BACKGROUND OF THE INVENTION
Field of the Invention
[0001] The present invention relates to a thermosensitive recording medium and an image
processing method, which can be suitably used for write-only image recording, as well
as repetitive image recording and image erasing.
Description of the Related Art
[0002] As for a thermosensitive recording medium, there are a thermosensitive recording
medium, to which write-only image recording is performed, and a thermosensitive recording
medium, to which image recording and image erasing can be repeatedly performed.
[0003] The thermoreversible recording medium has been recently used at a delivery and physical
distribution center (see, for example, Japanese Patent Application Laid-Open (JP-A)
No.
2000-136022 and Japanese Patent (JP-B) No.
3998193).
[0004] Proposed is a thermoreversible recording medium, in which laser light is used for
recording the thermoreversible recording medium, and particles of metal boride or
metal oxide or both are used as a photothermal converting material (see
JP-A No. 2011-194883). Among these photothermal converting materials, a tungsten oxide compound has relatively
low absorbance in the visible range, and a lager amount thereof can be added compared
to other metal boride or metal oxide. Therefore, use of the tungsten oxide compound
can improve image recording sensitivity and image erasing sensitivity.
[0005] However, the tungsten oxide compound has a problem that a color thereof is turned
into blue, as the tungsten oxide compound is irradiated with light, such as sun light,
for a long period (see
JP-A No. 2008-208274). It is considered that, as the tungsten oxide compound is irradiated with light,
such as sun light, for a long period, radicals generated by irradiation of ultraviolet
rays reduces tungsten atoms in the tungsten oxide compound to generate pentavalent
tungsten that has a color However, the color of the tungsten oxide compound tends
to be returned back to the original as it is left to stand in the dark for a certain
period, and the absorbance in the near infrared region is also returned back to the
original (see
JP-A No. 2013-173642). The reason for this is considered that the pentavalent tungsten is oxidized with
oxygen to return to hexavalent tungsten.
[0006] As a result of the study conducted by the present inventors to confirm the aforementioned
matter, it has been found that the tungsten oxide compound increases not only the
absorbance in the visible region, but also the absorbance in the near infrared region,
as it is irradiated with light, such as sun light for a long period. If the absorbance
in the infrared region increases, the absorbance of laser light increases when laser
light is used for recording an image on a thermosensitive recording medium. Therefore,
the thermosensitive recording medium is excessively heated, to thereby cause a problem
that a width of writing line is widened to lower readability of a resulting bar code.
In the case where laser light is used for recording a thermoreversible recording medium,
moreover, the thermoreversible recording medium is excessively heated as image recording
is repeated, which may cause a problem that unerased portions are remained due to
the deterioration to thereby lower resistance to repetitive use.
[0007] To solve the aforementioned problems, various proposals are disclosed, for example,
in
JP-A No. 2006-282736, International Patent Publication No.
WO/2010/101211, and
JP-A Nos. 2010-99979 and
2010-274585. Any of these proposals have some effect of suppressing coloring of the tungsten
oxide compound, but the effect thereof is not sufficient.
[0008] Moreover, an image recording layer of a thermosensitive recording medium contains
a leuco dye. The leuco dye however does not have sufficient resistance to light, and
it is necessary to block not only ultraviolet rays but also oxygen to prevent deterioration
of the leuco dye due to light (see
JP-A No. 2010-195035). If oxygen is blocked, however, oxygen is not supplied into a thermosensitive recording
medium using a tungsten oxide compound as a photothermal converting material so that
pentavalent tungsten tends not to be oxidized, and therefore a color of the tungsten
oxide compound, and the increased absorbance in the near infrared region tend not
to be returned to the original states. For example, in the state where oxygen is sufficiently
blocked by sandwiching a layer containing the tungsten oxide compound with two oxygen
barrier layers, there is a problem that the color of the tungsten oxide compound and
the increased absorbance in the near infrared region are hardly returned to the original
states even after a few weeks. This problem occurs not only with the tungsten oxide
compound, but also with other metal oxides having absorbance in the near infrared
region, such as indium-doped tin oxide.
[0009] Accordingly, there is a need for a thermosensitive recording medium, which uses metal
oxide particles as a photothermal converting material, has excellent image recording
sensitivity and image erasing sensitivity, does not change its image recording sensitivity
and image erasing sensitivity over time even when it is left outside, and irradiated
with light, such as sun light, for a long period, and does not leave unerased portions
after repetitive use.
SUMMARY OF THE INVENTION
[0010] The present invention aims to provide a thermosensitive recording medium, which has
excellent image recording sensitivity, and image erasing sensitivity, does not change
the image recording sensitivity and image erasing sensitivity with time even when
left to stand outdoor, and irradiated with light, such as sun light, for a long period,
and does not cause an erasion failure due to repetitive use.
[0011] The thermosensitive recording medium of the present invention, as the means for solving
the aforementioned problems, contains:
a support;
an image recording layer, which is provided on the support, and contains a leuco dye,
a color developer, and a metal oxide having absorbance in the near infrared region;
an oxygen barrier layer; and
a light-blocking layer,
wherein the oxygen barrier layer and the light-blocking layer are provided a surface
of the image recording layer, which is an opposite side to a surface thereof where
the support is provide, and
wherein an average transmittance of the light-blocking layer to light in a wavelength
range of 300 nm to 400 nm is 5% or less, and an average transmittance of the light-blocking
layer to light in a wavelength range of 380 nm to 495 nm is 20% or less.
[0012] The present invention can solve the aforementioned various problems in the art, achieve
the aforementioned object, and provide a thermosensitive recording medium, which has
excellent image recording sensitivity, and image erasing sensitivity, does not change
the image recording sensitivity and image erasing sensitivity with time even when
left to stand outdoor, and irradiated with light, such as sun light, for a long period,
and does not cause an erasion failure due to repetitive use.
BRIEF DESCRIPTION OF THE DRAWINGS
[0013]
FIG. 1A is a schematic diagram illustrating one example of a layer structure of the
thermosensitive recording medium.
FIG. 1B is a schematic diagram illustrating another example of a layer structure of
the thermosensitive recording medium.
FIG. 2A is a schematic diagram illustrating another example of a layer structure of
the thermosensitive recording medium.
FIG. 2B is a schematic diagram illustrating another example of a layer structure of
the thermosensitive recording medium.
FIG. 2C is a schematic diagram illustrating another example of a layer structure of
the thermosensitive recording medium.
FIG. 2D is a schematic diagram illustrating another example of a layer structure of
the thermosensitive recording medium.
FIG. 2E is a schematic diagram illustrating another example of a layer structure of
the thermosensitive recording medium.
FIG. 3A is a schematic diagram illustrating another example of a layer structure of
the thermosensitive recording medium.
FIG. 3B is a schematic diagram illustrating another example of a layer structure of
the thermosensitive recording medium.
FIG. 3C is a schematic diagram illustrating another example of a layer structure of
the thermosensitive recording medium.
FIG. 3D is a schematic diagram illustrating another example of a layer structure of
the thermosensitive recording medium.
FIG. 3E is a schematic diagram illustrating another example of a layer structure of
the thermosensitive recording medium.
FIG. 4A is a graph depicting coloring-erasing properties of the thermoreversible recording
medium.
FIG. 4B is a schematic diagram explaining a mechanism of coloring-erasing changes
of the thermoreversible recording medium.
FIG. 5 is a diagram explaining one example of an image processing device for use in
the image processing method of the present invention.
FIG. 6 is a graph depicting relationship between a wavelength and a transmittance
of the light-blocking layer of Examples 1, 2, 3, and 9, and Comparative Example 9.
FIG. 7 is a graph depicting relationship between a wavelength and a transmittance
of the light-blocking layer of Example 4.
FIG. 8 is a graph depicting relationship between a wavelength and a transmittance
of the light-blocking layer of Examples 5, 6, 7, and 8.
FIG. 9 is a graph depicting relationship between a wavelength and a transmittance
of the light-blocking layer of Examples 10, 11, 12, 13, and 14.
FIG. 10 is a graph depicting relationship between a wavelength and a transmittance
of the light-blocking layer of Example 15.
FIG. 11 is a graph depicting relationship between a wavelength and a transmittance
of the light-blocking layer of Comparative Examples 1, 2, 3, 4, and 5.
FIG. 12 is a graph depicting relationship between a wavelength and a transmittance
of the light-blocking layer of Comparative Example 6.
FIG. 13 is a graph depicting relationship between a wavelength and a transmittance
of the light-blocking layer of Comparative Example 7.
FIG. 14 is a graph depicting relationship between a wavelength and a transmittance
of the light-blocking layer of Comparative Example 8.
FIG. 15 is a graph depicting relationship between a wavelength and a transmittance
of the light-blocking layer of Comparative Example 10.
DETAILED DESCRIPTION OF THE INVENTION
(Thermosensitive Recording Medium)
[0014] In the first embodiment, the thermosensitive recording medium of the present invention
contains: a support; an image recording layer, which is provided on the support, and
contains a leuco dye, a color developer, and a metal oxide having absorbance in the
near infrared region; an oxygen barrier layer; and a light-blocking layer, where the
oxygen barrier layer and the light-blocking layer are provided a surface of the image
recording layer, which is an opposite side to a surface thereof where the support
is provide, and where an average transmittance of the light-blocking layer to light
in a wavelength range of 300 nm to 400 nm is 5% or less, and an average transmittance
of the light-blocking layer to light in a wavelength range of 380 nm to 495 nm is
20% or less. The thermosensitive recording medium may further contain other layers,
as necessary. Each of these layers may have a single-layer structure, or a laminate
structure. Moreover, these layers may be provided on the other surface of the support.
[0015] In the second embodiment, the thermosensitive recording medium of the present invention
contains: a support; an image recording layer containing a leuco dye and a color developer;
a photothermal conversion layer containing a metal oxide having absorbance in the
near infrared region; an oxygen barrier layer; and a light-blocking layer, where the
image recording layer and the photothermal conversion layer are provided on the support,
and the oxygen barrier layer and the light-blocking layer are provided on a surface
of the image recording layer or the photothermal conversion layer, which is an opposite
side to a surface thereof where the support is provided, and
[0016] wherein an average transmittance of the light-blocking layer to light in a wavelength
range of 300 nm to 400 nm is 5% or less, and an average transmittance of the light-blocking
layer to light in a wavelength range of 380 nm to 495 nm is 20% or less. The thermosensitive
recording medium may further contain other layers, as necessary. Each of these layers
may have a single-layer structure, or a laminate structure. Moreover, these layers
may be provided on the other surface of the support.
[0017] The thermosensitive recording media of the first embodiment and the second embodiment
of the present invention can be used for both an embodiment where a thermosensitive
recording layer, to which write-only image recording is performed once, is provided
as an image recording layer, and an embodiment where a thermoreversible recording
layer, to which image recording and image erasing are repeatedly performed, is provided
as an image recording layer. It is however particularly preferred that the thermosensitive
recording medium is a thermoreversible recording medium, which can be used by repeatedly
performing image recording and image erasing, as it can be used repeatedly.
<Image Recording Layer>
[0018] In the first embodiment the image recording layer contains a leuco dye, a color developer,
and a metal oxide having absorbance in the near infrared region, and may further contain
other components, if necessary.
[0019] In the second embodiment, the image recording layer contains a leuco dye, and a color
developer, and may further contain other components, as necessary.
[0020] In the case where recording is performed only once, the image recording layer is
a thermosensitive recording layer. In the case where image recording and image erasing
are repeatedly performed, the image recording layer is a thermoreversible recording
layer. The thermosensitive recording layer and the thermoreversible recording layer
are separately explained, hereinafter.
«Thermosensitive Recording Layer»
[0021] The thermosensitive recording layer contains at least a leuco dye, a color developer,
and a binder resin, and may further contain other components, as necessary.
[0022] In the case where the thermosensitive recording layer contains the metal oxide having
absorbance in the near infrared region as in the first embodiment, an amount of the
metal oxide is preferably 0.005 g/m
2 to 20 g/m
2, more preferably 0.01 g/m
2 to 10 g/m
2.
-Metal Oxide Having Absorbance in Near Infrared Region-
[0023] Examples of the metal oxide having absorbance in the near infrared region include
a metal oxide having absorbance in the near infrared region, which is a wavelength
region of 700 nm to 2,000 nm.
[0024] For example, the metal oxide is preferably at least one selected from the group consisting
of a tungsten oxide compound, indium-doped tin oxide, and antimony-doped tin oxide.
The aforementioned metal oxide having absorbance in the near infrared region has high
resistance to heat, unlike an organic dye, such as phthalocyanine. Moreover, the metal
oxide does not have an interaction with a leuco dye, when the metal oxide is missed
with the leuco dye, and the absorbance thereof in the near infrared region does not
decrease when the metal oxide is irradiated with laser light repeatedly. Therefore,
use of the metal oxide gives an advantage that a highly durable thermosensitive recording
medium can be attained.
[0025] Among the tungsten oxide compound, the indium-doped tin oxide, and the antimony-doped
tin oxide, the tungsten oxide compound and the indium-doped tin oxide are preferable,
as they have low absorbance in the visible range, and the tungsten oxide compound
is more preferable.
[0026] Examples of the tungsten oxide compound include composite tungsten oxide particles
represented by the general formula: WyOz (where W is tungsten, O is oxygen, and 2.2
≤ z/y ≤ 2.999), and tungsten oxide particles represented by the general formula: MxWyOz
(where M is at least one element selected from the group consisting of H, He, an alkali
metal, an alkaline earth metal, a rare earth element, Mg, Zr, Cr, Mn, Fe, Ru, Co,
Rh, Ir, Ni, Pd, Pt, Cu, Ag, Au, Zn, Cd, Al, Ga, In, Tl, Si, Ge, Sn, Pb, Sb, B, F,
P, S, Se, Br, Te, Ti, Nb, V, Mo, Ta, Re, Be, Hf, Os, Bi, and I, W is tungsten, O is
oxygen, 0.001 ≤ x/y ≤ 1, and 2.2 ≤ z/y ≤ 3.0), as disclosed in International Patent
Publication No.
WO/2005/037932, and
JP-A No. 2005-187323.
[0027] Among them, cesium-containing tungsten oxide is particularly preferable, as it has
large absorbance in the near infrared region, and small absorbance in the visible
region.
[0028] Since the metal oxide having absorbance in the near infrared has absorbance in the
near infrared region, which is a wavelength range of 700 nm to 2,000 nm, excellent
recording sensitivity can be attained by setting a wavelength of laser light sued
for recording and erasing of an image to the aforementioned wavelength range.
[0029] The average particle diameter of the metal oxide having absorbance in the near infrared
region is preferably 800 nm or smaller to reduce absorbance in the visible region,
and is preferably 200 nm or smaller to reduce scattering due to the particles. The
lower limit of the average particle diameter is preferably 1 nm or greater.
[0030] The average particle diameter can be measured, for example, by a laser diffraction/scattering
particle size distribution analyzer.
[0031] An amount of the metal oxide having absorbance in the near infrared region varies
depending on a type of the metal oxide for use, and cannot be collectively determined.
However, the amount thereof is preferably 0.005 g/m
2 to 20 g/m
2, more preferably 0.01 g/m
2 to 10 g/m
2, relative to a layer containing the metal oxide. When the amount thereof is less
than 0.005 g/m
2, sufficient recording sensitivity may not be attained. When the amount thereof is
greater than 20 g/m
2, a degree of tint on the background increases as the metal oxide has slight absorbance
in the visible region, which reducing contrast of an image.
[0032] Note that, whether or not the metal oxide having absorbance in the near infrared
region is present can be judged by measuring absorbance properties in the near infrared
region by means of a spectrophotometer (U-4100, manufactured by Hitachi High-Technologies
Corporation), as all of the metal oxides having the absorbance in the near infrared
region have unique absorbance properties.
-Leuco Dye-
[0033] The leuco dye is appropriately selected from leuco dyes typically used for thermosensitive
recording materials, without any limitation. As for the leuco dye, for example, a
leuco compound, such as a triphenylmethane-based dye, a fluoran-based dye, a phenothiazine-based
dye, an auramine-based dye, a spiropyran-based dye, an indolinophthalide-based dye,
is preferably used.
[0034] Examples of the leuco dye include 2-anilino-3-methyl-6-dibutylaminofluoran, 3,3-bis(p-dimethylaminophenyl)-phthalide,
3,3-bis(p-dimethylaminophenyl)-6-dimethylaminophthalide (another name: Crystal Violet
Lactone), 3,3-bis(p-dimethylaminophenyl)-6-diethylaminophthalide, 3,3-bis(p-dimethylaminophenyl)-6-chlorophthalide,
3,3-bis(p-dibutylaminophenyl)phthalide, 3-cyclohexylamino-6-chlorofluoran, 3-dimethylamino-5,7-dimethylfluoran,
3-diethylamino-7-chlorofluoran, 3-diethylamino-7-methylfluoran, 3-diethylamino-7,8-benzfluoran,
3-diethylamino-6-methyl-7-chlorofluoran, 3-(N-p-tolyl-N-ethylamino)-6-methyl-7-anilinoffuoran,
2-{N-(3'-trifluoromethylphenyl)amino}-6-diethylaminofluoran, 2-{3,6-bis(diethylamino)-9-(o-chloroanilino)xanthylbenzoic
acid lactam}, 3-diethylamino-6-methyl-7-(m-trichloromethylanilino)fluoran, 3-diethylamino-7-(o-chloroanilino)fluoran,
3-pyrrolidino-6-methyl-7-anilinofluoran, 3-di-n-butylamino-7-o-chloroanilino)fluoran,
3-N-methyl-N,n-amylamino-6-methyl-7-anilinofluoran, 3-N-methyl-N-cyclohexylamino-6-methyl-7-anilinofluoran,
3-diethylamino-6-methyl-7-anilinofluoran, 3-(N,N-diethylamino)-5-methyl-7-(N,N-dibenzylamino)fluoran,
benzoyl leuco methylene blue, 6'-chloro-8'-methoxy-benzoindolino-spiropyran, 6'-bromo-3'-methoxy-benzoindolino-spiropyran,
3-(2'-hydroxy-4'-dimethylaminophenyl)-3-(2'-methoxy-5'-chlorophenyl)phthalide, 3-(2'-hydroxy-4'-dimethylaminophenyl)-3-(2'-methoxy-5'-nitrophenyl)phthalide,
3-(2'-hydroxy-4'-diethylaminophenyl)-3-(2'-methoxy-5'-methylphenyl)phthalide, 3-(2'-methoxy-4'-dimethylaminophenyl)-3-(2'-hydroxy-4'-chloro-5'-methylphenyl)phthalide,
3-(N-ethyl-N-tetrahydrofurfuryl)amino-6-methyl-7-anilinofluoran, 3-N-ethyl-N-(2-ethoxypropyl)amino-6-methyl-7-anilinofluoran,
3-N-methyl-N-isobutyl-6-methyl-7-anilinofluoran, 3-morpholino-7-(N-propyl-trifluoromethylanilino)fluoran,
3-pyrrolidino-7-trifluoromethylanilinofluoran, 3-diethylamino-5-chloro-7-(N-benzyl-trifluoromethylanilino)fluoran,
3-pyrrolidino-7-(di-p-chlorophenyl)methylaminofluoran, 3-diethylamino-5-chloro-7-(α-phenylethylamino)fluoran,
3-(N-ethyl-p-toluidino)-7-(α-phenylethylamino)fluoran, 3-diethylamino-7-(o-methoxycarbonylphenylamino)fluoran,
3-diethylamino-5-methyl-7-(α-phenylethylamino)fluoran, 3-diethylamino-7-piperidinofluoran,
2-chloro-3-(N-methyltoluidino)-7-(p-n-butylanilino)fluoran, 3-di-n-butylamino-6-methyl-7-anilinofluoran,
3,6-bis(dimethylamino)fluorenespiro(9,3')-6'-dimethylaminophthalide, 3-(N-benzyl-N-cyclohexylamino)-5,6-benzo-7-α-naphthylamino-4'-bromofluoran,
3-diethylamino-6-chloro-7-anilinofluoran, 3-diethylamino-6-methyl-7-cimetidino-4',5'-benzfluoran,
3-N-methyl-N-isopropyl-6-methyl-7-anilinofluoran, 3-N-ethyl-N-isoamyl-6-methyl-7-anilinofluoran,
3-diethylamino-6-methyl-7-(2',4'-dimethylanilino)fluoran, 3-morpholino-7-(N-propyl-trifluoromethylanilino)fluoran,
3-pyrrolidino-7-trifluoromethylanilinofluoran, 3-diethylamino-5-chloro-7-(N-benzyl-trifluoromethylanilino)fluoran,
3-pyrrolidino-7-(di-p-chlorophenyl)methylaminofluoran, 3-diethylamino-5-chloro-(α-phenylethylamino)fluoran,
3-(N-ethyl-p-toluidino)-7-(α-phenylethylamino)fluoran, 3-diethylamino-7-(o-methoxycarbonylphenylamino)fluoran,
3-diethylamino-5-methyl-7-(α-phenylethylamino)fluoran, 3-diethylamino-7-piperidinofluoran,
2-chloro-3-(N-methyltoluidino)-7-(p-N-butylanilino)fluoran, 3,6-bis(dimethylamino)fluorenespiro(9,3')-6'-dimethylaminophthalide,
3-(N-benzyl-N-cyclohexylamino)-5,6-benzo-7-α-naphthylamino-4'-bromofluoran, 3-diethylamino-6-chloro-7-anilinofluoran,
3-N-ethyl-N-(-2-ethoxypropyl)amino-6-methyl-7-anilinofluoran, 3-N-ethyl-N-tetrahydrofurfurylamino-6-methyl-7-anilinofluoran,
3-p-dimethylaminophenyl)-3-{1,1-bis(p-dimethylaminophenyl)ethylen-2-yl}phthalide,
3-(p-dimethylaminophenyl)-3-{1,1-bis(p-dimethylaminophenyl)ethylen-2-yl}-6-dimethylami
nophthalide, 3-(p-dimethylaminophenyl)-3-(1-p-dimethylaminophenyl-1-phenylethylen-2-yl)phthalide,
3-(p-dimethylaminophenyl)-3-(1-p-dimethylaminophenyl-1-p-chlorophenylethylen-2-yl)-6-di
methylaminophthalide, 3-(4'-dimethylamino-2'-methoxy)-3-(1"-p-dimethylaminophenyl-1"-p-chlorophenyl-1",3"-but
adien-4"-yl)benzophthalide, 3-(4'-dimethylamino-2'-benzyloxy)-3-(1"-p-dimethylaminophenyl-1"-phenyl-1",3"-butadien-4
"-yl)benzophthalide, 3-dimethylamino-6-dimethylamino-fluorene-9-spiro-3'-(6'-dimethylamino)phthalide,
3,3-bis(2-(p-dimethylaminophenyl)-2-p-methoxyphenyl)ethenyl)-4,5,6,7-tetrachlorophthalid
e, 3-bis{1,1-bis(4-pyrrolidinophenyl)ethylen-2-yl}-5,6-dichloro-4,7-dibromophthalide,
bis(p-dimethylaminostyryl)-1-naphthalenesufonylmethane, and bis(p-dimethylaminostyryl)-1-p-trisulfonylmethane.
