Technical Field
[0001] The present invention relates to an inkjet recording method.
Background Art
[0002] In formation of an image by an inkjet system, droplets of ink are collected to thereby
form an image. Therefore, there are demands for advanced control of the landing positions
of the droplets, uniformity of the sizes of the droplets, and the like. The ink is
fed from an ink chamber to a pressure chamber and ejected from a nozzle. In an inkjet
recording apparatus having a common ink chamber for a plurality of pressure chambers,
a phenomenon called crosstalk may occur.
[0003] "Crosstalk" means that a pressure wave generated in one pressure chamber during ejection
of ink propagates to other pressure chamber to result in instability of the speed
of a droplet to be ejected (amount of a droplet). Crosstalk has an influence on the
size of a droplet and therefore may generate a streak in the scanning direction of
an inkjet head in an image formed. In particular, when ink is ejected in a large amount
as in formation of a solid image, the streak tends to be more easily generated.
[0004] As measures to crosstalk, the followings are known: a common ink chamber is divided
between rows of pressure chambers by a separation barrier to prevent a pressure wave
from propagating from one row of pressure chambers to other row of pressure chambers
(e.g., see PTL 1); the volume elasticity of a wall surface portion of a common ink
chamber, the surface portion facing the inlet of a pressure chamber, is set at a predetermined
value or less to attenuate a pressure wave propagating in the common ink chamber (e.g.,
see PTL 2), and the like. The streak, however, may be generated in formation of a
solid image, even if the above measures are taken. Thus, an inkjet recording method
has still room for improvement in measures to crosstalk. In PTLS 3 and 4, the influence
of the surface tension of ink on an image is described, but there is no description
about a relationship between the surface tension and crosstalk.
Document
EP 1 634 705 A discloses an ink-jet recording apparatus. The apparatus disclosed therein does not,
for example, employ a specific equation to represent the time difference which outputs
the drive signal with respect to each different drive group. Document
EP3 037 265 A has an earlier priority date than the current invention but was published after the
priority date of the current invention; i.e. the document is state of the art according
to Art. 54(3) EPC. This document discloses an inkjet dyeing method in which the ink
contains (among others) a disperse dye.
Citation List
Patent Literature
[0005]
PTL 1
Japanese Patent Application Laid-Open No. 2003-011368
PTL 2
Japanese Patent Application Laid-Open No. 2007-168185
PTL 3
Japanese Patent Application Laid-Open No. 2004-115708
PTL 4
Japanese Patent Application Laid-Open No. 2004-115649
Summary of Invention
Technical Problem
[0006] An object of the present invention is to more reduce generation of a streak in the
scanning direction of an inkjet head in a solid image.
[0007] The present invention relates to an inkjet recording method as set forth below:
- [1] An inkjet recording method including: applying a drive signal from a drive circuit
of an inkjet recording apparatus to each drive group to eject ink from a nozzle of
an inkjet head with respect to each drive group; in which the inkjet head comprises
a common ink chamber that receives ink, a head chip to which the ink in the common
ink chamber is to be fed, and a nozzle that ejects the ink fed to the head chip, the
head chip comprises a plurality of tubular pressure chambers that allow the nozzle
and the common ink chamber to be communicated, and a pressurizing portion that deforms
the pressure chambers to pressurize the pressure chambers, the pressure chambers are
aligned in two or more rows in the head chip, each row of the pressure chambers belongs
to a different drive group from a drive group of an adjacent row of the pressure chambers,
the drive circuit outputs the drive signal with respect to each different drive group
at time difference M represented by the following equation, and the ink has a surface
tension of 45 mN/m or less, and the ink contains a water-soluble dye, a pigment, a
reactive dye, an acid dye or a direct dye:

in which M represents a time difference, n represents an integer of 1 or more, AL
represents a half of an acoustic resonance period of a pressure wave in each of the
pressure chambers, and t represents a pressure wave transmission time to be determined
by "distance between nozzles in different drive groups"/"speed of sound transmitting
in ink".
- [2] The inkjet recording method according to [1], in which the ink comprises a surfactant,
and a content of the surfactant in the ink is 0.05 to 2mass%.
- [3] The inkjet recording method according to [1] or [2], in which the ink comprises
a water-soluble organic solvent having a surface tension of 40 mN/m or less.
- [4] The inkjet recording method according to any one of [1] to [3], in which the ink
has a dynamic surface tension of 50 mN/m or less at a bubble generation period of
10 Hz.
Advantageous Effects of Invention
[0008] According to the present invention, crosstalk is more reduced and therefore the dot
diameter after an ink ejected is landed on a recording medium is more uniformly controlled.
In addition, droplets of the ink are landed on the recording medium and then spread
thereon, and therefore dots of the ink are sufficiently overlapped. Accordingly, generation
of a streak in the scanning direction of an inkjet head in a solid image can be more
reduced.
Brief Description of Drawings
[0009]
FIG. 1 schematically illustrates one configuration example of an inkjet recording
apparatus for use in the present embodiment;
FIG. 2 is an exploded perspective view schematically illustrating a configuration
of an inkjet head of the inkjet recording apparatus;
FIG. 3 is a partial rear view of a head chip illustrated in FIG. 2;
FIG. 4 is a partial cross-sectional view of the head chip illustrated in FIG. 2;
FIG. 5 illustrates one example of a drive signal to be applied to an inkjet head in
the present embodiment;
FIG. 6A illustrates a part of one channel row of the inkjet head to which the drive
signal illustrated in FIG. 5 is not applied and FIG. 6B illustrates a part of one
channel row of the inkjet head to which the drive signal illustrated in FIG. 5 is
applied;
FIG. 7 illustrates the inkjet head in which two channel rows are divided into two
drive groups, respectively;
FIG. 8 illustrates respective drive signals to be applied to the two different drive
groups illustrated in FIG. 7;
FIG. 9 illustrates respective variations in droplet speed in the two drive groups
of the inkjet head;
FIG. 10A illustrates one example of drive periods of the drive signals applied to
the two drive groups of the inkjet head, and FIG. 10B illustrates an exploded view
of part B in FIG. 10A;
FIG. 11 illustrates an inkjet head having four channel rows;
FIG. 12 illustrates respective drive signals to be applied to two different drive
groups in the inkjet head illustrated in FIG. 11;
FIG. 13 illustrates an inkjet head having six channel rows;
FIG. 14 illustrates respective drive signals to be applied to three different drive
groups in the inkjet head illustrated in FIG. 13; and
FIG. 15 illustrates a mode where a drive apparatus in the present embodiment includes
two drive circuits that respectively drive two drive group sets, the sets each including
two different drive groups.
Description of Embodiments
[0010] An inkjet recording method according to one embodiment of the present invention includes
applying a drive signal from a drive circuit of an inkjet recording apparatus to each
drive group to eject ink from a nozzle of an inkjet head with respect to each drive
group.
First, one example of an inkjet recording apparatus for use in the present embodiment
is described.
[Inkjet recording apparatus]
[0011] FIG. 1 schematically illustrates one configuration example of inkjet recording apparatus
100 for use in the present embodiment. As illustrated in FIG. 1, inkjet recording
apparatus 100 includes conveyance mechanism 200 that conveys recording medium P, inkjet
head H disposed so as to face recording surface PS of recording medium P, and drive
apparatus 500 that drives inkjet head H.
[0012] Conveyance mechanism 200 includes a pair of conveyance rollers 201 that sandwiches
recording medium P, conveyance motor 202, and conveyance roller 203 to be rotatably
driven by conveyance motor 202. Recording medium P is conveyed by conveyance rollers
201 and conveyance roller 203 in Y direction (sub scanning direction) in FIG. 1.
[0013] Inkjet head H is mounted on carriage 400. Carriage 400 is disposed on guide rail
300 bridged over the width direction of recording medium P, in a reciprocative manner.
Guide rail 300 is disposed in a direction (X-X' direction (main scanning direction)
in FIG. 1) substantially perpendicular to the conveyance direction (sub scanning direction)
of recording medium P.
[0014] Drive apparatus 500 is electrically connected to inkjet head H via FPC 4.
[0015] FIG. 2 is an exploded perspective view of inkjet head H, FIG. 3 is a partial rear
view of the head chip, and FIG. 4 is a partial cross-sectional view of the head chip.
[0016] As illustrated in FIGS. 2 to 4, inkjet head H includes so-called harmonica type head
chip 1, nozzle plate 2, wiring substrate 3, FPC 4 and ink manifold 5.
[0017] Head chip 1 is an independent drive type head chip that performs recording by ejection
of ink from only drive channel 11. The shape of head chip 1 is a cuboid shape, and
head chip 1 has a plurality of through holes that pass from one surface of the cuboid
shape to other surface thereof. The through holes are arrayed in two rows on head
chip 1 in the plane direction. The shape of each of the through holes is a tubular
shape, and the shape in planar view of each of the through holes is a rectangular
shape. The "tubular shape" refers to a shape where the central axis line is substantially
straight and the distance from the central axis line to the wall surface is substantially
constant. The cross-sectional shape of each of the through holes may be a circular
or non-circular shape, for example. Thus, head chip 1 has two channel rows (row A
and row B) each including a plurality of channels arrayed. In the channel rows of
head chip 1, drive channel 11 as a pressure chamber from which ink is to be ejected
and dummy channel 12 to which no ink is ejected are alternately arrayed in the arraying
direction of the channels.
