[0001] Die Erfindung betrifft ein Verfahren zur Passivierung der Oberfläche von verzinnten
Stahlbändern, welche mit einer Bandgeschwindigkeit durch eine Beschichtungsanlage
bewegt werden, durch anodische Oxidation und Nachbehandlung des verzinnten Stahlbandes
mit einem chromfreien Nachbehandlungsmittel. Die Erfindung betrifft ferner die Verwendung
von Mitteln mit komplex gebundenen Übergangsmetallen oder von organischen Additiven,
die normalerweise zum Dispergieren oder zur Verbesserung der Benetzung eingesetzt
werden, als chromfreies Nachbehandlungsmittel bei der Herstellung von verzinnten Stahlbändern.
Gegenstand der Erfindung ist ferner ein verzinntes Stahlband oder -blech mit einer
Trägerschicht aus einem Fein- oder Feinstblech aus Stahl und einer darauf abgeschiedenen
Zinnschicht und einer Oberflächenschicht eines chromfreien Nachbehandlungsmittels.
[0002] Weißblech ist ein vielseitig einsetzbarer, ökonomisch und ökologisch vorteilhafter
Werkstoff, der vor allem in der Verpackungsindustrie zum Einsatz kommt. Weißblech
ist kaltgewalztes Stahlblech mit einer Dicke von bis zu 0,5 Millimetern, welches mit
einer dünnen Zinnschicht beschichtet ist, um das Stahlblech vor Korrosion zu schützen.
Die Zinnschicht wird bspw. elektrolytisch auf das Blech aufgebracht.
[0003] Bei der Herstellung von verzinntem Stahlblech, insbesondere in elektrolytisch arbeitenden
Bandverzinnungsanlagen, wird das beschichtete Stahlblech chemisch oder elektrochemisch
passiviert und anschließend befettet, um das verzinnte Stahlblech oxidationsbeständig
zu machen und um den Reibwert zu erniedrigen, damit das verzinnte Stahlblech bei der
nachfolgenden Verarbeitung, bspw. bei der Herstellung von Weißblech-Verpackungen für
Lebensmittel, besser verarbeitet werden kann. Die Passivierung erfolgt üblicherweise
unter Verwendung von Cr
6+-haltigen Lösungen. Der Einsatz von Chrom-haltigen Mitteln bei der Behandlung von
Metallerzeugnissen ist umweltschädlich und soll daher insbesondere bei Metallerzeugnissen,
welche für die Lebensmittelindustrie vorgesehen sind, gesetzlich reguliert werden.
Stand der Technik
[0004] Im Stand der Technik wurden aus diesem Grund Cr
6+-freie Passivierungslösungen vorgeschlagen. Beispielsweise offenbart
DE4205819A eine wasserfreie Zusammensetzung zur Erzeugung von Korrosionsschutzschichten auf
metallischen Oberflächen auf der Basis von Silariverbindungen und Verbindungen von
vierwertigem Titan oder Zirkonium.
[0005] EP1002143A offenbart ein Verfahren zur alkalischen Passivierung von verzinkten und legierungsverzinkten
Stahloberflächen sowie von Aluminium und dessen Legierungen in Bandanlagen. Durch
diese Passivierung mit einer wässrigen Lösung entsteht eine Korrosionsschutzschicht,
die als Grundlage für eine nachfolgende Lackierung dienen kann.
[0006] Diese Veröffentlichungen betreffen zum größten Teil insbesondere die Passivierung
von aluminium- und zinkhaltigen Oberflächen von feuerverzinktem Feinblech und anderen
feuerverzinkten Stahlteilen für den Einsatz in der Automobilindustrie. Ein in der
Praxis anwendbares Verfahren zur chromatfreien Passivierung von Weißblech, das zufriedenstellende
Ergebnisse liefert, ist dagegen noch nicht bekannt.
[0007] EP1270764A offenbart ein oberflächenbehandeltes Weißblech, umfassend eine Legierungsschicht
auf einer Oberfläche eines Stahlblechs, eine Zinnschicht, die auf die Legierungsschicht
so aufgetragen worden ist, dass die Legierungsschicht auf einem Flächenbereich von
3,0 % oder mehr frei liegt und darauf einen P und Si umfassenden Film mit einem Beschichtungsgewicht
von 0,5 bis 100 mg/m
2 bzw. 250 mg/m
2, aufgebracht auf die frei liegende Legierungsschicht und die Zinnschicht.
[0008] Chromfreie Nachbehandlungsmittel für Weißbleche sind in der
US 2009/0155621 A1 und den darin zitierten Veröffentlichungen beschrieben.
[0009] EP1767665A beschreibt ein Verfahren zur Passivierung eines Weißblechs, bei dem eine wässrige
Lösung einer oberflächenaktiven Substanz auf ein mit einer Bandgeschwindigkeit zwischen
200 und 600 m/min bewegtes und mit Zinn beschichtetes Stahlband gesprüht wird. Als
geeignete oberflächenaktive Substanzen werden u.a. Polymethylsiloxane mit Polyetherseitenketten
und saure Polyether erwähnt.
Nachteile des Standes der Technik
[0010] Bei der Verwendung von beschichtetem Stahlblech zur Herstellung von Lebensmittelbehältern
(Konservendosen) werden gegenüber den Anforderungen an die genannten Materialien,
die zum Einsatz in der Automobilindustrie vorgesehen sind, andere Anforderungen an
die Oxidationsbeständigkeit und damit an die Passivierung der beschichteten Metalloberfläche
gestellt. Insbesondere muss die Passivierung hier ein zu starkes Anwachsen der Zinnoxidschicht
bei der Lagerung des beschichteten Stahlblechs bzw. der daraus hergestellten Lebensmittelbehälter
bis zur Lackierung und darüber hinaus bis zum Verbrauch der Konserve verhindern. Weiterhin
soll die Passivierung Verfärbungen der beschichteten Metalloberfläche verhindern.
Solche Verfärbungen treten bspw. bei der Sterilisation von Konservendosen mit schwefelhaltigen
Füllgütern auf, weil der Schwefel mit dem Zinn der beschichteten Stahlblechoberfläche
reagiert, wenn diese nicht ausreichend passiviert ist. Durch die matte Verfärbung
(Marmorierung) oder Goldfärbung der Oberfläche der Verpackung kann beim Verbraucher
der Eindruck erwecket werden, dass das Füllgut verdorben ist. Durch die Reaktion mit
Schwefel kann es auch zu Lackhaftungsstörungen kommen, welche durch eine Passivierung
des beschichteten Stahlblechs vermieden werden können. Die Passivierung muss außerdem
die Beständigkeit des lackierten Metallbehälters nach der Befüllung mit Lebensmitteln
gegen in den Lebensmitteln enthaltene Säuren gewährleisten, wie z. B. Mercapto-Aminocarbonsäure-Anionen,
beispielsweise von Cystein und Methionin. Derartige Säureanionen im Füllgut können
bei nicht ausreichender Passivierung eine Delamination des Innenlacks des Behälters
verursachen.
[0011] Bei der herkömmlichen Herstellung von Weißblech in Bandverzinnungsanlagen wird das
kaltgewalzte Fein- oder Feinstblech nach dem Verzinnen zunächst durch Erhitzung auf
Temperaturen oberhalb des Zinnschmelzpunktes aufgeschmolzen und anschließend in einem
Wasserbad abgeschreckt. Danach erfolgt die Passivierung, indem das verzinnte Stahlblech
mit einer Chromat-Lösung behandelt und schließlich mit vollentsalztem Wasser gespült
und thermisch getrocknet wird. Anschließend erfolgt eine elektrostatische Befettung
mit Dioctylsebacat (DOS) oder Acetyltributylcitrat (ATBC). Das auf der Weißblechoberfläche
adsorbierte Chromat wird durch Reaktion mit den =Sn=O und =Sn-OH-Gruppen der Zinnoberfläche
zu Cr
3+ und bei elektrochemischer kathodischer Passivierung außerdem zum Teil zu Chrom-Metall
reduziert. Das Cr
3+ fällt als Cr
3+-Hydroxid aus. Die Passivierungsschicht enthält nach dem Spülen und Trocknen der Weißblechoberfläche
keine Cr
6+-Ionen mehr.