These may be used alone, or in combination.
-Color Developer-
[0035] As for the color developer, various electron-accepting compounds or oxidizing agents,
which colors the leuco dye when they are in contact with the leuco dye, are suitably
used.
[0036] The color developer is appropriately selected from those known in the art depending
on the intended purpose without any limitation. Examples thereof include 4,4'-isopropylidenebisphenol,
4,4'-isopropylidenebis(o-methylphenol), 4,4'-sec-butylidenebisphenol, 4,4'-isopropylidenebis(2-tert-butylphenol),
zinc p-nitrobenzoate, 1,3,5-tris(4-tert-butyl-3-hydroxy-2,6-dimethylbenzyl)isocyanurate,
2,2-(3,4'-dihydroxydiphenyl)propane, bis(4-hydroxy-3-methylphenyl)sulfide, 4-{β-(p-methoxyphenoxy)ethoxy}salicylic
acid, 1,7-bis(4-hydroxyphenylthio)-3,5-dioxaheptane, 1,5-bis(4-hydroxyphenylthio)-5-oxaheptane,
monocalcium salt of monobenzyl phthalte, 4,4'-cyclohexylidene diphenol, 4,4'-isopropylidenebis(2-chlorophenol),
2,2'-methylenebis(4-methyl-6-tert-butylphenol), 4,4'-butylidenebis(6- tert-butyl-2-methyl)phenol,
1, 1,3-tris(2-methyl-4-hydroxy-5-tert-butylphenyl)butane, 1,1,3-tris(2-methyl-4-hydroxy-5-cyclohexylphenyl)butane,
4,4'-thiobis(6-tert-butyl-2-methyl)phenol, 4,4'-diphenolsulfone, 4-isopropoxy-4'-hydroxydiphenylsulfone(4-hydroxy-4'-isopropoxydiphenylsulfone),
4-benzyloxy-4'-hydroxydiphenylsulfone, 4,4'-diphenolsulfoxide, isopropyl p-hydroxybenzoate,
benzyl p-hydroxybenzoate, benzyl protocatechuate, stearyl gallate, lauryl gallate,
octyl gallate, 1,3-bis(4-hydroxyphenylthio)-propane, N,N'-diphenylthiourea, N,N'-di(m-chlorophenyl)thiourea,
salicylanilide, methyl bis-(4-hydroxyphenyl)acetate, benzyl bis-(4-hydroxyphenyl)acetate,
1,3-bis(4-hydroxycumyl)benzene, 1,4-bis(4-hydroxycumyl)benzene, 2,4'-diphenolsulfone,
2,2'-diallyl-4,4'-diphenolsulfone, 3,4-dihydroxyphenyl-4'-methyldiphenylsulfone, zinc
1-acetyloxy-2-naphthoate, zinc 2-acetyloxy-1-naphthoate, zinc 2-acetyloxy-3-naphthoate,
α,α-bis(4-hydroxyphenyl)-α-methyltoluene, an antipyrine complex of zinc thiocyanate,
tetrabromobisphenol A, tetrabromobisphenol S, 4,4'-thiobis(2-methylphenol), 4,4'-thiobis(2-chlorophenol),
dodecylphosphonic acid, tetradecylphosphonic acid, hexadecylphosphonic acid, octadecylphosphonic
acid, eicosylphosphonic acid, docosylphosphonic acid, tetracosylphosphonic acid, hexacosylphosphonic
acid, octacosylphosphonic acid, α-hydroxydodecylphosphonic acid, α-hydroxytetradecylphosphonic
acid, α-hydroxyhexadecylphosphonic acid, α-hydroxyoctadecylphosphonic acid, α-hydroxyeicosylphosphonic
acid, α-hydroxydocosylphosphonic acid, α-hydroxytetracosylphosphonic acid, dihexadecyl
phosphate, dioctadecyl phosphate, dieicosyl phosphate, didocosyl phosphate, monohexadecyl
phosphate, monooctadecyl phosphate, monoeicosyl phosphate, monodocosyl phosphate,
methylhexadecyl phosphate, methyloctadecyl phosphate, methyleicosyl phosphate, methyldocosyl
phosphate, amylhexadecyl phosphate, octyl hexadecyl phosphate, and lauryl hexadecyl
phosphate. These may be used alone, or in combination.
[0037] An amount of the color developer is preferably 1 part by mass to 20 parts by mass,
more preferably 2 parts by mass to 10 parts by mass, relative to 1 part by mass of
the leuco dye.
-Binder Resin-
[0038] The binder resin is appropriately selected from binder resins known in the art depending
on the intended purpose without any limitation. Examples of the binder resin include:
a water-soluble polymer, such as polyvinyl alcohol, starch or a derivative thereof,
a cellulose derivative (e.g., methoxy cellulose, hydroxyethyl cellulose, carboxymethyl
cellulose, methyl cellulose, and ethyl cellulose), sodium polyacrylate, polyvinylpyrrolidone,
an acrylamide/acrylate copolymer, an acrylamide/acrylate/methacrylic acid tercopolymer,
an alkali salt of a styrene/maleic anhydride copolymer, an alkali salt of an isobutylene-maleic
anhydride copolymer, polyacrylamide, sodium alginate, gelatin, and casein; an emulsion,
such as polyvinyl acetate, polyurethane, polyacrylic acid, polyacrylate, polymethacrylate,
polybutyl methacrylate, a vinyl chloride-vinyl acetate copolymer, and an ethylene-vinyl
acetate copolymer; latex, such as a styrene-butadiene copolymer, and a styrene-butadiene/acryl-based
copolymer; polyethylene; polyvinyl acetate; polyacrylic amide; a maleic acid copolymer;
polyacrylate; polymethacrylate; a vinyl chloride/vinyl acetate copolymer; styrene
copolymer; polyester; polyurethane; polyvinyl butyral; ethyl cellulose; polyvinyl
acetal; polyvinyl acetoacetal; polycarbonate; an epoxy resin; and polyamide. These
may be used alone, or in combination.
[0039] In the thermosensitive recording layer, various thermoplastic materials can be used
as a sensitivity improving agent.
[0040] Examples of the thermoplastic material include fatty acid, fatty acid amide, fatty
acid metal salt, p-benzylbiphenyl, terphenyl, triphenylmethane, benzyl p-benzyloxybenzoate,
B-benzyloxynaphthalene, phenyl β-naphthoate, phenyl 1-hydroxy-2-naphthoate, methyl
1-hydroxy-2-naphthoate, diphenyl carbonate, dibenzyl terephthalate, dimethyl terephthalate,
1,4-dimethoxynaphthalene, 1,4-diethoxynaphthalene, 1,4-dibenzyloxynaphthalene, 1,2-bis(phenoxy)ethane,
1,2-bis(3-methylphenoxy)ethane, 1,2-bis(4-methylphenoxy)ethane, 1,4-bis(phenoxy)butane,
1,4-bis(phenoxy)-2-butene, 1,2-bis(4-methoxyphenylthio)ethane, dibenzoylmethane, 1,4-bis(phenylthio)butane,
1,4-bis(phenylthio)-2-butene, 1,2-bis(4-methoxyphenylthio)ethane, 1,3-bis(2-vinyloxyethoxy)benzene,
1,4-bis(2-vinyloxyethoxy)benzene, p-(2-vinyloxyethoxy)biphenyl, p-aryloxybiphenyl,
p-propargyloxybiphenyl, dibenzoyloxymethane, 1,3-dibenzoyloxypropane, dibenzyl disulfide,
1,1-diphenyl ethanol, 1,1-diphenyl propanol, p-(benzyloxy)benzyl alcohol, 1,3-diphenoxy-2-propanol,
N-octadecylcarbamoyl-p-methoxycarbonylbenzene, N-octadecylcarbamoylbenzene, dibenzyl
oxalate, and 1,5-bis(p-methoxyphenyloxy)-3-oxapentane. These may be used alone, or
in combination.
[0041] An antioxidant or photostabilizer is preferably added to the thermosensitive recording
layer for the purpose of suppressing absorbance increase of the metal oxide in the
infrared region due to light irradiation.
[0042] The antioxidant or photostabilizer is appropriately selected depending on the intended
purpose without any limitation. Examples thereof include a phenol-based compound,
a hindered phenol-based compound, an amine-based compound, a hindered amine-based
compound, an amide-based compound, a sulfur-based compound, a thioether-based compound,
a phosphorus-based compound, and a lactone-based compound. Among them, a hindered
phenol-based compound is preferable, as it has a large effect to the tungsten oxide
compound.
[0043] Examples of the hindered phenol-based compound include pentaerythritol-tetrakis(3-(3,5-di-t-butyl-4-hydroxyphenyl)propionate),
thiodiethylene-bis(3-(3,5-di-t-butyl-4-hydroxyphenyl)propionate), octadecyl-3-(3,5-di-t-butyl-4-hydroxyphenyl)propionate,
1,3,5-trimethyl-2,4,6-tris(3,5-di-tert-butyl-4-hydroxybenzyl)benzene, N,N'-hexan-1,6-diylbis(3-(3,5-di-t-butyl-4-hydroxyphenyl)propionamide),
diethyl((3,5-bis(1,1-dimethylethyl)-4-hydroxyphenyl)methyl) phosphate, 3,3',3",5,5',5"-hexa-t-butyl-a,a',a"-(mesitylene-2,4,6-triyl)tri-p-cresol,
ethylenebis(oxyethylene)bis(3-(5-t-butyl-4-hydroxy-m-triyl)propionate), hexamethylene-bis(3-(3,5-di-t-butyl-4-hydroxyphenyl)propionate),
1,3,5-tris(3,5-di-t-butyl-4-hydroxybenzyl)-1,3,5-triazine-2,4,6(1H,3H,5H)-trione,
1,3,5-tris((4-t-butyl-3-hydroxy-2,6-xylyl)methyl)-1,3,5-triazine-2,4,6(1H,3H,5H)-trione,
2,6-di-t-butyl-4-(4,6-bis(octylthio)-1,3,5-triazin-2-ylamino)phenol, and 3,9-bis(2-(3-(3-t-butyl-4-hydroxy-5-methylphenyl)propionyloxy)-1,1-dimethylethyl)-2,4,8,10-tetraoxaspiro(5,5)undecane.
These may be used alone, or in combination.
[0044] An amount of the antioxidant or photostabilizer cannot be collectively determined,
as it varies depending on a type of the metal oxide for use, but the amount thereof
is preferably 0.1 parts by mass to 100 parts by mass, more preferably 1 part by mass
to 50 parts by mass relative to 100 parts by mass of the metal oxide. When the amount
thereof is less than 0.1 parts by mass, an effect of supressing absorbance increase
may not be attained. When the amount thereof is greater than 100 parts by mass, the
thermal strength of the thermosensitive recording layer may be low, or the adhesion
to another layer may be reduced.
[0045] To the thermosensitive recording medium, various additives, such as a surfactant,
a lubricant, and filler, may be used in combination, as necessary. Examples of the
lubricant include higher fatty acid or a metal salt thereof, higher fatty acid amide,
higher fatty acid ester, animal wax, vegetable wax, mineral wax, and petroleum wax.
[0046] Examples of the filler include: inorganic powder, such as calcium carbonate, silica,
zinc oxide, titanium oxide, aluminium hydroxide, zinc hydroxide, barium sulfate, clay,
kaolin, talc, surface-treated calcium, and surface-treated silica; and organic powder,
such as a urea-formaldehyde resin, a styrene/methacrylic acid copolymer, a polystyrene
resin, and a vinylidene chloride resin.
[0047] The thermosensitive recording layer can be formed by a method generally known in
the art without any limitation. For example, the thermosensitive recording layer can
be formed by grinding and dispersing a leuco dye, and a color developer separately
with a binder resin and other components by means of a disperser, such as a ball mill,
Attritor, and a sand mill until the dispersed particle diameter thereof becomes 0.1
µm to 3 µm, blending the resultants with optional filler and/or a lubricant according
to the predetermined formulation to thereby prepare a thermosensitive recording layer
coating liquid, and applying the thermosensitive recording layer coating liquid onto
a support.
[0048] The average thickness of the thermosensitive recording layer is appropriately selected
depending on the intended purpose without any limitation, but the average thickness
thereof is preferably 1 µm to 20 µm, more preferably 3 µm to 15 µm.
«Thermoreversible Recording Layer»
[0049] The thermoreversible recording layer contains at least a leuco dye, a reversible
color developer, and a binder resin, and may further contain other components, as
necessary.
-Metal Oxide Having Absorbance in Near Infrared Region-
[0050] In the case where the thermoreversible recording layer contains the metal oxide having
absorbance in the near infrared region as in the first embodiment, an amount of the
metal oxide is preferably 0.005 g/m
2 to 20 g/m
2, more preferably 0.01 g/m
2 to 10 g/m
2.
-Leuco Dye-
[0051] The leuco dye is appropriately selected from those known in the art without any limitation.
For example, those usable for the thermosensitive recording layer can be used.
-Reversible Color Developer-
[0052] The reversible color developer is appropriately selected depending on the intended
purpose without any limitation, provided that it is capable of reversibly coloring
and erasing using heat as a factor. Preferred examples thereof include (1) a structure
having an ability of coloring the leuco dye (e.g., a phenolic hydroxyl group, a carboxylic
acid group, and a phosphoric acid group), or (2) a structure for controlling aggregation
force between molecules (e.g., a structure linked with a long-chain hydrocarbon group),
or both in a molecule thereof. Note that, the linking part may contain a bivalent
or higher linking group containing a hetero atom, and the ling-chain hydrocarbon group
may contain the same linking group, or an aromatic group, or both.
[0053] As for the (1) structure having an ability of coloring the leuco dye, phenol is particularly
preferable.
[0054] As for the (2) structure for controlling aggregation force between molecules, a C8
or higher long-chain hydrocarbon group is preferable, a C11 or higher long-chain hydrocarbon
group is more preferable. Moreover, the upper limit of the number of carbon atoms
is preferably 40 or less, more preferably 30 or less.
[0055] Among the aforementioned reversible color developers, a phenol compound represented
by the following general formula (1) is preferable, and a phenol compound represented
by the following general formula (2) is more preferable.
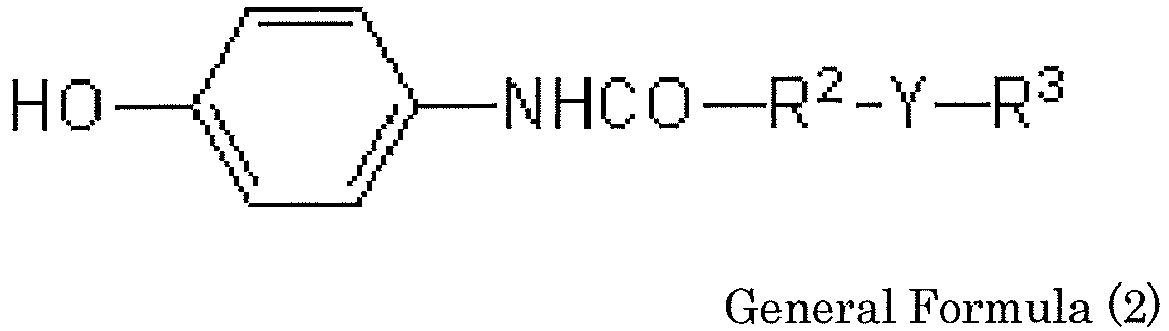
[0056] In the general formulae (1) and (2) above, R
1 is a single bond or C1-C24 aliphatic hydrocarbon group; R
2 is a C2 or higher aliphatic hydrocarbon group that may have a substituent, in which
a number of the carbon atoms is preferably 5 or greater, more preferably 10 or greater;
and R
3 is a C1 to C35 aliphatic hydrocarbon group, the number of carbon atoms of which is
preferably 6 to 35, and more preferably 8 to 35. These aliphatic hydrocarbon groups
may be used alone, or in combination.
[0057] A total number of carbon atoms in R
1, R
2, and R
3 is appropriately selected depending on the intended purpose without any limitation,
but the lower limit thereof is preferably 8 or greater, more preferably 11 or greater,
and the upper limit thereof is preferably 40 or less, more preferably 35 or less.
When the total number of the carbon atoms is less than 8, the stability of coloring
and erasing ability may be low. The aliphatic hydrocarbon group may be a straight-chain
aliphatic hydrocarbon group, or a branched-chain aliphatic hydrocarbon group, and
may contain an unsaturated bond. However, the aliphatic hydrocarbon group is preferably
a straight-chain aliphatic hydrocarbon group. Moreover, examples of a substituent
bonded to the hydrocarbon group include a hydroxyl group, a halogen atom, and an alkoxy
group. X and Y may be identical or different, and each represents a bivalent group
containing an N atom or an O atom. Specific examples thereof include an oxygen atom,
an amide group, a urea group, a diacylhydrazine group, an oxalic acid diamide group,
and an acyl urea group. Among them, an amide group, and a urea group are preferable.
In the general formulae (1) and (2), n is an integer of 0 to 1.
[0058] The reversible color developer is preferably used in combination with a compound
containing a -NHCO- group, or a -OCONH- group, or both in a molecule thereof as an
erasing accelerator, as an intermolecular interaction is induced between the erasing
accelerator and the color developer in the process of forming an erased state to thereby
improve coloring and erasing properties. The erasing accelerator is appropriately
selected depending on the intended purpose without any limitation.
[0059] To the thermoreversible recording layer, a binder resin, and optionally various additives
for improving or controlling coating properties of the thermoreversible recording
layer or coloring and erasing properties can be added. Examples of the additives include
a surfactant, a conducting agent, filler, an antioxidant, a photostabilizer, a coloring
stabilizer, and a photothermal conversion agent.
-Binder Resin-
[0060] The binder resin is appropriately selected depending on the intended purpose without
any limitation, provided that it can bind the thermoreversible recording layer on
the support. One, or two or more selected from resins known in the art can be used
alone or in combination, as the binder resin. Among them, a resin curable by heat,
UV rays, or electron beams is preferable in view of an improvement in durability for
repetitive use, and a thermoset resin using an isocyanate-based compound as a crosslinking
agent is particularly preferable. Examples of the binder resin include a resin containing
a group reactable with a crosslinking agent, such as a hydroxyl group and a carboxyl
group, and a resin obtained by copolymerizing a monomer containing a hydroxyl group
or a carboxyl group with another monomer.
[0061] Examples of the resin include a phenoxy resin, a polyvinyl butyral resin, a cellulose
acetate propionate resin, a cellulose acetate butylate resin, an acryl polyol resin,
a polyester polyol resin, and a polyurethane polyol resin. Among them, particularly
preferred are an acryl polyol resin, a polyester polyol resin, and a polyurethane
polyol resin.
[0062] As for the blending ratio (mass ratio) of the binder resin to the leuco dye in the
thermoreversible recording layer, the ratio of the binder resin is preferably 0.1
to 10, relative to the leuco dye (1). When the ratio of the binder resin is too low,
thermal strength of the thermoreversible recording layer may become insufficient.
When the ratio of the binder resin is too high, coloring density of the thermoreversible
recording layer may become low.
[0063] The crosslinking agent is appropriately selected depending on the intended purpose
without any limitation, and examples thereof include isocyanate, an amino resin, a
phenol resin, amine, and an epoxy compound. Among them, isocyanate is preferably,
and a polyisocyanate compound having a plurality of isocyanate groups is particularly
preferable. As for an amount of the crosslinking agent to the binder resin, preferred
is an amount thereof with which a ratio of the number of functional groups of the
crosslinking agent to the number of active groups contained in the binder resin is
in the range of 0.01 to 2. When the ratio is less than 0.01, the thermal strength
may be low. When the ratio is greater than 2, coloring and erasing properties may
be adversely affected. Moreover, a catalyst typically used for the aforementioned
use may be used as a crosslinking accelerator. In the case where the heat-activated
crosslink reaction is carried out, the gel fraction of the heat-crosslinkable resin
is preferably 30% or greater, more preferably 50% or greater, and even more preferably
70% or greater. When the gel fraction is less than 30%, the crosslinked state is not
sufficient, which may lead to insufficient durability.
[0064] Examples of a method for determining whether or not the binder resin is in the crosslinked
state or in the non-crosslinked state include a method where a coating film is immersed
in a solvent having high solubility. Specifically, the binder resin in the non-crosslinked
state is dissolved in the solvent, and does not remain in the solute.
[0065] Other components for use in the thermoreversible recording layer are appropriately
selected depending on the intended purpose without any limitation. Examples thereof
include a surfactant, and a plasticizer for the purpose of making image recording
easier.
[0066] A method for forming the thermoreversible recording layer is appropriately selected
from methods known in the art depending on the intended purpose without any limitation.
