(19) |
 |
|
(11) |
EP 2 928 644 B1 |
(12) |
EUROPÄISCHE PATENTSCHRIFT |
(45) |
Hinweis auf die Patenterteilung: |
|
13.04.2016 Patentblatt 2016/15 |
(22) |
Anmeldetag: 21.02.2014 |
|
(51) |
Internationale Patentklassifikation (IPC):
|
(86) |
Internationale Anmeldenummer: |
|
PCT/EP2014/053455 |
(87) |
Internationale Veröffentlichungsnummer: |
|
WO 2015/124204 (27.08.2015 Gazette 2015/34) |
|
(54) |
FINISHVORRICHTUNG UND VERFAHREN ZUR BEARBEITUNG VON WELLENAXIALLAGERN
FINISHING DEVICE AND METHOD FOR MACHINING SHAFT AXIAL BEARINGS
DISPOSITIF DE FINITION ET PROCÉDÉ D'USINAGE DE PALIERS D'ARBRE AXIAUX
|
(84) |
Benannte Vertragsstaaten: |
|
AL AT BE BG CH CY CZ DE DK EE ES FI FR GB GR HR HU IE IS IT LI LT LU LV MC MK MT NL
NO PL PT RO RS SE SI SK SM TR |
(43) |
Veröffentlichungstag der Anmeldung: |
|
14.10.2015 Patentblatt 2015/42 |
(73) |
Patentinhaber: Supfina Grieshaber GmbH & Co. KG |
|
77709 Wolfach (DE) |
|
(72) |
Erfinder: |
|
- SEGER, Martin
77709 Wolfach (DE)
- LAUBLE, Dieter
77709 Oberwolfach (DE)
- HEIZMANN, Jürgen
77709 Wolfach (DE)
- DEGNER, Bernd
78730 Lauterbach (DE)
|
(74) |
Vertreter: DREISS Patentanwälte PartG mbB |
|
Friedrichstrasse 6 70174 Stuttgart 70174 Stuttgart (DE) |
(56) |
Entgegenhaltungen: :
EP-A1- 2 617 522
|
US-A1- 2001 024 927
|
|
|
|
|
|
|
|
|
Anmerkung: Innerhalb von neun Monaten nach der Bekanntmachung des Hinweises auf die
Erteilung des europäischen Patents kann jedermann beim Europäischen Patentamt gegen
das erteilte europäischen Patent Einspruch einlegen. Der Einspruch ist schriftlich
einzureichen und zu begründen. Er gilt erst als eingelegt, wenn die Einspruchsgebühr
entrichtet worden ist. (Art. 99(1) Europäisches Patentübereinkommen). |
[0001] Die Erfindung betrifft eine Finishvorrichtung zur Bearbeitung von Wellenaxiallagern,
insbesondere von Kurbelwellenpasslagern, umfassend einen an einem Maschinengestell
anordenbaren oder angeordneten Halter, an welchem eine Bearbeitungseinheit mit einem
Finishwerkzeug bewegbar gelagert ist, wobei eine Bewegung der Bearbeitungseinheit
mit einer Einstellung eines mittels des Finishwerkzeugs zu bearbeitenden Durchmessers
eines Wellenaxiallagers einhergeht.
[0002] Vorstehend genannte und aus der
US 2001/0024927 A1 bekannte Finishvorrichtungen werden beispielsweise zur Bearbeitung von Kurbelwellenpasslagern
verwendet. Diese Lager weisen einander zugewandte Axiallagerflächen auf, welche radial
innen an eine Umfangsfläche eines Kurbelwellenhauptlagers angrenzen. Zur Anpassung
zumindest an den Innendurchmesser der Axiallagerflächen ist es erforderlich, die Lage
des Finishwerkzeugs so einzustellen, dass das Finishwerkzeug diesen Minimaldurchmesser
nicht unterschreitet. Hierfür muss die Bearbeitungseinheit mit dem Finishwerkzeug
in eine entsprechende Relativposition zu dem zu bearbeitenden Werkstück gebracht werden.
Der damit verbundene Einrichtungsaufwand kann für hohe Losgrößen, also für eine große
Stückzahl von aufeinander folgend zu bearbeitenden, identischen Kurbelwellen akzeptabel
sein; bei kleineren Losgrößen und häufigeren Wechseln zwischen über Losgrößen hinweg
unterschiedlichen Durchmessern ist der Einrichtungsaufwand jedoch störend und begründet
einen erheblichen Anteil an unproduktiven Nebenzeiten.
[0003] Hiervon ausgehend liegt der vorliegenden Erfindung die Aufgabe zugrunde, eine Vorrichtung
und ein Verfahren anzugeben, mit welchen die Bearbeitung von Wellenaxiallagern mit
über Losgrößen hinweg unterschiedlichen Durchmessern vereinfacht wird.
[0004] Diese Aufgabe wird erfindungsgemäß dadurch gelöst, dass zur Bewegung der Bearbeitungseinheit
eine motorische Antriebseinheit vorgesehen ist, welche die Bearbeitungseinheit entlang
einer Zustellachse antreibt.
[0005] Die erfindungsgemäße Finishvorrichtung ermöglicht eine präzise Zustellung der Bearbeitungseinheit
und des Finishwerkzeugs relativ zu einem zu bearbeitenden Werkstück. Auf diese Weise
kann der Aufwand zur Einrichtung einer neuen Losgröße erheblich reduziert werden.
