TECHNICAL FIELD
[0001] The present teaching relates to a motor control device that, when a motor including
coils of a plurality of phases is started from a stopped state, estimates a rotational
position of a rotor and determines a phase that is to be excited, based on the estimated
rotational position.
BACKGROUND ART
[0002] Motor control devices which, when a motor including coils of a plurality of phases
is started from a stopped state, estimate a rotational position of a rotor and determine
a phase that is to be excited, based on the estimated rotational position, have been
known. As such a motor control device, for example, a power conversion device including
a determination unit that, at the time of start of rotation of a switched reluctance
rotating machine, applies the same voltage to each of phases of the switched reluctance
rotating machine and determines an initial position of a rotor of the switched reluctance
rotating machine, based on a magnitude correlation between currents that flow in coils
of the phases, is disclosed in Patent Document 1.
[0003] Also, the power conversion device disclosed in Patent Document 1 described above
starts rotation of the rotor by exciting, based on an initial position of the rotor,
which has been determined by the determination unit, a predetermined phase that corresponds
to a rotational direction of the rotor.
[0004] The power conversion device disclosed in Patent Document 1 is able to detect the
initial position of the rotor and determine a phase of a stator, which is a first
target to be excited, even without a voltage sensor and a detailed inductance-current
data map.
CITATION LIST
PATENT DOCUMENT
[0005] Patent Document 1: Japanese Patent Application Publication No.
2016-103912
SUMMARY OF INVENTION
TECHNICAL PROBLEM
[0006] Incidentally, in a structure disclosed in Patent Document 1 described above, the
initial position of the rotor (a rotor) is determined based on the magnitude correlation
between currents that flow in the coils of the phases of the switched reluctance rotating
machine (a motor). Therefore, if a difference between the currents that flow in the
coils of the phases is small, there is a probability that the magnitude correlation
between the currents that flow in the coils of the phases is wrongly determined.
[0007] That is, the currents that flow in the coils of the phases of the motor vary in accordance
with the rotational position of the rotor, and therefore, the difference between the
currents that flow in the coils of the phases vary. If the difference between the
currents that flow in the coils of the phases is small, there is a probability that
largeness and smallness of the currents that flow in the coils of the phases are reversely
determined due to a detection error of a sensor that detects a current, an error or
the like when a value that has been detected by the sensor is converted.
[0008] Thus, a different relation from an original magnitude correlation between the currents
that flow in the coils of the phases is obtained as a determination result, and therefore,
there is a probability that a different phase from a phase that is to be excited in
order to cause the motor to rotate in a predetermined rotational direction is excited.
Thus, there is a probability that the motor rotates in an opposite direction to the
predetermined rotational direction.
[0009] It is an object of the present teaching to achieve a structure in which, in a motor
control device that performs start control of a motor, it is possible to cause, when
the motor is started, a rotor of the motor to rotate in a desired rotational direction
more reliably.
SOLUTION TO PROBLEM
[0010] A motor control device according to an embodiment of the present teaching is a motor
control device which, when a motor that includes a rotor and a stator including coils
of a plurality of phases is started from a stopped state, estimates a rotational position
of the rotor and determines a phase of the plurality of phases, which is to be excited,
based on the estimated rotational position. The motor control device includes an inductance
detection unit that, when the rotational position is estimated, applies a predetermined
voltage to the coils of the plurality of phases to calculate inductances of the plurality
of phases, a phase selection unit that selects, of the plurality of phases, a phase
the inductance of which is smallest as a first phase and a phase the inductance of
which is second smallest as a second phase, and an excitation phase determination
unit that determines, if a difference between the inductance of the first phase and
the inductance of the second phase is a predetermined value or less, a phase of the
first phase and the second phase, the inductance of which increases when the rotational
position changes in a rotational direction of the motor, as the phase that is to be
excited.
