Technical Field
[0001] The present invention relates to an aqueous lubricant for metal material plastic
working, a metal material having a lubricating coating formed by the aqueous lubricant
on/over a surface of the metal material, and a metal processed article obtained by
molding the metal material.
Background Art
[0002] In plastic working such as wire drawing, tube drawing, plate press, heading, and
forging, in order to facilitate the working into a desired shape and further to suppress
the occurrence of seizure, a lubricating coating is formed at the friction interface
between a metal mold and a workpiece. In recent years, a technique that can form this
lubricating coating with one solution has been proposed. For example, in Patent Literature
1, a water-soluble lubricant for plastic working containing at least an alkaline earth
metal salt of aliphatic monocarboxylic acid having 1 to 4 carbon atoms, an alkaline
earth metal salt of aliphatic dicarboxylic acid having 2 to 4 carbon atoms, or an
alkaline earth metal salt of aliphatic carboxylic acid having 2 to 4 carbon atoms
with 1 to 2 hydroxyl groups has been proposed. According to this technique, a water-soluble
lubricant for plastic working having excellent lubricity, which does not cause precipitation
solidification and further does not cause surface roughening or abrasion of a tool,
can be provided.
Citation List
Patent Literature
Summary of Invention
Technical Problem
[0004] However, with a lubricating coating formed by the lubricant that has been proposed
in Patent Literature 1, the lubricity (moisture absorption resistance) under a high
humidity environment is not sufficient, and further, the sufficient seizure resistance
cannot be obtained in metal working with high difficulty. Accordingly, an object of
the present invention is to provide an aqueous lubricant for metal material plastic
working that can form a lubricating coating having excellent lubricity (moisture absorption
resistance) under a high humidity environment, seizure resistance to metal working
with high difficulty, and the like, and further has excellent long-term agent stability;
a metal material having a lubricating coating formed by the aqueous lubricant on/over
a surface of the metal material; and a metal processed article obtained by molding
the metal material.
Solution to Problem
[0005] As a result of the intensive studies to solve the problems described above, the present
inventors have found that an aqueous lubricant, in which an aliphatic polycarboxylic
acid having 5 or more and 8 or less carbon atoms and a solubility in water at 20°C
of 10 g/100 mL or more and an alkaline earth metal compound are blended in water,
can form a lubricating coating having excellent lubricity (moisture absorption resistance)
under a high humidity environment, seizure resistance to metal working with high difficulty,
and the like, and further has excellent long-term agent stability, and thus have completed
the present invention.
[0006] That is, the present invention is
- (1) an aqueous lubricant for metal material plastic working, in which an aliphatic
polycarboxylic acid having 5 to 8 carbon atoms and a solubility in water at 20°C of
10 g/100 mL or more and an alkaline earth metal compound are blended in water, or
an alkaline earth metal salt of the aliphatic polycarboxylic acid is dissolved and/or
dispersed in water;
- (2) the aqueous lubricant described in the above (1), which further contains at least
one kind of organic lubricants selected from an oil, a soap, a wax, an amino acid
compound having a layered structure, an organic modified clay mineral, and an extreme-pressure
agent;
- (3) the aqueous lubricant described in the above (1) or (2), which contains, as a
binder component, at least one kind selected from a water-soluble inorganic acid salt,
a water-soluble organic acid salt, and a water-dispersible or water-soluble resin;
- (4) the aqueous lubricant described in any one of the above (1) to (3), which further
contains at least one kind of solid lubricants selected from zinc phosphate, zinc
oxide, titanium dioxide, mica, molybdenum disulfide, tungsten disulfide, tin disulfide,
graphite fluoride, graphite, boron nitride, calcium hydroxide, calcium carbonate,
lime, calcium sulfate, and barium sulfate;
- (5) the aqueous lubricant described in any one of the above (1) to (4), in which the
aliphatic polycarboxylic acid is citric acid;
- (6) a metal material having a lubricating coating formed by the aqueous lubricant
described in any one of the above (1) to (5) on/over a surface of the metal material;
- (7) a metal processed article obtained by molding the metal material described in
the above (6);
and the like.
Effects of Invention
[0007] According to the present invention, an aqueous lubricant for metal material plastic
working that can form a lubricating coating having excellent lubricity (moisture absorption
resistance) under a high humidity environment, seizure resistance to metal working
with high difficulty, and the like, and further has excellent long-term agent stability;
a metal material having a lubricating coating formed by the aqueous lubricant on/over
a surface of the metal material; and a metal processed article obtained by molding
the metal material can be provided.
Brief Description of Drawings
[0008] Fig. 1 is a drawing showing the evaluation criteria on seizure degree of the test
pieces to which a ball ironing process in the upsetting-ball ironing tribo-type friction
test method is performed in Examples of the present invention.
Description of Embodiments
[0009] Hereinafter, the present invention will be described in detail. Note that the embodiments
described below are merely an example, and the present invention is not limited to
the present embodiments.
[0010] The aqueous lubricant according to the present invention has excellent long-term
agent stability, and can form a lubricating coating having excellent lubricity (moisture
absorption resistance) under a high humidity environment, seizure resistance to metal
working with high difficulty, and the like, therefore, is useful for plastic working
of a metal material. Herein, the expression "long-term agent stability" in the present
specification means that as a highly concentrated lubricant before dilution, a state
in which sedimentation components are not substantially generated at 40°C for one
month or more is maintained, or that as a dilute lubricant (having a practical use
concentration) obtained by diluting a highly concentrated lubricant in order to form
a lubricating coating on/over a metal material, a state in which sedimentation components
are not substantially generated at a practical use temperature for one month or more
is maintained.
[0011] As the metal material for plastic working to which the aqueous lubricant according
to the present invention is applied, for example, iron, iron and steel, stainless
steel, aluminum, magnesium, copper, titanium, and the like can be mentioned. The shape
of the metal material varies depending on the application, and for example, a shape
of a sheet, a bar wire, a tube, a slab, or the like can be mentioned, but the shape
is not limited thereto.
[0012] The aqueous lubricant according to the present invention is not particularly limited
as long as being an aqueous lubricant in which an aliphatic polycarboxylic acid having
5 or more and 8 or less carbon atoms and a solubility in water at 20°C of 10 g/100
mL or more (hereinafter, simply referred to as "aliphatic polycarboxylic acid") and
an alkaline earth metal compound are blended in water, or an alkaline earth metal
salt of the aliphatic polycarboxylic acid is dissolved and/or dispersed in water;
and the aqueous lubricant, as needed, may contain an additive agent such as an organic
lubricant, a binder component, and a solid lubricant, a liquid conditioning component
such as a rheology modifier, a surfactant, and a pH adjusting agent, and the like.
Herein, the expression "aliphatic polycarboxylic acid" means an aliphatic compound
having 2 or more carboxyl groups in the molecule.
