BACKGROUND OF THE INVENTION
[0001] Conventional optical fabrication processes typically include 1) shaping, 2) grinding,
3) edge grinding/polishing, 4) full aperture intermediate polishing or lapping, 4)
full aperture final polish, and 5) small tool polishing. Significant advances in precision
optical fabrication have been made since the invention of the laser, when the demand
for high optical quality material including precise surface figure rose dramatically.
However, as generally practiced today, optical fabrication is an art rather than a
technology. In recent decades, significant progress has been made in the ability to
deterministically remove material during the grinding process based on advancements
in tooling and real time diagnostics using Computer Numerical Controlled (CNC) grinders.
Similarly, the advent of small tool polishing (e.g., computer controlled optical polishers
(CCOS)) and Magnetorheological Finishing (MRF) has revolutionized the polishing industry.
However, full aperture lap polishing, which is still the most commonly used and typically
the most economical method for polishing glass and silicon wafers, does not provide
a deterministic process. Although incremental improvements have been made, conventional
polishing still requires highly skilled opticians using artisan techniques. This type
of polishing typically requires multiple iterative cycles involving polishing, measuring,
and adjusting parameters to converge to the desired surface figure (i.e. flatness
or conformance to a specified radius). Thus, there is a need in the art for improved
methods and systems related to the polishing of optical elements.
[0002] Document
US 2010/0311308 A1 discloses a polishing system comprising a septum having an aperture formed therein
substantially the same radius as the workpiece. The aperture and the workpiece have
centers disposed at substantially the same radial distance from a center of the lap,
in different radial directions.
SUMMARY OF THE INVENTION
[0003] The present invention provides the polishing unit according to claim 1, and the high
humidity polishing system according to claim 10 comprising same.
[0004] According to the present invention, techniques related to optical systems are provided.
More particularly, embodiments of the present invention relate to deterministic polishing
of optical elements in as little as a single iteration. Merely by way of example,
the invention has been applied to the single iteration polishing of an optical element
under a fixed set of polishing parameters regardless of the initial shape of the element.
The methods and systems described herein are applicable to the processing and fabrication
of a wide variety of optical materials suitable for use with high power laser and
amplifier systems.
[0005] According to another embodiment of the present invention, methods and systems related
to surface fracture "free" finishing are provided. Scratches on the surface of high
value optics used in high-peak-power laser systems are known to lead to laser damage
initiation. Hence, much effort has been employed over the years to reduce the number
and size of scratches formed during optical fabrication. Scratches are caused, for
example, by sliding rogue particles or asperities that are under load on the surface
of the optic during cleaning, polishing, and handling. Previous work to reduce rogue
particles involved modifying and retrofitting existing full aperture polishers. This
method was sufficient for dealing with foreign rogue particles leading to scratching.
Current mitigation strategies are largely limited to cleanliness practices during
polishing. This strategy, however, is highly sensitive to the degree of cleanliness
practice, operator skill set, and complexity of the polisher. Additionally, these
strategies are difficult to implement with high efficiency. A second limitation in
control of rogue particles is the limited understanding and control of the particle
size distribution of the slurry during the polishing process. The current state of
technology is limited to using un-optimized, poorly understood filtration techniques.
[0006] Embodiments of the present invention reduce rogue particle introduction during polishing
by implementing one or more of the following steps: 1) creating a full polishing system
that ensures that no rogue particles enter the workpiece-lap interface by hermetically
sealing the polisher to prevent drying of the slurry; 2) providing a 100% humidity
environment in order to prevent dried slurry agglomeration which can act as rogue
particles; 3) using chemically stabilized polishing slurries that minimize within
slurry particle agglomeration; and 4) using optimized filtration constantly removing
any created rogue particles in the polishing system.
[0007] According to an embodiment of the present invention, a polishing system for polishing
an optical element is provided. The polishing system includes a polishing pad having
a radial dimension and a septum disposed on the polishing pad and configured to partially
surround the optical element. The optical element contacts the polishing pad over
a range of the radial dimension and a pad wear rate of the polishing pad is substantially
constant as a function of radial dimension over the range of the radial dimension.
[0008] According to another embodiment of the present invention, a high humidity polishing
system is provided. The high humidity polishing system includes a polishing unit including
a polishing pad and a slurry delivery system operable to provide a slurry to the polishing
pad. The high humidity polishing system also includes an enclosure surrounding the
polishing unit. A humidity inside the enclosure is sufficient to prevent substantial
drying of the slurry.
[0009] According to a specific embodiment of the present invention, a slurry system for
polishing an optical element is provided. The slurry system includes a solvent and
an abrasive component supported in the solvent. The slurry system also includes a
surfactant supported in the solvent.
[0010] According to another specific embodiment of the present invention, a method of mounting
a workpiece to a substrate is provided. The method includes determining a peak-to-valley
height value and determining a value related to pitch area. The method also includes
computing a relative area of pitch, computing a button radius, and computing a number
of pitch buttons. The method further includes coupling N pitch buttons to the workpiece
and coupling the N pitch buttons to the substrate.
[0011] Embodiments of the present invention provide an apparatus and method for polishing
flat and spherical round and rectangular surfaces on glass of various aspect ratios
(diameter/thickness). Polishing systems provided by embodiments of the present invention,
which can be referred to as a Convergent, Initial surface independent, Single iteration,
Rogue-particle free (CISR) polisher, provide one or more of the following characteristics:
- 1) polishing parameters are fixed (i.e. not variable) and the same during/between
polishing runs regardless of the initial surface figure of the workpiece;
- 2) polishing can be done in a single iteration from the ground state since the workpiece
figure will converge to the desired shape matching that of the lap; and
- 3) polishing is performed in a rogue particle-'free' environment leading to little
or no scratching on the workpiece.
- 4) polishing is performed using highly controlled particle size distribution using
chemical stabilization and/or engineered filtration system.
[0012] Embodiments of the present invention rely on one or more of the following principles
to achieve the desired polishing process:
- 1) essentially all factors contributing to non-uniform spatial material removal on
the optic are eliminated except for optic-lap mismatch (i.e. physical non-uniform
separation between optic and lap) which leads to convergence of the optic surface
figure to desired shape (i.e., the shape of the lap); and
- 2) the sources of entry and creation of rogue particles into/in the polisher system
have been removed or are actively removed which leads little/no scratching of the
workpiece.
[0013] As described more fully throughout the present specification, engineering features
provided by embodiments of the present invention may include one or more of the following:
- 1) using specially designed septum(s) for round and rectangular workpieces to counteract
non-uniform pad wear;
- 2) using a specially designed septum to counteract viscoelastic induced non-uniform
stress distribution and non-uniform material removal;
- 3) using a specially design septum to ensure uniform distribution of slurry to the
workpiece;
- 4) using a rectangular shaped septum of glass base to provide stability in uniform
pad wear;
- 5) using a rectangular shaped septum of CVO diamond base for conditioning pad ensuring
constant material removal rate with polishing time;
- 6) using a wheel driven workpiece to prevent moment force contributions to non-uniform
stress distribution and non-uniform material removal;
- 7) using low-z pivot point mounting to minimize moment forces on workpiece and septums;
- 8) using kinematics (motion of workpiece and lap) to cause uniform time average velocity
on the workpiece preventing non-uniform material removal due to kinematics;
- 9) using a chemically stabilized polishing slurry (e.g., use an anionic (for example,
micro-90) or cationic surfactant plus a chelator at appropriate pH & concentration
in cerium oxide (Hastilite PO) slurry) to minimize particle agglomeration (a source
of rogue particles);
- 10) using a 100% humidity hermetically sealed polishing chamber to: a) prevent the
creation of dried polishing slurry, which is known to result in scratch-causing rogue-particles
and b) prevent foreign rogue particles in the environment from entering into the polishing
system;
- 11) using a stiff button bonding technique (also called pitch button bonding (PBB)
to prevent workpiece deformation on high aspect ratio (thin) workpiece/optics;
- 12) using a compliant button bonding technique (also called foam button bonding (FBB)
to counteract the residual stress contribution from ground surfaces to non- uniform
removal and workpiece bending;
- 13) using a pre-etching technique (e.g., HF or buffered-oxide etch) on a ground workpiece
to remove residual stress which can cause non- uniform removal and workpiece bending;
- 14) using a pre-etching technique (e.g., HF or buffered-oxide etch) on a ground workpiece
to remove potential glass rogue particles on a ground surface which can contribute
to scratching;
- 15) using a fluorinated coating on interior of polisher housing and components providing
low slurry particle adhesion for ease of slurry cleaning and for minimization of rogue
particle generation between polishing iterations;
- 16) using a polisher design that minimizes nooks and crevices allowing slurry particles
to gather for minimizing generation of rogue particles; and/or
- 17) using an active slurry filtration system that efficiently removes rogue-particles
and controls the particle size distribution of the slurry.
