[0001] La présente invention est relative à un alliage austénitique fer-nickel chrome-cuivre,
plus particulièrement destinée à la fabrication de dispositifs électromagnétiques.
[0002] Les alliages fer-nickel et fer-nickel-chrome riches en nickel sont connus depuis
longtemps et utilisés dans de nombreuses applications du génie électrique (électronique,
électrotechnique), de la visualisation, du transport d'énergie, de la régulation thermique
ou de la sécurité électrique, grâce à leurs propriétés physiques originales et variées.
[0003] Ainsi, ils présentent des dilatabilités thermiques entre 20 et 100°C comprises entre
2 et 13.10
-6/°C selon leur composition, ce qui est une caractéristique exceptionnelle pour un
matériau ductile, propre à quelques rares matériaux.
[0004] Ils présentent également une bonne à très bonne tenue à la corrosion aqueuse, d'autant
meilleure que le pourcentage en nickel, voire en chrome, augmente.
[0005] On observe également une grande aptitude à la mise en forme, liée à la structure
austénitique monophasée, permettant laminage aisé à très faibles épaisseurs, découpe,
poinçonnage, étampage, emboutissage à grande vitesse.
[0006] Leur comportement ferromagnétique, caractérisé par l'existence d'un point de Curie
T
c (température de disparition du ferromagnétisme) est également remarquable ainsi que
leurs propriétés magnétiques (perméabilité relative µ
r, champ coercitif H
c, pertes magnétiques P).
[0007] Celles-ci sont très bonnes, allant dans le sens d'une faible consommation d'énergie
pour aimanter ces alliages. Ainsi ces alliages fer-nickel et fer-nickel-chrome sont
utilisés depuis longtemps dans les applications électromagnétiques où il est impératif,
soit d'économiser de l'énergie (moteurs électriques horlogers, relais haute sensibilité
de disjoncteur différentiel, moteurs à grande vitesse et faible échauffement, ...),
soit de disposer d'un hystérésis très réduit pour limiter significativement la dispersion
de mesure des capteurs magnétiques (transformateur de courant, capteur de courant
continu, résolveurs et synchro-résolveurs) ou les pertes hystérétiques (transformateur
de mesure, de modem ...), soit encore d'offrir une canalisation très privilégiée des
flux magnétiques comme dans certaines culasses magnétiques d'actionneur à grande dynamique
(injecteur électromagnétique d'essence par exemple), dans les moteur-roue, dans les
blindages magnétiques passifs à forte atténuation.
[0008] Les alliages fer-nickel, dont le champ coercitif est généralement inférieur à 125
mOe, permettent ainsi un saut réel de consommation d'énergie des systèmes électriques,
par rapport aux matériaux de type fer-silicium traditionnellement utilisés, puisque
ces derniers atteignent des champs coercitifs de l'ordre de 190 mOe suivant une seule
direction ce qui n'intéresse que peu d'application, soit plus généralement valent
de 500 à 1250 mOe lorsque l'application a besoin de véhiculer le flux magnétique dans
différentes directions du matériau (moteurs, génératrices, etc.).
US2005161123 décrit un alliage magnétique doux dont la composition comprend, en % en poids, Ni≤34%,
0%≤Co≤4%, 0%≤Cu≤4%, 1%≤Cr, 0%≤Mo≤8%, 0% ≤Nb≤1%, 0%≤Mn≤2%, 0%≤V≤5%, 0%≤W≤5%, 0%≤Si≤4%,
0%≤Al≤4%, 0% ≤C≤0.4%, éventuellement, un ou plusieurs éléments pris parmi le magnésium
et le calcium en des teneurs telles que leur somme reste inférieure à 0.1 %, le reste
étant du fer et des impuretés résultant de l'élaboration, la composition chimique
satisfaisant en outre les relations: 180,5≤6 x Ni-2.5 x (Cr + Mo +V +W + Si + Al)
+ 4 x (Co + Cu) ≤ 197,5 et Co + Cu ≤ 4% et son utilisation pour la fabrication d'un
stator de moteur d'horlogerie. Il existe cependant un besoin pour l'amélioration de
certaines propriétés de ces alliages fer-nickel, comme celle relatives à la résistance
à la corrosion en milieux aqueux acide et à la corrosion en brouillard salin qui ne
sont pas toujours suffisantes dans certains environnements agressifs.
[0009] En outre, la fabrication de feuilles de ces alliages comprend des traitements thermiques
industriels dans des atmosphères souvent peu pures, ce qui entraîne la formation d'une
couche oxydée en surface qui protège le métal de base contre une oxydation plus importante.
Mais, cette couche de surface est très peu adhérente et très peu solide mécaniquement,
ce qui rend son action protectrice peu efficace.
[0010] Le but de la présente invention est de remédier à ces inconvénients en proposant
une composition d'alliage présentant une résistance à la corrosion aqueuse acide et
à la corrosion en brouillard salin améliorée, apte à la formation d'une couche d'oxydation
de surface solide et adhérente, qui puisse être employée pour de nombreuses applications
et qui présente un coût réduit.
[0011] A cet effet, l'invention a pour premier objet un alliage austénitique fer-nickel-chrome-cuivre
dont la composition comprend en % en poids :

le reste étant du fer et des impuretés résultant de l'élaboration, les pourcentages
en nickel, chrome, cuivre, cobalt étant tels que l'alliage satisfait en outre les
conditions suivantes :

et la teneur en manganèse respectant en outre les conditions suivantes :
- si Eq3 ≥ 205, Mn ≤ Ni - 27,5 + Cu - Cr
- si 180,5 ≤ Eq3 ≤ 205, Mn ≤ 4%
- si Eq3 ≤ 180,5, Mn ≤ 2%
avec

[0012] La solution proposée est une famille d'alliages Fe-Ni-Cr-Cu austénitiques et ferromagnétiques
se prêtant à une élaboration industrielle économique, par four à arc ou à induction,
ayant peu d'éléments onéreux et offrant des performances élevées ou originales pour
plusieurs domaines d'applications qui vont être détaillés par la suite. Il n'a jamais
été découvert jusqu'à maintenant qu'une famille d'alliage pouvait satisfaire toutes
ces propriétés. De plus l'utilisation d'un même alliage pour applications très différentes
(par exemple en satisfaisant à la fois des besoins en dilatabilité réduite, en tenue
à la corrosion, en magnétisme et point de Curie) permet d'en produire un tonnage plus
important, d'avoir une plus grande expérience de production industrielle et donc un
alliage plus fiable en termes de reproductibilité des propriétés.
[0013] En outre, les présents inventeurs ont constaté l'aptitude du silicium, du chrome
et du cuivre, à renforcer mécaniquement et chimiquement la couche protectrice oxydée
de surface et à la rendre très adhérente. Ainsi la couche oxydée devient très stable
dans le temps du traitement thermique ou de l'utilisation en atmosphère ambiante oxydante,
très stable chimiquement vis à vis de produits chimiques extérieurs et très stable
mécaniquement vis à vis des chocs et frottements entre pièces métalliques lors du
cycle industriel de production.
[0014] En outre, cet oxyde très stable présente généralement une épaisseur fine de quelques
microns, selon le cycle de traitement thermique utilisé. Cette faible épaisseur d'oxyde
est particulièrement intéressante en horlogerie, car elle limite et calibre en même
temps l'entrefer entre stator et noyau magnétique de bobine, entrainant respectivement
à la fois une limitation de l'énergie consommée par la pile de la montre et une réduction
de la dispersion industrielle des moteurs horlogers.
[0015] L'invention va maintenant être décrite plus en détail mais de façon non limitative
et illustrée par des exemples.
[0016] L'alliage selon l'invention comprend en % poids, les teneurs définies ci-dessous.
[0017] La teneur en nickel est limitée à 36%, de préférence à 35% en poids et de façon plus
particulièrement préférée à 34%, voire à 29%. Une telle limitation permet de limiter
fortement le coût de la nuance. Elle permet également d'avoir une résistivité électrique
d'au moins 70µΩ.cm, voire d'au moins 80µΩ.cm si la teneur en nickel est inférieure
à 34%, ce qui est un des éléments d'une bonne dynamique d'aimantation (les deux autres
étant une faible épaisseur de métal et un faible champ coercitif). Pour certaines
applications, telle que la fabrication de bilames, on préfère maintenir la teneur
en nickel supérieure ou égale à 30% afin de garantir un point de Curie élevé. La teneur
en nickel est au minimum de 24% afin de garantir l'obtention d'une structure austénitique
dans l'ensemble du domaine de composition selon l'invention.
[0018] La teneur en chrome est supérieure ou égale à 0,02% car il faut un minimum de chrome
pour avoir les propriétés de tenue à la corrosion demandées. Par ailleurs, lorsque
la teneur en nickel est comprise entre 32,5 et 36%, la teneur en chrome est limitée
à 7,5%, afin de limiter le coût de l'ensemble des éléments autres que le fer et le
silicium.
[0019] Ces caractéristiques permettent d'améliorer la tenue à la corrosion aqueuse acide,
à la corrosion atmosphérique et à l'oxydation à chaud de la nuance, car on observe
la formation d'un oxyde superficiel très stable chimiquement, qui est en outre très
adhérent au métal. En outre, l'ajout de ces éléments ne dégrade pas significativement
les autres propriétés d'usage de l'alliage, telles que le point de Curie ou l'aimantation
à saturation.
[0020] La teneur en cuivre est supérieure ou égale à 0,1% et est limitée à une teneur de
15% et de préférence à une teneur de 10% (afin de limiter le coût de l'ensemble des
éléments autres que le fer et le silicium), avec substitution possible par du cobalt.
Outre son impact sur la résistance à la corrosion de la nuance, le cuivre améliore
sensiblement l'adhérence de la couche oxydée se formant à chaud à la surface de l'alliage.
[0021] On préfère que la nuance ne contienne pas de cobalt en raison de son coût et pour
cette même raison, si le cobalt est présent, il est nécessaire que sa teneur soit
inférieure à celle du cuivre. En outre, lorsque le chrome est présent à raison de
plus de 7,5%, le cobalt doit être limité à 4% au maximum, et de préférence à 2%, car
on veut limiter le coût de l'ensemble des éléments autres que le fer et le silicium
[0022] L'ajout d'au moins 0,02% de silicium permet d'améliorer de façon significative la
tenue à l'usure mécanique de la couche d'oxyde de surface. En outre, le silicium peut
être ajouté à hauteur de 2% à l'alliage selon l'invention pour participer à sa désoxydation
au four à arc, sans nuire aux autres propriétés de l'alliage.
[0023] Par ailleurs, les présents inventeurs ont constaté que les teneurs en nickel, chrome
et cuivre devaient respecter la relation suivante :

[0024] En effet, le respect de cette condition permet de garantir le caractère austénitique
de l'alliage, sans lequel aucune des propriétés d'usage de l'alliage ne seraient conforme
aux buts recherchés et qui empêcherait également d'avoir une bonne aptitude à la mise
en forme.
[0025] La teneur en manganèse est comprise entre 0,01 et 6% en poids, et de préférence entre
0,02 et 6% en poids, ce qui permet d'obtenir un alliage se transformant bien à chaud
grâce à la formation de sulfures, sans dégrader les propriétés d'usage de l'alliage,
telles que le point de Curie ou l'aimantation à saturation. Afin de maintenir des
valeurs d'induction à saturation Bs supérieures à 4000 G, on préfère que la teneur
en manganèse reste inférieure à 5 %. De façon plus particulièrement préférée, la teneur
en manganèse est comprise entre 0,1 et 1% en poids. De plus, en présence de chrome,
son effet sur l'induction à saturation est aggravé, d'où la nécessité de le limiter
comme suit :

avec

et

[0026] L'alliage peut également comprendre des éléments d'addition tels que le carbone,
le titane, l'aluminium, le molybdène, le vanadium, le tungstène, le niobium, le zirconium,
l'étain, le bore, le soufre, le sélénium, l'antimoine, le calcium ou le magnésium.
[0027] Le carbone peut être ajouté à l'alliage à hauteur de 2% et de préférence à hauteur
de 1% pour durcir l'alliage par formation de carbures. Cependant, lorsque l'application
de l'alliage nécessite un champ coercitif Hc de moins de 125 mOe, la teneur en carbone
sera maintenue inférieure à 0,1% après élaboration-solidification en lingot ou brame
car sa présence dégrade fortement cette caractéristique. De plus pour atteindre cette
caractéristique (Hc) et la conserver dans le temps, un traitement thermique de décarburation
pourra être appliqué à la tôle mince dans l'état final afin de diminuer significativement
le pourcentage de carbone à moins de 100ppm, et de préférence à moins de 50ppm.
[0028] Le titane et l'aluminium peuvent être ajoutés à l'alliage à hauteur cumulée de 3%
afin de durcir la nuance par précipitation de composés Ni
3(Ti,Al). L'ajout d'aluminium peut également améliorer l'aptitude à la soudabilité
de l'alliage sur du verre. Cependant, lors des traitements thermiques sous gaz réducteur,
on souhaite utiliser l'ammoniaque craqué ou un mélange préalable d'azote + hydrogène.
Hors, l'azote se combine dés les recuits à basse température en composés de type AIN
ou TiN, et il faut donc réduire la teneur en résiduels Al, Ti au plus bas pour assurer
la compatibilité entre hautes performances magnétiques et traitement thermique sous
gaz comportant de l'azote. Ce point s'applique en particulier à toute application
nécessitant des hautes performances magnétiques et impliquant des recuits sous atmosphère
contenant de l'azote. Dans ce cas de figure, on limite la teneur cumulée en titane
et aluminium à 30 ppm et de préférence à 20 ppm.
[0029] Le molybdène peut être ajouté à hauteur de 8 % pour améliorer à la fois la résistance
mécanique et la résistance à l'oxydation à chaud de l'alliage. On se limitera de préférence
à 4% pour limiter le coût des éléments autres que Fe et Si.
[0030] Le vanadium et le tungstène peuvent être ajoutés à l'alliage à hauteur cumulée de
6%, afin d'améliorer sa ténacité, et sont ajoutés de préférence à moins de 3% afin
de limiter le coût de l'ensemble des éléments autres que le fer et le silicium.
[0031] Le niobium et le zirconium peuvent être ajoutés à l'alliage à hauteur cumulée de
0,5% afin d'améliorer sa résistance mécanique.
[0032] L'étain peut être ajouté à l'alliage à hauteur de 1% en substitution partielle du
chrome.
[0033] Le bore peut être ajouté à l'alliage selon l'invention en des quantités allant de
2 à 60 ppm, et de préférence de 5 à 10 ppm, afin d'améliorer sa découpabilité par
formation de nitrures de bore. En dessous de cette fourchette, son effet n'est plus
observable, tandis que cet effet sature au-dessus de 60ppm.
[0034] Le soufre est une impureté présente dans les ferrailles utilisées pour l'élaboration
de l'alliage, mais peut également être ajoutée en des quantités allant de 5 à 80 ppm,
et de préférence de 10 à 30 ppm afin d'améliorer également la découpabilité et l'usinabilité
de l'alliage par formation de sulfure de manganèse. On pourra substituer tout ou partie
du soufre par l'ajout de sélénium et/ou d'antimoine.
[0035] Lorsqu'on les ajoute en tant qu'additifs de découpabilité, les teneurs cumulées en
soufre et en bore sont de préférence comprises entre 5 et 60 ppm et de préférence
on associe ces deux éléments dans le respect de leur plage préférée respective.
[0036] De la même façon, on peut ajouter à l'alliage selon l'invention du calcium et du
magnésium à hauteur cumulée de 4 à 200 ppm pour améliorer la découpabilité par formation
de composés de type MgO ou CaO, la large plage de Ca+Mg permettant de régler le compromis
entre l'aptitude à la découpe et les performances magnétiques, puisque contrairement
à certains sulfures (MnS...) et nitrures (AlN....) un recuit réducteur à haute température
ne pourra pas les dissoudre en fin de fabrication.
[0037] Le reste de la composition est constitué de fer et d'impuretés inévitables issues
de l'élaboration. Parmi celles-ci, on citera plus particulièrement le phosphore, l'azote
et l'oxygène qui sont contenus à hauteur maximum de 500ppm. Pour certaines applications,
il est nécessaire de limiter les teneurs cumulées en oxygène et azote à 100 ppm afin
de maintenir le champ coercitif dans les limites souhaitées.
[0038] D'une façon générale, l'alliage selon l'invention peut être élaboré et fabriqué sous
forme de bande laminée à chaud, puis à froid avant d'être recuite puis éventuellement
écrouie. On peut également s'arrêter au stade de la bande laminée à chaud.
[0039] L'alliage selon l'invention peut également être utilisé sous forme de produits massifs,
forgés ou non, de barres ou de fils issus d'un laminage à chaud éventuellement complété
d'un tréfilage.
[0040] Les bandes ou pièce en alliage pourront être obtenues par tout procédé adapté, tel
que l'homme du métier sait le faire.
[0041] Ainsi, l'alliage selon l'invention sera de préférence fondu au four à induction sous
vide en lingots. Les lingots pourront être forgés entre 1100 et 1300°C, puis laminés
à chaud jusqu'à une épaisseur de 2,5mm, entre 1000 et 1200°C. On pourra ensuite décaper
chimiquement la bande à chaud puis la laminer à froid jusqu'à l'épaisseur requise.
[0042] Lorsque l'on souhaite développer une structure cristallographique particulière, de
type {100}<001>, on procède à un laminage à froid avec un taux d'écrouissage global
de 90 à 99% en plusieurs passes sans recuit intermédiaire entre chaque passe.