ADVANTAGEOUS EFFECTS OF INVENTION
[0011] With a motor control device according to an embodiment of the present teaching, if
a difference between a first phase of a plurality of phases of a motor, an inductance
of which is smallest, and a second phase of the plurality of phases, an inductance
of which is second smallest, is a predetermined value or less, a phase of the first
phase and the second phase, the inductance of which increases when a rotational position
of a rotor changes in a rotational direction of the motor, is determined as an excitation
phase. Thus, even when a difference between the inductance of the first phase and
the inductance of the second phase is small and there is a probability that the order
of the first phase and the second phase is changed due to a measurement error or the
like, it is possible to cause the rotor of the motor to rotate in a desired rotational
direction. Therefore, when the motor is started, the rotor of the motor can be caused
to more reliably rotate in a desired rotational direction without causing the rotor
to rotate in an opposite direction.
BRIEF DESCRIPTION OF DRAWINGS
[0012]
FIG. 1 is a control block diagram illustrating a schematic structure of a motor control
device according to an embodiment.
FIG. 2 is a graph schematically illustrating an example of a relation between an applied
voltage that is applied to a coil of each phase of a motor and a current that flows
in the coil of the each phase of the motor.
FIG. 3 is a chart schematically illustrating a relation between a rotational position
of a rotor and an inductance of each phase.
FIG. 4 is a table illustrating a relation between a rotational position of a rotor
and an excitation phase.
FIG. 5 is a graph describing a predetermined range that is used when an inductance
difference is determined.
FIG. 6 is a flowchart illustrating a flow of an operation of excitation phase determination
when a motor is started by a motor startup control unit.
FIG. 7 is a chart schematically illustrating another example of the relationship between
the applied voltage that is applied to the coil of each phase of the motor and a current
that flows in the coil of the each phase of the motor.
DESCRIPTION OF EMBODIMENTS
[0013] A motor control device according to an embodiment of the present teaching is a motor
control device that, when a motor that includes a rotor and a stator including coils
of a plurality of phases is started from a stopped state, estimates a rotational position
of the rotor and determines, of the plurality of phases, a phase that is to be excited,
based on the estimated rotational position. The motor control device includes an inductance
detection unit that, when the rotational position is estimated, applies a predetermined
voltage to the coils of the plurality of phases to calculate inductances of the plurality
of phases, a phase selection unit that selects, of the plurality of phases, a phase
the inductance of which is smallest as a first phase and a phase the inductance of
which is second smallest as a second phase, and an excitation phase determination
unit that determines, if a difference between the inductance of the first phase and
the inductance of the second phase is a predetermined value or less, a phase of the
first phase and the second phase, the inductance of which increases when the rotational
position changes in a rotational direction of the motor, as the phase that is to be
excited (First Structure).
[0014] With the above-described structure, using the inductance of each of the phases of
the motor, a phase that is to be excited when the motor is started can be determined.
That is, it is considered that, in the above-described structure, of the differences
between the inductances of the plurality of phases of the motor, the difference between
the inductance of the first phase the inductance of which is smallest and the inductance
of the second phase the inductance of which is second smallest is smallest. Therefore,
there is a probability that, if the difference between the inductances is the predetermined
value or less, a magnitude correlation between the inductances of the first phase
and the second phase is determined as an inversed relation of an actual relation due
to a measurement error or the like. In contrast, in the above-described structure,
a phase of the first phase and the second phase, the inductance of which increases
when the rotational position of the rotor changes in the rotational direction of the
motor, is determined as a phase that is to be excited.
[0015] Thus, when the difference between the inductance of the first phase and the inductance
of the second phase is small, it is possible to prevent the magnitude correlation
between the inductances from being a different relation from an actual relation due
to a measurement error or the like. Therefore, when the motor is started, it is possible
to prevent exciting a different phase from a phase that it is originally desired to
excite.
[0016] Therefore, when the motor is started, it is possible to prevent the motor from rotating
in an opposite direction to a rotational direction in which it is desired to cause
the motor to rotate.
[0017] In the first structure, the excitation phase determination unit determines, if the
difference is larger than the predetermined value, a phase of the plurality of phases,
which is another phase than the first phase and the inductance of which increases
when the rotational position changes in the rotational direction of the motor, as
the phase that is to be excited (Second Structure).
