[0001] Bei der Herstellung von Methylmethacrylat durch C
4-basierte Oxidation von Methacrolein (
Arntz, W. et al., "Acroleine and Methacroleine" in Ullmann's Encyclopedia of Industrial
Chemistry, Elektronische Ausgabe, 329 (2012),
Bauer, W. "Methacrylic Acid and Derivatives in Ullmann's Encyclopedia of Industrial
Chemistry, Elektronische Ausgabe,1, (2012)) fallen Prozessströme an, die Methacrylsäure und Methacrolein und daneben übliche
Nebenkomponenten der spezifischen Synthesen, nämlich Formalinreste, Ameisensäure,
Essigsäure, Terepthalsäure etc. enthalten. Diese Stoffströme werden im Rahmen der
Monomerisolierung entsprechend aufgearbeitet.
[0002] Bei der Herstellung von Acrolein ausgehend von Propan oder Propylen (
Weigert, M., "Acrolein" in Ullmanns Encyklopädie der technischen Chemie, 4. Auflage,
Bd. 7, 77 (1974),
Arntz, W. et al., "Acroleine and Methacroleine" in Ullmann's Encyclopedia of Industrial
Chemistry, Elektronische Ausgabe, 329 (2012)) fällt ein Rohstrom an, der das Nebenprodukt der Partialoxidation von Propylen,
die Acrylsäure in signifikanten Anteilen neben weiteren Nebenkomponenten, wie Formalinreste,
Ameisensäure, Essigsäure etc. enthält. Dieser wird üblicherweise entsorgt.
[0003] Im Folgenden steht der Begriff "(Meth)acrylsäure" in diesem Zusammenhang sowohl für
Methacrylsäure als auch für Acrylsäure und/oder deren Mischungen. Der Begriff "(Meth)acrolein"
bedeutet in diesem Zusammenhang sowohl Methacrolein als auch Acrolein und/oder deren
Mischungen. Der Begriff Poly(meth)acrylsäure steht analog für Polymethacrylsäure,
Polyacrylsäure oder Copolymere, welche sowohl Acrylsäure-Einheiten als auch Methacrylsäure-Einheiten
enthalten
[0004] Die (Meth)acrylsäure enthaltenden Prozessströme sind alternativ zur Herstellung von
Polymeren im Sinne des erfindungsgemäßen Verfahrens geeignet, welches im Folgenden
beschrieben wird:
Die vorliegende Erfindung betrifft ein Verfahren zur Herstellung einer Poly(meth)acrylsäure,
dadurch gekennzeichnet, dass ein (Meth)acrylsäure enthaltender Prozessstrom aus der
(Meth)acrolein-Synthese der radikalischen Polymerisation unterworfen wird. Sie betrifft
außerdem die Veresterung des erhaltenen Polymers zu einem Copolymerester sowie dessen
Verwendung als Fließverbesserer.
[0005] Beton-Fließverbesserer werden zur Verbesserung des Fließverhaltens und der Verarbeitungsdauer
sowie der Eigenschaften von Beton eingesetzt. Polycarboxylatether (PCE), sogenannte
"Superplasticizer" (SP), stellen hier eine besonders wichtige und leistungsfähige
Polymerklasse dar (
Flatt, R., Schober I., "Superplasticizers and the Rheology of Concrete", in "Understanding
the Rheology of Concrete", Woodhead Publishing Ltd, 2012, 144). Bei PCE handelt es sich um Kammpolymere mit anionischem Hauptstrang ("Backbone")
und flexiblen, nicht-ionischen Seitenketten. Die Dispergierwirkung dieser Polymere
in zementösen Systemen während der Verarbeitung wird durch Adsorption des Backbones
an die Zementteilchen und zusätzlich durch die durch die Seitenketten induzierte sterische
Abstoßung erzielt. Bei den für den anionischen Hauptstrang verwendeten Monomeren handelt
es sich überwiegend um Methacrylsäure (MAS), Acrylsäure (AS), Maleinsäure (MAL) oder
Maleinsäureanhydrid (MSA), bei den Seitenketten mehrheitlich um Methoxypolyethylenglykol
(MPEG) und Polyethylenglykol (PEG). Ein einfacher PCE aus den Monomereinheiten (Meth)acrylsäure
und mit Seitenketten mit Methoxypolyethylenglykol-Funktionalität, ist in der Abbildung
1 dargestellt.
[0006] Somit handelt es sich bei den im Stand der Technik vorbeschriebenen SP chemisch gesehen
um Polymere, die als Backbone C-C verknüpfte Monomere und als funktionelle Seitengruppen
Brönstedtsaure Carboxylatgruppen, teilweise frei oder neutralisiert, enthalten, sowie
organische Ester- und Etherfunktionen.
[0007] PCE werden hauptsächlich über zwei Synthesewege, zum einen durch polymeranaloge Verfahren
(z.B. polymeranaloge Veresterung und/oder polymeranaloge Amidierung) oder zum anderen
durch Co-Polymerisation hergestellt (
Flatt, R., Schober I., "Superplasticizers and the Rheology of Concrete", in "Understanding
the Rheology of Concrete", Woodhead Publishing Ltd, 2012, 144;
Ferrari, G. et al., "Influence of Carboxylic Acid-Carboxylic Ester Ratio of Carboxylic
Acid Ester Superplasticizer on Characteristics of Cement Mixtures", International
Concrete Abstracts, 195, 2000, 505;
Lange, A., Plank, J., "Optimization of comb-shaped Polycarboxylate Cement Dispersants
to achieve fast-flowing Mortar and Concrete", J. Appl. Polym. Sci., 2015, 42529; Albrecht, G. et al., "Co-Polymere auf der Basis von Maleinsäurederivaten und Vinylmonomeren,
deren Herstellung und Verwendung",
EP 0 610 699, 1994; Arfaei, A. et al., "Improved cement admixture product having improved rheological
properties and process of forming same",
EP 0 739 320, 1999; Shawl, E., "Cement additives",
EP 0 889 860, 2000; Kroner, M. et al., "Verfahren zur Modifizierung von Säuregruppen enthaltenden Polymerisaten",
DE10015135, 2001; Sulser, U. et al., "Amid- und Estergruppen aufweisendes Polymer, dessen Herstellung
und Verwendung",
EP 1 577 327, 2005; Sulser, U. et al., "Kammpolymere mit verzögerter alkalischer Hydrolyse",
EP 2 567 988, 2011; Akira, I. et al., "Admixture for hydraulic composition",
JP 2013-082560, 2013; Cerulli, T., et al., "Zero slump-loss superplasticizer",
US 5362324, 1994; Yamato, F. et al., "Admixture for Concrete",
WO 95/16643, 1994; Amaya, T. et al., "Cement dispersant and concrete composition containing the dispersant",
EP 1 184 353, 1999; Lepori, A. et al., "Acrylic Co-Polymers",
US 6043329, 2000; Dreher S. et al., "Zementzusammensetzungen, enthaltend redispergierbare Polymerisatpulver",
DE 19 942 301, 2001; Kroner, M. et al., "Verwendung wasserlöslicher Polymerisate von Estern aus Acrylsäure,
Methacrylsäure und Alkylpolyalkylenglycolen als Zusatz zu zementösen Systemen",
EP 1 260 536, 2002; Maeder, U. et al., "Polymers in a solid state",
CA 2480061, 2003; Hirata, T., Kawakami, H., "Method for production of cement dispersant and polycarboxylic
acid type polymer for cement dispersant",
WO 2006/006712, 2006; Koshisaka, S. et al., "Cement dispersant and concrete composition containing the
dispersant",
AU 2004318289, 2006; Bando, H. et al., "Cement dispersant and concrete composition containing the dispersant",
US 7393886, 2008; Sugamata, T. et al., "Cement additives",
WO 2009/050104, 2009; Wang, Z. et al., "Verfahren zur Verwendung von bei der Produktion von Acrylaldehyd
angefallener Flüssigkeit zur Herstellung von Polycarboxylat-Wasserreduzierungsmittel",
CN 10 222 9691, 2011; Wang Z. et al., "Method for preparing polycarboxylic slump-retaining agent from
raffinate after acrolein production",
CN 102558454,
2011; Sulser, U. et al., "Dispergiermittel für Feststoffsuspensionen",
EP 2 578 608, 2011; Kuo, L. et al., "Method for treating clay and clay-bearing aggregates and compositions
thereof",
WO 2013/164471, 2013).
[0008] Bei polymeranalogen Verfahren (z.B. polymeranaloger Veresterung und/oder polymeranaloger
Amidierung) wird im ersten Schritt der Backbone durch radikalische Polymerisation
- teilweise auch in wässrigen Milieu - z.B. aus MAS und/oder AS hergestellt. Im zweiten
Schritt erfolgt die Veresterung der Säuregruppen des Backbones mit einem langkettigen
Alkohol, z.B. Methoxypolyethylenglykol (MPEG, auch MPEG-OH). Analog ist die Amidierung
mit entsprechenden Aminen, z.B. MPEG-NH
2, möglich.
