CROSS-REFERENCE TO RELATED APPLICATION
BACKGROUND
[0002] Laundry treating appliances, such as clothes washers, may include a perforate rotatable
drum or basket positioned within an imperforate tub. The drum may at least partially
define a treating chamber in which a laundry load may be received for treatment according
to a selected cycle of operation. During at least one phase of the selected cycle,
a motor may rotate the drum and laundry load about a rotational axis at a preselected
sufficiently high speed to centrifugally extract liquid from the laundry load. The
faster the drum may rotate, the more quickly the water may be removed from the laundry
load. Thus, extraction may be optimized by maximizing the rotational speed of the
drum, i.e. the maximum obtainable rotational speed as limited by the motor's capabilities,
which may minimize the cycle time.
[0003] Although the motor may limit the maximum rotational speed of the drum, physical limitations
of the system may prevent the maximum rotational speed from being safely obtained.
One example of such a limitation may be a large inertia associated with the drum,
such as from an unbalanced laundry load. If an inertia is too large, it may create
a bending stress on the motor shaft or a hoop stress in the drum that would exceed
the corresponding design limits. To maintain the operation within the design limits,
the drum speed may be limited if the inertia is too large, i.e. the rotational speed
may be reduced below the maximum rotational speed to prevent motor shaft and hoop
stresses from becoming too great. However, extraction at a lower speed may lengthen
the cycle time.
BRIEF DESCRIPTION OF THE INVENTION
[0004] A laundry treating appliance may have a rotatable drum defining a treating chamber
for receiving a laundry load, a motor rotatably driving the drum, and a controller
controlling the operation of the motor. The laundry treating appliance may be operated
by accelerating the drum with the motor toward a final speed greater than a satellizing
speed, determining a mass value indicative of the mass of the rotating drum and contents
within the treating chamber during the accelerating, determining a current rotational
speed during the acceleration, calculating a force value indicative of a force acting
on the drum based on the determined mass value and the current rotational speed, comparing
the force value to a reference force value, and repeating the determining, calculating,
and comparing during the acceleration, and ceasing the accelerating when the force
value obtains a predetermined relationship with the reference force value.
BRIEF DESCRIPTION OF THE DRAWINGS
[0006] Figure 1 is an exemplary schematic view of a laundry treating appliance in the form
of a washing machine according to an embodiment of an environment of the invention.
[0007] Figure 2 is an exemplary schematic view of a control system of the laundry treating
appliance of Figure 1 according to an embodiment of the invention.
[0008] Figure 3 is an exemplary graphical representation of rotational speed or torque vs.
time for the washing machine of Figure 1 comprising a sinusoidal signal superimposed
on a constant acceleration signal.
[0009] Figure 4 is an exemplary graphical representation of generally increasing rotational
speed and generally decreasing torque for an extraction phase of a laundry cycle.
[0010] Figure 5 is an exemplary graphical representation of a decrease in inertia with time
for an extraction phase of a laundry treatment cycle.
[0011] Figure 6 is an exemplary method flow chart for maximizing drum rotational speed by
continuously monitoring inertia during an extraction phase of a laundry treatment
cycle.
DETAILED DESCRIPTION
[0012] Figure 1 is a schematic view of a laundry treating appliance showing one embodiment
of an environment in which the invention operates. The laundry treating appliance
may be any appliance which performs a cycle of operation to clean or otherwise treat
items placed therein, non-limiting examples of which include a horizontal or vertical
axis clothes washer; a combination washing machine and dryer; a tumbling or stationary
refreshing/revitalizing machine; an extractor; a non-aqueous washing apparatus; and
a revitalizing machine.
[0013] The laundry treating appliance of Figure 1 is illustrated as a washing machine 10,
which may include a structural support system comprising a cabinet 12 which defines
a housing within which a laundry holding system resides. The housing may have a chassis
and/or a frame, defining an interior that encloses components typically found in a
conventional washing machine, such as motors, pumps, fluid lines, controls, sensors,
transducers, and the like. Such components will not be described further herein except
as necessary for a complete understanding of the invention.
