Technical field
[0001] The invention relates to waterproofing membranes for use in the construction industry,
for example for basements, roofing and tunneling applications to protect structures
against water penetration.
Background of the invention
[0002] Waterproofing membranes are commonly used in the construction industry for sealing
bases, underground surfaces or buildings against water penetration.
[0003] State-of-the-art waterproofing membranes are typically multilayer systems comprising
a polymer-based barrier layer as the principal layer to provide watertightness. Typical
polymers used in barrier layers include thermoplastics such as plasticized polyvinylchloride
(p-PVC) and thermoplastic polyolefins (TPO) or elastomers such as ethylene-propylene
diene monomer (EPDM) and crosslinked chlorosulfonated polyethylene (CSPE). One of
the drawbacks of polymer-based barrier layers is their poor bonding properties; they
typically show low bonding strength to adhesives that are commonly used in the construction
industry, such as epoxy adhesives, polyurethane adhesives, and cementitious compositions.
Therefore, a contact layer, for example, a fleece backing, is typically used to provide
sufficient bonding of the polymer-based barrier layer and the structure to be waterproofed.
[0004] In post-applied waterproofing applications, a waterproofing membrane is bonded to
a surface of a structure to be waterproofed whereas in pre-applied applications, the
waterproofing membrane is laid before the structure to be waterproofed is built. In
the first case, the membrane is bonded via its contact layer to the surface of the
structure by using an adhesive or a sealing tape. In the latter case, the waterproofing
membrane is placed with its waterproofing layer against an underlying structure or
formwork and fresh concrete is cast against the surface of the contact layer, thereby
fully and permanently bonding the membrane to the surface of the hardening concrete.
A layer of adhesive can be used between the waterproofing layer and the contact layer
to improve bonding to the fresh concrete cast. The adhesive should preferably enable
penetration of the casted concrete into the contact layer in order to ensure good
bonding between waterproofing membrane and the surface of the waterproofed structure.
[0005] One of the main challenges related to the multilayer waterproofing membranes is to
ensure watertightness after infiltration in case of leak in the barrier layer. Watertightness
after infiltration means in general that the sealing construction should be able to
prevent the infiltrated water from penetrating to the space between the membrane and
the waterproofed surface. A leak in the barrier layer can be a result of inward growing
tree roots, material failure or tensile or shear forces directed to the membrane.
If the watertightness after infiltration is lost, water is able to flow laterally
underneath the membrane and to invade the interior of the building structure. In such
cases the exact location of the leak in the barrier layer is also difficult to detect.
[0006] US 8793862 B2 describes a waterproofing membrane comprising a barrier layer, a composite layer
arranged on one side of the barrier layer and a network of sealant between the barrier
layer and the composite layer. The network of sealant is said to limit the size of
area affected by penetrating water in case of water leakage through the barrier layer.
In waterproofing applications the membrane is applied on a subsurface in such a way
that the barrier layer is directed against a concrete base and the composite layer
is facing the concrete casted against the membrane. During the hardening process,
the composite layer is penetrated by the liquid concrete forming a good bond with
the hardened concrete.
[0007] US2015/0231863 A1 discloses a waterproofing membrane including a barrier layer and a functional layer
including a thermoplastic polymer that changes consistency under the influence of
highly alkaline media and an adhesive. Once the functional layer gets into contact
with liquid concrete, the thermoplastic polymer dissolves and allows the adhesive
to bond to the cast concrete. The functional layer may additionally comprise other
thermoplastic polymers, fillers or concrete constituents. The construction of the
functional layer is said to enable working with membranes in adverse weather conditions
without diminishing the adhesive capacity of the membrane.
[0008] One of the disadvantages of the State-of-the-Art multilayer waterproofing membranes
is related to the use of non-woven backings as contact layer to provide sufficient
bonding between the membrane and the substrate to be waterproofed. In waterproofing
and roofing applications the adjacent membrane sheets have to be homogenously joined
to each other in a reliable way to ensure watertightness of the sealing construction.
Membranes having a non-woven backing cannot typically be joined by heat welding but
instead the edges of the membranes have to be bonded together either by using an adhesive
or with a sealing tape adhered on top of the seam and/or under the seam. The use of
an adhesive or a sealing tape to join adjacent membrane sheets complicates the installation
process and increases application costs.
[0009] There is thus a need for a novel type of waterproofing membrane, which is suitable
for use in pre-applied waterproofing applications and which provides high bonding
strength with casted concrete after hardening without the use of a non-woven backing.
Summary of the invention
[0010] The object of the present invention is to provide a waterproofing membrane, which
can be used for sealing of bases, underground surfaces or buildings against water
penetration. In particular it is the objective of the present invention to provide
a waterproofing membrane, which forms a permanent bond with a layer of cementitious
composition after hardening without the use of a fiber-based contact layer.
[0011] The subject of the present invention is a sealing device as defined in claim 1.
[0012] It was surprisingly found that the fiber-based contact layer typically used in prior
art waterproofing membranes can be replaced with a functional layer composed of an
at least partially cured moisture curing composition comprising at least one silane-terminated
polymer.
[0013] One of the advantages of the present invention is that unlike a fiber-based contact
layer, the functional layer of the present invention is relatively easy to clean by
a simple washing step. This is a significant advantage since the waterproofing membranes
are typically not stored in the form of rolls on the construction site but instead
the membranes are spread out on the surface to be waterproofed with the functional
layer facing upwards long before the casting of the concrete layer. The time period
between the casting of the concrete layer and installation of the waterproofing membrane
can be relatively long and during that time the functional layer is susceptible to
environmental conditions, such as effects of heat, UV-exposure, rain, and in particular
foot traffic across the membrane surface.
[0014] Since the waterproofing membranes are usually not provided with additional protective
layers, which would protect the functional layer from dirt accumulation, the outer
surface of the membrane has to be cleaned by washing before the casting of the concrete
layer to ensure proper bonding between the casted concrete and the functional layer.
Washing of fiber-based contact layers is per se a complicated process due to the porous
structure of the contact layer. The sufficiency of the cleaning treatment is also
difficult to verify since the dirt particles are typically absorbed deep inside the
fiber-based contact layer.
[0015] Other aspects of the present invention are presented in other independent claims.
Preferred aspects of the invention are presented in the dependent claims.
Brief description of the Drawings
[0016]
Fig. 1 shows a cross-section of a waterproofing membrane (1) comprising a barrier
layer (2) and a functional layer (3) covering the first major surface of the barrier
layer (2).
Fig. 2 shows a cross-section of a waterproofing membrane (1) comprising a barrier
layer (2), a functional layer (3), and a connecting layer (4) arranged between the
barrier layer (2) and the functional layer (3).
Fig. 3 shows a cross-section of a waterproofed construction comprising a substrate
(5) and a layer of concrete (6) and a waterproofing membrane (1) arranged between
the outer surface of the substrate (5) and the layer of concrete (6) such that the
first surface of the barrier layer (2) is directed against the outer surface of the
substrate and the second surface of the functional layer is bonded to the layer of
concrete (6).
Detailed description of the invention
[0017] The subject of the present invention is a waterproofing membrane comprising a waterproofing
membrane comprising a barrier layer having first and second major surfaces and a functional
layer having first and second major surfaces, wherein the functional layer and the
barrier layer are directly or indirectly connected over at least a part of their opposing
major surfaces and wherein the functional layer is composed of an at least partially
cured moisture curing composition comprising:
- a) At least one silane-terminated polymer and
- b) Optionally at least one monomeric silane crosslinker.
[0018] Substance names beginning with "poly" designate substances which formally contain,
per molecule, two or more of the functional groups occurring in their names. For instance,
a polyol refers to a compound having at least two hydroxyl groups. A polyether refers
to a compound having at least two ether groups.
[0019] The term "polymer" designates a collective of chemically uniform macromolecules produced
by a polyreaction (polymerization, polyaddition, polycondensation) where the macromolecules
differ with respect to their degree of polymerization, molecular weight and chain
length. The term also comprises derivatives of said collective of macromolecules resulting
from polyreactions, that is, compounds which are obtained by reactions such as, for
example, additions or substitutions, of functional groups in predetermined macromolecules
and which may be chemically uniform or chemically nonuniform.
[0020] The term "polyurethane polymer" designates polymers prepared by so called diisocyanate
polyaddition process. This also includes those polymers which are virtually free or
entirely free from urethane groups. Examples of polyurethane polymers are polyether-polyurethanes,
polyester-polyurethanes, polyether-polyureas, polyureas, polyester-polyureas, polyisocyanurates,
and polycarbodiimides.
[0021] The terms "silane" and "organosilane" respectively identify compounds which in the
first instance have at least one, customarily two or three, hydrolyzable groups bonded
directly to the silicon atom via Si-O- bonds, more particularly alkoxy groups or acyloxy
groups, and in the second instance have at least one organic radical bonded directly
to the silicon atom via an Si-C bond. Silanes with alkoxy or acyloxy groups are also
known to the person skilled in the art as organoalkoxysilanes and organoacyloxysilanes,
respectively. Tetraalkoxysilanes, consequently, are not organosilanes under this definition.
[0022] Correspondingly, the term "silane group" designates the silicon-containing group
bonded to the organic carbon radical via the Si-C bond. The silanes, and their silane
groups, have the property of undergoing hydrolysis on contact with moisture. In so
doing, they form organosilanols, these being organosilicon compounds containing one
or more silanol groups (Si-OH groups) and, by subsequent condensation reactions, organosiloxanes,
these being organosilicon compounds containing one or more siloxane groups (Si-O-Si
groups).
[0023] The term "silane-functional" designates compounds which have silane groups. "Silane-functional
polymers" accordingly, are polymers which have at least one silane group. The term
"silane-terminated polymer" designates polymers having silane-groups at their chain
ends.
[0024] Silane designations with functional groups as prefixes such as "aminosilanes" or
"mercaptosilanes", for example, identify silanes which carry the stated functional
group on the organic radical as a substituent.
[0025] The terms "organotitanate", "organozirconate", "organostannates", and "organoaluminate"
in the present document identify compounds which have at least one organic ligand
bonding via an oxygen atom to the titanium, zirconium, tin, and aluminum atom, respectively.
[0026] In this document, an amine or an isocyanate is called "aliphatic" when its amine
group or its isocyanate group, respectively, is directly bound to an aliphatic, cycloaliphatic
or arylaliphatic moiety. The corresponding functional group is therefore called an
aliphatic amine or an aliphatic isocyanate group, respectively.
[0027] In this document, an amine or an isocyanate is called "aromatic" when its amine group
or its isocyanate group, respectively, is directly bound to an aromatic moiety. The
corresponding functional group is therefore called an aromatic amine or an aromatic
isocyanate group, respectively.
[0028] The term "primary amine group" designates an NH
2-group bound to an organic moiety, and the term "secondary amine group" designates
a NH-group bound to two organic moieties which together may be part of a ring.
[0029] The term "(meth)acrylic" designates methacrylic or acrylic. Accordingly, (meth)acryloyl
designates methacryloyl or acryloyl. A (meth)acryloyl group is also known as (meth)acryl
group. A (meth)acrylic compound can have one or more (meth)acryl groups, such as mono-
di-, tri- etc. functional (meth)acrylic compounds.
[0030] The term "molecular weight" designates the molar mass (g/mol) of a molecule or a
part of a molecule, also referred to as "moiety". The term "average molecular weight"
designates the number average molecular weight (M
n) of an oligomeric or polymeric mixture of molecules or moieties. The number average
molecular weight can be determined by gel permeation chromatography (GPC) with a polystyrene
standard.
[0031] The term "glass transition temperature" (T
g) designates the temperature above which temperature a polymer component becomes soft
and pliable, and below which it becomes hard and glassy. The glass transition temperature
is preferably determined differential scanning calorimetry method (DSC) according
to ISO 11357 standard using a heating rate of 2 °C/min. The measurements can be performed
with a Mettler Toledo DSC 3+ device and the T
g values can be determined from the measured DSC-curve with the help of the DSC-software.