[0013] As to the alkaline earth metal salt of aliphatic polycarboxylic acid, for example,
an alkaline earth metal salt of aliphatic polycarboxylic acid can be obtained by adding
and blending an alkaline earth metal compound in an aqueous solution in which aliphatic
polycarboxylic acid has been dissolved in advance.
[0014] The aliphatic polycarboxylic acid, or the aliphatic polycarboxylic acid in an alkaline
earth metal salt is not particularly limited as long as having 5 to 8 carbon atoms
and a solubility in water at 20°C of 10 g/100 mL or more, and for example, glutaric
acid, citric acid, diacetyl-D-tartaric acid, diacetyl-L-tartaric acid, or the like
can be used. Here, the reason why the number of carbon atoms is limited to 5 or more
is because in the aliphatic polycarboxylic acid having 4 or less carbon atoms, or
an alkaline earth metal salt of the aliphatic polycarboxylic acid, the long-term agent
stability is poor, and a lubricating coating having excellent lubricity (moisture
absorption resistance) under a high humidity environment, seizure resistance to metal
working with high difficulty, and the like cannot be obtained. On the other hand,
the reason why the number of carbon atoms is limited to 8 or less is because in the
aliphatic polycarboxylic acid having 9 or more carbon atoms, or an alkaline earth
metal salt of the aliphatic polycarboxylic acid, precipitation solidification is generated
and an aqueous lubricant cannot be prepared. Further, the reason why the solubility
in water at 20°C is limited to 10 g/100 mL or more is because also in the aliphatic
polycarboxylic acid having a solubility in water at 20°C of less than 10 g/100 mL,
or an alkaline earth metal salt of the aliphatic polycarboxylic acid, precipitation
solidification is generated as in the aliphatic polycarboxylic acid having 9 or more
carbon atoms or an alkaline earth metal salt of the aliphatic polycarboxylic acid,
and an aqueous lubricant cannot be prepared.
[0015] The alkaline earth metal compound is not particularly limited as long as being a
compound of beryllium, magnesium, calcium, strontium, barium, or radium, and for example,
a magnesium compound such as magnesium carbonate, magnesium hydroxide, and magnesium
oxide; a calcium compound such as calcium carbonate, calcium hydroxide, and calcium
oxide; or the like can be used. Among them, from the point of being excellent in the
reactivity with the aliphatic polycarboxylic acid, magnesium carbonate, or calcium
carbonate is preferably used.
[0016] The aqueous lubricant according to the present invention can be produced, for example,
by adding predetermined aliphatic polycarboxylic acid and alkaline earth metal compound
in water, or by dissolving and/or dispersing an alkaline earth metal salt of the predetermined
aliphatic polycarboxylic acid in water, and then by adding an additive agent as needed,
but the method is not limited to such a method. Further, after production of an aqueous
lubricant, the pH of the aqueous lubricant may be adjusted to 7 or more by using a
pH adjusting agent. As the pH adjusting agent, for example, an alkali component such
as sodium hydroxide, or calcium hydroxide can be used.
[0017] In addition, in the production of an aqueous lubricant, the blending amount in a
case of adding aliphatic polycarboxylic acid and an alkaline earth metal compound
in water is not particularly limited, and is preferably within the range of 1 : 0.2
or more and 1 : less than 8, and more preferably within the range of 1 : 0.5 or more
and 1 : less than 2 in terms of a molar ratio of the aliphatic polycarboxylic acid
to the alkaline earth metal compound. By performing the production within these ranges,
each performance of the lubricity (moisture absorption resistance) under a high humidity
environment, the seizure resistance to metal working with high difficulty, and the
like can be more improved, and further, the long-term agent stability can be more
improved.
[0018] As the organic lubricant, for example, a supplementary component for lubrication
such as an oil, a soap, a wax, an amino acid compound having a layered structure,
an organic modified clay mineral, and an extreme-pressure agent can be mentioned.
[0019] As the oil used as the supplementary component for lubrication, for example, vegetable
oil, synthetic oil, mineral oil, or the like can be used, and more specifically, palm
oil, castor oil, rapeseed oil, machine oil, turbine oil, ester oil, silicone oil or
the like can be used.
[0020] The soap is, for example, a metal salt of fatty acid or the like, and more specifically,
a metal salt of saturated or unsaturated fatty acid having 8 to 22 carbon atoms such
as octanoic acid, decanoic acid, lauric acid, myristic acid, palmitic acid, icosanoic
acid, oleic acid, and stearic acid can be mentioned. As the metal salt, for example,
in addition to an alkali metal salt such as a sodium salt, and a potassium salt, a
polyvalent metal salt such as a calcium salt, a zinc salt, a magnesium salt, and a
barium salt, and the like can be mentioned.
[0021] Examples of the wax include polyethylene wax, polypropylene wax, carnauba wax, paraffin
wax, and polytetrafluoroethylene. As the polytetrafluoroethylene, for example, polytetrafluoroethylene
having a polymerization degree of around 1,000,000 to 10,000,000, and the like can
be mentioned. In addition, although not being similar to a wax, an amino acid compound
having a layered structure, which is amino acid with a hydrocarbon group having 11
or more carbon atoms or a derivative of the amino acid, and a lubricating material
exhibiting lubricity, such as an organic modified clay mineral in which at least one
inorganic cation in the clay mineral is ion-exchanged with an organic cation can also
be used. Various kinds of waxes and a lubricating material may be used alone or in
combination of two or more kinds thereof.
[0022] Examples of the extreme-pressure agent include a sulfur-based extreme-pressure additive,
an organic molybdenum-based extreme-pressure additive, a phosphorus-based extreme-pressure
additive, and a chlorine-based extreme-pressure additive. More specific examples of
the extreme-pressure agent include melamine cyanurate, olefin sulfide, ester sulfide,
sulfite, thiocarbonate, chlorinated fatty acid, phosphoric acid ester, phosphorous
acid ester, molybdenum dithiocarbamate (MoDTC), molybdenum dithiophosphate (MoDTP),
and zinc dithiophosphate (ZnDTP). These extreme-pressure agents may be used alone
or in combination of two or more kinds thereof.
[0023] As the binder component, for example, a water-soluble inorganic acid salt, a water-soluble
organic acid salt, a water-dispersible or water-soluble resin, or the like can be
used. These may be used alone or in combination of two or more kinds thereof.
In addition, the expression "water-soluble" in the present specification and claims
means that the amount to be dissolved in 100 ml of water at 20°C exceeds 0.1 g.
