PRIORITY INFORMATION
[0001] The present application claims priority to Chinese Application No.
201110142262.8, entitled Coated Cobalt Powder and Preparation Method Thereof, filed on 30.05.2011,
the entire contents of which are hereby incorporated by reference.
FIELD OF THE INVENTION
[0002] The present invention relates to primary cobalt powder in the field of hard alloys,
particularly relates to coated cobalt powder and preparation method thereof.
BACKGROUND OF THE INVENTION
[0003] Hard alloys are commonly composed of refractory metal carbide and metallic binder
(e.g., cobalt and nickel), the preparation method thereof comprises steps of: mixing
metal carbide and metallic binder, ball milling (stirring and mixing), forming (adding
forming agent, pelletizing, pressing, removing forming agent) and sintering.
[0004] Forming herein is an important process of the preparation of hard alloys. Because
hard alloys mainly consist of refractory metal carbides having high hardness, high
elastic modulus and high compressive strength, so it is difficult for the powders
to deform plastically and form. And there still are slight defects (holes, inclusions,
flakes and cracks) existing in the preform, such slight defects in the sintering process
are not easy to be eliminated, may seriously affect product quality. Forming agent
is added to help improve the performance of the blank and the sintered product. Meanwhile,
forming agent must be able to be completely removed; any residual may threaten the
sintered product quality.
[0005] At present, paraffin wax is a main forming agent commonly used at home and abroad
(PEG polyethylene glycol and polyethylene PE and other forming agent have also been
reported).Normally, the hard alloys are wet milled and dried, then mixed with paraffin
wax in the form of wax-gasoline while stirring, the stirring makes paraffin wax evenly
disperse in hard alloys. It is also reported that refractory metal carbides, metallic
bonder and paraffin wax can be ball milled directly. However, in these methods, before
doping wax, the metallic bonder (e.g., cobalt and nickel) tends to be oxidized by
oxygen or water vapor in the air, especially fine particles and ultrafine particles.
It is difficult to control the quality of hard alloys particles. In addition, before
adding forming agent, the processes of mixing and ball milling are easy to generate
lots of respirable dust, pollute the environment in a hard alloy production shop,
and seriously threaten the health of workers.
SUMMARY OF THE INVENTION
[0006] To solve the problem, the present invention is to provide coated cobalt powder and
preparation method thereof. The cobalt powder consists of cobalt powder and paraffin
wax, polyethylene glycol or polyethylene coated on the outer surface of the cobalt
powder. Using the coated cobalt powder to replace traditional cobalt powder as the
raw material for preparing hard alloys, the dusts generated during production can
be reduced, and the environment in a production shop can be improved; simultaneously,
the paraffin wax, the polyethylene glycol or the polyethylene coated on the surface
of the cobalt powder can effectively prevent the cobalt powder from being oxidized
by the oxygen or water vapor in the air, thus improving the quality of the cobalt
powder.
[0007] A first aspect of the invention is to provide coated cobalt powder, wherein consisting
of cobalt powder, and paraffin wax, polyethylene glycol or polyethylene coated on
the outer surface of the cobalt powder, said paraffin wax, polyethylene glycol or
polyethylene is in an amount of 1.5% to 2.5% by weight of said cobalt powder.
[0008] Herein, paraffin wax which is saturated straight-chain hydrocarbons has advantages
such as: no mechanical impurities, low molecular weight, and being able to volatilize
completely at a high temperature without leaving any residues; polyethylene glycol
(PEG) is completely soluble in water and compatible with many substances, showing
great compatibility with polar substances, non-toxic and non-irritating; polyethylene
(PE) is crystalline material, with flexible molecular chain, small bond forces, and
having low hygroscopicity, low melt viscosity and excellent mobility. Paraffin wax,
polyethylene glycol or polyethylene served as a forming agent is commonly added and
mixed with cobalt powder in the forming process during the preparation of hard alloys.
[0009] The present invention firstly provides the cobalt powder whose outer surface is coated
with appropriate amount of paraffin wax, polyethylene glycol or polyethylene. The
cobalt powder can replace traditional cobalt powder as the raw material for preparing
hard alloys. The particle size of the coated cobalt powder of the present invention
is larger than the primary cobalt powder. Paraffin wax, polyethylene glycol or polyethylene
in the coated cobalt powder uniformly coats on the surface of the primary cobalt powder.