[0018] If the difference between the inductance of the phase the inductance of which is
smallest and the inductance of the phase the inductance of which is second smallest
is larger than the predetermined value, there is a low probability that the phase
selection unit wrongly recognizes the magnitude correlation between the inductance
of the first phase and the inductance of the second phase due to a measurement error
or the like. Therefore, the excitation phase determination unit determines the phase
which is another phase than the first phase and the inductance of which increases
when the rotational position of the rotor changes in the rotational direction of the
motor as a phase that is to be excited, and thereby, it is possible to cause the rotor
to rotate in a desired rotational direction.
[0019] In the first or second structure, the inductance detection unit includes a voltage
application unit that applies the predetermined voltage to each of the coils of the
plurality of phases, a time measurement unit that measures a time from a start of
application of the predetermined voltage to each of the coils of the plurality of
phases by the voltage application unit to a time at which a corresponding one of currents
that flow in the coils of the phases reaches a fixed value, and an inductance calculation
unit that calculates inductances of the plurality of phases, based on the time that
has been measured by the time measurement unit. The voltage application unit stops
applying a voltage to the coil of a phase of the plurality of phases, the current
of which has reached the fixed value (Third Structure).
[0020] Thus, the inductance of each of the phases of the motor can be calculated based on
a current that flows in the coil of the each of the phases. Then, the voltage application
unit stops, when the current that flows in the coil of each of the phases of the motor
reaches the fixed value, applying a voltage to the coil of the each of the phases,
and therefore, it is possible to prevent the current that flows in the coil of the
each of the phases from being larger than the fixed value. It is possible to prevent,
by setting the fixed value to a smaller value than a current value at which the rotor
of the motor rotates, the current that causes the rotor to rotate from flowing in
the coils of the motor.
[0021] Therefore, with the above-described structure, it is possible to calculate the inductances
of the phases of the motor without causing the rotor of the motor to rotate.
[0022] An embodiment of the present teaching will be described in detail below with reference
to the accompanying drawings. In the drawings, the same or corresponding parts are
denoted by the same reference symbol and the description of the parts is not repeated.
[0023] FIG. 1 is a block diagram illustrating a schematic structure of a motor control device
1 according to an embodiment of the present teaching. The motor control device 1 outputs
a control signal to a drive circuit 3 that drives a motor 2. That is, the motor control
device 1 controls driving of the motor 2. The motor 2 is, for example, a switched
reluctance motor and includes a rotor 51 and a stator 55. Note that the motor 2 may
be some other motor than a switched reluctance motor as long as the motor 2 is a motor
that does not detect a rotational position of the rotor 51 by a sensor or the like.
In FIG. 1, the reference numeral 5 denotes a current detection circuit that detects
a current that flows in a coil 58 of each phase of the motor 2, which will be described
later. Data of a value of a current that has been detected by a current detection
circuit 5 is input to the motor control device 1.
[0024] The motor 2 is, for example, a motor of a so-called inner rotor type in which the
rotor 51 is arranged inside the cylindrical stator 55. Note that the motor 2 may be
a motor of a so-called outer rotor type in which a rotor rotates radially outside
a stator.
[0025] The rotor 51 includes a substantially columnar rotor body 52 and a plurality of (four
in this embodiment) salient poles 53 that protrude radially outward from the rotor
body 52. The rotor 51 is configured such that the rotor body 52 and the plurality
of salient poles 53 are integrally formed and is formed of an iron core.
[0026] The stator 55 includes a substantially cylindrical yoke 56, a plurality of (six in
this embodiment) teeth 57 that extend inward from an inner circumference surface of
the yoke 56, and coils 58 wound around the teeth 57. The yoke 56 and the plurality
of teeth 57 are integrally formed. In the stator 55 of this embodiment, when the yoke
56 is viewed in a cylinder axial direction (in a state of FIG. 1), the coils 58 of
the same phase are wound around two of the teeth 57 which oppose to one another in
a radial direction of the yoke 56. That is, in this embodiment, as illustrated in
FIG.1, the stator 55 has the coils 58 of three phases, that is, an A phase, a B phase,
and a C phase.
