BACKGROUND OF THE INVENTION
[0001] The present invention relates to footwear and more particularly to a sole assembly
for an article of footwear.
[0002] Because footwear is so ubiquitous, it is easy to underestimate the complexity of
the engineering required to meet the ever-increasing demands placed on footwear. This
is particularly true with respect to performance footwear intended for use in high
performance applications, such as sports and other athletic endeavors.
[0003] Running shoes are one of the most advanced types of footwear. Running is a demanding
activity in which footwear plays an important role. It is important for running shoes
to meet high technical specifications for cushioning and energy return, while still
being light weight and highly durable. One of the roles of running shoes is to protect
the runner's body from excessive local loads generated during the ground contact phase
of the stride. Elastomeric foams are an example of materials that are utilized in
the sole of the shoe to absorb some of the impact energy of the collision between
the foot and the ground. Typically even greater forces are generated during the propulsion
phase of contact, when the runner is pushing against the ground to lift herself up
into the air. These forces are applied by the forefoot of the runner. The primary
role of the cushioning materials under the forefoot in this phase of the stride is
not to reduce these forces, but to reduce local peak pressures by conforming to the
shape of the foot. The sole under the forefoot also performs a secondary action by
compressing and decompressing in response to the runner's stride dynamics.
[0004] Typical shoe constructions create a layer of non-stretch fabric cemented to the sole
located under the runner's foot. Commonly in athletic footwear construction, the upper
is fitted onto a last to form it into the desired three dimensional shape, and then
the bottom of the upper is closed with a flat piece that is roughly the shape of the
bottom of the last. This can be done with a variety of techniques including board
lasting, slip lasting, and strobel stitching. The closing stitch in a strobel-stitched
bottomed upper can be realized, for example, with a zigzag stitch or a strobel-stitch
from a Strobel stitching machine. The "Strobel Board" in this technique can be made
of many materials, typically textiles (non-wovens, wovens, knit). One typical requirement
for a strobel board is that it maintains the shape of the upper; ideally the board
does not stretch appreciably, particularly in the fore-aft direction. This relatively
rigid layer limits the ability of the shoe to conform to the runner's foot at the
loads typically applied during running.
[0005] A conventional running shoe will often include an inner sole (also referred to as
an "insole," a "footbed" or a "sockliner") that is positioned within the foot-receiving
cavity in the upper above the strobel board. The inner sole is typically manufactured
from ethylene vinyl acetate or "EVA". The inner sole typically enhances comfort because
it provides a layer of cushioning material that is directly below the foot above the
relatively rigid strobel board. In some applications, a thin foam layer is positioned
above the strobel board and below the inner sole. The primary purpose of this thin
foam layer is to improve the local pressure distribution of the wearer's foot to the
sole of the shoe. For example, a thin (e.g. 1-3 mm) sheet of foam (often EVA) can
be laminated to the textile of the strobel board to form a foam-strobel board laminate.
Experience has revealed that the laminated foam layer can provide a degree of improved
comfort. Regardless of whether the sole includes an inner sole and/or a strobel board
laminate, conventional sole constructions that include only EVA and other similar
cushioning materials above the strobel board have a limited ability to create a truly
comfortable platform. This deficiency arises for a number of reasons, including thickness
limitations of the foam layer, mechanical stiffness property limitations of the foam
layer, mechanical breakdown (particularly with respect to non-durable foams) and/or
compression limitations of the foam layer imparted by lamination of the foam layer
to non-stretch strobel material. For example, constructions that include only a foam-strobel
board laminate are too thin to adequately conform to the shape of the forefoot during
the propulsion phase of the running stride when typically the highest ground reaction
forces are generated. Quite simply, there isn't enough thickness/material to account
for total impact deformation such that the forefoot (or a portion thereof) will "bottom
out" on the underlying strobel board. Further, the strobel does not extend to the
full width of the forefoot, so the foam-strobel laminate does not cover the full contract
area of the foot. As another example, with constructions that include an inner sole
of conventional EVA foam (alone or combined with a foam-strobel board laminate), the
inner sole (and foam-strobel board laminate) suffers from irreversible plastic deformation
over time such that it is unable to adequately rebound. As a result, a construction
incorporating conventional EVA foam above the strobel board will either be too thin
to fully conform to the forefoot under peak load or be so thick that the permanent
compression set caused by repeated loading will materially change the fit of the shoe.
SUMMARY OF THE INTENTION
[0006] The present invention provides a footwear construction having a strobel-stitched
bottomed upper and a sole assembly with a topsole disposed above the strobel board.
The topsole is manufactured from a foam having an average modulus at a stress of 535
kilopascals (kPa) of from about 750 to about 950, about 800 to about 950, about 850
to about 950, or about 875 to about 950 kPa. The foam also has an energy efficiency
of at least about 78%, at least about 80%, or at least about 82%. Moreover, the foam
has a dynamic compression set of less than about 10%, less than about 8%, or less
than about 6%.
[0007] The topsole may extend beyond the strobel board, for example, to cover the entire
area that is loaded by the forefoot. In one embodiment, the topsole extends beyond
the periphery of the strobel board to cover the strobel stitching through the forefoot
region. In another embodiment, the topsole extends the full width of the last in the
forefoot region. In yet another embodiment, the topsole extends the full length and
width of the last through the forefoot, arch and heel regions.
[0008] In various embodiments, the topsole is laminated to the strobel board. The topsole
typically has an average thickness of from about 1mm to about 10mm, about 2mm to about
7mm, or about 2mm to about 5mm, in the forefoot region. It is to be appreciated that
thickness of the topsole may be uniform or may vary, based e.g., on configuration
of the footwear, the end user, etc. For example, the topsole may be thicker in the
forefoot region than in the arch region and the heel region.
[0009] In one embodiment, the footwear construction includes a sole assembly having an outsole
and a midsole disposed below the strobel board, and a topsole and inner sole disposed
above the strobel board. The midsole may be manufactured from conventional midsole
foam, such as EVA or polyurethane ("PU"). The thickness of the midsole may vary from
application to application, but is typically in the range of about 6mm to about 30mm
in the forefoot region and in the range of about 8mm to about 35mm in the heel region.
The inner sole may be manufactured from conventional inner sole foam, such as EVA
or PU, typically, having a thickness of between about 3mm and about 7mm.
[0010] In one embodiment, the topsole varies in thickness from region to region. In one
implementation, the topsole may be thicker in the forefoot region than in the arch
region and the heel region. The thickness of the topsole may be in the range of about
2mm to about 10mm in the forefoot region, in the range of about 1mm to about 7mm in
the arch region and in the range of about 1mm to about 7mm in the heel region.
[0011] In one embodiment, the strobel board may define an opening that allows more direct
interaction between the topsole and the sole components below the strobel board, such
as a midsole. The size, shape and configuration of the opening may vary. The opening
may extend through the forefoot, arch and heel region. Alternatively, the opening
may be defined in the forefoot region. In another alternative, the strobel board may
define multiple openings, such as one in the forefoot region and one in the heel region.
In some implementations, the material of the topsole may extend through the opening
or openings in the strobel board. In implementations of this nature, the midsole may
define one or more recesses intend to receive the topsole material that extends downwardly
through the strobel board.