Preferably, paraffin wax, polyethylene glycol or polyethylene is in an amount of 2%
by weight of cobalt powder.
[0010] Using the coated cobalt powder of the present invention to replace traditional cobalt
powder as the raw material for preparing hard alloys, the dusts generated during production
can be reduced, and the environment in a production shop can be improved; simultaneously,
the paraffin wax, the polyethylene glycol or the polyethylene coated on the surface
of the cobalt powder can effectively prevent the cobalt powder from being oxidized
by the oxygen or water vapor in the air, thus improving the quality of the cobalt
powder.
[0011] A second aspect of the present invention is to provide a method for preparing coated
cobalt powder, comprising: providing cobalt powder and paraffin wax in an amount of
1.5% to 2.5% by weight of cobalt powder; pouring paraffin wax into organic solvent
then dissolving and forming paraffin wax-organic solvent mixture; adding paraffin
wax-organic solvent mixture into cobalt powder, placing into planetary mixer for stirring
and mixing, vacuum drying to obtain waxed cobalt powder.
[0012] The organic solvent herein is organic solvent having low boiling point, and in which
paraffin wax has great solubility. Preferably, the organic solvent is n-hexane, n-heptane,
methylbenzene or ethyl acetate. More preferably, the organic solvent is ethyl acetate
because ethyl acetate, by contrast, has advantages that: ethyl acetate has low boiling
point, high flashing point, high burning point and relatively inexpensive price; ethyl
acetate is an organic solvent in which paraffin wax has moderate solubility; ethyl
acetate is easy to dry and relatively safe. Organic solvent together with condensate
is recycled in the reaction, it is suitable for industrial production. Different grades
of paraffin wax have different dissolving temperatures and mixing temperatures. Preferably,
solid-liquid ratio of ethyl acetate to cobalt powder (g / mL) is in the range of 20
to 50:1. More preferably, when dissolving No. 52 paraffin wax using ethyl acetate,
the solid-liquid ratio of ethyl acetate to cobalt powder (g / mL) is in the range
of 20 to 25:1. Preferably, the temperature of organic solvent is in the range of 2
to 50°C.Preferably, paraffin wax is in an amount of 2% by weight of cobalt powder.
[0013] Too short the mixing time leads to uneven coating, too long the mixing time leads
to increased time costs of industrial production. Preferably, the stirring and mixing
is carried out at a stirring speed in the range of 40 to 100 r/min for 1 to 5 h. More
preferably, the stirring and mixing is carried out for 1 to 2 h. There is no specific
requirement to the temperature and pressure during the stirring and mixing process,
low temperature (2 to 50°C) and normal pressure will be allowed. Subsequently preferably,
the vacuum drying temperature is in the range of 40 to 55 °C. After obtaining coated
cobalt powder, organic solvent is recycled together with condensate.
[0014] A third aspect of the present invention is to provide a method for preparing coated
cobalt powder, comprising: providing cobalt powder and paraffin wax in an amount of
1.5% to 2.5% by weight of cobalt powder; placing into planetary mixer, stirring and
mixing under the protection of vacuum or nitrogen to obtain waxed cobalt powder. Preferably,
paraffin wax is in an amount of 2% by weight of cobalt powder.
[0015] This method does not involve the process of dissolving paraffin wax with organic
solvent, but melting paraffin wax under a certain mixing temperature in the process
of stirring and mixing. Preferably, the stirring and mixing is carried out at a temperature
in the range of 55 to 60°CPreferably, the stirring and mixing is carried out at a
stirring speed in the range of 40 to 100 r/min for 1 to 5 h. More preferably, the
stirring and mixing is carried out for 1 to 2 h.
[0016] A fourth aspect of the present invention is to provide a method for preparing coated
cobalt powder, comprising: providing cobalt powder, and polyethylene glycol or polyethylene
in an amount of 1.5% to 2.5% by weight of cobalt powder; placing into planetary mixer,
vacuum drying to obtain cobalt powder coated with polyethylene glycol, or cobalt powder
coated with polyethylene.
