FIELD OF TECHNOLOGY
[0001] The present subject matter relates to shape memory stainless steels. More particularly,
the present subject matter relates to shape memory stainless steels with rare earth
elements Cerium (Ce) and Lanthanum (La).
BACKGROUND
[0002] Shape memory alloys are a promising class of advanced materials used in many high
technology applications, such as aerospace, electronics, and biotechnology. The shape
memory alloys at a high temperature can be used as functional materials, such as actuators
for aircraft engines, automobiles and pipe couplings. Further, the shape memory alloys
are used to absorb wind energy. Typically, Nickel-Titanium (Ni-Ti) and Copper (Cu)
based shape memory alloys have been used in such high technology applications. Even
though the Nickel-Titanium (Ni-Ti) and Copper (Cu) based shape memory alloys have
good shape memory effect, however their mechanical properties are lower and are significantly
more expensive to produce when compared with shape memory stainless steels. Further,
machinability of the Ni-Ti based shape memory alloys is relatively poor when compared
with the shape memory stainless steels.
[0003] Generally, the shape memory stainless steels are cheaper alternatives to the expensive
Ni-Ti and Cu based shape memory alloys. The existing shape memory stainless steels
exhibit good shape memory effect, mechanical properties, machinability, weldability
and corrosion resistance. However, the shape memory effect of the shape memory stainless
steels is not as good as the Ni-Ti and Cu based shape memory alloys.
[0004] It is well known that the shape memory effect in Iron (Fe) based shape memory alloys
is associated with the transformation of face centred cubic austenite (γ) to hexagonal
dosed packed (hcp) ε - martensite. The transformation can be divided into two components,
such as one involving formation of ε - martensite when cooled below a martensite start
temperature (Ms) and the other involving stress induced transformation of austenite.
There are different opinions on the effect of thermal martensite on recovery strain
of the Fe based shape memory alloys. One technique that is used to reduce an incidence
of thermal martensite is to reduce Ms by decreasing the austenite grain size, such
as addition of grain refining elements, thermo-mechanical treatments and so on.
SUMMARY
[0005] Shape memory stainless steels with rare earth elements Cerium (Ce) and Lanthanum
(La) are disclosed. According to one aspect of the present subject matter, the shape
memory stainless steels with rare earth elements include Manganese (Mn), Silicon (Si),
Chromium (Cr), Nickel (Ni), Carbon (C), Ce, La and Iron (Fe). The shape memory stainless
steels with rare earth elements Ce and La include, by weight, about 15 to 17% of Mn,
about 5 to 6% of Si, about 9 to 12% of Cr, about 8 to 10% of Ni, about 0.03 to 0.06%
of C, about 0.10 to 0.50% of Ce, about 0.5 to 1.0% of La and the balance being Fe.
[0006] According to another aspect of the present subject matter, raw materials including
Mn, Si, Cr, Ni, C, Ce, La and Fe are melted to form a molten alloy of the shape memory
stainless steels with rare earth elements Ce and La. Further, the molten alloy is
solidified to form an ingot. Furthermore, the ingot is subjected to nondestructive
evaluation to assess internal soundness of the ingot. In addition, the evaluated ingot
is homogenized to form homogenized shape memory stainless steels with rare earth elements
Ce and La. Moreover, a semi-finished product is formed from the homogenized shape
memory stainless steels with rare earth elements Ce and La. Also, a desired component
is formed from the semi-finished product.
[0007] The method disclosed herein may be implemented in any means for achieving various
aspects. Other features will be apparent from the accompanying drawings and from the
detailed description that follow.
BRIEF DESCRIPTION OF THE DRAWINGS
[0008] Various embodiments are described herein with reference to the drawings, wherein:
[0009] FIG. 1 illustrates a flow diagram of an exemplary method of forming shape memory stainless
steels with rare earth elements Cerium (Ce) and Lanthanum (La); and
[0010] FIG. 2 is a table including a range, by weight, of each element in the shape memory stainless
steels with rare earth elements Ce and La, according to one embodiment.
[0011] The drawings described herein are for illustration purposes only and are not intended
to limit the scope of the present disclosure in any way.
