(19) |
 |
|
(11) |
EP 3 039 338 B1 |
(12) |
FASCICULE DE BREVET EUROPEEN |
(45) |
Mention de la délivrance du brevet: |
|
09.10.2019 Bulletin 2019/41 |
(22) |
Date de dépôt: 26.08.2014 |
|
(86) |
Numéro de dépôt: |
|
PCT/IB2014/064060 |
(87) |
Numéro de publication internationale: |
|
WO 2015/028933 (05.03.2015 Gazette 2015/09) |
|
(54) |
FOUR D'INCINÉRATION DE PRODUITS PÂTEUX, EN PARTICULIER DE BOUES DE STATIONS D'ÉPURATION
VERBRENNUNGSOFEN FÜR PASTÖSE PRODUKTE, INSBESONDERE KLÄRSCHLAMM AUS REINIGUNGSSTATIONEN
INCINERATION FURNACE FOR PASTY PRODUCTS, IN PARTICULAR SLUDGE FROM PURIFYING STATIONS
|
(84) |
Etats contractants désignés: |
|
AL AT BE BG CH CY CZ DE DK EE ES FI FR GB GR HR HU IE IS IT LI LT LU LV MC MK MT NL
NO PL PT RO RS SE SI SK SM TR |
(30) |
Priorité: |
27.08.2013 FR 1358199
|
(43) |
Date de publication de la demande: |
|
06.07.2016 Bulletin 2016/27 |
(73) |
Titulaire: SUEZ International |
|
92040 Paris La Défense (FR) |
|
(72) |
Inventeur: |
|
- PARDO, Pierre Emmanuel
91400 Orsay (FR)
|
(74) |
Mandataire: IPAZ |
|
16, rue Gaillon 75002 Paris 75002 Paris (FR) |
(56) |
Documents cités: :
WO-A1-2012/066802 DE-A1- 19 714 073
|
DE-A1- 10 156 616 US-A- 3 515 381
|
|
|
|
|
|
|
|
|
Il est rappelé que: Dans un délai de neuf mois à compter de la date de publication
de la mention de la délivrance de brevet européen, toute personne peut faire opposition
au brevet européen délivré, auprès de l'Office européen des brevets. L'opposition
doit être formée par écrit et motivée. Elle n'est réputée formée qu'après paiement
de la taxe d'opposition. (Art. 99(1) Convention sur le brevet européen). |
[0001] La présente invention concerne un four d'incinération de produits pâteux, en particulier
de boues de stations d'épuration, à lit de matériau granulaire fluidisé par injection
d'un fluide gazeux, le four étant du genre de ceux qui comprennent au moins deux buses
d'injection de produits pâteux dans le lit, alimentées respectivement par une conduite
munie d'une vanne et reliée au refoulement d'une même pompe, et un conduit d'évacuation
des gaz de combustion.
[0002] Lors d'une combustion de produits pâteux dans un four à lit fluidisé, l'injection
la plus efficace est celle obtenue par un pompage refoulant directement dans le lit
de matériau granulaire. En effet, les produits pâteux sont alors finement distribués
dans le lit de matériau granulaire et la combustion est la plus efficace et la plus
complète. L'injection du produit est effectuée à travers un nombre limité de buses
à l'intérieur du lit. Cependant ce type d'injection peut générer plusieurs problèmes
: d'une part une buse d'injection peut se boucher sans que l'on observe rapidement
ce bouchage, d'autre part, ce bouchage peut entraîner une carbonisation de la boue
à l'orifice et un bouchage permanent de la buse d'injection.
[0003] Ces problèmes sont particulièrement présents lorsque les produits pâteux injectés
sont très visqueux, notamment dans le cas de boues de station d'épuration.
[0004] Plusieurs solutions ont été proposées pour remédier à ces problèmes.
[0005] Une première solution consiste en une fermeture cyclique de chacune des buses d'injection
du four alimentées par une même pompe : cette pompe pousse les produits dans le four
alternativement, grâce à un jeu de vannes, par une seule des buses. Les produits pâteux,
notamment la boue, sont obligés de sortir par cette buse, ce qui provoque son débouchage.
[0006] Cette solution présente plusieurs inconvénients. Elle nécessite la mise en place
de vannes guillotines automatiques qui fonctionnent fréquemment et qui vont s'user
relativement rapidement. De plus cette solution génère une forte perte de charge pour
faire passer en permanence l'ensemble du produit dans une seule buse, ce qui entraîne
un surdimensionnement de la pompe.
[0007] Une autre solution consiste en l'utilisation d'une pompe par buse d'injection. Dans
ce cas, l'injection est parfaitement contrôlée par la mise en place de débitmètre
sur chaque pompe. Mais cette solution est onéreuse car les pompes sous pression sont
d'un coût important.
[0008] DE 101 56 616 A1 décrit un four d'incinération de produits pâteux, ou de boues, à lit de matériau
granulaire fluidisé par injection d'un fluide gazeux, du genre défini précédemment.