[0009] Alternativ können die Kammpolymere grundsätzlich direkt über die Co-Polymerisation
von z.B. MAS und AS mit z.B. (M)PEG-(Meth)acrylat ((M)PEG-(M)A) erhalten werden. Auch
werden ungesättigte Polyether, wie z.B. Allylpolyethylenglykol (APEG), Methylallylpolyethylenglykol
(TPEG), Isoprenpolyethylenglykol (HPEG) oder Vinyloxybutylpolyethylenglykol (VOBPEG)
als Co-Monomere eingesetzt. In der wissenschaftlichen Literatur sind darüber hinaus
weitere Einsatzstoffe (u.a. Styrol, funktionelle (Meth)acrylate, funktionelle Amine
oder weitere Carbonsäuren und
deren Salze) beschrieben.
[0010] In Abhängigkeit von Einsatzstoffen und Syntheseroute werden Polymere mit unterschiedlichen
Leistungscharakteristiken erhalten. Wichtige Einflussfaktoren sind hierbei generell
die Chemie der Gruppen des Backbones (z.B. Acryl-, Methacryl-, Vinyl-, Allyl-Gruppen,
Maleinsäure), die Flexibilität des Backbones (ebenfalls einstellbar über die zuvor
genannten Gruppen), die Anzahldichte hydrophober Gruppen (z.B. -CH
2-, -CH
3) und hydrophiler Gruppen (z.B. -CH
2-CH
2-O-, -OH), die Anzahldichte ionischer Gruppen (z.B. Carbonsäuregruppen und deren Salze),
die Zusammensetzung der Seitenketten (mehrheitlich (M)PEG, aber auch Polypropylenoxid
(P(PO)) und Polybutylenoxid (P(BuO)), die Länge von Backbone und Seitenketten (typische
Molekulargewichte reichen von ∼ 4000 bis 7000 g/mol für das Backbone und von ∼ 500
bis 10000 g/mol, mehrheitlich 750 bis 5000 g/mol, für die Seitenketten), die Seitenkettenhäufigkeit,
die Ladungsdichte des Polymers oder die Natur und die Stabilität der Bindungen zwischen
Seitenkette und Backbone (Ester, Amid oder Ether). Auch innerhalb der Ester-Bindungen
gibt es Unterschiede in der Stabilität. PCE mit einer hohen Anzahl ionischer Gruppen
adsorbieren stärker an die Zementteilchen und zeigen eine anfänglich stärkere fließverbessernde
Wirkung als PCE mit einer hohen Anzahl an Acrylester- bzw. Methacrylester-Einheiten
(
Flatt, R., Schober I., "Superplasticizers and the Rheology of Concrete", in "Understanding
the Rheology of Concrete", Woodhead Publishing Ltd, 2012, 144;
Ferrari, G. et al., "Influence of Carboxylic Acid-Carboxylic Ester Ratio of Carboxylic
Acid Ester Superplasticizer on Characteristics of Cement Mixtures", International
Concrete Abstracts, 195, 2000, 505;
Lange, A., Plank, J., "Optimization of comb-shaped Polycarboxylate Cement Dispersants
to achieve fast-flowing Mortar and Concrete", J. Appl. Polym. Sci., 2015, 42529).
[0011] Die wässrige Lösung eines zementösen Systems (sog. "Porenlösung") weist einen hohen
pH-Wert, z.B. in der Größenordnung von 12.5 bis 13 (
Flatt, R., Schober I., "Superplasticizers and the Rheology of Concrete", in "Understanding
the Rheology of Concrete", Woodhead Publishing Ltd, 2012, 144) und höher (
Plank, J. et al., Experimental determination of the thermodynamic parameters affecting
the adsorption behaviour and dispersion effectiveness of PCE superplasticizers, Cement
and Concrete Res., 40, 2010, 699 bis 709) auf. Bei diesen Bedingungen hydrolysieren die Ester-Bindungen der Acrylester-Gruppen,
so dass PEG bzw. allgemein die Seitenkette abgespalten wird und als Folge wieder eine
ionische Carboxyl-Gruppe resultiert. Dadurch erhöht sich die lonenstärke des PCE mit
der Zeit, so dass eine längere, fließverbessernde Wirkung des Polymeren beobachtet
wird (
Flatt, R., Schober I., "Superplasticizers and the Rheology of Concrete", in "Understanding
the Rheology of Concrete", Woodhead Publishing Ltd, 2012, 144). Die Ester-Bindungen der Methacrylester-Einheiten sind bezüglich der Hydrolyse stabiler
als die Ester-Bindungen der Acrylester-Einheiten, Amid-Bindungen sind im Allgemeinen
besonders hydrolysestabil. Hiermit kann die Dauer der Fließverbesserung beeinflusst
werden. Die Viskosität eines mit PCE verflüssigten Betonsystems und dessen Fließgeschwindigkeit
werden durch das Verhältnis von hydrophilen zu lipophilen Gruppen (HLB-Wert) bestimmt.
Je höher der Anteil an hydrophilen Gruppen, desto niedriger die Viskosität der Zement-Suspension.
[0012] Eine mögliche Quelle für die bei der Herstellung von PCE benötigte (Meth)acrylsäure
ist die großchemische (Meth)acrolein-Synthese. Bei Acrolein (Acrylaldehyd) bzw. Methacrolein
(Methacrylaldehyd) handelt es sich um die einfachsten ungesättigten Aldehyde, die
bedeutende Zwischenprodukte in der chemischen Industrie darstellen. Beispielsweise
findet (Meth)acrolein als Zwischenprodukt Verwendung für die synthetische Herstellung
von Methionin, Polymeren, Harzen, Arzneimitteln, Pflanzenschutzmitteln und Aromastoffen.
Bei der Herstellung von (Meth)acrolein fällt eine wässrige Lösung von (Meth)acrylsäure
an. Gegenwärtig wird diese Lösung im Falle des Acrolein-Prozesses regelmäßig durch
Verbrennen entsorgt, im Falle von Methacrolein weiter aufgearbeitet.
[0013] Es besteht auch die Möglichkeit, aus der im Abwasser des (Meth)acrolein-Prozesses
verdünnt vorliegenden (Meth)acrylsäure ein Acrylat zu synthetisieren und abzutrennen.
Beschrieben ist beispielsweise die Gewinnung von Natriumacrylat durch Zugabe von Natronlauge
mit anschließender Abtrennung des Natriumacrylats (Sun, W. et al., "Treatment method
of acrolein production residual liquid",
CN 103435470, 2013).
[0014] Auch möglich ist die Oxidation des Rest(meth)acroleins zur (Meth)acrylsäure. Bei
einer Verwendung der bei der Produktion von (Meth)acrylaldehyd anfallenden Flüssigkeit
zur Herstellung von PCE können im Falle des Acrolein-Prozesses die für die Entsorgung
durch Verbrennen entstehenden Kosten eingespart werden. Im Falle von Methacrolein
kann eine alternative Verwendung des noch nicht aufgearbeiteten Prozessstroms erfolgen.
Darüber hinaus könnte auch eine effektive Senkung der Herstellungskosten für Beton-Fließverbesserer
auf PCE-Basis erreicht werden.
[0015] CN 102229691 beschreibt die Co-Polymerisation von in Abwasser des Acrolein-Prozesses enthaltener,
niedrig konzentrierter AS mit ungesättigten Polyethern (APEG, TPEG, HPEG) zu einem
PCE im Zulaufverfahren unter dem Einsatz von Oxidations- und Reduktionsmitteln. Die
Acrylsäure-Konzentration liegt bei 4 % bis 7 %, bezüglich weiterer Nebenkomponenten
ist das beschriebene Abwasser nicht weiter spezifiziert.
[0016] CN 102558454 beschreibt analog die Co-Polymerisation von in Abwasser des Acrolein-Prozesses enthaltener,
niedrig konzentrierter AS mit ungesättigten Polyethern (APEG, TPEG, HPEG sowie Isoprenyl-PEG)
und zusätzlich Hydroxyethyl- und Hydroxylpropyl-(Meth)acrylat sowie (Meth)acrylamid
zu einem PCE im Zulaufverfahren unter dem Einsatz von Oxidations- und Reduktionsmitteln.
Die Acrylsäure-Konzentration liegt bei 4,5 % bis 7 %, die Acroleinkonzentration bei
5,5 bis 6,5%, bezüglich weiterer Nebenkomponenten ist das beschriebene Abwasser nicht
spezifiziert.