DETAILED DESCRIPTION
[0012] Shape memory stainless steels with rare earth elements Cerium (Ce) and Lanthanum
(La) are disclosed. In the following detailed description of the embodiments of the
present subject matter, references are made to the accompanying drawings that form
a part hereof, and in which are shown by way of illustration specific embodiments
in which the present subject matter may be practiced. These embodiments are described
in sufficient detail to enable those skilled in the art to practice the present subject
matter, and it is to be understood that other embodiments may be utilized and that
changes may be made without departing from the scope of the present subject matter.
The following detailed description is, therefore, not to be taken in a limiting sense,
and the scope of the present subject matter is defined by the appended claims.
[0013] FIG. 1 illustrates a flow diagram 100 of an exemplary method of forming shape memory stainless
steels with rare earth elements Ce and La. At block 102, raw materials including Manganese
(Mn), Silicon (Si), Chromium (Cr), Nickel (Ni), Carbon (C), Ce, La and Iron (Fe) are
added. In one embodiment, as shown in
FIG. 2, the shape memory stainless steels with rare earth elements Ce and La include, by
weight, about 15 to 17% of Mn, about 5 to 6% of Si, about 9 to 12% of Cr, about 8
to 10% of Ni, about 0.03 to 0.06% of C, about 0.10 to 0.50% of Ce, about 0.5 to 1.0%
of La and the balance being Fe. At block 104, the added raw materials are melted to
form a molten alloy of the shape memory stainless steels with rare earth elements
Ce and La. In one embodiment, the added raw materials are melted at a temperature
of about 1600 °C to form the molten alloy. In this embodiment, the added raw materials
are melted conventionally or using vacuum induction at the temperature of about 1600
°C to form the molten alloy.
[0014] At block 106, the molten alloy is solidified to form an ingot. In one embodiment,
the molten alloy is solidified by cooling to form the ingot of a desired shape. At
block 108, the ingot is subjected to nondestructive evaluation to assess internal
soundness of the ingot based on quality parameters, such as internal defects, voids,
cracks, cavities and the like. In one embodiment, the nondestructive evaluation uses
gamma radiography. At block 110, the evaluated ingot is homogenized to form homogenized
shape memory stainless steels with rare earth elements Ce and La. In one embodiment,
the evaluated ingot is homogenized by heating the evaluated ingot at a temperature
in a range of about 1050 °C to 1150 °C for about 6 hours to form the homogenized shape
memory stainless steels with rare earth elements Ce and La. At block 112, a semi-finished
product is formed from the homogenized shape memory stainless steels with rare earth
elements Ce and La. Exemplary semi-finished product includes a rolled product, a forged
product and the like. At block 114, a desired component is formed from the semi-finished
product. In one embodiment, the semi-finished product is cold worked or machined to
form the desired component. Exemplary desired component includes an actuator for an
aircraft engine, an automobile component, a pipe coupling and the like.
[0015] In one embodiment, to measure shape memory effect of the shape memory stainless steels
with rare earth elements Ce and La, thin sheets of the homogenized shape memory stainless
steels with rare earth elements Ce and La are made and then small strips are extracted
from the thin sheets. In one embodiment, strips with different lengths are extracted
from the thin sheets to measure the shape memory effect. Further, the strips are bent
into a semicircular shape on mandrels with different diameters at a room temperature
with the ends of strips perpendicular to horizontal straight line. Furthermore, pre-strain
(ε
p) is computed for each strip using an equation:
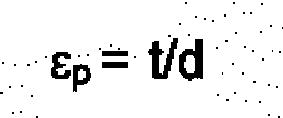
where t is thickness of the strips and d is diameter of the semicircular shapes of
a respective strip.
[0016] The strips are then allowed to recover at a temperature in a range about 400 °C -
450 °C. In addition, a degree of shape recovery (η
SME) for each strip is computed using an equation:

where θ is a residual angle.
[0017] Also, the shape memory effect (also referred as a net reversible strain (ε
R)), in percentage, for each strip is computed using an equation:
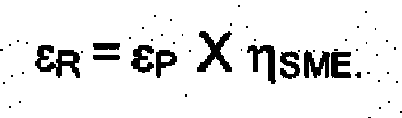
[0018] Referring now to
FIG. 2, a table 200 including a range, by weight, of each element in the shape memory stainless
steels with rare earth elements Ce and La, according to one embodiment. In the table
200, the first row includes various elements in the shape memory stainless steels
with rare earth elements Ce and La, such as Mn, Si, Cr, Ni, C, Ce, La and Fe. Further
in the table 200, the second row includes the range, by weight, of each element in
the shape memory stainless steels with rare earth elements Ce and La. Using the range
of the elements, in the table 200, one can form multiple shape memory stainless steels
with rare earth elements Ce and La.