Aufgabe der Erfindung
[0012] Hiervon ausgehend liegt der Erfindung die Aufgabe zugrunde, ein Verfahren zur chromfreien
Passivierung der Oberfläche von mit einer Zinn-Beschichtung überzogenen Stahlbändern,
welche mit einer Bandgeschwindigkeit durch eine Beschichtungsanlage bewegt werden,
bereitzustellen, mit dem eine effiziente Passivierung der Stahlbandoberfläche auch
bei hohen Bandgeschwindigkeiten ermöglicht wird. Darüber hinaus soll gleichzeitig
eine verbesserte Lackhaftung und Beständigkeit gegen Säuren in Lebensmitteln, insbesondere
gegen Schwefel enthaltende Aminosäuren, erzielt werden.
Lösung der Aufgabe der Erfindung
[0013] Gelöst werden diese Aufgaben mit einem Verfahren mit den Merkmalen des Anspruchs
1 sowie mit einem verzinnten Stahlblech oder-band mit den Merkmalen des Anspruchs
15. Bevorzugte Ausführungsformen werden in den Unteransprüchen definiert.
[0014] Bei dem erfindungsgemäßen Verfahren ist nach dem Aufschmelzen und Abschrecken des
verzinnten Stahlbands und vor der Behandlung mit einem chromfreien Nachbehandlungsmittel
die Durchführung einer anodischen Oxidation der Zinnoberfläche vorgesehen. Die Erfindung
geht von der Erkenntnis aus, dass die Passivierung der verzinnten Oberfläche des Stahlbands
durch Nachbehandlung mit einem chromfreien Nachbehandlungsmittel alleine nicht ausreichend
ist, um die Oberfläche vollflächig und dauerhaft gegen Korrosion und gegen Verfärbungen
(Marmorierungen) zu schützen. Insbesondere hat sich gezeigt, dass chromfreie Nachbehandlungsmittel
die verzinnte Stahlbandoberfläche nicht flächendeckend gegen eine Reaktion mit Schwefel
schützen. Es wurde nun in überraschender Weise fest gestellt, dass die Beständigkeit
der verzinnten Stahlbandoberfläche gegen Korrosion und Reaktion mit Schwefel beträchtlich
erhöht werden kann, wenn vor der Nachbehandlung mit einem chromfreien Nachbehandlungsmittel
zunächst eine Inertisierung der verzinnten Stahlbandoberfläche durch eine anodische
Oxidation erfolgt. Durch die anodische Oxidation wird eine Oxidschicht mit einer Schichtdicke
im nm-Bereich auf der verzinnten Stahlbandoberfläche erzeugt. Bei der Oxidschicht
handelt es sich im Wesentlichen um eine Schicht aus vierwertigem Zinnoxid (SnO
2), welches gegenüber zweiwertigem Zinnoxid (SnO) wesentlich inerter ist. Wird nun
erfindungsgemäß auf diese Oxidschicht eine dünne Oberflächenschicht eines chromfreien
Nachbehandlungsmittels aufgebracht, wird die Oberfläche des verzinnten Stahlbands
vollflächig und wirksam gegen Korrosion und gegen eine Reaktion mit Schwefel geschützt.
[0015] Nachfolgend wird das erfindungsgemäße Verfahren anhand eines Ausführungsbeispiels
näher beschrieben:
Schritt 1
[0016] Im ersten Schritt des erfindungsgemäßen Verfahrens erfolgt eine elektrochemische
Verzinnung eines kaltgewalzten Stahlbands (Fein- oder Feinstblech) in einer Bandverzinnungsanlage.
Das Stahlband wird dabei mit einer Bandgeschwindigkeit, welche üblicherweise im Bereich
von 200 m/min bis 750 m/min liegt, durch ein Elektrolysebad bewegt und elektrolytisch
mit Zinn beschichtet. Anschließend wird das Stahlband konduktiv oder induktiv (oder
auch konduktiv und induktiv) auf Temperaturen oberhalb des Zinnschmelzpunktes (232
°C) erhitzt, um die Zinnbeschichtung aufzuschmelzen. Danach wird das bewegte Stahlband
in einem Wasserbad abgeschreckt. Mit dieser frischen Oberfläche gelangt das verzinnte
Stahlband zum zweiten Schritt des Verfahrens, nämlich der anodischen Oxidation der
Zinnoberfläche.
Schritt 2
[0017] Im zweiten Schritt des erfindungsgemäßen Verfahrens erfolgt eine anodische Oxidation
in Sodalösung, d.h. in Natriumcarbonatlösung. Das verzinnte Stahlband wird dabei weiter
mit der Bandgeschwindigkeit bewegt und als Anode geschaltet in dem Soda-Elektrolytbad
polarisiert. Als Elektrolyt dient eine wässrige Sodalösung. Die Konzentration von
Natriumcarbonat in der Sodalösung beträgt bevorzugt 1 Gew.-% bis 10 Gew.-%, vorzugsweise
2 Gew.-% bis 8 Gew.-%, bevorzugt 3 Gew.-% bis 7 Gew.-%, vor allem 4 Gew.-% bis 6 Gew.-%,
insbesondere etwa 5 Gew.-%.
[0018] Die Einrichtung zur elektrolytischen anodischen Oxidation umfasst zweckmäßig ein
Elektrolysetauchbad mit einem Vertikaltank. In der Nähe des Bodens ist innerhalb des
Vertikaltanks eine Umlenkrolle angeordnet, über welche das verzinnte Stahlband umgelenkt
wird. Der Vertikaltank ist mit dem Elektrolyt gefüllt. Zwischen dem verzinnten Stahlband
und der Gegenelektrode(bspw. eine Stahl-Kathode) im Vertikaltank wird ein Potenzial
angelegt. Die Ladungsmenge Q liegt dabei zweckmäßig zwischen 0,2 C und 2 C, bevorzugt
zwischen 0,2 C und 0,6 C bei einer Stromdichte von 1-3 A/dm
2.
[0019] Die Anodisierungszeit entspricht der Verweilzeit des verzinnten Stahlbands im elektrochemischen
Oxidationsbad (Elektrolytbad). Diese ist durch die Länge des Elektrolytbads bzw. dessen
Füllstand sowie die Anodenlänge und die Bandgeschwindigkeit vorgegeben und liegt bei
den typischen Bandgeschwindigkeiten zweckmäßig im Bereich von 0,1 s bis 1 s, insbesondere
zwischen 0,1 s und 0,7 s, bevorzugt im Bereich von 0,15 s bis 0,5s und idealerweise
um 0,2 s. Über den Füllstand kann die Anodisierungszeit, in Abhängigkeit der Bandgeschwindigkeit,
auf die erfindungsgemäß geeigneten Werte eingestellt werden.
[0020] Der Abstand zwischen dem Stahlband und der Gegenelektrode in dem Elektrolytbad wird
anlagenbedingt eingestellt. Er liegt bspw. im Bereich von 3 bis 15 cm, vorzugsweise
im Bereich von 5 bis 10 cm und insbesondere um 10 cm.
[0021] Die Temperatur des elektrochemischen Oxidationsbads liegt vorzugsweise im Bereich
von 30 bis 60 °C, bevorzugter im Bereich von 35 bis 50 °C und insbesondere um 45 °C.
[0022] Die Stromdichte wird im Bereich von 1,0 bis 3 A/dm
2, vorzugsweise 1,3 bis 2,8 A/dm
2, bevorzugter 2 bis 2,6 A/dm
2, insbesondere um 2,4 A/dm
2 eingestellt. Die gesamte Ladungsmenge bewegt sich dabei im Bereich zwischen 0,2 C
und 0,6 C und beträgt bevorzugt bspw. 0,48 C. Die entsprechenden Ladungsdichten (bezüglich
der Fläche des behandelten Bands) liegen im Bereich von 0,2 C/dm
2 bis 0,6 C/dm
2.
Schritt 3
[0023] Im dritten Schritt des Verfahrens erfolgt eine gründliche Spülung des verzinnten
und oxidierten Stahlbands mit destilliertem oder vollständig entsalztem Wasser und
eine anschließende Trocknung, welche z.B. mit Heißluft erfolgen kann. Hierfür sind
jedoch auch andere Trocknungsmaßnahmen geeignet, wie die Trocknung mit wasseraufnehmenden
Lösemitteln und anschließend Trocknung mit einem Kalt- oder Heißluftgebläse, wobei
auch dafür die Verwendung von Heißluft bevorzugt wird, die Trocknung mit luftkonvektionsfreien
Trocknungsanlagen wie IR-Strahlungskörper, induktiver Beheizung oder Widerstandsheizung,
oder die Trocknung nur mit einem Kalt- oder Heißluft-Gebläse, vorzugsweise einem Heißluft-Gebläse.