[0014] The laundry holding system comprises a tub 14 supported within the cabinet 12 by
a suitable suspension system 28, and a drum 16 provided within the tub 14, the drum
16 defining at least a portion of a laundry treating chamber 18.
[0015] The laundry holding system may further include a door 24 which may be movably mounted
to the cabinet 12 to selectively close both the tub 14 and the drum 16. A bellows
26 may couple an open face of the tub 14 with the cabinet 12, with the door 24 sealing
against the bellows 26 when the door 24 closes the tub 14.
[0016] The suspension system 28 may dynamically suspend the laundry holding system within
the structural support system.
[0017] The washing machine 10 may include a drive system 80 for rotating the drum 16 within
the tub 14. The drive system 80 may include a motor 88, which may be directly coupled
with the drum 16 through a motor drive shaft 90, to rotate the drum 16 about a rotational
axis during a cycle of operation. The motor 88 may be a direct-drive, brushless permanent
magnet (BPM) motor having a stator 92 and a rotor 94. Alternately, the motor 88 may
be coupled to the drum 16 through a belt coupled with a drum drive shaft (not shown)
to rotate the drum 16, as is known in the art. Other motors, such as an induction
motor or a permanent split capacitor (PSC) motor, may also be used. The motor 88 may
rotate the drum 16 at various speeds in either rotational direction.
[0018] The washing machine 10 may also include a control system for controlling the operation
of the washing machine 10 to implement one or more cycles of operation. The control
system may include a controller 96 located within the cabinet 12 and a user interface
98 that is operably coupled with the controller 96. The user interface 98 may include
one or more knobs, dials, switches, displays, touch screens and the like for communicating
with the user, such as to receive input and provide output. The user may enter different
types of information including, without limitation, cycle selection and cycle parameters,
such as cycle options.
[0019] The controller 96 may include a machine controller and any additional controller
provided for controlling any of the components of the washing machine 10. For example,
the controller 96 may include the machine controller and a motor controller. Many
known types of controllers may be used for the controller 96, and the specific type
of controller is not germane to the invention. It is contemplated that the controller
may be a microprocessor-based controller that implements control software and sends/receives
one or more electrical signals to/from each of the various working components to effect
the control software. As an example, proportional control (P), proportional integral
control (PI), and proportional derivative control (PD), or a combination thereof,
i.e. a proportional integral derivative control (PID), may be used to control the
various components.
[0020] As illustrated in Figure 2, the controller 96 may be provided with a controller memory
100 and a central processing unit (CPU) 102. The memory 100 may store control software
that is executed by the CPU 102 in completing a cycle of operation using the washing
machine 10, and any additional software. Examples, without limitation, of cycles of
operation include: wash, heavy duty wash, delicate wash, quick wash, pre-wash, refresh,
rinse only, and timed wash.
[0021] The memory 100 may store information in a suitable format, such as a database or
tabular form, and may store data received from one or more components of the washing
machine 10 that may be communicably coupled with the controller 96. The database or
tabular form may be used to store the various operating parameters for the one or
more cycles of operation, including factory default values for the operating parameters
and any adjustments to them by the control system or by user input.
[0022] The controller 96 may be operably coupled with one or more components of the washing
machine 10 for communicating with and controlling the operation of the component to
complete a cycle of operation. For example, the controller 96 may be operably coupled
with the motor 88. The controller 96 may also be operably coupled with a sump heater
to heat wash liquid as required by the controller, one or more pumps, one or more
valves for controlling the flow of liquid during a cycle of operation, a steam generator,
and the like.
[0023] The controller 96 may also be coupled with one or more sensors associated with one
or more systems of the washing machine 10 for processing and storing information from
the sensors. Such sensors are known in the art and are not shown for simplicity. Non-limiting
examples of sensors that may be communicably coupled with the controller 96 include
a motor torque sensor 104, which may be used to determine a variety of system and
laundry characteristics, such as laundry load inertia or mass, and a motor speed sensor
108 for determining a speed output indicative of the rotational speed of the motor
88. The motor speed sensor 108 may be a separate component, or may be integrated directly
into the motor 88. Regardless of the type of speed sensor employed, or the coupling
of the drum 16 with the motor 88, the speed sensor 108 may be adapted to enable the
controller 96 to determine the rotational speed of the drum 16 from the rotational
speed of the motor 88.