[0014] Numerous benefits are achieved by way of the present invention over conventional
techniques. For example, embodiments of the present invention provide methods and
systems suitable for polishing optics to a predetermined shape in a single iteration.
These and other embodiments of the invention along with many of its advantages and
features are described in more detail in conjunction with the text below and attached
figures.
BRIEF DESCRIPTION OF THE DRAWINGS
[0015]
FIG. 1 is a chart illustrating parameters impacting polishing non-uniformity according
to an embodiment of the present invention;
FIG. 2A is a simplified plot illustrating peak-to-valley heights as a function of
polishing time for different polishing configurations according to an embodiment of
the present invention;
FIGS. 2B-2G illustrate different polishing configurations according to an embodiment
of the present invention;
FIG. 2H is a simplified plot illustrating peak-to-valley heights as a function of
polishing time for a polishing configuration according to an embodiment of the present
invention;
FIGS. 3A-3D are simplified plots illustrating polishing convergence for varying initial
shapes according to embodiments of the present invention;
FIGS. 4A-4E are surface contours illustrating peak-to-valley height at various polishing
times according to an embodiment of the present invention;
FIG. 5A is a simplified perspective illustration of a polishing septum according to
an embodiment of the present invention;
FIG. 5B is a simplified cross-section of a polishing septum according to an embodiment
of the present invention;
FIG. 6 is a simplified plot of pad wear rate as a function of radial distance according
to an embodiment of the present invention;
FIG. 7 is a simplified plot of septum width as a function of radial distance according
to an embodiment of the present invention;
FIGS. 8A-C are simplified plots of septum load as a function of radial distance according
to an embodiment of the present invention;
FIG. 9A is a simplified schematic diagram illustrating scratching by rogue particles;
FIG. 9B is an image illustrating scratching by rogue particles;
FIG. 10 is a simplified perspective diagram of a high humidity polishing system according
to an embodiment of the present invention;
FIG. 11 is a simplified plan view of a portion of a high humidity polishing system
;
FIG. 12 illustrates plots of normalized interface height for polishing solutions at
a range of dilutions as a function of time according to an embodiment of the present
invention;
FIG. 13 illustrates plots of normalized interface height for polishing solutions under
the influence of agitation according to an embodiment of the present invention;
FIG. 14 illustrates plots of normalized interface height for polishing solutions as
a function of time according to an embodiment of the present invention;
FIG. 15 is a simplified plot of relative interface height for stabilized and unstabilized
polishing solutions as a function of time according to an embodiment of the present
invention; and
FIG. 16 is a polishing solution volume for stabilized and unstabilized polishing solutions
as a function of particle size according to an embodiment of the present invention;
FIG. 17 is a simplified flowchart illustrating a method of polishing a set of optical
elements according to an embodiment of the present invention;
FIGS. 18A-18C are images illustrating surface curvature before grinding, after grinding,
and after chemical etching according to an embodiment of the present invention;
FIGS. 19A-19F are simplified schematic diagrams illustrating a method of performing
pitch button bonding according to an embodiment of the present invention;
FIG. 20 is a plot illustrating the measured change in surface figure of fused silica
and phosphate glass in various PPB configurations according to an embodiment of the
present invention;
FIG. 21 is a plot of measured thermal expansion of pitches according to an embodiment
of the present invention;
FIG. 22A is a plot of workpiece peak-to-valley height as a function of undercooling
of pitch for a single button and three buttons according to an embodiment of the present
invention;
FIG. 22B is a plot of workpiece peak-to-valley height as a function of pitch button
radius according to an embodiment of the present invention;
FIG. 22C is a plot of normalized workpiece peak-to-valley height as a function of
pitch button offset according to an embodiment of the present invention;
FIG. 22D is a plot of workpiece peak-to-valley height as a function of relative total
pitch button area according to an embodiment of the present invention;
FIG. 23 is a simplified schematic diagram illustrating pitch button bonding parameters
according to an embodiment of the present invention;
FIGS. 24A and 24B are drawings illustrating optimized pitch button bonding patterns
for optical elements according to an embodiment of the present invention;
FIG. 25A is a plot of workpiece peak-to-valley height as a function of spacing between
buttons according to an embodiment of the present invention;
FIG. 25B is a plot of workpiece peak-to-valley height as a function of area fraction
according to an embodiment of the present invention; and
FIG. 26 is a simplified flowchart illustrating a method of determining pitch button
bonding parameters according to an embodiment of the present invention.
DETAILED DESCRIPTION OF THE INVENTION
[0016] FIG. 1 is a chart illustrating parameters impacting polishing non-uniformity according
to an embodiment of the present invention. Embodiments of the present invention provide
techniques and systems to mitigate polishing non-uniformity. Control of some of the
parameters illustrated in FIG. 1 are described in more detail in U.S. Patent Application
Publication No.
US2010/0311308A1. As described more fully throughout the present application, a mirror septum is utilized
in embodiments of the present invention to reduce the elastic lap response (4.2) and
the viscoelastic effect (4.5) and to provide a constant lap wear (4.6.1). The optic
shape is then used to drive the polishing process to convergence (4.6.4).
[0017] As illustrated in FIG. 1, the various parameters have been reduced or eliminated
except for a single variable, which is then used to converge to the desired shape
for the optical element in a full aperture polishing system. This contrasts sharply
with previous techniques in which the various parameters were simultaneously varied
in real time by an optician in an attempt to produce the desired shape. As the inventors
have understood and reduced or eliminated the parameters affecting material removal
illustrated in FIG. 1, only one variable is left, the mismatch between the optic and
the lap. Using a lap with the shape that you want the optical element to eventually
take, the optic element is then polished in a convergent manner to match the shape
of the lap.
[0018] FIG. 2A is a simplified plot illustrating peak-to-valley heights as a function of
polishing time for different polishing configurations according to an embodiment of
the present invention. As illustrated in FIG. 2A, a plot of the peak-to-valley height
of the optical element as a function of time of polishing is illustrated for various
polishing configurations. As illustrated in the figure, as the parameters illustrated
in FIG. 1 were addressed by the inventors, optical elements can be polished with little
to no change in the peak-to-valley height as a function of polishing time. As illustrated
by the "Pad wear reduced" curve (#5), the inventors have determined that as you polish,
the pad changes shape and as a result that shape changes the pressure distribution
on the optical element as you polish. Embodiments of the present invention, therefore,
use a septum to contact the lap and achieve essentially the opposite wear (i.e., spatially)
that the optical element is producing, thereby counterbalancing the pad wear to produce
spatially uniform pad wear. Thus, embodiments of the present invention provide for
reduction in the viscoelastic effect as illustrated in curve #6, producing a substantially
flat peak-to-valley height as a function of time.
