Technical Field
[0001] The disclosure pertains generally to the field of oil and gas exploration. More particularly,
the disclosure relates to systems and methods for determining at least one property
of a subsurface formation penetrated by a wellbore using a formation tester.
Background
[0002] Over the past several decades, highly sophisticated techniques have been developed
for identifying and producing hydrocarbons, commonly referred to as oil and gas, from
subsurface formations. These techniques facilitate the discovery, assessment, and
production of hydrocarbons from subsurface formations.
[0003] When a subsurface formation containing an economically producible amount of hydrocarbons
is believed to have been discovered, a borehole is typically drilled from the earth
surface to the desired subsurface formation and tests are performed on the formation
to determine whether the formation is likely to produce hydrocarbons of commercial
value. These preliminary tests are conducted using formation testing tools, often
referred to as formation testers. In some cases, formation testers are lowered into
a wellbore by a wireline cable, tubing, drill string, or the like, and may be used
to determine various formation characteristics which assist in determining the quality,
quantity, and conditions of the hydrocarbons or other fluids located therein. Other
formation testers may form part of a drilling tool, such as a drill string, for the
measurement of formation parameters during the drilling process.
[0004] Formation testers are typically used to measure downhole parameters, such as wellbore
pressures, formation pressures, and formation mobilities. The formation properties
determined during a formation test are important factors in determining the commercial
value of a well and the manner in which hydrocarbons may be recovered from the well.
[0005] Despite the advances made in developing methods for performing pretests, there remains
a need to eliminate delays and errors in the pretest process, and to improve the accuracy
of the parameters derived from such tests, particularly in formations with low mobility
(e.g., less than 0.1 mD/cP).
Summary
[0006] In some embodiments, a method is provided. The method can include: a) creating a
pressure reduction in a flowline in a formation tester, the flowline in fluid communication
with a fluid having a pressure, b) measuring temperature change within the flowline
as the fluid is drawn into the flowline, c) normalizing temperature change as measured
in the flowline to temperature exterior to the formation tester (δ(Δ
T), d) measuring pressure change in the flowline (δ
P) as the fluid is drawn into the flowline, and e) determining whether a curve resulting
from the equation δ
P/δ(Δ
T) over a period of time indicates that the pressure reduction reached a flowline pressure
that is at or below the pressure of the fluid.
[0007] In some embodiments, the step of determining is done at substantially the same time
as the measuring steps.
[0008] In some embodiments, the determining step comprises calculating a time integral of
the curve, e.g., from the formula
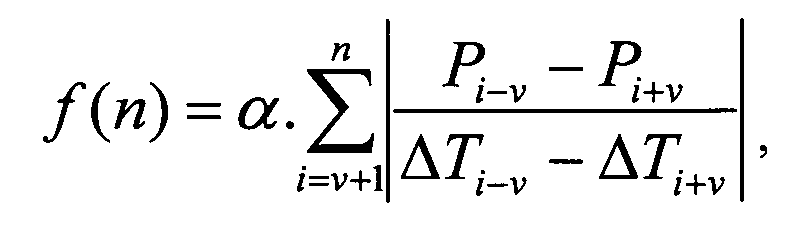
where
P is flowline pressure, Δ
T is flowline temperature normalized for temperature exterior to the flowline,
i is the index of pressure and temperature measurement starting at
i=1,
v is a value defining a smoothing window over which individual pressure and temperature
measurements are smoothed,
n is the number indices
i within the selected period of time, and α is an arbitrary scaling factor.
[0009] In some embodiments, the period of time is less than 2 minutes, from about 30 seconds
to about 100 seconds, or about 40 seconds.
[0010] In some embodiments, the method can further include repeating steps a through e if
the curve indicates that the pressure reduction did not reach a flowline pressure
that is at or below the pressure of the fluid.
[0011] In some embodiments, a system is provided. The system can include: a) a formation
tester having a flowline, the flowline in fluid communication with a fluid having
a pressure and one or more sensor, the one or more sensor operable to measure temperature
exterior to the formation tester and measure pressure and temperature within the flowline,
b) a processor that receives temperature and pressure data from the one or more sensor
and calculates a curve resulting from the equation δ
P/δ(Δ
T), where δ
P is pressure change in the flowline as the fluid is drawn into the flowline by the
creation of a first pressure reduction within the flowline, and where δ(Δ
T) is temperature change in the flowline normalized for temperature exterior to the
flowline.