[0043] A l'issue du laminage à froid, on pratique de préférence un recuit entre 800 et 1100°C
durant 1 heure pour adoucir la bande l'alliage et faciliter ainsi sa découpe ou sa
mise en forme ultérieure. Mais il peut être encore plus avantageux de découper par
poinçonnage, estampage à grande vitesse dans l'état écroui en fin de laminage à froid,
surtout si le métal a été optimisé vis-à-vis de cette mise en oeuvre par les éléments
cités précédemment tels que B, S, Ca, Mg, Se...
[0044] Après découpe ou mise en forme, les pièces obtenues pourront avantageusement être
recuites à 1100°C pendant 3 heures sous H2 purifié (point de rosée<-70°C) afin, notamment,
d'optimiser les propriétés magnétiques de l'alliage. En revanche, ce recuit peut être
tout à fait inutile si on recherche particulièrement des propriétés de dilatation
ou de point de Curie ou de résistance à la corrosion.
[0045] Comme on l'a vu précédemment, les alliages selon l'invention peuvent être produits
en recuit industriel sous tout type de gaz.
[0046] Les alliages selon l'invention trouvent des applications potentielles dans de nombreux
domaines. On définit ainsi des domaines de composition préférés, regroupant des alliages
plus particulièrement adaptés à une application donnée, qui vont être décrits en détail
ci-après.
Dispositifs électromagnétiques à autorégulation de température
[0047] Dans un premier mode de réalisation préféré, les pourcentages en nickel, chrome,
cuivre, cobalt, molybdène, manganèse, vanadium, tungstène, silicium et aluminium sont
tels que l'alliage satisfait en outre les conditions suivantes :

et
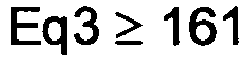
et

et

et

et

et
[0048] Cette composition est plus particulièrement adaptée à la fabrication de dispositifs
électromagnétiques à autorégulation de température.
[0049] Un matériau ferromagnétique doux présente une perméabilité µ très supérieure à la
perméabilité du vide. Lorsque ce matériau est soumis à une excitation magnétique variable
dans le temps, il génère beaucoup plus de pertes magnétiques avant d'atteindre une
valeur caractéristique appelée point de Curie T
c que lorsqu'il dépasse cette température au-delà de laquelle le matériau n'est plus
ferromagnétique. De plus, l'aimantation à saturation du matériau, ses pertes magnétiques
et donc sa génération de puissance thermique décroissent au fur et à mesure que l'on
se rapproche de T
c.
[0050] L'autorégulation en température est alors réalisée autour du point de Curie de l'alliage
si les pertes magnétiques résiduelles propres à tout conducteur non magnétique sont
évacuées, c'est à dire que le flux de chaleur partant de l'alliage soit supérieur
au flux de chaleur générée en pertes magnétiques. Pour cela, on a parfois besoin d'accoler
à l'alliage selon l'invention un matériau bien meilleur conducteur thermique comme
l'aluminium ou le cuivre, chargé d'évacuer les pertes paramagnétiques et permettant,
notamment, l'autorégulation de température dans les applications de cuisson par induction
où la chaleur d'un récipient chauffé malencontreusement à vide ne s'évacuerait sinon
que par convection naturelle.
[0051] Cette technique a été notamment décrite dans le brevet d'application
EP 1 455 622, où l'autorégulation de température est obtenue en associant des alliages à bas T
c entre 30 et 350°C et au moins 32,5%de nickel, avec un diffuseur thermique en aluminium
permettant d'évacuer les pertes magnétiques de l'alliage Fe-Ni-Cr lorsqu'il atteint
Tc.
[0052] La principale propriété d'usage reste donc le point de Curie fonctionnel qui est
recherché entre 30°C et 400°C pour la cuisson par induction, le chauffage industriel
par induction par exemple de buses d'injecteurs, de moules de composite, le réchauffage
d'aliments de boissons, nourritures, produits médicaux, de sang et constituants, de
matières molles ou organiques etc...
[0053] On recherche aussi une tenue minimale à la corrosion et à l'oxydation puisque les
alliages sont souvent au contact de différents milieux et/ou constituants dans des
atmosphères industrielles. On demande ainsi une bonne stabilité chimique de l'alliage
se traduisant par une bonne tenue à la corrosion aqueuse, une bonne tenue à la corrosion
en brouillard salin et une bonne stabilité mécanique (adhésion + tenue à l'usure)
de la couche oxydée de surface en atmosphère chaude et oxydante.
[0054] Par ailleurs, on recherche également de façon préférentielle, des alliages présentant
un coefficient de dilatation entre 20 et 100°C supérieur à 4.10
-6/°C, voire supérieure à 7.10
-6/°C. Cette caractéristique permet notamment de réduire l'éventuel effet bilame pouvant
exister entre l'alliage et une couche de conducteur étroitement associé à l'alliage
par placage, grippage, soudage, dépôt plasma, etc....
[0055] En revanche, il n'y a pas d'exigence particulière sur les propriétés magnétiques
et le champ coercitif peut être très dégradé. On peut donc ajouter des proportions
importantes de carbone de l'ordre de 2% au maximum et de préférence moins de 1%. Il
est en effet connu depuis longtemps que le carbone en grande quantité met le réseau
cristallin sous contrainte forte et accroit ainsi l'interaction d'échange entre moments
magnétiques et donc augmente le point de Curie, ce qui permet de diminuer encore le
pourcentage de nickel pour conserver le même niveau de point de Curie et donc la même
température d'autorégulation.
[0056] L'application d'autorégulation de température n'est cependant pas restreinte à la
cuisson par induction des liquides et solides alimentaires, mais s'adresse plus généralement
à tout système domestique ou industriel utilisant un inducteur électromagnétique et
au moins une pièce active thermiquement sur des éléments de passage qui doivent être
momentanément chauffés sans excéder certaine température critique.
[0057] A titre d'exemple, on citera l'injection de fluides plus ou moins visqueux, alimentaires
ou non, pour accélérer la production de portion de matière préchauffée pour dégustation,
ou aussi comme pré-requis avant une autre opération industrielle telle que le collage
thermo-activé, la polymérisation de plastiques, composites etc....
[0058] On citera également le chauffage rapide et autorégulé de surface de moules de forme
pour composites thermodurcissables (besoin de réguler la température entre 200 et
350°C selon le type de composite) ou thermoplastiques (besoin de réguler la température
entre 150 et 250°C selon le type de composite).
[0059] On citera encore le chauffage autorégulé d'une aiguille ou insert en alliage bas
Tc bio-compatibilisé par un revêtement, au centre d'une tumeur maligne (dont les cellules
craignent plus la chaleur que les cellules normales).
[0060] On citera enfin le chauffage autorégulé d'une matrice d'extrusion, de filage, etc.
permettant de limiter le gradient thermique dans la pièce mise en oeuvre au travers
de la filière, limitant ainsi contrainte interne, fragilisation de surface, gradient
de propriétés, inhomogénéités structurales....
[0061] Les alliages selon l'invention tels que définis ci-dessus permettent d'atteindre
toutes les propriétés requises.
[0062] En particulier, les inventeurs ont constaté que le respect des valeurs limites des
équations 2 à 7 permet de garantir aussi bien un niveau d'induction à saturation à
20°C supérieur à 0, et même supérieur à 1000G permettant d'émettre de la chaleur par
pertes magnétiques, qu'un point de Curie Tc ≥ 30°C.
[0063] D'une façon plus générale, et quelle que soit l'application selon l'invention, on
constate qu'en adaptant la composition de l'alliage, on peut modifier la valeur de
chacune des équations 2 à 7, de façon à être conforme à la valeur limite imposée dans
une application particulière, et ainsi régler le niveau d'induction, ainsi que la
valeur de Tc de l'alliage en question.
Dispositifs à autorégulation de flux magnétique
[0065] Cette composition est plus particulièrement adaptée à la fabrication de dispositifs
à autorégulation de flux magnétique.
[0066] La régulation de flux magnétique d'un dispositif en fonction de la température ambiante
s'appuie sur la décroissance de l'aimantation à saturation avec la température au
voisinage du point de Curie, avec un taux de décroissance sensiblement constant et
assez fort. Ceci permet par un système à dérivation de flux de compenser exactement
la décroissance d'aimantation des aimants en jouant sur les rapports de section de
passage de flux magnétique entre aimant et alliage de compensation et ainsi de fournir
toujours le même flux magnétique dans une plage donnée de température.
[0067] Cette autorégulation de flux magnétique est réalisée le plus couramment autour de
la température ambiante, et en particulier entre 30°C et +100°C. On a donc besoin
de différents alliages qui auront un point de Curie Tc à l'intérieur de cette plage
de température.
[0068] En revanche, il n'y a pas d'exigence particulière sur les propriétés magnétiques
et dans ce cas d'application le champ coercitif peut-être très dégradé par rapport
à la limite de 10A/m correspondant au potentiel de performance des nouveaux alliages
selon l'invention. Comme précédemment, on pourra ajouter jusqu'à 2% de carbone et
de préférence jusqu'à 1% de carbone.
Dispositifs à dilatation contrôlée
[0070] Cette composition est plus particulièrement adaptée à la fabrication de dispositifs
à dilatation contrôlée.
[0071] On entend par alliage à dilatation contrôlée, des alliages présentant des coefficients
de dilatation plus faibles que les autres alliages métalliques (α
20-100 > 10.10
-6/°C), c'est à dire typiquement, α
20-100 < 10.10
-6/°C ou α
20-300 <13.10
-6/°C.
[0072] Ils trouvent un usage dans les applications nécessitant de conserver une géométrie
et des cotes précises de certains de ces composants en fonction de la température,
ou bien nécessitant une forte compatibilité en dilatabilité thermique entre un de
ces matériaux actifs et un alliage à dilatation contrôlée, apportant d'autres fonctions
(conducteur de courant par exemple, ou encore support mécanique). Ces applications
ont en commun de faire subir aux composants des variations de température dans une
plage allant de 20 à 450°C.
[0073] Pour certaines applications, il est ainsi nécessaire d'être étroitement compatible
en dilatation thermique avec un autre matériau actif dans l'application (silicium,
germanium, AsGa, SiC, verres sodiques, autres verres, inox à faibles dilatations,
céramiques etc....). Cette étroite compatibilité entre un autre matériau et l'alliage
permet à l'ensemble de ces deux matériaux liés par plaquage, soudage, collage, brasage,
grippage... de se dilater ensemble sans modifier leur forme, les cotes évoluant uniquement
de façon prévisible en conséquence de la loi générale de dilatation thermique. Un
autre avantage de cette étroite compatibilité de dilatation est qu'il y a très peu
de contraintes internes d'origine thermique entre les deux matériaux ce qui rend la
fatigue thermique en fonctionnement du bi-matériau négligeable, prolongeant ainsi
considérablement sa durée de vie.
[0074] Une de ces applications est la connectique de circuit intégré (leadframe) où l'alliage
est lié étroitement au semi-conducteur pour lui amener le courant électrique. Il est
ainsi nécessaire d'employer un alliage à dilatation contrôlée, pour fortement limiter
la fatigue thermique et la détérioration prématurée de l'interface.
[0075] Une autre application est le pour support mécanique à faible dilatation dans une
plage de température prédéfinie. Par exemple, un vidéoprojecteur utilise une multitude
de petits miroirs dont la position doit bouger le moins possible avec la mise en chauffe
de l'appareil qui peut amener le support des miroirs jusqu'à 400-450°C localement.
[0076] Une autre application est la fabrication de supports et boitiers de transistor, semi-conducteurs
de circuit de l'optoélectronique (AsGa par ex), tubes de RX, traversées étanches de
verres ...
[0077] Dans toutes ces applications, l'alliage à dilatation contrôlée est étroitement lié
à un semi-conducteur ou à un verre ou à une céramique, et les besoins en dilatabilité
peuvent aller de 4 à 5.10
-6/°C. à 11.10
-6/°C. On peut citer pour exemple le support/cerclage des grandes vitres de toit automobiles
(ouvrantes ou non), où l'alliage doit impérativement se dilater avec la colle qui
les lie de la même façon que la dalle de verre. On peut citer aussi le support basse
déformation des céramiques comme les PZT piézoélectriques utilisées comme actionneur
en injection de carburant auto.
[0078] Il est également possible que l'alliage à dilatation contrôlée n'apporte que cette
seule fonction dans l'application, tout en étant apte à être mis en forme de façon
précise par pliage, emboutissage, estampage, fluotournage, usinage mécanique ou chimique
(gravure), soudage, etc..: Dans ce cas, la pièce mécanique aux cotes précises réalisées
dans l'alliage à dilatation contrôlée a pour avantage de se dilater faiblement et
de façon prédéfinie dans une large plage de température. Ainsi les pièces d'un canon
à électron chauffent sous l'effet des électrons, en ne leur offrant que certains trous
pour passer (calibrage du faisceau électronique) ce qui est la fonction de ces pièces
: on a donc besoin d'alliage se dilatant aussi peu que possible dans toute la plage
de température de travail, et ayant une bonne aptitude à la mise en forme.
[0079] Outre la dilatabilité, une bonne tenue à la corrosion aqueuse acide, une bonne tenue
à la corrosion sous brouillard salin et une bonne tenue à l'usure mécanique de la
couche d'oxyde sont des propriétés recherchées. Ces propriétés sont obtenues avec
des recuits industriels peu coûteux (point de rosée faible ou dégradé) ou dans des
environnements sévères sans avoir besoin de protection supplémentaire.
[0080] Ces alliages représentent donc de bonnes solutions de substitution aux alliages FeNi
conventionnels, tout en contenant moins de nickel que ceux-ci.
Capteurs de courants, de transformateurs de mesure ou capteurs magnéto-harmoniques
[0082] Cette composition est plus particulièrement adaptée à la fabrication de capteurs
de courants ou de transformateurs de mesure.
[0083] De préférence, on recherche une aptitude à obtenir les bonnes performances magnétiques
sous tout type d'atmosphère industrielle non oxydante telle que gaz neutre, He, H2,
N2, NH3 etc...ce qui contraint alors réduire le plus possible la teneur en Titane,
de préférence < 30ppmTi, de préférence <20ppmTi.
[0084] On entend par capteur de courant ou transformateur de mesure, les dispositifs de
détection de courant ou de champ magnétique dans un objectif d'alerte de dépassement
seuil (disjoncteur différentiel électronique) ou de mesure de courant, de champ (transformateur
de courant, de tension, compteur d'énergie, capteur de courant continu).
[0085] Ce type d'applications nécessite tout particulièrement un faible champ coercitif
tandis que l'aimantation à saturation peut-être faible (4000 à 8000G à 20°C) comme
par exemple dans nombre de cas de capteur de courant à boucle fermée, ou bien peut-être
élevée (>10 000G) comme dans le cas des capteurs de courant à boucle ouverte.
[0086] La grandeur principale de l'application est la précision de mesure qui est fortement
liée au champ coercitif de l'alliage utilisé, ainsi que dans beaucoup de cas la linéarité
B-H de la courbe d'aimantation ou du cycle d'hystérésis : plus Hc est faible, meilleure
est la précision de mesure.
[0087] Pour certaines applications, tels que les transformateurs-capteurs de courant à large
bande de fréquence, il faut une très faible hystérésis dynamique pour garantir une
bonne précision de mesure aux moyennes fréquences, ce qui peut être est obtenu par
des structures à boucle fermée fonctionnant à basse induction, mais aussi en choisissant
des matériaux à faible Hc et haute résistivité électrique.
[0088] En synthèse, un matériau adapté à ces applications doit présenter les caractéristiques
suivantes :
- Induction Bs à 20°C de 4000G à plus de 13000G selon l'application
- Hc < 75 mOe (de préférence < 37 mOe)
- Résistivité électrique ρel > 60µΩ.cm (de préférence ρel > 70µΩ.cm).
[0089] Dans certains cas d'applications, on recherche en outre la linéarité de la courbe
d'aimantation B-H jusqu'au coude de la courbe d'aimantation. Cette linéarité est caractérisée
par le rapport Br/Bm de l'induction rémanente sur une induction mesurée en zone d'approche
à saturation. Si Br/Bm <0,3 la linéarité devient exploitable dans ces applications
spécifiques à noyaux magnétiques sans entrefer localisé.
[0090] Les alliages selon l'invention permettent d'atteindre l'ensemble de ces propriétés.
[0091] La composition adaptée à ces applications est également adaptée à la fabrication
de capteurs magnéto-harmoniques.
[0092] Dans cette application, un matériau à haute perméabilité et faible champ coercitif
est soumis à la polarisation magnétique plus ou moins grande d'un matériau magnétique
semi-rémanent ; l'état d'aimantation de ce dernier (aimanté, désaimanté ou partiellement
aimanté) correspond à une information ou une alarme qui est transmise au matériau
doux au travers de la polarisation de celui-ci. Le matériau doux est excité en moyenne
fréquence par un champ magnétique externe, produisant pas, peu ou beaucoup d'harmonique
du fondamental émis selon que le matériau doux était soumis à respectivement un semi-rémanent
désaimanté, partiellement aimanté ou aimanté. Ainsi l'amplitude détectée d'harmonique
est l'image du niveau de polarisation du semi-rémanent.
[0093] Par exemple dans une bibliothèque, ce dispositif est glissé à l'état aimanté dans
la jaquette de chaque livre stocké. Lors d'un emprunt, le livre est enregistré et
en même temps désaimanté pour passer sans encombre le portique de sécurité (pas d'émission
d'harmonique). Si le livre n'a pas été désaimanté par l'appareillage spécifique, le
taux important d'émission d'harmonique enclenche la mise en route du signal d'alerte
lors du passage vers la sortie sous le portail de détection.
[0094] Pour réagir dynamiquement à de telle impulsions il faut une grande dynamique d'aimantation
c'est à dire une résistivité électrique élevée, une très faible épaisseur de bande
typiquement inférieure à 50µm, et de préférence inférieure à 30µm, et un faible champ
coercitif, typiquement Hc inférieure à 63 mOe, et de préférence inférieure à 25 mOe.