[0032] The term "softening point" designates a temperature at which compound softens in
a rubber-like state, or a temperature at which the crystalline portion within the
compound melts. The softening point can be measured by a ring and ball method according
to DIN EN 1238.
[0033] The "amount or content of at least one component X" in a composition, for example
"the amount of the at least one thermoplastic polymer P" refers to the sum of the
individual amounts of all thermoplastic polymers P contained in the composition. For
example, in case the composition comprises 20 wt.-% of at least one thermoplastic
polymer P, the sum of the amounts of all thermoplastic polymers P contained in the
composition equals 20 wt.-%.
[0034] The term "room temperature" designates a temperature of 23°C.
[0035] A dashed line in the chemical formulas of this document represents the bonding between
a moiety and the corresponding rest of the molecule.
[0036] The barrier layer is preferably a planar element having first and second major surfaces,
i.e. top and bottom surfaces, defined by peripheral edges. The term "planar element"
designates in the present document sheet-like elements having a length and width at
least 50 times, preferably at least 100 times, more preferably at least 500 times,
greater than the thickness of the element.
[0037] The functional layer is composed of an at least partially cured moisture curing composition.
The term "curing composition" or "curable composition" designates in the present document
compositions, which can be cured by initiation of the curing reactions. The term "curing
reaction" designates in the present document chemical reactions comprising forming
bonds resulting, for example, in chain extension and/or crosslinking of polymer chains.
The term "cured" as used in connection with a curing composition, for example "at
least partially cured moisture curing composition", is understood to mean that at
least a portion of the polymerizable and/or crosslinkable components that form the
moisture curing composition is cured. It may be preferable that the functional layer
is composed of a moisture curing composition having a curing degree of reactive groups,
in particular curing degree of silane groups of at least 15%, preferably at least
35%, more preferably at least 55%, even more preferable at least 65%, most preferably
at least 75%. The term "curing degree of silane groups" designates the number of silane
groups that have undergone a curing reaction relative to the number of silane groups
that were originally unreacted before initiation of the curing reactions. Furthermore,
it may be preferable that the functional layer is composed of a moisture curing composition
having a curing degree of reactive groups, in particular curing degree of silane groups
of at least 85%, more preferably at least 95%, even more preferably at least 97.5%,
most preferable at least 99%.
[0038] It may be preferable that the functional layer is composed of a moisture curing composition
that is essentially completely cured. The term "essentially completely cured" is understood
to mean that the composition has a curing degree of all reactive groups, in particular
of silane, epoxy, and amine groups, of at least of at least 85%, more preferably at
least 95%, even more preferably at least 97.5%, most preferable at least 99%.
[0039] According to one or more embodiments, the functional layer is composed of a continuous
layer of at least partially cured moisture curing composition. The term "continuous
layer" designates in the present document layers consisting of one single area of
the respective material. In contrast, a "discontinuous layer" is considered to consist
of more than one areas of the respective material, which areas are not connected with
each other to form one single continuous layer of the material.
[0040] The functional layer and the barrier layer are at directly or indirectly connected
over at least a part of their opposing major surfaces. It may, however, be preferable
that substantially the entire area of the first major surface of the functional layer
is directly or indirectly connected to the second major surface of the waterproofing
layer. It may furthermore be preferable that the functional layer and the waterproofing
layer have substantially the same width and length.
[0041] According to one or more embodiments, the functional layer and the barrier layer
are directly connected to each other over at least a part of their opposing major
surfaces. The expression "directly connected" is understood to mean in the context
of the present invention that no further layer or substance is present between the
layers, and that the opposing surfaces of the two layers are directly bonded to each
other or adhere to each other. At the transition area between the two layers, the
materials forming the layers can also be present mixed with each other. According
to one or more embodiments, substantially the entire first major surface of the functional
layer is directly connected to the second major surface of the barrier layer. In these
embodiments, it may for example be preferable that at least 90%, more preferably at
least 95%, of the first major surface of the functional layer is directly connected
to the second major surface of the barrier layer.
[0042] The moisture curing composition may be a single-component moisture curing composition
or a multiple-component moisture curing composition, in particular a two-component
moisture curing composition. In case of a multiple-component composition, the at least
partially cured moisture curing composition is obtained by mixing the components of
the multiple-component moisture curing composition with each other and allowing the
thus obtained mixture to cure.
[0043] The term "single-component composition" or "single-part composition" designates in
the present document storage-stable compositions, in which the constituents of the
composition are provided in a one component. Single-component compositions can be
provided packaged in one package whereas in two-component or multi-component compositions
the components are provided packaged in physically separated compartments or in separate
packages in order to ensure storage-stability. The terms "storage stability" and "shelf
life stability" refer to the ability of a composition to be stored at room temperature
in a suitable container under exclusion of moisture for a certain time interval, in
particular several months, without undergoing significant changes in application or
end-use properties.
[0044] Preferably, the at least one silane-terminated polymer has at least one terminal
group of formula (I):

wherein
R1 is an alkyl- group having 1 to 8 C atoms,
R2 is an acyl or alkyl group having 1 to 5 C atoms,
R3 is a linear or branched, or cyclic, alkylene group having 1 to 12 C atoms, optionally
with aromatic moieties, and optionally with 1 or more heteroatoms, and
a is 0 or 1 or 2, preferably 0.
[0045] Within a silane group of the formula (I), R
1 and R
2, each independently of one another, are the radicals as described. Thus, for example,
possible compounds of the formula (I) include those which represent the ethoxy-dimethoxy-alkylsilanes
(R
2 = methyl, R
2 = methyl, R
2 = ethyl).
[0046] Preferably, the silane-terminated polymer is a silane-terminated polyurethane polymer,
more preferably a silane-terminated polyurethane polymer that is entirely free of
isocyanate groups.
[0047] According to one or more embodiments, the at least one silane-terminated polymer
is a silane-terminated polyurethane polymer P1, which is obtainable by the reaction
of a silane having at least one group that is reactive toward isocyanate groups, with
a polyurethane polymer which contains terminal isocyanate groups. This reaction is
carried out preferably in a stoichiometric ratio of the groups that are reactive toward
isocyanate groups to the isocyanate groups of 1:1, or with a slight excess of groups
that are reactive toward isocyanate groups, meaning that the resulting silane-terminated
polyurethane polymer is preferably entirely free of isocyanate groups.
[0048] Suitable silanes which have at least one group that is reactive toward isocyanate
groups include, for example, mercaptosilanes, aminosilanes, and hydroxysilanes, in
particular aminosilanes and hydroxysilanes. Particularly suitable aminosilanes include
aminosilanes of the formula (la):
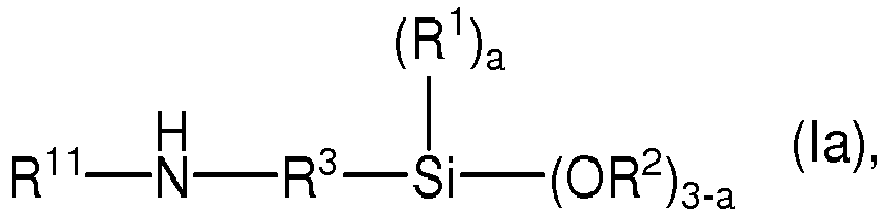
wherein the radicals R
1, R
2, R
3, and a have the already described meanings and R
11 is a hydrogen atom or is a linear or branched hydrocarbon radical having 1 to 20
C atoms that optionally contains cyclic moieties, or is a radical of the formula (II):

wherein the radicals R
12 and R
13, independently of one another, are a hydrogen atom or a radical from the group encompassing
-R
15, -CN, and -COOR
15, radical R
14 is a hydrogen atom or is a radical from the group encompassing -CH
2-COOR
15, -COOR
15, CONHR
15, -CON(R
15)
2, -CN, -NO
2, -PO(OR
15)
2, -SO
2R
15, and -SO
2OR
15, and the radical R
15 is a hydrocarbon radical having 1 to 20 C atoms that optionally comprises at least
one heteroatom.
[0049] Examples of preferred aminosilanes are primary aminosilanes such as 3-aminopropyltriethoxysilane,
3-aminopropyldiethoxymethylsilane; secondary aminosilanes such as N-butyl-3-aminopropyltriethoxysilane,
N-phenyl-3-aminopropyltriethoxysilane; the products of the Michael-like addition of
primary aminosilanes such as 3-aminopropyltriethoxysilane or 3-aminopropyldiethoxymethylsilane
onto Michael acceptors such as acrylonitrile, (meth)acrylic esters, (meth)acrylamides,
maleic diesters and fumaric diesters, citraconic diesters and itaconic diesters, examples
being dimethyl and diethyl N-(3-triethoxysilylpropyl)aminosuccinate; and also analogs
of the stated aminosilanes having methoxy or isopropoxy groups instead of the preferred
ethoxy groups on the silicon. Particularly suitable aminosilanes are secondary aminosilanes,
more particularly aminosilanes in which R
4 in formula (II) is different from H. Preferred are the Michael-like adducts, more
particularly diethyl N-(3-triethoxysilylpropyl)aminosuccinate.
[0050] The term "Michael acceptor" designates in the present document compounds which on
the basis of the double bonds they contain, activated by electron acceptor radicals,
are capable of entering into nucleophilic addition reactions with primary amino groups
(NH
2 groups) in a manner analogous to Michael addition (hetero-Michael addition).
[0052] Examples of suitable polyurethane polymers containing isocyanate groups for the preparation
of a silane-terminated polyurethane polymer include polymers which are obtainable
by the reaction of at least one polyol with at least one polyisocyanate, more particularly
a diisocyanate. This reaction may take place by the polyol and the polyisocyanate
being reacted by customary methods, as for example at temperatures of 50°C to 100°C,
optionally with accompanying use of suitable catalysts, the polyisocyanate being metered
such that its isocyanate groups are present in a stoichiometric excess in relation
to the hydroxyl groups of the polyol.
[0053] More particularly the excess of polyisocyanate is preferably selected such that in
the resulting polyurethane polymer, after the reaction of all hydroxyl groups of the
polyol, the remaining free isocyanate group content is from 0.1 to 5 wt.-%, preferably
0.1 to 2.5 wt.-%, more preferably 0.2 to 1 wt.-%, based on the overall polymer.
[0054] The polyurethane polymer may optionally be prepared with accompanying use of plasticizers,
in which case the plasticizers used contain no groups that are reactive toward isocyanates.
[0055] Preferred polyurethane polymers with the stated amount of free isocyanate groups
are those obtained from the reaction of diisocyanates with high molecular mass diols
in an NCO:OH ratio of 1.5:1 to 2:1.
[0056] Suitable polyols for preparing the polyurethane polymer are, in particular, polyether
polyols, polyester polyols, and polycarbonate polyols, and also mixtures of these
polyols.
[0057] Especially suitable polyether polyols, also called polyoxyalkylene polyols or oligoetherols,
are those which are polymerization products of ethylene oxide, 1,2-propylene oxide,
1,2- or 2,3-butylene oxide, oxetane, tetrahydrofuran, or mixtures thereof, optionally
polymerized with the aid of a starter molecule having two or more active hydrogen
atoms, such as water, ammonia, for example, or compounds having two or more OH or
NH groups such as, for example, 1,2-ethanediol, 1,2- and 1,3-propanediol, neopentyl
glycol, diethylene glycol, triethylene glycol, the isomeric dipropylene glycols and
tripropylene glycols, the isomeric butanediols, pentanediols, hexanediols, heptanediols,
octanediols, nonanediols, decanediols, undecanediols, 1,3- and 1,4-cyclohexanedimethanol,
bisphenol A, hydrogenated bisphenol A, 1,1,1-trimethylolethane, 1,1,1-trimethylolpropane,
glycerol, aniline, and mixtures of the stated compounds. Use may be made both of polyoxyalkylene
polyols which have a low degree of unsaturation (measured by ASTM D-2849-69 and expressed
in milliequivalents of unsaturation per gram of polyol (meq/g)), prepared for example
by means of double metal cyanide complex catalysts (DMC catalysts), and of polyoxyalkylene
polyols having a higher degree of unsaturation, prepared for example by means of anionic
catalysts such as NaOH, KOH, CsOH, or alkali metal alkoxides.