Preferable examples thereof include: (1)a method containing applying a thermoreversible
recording layer coating liquid, which is prepared by dissolving or dispersing the
resin, the leuco dye, and the reversible color developer in a solvent, onto a support,
and crosslinking at the same time as, or after evaporating the solvent and forming
into a sheet, (2) a method containing applying a thermoreversible recording layer
coating liquid, which is prepared by dispersing the leuco dye and the reversible color
developer in a solvent to which only the resin has been dissolved, onto a support,
and crosslinking at the same time as, or after evaporating the solvent and forming
into a sheet. Note that, in these methods, a sheet-shaped thermoreversible recording
medium can be also shaped without using the support. The solvent for use in the aforementioned
methods cannot be collectively determined, as it varies depending on the resin, leuco
dye, and reversible color developer for use. Examples of the solvent include tetrahydrofuran,
methyl ethyl ketone, methyl isobutyl ketone, chloroform, carbon tetrachloride, ethanol,
toluene, and benzene. Note that, the reversible color developer is present as dispersed
particles in the thermoreversible recording layer.
[0067] To the thermoreversible recording layer coating liquid, various pigments, defoaming
agents, coloring agents, dispersing agents, slipping agents, preservatives, crosslinking
agents, and plasticizers may be added for the purpose of realizing high performance
as a coating material.
[0068] Examples of the coating method include blade coating, wire-bar coating, spray coating,
air-knife coating, bead coating, curtain coating, gravure coating, kiss coating, reverse
roll coating, dip coating, and die coating.
[0069] The average thickness of the thermoreversible recording layer is appropriately selected
depending on the intended purpose without any limitation. For example, the average
thickness thereof is preferably 1 µm to 20 µm, more preferably 3 µm to 18 µm. When
the average thickness of the thermoreversible recording layer is less than 1 µm, a
contrast of a resulting image may be low, as the coloring density is low. When the
average thickness thereof is greater than 20 µm, a heat distribution within the layer
becomes wide so that there is an area which does not reach the coloring temperature
and does not color, and therefore desired color density cannot be attained.
[0070] In the case where a photothermal conversion layer is provided as in the second embodiment,
a first thermoreversible recording layer and a second thermoreversible recording layer
can be provided in the manner that the photothermal conversion layer is sandwiched
with the first and second thermoreversible recording layers. As a result of this structure,
heat generated in the photothermal conversion layer is efficiently used to thereby
attain excellent recording sensitivity.
[0071] In the case where a first thermoreversible recording layer and a second thermoreversible
recording layer are provided, the average thickness of the first thermoreversible
recording layer is preferably 0.1 µm to 15 µm, and the average thickness of the second
thermoreversible recording layer is preferably 0.1 µm to 15 µm.
<Photothermal Conversion Layer>
[0072] In the case where laser light having a wavelength in the near infrared region, such
as semiconductor laser, YAG laser, and fiber laser, is used, a photothermal conversion
layer is preferably provided.
[0073] The photothermal conversion layer contains at least metal oxide having absorbance
in the near infrared region, which is configured to absorb the aforementioned laser
light at high efficiency to generate heat. The metal oxide having absorbance in the
near infrared region may be contained in one of layers in contact with the thermoreversible
recording layer. In the case where the metal oxide having absorbance in the near infrared
region is contained in the thermoreversible recording layer, the thermoreversible
recording layer also functions as the photothermal conversion layer. Moreover, there
is a case where a barrier layer is formed between the thermoreversible recording layer
and the photothermal conversion layer for the purpose of preventing an interaction
between constitutional materials of the thermoreversible recording layer and the photothermal
conversion layer. In this case, a resin curable by heat, ultraviolet rays, or electron
beams is preferably contained as a material. The layer provided between the thermoreversible
recording layer and the photothermal conversion layer is appropriately selected depending
on the intended purpose without any limitation.
[0074] In the case where the photothermal conversion layer is provided, the photothermal
converting material is typically used in combination with a binder resin.
[0075] The binder resin is appropriately selected from binder resins known in the art without
any limitation, provided that it can hold the metal oxide having absorbance in the
near infrared region. As for the binder resin, a thermoplastic resin, and a thermoset
resin are preferable, and resins identical to those listed as the binder resin for
the thermoreversible recording layer can be suitably used. Among them, a resin curable
by heat, ultraviolet rays, or electron beam is preferable for improving resistance
to repetitive use, and a heat-crosslinkable resin using an isocyanate-based compound
as a crosslinking agent is particularly preferable.
[0076] The average thickness of the photothermal conversion layer is appropriately selected
depending on the intended purpose without any limitation, but the average thickness
thereof is preferably 0.1 µm to 20 µm.
[0077] An amount of the metal oxide having absorbance in the near infrared region is preferably
0.005 g/m
2 to 20 g/m
2, more preferably 0.01 g/m
2 to 10 g/m
2.
[0078] To the photothermal conversion layer, an antioxidant or a photostabilizer is preferable
added to prevent an increase in absorbance of the metal oxide in the near infrared
region.
[0079] The antioxidant or photostabilizer is appropriately selected depending on the intended
purpose without any limitation, and examples thereof include a phenol-based compound,
a hindered phenol-based compound, an amine-based compound, a hindered amine-based
compound, an amide-based compound, a sulfur-based compound, a thioether-based compound,
a phosphorus-based compound, and a lactone-based compound. Among them, a hindered
phenol-based compound is preferable, as an effect to the tungsten oxide compound is
large.
[0080] Examples of the hindered phenol-based compound include pentaerythritol-tetrakis(3-(3,5-di-t-butyl-4-hydroxyphenyl)propionate),
thiodiethylene-bis(3-(3,5-di-t-butyl-4-hydroxyphenyl)propionate), octadecyl-3-(3,5-di-t-butyl-4-hydroxyphenyl)propionate,
1,3,5-trimethyl-2,4,6-tris(3,5-di-tert-butyl-4-hydroxybenzyl)benzene, N,N'-hexan-1,6-diylbis(3-(3,5-di-t-butyl-4-hydroxyphenyl)propionamide),
diethyl((3,5-bis(1,1-dimethylethyl)-4-hydroxyphenyl)methyl) phosphate, 3,3',3",5,5',5"-hexa-t-butyl-a,a',a"-(mesitylene-2,4,6-triyl)tri-p-cresol,
ethylenebis(oxyethylene)bis(3-(5-t-butyl-4-hydroxy-m-tryl)propionate), hexamethylene-bis(3-(3,5-di-t-butyl-4-hydroxyphenyl)propionate),
1,3,5-tris(3,5-di-t-butyl-4-hydroxybenzyl)-1,3,5-triazine-2,4,6(1H,3H,5H)-trione,
1,3,5-tris((4-t-butyl-3-hydroxy-2,6-xylyl)methyl)-1,3,5-triazine-2,4,6(1H,3H,5H)-trione,
2,6-di-t-butyl-4-(4,6-bis(octylthio)-1,3,5-triazin-2-ylamino)phenol, and 3,9-bis(2-(3-(3-t-butyl-4-hydroxy-5-methylphenyl)propionyloxy)-1,1-dimethylethyl)-2,4,8,10-tetraoxaspiro(5,5)undecane.
These may be used alone, or in combination.
[0081] An amount of the antioxidant or the photostabilizer is not collectively defined,
as it varies depending on a type of the metal oxide for use. The amount thereof is
preferably 0.1 parts by mass to 100 parts by mass, more preferably 1 part by mass
to 50 parts by mass, relative to 100 parts by mass of the metal oxide. When the amount
thereof is less than 0.1 parts by mass, an effect of preventing an increase in absorbance
cannot be attained. When the amount thereof is greater than 100 parts by mass, the
photothermal conversion layer may have low thermal resistance, or low adhesion to
other layers.
<Light-Blocking Layer>
[0082] The light-blocking layer is appropriately selected depending on the intended purpose
without any limitation, provided that the average transmittance thereof to light in
a wavelength range of 300 nm to 400 nm is 5% or less, and the average transmittance
thereof to light in a wavelength range of 380 nm to 495 nm is 20% or less. The light-blocking
layer may have a single-layer structure, or a laminate structure composed of an ultraviolet
ray-blocking layer and the below-mentioned blue light-blocking layer.
[0083] In case of the laminate structure, an order of laminating the ultraviolet ray-blocking
layer and the blue light-blocking layer is appropriately selected depending on the
intended purpose without any limitation. In the case where it is desired to protect
a material in the blue light-blocking layer from ultraviolet rays, for example, the
ultraviolet ray-blocking layer is preferably provided at a surface side of the thermosensitive
recording medium. In the case where the blue light-blocking layer functioning also
as a protective layer, which is described later, is provided at the surface side of
the thermosensitive recording layer, a number of the layers provided can be reduced,
to thereby improve productivity.
[0084] Moreover, the ultraviolet ray-blocking layer and the blue light-blocking layer may
be provided next to each other, or another layer, such as the oxygen barrier layer,
may be provided between the ultraviolet ray-blocking layer and the blue light-blocking
layer.
[0085] The transmittance of the light-blocking layer can be measured by the following method.
[0086] In the case where a thermosensitive recording medium is a thermosensitive recording
medium, in which layers, such as an image recording layer, are provided on an opaque
substrate, and the light-blocking layer is laminated thereon, and moreover, other
layers, such as a protective layer, are provided on the light-blocking layer, first,
the opaque substrate is peeled by gradually scraping the substrate with a blade edge
of a cutter. Thereafter, other opaque layers, such as the image recording layer, are
gradually scraped from the back surface side of the thermosensitive recording medium
using the blade edge of the cutter and sand paper, to thereby remove the opaque layers,
such as the substrate and the image recording layer. Thereafter, the transmittance
of the remaining layers is measured by means of a spectrophotometer (U-4100, manufactured
by Hitachi High-Technologies Corporation) per 1 nm in a wavelength range of 300 nm
to 700 nm. Then, the average value of the measured transmittance at each wavelength
is calculated to thereby determine the average transmittance to light in the wavelength
range of 380 nm to 495 nm, or the average transmittance to light in the wavelength
range of 300 nm to 400 nm. Note that, the average transmittance of the light-blocking
layer to light in the wavelength range of 300 nm to 400 nm is 5% or less in order
to prevent photodeterioration of the leuco dye contained in the image recording layer,
preferably 3% or less, and more preferably 1% or less.
[0087] The light-blocking layer contains a binder resin, and a compound that absorbs, reflects,
or scatters light in a wavelength range of 500 nm or shorter, and may further contain
other components, such as filler, and a lubricant. The light-blocking layer may also
faction as a protective layer.
-Binder Resin-
[0088] The binder resin is appropriately selected depending on the intended purpose without
any limitation, and examples thereof include any of the binder resins described in
the image recording layer, a thermoplastic resin, a thermoset resin, and an ultraviolet
ray-curable resin.
[0089] Examples of the binder resin include polyethylene, polypropylene, polystyrene, polyvinyl
alcohol, polyvinyl butyral, polyurethane, saturated polyester, unsaturated polyester,
an epoxy resin, a phenol resin, polycarbonate, polyamide, acryl polyol, polyester
polyol, and polyurethane polyol. These may be used alone, or in combination.
[0090] The binder resin may be crosslinked with a crosslinking agent.
[0091] The crosslinking agent is appropriately selected depending on the intended purpose
without any limitation, and examples thereof include isocyanate, an amino resin, a
phenol resin, amine, and an epoxy compound. Among them, isocyanate is preferable,
and a polyisocyanate compound containing a plurality of isocyanate groups is particularly
preferable.
[0092] As for an amount of the crosslinking agent in the binder resin, preferred is the
amount with which a ratio of the number of the functional groups of the crosslinking
agent to the number of active groups contained in the binder resin is to be 0.01 to
2.
-Compound That Absorbs, Reflects, or Scatters Light Having Wavelength of 500 nm or
Shorter-
[0093] As for the compound that absorbs, reflects, or scatters light in a wavelength range
of 500 nm or shorter, any of an organic compound or an inorganic compound can be used.
Moreover, a polymer having a structure that absorbs light in a wavelength range of
500 nm or shorter at a principle chain or side chain may be used. In this case, such
the polymer can also function as a binder resin.
[0094] The compound that absorbs, reflects, or scatters light in a wavelength range of 500
nm or shorter can be selected from any of an organic compound or an inorganic compound,
provided that it is a yellowish compound. In the case where a thermosensitive recording
medium is used over a long period, the compound is preferably a yellowish pigment,
which has excellent resistance to light or heat. However, any of a pigment or a dye
can be used. Examples thereof include a quinophthalone-based compound, an isoindoline-based
compound, an isoindolinone-based compound, an anthraquinone-based compound, an azo-based
compound, a disazo-based compound, a benzimidazolone-based compound, and a complex
oxide pigment. Among them, a quinophthalone-based compound, an isoindoline-based compound,
an isoindolinone-based compound, an anthraquinone-based compound, an azo-based compound,
a disazo-based compound, and a benzimidazolone-based compound are preferable.
[0095] Examples of the quinophthalone-based compound include Pigment Yellow 138.
[0096] Examples of the isoindoline-based compound include Pigment Yellow 139.
[0097] Examples of the isoindolinone-based compound include Solvent Yellow 163, and Solvent
Yellow 167.
[0098] Examples of the anthraquinone-based compound include Pigment Yellow 109, Pigment
Yellow 110, Pigment Yellow 137, and Pigment Yellow 173.
[0099] Examples of the azo-based compound and the disazo-based compound include Pigment
Yellow 17, Pigment Yellow 55, Pigment Yellow 83, Pigment Yellow 169, Pigment Yellow
180, and Solvent Orange 54.
[0100] Examples of the benzimidazolone-based compound include Pigment Yellow 120, Pigment
Yellow 151, Pigment Yellow 154, and Pigment Yellow 175.
[0101] Examples of the complex oxide pigment include Pigment Yellow 53, Pigment Yellow 157,
Pigment Yellow 158, Pigment Yellow 160, and Pigment Yellow 184.
[0102] In the case where absorbance, reflection, or scattering of light having a wavelength
range of 300 nm to 400 nm is insufficient only with the compound that absorbs, reflects,
or scatters light in a wavelength range of 500 nm or shorter, a conventional ultraviolet
ray-blocking material known in the art can be used in combination.
[0103] The ultraviolet ray-blocking material can be any material selected from an organic
ultraviolet ray-blocking material, an organic UV-ray absorber, and an inorganic ultraviolet
ray-blocking material.
[0104] Examples of the organic ultraviolet ray-blocking material include a benzotriazole-based
UV-ray absorber, a benzophenone-based UV-ray absorber, a salicylic acid ester-based
UV-ray absorber, a cyanoacrylate-based UV-ray absorber, a cinnamic acid-based UV-ray
absorber, and a triazine-based UV-ray absorber. Among them, a benzotriazole-based
UV-ray absorber, and a triazine-based UV-ray absorber are preferable, and a UV-ray
absorber a hydroxyl group of which is protected with an adjacent bulky functional
group is particularly preferable.
[0105] Examples of the organic UV-ray absorber include 2-(2'-hydroxy-3',5'-di-t-butylphenyl)benzotriazole,
2-(2'-hydroxy-3'-t-butyl-5'-methylphenyl)benzotriazole, 2-(2'-hydroxy-3',5'-di-t-butylphenyl)-5-chlorobenzotriazole,
2-(2'-hydroxy-3'-t-butyl-5'-methylphenyl)-5-chlorobenzotriazole, 2-(2'-hydroxy-5'-t-octylphenyl)benzotriazole,
2,2'-methylenebis[6-2H-benzotriazol-2-yl]-4-(1,1,3,3-tetramethylbutyl)phenol]), 6,6',6"-(1,3,5-triazin-2,4,6-triyl)tris(3-hexyloxy-2-methylphenol),
and 2-(4,6-diphenyl-1,3,5-triazin-2-yl)-5-[2-(2-ethylhexyloxy)ethoxy]phenol. In the
case where a thermosensitive recording medium is used over a long period, moreover,
used as the organic UV-ray absorber may be the one where a skeleton having the UV-ray
absorbing ability is added in the form of a pendant to a polymer prepared by copolymerizing
an acrylic resin or a styrene-based resin, or the one where a surface of an inorganic
material (e.g. talc) is coated with the organic UV-ray absorber, followed by surface
treated with dimeticone, in order to prevent aggregation or bleeding of the UV-ray
absorber.
[0106] As for the inorganic ultraviolet ray-blocking material, a metal-based compound having
the average particle diameter of 100 nm or less is preferable. Examples thereof include:
metal oxide, such as zinc oxide, indium oxide, alumina, silica, zirconium oxide, tin
oxide, cerium oxide, iron oxide, antimony oxide, barium oxide, calcium oxide, barium
oxide, bismuth oxide, nickel oxide, magnesium oxide, chromium oxide, manganese oxide,
tantalum oxide, niobium oxide, thorium oxide, hafnium oxide, molybdenum oxide, iron
ferrite, nickel ferrite, cobalt ferrite, barium titanate, and calcium titanate, or
composite oxide thereof; metal sulfide or a sulfuric acid, such as zinc sulfide, and
barium sulfide; metal carbide, such as titanium carbide, silicon carbide, molybdenum
carbide, tungsten carbide, and tantalum carbide; and metal nitride, such as aluminium
nitride, silicon nitride, boron nitride, zirconium nitride, vanadium nitride, titanium
nitride, niobium nitride, and gallium nitride. Among them, metal oxide-based particles
are preferable, and silica, alumina, zinc oxide, titanium oxide, cerium oxide, and
bismuth oxide are more preferable. These may be surface treated with silicone, wax,
organic silane, or silica.
[0107] An amount of the compound that absorbs, reflects, or scatters light in a wavelength
range of 500 nm or shorter is preferably 1% by mass to 95% by mass relative to the
light-blocking layer.
[0108] A solvent used for a coating liquid of the light-blocking layer, a dispersing device
used for the coating liquid, a coating method, and a curing method are appropriately
selected from those known in the art depending on the intended purpose without any
limitation.
[0109] The average thickness of the light-blocking layer is preferably 0.1 µm to 30 µm,
more preferably 0.5 µm to 20 µm.
[0110] It is preferred that the average transmittance of the light-blocking layer to light
in a wavelength range of 380 nm to 495 nm be made 20% or less, preferably 10% or less,
more preferably 5% or less by adjusting the amount of the compound that absorbs, reflects,
or scatters light in a wavelength range of 500 nm or shorter contained in the light-blocking
layer, or the average thickness of the light-blocking layer. As a result of this,
an increase in the absorbance in the near infrared region of the metal oxide having
the absorbance in the near infrared region, which is caused by irradiation of light,
can be prevented.
[0111] In the case where the metal oxide having the absorbance in the absorbance in the
near infrared region, and the leuco dye are contained in the same layer, moreover,
the metal oxide may be tinted as it is irradiated with light, such as sun light, for
a long period, if the transmittance of the light-blocking layer to light having a
wavelength of 470 nm is greater than 10%, even when the average transmittance of the
light-blocking layer to light in the wavelength range of 380 nm to 495 nm is 10% or
less. This is a phenomenon occurred only when the metal oxide having the absorbance
in the near infrared region and the leuco dye are mixed. Moreover, this phenomenon
cannot expected because the leuco dye before reacting with a color developer does
not typically have absorbance in a wavelength range of 420 nm to 430 nm or greater.
To avoid this phenomenon, it is necessary to sufficiently block light of longer wavelengths,
and it is more preferred that the transmittance of the light-blocking layer to light
having a wavelength of 470 nm be 10% or less, and even more preferably 5% or less.
[0112] The average transmittance of the light-blocking layer to light in a wavelength range
of 600 nm to 700 nm is preferably 80% or greater. When a bar code recorded on the
thermosensitive recording medium is read, a bar code reader typically uses red light
having the wavelength of around 650 nm. Therefore, it is preferred that the light-blocking
layer transmit light having a wavelength around 650 nm. As a result of this, a contrast
of an image recorded on the thermosensitive recording medium is sufficiently attained,
and excellent bar code readability can be attained.
«Blue Light-Blocking Layer»
[0113] In the present specification, the term "blue light" means blue-colored light in a
wavelength range of 380 nm to 495 nm within visible light.
[0114] The blue light-blocking layer contains a binder resin, and a compound that absorbs,
reflects, or scatters light in a wavelength range of 500 nm or shorter, and may further
contain other components, such as fillers, and a lubricant, as necessary.
-Binder Resin-
[0115] The binder resin is appropriately selected depending on the intended purpose without
any limitation, and examples thereof include any of the binder resins described in
the descriptions of the image recording layer, a thermoplastic resin, and a thermoset
resin. Preferable examples thereof include polyethylene, polypropylene, polystyrene,
polyvinyl alcohol, polyvinyl butyral, polyurethane, saturated polyester, unsaturated
polyester, an epoxy resin, a phenol resin, polycarbonate, polyamide, acryl polyol,
polyester polyol, and polyurethane polyol.
[0116] The binder resin may be crosslinked with a crosslinking agent. As for these materials,
those used for the thermoreversible recording layer are suitably used. Moreover, the
blue light-blocking layer may contain other components, such as filler, as necessary.
-Compound That Absorbs, Reflects, or Scatters Light in Wavelength Range of 500 nm
or Shorter-
[0117] As for the compound that absorbs, reflects, or scatters light in a wavelength range
of 500 nm or shorter, the compound that absorbs, reflects, or scatters light in a
wavelength range of 500 nm or shorter, which is described in the descriptions of the
light-blocking layer, can be used.
[0118] An amount of the compound that absorbs, reflects, or scatters light in a wavelength
range of 500 nm or shorter is preferably 1% by mass to 95% by mass relative to the
blue light-blocking layer.
[0119] A solvent used in a coating liquid of the blue light-blocking layer, a dispersing
device of the coating liquid, a coating method, and a curing method are appropriately
selected from those known in the art depending on the intended purpose without any
limitation.
[0120] The average thickness of the blue light-blocking layer is preferably 0.1 µm to 30
µm, more preferably 0.5 µm to 20 µm.
[0121] As for the measuring method of the transmittance of the blue light-blocking layer,
a method similar to the measuring method of the transmittance of the light-blocking
layer can be used.
«Ultraviolet Ray-Blocking Layer»
[0122] The ultraviolet ray-blocking layer is preferably provided on a surface of the image
recording layer, which is opposite to the surface thereof where the support is provided,
for the purpose of preventing deterioration of the resin component contained in the
image recording layer due to ultraviolet rays, or preventing an erasion failure caused
by tinting of the leuco dye due to ultraviolet rays, or caused by photodeterioration
of the leuco dye.