[0006] Eine weitere Reduzierung von Nebenseiten wird dadurch ermöglicht, dass eine Steuereinrichtung
zur Steuerung der Antriebseinheit vorgesehen ist. Dies ermöglicht die Vorgabe von
Sollpositionen, die in Abhängig der Geometrie eines zu bearbeitenden Werkstücks vorgegeben
werden können.
[0007] Besonders bevorzugt ist es, wenn eine Sensoreinrichtung zur Erfassung der Position
der Bearbeitungseinheit entlang der Zustellachse vorgesehen ist. Dies ermöglicht einen
Abgleich zwischen einer Sollposition und einer Istposition der Bearbeitungseinheit
und somit einer Sollposition und einer Istposition eines Finishwerkzeugs relativ zu
einem zu bearbeitenden Werkstück.
[0008] Bei einer vorteilhaften Ausführungsform der Erfindung ist vorgesehen, dass die Sensoreinrichtung
ein erstes Sensorteil umfasst, welches an dem Halter angeordnet ist, und ein zweites
Sensorteil, welches an der Bearbeitungseinheit angeordnet ist, wobei die Sensoreinrichtung
die Relativposition der beiden Sensorteile erfasst. Dies ermöglicht die Erfassung
der Position der Bearbeitungseinheit relativ zu dem Halter unabhängig von der Geometrie
eines zu bearbeitenden Werkstücks.
[0009] Bei einer weiteren Ausführungsform der Erfindung ist vorgesehen, dass die Sensoreinrichtung
einen Abstandssensor zur Erfassung eines Abstands zwischen der Bearbeitungseinheit
und einer Referenzfläche des zu bearbeitenden Werkstücks, insbesondere der Umfangslagerfläche
eines Hauptlagers einer Kurbelwelle, umfasst. Dies ermöglicht eine präzise Positionierung
der Bearbeitungseinheit relativ zu einem zu bearbeitenden Werkstück.
[0010] Bei einer weiteren vorteilhaften Ausführungsform der Erfindung umfasst die Sensoreinrichtung
eine Messeinrichtung zur Messung einer Betriebsgröße der Antriebseinheit. Beispielsweise
kann eine zum Betrieb der Antriebseinheit erforderliche Größe erfasst werden, welche
mit dem Energiebedarf der Antriebseinheit korrespondiert. Auf diese Weise ist es möglich,
ein "Auffahren" der Bearbeitungseinheit auf das zu bearbeitende Werkstück zu erfassen;
ein solches "Auffahren" geht mit einem Anstieg des Energiebedarfs der Antriebseinheit
einher, beispielsweise mit einem Anstieg des Stroms bei einer elektrischen Antriebseinheit
oder mit einem Anstieg des Drucks eines Betriebsmediums einer pneumatischen oder hydraulischen
Antriebseinheit.
[0011] In vorteilhafter Weise umfasst die Finishvorrichtung eine Regelungseinrichtung zur
Regelung der Position der Bearbeitungseinheit entlang der Zustellachse. Dies ermöglicht
einen einfachen Abgleich von Sollpositionen und Istposition der Bearbeitungseinheit.
[0012] Bei einer weiteren vorteilhaften Ausführungsform der Erfindung ist vorgesehen, dass
die Finishvorrichtung einen Oszillationsantrieb umfasst, mittels welchem die Bearbeitungseinheit
in zu der Zustellachse winkliger, insbesondere senkrechter, Richtung oszillierend
antreibbar ist. Auf diese Weise kann einer Relativbewegung zwischen Finishwerkzeug
und zu bearbeitendem Werkstück, welche durch Rotation des zu bearbeitenden Werkstücks
entsteht, eine weitere Bewegung überlagert werden. Auf diese Weise können unterschiedliche
Abschnitte einer Wirkfläche eines Finishwerkzeugs mit der zu bearbeitenden Axiallagerfläche
in Eingriff gebracht werden. Hierbei wird das Finishwerkzeug (in zu der Werkstückachse
tangentialer Richtung) hin und her bewegt.
[0013] Bei dem Finishwerkzeug handelt es sich in vorteilhafter Weise um einen Finishband.
Ein solches Finishband ist vorzugsweise so geführt, dass es im Bereich von zwei einander
zugewandten Axiallagerflächen einen ersten Wirkflächenabschnitt aufweist, welcher
einer ersten Axiallagerfläche zugewandt ist und einen zweiten Wirkflächenabschnitt
aufweist, welcher einer zweiten Axiallagerfläche zugewandt ist.
[0014] Bevorzugt ist es, dass die Finishvorrichtung zwei Bearbeitungseinheiten umfasst,
welche jeweils ein Finishwerkzeug aufweisen, wobei die beiden Finishwerkzeuge zur
Bearbeitung von in Umfangsrichtung zueinander versetzten Oberflächenabschnitten desselben
Wellenaxiallagers ausgebildet sind. Auf diese Weise kann innerhalb einer Werkstückeinspannung
eine Materialabtragsrate verdoppelt werden.
[0015] Es ist denkbar, dass bei Verwendung von zwei Bearbeitungseinheiten diese in ihrem
Abstand zueinander einstellbar sind, sodass Wellenaxiallager mit unterschiedlichen
Durchmessern bearbeitbar sind.
[0016] Bei einer bevorzugten Ausführungsform der Erfindung sind zwei Bearbeitungseinheiten
voneinander unabhängig bewegbar. Hierdurch werden weitere Freiheitsgrade zur Bearbeitung
von Axiallagerflächen geschaffen.
[0017] Vorzugsweise sind zwei Bearbeitungseinheiten an demselben Halter bewegbar gelagert,
wodurch eine Relativpositionierung von zwei Bearbeitungseinheiten vereinfacht wird.
