(19) |
 |
|
(11) |
EP 3 029 392 B1 |
(12) |
EUROPEAN PATENT SPECIFICATION |
(45) |
Mention of the grant of the patent: |
|
05.04.2017 Bulletin 2017/14 |
(22) |
Date of filing: 03.12.2014 |
|
(51) |
International Patent Classification (IPC):
|
|
(54) |
Stabilizing and sealing arrangement
Stabilisierungs- und Dichtungsanordnung
Stabilisation et agencement d'étanchéité
|
(84) |
Designated Contracting States: |
|
AL AT BE BG CH CY CZ DE DK EE ES FI FR GB GR HR HU IE IS IT LI LT LU LV MC MK MT NL
NO PL PT RO RS SE SI SK SM TR |
(43) |
Date of publication of application: |
|
08.06.2016 Bulletin 2016/23 |
(73) |
Proprietor: Fläkt Woods AB |
|
55184 Jönköping (SE) |
|
(72) |
Inventors: |
|
- Sagström, Tobias
SE-55594 Jönköping (SE)
- Andersson, Ann-Sofie
SE-74963 Örsundsbro (SE)
- Piispanen, Marko
SE-74542 Enköping (SE)
- Baltzer, Tomas
SE-74542 Enköping (SE)
- Lilley, Stephen
Colchester, Essex C05 OSP (GB)
|
(74) |
Representative: Pitkänen, Hannu Alpo Antero |
|
Patenttitoimisto Pitkänen Oy
P.O. Box 1188 70211 Kuopio 70211 Kuopio (FI) |
(56) |
References cited: :
EP-A2- 1 031 799 CN-U- 201 616 959
|
WO-A2-01/50067 CN-U- 201 629 923
|
|
|
|
|
|
|
|
|
Note: Within nine months from the publication of the mention of the grant of the European
patent, any person may give notice to the European Patent Office of opposition to
the European patent
granted. Notice of opposition shall be filed in a written reasoned statement. It shall
not be deemed to
have been filed until the opposition fee has been paid. (Art. 99(1) European Patent
Convention).
|
Field of invention
[0001] Present invention relates to a stabilizing and sealing arrangement for smaller air
handling units with low installation height, so called "side-by-side" air handling
units, which differs from "normal" air handling units which in turn can be categorized
as "double deckers". The side-by-side air handling unit is often installed in the
false ceiling and are normally available up to air flows around 3200 m
3/s.
Background of the invention
[0002] Since all air handling units (AHU) handles over pressure and under pressure in different
sections within the AHU, air leakage is an issue while constructing, installing and
operating the AHU. Based on standards within the field, AHU's is categorized in leakage
classes L1, L2 and L3, where L1 is the class with highest demands, i.e. with low amount
of air leakage. As easily can be understood, a large AHU is easier to design to the
higher demands (L2, L1) because it is handling larger amounts of air, but still it
has the same number of corners and edges where leakage normally occur, if compared
to a small AHU like the side-by-side type. Small AHU's are often built with similar
design as large units, and therefore the leakage has a greater impact due to that
a small amount of leakage air represents a larger part of the total airflow, since
the airflows in these segments are lower. Several manufacturers states that class
L2 is fulfilled, but to achieve this class a lot of sealing effort has to be made,
often with the use of a great amount of sealing mastic. Benchmarking tests has been
performed by the applicant and these shows that several L2-classified AHU's in this
segment don't fulfil the stated demands.
[0003] Air handling units in this segment can be divided into two types - "framework units"
and "housing units". Framework units are designed in a similar way as what is common
at larger AHU's, with framework profiles as the stabilizing construction and panels
inserted and screwed to the framework, for enclosure, stability and isolation. A typical
panel consists of two steel sheet plates with insulation in between. Access to the
interior for maintenance and service of filters, heat exchangers, fans, controls etc.
is normally solved by openable panels in form of doors with hinges and locks. Panels
and doors are sealed with either sealing mastic, seals or sealing strips or a combination
of them, depending on function and where in the construction. Typically, sealing mastic
is used for permanent sealing and seals/sealing strips are often used at doors. The
framework units often have plastic or metal corners to join the framework profiles
and a lot of efforts have to be done to solve the sealing issue at the corners, which
are a critical spot in the framework construction.
[0004] Existing housing units are, roughly speaking, designed only with enclosing panels,
like top panel, bottom panel and connection panels (for connecting ducts), and interior
stabilizing walls and/or supports, which all are coupled together to a stable housing
with pop-rivets, screws or the like. Because of the stabilizing interior, the enclosing
panels on the installation side and the service side, is normally the same as the
doors used to access the interior parts for service and inspection. Since the smaller
air handling units, like side-by-side units, have small dimensions, it is often cheaper
to design them according to the "housing concept", but also the framework design exists.
Leakage is a common problem especially at the corners and around the doors.
[0005] All air handling units are more or less constantly exposed for movements and vibrations
due to running fans, over pressure and under pressure etc. Further, the design must
include access of filters, fans, heat exchangers etc., which means that doors or hatches
must be included. Because the access openings are to be opened and closed several
times per year there are problems to keep over time sustained seal. Existing solutions
for the actual segment (airflows up to 3200 m
3/s) have problems to provide a robust and air tight housing/unit with a competitive
cost, without the use of great amounts of sealing mastic, to achieve good air tightness.
