Object of the Invention
[0001] The present invention relates to a tube for a heat exchanger comprising a region
with dimples according to a specific pattern such that it increases the degree of
heat exchange with low pressure drop.
[0002] The use of a tube for a heat exchanger according to the invention in heat exchangers
for EGR (Exhaust Gas Recirculation) systems is of particular interest. The present
invention is also considered of interest for the environment as it increases the efficiency
of the heat exchangers for which it is designed.
Background of the Invention
[0003] Heat exchangers are devices promoting heat transfer between two fluids through an
exchange surface which prevents the mixing of both fluids. The amount of transferred
heat is proportional to the exchange surface and also proportional to the exchange
rate per unit area.
[0004] The heat exchange rate per unit area depends primarily on flow conditions around
the exchange surface and on fluid properties. Given that convective heat transfer
mechanisms are much more efficient than diffusive heat transfer mechanisms, solutions
used in the state of the art seek to enhance convection in the vicinity of the exchange
surface.
[0005] One of the means for increasing convection in the vicinity of the exchange surface
is the use of fins. The most widely used fins are projections in the form of plates
emerging from the surface. Fins have a dual effect on the flow flowing in the vicinity
of the exchange surface, the first effect being an increase in the effective surface
in contact with the fluid since the exchange surface remains the same except for the
area where the fin starts, plus the area on both sides of the fin; and the second
effect being an increase in turbulence in the vicinity of the exchange surface.
[0006] Increasing turbulence enhances convection effects since the occurrence of vortices
having a small characteristic diameter generates movement structures favoring mass
exchange between the vicinity of the exchange surface and regions further away where
the main flow is located, the final result being increased convective heat transport
between the exchange surface and the fluid.
[0007] This clear advantage has the drawback that although heat exchange increases, pressure
drop also increase. When the heat exchange area is formed by tubes through which a
first fluid flows and said tubes are immersed in a second fluid with which it exchanges
heat and which in turn is housed in a shell, pressure drop occur both between shell
inlet and outlet and between tube inlet and outlet.
[0008] A high pressure drop involves the need for higher propulsion energy. The pressure
drop allows establishing, together with heat exchange rate, the overall degree of
efficiency of the heat exchanger. An efficient heat exchanger therefore requires not
only a high heat exchange rate but also low pressure drop.
[0009] A high heat exchange rate allows reducing the volume necessary for housing the exchange
surface for specific heat requirements, for example.
[0010] A particular case of tubes for a heat exchanger that uses fins are those known in
this state of the art as hybrid tubes, fin and tube or fin and plate. Hybrid tubes
are tubes formed by means of sheet metal the shape of which is of a planar configuration,
i.e., according to the section thereof, it has two parallel planar segments laterally
closed by means of respective curved segments.
[0011] The inside of this tube having a planar configuration has a second part formed by
a sheet with several bends forming fins where this sheet is trapped between the two
planar surfaces.
[0012] Such tube is very efficient as regards exchange rate but has specific problems due
to the thermal expansion effect of the inner sheet, for example, which can cause fatigue
in areas where this expansion generates stresses. This is the case of the tube embedment
area, for example, where expansion of the inner part is limited by the embedment.
[0013] An alternative to such tubes is a tube also having a planar configuration containing
dimples on at least one of its faces. Dimples are not as efficient as fins since they
cannot be compacted as much nor can they increase the exchange area to the same extent,
but they have the advantage of not having the expansion problems indicated above and
of increasing tube rigidity.
[0014] The conventional way of manufacturing such tubes is based on a drawn metal sheet
that is subsequently bent according to a longitudinal direction until the tube is
closed. The tube is closed by means of a longitudinally extending weld bead joining
the edges facing one another, for example.
[0015] The presence of dimples increase turbulence and therefore the heat transfer rate.
Planar tubes formed by dimples having various dimple patterns to increase the heat
exchange rate are known.
[0016] Patterns that are modified downstream to take into account flow variations due to
the influence of dimples located upstream are also known. Nevertheless, such patterns
make manufacturing the tube difficult since the same mold cannot be used in stamping
along the entire length of the tube or actuators modifying the depth of the dimples
as the sheet stamping operation for obtaining the tube progresses are required in
machines.