[0018] Drive channels arrayed in one row (also referred to as "row A") of the two channel
rows are each defined as 11A, and dummy channels arrayed in row A are each defined
as 12A. In addition, drive channels arrayed in other row (also referred to as "row
B") of the two channel rows are each defined as 11B, and dummy channels arrayed in
row B are each defined as 12B.
[0019] As described above, drive channels (11A, 11B) and dummy channels (12A, 12B) are alternately
arrayed in respective channel rows (row A or row B). Partition 13 located between
each drive channel (11A, 11B) and each dummy channel (12A, 12B) that are adjacent
to each other is formed by a piezoelectric element such as PZT. Hereinafter, each
partition in row A and each partition in row B may be referred to as 13A and 13B,
respectively.
[0020] Furthermore, head chip 1 includes drive electrode 14 that is closely attached to
the inner surface of each channel (11A, 11B, 12A, 12B), and connection electrodes
15A and 15B that are each connected to drive electrode 14 and are arrayed on rear
end surface 1c of head chip 1. Connection electrodes 15A extend out from respective
channels A till one edge of rear end surface 1c, and connection electrodes 15B extend
out from respective channels B towards one edge of rear end surface 1c.
[0021] In head chip 1 in FIG. 2, an end surface at which ink is to be ejected is referred
to as "front end surface 1a" and an end surface opposite thereto is referred to as
"rear end surface 1c". Each drive channel (11A, 11B) and each dummy channel (12A,
12B) are opened on each of front end surface 1a and rear end surface 1c of head chip
1.
[0022] Nozzle plate 2 adheres to front end surface 1a of head chip 1 by an adhesive. Nozzle
plate 2 includes a plurality of nozzles 21 that are opened at positions corresponding
to respective drive channels 11A and 11B. The opening shape of each of nozzles 21
is, for example, a circular shape.
[0023] Wiring substrate 3 has a larger rectangular shape in planar view than head chip 1.
Wiring substrate 3 is bonded to rear end surface 1c of head chip 1 in bonding region
[0024] (region illustrated by a dashed line in FIG. 2) 31. Wiring substrate 3 includes through
holes 32A and 32B, and wiring electrodes 33A and 33B.
[0025] Through holes 32A and 32B correspond to drive channels 11A and 11B that are opened
on rear end surface 1c of head chip 1, respectively. Wiring electrodes 33A and 33B
are disposed on a surface of wiring substrate 3, the surface being closer to bonding
region 31, and are alternately arrayed in the arraying direction. Wiring electrodes
33A and wiring electrodes 33B are disposed at positions for connection to connection
electrodes 15A and at positions for connection to connection electrodes 15B, respectively.
Wiring electrodes 33A and 33B are formed by, for example, vapor deposition or a sputtering
method.
[0026] When wiring substrate 3 adheres to rear end surface 1c of head chip 1 in bonding
region 31, connection electrodes 15A and 15B of head chip 1 are electrically connected
to wiring electrodes 33A and 33B of wiring substrate 3, respectively. In addition,
when wiring substrate 3 adheres to rear end surface 1c of head chip 1 in bonding region
31, dummy channels 12A and 12B are clogged by wiring substrate 3.
[0027] Wiring substrate 3 and head chip 1 are bonded by an adhesive at a predetermined pressure
(for example, 1 MPa or more). The adhesive to be used may be an anisotropic conductive
adhesive including a conductive particle, and is preferably an adhesive including
no conductive particle in order to enhance certainty of shortage prevention.
[0028] FPC 4 adheres to one edge portion on a surface of wiring substrate 3, the surface
being closer to bonding region 31. When FPC 4 adheres to the one edge portion, wiring
electrodes 33A and 33B of wiring substrate 3 are electrically connected to wiring
of FPC 4 in corresponding manner.
[0029] Ink manifold 5 is, for example, a vessel having a rectangular opening and having
a bottom. When wiring substrate 3 adheres to ink manifold 5 at the opening of the
vessel, the interior space of the vessel is communicated with the exterior via each
of the channels and nozzles 21. The interior space serves as common ink chamber 51
to which ink is to be fed. Respective drive channels 11A and 11B are communicated
with each other via common ink chamber 51.
[Ink]
[0030] Ink is fed to common ink chamber 51 and received therein. The surface tension of
the ink is 45 mN/m or less. When the surface tension is more than 45 mN/m, streak
unevenness in the scanning direction of the inkjet head may be generated in a solid
image in solid image formation. The surface tension of the ink is preferably 33 mN/m
or less from the viewpoint of more enhancing uniformity of a solid image. The surface
tension can be determined by a known method such as a ring method (Denuce' method)
or a platinum plate method (Wilhelmy method) described in Japanese Patent Application
Laid-Open No.
2004-115708. The surface tension can also be adjusted by, for example, the content of a surfactant
in the ink.
[0031] The dynamic surface tension of the ink is preferably 50 mN/m or less, more preferably
45 mN/m or less as a dynamic surface tension value measured with a bubble pressure
method (maximum bubble pressure method) at a bubble generation period of 10 Hz, from
the viewpoint of stable ejection performance of the inkjet head. The dynamic surface
tension can be determined by other measurement method such as a known method, for
example, a meniscus method, a dropping method, a γ/A curve method, a vibration jet
method, or a curtain coater method, as described in Japanese Patent Application Laid-Open
No.
2004-115708. The dynamic surface tension can also be adjusted by compounding of a surfactant
and/or an organic solvent.
[0032] Examples of the ink include an ink containing water, a water-soluble organic solvent,
a surfactant and a colorant.
[0033] The water may be ion exchange water. The amount of the water relative to the total
mass of the ink is, for example, 20 to 60mass%.
[0034] The water-soluble organic solvent may be used singly or in combinations two or more.
Examples of the water-soluble organic solvent include a polyhydric alcohol, an amine,
a monohydric alcohol, an alkyl ether of a polyhydric alcohol, 2,2'-thiodiethanol,
an amide, a heterocyclic compound, and acetonitrile.
[0035] Examples of the polyhydric alcohol include ethylene glycol, glycerin, 2-ethyl-2-(hydroxymethyl)-1,3-propanediol,
tetraethylene glycol, triethylene glycol, tripropylene glycol, 1,2,4-butanetriol,
diethylene glycol, propylene glycol, dipropylene glycol, butylene glycol, 1,6-hexanediol,
1,2-hexanediol, 1,5-pentanediol, 1,2-pentanediol, 2,2-dimethyl-1,3-propanediol, 2-methyl-2,4-pentanediol,
3-methyl-1,5-pentanediol, 3-mcthyl-1,3-butanediol and 2-methyl-1,3-propanediol.
[0036] Examples of the amine include ethanolamine and 2-(dimethylamino)ethanol.
[0037] Examples of the monohydric alcohol include methanol, ethanol and butanol.
[0038] Examples of the alkyl ether of polyhydric alcohol include diethylene glycol monomethyl
ether, diethylene glycol monobutyl ether, triethylene glycol monomethyl ether, triethylene
glycol monobutyl ether, ethylene glycol monomethyl ether, ethylene glycol monobutyl
ether, propylene glycol monomethyl ether, propylene glycol monobutyl ether and dipropylene
glycol monomethyl ether.
[0039] Examples of the amide include N,N-dimethylformamide.
[0040] Examples of the heterocyclic compound include 2-pyrrolidone.
[0041] The water-soluble organic solvent preferably has a surface tension (static surface
tension) of 40 mN/m or less from the viewpoint that the surface tension of the ink
is properly adjusted. Examples of such a water-soluble organic solvent include triethylene
glycol monobutyl ether (36.2), propylene glycol (35.6), dipropylene glycol (32), dipropylene
glycol monopropyl ether (27.6) and tripropylene glycol monomethyl ether (30.0). The
numbers in parentheses are surface tension values (unit: mN/m).
[0042] When the surface tension of the ink is desired to be adjusted to a larger value,
a water-soluble organic solvent having a large surface tension is preferably used
singly or in combination. Examples of a water-soluble organic solvent having a surface
tension of more than 40 mN/m include ethylene glycol (48.4), diethylene glycol (48.5),
triethylene glycol (45.2), 1,5-pentanediol (43.2), glycerin (63.0) and 2-pyrrolidone
(47.0).
[0044] The amount of the water-soluble organic solvent relative to the total mass of the
ink is, for example, 10 to 60mass%.
[0045] The surfactant may be any of cationic, anionic, amphoteric and non-ionic surfactants.
The surfactant may be used singly or in combinations of two or more.
[0046] Examples of the cationic surfactant include an aliphatic amine salt, an aliphatic
quaternary ammonium salt, a benzalkonium salt, benzethonium chloride, a pyridinium
salt and an imidazolinium salt.