Schritt 4
[0024] Im vierten Schritt des Verfahrens erfolgt eine Beschichtung der verzinnten und oxidierten
Stahlbandoberfläche mit einem Nachbehandlungsmittel.
[0025] Auf das mit der Bandgeschwindigkeit bewegte Stahlband wird hierfür eine Lösung des
Nachbehandlungsmittels, vorzugsweise eine Lösung mit Wasser oder einem organischen
Lösungsmittel oder eine gebrauchsfertige Zubereitung des Nachbehandlungsmittels aufgespritzt.
Als zweckmäßig haben sich 1,5 bis 10%ige wässrige Lösungen des Nachbehandlungsmittels
erwiesen. Vorzugsweise wird die Lösung des Nachbehandlungsmittels danach mittels Quetschrollen
abgequetscht und getrocknet. Nach dem Abquetschen und Trocknen verbleibt lediglich
noch ein dünner Film des Nachbehandlungsmittels auf der Oberfläche des beschichteten
Metallbands, wobei die Auflage dieses dünnen Films in der Regel zwischen 2 und 30
mg/m
2 beträgt.
[0026] Das Nachbehandlungsmittel wird bspw. über Rohre aufgesprüht, welche im Abstand zur
beschichteten Metallbandoberfläche und quer zur Bandlaufrichtung angeordnet sind und
Bohrungen oder Düsen aufweisen, durch welche das Nachbehandlungsmittel auf die beschichtete
Stahlbandoberfläche gelangt. Bevorzugt ist auf jeder Seite des Stahlbandes mindestens
ein Rohr mit solchen Bohrungen angeordnet, um beide Seiten des Metallbandes mit dem
Nachbehandlungsmittel zu bespritzen bzw. zu besprühen. Bevorzugt wird der Abstand
der Rohre zum verzinnten und anodisch oxidierten Stahlband so eingestellt und die
Lage der Bohrungen bzw. Düsen bezüglich der Bewegungsrichtung des Stahlbands so gewählt,
dass das austretende flüssige Behandlungsmittel senkrecht auf die Stahlbandoberfläche
oder zumindest innerhalb eines Winkelbereichs von +- 45°, bevorzugt innerhalb eines
Winkelbereichs von +-15° um die Normale (Senkrechte) auf die Oberfläche des Stahlbands
auftreffen.
[0027] Alternativ zum Aufsprühen des Nachbehandlungsmittels auf die Oberfläche des verzinnten
Stahlbands ist auch eine Applizierung in einem Tauchverfahren möglich.
[0028] Zum Abquetschen des aufgesprühten Behandlungsmittels sind in Bandlaufrichtung hinter
den Rohren zweckmäßig zwei Quetschrollenpaare angeordnet. Der Abstand des ersten Quetschrollenpaars
zu den Rohren in Bandlaufrichtung beträgt etwa zwischen 20 und 100 cm. Nach dem Abquetschen
verbleiben nur wenige molekulare Schichten der Nachbehandlungs-Lösung auf der verzinnten
Stahlbandoberfläche, möglicherweise lediglich eine nur noch einmolekulare Lösungsschicht.
[0029] Die von den Quetschrollen abgequetschte Lösung sammelt sich in einem Vorratstank,
von wo die überschüssige Nachbehandlungs-Lösung über eine Pumpe ggf. einer Aufbereitung
und einer Wiederverwendung zugeführt wird.
[0030] Als Nachbehandlungsmittel können die weiter unten definierten Mittel verwendet werden.
Stellvertretend für diese wird das Auftragen eines Ti/Zr-enthaltenden Nachbehandlungsmittels
beschrieben. Als Ti/Zr enthaltendes Nachbehandlungsmittel wird bspw. die von der Henkel
KGaA unter dem Markenkennzeichen Granodine
® 1456 erhältliche Substanz eingesetzt. Diese wird als Lösung mit einer Trockenauflage
im Bereich von 0,5 bis 2 mg Ti/m
2, bevorzugter 0,8 bis 1,5 mg Ti/m
2, insbesondere um 1 mg Ti/m
2, auf die verzinnte und oxidierte Stahlbandoberfläche aufgetragen.
Schritt 5
[0031] Als fünfter Schritt erfolgt wiederum ein Trocknungsschritt, wobei die TrocknungsTemperatur
(Bandtemperatur) im Bereich von 30 bis 95 °C und bevorzugt zwischen 35 und 60°C liegt.
Die Trocknungszeit ist der Bandgeschwindigkeit angepasst. Es können dabei die in Schritt
3 genannten Trocknungseinrichtungen verwendet werden.
[0032] Durch das beschriebene Verfahren wird ein verzinntes Stahlblech mit einem Schichtaufbau
erzielt, der sich wie folgt zusammensetzt: Zuunterst befindet sich als Träger ein
kaltgewalztes Stahlblech, insbesondere ein Fein- oder Feinstblech mit einer Dicke
von 0,5 mm bis 3 mm (Feinblech) bzw. von weniger als 0,5 mm (Feinstblech). Auf das
Stahlblech folgt als nächste Schicht die bspw. elektrolytisch abgeschiedene Zinnschicht.
Die Zinnauflage beträgt in der Regel 0,1 bis 11,2 g/m
2, sie kann jedoch in Einzelfällen auch weniger als 0,1 g/m
2oder mehr als 11,2 g/ m
2 betragen. Etwaige Legierungsschichten von Trägermaterial und Zinn werden hier als
gesonderte Zwischenschichten vernachlässigt. Auf der Zinnschicht folgt dann die durch
die anodische Oxidation erzeugte Oxidschicht mit einer Dicke von weinigen nm, welche
im Wesentlichen aus vierwertigem Zinnoxid besteht. Schätzungsweise bewegt sich die
Dicke der Zinnoxidschicht im Bereich von 2 bis 10 nm. Auf die Oxidschicht folgt als
Oberflächenschicht die Nachbehandlungsmittelschicht, welche sich durch die Nachbehandlung
und die anschließende Trocknung auf der dünnen Oxidschicht abgeschieden hat. Die Auflage
des Nachbehandlungsmittels beträgt im trockenen Zustand (Trockenauflage) zweckmäßig
zwischen 2 und 30 mg/m
2.
[0033] Das erfindungsgemäß hergestellte und nachbehandelte Blech wird entweder in Form von
Blechtafeln zerteilt oder als Rolle (Coil) aufgerollt. Der Endverarbeiter, bspw. der
Hersteller von Konservendosen, wird das Blech in der Regel dann mit einer Lackschicht
versehen, bspw. mit einem Konservendosenlack oder einem Epoxidharz-Lack. Durch Tiefziehen
wird das lackierte Blech dann zu Formteilen, z.B. zu Konservendosen, verarbeitet.
Der sich durch die erfindungsgemäße Behandlung ergebende Schichtaufbau trägt dabei,
im Vergleich zu bekannten Weißblechmaterialien, zu einer verbesserten Lackhaftung
und einem verminderten Abplatzen des Lacks bei, z.B. aufgrund des Vorliegens von Mercapto-Gruppen-haltigen
Aminosäuren.
[0034] Die zur Anwendung im erfindungsgemäßen Verfahren zur Nachbehandlung der Oberfläche
von anodisch oxidiertem Weißblech geeigneten Substanzen müssen solche Eigenschaften
haben, dass sie auf der Zinnoberfläche haften können und gleichzeitig die Benetzung
der beim anschließenden Lackieren der Zinnoberfläche aufzubringende Lackschicht ermöglichen.
Die Bindung zwischen der funktionellen Gruppe an der anodisch oxidierten Zinnoberfläche
und den funktionellen Gruppen der Lackoberfläche mit ihren Haftvermittlermolekülen
muss nach dem Trocknen des Lackfilms so stark sein, dass sie beim Cystein-Test (Sterilisation
des lackierten Weißblechs 90 min bei 121°C in einer Lösung von 3,65 g/l KH
2PO
4 mit 7,22 g/l Na
2HPO
4 * 2H
2O und 1g/l Cystein) nicht zerstört werden. Weiterhin sollten die zur Nachbehandlung
verwendeten Substanzen chromfrei und ohne Zugabe von organischen Lösemittel einsetzbar
sein, oder in destilliertem Wasser löslich sein, da der Einsatz von Lösevermittlern
zu hohe Konzentrationen der Lösemittel in der Abluft verursachen und damit kostspielige
Reinigungsanlagen für die Beseitigung der Lösemittel erforderlich machen würde.