[0027] The motor 2 of this embodiment is, for example, a motor the number of poles of which
is four and the number of slots of which is six. Note that the motor 2 may be a motor
the number of poles of which is some other number than four and the number of slots
of which is some other number than six.
[0028] The drive circuit 3 is a switching circuit that includes a plurality of switching
elements 61, 62, 63, 64, 65, and 66 that form a three-phase bridge circuit to drive
the motor 2. Specifically, of the switching elements 61, 62, 63, 64, 65, and 66 of
the drive circuit 3, the switching elements 61 and 62 are connected to the coils 58
of the A phase of the motor 2, the switching elements 63 and 64 are connected to the
coils 58 of the B phase of the motor 2, and the switching elements 65 and 66 are connected
to the coils 58 of the C phase of the motor 2.
[0029] For the switching elements 61, 62, 63, 64, 65, and 66, for example, IGBT is used.
Diodes 71, 72, 73, 74, 75, and 76 are connected to the switching elements 61, 62,
63, 64, 65, and 66, respectively, in series. The diodes 71, 72, 73, 74, 75, and 76
are provided such that a current flows in one direction between each of the switching
elements 61, 62, 63, 64, 65, and 66 and the coil 58 of a corresponding one of the
phases of the motor 2.
[0030] The switching elements 61, 62, 63, 64, 65, and 66 are connected to a DC power source
4 in parallel. The switching elements 61, 62, 63, 64, 65, and 66 apply a voltage to
the motor 2 from the DC power source 4 by performing a switching operation in accordance
with a control signal (a switching signal) that is output from the motor control device
1, which will be described later.
[0031] The motor control device 1 outputs a control signal that drives the switching elements
61, 62, 63, 64, 65, and 66 to the drive circuit 3. Also, the motor control device
1 performs start control of the motor 2, based on a rotational position of the rotor
51 of the motor 2.
[0032] Specifically, the motor control device 1 includes a motor driving control unit 11
and a motor startup control unit 12. The motor driving control unit 11 generates a
control signal for the drive circuit 3. A structure of the motor driving control unit
11 is similar to a known structure, and therefore, detailed description thereof will
be omitted.
[0033] The motor startup control unit 12 determines a phase of the three phases of the motor
2, in which a current is caused to flow first, that is, a phase that is to be excited
first, in accordance with the rotational position of the rotor 51 of the motor 2 in
a stopped state. Specifically, the motor startup control unit 12 calculates an inductance
of each phase in the motor 2 in a stopped state and determines a phase that is to
be excited in accordance with a difference between inductances of two phases of the
three phases, the inductances of which are small. Note that an order related to a
rotational direction of the motor 2 when the motor 2 is started is input from outside
to the motor startup control unit 12.
[0034] Specifically, the motor startup control unit 12 includes an inductance detection
unit 21 that calculates an inductance of each phase of the motor 2, a phase selection
unit 22 that selects two phases of the three phase of the motor 2, the inductances
of which are small, an inductance difference calculation unit 23 that calculates a
difference between the inductances of the selected two phases, and an excitation phase
determination unit 24 that determines a phase that is to be excited, based on the
difference.
[0035] The inductance detection unit 21 applies a pulse voltage to the coil 58 of each phase
of the motor 2 in a stopped state, measures a time until a current that flows in the
coil 58 of each phase reaches a fixed value, and calculates an inductance of each
phase using the measured time. That is, the inductance detection unit 21 includes
a voltage application unit 31 that applies a pulse voltage to the coil 58 of each
phase of the motor 2, a time measurement unit 32 that measures a time until a current
that flows in the coil 58 of each phase reaches a fixed value, and an inductance calculation
unit 33 that calculates an inductance using the measured time. Note that data of a
value of a current that flows in the coil 58 of each phase of the motor 2, which has
been detected by the current detection circuit 5, is input to the inductance detection
unit 21.