[0012] In another aspect, the present invention provides a method for manufacturing an article
of footwear including the general steps of forming an upper, bottoming the upper using
a strobel board, affixing a sole to the undersurface of the strobel board and inserting
a topsole into the upper above strobel board, wherein the topsole is manufactured
from foam having an average modulus at a stress of 535 kPa of between about 750 and
950 kPa and an energy efficiency of at least about 78% and a dynamic compression set
of less than about 10%. The method may include in the step of laminating the topsole
to the strobel board. The laminating step may include molding the foam directly onto
the strobel board or it may include joining the topsole to the strobel board using
adhesive. The topsole may be laminated to the strobel board before or after the strobel
board is joined to the upper. The method may also include the step of defining an
opening in strobel board. The topsole may extend into and/or through the opening in
the strobel board. The method may also include the step of varying the thickness of
the topsole in different regions.
[0013] The present invention provides a footwear construction that provides high performance
and enhanced comfort. The topsole is manufactured from foam that provides comfort
and support characteristics believed to be unavailable in conventional strobel construction.
Given the physical characteristics of the topsole foam, the topsole (or topsole/inner
sole combination) can be manufacture with sufficient thickness to conform to the shape
of the forefoot even during the propulsion phase of the running stride without concern
about premature break-down or excessive compression set. The topsole can be incorporating
into the article of footwear in various ways, thereby providing flexibility in the
design and manufacture of footwear. If desired, the topsole may extend downwardly
through an opening in the strobel board to accommodate additional topsole material.
[0014] These and other objects, advantages, and features of the invention will be more fully
understood and appreciated by reference to the description of the current embodiment
and the drawings.
[0015] Before the embodiments of the invention are explained in detail, it is to be understood
that the invention is not limited to the details of operation or to the details of
construction and the arrangement of the components set forth in the following description
or illustrated in the drawings. The invention may be implemented in various other
embodiments and of being practiced or being carried out in alternative ways not expressly
disclosed herein. Also, it is to be understood that the phraseology and terminology
used herein are for the purpose of description and should not be regarded as limiting.
The use of "including" and "comprising" and variations thereof is meant to encompass
the items listed thereafter and equivalents thereof as well as additional items and
equivalents thereof. Further, enumeration may be used in the description of various
embodiments. Unless otherwise expressly stated, the use of enumeration should not
be construed as limiting the invention to any specific order or number of components.
Nor should the use of enumeration be construed as excluding from the scope of the
invention any additional steps or components that might be combined with or into the
enumerated steps or components. Any reference to claim elements as "at least one of
X, Y and Z" is meant to include any one of X, Y or Z individually, and any combination
of X, Y and Z, for example, X, Y, Z; X, Y; X, Z ; and Y, Z.
BRIEF DESCRIPTION OF THE DRAWINGS
[0016]
Fig. 1 is a perspective view of an article of footwear incorporating a topsole in
accordance with an embodiment of the present invention.
Fig. 2 is an exploded view of the article of footwear.
Fig. 3 is a sectional view of the article of footwear taken along line 3-3 of Fig.
1.
Fig. 4A is a top view of the sole assembly of the article of footwear with portions
removed.
Fig. 4B is a section view of the article of footwear taken along line 4B-4B of Fig.
4A.
Fig. 5 is a section view of the article of footwear taken along line 5-5 of Fig. 4A.
Fig. 6 is an exploded view of an article of footwear in accordance with an alternative
embodiment.
Fig. 7 is a sectional view of the alternative article of footwear similar to Fig.
3.
Fig. 8 is a sectional view of a first alternative foam-strobel board laminate.
Fig. 9 is a sectional view of a second alternative foam-strobel board laminate.
DESCRIPTION OF THE CURRENT EMBODIMENT
Overview.
[0017] An article of footwear incorporating an embodiment of the present invention is shown
in Fig. 1. The article of footwear 10 generally includes an upper 12 and a sole assembly
14. The upper 12 is manufactured using a strobel construction, and is bottomed with
a strobel board 16. The sole assembly 14 generally includes an outsole 20 and midsole
18 positioned below the strobel board 16, as well as a topsole 22 positioned above
the strobel board 16. The topsole 22 may be laminated or otherwise affixed to the
strobel board 16. An inner sole 24 (or sockliner) may be positioned above the topsole
22. The topsole 22 is manufactured from foam having an average modulus at a stress
of 535 kPa of between about 750 and about 950 kPa and an energy efficiency of at least
about 78% and a dynamic compression set of less than about 10%.
[0018] Although the current embodiments are illustrated in the context of athletic or running
shoes, they may be incorporated into any type or style of footwear, including performance
shoes, hiking shoes, trail shoes and boots, hiking boots, all-terrain shoes, barefoot
running shoes, sneakers, conventional tennis shoes, walking shoes, multisport footwear,
casual shoes, dress shoes or any other type of footwear or footwear components. It
also should be noted that directional terms, such as "vertical," "horizontal," "top,"
"bottom," "upper," "lower," "inner," "inwardly," "outer" and "outwardly," are used
to assist in describing the invention based on the orientation of the embodiments
shown in the illustrations. Further, the terms "medial," "lateral" and "longitudinal"
are used in the manner commonly used in connection with footwear. For example, when
used in referring to a side of the shoe, the term "medial" refers to the inward side
(that is, the side facing the other shoe) and "lateral" refers to the outward side.
When used in referring to a direction, the term "longitudinal direction" refers to
a direction generally extending along the length of the shoe between toe and heel,
and the term "lateral direction" refers to a direction generally extending across
the width of the shoe between the medial and lateral sides of the shoe. The use of
directional terms should not be interpreted to limit the invention to any specific
orientation.
[0019] Further, as used herein, the term "arch region" (or arch or midfoot) refers generally
to the portion of the footwear or sole assembly corresponding to the arch or midfoot
of the wearer's foot; the term "forefoot region" (or forefoot) refers generally to
the portion of the footwear forward of the arch region corresponding to the forefoot
(for example, including the ball and the toes) of a wearer's foot; and the term "heel
region" (or heel) refers generally to that portion of the footwear rearward of the
arch region corresponding to the heel of the wearer's foot. The forefoot region 60,
arch region or midfoot region 62 and heel region 64 are generally identified in Fig.
4A, however, it is to be understood that delineation of these regions may vary depending
upon the configuration of the sole assembly and footwear.
Topsole Foam.
[0020] As noted above, it is desirable for the topsole 22 to be manufactured from foam having
certain defined mechanical properties that are suitable for use above the strobel
board. For example, it is desirable for the topsole 22 foam to be compliant, resilient,
durable and highly conformable. Also, because the topsole 22 foam can be laminated
to the strobel board, it would also be beneficial for the topsole 22 foam to be capable
of being stitched through.
[0021] With regard to modulus, it is desirable for the topsole 22 foam to have a lower modulus
than conventional midsole foams, such as EVA midsole foams. There are practical limitations
on the use of lower modulus EVA foam in footwear because lower modulus EVA foam breaks
down quickly under the loads created during the peak forefoot loading. Examples of
breakdown include failure to rebound after load (e.g. permanent compression), tearing,
etc. To prevent premature breakdown, lower modulus EVA foam can only be used in relatively
thin (e.g. 1-3 mm) layers. Unfortunately, the use of a thin foam layer limits conformability,
which is an important objective for the sole under the forefoot. Therefore, it is
desirable for the topsole 22 foam to be sufficiently durable to use in a layer that
is thick enough to conform to the foot during forefoot loading and concomitant flex
without losing its properties over repeated cycles. In various embodiments, the topsole
22 is free of EVA foam.