[0017] Preferably, the stirring and mixing is carried out at a stirring speed in the range
of 40 to 100 r/min for 1 to 5 h. More preferably, the stirring and mixing is carried
out for 1 to 2 h. There is no specific requirement to the temperature and pressure
during the stirring and mixing process, low temperature (2 to 50°C) and normal pressure
will be allowed. Subsequently preferably, the vacuum drying is carried out at a temperature
in the range of 40 to 55 °C.
[0018] The present invention firstly providing coated cobalt powder and preparation method
thereof has the following advantages: Using the coated cobalt powder to replace traditional
cobalt powder as the raw material for preparing hard alloys, the dusts generated during
production can be reduced, and the environment in a production shop can be improved;
simultaneously, the paraffin wax, the polyethylene glycol or the polyethylene coated
on the surface of the cobalt powder can effectively prevent the cobalt powder from
being oxidized by the oxygen or water vapor in the air, thus improving the quality
of the cobalt powder. The preparation process of the coated cobalt powder is free
from contamination and the coated cobalt powder is suitable for industrialized production.
BRIEF DESCRIPTION OF THE DRAWINGS
[0019]
Fig. 1 is a picture of dust experiment of primary cobalt powder and waxed cobalt powder;
Fig. 2 is an SEM image of waxed cobalt powder (organic solvent is ethyl acetate);
Fig. 3 is an SEM image of waxed cobalt powder (organic solvent is n-hexane);
Fig. 4 is an SEM image of primary cobalt powder.
DETAILED DESCRIPTION OF ILLUSTRATED EMBODIMENTS
[0020] Further description of the present invention will be illustrated, which combined
with embodiments in the drawings, in order to make the purpose, the technical solution
and the advantages clearer. While the present invention has been described with reference
to particular embodiments, it will be understood that the embodiments are illustrative
and that the invention scope is not so limited.
Example 1
[0021] A method for preparing coated cobalt powder, comprising: forming paraffin wax-ethyl
acetate mixture by dissolving 9.6 g of paraffin wax into 20 mL of ethyl acetate at
25°C; adding paraffin wax-ethyl acetate mixture into 480 g of cobalt powder; placing
into planetary mixer; stirring and mixing at a speed of 60 r/min for 1.5 h ; then
vacuum drying at 50°C to obtain waxed cobalt powder.
[0022] The waxed cobalt powder can be used for preparing hard alloys. The method for preparing
hard alloys comprises the steps of: mixing tungsten carbide with waxed cobalt powder;
adding a small amount of paraffin wax as a forming agent; stirring and mixing; pressing
and forming; dewaxing at a low temperature; and sintering at a high temperature.
[0023] By reasonably controlling the total addition amount of paraffin wax, the paraffin
wax in the waxed cobalt powder and the paraffin wax served as forming agent which
is added subsequently can be completely removed in the step of dewaxing, also, it
will not affect the sintering of hard alloys. Using the waxed cobalt powder, the dusts
generated during production can be reduced, and the environment in a production shop
can be improved; simultaneously, the cobalt powder can be effectively prevented from
being oxidized by the oxygen or water vapor in the air, thus improving the quality
of the cobalt powder, and then creating additional value to cobalt powder, making
the cobalt powder more competitive.
[0024] After removal of paraffin wax, cobalt powders served as a binder during the sintering
process intersperse with tungsten lattices by sintering at a high temperature, the
morphology has little effect on the quality of hard alloys.
Example 2
[0025] A method for preparing coated cobalt powder, comprising: providing 500 g of cobalt
powder and 10 g of paraffin wax separately; placing into planetary mixer; stirring
and mixing under the protection of nitrogen to obtain waxed cobalt powder. The stirring
and mixing is carried out at 58°C and at a speed of 60 r /min for 3 h .
[0026] The method involves in melting paraffin wax directly at the mixing temperature of
58°C, the stirring and mixing makes the paraffin wax uniformly coat on the outer surface
of cobalt powder.
Example 3
[0027] A method for preparing coated cobalt powder, comprising: providing 500 g of cobalt
powder and 10 g of polyethylene glycol separately; placing into planetary mixer for
stirring and mixing, the stirring and mixing is carried out at a speed of 50 r /min
for 4 h; then vacuum drying at 45°C to obtain cobalt powder coated with polyethylene
glycol.