Patent document
EP-A-1031799 discloses an exemplary air handling unit comprising a stabilizing and sealing arrangement
according to the preamble of claim 1.
Disclosure of the invention
[0006] It is an object of the present invention to provide a stabilizing and sealing arrangement
for a side-by-side air handling unit which overcomes the problems stated above. The
new design of the AHU comprises a top panel, a bottom panel and two connection panels
in a similar way as existing units, but the invention is characterized by an extra
support plate which is arranged on each long side of the AHU, i.e. one on the installation
side and one on the service side. The support plates are fixedly arranged to the sides
of the top-, bottom- and connection panels i.e. the end sides facing the installation
side and the service side. By this "extra" support plate, preferably a steel sheet
metal plate, the housing is stabilized and the interior structures like filter holders,
heat exchanger holders, heater holders, partition walls etc. are also preferably attached
to the support plate at their end sides, and thereby gets stable, but it is mainly
the support plates that provides the stability of the housing. Existing side-by-side
units of housing type has normally interior structures for providing stability together
with the top-, bottom- and connection panels and the side panels are normally the
same as the doors for access, and thus the doors/side panels are not normally a part
of the stabilizing construction in existing housing units. According to the invention,
each support plate comprises a first seal on a first side, the side facing the housing,
and thereby forming a very air tight seal between the sides of the top-, bottom-and
connection panel sides and the support plate, when the support plate is fixedly connected
to the end sides. The first seal is arranged in such way that any contact between
adjacent end sides and the support plate has the first seal in between them, also
including the contact between end sides of the interior structures, holders etc. and
the support plate. By natural, the support plate has openings, both for access of
the interior, i.e. for service and maintenance, for installation purposes and also
openings for assembly of the support plate and assembly of other parts as interior
structures and accessories, like holes for pop-rivets and the like. To manage very
high air tightness, the first seal on the first side is complemented by that all openings
in the support plate are in turn covered by one or more hatch-like panels, each comprising
a second seal facing the support plate. This means that the seal abuts the second
side of the support plate - the side facing away from the housing, in such way that
the second seal is arranged between every possible contact of the hatch-like panel
and the support plate. The hatch-like panels are fitted to the support plate in a
removable way for access to the interior and covers one or more underlying openings.
Existing solutions do not comprise this complete sealing solution since for example
assembly holes for pop-rivets, screws or the like are not covered with sealing in
a proper way. According to the invention, firstly the first seal surrounds all openings
for assembly of the support plate to the sides of the housing in an overlaying manner
so the risk of air leakage to the assembly hole is already here a minimum. Secondly,
as stated above, all openings in the support plate are in turn covered in an overlaying
manner by the one or more hatch-like panels with the second sealing, meaning that
also in this layer, every opening is surrounded by seal and thereby provides a complete
tight seal. For example, a hatch for access to filters may also cover underlying pop-rivets
and their assembly holes and also other eventual holes. By this complete and careful
sealing design the AHU-casing nearly reaches similar air tightness as normal air ducts,
at least L2 class and even up to L1, which is far better than existing side-by-side
air handling units on the market, and also is a more robust and safe solution than
prior art solutions.
[0007] According to a preferred embodiment of the invention the first seal covers the complete
surface of the first side of the support plate - the side facing the housing and the
end sides of the housing panels. Holes provided for service and installation access
are though not covered by this first seal. By this sealing arrangement all adjacent
housing end sides and interior structures as filter holders, heat exchanger holders,
heater holders, partition walls etc. all getting an air tight seal to the support
plate, which thereby provides high leakage protection as well as stopping internal
leakage between the different air spaces within the AHU. The sealing arrangement in
existing housing units often consists of a sealing strip applied at the side panel
or door, hopefully in the correct position to seal between sides and adjacent interior
structures or sides. The present solution is a more "forgiving" design where the seal
is overlapping every part which is to be sealed with respect to the sides, and the
seal also covers any assembly hole in an overlapping manner, why the use of sealing
mastic for sealing at the end sides is unnecessary. This gives a short assembly time
and an easier assembly as well as a better over time sealing compared to prior art
solutions.
[0008] According to a further preferred embodiment the second side of the support plate
has a substantially smooth surface at least in the area where the second seal abuts.
The seal thickness is of course adapted to accommodate any irregularities in the underlying
surface, when the hatch-like panel is fitted to the support panel. But to keep the
seal thickness as low as possible and the leakage as low as possible it is an object
of the invention to keep the surface as smooth as possible for a good seal between
the second side of the support plate and the abutting hatch-like panels.
[0009] To keep the good sealing arrangement throughout the complete design of the air handling
unit also the hatch-like panels are adapted in the same way as the support plate.
Some of the hatch-like panels comprises/carries installations as a heater or controls,
which in turn needs to be covered since the installation in the hatch-like panel means
holes in the panel. Therefore according to a preferred embodiment of the invention,
any service opening, like for installations or maintenance, in the hatch-like panels
is covered by a lid-like arrangement, each arranged with a third seal, facing the
hatch-like panel, so that every contact between the lid-like arrangement and the hatch-like
panel has the third seal between them. The object of the invention is maintained with
always having a seal surrounding any possible leakage source like openings. The lid
is screwed to the hatch-like panel and the seal is achieved when the lid is assembled.
