Technical Field
[0001] The present invention relates to an oxygen absorbing multilayer container and a method
for producing the same.
Background Art
[0002] Examples of articles which easily deteriorate or degrade under the influence of oxygen
include foods, beverages, medicinal products and cosmetics. In order to prevent oxygen
oxidation of such articles and store them for a long period of time, oxygen absorbers,
which remove oxygen within packages storing these articles, are used.
[0003] In addition, a large number of oxygen absorbing containers, which are containers
for storing these articles and to which oxygen absorption property is provided, have
been proposed. Of them, as an oxygen absorbing container having excellent oxygen barrier
performance and oxygen absorption performance in a wide range of humidity conditions
from low humidity to high humidity, an oxygen absorbing multilayer container containing
a polymer having a predetermined tetralin ring and a transition metal catalyst (see,
Patent Literature 1) has been developed.
Citation List
Patent Literature
[0004] Patent Literature 1: International Publication No.
WO 2013/077436
Summary of Invention
Technical Problem
[0005] However, conventional oxygen absorbing multilayer containers described in e.g., Patent
Literature 1 have a problem in that it is difficult to keep all of impact resistance,
molding processability and transparency at high levels and in a balanced manner, by
a combination of resins to be used in individual layers.
[0006] The present invention was made under the aforementioned circumstances and is directed
to providing an oxygen absorbing multilayer container excellent in impact resistance,
molding processability and transparency.
Solution to Problem
[0007] The present inventors have conducted intensive studies on oxygen absorbing multilayer
containers. As a result, they found that the above problem can be overcome by an oxygen
absorbing multilayer container having at least three layers of a first resin layer
containing a thermoplastic resin (b), an oxygen absorbing layer containing an oxygen
absorbing resin composition which contains a polyester compound (a) containing a constituent
unit having a tetralin ring and a transition metal catalyst, and a second resin layer
containing a thermoplastic resin (b), in this order, in which a cycloolefin polymer
having a glass transition temperature of 50 to 110°C is used as the thermoplastic
resin (b). Based on the finding, the present invention was accomplished.
[0008] More specifically, the present invention is as follows.
- <1>
An oxygen absorbing multilayer container comprising at least three layers of:
a first resin layer comprising a thermoplastic resin;
an oxygen absorbing layer comprising an oxygen absorbing resin composition which comprises
a polyester compound (a) comprising a constituent unit having a tetralin ring and
a transition metal catalyst; and
a second resin layer comprising a same type of thermoplastic resin as the thermoplastic
resin in the first resin layer, in this order,
wherein the oxygen absorbing multilayer container comprises a cycloolefin polymer
having a glass transition temperature of 50 to 110°C as the thermoplastic resin.
- <2>
The oxygen absorbing multilayer container according to [1] above, wherein a melt viscosity
of the thermoplastic resin at a shear rate of 1216 sec-1 and 260°C is 100 to 300 Pa·sec.
- <3>
The oxygen absorbing multilayer container according to [1] or [2] above, wherein an
absolute value of difference in the melt viscosity at a shear rate of 1216 sec-1 and 260°C between the thermoplastic resin and the polyester compound (a) is 0 to
150 Pa·sec.
- <4>
The oxygen absorbing multilayer container according to any one of [1] to [3] above,
wherein the polyester compound (a) comprises a constituent unit represented by the
following formula (1).
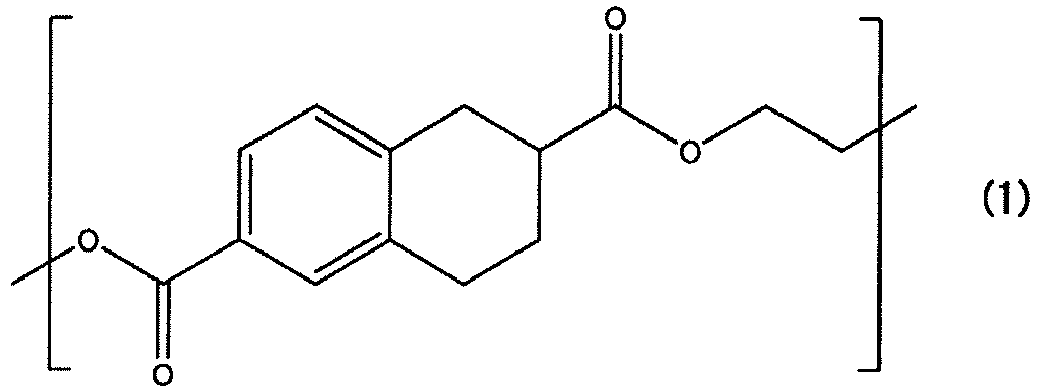
- <5>
The oxygen absorbing multilayer container according to [4] above, wherein a proportion
of the constituent unit represented by the above formula (1) based on all constituent
units in the polyester compound (a) is 50 to 100 mol%.
- <6>
The oxygen absorbing multilayer container according to any one of [1] to [5] above,
wherein the transition metal catalyst comprises at least one transition metal selected
from the group consisting of manganese, iron, cobalt, nickel and copper.
- <7>
The oxygen absorbing multilayer container according to any one of [1] to [6] above,
wherein an amount of the transition metal catalyst in terms of an amount of transition
metal is 0.001 to 10 parts by mass based on 100 parts by mass of the polyester compound.
- <8>
A method for producing the oxygen absorbing multilayer container according to any
one of [1] to [7] above, comprising
a step of forming a multilayer container by injecting at least three layers of the
first layer, the oxygen absorbing layer and the second layer from an injection cylinder,
wherein, in the step, the absolute value of difference between an injection cylinder
temperature for the first layer and an injection cylinder temperature for the oxygen
absorbing layer is 0 to 30°C.
Advantageous Effects of Invention
[0009] According to this invention, it is possible to provide an oxygen absorbing multilayer
container excellent in impact resistance, molding processability and transparency.
Furthermore, since the molding processability of the oxygen absorbing multilayer container
is improved, it is possible to provide an oxygen absorbing multilayer container further
excellent in appearance.
Description of Embodiments
[0010] Now, an embodiment for carrying out the present invention (hereinafter referred to
simply as "the present embodiment") will be described. Note that, the following embodiment
is just an example for explaining the present invention and should not be construed
as limiting the present invention to the following contents. The present invention
can be appropriately modified and carried out within the scope of the invention.