[0058] Particularly suitable are polyoxyethylene polyols and polyoxypropylene polyols, more
particularly polyoxyethylene diols, polyoxypropylene diols, polyoxyethylene triols,
and polyoxypropylene triols.
[0059] Especially suitable are polyoxyalkylene diols or polyoxyalkylene triols having a
degree of unsaturation of less than 0.02 meq/g and having an average molecular weight
in the range from 1,000 to 30,000 g/mol, and also polyoxyethylene diols, polyoxyethylene
triols, polyoxypropylene diols, and polyoxypropylene triols having an average molecular
weight of 400 to 20,000 g/mol. Likewise particularly suitable are so-called ethylene
oxide-terminated ("EO-endcapped", ethylene oxide-endcapped) polyoxypropylene polyols.
The latter are special polyoxypropylene-polyoxyethylene polyols which are obtained,
for example, by subjecting pure polyoxypropylene polyols, more particularly polyoxypropylene
diols and triols, to further alkoxylation with ethylene oxide after the end of the
polypropoxylation reaction, and which therefore have primary hydroxyl groups. Preferred
in this case are polyoxypropylene-polyoxyethylene diols and polyoxypropylene-polyoxyethylene
triols.
[0060] Additionally suitable are hydroxyl group terminated polybutadiene polyols, examples
being those prepared by polymerization of 1,3-butadiene and allyl alcohol or by oxidation
of polybutadiene, and their hydrogenation products.
[0061] Additionally suitable are styrene-acrylonitrile grafted polyether polyols, of the
kind available commercially, for example, under the trade name Lupranol® from BASF
SE, Germany.
[0062] Especially suitable as polyester polyols are polyesters which carry at least two
hydroxyl groups and are prepared by known processes, particularly by the polycondensation
of hydroxycarboxylic acids or the polycondensation of aliphatic and/or aromatic polycarboxylic
acids with dihydric or polyhydric alcohols.
[0063] Especially suitable polyester polyols are those prepared from di- to trihydric alcohols
such as, for example, 1,2-ethanediol, diethylene glycol, 1,2-propanediol, dipropylene
glycol, 1,4-butanediol, 1,5-pentanediol, 1,6-hexanediol, neopentyl glycol, glycerol,
1,1,1-trimethylolpropane, or mixtures of the aforesaid alcohols, with organic dicarboxylic
acids or their anhydrides or esters, such as, for example, succinic acid, glutaric
acid, adipic acid, trimethyladipic acid, suberic acid, azelaic acid, sebacic acid,
dodecanedicarboxylic acid, maleic acid, fumaric acid, dimer fatty acid, phthalic acid,
phthalic anhydride, isophthalic acid, terephthalic acid, dimethyl terephthalate, hexahydrophthalic
acid, trimellitic acid, and trimellitic anhydride, or mixtures of the aforesaid acids,
and also polyester polyols of lactones such as ε-caprolactone, for example.
[0064] Particularly suitable are polyester diols, especially those prepared from adipic
acid, azelaic acid, sebacic acid, dodecanedicarboxylic acid, dimer fatty acid, phthalic
acid, isophthalic acid, and terephthalic acid as dicarboxylic acid, or from lactones
such as ε-caprolactone, for example, and from ethylene glycol, diethylene glycol,
neopentyl glycol, 1,4-butanediol, 1,6-hexanediol, dimer fatty acid diol, and 1,4-cyclohexanedimethanol
as dihydric alcohol.
[0065] Especially suitable polycarbonate polyols are those obtainable by reaction, for example,
of the abovementioned alcohols, used for synthesis of the polyester polyols, with
dialkyl carbonates such as dimethyl carbonate, diaryl carbonates such as diphenyl
carbonate, or phosgene. Particularly suitable are polycarbonate diols, especially
amorphous polycarbonate diols.
[0066] Other suitable polyols are poly(meth)acrylate polyols.
[0067] Likewise suitable, moreover, are polyhydrocarbon polyols, also called oligohydrocarbonols,
examples being polyhydroxy-functional ethylene-propylene, ethylene-butylene or ethylene-propylene-diene
copolymers, as produced for example by Kraton Polymers, USA, or polyhydroxy-functional
copolymers of dienes such as 1,3-butanediene or diene mixtures and vinyl monomers
such as styrene, acrylonitrile or isobutylene, or polyhydroxy-functional polybutadiene
polyols, examples being those which are prepared by copolymerization of 1,3-butadiene
and allyl alcohol and which may also have been hydrogenated.
[0068] Additionally suitable are polyhydroxy-functional acrylonitrile/butadiene copolymers
of the kind preparable, for example, from epoxides or amino alcohols and carboxyl-terminated
acrylonitrile/butadiene copolymers, which are available commercially under the name
Hypro® (formerly Hycar® CTBN from Emerald Performance Materials, LLC, USA.
[0069] These stated polyols preferably have a molecular weight of 250 to 30,000 g/mol, more
particularly of 1,000 to 30,000 g/mol, and an average OH functionality in the range
from 1.6 to 3.
[0070] Particularly suitable polyols are polyester polyols and polyether polyols, more particularly
polyether polyols, such as polyoxyethylene polyol, polyoxypropylene polyol, and polyoxypropylene-polyoxyethylene
polyol, preferably polyoxyethylene diol, polyoxypropylene diol, polyoxyethylene triol,
polyoxypropylene triol, polyoxypropylene-polyoxyethylene diol, and polyoxypropylene-polyoxyethylene
triol.
[0071] Further to these stated polyols it is possible as well to use small amounts of low
molecular weight dihydric or polyhydric alcohols such as, for example, 1,2-ethanediol,
1,2- and 1,3-propanediol, neopentyl glycol, diethylene glycol, triethylene glycol,
the isomeric dipropylene glycols and tripropylene glycols, the isomeric butanediols,
pentanediols, hexanediols, heptanediols, octanediols, nonanediols, decanediols, undecanediols,
1,3- and 1,4-cyclohexanedimethanol, hydrogenated bisphenol A, dimeric fatty alcohols,
1,1,1-trimethylolethane, 1,1,1-trimethylolpropane, glycerol, pentaerythritol, sugar
alcohols such as xylitol, sorbitol or mannitol, sugars such as sucrose, other higher
alcohols, low molecular weight alkoxylation products of the aforesaid dihydric and
polyhydric alcohols, and also mixtures of the aforesaid alcohols, when preparing the
polyurethane polymer having terminal isocyanate groups.
[0072] As polyisocyanates for the preparation of the polyurethane polymer it is possible
to use commercially customary aliphatic, cycloaliphatic or aromatic polyisocyanates,
more particularly diisocyanates. Suitable diisocyanates by way of example are those
whose isocyanate groups are bonded in each case to one aliphatic, cycloaliphatic or
arylaliphatic C atom, also called "aliphatic diisocyanates", such as 1,6-hexamethylene
diisocyanate (HDI), 2-methylpentamethylene 1,5-diisocyanate, 2,2,4- and 2,4,4-trimethyl-1,6-hexamethylene
diisocyanate (TMDI), 1,12-dodecamethylene diisocyanate, lysine diisocyanate and lysine
ester diisocyanate, cyclohexane 1,3-diisocyanate, cyclohexane 1,4-diisocyanate, 1-isocyanato-3,3,5-trimethyl-5-isocyanatomethylcyclohexane
(= isophorone diisocyanate or IPDI), perhydro-2,4'-diphenylmethane diisocyanate and
perhydro-4,4'-diphenylmethane diisocyanate, 1,4-diisocyanato-2,2,6-trimethylcyclohexane
(TMCDI), 1,3- and 1,4-bis(isocyanatomethyl)cyclohexane, m- and p-xylylene diisocyanate
(m- and p-XDI), m- and p-tetramethyl-1,3-xylylene diisocyanate, m- and p-tetramethyl-1,4-xylylene
diisocyanate, bis(1-isocyanato-1-methylethyl)naphthalene; and also diisocyanates having
isocyanate groups bonded in each case to one aromatic C atom, also called "aromatic
diisocyanates", such as 2,4- and 2,6-tolylene diisocyanate (TDI), 4,4'-, 2,4'-, and
2,2'-diphenylmethane diisocyanate (MDI), 1,3- and 1,4-phenylene diisocyanate, 2,3,5,6-tetramethyl-1,4-diisocyanatobenzene,
naphthalene 1,5-diisocyanate (NDI), 3,3'-dimethyl-4,4'-diisocyanatodiphenyl (TODI);
oligomers and polymers of the aforementioned isocyanates, and also any desired mixtures
of the aforementioned isocyanates.
[0073] Suitable methoxysilane-funtional polymers are available commercially, for example,
under the trade name Polymer ST50 from Hanse Chemie AG, Germany, and also under the
trade name Desmoseal® from Covestro AG, Germany.
[0074] Preferably, the silane-terminated polymer
P1 is an ethoxysilane-terminated polyurethane polymer.
[0075] According to one or more preferred embodiments, the at least one silane-terminated
polymer is a silane-terminated polyurethane polymer
P2, which is obtainable through the reaction of isocyanotosilane with a polymer which
has functional end groups that are reactive toward isocyanates, these end groups being
more particularly hydroxyl groups, mercapto groups and/or amino groups. This reaction
takes place in a stoichiometric ratio of the isocyanate groups to the functional end
groups that are reactive toward isocyanate groups of 1:1, or with a slight excess
of the functional end groups that are reactive toward isocyanate groups, at temperatures,
for example, of 20°C to 100°C, optionally with accompanying use of catalysts.
[0076] Suitable isocyanatosilanes include compounds of the formula (lb):
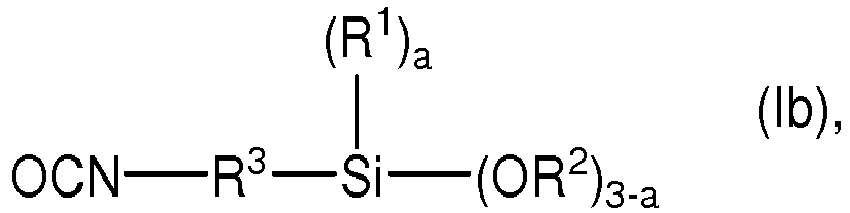
wherein R
1, R
2, R
3 have the already mentioned meanings. Examples of suitable isocyanatosilanes of the
formula (lb) are 3-isocyanatopropyltriethoxysilane, 3-isocyanatopropyldiethoxymethylsilane,
and their analogs with methoxy or isopropoxy groups in place of the ethoxy groups
in the silica.
[0077] The polymer preferably has hydroxyl groups as functional end groups, which are reactive
toward isocyanate groups of isocyanotosilane. Suitable polymers having hydroxyl groups
are, on the one hand, high molecular weight polyoxyalkylene polyols already identified,
preferably polyoxypropylene diols having a degree of unsaturation of less than 0.02
meq/g and having an average molecular weight in the range from 4,000 to 30,000 g/mol,
more particularly those having an average molecular weight in the range from 8,000
to 30,000 g/mol.