[0017] Although these patterns increase the heat transfer rate, they also increase pressure
drop.
[0018] The present invention relates to a tube incorporating dimples for increasing the
heat transfer rate which allows overcoming the drawbacks identified above using a
dimple pattern combining a high heat exchange rate and a low pressure drop.
Description of the Invention
[0019] The tube for a heat exchanger according to the present invention is a tube having
a flattened configuration comprising a first essentially planar face and a second
essentially planar face parallel to and spaced from the first face. The flattened
configuration of the tube must therefore be interpreted by the presence of the first
planar face and the second planar face arranged parallel to one another and both faces
being connected by side walls. Although the side walls can have any configuration,
the most common embodiments use a configuration in a semicircular segment according
to the section of the tube.
[0020] At least one face has a plurality of dimples configured according to a pattern that
is repeated along the longitudinal direction X-X' of the tube. The longitudinal direction
of the tube is the direction along which the directrix of the tube extends.
[0021] The pattern is configured by means of a plurality of groups of dimple alignments
covering the width of the planar face. The dimples usually have a fillet radius in
the root so that stamping does not generate excessive residual stresses or deformation
does not weaken the sheet. This fillet radius causes a certain spacing between other
dimples or the walls of the tube so the indication that the dimples cover the width
of the planar face must be interpreted to mean that there can be a transition area
or a passage channel between the dimples located on the sides of the planar face and
the walls of the tube.
[0022] The plurality of groups of alignments complies with:
being aligned according to one and the same direction Y-Y' arranged obliquely between
40° and 50° degrees with respect to the longitudinal direction X-X', and where at
least the tube comprises:
- a first group which is formed by two dimples, a first elongated dimple extending according
to the oblique direction Y-Y' aligned with a first point dimple such that a first
flow channel is established between the elongated dimple and the point dimple,
- a second group which is formed by four point dimples, a second point dimple, a third
point dimple, a fourth point dimple and a fifth point dimple, essentially aligned
according to the oblique direction Y-Y', such that a second flow channel is established
between the second point dimple and the third point dimple, a third flow channel is
established between the third point dimple and the fourth point dimple, a fourth flow
channel is established between the fourth point dimple and the fifth point dimple,
- a third group which is formed by two dimples, a sixth point dimple aligned with a
second elongated dimple, extending according to the oblique direction Y-Y', such that
a fifth flow channel is established between the sixth point dimple and the second
elongated dimple,
- a fourth group which is formed by four point dimples, a seventh dimple, an eighth
dimple, a ninth dimple and a tenth dimple, essentially aligned according to the oblique
direction Y-Y', such that a sixth flow channel is established between the seventh
point dimple and the eighth point dimple, a seventh flow channel is established between
the eighth point dimple and the ninth point dimple, an eighth flow channel is established
between the ninth point dimple and the tenth point dimple,
wherein the position of the first flow channel is such that the flow going through
same in the operating mode is mainly transported towards the third flow channel and
the fourth flow channel.
[0023] The pattern contains elongated dimples and point dimples. The elongated dimples have
a preferred direction. When a group of dimples is indicated as being aligned in a
specific direction, it must be interpreted as the elongated dimples extending with
the orientation of the alignment, and furthermore the axis along which they extend
also passes through the locations of the point dimples except for possible minor deviations.
[0024] The pattern formed by each group which is formed by the plurality of dimples has
an oblique orientation Y-Y' towards one and the same side. This orientation leads
to the existence of speed components that are also oblique but does not reorient the
entire flow in this direction. The strategic position of passage sites with continuity
between consecutively arranged groups of dimples generates preferred passage channels
oriented either in the longitudinal direction or even in the oblique direction but
with an opposite inclination with respect to the oblique direction Y-Y' according
to the symmetry defined by the longitudinal axis X-X'.