[0011] The oxygen absorbing multilayer container of the present embodiment is an oxygen
absorbing multilayer container having at least three layers of a first resin layer
(layer B1) containing a thermoplastic resin (b), an oxygen absorbing layer (layer
A) containing an oxygen absorbing resin composition which contains a polyester compound
(a) containing a constituent unit having a tetralin ring and a transition metal catalyst,
and a second resin layer (layer B2) containing the same type of thermoplastic resin
(b) as the thermoplastic resin contained in the first resin layer, in this order,
in which, a cycloolefin polymer having a glass transition temperature of 50 to 110°C
is contained as the thermoplastic resin (b). Hereinafter, the first resin layer (layer
B1) and the second resin layer (layer B2) will be sometimes collectively referred
to as "layer B".
[0012] The oxygen absorbing multilayer container of the present embodiment employs a cycloolefin
polymer (COP) having a glass transition temperature of 50 to 110°C as the thermoplastic
resin (b). Owing to this, oxygen present in the container is adsorbed, and if oxygen
permeates through the wall and enters from outside even in a small amount, such permeating
or entering oxygen is also adsorbed, with the result that e.g. deterioration of a
content (an article to be stored) stored in the container with oxygen can be prevented.
[0013] The constitution of layers of the oxygen absorbing multilayer container of the present
embodiment is not particularly limited as long as the arrangement of the layers is
B1/A/B2; more specifically, the number and types of oxygen absorbing layers (layer
A) and resin layers (layer B (layer B1, B2)) are not particularly limited. For example,
a five-layer structure having further two B layers and represented by B/B/A/B/B, i.e.,
a five-layer structure formed of three types of materials, may be employed. The oxygen
absorbing multilayer container of the present embodiment may optionally contain an
arbitrary layer such as an adhesion layer (layer AD), if necessary; for example, a
seven-layer structure consisting of four types of materials and represented by B/AD/B/A/B/AD/B,
may be employed.
[Oxygen absorbing layer (layer A)]
[0014] The oxygen absorbing layer (layer A) of the present embodiment contains an oxygen
absorbing resin composition which contains a polyester compound (a) having a tetralin
ring as a constituent unit and a transition metal catalyst.
<Polyester compound (a)>
[0015] The polyester compound (a) is not particularly limited as long as it is a polyester
compound having a tetralin ring as a constituent unit; for example, a polyester compound
described in e.g., Patent Literature 1, can be used. In view of molding processability
and oxygen absorption performance, a polyester compound (a) containing at least one
constituent unit having tetralin ring selected from the group consisting of the following
formulas (i) to (iv) is preferable. In particular, the constituent unit represented
by the general formula (i) is more preferably at least one selected from the group
consisting of the following formulas (1) to (3). Of these, a polyester compound having
a constituent unit represented by the following formula (1) is further preferable.
Herein, "having as a constituent unit" means that one or more of the constituent units
are contained in a compound. It is preferable that the constituent unit is contained
as a repeating unit in a polyester compound (a). Likewise, if the polyester compound
is a polymer, the polymer may be any one of a homopolymer of the above constituent
unit, a random copolymer of the above constituent unit and another constituent unit
and a block copolymer of the above constituent unit and another constituent unit.
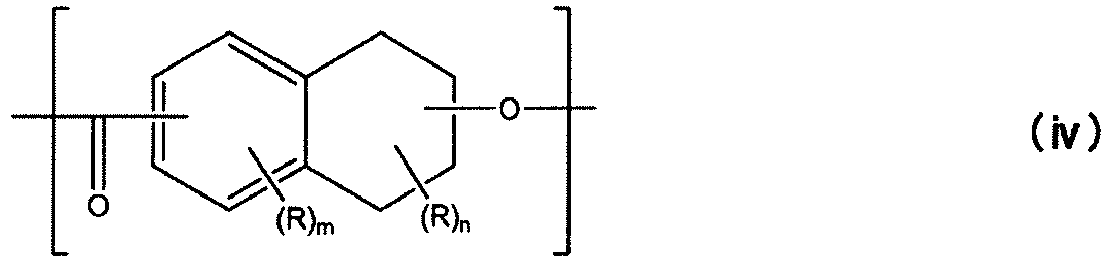
wherein, R each independently represents a hydrogen atom or a monovalent substituent;
the monovalent substituent is at least one selected from the group consisting of a
halogen atom, an alkyl group, an alkenyl group, an alkynyl group, an aryl group, a
heterocyclic group, a cyano group, a hydroxy group, a carboxyl group, an ester group,
an amide group, a nitro group, an alkoxy group, an aryloxy group, an acyl group, an
amino group, a thiol group, an alkylthio group, an arylthio group, a heterocyclic
thio group and an imide group, which may further have a substituent; m represents
an integer of 0 to 3; n represents an integer of 0 to 7, and a hydrogen atom is bonded
to at least one of the benzyl positions of the tetralin ring; and X represents a divalent
group containing at least one group selected from the group consisting of an aromatic
hydrocarbon group, a saturated or unsaturated alicyclic hydrocarbon group, a linear
or branched and saturated or unsaturated aliphatic hydrocarbon group and a heterocyclic
group.
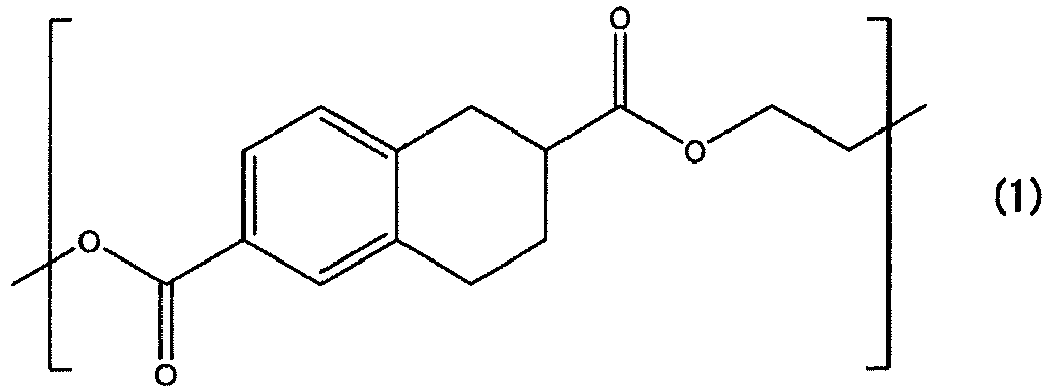
[0016] Further, in view of molding processability and oxygen absorption performance, the
proportion of the constituent unit represented by the above formula (1) based on the
all constituent units contained in the polyester compound (a), is preferably 50 to
100 mol%, more preferably 70 to 100 mol% and further preferably 90 to 100 mol%. If
the proportion of the constituent unit represented by the formula (1) falls within
the above range, the effect of the present embodiment is further improved and physical
properties of the oxygen absorbing multilayer container such as impact resistance,
molding processability, transparency and oxygen absorption performance can be maintained
at high levels and in a balanced manner.