[0022] With these objectives in mind, the topsole 22 is manufactured from a soft and highly
resilient (energy efficient) and durable material. Examples of suitable foams for
purposes of this disclosure include certain expanded thermoplastic polyurethane ("E-TPU")
foams and thermoplastic elastomer ("TPE") foams. In certain embodiments, the topsole
22 comprises, consists essentially of, or consists of E-TPU foam. In other embodiments,
the topsole 22 comprises, consists essentially of, or consists of TPE foam.
[0023] Specific examples of suitable foams include "180SD" E-TPU foam, which is commercially
available from Guo Sheng of Chidian Town, Jinjiang City, Fujian Province, China; High
Rebound TPE PH-60 foam commercially available from Ecocell of Nan-Cheng, Dongguan
city, Guangdong, China; "X-Bounce 45" foam, which is commercially available from Fine
Chemical of Kimhae-City, Gyungnam, South Korea; "S-Lite" foam, which is commercially
available from Superfoam of Dongguan City, Guangdong, China; and "Infinergy™" foam,
which is commercially available from BASF Corporation of Florham Park, NJ.
[0024] The topsole 22 foam is highly resilient, and more compliant than EVA foam at lower
stresses (for example those encountered during standing) and more resistant to change
in thickness after repeated impacts. In particular, the topsole 22 foam can provide
superior performance over EVA strobel board foams particularly in the forefoot. Softness
of the topsole 22 foam allows for increased conformability and supplemental impact
absorption during forefoot strikes. Furthermore, the topsole 22 foam provides a benefit
during propulsion. Specifically, the topsole 22 foam absorbs shear forces during landing
that is released during toe off. The increased energy efficiency of the topsole 22
foam can create a more efficient stride.
[0025] The foam used to manufacture the topsole 22 has "softness," "resilient" and "durable"
mechanical properties defined by impact testing on material samples. For example,
the mechanical properties of foams may be measured with an electromagnetically driven
impact test device (ElectroPuls E3000, Instron, Norwood MA). The protocol may be a
modified version of ASTM F1614-99(2006) "Standard Test Method for Shock Attenuating
Properties of Materials Systems for Athletic Footwear Procedure C." The principle
modification is the use of a 45 mm disk shaped sample (as opposed to a 3 inch minimum
square sample).
[0026] The loading curve is controlled to simulate a foot strike. Samples are approximately
20 mm thick (and resultant data is normalized by thickness). Mechanical attributes
of interest include Average Stiffness, Energy Efficiency, Dynamic Compression Set,
and Average Stiffness of the foam at 535 kilopascals (kPa). Here, 535 kPa is chosen
as a typical peak stress during a foot strike. In order for the topsole 22 foam to
be "soft" and "resilient", the notable mechanical attributes of interest are Average
Modulus and Energy Efficiency. Average Stiffness is normalized as Average Modulus
by factoring in the cross-sectional area of the impact tup (using a 45 mm diameter
tup or "striker") and multiplying by the thickness of the sample. Energy Efficiency
is the ratio of energy returned by the sample divided by the energy absorbed by the
sample.
[0027] Each of the foam samples is impact tested 1,000 times to get a baseline measurement
of mechanical characteristics. The 980
th, 990
th, and 1,000
th impact cycle are averaged to determine properties.
[0028] As a measure of durability, Dynamic Compression Set is used. Dynamic Compression
Set is the change in thickness of a sample for a given number of impacts. Each of
the foam samples is impact tested 1,000 times to get a baseline measurement of mechanical
characteristics (including Average Modulus and Energy Efficiency), then impact tested
100,000 times (with the same loading profile) to simulate extended loading cycles,
and then impact tested 1,000 more times to get a measurement of mechanical characteristics
after loading.
[0029] In various embodiments, the foam utilized to manufacture the topsole 22 of this disclosure
has an average modulus of from about 750 to about 950, about 800 to about 950, about
850 to about 950, or about 875 to 950, kPa. The average modulus is analyzed at a stress
of 535 kPa according to the modified version of ASTM F1614-99(2006). The foam also
has an energy efficiency of at least about 78, at least about 80, or at least about
82, %. The energy efficiency is analyzed according to the modified version of ASTM
F1614-99(2006). Moreover, the foam has a dynamic compression set of less than about
10, less than about 8, or less than about 6, %. The dynamic compression set is analyzed
according to the modified version of ASTM F1614-99(2006). An Asker C Durometer Gage
can be utilized to determine Asker C hardness values.
[0030] Because of the material properties of the topsole 22 foams, they can be used in a
greater thickness without prematurely losing their mechanical properties. Not only
do the topsole 22 foams provide enhanced mechanical properties, but by positioning
the topsole 22 above the strobel board 16, the topsole 22 also moves the relatively
rigid, non-conformable layer created by the strobel board 16 and cement further away
from the foot.
[0031] In various embodiments, the topsole 22 has an average thickness of from about 1mm
to about 10mm, about 2mm to about 7mm, or about 2mm to about 5mm, in the forefoot
region. It is to be appreciated that thickness of the topsole 22 may be uniform or
may vary, based e.g., on the configuration of the footwear, the end user, etc. The
thickness of the topsole 22 may vary from region to region in the shoe. For example,
in the forefoot region, the topsole 22 may have a thickness in the range of about
2mm to about 10mm or in the range of about 3mm to about 7 mm, and in the heel region,
the topsole 22 may have a thickness in the range of about 1mm to about 7mm or in the
range of about 2mm to about 5mm. In the embodiment of Fig. 1, the topsole 22 has a
maximum thickness of approximately 5 mm in the central forefoot region and a thickness
of approximately 3 mm throughout the heel region. The topsole 22 may gradually transition
between 5 mm and 3 mm through the arch region.
[0032] Examples of the soft, resilient, and durable foams suitable for purposes of this
disclosure, as well as examples of conventional foams not suitable for purposes of
this disclosure, are illustrated in Tables I-IV below. Specifically, Examples 1-4
are deemed comparative examples, while Examples 5-8 are deemed invention examples
suitable for forming the topsoles 22 of this disclosure.
[0033] Each of the foam samples for the respective example are tested as described above.
An Asker Durometer can be utilized to determine Asker C hardness values of each of
the foam samples. Asker Durometers are readily available from a number of commercial
suppliers and use thereof is understood by those in the art. Each of the examples
is described in greater detail immediately below.
[0034] Example 1 is an EVA foam that is conventionally used for midsoles having a hardness
of 52 Asker C, commercially available from Fine Chemical of Kimhae-City, Gyungnam,
South Korea.
[0035] Example 2 is an EVA foam that is conventionally used for strobel board lamination
having a hardness of 42 Asker C, commercially available from Xie Li of Gaobu Town,
Dongguan City, China.
[0036] Example 3 is polyurethane foam that is in the stiffness range for midsoles having
a hardness of 35 Asker C, commercially available from Jones and Vining of Brockton,
Massachusetts under the designation "U-2".
[0037] Example 4 is a softer conventional polyurethane foam having a hardness of 25 Asker
C, commercially available from Jones and Vining of Brockton, Massachusetts under the
designation "U-14 Soft".
[0038] Example 5 is an E-TPU foam available from Guo Sheng of Chidian Town, Jinjiang City,
Fujian Province, China under the designation "180SD".
[0039] Example 6 is a TPE foam having a hardness of 47 Asker C, commercially available from
Ecocell of Nan-Cheng of Dongguan City, Guangdong, China under the designation "PH-60".