[0025] Alternating one oblique direction and another increases local turbulence, in turn
allowing significant flow through the channels thus identified. The state of the art
teaches that the existence of a large number of dimples increases turbulence but reduces
the effective section of the tube since they are projections that penetrate the tube,
increasing resistance to passage.
[0026] The special configuration according to the present invention maintains a large number
of dimples having the effect of a high degree of turbulence, but it does not significantly
reduce the effective section since the formation of channels as established according
to the particular dimple pattern according to the invention maintains a flow with
low pressure drop since the flow finds preferred passage channels.
[0027] The formation of preferred passage channels depends not only on the relative position
of the space between dimples downstream of a specific channel but also on the influence
of other surrounding dimples. The final behavior of a specific dimple design cannot
be predicted due to this strong link between neighboring dimples both laterally and
in both the downstream and upstream flow direction, and much less so when the use
of a pattern which is periodically reproducible along the length of the tube is of
interest such as the case where there are changes from one pattern to the next in
the downstream flow.
[0028] The only way to determine if a pattern complies with efficiency objectives, i.e.,
high heat transfer with few losses, is by flow simulation in a tube incorporating
the proposed pattern. This simulation can be carried out by means of numerical models
(CFD (Computational Fluid Dynamics) simulations), for example. The simulations allow
carrying out numerical experiments assessing heat transfer and flow behavior where,
in contrast, comparison with other known patterns never allows extrapolating the results.
[0029] The pattern object of the present invention has been proven to efficiently solve
the described drawbacks. The combination of a distribution of groups of dimples in
one direction combined with the channels formed between consecutively arranged sets
has been proven to have an perturbing influence on the surrounding flow extending
a smaller distance than those known in the state of the art according to the direction
perpendicular to the plane on which the dimples are arranged. This allows the symmetrical
arrangement on both opposite faces of the tube to continue to maintain the increase
in heat transfer by pattern shown by the use of a pattern on a single face; i.e.,
the flow modified by the pattern on one face does not negatively interfere with the
flow modified by the dimple pattern of the opposite face, something that does occur
with other patterns when they are located facing one another.
[0030] The configuration of the pattern proposed by the invention causes vortices to be
generated downstream of the dimples which are then homogenized as a result of the
fluid flow established through specific preferred channels that are generated with
the spaces between dimples. Particularly, an S-shaped or similarly shaped path with
vortices is formed, successfully increasing heat transfer such that it makes up for
the pressure drop resulting from the dimples.
Description of the Drawings
[0031] The foregoing and other features and advantages of the invention will be more clearly
understood based on the following detailed description of a preferred embodiment provided
only by way of illustrative and non-limiting example in reference to the attached
drawings.
Figure 1 shows a plan view of a tube incorporating along its length X-X' an alignment
of patterns according to one embodiment of the invention.
Figure 2 shows a Nusselt number variation map for determining the increase in heat
transfer on the surface incorporating the plurality of patterns according to the embodiment
shown in Figure 1 in comparison with the heat transfer if this were to occur only
by conduction.
Figure 3 shows a tube where both flattened faces have a pattern such as that of the
example shown in Figure 1, i.e., repeated along the length of the tube. This figure
shows the two patterns being superimposed on one another, the pattern of the visible
face being shown by means of continuous lines and the pattern of the opposite non-visible
face being shown by means of dotted lines.
Detailed Description of the Invention
[0032] According to the first inventive aspect, the present invention relates to a tube
for a heat exchanger showing high convective heat transfer without significant pressure
drop. The configuration of the tube is planar, i.e., formed by two laterally connected
parallel planar surfaces where there is a plurality of dimples according to a specific
pattern located on one or both planar faces.
[0033] Figure 1 shows a tube according to an embodiment having a flattened configuration.
In this embodiment, the pattern shows a plurality of dimples (A, B, 1, 2, 3, 4, 5,
6, 7, 8, 9, 10) configured according to a pattern that is repeated along the longitudinal
direction X-X' of the tube. Direction X-X' is the longitudinal direction of the tube.
[0034] The group of dimples can be repeated along the length of the tube as many times as
necessary.