[0017] Nachteilig an den in
CN 102229691 und
CN 102558454 beschriebenen Verfahren sind die hohe Verdünnung der Acrylsäure sowie die Gegenwart
von Stabilisatoren, Inhibitoren und weiteren Komponenten, die die radikalische Polymerisation
behindern. Dies führt dazu, dass Reaktionszeiten (im Vergleich zu der Verwendung reiner
Komponenten) relativ lang sind und relativ hohe Konzentrationen an Radikalstartern
eingesetzt werden müssen. Da nach der Lehre der
CN 102229691 und
CN 102558454 die komplette Polymersynthese in der stark verdünnten Lösung stattfindet, ist außerdem
die volumenbezogene Polymerausbeute relativ gering, so dass nach Abschluss der Polymerisation
noch eine Aufkonzentrierung z.B. durch Abdestillation signifikanter Mengen von Wasser
erfolgen muss, wenn höhere Wertstoffkonzentrationen benötigt werden. Gemäß
CN 102229691 und
CN 102558454 wird ein PCE erzeugt, bestehend aus einem C-C-verknüpften Backbone mit funktionalen
Gruppen aus Carboxylatfunktionen (frei oder neutralisiert), im Falle von
CN 102558454 Esterfunktionen der (Meth)acrylate und Seitenketten, die über eine Etherbindung mit
dem Backbone verknüpft sind. Dieses Funktionalitätsmuster, insbesondere die Etherbindung
der Seitenkette, hat ein im Vergleich zu einer analogen Esterbindung in einer Seitenkette
grundsätzlich unterschiedliches Hydrolyseverhalten im Beton und führt zu grundsätzlich
unterschiedlichem Verhalten bezüglich Frühfestigkeit und der Zeitabhängigkeit der
Fließverbesserung (vgl. auch:
Flatt, R., Schober I., "Superplasticizers and the Rheology of Concrete", in "Understanding
the Rheology of Concrete", Woodhead Publishing Ltd, 2012, 144); lediglich das Wasserreduktionsverhalten im Zement ist ähnlich. In
CN 102229691 und
CN 102558454 ist die Verwendung eines ungesättigten Polyethers zwingend vorgeschrieben, da nur
dieser mit der inhibierten, stark verdünnten Acrylsäure in ausreichender Geschwindigkeit
wirtschaftlich umgesetzt werden kann (siehe
CN 102229691 und
CN 102558454, Ansprüche 1). Damit sind Anwendungen, bei denen Esterbindungen der Seitenketten
akzeptiert oder sogar vorteilhaft sind (siehe auch oben) nicht zugänglich. Außerdem
schreiben
CN 102229691 und
CN 102558454 zwingend die Verwendung von Perhydrol, ein eng definiertes Temperaturprogramm (Temperaturprofil),
eine eng definierte Dosierungsstrategie sowie die Zugabe von Reduktions- und Kettenübertragungsmitteln
vor. Aufgrund dieser Einschränkungen und Randbedingungen ist das beschriebene Verfahren
insgesamt sehr komplex und wenig effizient.
[0018] Aufgabe der vorliegenden Erfindung war es daher, einen Prozessstrom aus der (Meth)acrolein-Synthese,
der bisher aufwendig entsorgt oder aufwendig aufgearbeitet werden musste, als Edukt
für die Herstellung von Qualitätsprodukten für die Bauchemie einzusetzen. Dabei wird
insbesondere das durch die Oxidationsreaktion bei der Herstellung von (Meth)acrolein
entstandene Wasser zunächst nicht abgetrennt, sondern dient inklusive des hier enthaltenen
Komponentenspektrums als wässriges Reaktionsmedium für die Polymersynthese.
[0019] Weitere Aufgabe der vorliegenden Erfindung war es, ein nachhaltiges und gleichzeitig
von der Reaktionsführung her robustes Verfahren zu entwickeln, da die Polymerisation
des Backbones bei der Verwendung suboptimaler Eduktmischungen deutlich langsamer und
unvollständiger abläuft als beim Einsatz reiner Komponenten unter gleichen Bedingungen.
Das betrifft auch die Produktqualität, da vorhandene, typische Nebenkomponenten, wie
z.B. Aldehyde, mercaptanbasierte Standardregler desaktivieren, so dass typische Molekulargewichte
zunächst nicht zugänglich sind (siehe oben). Weitere hinderliche Nebenkomponenten
sind Substanzen mit stabilisierender Wirkung, wie z.B. Protoanemonin oder dessen Strukturisomere.
[0020] Aufgabe der vorliegenden Erfindung war es ebenfalls, ein Wertprodukt mit guter Performance
als Fließverbesserer herzustellen, einen Prozess mit auf das Reaktionsvolumen bezogener
hoher Polymerausbeute (Wirtschaftlichkeit) zu entwickeln und eine gut handhabbare
Formulierung mit gleichzeitig hohem Wirkstoffgehalt zur Verfügung zu stellen.
[0021] Diese Aufgaben werden erfindungsgemäß gelöst durch ein Verfahren zur Herstellung
einer Poly(meth)acrylsäure, dadurch gekennzeichnet, dass ein (Meth)acrylsäure enthaltender
Prozessstrom aus der (Meth)acrolein-Synthese der radikalischen Polymerisation unterworfen
wird.
[0022] Insbesondere wird die Aufgabe gelöst durch ein Verfahren zur Herstellung einer Poly(meth)acrylsäure,
dadurch gekennzeichnet, dass ein Prozessstrom aus der (Meth)acrolein-Synthese, der
zwischen 8 und 50 Gew.-% (Meth)acrylsäure enthält, bezogen auf das Gewicht des Prozessstroms,
in Anwesenheit von Wasser, das bei der Oxidationsreaktion der (Meth)acrolein-Synthese
entstanden ist, einer radikalischen Polymerisation unterworfen wird.
[0023] Der Begriff "
(Meth)acrylsäure" bedeutet in diesem Zusammenhang sowohl Methacrylsäure als auch Acrylsäure und/oder
deren Mischungen. Der Begriff
"(Meth)acrolein" bedeutet in diesem Zusammenhang sowohl Methacrolein als auch Acrolein und/oder deren
Mischungen.
[0024] "Polymerisation" bedeutet erfindungsgemäß sowohl Homo- als auch Copolymerisation.
[0025] Bei der erfindungsgemäß hergestellten Poly(meth)acrylsäure kann es sich um Polymethacrylsäure,
Polyacrylsäure oder Copolymere handeln, welche sowohl Acrylsäure-Einheiten als auch
Methacrylsäure-Einheiten enthalten.
Unter dem Begriff
"Polymethacrylsäure" wird erfindungsgemäß ein Polymer verstanden, das normalerweise mindestens 50 Gew.-%,
vorzugsweise mindestens 60 Gew.-%, besonders bevorzugt mindestens 70 Gew.-%, bevorzugt
mindestens 80 Gew.-%, ganz besonders bevorzugt mindestens 90 Gew.-% Methacrylsäure-Einheiten,
bezogen auf das Gewicht des Polymers, umfasst. Unter dem Begriff
"Polyacrylsäure" wird erfindungsgemäß ein Polymer verstanden, das typischerweise mindestens 50 Gew.-%,
vorzugsweise mindestens 60 Gew.-%, besonders bevorzugt mindestens 70 Gew.-%, bevorzugt
mindestens 80 Gew.-%, ganz besonders bevorzugt mindestens 90 Gew.-% Acrylsäure-Einheiten,
bezogen auf das Gewicht des Polymers, umfasst. Bei erfindungsgemäß hergestellten Copolymeren,
welche sowohl Acrylsäure-Einheiten wie auch Methacrylsäure-Einheiten enthalten, beträgt
die Gesamtmenge von (Meth)acrylsäure-Einheiten in der Regel mindestens 70 Gew.-%,
bevorzugt mindestens 80 Gew.-%, ganz besonders bevorzugt mindestens 90 Gew.-% (Meth)acrylsäure-Einheiten,
bezogen auf das Gewicht des Polymers.
[0026] Nach der Polymerisation kann die resultierende Poly(meth)acrylsäure, die mindestens
teilweise in Wasser gelöst ist, das zumindest teilweise bei der Oxidationsreaktion
der (Meth)acrolein-Synthese entstanden ist, einer weiteren Verarbeitung und/oder Funktionalisierung
unterzogen werden, bei der eine funktionalisierte Poly(meth)acrylsäure gebildet wird.
[0027] Unter einer
"weiteren Verarbeitung" wird vorliegend ein Verfahren verstanden, bei dem die Poly(meth)acrylsäure von dem
resultierenden Gemisch zumindest teilweise abgetrennt oder isoliert wird. Des Weiteren
umfasst der Begriff
"weitere Verarbeitung" eine Verdünnung des Gemisches oder seine Verwendung für eine Formulierung. Des Weiteren
umfasst der Begriff
"weitere Verarbeitung" eine physikalische und/oder chemische Modifikation des Polymeren und/oder der Lösung,
die das Polymer enthält.
[0028] Der Begriff
"Funktionalisierung" der Poly(meth)acrylsäure wird für einen Verfahrensschritt verwendet, bei dem Carboxylgruppen
der Poly(meth)acrylsäure zumindest teilweise zu Ester-Gruppen oder AmidGruppen chemisch
umgesetzt werden. Nachfolgend wird die resultierende polymere Verbindung als
"funktionalisierte Poly(meth)acrylsäure" bezeichnet. In einer bevorzugten Ausführungsform werden Carboxylgruppen der Poly(meth)acrylsäure
zumindest teilweise zu Ester-Gruppen umgesetzt. Wie bereits vorstehend ausgeführt,
kann es sich bei der Funktionalisierung der Poly(meth)acrylsäure um eine Veresterung
mit oligomeren, z.B. ethoxylierten und/oder propoxylierten Alkoholen handeln (polymeranaloge
Veresterung). Derartige Alkohole haben typischerweise ein Molekulargewicht Mw zwischen
500 g/mol und 15 000 g/mol, vorzugsweise 750 g/mol und 13 000 g/mol.
[0029] Wie im Stand der Technik hinreichend bekannt, enthält der Prozessstrom aus der (Meth)acrolein-Synthese
neben der (Meth)acrylsäure und Wasser in der Regel weitere Komponenten, welche nachfolgend
als
"Nebenkomponenten" bezeichnet werden. Bei Nebenkomponenten in dem Prozessstrom kann es sich beispielsweise
um folgende Verbindungen handeln:
Formaldehyd, Essigsäure, Maleinsäure, Maleinsäureanhydrid, Terephthalsäure, Ameisensäure,
Benzoesäure, (Meth)acrolein, Allylalkohol, Protoanemonin oder dessen Strukturisomere
und optional Kondensations- und Additionsprodukte insbesondere Ester dieser Komponenten;
Prozessstabilisatoren aus der Gruppe der Hydrochinone, Phenothiazine, N-oxidhaltige
Verbindungen wie TEMPOL und deren Derivate.
