TECHNICAL FIELD
[0001] The present invention relates to tissue papers for household use such as tissue papers
including toilet tissue papers, facial tissues, etc., and paper towels and more specifically
it relates to soft and pleasant-to-touch tissue papers for household use with high
strength.
BACKGROUND ART
[0002] Slushed pulp in a slurry state as prepared from chemical pulp obtained by cooking
hardwood or softwood chips, dry pulp obtained by dewatering and drying this slushed
pulp, or deinked recycled pulp obtained by deinking waste paper has been conventionally
used for so-called tissue papers for household use such as toilet tissue papers, tissue
papers including facial tissues, paper towels, etc., and these pulps are used as unbleached
or bleached pulps or unbeaten or beaten pulps alone or in combination depending on
the quality design.
[0003] Techniques for improving softness or hand feeling as an important quality of tissue
papers have been previously studied, and various proposals have been made, including
e.g., layered tissue papers in which the types or the proportions of the pulps layered
and converted into paper are controlled and processes for preparing them (patent document
1, patent document 2); methods for improving hand feeling and softness by appropriately
selecting paper machines such as Fourdrinier machines, paper machines having a short
forming section, twin-wire machines, cylinder machines with a Yankee dryer, etc.,
or by adding auxiliary chemicals to slushed pulp to improve the lubricity of the slushed
pulp per se, such as paper softeners, e.g., fatty acid ester-based softeners (patent
document 3), quaternary ammonium salt-based cationic surfactants (patent document
4), urethane alcohols or salts or cationized products thereof (patent document 5),
non-cationic surfactants (patent document 6, patent document 7), polyphosphates (patent
document 8), polysiloxanes (patent document 9, patent document 10), etc., or by once
concentrating and then mechanically kneading pulp to bend fibers (patent document
11, patent document 12).
[0004] The use of the auxiliary chemicals sometimes produced good softening effects, but
had the disadvantage that their high foamability might disturb the paper-making operation
per se and in some cases invite a decrease in paper strength and water absorbency.
The mechanical processes for bending fibers were disadvantageous in energy consumption
because of additional steps of concentrating raw materials.
[0005] In order to improve the wet strength of tissue papers, wet paper strength agents
such as polyamides, polyamines and epoxy resins are mainly used, but they had negative
effects on softness and hand feeling because they rigidify the tissue papers per se.
[0006] In order to improve surface smoothness, one or two calender sets consisting of a
pair of an upper and a lower sufficiently polished chilled rolls and metal rolls have
been conventionally used downstream of tissue paper making machines. However, this
calender caused problems such as decreased thickness, increased rigidity and hard
texture when the nip pressure was increased to improve smoothness.
References:
DISCLOSURE OF THE INVENTION
PROBLEMS TO BE SOLVED BY THE INVENTION
[0008] The present invention aims to provide soft and pleasant-to-touch tissue papers for
household use with high strength.
MEANS FOR SOLVING THE PROBLEMS
[0009] As a result of careful studies, we achieved the present invention on the basis of
the finding that soft and pleasant-to-touch tissue papers for household use with high
strength can be attained by including a pulp obtained by applying an impact force
provided during the collapse of bubbles generated by cavitation to pulp fibres in
an outer layer of the tissue paper, and said pulp fibers and outer layer are as defined
in Claim 1.
ADVANTAGES OF THE INVENTION
[0010] The present invention makes it possible to attain soft and pleasant-to-touch tissue
papers for household use with high strength.
BRIEF DESCRIPTION OF THE DRAWING
[0011] Figure 1 is a schematic diagram showing the cavitation jet treatment system used
in the examples.
EXPLANATION OF THE REFERENCE NUMERALS
[0012]
- 1:
- sample tank
- 2:
- nozzle
- 3:
- cavitation jet cell
- 4:
- plunger pump
- 5:
- upstream pressure regulating valve
- 6:
- downstream pressure regulating valve
- 7:
- upstream pressure meter
- 8:
- downstream pressure meter
- 9:
- water feed valve
- 10:
- circulating valve
- 11:
- drain valve
- 12:
- temperature sensor
- 13:
- mixer.