[0035] Als Nachbehandlungsmittel besonders geeignete Substanzen haben sich zum Beispiel
solche Substanzen erwiesen, die in der Praxis vorzugsweise als Additive für die bessere
Dispergierung von Pigmenten in Lacken bzw. zur Verbesserung der Benetzung und/oder
der Haftung von Lacken auf Metalloberflächen eingesetzt werden. Solche Mittel sind
ausgewählt aus Copolymeren von Acrylaten, Polymethylsiloxanen mit Polyetherseitenketten,
sauren Polyethern, und Polymeren mit heterocyclischen Gruppen. Aber auch solche Substanzen,
welche als Korrosionsschutzmittel für Bleche z.B. in der Kraftfahrzeugindustrie zur
Anwendung kommen, z.B. Bonder- oder Parkerisierungsmittel, können vorteilhaft eingesetzt
werden. Solche Stoffe sind ausgewählt aus sauren, wässrigen, flüssigen Zusammensetzungen,
welche komplexe Metall-Fluorid-Anionen mit zwei- bis vierwertigen Kationen und polymere
Stoffe enthalten
[0036] Als Nachbehandlungsmittel für das erfindungsgemäße Verfahren besonders geeignet haben
sich neben Copolymeren von Acrylaten folgende Substanzen erwiesen:
a) ein organisch-modifiziertes Polysiloxan mit einem Brechungsindex von 1,456 bis
1,466 nach DIN 53491 und einer Dichte bei 20°C von 1,09-1,13 g/cm3 nach DIN 51757, [im Handel unter der Bezeichnung "EFKA 3580" erhältlich],
b1) ein Polymer mit einer chemischen Zusammensetzung von einem sauren Polyether mit
einer Dichte von 1,20-1,30 g/cm3 nach DIN 51757 und einem Säurewert von 270-310 mg KOH/g nach DIN 53402, [EFKA 8512],
b2) ein mit Fluorcarbonresten modifiziertes Polyacrylat, neutralisiert mit Dimethylethanolamin,
wobei eine wässrige Lösung mit 59 bis 61 Gew.-% Wirkstoffen bei 20°C eine Dichte von
1,04 bis 1,06 g/cm3 nach DIN 51757, einen Brechungsindex von 1,420 bis 1,440 nach DIN 53491 und einen
Säurewert von 50 -70 mg KOH/g nach DIN 53402 aufweist, [EFKA 3570],
b3) ein modifiziertes Polyacrylat, welches bei einem Anteil von 38-42 Gew.-% Wirksubstanz
in Wasser eine Dichte von 1,02 bis 1,06 g/cm3 nach DIN 51757 und eine Aminzahl von 22 bis 28 mg KOH/g nach DIN 16945 aufweist,
[EFKA 4560],
c) ein Polymer das enthält:
- i) 0-80 Mol % von einem oder mehreren Monomeren der Formel
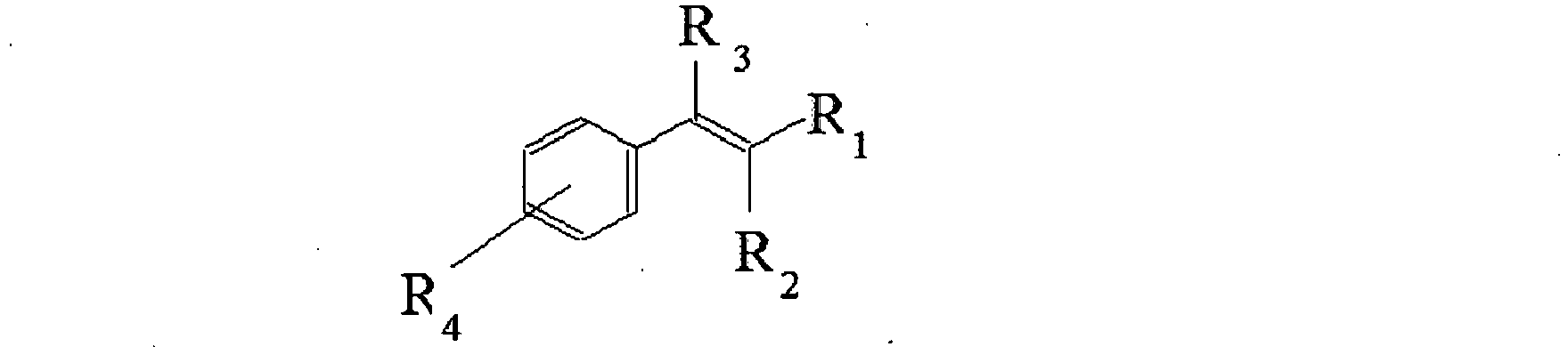
wobei R1, R2, R3 und R4 gleich oder verschieden sein können und H oder Alkyl darstellen,
- ii) 0-70 Mol % von einem oder mehreren Monomeren der Formel

worin R5, R6 und R7 gleich oder verschieden sein können und H oder Alkyl darstellen, und R8 Alkyl oder substituiertes Alkyl darstellt, und die Alkylgruppe R8 durch - O- Gruppen unterbrochen sein kann,
- iii) 5-50 Mol % von einem oder mehreren Monomeren, enthaltend eine heterocyclische
Gruppe mit mindestens einem basischen Ringstickstoffatom, oder an das bzw. an die
eine derartige heterocyclische Gruppe sich nach einer Polymerisation befindet,
- iv) 0-10 Mol % von einem oder mehreren Monomeren, enthaltend eine oder mehrere Gruppen,
die für Vernetzung oder Kupplung reaktiv sind, und
- v) 0-20 Mol % von einem oder mehreren Monomeren, die nicht in die vorstehenden Gruppen
i) - iv) fallen, wobei die Menge der Monomere von Gruppe i) zusammen mit Monomeren,
die eine Acrylatgruppe enthalten, mindestens 20 Mol % beträgt, sowie organische Salze
davon, oder
d) eine saure, wässrige, flüssige Zusammensetzung, die neben Wasser und ggf. Lösemitteln,
die folgenden Komponenten enthält:
- (A) Fluormetallatanionen mit Titan, Zirkonium, Hafnium, Silizium, Aluminium und/oder
Bor als Zentralatom; sowie gegebenenfalls ionisierbaren Wasserstoffatomen, und/oder
gegebenenfalls einem oder mehreren Sauerstoffatomen;
- (B) ein oder mehrere zwei- bis vierwertige, insbesondere zweiwertige und/oder vierwertige
Kationen von Kobalt, Magnesium, Mangan, Zink, Nickel, Zinn, Kupfer, Zirkonium, Eisen
und/oder Strontium;
- (C) Phosphor enthaltende anorganische Oxianionen und/oder Phosphonatanionen, und
- (D) ein oder mehrere wasserlösliche und/oder in Wasser dispergierbare organische Polymere
und/oder polymerbildende Harze.
[0037] Vorzugsweise ist die Substanz d) eine saure, wässrige, flüssige Zusammensetzung,
die neben Wasser die folgenden Komponenten enthält:
- (A) Fluormetallatanionen, die jeweils bestehen aus: (i) wenigstens vier Fluoratomen
und (ii) wenigstens 1 Atom eines metallischen Elements, das aus der Gruppe, bestehend
aus Titan, Zirkonium, Hafnium, Silizium, Aluminium und Bor, ausgewählt ist; sowie
gegebenenfalls (iii) ionisierbaren Wasserstoffatomen, und/oder gegebenenfalls (iv)
einem oder mehreren Sauerstoffatomen;
- (B) eine Menge von einem oder mehreren zwei- bis vierwertigen, insbesondere zweiwertigen
und/oder vierwertigen Kation(en) von Kobalt, Magnesium, Mangan, Zink, Nickel, Zinn,
Kupfer, Zirkonium, Eisen und/oder Strontium, so dass das Verhältnis der Gesamtzahl
des Kations (der Kationen) zu der Anzahl der Anionen in der Komponente (A) wenigstens
1:5 beträgt, jedoch nicht größer als 3:1 ist;
- (C) Phosphor enthaltende anorganische Oxyanionen und/oder Phosphonatanionen, und
- (D) ein oder mehrere wasserlösliche und/oder in Wasser dispergierbare organische Polymere
und/oder polymerbildende Harze, wobei die Menge dieser Komponente so ist, dass das
Verhältnis des Feststoffgehalts an organischem Polymer und polymerbildendem Harz in
der Zusammensetzung zu dem Feststoffgehalt der Komponente (A) im Bereich von 1:2 bis
3:1 liegt.