[0040] Example 7 is a foam having a hardness of 45 Asker C, commercially available from
Fine Chemical of Kimhae-City, Gyungnam, South Korea under the designation "X-Bounce
45".
[0041] Example 8 is a TPE blended foam having a hardness of 52 Asker C, commercially available
from Superfoam of Dongguan City, Guangdong, China under the designation "S-Lite".
[0042] Example 9 is an E-TPU foam available from Guo Sheng of Chidian Town, Jinjiang City,
Fujian Province, China under the designation "160SD".
[0043] Average Modulus of each example is determined according to the modified version of
ASTM F1614-99(2006) as described above. A limit of about 750 to about 950 kPa is chosen
as the threshold for Average Modulus. Example foams encompassed within the range are
deemed to have a desirable softness and example foams falling outside the range are
deemed to have undesirable softness. Results are illustrated in Table I below.
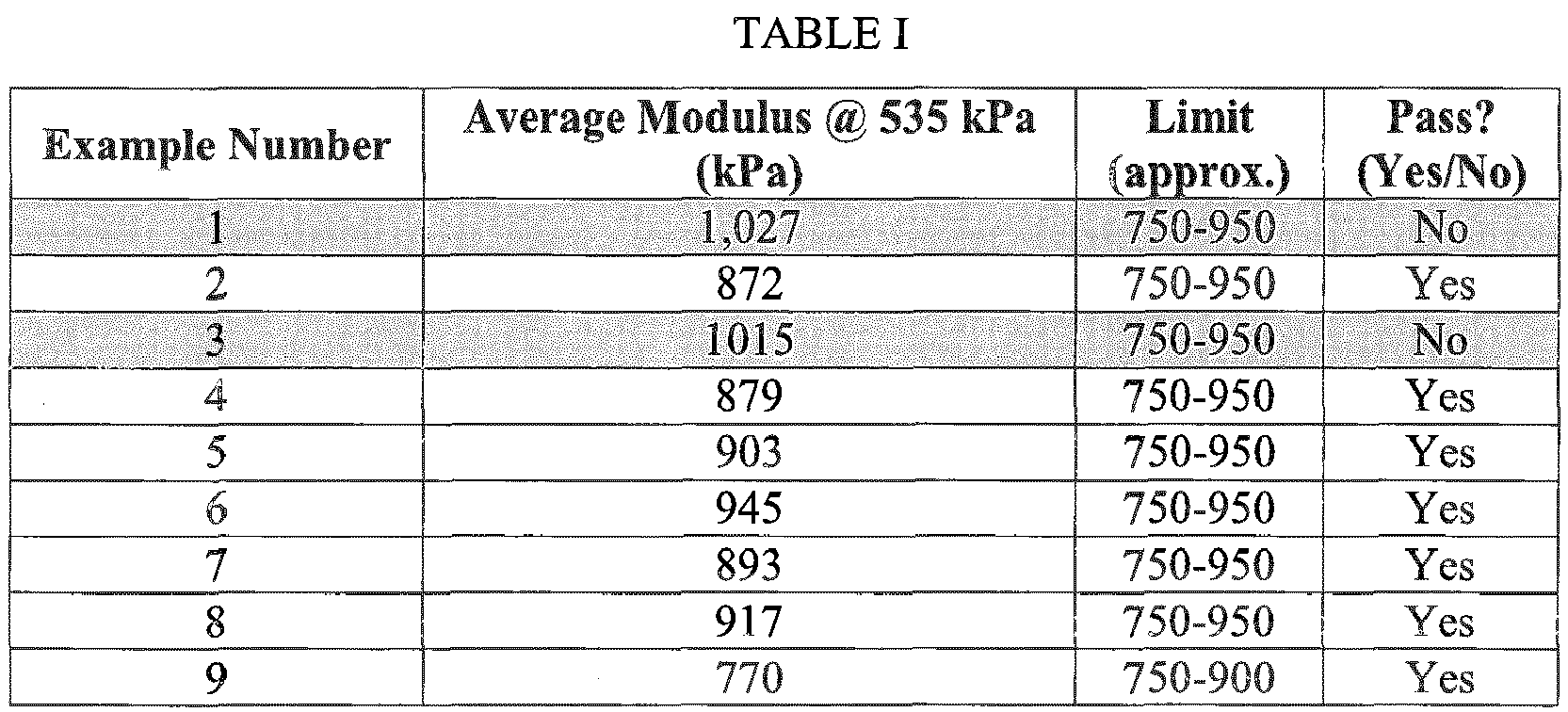
[0044] As illustrated in Table I above, each of Examples 1 and 3 fall outside the Average
Modulus range. In sum, each of Examples 1 and 3 have undesirable softness, whereas
each of Examples 2 and 4-9 have desirable softness.
[0045] Energy Efficiency of each example is also determined as described above. A limit
of at least about 78% is chosen as the threshold for Energy Efficiency. Example foams
encompassed within the range are deemed to have a desirable resiliency (i.e., a desirable
energy returned/energy absorbed ratio) and example foams falling outside the range
are deemed to have poor resiliency. Results are illustrated in Table II below.
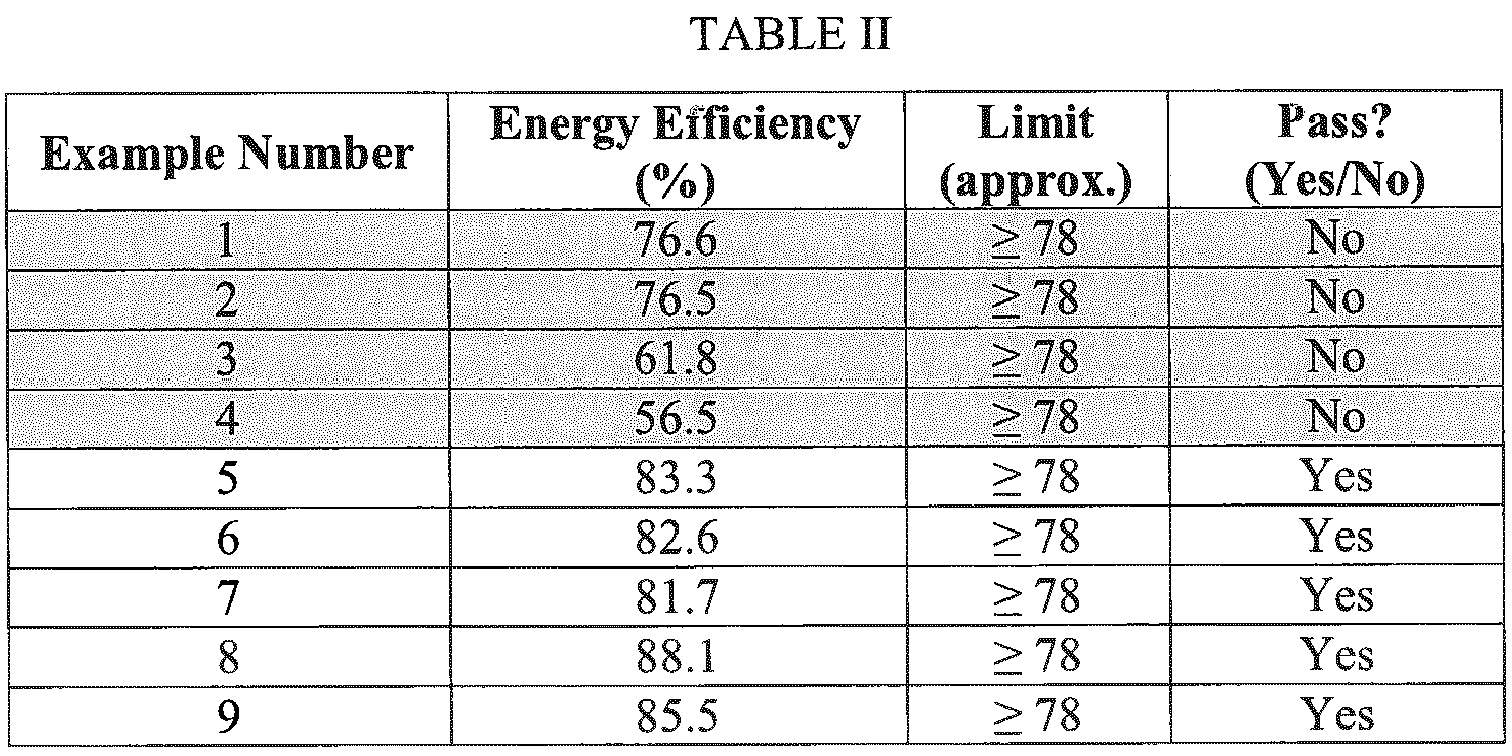
[0046] As illustrated in Table II above, each of Examples 1-4 fall outside the Energy Efficiency
range. In sum, each of Examples 1-4 have poor resiliency, whereas each of Examples
5-9 have desirable resiliency.