THE MOST PREFERRED EMBODIMENTS OF THE INVENTION
[0013] The tissue papers for household use of the present invention are characterized in
that they consist of two or more paper layers, wherein the outer layer of the paper
layers contains a pulp obtained by applying an impact force produced during the collapse
of bubbles generated by cavitation to pulp fibers. The application of an impact force
produced during the collapse of bubbles generated by cavitation to pulp will be hereinafter
referred to as cavitation treatment. In particular, the outer layer of the tissue
paper has been dried using a Yankee dryer and said pulp fibers have scale-like external
fibrils or hairs on the surface of the fiber having a width of 3µm or more, and consisting
of a wide layer formed of an assembly of microfibrils aligned side by side.
[0014] Pulps that can be used as targets for the cavitation treatment of the present invention
are not specifically limited, but include chemical pulps obtained by cooking a lignocelluloses
material with an alkaline cooking liquor (such as bleached kraft pulp (NBKP) or unbleached
kraft pulp (NUKP) of softwoods, bleached kraft pulp of hardwoods (LBKP)), mechanical
pulps (such as groundwood pulp (GP), refiner groundwood pulp (RGP), thermomechanical
pulp (TMP), chemithermomechanical pulp (CTMP), etc.), deinked pulp (DIP), etc. Chemical
pulps that can be used include kraft pulp, polysulfide pulp, soda pulp, alkaline sulphite
pulp, sodium carbonate pulp, and oxygen-soda pulp, etc.
[0015] The chemical pulps may also include those obtained by adding a cyclic keto compound
(e.g., anthraquinone, 1-4-dihydro-9, 10-diketoanthracene, etc.) to the cooking liquor.
Among the chemical pulps, kraft pulp is preferred for the present invention, which
may be obtained by the so-called modified alkaline cooking process comprising adding
the cooking liquor in portions and concurrent cooking and countercurrent cooking within
a digester. These chemical pulps can be used as unbleached or bleached pulps or unbeaten
or beaten pulps alone or in combination, as appropriate.
[0016] The cavitation treatment is more specifically defined as a process for promoting
external fibrillation of pulp by applying an impact force produced during the collapse
of bubbles generated by cavitation to pulp fibers while suppressing internal fibrillation
to adjust freeness. The cavitation treatment is preferably a cavitation jet treatment
as described in
WO2005/012632.
[0017] It should be noted that pulp fibers can also be externally fibrillated by combining
the cavitation treatment with mechanical beating. The pulp suspension may contain
inorganic fine particles from fillers or pigments contained in waste paper or broke
in addition to pulp fibers. The cavitation treatment affords a bulkier and stronger
pulp as compared with those conventionally obtained by beating with a mechanical force
using a refiner or the like at the same freeness because external fibrillation of
pulp fibers is promoted while internal fibrillation is suppressed. Tissue papers for
household use containing a pulp having external fibrils obtained by this cavitation
treatment are softer and stronger.
[0018] The Canadian Standard Freeness of the pulp prepared by the cavitation treatment is
preferably 50-650 ml in the case of chemical pulps and 50-400 ml in the case of mechanical
pulps or recycled (deinked) pulp. In the case of mixtures of these pulps, the total
Canadian Standard Freeness is preferably 100-550 ml.
[0019] Next, the cavitation treatment is explained in detail. When cavitation bubbles collapse,
a high impact force reaching several Giga Pascal is produced in a local region on
the order of several micrometers and the temperature microscopically rises to several
thousand degrees Celsius due to adiabatic compression during the collapse of bubbles,
as described in a book of
Katoh (New Edition Cavitation: Basics and Recent Advance, Written and Edited by Yoji
Katoh, Published by Makishoten, 1999). As a result, the temperature rises when cavitation occurs. For these reasons, cavitation
has harmful influences on fluid machinery such as damage, oscillation and performance
loss and it has been a technical challenge to control cavitation. Recently, rapid
advances in studies on cavitation made it possible to precisely control the region
in which cavitation occurs and even the impact force by using hydrodynamic parameters
of cavitation jet as operation factors. This led to expectations that the strong energy
of bubbles could be effectively utilized by controlling the impact force induced by
collapse of bubbles. Thus, it became possible to precisely control cavitation by operation/adjustment
based on hydrodynamic parameters. This shows that the stability of technical effects
can be maintained, and the present invention is characterized in that bubbles generated
by controlled cavitation are actively introduced into a pulp suspension to effectively
utilize their energy rather than the conventional uncontrollably harmful cavitation
spontaneously occurring in fluid machinery.
[0020] Means for generating cavitation in the present invention include, but not limited
to, a liquid jet, an ultrasonic transducer, a combination of an ultrasonic transducer
and a horn amplifier, and laser irradiation. It is preferable to use a liquid jet,
which is more effective for pulp fibers because it efficiently generates cavitation
bubbles and forms cavitation bubble clouds having a stronger impact force of collapse.