Le champ coercitif contrôle aussi au 1
er ordre la sensibilité du capteur magnéto-harmonique et permettra de le déclencher
pour un éloignement de l'antenne d'excitation d'autant plus grand que Hc est faible.
Le champ coercitif est la propriété la plus contraignante pour le domaine de composition
qui devra être limité en cuivre pour cette raison.
[0095] En synthèse, un matériau adapté à ces applications doit présenter les caractéristiques
suivantes :
- Hc< 63 mOe (de préférence <25 mOe) à la fois pour avoir une bonne sensibilité du capteur
au champ d'excitation moyenne fréquence et pour limiter l'hystérésis dynamique (donc
favoriser la dynamique d'aimantation)
- Résistivité électrique rel > 60µΩ.cm (de préférence rel > 80µΩ.cm) pour avoir une bonne dynamique de réponse à l'excitation externe moyenne
fréquence.
[0096] Les alliages selon l'invention permettent d'atteindre l'ensemble de ces propriétés.
Moteurs et actionneurs électromagnétiques
[0098] Cette composition est plus particulièrement adaptée à la fabrication de moteurs et
actionneurs électromagnétiques.
[0099] De préférence, on recherche une aptitude à obtenir de bonnes performances magnétiques
sous tout type d'atmosphère industrielle non oxydante telle que gaz neutre, He, H2,
N2, NH3 etc...ce qui contraint alors réduire le plus possible la teneur en Titane,
de préférence < 30ppmTi, de préférence <20ppmTi.
[0100] Les moteurs et actionneurs électromagnétique pouvant être fabriqués selon l'invention
présentent une puissance volumique moyenne à forte, une grande précision de mouvement,
une faible dissipation et un faible coût.
[0101] On englobera dans cette application tous les dispositifs électromagnétiques non polarisés
comportant une pièce mobile (rotor pour système rotatif t.q. moteur, alternateur,
synchro-résolveur, capteur de couple réluctant, moteur-roue etc..., palette ou noyau
pour les systèmes en translation t.q. moteur linéaire, électrovanne, injecteur, actionneur
linéaire impulsif type camless etc...) en matériau magnétique doux à haute résistivité
électrique et faibles pertes magnétiques, et une partie statique comportant un matériau
magnétique aimanté.
[0102] Les dispositifs selon l'invention présentent en particulier les caractéristiques
suivantes :
- un encombrement assez réduit à très réduit selon la puissance transférée dans l'application,
sachant que plus la puissance de l'actionneur ou capteur ou moteur est forte, plus
il est important de disposer d'un matériau à saturation élevée. Ceci implique une
induction à saturation supérieure à 5000 G,
- une faible dissipation d'énergie (ou bon rendement énergétique) grâce à une résistivité
électrique élevée (>70µΩ.cm), un faible Hc (< 125 mOe), une perméabilité assez élevée
en courant continu (>5 000µ0),
- une bonne précision de placement de la partie mobile en réduisant fortement le phénomène
d'hystérésis dynamique unidirectionnel ou rotationnel (obtenu avec Hc < 125 mOe, et
de préférence < 75 mOe). Cette propriété est tout particulièrement importante pour
les capteurs de couple à réluctance variable, pour les résolveurs et synchro-résolveurs
et plus généralement pour tous les systèmes rotatifs à faible réluctance d'entrefer.
[0103] Dans ce type d'applications, les culasses magnétiques peuvent être réalisées par
empilage de pièces découpées, à des épaisseurs assez faibles (>0,1mm, de préférence
0,15mm) permettant de limiter au maximum les courants induits macroscopiques, les
pertes magnétiques, le phénomène d'hystérésis dynamique ; dans les systèmes à sollicitations
magnétiques unidirectionnelles (électrovannes, électro-injection, actionneur Camless,
actionneur de sécurité gaz par exemple), on utilise plutôt une tôle épaisse ou un
fil mis à la forme de la culasse finale par emboutissage/ formage/ pressage/ usinage
etc avant recuit final.
[0104] Dans le cas des dispositifs à champs magnétiques tournants (systèmes rotatifs par
exemple) il est préférable que l'alliage présente une isotropie la meilleure possible
de ses performances magnétiques car sinon cela introduit des oscillations de couple
en fonction du pas de rotation (cas des moteurs), des fluctuations de réluctance magnétique
en fonction de la position de la pièce mobile (cas du synchro-résolveur, du capteur
de couple réluctant ...). On résout le problème soit en utilisant des séquences de
laminage-recuit ne développant pas de texture cristallographique, soit en développant
une texture de type « planaire » par exemple {100}<0vw> ou {111}<uvw>
[0105] Dans le cas de dispositif d'actionneur électromagnétique de sécurité, non polarisé,
tel que ceux utilisés pour prévenir les fuites de gaz domestique sur les systèmes
de chauffage à gaz (chauffe-eau par exemple), on a besoin de faibles courants d'enclenchement
et de déclenchement du dispositif (ainsi qu'une faible différence entre ces courants)
ce qui passe nécessairement par des faibles champs coercitifs (voir ci-dessus) et
de faibles entrefers entre culasse magnétique et noyau mobile de l'actionneur, mais
aussi par une faible rémanence pour garantir le déclenchement même avec de très faibles
entrefers, pour réduire la différence les courants d'enclenchement et déclenchement,
pour réduire la dispersion de production des performances du dispositif. On recherche
en particulier dans ce cas d'application B
r/B
max < 0,5 et de préférence <0,3 (B
max induction pour un champ magnétique au moins égal à 3H
c).
[0106] Les alliages selon l'invention permettent d'atteindre l'ensemble de ces propriétés.
Stators pour moteurs d'horlogerie
[0108] Cette composition est plus particulièrement adaptée à la fabrication de stators pour
moteurs d'horlogerie, en particulier du type pas à pas.
[0109] De préférence, on recherche une aptitude à obtenir les bonnes performances magnétiques
sous tout type d'atmosphère industrielle non oxydante telle que gaz neutre, He, H2,
N2, NH3 etc....ce qui contraint alors à réduire le plus possible la teneur en Titane,
de préférence < 30ppmTi, de préférence <20ppmTi.
[0110] Pour ce type d'applications, on recherche des alliages avec un coût faible tout en
satisfaisant un certain nombre de propriétés.
[0111] On recherche tout d'abord une bonne découpabilité de la bande d'alliage par poinçonnage,
estampage ou tout autre procédé adapté, permettant une faible usure d'outil et une
grande cadence de découpe. En effet, le métal est livré par le producteur à l'état
écroui ou adouci afin de conserver une dureté mécanique suffisante du métal propice
à la découpabilité par estampage et à grande cadence. Pourtant cette dureté n'est
pas suffisante pour parvenir à découper des centaines de milliers de pièces de stator
sans faire de bavures significatives et sans user la matrice de découpe et surtout
le poinçon de découpe au point de devoir le réaffûter ou le remplacer. Pour y parvenir,
il faut aussi insérer dans le métal certaines distributions inclusionnaires fines
jouant le rôle du « découper suivant le pointillé » lors du processus de découpe entre
poinçon et matrice. De plus ces fines inclusions doivent pouvoir s'éliminer lors du
recuit haute température ultérieur d'optimisation des propriétés magnétiques. C'est
pourquoi les alliages selon l'invention destinés à cette application incorporent de
8 à 40ppm de S, Se, Sb et/ou de 2 à 20ppm et/ou de 10 à 150ppm de Ca, Mg.
[0112] On recherche ensuite une induction à saturation Bs qui doit être supérieure à 4000
G à 60°C, et de préférence inférieure à 7000 G.
[0113] On cherche également à réduire au maximum la consommation électrique du moteur horloger
lorsqu'il est utilisé à sa puissance nominale, c'est à dire lorsque les alliages magnétiques
du stator travaillent à proximité du coude d'aimantation B-H du matériau.
[0114] Pour cela, pour une épaisseur de stator limitée à un minimum de 0,4mm en-dessous
de laquelle la rigidité mécanique ne serait plus suffisante, l'alliage doit présenter
une résistivité électrique de plus de 70µΩ.cm, et de préférence supérieure à 80 µΩ.cm
et un bas champ coercitif Hc inférieur à 125 mOe et de préférence inférieur à 75 mOe
avant montage dans la montre.
[0115] Par ailleurs, la consommation électrique de la montre ne doit pas augmenter significativement
lorsque la température ambiante augmente. En effet, si l'aimantation de travail diminue
significativement lorsque la température croît, alors pour fournir toujours le couple
minimum à la rotation d'un demi-tour du rotor, le générateur d'énergie doit fournir
beaucoup plus d'énergie pour conserver le niveau d'aimantation du stator et donc le
couple moteur s'appliquant sur le rotor. Ainsi dans le cas d'utilisation de la montre
en atmosphère chaude, la consommation augmentera sensiblement.
[0116] Pour contrôler la consommation électrique lorsque la température ambiante augmente,
il faut donc que l'aimantation à saturation Js reste stable dans la plage de fonctionnement
potentielle de la montre à savoir de -40°C à +60°C : une telle caractéristique est
systématiquement obtenue lorsque le point de Curie de l'alliage Tc est supérieur ou
égal à 100°C.
[0117] On recherche également une bonne tenue à la corrosion. En effet, les pièces magnétiques
de stator, une fois découpées et passées au traitement thermique d'optimisation des
performances magnétiques, sont stockées, acheminées puis montées à l'air libre dans
les mouvements horlogers. Ces montages se font de plus en plus massivement dans des
pays où règne une grande corrosion atmosphérique, notamment d'origine saline ou due
à la pollution atmosphérique (soufre, chlore...).
[0118] En fonction de la qualité et de la durée de vie recherchée pour la montre, l'exigence
de résistance à la corrosion acide sera plus ou moins élevée. En effet, la durée de
vie de la montre n'excède pas le temps de dégradation sensible de l'alliage du stator
par corrosion atmosphérique. S'il s'agit de moteur horloger de qualité entrant dans
des zones de fabrication de renom comme « Swiss-made » ou « Japan-made » , la montre
est faite pour durer quelques années et l'alliage horloger ne doit pas se corroder
significativement dans ce laps de temps. S'il s'agit d'un moteur horloger haut de
gamme ou de montre transparente avec notamment des pièces du moteur visibles, celui-ci
doit en principe fonctionner sans problème durant la vie d'une personne.
[0119] Les différents niveaux de tenue à la corrosion peuvent alors s'évaluer selon :
- mouvement horloger bas de gamme : tenue à la corrosion minimale avec Ioxmax ≤ 5mA,
- mouvement horloger de qualité type « Swiss-made » ou « Japan-made » : tenue à la corrosion
intermédiaire avec Ioxmax ≤ 3mA,
- mouvement horloger visible en fonctionnement (montre transparente) ou garanti à vie
: tenue à la corrosion haute performance, avec Ioxmax ≤ 1mA.
Inductances ou transformateurs pour l'électronique de puissance
[0121] Cette composition est plus particulièrement adaptée à la fabrication d'inductances
ou de transformateurs pour l'électronique de puissance.
[0122] Les circuits magnétiques des composants magnétiques passifs utilisés en électronique
de puissance ou dans tout autre système de conversion d'énergie en moyenne fréquence
(quelques centaines de Hz à quelques centaines de kHz) nécessitent l'utilisation d'inductance
de lissage ou de transformateurs qui constituent souvent des parties volumineuses
des alimentations de puissance.
[0123] Dans le dimensionnement de ces composants, c'est à la fois l'aimantation à saturation
du noyau magnétique mais aussi les pertes Joule-conducteur et les pertes magnétiques
générées et évacuées par l'ensemble du composant qui fixent le potentiel accessible
de réduction de volume lié au matériau magnétique doux utilisé.
[0124] Il en découle qu'un bon noyau magnétique de composant magnétique passif type inductance
de stockage ou lissage, ou transformateur de puissance doit tout d'abord avoir une
induction à saturation élevée aux températures d'utilisation, qui se situent typiquement
autour de 100-120°C. On recherche ainsi une induction à saturation Bs
100°C supérieure ou égale à 4000G, ce qui correspond à une induction à saturation à 20°C,
Bs
20°C qui soit supérieure à 8000G ou bien encore à un point de Curie Tc supérieur ou égal
à 150°C.
[0125] Il doit également présenter de faibles pertes magnétiques aux températures d'utilisation,
ce qui correspond, pour des épaisseurs de métal d'au plus 50µm, à une résistivité
électrique à 100°C supérieure à 60µΩ.cm, et de préférence supérieure à 100µΩ.cm et
à une faible hystérésis dynamique caractérisée par un champ coercitif Hc à 100°C inférieur
à 75 mOe et de préférence inférieur à 37,5 mOe. On n'impose donc que le champ coercitif
Hc à 20°C soit inférieur ou égal à 75 mOe, et de préférence inférieur à 37,5 mOe.
Il est en effet bien connu par l'homme de l'art que Hc décroit avec la température
dans les matériaux magnétiques doux, lorsque la température se rapproche du point
de Curie, et ainsi on obtiendra a fortiori les performances à 100°C si on les a garanties
à 20°C.
[0126] De plus, les pertes résiduelles des alliages selon l'invention pourront être compensées
par une bien meilleure aptitude à extraire ces pertes grâce à la conduction thermique
élevée des alliages métalliques et à la très grande aptitude à la mise en forme et
en oeuvre de ces culasses magnétiques très ductiles et permettant d'y installer facilement
des circuits de refroidissements ou de donner une forme complexe au circuit magnétique.
Bilames
[0128] Cette composition est plus particulièrement adaptée à la fabrication de bilames.
[0129] Dans cette application, une variation de température peut être transformée soit en
déformation du bilame, soit en élévation de l'extrémité du bilame, l'autre extrémité
étant maintenue en position, soit en force exercée par l'extrémité libre de bilame,
grâce à la liaison étroite de deux matériaux en forme de bande étroite et plate, de
dilatabilités différentes.
[0130] Les pièces de bilame peuvent servir aussi bien de capteur de surintensité au travers
de la résistivité électrique du matériau multicouche et de sa déflexion, de capteur
de température au travers de la déflexion du bilame qui coupe alors un circuit électrique
ou encore d'actionneur thermomécanique au travers de la force engendrée par la dilatation
non équilibrée des différents constituants du bilame. Dans tous les cas, l'action
du bilame passe par sa déflexion dont l'amplitude est proportionnelle à la différence
de dilatation entre les deux constituants externes du bilame. La sensibilité de l'actionneur
bilame sera d'autant plus grande que l'écart de dilatabilité sera grand pour des épaisseurs
données de bande et un écart donné de température.
[0131] On recherche donc un matériau présentant un coefficient de dilatation moyen entre
20 °C et 100°C α
20-100 qui soit inférieur ou égal à 7.10
-6/°C et de préférence inférieur ou égal à 5.10
-6/°C et simultanément un coefficient de dilatation moyen α
20-300 qui soit inférieur ou égal à 10.10
-6/°C et de préférence inférieur ou égal à 8.10
-6/°C, pour permettre une utilisation sur une large plage de température.
[0132] Une autre grandeur importante lorsque la source de chaleur provient du courant électrique
qui traverse le bilame, est la résistivité électrique ρ
el. Ainsi un bilame ayant une forte résistivité électrique moyenne chauffera beaucoup
plus et montera à une température plus élevée qu'un bilame à faible résistivité électrique.
Il en résultera soit une amplitude de flèche ou déflexion du bilame dans le même rapport,
ou une force du bilame-actionneur dans les mêmes rapports. De plus la résistivité
électrique est inversement proportionnelle à la conductivité thermique qui assure
de son côté l'uniformisation de la température et assure donc la dynamique de la réponse-bilame.
[0133] On recherche donc les matériaux présentant une résistivité électrique à 20°C - ρ
el - supérieure à 75 µΩ.cm, de préférence supérieure à 80µΩ.cm.
[0134] Par ailleurs, l'adjonction d'une troisième couche métallique comme le cuivre ou le
nickel entre les couches à faible et haute dilatabilité permet de régler différents
compromis de résistivité/conductivité sans changer les dilatabilités.
[0135] En outre, il est nécessaire d'avoir un matériau présentant un point de Curie Tc supérieur
ou égal à 160°C, et de préférence supérieur à 200°C pour conserver une bonne stabilité
en température des propriétés de dilatation.
[0136] Pour obtenir ce point de Curie élevé, cette faible dilatabilité, et cette forte résistivité
électrique, il est nécessaire que les alliages selon l'invention présentent plus de
30% de nickel et respectent l'équation 8 définie par :

Noyaux de bobines de moteurs d'horlogerie ou de relais électromagnétiques à haute
sensibilité
[0138] Cette composition est plus particulièrement adaptée à la fabrication de noyaux de
bobines de moteurs d'horlogerie ou de relais électromagnétiques à haute sensibilité.
[0139] De préférence, on recherche une aptitude à obtenir les bonnes performances magnétiques
sous tout type d'atmosphère industrielle non oxydante telle que gaz neutre, He, H2,
N2, NH3 etc...ce qui contraint alors à réduire le plus possible la teneur en titane,
de préférence < 30ppmTi, de préférence <20ppmTi.
[0140] Dans un objectif général de faible consommation électrique de la montre, le champ
magnétique destiné à aimanter le circuit magnétique horloger doit être produit avec
le minimum de courant électrique, c'est à dire avec le maximum de spires de la bobine
d'excitation, ce qui engendre d'utiliser un fil très fin et un noyau magnétique à
haut flux magnétique afin de réduire la section du noyau et de placer une bobine aussi
grosse que possible.
[0141] L'alliage magnétique du noyau doit donc nécessairement offrir une haute saturation
magnétique puisque le flux magnétique est le produit de l'aimantation par la section
du matériau. On recherche donc des alliages ayant une induction à saturation Bs à
20°C qui soit supérieure à 10 000G.