[0018] Vorzugsweise ist für jede der Bearbeitungseinheiten eine eigene Antriebseinheit zum
Antrieb entlang einer eigenen Zustellachse vorgesehen. Diese ermöglicht eine maximale
Flexibilität zur Bearbeitung von variierenden Axiallagerflächendurchmessern.
[0019] Ferner ist es bevorzugt, wenn für jede der Bearbeitungseinheiten eine eigene Sensoreinrichtung
zur Erfassung der jeweiligen Positionen längs der Zustellachse vorgesehen ist. Dies
ermöglicht einen einfachen Abgleich unterschiedlicher Soll- und Istpositionen unterschiedlicher
Bearbeitungseinheiten.
[0020] Die eingangs genannte Aufgabe wird bei einem Verfahren zur Bearbeitung von Wellenaxiallagern,
insbesondere von Kurbelwellenpasslagern, erfindungsgemäß auch dadurch gelöst, dass
unter Verwendung einer vorstehend beschriebenen Finishvorrichtung die Bearbeitungseinheit
mittels der Antriebseinheit entlang der Zustellachse bewegt wird, und zwar während
der Bearbeitung des Wellenaxiallagers mittels des Finishwerkzeugs.
[0021] Das vorstehend genannte Verfahren ermöglicht es, Axiallagerflächen zu bearbeiten,
deren Ringbreite größer ist als die in radialer Richtung wirksame Breite des Finishwerkzeugs,
welche beispielsweise durch die Breite des Finishbands bestimmt ist. Darüber hinaus
ist es vorteilhaft, dass ein Ausgleich von in radialer Richtung variierenden Schnittgeschwindigkeiten
ermöglicht wird; das Finishwerkzeug kann also beispielsweise in einer radial weiter
innen liegenden Position länger verweilen als in einer radial weiter außen liegenden
Position, in welcher bei Rotation des zu bearbeitenden Werkstücks höhere Schnittgeschwindigkeiten
auftreten.
[0022] Schließlich ist es vorteilhaft, wenn das vorstehend genannte erfindungsgemäße Verfahren
zur Erzeugung eines "Überlagerungshubs" verwendet wird. Hierbei wird das Finishwerkzeug
in radialer Richtung der zu bearbeitenden Axiallagerfläche hin und her bewegt, beispielsweise
um eine gewünschte Sollgeometrie zu erzielen und/oder um eine Axiallagerfläche mit
einer Kreuzschliffstruktur herzustellen.
[0023] Weitere Merkmale und Vorteile der Erfindung sind Gegenstand der nachfolgenden Beschreibung
und der zeichnerischen Darstellung eines bevorzugten Ausführungsbeispiels.
[0024] In den Zeichnungen zeigen:
Fig. 1 eine perspektivische Ansicht einer Ausführungsform einer Finishvorrichtung;
und
Fig. 2 die Finishvorrichtung gemäß Fig. 1 bei Ansicht entsprechend einer in Fig. 1
mit II bezeichneten Perspektive.
[0025] Eine Ausführungsform einer Finishvorrichtung ist in den Figuren 1 und 2 aus verschiedenen
Perspektiven dargestellt und insgesamt mit dem Bezugszeichen 10 bezeichnet. Die Finishvorrichtungen
10 dienen zur Finishbearbeitung von Axiallagerflächen eines Werkstücks 12, das insbesondere
als Kurbelwelle ausgebildet ist. Das Werkstück 12 weist eine Wellenachse 14 auf. Während
der Bearbeitung des Werkstücks 12 wird dieses mittels eines schematisch darstellen
Rotationsantriebs 16 angetrieben, sodass das Werkstück 12 um die Werkstückachse 14
rotiert.
[0026] Das Werkstück 12 weist mindestens eine, vorzugsweise zwei zu bearbeitende Axiallagerflächen
18, 20 auf. Die Axiallagerflächen 18 und 20 bilden gemeinsam ein Kurbelwellenpasslager,
welches bei Einbau in einem Verbrennungsmotor zur axialen Lagerung der Kurbelwelle
dient.
[0027] Die Finishvorrichtung 10 ist an einem an sich bekannten und daher nicht dargestellten
Maschinengestell 22 angeordnet. Dabei ist es möglich, dass die Finishvorrichtung 10
fest mit dem Maschinengestell 22 verbunden ist oder aber mittels eines an sich bekannten
und schematisch dargestellten Oszillationsantriebs 24 entlang einer Oszillationsachse
26 oszillierend antreibbar ist. Die Oszillationsachse 26 verläuft vorzugsweise senkrecht
zu der Werkstückachse 14.
[0028] Die Finishvorrichtung 10 umfasst einen insgesamt mit dem Bezugszeichen 28 bezeichneten
Halter. Bei dem dargestellten Ausführungsbeispiel umfasst der Halter 28 eine Horizontalplatte
30, die fest mit einer Vertikalplatte 32 verbunden ist. Der Halter 28 umfasst ferner
einen horizontalen Halteabschnitt 34 zur Anordnung bezogen auf den Halter 28 ortsfester
erster Sensorteile 36 und 38, welche jeweils Teil einer Sensoreinrichtung 40 bzw.
41 sind.
[0029] Die Finishvorrichtung 10 umfasst eine obere Bearbeitungseinheit 42 und eine untere
Bearbeitungseinheit 44. Die obere Bearbeitungseinheit 42 dient zur Führung eines ersten
Finishbands 46, welches so an der oberen Bearbeitungseinheit 42 geführt ist, dass
es in einem Eingriffsbereich mit dem Werkstück 12 mit einem ersten Wirkabschnitt 48
mit der Axiallagerfläche 20 und mit einem zweiten Wirkabschnitt 50 mit der Axiallagerfläche
18 in Eingriff steht.