[0030] In der Praxis enthält der Prozessstrom aus der (Meth)acrolein-Synthese eine oder
mehrere der oben genannten Nebenkomponenten.
[0031] Die (Meth)acrylsäure-Konzentration in dem erfindungsgemäß verwendeten Prozessstrom
aus der (Meth)acrolein-Synthese liegt typischerweise im Bereich von 8 bis 50 Gew.-%,
und damit deutlich höher als in
CN 102229691 beschrieben. In dem Prozessstrom können außerdem weitere Nebenkomponenten wie z.B.
Formaldehyd, Essigsäure und verschiedene weitere Säuren, Hydrochinon und Furan-Komponenten
enthalten sein.
[0032] Bevorzugt liegt die (Meth)acrylsäure-Konzentration in dem Prozessstrom aus der (Meth)acrolein-Synthese
im Bereich von 8 bis 40 Gew.-%, besonders bevorzugt von 8 bis 30 Gew.%, ganz besonders
bevorzugt von 10 bis 25 Gew.-%, bezogen auf das Gesamtgewicht des Prozessstroms.
[0033] Ein typischer Prozessstrom aus der (Meth)acrolein-Synthese, der im erfindungsgemäßen
Verfahren eigesetzt werden kann, enthält:
8 bis 50 Gew.-% (Meth)acrylsäure,
0,01 bis 20 Gew.-% Formaldehyd,
jeweils 0 bis 10 Gew.-%, bevorzugt 0 bis 5 Gew.-%, ganz besonders bevorzugt 0,1 bis
3 Gew.-% Essigsäure und/oder Ameisensäure,
0 bis 10 Gew.-%, bevorzugt 0 bis 3 Gew.-%, besonders bevorzugt 0,1 bis 3 Maleinsäureanhydrid,
0 bis 2 Gew.-%, bevorzugt 0,05 bis 1 Gew.-% Benzoesäure,
0 bis 2 Gew.-%, bevorzugt 0,01 bis 2 (Meth)acrolein,
0 bis 600 Gew.-ppm, bevorzugt 20 bis 300 Gew.-ppm Hydrochinon und gegebenenfalls
0 bis 0,5 Gew.-% Allylalkohol und/oder
0 bis 1000 Gew.-ppm Protoanemonin,
bezogen auf das Gesamtgewicht des Prozessstroms.
[0034] In einer besonders bevorzugten Ausführungsform enthält der Prozessstrom aus der (Meth)acrolein-Synthese,
der im erfindungsgemäßen Verfahren eigesetzt werden kann:
10 bis 25 Gew.-% (Meth)acrylsäure,
1 bis 5 Gew.-% Formaldehyd,
0,1 bis 5 Gew.-%Essigsäure,
0,05 bis 3 Gew.-% Ameisensäure,
0,01 bis 2 Gew.-% (Meth)acrolein,
0,05 bis 1 Gew.-% Benzoesäure,
20 bis 300 Gew.-ppm Hydrochinon, und
0,1 bis 3 Gew.-% Maleinsäureanhydrid,
bezogen auf das Gesamtgewicht des Prozessstroms.
[0035] Ein typischer Prozessstrom aus der (Meth)acrolein-Synthese, der im erfindungsgemäßen
Verfahren eigesetzt werden kann, hat beispielsweise die in Tabelle 1 wiedergegebene
Zusammensetzung:
Tab. 1: Zusammensetzung eines typischen (meth)acrylsäurehaltigen Prozessstroms aus
der (Meth)acrolein-Synthese (ermittelt durch GC-MS-Analyse)
Komponente |
Konzentration |
Einheit |
|
|
|
(Meth)acrylsäure |
8 bis 30 |
Gew.-% |
Formaldehyd |
0 bis 10 |
Gew.-% |
Essigsäure |
0,5 bis 5,0 |
Gew.-% |
Maleinsäureanhydrid/Maleinsäure |
0 bis 3,0 |
Gew.-% |
Ameisensäure |
0 bis 2,0 |
Gew.-% |
Benzoesäure |
0 bis 2,0 |
Gew.-% |
(Meth)acrolein |
0 bis 5,0 |
Gew.-% |
Allylalkohol |
0 bis 0,5 |
Gew.-% |
Hydrochinon |
0 bis 600 |
Gew.-ppm |
Protoanemonin |
0 bis 1000 |
Gew.-ppm |
Wasser |
Rest |
|
[0036] Typischerweise ist das erfindungsgemäße Verfahren dadurch gekennzeichnet, dass
- a. der Prozessstrom eine oder mehrere Verbindungen, ausgewählt aus Formaldehyd, Essigsäure,
Maleinsäure, Maleinsäureanhydrid, Terephthalsäure, Ameisensäure, Benzoesäure, (Meth)acrolein,
Allylalkohol, Protoanemonin oder dessen Strukturisomere, Terephthalaldehyd, Milchsäure,
Laktid, Diformylfuran, Hydroxyzimtsäure oder deren Strukturisomere oder Dihydropyrancarbaldehyd
und optional Kondensations- und Additionsprodukte oder Ester dieser Komponenten, enthält
und/oder
- b. der Prozessstrom Prozessstabilisatoren, ausgewählt aus Hydrochinonen, Phenothiazinen,
N-oxidhaltigen Verbindungen, vorzugsweise 4-hydroxy-2,2,6,6-tetramethylpiperidin-1-oxyl,
und/oder deren Kombination, enthält.
[0037] Während der Bildung der Poly(meth)acrylsäure können die oben genannten Nebenkomponenten
zu deren Folgeprodukten chemisch umgesetzt werden. Der Begriff
"Folgeprodukte" in der vorliegenden Patentanmeldung bezieht sich somit auf Verbindungen, die während
der Bildung der Poly(meth)acrylsäure aus Nebenkomponenten gebildet werden.
[0038] Die Polymerisation der (Meth)acrylsäure erfolgt optional in Gegenwart von Reglern,
radikalbildenden Initiatoren, vorzugsweise wässrigen Persulfatlösungen, besonders
bevorzugt Lösungen von Natrium-, Kalium- oder Ammoniumpersulfaten, wie Na
2S
2O
8; und/oder Reduktionsmitteln, bevorzugt NaHSO
3-Lösungen, Azo-Initiatoren oder organischen Peroxid-Initiatoren, bevorzugt tert.-Butylhydroperoxid,
oder einer Kombination aus mindestens einer Eisen-Verbindung mit H
2O
2-Lösung (Fentons Reagenz). Dabei kann dem Reaktionsgemisch gegebenenfalls zusätzliche
(Meth)acrylsäure zugefügt werden.
[0039] Vorzugsweise liegt die Reaktionstemperatur während der Polymerisation zwischen 20
und 150 °C, besonders bevorzugt zwischen 80 und 120 °C.
[0040] Die resultierende Poly(meth)acrylsäure liegt teilweise oder vollständig gelöst in
Wasser vor, das aus der Oxidationsreaktion bei der Herstellung von (Meth)acrolein
chemisch entstanden ist. Die Poly(meth)acrylsäure kann weiter verarbeitet und funktionalisiert
werden, bevorzugt verestert. Die Poly(meth)acrylsäure und/oder die funktionalisierte
Poly(meth)acrylsäure kann in fester Form oder teilweise oder vollständig gelöst in
Wasser vorliegen, das gegebenenfalls aus der Oxidationsreaktion stammt, das bei der
Herstellung von (Meth)acrolein chemisch entstanden ist.

Bevorzugt wird der Prozessstrom zur Deaktivierung der Aldehyde oder anderer störender
Bevorzugt wird der Prozessstrom zur Deaktivierung der Aldehyde oder anderer störender
Nebenkomponenten vorbehandelt, bevorzugt mit Harnstoff. Die Vorbehandlung der Aldehyde
(beispielsweise Formaldehyd) erfolgt mit unterstöchiometrischen Mengen oder überstöchiometrischen
Mengen Harnstoff, bevorzugt mit äquimolar eingesetztem Harnstoff oder anderen geeigneten
Fällungsmedien. Das gegebenenfalls in Lösung verbleibende Produkt kann im Prozessstrom
verbleiben oder wird nach Ausfällung abfiltriert. Der so behandelte Prozessstrom oder
ein unbehandelter Prozessstrom wird der Polymerisation zugeführt.
[0041] Die wässrige radikalische Polymerisation erfolgt vorzugsweise in Gegenwart eines
Radikalinitiators und/oder eines Molekulargewichtsreglers, vorzugsweise bei einem
pH < 4, besonders bevorzugt bei einem pH < 3.
[0042] Als Radikalinitiator kommt insbesondere Natrium-, Kalium- oder Ammoniumperoxodisulfat
in Betracht. Ebenfalls geeignet ist ein Redoxpaar z.B. auf Basis von H
2O
2 / Fe
2+ (Fentons Reagenz). Weiterhin geeignet sind wasserlösliche Azo-Initiatoren, wie z.B.
Azobis(2-amidinopropan)dihydrochlorid.
[0043] Als geeignete Molekulargewichtsregler können beispielsweise Alkalisulfite oder Hydrogensulfite
eingesetzt werden. Ebenfalls verwendet werden können Phosphinsäurederivate sowie organische
Verbindungen, welche eine Thiolgruppe enthalten, wie z.B. Mercaptoethanol.