[0142] L'alliage doit aussi offrir un faible champ coercitif Hc ainsi qu'une résistivité
électrique élevée pour réduire les pertes magnétiques, et ainsi limiter la consommation
électrique de la montre. On recherche donc des alliages présentant un champ coercitif
Hc à 20°C qui soit inférieur à 125mOe et de préférence inférieur à 75mOe et une résistivité
électrique ρ
el qui soit supérieure à 60µΩ.cm et de préférence supérieure à 80µΩ.cm.
[0143] En outre, les alliages selon l'invention destinés à cette application présentent
de préférence une bonne découpabilité et peuvent donc incorporer à titre optionnel,
de 8 à 40ppm de S, Se, Sb et/ou de 2 à 20ppm et/ou de 10 à 150ppm de Ca, Mg.
[0144] Les alliages selon l'invention permettent d'atteindre l'ensemble de ces propriétés.
[0145] Dans un mode de réalisation préféré, les alliages selon l'invention présentent une
induction à saturation Bs supérieure à 13 000G et leur composition doit alors respecter
l'équation 9 :

[0146] Les compositions adaptées à la fabrication de noyaux de bobines de moteurs horlogers
sont également adaptées à la fabrication de relais électromagnétiques à haute sensibilité.
[0147] Un relais électromagnétique est un actionneur mécanique à commande électrique, où
une culasse magnétique généralement massive pour de raison de facilité et faible coût
de production/mise en forme, est refermée par une pièce de matériau et en bascule
sur une extrémité de jambe de culasse. La position de bascule entre « ouverte » et
« fermée » résulte de l'équilibre entre une force mécanique de rappel d'un ressort
(placé à l'extérieur de la culasse et tendant à ouvrir le circuit magnétique en faisant
pivoter la palette mobile autour de la jambe de culasse) et une force électromagnétique
constituée au repos de la seule force d'attraction magnétique de la culasse aimantée
par un aimant sur la palette. Au repos, la palette ferme la culasse.
[0148] Un bobinage entoure une jambe de la culasse de telle sorte que si un courant électrique
provenant d'un événement extérieur et devant être converti en signal mécanique le
parcourt, il s'ajoute une force magnétique de répulsion de la palette par rapport
à la culasse, qui fait diminuer l'amplitude de la force d'attraction magnétique. Ainsi
suivant l'amplitude du courant électrique dans le bobinage, la force de répulsion
peut atteindre un niveau suffisant pour que l'action du ressort l'emporte en ouvrant
le relais et actionnant un système mécanique. C'est sur ce principe que fonctionnent
notamment les disjoncteurs électriques.
[0149] Pour que ce type de relais fonctionne avec une haute sensibilité il faut qu'une une
faible variation de courant I dans la bobine provoque une forte variation de la force
de répulsion et il faut en outre que ce comportement soit proportionnel sur une plage
suffisamment étendue de courant afin de permettre un préréglage adéquat du relais.
Ceci revient à définir un besoin de perméabilité élevée dans une plage d'induction
B-H assez linéaire, centrée sur le point de fonctionnement au repos du relais, qui
correspond à l'aimantation du relais polarisé par l'aimant et pour une fréquence de
sollicitation donnée.
[0150] Plus le matériau a une induction à saturation Bs élevée, plus la variation d'induction
dans la culasse sous l'effet du courant I sera élevée et plus la sensibilité du relais
sera grande et sa puissance élevée à perméabilité dynamique donnée. On a besoin également
d'une induction à saturation Bs à 20°C supérieure à 10 000 G et de préférence supérieure
à 13 000 G, ainsi que d'une bonne dynamique d'aimantation obtenue par une résistivité
électrique élevée, ρ
el supérieure à 60µΩ.cm et de préférence supérieure à 70µΩ.cm et d'un faible champ coercitif
Hc (à 20°C) inférieur à 125mOe et de préférence inférieur à 75mOe.
[0151] Par ailleurs, une tenue à la corrosion minimale est demandée car les relais sont
souvent protégés par des boitiers non hermétiques, laissant passer l'atmosphère environnante
potentiellement chaude, humide, oxydante (Cl, S...) alors que l'état non oxydé du
métal durant son fonctionnement pendant des années est important pour garantir la
reproductibilité des conditions de déclenchement par la non-dérive de ses performances
magnétiques. Il faut que I
oxmax reste inférieur à 5mA et de préférence inférieur à 3mA, voire inférieur à 1 mA.
Dispositifs de mesure de température et de marquage de dépassement de température, sans contact
[0153] Cette composition est plus particulièrement adaptée à la fabrication de dispositifs
de mesure de température ou de marquage de dépassement de température, sans contact.
[0154] Les pièces magnétiques d'étiquettes de mesure de température sans contact (mesure
en temps réel, utilisant un phénomène magnétique réversible) ou de mesure de dépassement
de température sans contact (mesure a postériori, utilisant un phénomène irréversible
mais permettant une réinitialisation de l'étiquette à la fin du processus de surveillance)
utilisent en même temps des matériaux très différents, tels que des matériaux magnétiquement
doux (« l'alliage ») et des matériaux magnétiques à aimantation permanente (MAP) dans
une configuration stabilisée de température et de champs magnétiques environnants.
Cette surveillance de température est, par le principe même de l'étiquette, réalisée
dans la plage de température immédiatement en dessous et autour du point de Curie
de l'alliage magnétique doux.
[0155] Dans cette application, on peut par exemple utiliser une plaque de MAP de section
S1 solidarisé avec une plaque de matériau à très haute perméabilité de section S
2, tel qu'un alliage FeNi mince ou un alliage amorphe, en laissant un entrefer faible
d entre les deux matériaux. Le matériau MAP joue le rôle de polariseur magnétique
du matériau magnétiquement doux adjacent. De plus, soit sur l'autre face du MAP soit
encore entre le MAP et le matériau à haute perméabilité, mais séparé du matériau de
celui-ci par l'entrefer d, on place une troisième plaque constituée d'un alliage selon
l'invention présentant une point de Curie Tc.
[0156] Lorsque la température ambiante se rapproche du point de Curie Tc de l'alliage selon
l'invention, celui-ci est moins aimanté et le flux magnétique du MAP se referme pour
une partie plus importante sur le matériau à haute perméabilité qui se trouve polarisé
à un niveau d'aimantation croissant et dépendant du ratio T/Tc.
[0157] En excitant alors le matériau à haute perméabilité avec un champ moyenne fréquence
à partir d'une antenne distante, une variation d'aimantation ΔJ est produite autour
de l'aimantation de polarisation J
1 et le matériau va émettre des harmoniques de façon importante, car on a préalablement
optimisé J1 dans ce sens, via le choix de S
1, S
2 et d.
[0158] Le point de Curie fonctionnel qui est recherché se situe entre -50°C et 400°C , et
en particulier entre -30°C et +100°C pour de nombreuses applications de surveillance
de température des produits comestibles comme la chaine du froid, les températures
des celliers à vin, les stockages et transports réfrigérés ou non de denrées comestibles
périssables, les conteneurs de poisson et viande, les produits sanguins et dérivés,
les stocks et expéditions de substances organiques non comestibles thermo-périssables
comme les plantes, fleurs, prélèvements humains pour implants ou autres, cultures
de cellules et germes ou bactéries, lots de polymères, macromolécules, etc. Ce point
de Curie est limité à 400°C au maximum et est de préférence compris entre -30°C et
100°C.
[0159] On recherche un champ coercitif suffisamment faible (<75 m0e, et de préférence <32,5
mOe) pour obtenir d'une part une haute sensibilité du capteur au champ d'excitation
à moyenne fréquence, et d'autre part, une grande dynamique du capteur par association
avec une résistivité électrique élevée (> 60µΩ.cm, et de préférence > 80µΩ.cm) et
de préférence une faible épaisseur de matériau. Cette restriction à de faibles champs
coercitifs oblige à limiter le pourcentage de cuivre à 10% maximum et de préférence
à moins de 6% en association avec une teneur maximum en nickel de 34%.
[0160] On recherche aussi une tenue minimale à la corrosion et à l'oxydation puisque les
alliages sont souvent au contact de différents milieux et/ou constituants dans des
atmosphères industrielles. Dans ces applications, on demande souvent une bonne stabilité
chimique de l'alliage se traduisant par une bonne tenue à la corrosion aqueuse (lox<5mA),
une bonne tenue à la corrosion en brouillard salin et une bonne stabilité mécanique
(adhésion + tenue à l'usure) de la couche oxydée de surface en atmosphère chaude et
oxydante.
[0161] Les alliages selon l'invention permettent d'atteindre l'ensemble de ces propriétés.
Substrats hyper-texturés pour épitaxie
[0163] On préfère en outre ajouter de 0,003 à 0,5% de niobium et/ou de zirconium.
[0164] Ces compositions sont plus particulièrement adaptées à la fabrication de substrats
hyper-texturés pour épitaxie.
[0165] En effet, de nombreuses applications nécessitent de faire croître de fines couches
de matériaux poly-cristallins les plus texturés possibles, c'est à dire avec une texture
si possible mono-composante la plus aiguë possible.
[0166] On entend pas texture mono-composante une distribution non aléatoire des orientations
cristallographiques du poly-cristal, de telle sorte qu'elles sont toutes situées dans
un angle solide (de demi-angle au sommet ω) entourant l'orientation idéale visée,
notée [hkl](uvw) en indice de Miller. ω est appelée désorientation moyenne de texture
et peut avoir différentes valeurs suivant qu'on la mesure dans le plan de laminage
ou hors du plan.
[0167] Ces matériaux déposés ont des propriétés physiques particulières, telles que, par
exemple, la supraconductivité des oxydes de type Y-Ba-Cu-O.
[0168] Ces propriétés sont très améliorées par de faibles densités de défauts aux joints
de grain, qui passent par de faibles désorientations entre cristaux adjacents (rôle
d'une texture aiguë) et par une taille de grain de l'ordre de quelques dizaines de
micron pour réduire la densité volumique de défauts à désorientation de texture identique.
[0169] Pour obtenir ces dépôts polycristallins très texturés, une des méthodes très utilisées
est la technique d'épitaxie à partir d'une phase vapeur ou liquide, sur un substrat
lui-même hyper-texturé avec un paramètre de maille assez proche de celui du produit
déposé, une texture aussi mono-composante et aiguë que possible, une bonne résistance
à l'oxydation lors des recuits oxydants éventuels nécessités par la formation des
oxydes déposés, une tenue mécanique minimale pour ne pas fluer lors des recuits et
résister à la mise en oeuvre du produit final (bobinage, enroulage, mise sous tension,
etc.)
[0170] Les propriétés d'usage spécifiques requises pour les substrats hyper-texturés sont
dont essentiellement la présence d'une fraction surfacique de macle et autres orientations
différentes des orientations centrées à moins de 15° de désorientation de l'orientation
idéale cubique [100](001), de préférence à moins de 10%, et de préférence à moins
de 5% ainsi qu'une désorientation ω de la principale composante de texture cubique
{100}<001>: inférieure à 10° et de préférence inférieure à 7°.
[0171] On recherche également une dilatabilité moyenne entre 20 °C et 100°C et une dilatabilité
moyenne entre 20 °C et 300°C variables selon les applications finales. On peut ainsi
avoir besoin, lorsqu'un dépôt sur substrat est réalisé à chaud, de mettre en compression
la couche déposée lorsque le produit est revenu à l'ambiante. Il faut donc pouvoir
choisir une dilatation réglée entre 20°C et la température de dépôt à un niveau très
variable selon la dilatation/contraction du matériau déposé.
[0172] Enfin, le point de Curie n'est pas limité pour cette propriété et dans certaines
applications supraconductrices il est même de loin préférable que le substrat soit
aussi peu magnétique que possible à la température d'utilisation c'est à dire 77K.
EXEMPLES
[0173] Dans le cadre de la présente invention, les abréviations suivantes sont utilisées
:
▪ Inv. : essai conforme à l'invention,
▪ Comp. : essai comparatif,
▪ NR : essai non réalisé,
▪ CBS : sensibilité à la corrosion en brouillard salin,
▪ UM : tenue à l'usure mécanique de la couche oxydée de surface des alliages sous
atmosphère industrielle oxydante,
▪ Bs20°C : induction à saturation, mesurée à 20°C et exprimée en Gauss.
▪ Bs60°C (G) : : induction à saturation, mesurée à 60°C et exprimée en Gauss.
▪ Tc : point de Curie du matériau, exprimée en °C.
▪ Hc : champ coercitif à 20°C, mesuré en mOe.
▪ Iox : courant maximal à potentiel imposé, mesuré en mA
▪ Br/Bm : rapport de l'induction rémanente Br sur l'induction mesurée en zone d'approche
à saturation Bm
▪ α20-100 : coefficient moyen de dilatation (appelé aussi « dilatabilité ») du matériau, mesuré
entre 20 et 100°C et exprimé en 10-6/°C et α20-300 : coefficient moyen de dilatation du matériau, mesuré entre 20 et 300°C et exprimé
en 10-6/°C et α20-77K : coefficient moyen de dilatation du matériau, mesuré entre 77K et 20°C exprimé en
10-6/°C.
▪ ρel ou ρ-elec : résistivité électrique à 20°C, mesurée en µΩ.cm
▪ µmaxCC : perméabilité relative maximum en courant continu, mesurée par comparaison à la
perméabilité du vide µ0 (= 4π.10-7) et donc sans dimension et unité.
▪ ω : désorientation moyenne de texture, mesurée en ° (degré).
TESTS ET MESURES
[0174] Pour tester les alliages selon l'invention, différentes compositions d'alliages ont
été élaborées par fusion par induction sous vide, sous forme de lingots de 50 kg à
la composition désirée. Le matériau est ensuite forgé entre 1 000 et 1 200°C, laminé
à chaud entre 1 150 et 800°C jusqu'à une épaisseur de 4,5 mm, décapé par voie chimique,
laminé à froid sans recuit intermédiaire jusqu'à 0,6 mm. Tous les alliages sont au
moins caractérisés à ce stade après découpe en différents échantillons tels que ceux
pour mesures de dilatabilité, de Tc, de I
oxmax, de Js et des rondelles de diamètre 25 x 36 mm.
[0175] Différents tests sont alors réalisés :
Résistance à la corrosion sous brouillard salin, CBS
[0176] Pour mesurer CBS, on immerge une tôle d'alliage dans une enceinte climatique de brouillard
salin fait d'une atmosphère à 95% d'humidité, saturée en sel NaCl, pendant 24h. On
rince ensuite les tôles à l'alcool puis on observe les piqûres de corrosion. La densité
et l'importance de la piqûration sont alors notées avec 3 niveaux de sensibilité :
0 : non sensible,
- : un peu sensible
-- : sensible et
--- : très sensible à la corrosion sous brouillard salin.
Usure mécanique de la couche d'oxyde de surface, UM
[0177] Pour mesurer UM, on procède tout d'abord à un recuit du métal écroui à l'épaisseur
0,6mm, à une température de 1100°C, pendant 3h sous hydrogène pur et vapeur d'eau
telle que le point de rosée soit de -30°C (simulation d'un recuit industriel). On
empile ensuite deux tôles ainsi recuites sous une masse uniformément répartie donnant
une pression équivalente à 1 kg pour 10cm
2. On réalise alors 100 glissements aller/retour jusqu'à mi-longueur d'une tôle par
rapport à l'autre puis on observe l'usure des surfaces notée avec 3 niveaux de tenue
à l'usure après examen de surface du métal:
- 0 : faible tenue à l'usure,
- + : tenue moyenne à l'usure mécanique et
- ++ : très bonne tenue à l'usure mécanique.
Point de Curie, Tc
[0178] Tc est mesurée par force magnétique au thermomagnétomètre de Chevenard : l'échantillon
est chauffé à 100°C/h jusqu'à 800°C puis refroidi à la même vitesse jusqu'à l'ambiante.
La valeur de Tc retenue est celle correspondant à l'exploitation du thermogramme à
la chauffe ; la valeur de Tc est extrapolée sur l'axe des origines (déviation = 0)
à partir de la tangente au point d'inflexion de la courbe force magnétique : f (T
re).
Tenue à la corrosion aqueuse acide Ioxmax
[0179] La tenue à la corrosion des alliages en milieux atmosphériques corrosifs ou en milieux
aqueux acides peut s'évaluer par la mesure du courant maximal obtenu lorsque l'on
immerge un échantillon-plaque d'alliage dans un bain d'acide sulfurique 0,01M et l'alliage
étant relié par un conducteur à une autre électrode-plaque de platine, en appliquant
différentes valeurs de tensions. Différentes valeurs d'intensité I sont ainsi mesurées
sur le conducteur reliant les deux électrodes et on détermine alors la valeur maximale
I
oxmax de I (U).
[0180] Par ce test à potentiel imposé entre plaques, l'évolution du courant dans le conducteur
et en particulier sa valeur maximale donne une évaluation correcte de l'aptitude de
l'alliage à constituer une couche d'oxyde stable à sa surface : plus I
oxmax est faible, plus l'alliage résiste bien à la corrosion.
Coefficients de dilatations (ou dilatabilité)
[0181] Les coefficients moyens de dilatation thermique entre 20°C et une température T -
notés <α
20→T> ou par commodité α
20-T - sont mesurés sur dilatomètre de Chevenard en se comparant à un échantillon étalon
de Pyros (Fe-Ni de composition et dilatation précises) : on enregistre la variation
d'allongement Δl d'un échantillon de longueur initiale « l
0 » en fonction de la température T : Δl = f(T). La dilatabilité moyenne entre 20°C
et la température T
1 est donnée par :
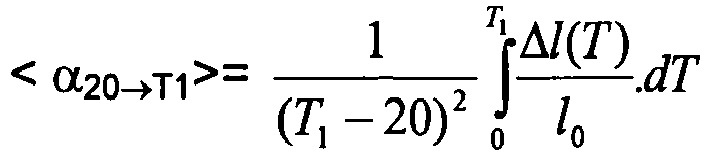
exprimé en 10
-6/°C (millionième d'allongement relatif par degré).