[0028] Paraffin wax, polyethylene glycol and polyethylene are well known forming agent used
in the preparation of hard alloys. An Example illustrating the effects of typical
waxed cobalt powder is therefore provided in the present invention.
[0029] An Example illustrating the effects
I Experimental method
[0030] Paraffin wax in an amount of 2% by weight of cobalt powder was weighed and dissolved
separately in 20 to 30 mL organic solvents at 2 to 50°C (n-hexane, n-heptane, methylbenzene
and ethyl acetate). Then 600 g of cobalt powder (normal cobalt powder, which can be
purchased in the market, hereinafter referred to as primary cobalt powder) was added.
The mixture was stirred in planetary mixer at a speed of 100 r/min and 0.6∼1 atm for
1 to 5 h, then vacuum dried at 50°C and labeled. Specific optimized process was as
follows: waxed cobalt powders obtained in different experiments were labeled with
different letters (for example, the label "ethyl acetate A" refers to the waxed cobalt
powder obtained by using ethyl acetate as organic solvent and under the conditions
corresponding to the Table 1).
II Results
1. Effects of different organic solvents on waxing
[0031] Paraffin wax has different solubility in different organic solvents, thus it is important
to choose proper organic solvent. This experiment aims to investigate the effects
of different organic solvents (n-hexane, methylbenzene, ethyl acetate and n-heptane)
on waxing. The results are shown in Table 1 (wherein paraffin wax refers to No. 52
paraffin wax, FSSS refers to Fisher particle size, paraffin wax% refers to the amount
of paraffin wax by weight of cobalt powder, similarly hereinafter; moreover, n-hexane
A and n-hexane B refer to that n-hexane reacts with primary cobalt powder 1; methylbenzene,
ethyl acetate A, ethyl acetate B and n-heptane reacts with primary cobalt powder 2,
respectively).
Table 1. Conditions and results of the experiments in preparing waxed cobalt powder
by using different organic solvents
Number |
Experimental conditions |
results |
|
paraffin wax |
dissolving temperature/°C |
mixing temperature/°C |
pressure /atm. |
solid-liquid ratio |
stirring time/h |
FSSS µm |
hydrogen loss % |
paraffin wax% |
primary cobalt powder 1 |
|
|
|
|
|
|
1.33 |
0.48 |
|
n-hexane A |
52 |
50 |
50 |
0.6 |
20 |
5 |
1.49 |
0.3 |
2.04 |
n-hexane B |
52 |
50 |
2 |
1 |
20 |
2 |
1.30 |
0.21 |
2.18 |
primary cobalt powder 2 |
|
|
|
|
|
|
1.2 |
0.45 |
|
methylbenzene |
52 |
50 |
2 |
1 |
20 |
5 |
1.27 |
0.15 |
2.05 |
ethyl acetate A |
52 |
50 |
2 |
1 |
20 |
5 |
1.3 |
0.32 |
2.02 |
ethyl acetate B |
52 |
50 |
50 |
0.6 |
20 |
5 |
1.37 |
0.36 |
2.28 |
n-heptane |
52 |
50 |
50 |
0.6 |
20 |
5 |
1.41 |
0.34 |
2.09 |
[0032] Conclusion: n-hexane, methylbenzene, ethyl acetate and n-heptane can be used as a
solvent to dissolve the paraffin wax in waxed cobalt powder. Ethyl acetate is preferred
in the present invention, considering that the first choice for industrial production
is an organic solvent having low boiling point, high flashing point, high burning
point and relatively inexpensive price, also the organic solvent is an organic solvent
in which paraffin wax has moderate solubility, and the organic solvent is easy to
dry and relatively safe.
2. Effects of different mixing conditions on waxing
[0033] This experiment investigates different mixing conditions (mixing time, mixing temperature,
mixing pressure and mixing solid-liquid ratio) on waxing by using ethyl acetate as
organic solvent to dissolve No. 52 paraffin wax. The results are shown in Table 2
to 4.