[0019] FIGS. 2B-2G illustrate different polishing configurations according to an embodiment
of the present invention. The parameters illustrated in FIGS. 2B-2G are matched to
the curve numbers in FIG. 2A.
[0020] The inventors have determined that although FIG. 2A illustrates stable peak-to-valley
heights for plot #6 (Viscoelastic reduce (77)), at times longer than 100 hours, the
peak-to-valley height can increase to higher levels, increasing the peak-to-valley
height as a function of time. FIG. 2H is a simplified plot illustrating peak-to-valley
heights as a function of polishing time for a polishing configuration according to
an embodiment of the present invention. As illustrated in FIG. 2H, the convergence
point is migrating in the time period between 0 hours and ∼150 hours. Without limiting
embodiments of the present invention, the inventors believe that one mechanism potentially
responsible for the migration of the convergence point is that the balance between
the pad wear caused by the optical element and the pad wear caused by the septum is
disturbed, resulting in the increase in peak-to-valley height.
[0021] Embodiments of the present invention adjust the convergence point by removing the
optical element being polished and operating the polishing system with only the septum.
By running the system with only the septum, the convergence point is adjusted to return
the peak-to-valley height to a value less than a predetermined level. Because the
migration of the convergence point occurs over a period longer than the period associated
with a polishing operation for a single optical element. As an example, a polishing
time for a particular optical element may be 10 hours, with numerous (e.g., 15 optical
elements) being polished in the ∼150 hour period illustrated in FIG. 2H prior to the
peak-to-valley height increasing above 2.5 µm. The adjustment of the convergence point
is therefore provided over a long-term time period in comparison to the time period
typically utilized to polish a single optical element. Embodiments of the present
invention are not limited to adjustment of the convergence point over such a long-term
time period, but the following example is presented in terms of a time period associated
with polishing processes for multiple optical elements.
[0022] Referring to FIG. 2H, the convergence point initially migrated to from about 0.5
µm to about 2.5 µm during the first 150 hours of polishing. In order to reduce the
value of the convergence point, embodiments of the present invention remove the optical
element in order to operate the polishing system using only the septum for a period
of time in order to reduce the peak-to-valley height to a predetermined level. As
illustrated in FIG. 2H, operation of the polishing system using only the 0.6 psi septum
during the period from ∼200 hours to ∼400 hours reduces the convergence point as illustrated
by the peak-to-valley height dropping to 0.48 mm. As shown, the rate of decrease in
the peak-to-valley height is relatively slow (e.g., ∼1.7 µm/212 hours = 7.3 nm/hr),
but is controllable and substantially linear. In the period after ∼400 hours, both
a septum and an optical element are utilized, which results in a renewed drift in
the convergence point during the period from ∼400 hours to ∼500 hours. As illustrated
by the last few data points, polishing using the septum only after ∼500 hours produces
a reduction in the convergence point as expected. Thus, embodiments utilize a process
in which polishing of a septum (e.g., a 0.6 psi septum) without the use of an optical
element as a method to fine tune the convergence point. One of ordinary skill in the
art would recognize many variations, modifications, and alternatives.
[0023] Additional description related to convergent pad polishing is provided in "
Convergent Pad Polishing of Amorphous Silica," Tayyab Suratwala, Rusty Steele, Michael
Feit, Richard Desjardin, Dan Mason, International Journal of Applied Glass Science,
Special Issue: Part 1, The Flow and Fracture of Advanced Glasses Part 2, General Glass
Science, Volume 3, Issue 1, pages 14-28, March 2012.
[0024] FIG. 17 is a simplified flowchart illustrating a method of polishing a set of optical
elements according to an embodiment of the present invention. The method 1700 includes
polishing a first subset of the optical elements using a septum and a polishing process
characterized by a peak-to-valley height less than a first predetermined value (1710).
The method also includes determining that the peak-to-valley height is greater than
or equal to the first predetermined value (1712). Once the peak-to-valley height reaches
the first predetermined value, the last optical element of the first subset of optical
elements is removed and the polishing system is operated with no optical element for
a period of time (1714). After the period of time, a determination is made that the
peak-to-valley height has decreased to less than a second predetermined value (1716).
In some embodiments, the second predetermined value is less than the first predetermined
value. In other embodiments, the second predetermined value is equal to the first
predetermined value.
[0025] In some embodiments, operation of the polishing system during the adjustment of the
convergence point utilizes the septum without an optical element, one of the optical
elements (as discussed in the alternative embodiment below), a device other than the
septum or an optical element, or the like. Thus, shapes other than the septum that
adjust the convergence point are included within the scope of the present invention.
[0026] Once the peak-to-valley height reaches the second predetermined value, a second subset
of the optical elements is polished using the septum and the polishing process characterized
by a peak-to-valley height less than the first predetermined value (1718).
[0027] In an alternative embodiment in which the peak-to-valley height increases in a negative
direction as a function of polishing time, the method illustrated in FIG. 17 can be
modified to remove the septum and polish one of the optical elements in the set of
optical elements or a dummy optical element without the use of the septum, thereby
modifying process 1714. Thus, the peak-to-valley height increasing in a negative direction
can be adjusted using this complementary correction method.
[0028] FIG. 3A is a simplified plot illustrating polishing convergence for varying initial
shapes according to an embodiment of the present invention. In FIG. 3A, the optical
element was a low aspect ratio round workpiece. As illustrated in FIG. 3A, the peak-to-valley
variation in the workpiece (i.e., the optical element), is originally about 7 µm for
Experiment 79 (i.e., about 14 waves) and is reduced to about -1 µm (i.e., about 2
waves). For experiment 80, the original peak-to-valley variation is about -7 µm and
is reduced to about -1.5 µm. Thus, embodiments of the present invention provide a
convergent polishing technique that results in optical polishing that converges to
a uniform smoothness independent of the original variations in the optical element.
Although the current convergence band illustrated in FIG. 3A is characterized by a
peak-to-valley variation less about 0.5 µm wide and negative, the present invention
is not limited to this particular variation and other bands with narrower variation
centered at zero are included within the scope of the present invention.
[0029] Utilizing embodiments of the present invention, figure convergence is driven by the
mismatch between the lap and the optic shape, enabling a single iteration, initial-surface-independent
polishing process. During polishing, the optic will converge to the same figure as
the lap due to the optic-lap mismatch normalization of pressure. Thus, embodiments
of the present invention provide for convergence of the polishing process to a band
characterized by a predetermined peak-to-valley height, with the peak-to-valley height
remaining in the band for extended periods of time.
[0030] One of the benefits provided by the present invention is that the convergent polishing
process terminates at a constant peak-to-valley variation and stays at this convergent
value for an extended period of time. In contrast with conventional polishing techniques
in which polishing has to be terminated at a precise time in order to not over-polish,
the convergent polishing technique is self-terminating in a single iteration, providing
the desired shape based on the shape of the lap independent of the initial surface
of the optical element.
[0031] FIG. 3B is a simplified plot illustrating polishing convergence for a low aspect
ratio round optical element according to an embodiment of the present invention. The
polishing pad utilized in the polishing process illustrated in FIG. 3B (i.e., an IC1000™
polishing pad available from Dow Chemical Company of Midland, MI) is different than
the polishing pad utilized in the polishing process illustrated in FIG. 3A (i.e.,
a Suba™ 550 polishing pad available from Dow Chemical Company). FIG. 3C is a simplified
plot illustrating polishing convergence for a square optical element according to
an embodiment of the present invention. FIG. 3D is a simplified plot illustrating
polishing convergence for a round, high aspect ratio optical element according to
an embodiment of the present invention.