[0019] In various embodiments, the method described in
FIGS. 1 and
2 enables to form the shape memory stainless steels with rare earth elements Ce and
La. The shape memory stainless steels with rare earth elements Ce and La are cheaper
compared to existing shape memory alloys. Further, the shape memory stainless steels
with rare earth elements Ce and La have good mechanical properties, machinability,
weldability and corrosion resistance.
[0020] Although the present embodiments have been described with reference to specific example
embodiments, it will be evident that various modifications and changes may be made
to these embodiments without departing from the broader spirit and scope of the various
embodiments.
1. Shape memory stainless steels with rare earth elements Cerium (Ce) and Lanthanum (La),
which comprise, Manganese (Mn), Silicon (Si), Chromium (Cr), Nickel (Ni), Carbon (C),
Ce, La and Iron (Fe), wherein the shape memory stainless steels with rare earth elements
Ce and La comprise, by weight, about 0.10 to 0.50% of Ce and about 0.5 to 1.0% of
La.
2. The shape memory stainless steels of claim 1, wherein the shape memory stainless steels
with rare earth elements Ce and La comprise, by weight, about 15 to 17% of Mn, about
5 to 6% of Si, about 9 to 12% of Cr, about 8 to 10% of Ni, about 0.03 to 0.06% of
C and the balance being Fe.
3. The shape memory stainless steels of claim 2, wherein the shape memory stainless steels
with rare earth elements Ce and La further comprise:
unavoidable impurities.
4. A method of forming shape memory stainless steels with rare earth elements Cerium
(Ce) and Lanthanum (La), comprising:
melting raw materials including Manganese (Mn), Silicon (Si), Chromium (Cr), Nickel
(Ni), Carbon (C), Ce, La and Iron (Fe) to form a molten alloy of the shape memory
stainless steels with rare earth elements Ce and La, wherein the shape memory stainless
steels with rare earth elements Ce and La comprise, by weight, about 0.10 to 0.50%
of Ce and about 0.5 to 1.0% of La;
solidifying the molten alloy to form an ingot;
subjecting the ingot to nondestructive evaluation to assess internal soundness of
the ingot; and
homogenizing the evaluated ingot to form homogenized shape memory stainless steels
with rare earth elements Ce and La.
5. The method of claim 4, wherein the shape memory stainless steels with rare earth elements
Ce and La comprise, by weight, about 15 to 17% of Mn, about 5 to 6% of Si, about 9
to 12% of Cr, about 8 to 10% of Ni, about 0.03 to 0.06% of C and the balance being
Fe.
6. The method of claim 4, wherein homogenizing the evaluated ingot to form the homogenized
shape memory stainless steels with rare earth elements Ce and La comprises:
homogenizing the evaluated ingot by heating the evaluated ingot at a temperature in
a range of about 1050°C to 1150°C for about 6 hours to form the homogenized shape
memory stainless steels with rare earth elements Ce and La.
7. The method of claim 4, wherein the nondestructive evaluation comprises nondestructive
evaluation using gamma radiography.
8. The method of claim 4, wherein melting the raw materials to form the molten alloy
comprises:
adding the raw materials; and
melting the added raw materials at a temperature of about 1600°C to form the molten
alloy.
9. The method of claim 8, wherein melting the added raw materials at the temperature
of about 1600°C comprises:
conventional melting of the added raw materials at the temperature of about 1600°C.
10. The method of claim 8, wherein melting the added raw materials at the temperature
of about 1600°C comprises:
vacuum induction melting of the added raw materials at the temperature of about 1600°C.
11. The method of claim 4, wherein solidifying the molten alloy to form the ingot comprises:
solidifying the molten alloy by cooling to form the ingot of a desired shape.
12. The method of claim 4, further comprising:
forming a semi-finished product from the homogenized shape memory stainless steels
with rare earth elements Ce and La.
13. The method of claim 12, wherein the semi-finished product comprises a rolled product
or a forged product.
14. The method of claim12, further comprising:
forming a desired component from the semi-finished product.
15. The method of claim 14, wherein the desired component is an actuator for an aircraft
engine, an automobile component and a pipe coupling.