Table 2. Conditions and results of the experiments in preparing waxed cobalt powder
for different mixing time
Number |
Experimental conditions |
results |
Organic solvent |
dissolving temperature/°C |
mixing temperature/°C |
pressure/ atm. |
solid-liquid ratio |
stirring time/h |
Fsss µm |
hydrogen loss % |
paraffin wax% |
primary cobalt powder 2 |
|
|
|
|
|
1.2 |
0.45 |
|
ethyl acetate C |
50 |
2 |
1 |
20 |
0.5 |
1.29 |
0.62 |
2.34 |
ethyl acetate D |
50 |
2 |
1 |
20 |
1 |
1.29 |
0.44 |
2.13 |
ethyl acetate E |
50 |
2 |
1 |
20 |
2 |
1.28 |
0.25 |
2.09 |
ethyl acetate F |
50 |
2 |
1 |
20 |
3 |
1.30 |
0.3 |
2.14 |
ethyl acetate G |
50 |
2 |
1 |
20 |
4 |
1.3 |
0.27 |
2.32 |
ethyl acetate H |
50 |
2 |
1 |
20 |
5 |
1.3 |
0.32 |
2.02 |
[0034] Analysis: It can be seen from Table 2 that when stirring for 0.5 h, the mixture is
mixed unevenly, leading to 2% higher amount of paraffin wax than the theoretical value,
and higher hydrogen loss. When stirring for 1h or more, the mixture is mixed evenly,
content of paraffin wax fluctuated around 2%, so that the mixing time is preferably
in the range of 1 to 2h.
Table 3. Conditions and results of the experiments in preparing waxed cobalt powder
at different mixing temperatures
Number |
Experimental conditions |
results |
Organic solvent |
dissolving temperature/°C |
mixing temperature/°C |
pressure/ atm. |
solid-liquid ratio |
stirring time/h |
Fsss µm |
hydrogen loss % |
paraffin wax% |
primary cobalt powder2 |
|
|
|
|
|
1.2 |
0.45 |
|
ethyl acetate I |
50 |
2 |
1 |
20 |
2 |
1.28 |
0.25 |
2.09 |
ethyl acetate J |
50 |
50 |
1 |
20 |
2 |
1.33 |
0.3 |
2.13 |
[0035] Analysis: It can be seen from Table 3 that there is no big difference in the experiment
results between the coated cobalt powders obtained under the conditions of mixing
temperature in the range of 2 to 50°C, 1 atm mixing pressure and 2 hours mixing time.
So the experiment has low requirement to environment (temperature and pressure). Low
temperature (2 to 50°C) and normal pressure will be allowed.
Table 4 Conditions and results of the experiments in preparing waxed cobalt powder
at different solid-liquid ratios
Number |
Experimental conditions |
results |
Organic solvent |
dissolving temperature/°C |
mixing temperature/°C |
pressure/ atm. |
solid-liquid ratio |
stirring time/h |
Fsss µm |
hydrogen loss % |
paraffin wax% |
primary cobalt powder2 |
|
|
|
|
|
1.2 |
0.45 |
|
ethyl acetateK |
50 |
2 |
1 |
20 |
2 |
1.28 |
0.25 |
2.09 |
ethyl acetate L |
50 |
2 |
1 |
25 |
2 |
1.25 |
0.26 |
1.89 |
ethyl acetateM |
50 |
2 |
1 |
30 |
2 |
Paraffin wax separated out |
[0036] Analysis: Solubility of No. 52 paraffin wax in ethyl acetate is 450 g/L, the theoretical
solid-liquid ratio can be figured out is 22.2. It can be seen from Table 4 that the
solution is supersaturated, so that the paraffin wax dissolves completely even the
solid-liquid ratio is increased to 25. Paraffin wax does not separate from cobalt
powder at 2 to 50°C, so it can coat uniformly on the surface of solid cobalt powder.
Solid-liquid ratio of ethyl acetate to cobalt powder (g/mL) is therefore preferably
in the range of 20 to 25:1. Considering that different grades of paraffin wax have
different dissolving temperature and mixing temperature, when employing other grade
of paraffin wax, solid-liquid ratio of ethyl acetate to cobalt powder (g/mL) is in
the range of 20 to 50:1.
[0037] Conclusion: when using ethyl acetate as organic solvent, the mixing is preferably
carried out for 1 to 2 h, solid-liquid ratio (g/mL) of ethyl acetate to cobalt powder
is preferably in the range of 20 to 50:1, low temperature (2 to 50°C) and normal pressure
will be allowed.