The cavitation generated by the means described above is clearly different from the
conventional uncontrollably harmful cavitation spontaneously occurring in fluid machinery.
[0021] As noted above, the cavitation treatment is preferably a cavitation jet treatment
using a liquid jet as described in
WO2005/012632 and as will be explained in detail below.
[0022] The liquid jet refers to a jet of a liquid or a fluid containing solid particles
or a gas dispersed or mixed in a liquid, including a liquid jet containing a slurry
of pulp or inorganic particles and bubbles. The gas here may include bubbles generated
by cavitation.
[0023] Flow rates and pressures are especially important for cavitation because it occurs
when a liquid is accelerated and a local pressure decreases below the vapor pressure
of the liquid. Therefore, the cavitation number σ, which is a basic dimensionless
number expressing a cavitation state, is defined as follows (
New Edition Cavitation: Basics and Recent Advance, Written and Edited by Yoji Katoh,
Published by Makishoten, 1999).
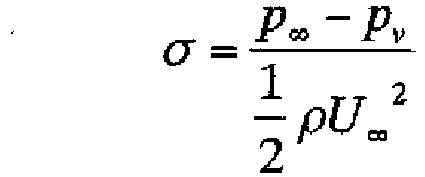
where
p∞: local pressure (absolute pressure),
U∞: characteristic flow velocity,
pv: vapor pressure of fluid (absolute pressure),
ρ: density.
[0024] If the cavitation number here is high, it means that the flow site is in a state
where cavitation occurs hard. Especially when cavitation is generated through a nozzle
or an orifice tube as in the case of a cavitation jet, the cavitation number σ can
be rewritten by equation (2) below where
p1: nozzle upstream pressure (absolute pressure),
p2: nozzle downstream pressure (absolute pressure),
pv: vapor pressure of fluid (absolute pressure), and the cavitation number σ can be
approximated as follows in the case of a cavitation jet because the pressure difference
between
p1,
p2 and
pv is significant so that
p1>>
p2>>pv (
H. Soyama, J. Soc. Mat. Sci. Japan, 47 (4), 381 1998).

[0025] In this manner, the cavitation number σ is expressed by two values, i.e., the pressures
upstream and downstream of the nozzle. It should be noted that all of the pressures
measured in the examples herein are gauge pressures, and the cavitation number σ in
the present invention is expressed by equation (3) below:

where p
3: nozzle upstream pressure (gauge pressure), p
4: nozzle downstream pressure (gauge pressure).
[0026] Cavitation conditions in the present invention are as follow: the cavitation number
σ defined above is desirably 0.001 or more and 0.5 or less, preferably 0.003 or more
and 0.2 or less, especially 0.01 or more and 0.1 or less. If the cavitation number
σ is less than 0.001, little benefit is attained because the pressure difference against
the surroundings is small when cavitation bubbles collapse, but if it is greater than
0.5, the pressure difference in the flow is too small to generate cavitation.
[0027] When a jetting liquid is emitted through a nozzle or an orifice tube to generate
cavitation, the pressure of the jetting liquid (nozzle upstream pressure) is desirably
0.01 MPa (gauge pressure) or more and 60 MPa (gauge pressure) or less, preferably
0.7 MPa (gauge pressure) or more and 30 MPa (gauge pressure) or less, especially 2
MPa (gauge pressure) or more and 15 MPa (gauge pressure) or less. If the nozzle upstream
pressure is less than 0.01 MPa (gauge pressure), little benefit is attained because
a pressure difference is less likely occur against the nozzle downstream pressure.
If the nozzle upstream pressure is greater than 60 MPa (gauge pressure), special pumps
and pressure vessels are required and energy consumption increases, leading to cost
disadvantages, but also pulp fibers are excessively damaged so that they become unsuitable
for use as raw materials for papermaking. On the other hand, the pressure in the vessel
(nozzle downstream pressure) is preferably 0.05 MPa (gauge pressure) or more and 2.6
MPa (gauge pressure) or less expressed in static pressure. A pressure is also applied
on the downstream side to increase the pressure in the region where cavitation bubbles
collapse by pressurizing the vessel containing a target liquid (pulp suspension),
resulting in an increase in the pressure difference between bubbles and the surroundings,
whereby bubbles more vigorously collapse to produce a stronger impact force. However,
cavitation per se hardly occurs if the pressure in the vessel excessively increases.