If a leakage occurs through openings in the hatch-like panels it is taken care of
by the third sealing applied on the lid.
[0010] According to a preferred embodiment also any assembly hole for pop-rivets or screws
in the hatch-like panels is covered by a plug to further stop any possible leakage
this way. Even though all assembly holes are surrounded with sealing through the second
sealing attached to the hatch-like panel for sealing between the support plate and
the panel, there might be a small leakage through the hole itself, if not covered
by a lid as presented in the preceding claim description. Therefore an extra sealing
is provided through the plug covering the assembly hole in the outer panel material.
Throughout the whole construction design the seal arrangement is well thought out
to fulfill the high demands regarding leakage. Known side-by-side units don't fulfill
the demands and therefore suffers from high leakage values.
[0011] In a preferred embodiment of the invention the support plate has a stabilizing C-shape
design. The C-shape is formed by folding a steel sheet plate in such a way as the
web is forming the connection part with dimensions corresponding to the installation
side and the service side of the housing and one flange at each end of the web is
formed, i.e. along the top and the bottom of the AHU and protruding away from the
housing. All eventual openings are located in the connection part and it is the connection
part that is covered with the first seal on the side facing the housing. The flanges
haven't only a stabilizing function, they also embraces the hatch-like panels on the
upper and lower side so that, when a hatch is opened it doesn't fall down, but instead
rests on the lower flange, which is convenient for the service technician. The upper
flange is also used for connecting a roof in a simple manner, if the unit is arranged
as an outdoor unit and need weather protection. By the flanges it is possible to attach
a roof to the housing without making holes in the housing and thereby so to speak
"puncture" the air tight enclosure. Prior art solutions without the support plate
have attachments for roof or eyebolts screwed directly into the housing.
[0012] By the invention a number of advantages compared to known solutions are obtained:
- A robust and safe construction design which minimizes impact of vibrations and fluctuations
in pressure and thereby is less sensitive for air leakage.
- The design also is less sensitive to assembly variations depending on the skill and
experience of the assembler, but also tolerances.
- Very air tight housing both with respect to air leakage to the surroundings as well
as internal leakage.
- The "layer-by layer" sealing solution always makes sure that any assembly openings
or service/installation openings are covered with at least one layer of sealing arrangement,
which give a very high level of air tightness.
- The C-shape of the support plate is stabilizing and also provides other advantages
as for example the possibility to attach a weather protection roof without affecting
the air tightness of the housing.
- A smooth surface in the area where a seal abuts the underlying areas gives a better
sealing.
Brief description of the drawings
[0013]
Fig. 1 shows a perspective view of a side-by-side air handling unit 1 during assembly
of a housing 2, where a support plate 10 with a first seal 11 are about to be assembled
to the housing 2.
Fig. 2 shows the side-by-side air handling unit 1 when the support plate 10 is attached
to the housing 2 and a number of hatch-like panels 15a...15n, each comprising a second
seal 16a...16n, are to be assembled.
[0014] The constructive design by the present invention is obvious in the following description
in detail of an example of embodiment of the invention related to the accompanying
figure showing a preferred, but not limited example of embodiment of the invention.
In addition the invention forwards the prior art in the field in different aspects.
This is realized in the present invention by that the device of the below described
art principally is constituted in a way that is obvious from the characterised part
of claim 1.
Detailed description of the drawing
[0015] Fig. 1 shows a preferred embodiment of the invention where a side-by-side air handling unit
1, with a housing 2 comprising a top panel 3, a bottom panel 4, and two connection
panels 5, 6, for connection of air ducts on respective short end of the housing 2.
The long sides of the housing 2 can be described as a service side 7 and an installation
side 8, and the housing 2 further comprises a number of interior structures 9, like
filter holders, heat exchanger holders, heater holders, partition walls etc. The side-by-side
air handling unit 1 of course also includes normal equipment for an AHU, like supply
fan, exhaust fan, controls, filters, heat exchangers etc. but these are not shown
or described here. The top panel 3, the bottom panel 4, and connection panels 5, 6
have end sides 3a, 3b; 4a, 4b; 5a, 5b; 6a, 6b facing the service side 7 and the installation
side 8 respectively, which end sides 3a, 3b; 4a, 4b; 5a, 5b; 6a, 6b have a substantially
smooth surface provided for best sealing possibilities. Also at least some of the
interior structures 9 have at least one end side 9a, b facing the service side 7 and
installation side 8 respectively. To the housing 2, on each long side, i.e. on the
service side 7 and on the installation side 8, a respective support plate 10 is fixedly
attached to the housing 2, preferably by pop-rivets or screws. The support plate 10
is preferably also fixedly attached to the interior structures 9 to stabilize also
these structures which give a robust housing 2 and interior. To gain stability and
also provide other positive features, the support plate 10 has a stabilizing C-shape
design. The C-shape is formed by folding a steel sheet plate in such a way as a web
23 is formed and utilizing the connection part with dimensions corresponding to the
service side 7 and the installation side 8 of the housing 2, and further one flange
24 at each end of the web 23 is formed and protruding away from the housing 2, in
direction of a second side 14 of the support plate 10. By the flanges 24 it is possible
to attach a weather protection roof (not shown) on top of the housing 2, without "puncture"
the air tight housing 2. For sealing purposes the support plate 10 comprises a first
seal 11, attached on a first side 12 (connection side) of the support plate 10. The
first side 12 is facing the housing 2 and thereby also facing the panel and interior
end sides 3a, 3b; 4a, 4b; 5a, 5b; 6a, 6b; 9a, 9b. The first seal 11 covers the whole
surface of the first side 12 of the support plate, which means that only openings
13 in the support plate is not covered by the first seal 11. By this arrangement all
contact surfaces between the end sides 3a, 3b; 4a, 4b; 5a, 5b; 6a, 6b; 9a, 9b and
the support plate 10 comprises a seal which give a good leakage control both for internal
leakage between air spaces inside the housing 2 as well as the external leakage, which
is tested according to the earlier presented standard classes. Since the support plate
10 is a steel sheet metal plate both the first side 12 and the second side 14 have
a smooth surface, which is preferred to achieve a good seal.