[0047] Examples of the anionic surfactant include fatty acid soap, an N-acyl-N-methylglycine
salt, an N-acyl-N-methyl-β-alanine salt, N-acylglutamate, alkyl ether carboxylate,
acylated peptide, alkyl sulfonate, alkylbenzene sulfonate, alkylnaphthalene sulfonate,
dialkyl sulfosccinate, alkyl sulfoacetate, α-olefin sulfonate, N-acylmethyltaurine,
sulfated oil, higher alcohol sulfate, higher secondary alcohol sulfate, alkyl ether
sulfate, higher secondary alcohol ethoxysulfate, polyoxyethylene alkyl phenyl ether
sulfate, monoglysulfate, fatty acid alkyloamide sulfate, alkyl ether phosphate and
alkyl phosphate.
[0048] Examples of the amphoteric surfactant include a carboxybetaine surfactant, a sulfobetaine
surfactant, an amino carboxylic acid salt, and imidazolinium betaine.
[0049] Examples of the non-ionic surfactant include polyoxyethylene alkyl ether, polyoxyethylene
secondary alcohol ether, polyoxyethylene alkyl phenyl ether (for example, Emulgen
911), polyoxyethylene sterol ether, a polyoxyethylene lanolin derivative, polyoxyethylene
polyoxypropylene alkyl ether (for example, Newpol PE-62), polyoxyethyleneglycerin
fatty acid ester, polyoxyethylene castor oil, hydrogenated castor oil, polyoxyethylene
sorbitan fatty acid ester, polyoxyethylene sorbitol fatty acid ester, polyethylene
glycol fatty acid ester, fatty acid monoglyceride, polyglycerin fatty acid ester,
sorbitan fatty acid ester, propylene glycol fatty acid ester, sucrose fatty acid ester,
fatty acid alkanolamide, polyoxyethylene fatty acid amide, polyoxyethylene alkyl amine,
alkyl amine oxide, acetylene glycol and acetylene alcohol. "Emulgen" is a registered
trademark of Kao Corporation, and "Newpol" is a registered trademark of Sanyo Chemical
Industries, Ltd.
[0050] The surfactant is preferably a non-ionic surfactant or an anionic surfactant, more
preferably sodium dodecylbenzenesulfonate, sodium 2-ethylhexylsulfosuccinate, sodium
alkylnaphthalenesulfonate, a phenol-ethylene oxide adduct, or an acetylenediol-ethylene
oxide adduct.
[0051] The content of the surfactant in the ink can be appropriately determined from the
viewpoints of enhancement in dispersibility of a colorant and adjustment of the surface
tension of the ink, and is, for example, 0.05 to 2mass%.
[0052] The colorant may be used singly or in combinations of two or more. The colorant include
a water-soluble dye, pigment, a reactive dye, an acid dye and a direct dye. As the
colorant, for example, any of various colorants described in "
Dyeing Note 21st Edition" (Shikisensha Co., Ltd.) can be used.
[0053] The water-soluble dye has an ionic water-soluble group in the molecule, and is compounded
in the ink in the state of being dissolved.
[0054] The pigment is not dissolved in water, and is compounded in the ink in the state
of being dispersed as a fine particle.
[0055] Examples of the pigment include carbon black; C. I. Pigment Yellow 1, 3, 12, 13,
14, 16, 17, 43, 55, 74, 81, 83, 109, 110, 128; C. I. Pigment Orange 13, 16, 34, 43;
C. I. Pigment Red 2, 5, 8, 12, 17, 22, 23, 41, 112, 114, 122, 123, 146, 148, 150,
166, 170, 220, 238, 245, 258; C. I. Pigment Violet 19, 23; C. I. Pigment Blue 15,
15:1, 15:3, 15:5, 29; C. I. Pigment Green 7, 8; C. I. Pigment Brown 22; C. I. Pigment
Black 1, 7; and C. I. Pigment White 6.
[0056] Examples of the reactive dye include C. I. Reactive Yellow 2, 3, 15, 17, 18, 22,
23, 24, 25, 27, 37, 39, 42, 57, 69, 76, 81, 84, 85, 86, 87, 92, 95, 102, 105, 111,
125, 135, 136, 137, 142, 143, 145, 151, 160, 161, 165, 167, 168, 175, 176; C. I. Reactive
Orange 1, 4, 5, 7, 11, 12, 13, 15, 16, 20, 30, 35, 56, 64, 67, 69, 70, 72, 74, 82,
84, 86, 87, 91, 92, 93, 95, 107; C. I. Reactive Red 2, 3, 3:1, 5, 8, 11, 21, 22, 23,
24, 28, 29, 31, 33, 35, 43, 45, 49, 55, 56, 58, 65, 66, 78, 83, 84, 106, 111, 112,
113, 114, 116, 120, 123, 124, 128, 130, 136, 141, 147, 158, 159, 171, 174, 180, 183,
187, 190, 193, 194, 195, 198, 218, 220, 222, 223, 228, 235; C. I. Reactive Violet
1, 2, 4, 5, 6, 22, 23, 33, 36, 38; C. I. Reactive Blue 2, 3, 4, 7, 13, 14, 15, 19,
21, 25, 27, 28, 29, 38, 39, 41, 49, 50, 52, 63, 69, 71, 72, 77, 79, 89, 104, 109,
112, 113, 114, 116, 119, 120, 122, 137, 140, 143, 147, 160, 161, 162, 163, 168, 171,
176, 182, 184, 191, 194, 195, 198, 203, 204, 207, 209, 211, 214, 220, 221, 222, 231,
235, 236; C. I. Reactive Green 8, 12, 15, 19, 21; C. I. Reactive Brown 2, 7, 9, 10,
11, 17, 18, 19, 21, 23, 31, 37, 43, 46; and C. I. Reactive Black 5, 8, 13, 14, 31,
34, 39.
[0057] Examples of the acid dye include C. I. Acid Yellow 1, 3, 11, 17, 18, 19, 23, 25,
36, 38, 40, 40:1, 42, 44, 49, 59, 59:1, 61, 65, 67, 72, 73, 79, 99, 104, 159, 169,
176, 184, 193, 200, 204, 207, 215, 219, 219:1, 220, 230, 232, 235, 241, 242, 246;
C. I. Acid Orange 3, 7, 8, 10, 19, 24, 51, 51S, 56, 67, 74, 80, 86, 87, 88, 89, 94,
95, 107, 108, 116, 122, 127, 140, 142, 144, 149, 152, 156, 162, 166, 168; C. I. Acid
Red 1, 6, 8, 9, 13, 18, 27, 35, 37, 52, 54, 57, 73, 82, 88, 97, 97:1, 106, 111, 114,
118, 119, 127, 131, 138, 143, 145, 151, 183, 195, 198, 211, 215, 217, 225, 226, 249,
251, 254, 256, 257, 260, 261, 265, 266, 274, 276, 277, 289, 296, 299, 315, 318, 336,
337, 357, 359, 361, 362, 364, 366, 399, 407, 415; C. I. Acid Violet 17, 19, 21, 42,
43, 47, 48, 49, 54, 66, 78, 90, 97, 102, 109, 126; C. I. Acid Blue 1, 7, 9, 15, 23,
25, 40, 61:1, 62, 72, 74, 80, 83, 90, 92, 103, 104, 112, 113, 114, 120, 127, 127:1,
128, 129, 138, 140, 142, 156, 158, 171, 182, 185, 193, 199, 201, 203, 204, 205, 207,
209, 220, 221, 224, 225, 229, 230, 239, 258, 260, 264, 277:1, 278, 279, 280, 284,
290, 296, 298, 300, 317, 324, 333, 335, 338, 342, 350; C. I. Acid Green 9, 12, 16,
19, 20, 25, 27, 28, 40, 43, 56, 73, 81, 84, 104, 108, 109; C. I. Acid Brown 2, 4,
13, 14, 19, 28, 44, 123, 224, 226, 227, 248, 282, 283, 289, 294, 297, 298, 301, 355,
357, 413; and C. I. Acid Black 1, 2, 3, 24, 24:1, 26, 31, 50, 52, 52:1, 58, 60, 63,
63S, 107, 109, 112, 119, 132, 140, 155, 172, 187, 188, 194, 207, 222.
[0058] Examples of the direct dye include C. I. Direct Yellow 8, 9, 10, 11, 12, 22, 27,
28, 39, 44, 50, 58, 86, 87, 98, 105, 106, 130, 137, 142, 147, 153; C. I. Direct Orange
6, 26, 27, 34, 39, 40, 46, 102, 105, 107, 118; C. I. Direct Red 2, 4, 9, 23, 24, 31,
54, 62, 69, 79, 80, 81, 83, 84, 89, 95, 212, 224, 225, 226, 227, 239, 242, 243, 254;
C. I. Direct Violet 9, 35, 51, 66, 94, 95; C. I. Direct Blue 1, 15, 71, 76, 77, 78,
80, 86, 87, 90, 98, 106, 108, 160, 168, 189, 192, 193, 199, 200, 201, 202, 203, 218,
225, 229, 237, 244, 248, 251, 270, 273, 274, 290, 291; C. I. Direct Green 26, 28,
59, 80, 85; C. I. Direct Brown 44, 44:1, 106, 115, 195, 209, 210, 212:1, 222, 223;
and C. I. Direct Black 17, 19, 22, 32, 51, 62, 108, 112, 113, 117, 118, 132, 146,
154, 159, 169.