[0017] The polyester compound (a) can further contain a constituent unit derived from at
least one polyfunctional compound selected from polyhydric alcohols of a trivalent
or more, polycarboxylic acids of a trivalent or more and derivatives thereof, and
hydroxycarboxylic acids of a trivalent or more and derivatives thereof. These polyfunctional
compounds may be used singly or in combinations of two or more. In the case where
a constituent unit derived from any one of these polyfunctional compounds is contained,
a branched structure may be introduced in the polyester compound (a), with the result
that a polyester compound (a) having a higher molecular weight than usual and improved
in viscosity can be obtained. Examples of the polyfunctional compound include, but
not limited to, polyhydric alcohols such as glycerin, trimethylol propane and pentaerythritol;
and polyvalent carboxylic acids and derivatives thereof such as trimellitic acid,
a trimellitic anhydride, pyromellitic acid and a pyromellitic anhydride. Of these,
glycerin is preferable.
[0018] In the case where the polyester compound (a) contains a constituent unit derived
from a polyfunctional compound, the proportion of the constituent unit derived from
a polyfunctional compound based on the all constituent units contained in the polyester
compound (a), is preferably 0.01 to 5 mol%, more preferably 0.1 to 3 mol% and further
preferably 0.2 to 1 mol%.
[0019] The polyester compound (a) can be produced by a known method described in e.g., Patent
Literature 1; for example, obtained by polycondensation between a monomer having a
tetralin ring or a derivative thereof and a polyfunctional compound such as a diol
or a derivative thereof. Further, into the polyester compound (a), a constituent unit
having no tetralin ring may be introduced as a copolymer component as long as it does
not affect the performance thereof. More specifically, a known compound described
in Patent Literature 1 can be used as a copolymer component.
[0020] It is preferable that a polyester compound (a) has a hydrogen atom at least one of
the benzyl positions of the tetralin ring. If a polyester compound having a hydrogen
atom at a benzyl position of the tetralin ring is used in combination with a transition
metal catalyst, the hydrogen at the benzyl position is removed. In this manner, it
is considered to produce excellent oxygen absorption performance (however, the effect
of the present embodiment is not limited to these).
[0021] According to the oxygen absorbing resin composition of the present embodiment, in
a preferable aspect thereof, generation of a low molecular-weight compound after absorption
of oxygen can be prevented. Although the reason is unknown, it is considered that
the suppression is probably made by the following mechanism of the oxidation reaction:
first, a hydrogen atom is removed from a benzyl position of the tetralin ring of a
polyester compound (a) to produce a radical, which thereafter, reacts with oxygen
to oxidize carbon at the benzyl position, with the result that a hydroxy group or
a ketone group is produced. Owing to this, in the oxygen absorbing resin composition,
no cleavage of a molecular chain by an oxidation reaction occurs and the structure
of the polyester compound (a) is maintained. Because of this, after oxygen absorption,
low molecular weight organic compounds, which are a cause of odor, are rarely produced.
As a result, an increase in intensity of odor after oxygen absorption, is suppressed;
at the same time, contamination of a content with low-molecular-weight compounds is
presumably prevented (however, the effect of the present embodiment is not limited
to these).
[0022] The glass transition temperature (Tg) of a polyester compound (a), is not particularly
limited; however, in view of e.g., the molding processability of the oxygen absorbing
multilayer container, Tg is preferably 50 to 110°C, more preferably 60 to 80°C, further
preferably 60 to 75°C and further more preferably 65 to 75°C. If the glass transition
temperature falls within the above range, the molding processability of the oxygen
absorbing multilayer container and oxygen absorption rate thereof are further improved.
Note that, the glass transition temperature herein refers to a value obtained by differential
scanning calorimetry performed in accordance with the method described in Examples
(described later).
[0023] The intrinsic viscosity (a measurement value obtained at 25°C by using a solvent
mixture of phenol and 1,1,2,2-tetrachloroethane in a mass ratio of 6: 4) of a polyester
compound (a) is not particularly limited; however, in view of the molding processability
of the oxygen absorbing multilayer container, the intrinsic viscosity is preferably
0.1 to 2.0 dL/g, more preferably 0.5 to 1.5 dL/g and further preferably 0.8 to 1.0
dL/g.
[0024] The melt viscosity of a polyester compound (a) is not particularly limited; however,
in view of the molding processability of the oxygen absorbing multilayer container,
the melt viscosity at a shear rate of 1216 sec
-1 and 260°C is preferably 100 to 300 Pa·sec and more preferably 150 to 250 Pa·sec.
If the melt viscosity falls within the above range, the molding processability of
the oxygen absorbing multilayer container is further improved.
<Transition metal catalyst>
[0025] The transition metal catalyst to be used in the oxygen absorbing resin composition
is not particularly limited as long as it can serve as a catalyst for the oxidation
reaction of a polyester compound (a), and can be appropriately selected from known
catalysts.
[0026] Specific examples of the transition metal catalyst include organic acids, halides,
phosphates, phosphites, hypophosphites, nitrates, sulfates, oxides and hydroxides
of transition metals. Examples of the transition metal to be contained in the transition
metal catalyst include, but are not limited to, titanium, vanadium, chromium, manganese,
iron, cobalt, nickel, copper, zinc, ruthenium and rhodium. Of these, manganese, iron,
cobalt, nickel and copper are preferable. Examples of the organic acids include, but
are not limited to, acetic acid, propionic acid, octanoic acid, lauric acid, stearic
acid, acetylacetone, dimethyldithiocarbamic acid, palmitic acid, 2-ethylhexanoic acid,
neodecanoic acid, linoleic acid, tall acid, oleic acid, capric acid and naphthenic
acid. As the transition metal catalyst, a combination of one of these transition metals
and an organic acid is preferable; and a combination of a transition metal, such as
manganese, iron, cobalt, nickel or copper, and an organic acid, such as acetic acid,
stearic acid, 2-ethylhexanoic acid, oleic acid or naphthenic acid, is more preferable.