[0038] Insbsondere ist die Substanz d) eine saure, wässrige, flüssige Zusammensetzung, die
im wesentlichen frei von sechswertigem Chrom und/oder Ferricyanid ist, zur Behandlung
von Metall-Oberflächen, die nicht mehr als 1,0 % und vorzugsweise nicht mehr als 0,0002
% sowohl des sechswertigen Chroms als auch des Ferricyanids enthalten und die ansonsten
neben Wasser die folgenden Komponenten enthalten:
- (A) wenigstens 0,010 M/kg Fluormetallatanionen, wobei diese Anionen jeweils bestehen
aus: (i) wenigstens vier Fluoratomen und (ii) wenigstens 1 Atom eines metallischen
Elements, das aus der Gruppe ausgewählt ist, die aus Titan, Zirconium, Hafnium, Silicium,
Aluminium und Bor besteht; sowie gegebenenfalls (iii) ionisierbaren Wasserstoffatomen,
und/oder gegebenenfalls (iv) einem oder mehreren Sauerstoffatomen;
- (B) eine Menge von zwei- bis vierwertigen, insbesondere einem oder mehreren zweiwertigen
und/oder vierwertigen Kation(en) des Cobalts, Magnesiums, Mangans, Zinks, Nickels,
Zinns, Kupfers, Zirconiums, Eisens und/oder Strontiums, so dass das Verhältnis der
Gesamtzahl des Kations (der Kationen) zu der Anzahl der Anionen in der Komponente
(A) wenigstens 1:5 beträgt, jedoch nicht größer als 3:1 ist;
- (C) wenigstens 0,015 MP/kg und vorzugsweise wenigstens 0,030 Mp/kg Phosphor enthaltender
anorganischer Oxianionen und/oder Phosphonatanionen, und
- (D) wenigstens 0,10 % und vorzugsweise wenigstens 0,20 % eines wasserlöslichen (oder
mehrerer wasserlöslicher) und/oder in Wasser dispergierbaren (in Wasser dispergierbarer)
organischen Polymers (organischer Polymere) und/oder polymerbildenden Harzes (polymerbildender
Harze), wobei die Menge dieser Komponente derartig ist, daß das Verhältnis des Feststoffgehalts
des organischen Polymers (der organischen Polymere) und des polymerbildenden Harzes
(der polymerbildenden Harze) in der Zusammensetzung zu dem Feststoffgehalt der Komponente
(A) im Bereich von 1:2 bis 3:1 liegt.
[0039] Vorzugsweise umfasst die Komponente d) Dihydrogenhexafluorotitanat(2-) und organische
Polymere. Besonders bevorzugt ist die Komponente Granodine 1456.
[0040] Das Polymer (D) kann eine Polymerverbindung sein, die ein Copolymermaterial umfasst,
wobei mindestens ein Teil von dem Copolymer die Struktur aufweist
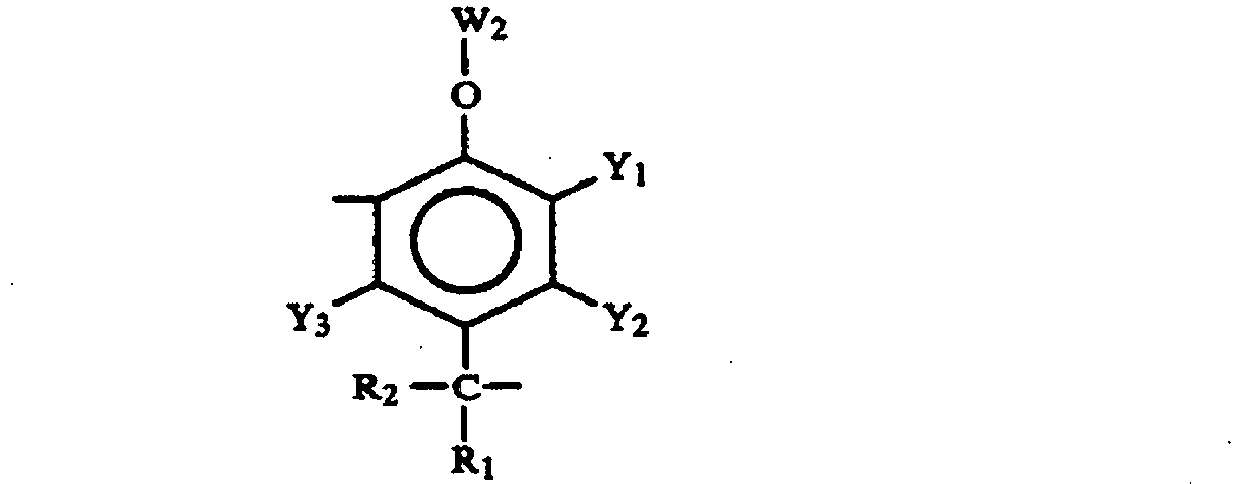
welche in Patentanspruch 1 und den abhängigen Patentansprüchen der Europäischen Patentanmeldung
mit der Publikationsnummer
EP0319017 A2 genauer definiert ist.
[0041] Ein solches Polymer kann z.B. wie folgt hergestellt werden:
Ein Kunststoffkolben wird mit 400 ml Propasol P (ein propoxyliertes Propan-Lösungsmittel,
erhältlich von Union Carbide Corp., Danbury, Conn.) und 160 g Resin M (ein Polyvinylphenol,
erhältlich von Maruzen Oil MW=5000) befüllt. Eine Aufschlämmung von 263,3 g N-Methyglucamin
in 400 desionisiertem Wasser wird zugegeben und das Gemisch wird auf 60-65 °C unter
Rühren erwärmt. Dann werden 100,2 ml- 37 % Formaldehyd über eine bis anderthalb Stunden
zugegeben. Das Gemisch wird dann auf 90°C erwärmt und für 6 Stunden gehalten. Nach
dem Kühlen wird das Gemisch mit desionisiertem Wasser auf 9,6 Gew.-% Feststoffe verdünnt.
Der pH-Wert der fertigen Lösung beträgt 9,1 und die Lösung umfasst ein N-Methylglucamin-Derivat.
[0042] Geeignet sind auch die Polyphenol-Derivate gemäß dem Patentanspruch 1 und den abhängigen
Patentansprüchen der Europäischen Patentanmeldung mit der Publikationsnummer
EP 0 319 016 A2:

[0043] Ein solches Polymer kann z.B. wie folgt hergestellt werden:
80 g eines Harzes obiger Formel mit einem mittleren Molekulargewicht von etwa 2 400,
worin R1, R13, R14 und W2 H sind, R2 -CH3 ist und Y2 ein Alkylamin-Rest oder ein Alkylammonium-Rest ist (bezogen auf die in EP 0 319 016 A2 angegebene Formel I und deren Definitionen), werden langsam in 160 ml Propasol P
(einem propoxylierten Propanol-Lösungsmittel, erhalten von Union Carbide Corp., Danbury,
Connecticut) in einem 1 Liter Kunststoff-Kolben unter Benutzung eines Hochgeschwindigkeits-Mischers
gelöst. Der Kunststoff-Kolben ist mit einem Blattrührer, einem Rückflusskühler und
einer Stickstoff-Spülung ausgerüstet. Zu der Harz-Lösung werden dann 53,5 g 2-(Methylamino)ethanol
und 160 ml entionisiertes Wasser gegeben. Es wird begonnen, vorsichtig auf 60°C zu
erwärmen. Wenn 60°C erreicht sind, wird mit der Zugabe von 50 ml 37-% Formaldehyd
in Wasser begonnen, und diese Zugabe wird während einer Zeitspanne von 1 h fortgesetzt.
Weitere 25 ml Propasol P werden zugesetzt, und die Reaktionsmischung wird 1,5 h auf
60°C gehalten. Die Temperatur wird auf 80 °C erhöht und dort 1,75 h gehalten. Man
lässt die Reaktionsmischung sich auf Raumtemperatur abkühlen, und 21,8 g 75-% H3PO4 und danach 960 ml entionisiertes Wasser werden hinzugefügt. Gegebenenfalls wird ein
Aminoxid, das keinen zusätzlichen Schritt der Neutralisation benötigt, durch Hinzufügen
von 0,75 Mol 30-% H2O2 (85 g) zu der Reaktionsmischung gebildet. Man lässt die Reaktionsmischung über Nacht
rühren und verdünnt sie dann mit 960 ml entionisiertem Wasser. Das Ergebnis dieses
wahlweise durchzuführenden Schrittes ist ein wasserlösliches Aminoxid-Harz, das zur
Wasser-Stabilität keine Neutralisation erfordert.