[0012] In some embodiments, the processor further calculates a time integral of the curve,
e.g., from the formula
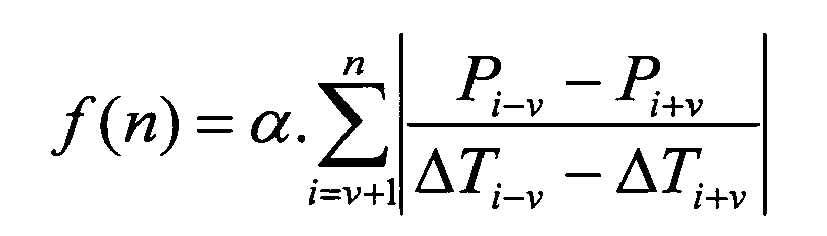
where
P is flowline pressure, Δ
T is flowline temperature normalized for temperature exterior to the flowline,
i is the index of pressure and temperature measurement starting at
i=1,
v is a value defining a smoothing window over which individual pressure and temperature
measurements are smoothed,
n is the number indices
i within the selected period of time, and α is an arbitrary scaling factor.
[0013] In some embodiments, the processor further indicates whether the first pressure reduction
reached a flowline pressure that is at or below the pressure of the fluid.
[0014] In some embodiments, the processor further initiates creation of a second pressure
reduction in the flowline if the curve from step c indicates that the first pressure
reduction did not reach a flowline pressure that is at or below the pressure of the
fluid.
[0015] While multiple embodiments with multiple elements are disclosed, still other embodiments
and elements of the present invention will become apparent to those skilled in the
art from the following detailed description, which shows and describes illustrative
embodiments of the invention. Accordingly, the drawings and detailed description are
to be regarded as illustrative in nature and not restrictive.
Brief Description of the Figures
[0016] Figure 1 is a schematic diagram of a wireline formation tester in accordance with
an embodiment of the disclosure.
[0017] Figure 2 is a cross sectional view of a modular wireline formation tester in accordance
with an embodiment of the disclosure.
[0018] Figure 3 is a graphical representation of an example of flowline pressure readings
over time.
[0019] Figure 4 is a graphical representation of example flowline pressure readings from
a series of drawdowns (A, C, E, G) and buildups (B, D, F, H).
[0020] Figure 5A is a graphical representation of an example of the relationship between
pressure and temperature over time in a flowline following a drawdown that reaches
a pressure at or below that of a fluid in a formation in which a well formation tester
is disposed.
[0021] Figure 5B is a graphical representation of an example of the relationship between
pressure and temperature over time in a flowline following a drawdown that does not
reach a pressure that is at or below that of a fluid in a formation in which a well
formation tester is disposed.
[0022] Figure 6A is a graphical representation of an example of a curve plotting change
in buildup pressure over change in temperature over time following a drawdown that
reaches a pressure at or below that of a fluid in a formation in which a well formation
tester is disposed.
[0023] Figure 6B is a graphical representation of an example of a slope of a curve plotting
the change in buildup pressure over change in temperature over time following a drawdown
that does not reach a pressure at or below that of fluid in a formation in which a
well formation tester is disposed.
[0024] Figure 7 is a flow chart illustrating a method in accordance with an embodiment of
the disclosure.
[0025] Figure 8A is a graphical representation of an example of flowline pressure and temperature
readings from a series of paired drawdowns and buildups (1, 2, 3).
[0026] Figure 8B is a graphical representation of a time integral curve calculated from
the pressure and temperature readings of buildup 1 of Fig. 7A.
[0027] Figure 8C is a graphical representation of a time integral curve calculated from
the pressure and temperature readings of buildup 2 of Fig. 7A.
[0028] Figure 8D is a graphical representation of a time integral curve calculated from
the pressure and temperature readings of buildup 3 of Fig. 7A.
[0029] Figure 9A is a graphical representation of an example of flowline pressure and temperature
readings from a series of paired drawdowns and buildups (1, 2, 3).
[0030] Figure 9B is a graphical representation of a time integral curve calculated from
the pressure and temperature readings of buildup 1 of Fig. 8A.
[0031] Figure 9C is a graphical representation of a time integral curve calculated from
the pressure and temperature readings of buildup 2 of Fig. 8A.