Propriétés magnétiques Hc, Br, µmaxCC
[0182] Ces propriétés sont mesurées par méthode flux-métrique selon norme IEC 404-6, sur
les rondelles recuites : le tracé du cycle d'hystérésis permet de déterminer les valeurs
de H
c, B
r, µ
maxCC.
Exemple 1 - Dispositifs magnétiques à autorégulation de température
[0183] Plusieurs alliages ont été élaborés jusqu'à l'épaisseur finale de 0,6 mm afin de
caractériser les propriétés d'usage. Les alliages sont élaborés à partir de matières
pures à 99,9%, fondus au four à induction sous vide en un lingot de 50kg. Le lingot
est forgé entre 1100 et 1300°C, puis laminé à chaud jusqu'à une épaisseur de 2,5mm,
entre 1000 et 1200°C puis décapé chimiquement. La bande est ensuite laminée à froid
depuis l'épaisseur de laminé à chaud jusqu'à l'épaisseur de 0,6mm, puis recuite entre
800 et 1100°C durant 1 heure, puis dégraissée, découpée en différentes pièces ou rondelles
pour mesures puis recuit à 1100°C/3h sous H2 purifié (point de rosée<-70°C).
[0184] Les nuances testées comportent les éléments mentionnés dans le tableau suivant, le
complément étant du fer et les impuretés inévitables.
Tableau 1 - Composition des nuances d'essais
|
Nuances |
%Ni |
%Cr |
%Cu |
%Mn |
%Si |
Inv. |
SV285mod-1 |
32,45 |
0,04 |
0,53 |
0,3 |
0,18 |
Inv. |
SV285mod-6 |
32,45 |
0,04 |
6 |
0,3 |
0,23 |
Inv. |
SV287-1 |
31,8 |
0,04 |
0,5 |
0,3 |
0,34 |
Inv. |
SV287-5 |
30,7 |
0,04 |
3,7 |
0,3 |
0,26 |
Inv. |
SV302mod-1 |
30 |
0,05 |
7 |
0,2 |
0,34 |
Inv. |
SV302mod-2 |
29,4 |
0,05 |
7 |
2 |
0,23 |
Inv. |
SV302mod-3 |
28,8 |
0,05 |
7 |
4 |
0,31 |
Inv. |
SV298-1 |
29,44 |
0,98 |
0,5 |
0,2 |
0,18 |
Inv. |
SV298-4 |
28,9 |
0,97 |
3 |
0,2 |
0,23 |
Inv. |
SV315-3 |
32,5 |
1,97 |
2 |
0,2 |
0,21 |
Inv. |
SV317-1 |
35 |
2 |
0,5 |
0,2 |
0,31 |
Inv. |
SV323-6 |
33 |
1,9 |
0,6 |
3,8 |
0,18 |
Inv. |
SV300-2 |
27,9 |
4 |
1 |
0,2 |
0,31 |
Comp. |
A |
28,9 |
0,03 |
0,15 |
0,2 |
0,31 |
Comp. |
SV297-1 |
26,9 |
1,9 |
1 |
0,2 |
0,34 |
Comp. |
SV300-1 |
28 |
4 |
0,5 |
0,2 |
0,23 |
Comp. |
SV305-1 |
28 |
6 |
0,5 |
0,2 |
0,18 |
Comp. |
Fe-30Ni |
30 |
0 |
0 |
0 |
0 |
Comp. |
B |
27 |
0,03 |
0,14 |
0,2 |
0,23 |
Comp. |
C |
28 |
0,03 |
0,12 |
0,2 |
0,21 |
Comp. |
D |
26,5 |
6 |
0,15 |
0,2 |
0,18 |
Comp. |
E |
26,33 |
4 |
0,12 |
0,2 |
0,17 |
[0185] On réalise une série de tests pour déterminer les valeurs de résistance à la corrosion
en brouillard salin, de résistance à l'usure mécanique, d'induction à saturation,
de point de Curie, de résistance à la corrosion acide et de dilatabilité entre 20
et 100°C.
[0186] Les résultats de ces tests sont rassemblés dans le tableau 2.
[0187] On voit qu'une partie des alliages selon l'invention contient moins de 30%Ni et peuvent
s'approcher très près du point de Curie de l'Invar® (Fe-36%Ni: Tc=250°C) comme par
exemple SV302mod1 (Tc = 199°C). On réduit donc sensiblement le coût d'alliage en substituant
une partie du nickel par du cuivre; de plus on améliore sensiblement la tenue à la
corrosion aqueuse, saline et à l'oxydation par les additions conjointes de Cu, Si,
Cr.
[0188] Comparativement, si on ne met pas de cuivre dans un alliage à 30%Ni, on obtient un
point de Curie aussi bas que 40°C et une très mauvaise tenue à la corrosion acide.
Tableau 2 - Résultats des essais
|
Nuance |
CBS |
UM |
Bs20°C (G) |
Tc (°C) |
Iox (mA) |
a20-100 (10-6/°C.) |
Inv. |
SV285mod-1 |
- |
++ |
9560 |
205 |
4,5 |
4,2 |
Inv. |
SV285mod-6 |
- |
++ |
12410 |
238 |
3,9 |
3,05 |
Inv. |
SV287-1 |
- |
++ |
8420 |
152 |
4,5 |
5,3 |
Inv. |
SV287-5 |
- |
++ |
9780 |
198 |
4,04 |
4,1 |
Inv. |
SV302mod-1 |
- |
++ |
9820 |
199 |
4,5 |
4,8 |
Inv. |
SV302mod-2 |
- |
++ |
7580 |
154 |
4,6 |
6,3 |
Inv. |
SV302mod-3 |
- |
++ |
5210 |
104 |
4,6 |
7,8 |
Inv. |
SV298-1 |
- |
++ |
5030 |
104 |
2,9 |
11 |
Inv. |
SV298-4 |
- |
++ |
6810 |
137 |
2,8 |
8,3 |
Inv. |
SV315-3 |
- |
++ |
9520 |
174 |
1,3 |
4,5 |
Inv. |
SV317-1 |
- |
++ |
11100 |
204 |
1,5 |
2,4 |
Inv. |
SV323-6 |
- |
++ |
4400 |
78 |
1,6 |
4,5 |
Inv. |
SV300-2 |
- |
++ |
1970 |
37 |
1,9 |
NR |
Comp. |
A |
- |
++ |
1650 |
25 |
4,5 |
NR |
Comp. |
SV297-1 |
- |
++ |
1530 |
24 |
2,6 |
NR |
Comp. |
SV300-1 |
- |
++ |
1570 |
24 |
1,7 |
NR |
Comp. |
SV305-1 |
- |
++ |
1140 |
18 |
1,4 |
NR |
Comp. |
Fe-30Ni |
-- |
-- |
120 |
40 |
7 |
NR |
Comp. |
B |
- |
++ |
0 |
-50 |
4,9 |
NR |
Comp. |
C |
- |
++ |
0 |
-10 |
4,7 |
NR |
Comp. |
D |
- |
++ |
0 |
-50 |
3,1 |
NR |
Comp. |
E |
- |
++ |
0 |
-50 |
3,7 |
NR |
[0189] On voit aussi dans l'exemple SV298-1 qu'on peut obtenir des dilatabilités élevées
entre 20 et 100°C (11.10
-6/°C dans l'exemple) en réglant les teneurs en Ni, Cr et Cu de façon adéquate et sans
dépasser 30%Ni. Le choix de composition règle en même temps le point de Curie.
Exemple 2 - Dispositifs à autorégulation de flux magnétique
[0190] Plusieurs alliages ont été élaborés jusqu'à l'épaisseur finale de 0,6 mm afin de
caractériser les propriétés d'usage. Les alliages sont élaborés à partir de matières
pures à 99,9%, fondus au four à induction sous vide en un lingot de 50kg. Le lingot
est forgé entre 1100 et 1300°C, puis laminé à chaud jusqu'à une épaisseur de 2,5mm,
entre 1000 et 1200°C puis décapé chimiquement. La bande est ensuite laminée à froid
depuis l'épaisseur de laminé à chaud jusqu'à l'épaisseur de 0,6mm, puis recuite entre
800 et 1100°C durant 1 heure, puis dégraissée, découpée en différentes pièces ou rondelles
pour mesures puis recuit à 1100°C/3h sous H2 purifié (point de rosée<-70°C).
[0191] Les nuances testées comportent les éléments mentionnés dans le tableau suivant, le
complément étant du fer et les impuretés inévitables.
Tableau 3 - Composition des nuances d'essais
|
Nuance |
% Ni |
% Cr |
% Cu |
% Mn |
% Si |
Inv. |
TD521-2 |
28 |
0,02 |
1 |
0,02 |
0,2 |
Inv. |
TD521-3 |
28 |
0,02 |
3 |
0,02 |
0,2 |
Inv. |
TD561-1 |
26 |
2 |
10 |
0,02 |
0,2 |
Inv. |
TD565-1 |
25 |
1 |
10 |
0,02 |
0,2 |
Inv. |
TD558-1 |
28 |
2 |
3 |
0,02 |
0,2 |
Inv. |
SV289-1 |
27,8 |
2 |
1 |
0,02 |
0,2 |
Inv. |
SV297-3 |
26,2 |
1,9 |
4 |
0,02 |
0,2 |
Comp. |
SV302mod-4 |
28,2 |
0,1 |
6 |
6 |
0,3 |
Comp. |
SV297-1 |
26,9 |
1,9 |
1 |
0 |
0,2 |
Comp. |
NMHG-1 |
28 |
0 |
0 |
0 |
0,2 |
Comp. |
NMHG-2 |
29 |
0 |
0 |
0 |
0,2 |
[0192] On réalise une série de tests pour déterminer les valeurs de résistance à la corrosion
en brouillard salin, de résistance à l'usure mécanique, d'induction à saturation,
de point de Curie, de résistance à la corrosion acide et de dilatabilité entre 20
et 100°C.
[0193] Les résultats de ces tests sont rassemblés dans le tableau 4.
[0194] On voit que la plupart des alliages selon l'invention ont des points de Curie de
30°C à environ 100°C et ceci pour des alliages contenant seulement de 25 à 28%Ni selon
la tenue à la corrosion et/ou à l'oxydation désirées. Le contre-exemple SV302mod-4
ne peut convenir car il contient un pourcentage de manganèse supérieur à 2%, et une
résistance à l'usure de la couche oxydée dégradée malgré la présence de silicium.
[0195] Les contre-exemples SV297-1, NMHG-1 et NMGH-2 ne sont pas selon l'invention car ils
ne respectent pas l'équation 2. On constate que leurs températures de Curie sont inférieures
à la valeur limite de 30°C, contrairement aux exemples selon l'invention.
Tableau 4 - Résultats des essais
|
Nuance |
CBS |
UM |
Bs20°C (G) |
Tc (°C) |
Iox (mA) |
Inv. |
TD521-2 |
- |
++ |
4610 |
75 |
3,2 |
Inv. |
TD521-3 |
- |
++ |
5420 |
98 |
2,3 |
Inv. |
TD561-1 |
- |
++ |
5070 |
100 |
1,1 |
Inv. |
TD565-1 |
- |
++ |
4000 |
81 |
1,6 |
Inv. |
TD558-1 |
- |
++ |
4900 |
95 |
1,3 |
Inv. |
SV289-1 |
- |
++ |
2540 |
43 |
1,7 |
Inv. |
SV297-3 |
- |
++ |
3170 |
53 |
1,8 |
Comp. |
SV302mod-4 |
- |
+ |
3450 |
67 |
4,7 |
Comp. |
SV297-1 |
- |
++ |
1530 |
24 |
2,5 |
Comp. |
NMHG-1 |
NR |
NR |
NR |
-10 |
NR |
Comp. |
NMHG-2 |
NR |
NR |
NR |
25 |
NR |
Exemple 3 - Dispositifs à dilatation contrôlée
[0196] Plusieurs alliages ont été élaborés jusqu'à l'épaisseur finale de 0,6 mm afin de
caractériser les propriétés d'usage. Les alliages sont élaborés à partir de matières
pures à 99,9%, fondus au four à induction sous vide en un lingot de 50kg. Le lingot
est forgé entre 1100 et 1300°C, puis laminé à chaud jusqu'à une épaisseur de 2,5mm,
entre 1000 et 1200°C puis décapé chimiquement. La bande est ensuite laminée à froid
depuis l'épaisseur de laminé à chaud jusqu'à l'épaisseur de 0,6mm, puis recuite entre
800 et 1100°C durant 1 heure, puis dégraissée, découpée en différentes pièces ou rondelles
pour mesures puis recuit à 1100°C/3h sous H2 purifié (point de rosée<-70°C).
[0197] Les mesures de dilatabilité sont réalisées sur un "dilatomètre de Chevenard" entre
-196°C et 800°C.
[0198] Les nuances testées comportent les éléments mentionnés dans le tableau suivant, le
complément étant du fer et les impuretés inévitables.
Tableau 5 - Composition des nuances d'essais
|
Nuance |
%Ni |
%Cr |
%Cu |
%Mn |
%Si |
Inv. |
36 |
32,45 |
0,04 |
4 |
0,3 |
0,17 |
Comp. |
Invar® |
36 |
0 |
0 |
0,2 |
0,05 |
Inv. |
SV285mod-1 |
32,45 |
0,04 |
0,53 |
0,3 |
0,18 |
Inv. |
SV285mod-2 |
32,45 |
0,04 |
1 |
0,3 |
0,17 |
Inv. |
SV287mod3 |
31,3 |
0,04 |
1,9 |
0,3 |
0,16 |
Inv. |
SV287mod4 |
31 |
0,04 |
2,8 |
0,3 |
0,22 |
Inv. |
SV287mod5 |
30,7 |
0,04 |
3,7 |
0,3 |
0,23 |
Inv. |
SV287mod6 |
30,2 |
0,04 |
5,5 |
0,3 |
0,19 |
Inv. |
SV315-5 |
31,9 |
1,93 |
4 |
0,2 |
0,18 |
Inv. |
SV318-6 |
34,1 |
1,89 |
6 |
0,2 |
0,23 |
Comp. |
N42 |
42 |
0 |
0 |
0,2 |
0,07 |
Inv. |
SV304-4 |
28,2 |
2 |
7 |
6 |
0,17 |
Inv. |
TD561-3 |
28 |
2 |
10 |
0,3 |
0,21 |
Comp. |
N426 |
42 |
6 |
0 |
0,25 |
0,22 |
Inv. |
SV296-4 |
28,2 |
1,9 |
3 |
0,2 |
0,19 |
Inv. |
TD521-4 |
28 |
0,03 |
6 |
0,2 |
0,2 |
Inv. |
TD561-1 |
26 |
2 |
10 |
0,3 |
0,22 |
Comp. |
N485 |
48 |
6 |
0 |
0,33 |
0,06 |
Inv. |
TD558-6 |
31 |
2 |
3 |
0,24 |
0,15 |
Inv. |
TD558-7 |
32 |
2 |
3 |
0,22 |
0,12 |
Inv. |
TD558-8 |
33 |
2 |
3 |
0,21 |
0,17 |
Inv. |
TD560-3 |
30 |
0,05 |
10 |
0,26 |
0,15 |
Inv. |
TD563-6 |
31 |
1,5 |
3 |
0,22 |
0,16 |
Comp. |
Invar M93 |
36 |
0 |
0 |
0,2 |
0,03 |
[0199] On réalise une série de tests pour déterminer les valeurs de résistance à la corrosion
en brouillard salin, de résistance à l'usure mécanique, de point de Curie, de résistance
à la corrosion acide et de dilatabilité entre 20 et 100°C et entre 20 et 300°C.
[0200] Les résultats de ces tests sont rassemblés dans le tableau 6.
[0201] Les deux premiers essais correspondent à des dilatations très faibles. Les neuf suivants
ont des dilatabilités proche des semi-conducteurs tels que Si, Ge, AsGa ou SiC. Les
sept suivants ont des dilatations proches de celles des verres. Les six suivants sont
compatibles avec l'utilisation comme réservoir étanche pour le transport de gaz liquéfié
à 77K dans des cales de méthanier.