Note that, the transition metal catalysts may be used singly or in combinations of
two or more.
[0027] The content of the transition metal catalyst can be appropriately determined according
to the types of polyester compound (a) and transition metal catalyst to be used and
the desired performance thereof, and is not particularly limited. In view of the oxygen
absorption performance of an oxygen absorbing resin composition, the content of the
transition metal catalyst based on 100 parts by mass of a polyester compound (a) is
preferably 0.001 to 10 parts by mass, more preferably 0.002 to 2 parts by mass and
further preferably, 0.005 to 1 part by mass, in terms of the amount of transition
metal.
[0028] A polyester compound (a) and a transition metal catalyst can be mixed by a known
method; however, they are preferably kneaded by an extruder. If an extruder is used,
an oxygen absorbing resin composition having further satisfactory dispersibility can
be obtained. To the oxygen absorbing resin composition, as long as the effect of the
present embodiment is not excessively impaired, additives such as a drying agent,
a pigment, a dye, an antioxidant, a slip agent, an antistatic agent and a stabilizer;
fillers such as calcium carbonate, clay, mica and silica; and a deodorant, may be
added. The materials to be added are not limited to those mentioned above and various
materials can be mixed.
[0029] Note that, the oxygen absorbing resin composition of the present embodiment may further
contain a radical-generating agent and a photo initiator, if necessary, in order to
accelerate an oxygen absorption reaction. The oxygen absorbing resin composition of
the present embodiment may be kneaded with another thermoplastic resin by an extruder
as long as achievement of the object of the present embodiment is not inhibited. As
the radical-generating agent, photo initiator and another thermoplastic resin, those
known in the art and described in Patent Literature 1 can be used.
[0030] The content of the thermoplastic resin (a) in layer A is preferably 50 mass% or
more, more preferably 70 mass% or more and further preferably 90 mass% or more. If
the content of the thermoplastic resin (a) falls within the above range, the oxygen
absorption performance can be more improved compared to the case where the content
is less than 50 mass%.
[0031] The thickness of the oxygen absorbing layer (layer A) is not particularly limited;
however the thickness of layer A is preferably 1 to 1000 µm, more preferably 20 to
800 µm and further preferably 50 to 700 µm. If the thickness of layer A falls within
the above range, the oxygen absorption performance can be further improved without
impairing economic efficiency.
[Resin layer (layer B (layer B1, B2)) containing thermoplastic resin (b)]
[0032] Layer B of the present embodiment is a resin layer containing a thermoplastic resin
(b). The content rate of the thermoplastic resin (b) in layer B is not particularly
limited; however, the content rate is preferably 70 to 100 mass%, more preferably
80 to 100 mass% and further preferably 90 to 100 mass%.
[0033] The oxygen absorbing multilayer container of the present embodiment has at least
two B layers and may have three B layers or more. The structures of a plurality of
B layers may be the same or different. In view of simplicity in producing and performance
of the oxygen absorbing multilayer container, it is preferable that layer B1 and layer
B2 have the same component compositions. The thickness of layer B can be appropriately
determined depending upon the use. In order to ensure physical properties required
for a multilayer container, including strength such as falling resistance, and flexibility,
the thickness is preferably 5 to 1000 µm, more preferably 50 to 800 µm and further
preferably 100 to 500 µm. In view of simplicity in producing and performance of the
oxygen absorbing multilayer container, it is preferable that layer B1 and layer B2
preferably have same thickness.
<Thermoplastic resin (b)>
[0034] The thermoplastic resin (b) contains a cycloolefin polymer (COP) having a glass transition
temperature of 50 to 110°C. COP is a polymer using a norbornene-based monomer at least
as a monomer and obtained by ring-opening polymerization followed by hydrogenation.
COP has an alicyclic structure in a molecule (structure) and is amorphous. Examples
of the norbornene-based monomer include 2-norbornene and/or a 2-norbornene compound
having a substituent. Examples of the 2-norbornene compound having a substituent include
2-norbornenes having an alkyl group, an alkylidene group and an aromatic group as
a substituent; and 2-norbornenes having these substituents which have a halogen, a
hydroxyl group, an ester group, an alkoxy group, a cyano group, an amide group, an
imide group and a silyl group. Specific examples thereof include 2-norbornene, 5-methyl-2-norbornene,
5,5-dimethyl-2-norbornene, 5-ethyl-2-norbornene, 5-butyl-2-norbornene, 5-ethylidene-2-norbornene,
5-methoxycarbonyl-2-norbornene, 5-cyano-2-norbornene, 5-methyl-5-methoxycarbonyl-2-norbornene,
5-phenyl-2-norbornene, 5-phenyl-5-methyl-2-norbornene, 5-hexyl-2-norbornene, 5-octyl-2-norbornene
and 5-octadecyl-2-norbornene.
[0035] COP may be a copolymer obtained by polymerization of a norbornene-based monomer in
combination with another monomer copolymerizable with the norbornene-based monomer.
For example, COP can be obtained by ring-opening polymerization of a norbornene-based
monomer and another cycloolefin used at least as monomers. Examples of another cycloolefin
include cyclopentene, cyclooctene, dicyclopentadiene, methyldicyclopentadiene, dimethyldicyclopentadiene
and 5,6-dihydrodicyclopentadiene.
[0036] In polymerization, a transition metal compound such as TiCl
4, WCl
6, MoCl
5, VCl
5, NiCl
2 and PdCl
2 and an alkyl compound of a metal (typical metal) such as Al, Li, Na and Mg are used
in combination as a polymerization catalyst. If necessary, hydrogenation may be carried
out by a known method using a metal such as Ni or Pd as a catalyst.
[0037] As the COP, a known COP can be used, for example, COP described in e.g., Japanese
Patent Laid-Open No.
5-317411 can be mentioned. Furthermore, a commercially available COP can be used. The commercially
available COP can be appropriately selected from grades such as "ZEONEX" (trade mark)
and "ZEONOR" (trade mark), manufactured by ZEON CORPORATION and "Daikyo Resin CZ"
(trade mark) manufactured by Daikyo Seiko, Ltd. COP has an advantage in that chemical
properties thereof such as heat resistance and light resistance and chemical resistance
are analogous to those of polyolefin resins; whereas physical properties thereof such
as mechanical properties, melt properties, flow properties and dimensional accuracy
are those exhibited by amorphous resins. Examples of the COP having a glass transition
temperature of 50 to 110°C include trade name: "ZEONEX 5000" (glass transition temperature:
68°C, melt viscosity at a shear rate of 1216 sec
-1 and 260°C is 194 Pa·sec) manufactured by ZEON CORPORATION, is mentioned.