[0047] Dynamic Compression Set of each example is also determined as described above. A
limit of less than about 10% is chosen as the threshold for Dynamic Compression Set.
Example foams encompassed within the range are deemed to have a desirable durability
and example foams falling outside the range are deemed to have poor durability. Results
are illustrated in Table III below.

[0048] As illustrated in Table III above, each of Examples 1 and 2 fall outside the Dynamic
Compression Set range. In sum, each of Examples 1 and 2 have poor durability, whereas
each of Examples 3-9 have desirable durability.
[0049] All of the results are tabulated and presented in Table IV below. In sum, each of
Examples 1-4 have one or more properties that make them undesirable for purposes of
this disclosure, whereas each of Examples 4-9 possess the properties that make them
suitable for forming the topsole 22 of this disclosure.
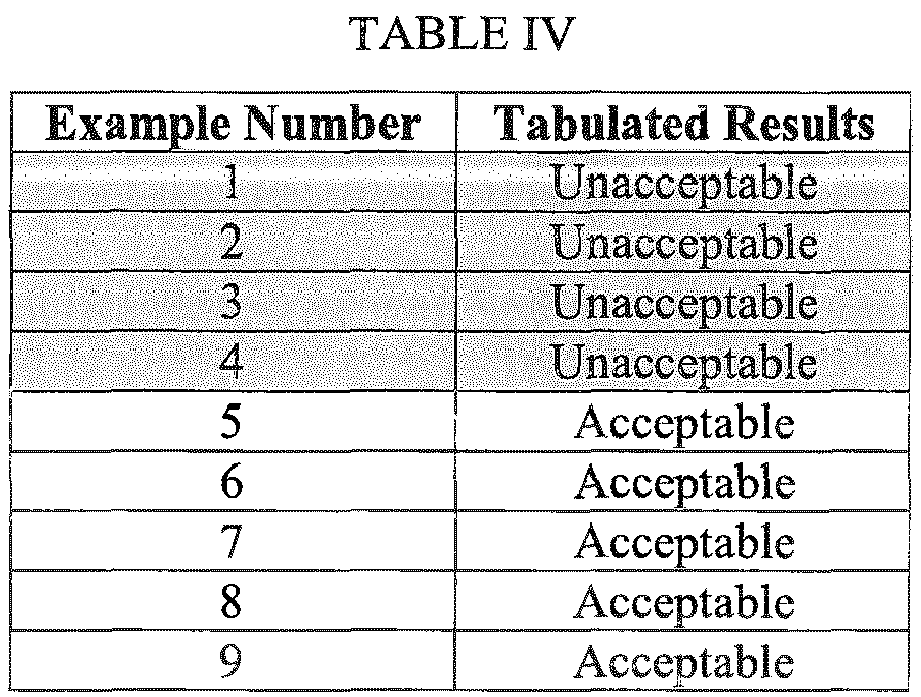
Footwear Construction.
[0050] As noted above, the article of footwear 10 shown in Fig. 1 generally includes an
upper 12 and a sole assembly 14. The upper 12 is manufactured using a strobel construction,
and is bottomed with a strobel board 16. The sole assembly 14 generally includes a
midsole 18 and an outsole 20 positioned below the strobel board 16, as well as a topsole
22 positioned above the strobel board 16. The topsole 22 may be laminated or otherwise
affixed to the strobel board 16. An inner sole 24 (or sockliner) may be positioned
above the topsole 22. The topsole 22 of the illustrated embodiment is manufactured
from foam having an average modulus at a stress of 535 kPa of between about 750 and
950 kPa and an energy efficiency of at least about 78% and a dynamic compression set
of less than about 10%. The topsole 22 is of sufficient thickness to conform to the
shape of the foot throughout the forefoot region during the propulsion phase of contact.
For example, in the illustrated embodiment, the topsole 22 has a thickness of about
5 mm through the center of the forefoot region.
[0051] The upper 12 is a generally conventional upper, the bottom of which is closed by
a strobel board 16. Although the construction of the upper 12 may vary from application
to applications, the upper 12 of Fig. 1 generally includes a vamp 40 (or toe box),
a tongue 42 and one or more quarters 44. The vamp 40 generally forms the forefoot
portion of the upper 12 and may be manufactured from any combination of pieces of
upper material. The tongue 42 may be joined to the vamp 40 and extend rearwardly to
underlie the laces (not shown). As with the vamp 40, the tongue 42 may be manufactured
from any combination of pieces. The tongue 42 may be padded, which in part helps to
protect the wearer's foot from the laces. The quarter or quarters 42 form the heel
portion of the upper 12 and may be manufactured from any combination of pieces of
upper material. The interior of the vamp 40, tongue 42 and quarters 44 may be covered
by a lining material, such as a layer of DriLex, Cambrelle or other lining materials.
The various pieces of the upper 12 may be manufactured from any of a wide range of
materials, such as leather, synthetic leather, mesh, canvas, textile (e.g. woven,
knit, bonded), fabric and molded components. The upper 12 may include various trim,
cushioning and reinforcing elements. For example, a heel counter (not shown) may be
fitted into the heel region to reinforce the heel cup and increase support. As another
example, a toe cap (not shown) may be provided to reinforce the vamp 40. Further,
padding may be sandwiched between the layers of the upper 12, such as between the
vamp 40 and the lining material. Reinforcing elements may be affixed to the upper
12 to reinforce the portions of the upper 12 that receive the laces. The construction
of the illustrated upper 12 is merely exemplary, and the present invention may be
incorporated into footwear that includes essentially any upper construction.