[0059] The content of the colorant in the ink is preferably 0.1 to 20mass%, more preferably
0.2 to 13mass%.
[0060] The average particle size of the pigment is preferably 300 nm or less, or the maximum
particle size of the pigment is preferably 900 nm or less. If the average particle
size or the maximum particle size exceeds the above range, clogging easily occurs
in inkjet textile printing where the ink is launched from a fine nozzle, and the ink
cannot be stably launched for a long period of time in some cases.
[0061] The average particle size or the maximum particle size can be measured by use of
a commercially available particle size measuring machine such as Zeta Sizer 1000 manufactured
by Malvern Instruments Ltd. according to a light scattering method, an electrophoresis
method, a laser Doppler method, or the like. In addition, the average particle size
or the maximum particle size can be adjusted by a dispersion treatment of the pigment
with a commercially available dispersant by a bead mill or the like, classification
of the pigment, mixing of classified products, or the like.
[0062] The ink may further contain other component as long as the surface tension thereof
is in the range of 45 mN/m or less. In order to stably maintain the viscosity and/or
keep the dye stable, or improve color development, the ink may contain, for example,
an inorganic salt. Examples of the inorganic salt include sodium chloride, sodium
sulfate, magnesium chloride and magnesium sulfide.
[0063] In addition, the ink may contain a preservative agent or an antifungal agent in order
to maintain long-term storage stability of the ink. Examples of the preservative agent
or the antifungal agent include an aromatic halogen compound (for example, Preventol
CMK), methylene dithiocyanate, a halogenated nitrogen-containing sulfur compound,
and 1,2- benzisothiazolin-3-one (for example, PROXEL GXL). "Preventol" is a registered
trademark of Lanxess AG, and "PROXEL" is a registered trademark of Arch Chemicals
Inc.
[Drive of inkjet head]
[0064] Next, drive of the inkjet head is described. FIG. 5 illustrates one example of a
drive signal to be applied to inkjet head H. The drive signal is a pulse that allows
the ink from nozzles 21 of inkjet head H to be ejected. The drive signal is a rectangular
wave having a positive voltage (+V) and pulse width PW, and allows a negative pressure
to be generated in each channel.
[0065] The "pulse" refers to a rectangular wave having a constant voltage peak value. Pulse
width PW refers to a time difference, in assumption of 0 V being 0% and the voltage
peak value being 100%, between the timing where the voltage rises from 0 V and reaches
10% and the timing where the voltage falls from the voltage peak value and reaches
10%. In addition, the rectangular wave means a waveform where voltage of each of the
rise time from 10% to 90% of the voltage peak value and the fall time from 90% to
10% of the voltage peak value is within a half, preferably a quarter of AL.
[0066] The ink ejection operation of inkjet head H by the drive signal is described with
reference to FIG. 6A and FIG. 6B. FIG. 6A illustrates a part of one channel row of
inkjet head H to which the drive signal illustrated in FIG. 5 is not applied, and
FIG. 6B illustrates a part of one channel row of inkjet head H to which the drive
signal illustrated in FIG. 5 is applied.
[0067] As illustrated in FIG. 6A, when the drive signal is not applied to drive electrode
14, partition 13 between drive channel 11 and dummy channel 12 is not deformed (in
a neutral state). When the drive signal is applied to drive electrode 14, an electric
field is produced in the direction perpendicular to the polarization directions (indicated
by arrows in the drawing) of a piezoelectric element forming partition 13. As a result,
as illustrated in FIG. 6B, the central portion of partition 13 located at each of
both side surfaces of drive channel 11, in planar view, is deformed by shearing towards
the outside. Therefore, the volume of drive channel 11 is expanded and the pressure
in drive channel 11 is a negative pressure. Accordingly, the ink flows into drive
channel 11.
[0068] The deformation state is maintained for predetermined pulse width PW, and thereafter
the potential of the drive signal returns to 0 to allow partition 13 to return to
the neutral state again. Therefore, the ink in drive channel 11 is pressurized and
ejected from nozzles 21 as droplets.
[0069] The drive signal is periodically applied to drive electrode 14 to thereby allow the
ink pressure in drive channel 11 to be changed "from negative to positive" and then
"from positive to negative" by deformation of partition 13 at every one period, as
described above.
[0070] The duration (pulse width PW) of the drive signal is represented by AL (Acoustic
Length). The AL corresponds to a half of the acoustic resonance period of a pressure
wave in drive channel 11. In order to efficiently eject droplets, pulse width PW of
the drive signal is preferably approximate to the time difference (1 AL) between the
timing where the pressure in drive channel 11 is converted "from negative to positive"
and the timing where the pressure is converted "from positive to negative", specifically
preferably in the range of 0.8 AL or more and 1.2 AL or less.
[0071] The AL is determined as a pulse width where, when the speed of a droplet to be ejected
in application of a drive signal having a rectangular wave to drive electrode 14 is
measured and pulse width PW of the rectangular wave is changed with the voltage value
of the rectangular wave being constant, the flying speed of the droplet reaches the
maximum.
[0072] Next, a method is described in which drive apparatus 500 applies a drive signal to
inkjet head H. In drive apparatus 500, all channel rows of inkjet head H are divided
into N (in which N represents an integer of 2 or more) drive groups, and each drive
group is independently driven. Adjacent channel rows belong to different drive groups.
[0073] FIG. 7 illustrates inkjet head H in which two channel rows is divided into two drive
groups, respectively. When the N is "2", two channel rows of inkjet head H, namely,
a channel row as row A and a channel row as row B, belong to drive group A (DG-A)
and drive group B (DG-B), respectively, for example, as illustrated in FIG. 7. In
other words, all the channel rows of inkjet head H are divided into two drive groups.
[0074] In inkjet head H, the drive signal from drive apparatus 500 is applied to drive channels
of a channel row belonging to one drive group within drive period T of inkjet head
H at the same timing. In other words, the same drive signal is simultaneously applied
to all drive channels 11 of a channel row belonging to the same drive group. Each
drive channel 11 and each dummy channel 12 included in one channel row is naturally
included in the same drive group.
[0075] In FIG. 7, "D" represents a "distance between nozzles in different drive groups",
and a distance between adjacent and different drive groups. When two drive groups
by two channel rows are present, the "distance between nozzles in different drive
groups" is designated as D as illustrated in FIG. 7.
[0076] Drive apparatus 500 outputs a drive signal with respect to each different drive group
at time difference M represented by the following equation. In the following equation,
M represents the time difference, n represents any integer of 1 or more, AL represents
a half of the acoustic resonance period of the pressure wave in each of the pressure
chambers, and t represents a pressure wave transmission time determined by "distance
between nozzles in different drive groups"/"speed of sound transmitting in ink".

[0077] FIG. 8 illustrates respective drive signals to be applied to two different drive
groups A and B. Drive apparatus 500 applies a drive signal to drive group B later
than a drive signal to drive group A by time difference M. Thus, there is a time difference
represented by "nAL + t" (hereinafter, also referred to as "retardation") between
the drive signal to be applied from drive apparatus 500 to drive electrode 14 of each
drive channel 11 forming drive group A and the drive signal to be applied from drive
apparatus 500 to drive electrode 14 of each drive channel 11 forming drive group B,
as illustrated in FIG. 8.
[0078] The drive signal is applied to drive group A at drive period T. Drive group A is
always driven before drive group B by time difference M. FIG. 8 illustrates an example
in which n = 1.
[0079] With respect to "t" in the equation, "speed of sound transmitting in ink" (C) can
be calculated by the following equation. Speed C is an intrinsic value for the ink.
In the following equation, K represents the volume elasticity of the ink, and ρ represents
the density of the ink.
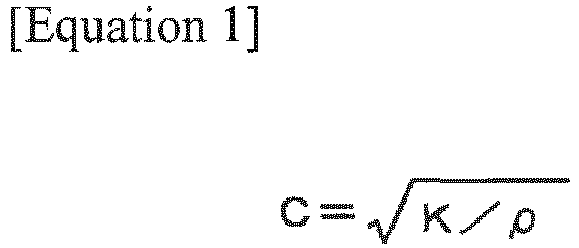
[0080] Drive channel 11A of drive group A and drive channel 11B of drive group B are communicated
with each other via common ink chamber 51. Therefore, when a drive signal is applied
to each of drive electrode 14 of drive channel 11A of drive group A and drive electrode
14 of drive channel 11B of drive group B to eject a droplet, the speed of the droplet
may considerably vary by the influence of crosstalk.
[0081] The present inventors, however, have found by experiments that when inkjet head H
is driven so that a droplet is ejected from drive channel 11A of drive group A and
a droplet is then ejected from drive channel 11B of drive group B after a predetermined
time lag, the speed of the droplet to be ejected from drive channel 11B of drive group
B periodically varies relative to the speed of the droplet to be ejected from drive
channel 11A of drive group A depending on the predetermined time lag, as described
below.