[0009] WO 2012/066802 A1 décrit un autre four d'incinération de boues muni de capteurs de température situés
dans différentes parties du lit de matériau granulaire et employés pour réguler la
température dans les parties correspondantes en agissant sur l'air de fluidisation.
[0010] US 3 515 381 A décrit un incinérateur comprenant un capteur de température situé au-dessus du lit
fluidisé et agissant et agissant par le biais d'un régulateur sur le débit des boues
introduites dans l'incinérateur.
[0011] L'invention a pour but, notamment, de proposer un four d'incinération permettant
le contrôle de l'injection des produits pâteux, et le débouchage des buses, lorsque
nécessaire, pour un coût modéré.
[0012] Selon l'invention, un four d'incinération de produits pâteux, en particulier de boues
de stations d'épuration, à lit de matériau granulaire fluidisé par injection d'un
fluide gazeux, du genre défini précédemment, est caractérisé en ce que le four comprend
au moins deux capteurs de température disposés au-dessus du lit de matériau granulaire,
chaque capteur de température étant situé dans une zone associée à au moins une buse
d'injection, et un moyen sensible à une différence de température entre les capteurs,
propre à détecter, lorsque la différence de température dépasse une valeur déterminée,
le bouchage d'au moins une buse.
[0013] Avantageusement, le moyen sensible à la différence de température entre les capteurs,
est propre à couper l'alimentation en boues de la, ou des buse(s) associée(s) au capteur
de température indiquant une température supérieure à celle fournie par l'autre capteur.
[0014] De préférence, le moyen sensible comprend un automate propre à commander la coupure
de l'alimentation en produits pâteux, en particulier en boues de la, ou des buse(s),
associée(s) au capteur de température indiquant une température supérieure, en particulier
d'au moins 10°C, à celle fournie par l'autre capteur.
[0015] Le lit de matériau granulaire peut être configuré fictivement en secteurs angulaires,
en particulier de taille égale, et au moins une buse d'injection est associée à chaque
secteur angulaire.
[0016] Avantageusement, chaque capteur de température est disposé à la verticale au-dessus
d'une buse d'injection, ou de la zone médiane d'un groupe de buses associées au capteur.
[0017] En variante, chaque capteur de température peut être disposé dans une partie de la
zone associée à chaque buse ou groupe de buses.
[0018] Chaque capteur de température peut se trouver à une distance comprise entre 0.1 et
2 mètres au-dessus du lit de matériau granulaire, l'ensemble de ces capteurs constituant
une première série. De préférence, chaque capteur de température de cette première
série se trouve à une distance de 0.5 mètre au-dessus du lit de matériau granulaire.
[0019] Le four peut comporter une seconde série de capteurs de température situés au-dessus
de la première série de capteurs de température. Chaque capteur de température de
la seconde série peut se trouver à une distance comprise entre 1.5 et 8 mètres au-dessus
du lit de matériau granulaire. Avantageusement, chaque capteur de température de la
seconde série se trouve à une distance d'environ 2 mètres au-dessus du lit de matériau
granulaire.
[0020] Le four peut comprendre deux buses d'injection, diamétralement opposées, chaque buse
étant surmontée d'un capteur de température.
[0021] Selon une variante, le four peut comprendre quatre buses d'injection, deux buses
étant affectées à un premier secteur angulaire semi-circulaire surmonté d'un premier
capteur de température et deux autres buses étant affectées à un second secteur angulaire
semi-circulaire surmonté d'un second capteur de température.
[0022] Chaque buse d'injection peut présenter une forme en V renversé, avec rétrécissement
de la section de passage jusqu'à la sortie, propre à créer une perte de charge au
moins égale à la différence maximale de perte de charge entre deux lignes d'injection
de produits pâteux à partir du refoulement d'une même pompe.
[0023] D'autres caractéristiques et avantages de l'invention apparaîtront dans la description
qui suit de modes de réalisation préférés avec référence aux dessins annexés mais
qui n'ont aucun caractère limitatif. Sur ces dessins :
Fig. 1 est un schéma d'un premier mode de réalisation d'un four selon l'invention,
Fig. 2 est un schéma à plus grande échelle de la zone d'injection des boues du four
de Fig. 1,
Fig. 3 est une coupe horizontale schématique de Fig. 1, et
Fig. 4 est une vue similaire à Fig. 3 d'un autre mode de réalisation de l'invention.
[0024] En se reportant à la Figure 1, on peut voir un four 1 d'incinération de produits
pâteux, en particulier de boues de stations d'épuration, à lit fluidisé de matériau
granulaire, notamment de sable.
[0025] Le four 1 comporte dans sa partie basse une boîte à vent 2 au-dessus de laquelle
est disposé un lit de sable 3. La boîte à vent 2 est reliée au refoulement d'une soufflante,
non représentée, pour le soufflage d'air au travers du lit 3. Des tubulures non représentées
permettent le passage de l'air depuis la boîte à air vers le lit de sable 3 afin d'assurer
la fluidisation du sable. Au-dessus du lit de sable se trouve une zone de postcombustion
4 surmontée par un orifice et une conduite 5 de sortie des fumées.