[0030] Bezogen auf die Umfangsrichtung der Axiallagerflächen 18 und 20 um 180° versetzt
stehen Wirkabschnitte 52 und 54 eines zweiten Finishbands 56 in Eingriff mit den Axiallagerflächen
18 und 20 des Werkstücks 12. Das zweite Finishband 56 ist an der unteren Bearbeitungseinheit
44 geführt.
[0031] Das erste Finishband 46 weist einen in vertikaler gemessenen Abstand 58 zu der Werkstückachse
14 auf. Das zweite Finishband 56 weist einen in vertikaler Richtung zu der Werkstückachse
14 gemessenen Abstand 60 auf. Es ist möglich, dass die Abstände 58 und 60 identisch
eingestellt sind, sodass die Wirkflächen 48 und 52 sowie die Wirkflächen 50 und 54
die Axiallagerflächen 18 und 20 in einem identischen Radienbereich, welcher der Breite
der Finishbänder 46 und 56 entspricht, bearbeitet wird. Es ist jedoch auch denkbar,
die Abstände 58 und 60 voneinander unterschiedlich einzustellen.
[0032] Zur Einstellung der Abstände 58 und 60 umfasst die Finishvorrichtung 10 nachfolgend
beschriebene Antriebseinheiten.
[0033] Eine erste Antriebseinheit 62 ist der oberen Bearbeitungseinheit 42 zugeordnet. Eine
zweite Bearbeitungseinheit 64 ist der unteren Bearbeitungseinheit 44 zugeordnet.
[0034] Die Antriebseinheiten 62 und 64 umfassen jeweils ein Antriebsgehäuse 66, 68 und relativ
zu den Antriebsgehäusen 66, 68 bewegbare Antriebselemente 70 bzw. 72.
[0035] Die Antriebselemente 70, 72 sind jeweils entlang vertikaler Zustellachsen 74, 76
bewegbar. Die freien Enden der Antriebselemente 70 und 72 sind jeweils über ein Gelenkauge
78 bzw. 80 mit der Vertikalplatte 32 des Halters 28 verbunden.
[0036] Die Antriebsgehäuse 66 und 68 der Antriebseinheiten 62 und 64 sind mit jeweils einer
der Bearbeitungseinheiten 42 und 44 verbunden. Das Antriebsgehäuse 66 der Antriebseinheit
62 ist mittels eines sich im Wesentlichen parallel zu dem Antriebselement 70 erstreckenden
Verbindungselements 82 mit einer Vertikalplatte 84 der oberen Bearbeitungseinheit
42 verbunden. Die Vertikalplatte 84 geht in einen Arm 86 der oberen Bearbeitungseinheit
42 über oder ist fest mit dem Arm 86 verbunden.
[0037] In entsprechender Weise ist das Antriebsgehäuse 68 der Antriebseinheit 64 über ein
Verbindungselement 88 mit einer Vertikalplatte 90 der unteren Bearbeitungseinheit
44 verbunden. Die Vertikalplatte 90 geht in einen Arm 92 der unteren Bearbeitungseinheit
44 über oder ist mit dem Arm 92 verbunden.
[0038] Zur Erfassung einer Bewegung einer Bearbeitungseinheit 42, 44 relativ zu dem Halter
28 sind zweite Sensorteile 94, 96 vorgesehen, deren Position in Abhängigkeit der Position
der Bearbeitungseinheiten 42, 44 relativ zu den ersten Sensorteilen 36, 38 variiert.
[0039] Zur Steuerung der Antriebseinheiten 62, 64 ist eine Steuereinheit 98 vorgesehen.
Mittels der Steuereinheit 98 können den Antriebseinheiten 62, 64 Sollposition der
oberen Bearbeitungseinheit bzw. der unteren Bearbeitungseinheit 44 entlang der jeweiligen
Zustellachsen 74, 76 vorgegeben werden. Die Istpositionen der Bearbeitungseinheiten
42, 44 längs der Zustellachsen 74, 76 können mit den Sensoreinrichtungen 40, 41 erfasst
werden.
[0040] Wenn ausgehend von dem in Figur 1 dargestellten Zustand ein Werkstück 12 mit größerem
Durchmesser bearbeitet werden soll, wird die Antriebseinheit 62 der oberen Bearbeitungseinheit
42 so angesteuert, dass das Antriebselement 70 aus dem Antriebsgehäuse 66 herausbewegt
wird. Dies führt dazu, dass das Antriebsgehäuse 66 relativ zum Antriebselement 70
angehoben und über das Verbindungselement 82 und die Vertikalplatte 84 auch die obere
Bearbeitungseinheit 42 angehoben wird.
[0041] Zur Vergrößerung des Abstands 60 wird die untere Bearbeitungseinheit 44 nach unten
bewegt, indem das Antriebselement 72 weiter in das Antriebsgehäuse 68 der zweiten
Antriebseinheit 64 hineinbewegt wird. Hierdurch wird das Antriebsgehäuse 68 der zweiten
Antriebseinheit 64 nach unten bewegt und diese Bewegung über das Verbindungselement
88 auf die Vertikalplatte 90 und auf die untere Bearbeitungseinheit 44 übertragen.