[0082] FIG. 9 illustrates respective variations in droplet speed in the two drive groups
of inkjet head H. As illustrated in FIG. 9, the speed of the droplet to be ejected
from drive channel 11B (droplet speed) is repeatedly inverted to a positive or negative
value at every 1 AL after a certain "time lag" from ejection of the droplet in drive
group A. During such inversion, the droplet speed of drive group B reaches substantially
the same speed as the speed of the droplet from drive channel 11A of drive group A
(droplet speed).
[0083] Furthermore, the "time lag" from ejection of the droplet in drive group A corresponds
to the "time t". In other words, it has been found that the speed of the droplet from
drive channel 11B of drive group B after a lapse of nAL + t from ejection of the droplet
from drive channel 11A of drive group A reaches substantially the same speed as the
speed of the droplet from drive channel 11A of drive group A.
[0084] Therefore, retardation nAL + t can be imparted between the drive signal to be applied
to drive group A and the drive signal to be applied to drive group B to thereby substantially
eliminate the influence of crosstalk between drive group A and drive group B that
share common ink chamber 51, without any modification of a main structure of inkjet
head H. In other words, the variation in droplet speed between channel rows can be
suppressed. Moreover, the retardation between the drive signal of drive group A and
the drive signal of drive group B is imparted and therefore the drive load is also
suppressed.
[0085] As illustrated in FIG. 9, the speed of the droplet from each drive channel 11 of
drive group B is inverted to a positive or negative value at every 1 AL after a lapse
of time t. Therefore, n may represent an integer of 1 or more. Preferably, however,
the drive signal for ejection from a drive group to be driven later is not overlapped
with next drive period T. In addition, if the value of n is too large, the difference
in drive timing between different drive groups can be larger to result in a reduction
in printing speed. Therefore, n preferably represents a value as small as possible,
most preferably represents 1, from the viewpoint of an increase in printing speed.
[0086] An inkjet head having a plurality of channel rows usually ejects droplets from nozzles
at different timings in advance in order to adjust displacement of landing positions
due to the difference in physical nozzle position between mutually adjacent channel
rows. FIG. 10A illustrates one example of drive periods of the drive signals applied
to drive groups A and B of inkjet head H, and FIG. 10B illustrates an exploded view
of part B in FIG. 10A.
[0087] For example, in inkjet head H, nozzle 21 in first row (for example, drive group A)
initiates ink ejection at a certain physical position on recording medium P, as illustrated
in FIG. 10A. Recording medium P and inkjet head H are then relatively moved, and nozzle
21 in second row (drive group B) arrives at the physical position. The time from the
initiation time of ejection in first row to the arrival time of second row correspond
to landing position adjustment period (P1). As soon as nozzle 21 in second row (drive
group B) arrives at the physical position, nozzle 21 in second row then initiates
ink ejection (P2). Thus, both the drive groups are driven together. Generally, each
drive channel 11 performs ejection at the same drive timing and ejects ink at the
same time point in each drive channel, and is merely different in the initiation time
and the termination time with respect to each channel row.
[0088] As illustrated in FIG. 10B, however, a drive signal is applied to drive group B after
the above time lag from application of a drive signal to drive group A in inkjet head
H. In other words, retardation nAL + t is imparted with respect to the timing of application
of a drive signal between drive group A and drive group B that are different, during
a period where the two drive groups are driven together. Thus, the timing itself where
a droplet is ejected differs between the drive groups. Retardation nAL + t between
the drive groups thus means the time lag not including the differences in the initiation
time and the termination time (landing position adjustment period between the drive
groups) due to landing position adjustment by the difference in physical nozzle position
between the drive groups.
[0089] Retardation nAL + t is imparted between drive group A and drive group B and thus,
strictly speaking, the droplet landing position may be necessary to be adjusted between
drive group A and drive group B. Such a problem, however, can be solved by adjusting
the relative movement speeds of recording medium P and inkjet head H.
[0090] One drive group may include a plurality of channel rows. The inkjet head in the present
embodiment may include a plurality of channel rows. For example, a plurality of channel
rows can be divided into N (in which N represents an integer of 2 or more) drive groups
to drive the inkjet head similarly as described above.
[0091] FIG. 11 illustrates an inkjet head having four channel rows. The inkjet head has
four channel rows as illustrated in FIG. 11. The four channel rows are divided into
two drive groups (drive group A and drive group B). Mutually adjacent channel rows
belong to mutually different drive groups, and drive group A and drive group B are
alternately arrayed in the direction perpendicular to the arraying direction of channels.
[0092] In FIG. 11, D' represents a distance between drive group sets, and represents a distance
between the centers of nozzles in adjacent channel rows in adjacent sets. D' is preferably
equal to D or large so that a pressure wave is sufficiently attenuated. D represents
the "distance between nozzles in different drive groups" described above.
[0093] FIG. 12 illustrates respective drive signals to be applied to two different drive
groups A and B in the inkjet head illustrated in FIG. 11. Also in the inkjet head
in FIG. 11, retardation 1 AL + t (when n = 1) is imparted between drive group A and
drive group B as in drive groups A and B in inkjet head H described above. Thus, suppression
of the variation in droplet speed between drive groups A and B and a reduction in
drive load can be achieved as in the above inkjet head.
[0094] Alternatively, the inkjet head may include three drive groups. FIG. 13 illustrates
an inkjet head having six channel rows, and FIG. 14 illustrates respective drive signals
to be applied to three different drive groups A, B and C in the inkjet head illustrated
in FIG. 13.
[0095] The inkjet head illustrated in FIG. 13 includes six channel rows. The six channel
rows are divided into two drive group sets, and each of the drive group sets is divided
into three drive groups (drive group A, drive group B and drive group C (DG-C)). In
the inkjet head, drive groups A, B, C, A, B, C are arrayed, in the order presented,
in the direction perpendicular to the arraying direction of channels so that mutually
adjacent channel rows belong to mutually different drive groups. In FIG. 13, both
of D and D' are as described with respect to the inkjet head in FIG. 11.
[0096] In the inkjet head illustrated in FIG. 13, as illustrated in FIG. 14, retardation
1 AL + t (when n = 1) is imparted between drive group A and drive group B that are
mutually adjacent, and between drive group B and drive group C that are mutually adjacent,
respectively. Thus, suppression of the variation in droplet speed among respective
drive groups A, B and C and a reduction in drive load can be achieved as in the above
inkjet head.
[0097] When channel rows are divided into three or more drive groups, n in retardation nAL
+ t among the drive groups may be changed, for example, n in the retardation between
drive groups A and B may be different from n in the retardation between drive groups
B and C, but all of n values are preferably the same from the viewpoint that a reduction
in printing speed is avoided.
[0098] In three or more channel rows, drive groups of adjacent channel rows are preferably
mutually different. The reason is because channel rows belonging to different drive
groups are disposed between channel rows belonging to the same drive group to thereby
increase the distance between the channel rows in the same drive group, resulting
in a reduction in the influence of crosstalk in the same drive group.
[0099] Drive apparatus 500 may include two or more drive circuits. In other words, all the
channel rows of inkjet head H may not be driven by one common drive circuit in drive
apparatus 500. While each of two or more drive circuits in drive apparatus 500 may
drive channel rows with respect to each drive group or each drive group set, channel
rows driven one drive circuit preferably belong to mutually different drive groups
(one drive circuit drives channel rows with respect to each drive group set).
[0100] FIG. 15 illustrates a mode where drive apparatus 500 includes two drive circuits
501 and 502 that respectively drive two drive group sets, the sets each including
two different drive groups. As illustrated in FIG. 15, inkjet head H includes four
channel rows. Adjacent two channel rows form a drive group set, and the adjacent two
channel rows in the set belong to drive groups A and B, respectively. Drive apparatus
500 includes two drive circuits 501 and 502, drive circuit 501 is connected to each
channel row of one of the drive group sets, and drive circuit 502 is connected to
each channel row of the other of the drive group sets.
[0101] The mode is more preferable from the viewpoint of reducing a reduction in droplet
speed. The reason is because a reduction in the number of drive channels to be simultaneously
driven in one drive circuit can reduce the load to the drive circuit to reduce waveform
rounding of a drive signal.
[0102] Inkjet head H scans and moves on recording surface PS of recording medium P in X-X'
direction illustrated, along with movement in the main scanning direction of carriage
400. A desired image is recorded by droplet ejection from nozzles in the course of
this scanning and moving.
[Modification Example]
[0103] While the drive signal has a rectangular wave having a positive voltage (+V) and
pulse width PW, as described above, in order to generate a negative pressure in drive
channel 11, the waveform of the drive signal can be appropriately determined as long
as droplet ejection can be made.
[0104] In addition, as described above, head chip 1 of inkjet head H is a so-called "harmonica
type head chip" exhibiting a hexagonal shape, in which the inlet and outlet of a channel
are disposed at opposite end surfaces. In harmonica type head chip 1, the inlet of
each drive channel 11 in all channel rows is disposed on rear end surface 1c, and
common ink chamber 51 is disposed facing the inlet of each drive channel 11. Therefore,
the influence of crosstalk is relatively large to allow the variation in droplet speed
to easily occur. Therefore, the configuration of the present embodiment easily exerts
a remarkable effect and is thus a preferable mode. The structure of the head chip
can be appropriately adopted as long as pressure chambers in a plurality of pressure
chamber rows are communicated via a common ink chamber.
