esters such as neopentyl glycol, trimethylolpropane,
pentaerythritol, dipentaerythritol and tripentaerythritol.
[0022] Silicon-based oils such as the polyalkyl-, polyaryl-, polyalkoxy- or polyaryloxysilicone
oils and silicate oils comprise another useful class of synthetic lubricants; such
oils include tetraethyl silicate, tetraisopropyl silicate, tetra-(2-ethylhexyl)silicate,
tetra-(4-methyl-2-ethylhexyl)silicate, tetra-(p-tert-butyl-phenyl) silicate, hexa-(4-methyl-2-ethylhexyl)disiloxane,
poly(methyl)siloxanes and poly(methylphenyl)siloxanes. Other synthetic lubricating
oils include liquid esters of phosphorus-containing acids (e.g., tricresyl phosphate,
trioctyl phosphate, diethyl ester of decylphosphonic acid) and polymeric tetrahydrofurans.
[0023] Unrefined, refined and re-refined oils can be used in lubricants of the present invention.
Unrefined oils are those obtained directly from a natural or synthetic source without
further purification treatment. For example, a shale oil obtained directly from retorting
operations; petroleum oil obtained directly from distillation; or ester oil obtained
directly from esterification and used without further treatment are unrefined oils.
POLYISOBUTYLENE
[0024] The polyisobutylene additive may be present in the following proportions: 1 to 20,
or 1 to 15, such as 1-10, such as 1-6, such as 1-5, such as 1-4 mass percent.
[0025] As mentioned above, the polyisobutylene has a number-average weight in the range
of 400 to 8,000, such as 1,300 to 2,225. Among other ranges that may be used, the
following may be mentioned: 900 - 3,000, 1,000 - 8,000, 1,500 - 6,000 and 2,000 -
5,000, and also a lower limit of 500.
[0026] Also, the polyisobutylene has a kinematic viscosity at 100°C in the range of 50 to
50,000, such as 630 to 2,500, mm
2/sec. Among other ranges that may be used, the following may be mentioned: 2,000 -
6,000, 2,000 - 5,000, and 3,000 - 4,500, mm
2/stc. Polyisobutylene also embraces mixtures of several polyisobutylenes, synthesised
separately and possibly having molecular weights outside the ranges of values indicated
above, provided that the mixture of the various polyisobutylenes has a molecular weight
lying within said ranges.
[0027] Polyisobutylene is commercially available.
CO-ADDITIVES
[0028] One or more of the following may also be indicated in the composition.
Detergents
[0029] A detergent is an additive that reduces formation of deposits, for example, high-temperature
varnish and lacquer deposits, in engines; it has acid-neutralising properties and
is capable of keeping finely divided solids in suspension. It is based on metal "soaps",
that is metal salts of acidic organic compounds, sometimes referred to as surfactants.
[0030] A detergent comprises a polar head with a long hydrophobic tail. Large amounts of
a metal base are included by reacting an excess of a metal compound, such as an oxide
or hydroxide, with an acidic gas such as carbon dioxide to give an overbased detergent
which comprises neutralised detergent as the outer layer of a metal base (e.g. carbonate)
micelle.
[0031] The detergent is preferably an alkali metal or alkaline earth metal additive such
as an overbased oil-soluble or oil-dispersible calcium, magnesium, sodium or barium
salt of a surfactant selected from phenol, sulphonic acid, carboxylic acid, salicylic
acid and naphthenic acid, wherein the overbasing is provided by an oil-insoluble salt
of the metal, e.g. carbonate, basic carbonate, acetate, formate, hydroxide or oxalate,
which is stabilised by the oil-soluble salt of the surfactant. The metal of the oil-soluble
surfactant salt may be the same or different from that of the metal of the oil-insoluble
salt. Preferably the metal, whether the metal of the oil-soluble or oil-insoluble
salt, is calcium.
[0032] The TBN of the detergent may be low, i.e. less than 50 mg KOH/g, medium, i.e. 50-150
mg KOH/g, or high, i.e. over 150 mg KOH/g, as determined by ASTM D2896. Preferably
the TBN is medium or high, i.e. more than 50 TBN. More preferably, the TBN is at least
60, more preferably at least 100, more preferably at least 150, and up to 500, such
as up to 350 mg KOH/g, as determined by ASTM D2896.
[0033] Surfactants for the surfactant system of the overbased detergent preferably contain
at least one hydrocarbyl group, for example, as a substituent on an aromatic ring.