[0123] Moreover, the ultraviolet ray-blocking layer may be additionally provided at a surface
side of the light-blocking layer in order to prevent discoloring or photodeterioration
of constitutional materials of the light-blocking layer.
[0124] The ultraviolet ray-blocking layer contains at least an ultraviolet ray-blocking
material, and may further contain other components, such as a binder resin, filler,
a lubricant, and a color pigment.
-Ultraviolet Ray-Blocking Material-
[0125] As for the ultraviolet ray-blocking material, the ultraviolet ray-blocking material
described in the descriptions of the light-blocking layer can be used.
[0126] In the case where an organic UV-ray absorber is used as the ultraviolet ray-blocking
material, an amount of the ultraviolet ray-blocking material is preferably 1% by mass
to 95% by mass relative to a total mass of the ultraviolet ray-blocking layer. In
the case where an inorganic UV-ray absorber is used as the ultraviolet ray-blocking
material, an amount of the ultraviolet ray-blocking material based on the volume fraction
is preferably 1% by volume to 95% by volume.
[0127] Note that, any of these organic or inorganic ultraviolet ray-blocking materials may
be contained in the image recording layer.
-Binder Resin-
[0128] The binder resin is not particularly limited, and the binder resin of the thermosensitive
recording layer, or a resin component such as a thermoplastic resin, and a thermoset
resin, can be used as the binder resin. Examples thereof include polyethylene, polypropylene,
polystyrene, polyvinyl alcohol, polyvinyl butyral, polyurethane, saturated polyester,
unsaturated polyester, an epoxy resin, a phenol resin, polycarbonate, polyamide, acryl
polyol, polyester polyol, and polyurethane polyol.
[0129] As for the binder resin, an UV-ray absorbing polymer may be used, and the binder
resin may be crosslinked with a crosslinking agent. As for these materials, the materials
described in the descriptions of the recording layer or the protective layer are suitably
used. The ultraviolet ray-blocking layer may further contain other components, such
as filler, as necessary.
[0130] The average thickness of the ultraviolet ray-blocking layer is preferably 0.1 µm
to 30 µm, more preferably 0.5 µm to 20 µm. As for a solvent used in a coating liquid
of the ultraviolet ray-blocking layer, a dispersing device of the coating liquid,
a coating method of the ultraviolet ray-blocking layer, and a curing method of the
ultraviolet ray-blocking layer, those used for the thermosensitive recording layer
can be used.
[0131] As for the measuring method of the transmittance of the ultraviolet ray-blocking
layer, a method similar to the measuring method of the transmittance of the light-blocking
layer can be used. In the case where the blue light-blocking layer and the ultraviolet
ray-blocking layer are laminated to compose the light-blocking layer, the transmittance
can be measured with the blue light-blocking layer and the ultraviolet ray-blocking
layer being laminated by a method similar to the measuring method of the transmittance
of the light-blocking layer.
<Support>
[0132] A shape, structure, and size of the support are appropriately selected depending
on the intended purpose without any limitation. Examples of the shape thereof include
a plate shape. The structure of the support may be a single-layer structure, or a
laminate structure. The size of the support is appropriately selected depending on
a size of the thermosensitive recording medium.
[0133] Examples of a material of the support include an inorganic material, and an organic
material. These may be used alone, or in combination.
[0134] Examples of the inorganic material include glass, quartz, silicon, silicon oxide,
aluminium oxide, SiO
2, and metal.
[0135] Examples of the organic material include paper, a cellulose derivative (e.g. cellulose
triacetate), synthetic paper, and a film of polyethylene terephthalate, polycarbonate,
polystyrene, or polymethyl methacrylate.
[0136] Among them, the organic material is preferable, a film of polyethylene terephthalate
(PET), polycarbonate, or polymethyl methacrylate is more preferable, and polyethylene
terephthalate (PET) is particularly preferable.
[0137] The support is preferably subjected to a surface treatment through corona discharging,
an oxidation reaction treatment (chromic acid), etching, an easy adhesion treatment,
or an anti-charging treatment, for the purpose of improving the adhesion with a coating
layer. The support is preferably turned into white by adding a white pigment, such
as titanium oxide.
[0138] The average thickness of the support is appropriately selected depending on the intended
purpose without any limitation, but the average thickness thereof is preferably 10
µm to 2,000 µm, more preferably 20 µm to 1,000 µm.
-Oxygen Barrier Layer-
[0139] The permeation of oxygen into the image recording layer can be provided by providing
an oxygen barrier layer on the image recording layer in the thermosensitive recording
medium. Therefore, use of the oxygen barrier layer can prevent an unerased portion
to be left, or coloring of the back ground due to photodeterioration of the leuco
dye contained in the image recording layer.
[0140] The oxygen permeation rate of the oxygen barrier layer at 25°C, 80%RH is preferably
20 mL/m
2/day/MPa or less, more preferably 5 mL/m
2/day/MPa or less, and even more preferably 1 mL/m
2/day/MPa or less.
[0141] When the oxygen permeation rate is greater than 20 mL/m
2/day/MPa, oxygen cannot be sufficiently blocked, and therefore light deteriorates
the leuco dye. As a result, an image cannot be completely erased. Note that, the oxygen
permeation rate is influenced by temperature and humidity of the atmosphere. Therefore,
the oxygen permeation rate is preferably low also under the high temperature and high
humidity conditions of 30°C, 80%RH, or 35°C, 80%RH, not only the conditions of 25°C,
80%RH.
[0142] As for the measurement of the oxygen permeation rate, for example, there is a measuring
method according to JIS K7126B (isopiestic method), or ATSMD3985. Examples of the
measuring device include: an oxygen permeation rate measuring device OX-TRAN2/21,
and OX-TRAN2/61 (both manufactured by MOCON, Inc); and an oxygen permeation analyzer
Model 8001 (manufactured by Systech Instruments Ltd.).
[0143] In the case where a water-soluble resin (e.g. polyvinyl alcohol, and an ethylene/polyvinyl
alcohol copolymer) is used as a material of the oxygen barrier layer, the resulting
oxygen barrier layer exhibits excellent oxygen barrier properties in the low humidity
environment, but the oxygen barrier layer absorbs moisture and significantly reduces
its oxygen barrier properties, as the surrounding humidity increases, because the
water-soluble resin is hydrophilic. In the case where the thermosensitive recording
medium is used outside in summer when the humidity is typically high, therefore, sufficient
oxygen barrier properties may not be attained. Accordingly, preferably used are an
inorganic oxide (e.g., silica, and alumina) vapor deposition layer having the oxygen
permeation rate of 20 mL/m
2/day/MPa or less at 25°C, 80%RH, or an inorganic vapor deposition film having the
oxygen permeation rate of 20 mL/m
2/day/MPa or less at 25°C, 80%RH, in which inorganic oxide is deposited on a polymer
film (e.g., polyethylene terephthalate (PET) and nylon) by vapor deposition. Examples
of the organic vapor deposition film include a silica vapor deposition film, an alumina
vapor deposition film, and a silica/alumina vapor deposition film. Among them, a silica
vapor deposition film is particularly preferable, as it is low in cost, has high oxygen
barrier properties, and receives less influence from temperature or humidity. Moreover,
the base material of the inorganic vapor deposition film is preferably polyethylene
terephthalate (PET) in view of vapor deposition compatibility, its stable oxygen barrier
properties, and heat resistance.
<Other Layers>
[0144] Other layers, such as an intermediate layer, protective layer, an adhesive layer,
and a bonding layer, may be provided between the oxygen barrier layer and the image
recording layer.
[0145] The oxygen barrier layer is provided on a surface of the image recording layer, which
is opposite to the surface thereof where the support is provided. Moreover, it is
preferred that a second oxygen barrier layer be provided between the support and the
image recording layer, or on a surface of the support, which is opposite to the surface
whereof where the image recording layer is provided, or both therebetween and thereon.
Oxygen can be more efficiently blocked by providing a first oxygen barrier layer on
a surface of the image recording layer, which is opposite to the surface thereof where
the support is provided, and a second oxygen barrier layer at the support side of
the image recording layer to sandwich the image recording layer with the first and
second oxygen barrier layers. Moreover, the first oxygen barrier layer and the second
oxygen barrier layer may be identical or different.
[0146] A formation method of the oxygen barrier layer is selected from conventional methods
known in the art without any limitation, and examples thereof include a typical coating
method, and a typical laminating method. In the case where only an inorganic vapor
deposition layer is formed as the oxygen barrier layer, moreover, examples of the
formation method include PVD, and CVD as a vapor deposition method.
[0147] The average thickness of the oxygen barrier layer is not particularly limited, and
varies depending on the oxygen permeation degree thereof. However, the average thickness
thereof is preferably 0.005 µm to 1,000 µm, more preferably 0.007 µm to 500 µm. When
the average thickness thereof is greater than 1,000 µm, a transparency thereof or
recording sensitivity of a resulting thermosensitive recording medium may be reduced.
In the case where a first oxygen barrier layer and a second oxygen barrier layer are
provided as the oxygen barrier layer, the average thickness of each of the first oxygen
barrier layer and the second oxygen barrier layer is preferably 0.005 µm to 1,000
µm.
[0148] In the case here an inorganic vapor deposition layer or inorganic vapor deposition
film is used as the oxygen barrier layer, the average thickness of the inorganic vapor
deposition layer is preferably 5 nm to 100 nm, more preferably 7 nm to 80 nm. When
the average thickness thereof is less than 5 nm, the oxygen barrier properties may
be insufficient. When the average thickness thereof is greater than 100 nm, a transparency
thereof may be reduced, or the barrier layer may be tinted.
-Adhesive Layer or Bonding Layer-
[0149] The adhesive layer or bonding layer may be provided between the oxygen barrier layer
and the layer below the oxygen barrier layer. A formation method of the adhesive layer
or bonding layer is not particularly limited, and a typical coating method or laminating
method is used as the formation method. The average thickness of the adhesive layer
or bonding layer is appropriately selected depending on the intended purpose without
any limitation, but the average thickness thereof is preferably 0.1 µm to 20 µm.
[0150] A material of the adhesive layer or bonding layer is appropriately selected depending
on the intended purpose without any limitation, and examples thereof include a urea
resin, a melamine resin, a phenol resin, an epoxy resin, a vinyl acetate -based resin,
a vinyl acetate/acryl-based copolymer, an ethylene/vinyl acetate copolymer, an acryl-based
resin, a polyvinyl ether-based resin, a vinyl chloride/vinyl acetate-based copolymer,
a polystyrene-based resin, a polyester-based resin, a polyurethane-based resin, a
polyamide-based resin, a polyolefin chloride-based resin, a polyvinyl butyral-based
resin, an acrylic acid ester-based copolymer, a methacrylic acid ester-based copolymer,
natural rubber, a cyanoacrylate-based resin, and a silicone-based resin. These materials
may be crosslinked with a crosslinking agent. Moreover, the material of the adhesive
layer or bonding layer may be of hot-melt type.
[0151] In the present invention, oxygen barrier properties are further improved by laminating
two or more inorganic vapor deposition films. In the case where inorganic vapor deposition
films are laminated, the films can be laminated using the adhesive layer or bonding
layer. The adhesive layer or bonding layer may contain a compound that absorbs, reflects,
or scatters light in a wavelength range of 500 nm or shorter.
[0152] As for a method for determining whether or not the oxygen barrier layer is present
in the thermosensitive recording medium, for example, it can be determined by measuring
the oxygen permeation rate of the thermosensitive recording medium by an oxygen permeation
rate measuring device. Specifically, in the case where the oxygen permeation rate
of the thermosensitive recording medium is 20 mL/m
2/day/MPa or less, the thermosensitive recording medium is determined to contain an
oxygen barrier layer.
-Protective Layer-
[0153] In the thermoreversible recording medium, a protective layer is preferably provided
on the thermoreversible recording layer for the purpose of protecting the thermoreversible
recording layer. The protective layer is appropriately selected depending on the intended
purpose without any limitation. For example, the protective layer may be formed on
one or more layers, and the protective layer is preferably provided on the exposed
outermost layer.
[0154] The protective layer contains a binder resin, and may further contain other components,
such as a release agent, and fillers, as necessary. The binder resin of the protective
layer is appropriately selected depending on the intended purpose without any limitation,
and examples thereof include a heat-crosslinkable resin, a thermoset resin, an ultraviolet
ray (UV) curable resin, and an electron beam curable resin. Among them, a UV-ray curable
resin, and a heat-crosslinkable resin are particularly preferable.
[0155] The UV-ray curable resin can form an extremely hard film after being cured, and the
hard film can prevent a damage caused by physical contact on a surface, and a deformation
of a medium by laser heat. Therefore, use of the UV-ray curable resin can provide
a thermoreversible recording medium having excellent durability against repetitive
use. Moreover, the heat-crosslinkable resin can also harden the surface, although
it is slightly inferior to the UV-ray curable resin, and can give excellent resistance
to repetitive use.
[0156] The UV-ray curable resin is appropriately selected depending on the intended purpose
without any limitation, and examples thereof include: an oligomer, such as a urethaneacrylate-based
oligomer, an epoxyacrylate-based oligomer, a polyester acrylate-based oligomer, a
polyether acrylate-based oligomer, a vinyl-based oligomer, and an unsaturated polyester-based
oligomer; and a monomer, such as monofunctional or polyfunctional acrylate, monofunctional
or polyfunctional methacrylate, vinyl ester, an ethylene derivative, and acrylic compound.
Among them, tetrafunctional or higher polyfunctional monomer or oligomer is particularly
preferable. A hardness, contraction rate, flexibility, and coating film strength of
a resin film can be appropriately adjusted by blending two or more monomers or oligomers
listed above. Moreover, it is necessary to use a photopolymerization initiator, or
a photopolymerization accelerator to cure the monomer or oligomer using ultraviolet
rays.
[0157] An amount of the photopolymerization initiator or photopolymerization accelerator
is preferably 0.1% by mass to 20% by mass, more preferably 1% by mass to 10% by mass
relative to a total mass of the resin components in the protective layer.
[0158] The irradiation of ultraviolet rays to cure the ultraviolet ray-curable resin is
appropriately selected depending on the intended purpose without any limitation, and
examples thereof include irradiation performed by an ultraviolet ray irradiation device.
Examples of the ultraviolet ray irradiation device include a device equipped with
a light source, a lamp, a power source, a cooling device, or a transporting device.
[0159] Examples of the light source include a mercury lamp, a metal halide lamp, a. potassium
lamp, a mercury xenon lamp, and a flash lamp. A wavelength of light emitted from the
light source is appropriately selected depending on a wavelength of UV absorbance
of a photopolymerization initiator or photopolymerization accelerator contained in
the thermoreversible recording medium. The conditions of the ultraviolet ray irradiation
are appropriately selected depending on the intended purpose without any limitation.
For example, the output of the lamp, or transporting speed can be determined depending
on the irradiation energy required for curing the resin.
[0160] As for the heat-crosslinkable resin, a binder resin usable for the thermoreversible
recording layer is suitably used. The heat-crosslinkable resin is preferably crosslinked.
[0161] As for the heat-crosslinkable resin, for example, a resin containing a group reactable
with a crosslinking agent, such as a hydroxyl group, an amino group, and a carboxyl
group, is preferable, and a polymer containing a hydroxyl group is more preferable.
As for the crosslinking agent, for example, a crosslinking agent usable for the thermoreversible
recording layer is suitably used.
[0162] As for the releasing agent, in order to improve transporting properties of a resulting
media, silicone containing a polymerizable group, a polymer to which silicone has
been grafted, zinc stearate, or silicone old can be used. An amount of the release
agent is preferably 0.01% by mass to 50% by mass, more preferably 0.1% by mass to
40% by mass, relative to a total mass of the resin component of the protective layer.
[0163] To the protective layer, a pigment, a surfactant, a leveling agent, or an anti-charging
agent can be added, as necessary..
[0164] In the case where the compound that absorbs, reflects, or scatters light in a wavelength
range of 500 nm or shorter, which insufficiently absorbs, reflects, or scatters light
in a wavelength range of 300 nm to 400 nm, is contained, the compound does not interferer
ultraviolet rays, which are used for UV curing. Therefore, the resulting protective
layer can also functions as the blue light-blocking layer. In this case, a number
of layers provided can be reduced, to thereby improve productivity.
[0165] As a solvent used in a coating liquid of the protective layer, a dispersing device
of the coating liquid, a coating method of the protective layer, and a drying method
of the protective layer, those known in the art and used for the image recording layer
can be used. In the case here an ultraviolet ray-curable resin is used in the protective
layer, a curing step where a film prepared by coating and drying is irradiated with
ultraviolet rays is required. The ultraviolet ray irradiation device, the light source,
and the irradiation conditions are as described earlier.
[0166] The average thickness of the protective layer is preferably 0.1 µm to 20 µm, more
preferably 0.5 µm to 10 µm, and even more preferably 1.5 µm to 6 µm. When the average
thickness thereof is less than 0.1 µm, the protective layer cannot sufficiently function
as a protective layer of the thermosensitive recording medium. As a result, the materials
used in the thermosensitive recording medium may be deteriorated by repetition hysteresis
due to heat, and the thermosensitive recording medium may not be able to use repeatedly.
When the average thickness thereof is greater than 20 µm, head from the layer containing
the photothermal converting material tends to escape to the side of the protective
layer, and image recording and image erasing may not be sufficiently performed with
heat.
-Intermediate Layer-
[0167] In the present invention, an intermediate layer is preferably provided on the image
recording layer for the purpose of improving the adhesion between the image recording
layer and the oxygen barrier layer, or leveling a surface of the image recording layer.
By providing the intermediate layer, image quality can be improved.
[0168] The intermediate layer contains at least a binder resin, and may further contain
filler, a lubricant, and a color pigment, as necessary. The binder resin is appropriately
selected depending on the intended purpose without any limitation. As for the binder
resin, the binder resin of the image recording layer, or a resin component, such as
a thermoplastic resin, and a thermoset resin, can be used. Moreover, the intermediate
layer may contain a UV-ray absorber. As for the UV-ray absorber, any of an organic
compound or an inorganic compound can be used.
[0169] Moreover, the intermediate layer may contain a compound that absorbs, reflects, or
scatters light in a wavelength range of 500 nm or shorter.
[0170] The average thickness of the intermediate layer is preferably 0.1 µm to 20 µm, more
preferably 0.5 µm to 10 µm. As for a solvent used in a coating liquid of the intermediate
layer, a dispersing device of the coating liquid, a coating method of the intermediate
layer, and a drying and curing method of the intermediate layer, those known in the
art and used for the image recording layer can be used.
-Under Layer-
[0171] In the present invention, an under layer may be provided between the image recording
layer and the support, for the purpose of effectively utilizing generated heat to
increase sensitivity, or improving the adhesion between the support and the image
recording layer, or preventing a material of the image recording layer from migrating
into the support.
[0172] The under layer contains at least hollow particles, and may further contain other
components, as necessary. Examples of the hollow particles include single-void particles,
where only one hollow part is present in each particle, and multi-void particles,
where a large number of hollow parts are present in each particle. These may be used
alone, or in combination. A material of the hollow particles is appropriately selected
depending on the intended purpose without any limitation. For example, a thermoplastic
resin is suitably used as the material thereof. The hollow particles may be appropriately
produced for use, or selected from commercial products. Examples of the commercial
product thereof include: Microsphere R-300 (manufactured by Matsumoto Yushi-Seiyaku
Co., Ltd.); Ropaque HP1055, Ropaque HP433J (both manufactured by Zeon Corporation);
and SX866 (manufactured by JSR CORPORATION). An amount of the hollow particles in
the under layer is appropriately selected depending on the intended purpose without
any limitation. For example, the amount thereof is preferably 10% by mass to 80% by
mass. As for the binder resin, a resin identical to the binder resin used in the image
recording layer, or the layer containing a polymer having a UV-ray absorbing structure,
can be used.
[0173] To the under layer, filler, a lubricant, a surfactant, or a dispersing agent may
be added, as necessary. Examples of the filler include inorganic filler and organic
filler. As for the filler, the inorganic filler is preferable. Examples of the inorganic
filler include calcium carbonate, magnesium carbonate, titanium oxide, silicon oxide,
aluminium hydroxide, kaolin, and talc.
[0174] The average thickness of the under layer is appropriately selected depending on the
intended purpose without any limitation, but the average thickness thereof is preferably
1 µm to 80 µm, more preferably 4 µm to 70 µm, and even more preferably 12 µm to 60
µm.
-Back Layer-
[0175] A back layer may be provided at the opposite side of the surface of the support to
the side thereof where the image recording layer is provided, for the purpose of preventing
curl or charging of the thermosensitive recording medium, and improving transporting
properties thereof.
[0176] The back layer contains at least a binder resin, and may further contain other components,
such as filler, a lubricant, and a color pigment, as necessary. The binder resin is
appropriately selected depending on the intended purpose without any limitation, and
examples thereof include a heat-crosslinkable resin, a thermoset resin, an ultraviolet
ray (UV) curable resin, and an electron beam curable resin. Among them, an ultraviolet
ray (UV) curable resin, and a heat-crosslinkable resin are particularly preferable.
As for the ultraviolet ray curable resin, the heat-crosslinkable resin, the filler,
the conductive filler, and the lubricant, those used in the image recording layer,
or the protective layer are suitably used.
-Adhesive Layer or Bonding Layer-
[0177] In the present invention, an adhesive layer or bonding layer is provided on a surface
of the support opposite to the surface thereof where the image recording layer is
provided, to thereby use the thermosensitive recording medium as a thermosensitive
recording label. As for a material of the adhesive layer or bonding layer, generally
used materials can be used.