[0044] Geeignete Nachbehandlungsmittel mit komplex gebundenen Übergangsmetallen sind beispielsweise
Produkte der Reihe Granodine
®, welche eine wässrige Lösung mit komplex gebundenen Übergangsmetallen (Ti, Mn, Zr)
und ggf. einem Silan darstellen. Als besonders geeignet haben sich titanhaltige und/oder
zirkonhaltige Nachbehandlungsmittel erwiesen, wie z.B. Produkte der Reihe Granodine
® (Hersteller: Henkel) oder Gardobond
® (Hersteller: Chemetall), insbesondere die Produkte "Granodine
® 1456" und "Gardobond
® X 4707". Diese titanhaltigen und zirkonhaltigen Produkte werden zweckmäßig als Nachbehandlungsmittel
für das erfindungsgemäße Verfahren so dosiert, dass nach dem Abquetschen und dem Trocknen
eine Titanauflage (Trockenauflage) von 0,5 mg/m
2 bis 2 mg/m
2 und insbesondere von ca. 1,0 mg/m
2 auf der Oberfläche des behandelten Weißblechs vorhanden ist. Hierfür werden typischerweise
1,5 - 10%-ige wässrige Lösungen dieser Nachbehandlungsmittel verwendet, wobei der
Titan-Anteil in der wässrigen Lösung bevorzugt zwischen 0,2 und 1,2 g/l und besonders
bevorzugt zwischen 0,2 und 0,5 g/I liegt.
[0045] Komponenten (a) bis (c) wurden von der Firma EFKA Chemicals bzw. EFKA Additives entwickelt
und werden derzeit von der BASF SE geliefert. Die Produkte werden in den Veröffentlichungen
US5688858A,
EP0311157 A1 (Seite 12, Zeile 45 bis Seite 13, Zeile 36, sowie den Beispielen),
US5399294A,
EP0438836 A1 (Spalte 10 Zeile 42 bis 57, sowie den Beispielen),
US5882393A,
WO97/26984 A1 (Seite 20, Zeilen 4 bis 20, sowie den Beispielen),
US2004063828A,
WO02/057004 A1 (Seite 11, Zeilen 1 bis 6, sowie den Beispielen),
US2004236007A,
WO03/033603 A1 (Seite 20, Zeilen 1 bis 23, sowie den Beispielen),
US2009234062A,
WO2004/045755 A2 (Seite 21, Zeilen 2 bis 13, sowie den Beispielen),
US2007293692A sowie
WO2005/085261 A1 (Seite 14, Zeilen 1 bis 25 sowie den Beispielen) ausführlich beschrieben, insbesondere
in den dort angeführten unabhängigen Ansprüchen.
[0046] Bevorzugt sind die nachstehenden Produkte der Firma BASF SE: EFKA 3570, EFKA 3580,
EFKA 4560 sowie EFKA 8512. Besonders bevorzugt ist EFKA 4560.
[0047] Für das Nachbehandlungsmittel haben sich Acrylat-haltige Mittel mit N-heterocyclischen
Gruppen als besonders geeignet erwiesen, z.B. EFKA 4560. Diese entsprechen den oben
definierten Komponenten (c).
Sie können beispielsweise wie folgt hergestellt werden
[0048] In einen für Polymerisationen geeigneten Reaktionskolben mit Rückflusskühler werden
in 9,86 g Xylol und 4,93 g Methoxypropylacetat 2,84 g Vinyltoluol, 4,55 g Isobutylmethacrylat,
7,36 g Ethylhexylacrylat, 5,20 g Hydroxyethylmethacrylat, 1,80 g Polyethylenglycolmonomethacrylat
mit einem Molekulargewicht von etwa 400 und 0,44 g Di-tertiär-butylperoxid gelöst.
Die Polymerisation wurde beim Siedepunkt des Gemischs unter Rühren und Einführen eines
Inertgases ausgeführt. Am Ende der Polymerization wurden 9,79 g Isophorondiisocyanat
in 16,58 g Isobutylacetat und 16,58 g Methoxypropylacetat gelöst, und die übrigen
freien NCO-Gruppen wurden dann mit 3,60 g Polyethylenglycolmonomethacrylat mit einem
Molekulargewicht von etwa 400 und 4,51 g 1-(3-Aminopropyl)imidazol umgesetzt.
[0049] Der Feststoffgehalt wurde dann mit Butylacetat auf 40 Gew.-% eingestellt.
[0050] In ähnlicher Weise wie vorstehend wurden 3,54 g Vinyltoluol, 5,69 g Isobornylmethacrylat,
9,20 g 2-Ethylhexylmethacrylat, 7,15 g Hydroxyethylmethacrylat, und 1,28 g Di-tertiär-butylperoxid,
gelöst in 11,94 g Xylol und 5,97 g Methoxypropylacetat, polymerisiert.
[0051] Anschließend wurden 12,23 g Isophorondiisocyanat, gelöst in 20,36 g Butylacetat und
20,36 g Methoxypropylacetat, hinzu gegeben. Die übrigen freien NCO-Gruppen wurden
dann mit 4,50 g Polyethylenglycolmonomethacrylat mit einem Molekulargewicht von etwa
400 und 3,78 g 3-Amino-1,2,4-triazol in 11,34 g N-Methylpyrrolidon umgesetzt.
[0052] Der Feststoffgehalt wurde dann mit Butylacetat auf 40 Gew.-% eingestellt.
[0053] Diese Substanzen werden gemäß dem oben beschriebenen Verfahren der Erfindung unverdünnt
oder als wässrige Lösung auf das verzinnte Stahlband aufgespritzt und ggf. anschließend
abgequetscht und getrocknet. Als Auftragsmenge für z.B. die Substanz EFKA 4560 sind
Trockenauflagen im Bereich von 2 bis 15 mg/m
2 und bevorzugt zwischen 2 und 10 mg/m
2 geeignet.
[0054] Mit dem/den Nachbehandlungsmittel(n) kann das (weitere) Zinnoxid-Wachstum auf der
beschichteten Metallbandoberfläche bei dessen Lagerung bis zum Lackieren stark reduziert
werden. Gleichzeitig erfolgt bei der erfindungsgemäßen Behandlung der anodisch oxidierten,
verzinnten Stahlbandoberfläche mit diesen Nachbehandlungsmitteln eine Verbesserung
der Lackhaftung. Die erfindungsgemäß behandelten Weißblechoberflächen haben sich als
sehr gut lackierbar erwiesen.
[0055] Als Ergebnis der erfindungsgemäßen Behandlung von Weißblech mit einer anodischen
Oxidation und dem Auftrag des chromfreien Nachbehandlungsmittels hat sich gezeigt,
dass schwefelhaltige Substanzen, die in Lebensmitteln vorkommen, welche z.B. von den
Aminosäuren Cystein oder Methionin stammen, nicht mehr über Diffusion durch die später
aufgetragene Lackschicht und die erfindungsgemäße Passivierung an die Zinnoberflächen
gelangen können und dort unansehnliche Marmorierungen (Gelbfärbungen oder Braunfärbungen)
verursachen, welche im Wesentlichen auf eine Bildung von Zinnsulfid zurückzuführen
sind, und welche im Extremfall zu einer Verschlechterung der Lackhaftung auf dem Weißblech
oder gar zu einer Ablösung des Lackauftrags führen könnten.
[0056] Die erfindungsgemäß behandelten Weißblechproben weisen zum Teil eine gegenüber unbehandeltem
Weißblech deutlich verringerte Gleitreibung auf, wobei bei einzelnen Substanzen sogar
geringere Gleitreibwerte ermittelt werden konnten als bei herkömmlicher Behandlung
des Weißblechs mit DOS.
[0057] Aus einer Gesamtschau der Ergebnisse von Vergleichsversuchen lässt sich erschließen,
dass mit dem erfindungsgemäßen Verfahren zur Passivierung der Oberfläche von Weißblech
durch anodische Oxidation und Beschichtung mit den erfindungsgemäß verwendeten Nachbehandlungsmitteln
die besten Ergebnisse hinsichtlich der Oxidations- und Marmorierungsbeständigkeit
(Sulfid-Sperrwirkung) und der Gleitreibung erhalten werden. Die Ergebnisse sind dabei
vergleichbar mit der Qualität der aus dem Stand der Technik bekannten Passivierung
von Weißblech mit chromhaltigen Nachbehandlungsmitteln.