The ratio between the pressure in the vessel and the pressure of the jetting liquid
((gauge pressure)/ (gauge pressure)) is preferably in the range of 0.001-0.5.
[0028] The jet flow rate of the jetting liquid is desirably in the range of 1 m/sec or more
and 200 m/sec or less, preferably in the range of 20 m/sec or more and 100 m/sec or
less. If the jet flow rate is less than 1 m/sec, little benefit is attained because
the pressure drop is too small to generate cavitation. If it is greater than 200 m/sec,
however, cost disadvantages occur because high pressure is required and therefore,
a special equipment is required.
[0029] The cavitation treatment in the present invention takes place at a site that can
be selected from, but not limited to, the inside of any vessel such as a tank or the
inside of a pipe. The treatment can be performed in one pass, but a greater effect
can be obtained by repeating a necessary number of cycles. The treatment can be performed
in parallel or in series using multiple generating means.
[0030] A jet for generating cavitation may be injected into a vessel open to the atmosphere
such as a pulper, but preferably within a pressure vessel to control cavitation.
[0031] In the method for generating cavitation by a liquid jet in the present invention,
liquids that can be jetted to a pulp suspension include, but not limited to, e.g.,
distilled water, tap water, industrial water, recycled water recovered from papermaking
processes, pulp drain water, white water, pulp suspensions, alcohols, etc. Preferably,
a pulp suspension per se is jetted to provide a greater benefit because not only cavitation
is generated around the jet but also a hydrodynamic shear force is obtained when the
jet is emitted from an orifice at a high pressure. When a pulp suspension is used
as a jet liquid, the total amount to be treated can be circulated.
[0032] When a pulp suspension is treated by cavitation generated by a liquid jet, the solids
content of the suspension is preferably 5 % by weight or less, more preferably 3 %
by weight or less, still more preferably 0.1-1.5 % by weight in terms of the bubble
generating efficiency..
[0033] The pH of the pulp suspension is preferably pH 1-13, more preferably pH 3-12, still
more preferably pH 4-11. If the pH is less than 1, problems such as corrosion of equipments
occur, which are disadvantageous in terms of materials and maintenance or the like.
If the pH exceeds 13, however, alkaline discoloration of pulp fibers occurs to unfavorably
lower brightness. Alkaline conditions are more desirable because pulp fibers are highly
swollen and more OH active radicals are produced.
[0034] According to the present invention, the flow rate of the jetting liquid increases
by increasing the jetting pressure of the liquid to generate stronger cavitation.
Moreover, the vessel containing a target liquid is pressurized to increase the pressure
in the region where cavitation bubbles collapse, resulting in an increase in the pressure
difference between bubbles and the surroundings, whereby bubbles vigorously collapse
to produce a stronger impact force. Here, the jetting liquid refers to a liquid emitted
from an orifice at a high pressure, and the target liquid refers to a liquid exposed
to a jet within a vessel or a pipe. Cavitation is influenced by the amount of gas
in the liquid, and if the gas is excessive, bubbles collide with each other and join
together to create a cushioning effect so that the impact force of collapse is absorbed
by other bubbles and the impact force decreases. Thus, the process temperature must
be the melting point or more and the boiling point or less in view of the influence
of dissolved gas and vapor pressure. When the liquid medium is water, significant
effects can be obtained at a temperature of preferably 0-80°C, more preferably 10°C
- 60°C. Considering that the impact force is normally maximal at the midpoint between
the melting point and the boiling point, temperatures around 50°C are most preferred
in the case of aqueous solutions, though significant effects can be obtained even
at lower temperatures within the range defined above because there is no influence
of vapor pressure. Temperatures exceeding 80°C are unsuitable because the pressure
resistance of the pressure vessel for generating cavitation considerably decreases
so that the vessel may be liable to damages.
[0035] According to the present invention, the energy required for generating cavitation
can be reduced by adding a material that lowers the surface tension of a liquid, such
as a surfactant. Materials that are added include, but not limited to, known or novel
surfactants, e.g., nonionic sufactants, anionic surfactants, cationic surfactants
e.g., nonionic sufactants, anionic surfactants , cationic surfactants and ampholytic
surfactants such as fatty acid salts, higher alkyl sulfates, alkyl benzene sulfonates,
higher alcohols, alkyl phenols, alky phenols, alkylene oxide adducts of fatty acids
or the like, or organic solvents, etc. These may be added as single components or
mixtures of two or more components. They may be added in any amount necessary for
lowering the surface tension of the jetting liquid and/or target liquid. They may
be added at any site in a process preceding the site where cavitation is generated,
and when the liquid is circulated, they may be added even after the site where cavitation
is generated.
