BACKGROUND
FIELD OF THE INVENTION
[0001] The present invention relates to a motor controller and a method for controlling
a motor.
DISCUSSION OF THE BACKGROUND
[0002] Japanese Unexamined Patent Application Publication No.
2007-159231 discloses that an induction motor in a free run state is turned into a
V/
F control state, and before the induction motor is turned into the
V/
F control state, a speed search is performed. In the speed search, the frequency of
a voltage applied to the induction motor is made close to the rotational speed of
the induction motor in the free run state.
[0003] The contents of Japanese Unexamined Patent Application Publication No.
2007-159231 are incorporated herein by reference in their entirety.
[0004] One method of the speed search is to gradually increase or decrease the frequency
of the voltage applied to the motor so as to find out a value of the frequency at
which a current through the motor is minimal. However, the method involves keeping
the frequency increased or decreased until the value of the frequency at which the
current is minimal is found. Thus, the search can take a long period of time. In addition,
the value of the frequency at which the current is minimal is not defined in advance.
Thus, it is difficult to precisely find out the value of the frequency at which the
current is minimal.
[0005] Another method of the speed search is to increase or decrease the frequency based
on an induced voltage attributed to a residual magnetic flux resulting from the induction
motor turning into the free run stage. Still another method of the speed search is
to increase or decrease the frequency based on an oscillation of a current resulting
from a DC voltage applied to the induction motor in the free run state. However, these
methods have a limited period of time allowed for the search, and may fail to make
the frequency sufficiently close to the rotational speed of the induction motor. Thus,
there is a possibility of a large error.
[0006] The present disclosure has been made in view of the above-described circumstances,
and it is an object of the present disclosure to provide a motor controller and a
method for controlling a motor that ensure promptness and readiness in making the
frequency of the voltage applied to the induction motor close to the rotational speed
of the induction motor in the free run state.
SUMMARY
[0007] According to one aspect of the present disclosure, a motor controller is configured
to make a frequency of a voltage applied to an induction motor close to a rotational
speed of the induction motor in a free run state. The motor controller includes an
evaluation value calculator and an evaluation value searcher. The evaluation value
calculator is configured to calculate an evaluation value represented by a function
including a
q-axis current value of a torque current component of a current through the induction
motor. The evaluation value has a first sign among a positive sign and a negative
sign when the rotational speed is greater than the frequency by a predetermined amount,
and has a second sign different from the first sign among the positive sign and the
negative sign when the rotational speed is smaller than the frequency by the predetermined
amount. The evaluation value searcher is configured to execute an evaluation value
search to increase or decrease the frequency based on whether the evaluation value
has the positive sign or the negative sign.
[0008] In one embodiment of the present disclosure, the function representing the evaluation
value may include the
q-axis current value and a
d-axis value of an excitation current component of the current through the induction
motor.
[0009] In one embodiment of the present disclosure, the function representing the evaluation
value linearly may change between a case of the rotational speed being greater than
the frequency by the predetermined value and a case of the rotational speed being
smaller than the frequency by the predetermined value.
[0010] In one embodiment of the present disclosure, the motor controller may further include
a closeness determiner configured to determine, in accordance with the evaluation
value, whether the frequency is close to the rotational speed.
[0011] In one embodiment of the present disclosure, the motor controller may further include
a previous searcher configured to perform at least one of a first search and a second
search before the evaluation value search. The first search is to increase or decrease
the frequency based on an induced voltage attributed to a residual magnetic flux resulting
from the induction motor turning into the free run state. The second search is to
increase or decrease the frequency based on an oscillation of a current that results
when a DC voltage is applied to the induction motor in the free run state.
[0012] In one embodiment of the present disclosure, the function representing the evaluation
value may linearly change to 0 when a difference between the rotational speed and
the frequency is approximately 0.
[0013] According to another aspect of the present disclosure, a motor controller is configured
to make a frequency of a voltage applied to an induction motor close to a rotational
speed of the induction motor in a free run state. The motor controller includes a
previous searcher and a post-searcher. The previous searcher is configured to perform
at least one of a first search and a second search. The first search is to increase
or decrease the frequency based on an induced voltage attributed to a residual magnetic
flux resulting from the induction motor turning into the free run state. The second
search is to increase or decrease the frequency based on an oscillation of a current
that results when a DC voltage is applied to the induction motor in the free run state.
The post-searcher is configured to perform a third search after the at least one of
the first search and the second search. The third search is to increase or decrease
the frequency based on a
q-axis current value of a torque current component of a current through the induction
motor.