[0044] In einer bevorzugten Ausgestaltung des erfindungsgemäßen Verfahrens wird die Polymerisation
in Gegenwart einer Kombination aus Natriumpersulfat und Natriumhydrogensulfit durchgeführt.
[0045] In einer weiteren bevorzugten Ausgestaltung des erfindungsgemäßen Verfahrens wird
die Polymerisation in Gegenwart von Ammoniumperoxodisulfat durchgeführt.
[0046] Die (Meth)acrylsäure wird erfindungsgemäß im wässrigen Medium, vorzugsweise bei Temperaturen
von 20 bis 150 °C, besonders bevorzugt bei Temperaturen von 80 bis 120 °C in Gegenwart
von wasserlöslichen Radikalbildnern, Reduktionsmitteln und Reglern, wie z.B. Schwefelverbindungen
mit Schwefel in der Oxidationsstufe +IV, polymerisiert. Die Polymerisation kann unter
Normaldruck, unter erhöhtem Druck oder auch unter vermindertem Druck durchgeführt
werden. Das Arbeiten unter erhöhtem Druck bietet sich in den Fällen an, in denen leichtflüchtige
Bestandteile im System verbleiben sollen, z. B. wenn man Schwefeldioxid als Regler
einsetzt oder die Polymerisation bei Temperaturen oberhalb des Siedepunktes von Wasser
durchführt. Die Polymerisation erfolgt vorteilhafterweise unter einer Inertgasatmosphäre.
[0047] Die erhaltene Poly(meth)acrylsäure kann isoliert oder verestert werden.
[0048] In einer bevorzugten Ausgestaltung des erfindungsgemäßen Verfahrens wird die erhaltene
Poly(meth)acrylsäure mit (Methoxy)polyethylenglykol verestert. Die Veresterung des
erhaltenen Poly(meth)acrylsäure kann in Gegenwart oder auch in Abwesenheit von Katalysatoren
erfolgen. Zur Veresterung können unter anderem Säuren oder Basen beigegeben werden.
Als Säure-Katalysatoren verwendet man beispielsweise Schwefelsäure, p-Toluolsulfonsäure,
Benzolsulfonsäure, Methansulfonsäure, Phosphorsäure, phosphorige Säure oder Chlorwasserstoffsäure.
[0049] In einer bevorzugten Ausgestaltung des erfindungsgemäßen Verfahrens wird kein Katalysator
eingesetzt.
[0050] Die Veresterung kann beispielsweise so durchgeführt werden, dass man die wässrigen
Lösungen nach der Polymerisation gegebenenfalls mit einer als Katalysator wirkenden
Säure und (Methoxy)polyethylenglykol versetzt und während der Reaktion Wasser abdestilliert.
Die Destillation des Wassers aus der Mischung erfolgt meistens unter Atmosphärendruck,
kann jedoch auch im Vakuum durchgeführt werden. Oft ist es von Vorteil, wenn während
der Destillation ein Gasstrom durch die Reaktionsmischung geleitet wird, um das Wasser
und andere flüchtige Anteile rascher zu entfernen. Als Gasstrom kann Luft oder Stickstoff
verwendet werden. Man kann das Wasser jedoch auch unter vermindertem Druck entfernen
und zusätzlich einen Gasstrom durch das Reaktionsgemisch leiten. Alternativ kann auch
ein Schleppmittel, wie z.B. Toluol, eingesetzt werden, um die Effizienz der Destillation
zu erhöhen. Um das Wasser bzw. das Wasser-Schleppmittelgemisch aus dem Reaktionsgemisch
zu destillieren, muss man der Mischung Energie zuführen. Geeignete Apparate hierfür
sind beispielsweise beheizbare Rührkessel, Rührkessel mit außenliegenden Wärmetauschern,
Rührkessel mit innenliegenden Wärmetauschern und Dünnschichtverdampfer. Das verdampfende
Wasser bzw. das Wasser-Schleppmittelgemisch wird über eine Brüdenleitung aus dem Reaktionsmedium
abgeführt und in einem Wärmetauscher (ggf. in einer Kolonne) kondensiert. Wird kein
Schleppmittel eingesetzt und enthält das Destillat nur geringe Mengen an organischen
Inhaltsstoffen, kann es über eine Kläranlage entsorgt werden.
[0051] Im Anschluss oder gleichzeitig mit dem Entfernen von Wasser aus dem Reaktionsgemisch
tritt eine Kondensationsreaktion zwischen der Poly(meth)acrylsäure und dem (Methoxy)polyethylenglykol
ein. Das dabei entstehende Wasser wird ebenfalls aus dem Reaktionsmedium entfernt.
Die Veresterung wird beispielsweise bei Temperaturen zwischen 100 und 250 °C durchgeführt.
Die Temperatur richtet sich dabei nach der Lage des Gleichgewichts der Veresterungsreaktion,
dem Reaktionsapparat und der Verweilzeit. In diskontinuierlich betriebenen Rührkesseln
benötigt man beispielsweise 1 bis 15 Stunden und führt die Kondensation meistens in
einem Temperaturbereich von 100 bis 250 °C durch.
[0052] Bevorzugt erfolgt die Veresterung bei erhöhten Temperaturen von 120 bis 200 °C, insbesondere
150 bis 180 °C. Dadurch kann die Ausbeute signifikant gegenüber niedrigeren Temperaturen
verbessert werden.
[0053] In einer Verfahrensvariante kann man zunächst die Säuregruppen enthaltende Poly(meth)acrylsäure
entwässern und das dabei erhaltene Pulver oder Granulat mit dem (Methoxy)polyethylenglykol
kondensieren.
[0054] Am Ende der Reaktion wird das Reaktionsgemisch abgekühlt und ggf. in Wasser gelöst.
Gleichzeitig oder im Anschluss an das Lösen des Kondensationsprodukts kann gegebenenfalls
eine Neutralisation verbliebener Säuregruppen erfolgen. Als Neutralisationsmittel
werden (Erd-)Alkalimetall(hydr)oxide in fester Form oder in Form von 10 bis 70 %-igen
wässrigen Lösungen oder Aufschlämmungen in Wasser verwendet. Beispiele für geeignete
Basen sind Lithiumhydroxid, Natriumhydroxid, Kaliumhydroxid, Calciumoxid, Calciumhydroxid,
Magnesiumoxid, Magnesiumhydroxid, Aluminiumoxid und Aluminiumhydroxid. Je nach Neutralisationsgrad
können die wässrigen Lösungen der Copolymerester pH-Werte zwischen 2,5 und 7 haben.
[0055] Nach der Kondensation kann die Reaktionsmasse auch unverdünnt bleiben. Beim Abkühlen
unter 60 °C erstarrt sie zu einer wachsartigen Masse, die leicht wieder aufgeschmolzen
werden kann. Daraus ergeben sich Variationen für den Transport. Man kann beispielsweise
die Reaktionsmasse in Fässer abfüllen, aus denen das Kondensationsprodukt wieder aufgeschmolzen
werden kann. Dazu eignen sich beheizbare und wärmeisolierte Kesselwagen und Lagerbehälter.
[0056] Alternativ ist es auch möglich, eine wässrige Lösung mit einem Wertstoffgehalt von
60 bis 90 % herzustellen und zu handhaben. Die Viskosität solcher Lösungen beträgt
beispielsweise 1000 bis 100.000 mPas.
[0057] Durch Zugabe von Wasser kann die Erstarrungstemperatur gesenkt werden. Hierbei kann
vorzugsweise das während der Veresterung abdestillierte Wasser wieder eingesetzt werden.
Die Schmelztemperatur der Polymerschmelze ist dabei u.a. abhängig von der Länge der
Seitenkette. Ein typisches Produkt mit einer MPEG1000-Seitenkette schmilzt beispielsweise
ohne Wasser im Bereich von 30 °C bis 40 °C, ist aber danach noch sehr zähflüssig.
Durch Zusatz geringer Mengen von Wasser erhält man ein schon bei Raumtemperatur fließfähiges
Konzentrat. Durch Zusatz von 10 bis 30 Gew.-% Wasser lassen sich die Lösungen bei
20 bis 40 °C gut handhaben. Diese Wirkung des Wassers (Erniedrigung der Schmelzviskosität)
kann für die Handhabung der Schmelze von Vorteil sein. Dadurch kann die Lagertemperatur
gesenkt werden.
[0058] Erfindungsgemäß hergestellte Poly(meth)acrylsäuren und funktionalisierte Poly(meth)acrylsäuren,
und insbesondere deren erfindungsgemäß hergestellten wässrige Lösungen, können vorteilhaft
als Fließverbesserer, vorzugsweise für Beton, Asphalt oder Teer, verwendet werden.
Die erfindungsgemäß hergestellten Poly(meth)acrylsäuren und funktionalisierte Poly(meth)acrylsäuren
verhalten sich bezüglich der erzielbaren Fließverbesserung und Verarbeitungsdauer
ähnlich gut wie vergleichbare kommerziell erhältliche Fließverbesserer für die Bauchemie.
Die Erfindung betrifft die Verwendung der Poly(meth)acrylsäuren und funktionalisierten
Poly(meth)acrylsäuren als Additive, Fließverbesserer und Wasserreduktionsmittel.