[0038] The glass transition temperature (Tg) of a thermoplastic resin (b) is 0 to 110°C,
more preferably 60 to 80°C and further preferably 60 to 75°C. If the glass transition
temperature falls within the above range, the molding processability of the oxygen
absorbing multilayer container is further improved. Note that, the glass transition
temperature herein refers to a value obtained by differential scanning calorimetry
in accordance with the method described in Examples (described later). Note that,
the glass transition temperature (Tg) of COP tends to decrease as the content of a
norbornene-based monomer increases. In contrast, Tg tends to increase as the content
of a cycloolefin such as dicyclopentadiene and the content of a polycyclic norbornene-based
monomer having three or more rings increases. Furthermore, Tg tends to increase as
the content of ring structures increases. If the structure of COP is appropriately
controlled in consideration of these, Tg can be efficiently controlled.
[0039] The absolute value of difference in glass transition temperature (Tg) between a thermoplastic
resin (b) and a polyester compound (a) is preferably 0 to 40°C and more preferably
0 to 20°C. As the absolute value of difference in glass transition temperature (Tg)
decreases, the molding processability of the oxygen absorbing multilayer container
is further improved.
[0040] The melt viscosity of a thermoplastic resin (b) is not particularly limited; however,
in view of the molding processability of the oxygen absorbing multilayer container,
the melt viscosity at a shear rate of 1216 sec
-1 and 260°C is preferably 100 to 300 Pa·sec and more preferably 150 to 250 Pa·sec.
If the melt viscosity falls within the above range, the molding processability of
the oxygen absorbing multilayer container is further improved.
[0041] The absolute value of difference in melt viscosity at a shear rate of 1216 sec
-1 and 260°C between a thermoplastic resin (b) and a polyester compound (a) is preferably
0 to 150 Pa·sec and more preferably 0 to 100 Pa·sec. As the absolute value of difference
in melt viscosity at a shear rate of 1216 sec
-1 and 260°C decreases, the molding processability of the oxygen absorbing multilayer
container is (further) improved.
[0042] Layer B may further contain a thermoplastic resin other than COP and known additives
as long as the effect of the present embodiment is not excessively impaired. The content
of the COP based on the total amount of the thermoplastic resin composition constituting
layer B, which is not particularly limited, is preferably 50 to 100 mass%, and in
view of transparency, more preferably 70 to 100 mass% and further preferably 90 to
100 mass%.
[0043] The oxygen absorbing multilayer container of the present embodiment may have an optional
layer in accordance with e.g., desired performance, in addition to an oxygen absorbing
layer (layer A) and a layer containing a thermoplastic resin (b) (layer B (layer B1,
layer B2)). Examples of such optional layer include an adhesion layer.
[0044] In the oxygen absorbing multilayer container of the present embodiment, when practical
interlayer adhesive strength is not obtained between adjacent two layers, an adhesion
layer (layer AD) is preferably provided between the two layers. The adhesion layer
preferably contains a thermoplastic resin having adhesiveness. Examples of the thermoplastic
resin having adhesiveness include acid-modified polyolefin resins, which are each
obtained by modifying a polyolefin resin (e.g., polyethylene or polypropylene) with
an unsaturated carboxylic acid (e.g., acrylic acid, methacrylic acid, maleic acid,
maleic anhydride, fumaric acid, itaconic acid); and polyester thermoplastic elastomers
containing a polyester block copolymer as a main component. In the adhesion layer,
in view of adhesiveness, a modified resin obtained by modifying the same type of thermoplastic
resin used as layer B is preferably used. The thickness of the adhesion layer is preferably
2 to 100 µm, more preferably 5 to 90 µm and further preferably 0 to 80 µm in order
to exhibit practical adhesive strength simultaneously with maintaining excellent molding
processability.
<Method for producing oxygen absorbing multilayer container>
[0045] A method for producing an oxygen absorbing multilayer container of the present embodiment
is not particularly limited, the oxygen absorbing multilayer is preferably produced
by an injection molding method. Further preferably, the method contains a step of
forming multilayer container by injecting at least three layers of a first layer (layer
B1), an oxygen absorbing layer (layer A) and a second layer (layer B2), from an injection
cylinder and, in this step, the absolute value of difference between the injection
cylinder temperature for the first layer (layer B1) and the injection cylinder temperature
for the oxygen absorbing layer (layer A) is 0 to 30°C. For example, for producing
a multilayer container of a three-layer (B/A/B) structure, there is a method in which
a material for constituting layer A and a material for constituting layer B are injected
from respective injection cylinders through a mold hot runner into a cavity by use
of a molding apparatus having two or more injection machines and injection molds.
Owing to the method, a multilayer container can be produced in accordance with the
shape of the injection mold. This method is particularly preferable in the case where
the component compositions of individual layers B (e.g., layer B1, layer B2) are identical.
[0046] For producing a multilayer container of a five-layer (B/A/B/A/B) structure, there
is a method in which a material for constituting layer B from an injection cylinder
is first injected, subsequently a material for constituting layer A alone is injected
from an injection cylinder and finally injecting a material for constituting another
layer B from an injection cylinder. By filling a cavity with these, a multilayer container
consisting of the five-layer (B/A/B/A/B) structure can also be produced. This method
is particularly preferable in the case where the component compositions of individual
layer B (e.g., layer B1, layer B2) are identical.
[0047] For producing a multilayer container of a five-layer (B/A/B/A/B) structure, there
is another method in which a material for constituting layer B is first injected from
an injection cylinder; subsequently a material for constituting layer A is injected
from another injection cylinder simultaneously with a resin for constituting another
B layer from another injection cylinder. By filling a cavity with these, a multilayer
container consisting of a five-layer (B/A/B/A/B) structure can also be produced. This
method is particularly preferable in the case where the component compositions of
individual layer B (e.g., layer B1, layer B2) are identical.