[0014] According to another aspect of the present disclosure, a motor controller is configured
to make a frequency of a voltage applied to an induction motor close to a rotational
speed of the induction motor in a free run state. The motor controller includes an
evaluation value calculator and an evaluation value searcher. The evaluation value
calculator is configured to calculate an evaluation value represented by a function
including a
q-axis power value of a torque power component of power supplied to the induction motor.
The evaluation value has a first sign among a positive sign and a negative sign when
the rotational speed is greater than the frequency by a predetermined amount, and
has a second sign different from the first sign among the positive sign and the negative
sign when the rotational speed is smaller than the frequency by the predetermined
amount. The evaluation value searcher is configured to perform an evaluation value
search to increase or decrease the frequency based on whether the evaluation value
has the positive sign or the negative sign.
[0015] According to the other aspect of the present disclosure, a method is for controlling
a motor so as to make a frequency of a voltage applied to an induction motor close
to a rotational speed of the induction motor in a free run state. The method includes
calculating an evaluation value represented by a function including a
q-axis current value of a torque current component of a current through the induction
motor. The evaluation value has a first sign among a positive sign and a negative
sign when the rotational speed is greater than the frequency by a predetermined amount,
and has a second sign different from the first sign among the positive sign and the
negative sign when the rotational speed is smaller than the frequency by the predetermined
amount. An evaluation value search is performed to increase or decrease the frequency
based on whether the evaluation value has the positive sign or the negative sign.
[0016] With the embodiments, the frequency is increased or decreased based on whether the
evaluation value has a positive sign or a negative sign. This ensures promptness and
readiness in making the frequency close to the rotational speed of the induction motor
in the free run state.
BRIEF DESCRIPTION OF THE DRAWINGS
[0017] A more complete appreciation of the present disclosure and many of the attendant
advantages thereof will be readily obtained as the same becomes better understood
by reference to the following detailed description when considered in connection with
the accompanying drawings, wherein:
FIG. 1 is a block diagram illustrating an exemplary motor control system;
FIG. 2 is a block diagram illustrating an exemplary motor controller;
FIG. 3A is a graph of an exemplary function representing an evaluation value;
FIG. 3B is an enlarged graph of a main part of FIG. 3A;
FIG. 4 is a block diagram illustrating an exemplary evaluation value searcher;
FIG. 5 is a time chart illustrating an exemplary speed search;
FIG. 6 is a time chart illustrating an exemplary speed search; and
FIG. 7 is a time chart illustrating an exemplary speed search.
DESCRIPTION OF THE EMBODIMENTS
[0018] The embodiments will now be described in detail with reference to the accompanying
drawings, wherein like reference numerals designate corresponding or identical elements
throughout the various drawings.
[0019] FIG. 1 is a block diagram illustrating a motor control system 100. The motor control
system 100 includes an induction motor 2, an inverter 3, an AC (Alternating Current)
power supply 4, a converter 5, and a motor controller 10.
[0020] The inverter 3 includes a three-phase bridge circuit to convert DC (Direct Current)
power supplied from the converter 5 into AC power based on a control signal generated
by the motor controller 10. Then, the inverter 3 outputs the converted AC power to
the induction motor 2.
[0021] The converter 5 includes a rectifier circuit 51 and a capacitor 52. The converter
5 converts AC power supplied from the AC power supply 4 into DC power. Then, the converter
5 outputs the converted DC power to the inverter 3.
[0022] The motor controller 10 includes a microprocessor, for example. The motor controller
10 performs information processing based on a program stored in a memory, so as to
generate a control signal to control the rotation of the induction motor 2. Then,
the motor controller 10 outputs the generated control signal to the inverter 3.
[0023] FIG. 2 is a block diagram illustrating an example of the motor controller 10. Each
block of the motor controller 10 is implemented by the microprocessor performing the
information processing based on the program stored in the memory.
[0024] The motor controller 10 performs a normal operation when a switch SW1 is at one side,
and performs a speed search when the switch SW1 is another side. In the normal operation,
the motor controller 10 performs
V/
F control to keep a constant ratio of a voltage V applied to the induction motor 2
to the frequency of the applied voltage V.
[0025] The speed search is a mode in which the induction motor 2 is turned from a free run
state into a
V/
F control state. In the free run state, the induction motor 2 is not supplied power
but keeps rotation by inertia.