[0178] A material of the adhesive layer or bonding layer is appropriately selected depending
on the intended purpose without any limitation, and examples thereof include a urea
resin, a melamine resin, a phenol resin, an epoxy resin, a vinyl acetate -based resin,
a vinyl acetate/acryl-based copolymer, an ethylene/vinyl acetate copolymer, an acryl-based
resin, a polyvinyl ether-based resin, a vinyl chloride/vinyl acetate-based copolymer,
a polystyrene-based resin, a poly ester-based resin, a polyurethane-based resin, a
polyamide-based resin, a chlorinated polyolefin-based resin, a polyvinyl butyral-based
resin, an acrylic acid ester-based copolymer, a methacrylic acid ester-based copolymer,
natural rubber, a cyanoacrylate-based resin, and a silicone-based resin. These materials
may be crosslinked with a crosslinking agent.
[0179] The material of the adhesive layer or bonding layer may be of a hot-melt type. Release
paper may be provided to the adhesive layer or bonding layer. Moreover, the adhesive
layer or bonding layer may be of a type where no release paper is used. The resulting
thermosensitive recording medium can be bonded to an entire or part of a thick substrate,
to which it is difficult to apply a recording layer by coating, such as a vinyl chloride
card with magnetic stripes by providing the adhesive layer or bonding layer. As a
result of this, user friendliness of the thermosensitive recording medium is improved,
such as in the manner that part of the information stored in the magnet can be displayed.
The thermosensitive recording label containing the adhesive layer or bonding layer
can be also used for a thick card, such as an IC card, and an optic card.
[0180] To the thermosensitive recording medium, a color layer may be provided between the
support and the image recording layer for the purpose of improving visibility. The
color layer may be formed by a method containing applying a solution or dispersion
liquid containing a colorant, and a binder resin onto a surface of a target, and drying,
or a method containing simply bonding a color sheet.
[0181] A color print layer may be provided to the thermosensitive recording medium.
[0182] In the thermosensitive recording medium, an irreversible recording layer may be used
in combination. In this case, color tones of these recording layers may be different.
Moreover, the color layer may be provided part or entire surface of the thermosensitive
recording medium, which is the same or opposite side of the image recording layer,
by providing the predetermined pattern by printing (e.g., offset printing, and gravure
printing), or by means of an inkjet printer, a thermal transfer printer, or a dye-sublimation
printer. Moreover, an OP varnish layer containing a curable resin as a main component
may be provided on a part or entire surface of the color layer. Moreover, a dye or
a pigment is simply added to any of the layers constituting the thermosensitive recording
layer to color the layer.
[0183] A hologram may be provided to the thermosensitive recording medium to improve a security
of the information recorded on the thermosensitive recording medium. Moreover, a design
(e.g., a figure, an emblem, and a symbol mark) may be provided to the thermosensitive
recording medium by giving relief or intaglio surface textures.
[0184] The thermosensitive recording medium can be processed into a desired shape depending
use thereof. Examples of the shape thereof include a card shape, a tag shape, a label
shape, a sheet shape, and a roll shape.
[0185] Examples of the thermosensitive recording medium processed into the card shape include
a prepaid card, a point card, and a credit card. The thermosensitive recording medium
in the size of a tag, which is smaller than the card size, can be used for a price
tag. Moreover, the thermosensitive recording medium in the size of a tag, which is
larger than the card size, can be used for a process management, a shipping instruction,
or a ticket. The thermosensitive recording medium in the form of a label can be attached
to another object, and thus such the thermosensitive recording medium is processed
into various sizes, and attached to a trolley, a container, a box, or a shipping container
to be used for a process or product management. Moreover, the thermosensitive recording
layer of a sheet size, which is larger than the card size, has a wider range to which
an image can be recorded, and therefore such the thermosensitive recording layer can
be used for general documents, or instructions for process management.
[0186] As for the layer structure of the thermosensitive recording medium of the present
invention, there is an embodiment where a support 101, and on the support, an image
recording layer 102, a light-blocking layer 103, and an oxygen barrier layer 104 are
provided in this order, as illustrated in FIG. 1A. In this case, permeation of oxygen
into the light-blocking layer is prevented, and therefore photodeterioration of the
binder resin or the compound that absorbs, reflects, or scatters light in a wavelength
range of 500 nm or shorter contained in the light-blocking layer 103 can be prevented.
[0187] Moreover, there is an embodiment where a support 101, and on the support, an image
recording layer 102, an oxygen barrier layer 104, and a light-blocking layer 103 are
provided in this order, as illustrated in FIG. 1B. in this case, light in a wavelength
range of 500 nm or shorter does not reach the oxygen barrier layer, and therefore
photodeterioration of the oxygen barrier layer is prevented.
[0188] There is an embodiment where a support 101, and on the support, an image recording
layer 102, a photothermal conversion layer 105, a light-blocking layer 103, and an
oxygen barrier layer 104 are provided in this order, as illustrated in FIG. 2A.
[0189] Moreover, there is an embodiment where a support 101, and on the support, an image
recording layer 102, a photothermal conversion layer 105, an oxygen barrier layer
104, and a light-blocking layer 103 are provided in this order, as illustrated in
FIG. 2B.
[0190] Moreover, there is an embodiment where a support 101, and on the support, a photothermal
conversion layer 105, an image recording layer 102, a light-blocking layer 103 and
an oxygen barrier layer 104 are provided in this order, as illustrated in FIG. 2C.
[0191] Moreover, there is an embodiment where a support 101, and on the support, a photothermal
conversion layer 105, an image recording layer 102, an oxygen barrier layer 104, and
a light-blocking layer 103 are provided in this order, as illustrated in FIG. 2D.
[0192] Moreover, there is an embodiment where a support 101, and on the support, a first
image recording layer 102, a photothermal conversion layer 105, a second recording
layer 102', a light-blocking layer 103, and an oxygen barrier layer 104 are provided
in this order, as illustrated in FIG. 2E.
[0193] There is an embodiment where a support 101, and on the support, an image recording
layer 102, a blue light-blocking layer 106, a ultraviolet ray-blocking layer 107,
and an oxygen barrier layer 104 are provided in this order, as illustrated in FIG.
3A. In this case, permeation of oxygen and ultraviolet rays to the blue light-blocking
layer 106 is prevented, and therefore photodeterioration of the compound that absorbs,
reflects, or scatters light in a wavelength range of 500 nm or shorter contained in
the blue light-blocking layer 106, via oxygen, can be prevented.
[0194] Moreover, there is an embodiment where a support 101, and on the support, an image
recording layer 102, an ultraviolet ray-blocking layer 107, a blue light-blocking
layer 106, and an oxygen barrier layer 104 are provided in this order, as illustrated
in FIG. 3B. Even in the case where the compound that absorbs, reflects, or scatters
light in a wavelength range of 500 nm or shorter contained in the blue light-blocking
layer 106 is an acidic material, the acidic material does not come into contact with
the leuco dye contained in the image recording layer 102 because of the aforementioned
layer structure, and therefore background fogging can be prevented.
[0195] Moreover, there is an embodiment where a support 101, and on the support, an image
recording layer 102, an oxygen barrier layer 104, a blue light-blocking layer 106,
and an ultraviolet ray-blocking layer 107 are provided in this order, as illustrated
in FIG. 3C. In this case, light in a wavelength range of 500 nm or shorter does not
reach the oxygen barrier layer 106, and therefore photodeterioration of the oxygen
barrier layer can be prevented. Moreover, ultraviolet rays do not reach the blue light-blocking
layer 106, and therefore photodeterioration of the compound that absorbs, reflects,
or scatters light in a wavelength range of 500 nm or shorter contained in the blue
light-blocking layer 106 can be prevented.
[0196] Moreover, there is an embodiment where a support 101, and on the support, an image
recording layer 102, an oxygen barrier layer 104, an ultraviolet ray-blocking layer
107, and a blue light-blocking layer 106 are provided in this order, as illustrated
in FIG. 3D. In this case, light in a wavelength range of 500 nm or shorter does not
reach the oxygen barrier layer, photodeterioration of the oxygen barrier layer can
be prevented. In the case where absorbance, reflection, or scattering of light in
a wavelength range of 300 nm to 400 nm by the compound that absorbs, reflects, or
scatters light in a wavelength range of 500 nm or shorter contained in the blue light-blocking
layer 106 is insufficient, moreover, ultraviolet rays applied for ultraviolet ray
curing are not disturbed, the blue light-blocking layer can also functions as a protective
layer, and therefore a number of the layers can be reduced, and productivity can be
improved.
[0197] Moreover, there is an embodiment where a support 101, and on the support, an image
recording layer 102, a blue light-blocking layer 106, an oxygen barrier layer 104,
and an ultraviolet ray-blocking layer 107 are provided in this order, as illustrated
in FIG. 3E. In this case, ultraviolet rays do not reach the oxygen barrier layer,
and therefore photodeterioration of the oxygen barrier layer can be prevented. Moreover,
ultraviolet rays and oxygen do not reach the blue light-blocking layer 106, and therefore
photodeterioration of the compound that absorbs, reflects, or scatters light in a
wavelength range of 500 nm or shorter contained in the blue light-blocking layer 106
can be prevented.
[0198] Although it is not illustrated, an under layer may be provided between the support
and the image recording layer, and a back layer, or an oxygen barrier layer, or both
may be provided on a surface of the support at which the image recording layer is
not provided.
<Mechanism of Image Recording and Image Erasing>
[0199] The mechanism of image recording and image erasion is an embodiment where a color
tone is reversible changed with heat. This embodiment uses a leuco dye and a reversible
color developer (may be referred to as a "color developer" hereinafter), and the color
tone reversibly changes between a transparent state and a colored state upon application
of heat.
[0200] FIG. 4A depicts one example of a temperature-coloring density change curve of the
thermoreversible recording medium containing the thermoreversible recording layer,
in which the leuco dye and the color developer are contained in the resin. FIG. 4B
illustrates a coloring-erasing mechanism of the thermoreversible recording medium,
which reversibly changes between the transparent state and the colored state with
heat.
[0201] As the recording layer initially in the erased state (A) is heated, first, the leuco
dye and the color developer are melted and mixed at the melting temperature T
1, to color and turn into a melt colored state (B). As the recording layer in the melt
colored state (B) is quenched, the recording layer can be cooled to room temperature
with maintaining the colored state, and is turned into the colored state (C) where
the colored state is stabilized and fixed. Whether or not this colored state is obtained
depends on the cooling speed from the melted state. When the temperature is slowly
cooled, the color is erased in the process of cooling, the recording layer is turned
into the erased state (A) that is identical to the initial state, or the state where
the density is relatively lower than the colored state (C) obtained by quenching.
As the recording layer in the colored state (C) is again heated, on the other hand,
the color is erased (from D to E) at the temperature T
2 lower than the coloring temperature. As the recording layer in this state is cooled,
the recording layer is turned back to the erased state (A) that is identical to the
initial state.
[0202] The colored state (C) obtained by quenching from the melted state is a state where
the leuco dye and the color developer are mixed in a manner that molecules thereof
can cause a catalytic reaction to each other, and often forms a solid state. In this
state, the melt mixture (the colored mixture) of the leuco dye and the color developer
is crystallized to maintain the color, and it is considered that the color is stabilized
by the formation of this structure. On the other hand, the erased state is a state
where the phase separation of the leuco dye and the color developer phase is caused.
In this case, at least molecules of one of the compounds are assembled together to
form a domain, or crystallized, and a stable state is created by separating the leuco
dye and the color developer due to the aggregation or crystallization. In most of
cases, more perfect erasion is realized, as the leuco dye and the color developer
causes phase separation and the color developer is crystallized.
[0203] Note that, the erasion realized by slowly cooling from the melted state, and the
erasion realized by heating from the colored state illustrated in FIG. 4A both case
phase separation or crystallization of the color developer, as the aggregated structure
is changed at T
2.
[0204] In FIG. 4A, moreover, there is a case where an erasion failure where erasion cannot
be carried out even after the recording layer is heated to the erasion temperature
may occur, when the recording layer is repeatedly heated to the temperature T
3 that is equal to or higher than the melting temperature T
1. It is assumed that this is because the color developer is thermally decomposed,
and therefore it is difficult to aggregate or crystallize the color developer. As
a result, it is difficult to separate the color developer from the leuco dye. In order
to prevent the deterioration of the thermoreversible recording medium due to repetitive
use, a difference between the melting temperature T
1 and the temperature T
3 of FIG. 4A is made small, when the thermoreversible recording medium is heated.
(Image Processing Method)
[0205] The image processing method of the present invention contains irradiating the thermosensitive
recording medium of the present invention with light to perform image recording, or
image erasing, or both.
[0206] As for the thermosensitive recording medium, any of an embodiment where a thermosensitive
recording layer is provided as an image recording layer, and write-only image recording
is performed thereon once, or an embodiment where a thermoreversible recording layer
is provided as an image recording layer, and image recording and image erasing are
repeatedly performed can be suitably used.
[0207] The image processing method of the present invention contains an image recording
step, or an image erasing step, or both, and may further contain appropriately selected
other steps, as necessary.
[0208] The image processing method of the present invention include an embodiment where
both recording and erasing of an image is performed, an embodiment where only recording
of an image is performed, and an embodiment where only erasing of an image is performed.
<Image Recording Step and Image Erasing Step>
[0209] The image recording step in the image processing method of the present invention
is a step containing heating the thermosensitive recording medium to record an image
on the thermosensitive recording medium. Examples of a method for heating the thermosensitive
recording medium include heating methods known in the art. In case of the image processing
method used in a physical distribution line, a method, in which the thermosensitive
recording medium is irradiated with laser light to heat the thermosensitive recording
medium, is particularly preferable, as an image can be formed in a non-contact manner.
[0210] The image erasing step in the image processing method of the present invention is
a step containing heating the thermosensitive recording medium to erase the image
recorded on the thermosensitive recording medium. As for the heat source, laser light
may be used, or a heat source other than laser light may be used. If heating is performed
by irradiation of laser light among the aforementioned heat sources, it takes a time
to scan one beam of laser light to irradiate the predetermined entire area. In the
case erasion is performed within a short period, it is preferred that the thermosensitive
recording medium be heated by means of an IR ray lamp, a heat roller, a hot stamp,
or a dryer to erase the image. In the case where the thermosensitive recording medium
is provided on a styrene form box as a transporting container for use in a physical
distribution line, the styrene form box is melted of the box itself is heated. Therefore,
it is preferred that laser light be applied to the thermosensitive recording medium
to heat only heat the thermosensitive recording medium, to thereby erase the image.
[0211] An image can be recorded on the thermosensitive recording medium in a non-contact
manner by irradiating the thermosensitive recording medium with laser light to heat
the thermosensitive recording medium.
[0212] In the image processing method of the present invention, typically, updating of an
image (the image erasing step) is performed when the thermosensitive recording medium
is reused, and then an image is recorded by the image recording step. However, the
order for performing recording and erasing of an image is not limited to the aforementioned
order. After recording an image by the image recording step, the image may be erased
by the image erasing step.
[0213] The laser light is appropriately selected depending on the intended purpose without
any limitation, and examples thereof include YAG laser, fiber laser, semiconductor
laser (LD), and laser light emitted from a semiconductor laser array. In case of use
of the thermosensitive recording medium in a physical distribution line, semiconductor
laser light is particularly preferable among the aforementioned light, in view of
advantages, such as a small size of the device, and low cost. In the image erasing
step, light emitted from the semiconductor laser array is preferable, as it can irradiate
a wide area at once to thereby reduce the time required for erasing.
[0214] The output of the laser light emitted in the image recording step is appropriately
selected depending on the intended purpose without any limitation, but the output
thereof is preferably 1 W or greater, more preferably 3 W or greater, and even more
preferably 5 W or greater. When the output of the laser light is less than 1 W, it
takes a long time to form an image, and the output is insufficient so that a high
density image cannot be attained, as the duration for forming an image is shortened.
Moreover, the upper limit of the output of the laser light is appropriately selected
depending on the intended purpose without any limitation, but the upper limit thereof
is preferably 200 W or lower, more preferably 150 W or lower, and even more preferably
100 W or lower. When the output of the laser light is greater than 200 W, a scale
of the laser device may become large.
[0215] The scanning speed of the laser light emitted in the image recording step is appropriately
selected depending on the intended purpose without any limitation, but the scanning
speed thereof is preferably 300 mm/s or greater, more preferably 500 mm/s or greater,
and even more preferably 700 mm/s or greater. When the scanning speed is less than
300 mm/s, it takes a long time to record an image. Moreover, the upper limit of the
scanning speed of the laser light is appropriately selected depending on the intended
purpose without any limitation, but the upper limit thereof is preferably 15,000 mm/s
or less, more preferably 10,000 mm/s or less, and even more preferably 8,000 mm/s
or less. When the scanning speed is greater than 15,000 mm/s, it is difficult to form
an image uniformly.
[0216] The spot diameter of the laser light emitted in the image recording step is appropriately
selected depending on the intended purpose without any limitation, but the spot diameter
thereof is preferably 0.02 mm or greater, more preferably 0.1 mm or greater, and even
more preferably 0.15 mm or greater. Moreover, the upper limit of the spot diameter
of the laser light is appropriately selected depending on the intended purpose without
any limitation, but the upper limit thereof is preferably 3.0 mm or less, more preferably
2.5 mm or less, and even more preferably 2.0 mm or less. When the spot diameter is
small, a line width of the image is thin, and thus the contrast is low to thereby
reduce visibility of the image. When the spot diameter is large, a line width of the
image is thick, so that adjacent lines are overlapped. As a result, it becomes impossible
to record an image of a small character.
[0217] Moreover, the output of the laser light emitted in the image erasing step, where
the thermosensitive recording medium is irradiated with the laser light to heat the
thermosensitive recording medium to thereby erase the image, is appropriately selected
depending on the intended purpose without any limitation. The output thereof is preferably
5 W or greater, more preferably 7 W or greater, and even more preferably 10 W or greater.
When the output of the laser light is less than 5 W, it takes a long time to erase
the image, and the output becomes insufficient to cause an erasion failure of an image,
as the duration for erasing the image is shortened. Moreover, the upper limit of the
output of the laser light is appropriately selected depending on the intended purpose
without any limitation, but the upper limit thereof is preferably 200 W or less, more
preferably 150 W or less, and even more preferably 100 W or less. When the output
of the laser light is greater than 200 W, a scale of the laser device may become large.
[0218] The scanning speed of the laser light emitted in the image erasing step, where the
thermosensitive recording medium is irradiated with the laser light to heat the thermosensitive
recording medium to thereby erase the image, is appropriately selected depending on
the intended purpose without any limitation. The scanning speed thereof is preferably
100 mm/s or greater, more preferably 200 mm/s or greater, and even more preferably
300 mm/s or greater. When the scanning speed is less than 100 mm/s, it takes a long
time to erase the image. Moreover, the upper limit of the scanning speed is appropriately
selected depending on the intended purpose without any limitation, but the upper limit
thereof is preferably 20,000 mm/s or less, more preferably 15,000 mm/s or less, and
even more preferably 10,000 mm/s or less. When the scanning speed is greater than
20,000 mm/s, it may be difficult to erase the image uniformly.
[0219] The spot diameter of the laser light emitted in the image erasing step, where the
thermosensitive recording medium is irradiated with the laser light to heat the thermosensitive
recording medium to thereby erase the image, is appropriately selected depending on
the intended purpose without any limitation. The spot diameter thereof is preferably
0.5 mm or greater, more preferably 1.0 mm or greater, and even more preferably 2.0
mm or greater.
[0220] Moreover, the upper limit of the spot diameter of the laser light is appropriately
selected depending on the intended purpose without any limitation, but the upper limit
thereof is preferably 14.0 mm or less, more preferably 10.0 mm or less, and even more
preferably 7.0 mm or less.
[0221] When the spot diameter is small, it takes a long time to erase the image. When the
spot diameter is large, moreover, the output of the laser light is insufficient, hence
causing an erasion failure of the image.
[0222] The semiconductor laser array for use in the image erasing step is a semiconductor
laser light source, in which a plurality of semiconductor lasers are linearly aligned,
and preferably contains 3 to 300 semiconductor lasers, more preferably 10 to 100 semiconductor
lasers.
[0223] When the number of the semiconductor lasers is small, the irradiation power cannot
be increased. When the number thereof is too large, it may be necessary to provide
a large scale cooling device to cool the semiconductor laser array. Note that, in
order to emit light from the semiconductor laser array, the semiconductor lasers are
heated. Therefore, cooling is necessary, and hence a cost of the device may increase.
[0224] The length of the light source of the semiconductor laser array is appropriately
selected depending on the intended purpose without any limitation, but the length
thereof is preferably 1 mm to 50 mm, more preferably 3 mm to 15 mm. When the length
of the light source of the semiconductor laser array is less than 1 mm, the irradiation
power may not be increased. When the length thereof is greater than 50 mm, it may
be necessary to provide a large scale cooling device to cool the semiconductor laser
array, which may increase a cost of the device.
[0225] The laser light emitted from the semiconductor laser array can be made into a linear
beam by collimating a width direction of the laser light with a width-direction collimating
unit.
[0226] The width-direction collimating unit is appropriately selected depending on the intended
purpose without any limitation, and examples thereof include a plane-convex cylindrical
lens, and a combination of pluralities of convex cylindrical lens.
[0227] The laser light emitted from the semiconductor laser array has the larger beam divergence
angle in the width direction than that in the length direction. As the width-direction
collimating unit is provided adjacent to the output surface of the semiconductor laser
array, the beam width is prevented from being wide, and the small size lens can be
used. Therefore, such arrangement is preferable.
[0228] Moreover, the length of the linear beam can be made longer than the length of the
light source of the semiconductor laser array, and the light distribution of the linear
beam can be made uniform in the length direction thereof by a length-direction light
distribution controlling unit.
[0229] The length-direction light distribution controlling unit is appropriately selected
depending on the intended purpose without any limitation. For example, the length-direction
light distribution controlling unit is composed of a combination of two spherical
lenses, an aspherical cylindrical lens (length direction), and a cylindrical lens
(width direction). Examples of the aspherical cylindrical lens (length direction)
include the Fresnel lens, a convex lens array, and a concave array.
The light distribution controlling unit is provided at the outlet side of the collimating
unit.
[0230] Moreover, at least either length or width of the linear beam, which has a length
longer than length of the light source of the semiconductor laser array, and a uniform
light distribution in the length direction, can be adjusted on the thermosensitive
recording medium, by a beam-size adjusting unit.