[0032] As illustrated in FIGS. 3A-3D, the peak-to-valley height converges to a predetermined
band as a function of polishing time for workpieces with different initial surface
figures and for four different configurations. As an example, in FIG. 3C, a low aspect
ratio square workpiece was polished using an IC1000™ polishing pad and in FIG. 3D,
a high aspect ratio round (ground or polished) workpiece was polished using an IC1000™
polishing pad. In the polishing runs illustrated in these figures, the workpieces,
which were characterized by varying initial surface figure, were polished identically,
with all of the workpieces converging to a final, nominally flat shape, thus demonstrating
convergent full aperture polishing.
[0033] FIGS. 4A-4E are surface contours illustrating peak-to-valley height at various polishing
times according to an embodiment of the present invention. The original surface is
illustrated in FIG. 4A, with a peak-to-valley height variation (PV) of 6.5 µm. The
surface after 1 hour of polishing is illustrated in FIG. 4B, with PV = 4.64 µm. Subsequent
polishing times are illustrated in FIGS. 4C-4E: 2 hours of polishing with PV = 3.59
µm (4C); 6 hours of polishing with PV = -1.04 µm (4D); and 24 hours of polishing with
PV = -0.95 µm (4E). As illustrated in FIGS. 4D and 4E, the convergent polishing process
terminates at a fixed PV after a predetermined period of time.
[0034] FIG. 5A is a simplified perspective illustration of a polishing septum according
to an embodiment of the present invention. The septum 500 in the embodiment illustrated
in FIG. 5A includes a curve 510 shaped to receive a round optical element. In other
embodiments, the septum, which can be a sacrificial workpiece that also results in
pad wear that counteracts the spatially non-uniform pad wear caused by the optical
element being polished) is modified to receive optical elements, which may be referred
to as workpieces, that have different shapes, including square optics, rectangular
optics, or the like. The septum 500 can include a stack of materials as illustrated
in FIG. 5B, for example, a structural layer 520 formed, for example, from 25 mm of
stainless steel or other materials with sufficient rigidity and density, a compliance
layer 522 formed, for example, from 3 mm of rubber or other compliant material, and
a polishing layer 524 formed, for example, from 1.1 mm of fused silica or other material
comparable to the optical element being polished. Depending on the desired mass of
the septum, the materials utilized in the various layers can be modified to provide
the functions of rigidity/mass, compliance, and polishing similarity. As an example,
the structural layer could be formed from aluminum or other material that is dense,
including laminated materials, to preferably provide a low aspect ratio for the septum.
Although the septum illustrated in FIG. 5A is suitable for polishing of a circular
optical elements, other shapes including square and rectangular optical elements are
included within the scope of the present invention.
[0035] The septum thus provides a flat shape due to the compliance layer that enables normalization
of the pressure to a uniform pressure across the septum as applied to the pad. Materials
of than rubber, for example, a soft polymer, foam, silicones, combinations thereof,
or the like, could be utilized. The compliance layer can be bonded to the structural
layer using epoxies or other adhesives as needed. The use of the same material for
the polishing layer as the optic being polished is useful in providing the same pad
wear rate, but other materials can be utilized as appropriate to the particular application.
The use of a material that is different from the optic being polished will result
in a different septum shape as will be evident to one of skill in the art. In the
septum design illustrated in FIG. 5A, the pressure (i.e., the load) on lap resulting
from the septum (i.e., 0.3 psi) is matched to the pressure from the optic. In other
designs, a different septum shape is produced by specifying a different pressure between
the septum and the optic.
[0036] FIG. 6 is a simplified plot of pad wear rate as a function of radial distance according
to an embodiment of the present invention. Referring to FIG. 6, the wear due to the
workpiece (i.e., the wear rate of the polishing pad) is illustrated by the area crosshatched
to the right as a function of the distance from the center of the polisher. This area
under the curve illustrates how much the pad is going to wear if you just put the
optical element on the lapping pad. For the illustrated graph, the optical element
(also referred to as an optic), is positioned at a location 25 mm from the center
of the polisher with a diameter of 100 mm. Where the optic makes no contact with the
pad (e.g., from 0-25 mm), there is no pad wear, resulting in a pad wear rate of zero
in this region. Similar zero pad wear is illustrated at distances greater than 125
mm. Considering the illustrated wear rate, as time progresses, the inverse of this
curve will be the shape of the groove worn in the pad during polishing.
[0037] The polishing pad wear resulting from the septum (illustrated as complimentary wear
by the area crosshatched to the left), is provided to produce an overall pad wear
rate that is constant as a function of distance (C). As will be evident to one of
skill in the art, the difference between the constant value and the wear due to the
workpiece will provide a guide for the design of the shape of the septum that will
produce the illustrate wear rate.
[0038] The pad wear rate can be represented by a combination of the pad wear due to the
workpiece (i.e., the optical element) and the pad wear due to the septum:

where
r = distance from the center of the pad,
s = displacement of the optical element from the center of the pad,
kL = Preston coefficient (the same value if the optical element and the polishing surface
of the septum are the same material),
µ = friction coefficient,
σ= load (pressure), which can be the same for both the optical element and the septum,
fo(r) = circumferential width of the optical element at r,
fs(r) = circumferential width of the septum at r,
Vro = relative velocity between the optical element and the pad at r, equal to Ros if Ro = RL,
Vrs = relative velocity between the septum and the pad at r, equal to RLr if Ro = RL,
Ro = rotation rate of the optical element, and
RL = rotation rate of the lap (i.e., the pad).
[0039] The shape of the septum for a constant pad wear rate
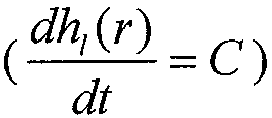
is determined by computing the width of the septum as:

For a circular optical element,
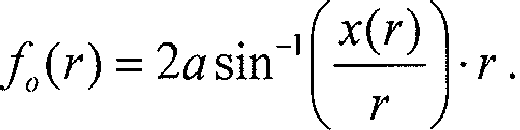
[0040] The septums provided by embodiments of the present invention, as illustrated in FIG.
5A, provide benefits not available using conventional polishing techniques. The shape
of the septum is designed, using the Preston equation as described in relation to
FIGS. 6 and 7, to provide for a uniform pad wear rate as a function of position across
the optic. In some embodiments, the uniformity of pad wear is characterized by a pad
wear rate value differing less than 5% over the portion of the pad in contact with
the optical element. In other embodiments, the pad wear rate value differs less than
2%, less than 1.5%, less than 1%, less than 0.75%, less than 0.5%, less than 0.4%,
less than 0.3%, less than 0.3%, less than 0.2%, less than 0.1%, less than 0.05%, less
than 0.025%, or less than 0.01%. For example, a first pad wear rate as a function
of position is associated with the wear due to the optical element and a second pad
wear rate as a function of position is associated with the septum (see FIG. 6). The
sum of these pad wear rates provides a substantially uniform rate at portions of the
pad that are in contact with the optical element. Although some embodiments provides
less than a wave of As will be evident to one of skill in the art, the pad wear rate
uniformity extends to portions of the pad not in contact with the optical element
(e.g., at radial distances less than 25 mm and greater than 125 mm in FIG. 6) as appropriate
to the particular application, although the uniformity may decrease in these regions.
One of ordinary skill in the art would recognize many variations, modifications, and
alternatives.
[0041] It should be noted that the use of septums as described herein may also have other
mutual benefits in addition to improving spatial pad wear uniformity, due to other
phenomena that scale linearly with velocity and pressure. Some examples of such phenomena
include pad compression and viscoelasticity, pad glazing, friction-induced temperature
effects, slurry distribution, and the like.