[0052] In the illustrated embodiment, the bottom of the upper 12 is closed by a strobel
board 16 or strobel textile (these terms are used interchangeably herein). The strobel
board 16 is typically manufactured from a non-stretch fabric or textile (i.e. does
not stretch appreciably). For example, the strobel board 16 may be manufactured from
a non-woven textile, a woven textile or a knit textile. Given that the strobel board
16 in intended to maintain the shape of the upper 12, the strobel board 16 does not
stretch appreciably, particularly in the fore-aft direction. The strobel board 16
may be a composite construction manufactured from a combination of different materials
that provide the strobel board 16 with different characteristics in different regions.
For example, a composite strobel board 16 of this type may have a forefoot region
and a heel region that are manufactured from different materials. This may allow the
strobel board 16 to provide different mechanical properties in different regions,
such as a more flexible forefoot or a more rigid arch or more rigid heel. In the illustrated
embodiment, the bottom end of the upper 12 terminates in a lasting allowance 50 that
is wrapped inwardly and is joined to the strobel board 16. In the illustrated embodiment,
the lasting allowance 50 is secured to the strobel board 16 in a butt-seam by stitching
52 (See Figs. 2 and 4A), such as a zig-zag stitch or a strobel-stitch from a Strobel
stitching machine. Although the illustrated embodiment includes a strobel construction,
the present invention may be incorporated into other footwear constructions that could
benefit from the use of a topsole, such as board lasted constructions or slip lasted
constructions. In these alternative lasted constructions, the topsole may be laminated
to the lasting board (for example, formed directly onto the lasting board or formed
first and then secured to the lasting board) or it may be separate from the lasting
board.
[0053] The sole assembly 14 of Fig. 1 can be of a two-piece construction as mentioned above,
generally including the midsole 18 and outsole 20. The midsole 18 can be constructed
from a material having a density that is generally less dense than the density of
the outsole 20. The first density can optionally be about 5 pounds per cubic foot
to about 20 pounds per cubic foot, and further optionally about 9 pounds per cubic
foot to about 15 pounds per cubic foot, or other densities depending on the application.
Generally, the density of the midsole is such that it compresses relatively easily
to provide cushion to the wearer's foot. The midsole material also can have a durometer,
optionally about 30 Asker C to about 55 Asker C, further optionally about 42 Asker
C to about 48 Asker C, and even further optionally about 45 Asker C or about 43 Asker
C. The midsole can be constructed from ethyl vinyl acetate (EVA), polyurethane, latex,
foam, a gel or other materials.
[0054] The midsole 18 can include an upper surface 30 and an opposing lower surface 32.
Generally, the upper surface 30 can be joined directly to the undersurface of the
closed upper 12. For example, the midsole 18 can be joined to the undersurface of
the strobel board 16 and the inwardly-turned marginal allowance of the upper 12. The
upper surface 30 can be contoured to closely follow the natural contours of the bottom
of a wearer's foot. For example, in the heel region, the midsole 18 can be shaped
to define a heel cup that generally extends around and receives a portion of the wearer's
heel therein when the footwear is worn by a wearer. The heel cup can include an upwardly
extending flange 34 that is a substantially continuous wall bounding and surrounding
the rearward portion of the wearer's heel. This upwardly extending flange or wall
34 also can extend upwardly along the lowermost portion of the upper 12 when the upper
is joined with the sole assembly 14. The flange 34 can extend upwardly optionally
about 1.0 mm to about 10.0 mm, further optionally about 2.0 mm to about 6.0 mm, or
other distances as desired. In the illustrated embodiment, the flange 34 gradually
tapers down toward the toe end of the sole assembly 14. The flange 34 can offer some
reinforcing support to the upper in the heel region, and generally resist lateral
or medial rolling of the heel.
[0055] The outsole 20 can be disposed below the midsole 18 and the upper 12. In the illustrated
embodiment, the outsole 20 is manufactured from a single, one-piece layer that is
generally coextensive with the undersurface 32 of the midsole 18. The outsole 20 may,
however, be manufactured from a plurality of discrete segments that are separately
secured to the undersurface 32 of the midsole 18 (See, for example, the alternative
embodiment shown in Fig. 5). The outsole 20 can be constructed from one or more materials,
and the current embodiment can be constructed from a mixture of foam and rubber. Alternatively,
it can be constructed from a thermoplastic polyurethane elastomer (TPU), rubber, nylon
or other polymer blend that includes nylon and/or TPU. These materials are merely
exemplary, and the outsole 20 can be constructed from essentially any relatively wear
resistant polymer, elastomer and/or natural or synthetic rubber or other materials
capable of providing the desired functional characteristics. The outsole also can
be constructed to include thermoplastic elastomers and/or thermoset elastomers. Other
materials such as fiber-reinforced polymers can be used. These can include epoxy,
polyethylene, polyester, thermosetting plastic reinforced with carbon, glass and/or
aramid fibers.
[0056] The outsole 20 of Figs. 1-4 is shown with a generally smooth bottom, ground-engaging
surface. As shown in connection with the alternative embodiment of Fig. 5, the bottom
surface of the outsole 20 can include multiple lugs 36' (or cleats, grooves, channels,
treads, siping, etc.). The lugs 36' can be in essentially any form and may be textured
or have surface features through the portions that engage the ground. As noted above,
the outsole 20 can be a single continuous section of material or it may be formed
from a plurality of discrete outsole segments. The outsole 20 or individual outsole
segments can also include one or more flex contours 38'. The flex contours 38' can
generally be disposed in the forefoot, between the ball of the foot and the toes,
to enable the toes to flex independently and more easily relative to the ball of the
foot. Generally, the flex contours 38' can be a region where the thickness of the
outsole is reduced relative to the thickness of the outsole (or entirely absent) in
the ball of the foot and/or the toes or a region.
[0057] The midsole 18 and outsole 20 may be manufactured as a unit sole, and the unit sole
may be secured to the bottom of the upper 12 after lasting. Alternatively, the midsole
18 may be joined to the bottom of the upper 12 first, and the outsole 20 may be joined
to the bottom of the midsole 18 after the midsole 18 has been joined to the upper
12.
[0058] As noted above, the article of footwear 10 includes a topsole 22 disposed above the
strobel board 16. The topsole 22 is manufactured from foam having an average modulus
at a stress of 535 kPa of between about 750 and about 950 kPa and an energy efficiency
of at least about 78% and a dynamic compression set of less than about 10%. However,
these values may vary from application to application as set forth above. For example,
the average modulus at a stress of 535 kPa may be between about 750 and about 950,
or between about 800 and about 950, or between 850 and about 950 or about 875 and
about 950 kPa. Further, the energy efficiency may be at least about 78%, at least
about 80% or at least about 82%. Finally, the dynamic compression set may be less
than about 10%, less than about 8% or less than about 6%.
[0059] In the illustrated embodiment, the topsole 22 is laminated to the upper surface of
the strobel board 16. For example, the topsole 22 may be adhesively secured to the
top of the strobel board 16 after the upper 12 and strobel board 16 have been joined.
However, the topsole 22 may be cemented to the strobel board 16 before or after lasting.
As an alternative to cementing, the topsole 22 may be formed in place directly on
the top surface of the strobel board 16. For example, the laminate may be formed by
placing the strobel board 16 in a mold, introducing the topsole foam into the mold
and causing the topsole foam to cure in place within the mold in intimate contact
with the strobel board 16. With this alternative, the topsole 22 may be molded in
place on the strobel board 16 prior to joining the strobel board 16 to the bottom
of the upper 12. In some applications, it may be possible to mold the topsole 22 in
place on the strobel board 16 after lasting. It is not necessary for the topsole 22
to be laminated to the strobel board 16. For example, in some applications, the topsole
22 may be loosely fitted into the upper 12 atop the strobel board 16 without any direct
connection between the two components. This option may be more feasible in applications
where the topsole 22 has sufficient inherent structural rigidity to maintain its shape
without being joined to the strobel board 16.