[0231] The beam-size adjusting unit is appropriately selected depending on the intended
purpose without any limitation. Examples thereof include a unit configured to change
a focal length of the cylindrical lens, or the spherical lens, a unit configured to
change a position of the lens, and a unit configured to a work distance between the
device and the thermoreversible recording medium.
[0232] The length of the linear beam after the adjustment is preferably 10 mm to 300 mm,
more preferably 30 mm to 160 mm. As an erasable region is determined by the length
of the beam, the erasable region is small when the length is short. When the length
of the linear beam is long, on the other hand, energy is applied to a region that
does not need to be erased, and thus energy loss may occur, or damage may be caused.
[0233] The length of the beam is preferably 2 times or greater the length of the light source
of the semiconductor laser array, more preferably 3 times or greater. When the length
of the beam is shorter than the length of the light source of the semiconductor laser
array, it is necessary to make the light source of the semiconductor laser array long
in order to secure a long erasion region, which may increase a cost or size of the
device.
[0234] Moreover, the width of the linear beam after the adjustment is preferably 0.1 mm
to 10 mm, more preferably 0.2 mm to 5 mm. The beam width can control the duration
for heating the thermosensitive recording medium. When the beam width is narrow, the
heating duration is short, which may reduce erasability. When the beam width is wide,
the heating duration is long, which may apply excess energy to the thermosensitive
recording medium, and require high energy to perform erasion at high speed. Therefore,
the device desirably adjusts the beam width suitable for the erasion properties of
the thermosensitive recording medium.
[0235] The output of the linear beam adjusted in the aforementioned manner is appropriately
selected depending on the intended purpose without any limitation, but the output
thereof is preferably 10 W or greater, more preferably 20 W or greater, and even more
preferably 40 W or greater. When the output of laser light is less than 10 W, it takes
a long time to erase an image, and the output becomes insufficient to cause an erasion
failure of an image, as the duration for erasing the image is shortened. Moreover,
the upper limit of the output of the laser light is appropriately selected depending
on the intended purpose without any limitation, but the upper limit thereof is preferably
500 W or less, more preferably 200 W or less, and even more preferably 120 W or less.
When the output of the laser light is greater than 500 W, a size of a cooling device
used for the light source of semiconductor laser becomes large.
[0236] The scanning speed of the linear beam is appropriately selected depending on the
intended purpose without any limitation, but the scanning speed thereof is preferably
2 mm/s or greater, more preferably 10 mm/s or greater, and even more preferably 20
mm/s or greater. When the scanning speed is less than 2 mm/s, it may take a long time
to erase an image. Moreover, the upper limit of the scanning speed of the laser light
is appropriately selected depending on the intended purpose without any limitation,
but the upper limit thereof is preferably 1,000 mm/s or less, more preferably 300
mm/s or less, and even more preferably 100 mm/s or less. When the scanning speed is
greater than 1,000 mm/s, it may be difficult to erase an image uniformly.
[0237] Moreover, it is preferred that an image recorded on the thermosensitive recording
medium be erased by moving the thermosensitive recording medium using a moving unit
relative to the linear beam, which is longer than the length of the light source of
the semiconductor laser array, and has a uniform light distribution in the length
direction, to thereby scan the linear beam on the thermosensitive recording medium.
Examples of the moving unit include a conveyor, and a stage. In this case, it is preferred
that the thermosensitive recording medium be attached to a surface of a boxy, and
be moved by moving the box by the conveyor.
[0238] The image processing device for use in the present invention contains at least a
laser light emitting unit, and may further contain other units, as necessary.
-Laser Light Emitting Unit-
[0239] The laser light emitting unit used in the image recording step and/or image erasing
step is appropriately selected depending on the intended purpose, provided that it
emits laser light having the maximum wavelength that is around the maximum absorbance
peak of the photothermal converting material contained in the thermosensitive recording
medium. Examples of the laser light emitting unit include a YAG laser, a fiber laser,
a semiconductor laser (LD), and a semiconductor laser array.
[0240] The wavelength of the laser light is particularly preferably a single wavelength.
[0241] The wavelength of laser light emitted from the YAG laser, the fiber laser, the semiconductor
laser, or the semiconductor laser array is in the visible to near infrared region
(a several hundreds nanometers to about 2 µm), and use of such wavelength range has
an advantage that a highly precise image can be formed because of short wavelengths.
Moreover, the YAG laser, and the fiber laser have high outputs, and have an advantage
that an image processing speed can be increased. The semiconductor laser itself is
small in size, and thus has an advantage of a down-sizing of a device, and moreover
low cost. In case of use in a physical distribution line, therefore, semiconductor
laser light is particularly preferably used.
[0242] Moreover, the wavelength of the laser light emitted from the laser light emitting
unit is appropriately selected depending on the intended purpose. The wavelength thereof
is preferably 700 nm to 2,000 nm which various resins contained in the thermosensitive
recording medium absorb less, and more preferably 780 nm to 1,600 nm. When the thermosensitive
recording medium is irradiated with laser light in the wavelength range of shorter
than 700 nm, there is a problem that the thermosensitive recording medium tends to
be deteriorated. When the wavelength of the laser light is greater than 2,000 nm,
the laser light is absorbed by the various resins contained in the thermosensitive
recording medium, there is a problem that a semiconductor laser of high output is
required, and a size of a device for use increases.
[0243] A basic structure of the image processing device is identical to that of so-called
laser marker, provided that the image processing device contains at least the laser
light emitting unit, and the image processing device is equipped with at least an
oscillator unit, a power-source controlling unit, and a programming unit.
[0244] FIG. 5 illustrates one example of the image processing device focusing on the laser
light emitting unit.
[0245] An oscillator unit contains a laser oscillator 1, a beam expander 2, and a scanning
unit 5.
[0246] The laser oscillator 1 is used to attain laser light having high light intensity
and directivity. For example, a couple of mirrors are respectively provided both sides
of a laser medium. The laser medium is pumped (supplied with energy), and as a result,
the number of atoms in the excited state is increased to form a reverse distribution,
to thereby induce emission. Then, only light in the light axial direction is selectively
amplified to increase the directivity of the light. In this manner, laser light is
released from an output mirror.
[0247] The scanning unit 5 is composed of galvanometers 4, and mirrors 4A attached to the
galvanometer 4. Then, the laser light output from the laser oscillator 1 is rotary
scanned at high speed with the two mirrors 4A for the X-axis direction and the Y-axis
direction, attached to the galvanometers 4, to thereby perform recording or erasing
an image on a thermosensitive recording medium 7.
[0248] The power-source controlling unit is composed of a driving power source of a light
source to excite the laser medium, a driving power source of the galvanometers, a
power source for cooling, such as Pelitier element, and a control unit configured
to control the entire image processing device.
[0249] The programming unit is configured to input conditions for image recording or image
erasing, such as intensity of laser light, and scanning speed of laser light, and
create and edit characters to be recorded through input from a touch panel, or key
board.
[0250] Note that, the laser light emitting unit, specifically, a head for image recording,
or image erasing, or both, is mounted in the image processing device. The image processing
device contains other members, such as a transporting unit of the thermosensitive
recording medium, a control unit thereof, and a monitor unit (touch panel).
[0251] The image processing method of the present invention can record and erase an image
at high speed in a non-contact manner on a thermosensitive recording medium, such
as a label attached to a transporting container (e.g., a cardboard box, and a plastic
container), and uses the thermosensitive recording medium which does not reduce an
image density or tints a background when exposed to light for a long period, and has
sufficient erasability. Therefore, the image processing method of the present invention
is particularly suitably used for a physical distribution or delivery system. In this
case, an image can be recorded and erased on the thermosensitive recording medium
(label), for example, while the cardboard box or plastic container placed on a belt
conveyor is moved. Therefore, a time required for shipping can be reduced, as it is
not necessary to stop the line. Moreover, the cardboard box or plastic container to
which the label is attached can be reused as it is, without peeling the label off,
and an image can be again recorded or erased on the label.
Examples
[0252] Examples of the present invention are explained hereinafter, but Examples shall not
be construed as to limit the scope of the present invention in any way.
[0253] In Examples and Comparative Examples, a thermoreversible recording medium was produced
and evaluated as a preferable example of the thermosensitive recording medium. The
case where image recording is performed on the thermoreversible recording medium only
once without repeating image recording and image erasing is determined as Example
which evaluates on a thermosensitive recording medium.
<Measurement of Transmittance of Light-Blocking Layer>
[0254] In Examples and Comparative Examples, a transmittance of a light-blocking layer was
measured by a spectrophotometer (U-4100, manufactured by Hitachi High-Technologies
Corporation). The average transmittance to light in the wavelength range of 380 nm
to 495 nm was calculated by measuring a transmittance per 1 nm in the wavelength region
of 380 nm to 495 nm, and calculating the average value of the measured transmittance
of each wavelength. The average transmittance to light in the wavelength range of
300 nm to 400 nm was also calculated by calculating-the average value in the same
manner.
(Example 1)
<Production of Thermoreversible Recording Medium>
[0255] A thermoreversible recording medium, a color tone of which reversibly changed with
heat, was produced in the following manner.
-Support-
[0256] As for the support, a 125 µm-thick white polyester film (Tetron Film U2L98W, manufactured
by Teijin DuPont Films Japan Limited) was used.
-Under Layer-
[0257] An under layer coating liquid was prepared by blending 30 parts by mass of a styrene-butadiene-based
copolymer (PA-9159, manufactured by Nippon A & L Inc.), 12 parts by mass of a polyvinyl
alcohol resin (POVAL PVA103, manufactured by Kuraray Co., Ltd.), 20 parts by mass
of hollow particles (Microsphere R-300, manufactured by Matsumoto Yushi-Seiyaku Co.,
Ltd.), and 40 parts by mass of water, and stirring the mixture for about 1 hour until
the mixture became homogeneous.
[0258] Subsequently, the obtained under layer coating liquid was applied on the support
with a wire-bar, and the coated layer was heated for 2 minutes at 80°C to dry, to
thereby form an under layer having a thickness of 20 µm.
-Thermoreversible Recording Layer-
[0259] By means of a ball mill, 5 parts by mass of the reversible color developer represented
by the following structural formula (1), 1 part by mass of the erasing accelerator
represented by the following structural formula (2), 10 parts by mass of a 50% by
mass acryl polyol solution (hydroxyl value: 200 mgKOH/g), and 80 parts by mass of
methyl ethyl ketone were ground and dispersed until the average particle diameter
thereof became 1 µm.
[Reversible Color Developer]
[0260]
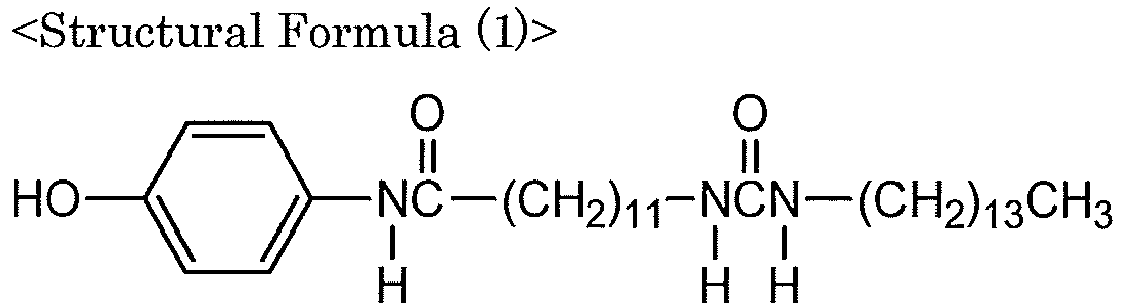
[Erasing Accelerator]
[0261]
<Structural Formula (2)> C
17H
35CONHC
18H
37
[0262] To the dispersion liquid, in which the reversible color developer had ground and
dispersed, 1 part by mass of 2-anilino-3-methyl-6-diethylaminofluoran serving as a
leuco dye, 1.5 parts by mass of a 18.5% by mass cesium-containing tungsten oxide compound
(serving as metal oxide having absorbance in the near infrared region) dispersion
liquid (YMF-01, manufactured by (Sumitomo Metal Mining Co., Ltd.), and 5 parts by
mass of isocyanate (Coronate HL, manufactured by Tosoh Corporation) were added. The
resulting mixture was sufficiently stirred, to thereby prepare a thermoreversible
recording layer coating liquid.
[0263] Subsequently, the obtained thermoreversible recording layer coating liquid was applied
on the support, to which the under layer had been formed, with a wire bar, and the
coated layer was heated for 2 minutes at 100°C to dry. Thereafter, the dried layer
was cured for 24 hours at 60°C, to thereby form a thermoreversible recording layer
having a thickness of 10 µm.
-Light-Blocking Layer-
[0264] A coating liquid was prepared by blending 5.0 parts by mass of a 40% by mass ultraviolet
ray-absorbing polymer solution (UV-G302, manufactured by Nippon Shokubai Co., Ltd.),
1.3 parts by mass of an azo-compound (LIBERA COLOR TXL-200 YELLOW, manufactured by
Cashew Co., Ltd.) serving as a compound that absorbed, reflected, or scattered light
in a wavelength range of 500 nm or shorter), 0.7 part by mass of hydrophobic silica
(RX-200, manufactured by Nippon Aerosil Co., Ltd.), 1.0 part by mass of an isocyanate
compound (Coronate HL, manufactured by Tosoh Corporation), and 9.2 parts by mass of
methyl ethyl ketone, and sufficiently stirring the mixture.
[0265] Subsequently, the coating liquid was applied on the support, to which the under layer
and the thermoreversible recording layer had been formed, and the coated layer was
heated for 1 minute at 90°C to dry. Thereafter, the dried layer was heated for 24
hours at 60°C, to thereby form a light-blocking layer having a thickness of 4 µm.
-First Oxygen Barrier Layer-
[0266] An adhesive layer coating liquid was prepared by blending 5 parts by mass of a urethane-based
adhesive (TM-567, manufactured by Toyo-Morton, Ltd.), 0.5 parts by mass of isocyanate
(CAT-RT-37, manufactured by Toyo-Morton, Ltd.), and 5 parts by mass of ethyl acetate,
and sufficiently stirring the mixture.
[0267] Subsequently the adhesive layer coating layer was applied on a silica-vapor deposition
PET film (IB-PET-C, manufactured by Dai Nippon Printing Co., Ltd., oxygen permeation
rate: 15 mL/m
2/day/MPa) with a wire bar, and the coated layer was heated for 1 minutes at 80°C to
dry. Thereafter, the resultant was bonded on the support, to which the under layer,
the thermoreversible recording layer, and the light-blocking layer had been formed,
and heated for 24 hours at 50°C, to thereby form a first oxygen barrier layer having
a thickness of 12 µm.
-Protective Layer-
[0268] A protective layer coating liquid was prepared by blending 3 parts by mass of pentaerythritol
hexaacrylate (KAYARAD DPHA, manufactured by Nippon Kayaku Co., Ltd.), 3 parts by mass
of urethane acrylate oligomer (Art Resin UN-3320HA, manufactured by Negami Chemical
Industrial Co., Ltd.), 3 parts by mass of acrylic acid ester of dipentaerythritol
caprolactone (KAYARAD DPCA-120, manufactured by Nippon Kayaku Co., Ltd.), 0.5 parts
by mass of a photopolymerization initiator (IRGACURE 184, manufactured by Nippon Chiba-Geigy
K.K.), and 11 parts by mass of isopropyl alcohol, and sufficiently stirring the mixture.
[0269] Subsequently, the protective layer coating liquid was applied on the first oxygen
barrier layer with a wire bar, and the coated layer was heated for 1 minute at 90°C
to dry. Thereafter, the dried layer was cured with a 80 W/cm lamp, to thereby form
a protective layer having a thickness of about 4 µm.
-Bonding Agent Layer-
[0270] An acryl emulsion-based bonding agent (BPW6111, manufactured by TOYOCHEM CO., LTD.,
solid content: 60% by mass) was applied onto release paper (LSW, manufactured by LINTEC
Corporation) with a wire bar to give a dry weight of 20 g/m
2, followed by drying the bonding agent. The resultant was bonded on a surface of the
support, which was opposite to the surface thereof where the thermoreversible recording
layer was provided, followed by leaving to stand for 7 days at 23°C, to thereby form
a bonding agent layer. In the manner as described above, a thermoreversible recording
medium of Example 1 was produced.
[0271] The produced thermoreversible recording medium of Example 1 was cut into a piece
in the size of 20 mm x 20 mm. The support was peeled from the cut piece by inserting
a blade of a cutter into an interface between the support and the under layer from
the cross section of the thermoreversible recording medium, and gradually scraping.
Thereafter, the under layer and the thermoreversible recording layer were gradually
scraped from the back surface of the thermoreversible recording medium using the cutter
and sand paper to thereby remove the opaque layers, such as the support and the thermoreversible
recording layer. Thereafter, the transmittance of the remaining layer was measured
by a spectrophotometer (U-4100, manufactured by Hitachi High-Technologies Corporation)
per 1 nm in the wavelength region of 300 nm to 700 nm. As a result, the average transmittance
of the light-blocking layer to light in a wavelength range of 300 nm to 400 nm was
1.8%, the average transmittance thereof to light in a wavelength range of 380 nm to
495 nm was 15.0%, and the transmittance thereof to light having a wavelength of 470
nm was 17.3%. A graph depicting a relationship between the wavelength and the transmittance
of the light-blocking layer of Example 1 is presented in FIG. 6.
(Example 2)
<Production of Thermoreversible Recording Medium>
[0272] The following photothermal conversion layer coating liquid was applied on the under
layer of Example 1 with a wire bar, and the coated layer was heated for 1 minute at
90°C to dry, followed by heating for 2 hours at 60°C, to thereby form a photoconversion
layer having a thickness of 3 µm.
-Preparation of Photothermal Conversion Layer Coating Liquid-
[0273] A photothermal conversion layer coating liquid was prepared by blending 6 parts by
mass of a 50% by mass acryl polyol resin solution (LR327, manufactured by Mitsubishi
Rayon Co., Ltd.), 1.25 parts by mass of a 18.5% by mass cesium-containing tungsten
oxide compound (serving as metal oxide having absorbance in the near infrared region)
dispersion liquid (YMF-01, manufactured by Sumitomo Metal Mining Co., Ltd.), 2.4 parts
by mass of isocyanate (Coronate HL, manufactured by Tosoh Corporation), and 14 parts
by mass of methyl ethyl ketone, and sufficiently stirring the mixture.
[0274] Subsequently, a thermoreversible recording layer was formed on the photoconversion
layer in the same manner as in Example 1, provided that metal oxide having absorbence
in the near infrared region was excluded from the thermoreversible recording layer
of Example 1.
[0275] Subsequently, the light-blocking layer identical to that of Example 1, the first
oxygen barrier layer identical to that of Example 1, and the protective layer identical
to that of Example 1 were formed on the thermoreversible recording layer in this order.
Moreover, the bonding agent layer identical to Example 1 was formed in the same manner
as in Example 1, to thereby produce a thermoreversible recording medium of Example
2.
[0276] The produced thermoreversible recording medium of Example 2 was measured by the spectrophotometer
(U-4100, manufactured by Hitachi High-Technologies Corporation) in the same manner
as in Example 1. As a result, the average transmittance of the light-blocking layer
of Example 2 to light in a wavelength range of 300 nm to 400 nm, the average transmittance
thereof to light in a wavelength range of 380 nm to 495 nm, and a transmittance thereof
to light having a wavelength of 470 nm were identical to those of Example 1. The graph
depicting a relationship between the wavelength and the transmittance of the light-blocking
layer was identical to FIG. 6.
(Example 3)
<Production of Thermoreversible Recording Medium>
[0277] A thermoreversible recording medium of Example 3 was produced in the same manner
as in Example 1, provided that a second oxygen barrier layer was provided between
the surface of the support of Example 1, which was opposite to the surface thereof
where the thermoreversible recording layer was provided, and the bonding agent layer
of Example 1, in the same manner as the formation of the first oxygen barrier layer
of Example 1.
[0278] The produced thermoreversible recording medium of Example 3 was measured by the spectrophotometer
(U-4100, manufactured by Hitachi High-Technologies Corporation) in the same manner
as in Example 1. As a result, the average transmittance of the light-blocking layer
of Example 3 to light in a wavelength range of 300 nm to 400 nm, the average transmittance
thereof to light in a wavelength range of 380 nm to 495 nm, and a transmittance thereof
to light having a wavelength of 470 nm were identical to those of Example 1. The graph
depicting a relationship between the wavelength and the transmittance of the light-blocking
layer was identical to FIG. 6.
(Example 4)
<Production of Thermoreversible Recording Medium>
[0279] A thermoreversible recording medium of Example 4 was produced in the same manner
as in Example 3, provided that the amount of the azo-compound (LIBERA COLOR TXL-200
YELLOW, manufactured by Cashew Co., Ltd.) serving as the compound that absorbed, reflected,
or scattered light in a wavelength range of 500 nm or shorter, which wa contained
in the light-blocking layer, was changed from 1.3 parts by mass to 2.4 parts by mass.
[0280] The produced thermoreversible recording medium of Example 4 was measured by the spectrophotometer
(U-4100, manufactured by Hitachi High-Technologies Corporation) in the same manner
as in Example 1. As a result, the average transmittance of the light-blocking layer
of Example 4 to light in a wavelength range of 300 nm to 400 nm was 0.9%, the average
transmittance thereof to light in a wavelength range of 380 nm to 495 nm was 8.9%,
and the transmittance thereof to light having a wavelength of 470 nm was 10.2%. A
graph depicting a relationship between wavelengths of the transmittance of the light-blocking
layer of Example 4 is presented in FIG. 7.
(Example 5)
<Production of Thermoreversible Recording Medium>
[0281] A thermoreversible recording medium of Example 5 was produced in the same manner
as in Example 3, provided that the amount of the azo-compound (LIBERA COLOR TXL-200
YELLOW, manufactured by Cashew Co., Ltd.) serving as the compound that absorbed, reflected,
or scattered light in a wavelength range of 500 nm or shorter, which was contained
in the light-blocking layer, was changed from 1.3 parts by mass to 3.1 parts by mass.