[0036] As illustrated in FIG. 2, the voltage application unit 31 applies a predetermined
pulse voltage (an applied voltage) V to the motor 2 in a stopped state. The voltage
application unit 31 simultaneously starts applying the predetermined pulse voltage
V to the coils 58 of the three phases of the motor 2 and continues to apply the pulse
voltage V until each of currents (motor currents) Ia, Ib, and Ic that flow in the
coils 58 of the phases reaches the fixed value. For example, as illustrated in FIG.
2, for the currents (motor currents) Ia, Ib, and Ic that flow in the coils 58 of the
phases of the motor 2, times ta, tb, and tc each of which is a time from a start of
application of the voltage V to a time at which a corresponding one of the currents
Ia, Ib, and Ic reaches the fixed value (an alternate long and two short dashes line
in FIG. 2) are different from one another. Note that a relation between the applied
voltage and each of the motor currents, which is illustrated in FIG. 2, is merely
an example and varies depending on the structure of the motor or the like.
[0037] When a current that flows in the coil 58 of each phase of the motor 2 reaches the
fixed value, the voltage application unit 31 stops applying the pulse voltage to the
coil 58 of the phase. Thus, it is possible to prevent the rotor 51 of the motor 2
from rotating due to an unnecessary current continuously flowing in the coil 58 of
each phase of the motor 2.
[0038] The time measurement unit 32 measures a time during which the predetermined pulse
voltage is applied to the coil 58 of each phase of the motor 2 by the voltage application
unit 31. That is, the time measurement unit 32 measures, in the coil 58 of each phase
of the motor 2, a time (ta, tb, and tc in the example of FIG. 2) from a time point
of a start of application of the pulse voltage to the coil 58 to a time at which the
current that flows in the coil 58 reaches the fixed value.
[0039] Note that the fixed value is set to a smaller value than a current value at which
the rotor 51 of the motor 2 rotates. Thus, it is possible to prevent a current that
causes the rotor 51 to rotate from flowing in the coil 58 of the motor 2.
[0040] The inductance calculation unit 33 calculates an inductance of each phase of the
motor 2 using the time that has been measured by the time measurement unit 32.
[0041] In this case, the inductance of each phase of the motor 2 is calculated using a current
that flows in the coil 58 of each phase of the motor 2. That is, an inductance L,
a voltage V, a current I, and a time t satisfy a relation of Expression 1 below. Accordingly,
a time tx until the predetermined voltage V is applied to the coil 58 of each phase
of the motor 2 and a current that flows in the coil 58 becomes a fixed value I is
measured for each phase of the motor 2, and thereby, an inductance Lx of each phase
can be calculated in accordance with Expression 2. Note that, in Expression 2, x is
a, b, or c and each of Lx and tx corresponds to a value in a corresponding one of
the phases of the motor 2.
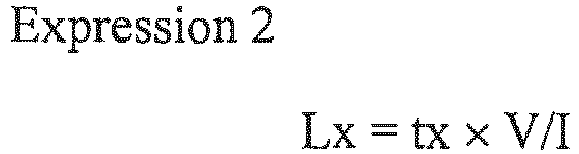
[0042] The inductance calculation unit 33 calculates the inductance Lx of each phase of
the motor 2 using Expression 2 above.
[0043] The phase selection unit 22 selects two phases the inductances of which are small
using the inductance of each phase of the motor 2, which has been calculated by the
inductance calculation unit 33 of the inductance detection unit 21. Specifically,
the phase selection unit 22 selects, of the phases of the motor 2, the phase the inductance
of which is smallest as the first phase and also the phase the inductance of which
is second smallest as the second phase.
[0044] The inductance difference calculation unit 23 calculates a difference (which will
be referred hereinafter to as an inductance difference) between the inductance of
the first phase and the inductance of the second phase each of which has been selected
by the phase selection unit 22.