[0026] Deux buses d'injection 6 et 7 situées de part et d'autre du lit de sable 3, de préférence
diamétralement opposées, permettent l'injection de boues à incinérer dans le lit de
sable 3. L'alimentation des buses 6 et 7 est régulée par l'ouverture et la fermeture
de vannes respectivement 8 et 9, de préférence des électrovannes. L'amenée des boues
sous pression se fait par l'intermédiaire de conduites et d'une pompe 10.
[0027] La turbulence du lit de sable induite par l'air soufflé, provenant de la boîte à
vent, permet un mélange homogène avec les boues en provenance des buses 6 et 7.
[0028] Lorsqu'une buse d'injection se bouche, une baisse de la température de l'ensemble
du lit peut être détectée. Mais du fait de l'homogénéité de la température dans le
lit de sable 3 et de son fort effet tampon thermique (forte capacité calorifique de
la masse de sable), il n'est pas possible de déterminer quelle est la buse qui est
bouchée.
[0029] D'une manière surprenante, et bien que la température du lit soit homogène, il est
apparu que des mesures de températures effectuées au-dessus du lit 3, de préférence
à la verticale des buses, faisaient apparaître rapidement une différence sensible,
d'au moins 10°C, entre la température plus élevée au-dessus d'une buse qui n'est pas
bouchée, et la température au-dessus d'une buse bouchée, alimentée par la même pompe
que l'autre buse.
[0030] Des capteurs de température, en particulier des thermocouples 11, 12, 13, 14, ont
été installés au-dessus du lit de sable, à la verticale des buses 6 et 7 (Fig. 1 et
3). Cette configuration permet de détecter si le produit pâteux est bien injecté par
chaque buse considérée.
[0031] Dans le lit de sable, il n'est pas possible de constater un bouchage, car la turbulence
dans le lit, provoquée par l'injection d'air horizontalement qui se transforme en
mouvement vertical, est très forte et il y a une véritable homogénéisation du lit.
La constatation effectuée au-dessus du lit de sable permet de penser que le flux d'air,
devenu vertical, dépend pour beaucoup de ce qui se passe à sa verticale plus bas.
De plus la combustion de la matière pâteuse se déroule en deux temps : une partie
dans le lit de sable et une autre partie au-dessus. C'est l'inhomogénéité de cette
deuxième partie qui est détectée.
[0032] Une mesure de température dans le lit de sable 3 permettrait de détecter la présence
d'un problème global, si une variation sensible de température était détectée, mais
pas de localiser précisément le problème.
[0033] On désigne par n0 l'altitude moyenne de la surface supérieure du lit de sable 3.
A un niveau n1 situé au-dessus de n0, sont disposés deux thermocouples 11 et 12, constituant
une première série. Le thermocouple 11 est disposé à la verticale de la buse d'injection
6 tandis que le thermocouple 12 est disposé à la verticale de la buse d'injection
7.
[0034] Le niveau n1, altitude à laquelle se situent les thermocouples 11 et 12, est situé
à environ 0,5 m au-dessus du niveau n0 correspondant à la surface supérieure du lit
de sable.
[0035] Une seconde série de deux thermocouples 13 et 14 se situe à un niveau n2 au-dessus
du niveau n1. Le thermocouple 13 se situe à la verticale de la buse d'injection 6
tandis que le thermocouple 14 se situe à la verticale de la buse d'injection 7.
[0036] Le niveau n2 est situé plus haut dans la zone de postcombustion.
[0037] Le niveau n2 se situe à environ 2 m au-dessus du niveau n0.
[0038] D'autres thermocouples 15 et 16 sont situés en partie supérieure de la zone de postcombustion
4.
[0039] Enfin, un thermocouple 17 est situé au niveau du conduit d'évacuation 1.
[0040] Les capteurs de température sont reliés à un automate A constituant un moyen sensible
à la différence de température entre les capteurs. Les mesures issues des différents
thermocouples sont traitées par l'automate A, qui est relié aux électrovannes 8, 9
pour les commander.
[0041] Dans le cas où une différence de température supérieure à une valeur déterminée,
en particulier 10°C, est détectée entre la température mesurée par le capteur 11 et
celle mesurée par le capteur 12, l'automate A peut émettre une alarme pour indiquer
la probabilité d'un bouchage de l'une des deux buses d'injection.
[0042] La température la plus basse indique la localisation du bouchage.
[0043] En effet, s'il n'y a plus introduction du produit dans une buse, la température va
rapidement descendre, et donc la température mesurée par le capteur situé à la verticale
de ladite buse sera inférieure.
[0044] Dans le cas de la détection d'un bouchage, par exemple si la température mesurée
par le thermocouple 11 est inférieure de plus de 10°C à la température mesurée par
le thermocouple 12, ce qui correspond à un bouchage de la buse d'injection 6, avantageusement
l'automate A commande la fermeture de la vanne 9 , de manière à orienter la totalité
du débit de boues provenant de la pompe 10 commune aux deux buses 5, 6 vers la seule
buse 6 bouchée, ce qui provoquera rapidement son débouchage, sans compromettre d'une
manière globale le débit injecté dans le four.