[0042] Utilizing embodiments of the present invention, the pad wear as a function of position
is substantially uniform as a function of position, for example, less than several
waves for optical elements. In an embodiment, the pad wear uniformity is within a
wave over the radial distance in contact with the optical element, although the uniformity
may be characterized by even more uniform pad wear, for example, less than a wave.
[0043] FIG. 7 is a simplified plot of septum width as a function of radial distance according
to an embodiment of the present invention. The septum width in FIG. 7 (i.e., a circumferential
width) is bounded by the maximum thickness set by the circumference of the lap at
the particular radial distance (there is only so much circumference available to cover
with the septum at small radial distances) and the minimum thickness set by the viscoelastic
and the rigid punch effect. For softer pads, the viscoelastic effect is more prominent,
whereas for harder pads, the rigid punch effect is more prominent.
[0044] In FIG. 7, the shape of the septum is determined for a circular optic, but other
shapes for the optical element are included within the scope of the present invention.
Utilizing the equations described herein, the loading of the septum can be different
from the loading of the optic, for example, even a non-uniform loading. The function
f
o(s) can be calculated for a given shape, for example, a circular or rectangular optic,
and then put into this formula to define the septum shape. The functions f
o(r) and f
s(r), called circumferential widths here, are defined as the fraction of the lap circumference
at radius r that is covered by the optic or septum, respectively.
[0045] It will be appreciated that at portions of the septum near the center of the polisher
(small radial distances on the lap), the constant value illustrated in FIG. 6 may
not be achievable since the radial velocity tends toward zero as the radial distance
decreases. However, since the optic is located a finite distance from the center (e.g.,
25 mm in the illustrated embodiment), this design constraint is met by the septum
designs described herein. Because the optic does not overlap with radial distances
less than 25 mm, a design flexibility for the constant pad wear rate is provided at
radial distances not overlapping with the optic.
[0046] FIGS. 8A-8C are simplified plots of septum load as a function of radial distance
according to an embodiment of the present invention. Embodiments of the present invention
can utilize septums that uniformly loaded (FIG. 8A), differentially loaded (FIG. 8B),
or continuously loaded (FIG. 8C). The plots in FIGS. 8A-8C illustrate that, as discussed
in relation to the pad wear rate, the load (o(r)) can be a function of position.
[0047] FIG. 9A is a simplified schematic diagram illustrating scratching by rogue particles.
In some optical element polishing applications, for example, for high energy laser
and amplifier systems, stringent requirements can be placed on the scratch density.
Without limiting embodiments of the present invention, the inventors believe that
some scratches are caused during polishing by rogue particles, which are particles
larger than other particles present in the polishing slurry, for example, either a
foreign particle or particles with a particle size distribution larger than the average
particle size of the other particles in the slurry. As shown in FIG. 9A, the rogue
particles produce a higher load on the optic and produce a scratch or a series of
scratches. Despite attempts to filter out rogue particles, scratching of optics is
still observed. FIG. 9B is an image illustrating scratching by rogue particles.
[0048] Without limiting embodiments of the present invention, the inventors believe that
an additional source producing rogue particles is the drying of the slurry. For example,
for polishing compounds including cerium oxide, not only does the slurry dry out,
but it chemically reacts with itself to produce, from a soft agglomerate, a hard agglomerate
upon drying. The agglomerates can then produce scratches as illustrated in FIG. 9B.
[0049] Embodiments of the present invention prevent drying of the slurry by enclosing the
polishing system, which prevents foreign particles from entering, but also provides
a high humidity environment so the slurry is prevented from drying out. A rinsing
system can be used to rinse the optic when removed from the system to prevent slurry
from remaining on the optic. Thus, the rinsed optic can be dried after removal without
the drying of the slurry, which was removed during the rinsing process. As an additional
aid in rinsing of slurry from the system, system components can be coated with a fluorinated
polymer layer to reduce the adhesion between the slurry and the various system components.
[0050] FIG. 10 is a simplified perspective diagram of a high humidity polishing system according
to an embodiment of the present invention. The high humidity polishing system 1000
includes a polishing surface 1010, which can be a polishing pad, and an optic 1012
partially surrounded by a septum 1014. A moveable cover 1020 is able to be positioned
in contact with an enclosure 1022 to form a controlled environment surrounding the
polishing surface. Inputs and output ports for polishing slurry (not shown) and an
input port 1030 and an output port 1032 for a humid gas (e.g., water vapor) are provided
as part of the system.
[0051] In the embodiment illustrated in FIG. 10, the humidity inside the polishing system
is higher than the ambient humidity, for example, higher than 80%, higher than 85%,
higher than 90%, higher than 95%, higher than 97%, higher than 98%, higher than 99%
and up to 100%. In some embodiments, the humidity is provided at a high level to prevent
substantial drying of the slurry in the system. The lack of drying in the environment
prevents the formation of the hard agglomerates and the associated scratching.
[0052] FIG. 11 is a simplified plan view of a portion of a high humidity polishing system
differing in some respects from the high humidity polishing system illustrated in
FIG. 10. As illustrated in FIG. 11, an optic 1105 is placed on a lap 1110 and spatially
controlled using guide wheels. In the example illustrated in FIG. 11, a different
septum design is used in which a mirror septum 1120 is provided to produce uniform
pad wear. A 100% humidity feed port 1030 is provided adjacent the lap 1110 so that
the polishing environment can provide the desired controlled high humidity atmosphere
in a manner similar to a sealed chamber (e.g., a hermetic chamber 1107). Embodiments
of the present invention are not represented by the design illustrated in FIG. 11,
but this is provided merely by way of example.
[0053] FIG. 12 illustrates plots of normalized interface height for polishing solutions
at a range of dilutions as a function of time according to an embodiment of the present
invention. The normalized interface height as a function of time provides insight
into the settling properties of the illustrates slurries since the interface between
the slurry and the solvent separating out of the slurry decreases in height as the
slurry settles to the bottom of the container (e.g., a graduated cylinder). Hastilite
PO mixed at a 1:4 ratio with DI water settles most quickly, with the normalized interface
height dropping to 30% within about 25 minutes. A 1:1 dilution of Hastilite PO and
DI water increases the settling time by an order of magnitude, with a 30% normalized
interface height being reached in about 300 minutes. The undiluted Hastilite PO provides
the longest settling time, dropping to around 60% at 300 minutes. Therefore, the dilution
of the slurry, for example, Hastilite PO, impacts the settling time.
[0054] FIG. 13 illustrates plots of normalized interface height for polishing solutions
under the influence of agitation according to an embodiment of the present invention.
As illustrated in FIG. 13, agitation produces negligible differences in the settling
times for the slurry diluted in either DI water or tap water.
[0055] In addition to dilution effects, the inventors have determined that stabilization
of the slurry and increases in settling time can be achieved by the addition of an
additive to the slurry that prevents agglomeration. FIG. 14 illustrates plots of normalized
interface height for polishing solutions as a function of time according to an embodiment
of the present invention. The slurry illustrated in FIG. 14 is Hastilite PO, but other
slurries are included within the scope of the present invention. Referring to FIG.
14, Hastilite PO diluted to Baume 9 (squares) is characterized by the fastest settling
time, dropping to 10% of the original normalized interface height in a period of about
30 minutes. The neat formulation of Hastilite PO (crosses) provides an increased settling
time in a manner similar to the dilution effects illustrated in FIG. 12. Addition
of an additive to prevent agglomeration provides the greatest settling times as illustrated
by Hastilite PO diluted to Baume 9 with 1 % volume of the surfactant µ-90 (diamonds).
As illustrated in FIG. 14, the addition of the surfactant increases the settling time
to provide a normalized interface height of almost 90% of the original height at 800
minutes.