[0036] According to the present invention, the proportion of the cavitation-treated pulp
to the total amount of pulp is not specifically limited, but stronger and softer tissue
papers for household use can be obtained as the proportion increases. From this point
of view, the proportion is preferably 5 % by weight or more, more preferably 30 to
100 % by weight, still more preferably 60 to 100 % by weight based on the bone dry
weight of the total pulp. If the proportion is less than 5 % by weight, the softness
and hand feeling remain unchanged and the strength cannot be improved.
[0037] The tissue papers for household use consist of multiple layers, and the multiple
layers may be prepared from a single cavitation-treated pulp or a mixture of two or
more cavitation-treated pulp and a conventional slushed pulp, dry pulp or deinked
pulp (DIP).
[0038] When two plies of a tissue paper for household use consisting of multiple layers
are layered, hand feeling is further improved when the layer containing the cavitation-treated
pulp faces outward so that the layer containing a cavitation-treated pulp contacts
hands. Hand feeling is further improved by drying the layer containing a cavitation-treated
pulp against a Yankee dryer and placing this face on the outside of two plies of a
tissue paper for household use in accordance with the present invention.
[0039] In addition to the cavitation-treated pulp, chemical pulps (bleached kraft pulp (NBKP)
or unbleached kraft pulp (NUKP) of softwoods, bleached draft pulp (LBKP) or unbleached
kraft pulp (LUKP) of hardwoods, etc.), mechanical pulps (groundwood pulp (GP), refiner
groundwood pulp (RGP), thermomechanical pulp (TMP), chemithermomechanical pulp (CTMP),
etc.), and deinked pulp (DIP) may be used as a mixture at any ratio.
[0040] The cavitation-treated pulp shows improved external fibrillation, and, in accordance
with the present invention, has scale-like external fibrils, as explained below.
[0041] According to a book of Isogai et al. (
Akira Isogai: "Materials Chemistry of Cellulose", The University of Tokyo Press, p.
68, 2001), beating of pulp refers to a process in which a mechanical shear stress is applied
to hydrated pulp fibers to form gaps between microfibrils within the pulp fibers (internal
fibrillation) and to raise fibrils on the outer sides of the pulp fibers (external
fibrillation), thereby increasing the specific surface area to improve swelling of
the pulp fibers with water, and at the same time, partially cutting the fibers and
generating fine fibers flaked off the outer peripheral faces of the fibers.
[0042] The beating process of pulp increases the bonding area between fibers formed during
papermaking, thereby causing changes in various mechanical properties, optical properties
and liquid absorption. However, when pulp fibers are observed at the molecular level,
the molecular weight of cellulose decreases only slightly and the crystallinity is
almost unchanged during the beating process. This is attributed to the fact that amorphous
and hydrophilic hemicellulose moieties serve as a cushion to absorb mechanical energy.
[0043] According to a book of Shimaji et al. (
Ken Shimaji et al.: "Wood Tissue", Morikita Publishing, p. 55, 1976). external fibrils seen in wood pulp beaten by conventional methods refer to filamentous
structures having a width of about 0.4 - 1 µm observable by light microscopy, while
microfibrils are elemental structural units present in cell walls as an assembly of
cellulose molecules having a width of about 9 - 37 nm. In the pulps having scale-like
external fibrils used in the present invention, the characteristic scale-like external
fibrils refer to flakes or hairs on the surface of a fiber having a width of 3 µm
or more, preferably similar to the width of the pulp fiber and consisting of a wide
layer formed of an assembly of the microfibrils aligned side by side, i.e., the microfibrils
on the surface of the fiber wall are flaked while retaining a layer structure. They
are also characterized by a thickness ranging from 90 nm to 2 µm. When a fiber is
observed by electron microscopy, it is desirably observed in the dry state eliminating
hydrogen bonding, but it is difficult to observe external fibrils with high precision
because such fibrils would be attracted to the surface of the fiber by capillarity
so that they would be difficult to discern if the fiber was simply dried.
[0044] The scale-like external fibrils in the present invention are characterized in that
they are stained by a high molecular dye having a molecular weight of 10,000 or more.