[0058] Die Substanzen "EFKA 3580", "EFKA 4560", "EFKA 8512" und "EFKA 3570" ergeben als
Nachbehandlungsmittel hinsichtlich der Eigenschaften niedrige Gleitreibwerte, Oxidationsbeständigkeit
(niedriges Zinnoxid-Wachstum) und Marmorierungsbeständigkeit (Sulfid-Sperrwirkung)
sehr gute Resultate. Als bevorzugtes Nachbehandlungsmittel hat sich diesbezüglich
"EFKA 4560" heraus gestellt. Hinsichtlich der Marmorierungsbeständigkeit und der Lackhaftung
zeigen die titanhaltigen Nachbehandlungsmittel der Produktreihen Granodine
® (insbesondere "Granodine
® 1456") und Gardobond
® (insbesondere Gardobond
® X 4707) sehr vorteilhafte Ergebnisse. Für die Durchführung des erfindungsgemäßen
Verfahrens eignen sich jedoch auch andere, teilweise aus dem Stand der Technik bereits
bekannte chromfreie Nachbehandlungsmittel. Das erfindungsgemäße Verfahren kann dabei
sowohl bei Weißblech mit aufgeschmolzener Zinnschicht als auch bei Weißblech angewandt
werden, bei dem die Zinnschicht nicht aufgeschmolzen worden ist.
1. Verfahren zur Passivierung der Oberfläche von verzinntem Stahlband, welches mit einer
Bandgeschwindigkeit von mindestens 200 m/min durch eine Beschichtungsanlage bewegt
wird, wobei nach dem Verzinnen des Stahlbandes zunächst die Oberfläche anodisch oxidiert
wird, um eine Oxidschicht auszubilden, welche im Wesentlichen aus vierwertigem Zinnoxid
(SnO2) besteht, und anschließend auf die Oxidschicht eine flüssige Lösung eines chromfreien
Nachbehandlungsmittels aufgetragen wird, wobei das Nachbehandlungsmittel ausgewählt
ist aus Copolymeren von Acrylaten, Polymethylsiloxanen mit Polyetherseitenketten,
sauren Polyethern, Polymeren mit heterocyclischen Gruppen und sauren, wässrigen, flüssigen
Zusammensetzungen, welche komplexe Metall-Fluorid-Anionen mit zwei- bis vierwertigen
Kationen und polymere Stoffe enthalten.
2. Verfahren nach Anspruch 1, wobei die anodische Oxidation mit einem basischen Elektrolyten
und bei einer Stromdichte von 1,0 A/dm2 bis 3 A/dm2 mittels Durchleiten des verzinnten Stahlbands durch ein Elektrolysebad ausgeführt
wird.
3. Verfahren nach Anspruch 2, wobei der basische Elektrolyt ausgewählt ist aus Alkalimetall-
oder Erdalkalimetall-Hydroxyd, -Carbonat, basischem Alkalimetall-Phosphat und basischem
organischem Alkalimetall- oder Erdalkalimetall-Salz.
4. Verfahren nach Anspruch 2 oder 3, wobei der Elektrolyt Natriumcarbonat enthält.
5. Verfahren nach Anspruch 2, dadurch gekennzeichnet, dass das Elektrolysebad so eingestellt ist, dass eine Ladung von mindestens 0,2 C erzielt
wird.
6. Verfahren nach einem der voranstehenden Ansprüche, dadurch gekennzeichnet, dass das Nachbehandlungsmittel Titan und/oder Zirkonium enthält.
7. Verfahren nach einem der voranstehenden Ansprüche, wobei nach der anodischen Oxidation
eine wässrige Lösung des Nachbehandlungsmittels oder eine gebrauchsfertige Lösung
des Nachbehandlungsmittels mittels Durchleiten durch ein das Nachbehandlungsmittel
enthaltendes Bad aufgetragen wird.
8. Verfahren nach einem der voranstehenden Ansprüche, dadurch gekennzeichnet, dass das Nachbehandlungsmittel über mindestens ein Rohr aufgesprüht wird, welches im Abstand
zur beschichteten Metallbandoberfläche angeordnet ist und mindestens eine Bohrung
oder Düse aufweist, durch welche das Nachbehandlungsmittel auf die oder jede beschichtete
Oberfläche des Stahlbands gesprüht wird.
9. Verfahren nach einem der voranstehenden Ansprüche, dadurch gekennzeichnet, dass die Lösung des Nachbehandlungsmittel auf beiden Seiten des Stahlbandes aufgebracht
wird.
10. Verfahren nach einem der Ansprüche 8 oder 9, dadurch gekennzeichnet, dass das Nachbehandlungsmittel in Form von Flüssigkeitsstrahlen auf die verzinnten Stahlbandoberfläche(n)
aufgespritzt wird, wobei die Flüssigkeitsstrahlen in einem Winkelbereich von zwischen
+45° und -45° zur Normalen auf die Oberfläche auftreffen.
11. Verfahren nach einem der voranstehenden Ansprüche, dadurch gekennzeichnet, dass die Lösung des Nachbehandlungsmittels nach dem Auftragen auf die verzinnte und oxidierte
Oberfläche des Stahlbands mittels Quetschrollen abgequetscht und das verzinnte Stahlband
nach dem Abquetschen des Nachbehandlungsmittels getrocknet wird.
12. Verfahren nach Anspruch 11, dadurch gekennzeichnet, dass nach dem Abquetschen des Nachbehandlungsmittels und dem Trocknen auf der Oberfläche
des verzinnten Stahlbands ein dünner Film des Nachbehandlungsmittels mit einer Auflage
zwischen 2 mg/m2 und 30 mg/m2vorhanden ist.
13. Verfahren nach Anspruch 11, dadurch gekennzeichnet, dass das Nachbehandlungsmittel titanhaltig ist und dass nach dem Abquetschen des titanhaltigen
Nachbehandlungsmittels und nach dem Trocknen auf der Oberfläche des verzinnten Stahlbands
ein dünner Film des Nachbehandlungsmittels mit einer Titan-Auflage zwischen 0,5 mg/m2 und 2 mg/m2 vorhanden ist.
14. Verfahren nach einem der voranstehenden Ansprüche, dadurch gekennzeichnet, dass die anodische Oxidation der verzinnten Oberfläche des Stahlbands innerhalb einer
Anodisierungszeit von 0,1 bis 1,0 Sekunden und bevorzugt innerhalb einer Anodisierungszeit
zwischen 0,2 bis 0,7 Sekunden erfolgt.
15. Verzinntes Stahlband oder -blech mit einer Trägerschicht aus einem Fein- oder Feinstblech
aus Stahl, einer darauf abgeschiedenen Zinnschicht und einer Oberflächenschicht eines
chromfreien Nachbehandlungsmittels, dadurch gekennzeichnet, dass zwischen der Zinnschicht und der Oberflächenschicht des Nachbehandlungsmittels eine
Oxidschicht ausgebildet ist, welche im Wesentlichen aus vierwertigem Zinnoxid (SnO2) besteht und dass das Nachbehandlungsmittel ausgewählt ist aus Copolymeren von Acrylaten,
Polymethylsiloxanen mit Polyetherseitenketten, sauren Polyethern, Polymeren mit heterocyclischen
Gruppen und sauren, wässrigen, flüssigen Zusammensetzungen, welche komplexe Metall-Fluorid-Anionen
mit zwei- bis vierwertigen Kationen und polymere Stoffe enthalten.
1. Method for passivation of the surface of tinned steel strip which is moved through
a coating installation at a strip speed of at least 200 m/min, wherein after the tinning
of the steel strip first the surface is anodically oxidised in order to form an oxide
layer which essentially consists of tetravalent tin oxide (SnO2), and then a liquid solution of a chromium-free after-treatment agent is applied
to the oxide layer, wherein the after-treatment agent is selected from copolymers
of acrylates, polymethyl siloxanes with polyether side chains, acid polyethers, polymers
with heterocyclic groups and acid, aqueous,liquid compounds which contain complex
metal fluoride anions with divalent to tetravalent cations and polymeric substances.
2. Method according to claim 1, wherein the anodic oxidation is carried out with a basic
electrolyte and with a current density of from 1.0 A/dm2 to 3 A/dm2 bypassing the tinned steel strip through an electrolysis bath.