[0042] Die Antriebseinheiten 62 und 64 sind innerhalb einer Vertikalebene angeordnet, welche
senkrecht zu der Werkstückachse 14 verläuft. Dies ermöglicht es, einen insgesamt sehr
schmal bauende Finishvorrichtung 10 zu schaffen, wodurch auf engem Bauraum mehrere
Finishvorrichtungen 10 nebeneinander anordenbar sind. Hierdurch verbleibt seitlich
benachbart zu der Finishvorrichtung 10 Bauraum für andere Werkzeugmaschinenteile.
1. Finishvorrichtung (10) zur Bearbeitung von Wellenaxiallagern, insbesondere von Kurbelwellenpasslagern,
umfassend einen an einem Maschinengestell (22) anordenbaren oder angeordneten Halter
(28), an welchem eine Bearbeitungseinheit (42, 44) mit einem Finishwerkzeug (46, 56)
bewegbar gelagert ist, wobei eine Bewegung der Bearbeitungseinheit (42, 44) mit einer
Einstellung eines mittels des Finishwerkzeugs (46, 56) zu bearbeitenden Durchmessers
eines Wellenaxiallagers einhergeht, dadurch gekennzeichnet, dass zur Bewegung der Bearbeitungseinheit (42, 44) eine motorische Antriebseinheit (62,
64) vorgesehen ist, welche die Bearbeitungseinheit (42, 44) entlang einer Zustellachse
(74, 76) antreibt.
2. Finishvorrichtung (10) nach Anspruch 1, dadurch gekennzeichnet, dass eine Steuereinrichtung (98) zur Steuerung der Antriebseinheit (62, 64) vorgesehen
ist.
3. Finishvorrichtung (10) nach einem der voranstehenden Ansprüche, dadurch gekennzeichnet, dass eine Sensoreinrichtung (40, 41) zur Erfassung der Position der Bearbeitungseinheit
(42, 44) entlang der Zustellachse (74, 76) vorgesehen ist.
4. Finishvorrichtung (10) nach Anspruch 3, dadurch gekennzeichnet, dass die Sensoreinrichtung (40, 41) ein erstes Sensorteil (36, 38) umfasst, welches an
dem Halter (28) angeordnet ist, und ein zweites Sensorteil (94, 96), welches an der
Bearbeitungseinheit (42, 44) angeordnet ist, wobei die Sensoreinrichtung (40, 41)
die Relativposition der beiden Sensorteile erfasst.
5. Finishvorrichtung (10) nach Anspruch 3 oder 4, dadurch gekennzeichnet, dass die Sensoreinrichtung (40, 41) einen Abstandssensor zur Erfassung eines Abstands
zwischen der Bearbeitungseinheit (42, 44) und einer Referenzfläche des zu bearbeitenden
Werkstücks (12), insbesondere der Umfangslagerfläche eines Hauptlagers einer Kurbelwelle,
umfasst.
6. Finishvorrichtung (10) nach einem der Ansprüche 3 bis 5, dadurch gekennzeichnet, dass die Sensoreinrichtung (40, 42) eine Messeinrichtung zur Messung einer Betriebsgröße
der Antriebseinheit (62, 64) umfasst.
7. Finishvorrichtung (10) nach einem der voranstehenden Ansprüche, dadurch gekennzeichnet, dass eine Regelungseinrichtung zur Regelung der Position der Bearbeitungseinheit (42,
44) entlang der Zustellachse (74, 76) vorgesehen ist.
8. Finishvorrichtung (10) nach einem der voranstehenden Ansprüche, dadurch gekennzeichnet, dass die Finishvorrichtung (10) einen Oszillationsantrieb (24) umfasst, mittels welchem
die Bearbeitungseinheit (42, 44) in zu der Zustellachse (74, 76) winkliger, insbesondere
senkrechter, Richtung oszillierend antreibbar ist.
9. Finishvorrichtung (10) nach einem der voranstehenden Ansprüche, dadurch gekennzeichnet, dass die Finishvorrichtung (10) zwei Bearbeitungseinheiten (42, 44) umfasst, welche jeweils
ein Finishwerkzeug (46, 56) aufweisen, wobei die beiden Finishwerkzeuge (46, 56) zur
Bearbeitung von in Umfangsrichtung zueinander versetzten Oberflächenabschnitten desselben
Wellenaxiallagers ausgebildet sind.
10. Finishvorrichtung (10) nach Anspruch 9, dadurch gekennzeichnet, dass die Bearbeitungseinheiten (42, 44) voneinander unabhängig bewegbar sind.
11. Finishvorrichtung (10) nach Anspruch 9 oder 10, dadurch gekennzeichnet, dass die Bearbeitungseinheiten (42, 44) an demselben Halter (28) bewegbar gelagert sind.
12. Finishvorrichtung (10) nach einem der Ansprüche 9 bis 11, dadurch gekennzeichnet, dass für jede der Bearbeitungseinheiten (42, 44) eine eigene Antriebseinheit (62, 64)
zum Antrieb entlang einer eigenen Zustellachse (74, 76) vorgesehen ist.
13. Finishvorrichtung (10) nach einem der Ansprüche 9 bis 12, dadurch gekennzeichnet, dass für jede der Bearbeitungseinheiten (42, 44) eine eigene Sensoreinrichtung (40, 41)
zur Erfassung der jeweiligen Position längs der Zustellachse (74, 76) vorgesehen ist.
14. Verfahren zur Bearbeitung von Wellenaxiallagern, insbesondere von Kurbelwellenpasslagern,
unter Verwendung einer Finishvorrichtung (10) nach einem der voranstehenden Ansprüche,
dadurch gekennzeichnet, dass - während der Bearbeitung des Wellenaxiallagers mittels des Finishwerkzeugs (46,
58) - die Bearbeitungseinheit (42, 44) mittels der Antriebseinheit (62, 64) entlang
der Zustellachse (74, 76) bewegt wird.