[0024] As the water-soluble inorganic acid salt, for example, an acid salt such as a salt
of sulfuric acids, a salt of boric acids, a salt of phosphoric acids, a salt of tungstic
acids, and a salt of silicic acids can be mentioned. As the salt constituting these
acid salts, for example, an alkali metal salt (sodium salt, potassium salt, lithium
salt, or the like), an ammonium salt, an amine salt (ethylamine salt, or the like),
an alkanolamine salt (monoethanolamine salt, diethanolamine salt, or the like) and
the like can be mentioned, and it is preferred to be an alkali metal salt, or an ammonium
salt. Specific examples of the water-soluble inorganic acid salt include sodium sulfate,
potassium sulfate, lithium borate (lithium tetraborate, or the like), sodium borate
(sodium tetraborate, or the like), potassium borate (potassium tetraborate, or the
like), a diethanolamine salt of boric acid, sodium silicate, potassium silicate, lithium
silicate, sodium metasilicate, sodium phosphate, potassium phosphate, sodium tripolyphosphate,
lithium tungstate, sodium tungstate, and potassium tungstate. As the salt of silicic
acids, a salt represented by the general formula M
2O·nSiO
2 (in the formula, n represents a number from 1 to 9, and M represents Na, K, Li, or
NH
4) can be mentioned. These water-soluble inorganic acid salts may be used alone or
in combination of two or more kinds thereof.
[0025] As the water-soluble organic acid salt, for example, a polycarboxylic acid salt having
3 to 6 carbon atoms, which may have a hydroxyl group, and the like can be mentioned,
and it is preferred to use at least one kind selected from a malic acid salt, a succinic
acid salt, a glutaric acid salt, a citric acid salt, and a tartaric acid salt. As
the salt constituting these acid salts, for example, an alkali metal salt (sodium
salt, potassium salt, lithium salt, or the like), an ammonium salt, an amine salt
(ethylamine salt, or the like), an alkanolamine salt (monoethanolamine salt, diethanolamine
salt, or the like) and the like can be mentioned, and it is preferred to be an alkali
metal salt, or an ammonium salt. Specific examples of the water-soluble organic acid
salt include sodium malate, potassium malate, lithium malate, sodium succinate, potassium
succinate, lithium succinate, sodium citrate, potassium citrate, lithium citrate,
sodium glutarate, potassium glutarate, lithium glutarate, sodium tartrate, potassium
tartrate, and lithium tartrate. These water-soluble organic acid salts may be used
alone or in combination of two or more kinds thereof.
[0026] The water-dispersible or water-soluble resin is not particularly limited as long
as having coat-forming properties, and for example, a water-soluble or water-dispersible
resin such as an acrylic resin, a phenolic resin, a urethane-based resin, an epoxy-based
resin, a polyester-based resin, and an isobutylene-based resin can be mentioned. These
water-dispersible or water-soluble resins may be used alone or in combination of two
or more kinds thereof.
[0027] The acrylic resin is not particularly limited as long as being obtained by polymerizing
at least one kind of acrylic monomers. Examples of the acrylic monomer include alkyl
(for example, C = 1 to 8) (meth)acrylate such as methyl acrylate, methyl methacrylate,
ethyl acrylate, ethyl methacrylate, isopropyl methacrylate, n-butyl acrylate, n-butyl
methacrylate, 2-ethylhexyl methacrylate, and octyl acrylate; lower alkoxy-lower alkyl
(meth)acrylate such as methoxymethyl acrylate, methoxyethyl acrylate, ethoxymethyl
acrylate, ethoxyethyl acrylate, methoxymethyl methacrylate, methoxyethyl methacrylate,
ethoxymethyl methacrylate, ethoxyethyl methacrylate, and methoxybutyl acrylate; hydroxy
lower alkyl (meth)acrylate such as 2-hydroxyethyl (meth)acrylate, and 3-hydroxypropyl
(meth)acrylate; acrylamide; methacrylamide; (meth)acrylamide having an N-unsubstituted
or substituted (particularly, lower alkoxy substituted) methylol group such as N-methylol
acrylamide, N-methylol methacrylamide, N-butoxymethyl acrylamide, and N-butoxymethyl
methacrylamide; phosphonyloxy lower alkyl (meth)acrylate such as phosphonyloxymethyl
acrylate, phosphonyloxyethyl acrylate, phosphonyloxypropyl acrylate, phosphonyloxymethyl
methacrylate, phosphonyloxyethyl methacrylate, and phosphonyloxypropyl methacrylate;
acrylonitrile; acrylic acid; and methacrylic acid. In the present invention, as the
acrylic resin, a copolymer of at least one kind of the acrylic monomers and at least
one kind of other ethylenic monomers (e.g., styrene, methyl styrene, vinyl acetate,
vinyl chloride, vinyl toluene, ethylene) which contains 30% by mole or more of acrylic
monomer units is also included. Note that the expression "lower" in the above means
that the number of carbon atoms is 1 to 6.
[0028] As the phenolic resin, for example, a phenolic resin obtained by the reaction of
at least one kind of phenols such as phenol, cresol, or xylenol with formaldehyde
can be mentioned, and any one of a novolak-type resin and a resol-type resin may be
used. In a case of using a novolak-type resin, it is preferred that hexamethylenetetramine
or the like coexists with the novolak-type resin as a curing agent.
[0029] The urethane-based resin is not particularly limited as long as being a synthetic
resin having a urethane bond (NHCOO), and a known urethane-based resin can be used.
For example, one obtained by the polyaddition reaction of a polyisocyanate compound
having 2 or more isocyanate groups with a polyol having 2 or more active hydrogen
groups can be mentioned. As the polyol, for example, a polyester polyol, a polyether
polyol, and the like can be mentioned.
[0030] As the polyester polyol, for example, a polyester compound having a hydroxyl group
at the terminal, which is obtained by the reaction of a polyol with a low molecular
weight (molecular weight of 1000 or less) such as ethylene glycol, diethylene glycol,
triethylene glycol, 1,2-propylene glycol, 1,3-propylene glycol, neopentyl glycol,
1,2-butylene glycol, 1,3-butylene glycol, 1,4-butylene glycol, 3-methylpentanediol,
hexamethylene glycol, bisphenol A, hydrogenated bisphenol A, trimethylolpropane, and
glycerin with a polybasic acid such as succinic acid, glutaric acid, adipic acid,
sebacic acid, phthalic acid, isophthalic acid, terephthalic acid, trimellitic acid,
tetrahydrophthalic acid, endomethylene tetrahydrophthalic acid, and hexahydrophthalic
acid can be mentioned.
[0031] As the polyether polyol, for example, a polyol with a low molecular weight (having
a molecular weight of 1000 or less) such as ethylene glycol, diethylene glycol, triethylene
glycol, 1,2-propylene glycol, 1,3-propylene glycol, neopentyl glycol, 1,2-butylene
glycol, 1,3-butylene glycol, 1,4-butylene glycol, 3-methylpentanediol, hexamethylene
glycol, bisphenol A, hydrogenated bisphenol A, trimethylolpropane, and glycerin, or
an ethylene oxide and/or propylene oxide high adducts (2 adducts or more) thereof;
a polyether polyol such as polyethylene glycol, polypropylene glycol, and polyethylene/propylene
glycol; a polycaprolactone polyol; a polyolefin polyol; a polybutadiene polyol; and
the like can be mentioned.