[0045] A l'issue d'un temps pré-paramétré, la vanne 9 sera de nouveau ouverte pour permettre
le retour à un fonctionnement normal.
[0046] Si les thermocouples 11 et 12 indiquent une persistance de différence de température,
et donc de bouchage à l'issue du temps pré-paramétré, un deuxième cycle de débouchage
est déclenché.
[0047] La deuxième rangée de thermocouples 13 et 14 permet en cas de dysfonctionnement,
par exemple de l'un des thermocouples de la première rangée de thermocouples 11, 12,
de basculer vers une régulation du débouchage automatique en utilisant les thermocouples
13 et 14. Elle permet aussi de déterminer un deuxième niveau d'alarme si la première
rangée de thermocouples ne détecte pas de différence de température alors que la seconde
en détecte une.
[0048] L'invention permet de nombreuses possibilités et, en particulier, ne se limite pas
à la gestion de deux injecteurs.
[0049] Il est possible d'utiliser un nombre plus important de buses d'injection, chacune
des buses comportant au moins un thermocouple situé préférentiellement à la verticale
au-dessus du lit de sable.
[0050] Il est également possible de grouper les buses d'injection par secteur angulaire,
l'ensemble des buses d'injection dudit secteur étant considéré comme une buse unique
dans le cadre du dispositif de débouchage selon l'invention. Le capteur de température
associé à un secteur est de préférence disposé dans la zone médiane de ce secteur.
[0051] Fig. 4 illustre le cas où on utilise quatre buses 6a, 6b, 7a, 7b également réparties
sur deux secteurs semi-circulaires S1 et S2 opposés, les secteurs S1 et S2 étant surmontés
par les thermocouples, respectivement 11 et 12.
[0052] Dans le cas où le thermocouple 11 situé à la verticale de la zone médiane du secteur
S1 détecte une baisse de température, et donc un bouchage, les vannes 9a et 9b alimentant
les buses 7a et 7b de l'autre secteur S2 sont temporairement fermées tandis que les
vannes 8a et 8b alimentant le secteur S1 sont maintenues ouvertes.
[0053] Après une première période de temps prédéterminée, si les thermocouples n'indiquent
pas que la situation est redevenue normale, les vannes 8a et 8b sont fermées alternativement
pour assurer le débouchage.
[0054] Il est cependant recommandé dans le cas des quatre buses de mettre quatre thermocouples
strictement au-dessus des buses ou dans un angle de 45° (360/4/2) autour des buses
pour contrôler l'action de chaque buse.
[0055] Le four selon l'invention comporte également des dispositions permettant de minimiser
le risque de bouchage des buses.
[0056] Ce risque de bouchage provient essentiellement du fait qu'une petite différence de
perte de charge, sur une des lignes d'injection provenant du refoulement d'une même
pompe, entraîne une baisse de débit dans cette ligne. Cette baisse de débit entraîne
un léger dépôt qui augmente la perte de charge, ce qui amplifie la baisse de débit,
et au final amène au bouchage.
[0057] Pour minimiser ce risque de bouchage, on prévoit selon Fig.2 des buses d'injection
6, 7 présentent chacune une forme en V renversé, en particulier tronconique, avec
rétrécissement de la section de passage jusqu'à la sortie. Une telle buse est prévue
pour créer une perte de charge au moins égale à la différence maximale de perte de
charge entre les deux lignes d'injection provenant de la même pompe.
[0058] La perte de charge créée par les buses, correspondant à 100 % du maximum de différence
possible de perte de charge entre les deux lignes d'injection, permet de réduire l'influence
relative de ladite perte de charge entre lignes. Cette perte de charge, créée par
la forme des buses, permet couvrir pratiquement 100% des « inhomogénéités » de perte
de charge.
[0059] Le four selon l'invention présente de nombreux avantages. Il permet d'une part de
minimiser les bouchages d'une des buses d'injection et d'autre part d'automatiser
le débouchage des buses en cas de bouchage et ce, sans avoir à multiplier les équipements
onéreux tels que les pompes d'injection ou sans avoir à les sur-dimensionner.
1. Four (1) d'incinération de produits pâteux, ou de boues, à lit de matériau granulaire
fluidisé par injection d'un fluide gazeux, le four comprenant au moins deux buses
d'injection (6, 7) de produits dans le lit, alimentées respectivement par une conduite
munie d'une vanne (8,9) et reliée au refoulement d'une même pompe, et un conduit d'évacuation
des gaz de combustion (5), caractérisé en ce que le four (1) comprend au moins deux capteurs de température (11, 12) situés au-dessus
du lit de matériau granulaire (3), chaque capteur de température (11, 12) étant situé
dans une zone associée à au moins une buse d'injection (6,7), et un moyen (A) sensible
à une différence de température entre les capteurs (11,12), propre à détecter le bouchage
d'au moins une buse lorsque la différence de température dépasse une valeur déterminée.