[0016] Fig. 2 shows the side-by-side air handling unit 1 with the support plate 10 fixedly attached
to the housing 2. The support plate 10 comprises openings 13 for access to the interior
for service and maintenance of fans, heat exchanger, filter exchange, etc. Any opening/hole
in the support plate 10 is a possible leakage source and therefore any opening 13,
like assembly holes, service openings and openings for installations like heaters
etc. is covered in an overlapping manner by a hatch-like panel 15a...15n, each comprising
a second seal 16a...16n, facing the second side 14 of the support plate 10, such as
each opening 13 is surrounded by the second seal 16a...16n. The second seal 16a...16n
preferably covers the whole surface, facing the second side 14 of the support plate
10, of the hatch-like panel 15a...15n. This means that all positions where screws
or pop-rivets are used for attaching the support plate 10 to the end sides of the
housing 2 are covered as well as the access openings for service and maintenance.
Installations like electrical heater (not shown) are assembled direct to the support
plate 10 and therefore built up in the same way as the hatch-like panels with a seal
between the installation mounting plate and the support plate. The installation plate
is then in turn covered with one of the hatch-like panels 15a...15n, and thereby also
is sealed in a proper manner according to the scope of the invention. In turn some
of the hatch-like panels 15a...15n comprises one or more openings like service openings
17 or installation openings 18. One example is the controls which are attached on
an installation plate directly to the support plate 10. The hatch-like panel 15b with
the second seal 16b covers the control installation plate in the same way as other
hatch-like panels covers underlying openings/installations, but the hatch-like panel
15b in this case also comprises an opening 17, 18 for access the supervision and settings
of the control system. This opening 17, 18 is in turn covered by a lid-like arrangement
19, which is arranged with a third seal 20, facing the hatch-like panel 15b in such
way that every contact between the lid-like arrangement 19 and the hatch-like panel
15b has the third seal 20 in between, for sealing of the underlying opening/openings.
Some of the hatch-like panels 15a...15n, like hatches for maintenance access of filters
etc., are arranged to be easily removed and therefore comprises hand operated "finger
screws" for unlocking and removing the hatch. Other hatch-like panels 15a...15n are
not to be opened frequently, and therefore fixedly assembled with standard screws.
These can of course be removed and the hatch removed if necessary, but this by using
tools. Assembly holes 21 in the outer skin of the hatch-like panel 15a...15n are in
that case covered by a plug 22 inserted in the assembly hole 21, to stop any possible
leakage this way. The plug 22 can be removed if the hatch-like panel shall be removed.