The term "hydrocarbyl" as used herein means that the group concerned is primarily
composed of hydrogen and carbon atoms and is bonded to the remainder of the molecule
via a carbon atom but does not exclude the presence of other atoms or groups in a
proportion insufficient to detract from the substantially hydrocarbon characteristics
of the group. Advantageously, hydrocarbyl groups in surfactants for use in accordance
with the invention are aliphatic groups, preferably alkyl or alkylene groups, especially
alkyl groups, which may be linear or branched. The total number of carbon atoms in
the surfactants should be at least sufficient to impart the desired oil-so lubility.
[0034] Phenols, for use in preparing the detergents may be non-sulphurized or, preferably,
sulphurized. Further, the term "phenol" as used herein includes phenols containing
more than one hydroxyl group (for example, alkyl catechols) or fused aromatic rings
(for example, alkyl naphthols) and phenols which have been modified by chemical reaction,
for example, alkylene-bridged phenols and Mannich base-condensed phenols; and saligenin-type
phenols (produced by the reaction of a phenol and an aldehyde under basic conditions).
[0035] Preferred phenols may be derived from the formula
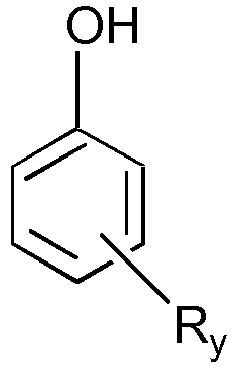
where R represents a hydrocarbyl group and y represents 1 to 4. Where y is greater
than 1, the hydrocarbyl groups may be the same or different.
[0036] The phenols are frequently used in sulphurized form. Sulphurized hydrocarbyl phenols
may typically be represented by the formula:

where x is generally from 1 to 4. In some cases, more than two phenol molecules may
be linked by S
x bridges.
[0037] In the above formulae, hydrocarbyl groups represented by R are advantageously alkyl
groups, which advantageously contain 5 to 100, preferably 5 to 40, especially 9 to
12, carbon atoms, the average number of carbon atoms in all of the R groups being
at least 9 in order to ensure adequate solubility in oil. Preferred alkyl groups are
nonyl (tripropylene) groups.
[0038] In the following discussion, hydrocarbyl-substituted phenols will for convenience
be referred to as alkyl phenols.
[0039] A sulphurizing agent for use in preparing a sulphurized phenol or phenate may be
any compound or element which introduces -(S)
x- bridging groups between the alkyl phenol monomer groups, wherein x is generally
from 1 to about 4. Thus, the reaction may be conducted with elemental sulphur or a
halide thereof, for example, sulphur dichloride or, more preferably, sulphur monochloride.
If elemental sulphur is used, the sulphurization reaction may be effected by heating
the alkyl phenol compound at from 50 to 250, preferably at least 100, °C. The use
of elemental sulphur will typically yield a mixture of bridging groups -(S)x- as described
above. If a sulphur halide is used, the sulphurization reaction may be effected by
treating the alkyl phenol at from -10 to 120, preferably at least 60, °C. The reaction
may be conducted in the presence of a suitable diluent. The diluent advantageously
comprises a substantially inert organic diluent, for example mineral oil or an alkane.
In any event, the reaction is conducted for a period of time sufficient to effect
substantial reaction. It is generally preferred to employ from 0.1 to 5 moles of the
alkyl phenol material per equivalent of sulphurizing agent.
[0040] Where elemental sulphur is used as the sulphurizing agent, it may be desirable to
use a basic catalyst, for example, sodium hydroxide or an organic amine, preferably
a heterocyclic amine (e.g., morpholine).
[0041] Details of sulphurization processes are well known to those skilled in the art.
[0042] Regardless of the manner in which they are prepared, sulphurized alkyl phenols useful
in preparing overbased detergents generally comprise diluent and unreacted alkyl phenols
and generally contain from 2 to 20 mass %, preferably 4 to 14 mass %, and most preferably
6 to 12 mass%, sulphur based on the mass of the sulphurized alkyl phenol.
[0043] As indicated above, the term "phenol" as used herein includes phenols that have been
modified by chemical reaction with, for example, an aldehyde, and Mannich base-condensed
phenols.