[0105] Furthermore, while inkjet head H ejects droplets while scanning in the width direction
(main scanning direction) of recording medium P, inkjet head H may be a linear inkjet
head secured in the width direction of recording medium P. When such an inkjet head
is used, printing can be performed by ejecting droplets from nozzles of the inkjet
head while allowing recording medium P to move in Y direction in FIG. 1. Channel rows
in the inkjet head are disposed in X-X' direction in FIG. 1, for example.
[Inkjet recording method]
[0106] As described above, the inkjet recording method according to the present embodiment
includes applying two or more drive signals from a drive circuit of an inkjet recording
apparatus to each drive group to eject an ink from a nozzle of an inkjet head with
respect to each drive group.
[0107] Recording medium P can be appropriately determined as long as an image can be formed
by an inkjet system. The inkjet recording method according to the present embodiment
can be utilized in textile printing (inkjet textile printing).
[0108] For example, recording medium P may be any of various fibers such as polyester, cotton,
silk, wool and nylon. In addition, recording medium P may also be a cloth made of
any of the fibers. Examples of the cloth include a woven fabric, a knitted fabric
and a non-woven fabric.
[0109] While a fiber constituting the cloth is preferably configured from only a fiber that
can be dyed by a disperse dye, the cloth may be a blend woven fabric or a blend non-woven
fabric of any of the fibers with rayon, cotton, polyurethane, acryl, nylon, sheep
wool, silk, and the like. The thickness of a thread forming the cloth is preferably,
for example, 10 to 100 d.
[0110] When the cloth is a cloth to be dyed by a high temperature steaming method, the cloth
preferably further includes a dyeing aid. The dyeing aid functions to form an eutectic
mixture with water condensed in a cloth to be textile printed, in steaming of the
cloth, to decrease the amount of water to be evaporated again and to decrease the
time of temperature rise. The eutectic mixture functions to melt a dye on a fiber
to aid diffusion of the dye in the fiber. Examples of the dyeing aid include urea.
[0111] In the textile printing, an image is formed on the fiber, in which the fiber can
be subsequently dyed with a disperse dye by a pretreatment, by the above formation
of an image. Thereafter, the cloth to which the ink is added is heat-treated (color
development), and the cloth heat-treated is washed (washing). The color development
and the washing allow textile printing to the cloth to be completed, to provide a
dyed product (textile printed product). Thus, the inkjet recording method may further
include an operation other than the above as long as the effect in the present embodiment
is exerted.
[0112] The pretreatment is to add to the cloth a pretreatment agent that allows the blur
prevention effect to be exerted. In the pretreatment, various methods such as a pad
method, a coating method and a spray method can be utilized.
[0113] For the pretreatment, a method suitable for a fiber and ink may be appropriately
selected from known methods such as a method of treating a fiber with a water-soluble
polymer. For example, the textile printing is preferably applied to a fiber to which
0.2 to 50mass% of at least one substance selected from the group consisting of a water-soluble
metal salt, a polycation compound, a water-soluble polymer, a surfactant and a water
repellent agent is added, because blur prevention can be achieved at a high level
and a high resolution image can be printed to a cloth. The method of forming such
a fiber is preferably selected for the pretreatment.
[0114] Examples of the water-soluble polymer include starches derived from corn or wheat;
cellulose derivatives such as carboxymethylcellulose, methylcellulose and hydroxyethylcellulose;
polysaccharides such as sodium alginate, guar gum, tamarind gum, locust bean gum and
gum arabic; protein substances such as gelatin, casein and keratin; and synthetic
water-soluble polymers such as polyvinyl alcohol, polyvinyl pyrrolidone and an acrylic
acid polymer.
[0115] Examples of the surfactant include anionic, cationic, amphoteric and nonionic surfactants.
Representative examples of the surfactant include anionic surfactants such as higher
alcohol sulfate, and sulfonate of a naphthalene derivative; cationic surfactants such
as a quaternary ammonium salt; amphoteric surfactants such as an imidazoline derivative;
and nonionic surfactants such as polyoxyethylene alkyl ether, a polyoxyethylene propylene
block copolymer, sorbitan fatty acid ester, polyoxyethylenesorbitan fatty acid ester
and an ethylene oxide adduct of acetylene alcohol.
[0116] The color development is to allow the dye of the ink that is merely attached to the
surface of the cloth after printing and that does not sufficiently adsorb or bond
to the cloth to adsorb or bond to the cloth. The color development allows the original
hue of the ink to be more clearly developed. For the color development, steaming by
steam, baking by dry heat, thermosol, an HT steamer by overheated steam, an HP steamer
by pressurized steam, or the like is utilized. A specific method for use in the color
development is appropriately selected depending on a printing material, the ink, and
the like. In addition, the cloth subjected to printing may be subjected to a heating
treatment immediately or after a while, and may be dried and subjected to the color
development depending on the intended use, as described above.
[0117] The washing is preferably performed from the viewpoint of preventing the dye not
involving in dyeing, from remaining. The washing more suppresses a reduction in color
stability and a reduction in dye fastness. The washing is preferably performed also
from the viewpoint of removing the pretreatment substance applied to the cloth from
the cloth. The pretreatment substance is removed to thereby more suppress discoloration
of the cloth. The washing can be appropriately performed depending on a subject to
be removed and the intended purpose. The washing is to generally treat the fiber or
the cloth with a mixed liquid of caustic soda, a surfactant and hydrosulfite, when
the fiber is made of polyester, for example. The washing may be performed by an open
soaper or the like in a continuous manner, or by a jet dyeing machine or the like
in a batch manner.
[0118] The textile printed product is dried by hanging, or by a dryer, a heat roll, ironing
or the like after the washing.
[0119] According to the inkjet recording method, not only crosstalk is reduced, but also
the droplet size is uniform, the dot diameter after landing of the ink is controlled,
and a dot landed is spread to thereby allow the dot to be sufficiently overlapped
with other dot. Therefore, a uniform solid image where no streak is generated can
be formed even at a lower recording density. Accordingly, formation of an image by
an inkjet system at a higher speed can be achieved.
[Effects]
[0120] As is clear from the above description, the inkjet recording method according to
the present embodiment includes applying a drive signal from a drive circuit of an
inkjet recording apparatus to each drive group to eject an ink from a nozzle of an
inkjet head with respect to each drive group. The inkjet head includes a common ink
chamber that receives ink, a head chip to which the ink in the common ink chamber
is to be fed, and a nozzle that ejects the ink fed to the head chip. In addition,
the head chip includes a plurality of tubular pressure chambers that allow the nozzle
and the common ink chamber to be communicated, and a pressurizing portion that deforms
the pressure chambers to pressurize the pressure chambers. Furthermore, the pressure
chambers are aligned in two or more rows in the head chip, each row of the pressure
chambers belongs to a different drive group from the drive group of an adjacent row
of the pressure chambers, the drive circuit outputs the drive signal with respect
to each different drive group at time difference M represented by the following equation,
and the ink has a surface tension of 45 mN/m or less. Accordingly, generation of a
streak in the scanning direction of the inkjet head can be more reduced in a solid
image.

In the equation, M represents the time difference, n represents an integer of 1 or
more, AL represents a half of the acoustic resonance period of a pressure wave in
each of the pressure chambers, and t represents the pressure wave transmission time
to be determined by "distance between nozzles in different drive groups"/"speed of
sound transmitting in ink".
[0121] In the inkjet recording method, it is much more effective from the viewpoints of
enhancement in dispersibility of a colorant and optimization of the surface tension
of the ink that the ink contain a surfactant and the content of the surfactant in
the ink be 0.05 to 2mass%.
[0122] In addition, in the inkjet recording method, it is much more effective from the viewpoint
of easy adjustment of the surface tension of the ink to a proper range that a water-soluble
organic solvent having a surface tension of 40 mN/m or less be contained.
[0123] In addition, in the inkjet recording method, it is much more effective from the viewpoints
of exhibiting wettability in a short time after landing of the droplet and expanding
the ink droplet in the radial direction that the dynamic surface tension of the ink
be 50 mN/m or less at a bubble generation period of 10 Hz.
Examples
[0124] Hereinafter, the present invention is described with reference to Examples in more
detail. The scope of the present invention is not interpreted to be limited to the
description of Examples.
[Preparation of dispersion liquids 1 and 2]
[0125] The following respective components were sequentially mixed, and thereafter the resulting
mixed liquid was dispersed by a sand grinder to prepare each of dispersion liquids
1 and 2. Each of dispersion liquids 1 and 2 was dispersed until the average particle
size of a colorant (carbon black or CIDB 60), with a particle size measuring instrument
S90 manufactured by Malvern Instruments Ltd., reached 190 nm.