[0078] Also suitable on the other hand are polyurethane polymers having hydroxyl groups,
especially terminated with hydroxyl groups, for reaction with isocyanatosilanes of
the formula (lb). Polyurethane polymers of this kind are obtainable through the reaction
of at least one polyisocyanate with at least one polyol. This reaction may be accomplished
by bringing the polyol and the polyisocyanate to reaction by customary processes,
at temperatures of 50°C to 100°C, for example, optionally with accompanying use of
suitable catalysts, the polyol being metered such that its hydroxyl groups are in
a stoichiometric excess in relation to the isocyanate groups of the polyisocyanate.
Preferred is a ratio of hydroxyl groups to isocyanate groups of 1.3:1 to 4:1, more
particularly of 1.8:1 to 3:1. The polyurethane polymer may optionally be prepared
with accompanying use of plasticizers, in which case the plasticizers used contain
no groups reactive toward isocyanates. Suitable for this reaction are the same polyols
and polyisocyanates already referenced as being suitable for the preparation of a
polyurethane polymer containing isocyanate groups that is used for preparing a silane-terminated
polyurethane polymer
P1.
[0079] Suitable methoxysilane-terminated polymers are commercially available, for example,
under the trade names SPUR+® 1010LM, 1015LM, and 1050MM from Momentive Performance
Materials Inc., USA, and also under the trade names Geniosil® STP-E15, STP-10, and
STP-E35 from Wacker Chemie AG, Germany, and also under the trade name Incorez STP
from Sika Incorez, UK. Preferably, the silane-terminated polymer
P2 is an ethoxysilane-terminated polyurethane polymer.
[0080] According to one or more embodiments, the silane-terminated polymer is a silane-terminated
polymer
P3, which is obtainable by a hydrosilylation reaction of polymers, having terminal double
bonds, examples being poly(meth)acrylate polymers or polyether polymers, more particularly
of allyl-terminated polyoxyalkylene polymers, as described for example in
US 3,971,751 and
US 6,207,766.
[0081] Suitable methoxysilane-terminated polymers are commercially available, for example,
under the trade names MS-Polymer® S203(H), S303(H), S227, S810, MA903, and S943, Silyl®
SAX220, SAX350, SAX400, and SAX725, Silyl® SAT350, and SAT400, and also XMAP® SA100S,
and SA310S from Kaneka Corp., Japan, and also under the trade names Excestar® S2410,
S2420, S3430, S3630, W2450, and MSX931 from Asahi Glass Co, Ltd., Japan. Preferably,
the silane-terminated polymer
P3 is an ethoxysilane-terminated polymer.
[0082] It is also possible to use as the at least one silane-terminated polymers other silane-terminated
polymers that are commercially available, for example, under the trade name Tegopac®
from Evonik Industries, Germany, more particularly Tegopac® Seal 100, Tegopac® Bond
150, Tegopac® Bond 250.
[0083] Preferably, the at least one silane-terminated polymer is free of methoxysilane-groups,
i.e. the composition preferably comprises no constituents which give off methanol
upon curing in the presence of water.
[0084] According to one or more embodiments, the at least one silane-terminated polymer
is present in the moisture curing composition in an amount of at least 5 wt.-%, preferably
at least 10 wt.-%, more preferably at least 15 wt.-%, most preferably at least 20
wt.-%, based on the total weight of the moisture curing composition. According to
one or more further embodiments, the at least one silane-terminated polymer is present
in the moisture curing composition in an amount of 5 - 85 wt.-%, more preferably 10
- 75 wt.-%, even more preferably 15 - 65 wt.-%, most preferably 20 - 55 wt.-%, based
on the total weight of the moisture curing composition.
[0085] According to one or more embodiments, the moisture curing composition further comprises:
b) At least one silane crosslinker.
[0086] Suitable silane crosslinkers include monomeric and oligomeric silane compounds containing
one or more, preferably two or more functional residues. Particularly suitable silane
crosslinkers include, for example, aminosilanes, epoxysilanes, mercaptosilanes, (meth)acrylosilanes,
vinylsilanes, urea silanes, and anhydridosilanes or adducts of the aforesaid silanes
with primary aminosilanes. According to one or more embodiments, the moisture curing
composition comprises at least one silane crosslinker selected from the group consisting
of aminosilanes, epoxysilanes, mercaptosilanes, (meth)acrylosilanes, and vinyl silanes.
The presence of the silane crosslinkers has been found to improve the mechanical properties
of the functional layer.
[0087] Particularly suitable silane crosslinker include vinyl trialkoxysilanes, 3-aminopropyl-dialkoxyalkylsilanes,
3-aminopropyl-trialkoxysilanes, N-(2-aminoethyl)-3-aminopropyl-dialkoxyalkylsilanes,
N-(2-aminoethyl)-3-aminopropyl-trialkoxysilanes, 3-glycidoxypropyltrialkoxysilanes
and 3-mercaptopropyl-trialkoxysilanes. According to one or more embodiments, the at
least silane crosslinker is selected from the group consisting of vinyl trimethoxysilane,
vinyl triethoxysilane, 3-aminopropyl-trimethoxysilane, 3-aminopropyl-triethoxysilane,
N-(2-aminoethyl)-3-aminopropyl-dimethoxymethylsilane, N-(2-aminoethyl)-3-aminopropyl-trimethoxysilane,
N-(2-aminoethyl)-3-aminopropyl-triethoxysilane, 3-glycidoxypropyltrimethoxysilane,
3-glycidoxypropyltriethoxysilane, 3-mercaptopropyl-trimethoxysilane and 3-mercaptopropyl-triethoxysilane.
[0088] The amount of silane crosslinkers in the moisture curing composition is not particularly
restricted. According to one or more embodiments, the at least one silane crosslinker
is present in the moisture curing composition in an amount of 0.5 - 10.0 wt.-%, more
preferably 1.0 - 7.5 wt.-%, most preferably 1.5 - 5.0 wt.-%, based on the total weight
of the moisture curing composition.
[0089] According to one or more embodiments, the moisture curing composition further comprises:
c) At least one filler, preferably at least one inert mineral filler.
[0090] The term "inert mineral filler" designates in the present document mineral fillers,
which, unlike mineral binders are not reactive with water, i.e. do not undergo a hydration
reaction in the presence of water. The presence of inert mineral fillers in the moisture
curing composition has been found out to improve the concrete adhesion strength of
the functional layer. The term "concrete adhesion strength" designates in the present
document the adhesive bond strength between a substrate and a surface of a concrete
specimen, which has been casted on the surface of the substrate and allowed to harden.
The concrete adhesion strength of a waterproofing membrane can be measured as average
peel force required to separate the membrane from the surface of a cured concrete
specimen.
[0091] Particularly suitable inert mineral fillers include, for example, sand, granite,
calcium carbonate, calcium kaolins, diatomaceous earth, pumice, mica, talc, dolomite,
xonotlite, perlite, vermiculite, Wollastonite, barite, magnesium carbonate, calcium
hydroxide, calcium aluminates, silica, fumed silica, precipitated silica, aerogels,
glass beads, hollow glass spheres, ceramic spheres, bauxite, comminuted concrete,
and zeolites. The term "calcium carbonate" designates in the present document calcitic
fillers produced from chalk, limestone or marble by grinding and/or precipitation.
[0092] According to one or more embodiments, the at least one filler is selected from the
group consisting of calcium carbonate, calcium kaolins, diatomaceous earth, silica,
fumed silica, and precipitated silica. According to one or more further embodiments,
the moisture curing composition comprises at least two different fillers, preferably
at least two different inert mineral fillers, preferably selected from the group consisting
of calcium carbonate, calcium kaolins, diatomaceous earth, silica, fumed silica, and
precipitated silica.
[0093] Preferably, the at least one filler has a median particle size d
50 of not more than 100 µm, more preferably not more than 50 µm, most preferably not
more than 25 µm. In particular, the median particle size d
50 of the at least one filler is in the range of 0.5 - 100.0 µm, preferably 0.5 - 50.0
µm, more preferably 1.0 - 25.0 µm, most preferably 1.0 - 10.0 µm.
[0094] The term median particle size d
50 designates in the present document the particle size below which 50% of all particles
by volume are smaller than the d
50 value. The term "particle size" designates the area-equivalent spherical diameter
of a particle. The particle size distribution can be measured by laser diffraction
according to the method as described in standard ISO 13320:2009. A Mastersizer 2000
device (trademark of Malvern Instruments Ltd, GB) can be used in measuring particle
size distribution.
[0095] According to one or more embodiments, the at least one filler, preferably at least
one inert mineral filler, is present in the moisture curing composition in an amount
of at least 2.5 wt.-%, more preferably at least 10.0 wt.-%, most preferably at least
15.0 wt.-%, based on the total weight of the moisture curing composition. According
to one or more further embodiments, the at least one filler, preferably at least one
inert mineral filler, is present in the moisture curing composition in an amount of
5 - 75 wt.-%, preferably 10 - 70 wt.-%, more preferably 15 - 65 wt.-%, most preferably
20 - 60 wt.-%, based on the total weight of the moisture curing composition.
[0096] According to one or more embodiments, the moisture curing composition is a two-component
composition composed of a first component A comprising:
- The at least one silane-terminated polymer,
- Optionally the at least one silane crosslinker, and
- Optionally at least one first filler, preferably at least one first inert mineral
filler, and
a second component B comprising:
- Water,
- Optionally at least one second filler, preferably at least one second inert mineral
filler, and
- Optionally at least one curing catalyst.
[0097] The at least one silane-terminated polymer, the at least one silane crosslinker,
and the at least one first and/or second filler contained in the two-component moisture
curing composition may be the same as those described above as components a), b),
and c), including the preferred embodiments identified there.
[0098] According to one or more embodiments, the proportion of the at least one silane crosslinker
is 0.1 - 15.0 wt.-%, preferably 0.5 - 10.0 wt.-%, based on the total weight of the
first component
A. It may be preferable that the first component
A comprises at least two different silane crosslinkers.
[0099] According to one or more embodiments, the proportion of the at least one first filler
is 0.5 - 25.0 wt.-%, preferably 1.0 - 20.0 wt.-%, based on the total weight of the
first component
A. It may be preferable that the first component
A comprises at least two different fillers, preferably at least two different inert
mineral fillers.
[0100] According to one or more embodiments, the weight ratio of the component
A to component
B is from 0.5:1 to 5:1, preferably from 1:1 to 3:1.
[0101] According to one or more embodiments, the proportion of water is 0.5 - 25.0 wt.-%,
preferably 1.0 - 20.0 wt.-%, based on the total weight of the second component
B.
[0102] According to one or more embodiments, the proportion of the at least one second filler
is 1.0 - 65.0 wt.-%, preferably 10.0 - 55.0 wt.-%, based on the total weight of the
second component
B. It may be preferable that the second component
B comprises at least two different fillers, preferably at least two different inert
mineral fillers.
[0103] According to one or more embodiments, the second component
B further comprises at least one curing catalyst.
[0104] Suitable curing catalysts to be used in the moisture curing composition include those
which accelerate the reaction of the silane groups with moisture. These include, for
example, organic titanium, tin, zirconium, aluminum, and phosphorus compounds. Particularly
preferable as curing catalyst are organotitanates, organozirconates, organostannates,
and organoaluminates. As organic ligands these catalysts can contain, in particular,
alkoxy groups, sulfonate groups, carboxyl groups, dialkylphosphate groups, dialkylpyrophosphate
and dialkyldiketonate groups.
[0105] Particularly suitable organotitanates include titanium(IV) complex compounds having
two 1,3-diketonate ligands, especially 2,4-pentanedionate (i.e., acetylacetonate),
and two alkoxide ligands; titanium(IV) complex compounds having two 1,3-ketoesterate
ligands, more particularly ethyl acetoacetate, and two alkoxide ligands; titanium(IV)
complex compounds having one or more amino alkoxide ligands, more particularly triethanolamine
or 2-((2-aminoethyl)amino)ethanol, and one or more alkoxide ligands; titanium(IV)
complex compounds having four alkoxide ligands; and organotitanates with higher degrees
of condensation, especially oligomeric titanium(IV) tetrabutoxide, also referred to
as polybutyl titanate.