[0024] The motor torque sensor 104 may include a motor controller or similar data output
transducer (not shown) on the motor 88 that may provide data communication with the
motor 88 and provide analog or digital motor characteristic signals, such as oscillations,
to the controller 96 that may be indicative of an applied torque. The controller 96
may use the motor characteristics data to determine the torque developed by the motor
88 using an algorithm that may be stored in the controller memory 100. The motor torque
sensor 104 may be any suitable sensor, such as a voltage or current sensor, for outputting
a current or voltage signal indicative of the current or voltage supplied to the motor
88 and enabling a determination of the torque applied by the motor 88. Additionally,
the motor torque sensor 104 may be a separate sensor or may be integrated with the
motor 88. For example, motor characteristics, such as speed, current, voltage, rotation
direction, torque etc., may be processed such that the data may provide information
in the same manner as a separate torque sensor. Contemporary motors often have a dedicated
controller that outputs data for such information.
[0025] One or more load amount, or mass, sensors 106 may be included in the washing machine
10 and may be positioned in any suitable location for providing a mass output indicative
of the mass of the rotating drum and laundry within the treating chamber 18. By way
of non-limiting example, it is contemplated that the amount of laundry in the treating
chamber may be determined based on the weight of the laundry and/or the volume of
laundry in the treating chamber 18. Thus, the load amount sensors 106 may output a
signal indicative of either the weight of the laundry load in the treating chamber
18 or the volume of the laundry load in the treating chamber 18.
[0026] The load amount sensors 106 may be any suitable type of sensor capable of measuring
the weight or volume of laundry in the treating chamber 18. Non-limiting examples
may include load volume, pressure, or force transducers, which may include, for example,
load cells and strain gauges. The load amount sensors 106 may be operably coupled
with the suspension system 28 to sense the weight borne by the suspension system 28.
The weight borne by the suspension system 28 may correlate to the weight of the laundry
loaded into the treating chamber 18 such that the load amount sensor 106 may indicate
the weight of the laundry loaded in the treating chamber 18. In the case of a suitable
load amount sensor 106 for determining volume, an IR or optical based sensor may be
employed to determine the volume of laundry in the treating chamber 18.
[0027] Alternatively, the washing machine 10 may have one or more pairs of feet extending
from the cabinet 12 and supporting the cabinet 12 on the floor, and a weight sensor
(not shown) may be operably coupled to at least one of the feet to sense the weight
borne by the at least one foot, which may correlate to the weight of the laundry loaded
into the treating chamber 18.
[0028] In another example, the amount of laundry within the treating chamber 18 may be determined
based on a motor sensor output, such as output from a motor torque sensor 104. The
motor torque may be a function of the inertia of the rotating drum and laundry load.
Generally, the greater the inertia of the rotating drum and laundry, the greater the
motor torque. There are known methods for determining the load inertia, and the load
mass, based on the motor torque. It may be understood that the details of load amount
sensors and motor torque sensors are not germane to the embodiments of the invention,
and that any suitable method and sensors may be employed to determine the amount of
laundry.
[0029] Prior to describing a method of operation in detail, a brief summary may be useful
to aid in an overall understanding. The described embodiment may, during an operational
cycle of the washing machine 10, control the acceleration and/or rotational speed
of the motor 88, determine a mass value for the rotating drum and laundry, calculate
a force value indicative of a force acting on the drum 16 based on the determined
mass value and the rotational speed, compare the calculated force value with a reference
force value, and control and ultimately terminate acceleration when the determined
force value satisfies a predetermined relationship with the reference force value.