[0282] The produced thermoreversible recording medium of Example 5 was measured by the spectrophotometer
(U-4100, manufactured by Hitachi High-Technologies Corporation) in the same manner
as in Example 1. As a result, the average transmittance of the light-blocking layer
of Example 5 to light in a wavelength range of 300 nm to 400 nm was 0.5%, the average
transmittance thereof to light in a wavelength range of 380 nm to 495 nm was 3.4%,
and the transmittance thereof to light having a wavelength of 470 nm was 3.9%. A graph
depicting a relationship between the wavelength and the transmittance of the light-blocking
layer of Example 5 is presented in FIG. 8.
(Example 6)
<Production of Thermoreversible Recording Medium>
[0283] A thermoreversible recording medium of Example 6 was produced in the same manner
as in Example 5, provided that 0.03 parts by mass of a hindered phenol-based compound
(SUMILIZER MDP-S, manufactured by Sumitomo Chemical Co., Ltd.) was added to the thermoreversible
recording layer coating liquid.
[0284] The produced thermoreversible recording medium of Example 6 was measured by the spectrophotometer
(U-4100, manufactured by Hitachi High-Technologies Corporation) in the same manner
as in Example 1. As a result, the average transmittance of the light-blocking layer
of Example 6 to light in a wavelength range of 300 nm to 400 nm, the average transmittance
thereof to light in a wavelength range of 380 nm to 495 nm, and a transmittance thereof
to light having a wavelength of 470 nm were identical to those of Example 5. The graph
depicting a relationship between the wavelength and the transmittance of the light-blocking
layer was identical to FIG. 8.
(Example 7)
<Production of Thermoreversible Recording Medium>
[0285] A thermoreversible recording medium of Example 7 was produced in the same manner
as in Example 5, provided that 1.5 parts by mass of the 18.5% by mass cesium-containing
tungsten oxide compound (serving as the metal oxide having the absorbance in the near
infrared region) dispersion liquid (YMF-01, manufactured by Sumitomo Metal Mining
Co., Ltd.) was replaced with 15 parts by mass of a 20% by mass indium-doped tin oxide
dispersion liquid (manufactured by Mitsubishi Materials Corporation).
[0286] The produced thermoreversible recording medium of Example 7 was measured by the spectrophotometer
(U-4100, manufactured by Hitachi High-Technologies Corporation) in the same manner
as in Example 1. As a result, the average transmittance of the light-blocking layer
of Example 7 to light in a wavelength range of 300 nm to 400 nm, the average transmittance
thereof to light in a wavelength range of 380 nm to 495 nm, and a transmittance thereof
to light having a wavelength of 470 nm were identical to those of Example 5. The graph
depicting a relationship between the wavelength and the transmittance of the light-blocking
layer was identical to FIG. 8.
(Example 8)
<Production of Thermoreversible Recording Medium>
[0287] A thermoreversible recording medium of Example 8 was produced in the same manner
as in Example 5, provided that 1.5 parts by mass of the 18.5% by mass cesium-containing
tungsten oxide compound (serving as the metal oxide having the absorbance in the near
infrared region) dispersion liquid (YMF-01, manufactured by Sumitomo Metal Mining
Co., Ltd.) was replaced with 15 parts by mass of a 30% by mass antimony-doped tin
oxide dispersion liquid (SN-14, manufactured by Ishihara Sangyo Kaisha, Ltd.).
[0288] The produced thermoreversible recording medium of Example 8 was measured by the spectrophotometer
(U-4100, manufactured by Hitachi High-Technologies Corporation) in the same manner
as in Example 1. As a result, the average transmittance of the light-blocking layer
of Example 8 to light in a wavelength range of 300 nm to 400 nm, the average transmittance
thereof to light in a wavelength range of 380 nm to 495 nm, and a transmittance thereof
to light having a wavelength of 470 nm were identical to those of Example 5. The graph
depicting a relationship between the wavelength and the transmittance of the light-blocking
layer was identical to FIG. 8.
(Example 9)
<Production of Thermoreversible Recording Medium>
[0289] After forming a thermoreversible recording layer in the same manner as in Example
3, the following intermediate layer coating liquid was applied to the support, to
which the thermoreversible recording layer had been formed, with a wire bar, and the
coated layer was heated for 1 minute at 90°C to dry. Thereafter, the dried layer was
heated for 2 hours at 60°C, to thereby form an intermediate layer having a thickness
of 2 µm.
-Preparation of Intermediate Layer Coating Liquid-
[0290] An intermediate layer coating liquid was prepared by blending 6 parts by mass of
a 50% by mass acryl polyol resin solution (LR327, manufactured by Mitsubishi Rayon
Co., Ltd.), 2.4 parts by mass of isocyanate (Coronate HL, manufactured by Tosoh Corporation),
and 14 parts by mass of methyl ethyl ketone, and sufficiently stirring the mixture.
[0291] Subsequently, the first oxygen barrier layer identical to Example 3, the light-blocking
layer identical to Example 3, and the protective layer identical to Example 3 were
formed on the intermediate layer in this order. Moreover, the second oxygen barrier
layer identical to Example 3, and the bonding agent layer identical to Example 3 were
formed on the surface of the support, which was opposite to the surface thereof where
the thermoreversible recording layer had been provided, to thereby produce a thermoreversible
recording medium of Example 9.
[0292] The produced thermoreversible recording medium of Example 9 was measured by the spectrophotometer
(U-4100, manufactured by Hitachi High-Technologies Corporation) in the same manner
as in Example 1. As a result, the average transmittance of the light-blocking layer
of Example 9 to light in a wavelength range of 300 nm to 400 nm, the average transmittance
thereof to light in a wavelength range of 380 nm to 495 nm, and a transmittance thereof
to light having a wavelength of 470 nm were identical to those of Example 3. The graph
depicting a relationship between the wavelength and the transmittance of the light-blocking
layer was identical to FIG. 6.
(Example 10)
<Production of Thermoreversible Recording Medium>
[0293] After forming a thermoreversible recording layer in the same manner as in Example
3, the following blue light-blocking layer coating liquid was applied to the support,
on which the thermoreversible recording layer had been formed, with a wire bar, and
the coated layer was heated for 1 minute at 90°C to dry. Thereafter, the dried layer
was heated for 2 hours at 60°C, to thereby form a blue light-blocking layer having
a thickness of 4 µm.
-Preparation of Blue Light-Blocking Layer Coating Liquid-
[0294] A blue light-blocking layer coating liquid was prepared by blending 5.0 parts by
mass of a 50% by mass acryl polyol resin solution (LR327, manufactured by Mitsubishi
Rayon Co., Ltd.), 2.9 parts by mass of an isoindolinone-based compound (SD-TT1140,
manufactured by RESINO COLOR INDUSTRY CO., LTD.) serving as a compound that absorbed,
reflected, or scattered light in a wavelength range of 500 nm or shorter, 1.2 parts
by mass of isocyanate (Coronate HL, manufactured by Tosoh Corporation), and 14.0 parts
by mass of methyl ethyl ketone, and sufficiently stirring the mixture.
[0295] Subsequently, the first oxygen barrier layer identical to Example 3 was formed on
the blue light-blocking layer. Moreover, the following ultraviolet ray-blocking layer
coating liquid was applied to the first oxygen barrier layer, and the coated layer
was heated for 1 minute at 90°C to dry. Thereafter, the dried layer was heated for
2 hours at 60°C, to thereby form an ultraviolet ray-blocking layer having a thickness
of 4 µm.
-Preparation of Ultraviolet Ray-Blocking Layer Coating Layer-
[0296] A ultraviolet ray-blocking layer was prepared by blending 5.0 parts by mass of a
40% by mass ultraviolet ray-absorbing polymer solution (UV-G302, manufactured by Nippon
Shokubai Co., Ltd.), 0.5 parts by mass of hydrophobic silica (RX-200, manufactured
by Nippon Aerosil Co., Ltd.), 1.0 part by mass of an isocyanate compound (Coronate
HL, manufactured by Tosoh Corporation), and 12 parts by mass of methyl ethyl ketone,
and sufficiently stirring the mixture.
[0297] Subsequently, the protective layer identical to Example 3 was formed on the ultraviolet
ray-blocking layer. Moreover, the second oxygen barrier layer identical to Example
3, and the bonding agent layer identical to Example 3 were formed on the surface of
the support, which was opposite to the surface thereof where the thermoreversible
recording layer had been provided, in the same manner as in Example 3, to thereby
produce a thermoreversible recording medium of Example 10.
[0298] The produced thermoreversible recording medium of Example 10 was measured by the
spectrophotometer (U-4100, manufactured by Hitachi High-Technologies Corporation)
in the same manner as in Example 1. As a result, the average transmittance of the
light-blocking layer of Example 10, in which the blue light-blocking layer and the
ultraviolet ray-blocking layer were laminated, to light in a wavelength range of 300
nm to 400 nm was 0.6%, the average transmittance thereof to light in a wavelength
range of 380 nm to 495 nm was 4.9%, and the transmittance thereof to light having
a wavelength of 470 nm was 7.5%. A graph depicting a relationship between the wavelength
and the transmittance of the light-blocking layer of Example 10 is presented in FIG.
9.
(Example 11)
<Production of Thermoreversible Recording Medium>
[0299] A thermoreversible recording medium of Example 11 was produced in the same manner
as in Example 10, provided that the order for laminating the blue light-blocking layer
and the ultraviolet ray-blocking layer was reversed.
[0300] The produced thermoreversible recording medium of Example 11 was measured by the
spectrophotometer (U-4100, manufactured by Hitachi High-Technologies Corporation)
in the same manner as in Example 1. As a result, the average transmittance of the
light-blocking layer of Example 11, in which the blue light-blocking layer and the
ultraviolet ray-blocking layer were laminated, to light in a wavelength range of 300
nm to 400 nm, the average transmittance thereof to light in a wavelength range of
380 nm to 495 nm, and a transmittance thereof to light having a wavelength of 470
nm were identical to those of Example 10. The graph depicting a relationship between
the wavelength and the transmittance of the light-blocking layer was identical to
FIG. 9.
(Example 12)
<Production of Thermoreversible Recording Medium>
[0301] A thermoreversible recording medium of Example 12 was produced in the same manner
as in Example 10, provided that the intermediate layer identical to Example 9 was
formed on the thermoreversible recording layer identical to Example 10, and the first
oxygen barrier layer identical to Example 10, the blue light-blocking layer identical
to Example 10, the ultraviolet ray-blocking layer identical to Example 10, and the
protective layer identical to Example 10 were formed on the intermediate layer in
this order.
[0302] The produced thermoreversible recording medium of Example 12 was measured by the
spectrophotometer (U-4100, manufactured by Hitachi High-Technologies Corporation)
in the same manner as in Example 1. As a result, the average transmittance of the
light-blocking layer of Example 12, in which the blue light-blocking layer and the
ultraviolet ray-blocking layer were laminated, to light in a wavelength range of 300
nm to 400 nm, the average transmittance thereof to light in a wavelength range of
380 nm to 495 nm, and a transmittance thereof to light having a wavelength of 470
nm were identical to those of Example 10. The graph depicting a relationship between
the wavelength and the transmittance of the light-blocking layer was identical to
FIG. 9.
(Example 13)
<Production of Thermoreversible Recording Medium>
[0303] A thermoreversible recording medium of Example 13 was produced in the same manner
as in Example 12, provided that the order for laminating the blue light-blocking layer
and the ultraviolet ray-blocking layer was reversed.
[0304] The produced thermoreversible recording medium of Example 13 was measured by the
spectrophotometer (U-4100, manufactured by Hitachi High-Technologies Corporation)
in the same manner as in Example 1. As a result, the average transmittance of the
light-blocking layer of Example 13, in which the blue light-blocking layer and the
ultraviolet ray-blocking layer were laminated, to light in a wavelength range of 300
nm to 400 nm, the average transmittance thereof to light in a wavelength range of
380 nm to 495 nm, and a transmittance thereof to light having a wavelength of 470
nm were identical to those of Example 10. The graph depicting a relationship between
the wavelength and the transmittance of the light-blocking layer was identical to
FIG. 9.
(Example 14)
<Production of Thermoreversible Recording Medium>
[0305] A thermoreversible recording medium of Example 14 was produced in the same manner
as in Example 10, provided that the order for laminating the ultraviolet ray-blocking
layer and the oxygen barrier layer was reversed.
[0306] The produced thermoreversible recording medium of Example 14 was measured by the
spectrophotometer (U-4100, manufactured by Hitachi High-Technologies Corporation)
in the same manner as in Example 1. As a result, the average transmittance of the
light-blocking layer of Example 14, in which the blue light-blocking layer and the
ultraviolet ray-blocking layer were laminated, to light in a wavelength range of 300
nm to 400 nm, the average transmittance thereof to light in a wavelength range of
380 nm to 495 nm, and a transmittance thereof to light having a wavelength of 470
nm were identical to those of Example 10. The graph depicting a relationship between
the wavelength and the transmittance of the light-blocking layer was identical to
FIG. 9.
(Example 15)
<Production of Thermoreversible Recording Medium>
[0307] After forming a thermoreversible recording layer in the same manner as in Example
3, the following light-blocking layer coating liquid was applied to the support, to
which the thermoreversible recording layer had been formed, with a wire bar, and the
coated layer was heated for 1 minute at 90°C to dry, to thereby form a light-blocking
layer having a thickness of 4 µm.
-Preparation of Light-Blocking Layer Coating Liquid-
[0308] A light-blocking layer coating liquid was prepared by blending 3.8 parts by mass
of a 50% by mass acryl polyol resin solution (LR327, manufactured by Mitsubishi Rayon
Co., Ltd.), 2.5 parts by mass of a screen ink containing a compound that absorbed,
reflected, or scattered light in a wavelength range of 500 nm or shorter (Vinyl Ink
H-type Half-tone (blue-yellow), manufactured by Jujo Chemical Co., Ltd.), 0.5 parts
by mass of hydrophobic silica (RX-200, manufactured by Nippon Aerosil Co., Ltd.),
and 6.3 parts by mass of methyl isobutyl ketone, and sufficiently stirring the mixture.
[0309] Subsequently, the first oxygen barrier layer identical to that of Example 3, the
protective layer identical to that of Example 3 were formed on the light-blocking
layer, and the second oxygen barrier layer identical to that of Example 3, and the
bonding agent layer identical to that of Example 3 were formed on the surface of the
support opposite to the surface thereof where the thermoreversible recording layer
had been provided in the same manner as in Example 3. In the manner as described,
a thermoreversible recording medium of Example 15 was produced.
[0310] The produced thermoreversible recording medium of Example 15 was measured by the
spectrophotometer (U-4100, manufactured by Hitachi High-Technologies Corporation)
in the same manner as in Example 1. As a result, the average transmittance of the
light-blocking layer of Example 15 to light having wavelength of 300 nm to 400 nm
was 4.5%, the average transmittance thereof to light in a wavelength range of 380
nm to 495 nm was 14.8%, and the transmittance thereof to light having a wavelength
of 470 nm was 25.6%. A graph depicting a relationship between the wavelength and the
transmittance of the light-blocking layer of Example 15 is presented in FIG. 10.
(Comparative Example 1)
<Production of Thermoreversible Recording Medium>
[0311] A thermoreversible recording medium of Comparative Example 1 was produced in the
same manner as in Example 1, provided that the azo-compound (LIBERA COLOR TXL-200
YELLOW, manufactured by Cashew Co., Ltd.) was excluded from the light-blocking layer.
[0312] The produced thermoreversible recording medium of Comparative Example 1 was measured
by the spectrophotometer (U-4100, manufactured by Hitachi High-Technologies Corporation)
in the same manner as in Example 1. Since the light-blocking layer of Comparative
Example 1 did not contain the compound that absorbed, reflected, or scattered light
in a wavelength range of 500 nm or shorter, the light-blocking layer thereof was substantially
an ultraviolet ray-blocking layer. The average transmittance of the light-blocking
layer of Comparative Example 1 to light in a wavelength range of 300 nm to 400 nm
was 6.0%, the average transmittance thereof to light in a wavelength range of 380
nm to 495 nm was 74.8%, and the transmittance thereof to light having a wavelength
of 470 nm was 86.5%. The results are depicted in FIG. 11.
(Comparative Example 2)
<Production of Thermoreversible Recording Medium>
[0313] A thermoreversible recording medium of Comparative Example 2 was produced in the
same manner as in Example 2, provided that the azo-compound (LIBERA COLOR TXL-200
YELLOW, manufactured by Cashew Co., Ltd.) was excluded from the light-blocking layer.
[0314] The produced thermoreversible recording medium of Comparative Example 2 was measured
by the spectrophotometer (U-4100, manufactured by Hitachi High-Technologies Corporation)
in the same manner as in Example 1. As a result, the average transmittance of the
light-blocking layer of Comparative Example 2 to light in a wavelength range of 300
nm to 400 nm, the average transmittance thereof to light in a wavelength range of
380 nm to 495 nm, and a transmittance thereof to light having a wavelength of 470
nm were identical to those of Comparative Example 1. The graph depicting a relationship
between the wavelength and the transmittance of the light-blocking layer was identical
to FIG. 11.
(Comparative Example 3)
<Production of Thermoreversible Recording Medium>
[0315] A thermoreversible recording medium of Comparative Example 3 was produced in the
same manner as Example 5, provided that the azo-compound (LIBERA COLOR TXL-200 YELLOW,
manufactured by Cashew Co., Ltd.) was excluded from the light-blocking layer.
[0316] The produced thermoreversible recording medium of Comparative Example 3 was measured
by the spectrophotometer (U-4100, manufactured by Hitachi High-Technologies Corporation)
in the same manner as in Example 1. As a result, the average transmittance of the
light-blocking layer of Comparative Example 3 to light in a wavelength range of 300
nm to 400 nm, the average transmittance thereof to light in a wavelength range of
380 nm to 495 nm, and a transmittance thereof to light having a wavelength of 470
nm were identical to those of Comparative Example 1. The graph depicting a relationship
between the wavelength and the transmittance of the light-blocking layer was identical
to FIG. 11.
(Comparative Example 4)
<Production of Thermoreversible Recording Medium>
[0317] A thermoreversible recording medium of Comparative Example 4 was produced in the
same manner as in Example 7, provided that the azo-compound (LIBERA COLOR TXL-200
YELLOW, manufactured by Cashew Co., Ltd.) was excluded from the light-blocking layer.
[0318] The produced thermoreversible recording medium of Comparative Example 4 was measured
by the spectrophotometer (U-4100, manufactured by Hitachi High-Technologies Corporation)
in the same manner as in Example 1. As a result, the average transmittance of the
light-blocking layer of Comparative Example 4 to light in a wavelength range of 300
nm to 400 nm, the average transmittance thereof to light in a wavelength range of
380 nm to 495 nm, and a transmittance thereof to light having a wavelength of 470
nm were identical to those of Comparative Example 1. The graph depicting a relationship
between the wavelength and the transmittance of the light-blocking layer was identical
to FIG. 11.
(Comparative Example 5)
<Production of Thermoreversible Recording Medium>
[0319] A thermoreversible recording medium of Comparative Example 5 was produced in the
same manner as in Example 8, provided that the azo-compound (LIBERA COLOR TXL-200
YELLOW, manufactured by Cashew Co., Ltd.) was excluded from the light-blocking layer.
[0320] The produced thermoreversible recording medium of Comparative Example 5 was measured
by the spectrophotometer (U-4100, manufactured by Hitachi High-Technologies Corporation)
in the same manner as in Example 1. As a result, the average transmittance of the
light-blocking layer of Comparative Example 5 to light in a wavelength range of 300
nm to 400 nm, the average transmittance thereof to light in a wavelength range of
380 nm to 495 nm, and a transmittance thereof to light having a wavelength of 470
nm were identical to those of Comparative Example 1. The graph depicting a relationship
between the wavelength and the transmittance of the light-blocking layer was identical
to FIG. 11.
(Comparative Example 6)
<Production of Thermoreversible Recording Medium>
[0321] A thermoreversible recording medium of Comparative Example 6 was produced in the
same manner as in Example 15, provided that the light-blocking layer coating liquid
was changed to the following light-blocking layer coating liquid.
-Preparation of Light-Blocking Layer Coating Liquid-
[0322] A light-blocking layer coating liquid was prepared by blending 6.0 parts by mass
of a 50% by mass acryl polyol resin solution (LR327, manufactured by Mitsubishi Rayon
Co., Ltd.), 2.0 parts by mass of a screen ink containing a compound that absorbed,
reflected, or scattered light in a wavelength range of 500 nm or shorter (Vinyl Ink
H-type Half-tone (blue-yellow), manufactured by Jujo Chemical Co., Ltd.), 0.7 parts
by mass of hydrophobic silica (RX-200, manufactured by Nippon Aerosil Co., Ltd.),
and 9.5 parts by mass of methyl isobutyl ketone, and sufficiently stirring the mixture.
[0323] The produced thermoreversible recording medium of Comparative Example 6 was measured
by the spectrophotometer (U-4100, manufactured by Hitachi High-Technologies Corporation)
in the same manner as in Example 1. As a result, the average transmittance of the
light-blocking layer of Comparative Example 6 to light in a wavelength range of 300
nm to 400 nm was 16.0%, the average transmittance to light in a wavelength range of
380 nm to 495 nm was 21.8%, and the transmittance thereof to light having a wavelength
of 470 nm was 39.1%. A graph depicting a relationship between the wavelength and the
transmittance of the light-blocking layer of Comparative Example 6 is presented in
FIG. 12.
(Comparative Example 7)
<Production of Thermoreversible Recording Medium>
[0324] A thermoreversible recording medium of Comparative Example 7 was produced in the
same manner as in Example 3, provided that the amount of the azo-compound (LIBERA
COLOR TXL-200 YELLOW, manufactured by Cashew Co., Ltd.) serving as the compound that
absorbed, reflected, or scattered light in a wavelength range of 500 nm or shorter
was changed from 1.3 parts by mass to 0.6 parts by mass.