Thus, the external fibrils refer to an assembly of microfibrils to which a high molecular
dye having a molecular weight of 10,000 or more can be adsorbed. Dyes having a molecular
weight of 10,000 or more include orange dyes such as CI Constitution nos. 40000 to
40006 including Direct Orange 15 (old Color Index (CI) no. 621, or CI Constitution
no. 40002/3) as described in a literature of Simon et al. (
F.L. Simons, Tappi Journal, 33 (7), 312 (1950)) and a literature of Xiaochun et al. (
Y. Xiaochun et al., Tappi Journal, 78 (6), 175 (1995)), but they are not specifically limited so far as they can stain cellulose-based
fibers.
[0045] According to the literature of Xiaochun et al., the dyes having a molecular weight
of 10,000 or more described above are molecules having a hydrodynamic size of 5 nm
or more as measured by light scattering and cannot permeate into pores of less than
5 nm present on the surfaces of pulp fibers. However, the dyes having a molecular
weight of 10,000 or more described above can readily access and selectively stain
fibrillated regions by adsorbing to them because fibrils consisting of an assembly
of microfibrils on the surfaces of pulp fibers are exposed outside the pulp fibers.
[0046] In order to optically highlight fibrillated regions, they can be observed with enhanced
contrast by staining the entire fiber using a low molecular dye such as Direct Blue
1 (old Color Index (CI) no. 518, or CI Constitution no. 24410) or Direct Blue 4, Direct
Blue 15, Direct Blue 22, Direct Blue 151 or the like as described in the literatures
above. The low molecular dye is adsorbed to the entire fiber, but displaced by a high
molecular dye having a higher bonding force. As a result, the fibrillated regions
to which the high molecular dye (orange dye) can be adsorbed can be stained in orange
while fiber pore regions to which the high molecular dye cannot be adsorbed can be
stained with the low molecular dye (blue dye), whereby the fibrillated regions can
be highlighted. Suitable low-molecular dyes contain 51 % or more of molecules having
a molecular weight of less than 10,000, preferably less than 2000, more preferably
300-1500.
[0047] In a single unit of the pulps having scale-like external fibrils of the present invention,
the area ratio of the externally fibrillated part expressed by equation 4 below is
preferably 20 % or more and the peripheral length index of the externally fibrillated
part expressed by equation 5 below is 1.5 or more. In the pulps of the present invention,
these values increase because the scale-like external fibrils have a greater surface
area as compared with conventional fibrils.
[0048] Area ratio of externally fibrillated part (%) = [(area of externally fibrillated
part) / (area of externally fibrillated part + total surface area of pulp fiber)]
x 100 (equation 4).
[0049] Peripheral length index of externally fibrillated part = (peripheral length of externally
fibrillated part + entire peripheral length of fiber) / (entire peripheral length
of pulp fiber) (equation 5)
MECHANISM
[0050] The reason why tissue papers containing cavitation-treated pulp show good hand feeling
and strength is assumed as follows.
[0051] Generally, tissue papers having a high bulk (low density) and a smooth surface show
improved hand feeling. As noted above, cavitation-treated pulp has been specifically
promoted in external fibrillation. Thus, external fibrillation has been promoted while
retaining fiber rigidity as described in
WO2006/085598, so that the strength increases at a similar bulk or the bulk increases when the
pulp is prepared at a similar strength as compared with conventional mechanical treatments
such as double disc refiners.
[0052] Moreover, papers prepared from cavitation-treated pulp tend to be smoother because
smooth surfaces such as metal rolls are readily transferred.
[0053] For these reasons, tissue papers containing cavitation-treated pulp are assumed to
tend to show good hand feeling and strength at the same time.
EXAMPLES
[0054] The following examples and comparative examples further illustrate the present invention
without, however, limiting the invention thereto. Unless otherwise specified, % in
the examples and comparative examples refers to % by weight. The pulps prepared in
the following examples and comparative examples were converted into papers in a twin-wire
triple layer paper machine with a Yankee dryer. The web was dry-creped by driving
the dryer and the winder reel at different speeds. Unless otherwise specified, two
plies of this raw tissue paper were layered in such a manner that the face having
contacted the Yankee dryer (YD face) might form the outside (i.e., the side contacting
users' hands) and the face dried against the Yankee dryer was soft-calendered. The
pulps used in all of the examples and comparative examples were bleached hardwood
pulps prepared by the kraft process from hardwood chips produced in Japan and bleached
to a Hunter brightness of 84 %.
[0055] The evaluation methods used in the examples and comparative examples are as follows.