III Characterization results
[0038] Primary cobalt powder 2 was provided to prepare waxed cobalt powder samples under
the preferred conditions set forth above, the samples were used in the characterization
experiment below. See Table 5.
Table 5 Conditions for the preparation of waxed cobalt powder samples
Number |
Experimental conditions |
|
dissolving temperature/°C |
mixing temperature/°C |
pressure/ atm. |
solid-liquid ratio |
stirring time/h |
waxed cobalt powder sample (ethyl acetate N) |
50 |
2 |
1 |
25 |
2 |
1. Resistance against oxidation
[0039] Hydrogen loss of the waxed cobalt powder sample (using ethyl acetate as organic solvent)
and primary cobalt powder was simultaneously measured over time. The results are shown
in Table 6.
Table 6 changes of hydrogen loss of cobalt powders over time at different temperatures
Time |
20° Cprimary cobalt powder hydrogen loss |
20°Cwaxed cobalt powder hydrogen loss |
40° Cprimary cobalt powder hydrogen loss |
40°Cwaxed cobalt powder hydrogen loss |
0 |
0.48 |
0.25 |
0.48 |
0.25 |
2h |
0.48 |
0.22 |
0.48 |
0.28 |
4h |
0.41 |
0.18 |
0.41 |
0.23 |
6h |
0.39 |
0.21 |
0.35 |
0.24 |
[0040] Analysis: paraffin wax mixed with the waxed cobalt powder sample may affect oxygen
& sulfur analyzer, so oxygen content is replaced with hydrogen loss. It can be seen
from Table 6 that in 20°C and 40°C environments, hydrogen loss of waxed cobalt powder
samples is lower than that of primary cobalt powder, which indicates that waxed cobalt
powder samples have resistance against oxidation to a certain extent.
2. Dust experiment
[0041] 100 g of primary cobalt powder and waxed cobalt powder samples (using ethyl acetate
as organic solvent) were placed into wild-mouth bottle separately, then the bottle
was shaken for 1 min. Primary cobalt powder was on the left, waxed cobalt powder sample
was on the right. The results are shown in Fig. 1. Fig. 1 is a picture of dust experiment
of primary cobalt powder and waxed cobalt powder.
[0042] Analysis: It can be seen from Fig. 1 that there is lots of dust, 1.1 g, sticking
to the wall of the bottle containing primary cobalt powder, whereas there is less
dust, 0.8 g, sticking to the wall of the bottle containing waxed cobalt powder. The
dust is reduced by 36% after waxing.
3. Dispersity
[0043] The dispersity is a measure of the heterogeneity of sizes of powders in the air.
The determination method involves dropping 10 g of primary cobalt powder and waxed
cobalt powder from a certain height, determining amount of the samples which fail
to fall into the receiver, calculating the percentage of the samples by weight of
the total amount of primary cobalt powder and waxed cobalt powder. The results are
shown in Table 7. Dispersity is related to dispersibility, floatability and splash
ability of the samples.