[0044] Aldehydes with which phenols may be modified include, for example, formaldehyde,
propionaldehyde and butyraldehyde. The preferred aldehyde is formaldehyde. Aldehyde-modified
phenols suitable for use are described in, for example,
US-A-5 259 967.
[0045] Mannich base-condensed phenols are prepared by the reaction of a phenol, an aldehyde
and an amine. Examples of suitable Mannich base-condensed phenols are described in
GB-A-2 121 432.
[0046] In general, the phenols may include substituents other than those mentioned above
provided that such substituents do not detract significantly from the surfactant properties
of the phenols. Examples of such substituents are methoxy groups and halogen atoms.
[0047] Salicylic acids used in accordance with the invention may be non-sulphurized or sulphurized,
and may be chemically modified and/or contain additional substituents, for example,
as discussed above for phenols. Processes similar to those described above may also
be used for sulphurizing a hydrocarbyl-substituted salicylic acid, and are well known
to those skilled in the art. Salicylic acids are typically prepared by the carboxylation,
by the Kolbe-Schmitt process, of phenoxides, and in that case, will generally be obtained
(normally in a diluent) in admixture with uncarboxylated phenol.
[0048] Preferred substituents in oil-soluble salicylic acids from which overbased detergents
in accordance with the invention may be derived are the substituents represented by
R in the above discussion of phenols. In alkyl-substituted salicylic acids, the alkyl
groups advantageously contain 5 to 100, preferably 9 to 30, especially 14 to 20, carbon
atoms.
[0049] Sulphonic acids used in accordance with the invention are typically obtained by sulphonation
of hydrocarbyl-substituted, especially alkyl-substituted, aromatic hydrocarbons, for
example, those obtained from the fractionation of petroleum by distillation and/or
extraction, or by the alkylation of aromatic hydrocarbons. Examples include those
obtained by alkylating benzene, toluene, xylene, naphthalene, biphenyl or their halogen
derivatives, for example, chlorobenzene, chlorotoluene or chloronaphthalene. Alkylation
of aromatic hydrocarbons may be carried out in the presence of a catalyst with alkylating
agents having from 3 to more than 100 carbon atoms, such as, for example, haloparaffins,
olefins that may be obtained by dehydrogenation of paraffins, and polyolefins, for
example, polymers of ethylene, propylene, and/or butene. The alkylaryl sulphonic acids
usually contain from 7 to 100 or more carbon atoms. They preferably contain from 16
to 80, or 12 to 40, carbon atoms per alkyl-substituted aromatic moiety, depending
on the source from which they are obtained.
[0050] When neutralizing these alkylaryl sulphonic acids to provide sulphonates, hydrocarbon
solvents and/or diluent oils may also be included in the reaction mixture, as well
as promoters and viscosity control agents.
[0051] Another type of sulphonic acid that may be used in accordance with the invention
comprises alkyl phenol sulphonic acids. Such sulphonic acids can be sulphurized. Whether
sulphurized or non-sulphurized these sulphonic acids are believed to have surfactant
properties comparable to those of sulphonic acids, rather than surfactant properties
comparable to those of phenols.
[0052] Sulphonic acids suitable for use in accordance with the invention also include alkyl
sulphonic acids, such as alkenyl sulphonic acids. In such compounds the alkyl group
suitably contains 9 to 100, advantageously 12 to 80, especially 16 to 60, carbon atoms.
[0053] Carboxylic acids that may be used in accordance with the invention include mono-
and dicarboxylic acids. Preferred monocarboxylic acids are those containing 1 to 30,
especially 8 to 24, carbon atoms. (Where this specification indicates the number of
carbon atoms in a carboxylic acid, the carbon atom(s) in the carboxylic group(s) is/are
included in that number.) Examples of monocarboxylic acids are iso-octanoic acid,
stearic acid, oleic acid, palmitic acid and behenic acid. Iso-octanoic acid may, if
desired, be used in the form of the mixture of C
8 acid isomers sold by Exxon Chemicals under the trade name "Cekanoic". Other suitable
acids are those with tertiary substitution at the α-carbon atom and dicarboxylic acids
with more than 2 carbon atoms separating the carboxylic groups. Further, dicarboxylic
acids with more than 35, for example, 36 to 100, carbon atoms are also suitable. Unsaturated
carboxylic acids can be sulphurized. Although salicylic acids contain a carboxylic
group, for the purposes of the present invention they are considered to be a separate
group of surfactants, and are not considered to be carboxylic acid surfactants. (Nor,
although they contain a hydroxyl group, are they considered to be phenol surfactants.)