[0032] As the polyisocyanate compound, for example, an aliphatic, alicyclic, or aromatic
polyisocyanate can be mentioned. Specifically, tetramethylene diisocyanate, hexamethylene
diisocyanate, lysine diisocyanate ester, hydrogenated xylylene diisocyanate, 1,4-cyclohexylene
diisocyanate, 4,4'-dicyclohexylmethane diisocyanate, 2,4'-dicyclohexylmethane diisocyanate,
isophorone diisocyanate, 3,3'-dimethoxy-4,4'-biphenylene diisocyanate, 1,5-naphthalene
diisocyanate, 1,5-tetrahydronaphthalene diisocyanate, 2,4-tolylene diisocyanate, 2,6-tolylene
diisocyanate, 4,4'-diphenylmethane diisocyanate, 2,4'-diphenylmethane diisocyanate,
phenylene diisocyanate, xylylene diisocyanate, tetramethylxylylene diisocyanate, and
the like can be mentioned.
[0033] As the epoxy-based resin, for example, a bisphenol-type epoxy resin such as a bisphenol
A type epoxy resin obtained by reacting bisphenols, in particular, a bisphenol A (2,2-bis(4'-hydroxyphenyl)propane)
with epichlorohydrin can be mentioned. In addition, a novolac type epoxy resin obtained
by glycidyl etherification of a phenolic hydroxyl group of a phenol novolak resin,
glycidyl ester of aromatic carboxylic acid, a peroxy acid epoxy type epoxy resin obtained
by epoxidizing double bond of ethylenically unsaturated compound with peroxy acid,
and the like can be mentioned. Further, those obtained by adding ethylene oxide or
propylene oxide to a resin skeleton of the above various epoxy resins, a glycidyl
ether type epoxy resin of polyhydric alcohol, and the like can also be mentioned.
Among them, it is preferred to use a bisphenol A type epoxy resin.
[0034] As the polyester resin, for example, a condensation resin obtained by condensing
a polybasic acid such as maleic acid, fumaric acid, itaconic acid, succinic acid,
glutaric acid, suberic acid, adipic acid, azelaic acid, sebacic acid, dimer acid,
trimer acid, isophthalic acid, terephthalic acid, trimellitic acid, trimesic acid,
pyromellitic acid, and naphthalene dicarboxylic acid with a polyol such as ethylene
glycol, diethylene glycol, trimethylol propane, neopentyl glycol, 1,4-CHDM (cyclohexane
dimethanol), and 1,6-hexanediol; a condensation resin obtained by condensing the above-described
polybasic acid with a polyol such as a polymer polyol, a polycaprolactone polyol,
a polycarbonate diol, a polybutadiene polyol, neopentyl glycol, and methyl pentadiol;
and the like can be mentioned. Moreover, a water-based resin obtained by using a monomer
having 3 or more carboxyl groups such as trimellitic acid or pyromellitic acid as
a part of the monomer, neutralizing the unreacted carboxylic acid with an alkali to
thereby be solubilized or water-dispersed, or a water-based resin obtained by using
a sulfonated monomer such as sulfophthalic acid as a part of the monomer to thereby
be solubilized or water-dispersed can also be used.
[0035] As the isobutylene-based resin, for example, a copolymer of isobutylene and maleic
anhydride, and the like can be mentioned. In addition, one obtained by ammonia-modifying
or imidizing the maleic anhydride moiety of the copolymer can also be mentioned, however,
from the viewpoint of the coat-forming properties, it is preferred to use the one
having a number average molecular weight of 10,000 or more (measurement value by GPC
(gel permeation chromatography) method).
[0036] As the solid lubricant (including one in a powder form), for example, zinc phosphate,
zinc oxide, titanium dioxide, mica, molybdenum disulfide, tungsten disulfide, tin
disulfide, graphite fluoride, graphite, boron nitride, calcium hydroxide, calcium
carbonate, lime, calcium sulfate, barium sulfate, and the like can be mentioned. These
solid lubricants may be used alone or in combination of two or more kinds thereof.
[0037] As the rheology modifier, for example, an aqueous polymer, an inorganic viscosity
modifier, and the like can be mentioned. As the aqueous polymer, for example, hydroxyethyl
cellulose, carboxymethyl cellulose, polyacrylic acid amide, sodium polyacrylate, sulfonic
acid-modified sodium polyacrylate, polyvinyl pyrrolidone, polyvinyl alcohol, and the
like can be mentioned. As the inorganic viscosity modifier, for example, silica, bentonite,
kaolin, mica, montmorillonite, hectorite, and the like can be mentioned. The inorganic
viscosity modifier may be a natural product or a synthetic product. These rheology
modifier may be used alone or in combination of two or more kinds thereof. By blending
a rheology modifier into the aqueous lubricant according to the present invention,
the components dispersed in the aqueous lubricant can be stabilized, and further,
improvement of the coating properties (for example, liquid viscosity) to a metal material
can be achieved.
[0038] As the surfactant, for example, a nonionic surfactant, an anionic surfactant, an
amphoteric surfactant, a cationic surfactant, and the like can be mentioned, and the
surfactant may be appropriately selected depending on the molecular structure, hydrophilic-lipophilic
balance (HLB), and the like as needed. These may be used alone or in combination of
two or more kinds thereof. By blending a surfactant into the aqueous lubricant according
to the present invention, improvement of the cleaning effect and wettability on a
surface of a metal material can be achieved. Note that this effect is general, therefore,
is not shown in Examples.
[0039] Next, the metal material and metal processed article according to the present invention
will be described. The metal processed article according to the present invention
can be obtained by molding the metal material. As the molding method, a method, in
which the metal material according to the present invention is molded by heat, pressure,
mechanical force, or the like using a metal mold, a tool or the like, can be mentioned.
The metal material according to the present invention can be obtained by forming a
lubricating coating on/over a surface of the metal material by the aqueous lubricant.
More specifically, the metal material can be produced by a method including a step
of bringing the aqueous lubricant into contact with a surface of the metal material,
followed by a step of drying the surface of the metal material with which the aqueous
lubricant has brought into contact. Further, before performing the step of bringing
the aqueous lubricant into contact with a surface, the surface may be cleaned by performing
all or a part of pretreatments of washing (usually using an alkaline cleaner), water-rinsing
after the washing, descaling (shot blasting or pickling with hydrochloric acid or
the like), water-rinsing after the descaling, and the like on a surface of a target
metal material. In this way, by the subsequent step (step of bringing the aqueous
lubricant into contact), a favorable lubricity coating can be obtained. Note that
in a case where oxide scale does not adhere, in a case where oxide scale is used for
the application of requiring the oxide scale, or the like, the descaling and the water-rinsing
after the descaling may be omitted. These pretreatments can be performed by a routine
procedure.