[0060] As noted above, the strobel board 16 closes the bottom of the upper 12. In the illustrated
embodiment, the strobel board 16 is generally continuous extending through the forefoot
region, the arch region and the heel region. In this embodiment, the strobel board
16 is formed without openings and substantially fills the entire opening in the bottom
of the upper, which is defined around its perimeter by the terminating edge of the
lasting allowance 50. The size, shape and configuration of the lasting allowance 50
may vary from application to application, which may in turn result in variations in
the size, shape and configuration of the strobel board 16.
[0061] If desired, the foot receiving cavity within the upper 12 may be enlarged in whole
or in part to accommodate the topsole 22. For example, with regard to the embodiment
of Figs. 1-4, the last may be enlarged through the length of the last to accommodate
the extra thickness of the topsole 22. The enlargement may be uniform through the
last or it may vary. For example, the amount of enlargement may be proportional to
the thickness of the topsole 22. As another example, the last may be enlarged only
in the forefoot region or other regions where the topsole 22 may be thickest.
[0062] In this embodiment, the topsole 22 forms the bottom of the foot receiving space on
the interior of the upper 12. As show, the topsole 22 is essentially coextensive with
the bottom of the upper 12 and the sole assembly 14 extending from toe to heel and
from lateral side to medial size. In this embodiment, the topsole 22 covers the lasting
allowance 50 and the strobel board 16 (See Fig. 3 and 4B). The topsole 22 may vary
in size, shape and configuration. For example, the topsole 22 may extend through only
select regions, such as the forefoot region, and be absent in other regions, such
as the heel region. As another example, the topsole 22 may have one or more apertures
or openings at select locations. The apertures or openings may be vacant or they may
be filled by a different material, such as a cushioning material with different mechanical
properties.
[0063] As perhaps best shown in Fig. 2, the topsole 22 of the illustrated embodiment is
generally uniform in thickness from toe to heel. In the illustrated embodiment, the
topsole 22 is about 3mm in thickness. The topsole 22 may alternatively have a thickness
of between about 1mm and about 10mm, or between about 2mm to about 7mm or between
about 2mm to about 5mm. As an alternative to uniform thickness, the topsole may vary
in thickness through different regions of the sole. For example, as shown in Fig.
5, the topsole 22' may be thicker in the forefoot region than in the arch region or
in the heel region. In the embodiment of Fig. 5, the topsole 22' has a maximum thickness
of approximately 5 mm through much of the forefoot region and a thickness of approximately
3 mm through the heel region. The topsole 22' includes a gradual transition between
these two thicknesses in the arch region. The thickness of the topsole 22' may, however,
vary from application to application and from region to region. For example, the topsole
may have a thickness in the forefoot region in the range of about 1mm to about 10mm
or in the range of about 2mm to about 7mm or in the range of about 2mm to about 5mm,
in the arch region in the range of about 1mm to about 7mm or in the range of about
1mm to about 5mm and in the heel region a thickness in the range of about 1mm to about
7mm or in the range of about 1mm to about 5mm.
[0064] An inner sole 24 may be fitted into the upper 12 above the topsole 22. The inner
sole 24 may extend the full length and width of the foot receiving space. The inner
sole 24 may be manufactured from a material having a density that is generally less
dense than the density of the midsole 18. The inner sole density can optionally be
about 5 pounds per cubic foot to about 15 pounds per cubic foot, and further optionally
about 7.5 pounds per cubic foot to about 12.5 pounds per cubic foot, or other densities
depending on the application. The inner sole 24 material also can have a durometer,
optionally about 15 Asker C to about 50 Asker C, further optionally about 20 Asker
C to about 45 Asker C, and even further optionally about 25 Asker C to about 35 Asker
C. The inner sole 24 can be constructed from EVA, polyurethane, latex, foam, a gel
or other materials. In the illustrated embodiment, the inner sole 24 is manufactured
from EVA and has a thickness of approximately 3mm to 7mm, but its thickness may vary
from application to application. For example, the inner sole may have a thickness
in the range of about 2mm to about 10mm or about 1mm to about 12mm. The inner sole
24 of the illustrated embodiment is uniform in thickness, but may vary in thickness
from application to application as desired. For example, the inner sole 24 may be
thicker in the heel region. The inner sole 24 may be loosely fitted into the upper
12 so that it can be easily installed and removed, or it may be adhesively secured
within the upper 12. For example, the inner sole 24 may be cemented to the top surface
of the topsole 22. Although referred to as an "inner sole", the inner sole 24 may
also be known as insole, footbed or sockliner.
[0065] In alternative embodiments, the strobel board may include one or more openings. For
example, an alternative embodiment is shown in Figs. 6-7. To facilitate disclosure,
the embodiment of Figs. 6-7 will include reference numerals corresponding with those
of Figs. 1-4, except followed by the double prime symbol (i.e. "). As perhaps best
shown in Figs. 6 and 7, the article of footwear 10" includes a strobel board 16" that
defines a central opening 54" (the perimeter of which is shown in broken lines in
Fig. 6). In this illustration, the central opening 54" extends through at least portions
of the forefoot region 60", arch region 62" and heel region 62". The number, size,
shape, location and configuration of strobel board openings may, however, vary from
application to application. For example, the strobel board 16" may include an opening
only in the forefoot region 60". As another example, the strobel board 16" may include
separate openings in the forefoot region 60" and in the heel region 64". Returning
now the embodiment of Fig. 6, the central opening 54" may be formed by removing a
central portion of the strobel board 16" by die cutting after lasting. Alternatively,
the strobel board 16" may be formed with perforations or another line of weakening
about the perimeter of the central opening 54" so that the strobel board material
occupying the central opening 54" can be torn away from the strobel board 16" after
lasting. In the embodiment of Figs. 6-7, the topsole 22" extends downwardly through
the central opening 54" and terminates in alignment with the bottom surface of the
strobel board 16". This configuration is merely exemplary and the topsole may extend
to different positions relative to the strobel board. For example, in those applications
in which there is an opening in the strobel board, the topsole 22"' may extend down
through the opening 54"' as shown in Fig. 8, or the topsole 22"" may extend over the
opening 54"" in the strobel board 16"" as shown in Fig. 9. The embodiment of Fig.
8 may be particularly useful in applications where it is desirable to include additional
topsole material and to provide more direct interaction between the topsole 22"' and
the midsole 18"'. In this embodiment, the topsole 22"' extends outwardly beyond the
perimeter of the strobel board 16"', which allows it to cover the lasting allowance
and butt seam. The embodiment of Fig. 9 may be particularly useful when the topsole
22"" is die cut from a sheet of topsole foam of uniform thickness. For example, in
this embodiment, the topsole 22"" may be die cut and then cemented to the top surface
of the strobel board 16"". In this embodiment, the topsole 22"" and the strobel board
16"" are coterminous in the sense that they share the same outer boundary. The coterminous
configuration may be useful in applications where it is unnecessary for the topsole
22"" to extend beyond the strobel board 16"" to cover a lasting allowance.