[0059] Erfindungsgemäß hergestellte Poly(meth)acrylsäuren und funktionalisierte Poly(meth)acrylsäuren
sind demnach wichtige Zwischenprodukte für die Bauchemie.
[0060] Gegenstand der vorliegenden Erfindung ist somit auch die durch das hier beschriebene
erfindungsgemäße Verfahren erhältliche Poly(meth)acrylsäure sowie die durch das hier
beschriebene erfindungsgemäße Verfahren erhältliche funktionalisierte Poly(meth)acrylsäure.
[0061] Gegenstand der vorliegenden Erfindung ist auch die Verwendung eines (Meth)acrylsäure
enthaltenden Prozessstroms aus der (Meth)acrolein-Synthese für die radikalische Homo-
oder Co-Polymerisation. Unter
"Homo-Polymerisation" wird im vorliegenden Fall verstanden, dass dem Prozessstrom vor der Polymerisation
keine weiteren polymerisierbaren Monomere zugegeben werden bzw. der Prozessstrom während
der Polymerisation nicht mit weiteren polymerisierbaren Monomeren vermischt wird.
Unter Co-Polymerisation wird im vorliegenden Fall verstanden, dass dem Prozessstrom
vor oder während der Polymerisation weitere polymerisierbare Monomere zugegeben werden,
insbesondere auch die Mischung aus Acrylsäure und Methacrylsäure (sowohl in Prozessstrom-Form
als auch in synthetischer Qualität), und/oder Maleinsäure.
[0062] Die vorliegende Erfindung wird anhand der nachfolgenden Beispiele näher beschrieben,
die jedoch nicht einschränkend sind.
Beispiele
Charakterisierung und Vorbehandlung des Prozessstroms (Beispiele 1 bis 4)
[0063] In den folgenden Beispielen wurde ein acrylsäurehaltiger Prozessstrom mit einer Konzentration
von
14,1 Gew.-% |
Acrylsäure, |
2,9 Gew.-% |
Formaldehyd, |
0,9 Gew.-% |
Essigsäure, |
0,2 Gew.-% |
Ameisensäure, |
0,1 Gew.-% |
Acrolein, |
0,2 Gew.-% |
Benzoesäure, |
129 ppm |
Hydrochinon, |
0,8 Gew.-% |
Maleinsäureanhydrid |
bezogen auf das Gewicht des Prozessstroms, eingesetzt.
[0064] Die vorhandenen Aldehyde (vornehmlich Formaldehyd) wurden mit äquimolar eingesetztem
Harnstoff gefällt und abfiltriert, um eine bestimmungsgemäße Polymerisation zu erleichtern.
Beispiel 1
[0065] In einem gerührten 5 L-Doppelmantelglasreaktor mit Rückflusskühler werden 400 g deionisiertes
Wasser vorgelegt und auf 100 °C erhitzt.
[0066] Im Anschluss werden innerhalb von 7 Stunden 2624 g eines Gemisches aus 2475 g des
acrylsäurehaltigen Prozessstroms und 149 g Methacrylsäure sowie 336 g einer 40%-igen
NaHSO
3-Lösung zu dosiert. Zeitgleich werden innerhalb von 8 Stunden 524 g einer 23%-igen
Na
2S
2O
8-Lösung zu dosiert.
[0067] Nach Ende der Dosierung wird die Reaktionsmischung für 1 Stunde bei 100°C gehalten.
[0068] Anschließend wird der Rückflusskühler durch eine Claissenbrücke ersetzt und unter
einem Vakuum von 50 mbar 2222 g Wasser abgezogen.
[0069] Dann werden 2200 g MPEG 1000 in den Reaktor zugegeben und unter Vakuum für weitere
4 Stunden Wasser abgezogen. Die Temperatur wird dabei bis auf 180 °C erhöht.
[0070] Der Reaktor wird auf ca. 80 °C abgekühlt und entleert.
Beispiel 2
[0071] In einem gerührten 5 L-Doppelmantelglasreaktor mit Rückflusskühler werden 250 g deionisiertes
Wasser vorgelegt und auf 100 °C erhitzt.
[0072] Im Anschluss werden innerhalb von 2 Stunden 190 g einer 40%-igen NaHSO
3-Lösung zu dosiert. Zeitgleich wird innerhalb von 3 Stunden 325 g einer 30%-igen Na
2S
2O
8-Lösung zu dosiert.
[0073] 10 Minuten nach Beginn der NaHSO
3- und der Na
2S
2O
8-Dosierung wird ein weiterer Zustrom gestartet, der innerhalb von 2 Stunden 1641 g
eines Gemisches aus 1578 g des acrylsäurehaltigen Prozessstroms und 93 g Methacrylsäure
dosiert.
[0074] Nach Ende der Dosierungen wird der Rückflusskühler durch eine Claissenbrücke ersetzt
und unter einem Vakuum von 50 mbar 1293 g Wasser abgezogen.
[0075] Dann werden 2750 g MPEG 2000 in den Reaktor zugegeben und unter Vakuum für weitere
4 Stunden Wasser abgezogen. Die Temperatur wird dabei bis auf 180 °C erhöht.
[0076] Der Reaktor wird auf ca. 80 °C abgekühlt und entleert.
Beispiel 3
[0077] In einem 500mL-Rundkolben mit Destillationskolonne werden 110 g MPEG1000 vorgelegt
und aufgeschmolzen und auf 150°C erhitzt.
[0078] Im Anschluss wird innerhalb von 3 Stunden 170 g des acrylsäurehaltigen Prozessstroms
dosiert. Zeitgleich wird innerhalb von 4 Stunden eine Lösung von 1,32 g TBPEH (Tert-Butylperoxy-2-Ethylhexanoat)
in 262,68 g Toluol dosiert.
[0079] Während der Dosierung wird Wasser und Toluol über Kopf abgezogen.
[0080] Nach Ende der Dosierung wird die Temperatur der Mischung auf 170 °C erhöht und weiterhin
Wasser und Toluol abgezogen.
[0081] Nach weiteren 3 Stunden wird der Kolben auf ca. 80 °C abgekühlt und entleert.
Beispiel 4
[0082] In einem gerührten 1 L-Doppelmantelglasreaktor mit Rückflusskühler werden 100 g deionisiertes
Wasser vorgelegt und auf 100 °C erhitzt.
[0083] Im Anschluss werden innerhalb von 7 Stunden 630 g eines Gemisches aus 592,7 g des
acrylsäurehaltigen Prozessstroms und 37,3 g Methacrylsäure sowie 126 g einer 40%-igen
NaHSO
3-Lösund zu dosiert. Zeitgleich wird innerhalb von 8 Stunden 131 g einer 23%-igen Na
2S
2O
8-Lösung zu dosiert.
[0084] Nach Ende der Dosierung wird die Reaktionsmischung noch für 1 Stunden bei 100 °C
gehalten.
[0085] Von der erhaltenen Polymerlösung werden 200 g in einem 500 mL Rundkolben mit Claissenbrücke
vorgelegt und bei einem Vakuum von ca. 50 mbar 145 g Wasser abgezogen.
[0086] Dann werden 110 g MPEG1000 zugegeben, 50 mbar Vakuum angelegt und die Mischung bis
auf 170 °C erhitzt. Dabei wird weiterhin Wasser abgezogen.
[0087] 5 Stunden nach Zugabe des MPEG1000 wird die Mischung auf ca. 80 °C abgekühlt und
der Kolben entleert.
[0088] Die im Rahmen der Erfindung hergestellten Polymere wurden in anwendungstechnischen
Untersuchungen hinsichtlich ihrer Eignung und Wirksamkeit als Beton-Fließverbesserer
getestet. Alle Polymere wurden den gleichen Prozeduren unterworfen.
[0089] Eingesetzte Versuchsapparatur und Metallformen sind in der Tabelle 2 und die verwendeten
Rohstoffe in der Tabelle 3 aufgeführt. Die eingesetzten Metallformen sind außerdem
in Abbildung 2 dargestellt.
Tab. 2: Versuchsapparatur und Metallformen
Mörtelmischer |
ToniMIX Bauform 6214 |
Metallform 1 |
konischer Kegelstumpf nach Norm DIN EN 12350-5 (Abmessungen verkleinert um den Faktor
2,35) |
|
D = 85 mm, d = 55 mm, h = 85 mm |
Metallform 2 |
konischer Kegelstumpf nach Norm DIN EN 12350-5 (Abmessungen verkleinert um den Faktor
3,25) |
|
D = 62 mm, d = 40 mm, h = 62 mm |
Tab. 3: Verwendete Rohstoffe
CEN Normsand nach DIN EN 196-1, Normsand GmbH |
Portlandzement CEM I 52,5 N "White" EN 197-1, Lafarge Holcim |
Portlandzement CEM I 42,5N DIN EN 197-1, Spenner Zement |
[0090] Im Folgenden werden die anwendungstechnischen Untersuchungen und deren Ergebnisse
beschrieben.
Anwendungstechnische Prüfung des Ausbreitmaßes zur Bestimmung der fließverbessernden
Eigenschaften bei unterschiedlichen PCE-Konzentrationen
[0091] Es wird 1350 g Normsand in den Sandzulaufbehälter des Mörtelmischers sowie 450 g
Zement in dessen Rührschüssel eingewogen.