1. Finishing apparatus (10) for machining shaft axial bearing surface combinations and
in particular crankshaft thrust bearing surface combinations, comprising a holder
(28), arranged or able to be arranged on a bed (22) of a machine, on which a machining
unit (42, 44) having a finishing tool (46, 56) is mounted to be movable, a movement
of the machining unit (42, 44) being paralleled by a setting of a diameter, to be
machined by means of the finishing tool (46, 56), of a shaft axial bearing surface
combination, characterised in that for the movement of the machining unit (42, 44) there is provided a motive drive
unit (62, 64) which drives the machining unit (42, 44) along an infeed axis (74, 76).
2. Finishing apparatus (10) according to claim 1, characterised that a control means
(98) is provided to control the drive unit (62, 64).
3. Finishing apparatus (10) according to either of the preceding claims, characterised in that a sensor means (40, 41) is provided to sense the position of the machining unit (42,
44) along the infeed axis (74, 76).
4. Finishing apparatus (10) according to claim 3, characterised in that the sensor means (40, 41) comprises a first sensor part (36, 38) which is arranged
on the holder (28) and a second sensor part (94, 96) which is arranged on the machining
unit (42, 44), the sensor means (40, 41) sensing the relative position of the two
sensor parts.
5. Finishing apparatus (10) according to claim 3 or 4, characterised in that the sensor means (40, 41) comprises a distance sensor for sensing a distance between
the machining unit (42, 44) and a reference surface on the workpiece (12) to be machined,
and in particular the circumferential bearing surface of a main bearing surface combination
of a crankshaft.
6. Finishing apparatus (10) according to one of claims 3 to 5, characterised in that the sensor means (40, 41) comprises a measuring means for measuring an operating
variable of the drive unit (62, 64).
7. Finishing apparatus (10) according to one of the preceding claims, characterised in that a regulating means is provided for regulating the position of the machining unit
(42, 44) along the infeed axis (74, 76).
8. Finishing apparatus (10) according to one of the preceding claims, characterised in that the finishing apparatus (10) comprises an oscillatory drive (24) by means of which
the machining unit (42, 44) can be driven in oscillation in a direction at an angle
to, and in particular perpendicular to, the infeed axis (74, 76).
9. Finishing apparatus (10) according to one of the preceding claims, characterised in that the finishing apparatus (10) comprises two machining units (42, 44) which each have
a finishing tool (46, 56), the two finishing tools (46, 56) being adapted to machine
portions of surfaces of the same shaft axial bearing surface combination which are
offset from one another in the circumferential direction.
10. Finishing apparatus (10) according to claim 9, characterised in that the machining units (42, 44) are movable independently of one another.
11. Finishing apparatus (10) according to claim 9 or 10, characterised in that the machining units (42, 44) are mounted to be movable on the same holder (28).
12. Finishing apparatus (10) according to one of claims 9 to 11, characterised in that there is provided for each of the machining units (42, 44) a drive unit (62, 64)
of its own for driving it along an infeed axis (74, 76) of its own.
13. Finishing apparatus (10) according to one of claims 9 to 12, characterised in that there is provided for each of the machining units (42, 44) a sensor means (40, 41)
of its own for sensing its individual position along the infeed axis (74, 76).
14. Method of machining shaft axial bearing surface combinations and in particular crankshaft
thrust bearing surface combinations, using a finishing apparatus (10) according to
one of the preceding claims, characterised in that, during the machining of the shaft axial bearing surface combination by means of
the finishing tool (46, 58), the machining unit (42, 44) is moved along the infeed
axis (74, 76) by means of the drive unit (62, 64).
1. Dispositif de finition (10) destiné à l'usinage de paliers d'arbre axiaux, en particulier
de paliers centraux de vilebrequin, comprenant un support (28) qui est apte à être
disposé ou est disposé sur un bâti de machine (22) et sur lequel une unité d'usinage
(42, 44) comprenant un outil de finition (46, 56) est logée à déplacement, un mouvement
de ladite unité d'usinage (42, 44) allant de pair avec un réglage d'un diamètre d'un
palier axial d'arbre, qui est à usiner au moyen dudit outil de finition (46, 56),
caractérisé par le fait que, pour déplacer ladite unité d'usinage (42, 44), une unité d'entraînement par moteur
(62, 64) est prévue qui entraîne ladite unité d'usinage (42, 44) le long d'un axe
d'avance (74, 76).
2. Dispositif de finition (10) selon la revendication 1, caractérisé par le fait qu'un dispositif de commande (98) pour commander ladite unité d'entraînement (62, 64)
est prévu.
3. Dispositif de finition (10) selon l'une quelconque des revendications précédentes,
caractérisé par le fait qu'un dispositif de capteur (40, 41) pour détecter la position de l'unité d'usinage (42,
44) le long de l'axe d'avance (74, 76) est prévu.
4. Dispositif de finition (10) selon la revendication 3, caractérisé par le fait que ledit dispositif de capteur (40, 41) comprend une première partie de capteur (36,
38) qui est disposée sur ledit support (28) ainsi qu'une deuxième partie de capteur
(94, 96) qui est disposée sur l'unité d'usinage (42, 44), ledit dispositif de capteur
(40, 41) détectant la position relative des deux parties de capteur.
5. Dispositif de finition (10) selon la revendication 3 ou 4, caractérisé par le fait que le dispositif de capteur (40, 41) comprend un capteur de distance destiné à détecter
une distance entre l'unité d'usinage (42, 44) et une surface de référence de la pièce
(12) à usiner, en particulier de la surface d'appui circonférentielle d'un palier
principal d'un vilebrequin.