[0040] Further, before performing the step of bringing the aqueous lubricant according to
the present invention into contact, chemical conversion treatment, surface preparation,
and the like may be performed as needed. As the chemical conversion treatment, for
example, iron phosphate conversion treatment, zinc phosphate conversion treatment,
zinc phosphate calcium conversion treatment, iron oxalate conversion treatment, aluminum
fluoride conversion treatment, zirconium oxide conversion treatment, and the like
can be mentioned. As the surface preparation, for example, a method in which a surface
preparation agent containing an alkali metal salt of boric acid, silicic acid, sulfuric
acid, phosphoric acid, or tungstic acid is brought into contact with a surface and
drying the surface, a method in which a solid lubricant is mechanically coated by
a projective technique such as blasting, and the like can be mentioned.
[0041] As the method for bringing the aqueous lubricant or surface preparation agent into
contact with a surface, for example, a known method of immersion, spraying, flowing,
brushing, or the like can be applied. In the contact by an aqueous lubricant or a
surface preparation agent, as long as the surface is sufficiently covered with the
lubricant or the surface preparation agent, the contact time is not particularly limited.
The drying of the metal material surface with which the aqueous lubricant or the surface
preparation agent has brought into contact can be performed by a known method, for
example, heat drying, air drying, or the like. The drying temperature and time are
not particularly limited, but it is preferred that the drying is performed at a peak
metal temperature of 60°C to 150°C for around 10 seconds to 60 minutes.
[0042] The mass of a lubricating coating formed by the aqueous lubricant according to the
present invention may be appropriately adjusted depending on the application of the
form of working, the degree of difficulty, and the like, and from the viewpoint of
preventing the seizure, the mass is usually in the dry coating within the range of
preferably 1 g/m
2 or more, and more preferably 3 to 50 g/m
2. In addition, the aqueous lubricant of the present invention may also be applied
not only on/over the metal material surface but also on/over a surface of a metal
mold in addition to the metal material surface. Note that in the lubricating coating,
it is presumed that the aliphatic polycarboxylic acid and the alkaline earth metal
form a salt. Herein, as the mass of the alkaline earth metal contained in a lubricating
coating, the alkaline earth is contained in the dried lubricating coating preferably
at a solid content ratio of 1% by mass or more, and from the viewpoint of improving
the seizure resistance, is contained more preferably at a solid content ratio of 5%
by mass or more, and particularly preferably at a solid content ratio of 10% by mass
or more. Note that the mass of the alkaline earth metal existed in the dried lubricating
coating can be calculated by measuring the metal material having the lubricating coating
with fluorescent X-rays.
[0043] A protective layer may be formed as the upper layer of the lubricating coating formed
by the aqueous lubricant according to the present invention for the purpose of compensating
the lubricity and the rust prevention. As the component used for forming the protective
layer, an oil, a soap, a metal soap, a wax, and the like can be mentioned, and among
them, one kind or two or more kinds thereof may be used. The protective layer can
be formed by applying these components. Further, the protective layer may be constituted
in a form of a composite layer holding the above components in a binder component.
Examples
[0044] The present invention will be further specifically described together with the effects
by describing Examples of the present invention together with Comparative Examples.
Note that the present invention should not be limited by these Examples.
(1) method for producing aqueous lubricant
[0045] The constituent components (the following components a to f) of various aqueous lubricants
according to the following Examples and Comparative Examples are shown below. In addition,
in Table 1, the carbon number of various "components a", and the solubility in water
(20°C) are shown. On the basis of the compositions shown in Tables 2 and 3, various
aqueous lubricants were produced by sequentially adding each component (any one of
the following al to a8, any one of b1 to b6, and as needed, c1 to c2, d1 to d3, e1
to e2, f1 to f4) of various aqueous lubricants into water while stirring, and by adjusting
the pH with sodium hydroxide or sodium carbonate. Note that the numerical values of
each component in Tables 2 and 3 means the % by mass of each additive component based
on the total mass of all added components.
(2) constituent component of aqueous lubricant
<aliphatic polycarboxylic acid: component a>
[0046]
a1: glutaric acid
a2: citric acid
a3: butanetetracarboxylic acid
a4: oxalic acid
a5: tartaric acid
a6: malic acid
a7: suberic acid
a8: 1,10-decanedicarboxylic acid
<metal compound to be reacted with aliphatic polycarboxylic acid: component b>
[0047]
b1: magnesium carbonate
b2: calcium carbonate
b3: calcium hydroxide
b4: strontium carbonate
b5: sodium hydroxide
b6: lithium hydroxide
<lubricant component: component c>
[0048]
c1: polyethylene wax
c2: calcium stearate
<binder component: component d>
[0049]
d1: potassium tetraborate
d2: sodium citrate
d3: isobutylene-based resin: a copolymer of isobutylene and maleic anhydride (molecular
weight of 90,000)
<solid lubricant: component e>
[0050]
e1: aqueous dispersion of zinc phosphate (manufactured by Nihon Parkerizing Co., Ltd.)
e2: organic modified synthetic mica: a material where distearyl dimethyl ammonium
chloride is intercalated between layers of hectorite
<viscosity modifier: component f>
[0051]
f1: hydroxyethyl cellulose
f2: carboxymethyl cellulose
f3: sulfonic acid-modified sodium polyacrylate
f4: polyvinyl alcohol
(Table 1) The carbon number and solubility in water of component a
[0052]
(Table 1) The carbon number and solubility in water of component a
|
component a |
the carbon number |
solubility in water (20°C) |
Example |
a1 |
5 |
43 |
a2 |
6 |
73 |
a3 |
8 |
≧ 10(19°C) |
Comparative Example |
a4 |
2 |
10.2 |
a5 |
4 |
43 |
a6 |
4 |
55.8 |
a7 |
8 |
0.2 |
a8 |
12 |
<0.1 |
(3) formation of lubricating coating
[0053] Formation of a lubricating coating on a test piece for evaluation of plastic working
performance using each aqueous lubricant of Examples 1 to 29 and Comparative Examples
1 to 8 was performed by dip coating the test piece in various aqueous lubricants,
and then drying the test piece. Further, the solid content concentration and dip coating
time of various aqueous lubricants were appropriately adjusted so that the coating
amount to be formed is around 5 g/m
2.