[0030] Extraction may begin by accelerating the drum and laundry items toward a satellizing
speed. A reference force value that is indicative of a not-to-exceed force acting
on the drum may be previously determined and stored in the memory 100. At preselected
time intervals during acceleration, a mass value indicative of the mass of the drum
and laundry items may be determined. The mass value may be determined from an inertia
value for the rotating drum and laundry load, or from other known methods. The inertia
value may be determined during acceleration from changes in motor torque or motor
power.
[0031] Contemporaneously, the rotational speed may be determined. A force value indicative
of a force acting on the drum may be calculated based on the determined mass value
and the rotational speed. The rotational speed may be determined by utilizing a known
speed transducer or by other known methods. Thus, at preselected time intervals, a
mass value, an inertia value, and a rotational speed may be determined.
[0032] The calculated force value may be compared to the reference force value. If the calculated
force value is less than the reference force value, acceleration of the drum and laundry
items may continue. At a preselected time interval, a mass value and an inertia value
may again be determined, along with the rotational speed. Another force value may
be calculated and compared to the reference force value. If the calculated force value
is less than the reference force value, acceleration may continue. Thus, as long as
the reference force value is not reached, the rotational speed of the drum and the
laundry items may be steadily increased, thereby steadily increasing the rate of extraction
of the liquid from the laundry items. When the calculated force value exceeds the
reference force value, depending on the degree of exceedance the rotational speed
may either be maintained at a constant value, or reduced until the calculated force
value is less than or equal to the reference force value and the rotational speed
may then be maintained at the constant value, i.e. the optimal extraction speed.
[0033] Extraction may continue at the optimal extraction speed, the mass value, inertia
value, and rotational speed may be determined, and force values may be calculated
and compared to the reference force value. As extraction continues, the mass value
and inertia value may decrease, which may be reflected in a decrease in the calculated
force value below the reference force value. The decrease in the calculated force
value may enable an increase in the extraction speed, thereby increasing the rate
of extraction. This continued increase in speed, determination of decreased mass value
and inertia value, calculation of the decreased force value and comparison with the
reference force value, and speed adjustment, may optimize the rate of extraction and
enable a shorter extraction period.
[0034] The exemplary embodiment of the invention may enable the inertia of the laundry load
to be determined during an acceleration phase that proceeds without the interposition
of a constant speed phase. This may be accomplished by applying a periodic signal
to an otherwise linear speed profile. It has been observed that the inertia of the
laundry load may be determined by applying a periodic torque signal to the speed profile
in such a manner as to split the periodic signal into two ½-period portions to enable
the inertia of the laundry load to be solved by cancelling out damping and friction
forces.
[0035] In all cases, the values for parameters used herein, like mass value, force value,
and inertia value, need not be a direct determination or calculation of the corresponding
value. While it may be possible to actually calculate the values, in most cases it
may not be necessary to do so. Often an output, such as a voltage signal or the like,
of a suitable sensor for a system parameter, such as inertia, torque, etc., can be
used and compared to a reference value for the output for the parameter, which negates
the need to go to the trouble to make a final determination. Thus, the values used
in here include both absolute values or a referential value, which may serve to indicate
a value without providing an absolute determination or calculation of the value, and
the values may be a direct or indirect indicator of the parameter, such as torque
under certain circumstances is an indicator of the inertia.
[0036] Figure 3 illustrates a periodic torque profile/signal 70 superimposed over a constant
acceleration phase 72 of a speed profile 68. The periodic torque profile 70 may enable
the inertia of the drum 16 and laundry load to be determined for each individual torque
signal period 78 during the acceleration phase 72. The periodic torque profile 70
may have a constant period 132, and may comprise a plurality of periods. The torque
from the motor 88 may be configured to periodically increase and decrease by communicating
with the motor torque sensor 104 and/or the controller 96. As a result, the resulting
torque profile 70 may be in the form of a periodic trace, such as saw-toothed as illustrated,
sinusoidal, or otherwise configured to enable the data analysis described hereinafter.
The periodic torque profile 70 may be applied to the acceleration phase 72 by reference
to a function or lookup table stored in the memory 100 in the controller 96.