[0035] The pattern is configured by means of a plurality of groups of dimple alignments
covering the width of the planar face, with the understanding that there is a fillet
radius between the side dimples and the edge. The plurality of groups of alignments
are aligned according to one and the same direction Y-Y' arranged obliquely between
40° and 50° degrees with respect to the longitudinal direction X-X'. In this embodiment
shown in Figure 1, the angle of the oblique axis Y-Y' is 45 degrees.
[0036] Particularly, the pattern is formed by at least four groups.
[0037] The first group is formed by two dimples (A, 1), a first elongated dimple (A) extending
according to the oblique direction Y-Y' aligned with a first point dimple (1) such
that a first flow channel (C1) is established between the elongated dimple (A) and
the point dimple (1).
[0038] The flow channel is a gap between the dimples, i.e., the first elongated dimple (A)
and the first point dimple (1). A flow channel will be understood hereinafter as such
gaps between dimples.
[0039] The flow can go through the position of a dimple since said dimple does not reach
the opposite wall of the tube. Nevertheless, it imposes oblique speed components.
The passage channels are not subjected to this imposition that laterally diverts part
of the flow and allows recovering either a longitudinal trajectory or even also an
oblique trajectory but with an inclination opposite that of the Y-Y' axis with respect
to the X-X' axis.
[0040] The second group is formed by four point dimples, a second point dimple (2), a third
point dimple (3), a fourth point dimple (4) and a fifth point dimple (5), essentially
aligned according to the oblique direction Y-Y', such that a second flow channel (C2)
is established between the second point dimple (2) and the third point dimple (3),
a third flow channel (C3) is established between the third point dimple (3) and the
fourth point dimple (4), a fourth flow channel (C4) is established between the fourth
point dimple (4) and the fifth point dimple (5).
[0041] As indicated above, the second channel (C2), the third channel (C3) and the fourth
channel (C4) do not have to be fed completely by the channels arranged upstream, but
they can also receive flow from the main flow of the tube. Such a complex response
of the flow to a specific pattern hence arises. In this particular case, the way to
align the different flow channels formed between dimples determining different effects
on the flow as will be identified below when describing all the elements forming the
pattern is of special interest.
[0042] The third group is formed by two dimples (6, B), a sixth point dimple (6) aligned
with a second elongated dimple (B), extending according to the oblique direction Y-Y',
such that a fifth flow channel (C5) is established between the sixth point dimple
(6) and the second elongated dimple (B).
[0043] The fourth group is formed by four point dimples, a seventh dimple (7), an eighth
dimple (8), a ninth dimple (9) and a tenth dimple (10), essentially aligned according
to the oblique direction Y-Y', such that a sixth flow channel (C6) is established
between the seventh point dimple (7) and the eighth point dimple (8), a seventh flow
channel (C7) is established between the eighth point dimple (8) and the ninth point
dimple (9), an eighth flow channel (C8) is established between the ninth point dimple
(9) and the tenth point dimple (10).
[0044] Having identified the third group and the fourth group, it is important to highlight
the similarity of these groups with the first and second groups. Nevertheless, this
similarity is not by means of a ratio of symmetry since they maintain the inclination
in the same direction, nor is it by means of ratio of repetition since the elongated
dimple (B) in the third group is located downstream instead of upstream or at the
start of the alignment as occurs in the first group.
[0045] In other words, as a result the alignment of all the groups follows the same inclination
but the particular alignments of the channels existing between dimples according to
the flow direction do not. Although a channel is formed by the passage between two
dimples, the channel is considered oriented where the orientation is the direction
perpendicular to the line connecting the centroids of both point dimples. Generally,
the orientation of the channel will be the direction perpendicular to the line connecting
both dimples where said connection is between the regions closest to one another.
[0046] In the pattern shown in Figure 1, it is observed that the position of the first flow
channel (C1) is such that the flow going through same in the operating mode is mainly
transported towards the third flow channel (C3) and the fourth flow channel (C4).
This branching has an effect on the way in which half the pattern arranged downstream
formed by the third and fourth groups is fed.