2. Four selon la revendication 1, caractérisé en ce que le moyen (A) sensible à une différence de température entre les capteurs, est propre
à couper l'alimentation en boues de la, ou des buse(s) associée(s) au capteur de température
indiquant une température supérieure d'au moins la valeur prédéterminée à celle fournie
par l'autre capteur.
3. Four selon la revendication 1, caractérisé en ce que le moyen sensible comprend un automate (A) propre à commander la coupure de l'alimentation
en produits pâteux, en particulier en boues de la, ou des buse(s), associée(s) au
capteur de température indiquant une température supérieure, en particulier d'au moins
10°C, à celle fournie par l'autre capteur.
4. Four selon l'une quelconque des revendications précédentes, caractérisé en ce que le lit de matériau granulaire (3) est configuré fictivement en secteurs angulaires
(S1, S2), en particulier de taille égale, au moins une buse d'injection (6, 7) étant
associée à chaque secteur (S1, S2).
5. Four selon l'une quelconque des revendications précédentes, caractérisé en ce que chaque capteur de température est disposé à la verticale au-dessus d'une buse d'injection,
ou de la zone médiane d'un groupe de buses associées au capteur.
6. Four selon l'une quelconque des revendications 1 à 4, caractérisé en ce que chaque capteur de température est disposé dans une partie de la zone associée à chaque
buse ou groupe de buses.
7. Four selon l'une quelconque des revendications précédentes, caractérisé en ce que chaque capteur de température (11, 12) d'une première série se trouve à une distance
comprise entre 0.1 et 2 mètres au dessus du lit de sable (3).
8. Four selon la revendication 7, caractérisé en ce que chaque capteur de température (11, 12) de la première série se trouve à une distance
de 0.5 mètre au-dessus du lit de sable (3).
9. Four selon la revendication 7 ou 8, caractérisé en ce que le four (1) comporte une seconde série de capteurs de température (13, 14) situés
au-dessus de la première série de capteurs de température (11, 12).
10. Four selon la revendication 9, caractérisé en ce que chaque capteur de température (13, 14) de la seconde série se trouve à une distance
comprise entre 1.5 et 8 mètres au-dessus du lit de sable (3).
11. Four selon la revendication 10, caractérisé en ce que chaque capteur de température (13, 14) de la seconde série se trouve à une distance
de 2 mètres au-dessus du lit de sable (3).
12. Four selon l'une quelconque des revendications 1 à 11, caractérisé en ce qu'il comprend quatre buses d'injection (6a, 6b, 7a, 7b), les buses (6a, 6b) étant affectées
à un premier secteur (S1) surmonté par un premier capteur de température (11) et les
buses (7a, 7b) étant affectées à un second secteur (S2) surmonté par un second capteur
de température (12).
13. Four selon l'une quelconque des revendications précédentes, caractérisé en ce que les buses d'injection (6, 7) présentent chacune une forme en V renversé, avec rétrécissement
de la section de passage jusqu'à la sortie, propre à créer une perte de charge au
moins égale à la différence maximale de perte de charge entre deux lignes d'injection.
1. Ofen (1) zur Verbrennung von pastösen Erzeugnissen, oder von Schlämmen, mit Granulatbett,
das durch Einspritzen eines gasförmigen Fluids fluidisiert ist, wobei der Ofen mindestens
zwei Düsen zum Einspritzen (6, 7) von Erzeugnissen in das Bett umfasst, die jeweils
von einer Rohrleitung beschickt werden, die mit einem Ventil (8, 9) versehen ist und
mit der Auslassöffnung einer gleichen Pumpe verbunden ist, und eine Leitung zum Ablassen
der Verbrennungsgase (5) umfasst, dadurch gekennzeichnet, dass der Ofen (1) mindestens zwei Temperatursensoren (11, 12) umfasst, die sich oberhalb
des Granulatbetts (3) befinden, wobei jeder Temperatursensor (11, 12) sich in einer
Zone befindet, die mindestens einer Einspritzdüse (6, 7) zugeordnet ist, und ein gegenüber
einem Temperaturunterschied zwischen den Sensoren (11, 12) empfindliches Mittel (A)
umfasst, das imstande ist, das Verstopfen mindestens einer Düse zu detektieren, wenn
der Temperaturunterschied einen festgelegten Wert überschreitet.
2. Ofen nach Anspruch 1, dadurch gekennzeichnet, dass das gegenüber einem Temperaturunterschied zwischen den Sensoren empfindliche Mittel
(A) imstande ist, die Beschickung mit Schlämmen der Düse oder Düsen zu unterbrechen,
die dem Temperatursensor zugeordnet ist bzw. sind, der eine Temperatur anzeigt, die
um einen vorab festgelegten Wert höher ist als diejenige, die von dem anderen Sensor
geliefert wird.