[0037] The speed profile 68 may include the acceleration phase 72 and an extraction phase
84. The acceleration phase 72 may be linear, i.e. the rotational speed of the drum
16 and laundry load may increase linearly, thus the acceleration may be constant and
continuous, although as discussed above it may also periodically vary somewhat. The
acceleration phase 72 may be adapted to increase the rotational speed from zero up
to an extraction speed, ES, 84 somewhat greater than a satellizing speed, SS, 82.
As used herein, the term "satellizing speed" refers to a drum rotational speed at
which the laundry load satellizes, which may be higher than the speed at which satellizing
first occurs.
[0038] The periodic torque signal 70 may be generated in different ways. A laundry load
imbalance in the treating chamber 18 may induce a periodic torque or speed signal
during the rotation of the drum 16. Alternatively, if the torque or speed signal is
not inherently periodic, the torque or speed signal may be conditioned to have a periodic
component. Since power is proportional to torque and may be determined based on torque,
torque may conversely be determined based on power consumed by the motor 88.
[0039] Specifically, power,
P = τ * ω). In this manner, the motor torque sensor 104 outputting a signal indicative
of the torque of the motor 88 may effectively operate as a power sensor for generating
a power signal indicative of the power provided to the motor 88. This may be accomplished
by the motor controller generating a periodic waveform as the basis for the acceleration
phase 72. The periodic waveform having a selected frequency, e.g. less than 2 Hz,
may be superimposed on the acceleration phase 72 of the speed profile 68.
[0040] The waveform may include a plurality of equal periods 78. Each period 78 may be bisected
into a first half period 74 corresponding to an increasing trace of the periodic waveform,
representing a positive torque, and a second half period 76 corresponding to a decreasing
trace of the periodic waveform, representing a negative torque. The first half period
74 and the second half period 76 may be alternately symmetrical with respect to the
acceleration phase 72.
[0041] It may be noted that the amplitude of the periodic torque signal 70 in Figure 3 is
exaggerated for clarification. In fact, the amplitude of each half period 74, 76 may
be limited to a small value to minimize the duration of any speed plateaus and optimize
the time to reach the extraction speed 84. The torque associated with the first half
period 74 may be greater than the torque associated with the second half period 76
due to the alternating nature of the torque profile 70. As illustrated in Figure 3,
torque may increase during the first half period 74 and decrease or remain constant
during the second half period 76. From this, the inertia may be determined.
[0042] Generally, motor torque for rotating the drum 16 and laundry load may be represented
as follows:

where, τ = torque,
J = inertia, ω̇ = acceleration, ω = rotational speed,
B = viscous damping coefficient, and C = coulomb friction. Utilizing the relationship
expressed in equation (1), the torque for the first positive half period 74 and the
second negative half period 76 may be determined in the following manner:

Subtracting τ
74 from τ
76, and solving for inertia,

in which ω̇ is constant.
[0043] Both τ
74 and τ
76 may be determined by output from the motor torque sensor 104 and/or the controller
96. Acceleration, ω̇, may be a known value, such as a preselected constant acceleration
controlled by the controller 96, or may be determined by a suitable sensor. Therefore,
an inertia value may be determined for each single period 78 of the torque profile
70 as the acceleration phase 72 continues. A sequence of inertia values may be readily
developed and stored in the memory 100 while acceleration progresses uninterrupted.
[0044] A mass value indicative of the mass of the rotating drum 16 and laundry load may
be determined. The mass value may be determined as an equivalent of an inertia value,
which as described above may be determined from a change in torque.
[0045] Rotation of the drum 16 and a laundry load contained therein may create a force on
the motor drive shaft 90, and/or a hoop force on the drum 16, that exceeds a maximum
design force value. This may be represented as:
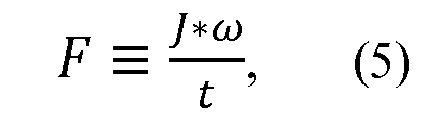
or, in other words, the force, F, is equivalent to the product of the inertia,
J, and the rotational speed, ω, determined over a time period, t. F, however, is primarily
a function of
J and ω regardless of the magnitude of
t. The motor drive shaft force and the hoop force may be determined as a combined value,
or individually. The design limits for the drive shaft force and the hoop force may
be established for a selected washer. Thus, the determined drive shaft and hoop forces
may be compared to the design limits for the drive shaft and hoop forces, respectively.