6. Dispositif de finition (10) selon l'une quelconque des revendications 3 à 5, caractérisé par le fait que le dispositif de capteur (40, 41) comprend un dispositif de mesure destiné à mesurer
une grandeur de fonctionnement de ladite unité d'entraînement (62, 64).
7. Dispositif de finition (10) selon l'une quelconque des revendications précédentes,
caractérisé par le fait qu'un dispositif de réglage destiné à régler la position de l'unité d'usinage (42, 44)
le long de l'axe d'avance (74, 76) est prévu.
8. Dispositif de finition (10) selon l'une quelconque des revendications précédentes,
caractérisé par le fait que le dispositif de finition (10) comprend un mécanisme d'entraînement par oscillations
(24) au moyen duquel l'unité d'usinage (42, 44) peut être entraînée de manière oscillante
dans la direction angulaire, en particulier perpendiculaire, par rapport à l'axe d'avance
(74, 76).
9. Dispositif de finition (10) selon l'une quelconque des revendications précédentes,
caractérisé par le fait que le dispositif de finition (10) comprend deux unités d'usinage (42, 44) qui présentent
chacune un outil de finition (46, 56), les deux outils de finition (46, 56) étant
réalisés pour l'usinage de sections de surface du même palier axial d'arbre décalées
dans la direction circonférentielle les unes par rapport aux autres.
10. Dispositif de finition (10) selon la revendication 9, caractérisé par le fait que les unités d'usinage (42, 44) sont déplaçables l'une indépendamment de l'autre.