[0032] Figure 9D is a graphical representation of a time integral curve calculated from
the pressure and temperature readings of buildup 3 of Fig. 8A.
[0033] Figure 10A is a graphical representation of an example of flowline pressure and temperature
readings from a series of paired drawdowns and buildups (1, 2, 3, 4).
[0034] Figure 10B is a graphical representation of a time integral curve calculated from
the pressure and temperature readings of buildup 1 of Fig. 9A.
[0035] Figure 10C is a graphical representation of a time integral curve calculated from
the pressure and temperature readings of buildup 2 of Fig. 9A.
[0036] Figure 10D is a graphical representation of a time integral curve calculated from
the pressure and temperature readings of buildup 3 of Fig. 9A.
[0037] Figure 10E is a graphical representation of a time integral curve calculated from
the pressure and temperature readings of buildup 4 of Fig. 9A.
[0038] Figure 11A is a graphical representation of an example of flowline pressure and temperature
readings from a series of paired drawdowns and buildups (1, 2, 3).
[0039] Figure 11B is a graphical representation of a time integral curve calculated from
the pressure and temperature readings of buildup 1 of Fig. 10A.
[0040] Figure 11C is a graphical representation of a time integral curve calculated from
the pressure and temperature readings of buildup 2 of Fig. 10A.
[0041] Figure 11D is a graphical representation of a time integral curve calculated from
the pressure and temperature readings of buildup 3 of Fig. 10A.
[0042] Figure 12A is a graphical representation of an example of flowline pressure and temperature
readings from a series of paired drawdowns and buildups (1, 2).
[0043] Figure 12B is a graphical representation of a time integral curve calculated from
the pressure and temperature readings of buildup 1 of Fig. 11A.
[0044] Figure 12C is a graphical representation of a time integral curve calculated from
the pressure and temperature readings of buildup 2 of Fig. 11A.
[0045] Figure 13 is a schematic block diagram depicting a computing apparatus in accordance
with an embodiment of the disclosure
Detailed Description
[0046] One or more specific embodiments of the present disclosure will be described below
including method, apparatus and system embodiments. These described embodiments and
their various elements are only examples of the presently disclosed techniques. It
should be appreciated that in the development of any such actual implementation, as
in any engineering or design project, numerous implementation-specific decisions can
be made to achieve the developers' specific goals, such as compliance with system-related
and business-related constraints, which can vary from one implementation to another.
Moreover, it should be appreciated that such a development effort might be time consuming,
but would nevertheless be a routine undertaking of design, fabrication, and manufacture
for those of ordinary skill having the benefit(s) of this disclosure.
[0047] When introducing elements of various embodiments of the present disclosure, the articles
"a," "an," and "the" are intended to mean that there are one or more of the elements.
The terms "comprising," "including," and "having" are intended to be inclusive and
mean that there can be additional elements other than the listed elements. Additionally,
it should be understood that references to "one embodiment" or "an embodiment" of
the present disclosure are not intended to be interpreted as excluding the existence
of additional embodiments that also incorporate the listed elements.
[0048] Figure 1 illustrates an embodiment of a wireline formation testing apparatus, system,
and methodology. The wireline formation testing system of Figure 1 can be onshore
or offshore for, for example, exploring oil, natural gas, and other resources that
can be used, refined, and otherwise processed for fuel, raw materials and other purposes.
In the wireline formation testing system of Figure 1, a borehole 3 can be formed in
subsurface formations 5, such as rock formations, by rotary drilling using any suitable
technique. A wireline tester 100 can be lowered using a wireline cable 6 into the
open borehole 3 lined with mudcake 4 deposited onto the wall of the wellbore during
drilling operations. A surface system of the wireline formation testing system of
Figure 1 can include a platform and derrick assembly 2 positioned over the borehole
3.
[0049] Any suitable wireline tester can be used to perform the methods provided herein.
Figure 2 illustrates an embodiment of a wireline tester 100 suitable for use in the
wireline formation testing system of Figure 1. The wireline tester 100 can include
a probe 112 in fluid communication with the exterior of wireline tester 100 and a
flowline 119 on the interior of the wireline tester 100. The wireline tester 100 can
further include a piston 118 within a pretest chamber 114 in fluid communication with
flowline 119 and a pressure sensor or gauge 120 (e.g., a sapphire or quartz pressure
gauge) that measures pressure within flowline 119. In some embodiments, wireline tester
100 can include a temperature sensor or gauge (not shown) that measures temperature
within flowline 119. In some embodiments, wireline tester 100 can include a temperature
sensor or gauge (not shown) that measures temperature of a fluid exterior to the tester
100 (e.g., a fluid in borehole 3). Each temperature or pressure sensor can have any
appropriate sampling rate, which may or may not be adjustable. In some embodiments,
the temperature and pressure sampling rates are the same.