[0054] Examples of other surfactants which may be used in accordance with the invention
include the following compounds, and derivatives thereof: naphthenic acids, especially
naphthenic acids containing one or more alkyl groups, dialkylphosphonic acids, dialkylthiophosphonic
acids, and dialkyldithiophosphoric acids, high molecular weight (preferably ethoxylated)
alcohols, dithiocarbamic acids, thiophosphines, and dispersants. Surfactants of these
types are well known to those skilled in the art. Surfactants of the hydrocarbyl-substituted
carboxylalkylene-linked phenol type, or dihydrocarbyl esters of alkylene dicarboxylic
acids, the alkylene group being substituted with a hydroxy group and an additional
carboxylic acid group, or alkylene-linked polyaromatic molecules, the aromatic moieties
whereof comprise at least one hydrocarbyl-substituted phenol and at least one carboxy
phenol, may also be suitable for use in the present invention; such surfactants are
described in
EP-A-708 171.
[0055] Further examples of detergents useful in the present invention are optionally sulphurized
alkaline earth metal hydrocarbyl phenates that have been modified by carboxylic acids
such as stearic acid, for examples as described in
EP-A- 271 262 (LZ-Adibis); and phenolates as described in
EP-A- 750 659 (Chevron).
[0056] Also suitable for use in the present invention are overbased metal compounds, preferably
overbased calcium detergents, that contain at least two surfactant groups, such as
phenol, sulphonic acid, carboxylic acid, salicylic acid and naphthenic acid, that
may be obtained by manufacture of a hybrid material in which two or more different
surfactant groups are incorporated during the overbasing process.
[0057] Examples of hybrid materials are an overbased calcium salt of surfactants phenol
and sulphonic acid; an overbased calcium salt of surfactants phenol and carboxylic
acid; an overbased calcium salt of surfactants phenol, sulphonic acid and salicylic
acid; and an overbased calcium salt of surfactants phenol and salicylic acid.
[0058] In the instance where at least two overbased metal compounds are present, any suitable
proportions by mass may be used, preferably the mass to mass proportion of any one
overbased metal compound to any other metal overbased compound is in the range of
from 5:95 to 95:5; such as from 90:10 to 10:90; more preferably from 20:80 to 80:20;
especially from 70:30 to 30:70; advantageously from 60:40 to 40:60.
[0059] The hybrid detergent preferably includes at least 5 mass% of salicylate, more preferably
at least 10 mass% of salicylate. The hybrid detergent preferably includes at least
5 mass% of phenate. The amount of salicylate and phenate in the hybrid detergent can
be determined using techniques such as chromatography, spectroscopy and/or titration,
well known to persons skilled in the art. The hybrid detergent may also include other
surfactants such as sulphonate, sulphurized phenate, thiophosphate, naphthenate, or
oil-soluble carboxylate. The hybrid detergent may include at least 5 mass% of sulphonate.
The surfactant groups are incorporated during the overbasing process.
[0061] By an "overbased calcium salt of surfactants" is meant an overbased detergent in
which the metal cations of the oil-insoluble metal salt are essentially calcium cations.
Small amounts of other cations may be present in the oil-insoluble metal salt, but
typically at least 80, more typically at least 90, for example at least 95, mole %,
of the cations in the oil-insoluble metal salt, are calcium ions. Cations other than
calcium may be derived, for example, from the use in the manufacture of the overbased
detergent of a surfactant salt in which the cation is a metal other than calcium.
Preferably, the metal salt of the surfactant is also calcium.
[0062] Preferably, the TBN of the hybrid detergent is at least 300 mg KOH/g, such as at
least 330 mg KOH/g, more preferably at least 350 mg KOH/g, more preferably at least
400 mg KOH/g, most preferably in the range of from 400 to 600 mg KOH/g, such as up
to 500 mg KOH/g, as determined by ASTM D2896.
[0063] Preferably, the amount of overbased metal detergent in the lubricant is at least
0.5, preferably in the range of from 5 to 50, more preferably from 10 to 50, mass
% based on the total amount of the lubricant composition.
[0064] The overbased metal detergents may or may not be borated, and typically the boron
contributing compound, e.g the metal borate, is considered to form part of the overbasing.
The detergent may include both a non-borated detergent and a borated detergent.