PARTS LIST
[0017]
- 1 =
- side-by-side air handling unit
- 2 =
- housing
- 3 =
- top panel
- 4 =
- bottom panel
- 5 =
- connection panel
- 6 =
- connection panel
- 7 =
- service side
- 8 =
- installation side
- 9 =
- interior structures
- 10 =
- support plate
- 11 =
- first seal
- 12 =
- first side (of the support plate)
- 13 =
- opening
- 14 =
- second side (of the support plate)
- 15 =
- hatch-like panel
- 16 =
- second seal
- 17 =
- service opening
- 18 =
- installation opening
- 19 =
- lid-like arrangement
- 20 =
- third seal
- 21 =
- assembly hole
- 22 =
- plug
- 23 =
- web
- 24 =
- flange
1. Stabilizing and sealing arrangement for an side-by-side air handling unit (1), which
air handling unit (1) comprises a housing (2), with a top panel (3), a bottom panel
(4), two connection panels (5, 6) for connection of ducts, and a service side (7)
and an installation side (8), and the panels (3, 4, 5, 6) have end sides (3a, 3b;
4a, 4b; 5a, 5b; 6a, 6b) facing the service side (7) and the installation side (8),
which end sides (3a, 3b; 4a, 4b; 5a, 5b; 6a, 6b) have substantially smooth surface,
and the housing (2) further comprises interior structures (9) like filter holders,
heat exchanger holders, heater holders, partition walls etc. where at least some of
the interior structures (9) have at least one end side (9a,b) facing the service side
(7) and installation side (8) respectively, characterized by that a support plate (10) is arranged at the service side (7) and at the installation
side (8) respectively, which support plate (10) is respectively fixedly connected
to the end sides (3a, 3b; 4a, 4b; 5a, 5b; 6a, 6b) of the top-, bottom- and connection
panels (3, 4, 5, 6) in a stabilizing manner, and preferably fixedly connected to at
least some of the end sides (9a,b) of interior structures (9), and which respective
support plate (10) comprising a first seal (11) at least on one first side (12) facing
the housing (2), and which first seal (11) is arranged in such way that every contact
between adjacent end sides (3a, 3b; 4a, 4b; 5a, 5b; 6a, 6b; 9a, 9b) and the support
plate (10) has the first seal (11) in between, and further that any opening (13) in
respective support plate (10) is covered, at a second side (14) of the support plate
(10), opposite the first side (12) and facing away from the housing (2), by at least
one hatch-like panel (15a,....15n), each comprising a second seal (16a,...16n) facing
the second side (14) of the support plate (10), and which second seal (16a,...16n)
is arranged in such way that every contact between the at least one hatch-like panel
(15a,....15n) and the second side (14) of the support plate (10) has the second seal
(16a,...16n) in between, whereby every opening (13) in the support plate (10) is covered
in an overlapping manner, such as each opening (13) is surrounded by the second seal
(16a,...16n).
2. Arrangement according to claim 1, characterized by that the first seal (11) covers the whole surface of the first side (12) of the support
plate (10).
3. Arrangement according to claim 1 or 2, characterized by that that the second side (14) of the support plate (10) has a substantially smooth
surface, at least in the area where the second seal (16a,...16n) abuts.
4. Arrangement according to any of the preceding claims, characterized by that any service opening (17) and installation opening (18) in the at least one hatch-like
panel (15a,....15n) is covered by a lid-like arrangement (19), arranged with a third
seal (20) facing the at least one hatch-like panel (15a,....15n), and which third
seal (20) is arranged in such way that every contact between the lid-like arrangement
(19) and the at least one hatch-like panel (15a,....15n) has the third seal (20) in
between.
5. Arrangement according to any of the preceding claims, characterized by that any assembly hole (21) in the at least one hatch-like panel (15a,....15n) is
covered by a plug (22).
6. Arrangement according to any of the preceding claims, characterized by that the support plate (10) is C-shaped, with a web (23) which forms the connection
part and two flanges (24) perpendicular to the web (23) and protruding away from the
housing (2).
1. Stabilisier- und Dichtungsanordnung für eine Seite-an-Seite-Luftbehandlungseinheit
(1), wobei die Luftbehandlungseinheit (1) ein Gehäuse (2) mit einem Oberpaneel (3),
einem Bodenpaneel (4), zwei Anschlusspaneelen (5, 6) zum Anschließen von Leitungen,
und einer Serviceseite (7) und einer Installationsseite (8) aufweist, und wobei die
Paneele (3, 4, 5, 6) Endseiten (3a, 3b; 4a, 4b; 5a, 5b; 6a, 6b) aufweisen, die der
Serviceseite (7) und der Installationsseite (8) zugewandt sind, wobei die Endseiten
(3a, 3b; 4a, 4b; 5a, 5b; 6a, 6b) eine im Wesentlichen ebene Oberfläche aufweisen,
und wobei das Gehäuse (2) weiterhin innere Strukturen (9) wie Filterhalter, Wärmeaustauscherhalter,
Heizungshalter, Teilungswände usw. aufweist, wobei zumindest manche der inneren Strukturen
(9) zumindest eine Endseite (9a,b) aufweisen, die der Serviceseite (7) bzw. der Installationsseite
(8) zugewandt ist, dadurch gekennzeichnet, dass eine Stützplatte (10) jeweils an der Wartungsseite (7) und an der Installationsseite
(8) angeordnet ist, wobei die Stützplatte (10) jeweils fest mit den Endseiten (3a,
3b; 4a, 4b; 5a, 5b; 6a, 6b) des Ober-, Boden- und der Anschlusspaneele (3, 4, 5, 6)
stabilisierend verbunden ist, und vorzugsweise mit zumindest manchen der Endseiten
(9a,b) der inneren Strukturen (9) fest verbunden ist, und wobei die jeweilige Stützplatte
(10) eine erste Dichtung (11) an zumindest einer ersten Seite (12) aufweist, die dem
Gehäuse (2) zugewandt ist, und wobei die erste Dichtung (11) derart angeordnet ist,
dass jeder Kontakt zwischen benachbarten Endseiten (3a, 3b; 4a, 4b; 5a, 5b; 6a, 6b;
9a, 9b) und der Stützplatte (10) die erste Dichtung 11 dazwischen aufweist, und weiterhin,
dass jegliche Öffnung (13) in der jeweiligen Stützplatte (10) an einer zweiten Seite
(14) der Stützplatte (10), die der ersten Seite (12) entgegengesetzt ist und von dem
Gehäuse (2) abgewandt ist, durch zumindest ein lukenartiges Paneel (15a,.... 15n)
bedeckt ist, von denen jedes eine zweite Dichtung (16a,....16n) aufweist, die der
zweiten Seite (14) der Stützplatte (10) zugewandt ist, und wobei die zweite Dichtung
(16a,....16n) derart angeordnet ist, dass jeder Kontakt zwischen dem zumindest einen
lukenartigen Paneel (15a,....15n) und der zweiten Seite (14) der Stützplatte (10)
die zweite Dichtung (16a,....16n) dazwischen aufweist, wodurch jede Öffnung (13) in
der Stützplatte (10) überlappend bedeckt ist, so wie jede Öffnung (13) von der zweiten
Dichtung (16a,....16n) umgeben ist.