[0066] The above description is that of current embodiments of the invention. Various alterations
and changes can be made without departing from the spirit and broader aspects of the
invention as defined in the appended claims, which are to be interpreted in accordance
with the principles of patent law including the doctrine of equivalents. This disclosure
is presented for illustrative purposes and should not be interpreted as an exhaustive
description of all embodiments of the invention or to limit the scope of the claims
to the specific elements illustrated or described in connection with these embodiments.
For example, and without limitation, any individual element(s) of the described invention
may be replaced by alternative elements that provide substantially similar functionality
or otherwise provide adequate operation. This includes, for example, presently known
alternative elements, such as those that might be currently known to one skilled in
the art, and alternative elements that may be developed in the future, such as those
that one skilled in the art might, upon development, recognize as an alternative.
Further, the disclosed embodiments include a plurality of features that are described
in concert and that might cooperatively provide a collection of benefits. The present
invention is not limited to only those embodiments that include all of these features
or that provide all of the stated benefits, except to the extent otherwise expressly
set forth in the issued claims. Any reference to claim elements in the singular, for
example, using the articles "a," "an," "the" or "said," is not to be construed as
limiting the element to the singular.
[0067] Any ranges and subranges expressly disclosed in connection the various embodiments
of the present invention should be interpreted to also describe, contemplate, encompass
and disclose all subranges within such ranges and subranges, including whole and/or
fractional values therein, even if such values are not expressly written herein. Accordingly,
expressly enumerated ranges and subranges should be interpreted to disclose and provide
support for all possible subranges within the enumerated ranges and subranges. This
includes, but is not limited to, ranges and subranges that are divisions of the enumerated
ranges and subranges, such as delineation into fractional segments, such as halves,
thirds, quarters, fifths, and so on. As just one example, express disclosure of a
range "of from 0.1 to 0.9" should be interpreted to inherently disclose any and all
possible values and subranges within the range of 0.1 to 0.9, including any individual
value between 0.1 and 0.9, as well as any subrange of values bounded on the lower
end by any value between 0.1 and 0.9 and bounded on the upper end by any value between
0.1 and 0.9. It should also be interpreted to include all subranges that are derived
by delineated the range into fractional segments, such as into a lower third, i.e.,
from 0.1 to 0.3, a middle third, i.e., from 0.4 to 0.6, and an upper third, i.e.,
from 0.7 to 0.9. Accordingly, the express enumeration of a range or subrange should
be interpreted (individually and/or collectively) to provide adequate support for
any and all claim language directed to any value or subrange of values within the
expressly enumerated range. In addition, with respect to the language which defines
or modifies a range, such as "at least," "greater than," "less than," "no more than,"
and the like, it is to be understood that such language includes subranges and/or
an upper or lower limit. As another example, a range of "at least 10" should be interpreted
to include a subrange cf from at least 10 to 35, a subrange of from at least 10 to
25, a subrange of from 25 to 35, and so on. As a further example, a disclosed range
or subrange should be interpreted to disclose and provide support for any individual
number within that range or subrange. To illustrate, a range "of from 1 to 9" should
be interpreted to include any individual value from 1 to 9, including individual integers,
such as 3, as well as numbers including a decimal point (or fraction), such as 4.1.
[0068] The present disclosure extends to the following statements which are useful for understanding
the present invention:
S1. An article of footwear, comprising:
an upper having a bottom closed by a strobel board, said upper having a lasting allowance
joined to said strobel board in a butt-seam by a stitch;
a midsole disposed below said strobel board;
a topsole disposed above said strobel board, said topsole manufactured from foam having
an average modulus at a stress of 535 kPa of between about 750 and 950 kPa and an
energy efficiency of at least about 80% and a dynamic compression set of less than
about 8%; and
an inner sole disposed above said topsole.
S2. The article of footwear of statement S1 wherein said topsole has a thickness of
at least 1 millimeter and said inner sole has a thickness of at least 3 millimeters;
said topsole and said inner sole having a combined thickness of at least 5 millimeters
in a central portion of a forefoot region of the article of footwear.
S3. The article of footwear of statement S1 wherein said topsole has a thickness of
at least 3 millimeters and a combined thickness of said topsole and said inner sole
is at least 5 millimeters in a central portion of a forefoot region of the article
of footwear.
S4. The article of footwear of statement S2 wherein said topsole extends through a
forefoot region, an arch region and a heel region of the article of footwear.
S5. The article of footwear of statement S2 wherein said topsole is laminated to said
strobel board.
S6. The article of footwear of statement S5 wherein said topsole is formed directly
on said strobel board.
S7. The article of footwear of statement S6 wherein said strobel board defines an
opening, said topsole generally disposed above said strobel board and having a downward
extension extending into said opening.
S8. The article of footwear of statement S6 wherein said strobel board defines an
opening, said topsole generally disposed above said strobel board and having a downward
extension extending through said opening to a distance substantially below said strobel
board.
S9. A sole assembly for an article of footwear having an upper bottomed with a strobel
board, comprising:
a midsole disposed below the strobel board;
a topsole disposed above the strobel board, said topsole manufactured from foam having
an average modulus at a stress of 535 kPa of between about 750 and about 950 kPa and
an energy efficiency of at least about 80% and a dynamic compression set of less than
about 8%; and
an inner sole disposed above said topsole.
S10. The sole assembly of statement S9 wherein said topsole has a thickness of at
least 1 millimeter and said inner sole has a thickness of at least 3 millimeters;
said topsole and said inner sole having a combined thickness of at least 5 millimeters
in a central portion of a forefoot region of the article of footwear.
S11. The sole assembly of statement S10 wherein said inner sole is manufactured from
EVA. S12. The sole assembly of statement S10 wherein said inner sole is manufactured
from foam having an energy efficiency of less than about 80% and a dynamic compression
set of greater than about 10%.
S 13. The sole assembly of statement S12 wherein said topsole is laminated to said
strobel board.
S 14. The sole assembly of statement S 13 wherein said topsole has a first thickness
in forefoot region and a second thickness in a heel region, said first thickness being
greater than said second thickness.
S 15. The sole assembly of statement S 14 wherein said strobel board defines an opening.
S16. The sole assembly of statement S15 wherein said topsole extends into said opening.
S 17. An article of footwear comprising:
an upper having a closed bottom, said upper defining a foot-receiving space above
said closed bottom;
a topsole disposed in said foot-receiving space, said topsole manufactured from foam
having an average modulus at a stress of 535 kPa of between about 750 and 950 kPa
and an energy efficiency of at least about 80% and a dynamic compression set of less
than about 8%; and
an inner sole disposed in said foot-receiving space above said topsole, said inner
sole manufactured from a foam having an energy efficiency of less than about 80% and
a dynamic compression set of greater than about 10%;
wherein said topsole has a thickness of at least 1 millimeter and said inner sole
has a thickness of at least 3 millimeters; said topsole and said inner sole having
a combined thickness of at least 5 millimeters in a central portion of a forefoot
region of the article of footwear.
S18. The article of footwear of statement S17 wherein said upper is closed by a strobel
board, said topsole being joined to said strobel board.
S19. The article of footwear of statement S18 wherein said upper includes a lasting
allowance, said strobel board joined to said lasting allowance in a butt seam, said
topsole extending over said strobel board, said butt seam and said lasting allowance.
S20. The article of footwear of statement S19 wherein said topsole is an expanded
TPU foam or a TPE foam.
[0069] The embodiments of the invention in which an exclusive property or privilege is claimed
are defined as follows: