TECHNICAL FIELD
[0001] The present invention relates to a method of manufacturing a steel sheet.
BACKGROUND ART
[0002] Various types of treatment steps are performed to manufacture a cold rolled steel
sheet or a cold rolled coil. Examples thereof include an acid cleaning step of removing
an oxide layer and an alkali cleaning step of removing rolling oil or rust-preventive
oil. In these cleaning steps, an acid cleaning liquid or an alkali cleaning liquid
is rinsed with warm water and dried with hot air. Because rust is generated if the
drying is insufficient, a dewatering process of removing water attached to the steel
sheet is important, and various dewatering methods have been carried out. In these
methods, for example, water is mechanically wrung out by using a rubber roll called
a wringer roll, or an air wiper is installed before hot air drying to blow away water
attached to the steel sheet as much as possible. The temperature of the rinsing water
for rinsing the cleaning liquid is generally 70°C or higher in order to enhance the
drying properties. However, at present, a high energy cost is required to increase
the temperature to a prescribed temperature because a large amount of water is used
in this rinsing treatment.
[0003] JP-A-06-238102 discloses a dewatering agent containing, as an active ingredient, a salt consisting
of an amine and/or an imine and an aliphatic carboxylic acid as an aqueous solution
type dewatering agent capable of preventing the generation of rust even when being
applied to metal as a dewatering method of making the surface of the steel sheet water-repellent
in order to suppress the use of rinsing water.
[0004] JP-A-09-255940 discloses a dewatering agent containing a specific nitrogen-containing compound as
a dewatering agent having excellent safety with no environmental contamination, having
excellent dewatering properties, capable of suppressing the generation of water stains,
having discoloration preventing and rust preventing effects on a metal part, and whose
component evaporates by drying, which makes the dewatering agent be difficult to remain
on the surface of the part.
[0005] JP-A-09-57005 discloses a dewatering agent containing a compound having a specific amino group
or a specific quaternary ammonium group as a surface treatment agent having excellent
safety with no environmental contamination, that hydrophobizes the surface of various
types of parts to be treated when the agent is used in the cleaning step to reduce
the amount of water attached to the parts in final pure water substitution, that prevents
the generation of water stains to reduce the drying time, having a rust preventing
effect on the metal part, and capable of preventing wet spreading of a conductive
adhesive used on the parts after the treatment into unnecessary places.
[0006] JP-A-2006-265726 discloses a rinsing agent composition for a steel sheet containing a specific cationic
compound and a specific nonionic compound as a rinsing agent composition for a steel
sheet that makes, even in a small amount, the surface of a steel sheet water-repellent
to give good dewatering properties even at a low temperature of 40°C or lower, that
is capable of reducing energy cost, that is capable of reducing the drying load, that
has a good rust-preventive effect even when water remains, and that has excellent
antifoaming properties.
SUMMARY OF THE INVENTION
[0007] The method of manufacturing a steel sheet of the present invention is a method of
manufacturing a steel sheet, including a cleaning step (1) of cleaning a steel sheet
after cold rolling, a rinsing step (2) of rinsing the steel sheet after being subjected
to the cleaning step (1), and a drying step (3) of drying the steel sheet after being
subjected to the rinsing step (2) ; wherein the rinsing step (2) includes one or more
rinsing treatments, a rinsing agent α used in a final rinsing treatment contains at
least one type of component (a) selected from compounds represented by the following
formula (1):
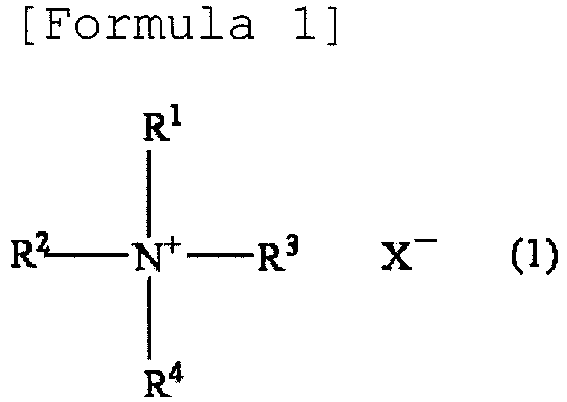
(wherein R
1 represents a hydrocarbon group having 6 or more and 22 or less carbon atoms, R
2 represents a hydrogen atom or a hydrocarbon group having 1 or more and 22 or less
carbon atoms, R
3 and R
4 are the same or different and each represent a hydrogen atom or a hydrocarbon group
having 1 or more and 3 or less carbon atoms, and X
- represents an inorganic anion or an organic anion), the concentration of the component
(a) is 150 mg/kg or less in the rinsing agent α, the cation concentration P
c (mmol/kg) (P
c = Σ(A X i) (wherein A represents the concentration of a cation per component (mmol/kg),
and i represents the valence of the cation)) of an inorganic salt in the rinsing agent
α is 2.0 mmol/kg or more and 18.0 mmol/kg or less, and the sulfate ion concentration
in the rinsing agent α is 0.75 mmol/kg or less.
DETAILED DESCRIPTION OF THE INVENTION
[0008] JP-A-06-238102,
JP-A-09-255940,
JP-A-09-57005, and
JP-A-2006-265726 describe a dewatering agent and a rinsing agent for a steel sheet containing a specific
amine compound and further a specific nonionic surfactant. However, those agents should
be used at a somewhat high concentration in order to make the steel sheet water-repellent.
[0009] An object of the present invention is to provide a method of manufacturing a steel
sheet, with which a steel sheet is made water-repellent by using an amine compound
and a nonionic surfactant at a low concentration compared to a conventional rinsing
agent to realize a small load in wastewater treatment and a reduced energy cost for
drying the steel sheet or the like after cleaning.
[0010] The present inventors found that a sufficient water-repelling effect may be exhibited
even if the concentration of the rinsing agent is low depending on the types of water
such as industrial water used in a manufacturing plant for a steel sheet. They focused
on the cation concentration of an inorganic salt in the rinsing agent. As a result,
they found that the cation concentration is adjusted to a specific range to reduce
the use amounts of the amine compound and the nonionic surfactant, and to reduce the
energy cost for drying the steel sheet or the like after cleaning, and completed the
present invention.
[0011] The method of manufacturing a steel sheet of the present invention is a method of
manufacturing a steel sheet, including a cleaning step (1) of cleaning a steel sheet
after cold rolling, a rinsing step (2) of rinsing the steel sheet after being subjected
to the cleaning step (1), and a drying step (3) of drying the steel sheet after being
subjected to the rinsing step (2) ; wherein the rinsing step (2) includes one or more
rinsing treatments, a rinsing agent α used in a final rinsing treatment contains at
least one type of component (a) selected from compounds represented by the following
formula (1):
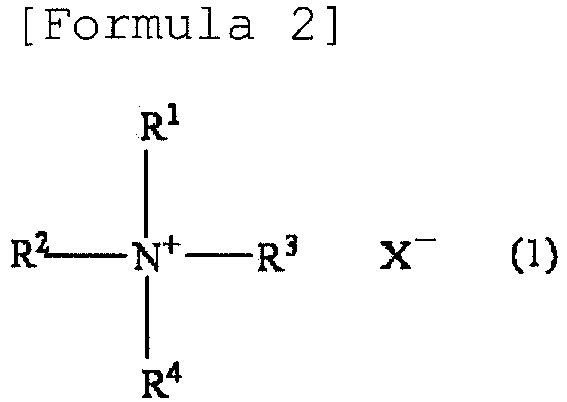
(wherein R
1 represents a hydrocarbon group having 6 or more and 22 or less carbon atoms, R
2 represents a hydrogen atom or a hydrocarbon group having 1 or more and 22 or less
carbon atoms, R
3 and R
4 are the same or different and each represent a hydrogen atom or a hydrocarbon group
having 1 or more and 3 or less carbon atoms, and X
- represents an inorganic anion or an organic anion), the concentration of the component
(a) is 150 mg/kg or less in the rinsing agent α the cation concentration P
c (mmol/kg) (P
c = Σ(A X i) (wherein A represents the concentration of a cation per component (mmol/kg),
and i represents a valence of the cation)) of an inorganic salt in the rinsing agent
α is 2.0 mmol/kg or more and 18.0 mmol/kg or less, and the sulfate ion concentration
in the rinsing agent α is 0.75 mmol/kg or less.
[0012] The present invention can provide a method of manufacturing a steel sheet having
a smaller load in wastewater treatment than that in a case where a conventional rinsing
agent is used and is capable of reducing the energy cost for drying a steel sheet
or the like after cleaning.
[0013] One embodiment of the present invention will be explained below.
[0014] The method of manufacturing a steel sheet of the present embodiment is a method of
manufacturing a steel sheet, including a cleaning step (1) of cleaning a steel sheet
after cold rolling, a rinsing step (2) of rinsing the steel sheet after being subjected
to the cleaning step (1), and a drying step (3) of drying the steel sheet after being
subjected to the rinsing step (2) ; wherein the rinsing step (2) includes one or more
rinsing treatments, a rinsing agent α used in a final rinsing treatment contains at
least one type of component (a) selected from compounds represented by the formula
(1), the concentration of the component (a) is 150 mg/kg or less in the rinsing agent
α the cation concentration P
c (mmol/kg) (P
c = Σ(A X i) (wherein A represents the concentration of a cation per component (mmol/kg),
and i represents a valence of the cation)) of an inorganic salt in the rinsing agent
α is 2.0 mmol/kg or more and 18.0 mmol/kg or less, and the sulfate ion concentration
in the rinsing agent α is 0.75 mmol/kg or less.
[0015] According to the method of manufacturing a steel sheet of the present embodiment,
the load in wastewater treatment and the energy cost for drying the steel sheet or
the like after cleaning can be reduced. The reasons why these effects are exhibited
are not clear; however, they can be considered as follows.
[0016] It is considered that the electric charge of the component (a) changes when the cation
concentration of an inorganic salt in the rinsing agent is set to a specific range,
making the component (a) be easily adsorbed to the surface of the steel sheet. It
is considered that the adsorption of the component (a) onto the surface of the steel
sheet gives water repellency to suppress the attachment of water onto the surface
of the steel sheet. It is also considered that an excessive amount of sulfate ions
causes the component (a) and the sulfate ion to form a complex to hinder the adsorption
of the component (a) onto the surface of the steel sheet.
[Cleaning step (1) of cleaning steel sheet after cold rolling]
[0017] In the cleaning step (1), stains from rolling oil or the like attached to a steel
sheet are cleaned with a detergent according to conditions of a conventional method.
The steel sheet may be made of any type of metal; however, iron is preferably used
from a viewpoint of promoting drying to prevent rust. Examples of the detergent include
alkaline detergents described in
JP-A-10-280179 and
JP-A-10-324900.
[0018] An aqueous solution containing an alkaline agent is used as the alkaline detergent.
In order to secure oil stain removability, any alkaline agent can be used as long
as the alkaline agent is water soluble. Specific examples of the alkaline agent include
alkali metal hydroxides such as sodium hydroxide and potassium hydroxide; silicates
such as sodium orthosilicate, sodium metasilicate, and sodium sesquisilicate; phosphates
such as trisodium phosphate; carbonates such as disodium carbonate, sodium bicarbonate,
and dipotassium carbonate; and borates such as sodium borate. Two types or more of
water-soluble alkaline agents may be combined. The content of the alkaline agent in
the alkaline detergent is preferably 0.1% by mass or more, and more preferably 1%
by mass or more; and is preferably 10% by mass or less, and more preferably 3% by
mass or less.
[0019] Besides the alkaline agent, examples of chemicals that can be added in the alkaline
detergent include nonionic surfactants such as polyoxyalkylene alkyl ether; chelating
agents that react with stains of iron soap or the like to chelate iron ions or the
like into fatty acid soap, and make stains be easily dissolved to improve cleaning
properties; and, from a viewpoint of securing the stability in storage and the stability
of the effects after storage, aliphatic carboxylic acids and salts thereof. Any additives
can be added in the alkaline detergent. For example, generally used additives such
as an organic builder for improving the cleaning properties can be compounded in the
alkaline detergent in consideration of the cost increase or the like. The ratio of
the components other than the alkaline agent to the alkaline detergent is appropriately
determined, and the ratio is preferably 1 part by mass or less, and more preferably
0.5 part by mass or less to 1 part by mass of the alkaline agent. The ratio of non-volatile
contents including the alkaline agent and components other than the alkaline agent
to the alkaline detergent is preferably 1% by mass or more and 10% by mass or less.
[0020] Examples of the cleaning step (1) include immersion cleaning, spray cleaning, brush
cleaning, and electrolytic cleaning. The electrolytic cleaning is a cleaning method
of making a steel sheet positively charged (or negatively charged) in the cleaning
liquid to feed a DC current, and is a step of removing, by a physical force, oil stains
and solid stains such as iron powder attached to the steel sheet using gas bubbles
of oxygen (or hydrogen) generated from the steel sheet due to the current. The cleaning
step (1) may be acid cleaning of removing the oxide film formed on the surface of
the steel sheet with an acid detergent.
[Rinsing step (2) of rinsing steel sheet after being subjected to cleaning step (1)]
[0021] In the rinsing step (2), the steel sheet after being subjected to the cleaning step
(1) is rinsed with water or a rinsing agent to remove the detergent and the remaining
rolling oil. The rinsing agent used in a final treatment of the rinsing step (2) (referred
to as a rinsing agent α below) contains the component (a) and has a cation concentration
and a sulfate ion concentration each in a specific range.
<Component (a)>
[0022] The component (a) is at least one type of organic cationic compound selected from
the compounds represented by the formula (1). The component (a) is preferably an alkylamine
acid salt and an alkylammonium salt, and more preferably an alkylamine acid salt.
[0023] In the formula (1), R
1 represents a hydrocarbon group having 6 or more carbon atoms. The number of carbon
atoms is preferably 8 or more, more preferably 12 or more, and further preferably
16 or more; and is 22 or less, and preferably 18 or less from a viewpoint of sufficiently
hydrophobizing the surface of the steel sheet. From a viewpoint of sufficiently hydrophobizing
the surface of the steel sheet, R
1 is preferably a straight chain or branched chain alkyl group or alkenyl group, and
more preferably a straight chain alkyl group or alkenyl group. Examples of R
1 include a hexyl group, an octyl group, a 2-ethylhexyl group, a decyl group, a lauryl
(dodecyl) group, a tridecyl group, a myristyl (tetradecyl) group, a palmityl (hexadecyl)
group, a stearyl (octadecyl) group, a behenyl group, and an oleyl group. From a viewpoint
of sufficiently hydrophobizing the surface of the steel sheet, R
1 is preferably a hexyl group, an octyl group, a lauryl (dodecyl) group, a tridecyl
group, a myristyl (tetradecyl) group, a palmityl (hexadecyl) group, a stearyl (octadecyl)
group, a behenyl group, or an oleyl group; more preferably a tridecyl group, a lauryl
(dodecyl) group, a myristyl (tetradecyl) group, a palmityl (hexadecyl) group, a stearyl
(octadecyl) group, a behenyl group, or an oleyl group; further preferably a lauryl
(dodecyl) group, a myristyl (tetradecyl) group, a palmityl (hexadecyl) group, a stearyl
(octadecyl) group, or an oleyl group; and even more preferably a palmityl (hexadecyl)
group or an oleyl group.
[0024] In the formula (1), R
2 represents a hydrogen atom or a hydrocarbon group having 1 or more carbon atoms.
The number of carbon atoms is preferably 6 or more, more preferably 8 or more, further
preferably 12 or more, and even more preferably 16 or more; and is 22 or less, and
preferably 18 or less from a viewpoint of sufficiently hydrophobizing the surface
of the steel sheet. From a viewpoint of sufficiently hydrophobizing the surface of
the steel sheet, R
2 is preferably a straight chain or branched chain alkyl group or alkenyl group, and
more preferably a straight chain alkyl group or alkenyl group. Examples of R
2 include a hydrogen atom, a methyl group, an ethyl group, an isopropyl group, a hexyl
group, an octyl group, a 2-ethylhexyl group, a decyl group, a lauryl (dodecyl) group,
a tridecyl group, a myristyl (tetradecyl) group, a palmityl (hexadecyl) group, a stearyl
(octadecyl) group, a behenyl group, and an oleyl group. From a viewpoint of sufficiently
hydrophobizing the surface of the steel sheet, R
2 is preferably a hydrogen atom.
[0025] R
3 and R
4 are the same or different; and each represent a hydrogen atom or a hydrocarbon group
having 1 or more and 3 or less carbon atoms such as a methyl group, an ethyl group,
and an isopropyl group. From a viewpoint of sufficiently hydrophobizing the surface
of the steel sheet, R
3 and R
4 are preferably hydrogen atoms.
[0026] Specific examples of X
- include halide ions such as a chloride ion and a bromide ion; organic anions resulting
from removal of a proton from an organic acid such as acetic acid, lactic acid, or
citric acid; an alkyl carbonate ion (CH
3CO
3-) ; and an alkyl phosphate ion. From a viewpoint of sufficiently hydrophobizing the
surface of the steel sheet, X
- is preferably a halide ion such as a chloride ion or a bromide ion, or an organic
anion such as CH
3CO
3-, and is more preferably an organic anion. A sulfate ion can also be used. However,
in this case, the concentration of the sulfate ion in the rinsing agent α should be
0.75 mmol/kg or less.
[0027] Examples of the component (a) include acid neutralized products of dioctylamine,
didecylamine, dilaurylamine, dimyristylamine, decyloctylamine, lauryloctylamine, laurylamine,
lauryl dimethyl amine, myristylamine, myristyl dimethyl amine, palmitylamine, palmityl
dimethyl amine, stearylamine, stearyl dimethyl amine, oleylamine, and oleyl dimethyl
amine; and quaternary ammonium salts. When an acid neutralized product is used as
the component (a), at least one of R
2, R
3, and R
4 represents a hydrogen atom.
[0028] Examples of the preferred acid for obtaining the acid neutralized product include
hydrochloric acid, nitric acid, phosphoric acid, acetic acid, formic acid, maleic
acid, fumaric acid, citric acid, tartaric acid, adipic acid, sulfamic acid, toluenesulfonic
acid, lactic acid, pyrrolidone-2-carboxylic acid, and succinic acid. From a viewpoint
of sufficiently hydrophobizing the surface of the steel sheet, the acid is preferably
hydrochloric acid and acetic acid, and more preferably acetic acid. Examples of preferred
quaternization agent for obtaining a quaternary ammonium salt include general alkylation
agents such as alkyl halides including methyl chloride, ethyl chloride, methyl bromide,
and methyl iodide.
[0029] Examples of the component (a) include an acid neutralized product of a monoalkylamine
having 6 or more and 22 or less carbon atoms, an acid neutralized product of a monoalkyl
methyl amine having 6 or more and 22 or less carbon atoms, an acid neutralized product
of a monoalkyl dimethyl amine having 6 or more and 22 or less carbon atoms, an acid
neutralized product of a dialkyl methyl amine having 1 or more and 22 or less carbon
atoms, an acid neutralized product of a dialkyl dimethyl amine having 1 or more and
22 or less carbon atoms, a alkyltrimethyl ammonium having 6 or more and 22 or less
carbon atoms, and dialkyl ammonium having 1 or more and 22 or less carbon atoms. Specific
examples include dioctylamine hydrochloride, dioctyl dimethyl ammonium chloride, dilauryl
dimethyl ammonium chloride, dimyristyl dimethyl ammonium chloride, distearyl dimethyl
ammonium chloride, dioleyl dimethyl ammonium chloride, lauryl trimethyl ammonium bromide,
stearyl trimethyl ammonium chloride, oleyl trimethyl ammonium chloride, lauryl trimethyl
ammonium chloride, laurylamine hydrochloride, stearylamine hydrochloride, oleylamine
hydrochloride, laurylamine acetate, myristylamine acetate, myristyl trimethyl ammonium
chloride, palmitylamine acetate, palmityl trimethyl ammonium chloride, stearylamine
hydrochloride, stearyl trimethyl ammonium chloride, oleylamine acetate, hexylamine
acetate, behenylamine acetate, and behenyl trimethyl ammonium chloride. From a viewpoint
of sufficiently hydrophobizing the surface of the steel sheet, the component (a) is
preferably hexylamine acetate, octylamine acetate, laurylamine acetate, hexadecylamine
acetate, oleylamine acetate, stearylamine acetate, behenylamine acetate, hexylamine
hydrochloride, octylamine hydrochloride, laurylamine hydrochloride, hexadecylamine
hydrochloride, oleylamine hydrochloride, stearylamine hydrochloride, or behenylamine
hydrochloride; and is more preferably hexadecylamine acetate, oleylamine acetate,
hexadecylamine hydrochloride, or oleylamine hydrochloride.
[0030] From a viewpoint of sufficiently hydrophobizing the surface of the steel sheet, the
concentration of the component (a) in the rinsing agent α is preferably 5 mg/kg or
more, more preferably 10 mg/kg or more, and further preferably 20 mg/kg or more. From
a viewpoint of preventing the excessive component (a) from being attached to the steel
sheet and hindering the subsequent annealing process and plating process, the concentration
is 150 mg/kg or less, preferably 148 mg/kg or less, more preferably 145 mg/kg or less,
further preferably 120 mg/kg or less, and even more preferably 110 mg/kg or less.
[0031] The cation concentration P
c (mmol/kg) of the inorganic salt in the rinsing agent α is 2.0 mmol/kg or more and
18.0 mmol/kg or less. The cation concentration P
c of water is adjusted when preparing the rinsing agent α to adjust the cation concentration
P
c of the inorganic salt. Accordingly, the method of manufacturing a steel sheet of
the present embodiment may have a cation concentration P
c measurement step of measuring the cation concentration P
c of the inorganic salt in water for preparing the rinsing agent α and a rinsing agent
α preparation step of preparing the rinsing agent α used in the rinsing step (2) so
that the cation concentration P
c of the inorganic salt is within the above-described range based on a value measured
in the cation concentration P
c measurement step. The cation concentration P
c can be measured by a general method. For example, the cation concentration P
c can be measured by a method described in the examples. An example of the method of
preparing the rinsing agent α used in the rinsing step (2) so that the cation concentration
P
c of the inorganic salt is within the above-described range based on a value measured
in the cation concentration P
c measurement step is a method of adjusting the cation concentration P
c of water for preparing the rinsing agent α and preparing the rinsing agent α using
the adjusted water. An example of the method of adjusting the cation concentration
P
c of water when preparing the rinsing agent α is, when the cation concentration P
c of industrial water used in a manufacturing plant for a steel sheet is low, a method
of adding the inorganic salt into the industrial water to increase the cation concentration
P
c, or, when the cation concentration P
c of the industrial water is high, a method of mixing water having a low cation concentration
P
c, such as deionized water, into the industrial water to lower the cation concentration
P
c. When the industrial water, deionized water or the like having a low cation concentration
P
c is used to prepare the rinsing agent α the rinsing agent may be prepared using the
industrial water having a low cation concentration P
c, and the inorganic salt may be added into the rinsing agent to adjust the cation
concentration P
c.
[0032] Examples of the method of obtaining the deionized water include a method of treating
water with an ion exchange resin or an ion exchange membrane, a method of treating
water by ultrafiltration, and a method of treating water by distillation. Examples
of the inorganic salt include one or more types of compounds selected from an alkali
metal salt, an alkaline earth metal salt, and an aluminum salt. Specific examples
include chlorides such as sodium chloride, potassium chloride, calcium chloride, magnesium
chloride, and aluminum chloride; nitrates such as sodium nitrate; and carbonates such
as sodium carbonate. The cation that achieves the cation concentration P
c is an inorganic cation, and examples include alkali metal ions such as a sodium ion
and a potassium ion, alkaline earth metal ions such as a calcium ion and a magnesium
ion, and an aluminum ion.
[0033] The rinsing agent α exhibits water-repellency. From a viewpoint of suppressing the
attachment of water to the surface of the steel sheet, the cation concentration P
c of the inorganic salt is 2.0 mmol/kg or more, preferably 4.0 mmol/kg or more, more
preferably 5.0 mmol/kg or more, and further preferably 6.0 mmol/kg or more; and is
18.0 mmol/kg or less, preferably 17.0 mmol/kg or less, and more preferably 10.0 mmol/kg
or less.
[0034] In the present description, the cation concentration P
c of the inorganic salt can be obtained by the following formula (a) :

(wherein A represents the concentration of a cation per component (mmol/kg), and
i represents a valence of the cation).
[0035] If the sulfate ion concentration in the rinsing agent α exceeds 0.75 mmol/kg, the
water-repellency deteriorates. It is considered that this is because the component
(a) and the sulfate ion form a complex if there is too large an amount of sulfate
ions, which hinders the attachment of the component (a) onto the surface of the steel
sheet. From a viewpoint of exhibiting water-repellency and suppressing the attachment
of water to the surface of the steel sheet, the sulfate ion concentration in the rinsing
agent α is 0.75 mmol/kg or less, preferably 0.70 mmol/kg or less, more preferably
0.40 mmol/kg or less, further preferably 0.20 mmol/kg or less, and even more preferably,
the rinsing agent α contains no sulfate ion. When the sulfate ion concentration is
high, water having a low sulfate ion concentration such as ion exchange water can
be mixed to lower the sulfate ion concentration. The method of manufacturing a steel
sheet of the present embodiment preferably includes a step of measuring the sulfate
ion concentration in water for preparing the rinsing agent α and a step of preparing
the rinsing agent α used in the rinsing step (2) so that the sulfate ion concentration
is within the above-described range based on a value measured in the sulfate ion concentration
measurement step.
[0036] The rinsing agent α is an aqueous composition containing the component (a), and water
is used as an aqueous medium. Examples of the preferable water include deionized water,
ion exchange water, tap water, and industrial water. From a viewpoint of adjusting
the cation concentration P
c and the sulfate ion concentration, water having a cation concentration P
c and a sulfate ion concentration within the above-described ranges is preferable.
[0037] The rinsing agent α may contain a defoaming agent, a chelating agent, a preservative,
and the like as long as the effect of the present invention is exhibited. However,
the cation concentration P
c of the inorganic salt and the sulfate ion concentration in the rinsing agent α are
adjusted to be within the above-described range even when the rinsing agent α contains
the defoaming agent, the chelating agent, the preservative, and the like. From a viewpoint
of making the surface of the steel sheet water-repellent, the pH of the rinsing agent
α is preferably 3 or more, more preferably 5 or more, and more preferably 6 or more;
and is preferably 10 or less, and more preferably 9 or less.
[0038] In order to reduce the energy cost required to increase the temperature of the rinsing
agent in the rinsing step (2), the rinsing agent α is preferably used at 60°C or lower,
more preferably 50°C or lower, further preferably 40°C or lower, and even more preferably
30°C or lower. The lower limit is not particularly limited; however, it is normally
5°C or higher.
[0039] The rinsing step (2) can include one or more rinsing treatments. In the final rinsing
treatment of the rinsing step (2) before the drying step, the rinsing agent α is made
to contact the steel sheet after being subjected to the cleaning step (1). When the
rinsing step (2) includes two or more rinsing treatments, a rinsing agent other than
the rinsing agent α or water can be used to perform the rinsing treatments in the
rinsing step (2); however, it is necessary to use the rinsing agent α in the final
rinsing treatment of the rinsing step (2).
[0040] Specific examples of the rinsing agent treatment using the rinsing agent α performed
in the final rinsing treatment of the rinsing step (2) include a brush rinsing treatment
of spraying the rinsing agent α onto the steel sheet while brushing the steel sheet
to rinse the steel sheet, a spray rinsing treatment of spraying the rinsing agent
α onto the steel sheet without brushing the steel sheet to rinse the steel sheet,
and an immersion rinsing treatment of immersing the steel sheet in the rinsing agent
α to rinse the steel sheet. Among these, from a viewpoint of making the rinsing agent
α efficiently acting on the steel sheet, the immersion rinsing treatment and/or the
spray rinsing treatment is preferable; and from a viewpoint of making the rinsing
agent α directly and efficiently acting on the steel sheet, the spray rinsing treatment
is more preferable. From a viewpoint of recycling the rinsing agent α, preferably,
the rinsing agent α is sprayed onto the steel sheet, the rinsing agent α distilled
from the surface of the steel sheet after the spray treatment is introduced into an
immersion tank, and the rinsing agent α is used in the immersion rinsing treatment.
[0041] In the brush rinsing treatment, the steel sheet and a brush roll are sprayed with
the rinsing agent α while the steel sheet is conveyed between the brush rolls or between
the brush roll and a conveying roll, so that the steel sheet is brought into contact
with the rinsing agent α. The rotational speed of the brush roll is preferably 100
rotations/min or more, and more preferably 500 rotations/min or more; and is preferably
1,200 rotations/min or less, and more preferably 1,000 rotations/min or less.
[0042] In the spray rinsing treatment, the steel sheet is directly sprayed with the rinsing
agent α so that the steel sheet is brought into contact with the rinsing agent α.
As for the conditions of spraying, the spray pressure is preferably 0.05 MPa or more,
and more preferably 0.1 MPa or more; and is preferably 1.5 MPa or less, and more preferably
1 MPa or less. The spray amount is preferably 1 m
3/hour or more, more preferably 5 m
3/hour or more, and further preferably 7 m
3/hour or more; and is preferably 100 m
3/hour or less, more preferably 70 m
3/hour or less, and further preferably 60 m
3/hour or less. The spray time (contact time in the spray rinsing treatment) is preferably
0.01 second or more, more preferably 0.1 second or more, and further preferably 1
second or more; and is preferably 30 seconds or less, and more preferably 10 seconds
or less.
[0043] In the immersion rinsing treatment, the immersion time of the steel sheet in the
rinsing agent α is preferably 1 second or more and 5 seconds or less. When the steel
sheet is showered with the rinsing agent α the spray pressure is preferably 0.05 MPa
or more and 1.5 MPa or less, and the spray time is preferably 0.1 second or more and
5 seconds or less.
[0044] When the steel sheet is treated with water or a rinsing agent other than the rinsing
agent α in the rinsing step (2) including two or more rinsing treatments, a method
of performing the brush rinsing treatment with water or a rinsing agent other than
the rinsing agent α and the immersion rinsing treatment with the rinsing agent α,
and a method of performing the immersion rinsing treatment with water or a rinsing
agent other than the rinsing agent α and the spray rinsing treatment with the rinsing
agent α are preferable. From a viewpoint of reducing a load in the wastewater treatment,
the steel sheet is more preferably rinsed with water and then with the rinsing agent
α. Specifically, a method of performing the brush rinsing treatment with water and
the immersion rinsing treatment with the rinsing agent α, and a method of performing
the immersion rinsing treatment with water and the spray rinsing treatment with the
rinsing agent α are more preferable.
[0045] When the steel sheet is treated with water or a rinsing agent other than the rinsing
agent α, the temperature of water that is used is preferably 5°C or higher, and more
preferably 10°C or higher; and is preferably 60°C or lower, more preferably 50°C or
lower, further preferably 40°C or lower, and even more preferably 30°C or lower. As
a method of treating the steel sheet with water, the steel sheet may be immersed in
water or a rinsing agent, or the steel sheet may be rinsed with shower or the like.
When the steel sheet is immersed in water or a rinsing agent, the immersion time is
preferably 1 second or more and 5 seconds or less. When the steel sheet is showered
with water or a rinsing agent, the spray pressure is preferably 0.05 MPa or more and
1.5 MPa or less, and the spray time is preferably 0.1 second or more and 5 seconds
or less.
[0046] In the brush rinsing treatment, the steel sheet and a brush roll are sprayed with
water or a rinsing agent while the steel sheet is conveyed between the brush rolls
or between the brush roll and a conveying roll, so that the steel sheet is brought
into contact with water or a rinsing agent. The rotational speed of the brush roll
is preferably 100 rotations/min or more, and more preferably 500 rotations/min or
more; and is preferably 1, 200 rotations/min or less, and more preferably 1,000 rotations/min
or less.
[0047] In the spray rinsing treatment, the steel sheet is directly sprayed with water or
a rinsing agent, so that the steel sheet is brought into contact with water or a rinsing
agent. For the conditions of spraying, the spray pressure is preferably 0.05 MPa or
more, and more preferably 0.1 MPa or more; and is preferably 1.5 MPa or less, and
more preferably 1 MPa or less. The spray amount is preferably 1 m
3/hour or more, more preferably 5 m
3/hour or more, and further preferably 7 m
3/hour or more; and is preferably 100 m
3/hour or less, more preferably 70 m
3/hour or less, and further preferably 60 m
3/hour or less. The spray time (contact time in the spray rinsing treatment) is preferably
0.01 second or more, more preferably 0.1 second or more, and further preferably 1
second or more; and is preferably 30 seconds or less, and more preferably 10 seconds
or less.
[0048] When the steel sheet is immersed in water or a rinsing agent in the rinsing step
(2), the immersion time of the steel sheet in water or a rinsing agent is preferably
0.5 second or more, and more preferably 1 second or more; and is preferably 10 seconds
or less, and more preferably 5 seconds or less.
[0049] The cleaning step (1) and the rinsing step (2) are normally provided as a continuous
line for conveying a steel sheet. The conveying speed of the steel sheet is normally
30 m/min or more, and preferably 50 m/min or more; and is 1,000 m/min or less, and
preferably 800 m/min or less. The treatment time for each of the cleaning step (1)
and the rinsing step (2) is set in consideration of the speed of the conveying line.
[0050] From a viewpoint of reducing a load in the drying step (3), a treatment of holding
a surface of the steel sheet after being subjected to a rinsing agent treatment using
the rinsing agent α to be substantially perpendicular to the ground is preferably
performed between the rinsing agent treatment using the rinsing agent α and the drying
step (3). With this treatment, water on the surface of the steel sheet, to which water-repellency
is given by the rinsing agent α, drops by gravity to reduce the amount of water remaining
on the surface of the steel sheet. From a viewpoint of reducing the moisture amount
at the surface of the steel sheet, the time of holding a surface of the steel sheet
to be substantially perpendicular to the ground is preferably 1 second or more, and
more preferably 3 seconds or more; and from a viewpoint of conveying the steel sheet,
the time is preferably 30 seconds or less, and more preferably 20 seconds or less.
The surface of the steel sheet being substantially perpendicular to the ground means
that the surface of the steel sheet is held at a certain degree of angle to the ground
so that the water droplets on the steel sheet drop by gravity. Specifically, the angle
of the surface of the steel sheet to the ground is preferably 90 ± 10°, and more preferably
90 ± 5°.
[0051] From a viewpoint of reducing a load in the drying step (3), a treatment of spraying
a gas such as air onto the surface of the steel sheet to blow away the moisture on
the steel sheet is preferably performed between the rinsing agent treatment using
the rinsing agent α and the drying step (3).
[Drying step (3) of drying steel sheet after being subjected to rinsing step (2)]
[0052] In the drying step (3), the steel sheet after being subjected to the rinsing step
(2) and attached with the rinsing agent α is dried. In the drying step (3), the steel
sheet attached with the rinsing agent α is dried according to conditions of a conventional
method. An example of the drying means in the drying step is a method of placing the
steel sheet in an oven at 80°C or higher and 150°C or lower and preferably 120°C or
lower. Another example thereof is a method of spraying a gas such as air whose temperature
is adjusted to be in this range onto the surface of the steel sheet. From a viewpoint
of reducing the number of heaters in the continuous line in which the steel sheet
is conveyed to reduce the energy cost, the drying time is preferably 60 seconds or
less, more preferably 40 seconds or less, and further preferably 20 seconds or less.
In the manufacturing facility of the steel sheet plant, an example of the drying means
is a method of heating the steel sheet for 3 seconds to 10 seconds at a temperature
of 80°C or higher and 150°C or lower and preferably 120°C or lower to dry the steel
sheet.
[0053] The steel sheet obtained after cleaning can be used in various uses such as a steel
sheet for automobiles, a steel sheet for drinks such as a can, and a steel sheet for
home electric appliances. The amount of oil stains and the like attached onto the
surface of the steel sheet after cleaning differs depending on the use of the steel
sheet; however, the amount is preferably 10% or less, more preferably 5% or less,
and even more preferably 3% or less after cleaning relative to the mass of carbon
attached to the steel sheet before cleaning being 100%.
[0054] The present description also discloses the following manufacturing method, composition,
and uses related to the above-described embodiment.
- <1> A method of manufacturing a steel sheet, including a cleaning step (1) of cleaning
a steel sheet after cold rolling, a rinsing step (2) of rinsing the steel sheet after
being subjected to the cleaning step (1), and a drying step (3) of drying the steel
sheet after being subjected to the rinsing step (2); wherein the rinsing step (2)
includes one or more rinsing treatments, a rinsing agent α used in a final rinsing
treatment contains at least one type of component (a) selected from compounds represented
by the following formula (1):
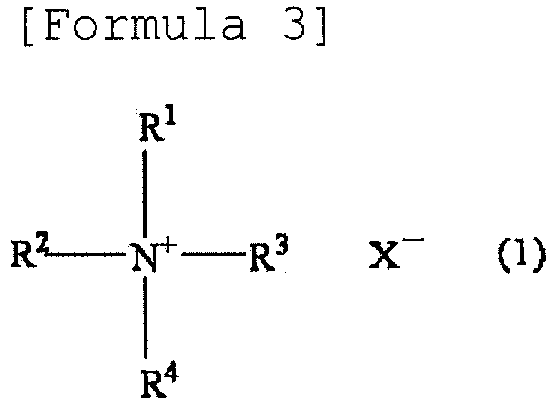
(wherein R1 represents a hydrocarbon group having 6 or more and 22 or less carbon atoms, R2 represents a hydrogen atom or a hydrocarbon group having 1 or more and 22 or less
carbon atoms, R3 and R4 are the same or different and each represent a hydrogen atom or a hydrocarbon group
having 1 or more and 3 or less carbon atoms, and X- represents an inorganic anion or an organic anion), the concentration of the component
(a) is 150 mg/kg or less in the rinsing agent α, the cation concentration Pc (mmol/kg) (Pc = E (A X i) (wherein A represents the concentration of a cation per component (mmol/kg),
and i represents a valence of the cation)) of an inorganic salt in the rinsing agent
α is 2.0 mmol/kg or more and 18.0 mmol/kg or less, and the sulfate ion concentration
in the rinsing agent α is 0.75 mmol/kg or less.
- <2> The method of manufacturing a steel sheet according to <1>, wherein R1 is a straight chain or branched chain alkyl group or alkenyl group having 6 or more
carbon atoms, preferably 8 or more carbon atoms, more preferably 12 or more carbon
atoms, and further preferably 16 or more carbon atoms; and 22 or less carbon atoms,
and preferably 18 or less carbon atoms.
- <3> The method of manufacturing a steel sheet according to <1> or <2>, wherein R2 is a hydrogen atom, preferably a straight chain or branched chain alkyl group or
alkenyl group, and more preferably a straight chain alkyl group or alkenyl group having
1 or more carbon atoms, preferably 6 or more carbon atoms, more preferably 8 or more
carbon atoms, further preferably 12 or more carbon atoms, and even more preferably
16 or more carbon atoms; and 22 or less carbon atoms, and preferably 18 or less carbon
atoms.
- <4> The method of manufacturing a steel sheet according to any of <1> to <3>, wherein
R3 and R4 are the same or different; and preferably each represent a hydrogen atom or a hydrocarbon
group having 1 or more and 3 or less carbon atoms, and more preferably a hydrogen
atom.
- <5> The method of manufacturing a steel sheet according to any of <1> to <4>, wherein
the concentration of the component (a) in the rinsing agent α is preferably 5 mg/kg
or more, more preferably 10 mg/kg or more, and further preferably 20 mg/kg or more;
and is 150 mg/kg or less, preferably 148 mg/kg or less, more preferably 145 mg/kg
or less, further preferably 120 mg/kg or less, and even more preferably 110 mg/kg
or less.
- <6> The method of manufacturing a steel sheet according to any of <1> to <5>, wherein
the cation concentration is 2.0 mmol/kg or more, preferably 4.0 mmol/kg or more, more
preferably 5.0 mmol/kg or more, and further preferably 6.0 mmol/kg or more; and is
18.0 mmol/kg or less, preferably 17.0 mmol/kg or less, and more preferably 10.0 mmol/kg
or less.
- <7> The method of manufacturing a steel sheet according to any of <1> to <6>, wherein
the sulfate ion concentration is 0.75 mmol/kg or less, preferably 0.70 mmol/kg or
less, more preferably 0.40 mmol/kg or more, further preferably 0.20 mmol/kg or less,
and even more preferably, the rinsing agent α contains no sulfate ion.
- <8> The method of manufacturing a steel sheet according to any of <1> to <7>, wherein
the temperature of the rinsing agent α in the rinsing step (2) is preferably 5°C or
higher; and is preferably 60°C or lower, more preferably 50°C or lower, further preferably
40°C or lower, and even more preferably 30°C or lower.
- <9> The method of manufacturing a steel sheet according to any of <1> to <8>, wherein
the final rinsing treatment of the rinsing step (2) is a spray rinsing treatment.
- <10> The method of manufacturing a steel sheet according to any of <1> to <9>, wherein
the final rinsing treatment of the rinsing step (2) is performed after a rinsing treatment
with water.
- <11> The method of manufacturing a steel sheet according to any of <1> to <10>, wherein
the steel sheet is subjected to a treatment of holding a surface of the steel sheet
to be substantially perpendicular to the ground, that is, preferably 90 ± 10°, and
more preferably 90 ± 5° between the final rinsing treatment of the rinsing step (2)
and the drying step (3).
- <12> The method of manufacturing a steel sheet according to any of <1> to <11>, wherein
the cleaning step (1) and the rinsing step (2) are provided as a continuous line for
conveying a steel sheet, and the conveying speed of the steel sheet is 30 m/min or
more.
- <13> The method of manufacturing a steel sheet according to any of <1> to <12>, including
a cation concentration measurement step of measuring the cation concentration Pc of the inorganic salt in water for preparing the rinsing agent α and a rinsing agent
α preparation step of preparing the rinsing agent α used in the rinsing step (2) based
on a value measured in the cation concentration Pc measurement step.
- <14> The method of manufacturing a steel sheet according to any of <1> to <13>, wherein
the rinsing agent α preparation step includes a step of adjusting the cation concentration
Pc of water for preparing the rinsing agent α and a step of preparing the rinsing agent
α using the adjusted water.
- <15> The method of manufacturing a steel sheet according to any of <1> to <14>, wherein
the step of adjusting the cation concentration Pc of water for preparing the rinsing agent α is, when the cation concentration Pc of water is low, a step of adding the inorganic salt into the water to increase the
cation concentration Pc, or, when the cation concentration Pc of the water is high, a step of lowering the cation concentration Pc using water having a low cation concentration Pc such as deionized water.
- <16> The method of manufacturing a steel sheet according to any of <1> to <15>, wherein
the step of adjusting the cation concentration Pc of water for preparing the rinsing agent α is, when industrial water, deionized water
or the like having a low cation concentration Pc is used to prepare the rinsing agent α, is a step of preparing the rinsing agent
using the industrial water having a low cation concentration Pc, and adding the inorganic salt into the rinsing agent to adjust the cation concentration
Pc.
- <17> The method of manufacturing a steel sheet according to any of <1> to <16>, wherein
the inorganic salt is one or more types of compounds selected from an alkali metal
salt, an alkaline earth metal salt, and an aluminum salt.
- <18> The method of manufacturing a steel sheet according to any of <1> to <17>, wherein
the inorganic salt is one or more types of compounds selected from chlorides such
as sodium chloride, potassium chloride, calcium chloride, magnesium chloride, and
aluminum chloride; nitrates such as sodium nitrate; and carbonates such as sodium
carbonate.
- <19> A method of rinsing a steel sheet including a rinsing step (2) of rinsing a steel
sheet after being subjected to a cleaning step (1) after cold rolling, wherein the
rinsing step (2) includes one or more rinsing treatments, a rinsing agent α used in
a final rinsing treatment contains at least one type of component (a) selected from
compounds represented by the following formula (1) :
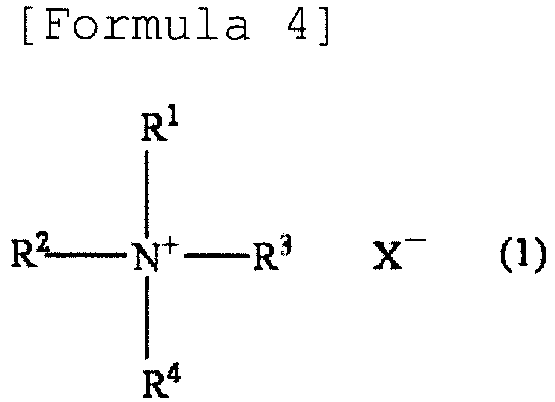
(wherein R1 represents a hydrocarbon group having 6 or more and 22 or less carbon atoms, R2 represents a hydrogen atom or a hydrocarbon group having 1 or more and 22 or less
carbon atoms, R3 and R4 are the same or different and each represent a hydrogen atom or a hydrocarbon group
having 1 or more and 3 or less carbon atoms, and X- represents an inorganic anion or an organic anion), the concentration of the component
(a) is 150 mg/kg or less in the rinsing agent α, the cation concentration Pc (mmol/kg) (Pc = E(A X i) (wherein A represents the concentration of a cation per component (mmol/kg),
and i represents a valence of the cation)) of an inorganic salt in the rinsing agent
α is 2.0 mmol/kg or more and 18.0 mmol/kg or less, and the sulfate ion concentration
in the rinsing agent α is 0.75 mmol/kg or less.
- <20> The method of rinsing a steel sheet according to <19>, wherein R1 is a straight chain or branched chain alkyl group or alkenyl group having 6 or more
carbon atoms, preferably 8 or more carbon atoms, more preferably 12 or more carbon
atoms, and further preferably 16 or more carbon atoms; and 22 or less carbon atoms,
and preferably 18 or less carbon atoms.
- <21> The method of rinsing a steel sheet according to <19> or <20>, wherein R2 is a hydrogen atom, preferably a straight chain or branched chain alkyl group or
alkenyl group, and more preferably a straight chain alkyl group or alkenyl group having
1 or more carbon atoms, preferably 6 or more carbon atoms, more preferably 8 or more
carbon atoms, further preferably 12 or more carbon atoms, and even more preferably
16 or more carbon atoms; and 22 or less carbon atoms, and preferably 18 or less carbon
atoms.
- <22> The method of rinsing a steel sheet according to any of <19> to <21>, wherein
R3 and R4 are the same or different; and preferably each represent a hydrogen atom or a hydrocarbon
group having 1 or more and 3 or less carbon atoms, and more preferably a hydrogen
atom.
- <23> The method of rinsing a steel sheet according to any of <19> to <22>, wherein
the concentration of the component (a) in the rinsing agent α is preferably 5 mg/kg
or more, more preferably 10 mg/kg or more, and further preferably 20 mg/kg or more;
and is 150 mg/kg or less, preferably 148 mg/kg or less, more preferably 145 mg/kg
or less, further preferably 120 mg/kg or less, and even more preferably 110 mg/kg
or less.
- <24> The method of rinsing a steel sheet according to any of <19> to <23>, wherein
the cation concentration is 2.0 mmol/kg or more, preferably 4.0 mmol/kg or more, more
preferably 5.0 mmol/kg or more, and further preferably 6.0 mmol/kg or more; and is
18.0 mmol/kg or less, preferably 17.0 mmol/kg or less, and more preferably 10.0 mmol/kg
or less.
- <25> The method of rinsing a steel sheet according to any of <19> to <24>, wherein
the sulfate ion concentration is 0.75 mmol/kg or less, preferably 0.70 mmol/kg or
less, more preferably 0.40 mmol/kg or less, further preferably 0.20 mmol/kg or less,
and even more preferably, the rinsing agent α contains no sulfate ion.
- <26> The method of rinsing a steel sheet according to any of <19> to <25>, wherein
the temperature of the rinsing agent α in the rinsing step (2) is preferably 5°C or
higher; and is preferably 60°C or lower, more preferably 50°C or lower, further preferably
40°C or lower, and even more preferably 30°C or lower.
- <27> The method of rinsing a steel sheet according to any of <19> to <26>, wherein
the final rinsing treatment of the rinsing step (2) is a spray rinsing treatment.
- <28> The method of rinsing a steel sheet according to any of <19> to <27>, wherein
the final rinsing treatment of the rinsing step (2) is performed after a rinsing treatment
with water.
- <29> The method of rinsing a steel sheet according to any of <19> to <28>, wherein
the cleaning step (1) and the rinsing step (2) are provided as a continuous line for
conveying a steel sheet, and the conveying speed of the steel sheet is 30 m/min or
more.
- <30> The method of rinsing a steel sheet according to any of <19> to <29>, wherein
the inorganic salt is one or more types of compounds selected from an alkali metal
salt, an alkaline earth metal salt, and an aluminum salt.
- <31> The method of rinsing a steel sheet according to any of <19> to <30>, wherein
the inorganic salt is one or more types of compounds selected from chlorides such
as sodium chloride, potassium chloride, calcium chloride, magnesium chloride, and
aluminum chloride; nitrates such as sodium nitrate; and carbonates such as sodium
carbonate.
- <32> Use of a composition as a rinsing agent used in the final rinsing treatment of
the rinsing step (2) in the method of manufacturing a steel sheet according to any
of <1> to <18> or the method of rinsing a steel sheet according to any of <19> to
<31>, wherein the composition contains at least one type of component (a) selected
from compounds represented by the following formula (1):
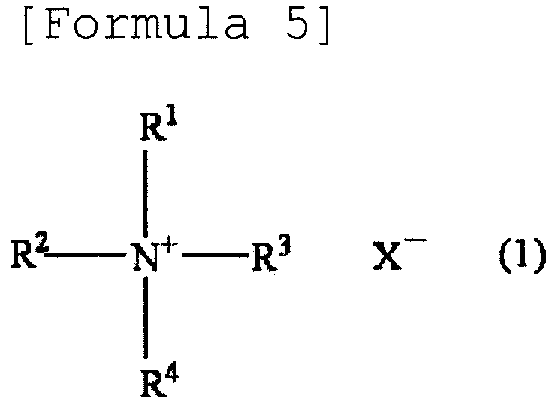
(wherein R1 represents a hydrocarbon group having 6 or more and 22 or less carbon atoms, R2 represents a hydrogen atom or a hydrocarbon group having 1 or more and 22 or less
carbon atoms, R3 and R4 are the same or different and each represent a hydrogen atom or a hydrocarbon group
having 1 or more and 3 or less carbon atoms, and X- represents an inorganic anion or an organic anion), and the concentration of the
component (a) is 150 mg/kg or less in the rinsing agent α, and the cation concentration
Pc (mmol/kg) (Pc = Σ(AXi) (wherein A represents the concentration of a cation per component (mmol/kg),
and i represents a valence of the cation)) of an inorganic salt in the rinsing agent
α is 2.0 mmol/kg or more and 18.0 mmol/kg or less, and the sulfate ion concentration
in the rinsing agent α is 0.75 mmol/kg or less.
- <33> The use according to <32>, wherein the composition is the rinsing agent α used
in the method of manufacturing a steel sheet according to any of <1> to <18> or the
method of rinsing a steel sheet according to any of <19> to <31>.
EXAMPLES
[0055] The present invention will be explained in more detail with reference to examples;
however, the present invention is not limited to these examples at all.
<Effect of timing of rinsing agent treatment>
[Preparation of detergent]
[0056] A solution obtained by mixing 2% by mass of sodium hydroxide, 0.2% by mass of sodium
gluconate, 0.1% by mass of sodium ethylenediamine tetraacetate, 0.023% by mass of
a nonionic surfactant [C
14H
29O(EO)
7(PO)
2(EO)
7H], 0.025% by mass of sodium polyacrylate, and 97.652% by mass of water was used as
a detergent A.
[Preparation of test water]
[0057] Test water was prepared and used in the experiment as a model of water containing
ions, such as industrial water used in a manufacturing plant of a steel sheet. One
or more types of inorganic salts selected from sodium chloride, calcium chloride (dihydrate),
magnesium chloride (hexahydrate), potassium chloride, sodium nitrate, aluminum chloride,
sodium carbonate, and sodium sulfate were added in ion exchange water, and the mixture
was stirred to completely dissolve the components to prepare test water types W-1
to W-19. The analytical values of the cation concentration and the sulfate ion concentration
for each test water type are shown in Table 1.
[0058] The cation concentration and the sulfate ion concentration were measured by the following
methods.
(For sodium ion and potassium ion)
[0059] The concentration was measured using an atomic absorption method.
[0060] Measurement conditions: "Spectra AA" manufactured by Varian Inc., wavelength: Na
589.0 nm, K 766.5 nm, frame acetylene (1.7 L/min) - air (15 L/min), burner height
7.5 mm, integration time 3 seconds (X 3 times average)
(For calcium ion, magnesium ion, and aluminum ion)
[0061] The concentration was measured using ICP emission spectrometry.
[0062] Measurement conditions: "Optima 5300DV" manufactured by PerkinElmer, Inc., wavelength:
Ca 317.933 nm, Mg 285.213 nm, integration time automatic (1 second to 5 seconds X
3 times average), high frequency output 1.3 kW, plasma gas 15 L/min, auxiliary gas
0.2 L/min, sheath gas 0.7 mL/min
(For sulfate ion)
[0063] The concentration was measured using ion chromatography.
[0064] Measurement conditions: "DX320" manufactured by Dionex Corporation, column "Ion Pac
AS11-HC" and "Ion Pac AG11-HC" (guard column) manufactured by Dionex Corporation,
eluent KOH, analysis by gradient elution, flow rate 1.5 mL/min, detector electric
conductivity, detector temperature 35°C, sample injection amount 25 µL

[Preparation of rinsing agents A to C and a]
[0065] The test water type W-3 (1 kg) was heated to 80°C, and 5.3 mg of an acid (acetic
acid) and 23.7 mg of an alkylamine (oleylamine) (29.0 mg as oleylamine acetate) were
added in this order as the component (a) and dissolved in the heated test water type
W-3 to prepare a rinsing agent A. Each of the rinsing agents B, C, and a was prepared
in the same manner as for the rinsing agent A except that the amount of the component
(a) added was changed to be the concentration shown in Table 2. The rinsing agents
A to C and a, whose temperatures were adjusted to 25°C, were used in the steps shown
in Table 3.
[Table 2]
|
|
Rinsing agent A |
Rinsing agent B |
Rinsing agent C |
Rinsing agent a |
Component (a) |
Oleylamine acetate |
mg/kg |
29 |
100 |
150 |
200 |
* Water used for dilution was the test water type W-3 (cation concentration: 8.09
mg/kg, sulfate ion concentration: 0 mg/kg) in all cases. |
<Examples A to C and Comparative Example a>
<Cleaning step: alkali cleaning>
[0066] A cold-rolled steel sheet (stain: iron powder and rolling oil) having a thickness
of 0.7 mm cut into a piece of 70 mm in length and 100 mm in width was immersed in
the detergent A in an alkali cleaning tank (immersion time 2 seconds), and pulled
out of the alkali cleaning tank.
<Cleaning step: electrolytic cleaning>
[0067] The steel sheet after being subjected to the alkali cleaning step was immersed in
the detergent A in an electrolytic cleaning tank, subjected to electrolytic cleaning
(electrolysis time: switching interval between the negative and positive electrodes
was 0.4 second for each of positive electrolysis and reverse electrolysis, current
density: 14 A/dm
2), and pulled out of the electrolytic cleaning tank.
<Cleaning step: brush cleaning>
[0068] The steel sheet after being subjected to the electrolytic cleaning step was subjected
to brush cleaning using a brush roll cleaning testing machine (manufactured by Showa
Industries Inc. , nylon brush, brush rotation speed: 500 rotations/min, brush rolling
draft: 1 mm, steel sheet conveying speed: 60 m/min) while being sprayed with the test
water type W-1 at a spray pressure of 0.2 MPa and a spray amount of 10 mL/sec using
a nozzle (spray nozzle "1/4MVE11578" manufactured by H. IKEUCHI & Co. , Ltd.).
<Rinsing step: immersion rinsing treatment>
[0069] The steel sheet after the brush cleaning step was immersed in the test water type
W-1 (immersion time: 2 seconds), and pulled out of a water-rinsing immersion tank.
<Rinsing step: spray rinsing treatment>
[0070] The steel sheet was sprayed with the rinsing agent shown in Table 3 at a spray pressure
of 0.2 MPa and a spray amount of 33 mL/sec for 3 seconds using a nozzle (spray nozzle
"1/4MJ100NBW" manufactured by H. IKEUCHI & Co., Ltd.). The surface of the steel sheet
treated with the rinsing agent was held perpendicular to the ground for 5 seconds.
<Drying step>
[0071] The steel sheet having been subjected to the rinsing step was placed in a dryer (Forced
Air Flow Oven "WFO-401W" manufactured by TOKYO RIKAKIKAI CO., LTD.) at 80°C to be
dried. The time required for the surface of the steel sheet to be dried was visually
measured. The results are shown in Table 3. In Table 3, a case in which the surface
was not dried in 1 minute is recorded as 1 minute or more, and a case in which water
was not observed at the stage of completion of the rinsing step is recorded as *.
<Comparative Examples b and A to C>
[0072] The same treatment as in Example A was performed except that the rinsing agent shown
in Table 3 was used instead of the test water type W-1 in the immersion rinsing step
and the test water type W-1 was used in the spray rinsing step.
<Comparative Examples D and E>
[0073] The same treatment as in Example A was performed except that the rinsing agent shown
in Table 3 was used instead of the test water type W-1 in the brush cleaning step
and the test water type W-1 was used in the spray rinsing step.
<Comparative Examples F and G>
[0074] The same treatment as in Example A was performed except that the rinsing agent shown
in Table 3 was used instead of the detergent A in the electrolytic cleaning step and
the test water type W-1 was used in the spray rinsing step.
<Comparative Examples H and I>
[0075] The same treatment as in Example A was performed except that the rinsing agent shown
in Table 3 was used instead of the detergent A in the alkali cleaning step and the
test water type W-1 was used in the spray rinsing step.