[0065] The overbased metal detergents preferably have a sulphated ash content (as determined
by ASTM D874) of at least 0.85%, more preferably at least 1.0% and even more preferably
at least 1.2%.
[0066] The detergent or detergents may include phenol as an unreacted component and, if
so, the amount of phenol contributes to the total phenol content present in the trunk
piston diesel engine lubricant composition. All of the phenol present in the trunk
piston diesel engine lubricant composition may come from the detergent or detergents.
[0067] The trunk piston engine oil preferably also includes at least one dispersant, anti-wear
additive or anti-oxidant.
Dispersants
[0068] The trunk piston diesel engine lubricant composition may include at least one dispersant.
A dispersant is an additive for a lubricating composition whose primary function is
to improve engine cleanliness.
[0069] A noteworthy class of dispersants are "ashless", meaning a non-metallic organic material
that forms substantially no ash on combustion, in contrast to metal-containing, hence
ash-forming, materials. Ashless dispersants comprise a long chain hydrocarbon with
a polar head, the polarity being derived from inclusion of, e.g. an O, P or N atom.
The hydrocarbon is an oleophilic group that confers oil-solubility, having for example
40 to 500 carbon atoms. Thus, ashless dispersants may comprise an oil-soluble polymeric
hydrocarbon backbone having functional groups that are capable of associating with
particles to be dispersed.
[0070] Examples of ashless dispersants are succinimides, e.g. polyisobutene succinic anhydride;
and polyamine condensation products that may be borated or unborated.
[0071] If present, the dispersant is preferably present in an amount from 0.5 to 5 mass
%, based on the total amount of the lubricant composition.
Anti-wear Additive
[0072] The trunk piston diesel engine lubricant composition may include at least one anti-wear
additive. The anti-wear additive may be metallic or non-metallic, preferably the former.
[0073] Dihydrocarbyl dithiophosphate metal salts are examples of the anti-wear additives.
The metal in the dihydrocarbyl dithiophosphate may be an alkali or alkaline earth
metal, or aluminium, lead, tin, molybdenum, manganese, nickel or copper. Zinc salts
are preferred, preferably in the range of 0.1 to 1.5, preferably 0.5 to 1.3, mass
%, based upon the total mass of the lubricating oil composition. They may be prepared
in accordance with known techniques by firstly forming a dihydrocarbyl dithiophosphoric
acid (DDPA), usually by reaction of one or more alcohols or a phenol with P
2S
5 and then neutralizing the formed DDPA with a zinc compound. For example, a dithiophosphoric
acid may be made by reacting mixtures of primary and secondary alcohols. Alternatively,
multiple dithiophosphoric acids can be prepared comprising both hydrocarbyl groups
that are entirely secondary and hydrocarbyl groups that are entirely primary. To make
the zinc salt, any basic or neutral zinc compound may be used but the oxides, hydroxides
and carbonates are most generally employed. Commercial additives frequently contain
an excess of zinc due to use of an excess of the basic zinc compound in the neutralisation
reaction.
[0074] The preferred zinc dihydrocarbyl dithiophosphates are oil-soluble salts of dihydrocarbyl
dithiophosphoric acids and may be represented by the following formula:
[(RO) (R
1O) P(S)S]
2 Zn
where R and R
1 may be the same or different hydrocarbyl radicals containing from 1 to 18, preferably
2 to 12, carbon atoms and including radicals such as alkyl, alkenyl, aryl, arylalkyl,
alkaryl and cycloaliphatic radicals. Particularly preferred as R and R
1 groups are alkyl groups of 2 to 8 carbon atoms. Thus, the radicals may, for example,
be ethyl, n-propyl, I-propyl, n-butyl, I-butyl, sec-butyl, amyl, n-hexyl, I-hexyl,
n-octyl, decyl, dodecyl, octadecyl, 2-ethylehexyl, phenyl, butylphenyl, cyclohexyl,
methylcyclopentyl, propenyl, butenyl. In order to obtain oil-solubility, the total
number of carbon atoms (i.e. in R and R
1) in the dithiophoshoric acid will generally be 5 or greater. The zinc dihydrocarbyl
dithiophosphate can therefore comprise zinc dialkyl dithiophosphates.
[0075] If present, the anti-wear additive is preferably present in an amount from 0.10 to
3.0 mass %, based on the total amount of the lubricant composition.
Anti-oxidants
[0076] The trunk piston diesel engine lubricant composition may include at least one anti-oxidant.