3. Ofen nach Anspruch 1, dadurch gekennzeichnet, dass das empfindiche Mittel eine Automatik (A) umfasst, die imstande ist, die Unterbrechung
der Beschickung mit pastösen Erzeugnissen, insbesondere mit Schlämmen, der Düse oder
Düsen zu steuern, die dem Temperatursensor zugeordnet ist bzw. sind, der eine Temperatur
anzeigt, die um mindestens 10 °C höher ist als diejenige, die von dem anderen Sensor
geliefert wird.
4. Ofen nach einem der vorhergehenden Ansprüche, dadurch gekennzeichnet, dass das Granulatbett (3) fiktiv in Winkelsektoren (S1, S2), insbesondere gleicher Größe,
ausgebildet ist, wobei mindestens eine Einspritzdüse (6, 7) jedem Sektor (S1, S2)
zugeordnet ist.
5. Ofen nach einem der vorhergehenden Ansprüche, dadurch gekennzeichnet, dass jeder Temperatursensor vertikal oberhalb einer Einspritzdüse, oder der Mittelzone
einer Gruppe von Düsen, die dem Sensor zugeordnet sind, angeordnet ist.
6. Ofen nach einem der Ansprüche 1 bis 4, dadurch gekennzeichnet, dass jeder Temperatursensor in einem Teil der Zone angeordnet ist, die jeder Düse oder
Gruppe von Düsen zugeordnet ist.
7. Ofen nach einem der vorhergehenden Ansprüche, dadurch gekennzeichnet, dass jeder Temperatursensor (11, 12) einer ersten Reihe sich in einem Abstand zwischen
0,1 und 2 Meter oberhalb des Sandbetts (3) befindet.
8. Ofen nach Anspruch 7, dadurch gekennzeichnet, dass jeder Temperatursensor (11, 12) der ersten Reihe sich in einem Abstand von 0,5 Meter
oberhalb des Sandbetts (3) befindet.
9. Ofen nach Anspruch 7 oder 8, dadurch gekennzeichnet, dass der Ofen (1) einen zweite Reihe von Temperatursensoren (13, 14) aufweist, die sich
oberhalb der ersten Reihe von Temperatursensoren (11, 12) befinden.
10. Ofen nach Anspruch 9, dadurch gekennzeichnet, dass jeder Temperatursensor (13, 14) der zweiten Reihe sich in einem Abstand zwischen
1,5 und 8 Meter oberhalb des Sandbetts (3) befindet.
11. Ofen nach Anspruch 10, dadurch gekennzeichnet, dass jeder Temperatursensor (13, 14) der zweiten Reihe sich in einem Abstand von 2 Meter
oberhalb des Sandbetts (3) befindet.
12. Ofen nach einem der Ansprüche 1 bis 11, dadurch gekennzeichnet, dass er vier Einspritzdüsen (6a, 6b, 7a, 7b) umfasst, wobei die Düsen (6a, 6b) einem ersten
Sektor (S1) zugewiesen sind, der von einem ersten Temperatursensor (11) überragt wird,
und wobei die Düsen (7a, 7b) einem zweiten Sektor (S2) zugewiesen sind, der von einem
zweiten Temperatursensor (12) überragt wird.
13. Ofen nach einem der vorhergehenden Ansprüche, dadurch gekennzeichnet, dass die Einspritzdüsen (6, 7) jede die Form eines umgekehrten V aufweisen, mit Verjüngung
des Durchtrittsquerschnitts zu dem Auslass hin, die in der Lage ist, einen Lastverlust
zu erzeugen, der mindestens gleich des maximalen Lastverlustunterschieds zwischen
zwei Einspritzleitungen ist.
1. A furnace (1) for incineration of pasty products, or sludge, with a bed of granular
material which is fluidized by injection of a gaseous fluid, the furnace comprising
at least two nozzles (6, 7) for injection of products into the bed, which nozzles
are supplied respectively by a duct which is provided with a valve (8, 9), and is
connected to the discharge of a single pump, and a pipe (5) for discharge of the combustion
gases, characterized in that the furnace (1) comprises at least two temperature sensors (11, 12) which are situated
above the bed of granular material (3), each temperature sensor (11, 12) being situated
in an area which is associated with at least one injection nozzle (6, 7), and means
(A) which are sensitive to a temperature difference between the sensors (11, 12),
which, when the temperature difference exceeds a predetermined value, can detect the
clogging of at least one nozzle.
2. The furnace as claimed in claim 1, characterized in that the means (A) which are sensitive to a temperature difference between the sensors
can cut off the supply of sludge to the nozzle (s) associated with the temperature
sensor which is indicating a temperature which is higher by at least the predetermined
value than that provided by the other sensor.
3. The furnace as claimed in claim 1, characterized in that the sensitive means comprise an automaton (A) which can command the cutting off of
the supply of pasty products, in particular of sludge, to the nozzle(s) associated
with the temperature sensor which is indicating a temperature which is higher, in
particular by at least 10°C, than that provided by the other sensor.