[0106] Especially suitable as alkoxide ligands are isobutoxy, n-butoxy, isopropoxy, ethoxy,
and 2-ethylhexoxy. Especially suitable are bis(ethylacetoacetato)diisobutoxytitanium(IV),
bis(ethylacetoacetato)diisopropoxytitanium(IV), bis(acetylacetonato)-diisopropoxytitanium(IV),
bis(acetylacetonato)diisobutoxytitanium(IV), tris(oxyethyl)amineisopropoxytitanium(IV),
bis[tris(oxyethyl)amine]diisopropoxytitanium(IV), bis(2-ethylhexane-1,3-dioxy)titanium(IV),
tris[2-((2-aminoethyl)amino)ethoxy]ethoxytitanium(IV), bis(neopentyl(diallyl)oxydiethoxytitanium(IV),
titanium(IV) tetrabutoxide, tetra-(2-ethylhexyloxy)titanate, tetra(isopropoxy)titanate,
and polybutyl titanate.
[0107] Suitable organotitanates are commercially available under the trade name of Tyzor®
AA, GBA, GBO, AA-75, AA-65, AA-105, DC, BEAT, BTP, TE, TnBT, KTM, TOT, TPT or IBAY
(all from Du Pont / Dorf Ketal); under the trade name of Tytan® PBT, TET, X85, TAA,
ET, S2, S4 or S6 (all from TensoChema), and under the trade name of Ken-React® KR®
TTS, 7, 9QS, 12, 26S, 33DS, 38S, 39DS, 44, 134S, 138S, 133DS, 158FS or LICA® 44 (all
from Kenrich Petrochemicals).
[0108] Suitable organozirconates are commercially available under the trade name of Ken-React®
NZ® 38J, KZ® TPPJ, KZ® TPP, NZ® 01, 09, 12, 38, 44 or 97 (all from Kenrich Petrochemicals)
and under the trade name of Snapcure® 3020, 3030, 1020 (all from Johnson Matthey &
Brandenberger). A particularly suitable organoaluminate is the commercially available
under the trade name of K-Kat® 5218 (from King Industries).
[0109] According to one or more embodiments, the proportion of the at least one curing catalyst
is 0.1 - 10.0% by weight, preferably 0.5 - 7.5% by weight, even more preferably 1.0
- 5.0% by weight, most preferably 1.5 - 5.0% by weight, based on the total weight
of the second component
B.
[0110] According to one or more further embodiments, the moisture curing composition is
a two-component composition composed of a first component
A comprising:
- The at least one silane-terminated polymer,
- At least one hardener or accelerator for epoxy resins,
- Optionally the at least one silane crosslinker, and
- Optionally at least one first filler, preferably at least one first inert mineral
filler,
and a second component
B comprising:
- At least one aqueous emulsion of at least one epoxy resin, and
- Optionally at least one second filler, preferably at least one second inert mineral
filler.
[0111] The at least one silane-terminated polymer, the at least one silane crosslinker,
and the at least one first and/or second filler contained in the two-component moisture
curing composition may be the same as those described above as components a), b),
and c), including the preferred embodiments identified there.
[0112] The at least one epoxy resin is preferably a liquid resin. Preferred liquid epoxy
resins have the formula (III):

[0113] Here, the substituents R
1 and R
2 independently represent either H or CH
3. In addition, the subscript r represents a value of 0 to 1. Preferably, r represents
a value of ≤ 0.2.
[0114] Thus these are preferably diglycidyl ethers of bisphenol A (DGEBA), bisphenol F and
bisphenol A/F. The designation "A/F" here designates a mixture of acetone with formaldehyde,
which is used as an educt in the production of bisphenol A/F. Suitable liquid resins,
for example, are commercially available under the trade names Araldite® GY 250, Araldite®
GY 282, Araldite® PY 304 from Huntsman International LLC, USA, or D.E.R.® 330 or D.E.R.®
331 from Dow Chemical Company, USA, or under the trade names Epikote® 828 or Epikote®
862 from Hexion Specialty Chemicals Inc., USA.
[0115] The term "aqueous emulsion" designates in the present document to emulsions having
water as the main continuous (carrier) phase. Preferably, the term "aqueous" designates
a 100% water carrier.
[0116] The at least one epoxy resin is typically present in the aqueous emulsion in an unmodified
form. In particular, it is not modified for better emulsifiability, for example with
a fatty acid.
[0117] The aqueous emulsion of at least one epoxy resin optionally contains at least one
reactive diluent. Suitable reactive diluents include especially monofunctional epoxides,
preferably glycidylated fatty alcohols.
[0118] Preferably the emulsion also contains at least one external emulsifier, especially
a nonionic emulsifier, for example a fatty alcohol ethoxylate. The at least one external
emulsifier may be present in the aqueous emulsion in ana mount of not more than 10
wt.-%, preferably not more than 5 wt.-%, based on the total weight of the emulsion.
[0119] The emulsion preferably has a solids content of 60 to 90% by weight, especially of
70 to 90% by weight, preferably of 75 to 85%. Correspondingly, the aqueous emulsion
of at least one epoxy resin may contain 10 - 40 % wt.-%, 10 - 30 wt.-%, preferably
15 - 25 wt.-%, of water, based on the total weight of the emulsion.
[0120] Preferably, the mean particle size (droplet diameter) of the at least one epoxy resin
in the aqueous emulsion is in the range of 0.05 - 10 µm, in particular 0.1 - 7 µm,
more preferably 0.2 - 5 µm.
[0121] The emulsion preferably has a narrow particle size distribution, wherein the size
ratio of the largest to the smallest particle has a value in the range of ≤ 25, preferably
≤ 20. Especially the particle size distribution is such that 90% of the particles
in the emulsion are smaller than 6 µm, preferably smaller than 4 µm, particularly
preferably smaller than 3 µm. As a result of the small mean particle size and the
narrow particle size distribution, the emulsion has a low tendency toward creaming
or hardening and thus has a long storage life.
[0122] The preparation of the aqueous emulsion preferably takes place in a continuous process,
especially using a stator-rotor mixer. Such a method is known to the person skilled
in the art.
[0123] The first component
A of the two-component composition further contains, in addition to the at least one
silane-functional polymer, at least one hardener or accelerator for epoxy resins.
These are in particular polyamines, for example isophorone diamine, m-xylylenediamine,
polyether amines such as those that are commercially available under the trade names
of Jeffamine® (from Huntsman International LLC, USA), polyethylenimines, polyamidoamines,
polyalkyleneamines such as diethylenetriamine (DETA), triethylenetetramine (TETA),
tetraethylenepentamine (TEPA) or pentaethylenhexamine (PEHA), amine-epoxy adducts,
pentamethyl diethylenetri-amine, N,N-dimethyl-N'-(dimethylaminopropyl)-1,3-propanediamine,
bis(2-dimethylaminoethyl) ether, bis-(dimethylaminoethyl)-piperazine, N,N'-dimethylpiperazine;
Mannich bases, for example dimethylaminomethylphenol, 2,4,6-tris(dimethylaminomethyl)phenol
and 2,4,6-tris((3-(dimethylamino)propyl)-aminomethyl)phenol; polymercaptans, for example
liquid mercaptan-terminated poly-sulfide polymers, such as those commercially available
under the trade name of Thiokol® (from SPI Supplies, USA or from Toray Fine Chemicals,
Japan), and under the trade name of Thioplast® (from Akzo Nobel NV, Netherlands);
mercaptan-endcapped polyoxyalkylene derivatives, such as those available under the
trade names of Capharden® (from Cognis GmbH, Germany), polyesters of thiocarboxylic
acids such as pentaerythritol tetramercaptoacetate, trimethylolpropane trimercaptoacetate
and glycol dimercaptoacetate, and aromatic polymercaptans such as 2,4,6-trimercapto-1,3,5-triazine;
or imidazoles, for example imidazole, 1-methylimidazole, 1-ethylimidazole, 1-vinylimidazole,
2-methylimidazole, 2-ethylimidazole, 2-isopropylimidazold, 2-heptadecylimidazole,
2-phenylimidazole, 2-ethyl-4-methylimidazole, 1-benzyl-2-methylimidazole and 2,4-diamino-6-(2'-methylimidazolyl-(1'))-ethyl-s-triazine;
and mixtures of the aforementioned hardeners or accelerators for epoxy resins.
[0124] In addition to the at least one hardener or accelerator mentioned, additional accelerators,
especially phosphites, or acids, especially phosphoric acid and carboxylic acids,
may be contained in the first component
A.
[0125] Preferable as the at least one hardener or accelerator for epoxy resins are tertiary
polyamines, especially pentamethyl-diethylene triamine, N,N-dimethyl-N'-(dimethylaminopropyl)-1,3-propanediamine,bis(2-dimethylaminoethyl)ether,
bis-(dimethylaminoethyl)-piperazine, N,N'-dimethylpiperazine; Mannich bases, especially
dimethylaminomethylphenol, 2,4,6-tris(dimethylaminomethyl)phenol and 2,4,6-tris((3-(dimethylamino)propyl)aminomethyl)phenol;
as well as imidazoles, especially 1-methylimidazole, 1-ethylimidazole, 1-vinylimidazole,
2-methylimidazole, 2-ethylimidazole, 2-isopropylimidazole, 2-heptadecylimidazole,
2-ethyl-4-methylimidazole and 1-benzyl-2-methylimidazole. Particularly preferred are
the Mannich bases mentioned.
[0126] According to one or more embodiments, the proportion of the at least one hardener
or accelerator for epoxy resins is 0.5 - 25.0 wt.-%, preferably 1.0 - 20.0 wt.-%,
based on the total weight of the first component
A.
[0127] According to one or more further embodiments, the first component
A comprises:
- The at least one silane-terminated polymer,
- The at least one hardener or accelerator for epoxy resins,
- The at least one silane crosslinker, and
- At least one first filler, preferably at least one first inert mineral filler.
[0128] The second component
B comprises:
- At least one aqueous emulsion of at least one epoxy resin, and
- At least one second filler, preferably at least one second inert mineral filler.
[0129] In the embodiments, in which the second component
B of the two-component moisture curing composition comprises at least one aqueous emulsion
of at least one epoxy resin, it may be preferable that:
- The proportion of the at least one silane crosslinker is 1.0 - 15.0 wt.-%, preferably
1.5 - 10.0 wt.-%, based on the total weight of the first component A and/or
- The first component A comprises at least two different silane crosslinkers and/or
- The proportion of the at least one first filler, preferably at least one first inert
mineral filler is 1.0 - 25.0 wt.-%, preferably 1.5 - 20.0 wt.-%, based on the total
weight of the first component A and/or
- The first component A comprises at least two different fillers, preferably at least two different inert
mineral fillers and/or
- The weight ratio of the component A to component B is from 0.5:1 to 5:1, preferably from 1:1 to 3:1 and/or
- The proportion of the at least one second filler, preferably at least one second inert
mineral filler is 1.0 - 65.0 wt.-%, preferably 10.0 - 55.0 wt.-%, based on the total
weight of the second component B and/or
- The second component B comprises at least two different fillers, preferably at least two different inert
mineral fillers.
[0130] It is further preferred that the functional layer of the waterproofing membrane of
the present invention is non-tacky at normal room temperature. Whether a surface of
a specimen is tacky or not can be determined by pressing the surface with the thumb
at a pressure of about 5 kg for 1 second and then trying to lift the specimen by raising
the hand. In case the thumb does not remain adhered to the surface and the specimen
cannot be raised up, the surface is considered to be non-tacky. In the context of
the waterproofing membrane of the present invention, the "specimen" used in the tackiness
test refers to a waterproofing membrane having a width of 10 cm and length of 20 cm.