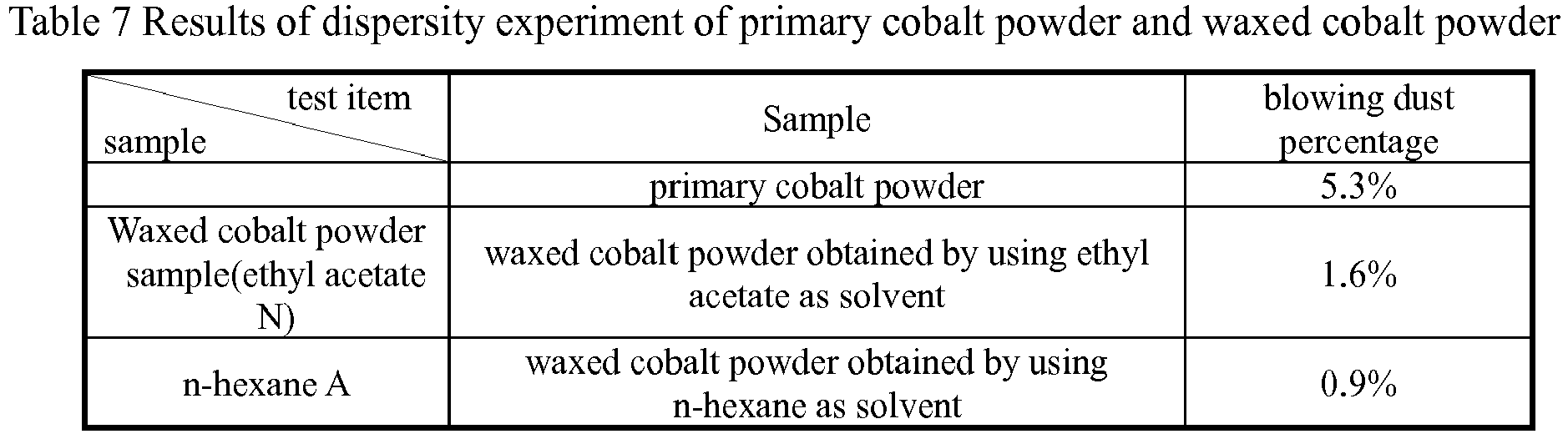
[0044] Analysis: it can be seen from the data that, dispersity of cobalt powder decreases
apparently after adding paraffin wax, dispersity decreases from 5.3% to 1.6% even
lower to 0.9%, indicating that waxed cobalt powder generates less dusts than primary
cobalt powder.
4. SEM
[0045] Fig. 2, Fig. 3 and Fig. 4 are SEM images. Fig. 2 is an SEM image of waxed cobalt
powder sample (using ethyl acetate as organic solvent), Fig. 3 is an SEM image of
waxed cobalt powder (using n-hexane A as organic solvent), Fig. 4 is an SEM image
of primary cobalt powder.
[0046] Analysis: it can be seen from Fig. 2, Fig. 3 and Fig. 4 that particle size of waxed
cobalt powder is greater than primary cobalt powder. The paraffin wax in waxed cobalt
powder uniformly coats on the surface of primary cobalt powder.
1. Coated cobalt powder, wherein consisting of
cobalt powder, and
paraffin wax, polyethylene glycol or polyethylene coated on the outer surface of the
cobalt powder;
said paraffin wax, polyethylene glycol or polyethylene is in an amount of 1.5% to
2.5% by weight of said cobalt powder.
2. The cobalt powder according to claim 1, wherein said paraffin wax, polyethylene glycol
or polyethylene is in an amount of 2% by weight of said cobalt powder.
3. A method for preparing coated cobalt powder, comprising:
providing cobalt powder and paraffin wax in an amount of 1.5% to 2.5% by weight of
cobalt powder;
pouring paraffin wax into organic solvent then dissolving and forming paraffin wax-organic
solvent mixture;
adding paraffin wax-organic solvent mixture into cobalt powder, placing into planetary
mixer for stirring and mixing, vacuum drying to obtain waxed cobalt powder.
4. The method for preparing coated cobalt powder according to claim 3, wherein said organic
solvent is n-hexane, n-heptane, methylbenzene or ethyl acetate.
5. The method for preparing coated cobalt powder according to claim 4, wherein solid-liquid
ratio of said cobalt powder to ethyl acetate is in the range of 20 to 50:1.
6. The method for preparing coated cobalt powder according to claim 3, wherein the stirring
and mixing is carried out at a stirring speed in the range of 40 to 100 r/min for
1 to 5 h.
7. A method for preparing coated cobalt powder, comprising:
providing cobalt powder and paraffin wax in an amount of 1.5% to 2.5% by weight of
cobalt powder;
placing into planetary mixer, stirring and mixing under the protection of vacuum or
nitrogen to obtain waxed cobalt powder.
8. The method for preparing coated cobalt powder according to claim 7, wherein the stirring
and mixing is carried out at a temperature in the range of 55 to 60°C.
9. The method for preparing coated cobalt powder according to claim 7, wherein the stirring
and mixing is carried out at a stirring speed in the range of 40 to 100 r/min for
1 to 5 h.
10. A method for preparing coated cobalt powder, comprising:
providing cobalt powder, and polyethylene glycol or polyethylene in an amount of 1.5%
to 2.5% by weight of cobalt powder;
placing into planetary mixer, vacuum drying to obtain cobalt powder coated with polyethylene
glycol, or cobalt powder coated with polyethylene.