4. The furnace as claimed in any one of the preceding claims, characterized in that the bed of granular material (3) is configured imaginarily into angular sectors (S1,
S2), in particular with an equal size, at least one injection nozzle (6, 7) being
associated with each angular sector (S1, S2) .
5. The furnace as claimed in any one of the preceding claims, characterized in that each temperature sensor is arranged vertically above an injection nozzle, or the
median area of a group of nozzles associated with the sensor.
6. The furnace as claimed in any one of claims 1 to 4, characterized in that each temperature sensor is arranged in a part of the area associated with each nozzle
or group of nozzles.
7. The furnace as claimed in any one of the preceding claims, characterized in that each temperature sensor (11, 12) of a first series is located at a distance of between
0.1 and 2 m above the bed of sand (3).
8. The furnace as claimed in claim 7, characterized in that each temperature sensor (11, 12) of the first series is at a distance of 0.5 m above
the bed of sand (3).
9. The furnace as claimed claim 7 or 8, characterized in that the furnace (1) comprises a second series of temperature sensors (13, 14) situated
above the first series of temperature sensors (11, 12).
10. The furnace as claimed in claim 9, characterized in that each temperature sensor (13, 14) of the second series is at a distance of between
1.5 and 8 m above the bed of sand (3).
11. The furnace as claimed in claim 10, characterized in that each temperature sensor (13, 14) of the second series is at a distance of 2 m above
the bed of sand (3).
12. The furnace as claimed in any one of claims 1 to 11, characterized in that it comprises four injection nozzles (6a, 6b, 7a, 7b), the nozzles (6a, 6b) being
allocated to a first sector (S1) which is surmounted by a first temperature sensor
(11), and the nozzles (7a, 7b) being allocated to a second sector (S2) which is surmounted
by a second temperature sensor (12).
13. The furnace as claimed in any one of the preceding claims, characterized in that the injection nozzles (6, 7) are each in the form of an inverted "V", with narrowing
of the cross-section of passage as far as the exit, thus being able to create a loss
of load which is at least equal to the maximum difference of loss of load between
two injection lines.
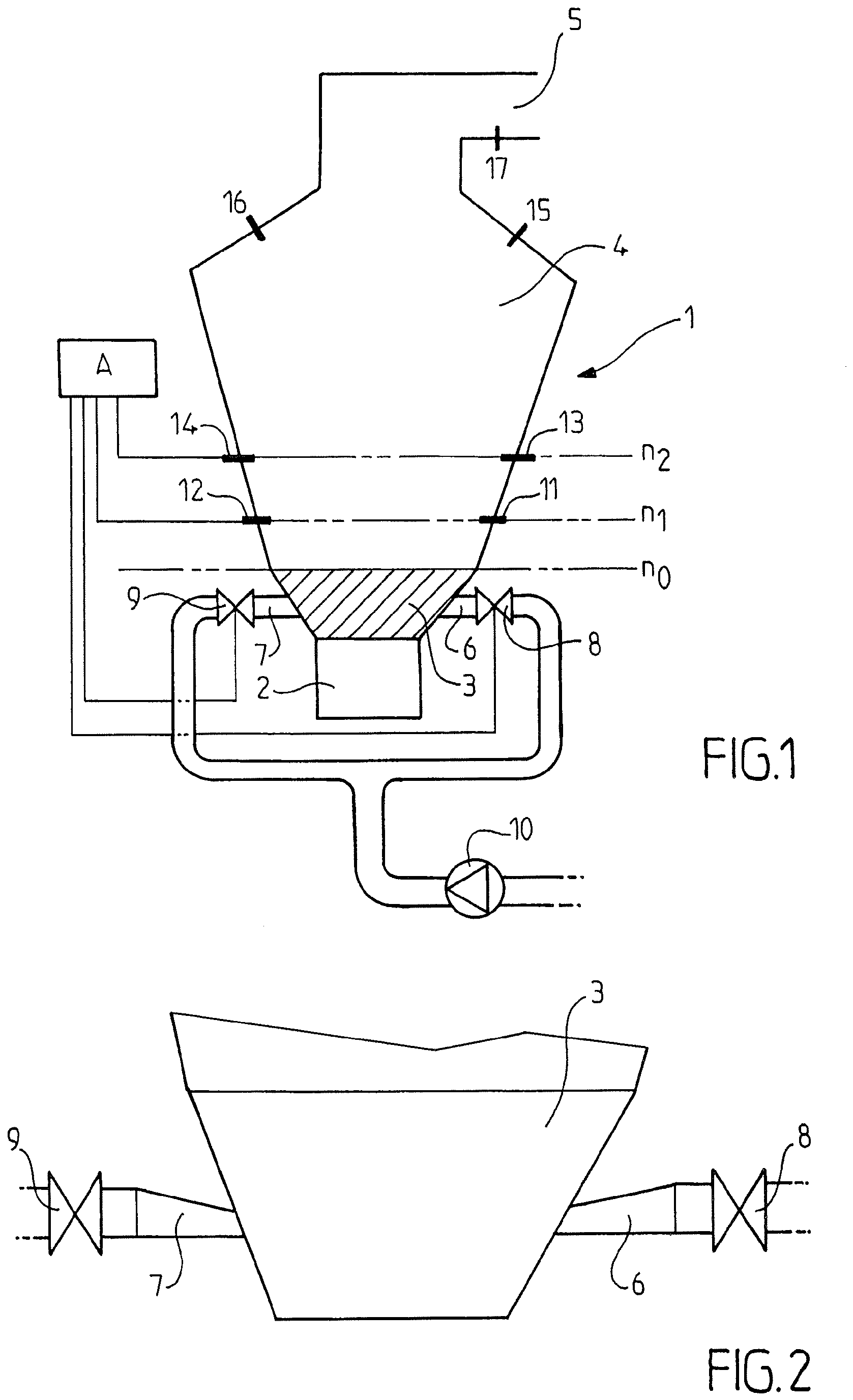
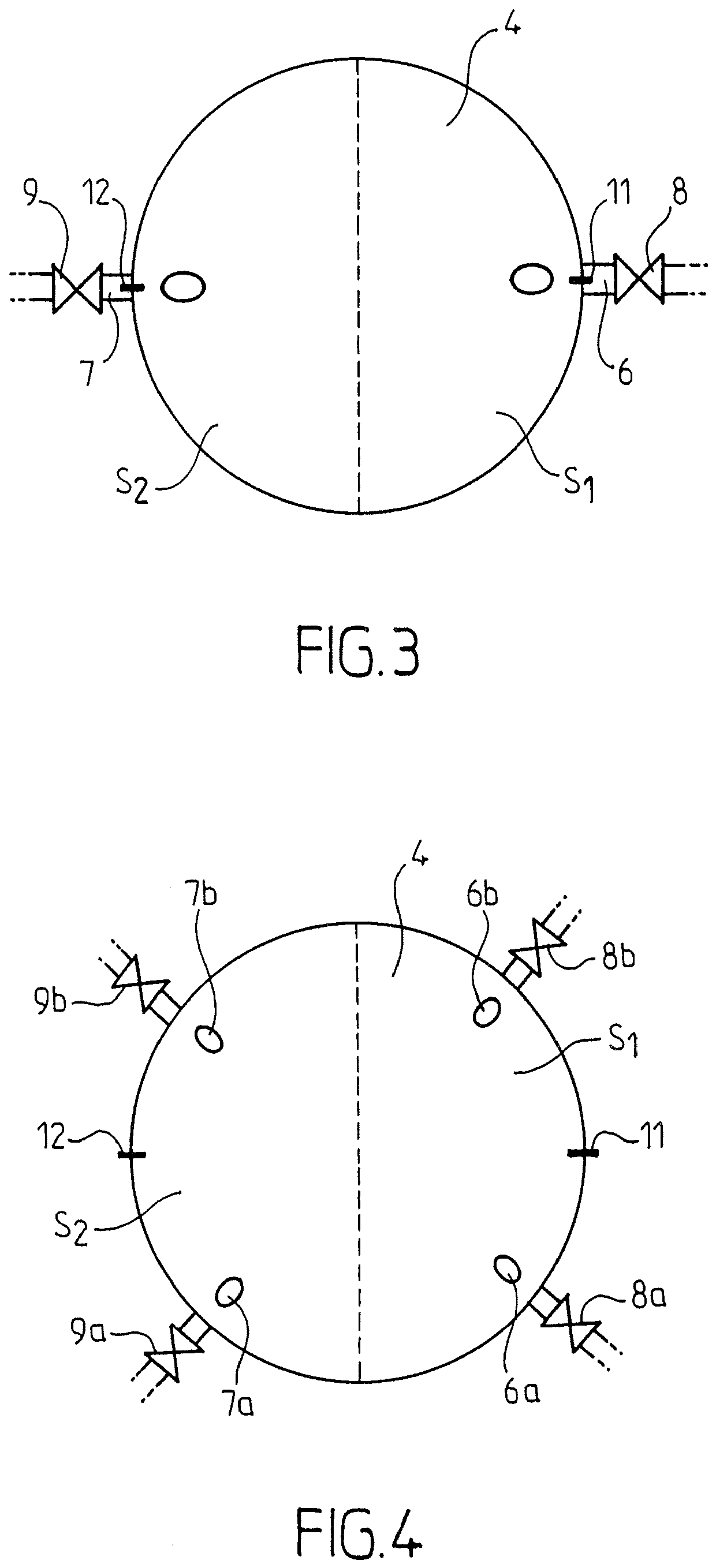
RÉFÉRENCES CITÉES DANS LA DESCRIPTION
Cette liste de références citées par le demandeur vise uniquement à aider le lecteur
et ne fait pas partie du document de brevet européen. Même si le plus grand soin a
été accordé à sa conception, des erreurs ou des omissions ne peuvent être exclues
et l'OEB décline toute responsabilité à cet égard.
Documents brevets cités dans la description