[0092] Der Fließverbesserer wird als wässrige Polymer-Lösung in ein Becherglas eingewogen
und mit der zum Erreichen einer Gesamtwassermenge von 225 g benötigten Wassermenge
gemischt. Die Menge der Polymer-Lösung wird (unter Berücksichtigung der Konzentration
des Fließverbesserer in der wässrigen Lösung) gemäß der zu untersuchenden Wirkstoffkonzentration
im Zement gewählt.
[0093] Nach Zugabe der wässrigen Polymer-Lösung zu dem in der Schüssel befindlichen Zement
wird diese in Arbeitsstellung gebracht und das automatische Programm EN196-1 gestartet:
Die Mischung wird für 30 sec mit einer Umdrehungszahl von 65 U/min gerührt, unter
weiterem Rühren wird dann über einen Zeitraum von 30 sec der eingewogene Normsand
in die Mischschüssel dosiert.
[0094] Nach der Zugabe des Normsandes wird die Mörtelmischung für 30 sec mit einer Umdrehungszahl
von 130 U/min weiter gerührt.
[0095] Anschließend folgt eine Ruhephase von 90 sec, in der während der ersten 30 sec die
Mischschüssel innen mittels einem Schaber abgestreift wird.
[0096] Zum Abschluss des Mischvorgangs wird noch einmal für 60 sec bei 130 U/min gerührt.
[0097] Nach Beendigung des Programms wird der Mörtel mit einem Schaber vom Rand der Schüssel
entfernt, durchmischt und in die mit VE-Wasser angefeuchtete Metallform 1, die auf
einer ebenfalls mit VE-Wasser angefeuchteten Metallplatte steht, gefüllt.
[0098] Durch 10-maliges Stochern mit einem Spatel werden eventuelle Lufteinschlüsse entfernt
und der Mörtel verdichtet.
[0099] Anschließend wird die Metallform zügig senkrecht nach oben angehoben, so dass der
Mörtel auslaufen kann.
[0100] Nach dem Abbinden und Trocknen des Mörtels (in der Regel am nächsten Tag), wird das
Ausbreitmaß in zwei Richtungen vermessen und der Mittelwert in Millimetern angegeben.
[0101] Die Ergebnisse sind in den Tabellen 4 und 5 zusammengefasst.
Tab. 4: Ausbreitmaße in Portlandzement CEM I 52,5 N "White", DIN EN 197-1, Lafarge
Holcim
Fließverbesserer |
Konzentration kgPCE/kgZement |
Ausbreitmaß (Metallform 1) mm |
|
Beispiel 1 |
0,20 % |
177,5 |
|
Beispiel 1 |
0,30 % |
224,0 |
|
Beispiel 1 |
0,40 % |
229,3 |
leichtes Bluten |
Beispiel 1 |
0,50 % |
236,5 |
leichtes Bluten |
Beispiel 1 |
0,75 % |
243,8 |
Bluten |
|
|
|
|
Beispiel 2 |
0,20% |
142 |
|
Beispiel 2 |
0,30% |
198,5 |
|
|
|
|
|
Beispiel 3 |
0,30% |
175 |
|
Beispiel 3 |
0,50% |
253 |
leichtes Bluten |
|
|
|
|
Beispiel 4a) |
0,10 % |
87,8 |
|
Beispiel 4a) |
0,20 % |
195,5 |
|
Beispiel 4a) |
0,50 % |
252,3 |
|
Beispiel 4b) |
0,10 % |
87 |
|
Beispiel 4b) |
0,20 % |
211 |
|
Beispiel 4b) |
0,50 % |
248,3 |
leichtes Bluten |
a), b) Von der Rezeptur nach Beispiel 4 wurden zwei Ansätze hergestellt, die beide nach
der beschriebenen Vorgehensweise getestet wurden. Die Ergebnisse sind in der Tabelle
mit "Beispiel 4a)" und "Beispiel 4b)" gekennzeichnet. |
Tab. 5: Ausbreitmaße in Portlandzement CEM I 42,5 N, DIN-EN 197-1, Spenner Zement
Fließverbesserer |
Konzentration kgPCE/kgZement |
Ausbreitmaß (Metallform 1) mm |
|
Beispiel 2 |
0,40 % |
150,8 |
leichtes Bluten, Mörtel nicht vollständig abgebunden |
Beispiel 3 |
0,40 % |
245 |
|
|
|
|
|
Beispiel 4a) |
0,10 % |
95,8 |
|
Beispiel 4a) |
0,30 % |
136,0 |
|
Beispiel 4a) |
0,50 % |
201,3 |
|
Beispiel 4a) |
1,00 % |
213,8 |
|
|
|
|
|
Beispiel 4b) |
0,10 % |
107,8 |
|
Beispiel 4b) |
0,30 % |
196,5 |
|
Beispiel 4b) |
1,00 % |
217,3 |
Bluten |
a), b) Von der Rezeptur nach Beispiel 4 wurden zwei Ansätze hergestellt, die beide nach
der beschriebenen Vorgehensweise getestet wurden. Die Ergebnisse sind in der Tabelle
mit "Beispiel 4a)" und "Beispiel 4b)" gekennzeichnet. |
Anwendungstechnische Prüfung der Langzeitwirkung der fließverbessernden Eigenschaften
(Konsistenzerhaltung des Mörtels)
[0102] Es werden 1350 g Normsand in den Sandzulaufbehälter des Mörtelmischers sowie 450
g Zement in dessen Rührschüssel eingewogen.
[0103] Der Fließverbesserer wird als wässrige Polymer-Lösung in ein Becherglas eingewogen
und mit der zum Erreichen einer Gesamtwassermenge von 225 g benötigten Wassermenge
gemischt. Die Menge der Polymer-Lösung wird (unter Berücksichtigung der Konzentration
des Fließverbesserer in der wässrigen Lösung) gemäß der zu untersuchenden Wirkstoffkonzentration
im Zement gewählt.
[0104] Nach Zugabe der wässrigen Polymer-Lösung zu dem in der Schüssel befindlichen Zement
wird diese in Arbeitsstellung gebracht und das automatische Programm EN196-1 gestartet:
Die Mischung wird für 30 sec mit einer Umdrehungszahl von 65 U/min gerührt, unter
weiterem Rühren wird dann über einen Zeitraum von 30 sec Normsand in die Mischschüssel
dosiert.
[0105] Nach der Zugabe des Normsandes wird die Mörtelmischung für 30 sec mit einer Umdrehungszahl
von 130 U/min weiter gerührt.
[0106] Anschließend folgt eine Ruhephase von 90 sec, in der während der ersten 30 sec die
Mischschüssel innen mittels einem Schaber abgestreift wurde.
[0107] Zum Abschluss des Mischvorgangs wird noch einmal für 60 sec bei 130 U/min gerührt.
[0108] Nach Beendigung des Programms wird der Mörtel mit einem Schaber vom Rand der Schüssel
entfernt, durchmischt und in die mit VE-Wasser angefeuchtete Metallform 2, die auf
einer ebenfalls mit VE-Wasser angefeuchteten Metallplatte steht, gefüllt.
[0109] Durch 10-maliges Stochern mit einem Spatel wurden eventuelle Lufteinschlüsse entfernt
und der Mörtel verdichtet.
[0110] Anschließend wird die Metallform zügig senkrecht nach oben angehoben, so dass der
Mörtel auslaufen kann.
[0111] Im Anschluss wird die Mischschüssel erneut in Arbeitsstellung gebracht und über das
manuelle Programm eine Umdrehungszahl von 65 U/min eingestellt.
[0112] Nach zusätzlichen Mischzeiten von insgesamt 15 min, 30 min, 45 min, 60 min, 75 min
und 90 min wird jeweils erneut die Metallform wie oben beschrieben befüllt, Lufteinschlüsse
entfernt und anschließend zügig senkrecht nach oben angehoben, so dass der Mörtel
auslaufen kann.
[0113] Nach dem Abbinden und Trocknen des Mörtels (in der Regel am nächsten Tag), werden
die verschiedenen Ausbreitmaße in zwei Richtungen vermessen und der Mittelwert in
Millimetern angegeben.
[0114] Den Ergebnissen der ersten Messung wird der Zeitpunkt 0 zugewiesen, den Folgemessungen
dann die zusätzlichen Gesamtmischzeiten.
[0115] Die Ergebnisse sind in den Tabellen 6 und 7 zusammengefasst.
Tab. 6: Ausbreitmaße in Portlandzement CEM I 42,5 N, DIN-EN 197-1, Spenner Zement
in Abhängigkeit von der Zeit
|
Beispiel 3 |
Beispiel 3 |
Beispiel 4a) |
Beispiel 4b) |
Konzentration kgPCE/kgZement |
0,75 % |
1,0 % |
0,5 % |
0,5 % |
Zus. Mischzeit min. |
Ausbreitmaß (Metallform 2) mm |
Ausbreitmaß (Metallform 2) mm |
Ausbreitmaß (Metallform 2) mm |
Ausbreitmaß (Metallform 2) mm |
0 |
162 |
168 |
147,5 |
152,5 |
15 |
169 |
169 |
104 |
105 |
30 |
101,5 |
146,5 |
87,5 |
105 |
45 |
93,5 |
94 |
80 |
102,5 |
60 |
75,5 |
91 |
70 |
100 |
75 |
64 |
81 |
60 |
90 |
90 |
63 |
64 |
|
67,5 |
a), b) Von der Rezeptur nach Beispiel 4 wurden zwei Ansätze hergestellt, die beide nach
der beschriebenen Vorgehensweise getestet wurden. Die Ergebnisse sind in der Tabelle
mit "Beispiel 4a)" und "Beispiel 4b)" gekennzeichnet. |

Anwendungstechnische Prüfung des Ausbreitmaßes zur Bestimmung der fließverbessernden
Eigenschaften bei variierenden Wasser/Zement- Verhältnissen
[0116] Es werden 1350 g Normsand in den Sandzulaufbehälter des Mörtelmischers sowie 450
g Zement in dessen Rührschüssel eingewogen.