<Hand feeling>
[0056] Feel against hands and skin was evaluated by ten panelists. The results were expressed
as follows. ⊚: very good, ○: good, Δ: fair, X: poor.
<Determination method of (longitudinal) tensile strength>
[0057] Tensile strength: Samples of 15 mm in MD and CD directions were cut and the tensile
strength of a single ply in each direction was measured to calculate the total tensile
strength by the equation below.
[0058] Tensile strength (g) = (tensile strength in MD x tensile strength in CD)
1/2.
<Determination method of bulk>
[0059] Bulk was expressed as the thickness (mm) of 10 plies of each sample.
<Determination of basis weight>
[0060] Basis weight was determined according to JIS P 8124: 1998 (ISO 536: 1995).
<Preparation of cavitation-treated pulp>
[0061] Cavitation treatment was performed in the cavitation jet treatment system shown in
Figure 1. In Figure 1, a pulp suspension (consistency 1.1 %) not shown is contained
in a sample tank 1, and a temperature sensor 12 and a mixer 13 are inserted into the
sample tank 1. The pulp suspension in the sample tank 1 is introduced as a jetting
liquid into a cavitation jet cell 3 via a given line provided with a plunger pump
4. A nozzle 2 is provided at the bottom of the cavitation jet cell 3, and more specifically,
the pulp suspension in the sample tank 1 is injected from the nozzle 2 into the jet
cell 3. On a line extending from the periphery of the sample tank 1 to the jet cell
3 are provided a water feed valve 9 and a circulating valve 10, through which the
pulp suspension in the sample tank 1 is supplied as a target liquid into the jet cell
3. On another line extending from the periphery of the sample tank 1 to the nozzle
2 is provided an upstream pressure regulating valve 5. On another line extending from
the top of the jet cell 3 to the sample tank 1 is provided a downstream pressure regulating
valve 6 so that the jetting pressure of the pulp suspension into the nozzle 2 can
be controlled by adjusting each valve 5, 6. An upstream pressure meter 7 is provided
at the inlet of the nozzle 2, and a downstream pressure meter 8 is provided at the
top of the jet cell 3. A drain valve 11 is provided at the bottom of the jet cell
3.
EXAMPLE 1
[0062] The raw material for the top and bottom layers of triple layers was prepared as follows.
A pulp sheet of a bleached hardwood kraft pulp was disintegrated in a low-consistency
pulper and adjusted to a desired consistency, and then treated in one pass by using
the cavitation jet treatment system (nozzle diameter 1.5 mm) shown in Figure 1 at
a jetting liquid pressure (nozzle upstream pressure) of 8 MPa (gauge pressure, jet
flow rate 80 m/sec.) and a pressure in the target vessel (nozzle downstream pressure)
of 0.4 MPa (gauge pressure). A pulp suspension having a consistency of 3 % by weight
was used as a jetting liquid to treat the pulp suspension (consistency 3 % by weight)
in the vessel by cavitation, thus giving raw material A having a Canadian Standard
Freeness of 435 mL. A facial tissue was prepared from raw material A and raw material
B for the middle layer (prepared by disintegrating a pulp sheet of a bleached hardwood
kraft pulp in a low-consistency pulper and having a Canadian Standard Freeness of
500 mL). The basis weight of the resulting facial tissue was adjusted to 16.6 g/m
2.
COMPARATIVE EXAMPLE 1
[0063] The raw material for the top and bottom layers was prepared by beating in a double
disc refiner instead of the cavitation treatment to give raw material C having a Canadian
Standard Freeness of 470 mL. A facial tissue was prepared from raw material C and
raw material B for the middle layer. The basis weight of the resulting facial tissue
was adjusted to 16.6 g/m
2.
Table 1
|
Example 1 |
Comparative example 1 |
Hand feeling |
Δ |
Δ |
Bulk (mm/10 plies) |
0.88 |
0.91 |
Tensile strength (g) |
263 |
214 |
[0064] As shown in Table 1, Example 1 and Comparative example 1 were comparable in hand
feeling, but the tensile strength of Example 1 was higher by about 20 % than that
of Comparative example 1. Example 1 remarkably increased in strength over Comparative
example 1 despite of a slight decrease in bulk.
EXAMPLE 2
[0065] The raw material for the top and bottom layers was prepared by the same treatment
as in Example 1 to give raw material D having a Canadian Standard Freeness of 420
mL. A facial tissue was prepared from raw material D and raw material B for the middle
layer by adding 0.1 % (based on the bone dry weight of the pulp) of a wet paper strength
agent. The basis weight of the resulting facial tissue was adjusted to 13.0 g/m
2.