[0045] The excitation phase determination unit 24 determines a phase of the phases of the
motor 2, which is to be excited at the time of a start of the motor 2, using the inductance
difference that has been calculated by the inductance difference calculation unit
23. Specifically, in this embodiment, if the inductance difference is larger than
a predetermined value, the excitation phase determination unit 24 determines, as an
excitation phase, a phase of the phases of the motor 2, which is another phase than
the first phase and the inductance of which increases when the rotational position
of the rotor 51 moves in the rotational direction of the motor 2. On the other hand,
if the inductance difference is the predetermined value or less, the excitation phase
determination unit 24 determines, as an excitation phase, a phase of the first phase
and the second phase, the inductance of which increases when the rotational position
of the rotor 51 changes in the rotational direction of the motor 2. Note that the
rotational direction of the motor 2 is a direction in which the motor 2 rotates at
the time of a start of the motor 2. Information related to the rotational direction
is included in the order that is input to the motor startup control unit 12.
[0046] For example, if the inductances of the three phases of motor 2 change in accordance
with the rotational position of the rotor 51, as illustrated in FIG. 3, the excitation
phase determination unit 24 divides the rotational position of the rotor 51 into seven
areas and determines an excitation phase for each area. An example of determination
of an excitation phase by the excitation phase determination unit 24 is illustrated
in FIG. 4.
[0047] If the inductance difference is larger than the predetermined value, the excitation
phase determination unit 24 sets the first phase as a reference phase that is a reference
used for determining an excitation phase. On the other hand, if the inductance difference
is the predetermined value or less, the excitation phase determination unit 24 sets
the first phase and the second phase as the reference phases. That is, the excitation
phase determination unit 24 estimates the rotational position of the rotor 51 in the
motor 2 in a stopped state. The excitation phase determination unit 24 determines
an excitation phase, based on the estimated rotational position, in the following
manner.
[0048] As illustrated in FIG. 4, in each area, if there is one reference phase (for example,
the A phase in an area (1) in FIG. 4), the excitation phase determination unit 24
determines, as an excitation phase, a phase the inductance of which increases when
the rotational position of the rotor 51 changes in the rotational direction of the
motor 2 (for example, the C phase, when the rotational direction of the rotor 51 is
clockwise (CW), and the B phase, when the rotational direction of the rotor 51 is
counter clockwise (CCW) in the area (1) in FIG. 4). Note that CW is a rotational direction
in which a value of the rotational position (an angle) of the rotor increases in FIG.
4 and CCW is a direction in which the value of the rotational position (the angle)
of the rotor decreases in FIG. 4.
[0049] On the other hand, as illustrated in FIG. 4, in each area, if there are two reference
phases (for example, the A and B phases in an area (2) in FIG. 4), the excitation
phase determination unit 24 determines, as an excitation phase, a phase of the two
phases, the inductance of which increases when the rotational position of the rotor
51 changes in the rotational direction of the motor 2 (for example, the A phase, when
the rotational direction of the rotor 51 is CW, and the B phase, when the rotational
direction of the rotor 51 is CCW in the area (2) of FIG. 4).
[0050] Thus, when the motor 2 in a stopped state is started, it is possible to prevent the
motor 2 from rotating in an opposite direction to a desired rotational direction that
has been input to the motor startup control unit 12. That is, in some cases, if the
inductance difference between the inductances of the two phases of the phases of the
motor 2, the inductances of which are small, is the predetermined value or less, the
phase the inductance of which is smallest is wrongly recognized due to a measurement
error, a conversion error, or the like (which will be hereinafter referred to merely
as a measurement error or the like) of a current. However, as described above, if
the inductance difference between the inductances of the two phases of the phases
of the motor 2, the inductances of which are small, is the predetermined value or
less, an excitation phase of the motor 2 can be correctly determined without being
influenced by the measurement error or the like by setting one of the two phases as
the phase the inductance of which is smallest. Therefore, when the motor 2 is started,
it is possible to prevent the motor 2 from rotating in an unintended direction.
[0051] As illustrated in FIG. 5, the predetermined value is set to a maximum value D of
the difference between the inductance of the first phase and the inductance of the
second phase in a range R of the rotational position in which, when the rotational
position of the rotor 51 changes in the rotational direction of the motor 2 in the
first phase (the A phase in the example of FIG. 5), the inductance increases. Note
that, in FIG. 5, a case in which the first phase is the A phase is illustrated but
similar applies to a case in which the first phase is the B phase or the C phase.