[0050] Once wireline tester 100 is lowered to the desired position in borehole 3, fluid
in the borehole can be allowed to enter the flowline 119, for example, by opening
an equalization valve (not shown). An example of pressure measured in flowline 119
by pressure sensor 120 at this point is graphically depicted as line 103 in Figure
3. In some embodiments, the wireline tester 100 can be anchored in place and probe
112 can be positioned in fluid communication with a fluid in formation 5 using, for
example, hydraulically-actuated pistons, and the interior of the wireline tester 100
can be isolated from the fluid in the borehole by closing the equalization valve.
An example of a pressure measurement at the time of establishment of fluid communication
of probe 112 with a fluid in formation 5 is graphically illustrated at 105 in Figure
3. A pressure reduction (also termed herein as a "drawdown phase") can then be created
in flowline 119, for example, by retracting piston 118. An example of a pressure reduction
in flowline 119 of a drawdown phase is graphically depicted as line 107 in Figure
3. In some embodiments, a fluid in fluid communication with flowline 119 (e.g., a
fluid from formation 5) can then be drawn into flowline 119.
[0051] When piston 118 stops retracting, fluid (e.g., from formation 5) continues to enter
probe 112, causing an increase in pressure (also termed herein as a "buildup phase")
in flowline, 119. An example of a pressure measured when piston 118 stops retracting
is graphically depicted at 111 in Figure 3, while an example of a buildup phase pressure
increase is depicted as line 113 in Figure 3. When probe 112 is disengaged from formation
5, as represented at point 115 of Figure 3, pressure in flowline 119 can equilibrate
to a pressure that approximates the pressure of fluid in borehole 3, as graphically
illustrated in Figure 3 as 117.
[0052] In some embodiments, temperature inside flowline 119 can be measured during all or
part of one or more drawdown and/or buildup phases. In some embodiments, temperature
exterior to wireline tester 100 (e.g., temperature of a fluid in borehole 3) can be
measured during one or more drawdown and/or buildup phase.
[0053] In some embodiments, if a drawdown phase is performed that reaches a pressure at
or below that of a fluid in formation 5, pressure in flowline 119 can equilibrate
to a final pressure that is approximately the same as the pressure of a fluid in formation
5, as graphically illustrated as line 115 in Figure 3. As used herein, a buildup phase
that can be used to approximate a pressure of a fluid in a formation 5 is termed "genuine
buildup." In some embodiments, where a drawdown phase does not reach a pressure at
or below that of a fluid in formation 5, a subsequent buildup phase pressure increase
can be due to temperature and pressure equalization following adiabatic cooling within
flowline 119 when a pressure reduction is created by piston 118. In such embodiments,
a pressure measured in flowline 119 is not representative of a pressure of a fluid
in formation 5, and is termed herein a "pseudo buildup."
[0054] In some embodiments, the steps of creating a pressure reduction and measuring pressure
in flowline 119 can be repeated until a drawdown phase reaches a pressure at or below
that of a fluid in formation 5, such that a subsequent buildup phase can be used to
approximate a pressure of a fluid in formation 5. Figure 4 graphically illustrates
an example of pressure measurements over multiple cycles of drawdown phases A, C,
E, G and buildup phases B, D, F, H performed over time. In some embodiments, cycles
of drawdown and buildup phases can be repeated until two or more repeatable buildup
phases are achieved, where each of the repeatable buildup phases reaches approximately
the same pressure (e.g., within the margin of pressure gauge or sensor sensitivity),
as illustrated with buildup phases F and H in Figure 4. Drawdown phases E and G, then,
can be identified as having reached a pressure at or below that of a fluid in formation
5, and pressure of formation 5 can be determined as approximately equivalent to the
final pressure in flowline 119 during one or more of the repeatable buildup phases.