[0131] The thickness of the functional layer is not particularly restricted and it may not
be constant in the longitudinal and/or transverse direction of the sealing device.
Preferably, the functional layer has a maximum thickness, determined by using the
measurement method as defined in DIN EN 1849-2 standard, of 10 - 1000 µm, preferably
15 - 500 µm, even more preferably 25 - 250 µm, most preferably 50 - 200 µm. Furthermore,
it may be advantageous that the functional layer has an average thickness, calculated
as arithmetic average of the maximum and minimum thicknesses, determined by using
the measurement method as defined in DIN EN 1849-2 standard, of 10 - 1000 µm, preferably
15 - 500 µm, even more preferably 25 - 250 µm, most preferably 50 - 200 µm.
[0132] The detailed composition of the barrier layer is not particularly restricted but
should be as waterproof as possible and not to decompose or be mechanically damaged
even under prolonged influence of water or moisture. Preferably, the barrier layer
comprises at least one thermoplastic polymer, which is present in the barrier layer
in an amount of at least 70 wt.-%, more at least 75 wt.-%, even more preferably at
least 80 wt.-%, most preferably at least 85 wt.-%, based on the total weight of the
barrier layer.
[0133] Suitable thermoplastic polymers to be used in the barrier layer include, for example,
ethylene - vinyl acetate copolymer (EVA), ethylene - acrylic ester copolymers, ethylene
- α-olefin co-polymers, ethylene - propylene co-polymers, polypropylene (PP), polyethylene
(PE), polyethylene terephthalate (PET), polystyrene (PS), polyamides (PA), chlorosulfonated
polyethylene (CSPE), ethylene propylene diene rubber (EPDM), and polyisobutylene (PIB).
It may be preferable that the at least one thermoplastic polymer is selected from
the group consisting of low-density polyethylene, linear low-density polyethylene,
high-density polyethylene, ethylene - vinyl acetate copolymer (EVA), ethylene - acrylic
ester copolymers, ethylene - α-olefin co-polymers, and ethylene - propylene co-polymers.
[0134] The thickness of the barrier layer is not particularly restricted. The barrier layer
may have a thickness, determined by using the measurement method as defined in DIN
EN 1849-2 standard, of 0.1 - 5.0 mm, preferably 0.25 - 3.5 mm, more preferably 0.25
- 2.5 mm, most preferably 0.3 - 2.0 mm
[0135] According to one or more embodiments, the waterproofing membrane further comprises
a connecting layer having first and second major surfaces and arranged between the
barrier layer and the functional layer.
[0136] It may be preferred that at least a part of the first major surface of the connecting
layer is directly connected to at least a part of the second major surface of the
barrier layer and/or that at least a part of the second major surface of the connecting
layer is directly connected to at a least part of the first major surface of the functional
layer.
[0137] It may also be preferable that substantially the entire area of the first major surface
of the connecting layer is directly connected to the second major surface of the barrier
layer and/or that substantially the entire area of the second major surface of the
connecting layer is directly connected to the first major surface of the functional
layer. It may, for example, be preferable that at least 90%, more preferably at least
95%, of the first major surface of the connecting layer is directly connected to the
second major surface of the barrier layer and/or that at least 90%, more preferably
at least 95%, of the second major surface of the connecting layer is directly connected
to the first major surface of the functional layer. Furthermore, it may also be preferable
that the functional layer and the connecting layer have substantially the same width
and length.
[0138] According to one or more embodiments, the connecting layer is composed of an at least
partially cured film-forming curable composition comprising at least one epoxy resin
and at least one hardener or accelerator for epoxy resins. According to one or more
embodiments, the connecting layer is composed of a continuous layer of the at least
partially cured film-forming curable composition.
[0139] The at least one epoxy resin contained in the film-forming curable composition is
preferably a solid epoxy resin, more preferably a solid epoxy resin of the formula
(III), wherein the substituents R
1 and R
2 independently is either H or CH
3 and the subscript r has a value of ≥ 1, in particular ≥ 1.5, more preferably in the
range from 2 to 12.
[0140] Suitable hardeners and accelerators to be used in the curable composition include
the ones discussed above related to the two-component moisture curing composition.
[0141] The curable composition may further comprise at least one silane chain extender or
silane coupling agent. Suitable silane chain extenders and coupling agents include,
for example vinyl trialkoxysilanes, 3-aminopropyl-dialkoxyalkylsilanes, 3-aminopropyl-trialkoxysilanes,
N-(2-aminoethyl)-3-aminopropyl-dialkoxyalkylsilanes, N-(2-aminoethyl)-3-aminopropyl-trialkoxysilanes,
3-glycidoxypropyltrialkoxysilanes and 3-mercaptopropyl-trialkoxysilanes. Particularly
suitable silane chain extenders and silane coupling agents include vinyl trimethoxysilane,
vinyl triethoxysilane, 3-aminopropyl-trimethoxysilane, 3-aminopropyl-triethoxysilane,
N-(2-aminoethyl)-3-aminopropyl-dimethoxymethylsilane, N-(2-aminoethyl)-3-aminopropyl-trimethoxysilane,
N-(2-aminoethyl)-3-aminopropyl-triethoxysilane, 3-glycidoxypropyltrimethoxysilane,
3-glycidoxypropyltriethoxysilane, 3-mercaptopropyl-trimethoxysilane and 3-mercaptopropyl-triethoxysilane.
[0142] The curable composition may further comprise at least one organic solvent. The term
"organic solvent" designates in the present document non- aqueous solvents and combinations
of non-aqueous solvents, and, in particular, to solvents comprising organic compounds.
Preferably, the at least one organic solvent is selected from the group consisting
of toluene, xylene, hexane, octane, and mixtures thereof.
[0143] According to one or more embodiments, the film-forming curable composition comprises
at least 10 wt.-%, preferably at least 20 wt.-%, more preferably at least 35 wt.-%
of at least one solid epoxy resin, based on the total weight of the curable composition.
It may be preferable that the film-forming curable composition comprises 15 - 75 wt.-%,
more preferably 25 - 65 wt.-% of at least one solid epoxy resin, based on the total
weight of the film-forming curable composition.
[0144] According to one or more embodiments, the film-forming curable composition comprises:
- 0.1 - 10 wt.-%, preferably 0.5 - 7.5 wt.-% of the at least one hardener or accelerator
for epoxy resins, based on the total weight of the film-forming curable composition
and/or
- 0.1 - 10 wt.-%, preferably 0.5 - 7.5 wt.-% of the at least one silane chain extender
or silane coupling agent, based on the total weight of the film-forming curable composition
and/or
- 5.0 - 50.0 wt.-%, preferably 15.0 - 45.0 wt.-% of the at least one organic solvent,
based on the total weight of the film-forming curable composition
[0145] According to one or more further embodiments, the connecting layer is a thermoplastic
polymer layer comprising at least 80 wt.-% of at least one thermoplastic polymer.
[0146] The at least one thermoplastic polymer is preferably ethyl vinyl acetate copolymer,
more preferably ethyl vinyl acetate copolymer having a content of a structural unit
derived from vinyl acetate (hereinafter referred to as "vinyl acetate unit") of at
least 30 wt.-%, more preferably at least 35 wt.-%, most preferably at least 40 wt.-%.
[0147] According to one or more further embodiments, the connecting layer is composed of
a pressure sensitive adhesive (PSA) composition or pressure sensitive hot-melt adhesive
(HM-PSA) composition.
[0148] Suitable pressure sensitive adhesives include compositions based on acrylic polymers,
styrene block copolymers, amorphous poly-α-olefins (APAO), vinyl ether polymers, elastomers
such as, for example, butyl rubber, ethylene vinyl acetate, natural rubber, nitrile
rubber, silicone rubber, and ethylene-propylene-diene rubber. In addition to the above
mentioned polymers, suitable pressure sensitive adhesive compositions typically comprise
one or more additional constituents including, for example, tackifying resins, waxes,
and plasticizers as wells as one or more additives such as, for example, UV-light
absorption agents, UV- and heat stabilizers, optical brighteners, pigments, dyes,
and desiccants.
[0149] According to one embodiment, the adhesive is a styrene block copolymer-based pressure
sensitive adhesive or styrene block copolymer-based pressure sensitive hot-melt adhesive
comprising at least one styrene block copolymer.
[0150] Suitable styrene block copolymers include block copolymers of the SXS type, in each
of which S denotes a non-elastomer styrene (or polystyrene) block and X denotes an
elastomeric α-olefin block, which may be polybutadiene, polyisoprene, polyisoprene-polybutadiene,
completely or partially hydrogenated polyisoprene (poly ethylene-propylene), completely
or partially hydrogenated polybutadiene (poly ethylene-butylene). The elastomeric
α-olefin block preferably has a glass transition temperature in the range from -55°C
to - 35°C. The elastomeric α-olefin block may also be a chemically modified α-olefin
block. Particularly suitable chemically modified α-olefin blocks include, for example,
maleic acid-grafted α-olefin blocks and particularly maleic acid-grafted ethylene-butylene
blocks.
[0151] Preferably, the at least one styrene block copolymer is selected from the group consisting
of SBS, SIS, SIBS, SEBS, and SEPS block copolymers. These can have a linear, radial,
diblock, triblock or star structure, linear structure being preferred. Suitable styrene
block copolymers of the SXS type include block copolymers based on saturated or unsaturated
middle blocks X. Hydrogenated styrene block copolymers are also suitable. The at least
one styrene block copolymer may be present in the adhesive in an amount of 5 - 60
wt.-%, more preferably 10 - 55 wt.-%, most preferably 20 - 50 wt.-%, based on the
total weight of the adhesive.
[0152] The styrene block copolymer-based pressure sensitive adhesive preferably comprises
at least one tackifying resin. The term "tackifying resin" designates in the present
document resins that in general enhance the adhesion and/or tackiness of an adhesive
composition. The term "tackiness" designates in the present document the property
of a substance of being sticky or adhesive by simple contact. The tackiness can be
measured, for example, as a loop tack. Preferred tackifying resins are tackifying
at a temperature of 25°C.
[0153] Suitable tackifying resins include synthetic resins, natural resins, and chemically
modified natural resins. The at least one tackifying resin may be present in the styrene
block copolymer based pressure sensitive adhesive in an amount of 5 - 60 wt.-%, preferably
10 - 55 wt.-%, most preferably 20 - 50 wt.-%, based on the total weight of the adhesive.
[0154] Examples of suitable natural resins and chemically modified natural resins include
rosins, rosin esters, phenolic modified rosin esters, and terpene resins. The term
"rosin" is to be understood to include gum rosin, wood rosin, tall oil rosin, distilled
rosin, and modified rosins, for example dimerized, hydrogenated, maleated and/or polymerized
versions of any of these rosins.
[0155] Suitable terpene resins include copolymers and terpolymers of natural terpenes, such
as styrene/terpene and alpha methyl styrene/terpene resins; polyterpene resins obtainable
from the polymerization of terpene hydrocarbons, such as the bicyclic monoterpene
known as pinene, in the presence of Friedel-Crafts catalysts at moderately low temperatures;
hydrogenated polyterpene resins; and phenolic modified terpene resins including hydrogenated
derivatives thereof.
[0156] The term "synthetic resin" designates in the present document compounds obtained
from the controlled chemical reactions such as polyaddition or polycondensation between
well-defined reactants that do not themselves have the characteristic of resins. Monomers
that may be polymerized to synthesize the synthetic resins may include aliphatic monomer,
cycloaliphatic monomer, aromatic monomer, or mixtures thereof. Aliphatic monomers
can include C
4, C
5, and C
6 paraffins, olefins, and conjugated diolefins. Examples of aliphatic monomers or cycloaliphatic
monomers include butadiene, isobutylene, 1,3-pentadiene, 1,4-pentadiene, cyclopentane,
1-pentene, 2-pentene, 2- methyl-1-pentene, 2-methyl-2-butene, 2-methyl-2-pentene,
isoprene, cyclohexane, 1- 3-hexadiene, 1-4-hexadiene, cyclopentadiene, and dicyclopentadiene.