Tableau 6 - Résultats des essais
|
Nuance |
CBS |
UM |
α20-100 (10-6/°C) |
α20-300 (10-6/°C) |
α20-77K (10-6/°C) |
Ioxmax (mA) |
Inv. |
36 |
- |
++ |
2,7 |
NR |
NR |
3,9 |
Comp. |
Invar® |
-- |
0 |
1,5 |
3 |
NR |
6,2 |
Inv. |
SV285mod-1 |
- |
++ |
4,2 |
10 |
NR |
4,5 |
Inv. |
SV285mod-2 |
- |
++ |
3,9 |
9,6 |
NR |
4,4 |
Inv. |
SV287mod3 |
- |
++ |
4,5 |
10 |
NR |
4,17 |
Inv. |
SV287mod4 |
- |
++ |
4,03 |
9,6 |
NR |
4,4 |
Inv. |
SV287mod5 |
- |
++ |
4,1 |
9,4 |
NR |
4,04 |
Inv. |
SV287mod6 |
- |
++ |
4,19 |
9,1 |
NR |
3,95 |
Inv. |
SV315-5 |
- |
++ |
4,6 |
9,3 |
NR |
1,1 |
Inv. |
SV318-6 |
0 |
++ |
4,4 |
6 |
NR |
1,2 |
Comp. |
N42 |
-- |
0 |
4 |
4,3 |
NR |
5,7 |
Inv. |
SV304-4 |
- |
++ |
7,1 |
11,9 |
NR |
1,02 |
Inv. |
TD561-3 |
- |
++ |
6,7 |
11,6 |
NR |
0,9 |
Comp |
N426 |
0 |
+ |
8,3 |
NR |
NR |
NR |
Inv. |
SV296-4 |
- |
++ |
8,5 |
13,4 |
NR |
4,2 |
Inv. |
TD521-4 |
- |
++ |
9,6 |
11,9 |
NR |
2,1 |
Inv. |
TD561-1 |
- |
++ |
9,5 |
14,1 |
NR |
0,7 |
Comp. |
N485 |
0 |
+ |
9,2 |
9,3 |
NR |
NR |
Inv. |
TD558-6 |
- |
++ |
5,79 |
11,19 |
3,5 |
1,9 |
Inv. |
TD558-7 |
- |
++ |
4,58 |
9,75 |
3,05 |
1,7 |
Inv. |
TD558-8 |
- |
++ |
3,78 |
8,42 |
3 |
1,6 |
Inv. |
TD560-3 |
- |
++ |
3,99 |
7,94 |
3,68 |
3,3 |
Inv. |
TD563-6 |
- |
++ |
5,09 |
10,8 |
3,23 |
2,6 |
Comp. |
Invar M93 |
- |
+ |
<2 |
NR |
<2 |
NR |
[0202] Dans l'exemple 36, comparativement à l'Invar®, il apparaît que substituer 3,5%Ni
par 4%Cu et de faibles teneurs en Si et Cr permet de conserver une dilatabilité inférieure
à 3.10
-6/°C entre 20 et 100°C, ce qui est suffisant pour beaucoup d'application nécessitant
de limiter à la fois le coût et la dilatation vers l'ambiante comme les masques d'ombre
des écrans de tubes cathodiques à haute définition, les supports d'actionneur d'injecteur
automobile de carburant piézoélectrique, les moules massifs de pièces aéronautique
en fibre de carbone et autres, et aussi nécessitant que le matériau s'oxyde peu en
recuit industriel sous atmosphère très faiblement réductrice voire sous atmosphère
oxydante, et permet d'éviter d'utiliser une atmosphère de gaz protecteur, simplifiant
ainsi la mise en oeuvre industrielle.
[0203] Dans l'exemple SV318-6, comparativement au N42, il apparaît que substituer 8%Ni par
6%Cu et 2%Cr et une faible teneur en Si permet de conserver une dilatabilité inférieure
ou égale à 6.10
-6/°C entre 20 et 300°C, et même une dilatabilité équivalente entre 20 et 100°C ce qui
est suffisant pour la plupart des applications nécessitant de limiter à la fois le
coût et la dilatation au contact des matériaux semi-conducteurs dans une plage restreinte
de température de 100 à 300°C au dessus de l'ambiante comme les supports de circuits
intégré.
[0204] Dans les exemples SV304-4 ou TD561-3 de ce tableau, comparativement au N426 utilisé
pour sa compatibilité en dilatation avec les verres de type verres sodique au Pb,
il apparaît que substituer 14%Ni par 7 à 10%Cu et de faibles teneurs en Si et Cr permet
de conserver une dilatabilité de l'ordre de 7.10
-6/°C entre 20 et 100°C et de 11,5.10
-6/°C entre 20 et 300°C, ce qui est suffisant pour beaucoup d'application nécessitant
de limiter à la fois le coût et la dilatation au contact de certains verres, de l'alumine,
de l'oxyde de Béryllium , de certains semi-conducteurs comme l'AsGa, etc....dans une
plage restreinte de température de 100 à 300°C au dessus de l'ambiante.
[0205] Dans l'exemple TD521-4 de ce tableau, comparativement au N485, il apparaît que substituer
20%Ni par 6%Cu et moins de 2%Cr et une faible teneur en Si permet de conserver une
dilatabilité de l'ordre 9,5.10
-6/°C entre 20 et 100°C et de 11,9.10
-6/°C entre 20 et 300°C, ce qui est suffisant pour beaucoup d'application nécessitant
de limiter à la fois le coût et la dilatation au contact de ces verres très dilatables,
de ZrO2, de la forstérite, etc.....dans une plage restreinte de température de 100
à 300°C au dessus de l'ambiante.
[0206] Dans les méthaniers, on a besoin d'une très basse dilatabilité entre -196°C (température
de liquéfaction du gaz) et l'ambiante afin que les conteneurs géants du gaz liquide
résistent aux forces destructives de dilatation, en particulier aux joints triples
de soudure des conteneurs. Il apparaît sur les derniers exemples du tableau que substituer
3 à 6%Ni par 3 à 10%Cu et de faibles teneurs en Si et Cr permet de conserver une dilatabilité
de l'ordre 3 à 3,5.10
-6/°C entre -196°C et 20°C, ce qui est suffisant pour cette application nécessitant
de limiter à la fois le coût et la dilatation de la superstructure entre le gaz liquéfié
à -196°C sur une face, et la température ambiante sur l'autre face.
Exemple 4 - Capteurs de courant et transformateurs de mesure
[0207] Plusieurs alliages ont été élaborés jusqu'à l'épaisseur finale de 0,6mm afin de caractériser
les propriétés d'usage. Les alliages sont élaborés à partir de matières pures à 99,9%,
fondus au four à induction sous vide en un lingot de 50kg. Le lingot est forgé entre
1100 et 1300°C, puis laminé à chaud jusqu'à une épaisseur de 2,5mm, entre 1000 et
1200°C puis décapé chimiquement. La bande est ensuite laminée à froid sans recuit
intermédiaire depuis l'épaisseur de laminé à chaud jusqu'à l'épaisseur de 0,6mm, puis
découpée en différentes pièces ou rondelles pour mesures (voir précédemment les différents
types de caractérisation utilisés) avant dégraissage puis recuit à 1100°C pendant
3 heures sous H2 purifié (point de rosée<-70°C).
[0208] Les nuances testées comportent les éléments mentionnés dans le tableau suivant, le
complément étant du fer et les impuretés inévitables.
Tableau 7 - Composition des nuances d'essais
|
Nuance |
%Ni |
%Cr |
% Cu |
% Mn |
%Si |
Inv. |
TC768 / SP302+ |
30 |
2 |
3 |
0,3 |
0,16 |
Inv. |
SV304-2 |
29,4 |
2 |
7 |
2 |
0,19 |
Inv. |
SV314-6 |
30,3 |
1,89 |
6 |
0,2 |
0,17 |
Inv. |
SV318-6 |
34,1 |
1,89 |
6 |
0,2 |
0,16 |
Inv. |
SV290-4 |
28,2 |
2 |
3 |
0,3 |
0,16 |
Inv. |
SV296-2 |
29,2 |
1,9 |
1 |
0,2 |
0,17 |
Inv. |
SV316-4 |
33,2 |
1,95 |
3 |
0,2 |
0,18 |
Inv. |
SV317-5 |
33,8 |
1,93 |
4 |
0,2 |
0,17 |
Inv. |
SV302mod-3 |
28,8 |
0,05 |
7 |
4 |
0,17 |
Inv. |
SV298-3 |
29,1 |
0,97 |
2 |
0,2 |
0,19 |
Inv. |
SV330-4 |
27,5 |
0,03 |
3 |
0,2 |
0,18 |
Inv. |
SV330-6 |
27,5 |
0,03 |
7 |
0,2 |
0,17 |
Inv. |
SV333-2 |
29 |
0,03 |
1 |
0,2 |
0,16 |
Inv. |
SV333-5 |
29 |
0,03 |
5 |
0,2 |
0,17 |
Inv. |
SV339-2 |
29 |
0,2 |
1 |
0,2 |
0,19 |
Inv. |
SV339-5 |
29 |
0,2 |
5 |
0,2 |
0,17 |
Comp. |
SV330-8 |
27,5 |
0,03 |
13 |
0,2 |
0,18 |
Comp. |
SV333-8 |
29 |
0,03 |
13 |
0,2 |
0,18 |
Comp. |
SV339-8 |
29 |
0,2 |
13 |
0,2 |
0,15 |
[0209] On réalise une série de tests pour déterminer les valeurs de résistance à la corrosion
en brouillard salin, de résistance à l'usure mécanique, d'induction à saturation à
20°C, de rectangularité du cycle d'hystérésis à 20°C, de champ coercitif à 20°C, de
résistivité électrique à 20°C et de résistance à la corrosion acide.
[0210] Les résultats de ces tests sont rassemblés dans le tableau 8.
Tableau 8 - Résultats des essais
|
Nuance |
CBS |
UM |
Bs20°C (G) |
Br/Bm |
Hc (mOe) |
ρ-elec (µΩ.cm) |
Iox (mA) |
Inv. |
TC768 / SP302+ |
- |
++ |
7380 |
NR |
41 |
88,6 |
1,3 |
Inv. |
SV304-2 |
0 |
++ |
6310 |
0,32 |
32 |
85 |
0,9 |
Inv. |
SV314-6 |
0 |
++ |
9190 |
0,33 |
34 |
86 |
1,2 |
Inv. |
SV318-6 |
0 |
++ |
11960 |
0,34 |
31 |
82 |
1,2 |
Inv. |
SV290-4 |
0 |
++ |
5180 |
0,41 |
25 |
87 |
4,2 |
Inv. |
SV296-2 |
0 |
++ |
5560 |
0,47 |
30 |
87,5 |
4,1 |
Inv. |
SV316-4 |
0 |
++ |
10620 |
0,34 |
37 |
87 |
1,3 |
Inv. |
SV317-5 |
0 |
++ |
11540 |
0,35 |
34 |
86,5 |
1,1 |
Inv. |
SV302mod-3 |
0 |
++ |
5210 |
0,32 |
21 |
75 |
4,6 |
Inv. |
SV298-3 |
0 |
++ |
6170 |
0,43 |
32 |
87 |
2,8 |
Inv. |
SV330-4 |
- |
++ |
4430 |
NR |
19 |
87 |
4,9 |
Inv. |
SV330-6 |
- |
++ |
6800 |
NR |
33 |
88 |
4,7 |
Inv. |
SV333-2 |
- |
++ |
4250 |
NR |
18 |
85 |
4,6 |
Inv. |
SV333-5 |
- |
++ |
8360 |
NR |
43 |
90 |
4,4 |
Inv. |
SV339-2 |
- |
++ |
4300 |
NR |
20 |
85 |
3,7 |
Inv. |
SV339-5 |
- |
++ |
8430 |
NR |
40 |
90 |
3,4 |
Comp. |
SV330-8 |
- |
++ |
8340 |
NR |
270 |
76 |
4,4 |
Comp. |
SV333-8 |
- |
++ |
9970 |
NR |
330 |
78 |
4,2 |
Comp. |
SV339-8 |
- |
++ |
10070 |
NR |
364 |
78 |
3,1 |
[0211] On observe que les alliages comportant plus de 10%Cu présentent des champs coercitifs
très élevés de 200 à 400mOe incompatibles avec une application de type transformateur
de mesure.
[0212] L'alliage SV330-4 est particulièrement économique avec ses 28%Ni et 3%Cu, avec une
très bas Hc de 19mOe permettant une grande précision du transformateur de mesure,
en revanche sa basse saturation (4430G) le restreint à des applications vers la température
ambiante.
[0213] Dans un autre exemple de l'invention, l'alliage SV330-6 est presque aussi économique
avec 28%Ni et 7%Cu et permettant une bonne précision de capteur de courant à boucle
fermée grâce à Hc=33mOe ; de plus sa saturation plus élevée (6800G) le rend nettement
plus stable en température et permettra un fonctionnement du transformateur de mesure
jusqu'à 70°C.
[0214] Dans un dernier exemple l'alliage SV317-5 à saturation élevée (11540G) et faible
champ coercitif (34mOe) permet la réalisation de capteur de courant en boucle ouverte
de grande précision , et de façon économique (34%Ni) tout en garantissant une bonne
tenue à la corrosion dans de nombreux milieux grâce à la conjonction de 2%Cr et 4%Cu
associés au silicium.
Exemple 5 - Capteurs magnéto-harmoniques
[0215] Plusieurs alliages ont été élaborés jusqu'à l'épaisseur finale de 0,04 mm afin de
caractériser les propriétés d'usage. Les alliages sont élaborés à partir de matières
pures à 99,9%, fondus au four à induction sous vide en un lingot de 50kg. Le lingot
est forgé entre 1100 et 1300°C, puis laminé à chaud jusqu'à une épaisseur de 2,5mm,
entre 1000 et 1200°C puis décapé chimiquement. La bande est ensuite laminée à froid
depuis l'épaisseur de laminé à chaud jusqu'à l'épaisseur de 0,6mm, puis recuite entre
800 et 1100°C durant 1 heure, puis laminée jusqu'à l'épaisseur finale de 40µm puis
dégraissée, découpée en différentes pièces ou tores enroulés pour mesures puis recuit
à 1100°C pendant 3 heures sous H2 purifié (point de rosée<-70°C).
[0216] Les nuances testées comportent les éléments mentionnés dans le tableau suivant, le
complément étant du fer et les impuretés inévitables.
Tableau 9 - Composition des nuances d'essais
|
Nuance |
%Ni |
%Cr |
%Cu |
%Mn |
%Si |
Inv. |
SV292-3 |
29,9 |
0,5 |
0,5 |
0,3 |
0,22 |
Inv. |
SV323-6 |
33 |
1,9 |
0,6 |
3,8 |
0,23 |
Inv. |
SV289-3 |
27 |
1,99 |
3,85 |
0,3 |
0,25 |
Inv. |
SV290-3 |
28,4 |
2 |
2 |
0,3 |
0,23 |
Inv. |
SV296-1 |
29,3 |
1,9 |
0,5 |
0,2 |
0,24 |
Inv. |
SV306-4 |
28,3 |
3,9 |
3 |
0,2 |
0,25 |
Inv. |
SV289-4 |
26,5 |
1,98 |
5,6 |
0,3 |
0,24 |
Inv. |
SV304-3 |
28,8 |
2 |
7 |
4 |
0,24 |
[0217] On réalise une série de tests pour déterminer les valeurs de résistance à la corrosion
en brouillard salin, de résistance à l'usure mécanique, d'induction à saturation à
20°C, de champ coercitif à 20°C, de résistivité électrique à 20°C et de résistance
à la corrosion acide.
[0218] Les résultats de ces tests sont rassemblés dans le tableau 10.
Tableau 10 - Résultats des essais
|
Nuance |
CBS |
UM |
Bs20°C (G) |
Hc (mOe) |
r elec (µΩ.cm) |
Iox (mA) |
Inv. |
SV292-3 |
- |
++ |
4960 |
46 |
84 |
4,3 |
Inv. |
SV323-6 |
- |
++ |
4400 |
15 |
84,5 |
1,6 |
Inv. |
SV289-3 |
- |
++ |
4470 |
18 |
88,5 |
3,9 |
Inv. |
SV290-3 |
- |
++ |
4580 |
19 |
86 |
4,3 |
Inv. |
SV296-1 |
- |
++ |
4820 |
23 |
85 |
4,1 |
Inv. |
SV306-4 |
0 |
++ |
4480 |
18 |
88 |
3,6 |
Inv. |
SV289-4 |
- |
++ |
4720 |
31 |
87 |
1,1 |
Inv. |
SV304-3 |
- |
++ |
4380 |
21 |
86,5 |
0,93 |
[0219] L'exemple de l'invention SV323-6 présente une tenue à la corrosion en milieu aqueux
très améliorée et la sensibilité du capteur est excellente (Hc=15mOe).
[0220] Dans l'exemple SV306-4, la teneur en nickel est abaissée vers 28% tandis que les
tenues à la corrosion, à la corrosion sous brouillard salin, à l'oxydation en atmosphère
chaude et oxydante sont toutes excellentes ainsi que la sensibilité du capteur (Hc=18mOe)
: ceci est permis grâce à une optimisation des compositions relatives en Ni, Cr, Cu
, Mn et Si. Le coût du capteur peut être encore sensiblement abaissé dans l'exemple
SV289-4 avec seulement 26,5%Ni grâce à une forte présence de cuivre (5,6%) permettant
de conserver de bonnes tenues à la corrosion et à l'oxydation, et une très bonne sensibilité
du capteur (Hc=31mOe).
Exemple 6 - Moteurs et actionneurs électromagnétiques
[0221] Plusieurs alliages ont été élaborés jusqu'à l'épaisseur finale de 0,6mm afin de caractériser
les propriétés d'usage. Les alliages sont élaborés à partir de matières pures à 99,9%,
fondus au four à induction sous vide en un lingot de 50kg. Le lingot est forgé entre
1100 et 1300°C, puis laminé à chaud jusqu'à une épaisseur de 2,5mm, entre 1000 et
1200°C puis décapé chimiquement. La bande est ensuite laminée à froid sans recuit
intermédiaire depuis l'épaisseur de laminé à chaud jusqu'à l'épaisseur de 0,6mm, puis
découpée en différentes pièces ou rondelles pour mesures avant dégraissage puis recuit
à 1100°C pendant 3 heures sous H2 purifié (point de rosée<-70°C).
[0222] Les nuances testées comportent les éléments mentionnés dans le tableau suivant, le
complément étant du fer et les impuretés inévitables.