[0056] Exemplary anionic surfactants in addition to µ-90 include Alkyl sulfates (e.g., Sodium
dodecyl sulfate, ammonium lauryl sulfate, or the like); Alkyl sulfonates (e.g., Dodecyl
benzene sulfonic acid, Sulfonic 100, Calimulse EM-99, or the like); Alkyl ether phosphates
(e.g., Triton H66, Triton QS44, or the like); Alkyl carboxylates (e.g. Sodium stearate
or the like), or other suitable anionic surfactants. It should be noted that the surfactant,
which can be used as an additive to the polishing slurry can include sodium, ammonium,
or potassium salts in which the counterion is not active. The inventors have determined
that the stabilization of the slurry by the surfactant (at an appropriate pH in some
embodiments) provides for improved polishing results.
[0057] Embodiments of the present invention are not limited to the use of anionic surfactants,
but can also use cationic surfactants. Exemplary cationic surfactants include Trimethylalkylammonium
chlorides (e.g. cetyl trimethylammonium bromide (CTAB), distearyl dimethyl ammonium
chloride, or the like); Benzalkonium chlorides; Alkylpyridinium chlorides (e.g. Cetyl
pyridinium chloride); or other suitable cationic surfactants. It should be noted that
the surfactant can include chloride or bromide salts in which the counterion is not
active.
[0058] In some implementations, the surfactant is effective to separate the polishing by-products
from optical element undergoing polishing. The presence of the by-product can reduce
the stability of the polishing slurry. In some embodiments, the surfactant is effective
to prevent the agglomeration of the by-products, thereby increasing the long-term
stability of the polishing slurry. Examples of by-products are cations (such as K+,
Na+, Ca2+, Mg2+, etc) from the polished away glass during polishing.
[0059] In some embodiments, the water used to prepare the slurry may contain varying concentrations
of metallic cations. In addition, cations such as Na+, B3+, Fe2+, Ca2+, Mg2+, and
A13+ are released into the slurry as by-products of the polishing process. The presence
of these ions has the potential to reduce stabilizer efficacy by disrupting the electrostatic
interaction between the slurry particles and stabilizer molecules.
[0060] Chelation agents (e.g., glycine, citric acid, ethylenediaminetetraacetic acid (EDTA),
or the like) form favorable complexes with cations, sequestering them in solution
and preventing their interaction with the slurry particles. Therefore, the addition
of a chelation agent to the slurry may both improve initial stabilization efficiency
and may prolong its stability as polishing by-products accumulate. Thus, embodiments
of the present invention utilize chelation agents to improve slurry stabilization.
[0061] FIG. 15 is a simplified plot of relative interface height for stabilized and unstabilized
polishing solutions as a function of time according to an embodiment of the present
invention. As illustrated in FIG. 15, the stabilization of the slurry by, for example,
the addition of the anionic surfactant additive, produces significant increases in
settling time.
[0062] FIG. 16 is a polishing solution volume for stabilized and unstabilized polishing
solutions as a function of particle size according to an embodiment of the present
invention. In addition to increases in settling time and stabilization of the slurry,
the addition of the additive to the slurry results in a reduction in the particle
sizes in the slurry. Referring to FIG. 15, the particle size distribution for the
stabilized slurry is characterized by the majority of the particles being less than
1 µm in size, with a peak of the distribution at about 0.25 µm. For the unstabilized
slurry, the peak of the distribution is centered at about 1 µm with either half or
the majority of particles being characterized by the larger particle size distribution.
The stabilized slurry results in an improved polishing outcome because the smaller
particle size distribution provides smaller slurry particles during the polishing
process. The inventors have demonstrated that the addition of the additive provides
a slurry that is still characterized by an acceptable material removal rate and improved
micro-roughness.
[0063] The inventors have determined that in some optical finishing operations utilizing
grinding followed by polishing of thin optical elements, stress is introduced by the
grinding operation, resulting in a tendency of the optical element to bend in response
to the grinding induced stress. In order to reduce the stress, the optical element
is chemically etched to remove surface layers, thereby reducing the stress present
in the optical element. As an example, the optical element can be exposed to an acid
or other suitable etchant (e.g., immersed in an acid bath) after grinding to remove
a predetermined surface region of the optical element.
[0064] In an embodiment, an optical element characterized by a first bend curvature is ground.
After grinding, the optical element is characterized by a second bend curvature greater
than the first bend curvature. In some embodiments, the increase in bend curvature
results from stress introduced into the workpiece during the grinding process. The
optical element is chemically etched to remove a predetermined portion of the optical
element. After chemical etching, the optical element is characterized by a third bend
curvature less than the second bend curvature. In some embodiments, the third bend
curvature is less than or equal to the first bend curvature, returning the optical
element to the curvature characterizing the optical element before the beginning of
the finishing process. Thus, the chemical etching process reduces the stress introduced
during grinding in some embodiments.
[0065] FIGS. 18A-18C are images illustrating surface curvature before grinding, after grinding,
and after chemical etching according to an embodiment of the present invention. As
illustrated in FIG. 18A, the surface curvature prior to grinding is characterized
by a peak-to-valley value of 1.29 µm. Due to the instruction of stress by the grinding
process, the surface curvature after grinding is characterized by a peak-to-valley
value of 3.65 µm as illustrated in FIG. 18B. Embodiments of the present invention
utilize chemical etching of the ground surface to remove residual stress present after
the grinding process to return the figure to approximately the original shape as shown
in FIG. 18C, in which the surface curvature after post-grinding etching is characterized
by a peak-to-valley value of 1.16 µm. Thus, embodiments of the present invention provide
methods and systems in which chemical etching is a useful mitigation technique to
reduce or eliminate residual stress contributing to optic/lap mismatch.
[0066] The inventors have determined that in some polishing applications, pitch button bonding
techniques can be used to improve the quality of the finished optical elements. Table
1 provides a summary of pitch button bonding (PBB) processes (also referred to as
pitch button blocking processes) showing process parameters and the measured changes
in surface figure, such as the change in the peak-to-valley height of the workpiece
(also referred to as an optical element) (ΔPV), before and after blocking. As described
herein, PBB includes a mounting technique that uses small islands of pitch between
the workpiece and the mount that are cooled from the softening temperature of the
pitch. At room temperature, the workpiece-pitch button-mount system is stiff, and
the workpiece largely maintains its initial surface figure. After polishing using
PBB techniques, the workpiece converges to the shape of the lap because, without limiting
embodiments of the present invention, of the lack of workpiece bending and a dominance
of the workpiece-lap mismatch due to the workpiece shape effect on the pressure distribution.