[0026] The motor controller 10 includes a
V/
F converter 11, a gain section 12, a voltage commander 13, a voltage phase section
14, an integrator 15, an adder 16, and a PMW controller 17. These blocks are in particular
for implementing the normal operation. The motor controller 10 includes an
α-β converter 21 and a
d-q converter 22.
[0027] The motor controller 10 includes a previous searcher 31 and a rotational direction
setting section 33. These blocks are for implementing a previous search. The previous
search is a part of the speed search.
[0028] The motor controller 10 includes an evaluation value calculator 61, an evaluation
value searcher 63, and a search ending determiner 65. These blocks are for implementing
an evaluation value search. The evaluation value search is also a part of the speed
search.
[0029] The
V/
F converter 11 performs
V/
F conversion of a frequency command
ω*, which is obtained from an upper-level system, so as to generate a
q-axis voltage base value. Then, the
V/
F converter 11 outputs the
q-axis voltage base value to the gain section 12.
[0030] The gain section 12 receives the
q-axis voltage base value from the
V/
F converter 11, and multiplies the
q-axis voltage base value by a gain
a so as to calculate a
q-axis voltage command
Vq*. Then, the gain section 12 outputs the
q-axis voltage command
Vq* to the voltage commander 13 and the voltage phase section 14.
[0031] The voltage commander 13 calculates a voltage command
V* based on the
q-axis voltage command
Vq* from the gain section 12 and based on a
d-axis voltage command
Vd* (= 0) from the upper-level system. Then, the voltage commander 13 outputs the voltage
command
V* to the PMW controller 17.
[0032] The voltage phase section 14 calculates a voltage phase correction value based on
the
q-axis voltage command
Vq* from the gain section 12 and based on the
d-axis voltage command
Vd* (= 0). Then, the voltage phase section 14 outputs the correction value to the adder
16.
[0033] The integrator 15 integrates the frequency command
ω* to calculate a voltage phase base value. Then, the integrator 15 outputs the voltage
phase base value to the adder 16.
[0034] The adder 16 adds the voltage phase correction value obtained from the voltage phase
section 14 to the voltage phase base value obtained from the integrator 15 so as to
calculate a voltage phase
θ*. Then, the adder 16 outputs the voltage phase
θ* to the PMW controller 17 and the
d-q converter 22.
[0035] The PMW controller 17 calculates a control signal based on the voltage command
V* from the voltage commander 13 and based on the voltage phase
θ* from the adder 16. The control signal is used for PMW control of the rotation of
the induction motor 2. Then, the PMW controller 17 outputs the control signal to the
inverter 3.
[0036] The
α-β converter 21 performs
α-β conversion of a current detection value of the three-phase AC power that the inverter
3 supplies to the induction motor 2 so as to calculate a current detection value in
a fixed coordinate system
α-β. Then, the
α-β converter 21 outputs the current detection value to the
d-q converter 22.
[0037] The
d-q converter 22 uses the voltage phase
θ* obtained from the adder 16 to perform
d-q conversion of the current detection value in the fixed coordinate system
α-β obtained from the
α-β converter 21. Thus, the
d-q converter 22 calculates a
q-axis current value
Iq and a
d-axis current value
Id in a rotary coordinate system
d-q. Then, the
d-q converter 22 outputs the
q-axis current value
Iq and the
d-axis current value
Id to the evaluation value calculator 61 and the search ending determiner 65. The
q-axis current value
Iq is a torque current component. The
d-axis current value
Id is an excitation current component.
[0038] The motor controller 10 performs the previous search when a switch SW2 is at one
side, and performs the evaluation value search when the switch SW2 is at another side.
In the speed search, the motor controller 10 performs the previous search first and
performs the evaluation value search next.
[0039] The previous search 31 is a block to perform the previous search. Examples of the
previous search include, but are not limited to, a method of increasing or decreasing
frequency based on an induced voltage attributed to a residual magnetic flux that
results when the induction motor 2 turns into the free run state, and a method of
increasing or decreasing frequency based on an oscillation of a current that results
when a DC voltage is applied to the induction motor 2 in the free run state. The methods
are conventional techniques and will not be elaborated.
[0040] The previous searcher 31 performs the previous search to obtain information indicating
the rotational direction of the induction motor 2. Then, the previous searcher 31
outputs the information to the rotational direction setting section 33.
[0041] The rotational direction setting section 33 obtains from the previous searcher 31
the information indicating the rotational direction of the induction motor 2, and
adds the information to a frequency command
ωsear*, which is obtained from the evaluation value searcher 63.