11. Dispositif de finition (10) selon la revendication 9 ou 10, caractérisé par le fait que lesdites unités d'usinage (42, 44) sont logées de manière déplaçable sur le même
support (28).
12. Dispositif de finition (10) selon l'une quelconque des revendications 9 à 11, caractérisé par le fait que pour chacune des unités d'usinage (42, 44) est prévue une propre unité d'entraînement
(62, 64) pour l'entraînement le long d'un propre axe d'avance (74, 76).
13. Dispositif de finition (10) selon l'une quelconque des revendications 9 à 12, caractérisé par le fait que pour chacune des unités d'usinage (42, 44) est prévu un propre dispositif de capteur
(40, 41) pour détecter la position respective le long de l'axe d'avance (74, 76).
14. Procédé d'usinage de paliers d'arbre axiaux, en particulier de paliers centraux de
vilebrequin, en utilisant un dispositif de finition (10) selon l'une quelconque des
revendications précédentes, caractérisé par le fait que, durant l'usinage du palier axial d'arbre au moyen de l'outil de finition (46, 58),
ladite unité d'usinage (42, 44) est déplacée au moyen de l'unité d'entraînement (62,
64) le long de l'axe d'avance (74, 76).
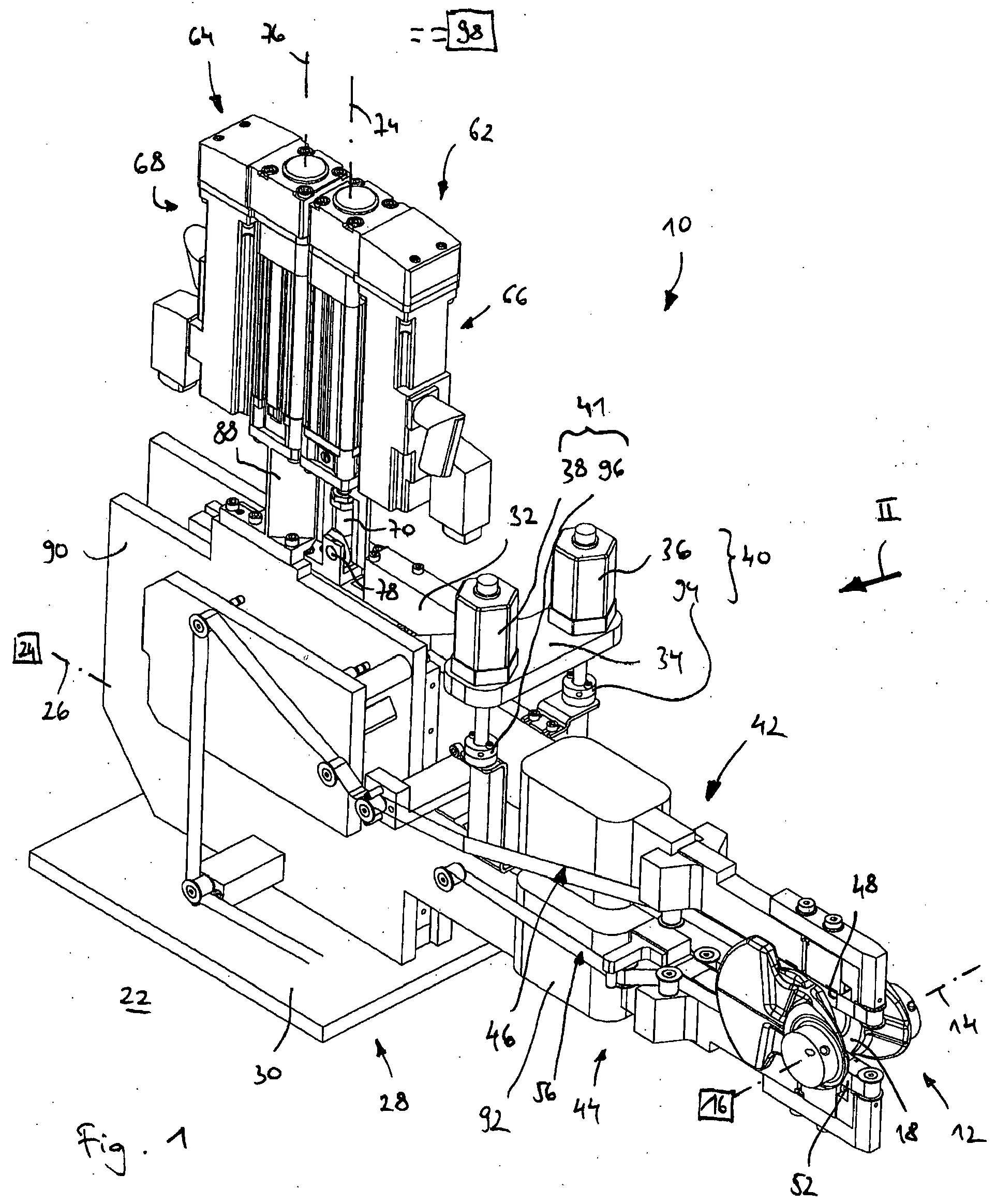
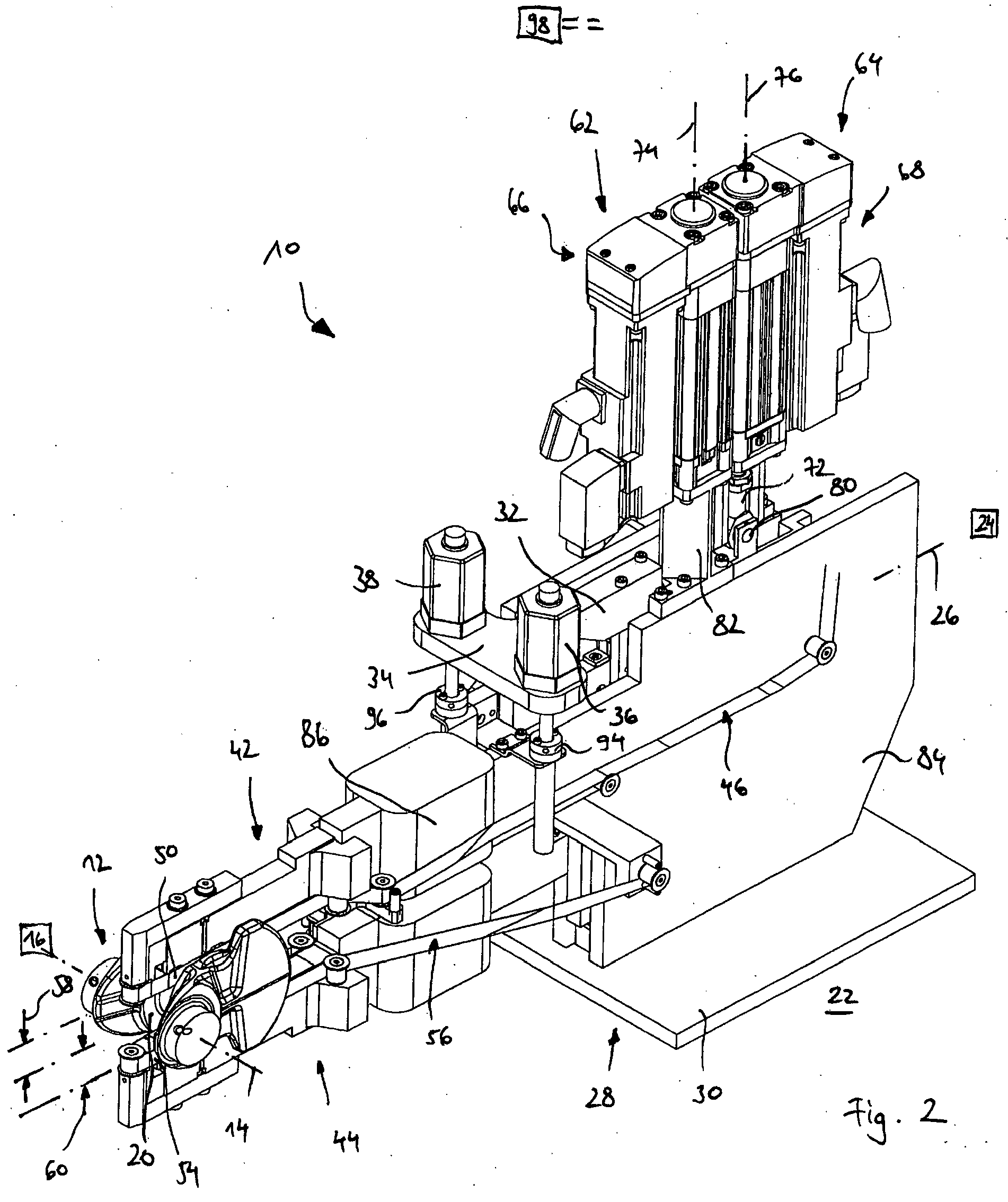
IN DER BESCHREIBUNG AUFGEFÜHRTE DOKUMENTE
Diese Liste der vom Anmelder aufgeführten Dokumente wurde ausschließlich zur Information
des Lesers aufgenommen und ist nicht Bestandteil des europäischen Patentdokumentes.
Sie wurde mit größter Sorgfalt zusammengestellt; das EPA übernimmt jedoch keinerlei
Haftung für etwaige Fehler oder Auslassungen.
In der Beschreibung aufgeführte Patentdokumente