Aromatic monomers can include C
8, C
9, and C
10 aromatic monomer, such as styrene, indene, derivatives of styrene, derivatives of
indene, coumarone and combinations thereof.
[0157] In particular, suitable synthetic resins include synthetic hydrocarbon resins made
by polymerizing mixtures of unsaturated monomers that are obtained as by-products
of cracking of natural gas liquids, gas oil, or petroleum naphthas. Synthetic hydrocarbon
resins obtained from petroleum based feedstocks are referred in the present document
as "petroleum hydrocarbon resins". These include also pure monomer aromatic resins,
which are made by polymerizing aromatic monomer feedstocks that have been purified
to eliminate color causing contaminants and to precisely control the composition of
the product. Petroleum hydrocarbon resins typically have a relatively low average
molecular weight (M
n), such in the range of 250 - 5'000 g/mol and a glass transition temperature of above
0°C, preferably equal to or higher than 15°C, more preferably equal to or higher than
30°C.
[0158] It may be preferable that the at least one tackifying resin is selected from the
group consisting of C5 aliphatic petroleum hydrocarbon resins, mixed C5/C9 aliphatic/aromatic
petroleum hydrocarbon resins, aromatic modified C5 aliphatic petroleum hydrocarbon
resins, cycloaliphatic petroleum hydrocarbon resins, mixed C5 aliphatic/cycloaliphatic
petroleum hydrocarbon resins, mixed C9 aromatic/cycloaliphatic petroleum hydrocarbon
resins, mixed C5 aliphatic/cycloaliphatic/C9 aromatic petroleum hydrocarbon resins,
aromatic modified cycloaliphatic petroleum hydrocarbon resins, and C9 aromatic petroleum
hydrocarbon resins as well hydrogenated versions of the aforementioned resins. The
notations "C5" and "C9" indicate that the monomers from which the resins are made
are predominantly hydrocarbons having 4-6 and 8-10 carbon atoms, respectively. The
term "hydrogenated" includes fully, substantially and at least partially hydrogenated
resins. Partially hydrogenated resins may have a hydrogenation level, for example,
of 50%, 70%, or 90%.
[0159] Preferred thickness of the connecting layer depends on the composition of the connecting
layer and it may not be constant in the longitudinal and/or transverse direction of
the waterproofing membrane.
[0160] In case the connecting layer is composed of a cured material of a curable solvent-based
epoxy resin composition, it may be preferable that it has a maximum thickness of,
determined by using the measurement method as defined in DIN EN 1849-2 standard, of
10 - 1000 µm, preferably 15 - 500 µm, even more preferably 25 - 350 µm, most preferably
50 - 250 µm. Furthermore, it may be advantageous that the connecting layer has an
average thickness, calculated as arithmetic average of the maximum and minimum thicknesses,
determined by using the measurement method as defined in DIN EN 1849-2 standard, of
10 - 1000 µm, preferably 15 - 500 µm, even more preferably 25 - 350 µm, most preferably
50 - 250 µm.
[0161] In case the connecting layer is a thermoplastic polymer layer, it may be preferable
that it has a maximum thickness, determined by using the measurement method as defined
in DIN EN 1849-2 standard, of 10 - 1000 µm, preferably 15 - 500 µm, even more preferably
25 - 350 µm, most preferably 50 - 250 µm. Furthermore, it may be advantageous that
the connecting layer has an average thickness, calculated as arithmetic average of
the maximum and minimum thicknesses, determined by using the measurement method as
defined in DIN EN 1849-2 standard, of 10 - 1000 µm, preferably 15 - 500 µm, even more
preferably 25 - 350 µm, most preferably 50 - 250 µm.
[0162] In case the connecting layer is composed of a pressure sensitive adhesive composition,
it may be preferable that it has a maximum thickness, determined by using the measurement
method as defined in DIN EN 1849-2 standard, of 50 - 1500 µm, preferably 100 - 1000
µm, even more preferably 150 - 1000 µm, most preferably 250 - 750 µm. Furthermore,
it may be advantageous that the connecting layer has an average thickness, calculated
as arithmetic average of the maximum and minimum thicknesses, determined by using
the measurement method as defined in DIN EN 1849-2 standard, of 50 - 1500 µm, preferably
100 - 1000 µm, even more preferably 150 - 1000 µm, most preferably 250 - 750 µm.
[0163] The second major surface of the barrier layer may have been subjected to a pre-treatment
step in order to improve the bonding of the barrier layer to the functional layer
or to the connecting layer, if used. Suitable pre-treatment steps include, for example,
air-pressure plasma treatment, wet chemical functional grafting, and oxo-fluorination.
[0164] Air pressure plasma-treatment can be used to clean the surface of the barrier layer
from organic pollution and/or to increase the free surface energy. The air pressure
plasma-treatment can be conducted using conventional techniques known to a person
skilled in the art.
[0165] In wet chemical functional grafting, a grafting compound, such as a silane compound
is grafted upon the molecules of the material of the barrier layer to increase the
free surface energy and/or to improve bonding with the functional layer. In case a
silane grafting solution is used, silicon is covalently bonded to the material of
the membrane and it can act as a link between the barrier layer and the functional
layer containing silane-terminated polymers. The silane grafting solution used in
the functional grafting is typically a solvent-based solution of at least one organic
silane, such as organoalkoxysilane or aminoalkyl organoalkoxysilane, and at least
one free-radical initiator. The free-radical iniator can be heat activated, such as
peroxide initiator, or a UV-radiation activated, such as a benzophenone.
[0166] In an oxo-fluorination treatment, the surface of the barrier layer is first subjected
to a fluorination treatment to provide a surface fluorinated barrier layer, which
is subsequently treated with an oxidant fluid to oxidize the fluorinated surface.
The fluorination and oxidation steps may also be conducted in simultaneously in one
single treatment step. The stability of the oxidized surface fluorinated barrier layer
may further be improved by treating the surface with an antioxidant, such as nitrogen
dioxide, nitric oxide, dinitrogen dioxide, dinitrogen trioxide, dinitrogen tetroxide,
sulfur dioxide, or sulfur trioxide.
[0167] The waterproofing membrane may further comprise a reinforcement layer in order to
improve the dimensional stability of the membrane. The reinforcement layer is preferably
at least partially embedded into the barrier layer. Suitable reinforcement layers
include, for example, reinforcing scrims and reinforcing fiber materials.
[0168] Any kind of reinforcing scrims commonly used for improving the dimensional stability
of thermoplastic waterproofing membranes can be used. Typically such reinforcing scrims
comprise a mesh of interwoven strands, which comprises or are composed of plastic
or metal material. Suitable reinforcing scrims have a tensile strength sufficient
to resist tearing when exposed to typical tensile loads experienced by waterproofing
membranes from various directions. Particularly suitable materials for the reinforcing
scrim layer include, for example, polypropylene, polyethylene terephthalate (PET),
and polyester.
[0169] The term "fiber material" designates in the present document materials composed of
fibers. The fibers can comprise or consist of organic or synthetic material. These
include, in particular, cellulose fibers, cotton fibers, protein fibers, synthetic
organic fibers, and synthetic inorganic fibers. Suitable synthetic fibers include
fibers made of polyester, a homopolymer or copolymer of ethylene and/or propylene,
viscose, nylon, and glass. The fibers can be short fibers or long fibers, spun, woven
or unwoven fibers or filaments. The fibers can moreover be aligned or drawn fibers.
Moreover, it may be advantageous to use different fibers, both in terms of geometry
and composition, together. The reinforcing fiber material can be in the form of a
fiber mat, a nonwoven fabric, or a fibrous tissue. Particularly suitable materials
for the reinforcing fiber material include glass fibers, polyester fibers, and nylon
fibers.
[0170] According to one or more embodiments, the waterproofing membrane comprises a reinforcement
layer, which is fully embedded into the barrier layer. By the expression "fully embedded"
is meant that the reinforcement layer is substantially fully covered by the matrix
of the barrier layer.
[0171] Another subject of the present invention is a method for producing a waterproofing
membrane of the present invention, the method comprising steps of:
- i) Providing a moisture curing composition comprising the constituents as defined
above,
- ii) Applying the moisture curing composition in a fluid state to at least a part of
the second major surface of the barrier layer or to at least a part of the second
major surface of the connecting layer, if present, to form a layer of the moisture
curing composition,
- iii) Allowing the applied moisture curing composition to cure to form a layer of at
least partially cured moisture curing composition.
[0172] In case the moisture curing composition is a multiple-component composition, step
i) is conducted by mixing the components A and B of the multiple-component composition
with each other.
[0173] The moisture curing composition may be applied to the surface of the barrier layer
or connecting layer, if present, by using any conventional means such as by die coating,
extrusion coating, roller coating, or by spray lamination techniques.
[0174] According to one or more embodiments, the moisture curing composition is applied
in fluid state to at least a part of the second surface of a connecting layer and
the method comprises a further step of:
i') Providing a composition of the connecting layer with the constituents as defined
above and applying the composition to at least a part of the second major surface
of the barrier layer to form a layer of the composition.
[0175] The barrier layer can be produced by using any conventional technology suitable for
producing thermoplastic membranes. The barrier layer can be produced, for example,
by using conventional extruding, calendering, compressing, or casting techniques.
It goes without saying that the step i') precedes the step ii).
[0176] The moisture curing composition may be applied only on a part or on substantially
the entire area of the second major surface of the barrier layer or of the connecting
layer. It may also be preferable that the moisture curing composition is applied over
substantially the entire area of the second major surface of the barrier layer or
of the connecting layer. It may, for example, be preferable that the moisture curing
composition is applied over at least 80%, more preferably at least 90%, most preferably
at least 95%, of the area of the second major surface of the barrier layer or of the
connecting layer.
[0177] Another subject of the present invention is a method for waterproofing a substrate
comprising steps of:
i") Applying a waterproofing membrane of the present invention to a surface of the
substrate such that the first major surface of the barrier layer is directed against
the surface of the substrate,
ii") Casting a fresh cementitious composition on the second major surface of the functional
layer,
iii") Allowing the fresh cementitious composition to harden.
[0178] The term "cementitious composition" designates concrete, shotcrete, grout, mortar,
paste or a combination thereof. The terms "paste", "mortar", "concrete", "shotcrete",
and "grout" are well-known terms in the State-of-the-Art. Pastes are mixtures comprising
a hydratable cement binder, usually Portland cement, masonry cement, or mortar cement.
Mortars are pastes additionally including fine aggregate, for example sand. Concrete
is a mortar additionally including coarse aggregate, for example crushed gravel or
stone. Shotcrete is concrete (or sometimes mortar) conveyed through a hose and pneumatically
projected at high velocity onto a surface. Grout is a particularly flowable form of
concrete used to fill gaps.
[0179] Cementitious compositions can be formed by mixing required amounts of certain components,
for example, a hydratable cement, water, and fine and/or coarse aggregate, to produce
the particular cementitious composition. The term "fresh cementitious composition"
or "liquid cementitious composition" designate cementitious compositions before hardening,
particularly before setting.
[0180] The casted cementitious composition after hardening can be part of a structure, in
particular, an above-ground or underground structure, for example a building, garage,
tunnel, landfill, water retention, pond, dike or an element for use in pre-fabricated
constructions.
[0181] Another subject of the present invention is a waterproofed construction comprising
a layer of concrete and a waterproofing membrane according to the present invention
arranged between a surface of a substrate and the layer of concrete such that the
first surface of the barrier layer is directed against the surface of the substrate
and the second surface of the functional layer is bonded to the layer of concrete.
[0182] Still another subject of the present invention is the use of the waterproofing membrane
of the present invention for sealing of under and above ground structures against
water penetration.