(Table 2)
[0054]
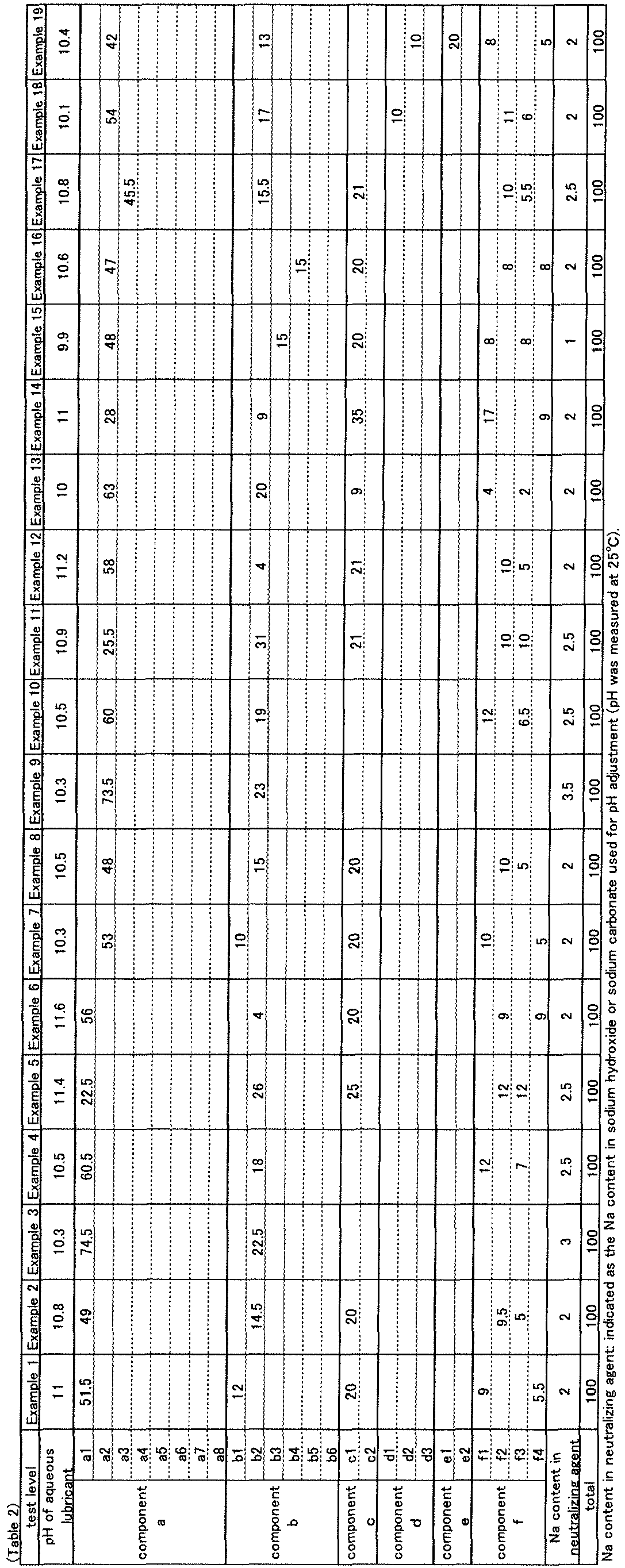
(Table 3)
[0055]
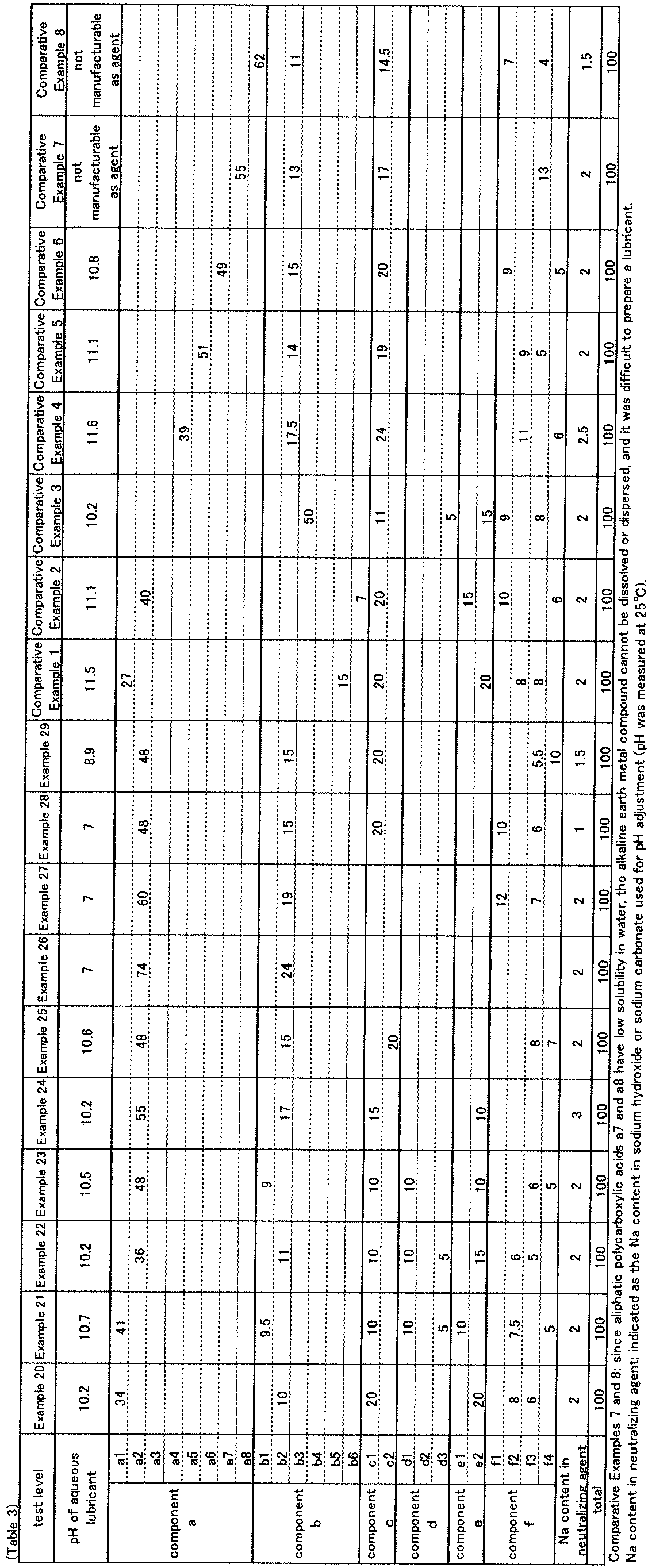
(4) evaluation
[0056] long-term agent stability:
Evaluation before dilution was performed as follows: each 100 mL of various aqueous
lubricants having a high concentration (solid content concentration of 20% by mass)
was filled in a transparent plastic container, left to stand in a thermostatic bath
at 40°C for one day, one week, or one month, and the dispersity degree of the aqueous
lubricant was measured. Further, evaluation after dilution was performed as follows:
each 100 mL of various aqueous lubricants having a practical use concentration (solid
content concentration of 8% by mass) was filled in a transparent plastic container,
left to stand in a thermostatic bath at 60°C for one day, one week, or one month,
and the dispersity degree of the aqueous lubricant was measured. The dispersity degree
(%) of the aqueous lubricant was determined by using the height from the bottom surface
of the container to the phase separation surface when the total height of the aqueous
lubricant was taken as 100% as the ratio of the dispersion degree. When the evaluation
result is "Δ" or more, there is no worry of sedimentation solidification, and it was
determined to have practical performance level.