[0052] Also, in accordance with measurement accuracy of the current detection circuit 5,
the predetermined value may be set to be in a range of a predetermined multiple (for
example, twice) of the measurement accuracy.
[0053] Thus, if the difference between the inductance of the first phase and the inductance
of the second phase is the predetermined value or less, the first phase the inductance
of which increases when the rotational position of the rotor 51 changes in the rotational
direction of the motor 2 can be determined as an excitation phase. Therefore, when
a motor is started, it is possible to prevent the motor from rotating in an unintended
direction (an opposite direction).
[0054] Next, an operation of the motor startup control unit 12 having the above-described
structure will be described using a flow illustrated in FIG. 6.
[0055] When the flow illustrated in FIG. 6 starts (START), first, in Step S1, the voltage
application unit 31 applies a fixed pulse voltage to the coil 58 of each phase of
the motor 2. The voltage application unit 31 continues to apply the pulse voltage
to the coil 58 of each phase of the motor 2 until a current that flows in the coil
58 reaches a fixed value.
[0056] Note that, at a time when the current that flows in the coil 58 of each phase reaches
the fixed value, the voltage application unit 31 stops applying the pulse voltage
to the coil 58 of the phase. Thus, it is possible to retrain a flow of an excessive
current in the coils 58 of the motor 2. Therefore, it is possible to prevent, by the
pulse voltage, the rotor 51 of the motor 2 from rotating.
[0057] In subsequent Step S2, the time measurement unit 32 measures a time until the current
that flows in the coil 58 of each phase reaches the fixed value. The inductance of
each phase of the motor 2 is proportional to the time.
[0058] In Step S3, the inductance calculation unit 33 calculates the inductance of each
phase of the motor 2 using the time that has been measured in Step S2.
[0059] In subsequent Step S4, the phase selection unit 22 compares the respective inductances
of the phases, which have been calculated in Step S3, and selects two of the phases
of the motor 2, the inductances of which are small. The phase selection unit 22 selects,
as the first phase, the phase the inductance of which is smallest and, on the other
hand, selects, as the second phase, the phase the inductance of which is second smallest.
[0060] In Step S5 to which the process proceeds thereafter, the inductance difference calculation
unit 23 calculates the difference (the inductance difference) between the inductance
of the first phase and the inductance of the second phase that have been selected
by the phase selection unit 22.
[0061] In subsequent Step S6, the excitation phase determination unit 24 determines whether
or not the inductance difference is the predetermined value or more. If the inductance
difference is the predetermined value or less (YES in Step S6), the process proceeds
to Step S7 and the excitation phase determination unit 24 sets, as an excitation phase,
one of the first phase and the second phase. Specifically, if the inductance difference
is the predetermined value or less, the excitation phase determination unit 24 sets
a phase of the first phase and the second phase, the inductance of which increases
when the rotational position of the rotor 51 moves in the rotational direction of
the motor 2, as an excitation phase.
[0062] On the other hand, if the inductance difference is larger than the predetermined
value (NO in Step S6), the process proceeds to Step S8 and the excitation phase determination
unit 24 sets a phase of the phases of the motor 2, which is another phase than the
first phase, as an excitation phase. Specifically, if the inductance difference is
larger than the predetermined value, the excitation phase determination unit 24 sets
a phase of the phases of the motor 2, which is another phase than the first phase
and the inductance of which increases when the rotational position of the rotor 51
moves in the rotational direction of the motor 2, as an excitation phase.
[0063] After the excitation phase determination unit 24 determines an excitation phase in
Step S7 and S8, the flow is terminated (END).
[0064] In the above-described structure, when the motor 2 is started, if the inductance
difference between the inductances of two phases of the phases of the motor 2, the
inductances of which are smallest, is the predetermined value or less, one of the
two phases is determined as an excitation phase without determining the phase the
inductance of which is smallest. Thus, when the phase the inductance of which is smallest
is determined, it is possible to prevent wrong recognition of a different phase from
an actual phase as the phase the inductance of which is smallest due to a measurement
error or the like. Therefore, it is possible to prevent wrong determination of a phase
that is to be excited when the motor 2 is started due to a measurement error or the
like and to prevent reverse rotation of the motor 2.