[0047] It has been pointed out that the four groups have an oblique orientation and the
channels formed between dimples establish speed components with transverse components
giving rise to oblique flows but with an inclination opposite the Y-Y' direction.
In this embodiment, it is observed that in the second group formed by four point dimples
essentially aligned according to the oblique direction Y-Y', the first pair of dimples
formed by the second point dimple (2) and third point dimple (3) is aligned according
to the oblique direction Y-Y', the second pair of dimples formed by the fourth point
dimple (4) and the fifth point dimple (5) is aligned according to the oblique direction
Y-Y'; and the alignment of the first pair and the alignment of the second pair are
misaligned a specific distance despite being parallel.
[0048] This misalignment is shown in Figure 1 by means of two close parallel lines Y-Y'.
The technical effect is a change in orientation of the third channel (C3) causing
a higher degree of inclination in the direction opposite the inclination of the axis
Y-Y' so that a higher flow rate is directed towards the fifth channel (C5) which is
located close to the side opposite the side which tends to divert the inclination
of the axis Y-Y' imposed on all the groups of dimples. This fifth channel (C5) mainly
feeds the passage through the remaining channels located downstream resulting in greater
flow uniformity through all the dimples such that the largest possible exchange area
is used.
[0049] This same technical effect is achieved with the configuration of the fourth group
of point dimples, which are essentially aligned according to the oblique direction
Y-Y'. The first pair of dimples formed by the seventh dimple (7) and the eighth dimple
(8) is aligned according to the oblique direction Y-Y', the second pair of dimples
formed by the ninth dimple (9) and the tenth dimple (10) is aligned according to the
oblique direction Y-Y'; and the alignment of the first pair and the alignment of the
second pair are misaligned despite being parallel.
[0050] This configuration makes homogenizing the flow easier when the pattern is periodically
repeated downstream.
[0051] Generating preferred paths according to an oblique direction with an inclination
opposite that established by the axis Y-Y' is enhanced by the condition that the first
flow channel (C1), the third flow channel (C3) and the fifth flow channel (C5) are
essentially aligned. This preferred path provides a flow reaching even the side opposite
the side on which the inclination of the axis Y-Y' offers the bias thereof.
[0052] This configuration with the alignment of three channels, the first flow channel (C1),
the third flow channel (C3) and the fifth flow channel (C5), also contributes to flow
homogenization when the pattern is periodically repeated downstream.
[0053] The described pattern can also be configured as shown in Figures 1 and 3, such that
there is an alignment between the first channel (C1), the fourth channel (C4) and
the eighth channel (C8). These three channels form a preferred path for longitudinal
guiding of the flow so that it does not tend to keep excessively towards the outside
of the pattern, the side wall of the tube. In the alignment of these three channels
(C1, C4, C8), the elongated dimple (B) of the third group is interposed between the
fourth channel (C4) and the eighth channel (C8). Nevertheless, this interposition
does not prevent the effect of the alignment since, as indicated above, the flow reaching
a channel is fed not only by the flow from channels arranged upstream but also by
the main flow of the tube.
[0054] Given that the preferred path formed by the alignment of channels is configured between
dimples, this path is undulated and enhances vorticity generation, having as an immediate
consequence an increase in the degree of heat transfer with the surface of the tube.
[0055] Additionally, the pattern according to this same embodiment greatly enhances the
creation of preferred paths on the side opposite the side on which the inclination
of the axis Y-Y' offers the bias thereof, establishing the alignment of the second
channel (C2), the fifth channel (C5) and the sixth channel (C6).
[0056] In this same example, the second point dimple (2), the fifth point dimple (5), the
seventh point dimple (7) and the tenth point dimple (10) are widened in the direction
transverse to the oblique direction Y-Y'. The technical effect of this widening is
the prolongation of the dimples towards the sides of the tube so that the main flow
does not seek preferred paths for passage through these sides and is concentrated
on the segment with dimples for increasing heat exchange.