3. Method according to claim 2, wherein the basic electrolyte is selected from alkali
metal or alkaline earth metal hydroxide or carbonate, basic alkali metal phosphate
and basic organic alkali metal or alkaline earth metal salt.
4. Method according to claim 2 or 3, wherein the electrolyte contains sodium carbonate.
5. Method according to claim 2, characterised in that the electrolysis bath is adjusted so that a charge of at least 0.2 C is obtained.
6. Method according to one of the preceding claims, characterised in that the after-treatment agent contains titanium and/or zirconium.
7. Method according to one of the preceding claims, wherein after the anodic oxidation
an aqueous solution of the after-treatment agent or a ready to use solution of the
after-treatment agent is applied by passage through a bath containing the after-treatment
agent.
8. Method according to one of the preceding claims, characterised in that the after-treatment agent is sprayed on by means of at least one pipe which is arranged
a distance from the coated surface of the metal strip and exhibits at least one bore
or nozzle through which the after-treatment agent is sprayed on to the or each coated
surface of the steel strip.
9. Method according to one of the preceding claims, characterised in that the solution of the after-treatment agent is applied on both sides of the steel strip.
10. Method according to one of claims 8 or 9, characterised in that the after-treatment agent is sprayed on to the tinned steel strip surface(s) in the
form of jets of liquid, wherein the jets of liquid impinge on the surface at an angle
ranging from +45° to -45° with respect to the normal.
11. Method according to one of the preceding claims, characterised in that after the application on the tinned and oxidised surface of the steel strip, the
solution of the after-treatment agent is squeezed off by means of squeezing rollers
and after the after-treatment agent has been squeezed off the tinned steel strip is
dried.
12. Method according to claim 11, characterised in that after the squeezing off of the after-treatment agent and the drying, a thin film
of the after-treatment agent with a coatingof between 2 mg/m2 and 30 mg/m2 is present on the surface of the tinned steel strip.
13. Method according to claim 11, characterised in that the after-treatment agent contains titanium and in that after the squeezing off of the titanium-containing after-treatment agent and after
the drying, a thin film of the after-treatment agent with a titanium coatingof between
0.5 mg/m2 and 2 mg/m2 is present on the surface of the tinned steel strip.
14. Method according to one of the preceding claims, characterised in that the anodic oxidation of the tinned surface of the steel strip is carried out within
an anodisation time of from 0.1 to 1.0 seconds and preferably within an anodisation
time of between 0.2 and 0.7 seconds.
15. Tinned steel strip or sheet with a carrier layer composed of a fine or ultra-fine
sheet of steel, a layer of tin deposited thereon and a surface layer of a chromium-free
after-treatment agent, characterised in that between the layer of tin and the surface layer of the after-treatment agent is formed
an oxide layer which essentially consists of tetravalent tin oxide (SnO2) and in that the after-treatment agent is selected from copolymers of acrylates, polymethyl siloxanes
with polyether side chains, acid polyethers, polymers with hetrocyclic groups and
acid, aqueous, liquid compounds which contain complex metal fluoride anions with divalent
to tetravalent cations and polymeric substances.
1. Procédé de passivation de la surface d'une bande d'acier étamée, qui est déplacée
à une vitesse de bande d'au moins 200 m/min à travers une installation de revêtement,
sachant qu'après l'étamage de la bande d'acier, la surface est dans un premier temps
oxydée de manière anodique afin de réaliser une couche d'oxyde, qui est constituée
essentiellement d'un oxyde d'étain (SnO2) tétravalent puis qu'une solution liquide d'un agent de post-traitement sans chrome
est appliquée immédiatement après sur la couche d'oxyde, sachant que l'agent de post-traitement
est choisi parmi des copolymères d'acrylates, des polyméthylsiloxanes comprenant des
chaînes latérales de polyéther, des polyéthers acides, des polymères comprenant des
groupes hétérocycliques et des compositions liquides aqueuses acides, qui contiennent
des anions de fluorure métallique complexes comprenant des cations bi- à tétravalents
et des substances polymères.
2. Procédé selon la revendication 1, sachant que l'oxydation anodique est exécutée avec
un électrolyte basique et à une densité de courant allant de 1,0 A/dm2 à 3 A/dm2 en faisant passer la bande d'acier étamée à travers un bain d'électrolyse.
3. Procédé selon la revendication 2, sachant que l'électrolyte basique est choisi parmi
un hydroxyde métallique alcalin ou alcalino-terreux, un carbonate métallique alcalin
ou alcalino-terreux, un phosphate métallique alcalin basique et un sel métallique
alcalin ou alcalino-terreux organique basique.
4. Procédé selon la revendication 2 ou 3, sachant que l'électrolyte contient du carbonate
de potassium.
5. Procédé selon la revendication 2, caractérisé en ce que le bain d'électrolyse est réglé de telle manière qu'une charge d'au moins 0,2 C est
obtenue.
6. Procédé selon l'une quelconque des revendications précédentes, caractérisé en ce que l'agent de post-traitement contient du titane et/ou du zirconium.
7. Procédé selon l'une quelconque des revendications précédentes, sachant qu'une solution
aqueuse de l'agent de post-traitement ou une solution prête à l'emploi de l'agent
de post-traitement est appliquée, après l'oxydation anodique, au moyen du passage
à travers un bain contenant l'agent de post-traitement.
8. Procédé selon l'une quelconque des revendications précédentes, caractérisé en ce que l'agent de post-traitement est pulvérisé par l'intermédiaire au moins d'un tube,
qui est disposé à distance par rapport à la surface de bande métallique revêtue et
qui présente au moins un alésage ou une buse, par lequel/laquelle l'agent de post-traitement
est pulvérisé sur la ou chaque surface revêtue de la bande d'acier.
9. Procédé selon l'une quelconque des revendications précédentes, caractérisé en ce que la solution de l'agent de post-traitement est appliquée sur les deux côtés de la
bande d'acier.
10. Procédé selon l'une quelconque des revendications 8 ou 9, caractérisé en ce que l'agent de post-traitement est pulvérisé sous la forme de jets de liquide sur la
ou les surfaces étamées de bande d'acier, sachant que les jets de liquide atteignent
la surface selon une plage angulaire comprise entre +45° et -45° par rapport à la
normale.
11. Procédé selon l'une quelconque des revendications précédentes, caractérisé en ce que la solution de l'agent de post-traitement est compressée après l'application sur
la surface étamée et oxydée de la bande d'acier au moyen de rouleaux compresseurs,
et en ce que la bande d'acier étamée est séchée après la compression de l'agent de post-traitement.
12. Procédé selon la revendication 11, caractérisé en ce qu'un film de faible épaisseur de l'agent de post-traitement est présent en une couche
comprise entre 2 mg/m2 et 30 mg/m2, après la compression de l'agent de post-traitement et le séchage, sur la surface
de la bande d'acier étamée.
13. Procédé selon la revendication 11, caractérisé en ce que l'agent de post-traitement contient du titane, et en ce qu'un film de faible épaisseur de l'agent de post-traitement est présent en une couche
de titane comprise entre 0,5 mg/m2 et 2 mg/m2, après la compression de l'agent de post-traitement contenant du titane et après
le séchage, sur la surface de la bande d'acier étamée.
14. Procédé selon l'une quelconque des revendications précédentes, caractérisé en ce que l'oxydation anodique de la surface étamée de la bande d'acier est effectuée dans
un laps de temps d'anodisation allant de 0,1 à 1,0 seconde, et, de manière préférée,
dans un laps de temps d'anodisation compris entre 0,2 et 0,7 seconde.
15. Bande ou tôle d'acier étamée comprenant une couche de support composée d'une tôle
fine ou la plus fine en acier, d'une couche d'étain déposée sur cette dernière et
d'une couche de surface d'un agent de post-traitement sans chrome, caractérisée en ce qu'une couche d'oxyde est réalisée entre la couche d'étain et la couche de surface de
l'agent de post-traitement, laquelle est constituée essentiellement d'un oxyde d'étain
(SnO2) tétravalent, et en ce que l'agent de post-traitement est choisi parmi des copolymères d'acrylates, des polyméthylsiloxanes
comprenant des chaînes latérales de polyéther, des polyéthers acides, des polymères
comprenant des groupes hétérocycliques et des compositions liquides aqueuses acides,
qui contiennent des anions de fluorure métallique complexes comprenant des cations
bi- à tétravalents et des substances polymères.