[0065] Also, when the inductance of each phase of the motor 2 is calculated, at the time
when the current that flows in the coil 58 reaches the fixed value, the voltage application
unit 31 stops applying the pulse voltage to the coil 58. Thus, it is possible to prevent
a current from unnecessarily flowing in the coil 58. Therefore, it is possible to
prevent the motor 2 from rotating unintentionally.
(Other Embodiments)
[0066] An embodiment of the present teaching has been described above, but the above-described
embodiment is merely an illustrative example of a preferred embodiment of the present
teaching. Therefore, the present teaching is not limited to the above-described embodiment
and the above-described embodiment can be appropriately modified and implemented without
departing from the gist of the invention.
[0067] In the above-described embodiment, the motor 2 includes coils of three phases. However,
the motor 2 may include coils of four phases or more.
[0068] In the above-described embodiment, the motor 2 is configured such that a waveform
of an inductance of each phase with respect to the rotational position of the rotor
51 has a sine wave shape (see FIG. 3). However, the motor 2 may be configured such
that the waveform of the inductance of each phase has some other shape than a sine
wave shape, that is, for example, a shape with which the inductance is fixed in a
range of the predetermined rotational position of the rotor 51.
[0069] In the above-described embodiment, the voltage application unit 31 simultaneously
starts applying the pulse voltage to the coils 58 of the phases of the motor 2. However,
the voltage application unit may be configured such that a timing at which the pulse
voltage is applied to the coil 58 of each of the phases of the motor 2 is shifted
from timings of application to the coils 58 of the other phases.
[0070] Specifically, for example, as illustrated in FIG. 7, the voltage application unit
first starts applying the pulse voltage to the coil 58 of the A phase of the motor
2 and continues to apply the pulse voltage until a current that flows in the coil
58 of the A phase becomes a fixed value. Thereafter, the voltage application unit
stops applying the pulse voltage to the coil 58 of the A phase. Next, the voltage
application unit starts applying the pulse voltage to the coil 58 of the B phase and
continues to apply the pulse voltage until a current that flows in the coil 58 of
the B phase becomes the fixed value. Thereafter, the voltage application unit stops
applying the pulse voltage to the coil 58 of the B phase. Then, the voltage application
unit starts applying the pulse voltage to the coil 58 of the C phase and continues
to apply the pulse voltage until a current that flows in the coil 58 of the C phase
becomes the fixed value. Thereafter, the voltage application unit stops applying the
pulse voltage to the coil 58 of the C phase.
[0071] Thus, when the voltage is applied to the coil 58 of each phase of the motor 2, influence
of a magnetic leakage flux between the coils 58 of the phases can be prevented. That
is, as in the above-described embodiment, in a case in which the pulse voltage is
simultaneously applied to the coils 58 of the phases of the motor 2, there is a probability
that a magnetic flux that is generated in the coil 58 of each phase influences, as
a leakage magnetic flux, the other phases. Accordingly, there is a probability that
the inductance of each phase of the motor 2 cannot be measured with high accuracy.
In contrast, it is possible to prevent, by shifting the timing at which the pulse
voltage is applied to the coil 58 of each phase of the motor 2 is shifted from the
timings of application to the coils 58 of the other phases, as described above, influence
of the magnetic flux that is generated in the coil 58 of each phase to the other phases.
Therefore, the inductance of each phase of the motor 2 can be measured with high accuracy.
[0072] Note that, in an example of FIG. 7, the pulse voltage is applied to the coils 58
of an order of the A phase, the B phase, and the C phase. However, the order in which
the pulse voltage is applied to the coils 58 of the A phase, the B phase, and the
C phase may be any order.
INDUSTRIAL APPLICABILITY
[0073] The present teaching is applicable to a motor control device that performs start
control in a motor that does not include a sensor that detects a rotational position
of a rotor.