Alternatively, the determined value for the combined motor drive shaft force and hoop
force may be compared to a design limit for the combined drive shaft force and hoop
force. To maintain such forces within design limits, at least one of inertia and rotational
speed may be controlled to maintain the drive shaft force and hoop force below a predetermined
value corresponding to the maximum design force for the drum 16. Rotational speed
may be more readily controlled than inertia.
[0046] Figure 4 is a graphical representation of a speed profile 124 illustrating an interrelationship
between speed and torque over time. Speed may be increased linearly during a first
acceleration phase 126 and a second acceleration phase 130, as described previously
herein. During the acceleration phases 126, 130, the torque may decrease as moisture
is extracted. If the acceleration phases 126, 130 are interrupted by a constant speed
plateau 128, it may be noted that torque will continue to decrease during the speed
plateau, although at a reduced rate. Inertia values may be determined, i.e. updated,
for selected speed or time intervals pursuant to equation (4); for example, time intervals
140-142, 142-144, 144-146, 152-154, 154-156A, and so on. Inertia values may also be
determined for a time interval 148-150, if a speed plateau is included.
[0047] It may be noted that speed plateaus may be omitted so that the acceleration may be
constant up to a selected extraction speed, which for this description may be a function
of the design limits of the drum. Figure 4 illustrates such a condition, in which
the first acceleration phase 126 may continue unchanged beyond the time interval point
148 to the selected extraction speed 134 corresponding with a time interval point
156B. As described previously herein, the constant acceleration to the selected extraction
speed 134 may include small-amplitude oscillations superimposed on the constant acceleration.
Figure 4 illustrates that maintaining a linear speed profile may shorten the drying
time by a time differential 138 as compared with the profile including the speed plateau
128.
[0048] As the inertia may be repeatedly updated, the speed of the drum 16 and laundry items
may be repeatedly updated. Therefore, the drum 16 may be controlled to rotate at or
below a design maximum speed 136 corresponding to design limits for the drive shaft
force and hoop force. The selected extraction speed 134 may be set at a value somewhat
less than the design maximum speed 136. The design maximum speed 136 may include a
buffer, to which the drum may be accelerated. In those cases in which a buffer is
not included, a buffer may be selected, which is represented by the extraction speed
134. Additionally, the speed 134 may be selected based on the type of laundry. For
example, certain fabrics may wrinkle more readily than others when subjected to high
centrifugal forces. Thus, it may be desirable to set the speed 134 to avoid such wrinkling
and the like.
[0049] When the rotational speed reaches the selected extraction speed 134, acceleration
may be discontinued so that extraction may continue at the selected extraction speed
134. As the extraction progresses, however, the torque may continue to decrease in
an asymptotic manner, as illustrated in Figure 4. As the torque may continue to decrease,
the inertia may similarly decrease and approach an asymptote 169.
[0050] Figure 5 illustrates an idealized asymptotic inertia decay curve 110. Referring as
well to Figure 4, this exemplary asymptotic decay in inertia may be continuously monitored
as the decay curve 110 approaches the asymptote 169, until the inertia reaches an
asymptotic reference value 164 representing an optimal extraction time 166 and residual
moisture content (RMC). As the load spins at a high speed, liquid may be extracted
from the laundry load. Initially, when the moisture content is high, the rate of liquid
extraction may be large. As a result of this large liquid extraction, the inertia
may drop substantially. However, as time passes at a high spin speed, less liquid
may be extracted over a given period of time. As a result, the change in inertia may
tend toward the reference value. Therefore, by monitoring the change in calculated
inertia, the optimal time to stop spinning may be identified.