[0055] As provided herein, a drawdown phase can be predicted as having reached a pressure
that is at or below the pressure of a fluid in a formation 5 prior to performing another
drawdown phase by predicting whether a subsequent buildup phase is a genuine buildup
(i.e., the drawdown phase had reached a pressure that is at or below that of a fluid
in formation 5) or a pseudo buildup (i.e., the drawdown phase had not reached a pressure
that is at or below that of a fluid in formation 5). As shown in Figure 7, a method
1000 for predicting whether a drawdown phase has reached a pressure that is at or
below the pressure of a fluid in fluid communication with a flowline can include,
after creating a pressure reduction in the flowline 1050, measuring temperature within
the flowline as fluid is drawn into the flowline 1052, measuring pressure within the
flowline as fluid is drawn into the flowline 1056, and determining whether a curve
based on the ratio of pressure change to temperature change indicates that the pressure
reduction reached a pressure that is at or below that of a fluid in fluid communication
with the flowline 1058. Pressure increase in flowline 119 over a period of time in
a genuine buildup can be observed to diverge from temperature increase in flowline
119 over the same period of time, as illustrated in the example shown in Figure 5A.
As illustrated in Figure 5B, pressure increase in flowline 119 over a period of time
in a pseudo buildup can be observed to trend closely with temperature increase in
flowline 119 over the same period of time.
[0056] In some embodiments, a curve can be calculated from the ratio of change in pressure
(δ
P) over change in temperature (δ
T) in flowline 119 over a period of time. A buildup phase can be predicted as more
likely to be genuine as the curvature resulting from the equation δ
P/δ
T(Eq. 1) becomes greater. Conversely, a buildup phase can be predicted as more likely
to be a pseudo buildup as the curvature of a curve resulting from Equation 1 becomes
smaller.
[0057] In some embodiments, as shown in Figure 7, temperature in flowline 119 can be normalized
1054 to temperature of fluid exterior to formation tester 100 in order to take into
account temperature changes that are not related to adiabatic cooling (e.g., a change
in temperature of the borehole 3). A normalized temperature (Δ
T) in flowline 119 can be calculated by subtracting temperature measured in fluid exterior
(e.g., fluid in borehole 3) to the formation tester 100 from temperature measured
in the flowline 119 at each measured time point. A curve resulting from the equation
δ
P/δ(Δ
T) (Eq. 2) over a period of time can then be calculated. As illustrated in the example
shown in Figure 6A, a buildup phase can be predicted as more likely to be genuine
as the curvature resulting from Equation 2 becomes greater. Conversely, as shown in
the example in Figure 6B, a buildup phase can be predicted as more likely to be a
pseudo buildup as the curvature of a curve resulting from Equation 2 becomes smaller.
[0058] In some instances, temperature normalization can result in zero or negative values
when differences between temperature within flowline 119 and temperature of fluid
outside of the formation tester 100 are within sensor resolution. In some embodiments,
normalized temperatures having zero or negative values can be avoided by using various
methods of data conditioning. For example, normalized temperatures having zero or
negative values can be avoided by linearly interpolating values that are within sensor
resolution. In some embodiments, values that are within sensor resolution (z) can
be linearly interpolated for
i=1,n using Equation 3:

where
T(i) is the temperature measurement at index
i=1,
n is the number indices
i following
i=1 over which temperature is interpolated, and
T'(i) is the linearly interpolated temperature.
[0059] In some embodiments, pressure values within sensor resolution (e.g., about 0.2 psi
when using a sapphire gauge) can be linearly interpolated using methods similar to
those used to linearly interpolate temperature.
[0060] In some embodiments, a time integral of a curve calculated from Equation 1 or Equation
2 can be used to predict whether a buildup is a genuine buildup or a pseudo buildup.
For example, in some embodiments, a time integral calculated using Equation 4:

where
P is flowline pressure and Δ
T is flowline temperature normalized for temperature of a fluid exterior to the flowline.
The variables
i,
v,
n, and α are discussed below.
[0061] Variable
i in Equation 4 is a whole number representing the index of the current pressure and
temperature measurements are taken. For example, for a sampling rate of 0.3 seconds,
the first index
i=1 represents the first pressure and temperature measurements taken 0.3 seconds after
the start of the buildup, while the tenth index
i=10 represents the tenth temperature and pressure measurements taken 3 seconds after
the start of the buildup.
[0062] Variable
n in Equation 4 is the number of indices within a selected period of time following
a drawdown phase. For example, with a sampling rate of 0.3 seconds, at 30 seconds,
n=100.