Tableau 11 - Composition des nuances d'essais
|
Nuance |
%Ni |
%Cr |
%Cu |
%Mn |
% Si |
%S (ppm) |
%B (ppm) |
Inv. |
TD560-1 |
28 |
0,04 |
10 |
0,2 |
0,23 |
23 |
4 |
Inv. |
TD560-3 |
30 |
0,04 |
10 |
0,2 |
0,26 |
32 |
0 |
Inv. |
TD560-5 |
32 |
0,04 |
10 |
0,2 |
0,28 |
29 |
0 |
Inv. |
TD560-7 |
34 |
0,04 |
10 |
0,2 |
0,23 |
27 |
0 |
Inv. |
TD560-8 |
35 |
0,04 |
10 |
0,2 |
0,23 |
24 |
5 |
Inv. |
TD561-3 |
28 |
2 |
10 |
0,2 |
0,26 |
28 |
0 |
Inv. |
TD561-5 |
30 |
2 |
10 |
0,2 |
0,26 |
29 |
0 |
Inv. |
TD561-7 |
32 |
2 |
10 |
0,2 |
0,23 |
31 |
7 |
Inv. |
TD565-6 |
34 |
2 |
10 |
0,2 |
0,22 |
33 |
8 |
Comp. |
SV292-4mod |
29 |
0,5 |
0,9 |
0,3 |
0,24 |
16 |
5 |
Comp. |
SV304-2mod |
29,4 |
2 |
7 |
4,5 |
0,24 |
18 |
0 |
[0223] On réalise une série de tests pour déterminer les valeurs de résistance à la corrosion
en brouillard salin, de résistance à l'usure mécanique, d'induction à saturation à
20°C, de champ coercitif à 20°C, de résistivité électrique à 20°C et de résistance
à la corrosion acide.
[0224] Les résultats de ces tests sont rassemblés dans le tableau 12.
[0225] On voit que les propriétés de sensibilité à la corrosion sous brouillard salin et
de tenue à l'usure mécanique de la couche oxydée de surface sont toujours bonnes pourvu
que les minima de Cr, Si et Cu soient respectés.
Tableau 12 - Résultats des essais
|
Nuance |
CBS |
UM |
Bs20°C (G) |
Hc (mOe) |
Br/Bm |
µmaxCC |
Inv. |
TD560-1 |
- |
++ |
7950 |
70 |
0,17 |
6000 |
Inv. |
TD560-3 |
- |
++ |
10300 |
62 |
0,17 |
8500 |
Inv. |
TD560-5 |
- |
++ |
12300 |
55 |
0,17 |
11000 |
Inv. |
TD560-7 |
- |
++ |
13300 |
51 |
0,19 |
15000 |
Inv. |
TD560-8 |
- |
++ |
13700 |
NR |
NR |
16000 |
Inv. |
TD561-3 |
- |
++ |
7000 |
76 |
0,22 |
6000 |
Inv. |
TD561-5 |
0 |
++ |
9200 |
72 |
0,22 |
8500 |
Inv. |
TD561-7 |
0 |
++ |
10700 |
56 |
0,23 |
12500 |
Inv. |
TD565-6 |
0 |
++ |
11800 |
46 |
0,30 |
20500 |
Comp. |
SV292-4mod |
- |
++ |
4800 |
55 |
NR |
NR |
Comp. |
SV304-2mod |
0 |
++ |
4080 |
21 |
NR |
NR |
[0226] De nombreux alliages aux compositions variées de 28 à 34% de nickel permettent l'obtention
de saturations magnétiques de 5000 à 12 000G, et des résistivités électriques de 80
à 90µΩ.cm, tout en maintenant des champs coercitifs bas et des tenues à la corrosion
variées selon le besoin précis de l'application.
[0227] En contre-exemple l'alliage SV292-4mod ne vérifie pas l'équation 2, ce qui se traduit
par saturation trop basse (4800G) liée à un %Cu insuffisant vis à vis de la teneur
en Nickel. Dans un autre contre-exemple l'alliage SV304-2mod ne vérifie pas l'invention
puisque sa saturation est beaucoup trop basse (4080G au lieu du minimum de 5000G),
ce qui est du à sa trop forte teneur en manganèse.
[0228] L'alliage TD560-8 présente 35%Ni et une haute saturation. On a mesuré sa perméabilité
µmax suivant les directions 0°, 45° et 90° par rapport à la direction de laminage.
On obtient respectivement, 19000, 17200 et 17600, ce qui montre que l'alliage est
presque parfaitement isotrope grâce à la succession de laminage poussé et de recuit
final à haute température. Par cette propriété le flux magnétique circulera de façon
isotrope et ne privilégiera pas certaines directions de la tôle, origine fréquente
de fluctuation de couple électromagnétique dans les machines électriques. Les alliages
selon l'invention ont donc aussi la propriété, au travers des laminages à froid et
recuit appropriés, de pouvoir présenter si besoin une bonne isotropie des propriétés
magnétiques.
[0229] On observe également que les alliages selon l'invention présentent une faible rémanence
(rectangularité du cycle d'hystérésis Br/Bm < 0,3) ce qui permet soit de se désaimanter
en grande partie naturellement dés que l'excitation est coupée (« défluxage » naturel),
soit de ne pas être sensible aux champs parasites perturbateurs (champs superposés,
surintensité très forte et très fugitive qui sature le matériau pendant très peu de
temps). On note en particulier qu'il est avantageux de baisser le %Nickel et le %chrome
pour abaisser la rectangularité Br/Bm à de très faibles valeurs telles que 0,17 sur
les alliages TD560-1, 3 et 5 contenant un minimum de %Cr, 28 à 32%Ni et 10%Cu.
Exemple 7 - Stators pour moteurs d'horlogerie
[0230] Plusieurs alliages ont été élaborés jusqu'à l'épaisseur finale de 0,6mm afin de caractériser
les propriétés d'usage. Les alliages sont élaborés à partir de matières pures à 99,9%,
fondus au four à induction sous vide en un lingot de 50kg. Le lingot est forgé entre
1100 et 1300°C, puis laminé à chaud jusqu'à une épaisseur de 2,5mm, entre 1000 et
1200°C puis décapé chimiquement. La bande est ensuite laminée à froid sans recuit
intermédiaire depuis l'épaisseur de laminé à chaud jusqu'à l'épaisseur de 0,6mm, puis
découpée en différentes pièces ou rondelles pour mesures avant dégraissage puis recuit
à 1100°C pendant 3 heures sous H2 purifié (point de rosée<-70°C).
[0231] Les nuances testées comportent les éléments mentionnés dans le tableau suivant, le
complément étant du fer et les impuretés inévitables.
Tableau 13 - Composition des nuances d'essais
|
Nuance |
%Ni |
%Cr |
%Co |
%Cu |
%Mn |
%Si |
%S |
%B |
%O+N |
Inv. |
TC767 |
31,7 |
8 |
0,01 |
2,97 |
0,32 |
0,2 |
19 |
0 |
59 |
Inv. |
TD521mod |
28 |
0,03 |
0 |
5,5 |
0,2 |
0,22 |
24 |
0 |
59 |
Inv. |
SV302mod2 |
29,4 |
0,05 |
0 |
7 |
2 |
0,25 |
12 |
0 |
64 |
Inv. |
SV292-5 |
29,2 |
0,5 |
0 |
2,8 |
0,3 |
0,23 |
17 |
0 |
58 |
Inv. |
SV292-6 |
28,6 |
0,5 |
0 |
4,5 |
0,3 |
0,19 |
19 |
4 |
73 |
Inv. |
SV298-4 |
28,9 |
0,97 |
0 |
3 |
0,2 |
0,11 |
36 |
8 |
59 |
Inv. |
SV298-5 |
28,6 |
0,96 |
0 |
4 |
0,2 |
0,22 |
24 |
5 |
67 |
Inv. |
SV296-4 |
28,2 |
1,9 |
0 |
3 |
0,2 |
0,24 |
9 |
7 |
58 |
Inv. |
SV304-2 |
29,4 |
2 |
0 |
7 |
0,2 |
0,23 |
25 |
0 |
48 |
Inv. |
SV316-6 |
32,2 |
1,89 |
0 |
6 |
0,2 |
0,19 |
24 |
0 |
59 |
Inv. |
TD561-3 |
28 |
2 |
0 |
10 |
0,3 |
0,2 |
28 |
0 |
56 |
Comp. |
SV306-6 |
27,4 |
3,8 |
0 |
6 |
0,28 |
0,2 |
25 |
8 |
84 |
Comp. |
TC757 |
31,8 |
8,2 |
3,07 |
0,06 |
0,24 |
0,2 |
23 |
0 |
67 |
Comp. |
SV298-1 |
29,4 |
1 |
0 |
0,5 |
0,43 |
0,2 |
27 |
5 |
61 |
Comp. |
SV288-2 |
29,5 |
1 |
0 |
1 |
0,32 |
0,3 |
25 |
7 |
48 |
Comp. |
SV299-6 |
28,2 |
4,7 |
0 |
2,95 |
0,35 |
0,3 |
23 |
0 |
70 |
Comp. |
SV301-1 |
30 |
0 |
0 |
0,1 |
0,32 |
0,2 |
24 |
0 |
75 |
Comp. |
22 bis |
30 |
0,1 |
0 |
0,2 |
3,5 |
0,17 |
15 |
5 |
58 |
[0232] Le point de Curie est déterminé par un aller-retour du thermomagnétomètre jusqu'à
une température de 800°C.
[0233] On réalise aussi une série de tests pour déterminer les valeurs de résistance à la
corrosion en brouillard salin, de résistance à l'usure mécanique, de résistivité électrique
à 20°C, de point de Curie, le champ coercitif à 20°C, d'induction à saturation à 20°C
et d'induction à saturation à 60°C.
[0234] Les résultats de ces tests sont rassemblés dans le tableau 14.
Tableau 14 - Résultats des essais
|
Nuance |
CBS |
UM |
ρel (µΩ.cm) |
Tc (°C) |
Hc (mOe) |
Bs20°C (G) |
Bs60°C (G) |
Inv. |
TD521mod |
- |
++ |
85 |
156 |
48 |
7430 |
5500 |
Inv. |
SV302mod2 |
- |
++ |
83 |
154 |
44 |
7580 |
5700 |
Inv. |
SV292-5 |
- |
++ |
86,5 |
137 |
64 |
6700 |
4300 |
Inv. |
SV292-6 |
- |
++ |
86,5 |
154 |
70 |
7530 |
5600 |
Inv. |
SV298-4 |
- |
++ |
87,5 |
137 |
38 |
6810 |
4700 |
Inv. |
SV298-5 |
- |
++ |
87,5 |
144 |
46 |
7150 |
4900 |
Inv. |
SV296-4 |
- |
++ |
86,7 |
112 |
41 |
6310 |
4100 |
Inv. |
SV304-2 |
0 |
++ |
85 |
111 |
32 |
6310 |
4150 |
Inv. |
SV316-6 |
0 |
++ |
85 |
211 |
38 |
10810 |
9500 |
Inv. |
TD561-3 |
0 |
++ |
82 |
131 |
76 |
7450 |
5200 |
Comp. |
SV306-6 |
- |
++ |
NR |
93 |
NR |
5060 |
NR |
Comp. |
TC757 |
0 |
+ |
NR |
95 |
NR |
5470 |
4630 |
Comp. |
SV298-1 |
- |
++ |
NR |
92 |
NR |
5030 |
NR |
Comp. |
SV288-2 |
- |
++ |
NR |
98 |
NR |
5510 |
NR |
Comp. |
SV299-6 |
0 |
++ |
NR |
80 |
NR |
4520 |
NR |
Comp. |
SV301-1 |
-- |
++ |
NR |
76 |
NR |
4300 |
NR |
Comp. |
22 bis |
- |
++ |
83 |
76 |
22 |
4300 |
2200 |
Exemple 8 - Inductance et transformateur pour l'électronique de puissance
[0235] Plusieurs alliages ont été élaborés jusqu'à l'épaisseur finale de 0,6 mm afin de
caractériser les propriétés d'usage. Les alliages sont élaborés à partir de matières
pures à 99,9%, fondus au four à induction sous vide en un lingot de 50kg. Le lingot
est forgé entre 1100 et 1300°C, puis laminé à chaud jusqu'à une épaisseur de 2,5mm,
entre 1000 et 1200°C puis décapé chimiquement. La bande est ensuite laminée à froid
depuis l'épaisseur de laminé à chaud jusqu'à l'épaisseur de 0,6mm, puis recuite entre
800 et 1100°C durant 1 heure, puis dégraissée, laminée à froid jusqu'à l'épaisseur
0,05mm, cisaillée, enduite d'un isolant minéral pour éviter le collage des sires au
cours du recuit et enroulée en tores de diamètres 30x20mm, hauteur 20mm, puis recuit
à 1100°C/3h sous H2 purifié (point de rosée<-70°C).
[0236] Les nuances testées comportent les éléments mentionnés dans le tableau suivant, le
complément étant du fer et les impuretés inévitables.
Tableau 15 - Composition des nuances d'essais
|
Nuance |
%Ni |
%Cr |
%Cu |
%Mn |
Inv. |
TD521-4 |
28 |
0,03 |
6 |
0,2 |
Inv. |
SV287-1 |
31,8 |
0,04 |
0,5 |
0,3 |
Inv. |
SV302mod-2 |
29,4 |
0,05 |
7 |
2 |
Inv. |
SV292-6 |
28,6 |
0,5 |
4,5 |
0,3 |
Inv. |
SV298-6 |
28,05 |
0,95 |
6 |
0,2 |
Inv. |
15 |
33,78 |
1,02 |
0,13 |
0,18 |
Inv. |
SV304-1 |
30 |
2 |
7 |
0,1 |
Inv. |
SV313-6 |
29,3 |
1,89 |
6 |
0,2 |
Inv. |
SV326-6 |
28,4 |
1,88 |
6 |
0,2 |
Inv. |
TD561-4 |
29 |
2 |
10 |
0,3 |
Inv. |
SV302mod-1 |
30 |
0,05 |
7 |
0,2 |
Inv. |
SV315-3 |
32,5 |
1,97 |
2 |
0,2 |
Inv. |
SV317-3 |
34,5 |
1,97 |
2 |
0,2 |
Inv. |
SV314-6 |
30,3 |
1,89 |
6 |
0,2 |
Inv. |
SV317-6 |
33,1 |
1,89 |
6 |
0,2 |
Inv. |
TD561-5 |
30 |
2 |
10 |
0,3 |
Comp. |
SV301mod-1 |
30 |
0,05 |
0,15 |
0,2 |
Comp. |
SV292-1 |
29,9 |
0,5 |
0,12 |
0,3 |
Comp. |
TC768 |
30 |
2 |
3 |
0,3 |
[0237] On réalise une série de tests pour déterminer les valeurs d'induction à saturation
à 20°C, de point de Curie, de champ coercitif à 20°C, de résistivité électrique à
20°C et de résistance à la corrosion acide.
[0238] Les résultats de ces tests sont rassemblés dans le tableau 16.
Tableau 16 - Résultats des essais
|
Nuance |
Bs20°C (G) |
Tc (°C) |
Hc (mOe) |
ρel (µΩ.cm) |
IOX (mA) |
Inv. |
TD521-4 |
8030 |
156 |
71 |
84,5 |
2,1 |
Inv. |
SV287-1 |
8420 |
152 |
41 |
83 |
4,5 |
Inv. |
SV302mod-2 |
7580 |
154 |
44 |
84 |
4,6 |
Inv. |
SV292-6 |
7530 |
154 |
70 |
87 |
3,9 |
Inv. |
SV298-6 |
7590 |
153 |
57 |
85,5 |
2,4 |
Inv. |
15 |
8150 |
159 |
42,5 |
81 |
2,5 |
Inv. |
SV304-1 |
8530 |
163 |
48 |
85 |
0,85 |
Inv. |
SV313-6 |
8320 |
161 |
33 |
86,5 |
1,2 |
Inv. |
SV326-6 |
8490 |
168 |
55 |
86,5 |
2,9 |
Inv. |
TD561-4 |
8490 |
178 |
75 |
80,5 |
0,9 |
Inv. |
SV302mod-1 |
9820 |
199 |
75 |
85 |
4,5 |
Inv. |
SV315-3 |
9520 |
174 |
39 |
87 |
1,3 |
Inv. |
SV317-3 |
11360 |
205 |
38,5 |
85 |
1,3 |
Inv. |
SV314-6 |
9190 |
183 |
34 |
86 |
1,2 |
Inv. |
SV317-6 |
11470 |
229 |
36 |
84,5 |
1,2 |
Inv. |
TD561-5 |
9370 |
178 |
70 |
81 |
0,9 |
Comp. |
SV301mod-1 |
4300 |
86 |
23 |
81 |
4,5 |
Comp. |
SV292-1 |
4490 |
90 |
36 |
81,5 |
4,4 |
Comp. |
TC768 |
7380 |
118 |
41 |
88,6 |
1,3 |
[0239] On voit que tous les alliages selon l'invention ont au moins 80µΩ.cm de résistivité
électrique à 20°C et un champ coercitif de moins de 75mOe, et en général de moins
de 41mOe à 20°C: ces performances associées à une faible épaisseur et une bonne isolation
inter-spire garantissent de faibles pertes magnétiques, d'autant plus admissible dans
ces noyaux magnétiques de composants magnétiques passifs que leur bonne conduction
thermique permet d'extraire aisément ces pertes magnétiques.
[0240] On voit dans les contre-exemples SV301mod-1, SV292-1 et TC768 que la balance entre
%Ni et %Cu doit être bien assurée pour que la saturation soit suffisante, c'est à
dire pour que le dimensionnement du circuit magnétique amène à un volume suffisamment
intéressant vis à vis des ferrites.
Exemple 9 - Bilames
[0241] Plusieurs alliages ont été élaborés jusqu'à l'épaisseur finale de 0,6 mm afin de
caractériser les propriétés d'usage. Les alliages sont élaborés à partir de matières
pures à 99,9%, fondus au four à induction sous vide en un lingot de 50kg. Le lingot
est forgé entre 1100 et 1300°C, puis laminé à chaud jusqu'à une épaisseur de 2,5mm,
entre 1000 et 1200°C puis décapé chimiquement. La bande est ensuite laminée à froid
jusqu'à l'épaisseur 0,6mm, puis recuite entre 800 et 1100°C durant 1h, puis dégraissée,
découpée en différentes pièces ou rondelles pour mesures puis recuit à 1100°C pendant
3h sous H2 purifié (point de rosée<-70°C).
[0242] Les nuances testées comportent les éléments mentionnés dans le tableau suivant, le
complément étant du fer et les impuretés inévitables.