[0048] In view of molding processability, the absolute value of difference in injection
temperature between a material for constituting layer B and a material for constituting
layer A is preferably 0 to 30°C, more preferably 0 to 20°C and further more preferably
0 to 10°C. The injection temperature herein refers to the temperature of a material
passing through an injection cylinder. In view of molding processability, the absolute
value of difference in melt viscosity at the injection temperature between individual
layers is preferably 0 to 150 Pa·sec and more preferably 0 to 100 Pa·sec. The melt
viscosity of each layer refers to the melt viscosity of a material passing through
an injection cylinder at the injection temperature.
[0049] As a method for producing the oxygen absorbing multilayer container of the present
embodiment, an injection molding method is usually preferable; however, e.g., a compression
molding method may be employed for obtaining a multilayer body. For example, an oxygen
absorbing resin agent is provided in a thermoplastic resin melt and the resultant
molten mass is supplied to a male die and simultaneously compressed by a female die,
and a compression molding is cooled and solidified to obtain a multilayer body. Furthermore,
a multilayer body may be molded into a desired container shape by a molding means
such as extrusion molding and compression molding (sheet molding, blow molding).
[Oxygen absorbing multilayer container]
[0050] The shape, size and others of the oxygen absorbing multilayer container of the present
embodiment are not particularly limited and appropriately selected depending upon
the article to be stored and preserved. Preferable examples of such a container include
a pouch, a cup, a tray, a bottle, a vial, an ampule, a prefilled syringe and a vacuum
blood collection tube.
[0051] Further, if a sheet-form (sometimes called as "film-form") oxygen absorbing multi-layer
laminate is subjected to a bag-making, e.g., a three sided seal sack, a standing pouch,
a gussetted packaging bag, a pillow packaging bag, a multi-chamber pouch consisting
of a main chamber and a sub chamber with an easy-to-peel wall interposed between the
chambers and a shrink film packaging can be obtained. Furthermore, if thermoforming
is applied, containers having arbitrary shapes can be obtained.
[0052] More specifically, the above oxygen absorbing multi-layer laminate sheet is molded
by a method such as vacuum molding, air-pressure forming and plug assist molding to
manufacture an oxygen absorbing multilayer container having a predetermined shape
such as a tray, a cup, a bottle, a tube and a PTP (press-through package). Furthermore,
multilayer containers having predetermined shape can be molded at a time by co-injecting
or subsequently injecting a molten resin into an injection mold through multi-layer
multiple-dies by use of an injection machine.
[0053] Note that, when an oxygen absorbing multilayer container having a flange portion
is produced, a special treatment for imparting an easy-to-peel function may be applied
to the flange portion. Furthermore, if the above oxygen absorbing multi-layer laminate
is used as a member such as a container lid and a top seal, containers having an oxygen
absorption function can be provided.
[0054] When the oxygen absorbing multilayer container of the present embodiment is used,
starting of an oxygen absorption reaction can be facilitated and the oxygen absorption
rate can be enhanced by irradiation of an energy line. Examples of the energy line
that can be used include visible light beams, ultraviolet rays, X-rays, electron beams
and gamma rays. The irradiation amount of energy can be appropriately selected depending
upon the type of energy line.
[0055] The oxygen absorbing multilayer container of the present embodiment requires no moisture
for absorbing oxygen. Because of this, the oxygen absorbing multilayer container of
the present embodiment has the advantage that not only excellent oxygen absorption
performance in a wide range of humidity conditions from low humidity to high humidity
(relative humidity 0% to 100%) but also excellent quality retention of a content can
be provided. For the reason, the oxygen absorbing multilayer container is suitable
for storing and containing various specific articles. For example, medicinal products
are suitably stored and contained. More specifically, vitamin preparations such as
vitamin A, vitamin B2, vitamin B12, vitamin C, vitamin D, vitamin E and vitamin K;
alkaloids such as atropine; hormone agents such as adrenaline and insulin; sugars
such as glucose and maltose; antibiotics such as ceftriaxone, cephalosporins and cyclosporine;
and benzodiazepine medicinal agents such as oxazolam, flunitrazepam, clotiazepam and
clobazam can be packed regardless of natural or synthetic compound. If these natural
and synthetic compounds are packed in the oxygen absorbing multilayer container of
the present embodiment, the amount of these natural and synthetic compounds adsorbed
is low and deterioration of these compounds due to oxidation can be suppressed, and
further, evaporation of a solvent (for example, moisture) can be suppressed. Specific
examples of the content except medicinal products include, but are not particularly
limited to, beverages such as milk, juice, coffee, tea and alcohol beverage; liquid
seasonings such as sauce, soy sauce and dressing; cooked foods such as soup, stew
and curry; paste foods such as jam and mayonnaise; fishery products such as tuna and
seafood; dairy products such as cheese and butter; meat processed products such as
meat, salami, sausage and ham; vegetables such as carrot and potato; eggs; noodles;
rice uncooked; processed rice products such as cooked rice and rice gruel; dry foods
such as powder seasoning, coffee powder, milk powder for infants, cooked food for
infants, powder diet food, nursing care cooked food, dry vegetables and rice crackers;
chemicals such as a pesticide and an insecticide; cosmetics; pet foods; and commodities
such as a detergent.
[Sterilization treatment]
[0056] Note that, before and after these contents are packed (packaged), containers and
contents can be sterilized in appropriate ways suitable for the contents. Examples
of sterilization methods include, heat sterilization such as a treatment with hot
water of 100°C or less, a treatment with pressurized hot water of 100°C or more and
heating to an extremely high temperature of 130°C or more; sterilization with electromagnetic
wave such as ultraviolet, microwave and gamma-ray; treatment with gas such as ethylene
oxide; and sterilization with a chemical agent such as hydrogen peroxide and hypochlorous
acid.
Examples
[0057] Now, the present invention will be more specifically described by way of Examples
and Comparative Examples; however, the present invention is not limited by these.
Note that, unless otherwise specified, NMR measurement was carried out by use of "AVANCE
III-500" manufactured by BRUKER at room temperature. Note that, in the following Examples,
vials are described as an example; however, since properties required for ampules
and prefilled syringe are the same as those required for vials, the present invention
with respect to this point is not limited by these Examples.
[0058] Various property values of the compounds and others obtained in Production Example
(described later) were measured by the following measurement methods and measurement
devices.
(Method for measuring glass transition temperature)
[0059] Glass transition temperature was measured in accordance with JIS K7122. As a measurement
device, a differential scanning calorimeter (DSC; "DSC-60", manufactured by Shimadzu
Corporation) was used. Note that, measurement conditions of DSC were as follows.