[0051] The high-speed portion of the spin cycle illustrated in Figure 4, i.e. the selected
extraction speed plateau 134, may be reflected in the continuing decrease in torque
and inertia. As the torque and the inertia decrease, the rotational speed of the drum
16 and laundry load may also tend to decrease, dropping further below the design maximum
speed 136. Consequently, the drum 16 and laundry load may be accelerated to a first
increased speed 158 greater than the selected extraction speed 134. With the increase
in speed, torque and inertia may again tend to decrease, in response to which the
speed may be accelerated to a second increased speed 160. This increase in speed following
a decrease in torque and inertia may continue until a final increased speed 162 may
be reached. At some point during the final speed increase 162, the asymptotic torque
reference value 164 may be reached, corresponding to an optimal extraction time 168,
at which point 166, the extraction may be terminated.
[0052] While the increase in speed from the time interval point 156A to the time interval
point 168 is illustrated as preselected sequential steps, it need not be. It is just
as likely that the increase in speed may be continuous, as exemplified by profile
portion 126A. The speed may also asymptotically increase in response to the asymptotic
decrease of the inertia, i.e. inertia decreases and speed consequently increases,
as exemplified by profile portion 126B. Regardless of the manner in which the speed
continues, both profile portions 126A, 126B may reach the design maximum speed 136.
In such a case, the controller 96 may be programmed to immediately terminate the operation
cycle, reduce the speed to a value less than the design maximum speed 136, reduce
the speed to the selected extraction speed 134, transmit an error or warning signal,
and the like.
[0053] Referring now to Figure 6, a flow chart of a method for maximizing the rotational
speed of the drum 16 in the washing machine 10 during extraction by continuously monitoring
the inertia is illustrated. The sequence of steps depicted for this method is for
illustrative purposes only, and is not meant to limit the method in any way as it
may be understood that the steps may proceed in a different order, or additional or
intervening steps may be included, without detracting from the invention. The method
of Figure 6 begins with the step 36 of determining a maximum force condition of the
drum 16 as a function of 1) the mass of the drum and laundry load, and 2) a drum rotational
speed. The maximum force condition may be determined for both the motor drive shaft
90 and hoop stress individually, or in combination.
[0054] A maximum drum rotational speed that is greater than a satellizing speed may be set
in step 38. The drum 16 and laundry load may be accelerated in step 40 toward a final
speed greater than a satellizing speed for the washer 10. At a preselected interval,
which may be an interval of time, speed, or the like, the rotational speed of the
drum 16 may be determined in step 42. The torque may be determined at the preselected
interval in step 44. The difference in value of the torque at the immediately previous
interval and at the preselected interval may be determined in step 46, and utilized
to determine an inertia value at step 48.
[0055] From the inertia value, a mass value indicative of the mass of the rotating drum
16 and laundry load at the preselected interval may be determined at step 50. A force
value indicative of a force acting on the drum 16 may be calculated based on the determined
mass value and the current rotational speed at the preselected interval at step 52.
The force value may be a calculated force, or may be represented by an inertia value,
a change in torque, or the value directly correlated with a force acting on the drum
at the preselected interval. The force value may be compared with a reference force
value at step 54.
[0056] The reference force value may be indicative of the maximum force condition, or a
threshold force value less than the maximum force condition. If the force value exceeds
the reference force value, the cycle may be terminated in step 58. If the force value
does not exceed the reference force value, the maximum rotational speed may be reset
based upon the mass value and the determined rotational speed in step 56, and the
method may be repeated beginning with step 40.
[0057] By monitoring the inertia of the drum and laundry load during extraction, the washer
10 may identify whether the inertia has decreased to a level that may enable the drum
speed to be safely increased. Thus, the drum 16 and laundry load may always be spinning
at a maximum safe spin speed, thereby extracting liquid from a laundry load in a minimum
time.
[0058] While the invention has been specifically described in connection with certain specific
embodiments thereof, it is to be understood that this is by way of illustration and
not of limitation. Reasonable variation and modification are possible within the scope
of the forgoing description and drawings without departing from the spirit of the
invention, which is defined in the appended claims.