The anti-oxidant may be aminic or phenolic. As examples of amines there may be mentioned
secondary aromatic amines such as diarylamines, for example diphenylamines wherein
each phenyl group is alkyl-substituted with an alkyl group having 4 to 9 carbon atoms.
As examples of anti-oxidants there may be mentioned hindered phenols, including mono-phenols
and bis-phenols.
[0077] Preferably, the anti-oxidant, if present, is provided in the composition in an amount
of up to 3 mass %, based on the total amount of the lubricant composition.
[0078] Other additives such as pour point depressants, anti-foamants, metal rust inhibitors,
pour point depressants and/or demulsifiers may be provided, if necessary.
[0079] The terms 'oil-soluble' or 'oil-dispersable' as used herein do not necessarily indicate
that the compounds or additives are soluble, dissolvable, miscible or capable of being
suspended in the oil in all proportions. These do mean, however, that they are, for
instance, soluble or stably dispersible in oil to an extent sufficient to exert their
intended effect in the environment in which the oil is employed. Moreover, the additional
incorporation of other additives may also permit incorporation of higher levels of
a particular additive, if desired.
[0080] The lubricant compositions of this invention comprise defined individual (i.e. separate)
components that may or may not remain the same chemically before and after mixing.
[0081] It may be desirable, although not essential, to prepare one or more additive packages
or concentrates comprising the additives, whereby the additives can be added simultaneously
to the oil of lubricating viscosity to form the lubricating oil composition. Dissolution
of the additive package(s) into the lubricating oil may be facilitated by solvents
and by mixing accompanied with mild heating, but this is not essential. The additive
package(s) will typically be formulated to contain the additive(s) in proper amounts
to provide the desired concentration, and/or to carry out the intended function in
the final formulation when the additive package(s) is/are combined with a predetermined
amount of base lubricant.
[0082] Thus, the additives may be admixed with small amounts of base oil or other compatible
solvents together with other desirable additives to form additive packages containing
active ingredients in an amount, based on the additive package, of, for example, from
2.5 to 90, preferably from 5 to 75, most preferably from 8 to 60, mass % of additives
in the appropriate proportions, the remainder being base oil.
[0083] The final formulations may typically contain about 5 to 40 mass % of the additive
packages(s), the remainder being base oil.
EXAMPLES
[0084] The present invention is illustrated by, but in no way limited to, the following
examples.
Examples
[0085] The following examples use a centrifuge water shedding test which evaluates the ability
of an oil to shed water from a prepared test mixture of oil and water. The test uses
an Alfa Laval MAB103B 2.0 centrifuge coupled to a Watson Marlow peristaltic pump.
The centrifuge is sealed with 2 litres of water. A measurement is made of the amount
of deposits formed in the centrifuge during the test. The test is carried out at 87°C.
Pre-measured amounts of water and the test oil are mixed together and then passed
through the centrifuge at a rate of 2 litres/min. The test is run for an hour and
a half, allowing the mixture to pass through the centrifuge about 10 times. The centrifuge
is weighed before and after the test. A poor trunk piston diesel engine lubricant
composition will produce a larger amount of deposits in the centrifuge system.
[0086] Trunk piston engine oils (`TPEOs') were prepared having TBNs of about 40. The TPEOs
were subjected to the centrifuge water shedding test. Details of the TPEOs and the
test results are shown below in Table 1.
TABLE 1
Example |
Reference |
1 |
2 |
Co-Additives (mass %) |
16 |
16 |
16 |
Lubricating Oil (mass %) |
75.5 |
82.3 |
80.94 |
Brightstock (mass %) |
8.5 |
- |
- |
PIB 2225 (mass %) |
- |
1.7 |
- |
PIB 450 (mass %) |
- |
- |
3.06 |
TBN |
41.17 |
40.46 |
40.63 |
VI |
104 |
105 |
104 |
|
|
|
|
Deposits (g) |
|
|
|
Bowl |
4 |
8 |
5 |
Hood |
3 |
0 |
0 |
Top Disc |
1 |
0 |
0 |
Distributor & Disc |
37 |
4 |
28 |
|
|
|
|
Total Deposits (g) |
45 |
12 |
33 |
PIB = Polyisobutylene (number-average molecular weight given). |
[0087] The results show that Examples 1 and 2, containing PIB and no brightstock, performed
better in the water-shedding test than the Reference Example that contained brightstock,
but no PIB.