Table 1
Process |
Process |
Workpiece |
Pitch |
Process Temp (C) |
# of Buttons (N) |
Button Thick, t (mm) |
Button Diameter d (mm) |
Button spacing (dm) |
Area Fraction |
ΔPV (µm)* |
R16 |
S1 |
FS |
G73 |
65 |
37 |
1 |
10 |
4.6 |
0.370 |
-0.15 |
R13 |
S2 |
FS |
G73 |
65 |
37 |
1 |
10 |
4.6 |
0.370 |
-0.44 |
R14 |
S3 |
FS |
G82 |
72 |
3 |
1 |
10 |
41.2 |
0.030 |
-0.01 |
R15 |
S4 |
FS |
G82 |
72 |
4 |
1 |
9 |
35.3 |
0.032 |
0.00 |
R20 |
S5 |
FS |
G82 |
72 |
9 |
1.2 |
8 |
21.5 |
0.058 |
-0.06 |
R17 |
S6 |
FS |
G82 |
72 |
21 |
1.1 |
9 |
10.3 |
0.170 |
-0.08 |
R19 |
S7 |
FS |
G82 |
72 |
21 |
1.2 |
8 |
11.3 |
0.134 |
0.00 |
R7 |
S8 |
FS |
G82 |
72 |
37 |
1.1 |
11 |
3.6 |
0.448 |
-1.00 |
R8 |
S9 |
FS |
G82 |
72 |
37 |
0.9 |
12 |
2.6 |
0.533 |
-0.60 |
R9 |
S10 |
FS |
G82 |
72 |
37 |
0.8 |
13 |
1.6 |
0.625 |
-1.52 |
R10 |
S11 |
FS |
G82 |
72 |
37 |
1 |
11 |
3.6 |
0.448 |
-0.60 |
R11 |
S12 |
FS |
G82 |
72 |
37 |
0.7 |
14 |
0.6 |
0.725 |
-1.20 |
R12 |
S13 |
FS |
G82 |
72 |
37 |
0.8 |
11 |
3.6 |
0.448 |
-1.20 |
R31 |
S14 |
FS |
G82 |
78 |
1 |
2 |
NA |
NA |
1.000 |
1.73 |
R107 |
S15 |
FS |
Cycad |
75 |
37 |
1.2 |
8 |
6.6 |
0.237 |
-0.33 |
R104 |
S16 |
FS |
Cycad |
75 |
37 |
1.3 |
7 |
7.6 |
0.181 |
-0.26 |
R3 |
S17 |
FS |
Cycad |
92 |
1 |
NA |
NA |
NA |
1.000 |
5.53 |
R73 |
S18 |
FS |
BP-1 |
60 |
11 |
0.85 |
5 |
21.7 |
0.028 |
0.00 |
R75 |
S19 |
FS |
BP-1 |
60 |
11 |
0.7 |
4.5 |
22.2 |
0.022 |
-0.10 |
R76 |
S20 |
FS |
BP-1 |
60 |
11 |
0.7 |
4.5 |
22.2 |
0.022 |
-0.02 |
R74 |
S21 |
FS |
BP-1 |
60 |
11 |
1.35 |
6.5 |
20.2 |
0.046 |
-0.04 |
R77 |
S22 |
FS |
BP-1 |
60 |
11 |
1.4 |
9 |
17.7 |
0.089 |
-0.03 |
R78 |
S23 |
FS |
BP-1 |
60 |
11 |
1.5 |
11.5 |
15.2 |
0.145 |
-0.18 |
R88 |
S24 |
FS |
BP-1 |
60 |
37 |
0.75 |
9 |
5.6 |
0.300 |
-0.15 |
R89 |
S25 |
FS |
BP-1 |
105 |
1 |
NA |
0.5 |
NA |
1.000 |
4.90 |
R91 |
S23 |
FS |
BP-1 |
105 |
1 |
NA |
0.8 |
NA |
1.000 |
6.40 |
R71 |
P1 |
P |
BP-1 |
60 |
11 |
0.6 |
4.5 |
22.2 |
0.022 |
0.04 |
R72 |
P2 |
P |
BP-1 |
60 |
11 |
0.9 |
4.5 |
22.2 |
0.022 |
0.03 |
R69 |
P3 |
P |
BP-1 |
60 |
11 |
0.8 |
6.5 |
20.2 |
0.046 |
0.23 |
R70 |
P4 |
P |
BP-1 |
60 |
21 |
0.6 |
5 |
14.3 |
0.053 |
0.43 |
R68 |
P5 |
P |
BP-1 |
60 |
11 |
1 |
7.5 |
19.2 |
0.062 |
0.28 |
R67 |
P6 |
P |
BP-1 |
63 |
11 |
0.6 |
9 |
17.7 |
0.089 |
0.46 |
R66 |
P7 |
P |
BP-1 |
70 |
11 |
0.4 |
13.5 |
13.2 |
0.200 |
1.10 |
R87 |
P8 |
P |
BP-1 |
60 |
37 |
0.55 |
8 |
6.6 |
0.237 |
1.10 |
R90 |
P9 |
P |
BP-1 |
105 |
1 |
NA |
0.5 |
NA |
1.000 |
7.90 |
R92 |
P10 |
P |
BP-1 |
105 |
1 |
NA |
0.85 |
NA |
1.000 |
9.90 |
P= Phosphate Glass;
FS= fused silica;
NA= not applicable;
*sign convention (negative is convex, positive is concave) |
[0067] The inventors have determined that an optical element (e.g., a fused silica or phosphate
glass optic) can be bonded to a substrate (e.g., a stainless steel blank) using pitch
buttons. The geometry of the pitch buttons, as described more fully below, prevents
the deflection of the workpiece due to differences in coefficients of thermal expansion
between the workpiece and the substrate. In some embodiments, isothermal cooling is
utilized to reduce or eliminate deflection of the workpiece.
[0068] FIGS. 19A-19F are simplified schematic diagrams illustrating a method of performing
pitch button bonding according to an embodiment of the present invention. As illustrated
in FIG. 19A, an adhesion/protection layer that increases adhesion between the glass-pitch
interface and protects the glass surface from staining due to the pitch contact, residual
slurry making contact, and the like) is applied to surface S2 of the workpiece and
the reflected wavefront is measured through surface S1. The adhesion/protection layer
is a tape in some embodiments and the tape is optional in some embodiments. Pitch
buttons are applied to the surface of the tape (or surface S2 of the workpiece) as
illustrated in FIG. 19B. The application of the pitch buttons is performed in light
of several variables including the pitch type, the radius (r
p) of the pitch buttons, the thickness (tp) of the pitch buttons, the spacing (s) between
pitch buttons, and the like. The pitch buttons are annealed (e.g., in an oven) using,
for example, heating elements, as illustrated in FIG. 19C. The temperature of the
annealing process, which may vary as a function of time, is selected to bring the
whole system (e.g., glass, block, & pitch) to an elevated temperature near the temperature
of the pitch at which the pitch starts to undergo significant stress relaxation (referred
to as Tg) of the pitch and then cool the system as isothermally as possible to prevent
or reduce the impact of residual stresses deforming the workpiece shape.
[0069] FIG. 19D illustrates attachment of the workpiece with annealed pitch buttons to a
preheated substrate (e.g., an aluminum or stainless steel block) with sufficient rigidity
and mechanical properties for use during a polishing operation. Shims of a predetermined
thickness (e.g., 1.25 mm) may be used during the mounting of the workpiece to the
substrate. The mounted structure is then centered on the substrate, cooled, for example,
using air cooling, and the shims are removed as illustrated in FIG. 19E. To characterize
the optical properties of the workpiece after mounting, the reflected wavefront can
be measured through surface S1 as illustrated in FIG. 19F.
[0070] FIG. 20 is a plot illustrating the measured change in surface figure of fused silica
and phosphate glass in various PPB configurations according to an embodiment of the
present invention. As shown in FIG. 20, the changes in surface figure of fused silica
(FS) and phosphate glass (PG) optical elements for three conditions are shown. The
workpieces used in the measurements shown in FIG. 20 were 100 mm in diameter with
a thickness of 2.2 mm. For bonding with a solid layer of pitch, the relative surface
height (FS) varies from about 7.5 µm at peripheral portions to about 3.7 µm at central
portions and from about 10.1 µm to about 4.2 µm for PG.
[0071] Mounting of the workpiece using PBB techniques reduced the relative surface height
variation considerably, using first, an un-optimized PBB technique that produced a
variation of about half a micron of convex curvature (FS) and concave curvature (PS).
By optimizing the PBB process as described herein, the variation in relative surface
height is effectively reduced to zero as shown in FIG. 20.