[0057] In this same embodiment, the pattern shown in Figure 1 is repeated on the opposite
face. It has been proven by means of numerical simulation that pressure drop due to
the inclusion of a dimple pattern on one face, when comparing said pressure drop with
that obtained in an embodiment in which only one face of the tube has a dimple pattern,
is not greater than two-fold even when the projection according to a plane transverse
to the tube shows that the dimples have a depth reducing the section on both faces
to one third. In other words, the heat transfer:pressure drop ratio is more favorable
if there is a dimple pattern on both faces of the tube than if there is a pattern
on only one face.
[0058] This means that flow perturbations generated by the dimples on one face do not have
a negative influence on the pressure drop in the other face. This influence will be
even less with sections in which the depth of the dimples is proportionally less than
that indicated.
[0059] Figure 2 depicts the Nusselt number value on the surface of the tube, a high Nusselt
number value being observed homogenously for all the dimples. This indicates that,
for the position corresponding to a dimple, there is a large increase in heat transfer
on the surface in comparison with the heat transfer that occurs only by conduction,
and all this with reduced pressure drop.
[0060] Said Nusselt number value is obtained by means of the following ratio:
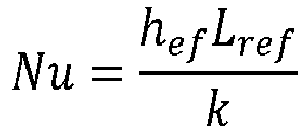
where
Lref is the hydraulic diameter of the tube,
k is the conductivity of said tube and
hef is the film coefficient value, or convective heat transfer coefficient according
to the ratio:
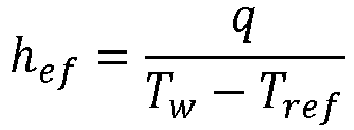
where q is the thermal power transferred in the convective process,
Tw is the wall temperature of the tube and
Tref is a reference temperature value which corresponds to the temperature at the hot
gas inlet of the tube.
[0061] In the example shown in Figure 2, 6.75 mm has been used as the value of the hydraulic
radius
Lref.
[0062] In the example shown in Figure 2, 673.15 K has been used as the reference temperature
value
Tref.
[0063] The figure therefore shows the distribution of Nusselt number values as a function
of the heat transfer that occurs with the passage of a hot gas flow through the tube,
the direction of which is also shown in the figure.
[0064] A dimple pattern of these characteristics results in a highly efficient tube when
it is part of a heat exchanger, according to the transferred thermal power values
as demonstrated by the Nusselt number values represented.
[0065] Figure 3 shows a tube where both flattened faces have a pattern such as that of the
example shown in Figure 1 which is repeated along the length of the tube. This figure
shows the two patterns being superimposed on one another, the pattern of the visible
face is shown by means of continuous lines and the pattern of the opposite non-visible
face is shown by means of dotted lines. To make identifying the dimples on both faces
easier, the reference numbers of the visible face are located on each dimple whereas
the numbers of the dimples located on the non-visible face are located outside the
area occupied by the depiction of the tube.
[0066] The pattern of the first face and the pattern of the second face are distributed
longitudinally such that they extend the same length. In this case, it is not only
because the dimples have the same size, but because the distribution shown on both
faces takes up the same length.
[0067] The pattern of the first face and the pattern of the second face are positioned such
that the end of the first elongated dimple (A) located closest to the central axis
of the tube of the first face and the end of the second elongated dimple (B) located
closest to the central axis of the tube of the second face overlap one another according
to a projection on a plane parallel to both faces. In this manner, flow perturbations
due to the presence of dimples on one face has been shown to not significantly affect
the flow modified by the presence of dimples on the opposite face.