<Evaluation of drying properties of steel sheet>
[0076] In the drying step, the steel sheet having been subjected to the rinsing step was
placed in a dryer at 80°C, and the time required until the dryness of the surface
of the steel sheet had been visually observed was used as a drying time. The shorter
the drying time is, the better the drying properties are. The evaluation results are
shown in Table 3. An index showing the water wettability in terms of area (WB: water
break) was used to evaluate the water wettability of the surface of the steel sheet
after being subjected to the rinsing step. A picture of the steel sheet before the
drying step was taken, and a transparent film to which graph paper (minimum scale
1 mm) was copied was applied to the area of the part wetted with water to calculate
the WB. The smaller the value of WB is, the better the drying properties are. The
detergent, the rinsing agent, and the type of water used in each step, and the evaluation
results are shown in Table 3. Because no agent or water was used in the drying step,
the column of drying step is recorded as "-."
[Table 3]
|
Example A |
Example B |
Example C |
Comparative Example a |
Comparative Example A |
Comparative Example B |
Comparative Example C |
Comparative Example b |
Comarative Example D |
Comparative Example E |
Comparative Example F |
Comparative Example G |
Comparative Example H |
Comparative Example I |
Cleaning step |
Alkali cleaning |
Detergent A |
Detergent A |
Detergent A |
Detergent A |
Detergent A |
Detergent A |
Detergent A |
Detergent A |
Detergent A |
Detergent A |
Detergent A |
Detergent A |
Rinsing Agent A |
Rinsing Agent a |
Electrolytic cleaning |
Detergent A |
Detergent A |
Detergent A |
Detergent A |
Detergent A |
Detergent A |
Detergent A |
Detergent A |
Detergent A |
Detergent A |
Rinsing Agent A |
Rinsing Agent a |
Detergent A |
Detergent A |
Brush cleaning |
Test Water Type W-3 |
Test Water Type W-3 |
Water Type W-3 |
Test Water Type W-3 |
Test Water Type W-3 |
Test Water Type W-3 |
Test Water Type W-3 |
Test Water Type W-3 |
Rinsing Agent A |
Rinsing Agent a |
Test Water Type W-3 |
Test Water Type W-3 |
Test Water Type W-3 |
Test Water Type W-3 |
Rinsing step |
Immersion rinsing treatment |
Test Water Type W-3 |
Test Water Type W-3 |
Test Water Type W-3 |
Test Water Type W-3 |
Rinsing Agent A |
Rinsing Agent B |
Rinsing Agent C |
Rinsing Agent a |
Test Water Type W-3 |
Test Water Type W-3 |
Test Water Type W-3 |
Test Water Type W-3 |
Test Water Type W-3 |
Test Water Type W-3 |
Spray rinsing treatment (final spray before drying step) |
Rinsing Agent A |
Rinsing Agent B |
Rinsing Agent C |
Rinsing Agent a |
Test Water Type W-3 |
Test Water Type W-3 |
Test Water Type W-3 |
Test Water Type W-3 |
Test Water Type W-3 |
Test Water Type W-3 |
Test Water Type W-3 |
Test Water Type W-3 |
Test Water Type W-3 |
Test Water Type W-3 |
Drying step |
Drying step |
- |
- |
- |
- |
- |
- |
- |
- |
- |
- |
- |
- |
- |
- |
Drying properties of steel sheet |
Drying time in drying step |
26 seconds |
* |
* |
* |
1 minute or more |
1 minute or more |
55 seconds |
35 seconds |
1 minute or more |
1 minute or more |
1 minute or more |
1 minute or more |
1 minute or more |
1 minute or more |
WB after rinsing step |
27.5 |
0 |
0 |
0 |
100 |
100 |
80 |
40 |
100 |
100 |
100 |
100 |
100 |
100 |
* The surface of the steel sheet has already been dried before being placed in a dryer. |
[0077] From the results in Table 3, it was found that the water amount on the surface of
the steel sheet decreases and the drying properties are improved in the rinsing step
by the time when the surface of the steel sheet is dried and in the drying step since
the surface of the steel sheet is treated with the rinsing agent using water with
a specific cation concentration right before the drying step. It was also found that
the drying time in the drying step is correlated with the water break after the rinsing
step. The drying properties are improved even in the case where the surface of the
steel sheet is treated with water after being treated with the rinsing agent when
the concentration of the component (a) in the rinsing agent is 200 mg/kg (Comparative
Examples a and b). It was also found that the drying properties are improved even
when the content of the component (a) is reduced if the surface of the steel sheet
is treated with the rinsing agent prepared using a specific cation concentration right
before the drying step (Examples A to C and Comparative Examples A to C).
<Effect of cation concentration>
<Examples A-1 to A-14 and Comparative Examples 1 to 9>
[0078] Each rinsing agent was prepared in the same manner as in Example A to evaluate the
drying properties by using the water break after the rinsing step expect that each
of the test water types W-1 to W-23 was used. The evaluation results are shown in
Tables 4 and 5.
[Table 4]
|
|
Examples |
A-1 |
A-2 |
A-3 |
A-4 |
A-5 |
A-6 |
A-7 |
A-8 |
A-9 |
A-10 |
A-11 |
A-12 |
A-13 |
A-14 |
Component (a) |
Acetic acid salt of oleylamine |
mg/kg |
29 |
29 |
29 |
29 |
29 |
29 |
29 |
29 |
29 |
29 |
29 |
29 |
29 |
29 |
Test water |
|
|
W-1 |
W-2 |
W-3 |
W-4 |
W-5 |
W-6 |
W-7 |
W-8 |
W-9 |
W-10 |
W-20 |
W-21 |
W-22 |
W-23 |
Cation concentration |
mmol/kg |
2.07 |
5.17 |
8.09 |
17.22 |
8.80 |
9.50 |
4.02 |
6.04 |
8.06 |
16.15 |
6.12 |
6.35 |
6.16 |
6.52 |
Sulfate ion concentration |
mmol/kg |
|
|
|
|
0.35 |
0.70 |
|
|
|
|
|
|
|
|
Drying properties of steel sheet |
WB after rinsing step |
|
48.3 |
20 |
35 |
50 |
40 |
50 |
35 |
10 |
15 |
45 |
10 |
10 |
10 |
10 |
[Table 5]
|
|
Comparative Examples |
1 |
2 |
3 |
4 |
5 |
6 |
7 |
8 |
9 |
Component (a) |
Oleylamine acetate |
mg/kg |
29 |
29 |
29 |
29 |
29 |
29 |
29 |
29 |
29 |
Test water |
|
|
W-11 |
W-12 |
W-13 |
W-14 |
W-15 |
W-16 |
W-17 |
W-18 |
W-19 |
Cation concentration |
mmol/kg |
0.02 |
0.17 |
20.14 |
50.28 |
9.78 |
11.47 |
0.50 |
1.72 |
22.06 |
Sulfate ion concentration |
mmol/kg |
|
|
|
|
0.84 |
1.69 |
|
|
|
Drying properties of steel sheet |
WB after rinsing step |
|
90 |
70 |
83.3 |
100 |
70 |
100 |
97.5 |
90 |
100 |
[0079] From the results in Tables 4 and 5, it was found that the drying properties of the
steel sheet are improved when the cation concentration of the inorganic salt in the
rinsing agent is within the specific range.
<Effect of acid and acid salt of alkylamine>
<Examples 1 to 7>
[0080] The rinsing agent was prepared in the same manner as in Example A expect that the
acid salt was compounded so that the concentration and the composition described in
Table 6 were achieved to evaluate the drying properties by using the water break after
the rinsing step. The evaluation results are shown in Table 6.
[Table 6]
|
|
Examples |
1 |
2 |
3 |
4 |
5 |
6 |
7 |
Component (a) |
Hexylamine acetate |
mg/kg |
100 |
|
|
|
|
|
|
Octylamine acetate |
mg/kg |
|
100 |
|
|
|
|
|
Laurylamine hydrochloride |
mg/kg |
|
|
100 |
|
|
|
|
Hexadecylamine acetate |
mg/kg |
|
|
|
100 |
|
|
|
Oleylamine acetate |
mg/kg |
|
|
|
|
100 |
|
|
Stearylamine acetate |
mg/kg |
|
|
|
|
|
100 |
|
Behenylamine acetate |
mg/kg |
|
|
|
|
|
|
100 |
Drying properties of steel sheet |
WB after rinsing Step |
|
60 |
50 |
20 |
0 |
0 |
20 |
50 |
* Water used for dilution was the text water type W-3 (cation concentration: 8.09
mg/kg, sulfate ion concentration: 0 mg/kg) in all cases. |
[0081] From the results in Table 6, it was found that the drying properties of the steel
sheet are improved when an acid salt of a specific amine is the component (a).