<evaluation criteria>
[0057] long-term agent stability:
⊚: Even after storage for one month, the dispersion degree was 80% or more, and sedimentation
solidification was not observed even at the bottom of the container
○: Even after storage for one weeks to one month, the dispersion degree was 50% or
more and less than 80%, and sedimentation solidification was not observed at the bottom
of the container
Δ: After storage for one day to one week, the dispersion degree was less than 50%,
but sedimentation solidification was not observed at the bottom of the container
×: After storage for one day, the dispersity degree was less than 50%, and sedimentation
solidification was observed at the bottom of the container
[0058] lubricity evaluation by pull-out test (lubricity, moisture absorption resistance,
and scum-clogging resistance):
In order to evaluate the lubrication performance of a lubricating coating formed by
each of various aqueous lubricants for metal material plastic working, wire drawing
was performed on a steel wire rod on which a lubricating coating had been formed,
and the lubricity, the moisture absorption resistance, the scum-clogging resistance,
and the like at the time of wire drawing were evaluated in accordance with the following
evaluation method and evaluation criteria. The wire drawing was performed by pulling
out the steel wire rod using an R die (φ 11.85 mm). As the steel wire rod, a steel
wire rod (φ 13.00 mm, and length 1.5 m) of SCM435 was used. Surface treatment (including
a forming of the lubricating coating) of the steel wire rod was performed by the following
steps i to viii. In the above evaluation results, "Δ" or more was determined to have
practical performance level.
- i) alkaline degreasing (FINECLEANER E6400 (manufactured by Nihon Parkerizing Co.,
Ltd.), 20 g/L, 60°C, 20 minutes, immersion)
- ii) water-rinsing (industrial water, 20°C, 30 seconds, immersion)
- iii) scale removal pickling (18% hydrochloric acid solution, 20°C, 20 minutes, immersion)
- iv) water-rinsing (industrial water, 20°C, 30 seconds, immersion)
- v) neutralization (PREPALENE 27 (manufactured by Nihon Parkerizing Co., Ltd.), 3 g/L,
20°C, 30 seconds, immersion)
- vi) formation of a lubricating coating by various aqueous lubricants (practical use
concentration, 60°C, 30 seconds, immersion)
- vii) drying (100°C, 5 minutes)
- viii) The steel wire rod to be evaluated for moisture absorption resistance was left
to stand for 24 hours in a room at 30°C × 80% RH after the step of vii).
<evaluation method>
[0059] lubricity without moisture absorption:
After the step of vii), the temperature of the steel wire rod was returned to room
temperature, and then wire drawing was performed, and the lubricity was evaluated
in accordance with the following evaluation criteria.
[0060] moisture absorption resistance (lubricity after moisture absorption):
After the step of viii), the wire drawing was performed by using a steel wire rod,
and the moisture absorption resistance was evaluated in accordance with the following
evaluation criteria.
<evaluation criteria>
[0061]
⊚: Lubricity was extremely favorable, and seizure, flaws, or the like was not observed
at all on the steel wire rod and the R die
○: Lubricity was favorable, and it is a degree that seizure or flaws of less than
10% in the area ratio was observed on the steel wire rod surface or the R die
Δ: Lubricity was standard, and flaws or adhesion was observed in the range of 10%
or more and less than 25% in the area ratio on the steel wire rod surface or the R
die
×: Lubricity is lowered, and flaws or adhesion was observed in the range of 25% or
more in the area ratio on the steel wire rod surface or the R die, or the steel wire
rod was broken during wire drawing because of being insufficient lubrication
<evaluation method>
[0062] scum-clogging resistance:
During metal working, when the scum generation amount of the lubricating coating is
large, the R die may be easily clogged by the scum. Therefore, the generation of scum
when wire drawing was performed under the condition without moisture absorption was
visually confirmed, and the scum-clogging resistance was evaluated in accordance with
the following evaluation criteria.
<evaluation criteria>
[0063]
⊚: Generation of scum was not substantially observed (scum generation amount was less
than 10% of the lubricating coating amount)
○: Generation of scum was small, and the generated scum was not viscous and not adsorbed
to the R die (scum generation amount was 10% or more and less than 30% of the lubricating
coating amount)
Δ: Scum generation amount was large, and the R die was easily clogged (scum generation
amount is 30% or more and less than 50% of the lubricating coating amount), or at
least the generated scum was adsorbed to the R die because the scum was viscous (scum
generation amount is 10% or more and less than 30% of the lubricating coating amount)
×: Scum generation amount was extremely large, and the R die was easily clogged (scum
generation amount is 50% or more of the lubricating coating amount), or the scum was
adsorbed to the R die because the scum was viscous (scum generation amount is 30%
or more of the lubricating coating amount)
[0064] workability with high difficulty (seizure resistance, moisture absorption resistance):
Working with high difficulty was performed, and the seizure resistance was evaluated.
In performance evaluation of the working with high difficulty, only an ironing step
in the upsetting-ball ironing tribo-type friction test method disclosed in a reference
document (Akinori Takahashi, Masatoshi Hirose, Shinobu Komiyama, and Wang Zhigang:
62nd Plastic Working Federation Lecture Meeting Preprint (2011), 89-90) was performed.
The evaluation before moisture absorption was performed after each of various aqueous
lubricants was applied onto a surface of the barrel-shaped test piece, followed by
the test piece being dried in an air heating furnace at 100°C to form a lubricating
coating on the surface of the test piece. Evaluation of the moisture absorption resistance
was performed after the test piece, on a surface of which a lubricating coating had
been formed, was left to stand for 24 hours in a thermo-hygrostat testing machine
at 30°C × 80% RH. Further, the formed coating amount was about 5 g/m2 in any one of the cases. Furthermore, the barrel-shaped test piece was used, the
test piece being prepared by performing the upsetting up to an upsetting ratio of
45% in a state that both end faces were restrained so as not to spread using a cylindrical
steel material (S10C) with a diameter of 14 mm and a length of 32 mm. The surface
roughness in the vicinity of the most protruded part on the side face of the test
piece was around Rz 9 µm. The upper and lower end faces of the barrel-shaped test
piece on which a lubricating coating had been formed were sandwiched between metal
molds, and the most protruded part was subjected to the ironing using three ball-shaped
molds (SUJ-2 bearing ball with a diameter of 10 mm). In addition, the ironing is strong
working in which the maximum surface area enlargement in the ironing part exceeds
200 times, and is working with extremely high difficulty.
<evaluation criteria>
[0065] In evaluation of the seizure resistance of the test piece to which working with high
difficulty had been performed, the degree of the seizure in the latter part of the
ironing with a large surface area enlargement was confirmed, and the evaluation was
performed in accordance with the evaluation criteria shown in Fig. 1.