2. Anordnung nach Anspruch 1, dadurch gekennzeichnet, dass die erste Dichtung (11) die gesamte Fläche der ersten Seite (12) der Stützplatte
(10) bedeckt.
3. Anordnung nach Anspruch 1 oder 2, dadurch gekennzeichnet, dass die zweite Seite (14) der Stützplatte (10) eine im Wesentlichen ebene Oberfläche
aufweist, zumindest in dem Bereich, wo die zweite Dichtung (16a,....16n) anliegt.
4. Anordnung nach irgendeinem der vorhergehenden Ansprüche, dadurch gekennzeichnet, dass jegliche Serviceöffnung (17) und Installationsöffnung (18) in dem zumindest einen
lukenartigen Paneel (15a,....15n) durch eine deckelartige Anordnung (19) bedeckt ist,
die mit einer dritten Dichtung (20) angeordnet ist, die dem zumindest einen lukenartigen
Paneel (15a,....15n) zugewandt ist, und wobei die dritte Dichtung (20) derart angeordnet
ist, dass jeder Kontakt zwischen der deckelartigen Anordnung (19) und dem zumindest
einen lukenartigen Paneel (15a,....15n) die dritte Dichtung (20) dazwischen aufweist.
5. Anordnung nach irgendeinem der vorhergehenden Ansprüche, dadurch gekennzeichnet, dass jegliches Montageloch (21 ) in dem zumindest einen lukenartigen Paneel (15a,....15n)
durch einen Stöpsel (22) bedeckt ist.
6. Anordnung nach irgendeinem der vorhergehenden Ansprüche, dadurch gekennzeichnet, dass die Stützplatte (10) C-förmig ist, mit einem Steg (23), der den Verbindungsteil bildet,
und zwei Flanschen (24) senkrecht zu dem Steg (23), und die von dem Gehäuse (2) weg
ragen.
1. Arrangement de stabilisation et d'étanchéisation pour une unité juxtaposée de traitement
de l'air (1), ladite unité de traitement de l'air (1) comprenant un logement (2) muni
d'un panneau supérieur (3), d'un panneau inférieur (4), de deux panneaux de connexion
(5, 6) pour la connexion de conduits, et un côté de service (7) et un coté de montage
(8), et les panneaux (3, 4, 5, 6) possédant des côtés terminaux (3a, 3b ; 4a, 4b ;
5a, 5b ; 6a, 6b) opposés au côté de service (7) et au côté de montage (8), lesdits
côtés terminaux (3a, 3b ; 4a, 4b ; 5a, 5b ; 6a, 6b) possédant une surface essentiellement
lisse, et le logement (2) comprenant en outre des structures internes (9) telles que
des supports de filtres, des supports d'échangeurs de chaleur, des supports de dispositifs
de chauffage, des parois de séparation, etc., au moins un certain nombre des structures
internes (9) possédant au moins un côté terminal (9a, b) opposé au côté de service
(7) et au côté de montage (8), respectivement, caractérisé par le fait qu'une plaque de support (10) est disposée du côté du service (7) et du côté du montage
(8), respectivement, ladite plaque de support (10) étant reliée respectivement à demeure
aux côtés terminaux (3a, 3b ; 4a, 4b ; 5a, 5b ; 6a, 6b) des panneaux supérieur, inférieur
et de connexion (3, 4, 5, 6) d'une manière procurant une stabilisation, et de préférence
reliée à demeure à au moins un certain nombre des côtés terminaux (9a, b) des structures
internes (9), et ladite plaque de support respective (10) comprenant un premier joint
d'étanchéité (11) à au moins un premier côté (12) opposé au logement (2), et ledit
premier joint d'étanchéité (11) étant arrangé d'une manière telle qu'à chaque contact
entre des côtés terminaux adjacents (3a, 3b ; 4a, 4b ; 5a, 5b ; 6a, 6b ; 9a, 9b) et
la plaque de support (10), le premier joint d'étanchéité (11) vient se disposer entre
eux, et en outre en ce que n'importe quelle ouverture (13) dans la plaque de support
respective (10) est recouverte, à un deuxième côté (14) de la plaque de support (17),
opposé au premier côté (12) et s'écartant du logement (2), par au moins un panneau
analogue à une écoutille (15a, ... 15n), chacun comprenant un deuxième joint d'étanchéité
(16a, ... 16n) opposé au deuxième côté (14) de la plaque de support (10) et ledit
deuxième joint d'étanchéité (16a, ... 16n) est arrangé d'une manière telle qu'à chaque
contact entre ledit au moins un panneau analogue à une écoutille (15a, ... 15n) et
le deuxième côté (14) de la plaque de support (10), le deuxième joint d'étanchéité
(16a, ... 16n) vient se disposer entre eux, dans lequel chaque ouverture (13) dans
la plaque de support (10) est recouverte d'une manière chevauchante, de telle façon
que chaque ouverture (13) est entourée par le deuxième joint d'étanchéité (16a, ...