[0063] Variable
v in Equation 4 is an value that defines a smoothing window over which individual pressure
and temperature measurements are smoothed. Any appropriate value can be used for
v. For example, if individual pressure and temperature measurements are to be smoothed
over a window of 5 measurements before and 5 measurements after each individual measurement,
then the value of
v would be 5. In some embodiments, a value for
v can be chosen based on a desired smoothing effect that can be provided by the smoothing
window defined by
v. In some embodiments,
v can have a value of at least 3 (e.g., 3, 4, 5, 6, 7, 8, 9, and the like). In some
embodiments, individual pressure and temperature measurements are not centered within
a smoothing window. For example, each individual measurement can be smoothed over
a window of 4 measurements before and 3 measurements after the individual measurement.
In such an embodiment, variable
v can have multiple values as appropriate to define the desired window.
[0064] Variable α in Equation 4 is an arbitrary scaling factor. Any desired value for α
can be chosen to provide a convenient graphical representation of values calculated
from Equation 4. An appropriate value for α can depend on, for example, a period of
time over which temperature and pressure are measured, a pressure or temperature sampling
rate, a sensor resolution, or a desired range of values calculated from Equation 4.
[0065] The period of time over which a time integral of a curve is calculated can be any
appropriate period of time. For example, in some embodiments, an appropriate period
of time is less than 2 minutes. In some embodiments, an appropriate period of time
is from about 20 seconds to about 100 seconds (e.g., from about 30 seconds to about
100 seconds, from about 30 to about 60 seconds, from about 40 to about 60 seconds,
from about 45 to about 80 seconds, 35 seconds, 40 seconds, 50 seconds, 60 seconds,
75 seconds, 90 seconds, or the like). The period of time over which a time integral
of a curve is calculated can be adjusted to account for various conditions, such as
mobility of a fluid for which pressure will be estimated, pressure and/or temperature
gauge sensitivity, the volume of the flowline, and the like.
[0066] In some embodiments, a threshold value calculated from Equation 4 at a selected time
point can be identified as being predictive of whether a drawdown phase has reached
a pressure that is at or below that of a fluid in communication with flowline 119.
For example, in some embodiments, for a sampling rate of 0.3 seconds using α=0.0001,
a value calculated at 40 seconds from Equation 4 that is greater than 10 during a
40 second period of time indicates that a buildup phase is a genuine buildup and/or
that the previous drawdown phase had reached a pressure that is at or below that of
a fluid in communication with flowline 119. Conversely, in the same example, a value
calculated at 40 seconds from Equation 4 that is less than 10 indicates that the buildup
phase is a pseudo buildup and/or that the previous drawdown phase had not reached
a pressure that is at or below that of a fluid in communication with flowline 119.
In some embodiments, a buildup that has been calculated to be a pseudo buildup can
indicate that a fluid in communication with flowline 119 is not flowing into flowline
119.
[0067] Figures 8A, 9A, 10A, 11A, and 12A illustrate examples of time integral curves from
various drawdown and buildup sets. Each of the curves are calculated using Figures
8B, 9B, 10B, 10C, 11B, 11C, and 12B and are graphical representations of curves calculated
from Equation 4 using a sampling rate of 0.3 seconds, α=0.0001, and pressure and normalized
temperature data from buildup 1 of Figure 8A, buildup 1 of Figure 9A, buildup 1 of
Figure 10A, buildup 2 of Figure 10A, buildup 1 of Figure 11A, buildup 2 of Figure
11A, and buildup 1 of Figure 12A, respectively. Each of the curves from 8B, 9B, 10B,
10C, 11B, 11C, and 112B indicate a pseudo buildup.
[0068] Figures 8C, 8D, 9C, 9D, 10D, 10E, 11D, and 12C are graphical representations of time
integral curves calculated from Equation 4 using a sampling rate of 0.3 seconds, α=0.0001,
and pressure and normalized temperature data from buildup 2 of Figure 8A, buildup
3 of Figure 8A, buildup 2 of Figure 9A, buildup 3 of Figure 9A, buildup 3 of Figure
10A, buildup 4 of Figure 10A, buildup 3 of Figure 11A, and buildup 2 of Figure 12A,
respectively. Each of the curves from 8C, 8D, 9C, 9D, 10D, 10E, 11D, and 12C indicate
a genuine buildup.