1. A tube for a heat exchanger having a flattened configuration comprising a first essentially
planar face and a second essentially planar face parallel to and spaced from the first
face; both faces being connected by side walls where at least one face has a plurality
of dimples (A, B, 1, 2, 3, 4, 5, 6, 7, 8, 9, 10) configured according to a pattern
that is repeated along the longitudinal direction X-X' of the tube, where this pattern
is configured by means of a plurality of groups of dimple alignments covering the
width of the planar face, aligned according to one and the same direction Y-Y' arranged
obliquely between 40° and 50° degrees with respect to the longitudinal direction X-X',
and where it at least comprises:
- a first group which is formed by two dimples (A, 1), a first elongated dimple (A)
extending according to the oblique direction Y-Y' aligned with a first point dimple
(1) such that a first flow channel (C1) is established between the elongated dimple
(A) and the point dimple (1),
- a second group which is formed by four point dimples, a second point dimple (2),
a third point dimple (3), a fourth point dimple (4) and a fifth point dimple (5),
essentially aligned according to the oblique direction Y-Y', such that a second flow
channel (C2) is established between the second point dimple (2) and the third point
dimple (3), a third flow channel (C3) is established between the third point dimple
(3) and the fourth point dimple (4), a fourth flow channel (C4) is established between
the fourth point dimple (4) and the fifth point dimple (5),
- a third group which is formed by two dimples (6, B), a sixth point dimple (6) aligned
with a second elongated dimple (B), extending according to the oblique direction Y-Y',
such that a fifth flow channel (C5) is established between the sixth point dimple
(6) and the second elongated dimple (B),
- a fourth group which is formed by four point dimples, a seventh dimple (7), an eighth
dimple (8), a ninth dimple (9) and a tenth dimple (10), essentially aligned according
to the oblique direction Y-Y', such that a sixth flow channel (C6) is established
between the seventh point dimple (7) and the eighth point dimple (8), a seventh flow
channel (C7) is established between the eighth point dimple (8) and the ninth point
dimple (9), an eighth flow channel (C8) is established between the ninth point dimple
(9) and the tenth point dimple (10),
where the position of the first flow channel (C1) is such that the flow going through
same in the operating mode is mainly transported towards the third flow channel (C3)
and the fourth flow channel (C4).
2. The tube according to claim 1, where in the second group formed by four point dimples
essentially aligned according to the oblique direction Y-Y', the first pair of dimples
formed by the second point dimple (2) and third point dimple (3) is aligned according
to the oblique direction Y-Y', the second pair of dimples formed by the fourth point
dimple (4) and the fifth point dimple (5) is aligned according to the oblique direction
Y-Y'; and the alignment of the first pair and the alignment of the second pair are
misaligned a specific distance despite being parallel.
3. The tube according to claim 1 or 2, where in the fourth group formed by four point
dimples essentially aligned according to the oblique direction Y-Y', the first pair
of dimples formed by the seventh dimple (7) and the eighth dimple (8) is aligned according
to the oblique direction Y-Y', the second pair of dimples formed by the ninth dimple
(9) and the tenth dimple (10) is aligned according to the oblique direction Y-Y';
and the alignment of the first pair and the alignment of the second pair are misaligned
despite being parallel.
4. The tube according to any of the preceding claims, where the first flow channel (C1),
the third flow channel (C3) and the fifth flow channel (C5) are essentially aligned.
5. The tube according to any of the preceding claims, where the first flow channel (C1),
the fourth flow channel (C4) and the eighth flow channel (C8) are essentially aligned.
6. The tube according to any of the preceding claims, where the second flow channel (C2),
the fifth flow channel (C5) and the sixth flow channel (C6) are essentially aligned.
7. The tube according to any of the preceding claims, where the second point dimple (2),
the fifth point dimple (5), the seventh point dimple (7) and the tenth point dimple
(10) are widened in the direction transverse to the oblique direction Y-Y'.
8. The tube according to any of the preceding claims, where the tube has one and the
same pattern on the first face and the second face.
9. The tube according to any of the preceding claims, where it comprises on a first flattened
face one or more patterns distributed along the length of the tube and comprises on
a second flattened face, the opposite face, one or more patterns distributed along
the length of the tube, and where
- the pattern of the first face and the pattern of the second face are distributed
longitudinally such that they extend with the same length,
- the pattern of the first face and the pattern of the second face are positioned
such that the end of the first elongated dimple (A) located closest to the central
axis of the tube of the first face and the end of the second elongated dimple (B)
located closest to the central axis of the tube of the second face overlap one another
according to a projection on a plane parallel to both faces.
10. A heat exchanger comprising one or more tubes according to any of the preceding claims.