[0066] corrosion resistance:
Various aqueous lubricants having a practical use concentration were coated on a steel
material of carbon steel S45C material that had been degreased and cleaned, followed
by drying with hot air to prepare each test piece for corrosion resistance evaluation
(coating adhesion mass after moisture volatilization was 5 g/m2). In corrosion resistance evaluation of each test piece, a test piece was left to
stand for 120 hours in a thermos-hygrostat at a temperature of 30°C, and a humidity
of 80%, and then the area where rust had been generated was measured, and the evaluation
was performed in accordance with the following evaluation criteria. Note that when
the evaluation result is "○" or more, it can be said that the test piece exhibited
excellent corrosion resistance even under a humid environment, therefore, it was determined
to have practical performance level.
<evaluation criteria>
[0067]
⊚: Rust occurrence area ratio was less than 10%
○: Rust occurrence area ratio was 10% or more and less than 20%
Δ: Rust occurrence area ratio was 20% or more and less than 50%
×: Rust occurrence area ratio was 50% or more
[0068] The above evaluation results are shown in Table 4. As is apparent from the Table
4, in Examples 1 to 29 in which the aqueous lubricant for metal material plastic working
of the present invention had been used, it was a practical level in all of the evaluation
items. On the other hand, in Comparative Examples 1 and 2 in which an alkali metal
salt of aliphatic polycarboxylic acid being outside the range of the present invention
had been used, the level was not a practical level in any of the seizure resistance,
the moisture absorption resistance, the scum-clogging resistance, and the corrosion
resistance. In Comparative Example 3 in which an alkaline earth metal had been used
without using aliphatic polycarboxylic acid, being outside the range of the present
invention, the level of the long-term agent stability did not reach a practical level.
Further, in Comparative Examples 4, 5, and 6 in which the carbon number of aliphatic
polycarboxylic acid was outside the range of the present invention, the level was
not a practical level in the seizure resistance, the moisture absorption resistance,
and the corrosion resistance. Furthermore, in Comparative Example 6, the level of
also the long-term agent stability did not reach a practical level. In Comparative
Example 7 in which the solubility in water of aliphatic polycarboxylic acid was outside
the range of the present invention, and in Comparative Example 8 in which the carbon
number and solubility in water of aliphatic polycarboxylic acid were outside the ranges
of the present invention, the alkaline earth metal salt of aliphatic polycarboxylic
acid could not be formed, and an aqueous lubricant could not be prepared in any of
Comparative Examples 7 and 8.
(Table 4)
[0069]
(Table 4)
|
long-term agent stability |
pull-out test |
workability with high difficulty |
corrosion resistance |
without moisture absorption |
with moisture absorption |
without moisture absorption |
with moisture absorption |
before dilution |
after dilution |
lubricity |
scum-clogging resistance |
lubricity |
seizure resistance |
seizure resistance |
|
1 |
○ |
Δ |
⊚ |
⊚ |
○ |
⊚ |
○ |
○ |
|
2 |
○ |
Δ |
⊚ |
⊚ |
○ |
⊚ |
○ |
○ |
|
3 |
⊚ |
⊚ |
○ |
○ |
○ |
○ |
○ |
○ |
|
4 |
⊚ |
⊚ |
○ |
○ |
○ |
○ |
○ |
○ |
|
5 |
Δ |
Δ |
⊚ |
⊚ |
○ |
⊚ |
⊚ |
○ |
|
6 |
Δ |
Δ |
Δ |
○ |
Δ |
○ |
Δ |
○ |
|
7 |
⊚ |
⊚ |
⊚ |
⊚ |
⊚ |
⊚ |
⊚ |
○ |
|
8 |
⊚ |
⊚ |
⊚ |
⊚ |
⊚ |
⊚ |
⊚ |
○ |
|
9 |
⊚ |
⊚ |
○ |
○ |
○ |
○ |
○ |
○ |
|
10 |
⊚ |
⊚ |
○ |
○ |
○ |
○ |
○ |
○ |
|
11 |
Δ |
Δ |
⊚ |
⊚ |
○ |
⊚ |
⊚ |
○ |
|
12 |
○ |
Δ |
Δ |
○ |
Δ |
○ |
Δ |
○ |
|
13 |
⊚ |
⊚ |
⊚ |
⊚ |
⊚ |
⊚ |
⊚ |
○ |
|
14 |
⊚ |
⊚ |
⊚ |
○ |
⊚ |
⊚ |
⊚ |
○ |
Example |
15 |
○ |
Δ |
⊚ |
⊚ |
○ |
⊚ |
○ |
○ |
|
16 |
⊚ |
⊚ |
⊚ |
⊚ |
⊚ |
⊚ |
⊚ |
○ |
|
17 |
Δ |
Δ |
Δ |
○ |
Δ |
Δ |
Δ |
○ |
|
18 |
⊚ |
⊚ |
○ |
○ |
○ |
○ |
○ |
○ |
|
19 |
⊚ |
⊚ |
○ |
○ |
○ |
○ |
○ |
○ |
|
20 |
⊚ |
⊚ |
⊚ |
⊚ |
⊚ |
⊚ |
⊚ |
○ |
|
21 |
⊚ |
⊚ |
⊚ |
⊚ |
⊚ |
⊚ |
⊚ |
○ |
|
22 |
⊚ |
⊚ |
⊚ |
⊚ |
⊚ |
⊚ |
⊚ |
○ |
|
23 |
⊚ |
⊚ |
⊚ |
⊚ |
⊚ |
⊚ |
⊚ |
○ |
|
24 |
⊚ |
⊚ |
⊚ |
⊚ |
⊚ |
⊚ |
⊚ |
○ |
|
25 |
⊚ |
⊚ |
○ |
⊚ |
○ |
○ |
○ |
○ |
|
26 |
⊚ |
⊚ |
○ |
○ |
○ |
○ |
○ |
○ |
|
27 |
⊚ |
⊚ |
○ |
○ |
○ |
○ |
○ |
○ |
|
28 |
⊚ |
⊚ |
⊚ |
⊚ |
⊚ |
⊚ |
⊚ |
○ |
|
29 |
⊚ |
⊚ |
⊚ |
⊚ |
⊚ |
⊚ |
⊚ |
○ |
Comparative Example |
1 |
⊚ |
⊚ |
Δ |
× |
× |
× |
× |
Δ |
2 |
⊚ |
⊚ |
Δ |
× |
× |
× |
× |
Δ |
3 |
× |
× |
○ |
○ |
○ |
○ |
○ |
○ |
4 |
Δ |
Δ |
○ |
○ |
× |
× |
× |
Δ |
5 |
Δ |
Δ |
○ |
○ |
× |
× |
× |
Δ |
6 |
× |
× |
○ |
○ |
× |
× |
× |
Δ |
7 |
- |
- |
- |
- |
- |
- |
- |
- |
8 |
- |
- |
- |
- |
- |
- |
- |
- |