Detailed description of the Drawings
[0183] Fig. 1 shows a cross-section of a waterproofing membrane (1) comprising a barrier
layer (2) having first and second opposed major surfaces and a functional layer (3)
having first and second opposed major surfaces. In this embodiment, substantially
the entire first major surface of the functional layer (3) is directly connected to
the second major surface of the barrier layer (2).
[0184] Fig. 2 shows cross-section of a waterproofing membrane (1) comprising a barrier layer
(2), a functional layer (3), and a connecting layer (4) arranged between the barrier
layer (2) and the functional layer (3). In this embodiment, substantially the entire
first major surface of the connecting layer (4) is directly connected to the second
major surface of the barrier layer (2) and substantially the entire second major surface
of the connecting layer (4) is directly connected to the first major surface of the
functional layer (2).
[0185] Fig. 3 shows a cross-section of a waterproofed construction comprising a substrate
(5) and a layer of concrete (6) and a waterproofing membrane (1) arranged between
the outer surface of the substrate (5) and the layer of concrete (6) such that the
first surface of the barrier layer (2) is directed against the outer surface of the
substrate and the second surface of the functional layer is bonded to the layer of
concrete (6).
Examples
[0186] The followings compounds and products were used in the examples:
Table 1
Geniosil® STP-E15 |
Silane-terminated polymer |
Wacker Chemie AG, Germany |
Silquest® A-171 |
Vinyl silane |
Momentive Performance Materials Inc., USA |
Silquest® A-1110 |
3-Aminopropyl-trimethoxysilane |
Momentive Performance Materials Inc., USA |
Jeffamine® D-230 |
Amine hardener for epoxy resins |
Huntsmann International LLC |
Omyacarb® 5GU |
Calcium carbonate filler |
Omya AG, Switzerland |
Araldite® GY 250 |
Liquid epoxy resin |
Huntsmann International LLC |
DBTDL in DIDP |
Dibutyltin dilaurate dissolved in diisodecyl phthalate (4 wt.-%) |
Sigma Aldrich, Switzerland |
Aerosil® R200 |
Fumed silica filler |
Evonik Industries |
Araldite®GZ 7071 X75 |
Medium molecular weight liquid epoxy resin in xylene |
Huntsmann International LLC |
Jeffamine® D-400 |
Amine hardener for epoxy resins |
Huntsmann International LLC |
Dynasylan® AMEO |
3-Aminopropyltriethoxysilane |
Evonik Industries |
Preparation of the sample waterproofing membranes
[0187] The sample waterproofing membranes were prepared by applying the composition of a
functional layer or the composition of the connecting layer, if applicable, to one
of the outer surfaces of a thermoplastic barrier layer.
[0188] Two different thermoplastic waterproofing products, WT-1210-06-HF and Combiflex SG
(both from Sika Schweiz AG), were used as the thermoplastic barrier layer. The first
one is an ethylene vinyl acetate copolymer (EVA) based waterproofing membrane and
the second one is a waterproofing tape based on ethylene-propylene copolymer. Surfaces
of both types of barrier layers have been subjected to oxo-fluorination treatment.
[0189] The compositions of the functional layer were applied on the surface of the barrier
layer or connecting layer using a K-control coater (from Erichsen) and constant coating
speed of 1 m/min. The thickness of the applied layer was controlled by wire bars.
After the application, the composition of the functional layer was allowed to cure
at normal room temperature (23°C, relative humidity of 50%).
[0190] In examples Ref-1, Ex-1 - Ex-8, and Ex-10, an epoxy resin-based connecting layer
was applied on the barrier layer before application of the composition of the functional
layer. The epoxy resin-based layer was applied with a coating thickness of 100 µm
using a K-control coater (from Erichsen) and constant coating speed of 1 m/min. After
the application, the connecting layer was allowed to cure at normal room temperature
(23°C, relative humidity of 50%).
[0191] The build-up of the sample membranes is shown in Table 3.
Preparation of the moisture curing composition, functional layer
[0192] The moisture curing compositions were produced by adding the ingredients of the components
A and B as shown in Table 2 to a speed mixer and mixing the contents using a mixing
speed of 1000 rounds per minute until a homogeneous mixture was obtained. The moisture
curing composition of example FL-1 is a one-component composition (only component
A) whereas the compositions FL-2 to FL-8 are two-component moisture curing compositions.
[0193] The "STP-S" silane-terminated polymer contained in compositions FL2- to FL-8 was
prepared as follows:
1000 g polyol (Acclaim® 12200, low monol polyoxypropylene diol from Covestro; OH-number
11.0 mg KOH/g; water content ca. 0.02 wt.-%), 35.2 g isophorone diisocyanate (Vestanat®
IPDI from Evonik Industries), 122.5 g diisodecyl phthalate, and 0.12 g dibutyltin
dilaurate were heated under exclusion of moisture and with continuous stirring to
a temperature of 90°C and kept at this temperature until the content of free isocyanate
groups, determined by titrimetry, reached a value of 0.39 wt.-%. Subsequently, 36.9
g N-(3-trimethoxysilylpropyl)aminosuccinic acid diethyl ester were added and the stirring
was continued until no free isocyanate groups were detected by FT-IR spectroscopy.
The produced silane-terminated polymer was cooled to room temperature and stored under
the exclusion of moisture.
Preparation of the film-forming curable composition, connecting layer
[0194] The film-forming curable composition was produced adding the ingredients of the composition
as presented below to a speed mixer and mixing the contents using a mixing speed of
1000 rounds per minute until a homogeneous mixture was obtained.
[0195] The film-forming curable composition contained:
53.9 wt.-% of Araldite GZ 7071 X75 (amount without solvent)
4.88 wt.-% of Jeffamine D-400,
4.69 wt.-% of Dynasylan AMEO, and
36.52 wt.-% of xylene
Peel resistance measurement
[0196] The concrete adhesion strength of the exemplary waterproofing membranes was tested
by measuring the 90° peel resistance from a cured concrete surface. For the determination
of the peel resistance, concrete specimen having a sample membrane adhered on its
surface were first prepared as follows.
[0197] A sample membrane having dimensions of 15 cm x 15 cm was prepared with respective
barrier, functional layer, and connecting layer, if applicable. One edge of the sample
membrane on the side of the functional layer was covered with an adhesive tape to
prevent the adhesion to the hardened concrete. The membrane was dried for at least
one week and placed into a framework having approximately the same width and length
as the membrane with the functional layer facing upwards and the barrier layer against
the bottom of the framework.
[0198] A batch of fresh concrete formulation having a water-cement ratio of 0.44 was then
prepared by mixing the following ingredients:
32.1 wt.-% of cement (CEM I 42.5 N)
46.3 of sand having particles size range of 0 - 1 mm,
14.3 wt.-% of water,
7.1 wt.-% of limestone filler Nekafill®-15 (from KFN), and
2.2 wt.-% of Viscocrete® 3082 (from Sika Schweiz AG).
[0199] The formworks containing the sample membranes were subsequently filled with the fresh
concrete formulation such that the membrane was bonded with the concrete on the side
of the functional layer. The casted concrete was allowed to cure for one day covered
with a polyethylene foil. The film was then removed and the concrete block was stripped
from the framework and stored in wet room (23°C, 95% relative humidity) for 28 days
to complete the hydration of the cement. The membrane was then cut into three stripes
with a gap of approximately 1 cm between the stripes for measurement of peel resistances.
[0200] The measurement of peel resistances of the sample membranes from the concrete block
was conducted in accordance with the procedure laid out in the standard DIN EN 1372:2015-06.
A Zwick Roell AllroundLine Z010 material testing apparatus equipped with a Zwick Roell
90°-peeling device (type number 316237) was used for conducting the peel resistance
measurements.
[0201] In the peel resistance measurement, the membrane was peeled off from the surface
of the concrete block at a peeling angle of 90° and at a constant cross beam speed
of 100 mm/min at normal room temperature and humidity (23°C, 50% relative humidity).
The values for peel resistance were calculated as average peel force per width of
the sample membrane [N/ 50 mm] during peeling excluding the first and last quarter
of the total peeling length from the calculation. The average peel resistances shown
in Table 2 and 3 are calculated based on measurements obtained with three strips of
the same sample membrane.
Table 2
Composition [pbw] |
FL-1 |
FL-2 |
FL-3 |
FL-4 |
FL-5 |
FL-6 |
FL-7 |
FL-8 |
Componbent A |
|
|
|
|
|
|
|
|
Geniosil STP-E15 |
94.00 |
- |
- |
- |
- |
- |
- |
- |
STP-S |
- |
80.00 |
68.00 |
80.00 |
80.00 |
80.00 |
80.00 |
80.00 |
Silquest A-171 |
- |
5.00 |
4.25 |
5.00 |
5.00 |
5.00 |
5.00 |
5.00 |
Silquest A-1110 |
6.00 |
2.00 |
1.70 |
2.00 |
2.00 |
2.00 |
2.00 |
2.00 |
Jeffamine D-230 |
- |
- |
15.47 |
18.20 |
18.20 |
18.20 |
9.58 |
31.93 |
Omyacarb 5GU |
- |
49.74 |
0.00 |
94.80 |
32.80 |
197.00 |
76.00 |
126.00 |
Component B |
|
|
|
|
|
|
|
|
Araldite GY 250 |
- |
- |
57.00 |
57.00 |
57.00 |
57.00 |
30.00 |
100.00 |
Water |
- |
10.00 |
4.00 |
10.00 |
10.00 |
10.00 |
10.00 |
10.00 |
DBTDL in DIDP |
- |
1.00 |
0.00 |
0.00 |
0.00 |
0.00 |
0.00 |
0.00 |
Omyacarb 5GU |
- |
16.26 |
0.00 |
31.00 |
10.70 |
64.40 |
25.00 |
41.00 |
Aerosil R200 |
- |
2.00 |
0.00 |
2.00 |
2.00 |
2.00 |
2.00 |
2.00 |
Total |
100.00 |
166.00 |
150.42 |
300.00 |
217.70 |
435.60 |
239.58 |
397.93 |
Concrete adhesion strenght, after 28 days [N/50 mm] |
27 |
21 |
21 |
55 |
34 |
21 |
43 |
37 |
Table 3
Build-up of membrane |
Ref-1 |
Ex-1 |
Ex-2 |
Ex-3 |
Ex-4 |
Ex-5 |
Ex-6 |
Ex-7 |
Ex-8 |
Ex-9 |
Ex-10 |
Barrier layer |
EVA |
EVA |
EVA |
EVA |
EVA |
EVA |
EVA |
EVA |
EVA |
E-P |
E-P |
Thickness [mm] |
0.6 |
0.6 |
0.6 |
0.6 |
0.6 |
0.6 |
0.6 |
0.6 |
0.6 |
1 |
1 |
Surface modification |
Yes |
Yes |
Yes |
Yes |
Yes |
Yes |
Yes |
Yes |
Yes |
Yes |
Yes |
Connecting layer |
Epoxy |
Epoxy |
Epoxy |
Epoxy |
Epoxy |
Epoxy |
Epoxy |
Epoxy |
Epoxy |
No |
Epoxy |
Thickness [mm] |
0.1 |
0.1 |
0.1 |
0.1 |
0.1 |
0.1 |
0.1 |
0.1 |
0.1 |
- |
0.1 |
Functional layer |
No |
FL-1 |
FL-2 |
FL-3 |
FL-4 |
FL-5 |
FL-6 |
FL-7 |
FL-8 |
FL-4 |
FL-4 |
Thickness [mm] |
- |
0.1 |
0.1 |
0.1 |
0.1 |
0.1 |
0.1 |
0.1 |
1.1 |
0.1 |
0.1 |
Concrete adhesion strenght, after 28 days [N/50 mm] |
0 |
27 |
21 |
21 |
55 |
34 |
21 |
43 |
37 |
24 |
57 |