[0325] The produced thermoreversible recording medium of Comparative Example 7 was measured
by the spectrophotometer (U-4100, manufactured by Hitachi High-Technologies Corporation)
in the same manner as in Example 1. As a result, the average transmittance of the
light-blocking layer of Comparative Example 7 to light in a wavelength range of 300
nm to 400 nm was 3.4%, the average transmittance to light in a wavelength range of
380 nm to 495 nm was 34.9%, and the transmittance thereof to light having a wavelength
of 470 nm was 40.9%. A graph depicting a relationship between the wavelength and the
transmittance of the light-blocking layer of Comparative Example 7 is presented in
FIG. 13.
(Comparative Example 8)
<Production of Thermoreversible Recording Medium>
[0326] A thermoreversible recording medium of Comparative Example 8 was produced in the
same manner as in Example 3, provided that the light-blocking layer coating liquid
was changed to the following light-blocking layer coating liquid.
-Preparation of Light-Blocking Layer Coating Liquid-
[0327] A light-blocking layer coating liquid was prepared by blending 2.0 parts by mass
of a 50% by mass acryl polyol resin solution (LR327, manufactured by Mitsubishi Rayon
Co., Ltd.), 4.0 parts by mass of a screen ink containing a compound that absorbed,
reflected, or scattered light in a wavelength range of 500 nm or shorter (Vinyl Ink
H-type Half-tone (blue-yellow), manufactured by Jujo Chemical Co., Ltd.), 0.4 parts
by mass of hycliophobic silica (RX-200, manufactured by Nippon Aerosil Co., Ltd.),
and 4.0 parts by mass of methyl isobutyl ketone, and sufficiently stirring the mixture.
[0328] The produced thermoreversible recording medium of Comparative Example 8 was measured
by the spectrophotometer (U-4100, manufactured by Hitachi High-Technologies Corporation)
in the same manner as in Example 1. As a result, the average transmittance of the
light-blocking layer of Comparative Example 8 to light in a wavelength range of 300
nm to 400 nm was 22.3%, the average transmittance to light in a wavelength range of
380 nm to 495 nm was 11.1%, and the transmittance thereof to light having a wavelength
of 470 nm was 10.4%. A graph depicting a relationship between the wavelength and the
transmittance of the light-blocking layer of Comparative Example 8 is presented in
FIG. 14.
(Comparative Example 9)
<Production of Thermoreversible Recording Medium>
[0329] A thermoreversible recording medium of Comparative Example 9 was produced in the
same manner as in Example 1, provided that the first oxygen barrier layer was excluded.
[0330] The produced thermoreversible recording medium of Comparative Example 9 was measured
by the spectrophotometer (U-4100, manufactured by Hitachi High-Technologies Corporation)
in the same manner as in Example 1. As a result, the average transmittance of the
light-blocking layer of Comparative Example 9 to light in a wavelength range of 300
nm to 400 nm, the average transmittance thereof to light in a wavelength range of
380 nm to 495 nm, and a transmittance thereof to light having a wavelength of 470
nm were identical to those of Example 1. The graph depicting a relationship between
the wavelength and the transmittance of the light-blocking layer was identical to
FIG. 6.
(Comparative Example 10)
<Production of Thermoreversible Recording Medium>
[0331] A thermoreversible recording medium of Comparative Example 10 was produced in the
same manner as in Example 3, provided that the light-blocking layer coating liquid
was replaced with the following light-blocking layer coating liquid.
-Preparation of Light-Blocking Layer Coating Liquid-
[0332] A light-blocking layer coating liquid was prepared by blending 2.5 parts by mass
of a 50% by mass acryl polyol resin solution (LR327, manufactured by Mitsubishi Rayon
Co., Ltd.), 2.7 parts by mass of an azo-compound ((LIBERA COLOR TXL-200 YELLOW, manufactured
by Cashew Co., Ltd.) serving as the compound that absorbed, reflected, or scattered
light in a wavelength range of 500 nm or shorter, 0.6 parts by mass of hydrophobic
silica (RX-200, manufactured by Nippon Aerosil Co., Ltd.), 1.2 parts by mass of an
isocyanate compound (Coronate HL, manufactured by Tosoh Corporation), and 10.0 parts
by mass of methyl ethyl ketone, and sufficiently stirring the mixture.
[0333] The produced thermoreversible recording medium of Comparative Example 10 was measured
by the spectrophotometer (U-4100, manufactured by Hitachi High-Technologies Corporation)
in the same manner as in Example 1. As a result, the average transmittance of the
light-blocking layer of Comparative Example 10 to light in a wavelength range of 300
nm to 400 nm was 18.1%, the average transmittance thereof to light in a wavelength
range of 380 nm to 495 nm was 7.2%, and the transmittance thereof to light having
a wavelength of 470 nm was 6.6%. A graph depicting a relationship between the wavelength
and the transmittance of the light-blocking layer of Comparative Example 10 is presented
in FIG. 15.
[0334] A laser recording evaluation and evaluation of absorbance changes by light irradiation
were performed on each of the thermoreversible recording media of Examples 1 to 15
and Comparative Examples 1 to 10 in the following manners. The results are presented
in Table 1.
<Laser Recording Evaluation>
[0335] As for a laser device, Ricoh Rewritable Laser Marker (LDM200-110, manufactured by
Ricoh Company Limited, center wavelength: 980 nm) was used. A solid image was recorded
on each of the thermosensitive recording medium produced in Examples 1 to 5 and Comparative
Examples 1 to 10 with adjusting the irradiation distance to 150 mm, and the scanning
speed to 2,000 mm/s. During the recording, the output of the laser was 13.5 W in Example
2 and Comparative Example 2, and was 11.0 W in other Examples and Comparative Examples.
[0336] As for erasion of the image, Ricoh Rewritable Laser Eraser (LDE800-A, manufactured
by Ricoh Company Limited, center wavelength: 976 nm) was used. Laser light was applied
to each of the recording media, to which the solid image had been recorded, with adjusting
the irradiation distance to 110 mm, the beam short width to 1.1 mm, and the scanning
speed to 45 mm/s, to thereby erase the image. During the erasing, the effective output
of the laser on the thermosensitive recording medium was 36.0 W in Example 2 and Comparative
Example 2, and was 30.0 W in other Examples and Comparative Examples.
<Evaluation of Absorbance Change by Light Irradiation>
[0337] At first, an initial state of each of thermosensitive recording media of Examples
1 to 15 and Comparative Examples 1 to 10 was subjected to the measurement of the absorbance
of light having a wavelength of 980 nm by means of a spectrophotometer (U-4100, manufactured
by Hitachi High-Technologies Corporation), followed by recording an image thereon
under the aforementioned laser recording conditions.
[0338] Subsequently, the thermosensitive recording medium was irradiated with light by means
of a solar simulator (manufactured by SERUC., Ltd.) for 14 days at 30°C, 80%RH, with
80 klx. Therefore, the absorbance of the thermosensitive recording medium to light
having a wavelength of 980 nm was measured by the spectrophotometer in the same manner
as described above. Moreover, the thermosensitive recording medium was left to stand
for 24 hours at 22°C, 50%RH. Therefore, the absorbance of the thermosensitive recording
medium to light having a wavelength of 980 nm was measured by the spectrophotometer
in the same manner as described above. The results of the absorbance as measured were
compared to the absorbance of the thermosensitive recording medium of the initial
state to light having a wavelength of 980 nm. The results are presented in Table 1.
Note that, the evaluation performed with simulated solar light here is a mandatory
test, the properties required for a thermosensitive recording medium in the market
are corresponded to exposure to light under the conditions of the present evaluation.
[0339] Next, after each of the thermosensitive recording media of Examples 1 to 15 and Comparative
Examples 1 to 10 was irradiated with light by means of the solar simulator, followed
by being left to stand for 24 hours, the image thereon was erased under the aforementioned
laser erasing conditions. Then, the density of the erased area, and the density of
the background were measured by means of a reflection densitometer (X-Rite938, manufactured
by X-Rite Inc.), and a difference between the density of the erased area and the density
of the background was determined as an unerased density. The unerased density being
0.040 or less was determined that the image could be erased. The unerased density
being 0.030 or less was determined as that the image was sufficiently erased. The
results are presented in Table 1.
Table 1-1
|
Average transmittance at the wavelength of 300 nm to 400 nm(%) |
Average transmittance at the wavelength of 380 nm to 495 nm(%) |
Transmittance at the wavelength of 470 nm (%) |
Ex. 1 |
1.8 |
15.0 |
17.3 |
Ex. 2 |
1.8 |
15.0 |
17.3 |
Ex. 3 |
1.8 |
15.0 |
17.3 |
Ex. 4 |
0.9 |
8.9 |
10.2 |
Ex. 5 |
0.5 |
3.4 |
3.9 |
Ex. 6 |
0.5 |
3.4 |
3.9 |
Ex. 7 |
0.5 |
3.4 |
3.9 |
Ex. 8 |
0.5 |
3.4 |
3.9 |
Ex. 9 |
1.8 |
15.0 |
17.3 |
Ex. 10 |
0.6 |
4.9 |
7.5 |
Ex. 11 |
0.6 |
4.9 |
7.5 |
Ex. 12 |
0.6 |
4.9 |
7.5 |
Ex. 13 |
0.6 |
4.9 |
7.5 |
Ex. 14 |
0.6 |
4.9 |
7.5 |
Ex. 15 |
4.5 |
14.8 |
25.6 |
Comp. Ex. 1 |
6.0 |
74.8 |
86.5 |
Comp. Ex. 2 |
6.0 |
74.8 |
86.5 |
Comp. Ex. 3 |
6.0 |
74.8 |
86.5 |
Comp. Ex. 4 |
6.0 |
74.8 |
86.5 |
Comp. Ex. 5 |
6.0 |
74.8 |
86.5 |
Comp. Ex. 6 |
16.0 |
21.8 |
39.1 |
Comp. Ex. 7 |
3.4 |
34.9 |
40.9 |
Comp. Ex. 8 |
22.3 |
11.1 |
10.4 |
Comp. Ex. 9 |
1.8 |
15.0 |
17.3 |
Comp. Ex. 10 |
18.1 |
7.2 |
6.6 |
Table 1-2
|
Absorbance of wavelength 980 nm |
Unerased density after light irradiation |
Initial |
After light irradiation |
After irradiation followed by being left to stand for 24 hours |
Ex. 1 |
0.66 |
0.70 |
0.68 |
0.035 |
Ex. 2 |
0.69 |
0.73 |
0.71 |
0.036 |
Ex. 3 |
0.67 |
0.70 |
0.69 |
0.010 |
Ex. 4 |
0.67 |
0.69 |
0.69 |
0.006 |
Ex. 5 |
0.67 |
0.68 |
0.68 |
0.005 |
Ex. 6 |
0.68 |
0.68 |
0.68 |
0.009 |
Ex. 7 |
0.65 |
0.70 |
0.70 |
0.020 |
Ex. 8 |
0.60 |
0.71 |
0.70 |
0.025 |
Ex. 9 |
0.68 |
0.69 |
0.69 |
0.004 |
Ex. 10 |
0.67 |
0.68 |
0.68 |
0.005 |
Ex. 11 |
0.68 |
0.69 |
0.69 |
0.006 |
Ex. 12 |
0.68 |
0.68 |
0.68 |
0.002 |
Ex. 13 |
0.67 |
0.68 |
0.68 |
0.005 |
Ex. 14 |
0.69 |
0.69 |
0.69 |
0.002 |
Ex. 15 |
0.67 |
0.69 |
0.69 |
0.009 |
Comp. Ex. 1 |
0.66 |
0.81 |
0.68 |
0.034 |
Comp. Ex. 2 |
0.67 |
0.82 |
0.69 |
0.031 |
Comp. Ex. 3 |
0.68 |
0.80 |
0.80 |
0.010 |
Comp. Ex. 4 |
0.65 |
0.85 |
0.85 |
0.018 |
Comp. Ex. 5 |
0.62 |
1.01 |
1.00 |
0.020 |
Comp. Ex. 6 |
0.66 |
0.75 |
0.74 |
0.133 |
Comp. Ex. 7 |
0.67 |
0.77 |
0.77 |
0.011 |
Comp. Ex. 8 |
0.68 |
0.78 |
0.77 |
0.155 |
Comp. Ex. 9 |
0.67 |
0.68 |
0.67 |
0.245 |
Comp. Ex. 10 |
0.66 |
0.67 |
0.67 |
0.323 |
[0340] It was found from the results of Table 1 that an increase in the absorbance of light
having a wavelength of 980 nm after light irradiation, which was due to an increased
in the absorbance of the metal oxide, was suppressed in Examples 1 to 15, as the thermosensitive
recording media thereof each use the light-blocking layer with which the average transmittance
to light in the wavelength range of 300 nm to 400 nm was 5% or less, and the average
transmittance to light in the wavelength range of 380 nm to 495 nm was 20% or less.
As the light-blocking layer, whose average transmittance to light in the wavelength
range of 380 nm to 495 nm was 10% or less was used in Examples 4 to 8 and 10 to 14,
moreover, an increase in the absorbance of light having the wavelength of 980 nm was
prevented even after light irradiation. Especially in Examples 5 to 6 and 10 to 14,
the tungsten oxide compound was used as the metal oxide having absorbance in the near
infrared region, and the light-blocking layer whose transmittance to light having
a wavelength of 470 nm was 10% or less was used, the absorbance at the wavelength
of 980 nm hardly changed after light irradiation. Furthermore, as oxygen was sufficiently
blocked in Examples 3 to 15, the unerased density after light irradiation was low,
and the image could be sufficiently erased.
[0341] On the other hand, in Comparative Examples 1 to 5, the absorbance at the wavelength
of 980 nm was significantly increased after light irradiation, as the thermosensitive
recording media of Comparative Examples 1 to 5 did not contain the compound that absorbed,
reflected, or scattered light in the wavelength range of 500 nm or shorter. If the
absorbance of laser light having a wavelength of 980 nm is increased in the aforementioned
manner, an image printing quality of a bar code is degraded as in the following evaluations
of Comparative Examples 1 to 3.
[0342] Moreover, oxygen could be sufficiently blocked in Comparative Examples 3 to 5, and
therefore the increased absorbance at the wavelength of 980 nm stayed the same even
after leaving to stand for 24 hours after light irradiation.
[0343] Since light in the wavelength range of 500 nm or shorter was insufficiently blocked
in Comparative Examples 6 to 8, the absorbance at the wavelength of 980 nm was largely
increased after light irradiation. Especially in Comparative Examples 6 and 8, the
unerased density after light irradiation was large, as the average transmittance to
light in the wavelength range of 300 nm to 400 nm was significantly greater than 5%.
Moreover, light in the wavelength range of 380 nm to 495 nm was sufficiently blocked
in Comparative Example 10, but the unerased density after light irradiation was significantly
large, as the average tranmittance to light in the wavelength range of 300 nm to 400
nm was significantly greater than 5%.
[0344] As an oxygen barrier layer was not provided to the thermosensitive recording medium
of Comparative Example 9, moreover, the absorbance at the wavelength of 980 nm hardly
changed after light irradiation, as oxygen was supplied. However, the unerased density
after light irradiation was significantly large, as oxygen could not be blocked.
<Evaluation of Image Printing Quality of Bar code>
[0345] A bar code was recorded on an initial state of each of the thermosensitive recording
media of Examples 1 to 2, and 5, and Comparative Examples 1 to 3 under the aforementioned
laser recording conditions. As for the evaluation of the image printing quality of
the bar code, the bar code image was read by a one-dimensional bar code reader (WEBSCANTruCheck
401-RL, manufactured by WEBSCAN) to thereby measure a grade of the bar code. As a
result, the bar codes recorded on the thermosensitive recording media of Examples
1 to 2, and 5, and Comparative Examples 1 to 3 were all grade C. Note that, as for
the grade of the bar code, the grade D or better is typically regarded as readable
by a bar code reader. When the grade is F, it is determined it cannot be read by a
bar code reader.
[0346] Subsequently, each of the thermosensitive recording media of Examples 1, 2, and 5,
and Comparative Examples 1 to 3 was irradiated with light by means of a solar simulator
manufactured by SERUC., Ltd. for 14 days at 30°C, 80%RH, with 80 klx. Thereafter,
a bar code was recorded on each of the thermosensitive recording media of Examples
1, 2, and 5 and Comparative Examples 1 to 3, which had been irradiated with light,
under the aforementioned laser recording conditions. As for the evaluation of the
image printing quality of the bar code, the bar code image was read by a one-dimensional
bar code reader (WEBSCANTruCheck 401-RL, manufactured by WEBSCAN) to thereby measure
a grade of the bar code. As a result, the bar codes recorded on the thermosensitive
recording media of Examples 1 to 2, and 5 were grade C. This is because the absorbed
quantity of laser light did not change, as the absorbance at the wavelength of 980
nm hardly changed, and as a result, the thermosensitive recording medium was not excessively
heated, and a writing line width did not change. On the other hand, the bar codes
recorded on the thermosensitive recording media of Comparative Examples 1 to 3 were
grade F, and the bar codes could not be read. This is because the absorbed quantity
of laser light increased due to the increase in the absorbance at the wavelength of
980 nm to excessively heat the thermosensitive recording medium, and thus the writing
line width widened, and the bar code readability was degraded. Furthermore, a bar
code was recorded on each of the thermosensitive recording media of Comparative Examples
1 to 3, which had been left to stand for 24 hours after the light irradiation, under
the aforementioned laser recording conditions. In Comparative Examples 1 to 2, the
increased absorbance at the wavelength of 980 nm as returned back, as therefore the
thermosensitive recording medium was not excessively heated, and the grade of the
bar code was grade C as measured by the one-dimensional bar code reader. In Comparative
Example 3, the increased absorbance at the wavelength of 980 nm stayed the same even
after being left for 24 hours after the light irradiation, and thus the grade of the
bar code was still grade F, and the bar code could not be read. Note that, Examples
1, 2, and 5, and Comparative Examples 1 to 3 in the evaluation of the image printing
quality of the bar code are corresponded to Examples and Comparative Examples applied
for a write-only thermosensitive recording medium.
[0347] The thermosensitive recording medium of the present invention contains: a layer containing,
as a photothermal converting material, metal oxide having absorbance in the near infrared
region; an oxygen barrier layer; and a light-blocking layer, with which the average
transmittance to light in a wavelength range of 300 nm to 400 nm is 5% or less, and
the average transmittance to light in a wavelength range of 380 nm to 495 nm is 20%
or less, and therefore, a high-contrast image can be repeatedly recorded and erased
in a non-contact manner with the thermosensitive recording medium being attached to
a container, such as a cardboard box, and a plastic container, and changes in the
image recording sensitivity and image erasing sensitivity over time can be prevented
even when the thermosensitive recording medium is left outside and irradiated with
light, such as sun light, for a long period. Accordingly, the thermosensitive recording
medium of the present invention is particularly suitably used for a physical distribution
or delivery system.
[0348] The embodiments of the present invention are, for example, as follows:
- <1> A thermosensitive recording medium, including:
a support;
an image recording layer, which is provided on the support, and contains a leuco dye,
a color developer, and a metal oxide having absorbance in the near infrared region;
an oxygen barrier layer; and
a light-blocking layer,
wherein the oxygen barrier layer and the light-blocking layer are provided a surface
of the image recording layer, which is an opposite side to a surface thereof where
the support is provide, and
wherein an average transmittance of the light-blocking layer to light in a wavelength
range of 300 nm to 400 nm is 5% or less, and an average transmittance of the light-blocking
layer to light in a wavelength range of 380 nm to 495 nm is 20% or less.
- <2> A thermosensitive recording medium, containing:
a support;
an image recording layer containing a leuco dye and a color developer;
a photothermal conversion layer containing a metal oxide having absorbance in the
near infrared region;
an oxygen barrier layer; and
a light-blocking layer,
wherein the image recording layer and the photothermal conversion layer are provided
on the support, and the oxygen barrier layer and the light-blocking layer are provided
on a surface of the image recording layer or the photothermal conversion layer, which
is an opposite side to a surface thereof where the support is provided, and
wherein an average transmittance of the light-blocking layer to light in a wavelength
range of 300 nm to 400 nm is 5% or less, and an average transmittance of the light-blocking
layer to light in a wavelength range of 380 nm to 495 nm is 20% or less.
- <3> The thermosensitive recording medium according <1> or <2>, wherein the average
transmittance of the light-blocking layer to light in a wavelength range of 380 nm
to 495 nm is 10% or less.
- <4> The thermosensitive recording medium according to any one of <1> to <3>, wherein
a transmittance of the light-blocking layer to light having a wavelength of 470 nm
is 10% or less.
- <5> The thermosensitive recording medium according to any one of <1> to <4>, wherein
the light-blocking layer contains an ultraviolet ray-blocking layer and a blue light-blocking
layer.
- <6> The thermosensitive recording medium according to any one of <1> to <5>, wherein
the metal oxide having absorbance in the near infrared region is a tungsten oxide
compound, indium-doped tin oxide, or antimony-doped tin oxide, or any combination
thereof.
- <7> The thermosensitive recording medium according to any one of <1> to <6>, wherein
the metal oxide having absorbance in the near infrared region is a tungsten oxide
compound.
- <8> The thermosensitive recording medium according to any one of <1> to <7>, wherein
the oxygen barrier layer is composed of a first oxygen barrier layer and a second
oxygen barrier layer, and wherein the first oxygen barrier layer is provided on a
surface of the image recording layer or the photothermal conversion layer, which is
an opposite side to a surface thereof where the support is provided, and the second
oxygen barrier layer is provided between the image recording layer and the support,
or on a surface of the support, which is an opposite side to a surface thereof where
the image recording layer is provided, or both therebetween and thereon.
- <9> An image processing method, containing:
irradiating the thermosensitive recording medium according to any one of <1> to <8>
with light to perform image recording, or image erasing, or both.
- <10> The image processing method according to <9>, wherein light with which the thermosensitive
recording medium is irradiated is near infrared laser light in a wavelength range
of 700 nm to 2,000 nm.