16n).
2. Arrangement selon la revendication 1, caractérisé par le fait que le premier joint d'étanchéité (11) recouvre toute la surface du premier côté (12)
de la plaque de support (10).
3. Arrangement selon la revendication 1 ou 2, caractérisé par le fait que le deuxième côté (14) de la plaque de support (10) possède une surface essentiellement
lisse, au moins dans la zone dans laquelle vient s'appuyer le deuxième joint d'étanchéité
(16a,... 16n).
4. Arrangement selon l'une quelconque des revendications précédentes, caractérisé par le fait que n'importe quelle ouverture de service (17) et n'importe quelle ouverture de montage
(18) dans ledit au moins un panneau analogue à une écoutille (15a, ... 15n) est recouverte
par un arrangement en forme de couvercle (19), muni d'un troisième joint d'étanchéité
(20) opposé audit au moins un panneau analogue à une écoutille (15a, ... 15n), et
ledit troisième joint d'étanchéité (20) est disposé d'une manière telle qu'à chaque
contact entre l'arrangement en forme de couvercle (19) et ledit au moins un panneau
analogue à une écoutille (15a, ... 15n) le troisième joint d'étanchéité (20) vient
se disposer entre eux.
5. Arrangement selon l'une quelconque des revendications précédentes, caractérisé par le fait que n'importe quel trou de montage (21) dans ledit au moins un panneau analogue à une
écoutille (15a, ... 15n) est recouvert d'un bouchon (22).
6. Arrangement selon l'une quelconque des revendications précédentes, caractérisé par le fait que la plaque de support (10) possède une configuration en forme de C, comprenant une
nervure (23) qui forme la partie de connexion et deux brides (24) perpendiculaires
à la nervure (23) et faisant saillie par rapport au logement (2).
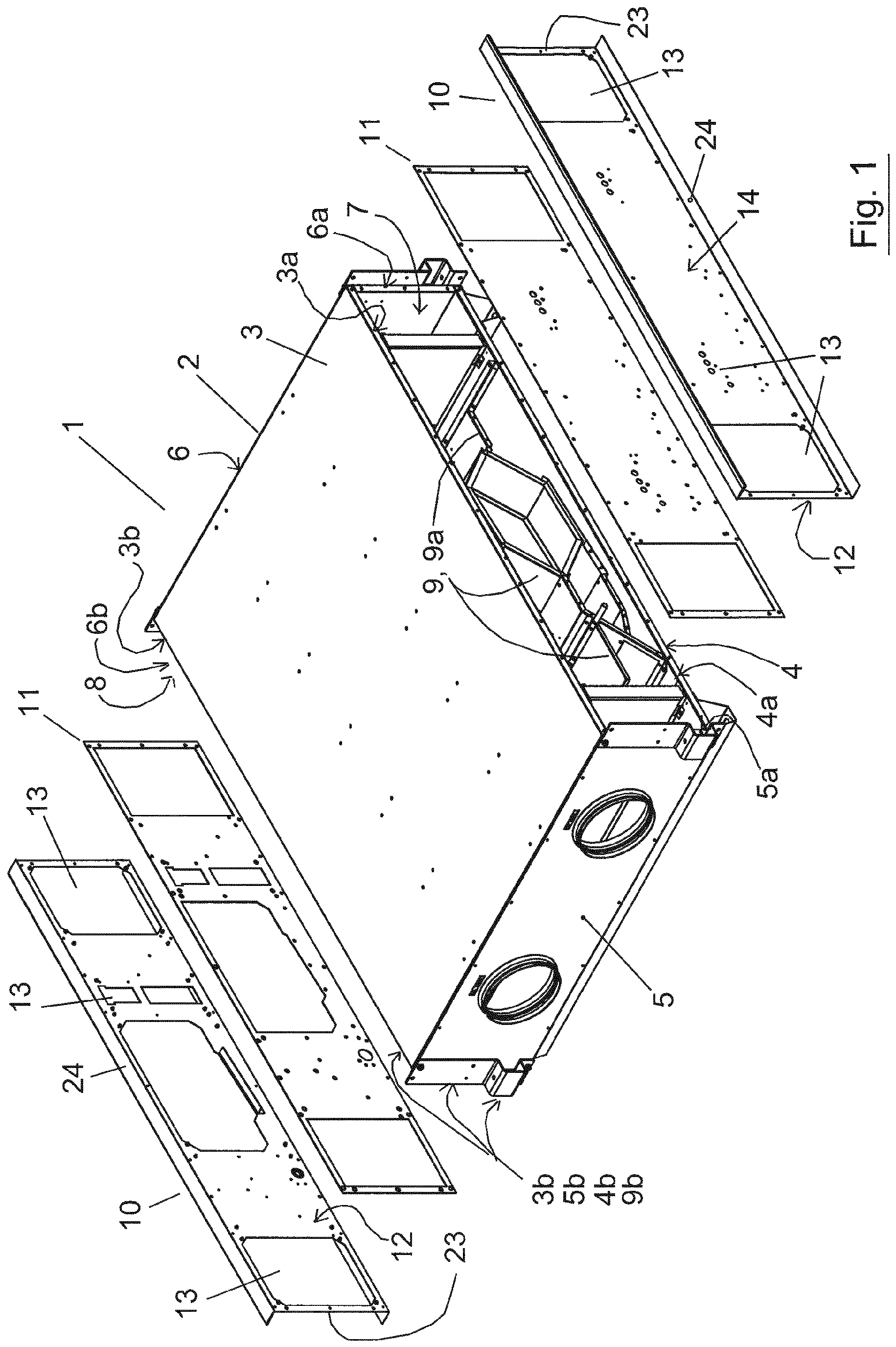
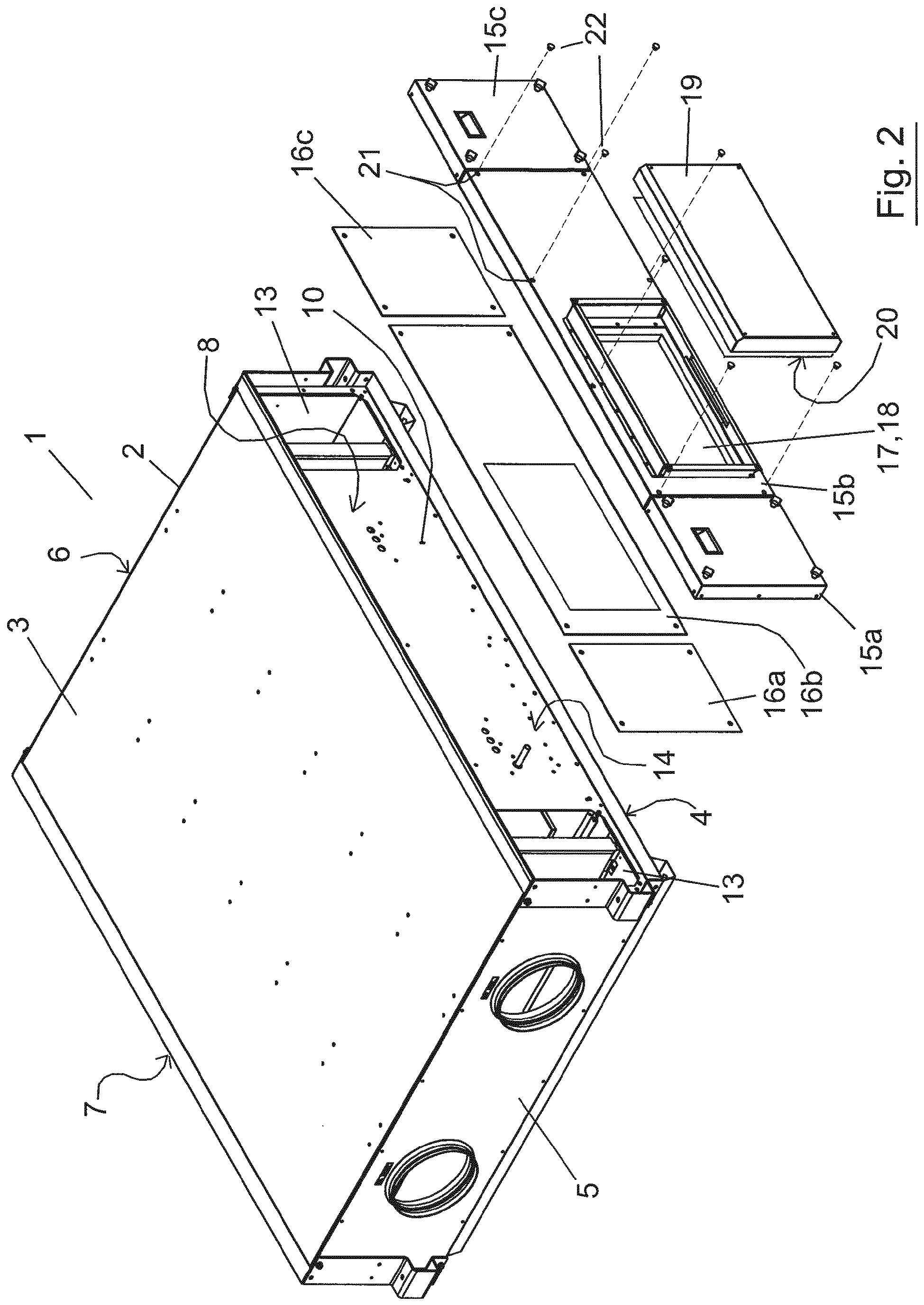
REFERENCES CITED IN THE DESCRIPTION
This list of references cited by the applicant is for the reader's convenience only.
It does not form part of the European patent document. Even though great care has
been taken in compiling the references, errors or omissions cannot be excluded and
the EPO disclaims all liability in this regard.
Patent documents cited in the description