Tableau 17 - Composition des nuances d'essais
|
Nuance |
%Ni |
%Cr |
%Cu |
%Mn |
Inv. |
SV285mod-3 |
32 |
0,04 |
2 |
0,3 |
Inv. |
SV285mod-5 |
32 |
0,04 |
4 |
0,3 |
Inv. |
SV287-5 |
31 |
0,04 |
3,7 |
0,2 |
Inv. |
SV316-6 |
32 |
1,89 |
6 |
0,2 |
Inv. |
TD561-6 |
31 |
2 |
10 |
0,3 |
Inv. |
TD561-8 |
33 |
2 |
10 |
0,3 |
Comp. |
Invar |
36 |
0 |
0 |
0,2 |
Comp. |
N42 |
42 |
0 |
0 |
0,2 |
Comp. |
SV285mod-1 |
32 |
0,04 |
0,53 |
0,3 |
Comp. |
SV285mod-7 |
32 |
0,04 |
0,01 |
0,3 |
Comp. |
SV287-1 |
32 |
0,04 |
0,5 |
0,2 |
Comp. |
TD521-1 |
28 |
0,03 |
0,12 |
0,2 |
Comp. |
TD521-4 |
28 |
0,03 |
6 |
0,2 |
[0243] On réalise une série de tests pour déterminer les valeurs de résistance à la corrosion
en brouillard salin, de résistance à l'usure mécanique, de point de Curie, de résistivité
électrique à 20°C, de coefficient de dilatation entre 20 et 200°C et entre 20 et 300°C.
[0244] Les résultats de ces tests sont rassemblés dans le tableau 18.
Tableau 18 - Résultats des essais
|
Nuance |
CBS |
UM |
Tc (°C) |
ρel (µΩ. cm) |
α20-100 (10-6/°C) |
α20-300 (10-6/°C) |
Inv. |
SV285mod-3 |
- |
++ |
211 |
85 |
3,1 |
8,7 |
Inv. |
SV285mod-5 |
- |
++ |
229 |
85,8 |
2,7 |
6,9 |
Inv. |
SV287-5 |
- |
++ |
198 |
86,5 |
4,1 |
9,4 |
Inv. |
SV316-6 |
0 |
++ |
211 |
85 |
4,8 |
8,3 |
Inv. |
TD561-6 |
0 |
++ |
204 |
80,1 |
5,1 |
8,5 |
Inv. |
TD561-8 |
0 |
++ |
247 |
78,7 |
5,6 |
7,4 |
Comp. |
Invar |
-- |
++ |
250 |
75 |
1,5 |
6 |
Comp. |
N42 |
-- |
++ |
330 |
63 |
4 |
4,3 |
Comp. |
SV285mod-1 |
- |
++ |
205 |
84 |
4,2 |
10,1 |
Comp. |
SV285mod-7 |
- |
++ |
185 |
83,5 |
4,9 |
10,7 |
Comp. |
SV287-1 |
- |
++ |
152 |
83 |
5,3 |
10,9 |
Comp. |
TD521-1 |
- |
++ |
-10 |
82 |
16,8 |
18,5 |
Comp. |
TD521-4 |
- |
++ |
156 |
84,5 |
9,6 |
11,9 |
Exemple 10 - Noyaux de bobines de moteurs d'horlogerie et relais électromagnétique
à haute sensibilité
[0245] Plusieurs alliages ont été élaborés jusqu'à l'épaisseur finale de 0,6mm afin de caractériser
les propriétés d'usage. Les alliages sont élaborés à partir de matières pures à 99,9%,
fondus au four à induction sous vide en un lingot de 50kg. Le lingot est forgé entre
1100 et 1300°C, puis laminé à chaud jusqu'à une épaisseur de 2,5mm, entre 1000 et
1200°C puis décapé chimiquement. La bande est ensuite laminée à froid sans recuit
intermédiaire depuis l'épaisseur de laminé à chaud jusqu'à l'épaisseur de 0,6mm, puis
découpée en différentes pièces ou rondelles pour mesures avant dégraissage puis recuit
à 1100°C pendant 3 heures sous H2 purifié (point de rosée<-70°C).
[0246] Les nuances testées comportent les éléments mentionnés dans le tableau suivant, le
complément étant du fer et les impuretés inévitables.
Tableau 19 - Composition des nuances d'essais
|
Nuance |
%Ni |
%Cr |
%Cu |
%Mn |
%Si |
Inv. |
SV285-3 |
31,8 |
0,04 |
2 |
0,3 |
0,21 |
Inv. |
SV287-6 |
30,2 |
0,04 |
5,5 |
0,3 |
0,23 |
Inv. |
SV315-5 |
31,9 |
1,93 |
4 |
0,2 |
0,26 |
Inv. |
SV315-6 |
31,2 |
1,89 |
6 |
0,2 |
0,26 |
Inv. |
TD561-6 |
31 |
2 |
10 |
0,3 |
0,24 |
Inv. |
SV288-1 |
35,8 |
0,05 |
0,5 |
0,3 |
0,23 |
Inv. |
SV288-4 |
34,9 |
0,05 |
2,9 |
0,3 |
0,26 |
Inv. |
SV288-6 |
34 |
0,05 |
5,6 |
0,3 |
0,25 |
Inv. |
SV285mod-4 |
32,45 |
0,04 |
3 |
0,3 |
0,35 |
Inv. |
SV285mod-6 |
32,45 |
0,04 |
6 |
0,3 |
0,38 |
Inv. |
SV316-3 |
33,5 |
1,97 |
2 |
0,2 |
0,33 |
Inv. |
SV316-5 |
33,2 |
1,93 |
4 |
0,2 |
0,37 |
Inv. |
SV317-2 |
34,8 |
1,99 |
1 |
0,2 |
0,35 |
Inv. |
SV317-4 |
34,1 |
1,95 |
3 |
0,2 |
0,36 |
Inv. |
SV316-6 |
32,2 |
1,89 |
6 |
0,2 |
0,35 |
Inv. |
TD561-8 |
33 |
2 |
10 |
0,3 |
0,34 |
Inv. |
SV288-5 |
34,6 |
0,05 |
3,8 |
0,21 |
0,23 |
Inv. |
SV288-6 |
34 |
0,05 |
5,6 |
0,23 |
0,43 |
Inv. |
SV560-6 |
33 |
0,1 |
10 |
0,2 |
0,35 |
Inv. |
SV560-9 |
35,95 |
0,05 |
10 |
0,2 |
0,19 |
Inv. |
SV316-1 |
34 |
2 |
0,5 |
0,2 |
0,32 |
Comp. |
TC661 |
33,8 |
5 |
2 |
0,15 |
0,22 |
[0247] On réalise une série de tests pour déterminer les valeurs de résistance à la corrosion
en brouillard salin, de résistance à l'usure mécanique, de résistivité électrique
à 20°C, de point de Curie, d'induction à saturation à 20°C, de champ coercitif à 20°C
et de résistance à la corrosion acide.
[0248] Les résultats de ces tests sont rassemblés dans le tableau 20.
[0249] On voit qu'on peut obtenir une saturation de 10 000G à 20°C avec seulement 30%Ni,
et une saturation de 13 000G à 20°C avec seulement 34%Ni.
[0250] Ces performances sont tout à fait intéressantes et innovantes, en plus des propriétés
de bonne tenue à la corrosion et à l'usure mécanique de la couche oxydée.
Tableau 20 - Résultats des essais
|
Nuance |
CBS |
UM |
relec (µΩ. cm) |
Tc (°C) |
Bs20°C (G) |
Hc (mOe) |
lox (mA) |
Inv. |
SV285-3 |
- |
++ |
85 |
198 |
10050 |
53 |
4,4 |
Inv. |
SV287-6 |
- |
++ |
84,5 |
202 |
10010 |
72 |
3,95 |
Inv. |
SV315-5 |
0 |
++ |
88 |
189 |
10020 |
42 |
1,1 |
Inv. |
SV315-6 |
0 |
++ |
85,5 |
197 |
10050 |
43 |
1,2 |
Inv. |
TD561-6 |
0 |
++ |
80 |
204 |
10090 |
65 |
0,8 |
Inv. |
SV288-1 |
- |
++ |
65 |
NR |
13230 |
88 |
4,1 |
Inv. |
SV288-4 |
- |
++ |
75 |
NR |
13430 |
71 |
3,3 |
Inv. |
SV288-6 |
- |
++ |
79 |
NR |
13430 |
67 |
3,7 |
Inv. |
SV285mod-4 |
- |
++ |
86,5 |
218 |
12030 |
74 |
4,03 |
Inv. |
SV285mod-6 |
- |
++ |
83 |
238 |
12410 |
91 |
3,9 |
Inv. |
SV316-3 |
- |
++ |
83 |
198 |
10460 |
37 |
1,3 |
Inv. |
SV316-5 |
0 |
++ |
88 |
201 |
10790 |
40 |
1,1 |
Inv. |
SV317-2 |
0 |
++ |
76 |
204 |
11140 |
35,5 |
1,5 |
Inv. |
SV317-4 |
0 |
++ |
84 |
205 |
11460 |
36,5 |
1,3 |
Inv. |
SV316-6 |
0 |
++ |
85 |
211 |
10810 |
38 |
1,2 |
Inv. |
TD561-8 |
0 |
++ |
78 |
247 |
11350 |
56 |
0,8 |
Inv. |
SV288-5 |
- |
++ |
72 |
NR |
13420 |
72 |
3,2 |
Inv. |
SV288-6 |
- |
++ |
73 |
NR |
13430 |
67 |
2,9 |
Inv. |
SV560-6 |
- |
++ |
70,5 |
NR |
13100 |
59 |
3,3 |
Inv. |
SV560-9 |
- |
++ |
60,1 |
NR |
14070 |
77 |
1,6 |
Inv. |
SV316-1 |
- |
++ |
83 |
191 |
10060 |
41 |
1,5 |
Comp. |
TC661 |
0 |
++ |
88 |
174 |
9000 |
49 |
0,5 |
Exemple 11 - Dispositifs de mesure de température et de marquage de dépassement de
température, sans contact
[0251] Plusieurs alliages ont été élaborés jusqu'à l'épaisseur finale de 0,6 mm afin de
caractériser les propriétés d'usage. Les alliages sont élaborés à partir de matières
pures à 99,9%, fondus au four à induction sous vide en un lingot de 50kg. Le lingot
est forgé entre 1100 et 1300°C, puis laminé à chaud jusqu'à une épaisseur de 2,5mm,
entre 1000 et 1200°C puis décapé chimiquement. La bande est ensuite laminée à froid
depuis l'épaisseur de laminé à chaud jusqu'à l'épaisseur de 0,6mm, puis recuite entre
800 et 1100°C durant 1 heure, puis dégraissée, découpée en différentes pièces ou rondelles
pour mesures (voir précédemment les différents types de caractérisation utilisés)
puis recuit à 1100°C pendant 3 heures sous H2 purifié (point de rosée<-70°C).
[0252] Les nuances testées comportent les éléments mentionnés dans le tableau suivant, le
complément étant du fer et les impuretés inévitables.
Tableau 21 - Composition des nuances d'essais
|
Nuance |
%Ni |
%Cr |
%Cu |
%Mn |
%Si |
Inv. |
AA |
26,33 |
4 |
0,12 |
0,2 |
0,17 |
Inv. |
AB |
26,5 |
6 |
0,15 |
0,2 |
0,18 |
Inv. |
SV297-1 |
26,9 |
1,9 |
1 |
0,2 |
0,34 |
Inv. |
SV289-1 |
27,9 |
2 |
0,97 |
0,3 |
0,16 |
Inv. |
SV300-2 |
27,9 |
4 |
1 |
0,2 |
0,31 |
Inv. |
SV300-1 |
28 |
4 |
0,5 |
0,2 |
0,23 |
Inv. |
SV305-1 |
28 |
6 |
0,5 |
0,2 |
0,18 |
Inv. |
AC |
28 |
0,03 |
0,12 |
0,2 |
0,21 |
Inv. |
SV306-3 |
28,7 |
3,9 |
2 |
0,2 |
0,16 |
Inv. |
AD |
29 |
0,03 |
0,15 |
0,2 |
0,31 |
Inv. |
SV287-1 |
31,8 |
0,04 |
0,5 |
0,3 |
0,17 |
Inv. |
SV323-5 |
32 |
1,92 |
0,6 |
3,84 |
0,18 |
Inv. |
SV285mod-3 |
32,45 |
0,04 |
2 |
0,3 |
0,15 |
Comp. |
AE |
27 |
0,03 |
0,14 |
0,2 |
0,23 |
[0253] On réalise une série de tests pour déterminer les valeurs de résistance à la corrosion
en brouillard salin, de résistance à l'usure mécanique, d'induction à saturation à
20°C, de point de Curie, de champ coercitif à 20°C et de résistance à la corrosion
acide.
[0254] Les résultats de ces tests sont rassemblés dans le tableau 22.
Tableau 22 - Résultats des essais
|
Nuance |
CBS |
UM |
Bs20°C (G) |
Tc (°C) |
Hc (mOe) |
Iox (mA) |
Inv. |
AA |
- |
++ |
0 |
-50 |
NR |
3,7 |
Inv. |
AB |
- |
++ |
0 |
-50 |
NR |
3,1 |
Inv. |
SV297-1 |
- |
++ |
1530 |
24 |
21,3 |
2,6 |
Inv. |
SV289-1 |
- |
++ |
2540 |
43 |
NR |
NR |
Inv. |
SV300-2 |
- |
++ |
1970 |
37 |
27,5 |
1,9 |
Inv. |
SV300-1 |
- |
++ |
1570 |
24 |
18,8 |
1,7 |
Inv. |
SV305-1 |
- |
++ |
1140 |
18 |
13,8 |
1,4 |
Inv. |
AC |
- |
++ |
0 |
-10 |
NR |
4,7 |
Inv. |
SV306-3 |
- |
++ |
3840 |
70 |
NR |
NR |
Inv. |
AD |
- |
++ |
1650 |
25 |
17,5 |
4,5 |
Inv. |
SV287-1 |
- |
++ |
8420 |
152 |
NR |
NR |
Inv. |
SV323-5 |
- |
++ |
3620 |
56 |
NR |
NR |
Inv. |
SV285mod-3 |
- |
++ |
11060 |
211 |
NR |
NR |
Comp. |
AE |
- |
++ |
3700 |
-50 |
350 |
4,9 |
[0255] On note que le contre-exemple ne vérifie pas l'équation 1 ce qui signifie que l'alliage
n'est pas totalement austénitique. Le caractère non austénitique de l'alliage ne permet
pas d'atteindre les valeurs de champ coercitif requises.
Exemple 12 - Substrats hyper-texturés pour épitaxie
[0256] Plusieurs alliages ont été élaborés jusqu'à l'épaisseur finale de 0,1 mm afin de
caractériser leurs propriétés d'usage. Les alliages sont élaborés à partir de matières
pures à 99,9%, fondus au four à induction sous vide en un lingot de 50kg. Le lingot
est forgé entre 1100 et 1300°C, puis laminé à chaud jusqu'à une épaisseur de 5mm,
entre 1000 et 1200°C puis décapé chimiquement. La bande est ensuite laminée à froid
jusqu'à l'épaisseur 0,1mm sans recuit intermédiaire, puis polie mécaniquement au feutre
de polissage abrasif jusqu'à un grain de polissage très fin de l'ordre du micron.
Le métal est ensuite recuit entre 800 et 1100°C durant 1 heure, puis découpé en différentes
pièces pour mesures de figures de pôles par RX pour évaluer le type et l'intensité
de la texture obtenue.
[0257] Les nuances testées comportent les éléments mentionnés dans le tableau suivant, le
complément étant du fer et les impuretés inévitables.
Tableau 23 - Composition des nuances d'essais
|
Nuance |
%Ni |
%Cr |
%Cu |
%Mn |
%Si |
%S+ Se+Sb |
%Ti+Al |
Inv. |
TC659 |
33,5 |
4,9 |
0,15 |
0,13 |
0,025 |
5 |
13ppm |
Inv. |
TD544-4 |
31 |
0,5 |
3 |
0,23 |
0,21 |
7 |
11ppm |
Comp. |
Fe-50%Ni |
48 |
0,06 |
0,03 |
0,35 |
0,03 |
23 |
15ppm |
[0258] On réalise une série de tests pour déterminer les valeurs de résistance à la corrosion
en brouillard salin, de résistance à l'usure mécanique, de point de Curie, de résistance
à la corrosion acide, de dilatabilité entre 20 et 300°C, de taux de macle et de désorientation
moyenne de texture.
[0259] Les résultats de ces tests sont rassemblés dans le tableau 24.
Tableau 24 - Résultats des essais
|
Nuance |
Ecrouissage (%) |
CBS |
UM |
Tc (°C) |
Ioxmax (mA) |
α20-300°C (10-6/°C) |
Taux de macle (%) |
ω(°) |
Inv. |
TC659 |
98 |
0 |
++ |
149 |
1,5 |
16,5 |
5 |
8 |
Inv. |
TD544-4 |
92 |
0 |
++ |
175 |
3,6 |
9,8 |
8 |
9 |
Comp. |
Fe-Ni 50 |
96 |
- |
++ |
450 |
4,2 |
9 |
3 |
7 |
[0260] On voit que les alliages selon l'invention présentent une forte aptitude à la texturation
cubique {100]<001> avec un faible taux de macle (<10%) et une faible désorientation
moyenne de texture ω (<10°), une forte tenue à l'usure mécanique de la couche oxydée
sous atmosphère dégradée de fonctionnement ou de recuit grâce à l'adjonction de teneurs
minimales de Cr, Si et Cu, et des dilatabilités variables dans une large plage permettant
de répondre à la plupart des besoins de dilatation des dépôt sur substrat pour épitaxie.