[0072] FIG. 21 is a plot of measured thermal expansion of pitches according to an embodiment
of the present invention. Referring to FIG. 21, the thermal expansion of two pitches,
(Blocking Pitch-1 Black, available from Universal Photonics and Cycad Blackgold optical
polishing pitch available from Cycad Products) as measured using a thermal-mechanical
analysis, is illustrated. As the temperature increases, the pitches increase in dimension,
with a measured coefficient of thermal expansion of 37 x 10
-6 °C
-1 for BP1 and 43 x 10
-6 °C
-1 for Cycad.
[0073] FIG. 22A is a plot of workpiece peak-to-valley (PV) height as a function of undercooling
of pitch for a single button and three buttons according to an embodiment of the present
invention. In FIGS. 22A-22D, a fused silica workpiece (d
w=100 mm diameter, t
w=2.2 mm, E
p = 73 GPa, α = 5.4 x 10
-7 °C
-1) was utilized. The workpiece PV height after PPB is plotted as a function of degree
of undercooling of the pitch for a single button (r = 25 mm) as well as for 3 buttons
(s = 50 mm; r = 10 mm). The use of multiple pitch buttons significantly reduced the
workpiece PV height.
[0074] FIG. 22B is a plot of workpiece peak-to-valley height as a function of pitch button
radius according to an embodiment of the present invention. The pitch button radius
impacts the workpiece PV height as shown in FIG. 22B, which plots the PV height for
a single button case and for various pitch moduli, thickness, and thermal expansion
coefficients; (ΔT=54 °C).
[0075] FIG. 22C is a plot of normalized workpiece peak-to-valley height as a function of
pitch button offset according to an embodiment of the present invention. The PV height
after PBB is normalized in FIG. 22C by dividing it by the relative total button area
in microns and plotted as a function of the separation distance between buttons (d
m), measured in millimeters for 3 button and 9 button cases. For the 3 button cases,
the size of the pitch buttons are varied from 10 mm radius to 20 mm radius. The pitch
button parameters were ΔT = 54 °C; t = 1 mm; E
p = 0.22 GPa; α
p = 54 x 10
-6 °C
-1. The curve in FIG. 22C represents an empirical curve fit to the computed data.
[0076] FIG. 22D is a plot of workpiece peak-to-valley height as a function of relative total
pitch button area according to an embodiment of the present invention. FIG. 22D illustrates
3 and 9 button cases after PPB in which the spacing between buttons is kept at a value
greater than 20 mm. The line in FIG. 22D represents an empirical curve fit to the
computed data.
[0077] FIG. 23 is a simplified schematic diagram illustrating pitch button bonding parameters
according to an embodiment of the present invention. The PBB parameters include the
modulus (Ep and E
w), coefficient of thermal expansion (α
p and α
w), and the thickness (t
p and t
w) of both the pitch buttons and the workpiece, respectively. The PBB parameters also
include the radius of the pitch buttons (r
p), the radius of the workpiece (r
w), the center to center separation between pitch buttons (s), and the spacing between
pitch buttons (d
m). The total number of pitch buttons is indicated by N. The pitch buttons can have
uniform dimensions or varying dimensions as appropriate to the particular application.
Thus, both material and geometric parameters are utilized in the methods and systems
described herein.
[0078] FIGS. 24A and 24B are drawings illustrating optimized pitch button bonding patterns
for optical elements according to an embodiment of the present invention. In FIG.
24A, an optimized PBB pattern is illustrated for a 100 mm diameter fused silica workpiece
(i.e., Samples S18-S20). In FIG. 24B, an optimized PBB patter is illustrated for a
100 mm diameter phosphate glass workpiece (Samples P1-P2).
[0079] FIG. 25A is a plot of workpiece peak-to-valley height as a function of spacing between
buttons according to an embodiment of the present invention. FIG. 25A illustrates
the change in surface figure of a fused silica workpiece (i.e., 100 mm diameter x
2.2 mm thick FS optical element) in various PPB configurations using pitch materials
as a function of button spacing (d
m). FIG. 25B is a plot of workpiece peak-to-valley height as a function of area fraction
according to an embodiment of the present invention. The change in surface figure
of both fused silica and phosphate glass workpieces (i.e., 100 mm diameter x 2.2 mm
thick workpieces) is illustrated in various PBB configurations (N=11 and d
m > 20 mm) as a function of area fraction. The points in FIG. 25B represent measured
data and the lines are curve fits using α
p = 2.4 x 10
-6 °C
-1.
[0080] FIG. 26 is a simplified flowchart illustrating a method of determining pitch button
bonding parameters according to an embodiment of the present invention. The method
includes determining a peak-to-valley (PV) height value (2610) and determining a value
related to pitch area (2612). In an embodiment, the PV height value can be a minimum
acceptable PV height measured in terms of dimensions (e.g., 0.05 µm) or in terms of
the wavelength of light transmitted by the optical element (e.g., λ/10). The value
related to the pitch area (which can be referred to as an area constant) can be approximated
by the PV height variation associated with a solid layer of pitch (e.g., C = 1.0 µm).
The area constant C can be determined in some embodiments by measuring the PV height
associated with a solid pitch layer and can be valid for a given material system based
on the processing conditions (ΔT = 54 °C), the coefficient of thermal expansion (e.g.,
α
p = 54 x 10
-7 °C
-1), modulus (e.g., E
p = 0.22 GPa), pitch thickness (tp = 1.0 mm), and the like. Typically, the values of
the area constant will scale as:

where Δα is the change in thermal expansion coefficient between pitch and workpiece
material, ΔT is the temperature decrease from Tg to room temperature, and tp is the
pitch thickness. As will be evident to one of skill in the art, changing the pitch
or the workpiece will results in changes in C and the observed deflection, since,
for example, phosphate glass has a higher coefficient of thermal expansion than fused
silica. It should also be noted that fused silica deflection is convex while phosphate
glass deflection is concave. In some embodiments, it is useful to maximize the areal
coverage in order to increase the interface strength between the workpiece and the
substrate.
[0081] The method also includes computing a relative area of pitch (A
r) (2614), which is computed as:
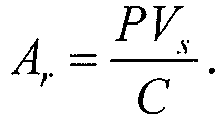
As an example, for PV
s = 0.05 µm and C = 1.0 µm, A
r = 0.05.
[0082] The method further includes computing a button radius (r
p) (2616), which is computed using:
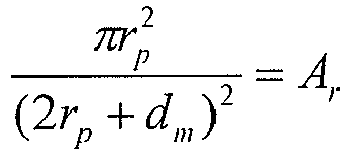
Continuing with the example above, for d
m = 23.1 mm, r
p = 3.4 mm.
[0083] The method additionally includes computing the number of pitch buttons (N) (2618),
which may be evenly spaced. The N pitch buttons are then applied to the workpiece
(2620) in accordance with the parameters computed using the method in order to couple
the pitch buttons to the workpiece. As illustrated in FIG. 19B, the pitch buttons
can be applied to an adhesive and/or protective material such as a tape or other suitable
material coupled to the workpiece. The workpiece is then mounted to a substrate, e.g.,
an optical flat comprising stainless steel, aluminum, combinations thereof, or the
like, by coupling the N pitch buttons to the substrate (2622).
[0084] It should be appreciated that the specific steps illustrated in FIG. 26 provide a
particular method of determining pitch button bonding parameters according to an embodiment
of the present invention. Other sequences of steps may also be performed according
to alternative embodiments. For example, alternative embodiments of the present invention
may perform the steps outlined above in a different order. Moreover, the individual
steps illustrated in FIG. 26 may include multiple sub-steps that may be performed
in various sequences as appropriate to the individual step. Furthermore, additional
steps may be added or removed depending on the particular applications. One of ordinary
skill in the art would recognize many variations, modifications, and alternatives.
[0085] It is also understood that the examples and embodiments described herein are for
illustrative purposes only and that various modifications or changes in light thereof
will be suggested to persons skilled in the art within the scope of the appended claims.