[0042] The evaluation value calculator 61 calculates an evaluation value J based on the
q-axis current value
Iq and the
d-axis current
Id obtained from the
d-q converter 22, and outputs the evaluation value J to the evaluation value searcher
63. The calculation of the evaluation value J will be described in detail later.
[0043] The evaluation value searcher 63 calculates the frequency command
ωsear* based on the evaluation value J obtained from the evaluation value calculator 61,
and outputs the frequency command
ωsear* to the
V/
F converter 11 and the voltage phase section 14. The evaluation value searcher 63 will
be described in detail later.
[0044] Based on the
q-axis current value
Iq and the
d-axis current
Id obtained from the
d-q converter 22, the search ending determiner 65 determines whether to end the evaluation
value search. For example, the search ending determiner 65 determines to end the evaluation
value search when the
q-axis current value
Iq is below a threshold.
[0045] The search ending determiner 65 may determine whether to end the evaluation value
search based on the evaluation value J calculated by the evaluation value calculator
61 (here, the search ending determiner 65 serves as a closeness determiner).
[0046] FIG. 3A is a graph of an exemplary function representing the evaluation value J.
FIG. 3B is an enlarged graph of a main part of FIG. 3A. The main part is surrounded
by a broken line frame at a center portion of FIG. 3A.
[0047] As illustrated in each graph, the vertical axis represents the evaluation value J,
while the horizontal axis represents speed error. The speed error is a difference
between the rotational speed of the induction motor 2 and the frequency of the voltage
applied to the induction motor 2. Also as illustrated in each graph, the solid line
represents a function of the evaluation value
J, the single-dashed line represents the
q-axis current value
Iq, and the double-dashed line represents the
d-axis current value
Id.
[0048] The following Formula 1 is an example of the function of the evaluation value
J. K represents a weighting factor (0
< K < 1). In the function of the evaluation value
J illustrated in the graphs, K = 0.5.
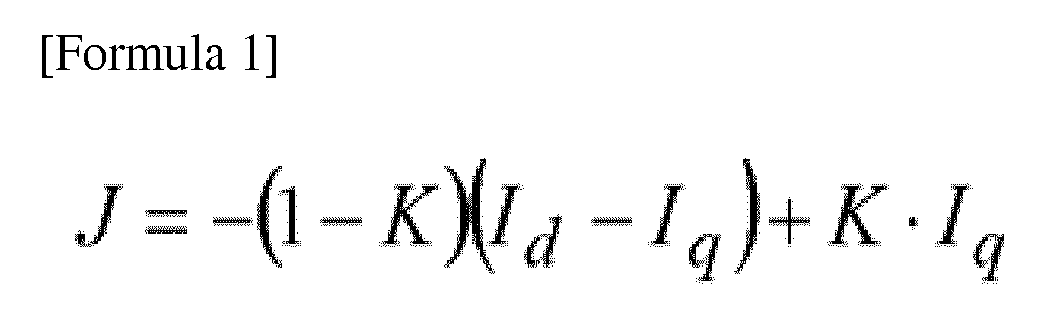
[0049] The function of the evaluation value J includes the
q-axis current value
Iq and the
d-axis current value
Id. It should be noted that the function of the evaluation value J may not include the
d-axis current value
Id (for example, when
K = 1 in Formula 1, a function with the
q-axis current value
Iq and without the
d-axis current value
Id results).
[0050] The function of the evaluation value
J has one sign among the positive sign and the negative sign when the speed error is
a predetermined positive value, and has another sign different from the one sign among
the positive sign and the negative sign when the speed error is a predetermined negative
value. For example, the evaluation value
J shows a different sign, the positive sign or the negative sign, at one end (for example,
5
Hz) and the other end (for example, -5
Hz) of the range of the speed error illustrated in FIG. 3B. It is particularly preferred
that the sign of the evaluation value
J be reversed between the positive sign and the negative sign when the speed error
is approximately 0.
[0051] The function of the evaluation value
J linearly changes between the predetermined positive value and the predetermined negative
value of the speed error. For example, the evaluation value
J linearly changes in a part including 0 of the speed range illustrated in FIG. 3B
(for example, -2
Hz to 2
Hz). It is particularly preferred that the function of the evaluation value
J linearly change to 0 when the speed error is approximately 0.
[0052] In the function of the evaluation value
J, the sign of the evaluation value
J is reversed between the positive sign and the negative sign when the speed error
is approximately 0. This makes it easier to make the frequency of the voltage applied
to the induction motor 2 close to the rotational speed of the induction motor 2. For
example, it is possible to increase the frequency when the evaluation value
J has one of the positive sign and the negative sign, and to decrease the frequency
when the evaluation value
J has the other one of the positive sign and the negative sign.
[0053] When
K = 1, the function of the evaluation value
J is
Iq. In this case, the evaluation value
J changes to 0 when the speed error is further at the regeneration side than 0. That
is, the evaluation value
J changes to 0 when the rotational speed is greater than the frequency (that is, at
the right side in FIG. 3). In this case, if the frequency is controlled to make the
evaluation value
J change to 0, the frequency converges further at the regeneration side than the actual
rotational speed.
[0054] When
K = 0, the function of the evaluation value
J is
Id - Iq. In this case, the evaluation value
J changes to 0 when the speed error is further at the electromotion side than 0. That
is, the evaluation value
J changes to 0 when the rotational speed is smaller than the frequency (that is, at
the left side in FIG. 3). In this case, if the frequency is controlled to make the
evaluation value
J change to 0, the frequency converges further at the electromotion side than the actual
rotational speed.
[0055] The function of the evaluation value
J may include a
q-axis power value
Pq and a
d-axis power value
Pd instead of the
q-axis current value
Iq and the
d-axis current value
Id. Since power value
P is obtained by multiplying a current value
I and a voltage value
V together, the relationship indicated in Formula 1 remains unchanged even when the
q-axis current value
Iq and the
d-axis current value
Id are replaced with the
q-axis power value
Pq and the
d-axis power value
Pd.
[0056] FIG. 4 is a block diagram illustrating an example of the evaluation value searcher
63. The evaluation value searcher 63 includes a first evaluation value searcher 7,
a second evaluation value searcher 8, and a third evaluation value searcher 9. A switch
SW3 switches the output of the evaluation value searcher 63 among the first to third
evaluation value searchers 7 to 9.
[0057] The first evaluation value searcher 7 and the second evaluation value searcher 8
are blocks to increase or decrease the frequency based on whether the evaluation value
J has the positive sign or the negative sign so as to cause the evaluation value
J to converge at approximately 0.
[0058] The first evaluation value searcher 7 includes a subtractor 71, a sign determiner
73, a multiplier 75, and an integrator 77. The first evaluation value searcher 7 performs
hysteresis control.
[0059] When the evaluation value
J is input, the subtractor 71 performs a calculation to reverse the positive sign of
the input evaluation value
J into the negative sign, thus obtaining -J. Then, the subtractor 71 outputs
the -J to the sign determiner 73.
[0060] When the
-J from the subtractor 71 is positive, the sign determiner 73 outputs a predetermined
positive value to the multiplier 75. When the
-J from the subtractor 71 is negative, the sign determiner 73 outputs a predetermined
negative value to the multiplier 75.
[0061] The multiplier 75 multiplies the predetermined positive value or the predetermined
negative value obtained from the sign determiner 73 by an adjustment value
b, and outputs the product to the integrator 77.
[0062] The integrator 77 integrates the product obtained from the multiplier 75 and outputs
the integrated value as the frequency command
ωsear*.
[0063] The frequency at the start of the search is the frequency at the end of the previous
search performed by the previous searcher 31.
[0064] The first evaluation value searcher 7 ensures promptness in making the frequency
command
ωsear* close to the rotational speed of the induction motor 2 while reducing the load of
calculating the frequency command
ωsear*.
[0065] The second evaluation value searcher 8 includes a subtractor 81 and a PI controller
83. The second evaluation value searcher 8 performs a PI control mode.
[0066] When the evaluation value
J is input, the subtractor 81 performs a calculation to reverse the positive sign of
the input evaluation value
J into the negative sign, thus obtaining
-J. Then, the subtractor 81 outputs
the -J to the PI controller 83.
[0067] The PI controller 83 performs PI control to calculate the frequency command
ωsear* to cause the -
J from the subtractor 81 to converge at 0. Then, the PI controller 83 outputs the frequency
command
ωsear*.
[0068] The second evaluation value searcher 8 ensures accuracy in making the frequency command
ωsear* close to the rotational speed of the induction motor 2.
[0069] The third evaluation value searcher 9 changes the frequency command
ωsear* from the frequency at the start of the search by a predetermined rate.
[0070] The third evaluation value searcher 9 ends the search when the evaluation value
J converges at approximately 0.
[0071] The third evaluation value searcher 9 ensures accuracy in making the frequency command
ωsear* close to the rotational speed of the induction motor 2.
[0072] The evaluation value searcher 63 selectively uses one of the evaluation value searchers
7 to 9 to cause the evaluation value
J to converge at approximately 0. For example, it is possible to first perform the
hysteresis control using the first evaluation value searcher 7 and then perform the
PI control mode using the second evaluation value searcher 8. This ensures promptness
and accuracy in making the frequency command
ωsear* close to the rotational speed of the induction motor 2.
[0073] FIG. 5 is a time chart illustrating an exemplary speed search. FIG. 5 illustrates
a flow of a momentary power failure followed by the speed search and the normal operation.
[0074] When a momentary power failure occurs, the output of the inverter 3 stops and the
induction motor 2 turns into the free run state. Then, the rotational speed gradually
decreases.
[0075] When power supply resumes, the motor controller 10 starts the speed search to make
the frequency of the voltage applied to the induction motor 2 close to the rotational
speed of the induction motor 2. In the speed search, the motor controller 10 performs
the previous search first and performs the evaluation value search next.
[0076] The motor controller 10 performs the previous search. The frequency at the end of
the previous search is the frequency at the start of the evaluation value search.
The motor controller 10 determines the rotational direction of the induction motor
2. The determination as to the rotational direction of the induction motor 2 is made
at the end of the previous search.
[0077] In the evaluation value search, the motor controller 10 increases or decreases the
frequency based on whether the evaluation value
J has the positive sign or the negative sign, so as to cause the evaluation value
J to converge at approximately 0. Thus, the frequency gradually becomes closer to the
rotational speed. The evaluation value search is as described above. The evaluation
value search ends when the evaluation value
J converges at approximately 0.
[0078] After the evaluation value search, the motor controller 10 adjusts the gain
a (see FIG. 2) while keeping the frequency unchanged, so as to restore the applied
voltage. Then, the motor controller 10 turns into the normal operation.
[0079] FIG. 6 is a time chart illustrating an exemplary speed search. The following description
is concerning those respects different from FIG. 5.
[0080] FIG. 6 illustrates a state in which the rotational speed of the induction motor 2
in the free run state has a negative value (that is, a state in which the rotational
direction is reversed). In the previous search, the motor controller 10 makes the
rotational speed of negative value close to the frequency. In the evaluation value
search, the motor controller 10 makes the rotational speed closer to the frequency.
In the estimation of the frequency in the evaluation value search, the rotational
direction found in the previous search is added to the frequency, as described above
(see FIG. 2). This ensures estimation of the frequency based on a correct rotational
direction.
[0081] FIG. 7 is a time chart illustrating an exemplary speed search. The following description
is concerning those respects different from FIG. 5 or 6.
[0082] FIG. 7 illustrates a state in which no previous search is performed; instead the
evaluation value search is performed at the start of the speed search. In this example,
the rotational direction of the induction motor 2 and the frequency at the start are
set in advance, and the evaluation value search is performed based on these rotational
direction and frequency. For example, when the rotational direction of the induction
motor 2 is positive and the frequency at the start of the search is maximum, then
the motor controller 10 starts decreasing the frequency from the maximum toward 0,
and finally causes the evaluation value J to converge at approximately 0.
[0083] Obviously, numerous modifications and variations of the present disclosure are possible
in light of the above teachings. It is therefore to be understood that within the
scope of the appended claims, the present disclosure may be practiced otherwise than
as specifically described herein.
- 2
- Induction motor
- 3
- Inverter
- 4
- AC power supply
- 5
- Converter
- 10
- Motor controller
- 11
- V/F converter
- 12
- Gain section
- 13
- Voltage commander
- 14
- Voltage phase section
- 15
- Integrator
- 16
- Adder
- 17
- PMW controller
- 21
- α-β converter
- 22
- d-q converter
- 31
- Previous searcher
- 33
- Rotational direction setting section
- 51
- Rectifier
- 52
- Capacitor
- 61
- Calculator
- 63
- Evaluation value searcher
- 65
- Search ending determiner
- 7
- Evaluation value searcher
- 71
- Subtractor
- 73
- Sign determiner
- 75
- Multiplier
- 77
- Integrator
- 8
- Evaluation value searcher
- 81
- Subtractor
- 83
- PI controller
- 9
- Evaluation value searcher
- 100
- Motor control system