1. A method of operating a laundry treating appliance (10) having a rotatable drum (16)
defining a treating chamber (18) for receiving a laundry load for treatment, a motor
(88) rotatably driving the drum (16), and a controller (96) controlling the operation
of the motor to effect the rotation of the drum(16), the method comprising:
a) accelerating the drum with the motor (88) to increase a rotational speed of the
drum (16) toward a final speed greater than a satellizing speed;
b) determining a mass value indicative of the mass of the rotating drum and laundry
load within the drum during the accelerating;
c) determining a current rotational speed during the acceleration;
d) calculating a force value indicative of a force acting on the drum based on the
determined mass value and the current rotational speed;
e) comparing the force value to a reference force value; and
f) repeating b-e during the accelerating, and terminating the accelerating when the
force value satisfies a predefined relationship with the reference force value.
2. The method of claim 1 wherein the determining the mass value comprises determining
an inertia of the rotating drum (16) and laundry load within the drum (16).
3. The method of claim 2 wherein the determining the inertia comprises determining at
least a combined inertia of the drum (16) and the laundry load within the drum (16).
4. The method of claim 2 wherein the determining the inertia comprises determining a
change in torque of the motor (88) or power utilized by the motor (88).
5. The method of claim 1 wherein the calculating a force value indicative of a force
acting on the drum (16) comprises calculating at least one of a first force value
indicative of a hoop stress on the drum and a second force value indicative of a bending
moment acting on the drum shaft.
6. The method of claim 5 wherein the calculating a force value indicative of a force
acting on the drum (16) comprises calculating both the first and second force values.
7. The method of claim 6 wherein the comparing the force value comprises comparing both
the first and second force values to corresponding first and second reference force
values, and terminating the accelerating comprises terminating the accelerating when
at least one of the first and second force values satisfies a predefined relationship
with the corresponding first and second reference force values.
8. The method of claim 1 wherein the reference force value comprises a threshold force
value and the predefined relationship comprises the force value satisfying the threshold
force value, or comprises the force value exceeding the threshold force value.
9. A method according to any of the preceding claims comprising:
setting a maximum rotational speed of the drum (16), which is greater than a satellizing
speed, based on a maximum force condition of the drum that is a function of the mass
of the drum (16) and the rotational speed of the drum (16);
accelerating the drum (16), with the motor, to increase a rotational speed of the
drum (16) toward the maximum rotational speed, preferably defining a speed profile
without any speed plateaus;
repeatedly determining the mass and the rotational speed during the accelerating;
re-setting the maximum rotational speed based on the determined mass and rotational
speed; and
terminating the accelerating when the determined rotational speed satisfies a predefined
relationship with the maximum rotational speed.
10. The method of claim 9 wherein the accelerating of the drum is continuous, or costant
or defining a speed profile without any speed plateaus.
11. The method of claim 10 wherein the determining the mass comprises determining an inertia
of the rotating drum and laundry load.
12. The method of claim 11 wherein the maximum force condition comprises at least one
of a maximum hoop stress on the drum and a maximum bending moment acting on the drum
shaft (90).
13. A laundry treating appliance (10) according to any of the preceding claims.
14. A laundry treating appliance for treating a laundry load according to claim 13 comprising:
a rotatable drum (16) defining a treating chamber (18) for receiving a laundry load
for treatment;
a motor (88) operably coupled to and rotatably driving the drum (16);
a speed sensor (108) providing a speed output indicative of the rotational speed of
the drum;
a mass sensor (106) providing a mass output indicative of the mass of the rotating
drum; and
a controller (96) receiving as input the speed output and the mass output, and controlling
the motor (88) to effect an accelerating of the drum toward a maximum rotational speed
of the drum (16), which is calculated by the controller based on a maximum force condition
of the drum that is a function of the mass of the drum and the rotational speed of
the drum, while re-setting the maximum rotational speed during the accelerating based
on the received speed output and mass output, and terminating the accelerating when
the rotational speed satisfies a predefined relationship with the maximum rotational
speed.
15. The laundry treating appliance of claim 14 wherein the maximum force condition comprises
at least one of a maximum hoop stress on the drum and a maximum bending moment acting
on the drum shaft and wherein the speed output and the mass output are both outputs
related to the operation of the motor.