Measurement device: "DSC-60", manufactured by Shimadzu Corporation,
Starting temperature of measurement: 25°C
Temperature raising rate: 10°C/minute
Achieving temperature: 220°C
Temperature decreasing rate: 5°C/minute
(Method for measuring melt viscosity)
[0060] Melt viscosity was measured by use of a capillary rheometer "CAPILOGRAPH 1D", manufactured
by TOYO SEIKI SEISAKU-SHO, LTD., at a temperature of 260°C and a shear rate of 1216
sec
-1.
[Monomer Synthesis Example]
[0061] To an autoclave having an inner volume of 18 L, dimethyl naphthalene-2,6-dicarboxylate
(2.20 kg), 2-propanol (11.0 kg) and a catalyst (350 g (containing 50 wt% of water))
consisting of active carbon carrying 5% palladium were placed. Then, the air of the
autoclave was replaced with nitrogen and the nitrogen was further replaced with hydrogen.
Thereafter, hydrogen was supplied until the interior pressure of the autoclave reached
0.8 MPa. Next, a stirrer was driven and the rotational speed thereof was adjusted
to 500 rpm. The interior temperature was raised up to 100°C over 30 minutes, further
hydrogen was supplied to adjust the pressure to 1 MPa. Thereafter, supply of hydrogen
was continued so as to maintain 1 MPa in response to a pressure drop with the progress
of the reaction. Since no pressure drop was observed seven hours later, the autoclave
was cooled and unreacted residual hydrogen was released. Thereafter a reaction solution
was taken out from the autoclave. After the reaction solution was filtered to remove
the catalyst, 2-propanol was vaporized from the filtrate separated by an evaporator.
To the resultant crude product, 2-propanol (4.40 kg) was added and purification was
performed by recrystallization to obtain tetralin-2,6-dicarboxylic acid dimethyl in
a yield of 80% (yield based on naphthalene-2,6-dicarboxylic acid dimethyl). Note that,
the analysis results of NMR were as follows.
1H-NMR (400 MHz CDCl
3) δ 7.76-7.96 (2H m), 7.15 (1H d), 3.89 (3H s), 3.70 (3H s), 2.70-3.09 (5H m), 1.80-1.95
(1H m).
<Production Example of polymer>
(Production Example 1)
[0062] A polyester resin producing apparatus equipped with a packed tower rectifying column,
a partial condenser, a total condenser, a cold trap, a stirrer, a heating device and
a nitrogen inlet tube was charged with dimethyl tetralin-2,6-dicarboxylate (543 g)
obtained in Monomer Synthesis Example, ethylene glycol (217 g), glycerin (1.0 g) as
a polyfunctional compound, tetrabutyl titanate (0.038 g) and zinc acetate (0.15 g).
The temperature of the reaction system was increased to 230°C under a nitrogen atmosphere
and a transesterification reaction was carried out. After the reaction conversion
rate of a dicarboxylic acid component reached 90% or more, temperature was increased
and pressure was reduced gradually over 90 minutes. Polycondensation was performed
for one hour at 260°C and 133 Pa or less to obtain a polyester compound (1) having
a repeating structure represented by the following formula (1).
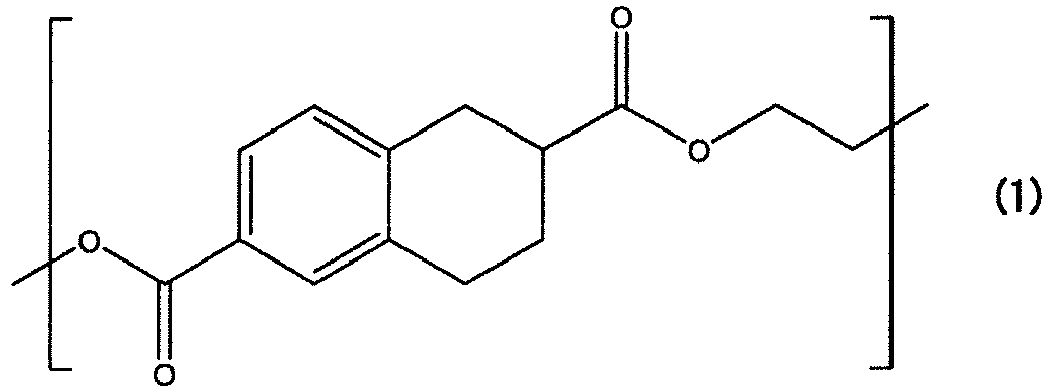
[0063] The glass transition temperature and melting point of the polyester compound (1)
obtained were measured by a differential scanning calorimeter (DSC). As a result,
the glass transition temperature of the polyester compound (1) was determined to be
69°C; whereas the melting point was not determined because of an amorphous structure.
Furthermore, the melt viscosity of the polyester compound (1) was measured by use
of a capillary rheometer ("Capirograph 1D", manufactured by TOYO SEIKI SEISAKU-SHO,
LTD.). The physical properties of the polyester compound (1) are shown in Table 1.
[Table 1]
|
Name of resin |
Glass transition temperature (°C) |
Melt viscosity1) (Pa·sec) |
Production Example 1 |
Polyester compound (1) |
69 |
164 |
1) Melt viscosity at a shear rate of 1216 sec-1 and 260°C |
<Production of vial>
[0064] In the following conditions, a material for constituting layer B was injected from
an injection cylinder and subsequently a material for constituting layer A was injected
from another injection cylinder simultaneously with a resin for constituting layer
B, and then, the cavity in an injection mold was filled with a resin for constituting
layer B by injecting the resin in a required amount to obtain an injection molded
article of a three (B/A/B) layer structure. The injection molded article obtained
was cooled to a predetermined temperature, transferred to a blow mold and subjected
to blow molding to obtain vials (bottle portions). This cycle of process (one cycle
takes 15 minutes) was continuously repeated for 3 hours (continuous molding for 3
hours).
- Total mass of vial: 5 g
- Mass of layer A: 30 mass% based on the total mass of vial
<Shape of vial>
[0065] The shape of the vials was specified by a height of 45 mm, an outer diameter of 24
mmϕ and a wall thickness of 1 mm. Note that, the vials were produced by using a one-step
injection stretch blow machine (mode "ASB12N-10T", proving 4 vials, manufactured by
NISSEI ASB MACHINE CO., LTD.).