COMPARATIVE EXAMPLE 2
[0066] The raw material for the top and bottom layers was prepared by the same treatment
as in Comparative Example 1 to give raw material E having a Canadian Standard Freeness
of 410 mL. A facial tissue was prepared from raw material D and raw material B for
the middle layer by adding 0.1 % (based on the bone dry weight of the pulp) of a wet
paper strength agent. The basis weight of the resulting facial tissue was adjusted
to 13.0 g/m
2.
Table 2
|
Example 2 |
Comparative example 2 |
Hand feeling |
⊚ |
○ |
Bulk (mm/10 plies) |
0.78 |
0.73 |
Tensile strength (g) |
155 |
160 |
[0067] As shown in Table 2, Example 2 showed better hand feeling than that of Comparative
example 2 and a nearly comparable tensile strength. Moreover, Example 2 improved in
bulk by about 7 % over Comparative example 2.
EXAMPLE 3
[0068] The raw material for the top and bottom layers was prepared by the same treatment
as in Example 1 except that 2 pass treatment was performed by using the cavitation
jet treatment system (nozzle diameter 1.5 mm) at a jetting liquid pressure (nozzle
upstream pressure) of 8 MPa (gauge pressure, jet flow rate 80 m/sec.) and a pressure
in the target vessel (nozzle downstream pressure) of 0.4 MPa (gauge pressure) to give
raw material F having a Canadian Standard Freeness of 390 mL. A facial tissue was
prepared from raw material F and raw material B for the middle layer by adding 0.1
% (based on the bone dry weight of the pulp) of a wet paper strength agent. The basis
weight of the resulting facial tissue was adjusted to 15.1 g/m
2.
COMPARATIVE EXAMPLE 3
[0069] The raw material for the top and bottom layers was prepared by the same treatment
as in Comparative Example 1 to give raw material G having a Canadian Standard Freeness
of 470 mL. A facial tissue was prepared from raw material G and raw material B for
the middle layer by adding 0.1 % (based on the bone dry weight of the pulp) of a wet
paper strength agent. The basis weight of the resulting facial tissue was adjusted
to 15.1 g/m
2.
Table 3
|
Example 3 |
Comparative example 3 |
Hand feeling |
⊚ |
○ |
Bulk (mm/10 plies) |
0.85 |
0.87 |
Tensile strength (g) |
205 |
174 |
[0070] As shown in Table 3, Example 3 showed better hand feeling and a tensile strength
higher by about 20 % as compared with Comparative example 3. Example 3 remarkably
increased in strength over Comparative example 3 despite of a slight decrease in bulk.
EXAMPLE 4
[0071] The raw material for the top and bottom layers was prepared by the same treatment
as in Example 1 except that a bleached hardwood kraft pulp sheet tending to favor
strength but compromise hand feeling (a pulp sheet having a moisture content of about
50 % by weight (based on the bone dry weight of the pulp)) was used to give raw material
H having a Canadian Standard Freeness of 440 mL. A facial tissue was prepared from
raw material H and raw material B for the middle layer by adding 0.1 % (based on the
bone dry weight of the pulp) of a wet paper strength agent. The basis weight of the
resulting facial tissue was adjusted to 15.1 g/m
2.
COMPARATIVE EXAMPLE 4
[0072] The raw material for the top and bottom layers was prepared by the same treatment
as in Comparative Example 1 except that a bleached hardwood kraft pulp sheet tending
to favor hand feeling (a pulp sheet having a moisture content of about 10 % by weight
(based on the bone dry weight of the pulp)) was used to give raw material I having
a Canadian Standard Freeness of 480 mL. A facial tissue was prepared from raw material
I and raw material B for the middle layer by adding 0.1 % (based on the bone dry weight
of the pulp) of a wet paper strength agent. The basis weight of the resulting facial
tissue was adjusted to 15.1 g/m
2.
Table 4
|
Example 4 |
Comparative example 4 |
Hand feeling |
○ |
○ |
Bulk (mm/10 plies) |
0.79 |
0.84 |
Tensile strength (g) |
247 |
177 |
[0073] As shown in Table 4, Example 4 using a bleached hardwood kraft pulp tending to compromise
hand feeling was comparable in hand feeling as compared with even Comparative example
4 using a bleached hardwood kraft pulp sheet tending to favor hand feeling. Moreover,
Example 4 improved in tensile strength by about 40 % over Comparative example 4.