(Dispersion liquid 1)
[0126]
Carbon black |
20 parts by weight |
Glycerin |
30 parts by weight |
Sodium ligninesulfonate |
8 parts by weight |
Ion exchange water |
balance |
(Dispersion liquid 2)
[0127]
CIDB 60 |
20 parts by weight |
Glycerin |
30 parts by weight |
Sodium ligninesulfonate |
8 parts by weight |
Ion exchange water |
balance |
[0128] "Printex 35" produced by Degussa AG was used for the carbon black in dispersion liquid
1. "Printex" is a registered trademark of carbon black produced by Evonik. "CIDB 60"
in dispersion liquid 2 was "C.I. Disperse Blue 60". "Vanillex RN" produced by Nippon
Paper Industries Co., Ltd. was used for the sodium ligninesulfonate in each of dispersion
liquids 1 and 2. "Vanillex" is a registered trademark of Nippon Paper Industries Co.,
Ltd. In addition, the "balance" with respect to ion exchange water in each of dispersion
liquids 1 and 2 means an amount to be required for allowing the total amount of each
of the dispersion liquids to be 100 parts by weight.
[Preparation of inks A1 to A5]
[0129] The following components were mixed to prepare ink A1.
Dispersion liquid 1 |
25 parts by weight |
Glycerin (Gly) |
q.s. |
Ethylene glycol (EG) |
30 parts by weight |
PROXELGXL(S) (P-GXL) |
0.05 parts by weight |
Ion exchange water |
balance |
[0130] Both of "Glycerin" and "Ethylene glycol" above were commercial products from Kanto
Chemical Co., Ltd., and "PROXELGXL(S)" was a preservative agent produced by Arch Chemicals
Inc. "PROXEL" is a registered trademark of Arch Chemicals Inc. The "q.s" with respect
to "Glycerin" was an amount so that the viscosity of ink A1 was 5.7 mPa·s. The viscosity
of ink A1 was modulated by preparing two kinds of inks A1 in which only the amount
of glycerin to be added was different from each other, and appropriately mixing both
of the inks. The "balance" with respect to ion exchange water means an amount to be
required for allowing the total amount of ink A1 to be 100 parts by weight.
[0131] Ink A1 was allowed to pass through a hollow fiber membrane having gas permeability
(manufactured by Mitsubishi Rayon Co., Ltd.), and the outer surface of the hollow
fiber membrane was subjected to pressure reduction by a water aspirator to thereby
remove a dissolved gas in ink A1 (degassing). In addition, ink A1 after degassing
was packed in a vacuum pack to prevent air from being incorporated into ink A1.
[0132] In addition, the static surface tension of ink A1 was measured with a surface tensiometer
(manufactured by Kyowa Interface Science Co., Ltd.: CBVP-Z) according to a platinum
plate method at an ink temperature of 25°C. In addition, the dynamic surface tension
of ink A1 was determined as the surface tension value at an ink temperature of 25°C
and a bubble generation period of 10 Hz with a dynamic surface tensiometer ("Sensadyne
6000" manufactured by Chem-Dyne Research Corp.). Furthermore, the viscosity of ink
A1 was measured with an E-type viscometer (manufactured by Toki Sangyo Co., Ltd.).
[0133] As a result, the static surface tension STs and the dynamic surface tension STd of
ink A1 were 50 mN/m and 55 mN/m, respectively.
[0134] Furthermore, each of inks A2 to A5 was prepared in the same manner as in ink A1 except
that each composition shown in Table 1 was adopted, and the static surface tension
and the dynamic surface tension thereof were measured. In Table 1, "Olfine E1010"
(O-E1010) is a surfactant produced by Nisshin Chemical Co., Ltd., and "dipropylene
glycol monomethyl ether" (DPGMM) is "DPnP" produced by The Dow Chemical Company. The
respective compositions and surface tension values of inks A1 to A5 are shown in Table
1.
[Table 1]
Ink No. |
Dispersion liquid |
Amount to be added (parts by weight) |
STs (mN/m) |
STd (mN/m) |
η (mPa·s) |
No. |
Content (parts by weight) |
EG |
O-E1010 |
DPGMM |
P-GXL |
A1 |
1 |
25 |
30 |
0 |
0 |
0.05 |
50 |
55 |
5.7 |
A2 |
2 |
25 |
30 |
0 |
0 |
0.05 |
48 |
55 |
5.7 |
A3 |
1 |
25 |
30 |
0.1 |
0 |
0.05 |
35 |
48 |
5.7 |
A4 |
2 |
25 |
30 |
0.1 |
0 |
0.05 |
34 |
45 |
5.7 |
A5 |
2 |
25 |
30 |
0.1 |
10 |
0.05 |
32 |
43 |
5.7 |
[0135] In addition, each of inks B1 to B4 was prepared in the same manner as in ink A1 except
that each composition was changed as described in Table 2 below and the viscosity
of each ink was modulated to 5.7 mPa·s by the amount of glycerin to be added, and
the static surface tension and the dynamic surface tension thereof were measured.
In Table 2, "KF-351A" is a polyether-modified silicone surfactant produced by Shin-Etsu
Chemical Co., Ltd.
The respective compositions and surface tension values of inks B1 to B4 are shown
in Table 2.
[Table 2]
Ink No. |
Dispersion liquid |
Amount to be added (parts by weight) |
STs (mN/m) |
η (mPa·s) |
No. |
Content (parts by weight) |
EG |
KF-351A |
DPGMM |
P-GXL |
B1 |
2 |
25 |
30 |
0.03 |
10 |
0.05 |
33 |
5.7 |
B2 |
2 |
25 |
30 |
0.05 |
10 |
0.05 |
30 |
5.7 |
B3 |
2 |
25 |
30 |
0.8 |
10 |
0.05 |
25 |
5.7 |
B4 |
2 |
25 |
30 |
2.2 |
10 |
0.05 |
25 |
5.7 |
[0136] In addition, each of inks C1 to C12 was prepared in the same manner as in ink A1
except that each composition was changed as described in Table 3 below and the viscosity
of each ink was modulated to 5.7 mPa·s by the amount of glycerin to be added, and
the static surface tension and the dynamic surface tension thereof were measured.
[0137] In Table 3, "dye 1" is C.I. Reactive Blue 15 and "dye 2" is C.I. Reactive Red 24.
In addition, "PO-T" is a surfactant "Pelex OT-P" produced by Kao Corporation.
[0138] Furthermore, all of "DPGMP", "TEGMB", "PG" and "TPGMM" are each a water-soluble organic
solvent having a surface tension of 40 mN/m or less. "DPGMP" is dipropylene glycol
monopropyl ether, "TEGMB" is triethylene glycol monobutyl ether, "PG" is propylene
glycol, and "TPGMM" is tripropylene glycol monomethyl ether.
The respective compositions and surface tension values of inks C1 to C12 are shown
in Table 3.
[Table 3]
Ink No. |
Dye |
Amount to be added (parts by weight) |
STs (mN/m) |
η (mPa·s) |
EG |
P-OT |
O-EI010 |
Water-soluble organic solvent (STs ≤ 40 mN/m) |
P-GXL |
No. |
Content (parts by weight) |
DPGMP |
TEGMB |
PG |
TPGMM |
C1 |
1 |
8 |
30 |
0 |
0 |
0 |
0 |
0 |
0 |
0.05 |
50 |
5.7 |
C2 |
2 |
8 |
30 |
0 |
0 |
0 |
0 |
0 |
0 |
0.05 |
48 |
5.7 |
C3 |
1 |
8 |
30 |
0 |
0.1 |
0 |
0 |
0 |
0 |
0.05 |
43 |
5.7 |
C4 |
2 |
8 |
30 |
0.2 |
0 |
0 |
0 |
0 |
0 |
0.05 |
32 |
5.7 |
C5 |
1 |
8 |
20 |
0 |
0.1 |
10 |
0 |
0 |
0 |
0.05 |
43 |
5.7 |
C6 |
2 |
8 |
20 |
0.2 |
0 |
10 |
0 |
0 |
0 |
0.05 |
32 |
5.7 |
C7 |
1 |
8 |
20 |
0 |
0.1 |
0 |
10 |
0 |
0 |
0.05 |
43 |
5.7 |
C8 |
2 |
8 |
20 |
0.2 |
0 |
0 |
10 |
0 |
0 |
0.05 |
32 |
5.7 |
C9 |
1 |
8 |
20 |
0 |
0.1 |
0 |
0 |
10 |
0 |
0.05 |
43 |
5.7 |
C10 |
2 |
8 |
20 |
0.2 |
0 |
0 |
0 |
10 |
0 |
0.05 |
32 |
5.7 |
C11 |
1 |
8 |
20 |
0 |
0.1 |
0 |
0 |
0 |
10 |
0.05 |
43 |
5.7 |
C12 |
2 |
8 |
20 |
0.2 |
0 |
0 |
0 |
0 |
10 |
0.05 |
32 |
5.7 |
(Examples 1 to 3 and Comparative Examples 1 to 2)
[0139] An A4-size solid image having a printing resolution of 540 dpi × 720 dpi was printed
on an inkjet medium (recording medium) with an inkjet recording apparatus illustrated
in FIG. 1. The inkjet head of the inkjet recording apparatus has four channel rows
as illustrated in FIG. 11. All the channel rows are divided into two drive groups
A and B so that adjacent channel rows belong to different drive groups. Each channel
row has 256 nozzles, and distance D between nozzles in channel rows serving as adjacent
drive groups is 0.846 mm. In addition, AL is 5.0 µs.