<Evaluation of vial>
[0066] The molding processability, drop test, oxygen permeability and transparency of the
vials obtained in Examples and Comparative Examples were evaluated by the following
methods.
• Molding processability
[0067] Molding processability of vials (bottle portion) obtained in the above "<Production
of vial>" was evaluated based on e.g., appearance of the three layer structure of
the vials (bottle portion). More specifically, molding processability was evaluated
based on the following criteria.
- (a) the presence or absence of lambency in appearance due to non-smoothness and disturbance
at the interface between layer A and layer B (layer B1, layer B2) was determined by
visual inspection (presence or absence of "disturbance"). Then, the ratio of number
of vials determined as having no disturbance based on the total number of vials obtained
by continuous molding for 3 hours, was obtained. The ratio was specified as an "acquisition
rate" (number of vials having no disturbance/total number of vials).
- (b) the presence or absence of irregularity, which was derived from deposition of
e.g. a resin component onto the bottoms of the vials obtained (corresponding to the
gate portion when vials were injected from a mold), was determined (presence or absence
of "irregularity").
- A: Acquisition rate 90% or more, no irregularity
- B: Acquisition rate 90% or more, irregularity is present
- C: Acquisition rate 50% or more and less than 90%, no irregularity
- D: Acquisition rate 50% or more and less than 90%, irregularity is present
- E: Acquisition rate of less than 50%, no irregularity
- F: Acquisition rate of less than 50%, irregularity is present
• Impact resistance test (drop test)
[0068] A vial was filled with pure water (10 mL) and hermetically sealed with a rubber stopper
and an aluminum cap. This container was dropped from a height of 1.5 m and the presence
or absence of breakage of the vial was checked. When the container was broken, if
water packed in the container was scattered from a broken site, the container was
determined as having a defect. Twenty samples were checked. Note that the landing
area had a smooth surface made of a stainless steel and vials were dropped such that
the bottoms of vials came into contact with the surface of the landing area.
• Oxygen permeability (OTR)
[0069] The atmosphere outside a vial was controlled to have a relative humidity of 50% and
the interior atmosphere of the vial was controlled to have a relative humidity of
100%, at 23°C. An oxygen permeability was measured on the 30th day after initiation
of measurement. The measurement was performed by using an oxygen permeability measurement
device (trade name, "OX-TRAN 2-21 ML", manufactured by MOCON). The lower the measured
value, the more satisfactory the oxygen barrier property was. Note that, the lower
detection limit of oxygen permeability in measurement was 5 × 10
-5 mL/ (0.21 atm·day·package).
• Transparency
[0070] The transparency (haze value) of a vial was measured by a haze meter ("color difference-turbidity
measuring instrument COH-400", manufactured by Nippon Denshoku Industries Co., Ltd.)
in accordance with JIS K7136. Note that, the transparency of a site on the side surface
of a vial at a distance of 15 mm from the bottom portion of a vial was measured.
(Example 1)
[0071] Cobalt stearate (II) was dry-blended such that the amount of cobalt based on 100
parts by mass of the polyester compound (1) became 0.02 parts by mass to obtain an
oxygen absorbing resin composition. The oxygen absorbing resin composition was used
as a resin for constituting layer A and a cycloolefin polymer 1 (trade name "ZEONEX
5000", manufactured by ZEON CORPORATION, glass transition temperature: 68°C, melt
viscosity at a shear rate of 1216 sec
-1 and 260°C: 194 Pa·sec) was used as layer B. Vials were produced in the molding conditions
shown below and evaluated. Note that, no resin deposition onto the mold was observed
at the time of injection molding of the vials and the evaluation result of the above
described "molding processability" was "A". The producing condition and physical properties
of Example 1 are shown in Table 2.
(Molding conditions for vial)
[0072]
Temperature of injection cylinder for layer A: 260°C
Temperature of injection cylinder for layer B: 260°C
Temperature of resin flow channel in injection mold: 260°C
Temperature of injection mold: 50°C
Temperature of cooling water for blow mold: 30°C
Cycle time: 15 seconds
(Comparative Example 1)
[0073] Vials were produced in the same manner as in Example 1 except that cycloolefin polymer
2 (trade name, "ZEONEX 690R", produced by ZEON CORPORATION, glass transition temperature:
136°C, melt viscosity at a shear rate of 1216 sec
-1 and 260°C: 362 Pa·sec) was used for layer B and that the following molding conditions
were employed, and subjected to evaluation. Note that, within 30 minutes after continuous
injection molding of vials was started, resin deposition onto the mold was observed.
Once the resin was deposited onto a mold during the continuous molding process, irregularity
on the bottom portions of vials produced thereafter was continuously observed. The
evaluation result of the above described "molding processability" was "F". The producing
conditions and physical properties of Comparative Example 1 are shown in Table 2.
(Molding conditions for vial)
[0074]
Temperature of injection cylinder for layer A: 260°C
Temperature of injection cylinder for layer B: 300°C
Temperature of resin flow channel in injection mold: 300°C
Temperature of injection mold: 90°C
Temperature of cooling water for blow mold: 30°C
Cycle time: 15 seconds
[Table 2]
|
Resin used for Layer A |
Resin used for Layer B |
Molding processability |
Drop test |
Transparency (haze) (%) |
Oxygen permeability2) |
Type of resin (trade name) |
Glass transition temperature (°C) |
Melt viscosity1) (Pa·sec) |
Example 1 |
Polyester Compound (1) |
COP1 (ZEONEX5000) |
68 |
194 |
A |
No breakage |
10.8 |
Detection limit or less |
Comparative Example 1 |
COP2 (ZEONEX690R) |
136 |
362 |
F |
15 out of 20 were broken |
11.1 |
Detection limit or less |
1) Melt viscosity at a shear rate of 1216 sec-1 and 260°C
2) Unit: mL/(0.21 atm·day·package), detection lower limit: 5 × 10-5 mL/(0.21 atm·day·package) |
[0075] As is apparent from Table 2, it was confirmed at least that Example 1 has a satisfactory
oxygen barrier property and excellent molding processability, impact resistance and
transparency.
[0076] The present application claims a priority based on Japanese Patent Application No.
2014-062918 filed on March 26, 2014 with the Japan Patent Office, the contents of which are incorporated herein by reference.
Industrial Applicability
[0077] The oxygen absorbing multilayer container according to the present invention can
be widely used and examples thereof include containers for storing various products
such as foods, beverages, medicinal products and cosmetics.