[0069] In some embodiments, as illustrated in Figure 13, a computing apparatus 2000 can
be used to calculate whether a drawdown phase had reached a pressure that is at or
below that of a fluid exterior to formation tester 2300. According to various embodiments,
the computing apparatus 2000 can include any type of computing device suitable for
implementing embodiments of the subject matter disclosed herein. Examples of computing
devices include "workstations," "servers," "laptops," "desktops," "tablet computers,"
"hand-held devices," and the like. In some embodiments, the computing apparatus 2000
can include more than one computing device such as, for example, in a distributing
computing environment, a networked environment, and the like.
[0070] In some embodiments, a computing apparatus 2000 comprises a processor 2100 and storage
device 2200, the storage device 2200 comprising a program 2210 that directs the processor
2100 receive pressure and temperature data from a formation tester 2300 to calculate
a whether a drawdown phase has reached a pressure that is at or below that of a fluid
in fluid communication with a flowline of the formation tester 2300 using, for example,
any of Equations 1, 2, or 4. In some embodiments, the program 2210 can also direct
the processor 2100 to linearly interpolate temperature data using, for example, Equation
3. In some embodiments, the program 2210 can also direct the processor 2100 to linearly
interpolate pressure data. A computing apparatus 2000 can be configured to receive
pressure and temperature data directly or indirectly from one or more pressure sensor
2310 and/or temperature sensor 2320. In some embodiments, pressure sensor 2310 and
temperature sensor 2320 are a single combined sensor. In some embodiments, a computing
apparatus 2000 can be configured to receive pressure and temperature data from a storage
device (e.g., a storage device storing program 2210 or a different storage device)
that has stored pressure and temperature data from one or more pressure and temperature
sensor 2310, 2320.
[0071] In some embodiments, a computing apparatus 2000 can be configured to perform calculations
at substantially the same time as the measurements are recorded by one or more temperature
and/or pressure sensor 2310, 2320. By substantially the same time, it is meant that
calculations could be made at the same time or not at the exact same time pressure
and/or temperature measurements are made, such as milliseconds to seconds apart or
shorter or longer periods of time (e.g., 0.001, 0.03, 0.1, 0.5, 1, 2, 5, 10 or more
seconds apart) that do not significantly adversely affect the benefit of the apparatus
or methodology. In some embodiments, a computing apparatus 2000 can be configured
to perform calculations at a time point after pressure and temperature data points
are recorded, for example, on a storage device.
[0072] In some embodiments, a computing apparatus 2000 further includes a display (not shown)
on which the program 2210 can direct the processor 2100 to display a graphical representation
of a curve calculated from Equation 1 or 2, or to display an indication of a calculation
resulting from Equation 4. In some embodiments, a computing apparatus 2000 includes
an indicator (not shown) that displays an indication as to whether a drawdown phase
had reached a pressure that is at or below that of a fluid exterior to formation tester
2300.
[0073] In some embodiments, a computing apparatus 2000 can be configured to automatically
initiate another drawdown phase if a calculation using Equation 1, 2, or 4 indicates
a drawdown phase did not reach a pressure at or below a pressure of a fluid outside
of formation tester 2300.
[0074] In some embodiments, a computing apparatus 2000 can include one or more additional
component, such as a power supply 2400, input/output (I/O) port 2500, I/O component
2600, and the like, as appropriate for a desired configuration or to perform selected
functions.
[0075] In some embodiments, components from computing apparatus 2000, such as processor
2100 and storage device 2200 storing program 2210 can be included in a system further
comprising a formation tester that includes a flowline and one or more sensor operable
to measure temperature of a fluid exterior to the formation tester and measure pressure
and temperature within the flowline. In some embodiments, a system provided herein
can include one or more additional components associated with formation testers and/or
computing apparatuses described herein.
[0076] The components of computing apparatus 2000 can be directly or indirectly connected
using any appropriate means, such as, for example, one or more busses 2700.
[0077] As can be appreciated by those skilled in the art, the provided methods, software,
and/or computing apparatuses can be used in geologic formations other than those containing
oil, natural gas, or other petrochemicals.
[0078] Various modifications, additions and combinations can be made to the exemplary embodiments
and their various features discussed without departing from the scope of the present
invention. For example, while the embodiments described above refer to particular
features, the scope of this invention also includes embodiments having different combinations
of features and embodiments that do not include all of the above described features.