[0140] The drive apparatus that outputs a drive signal is a common apparatus for all the
channel rows, and the drive signal is applied to all the channel rows from the drive
apparatus. The drive signal has a rectangular wave having only a positive voltage
(+V), as illustrated in FIG. 5. Pulse width PW and drive period T of the rectangular
wave were 1 AL (= 5.0 µs) and 100 µs, respectively.
[0141] In addition, the viscosity of the ink used was 5.7 mPa·s, and the speed of sound
transmitting in the ink was 1,600 m/s. Accordingly, the pressure wave transmission
time t to be determined by "distance between nozzles in adjacent pressure chambers"/"speed
of sound transmitting in ink" was 846 (µm)/{1,600 × 10
6}(µm/s) = 0.53 × 10
-6 (s) = 0.53 (µs), and t = 0.5 (µs) was derived from the calculated value described
above. The retardation (nAL + t) between drive groups A and B was calculated with
n = 1, and the drive signal was applied to drive group A prior to drive group B by
the retardation to drive the inkjet head.
[0142] For the recording medium, two media: "PictoricoPro white film" manufactured by Pictorico
and a photographic sheet "Crispia <High Glossy>" manufactured by Seiko Epson Corp.;
were used. "PictoricoPro" is a registered trademark of Mitsubishi Paper Mills Ltd.,
and "Crispia" is a registered trademark of Epson Sales Japan Corp.
[0143] The solid image formed on the recording medium was visually observed, and generation
of a streak in the scanning direction of the inkjet head in the solid image was evaluated
according to the following criteria. The type of the ink used and the evaluation results
in each of Examples 1 to 3 and Comparative Examples 1, 2 are shown in Table 4.
(Evaluation criteria)
[0144]
- A: No streak was observed at all in all recording media
- B: Little streak was observed in PictoricoPro white film
- C: Little streak was observed in a photographic sheet Crispia
- D: Streaks were remarkably observed in a photographic sheet Crispia
(Comparative Examples 3 to 7)
[0145] Each solid image was formed in the same manner as in Examples 1 to 3 and Comparative
Examples 1 and 2 except that no retardation between drive groups A and B was provided
in printing, and the solid image was evaluated. The type of the ink used and the evaluation
results in each of Comparative Examples 3 to 7 are shown in Table 4.
[Table 4]
|
Ink No. |
t (µs) |
nAL+t (µs) |
Retardation |
Generation of streak |
Comparative Example 1 |
A1 |
0.5 |
5.5 |
Provided |
D |
Comparative Example 2 |
A2 |
0.5 |
5.5 |
Provided |
D |
Example 1 |
A3 |
0.5 |
5.5 |
Provided |
B |
Example 2 |
A4 |
0.5 |
5.5 |
Provided |
B |
Example 3 |
A5 |
0.5 |
5.5 |
Provided |
A |
Comparative Example 3 |
A1 |
0.5 |
5.5 |
Not provided |
D |
Comparative Example 4 |
A2 |
0.5 |
5.5 |
Not provided |
D |
Comparative Example 5 |
A3 |
0.5 |
5.5 |
Not provided |
D |
Comparative Example 6 |
A4 |
0.5 |
5.5 |
Not provided |
D |
Comparative Example 7 |
A5 |
0.5 |
5.5 |
Not provided |
D |
(Examples 4 to 7 and Comparative Examples 8 and 9)
[0146] Each solid image was formed in the same manner as in Example 1 except that each of
ink A1 and inks B1 to B4 was used, the printing resolution was 540 dpi × 540 dpi,
and only "PictoricoPro white film" (A4) was used for a recording medium. The number
of streaks generated in one solid image was then counted. In addition, nozzles were
left for 5 minutes without being capped, thereafter an A4 solid image was formed,
and the number of lost nozzles that were generated after printing of the solid image
was counted. The "lost nozzle" refers to a nozzle that can launch no ink therefrom,
and the number of lost nozzles can be counted based on a distinct streak generated
in the image. The streak to be generated due to loss of nozzle(s) can be distinguished
from the streak to be generated due to crosstalk because it is different therefrom
in terms of the width and is a white streak having a width of 20 µm or more. In addition,
"t" in each of inks B1 to B4 was determined in the same manner as in inks A1 to A5,
and was found that the t was 0.5 µs and nAL + t in use of the ink was 5.5 µs. The
type of the ink used and the evaluation results in each of Examples 4 to 7 and Comparative
Examples 8 and 9 are shown in Table 5.
[Table 5]
|
Ink No. |
t (µs) |
nAL+t (µs) |
Retardation |
The number of streaks (-) |
The number of lost nozzles (-) |
Comparative Example 8 |
A1 |
0.5 |
5.5 |
Provided |
10 |
0 |
Comparative Example 9 |
A1 |
0.5 |
5.5 |
Not provided |
20 |
0 |
Example 4 |
B1 |
0.5 |
5.5 |
Provided |
3 |
0 |
Example 5 |
B2 |
0.5 |
5.5 |
Provided |
0 |
0 |
Example 6 |
B3 |
0.5 |
5.5 |
Provided |
0 |
0 |
Example 7 |
B4 |
0.5 |
5.5 |
Provided |
0 |
2 |
(Examples 8 to 17 and Comparative Examples 10 to 13)
[0147] Each solid image was formed in the same manner as in Example 4 except that each of
inks C1 to C12 was used, and the number of streaks in the solid image was counted.
In addition, "t" in each of inks C1 to C12 was determined in the same manner as in
inks A1 to A5, and was found that the t was 0.5 µs and nAL + t in use of the ink was
5.5 µs. The type of the ink used and the evaluation results in each Examples 8 to
17 and Comparative Examples 10 to 13 are shown in Table 6.
[Table 6]
|
Ink No. |
t (µs) |
nAL+t (µs) |
Retardation |
The number of streaks (-) |
Comparative Example 10 |
C1 |
0.5 |
5.5 |
Provided |
10 |
Comparative Example 11 |
C1 |
0.5 |
5.5 |
Not provided |
20 |
Comparative Example 12 |
C2 |
0.5 |
5.5 |
Provided |
10 |
Comparative Example 13 |
C2 |
0.5 |
5.5 |
Not provided |
20 |
Example 8 |
C3 |
0.5 |
5.5 |
Provided |
1 |
Example 9 |
C4 |
0.5 |
5.5 |
Provided |
1 |
Example 10 |
C5 |
0.5 |
5.5 |
Provided |
0 |
Example 11 |
C6 |
0.5 |
5.5 |
Provided |
0 |
Example 12 |
C7 |
0.5 |
5.5 |
Provided |
0 |
Example 13 |
C8 |
0.5 |
5.5 |
Provided |
0 |
Example 14 |
C9 |
0.5 |
5.5 |
Provided |
0 |
Example 15 |
C10 |
0.5 |
5.5 |
Provided |
0 |
Example 16 |
C11 |
0.5 |
5.5 |
Provided |
0 |
Example 17 |
C12 |
0.5 |
5.5 |
Provided |
0 |
[0148] It was revealed from the results in Examples 1 to 3 and Comparative Examples 1 and
2 that when a solid image was formed by using an ink having a static surface tension
of 45 mN/m or less in an inkjet head that included a common ink chamber for a plurality
of pressure chambers and that was to be driven by a drive signal displaced by a specific
retardation, generation of streak unevenness was sufficiently suppressed.
[0149] In particular, it was revealed from the results in Examples 2 and 3 that an ink having
a static surface tension of less than 34 mN/m or an ink having a dynamic surface tension
of less than 45 N/m was more effective from the viewpoint of suppressing generation
of streak unevenness, and it was revealed from the results in Examples 4 to 7 that
an ink having a static surface tension of 30 mN/m or less was much more effective
from the viewpoint of suppressing generation of streak unevenness.
[0150] Furthermore, it was found from the results in Examples 8 to 17 that inks (C5 to C12)
containing a water-soluble organic solvent having a surface tension of 40 mN/m or
less could much more suppress generation of streak unevenness than inks (C3, C4) containing
a water-soluble organic solvent having a surface tension of more than 40 mN/m.
Industrial Applicability
[0151] The present invention provides an inkjet recording method including applying a drive
signal with respect to each row of pressure chambers communicated via an ink chamber,
the pressure chambers each being disposed in parallel, and the method can substantially
prevent an adverse effect of crosstalk on launching of ink. The present invention
is expected to contribute to a further development of a high-speed and high-resolution
inkjet recording method.
Reference Signs List
[0152]
1 head chip
1a front end surface
1c rear end surface
2 nozzle plate
3 wiring substrate
3a end portion
4 FPC
5 ink manifold
11, 11A, 11B drive channel
12, 12A, 12B dummy channel
13, 13A, 13B partition
14 drive electrode
15A, 15B connection electrode
21 nozzle
31 bonding region
32A, 32B through hole
33A, 33B wiring electrode
51 common ink chamber
100 inkjet recording apparatus
200 conveyance mechanism
201, 203 conveyance roller
202 conveyance motor
300 guide rail
400 carriage
500 drive apparatus
501, 502 drive circuit
H inkjet head
P recording medium
PS recording surface