[0117] Der Fließverbesserer wird als wässrige Polymer-Lösung in ein Becherglas eingewogen
und mit der zum Erreichen des zu untersuchenden Wasser/Zement-Verhältnisses (w/z-Verhältnis)
benötigten Wassermenge gemischt. Die Menge der Polymer-Lösung wird (unter Berücksichtigung
der Konzentration des Fließverbesserer in der wässrigen Lösung) gemäß der zu untersuchenden
Wirkstoffkonzentration im Zement gewählt.
[0118] Nach Zugabe der wässrigen Polymer-Lösung zu dem in der Schüssel befindlichen Zement
wird diese in Arbeitsstellung gebracht und das automatische Programm EN196-1 gestartet:
[0119] Die Mischung wird für 30 sec mit einer Umdrehungszahl von 65 U/min gerührt, unter
weiterem Rühren wird dann über einen Zeitraum von 30 sec der eingewogene Normsand
in die Mischschüssel dosiert.
[0120] Nach der Zugabe des Normsandes wird die Mörtelmischung für 30 sec mit einer Umdrehungszahl
von 130 U/min weiter gerührt.
[0121] Anschließend folgt eine Ruhephase von 90 sec, in der während der ersten 30 sec die
Mischschüssel innen mittels einem Schaber abgestreift wird.
[0122] Zum Abschluss des Mischvorgangs wurde noch einmal für 60 sec bei 130 U/min gerührt.
[0123] Nach Beendigung des Programms wird der Mörtel mit einem Schaber vom Rand der Schüssel
entfernt, durchmischt und in die mit VE-Wasser angefeuchtete Metallform 1, die auf
einer ebenfalls mit VE-Wasser angefeuchteten Metallplatte steht, gefüllt.
[0124] Durch 10-maliges Stochern mit einem Spatel werden eventuelle Lufteinschlüsse entfernt
und der Mörtel verdichtet.
[0125] Anschließend wird die Metallform zügig senkrecht nach oben angehoben, so dass der
Mörtel auslaufen kann.
[0126] Nach dem Abbinden und Trocknen des Mörtels (in der Regel am nächsten Tag), wird das
Ausbreitmaß in zwei Richtungen vermessen und der Mittelwert in Millimetern angegeben.
[0127] Die Ergebnisse sind in der Tabelle 8 zusammengefasst. Zum Vergleich sind ebenfalls
die Werte für das Ausbreitmaß ohne Einsatz des Fließverbesserers angegeben.
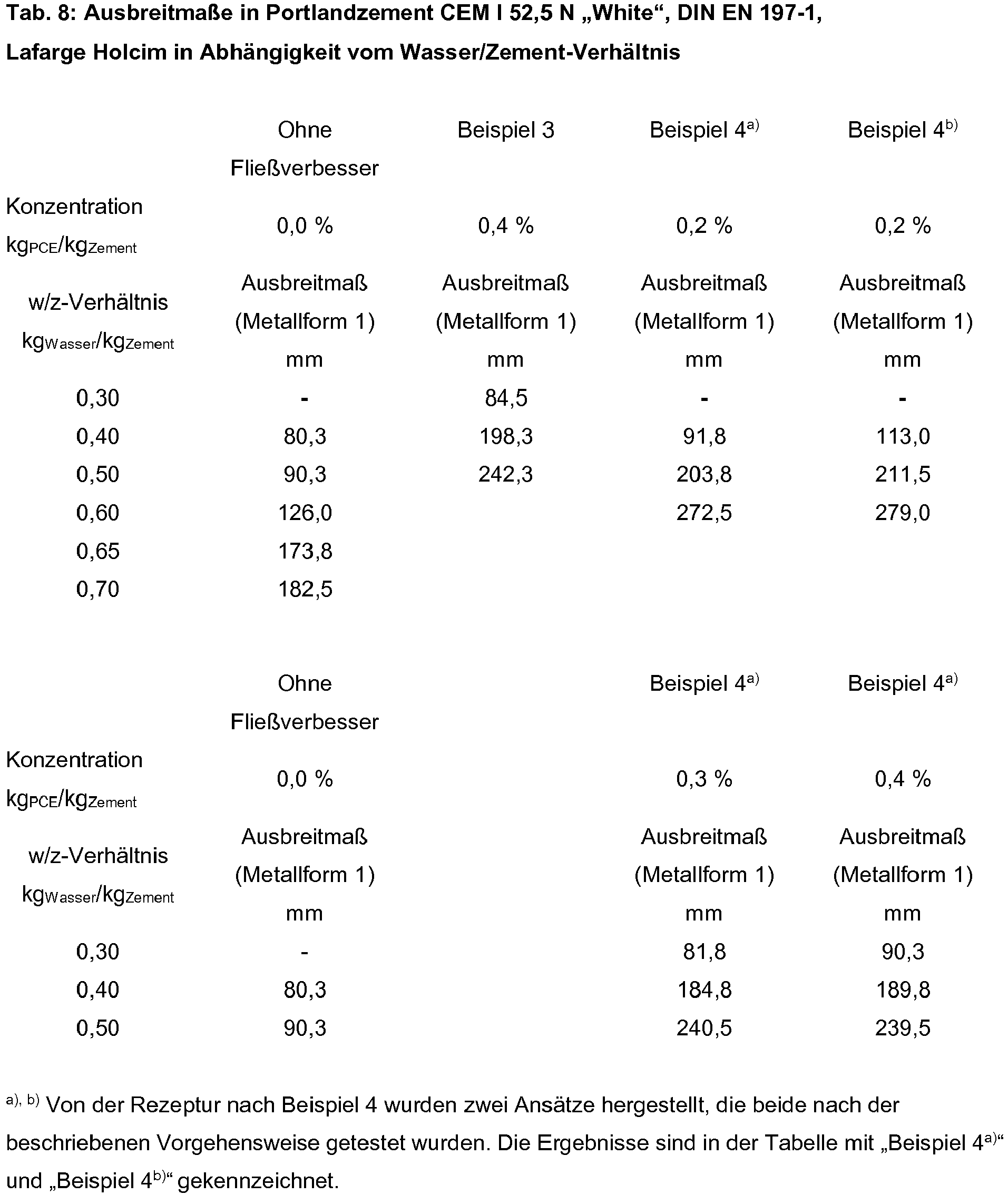
[0128] Zur Beurteilung der Ergebnisse der anwendungstechnischen Untersuchungen für erfindungsgemäßen
Polymerisate wurden vergleichende Messungen mit den gleichen Methoden an kommerziell
erhältlichen Produktmustern durchgeführt. Dabei wurde eine gute fließverbessernde
Wirkung der erfindungsgemäßen Produkte festgestellt.
1. Verfahren zur Herstellung einer Poly(meth)acrylsäure, dadurch gekennzeichnet, dass ein Prozessstrom aus der (Meth)acrolein-Synthese, der zwischen 8 und 50 Gew.-% (Meth)acrylsäure
enthält, bezogen auf das Gewicht des Prozessstroms, in Anwesenheit von Wasser, das
bei der Oxidationsreaktion der (Meth)acrolein-Synthese entstanden ist, einer radikalischen
Polymerisation unterworfen wird.
2. Verfahren nach Anspruch 1, wobei die resultierende Poly(meth)acrylsäure, die mindestens
teilweise in Wasser gelöst ist, das zumindest teilweise bei der Oxidationsreaktion
der (Meth)acrolein-Synthese entstanden ist, einer weiteren Verarbeitung und/oder Funktionalisierung
unterzogen wird, bei der eine funktionalisierte Poly(meth)acrylsäure gebildet wird.
3. Verfahren nach Anspruch 2, wobei es sich bei der Funktionalisierung um eine zumindest
teilweise polymeranaloge Veresterung handelt.
4. Verfahren nach mindestens einem der Ansprüche 1 bis 3, wobei
a. der Prozessstrom eine oder mehrere Verbindungen, ausgewählt aus Formaldehyd, Essigsäure,
Maleinsäure, Maleinsäureanhydrid, Terephthalsäure, Ameisensäure, Benzoesäure, (Meth)acrolein,
Allylalkohol, Protoanemonin oder dessen Strukturisomere, Terephthalaldehyd, Milchsäure,
Laktid, Diformylfuran, Hydroxyzimtsäure oder deren Strukturisomere oder Dihydropyrancarbaldehyd
und optional Kondensations- und Additionsprodukte oder Ester dieser Komponenten, enthält
und/oder
b. der Prozessstrom Prozessstabilisatoren, ausgewählt aus Hydrochinonen, Phenothiazinen,
N-oxidhaltigen Verbindungen, vorzugsweise 4-hydroxy-2,2,6,6-tetramethylpiperidin-1-oxyl,
und/oder deren Kombination, enthält.
5. Verfahren nach mindestens einem der Ansprüche 1 bis 4, wobei der Prozessstrom in Gegenwart
von Reglern, radikalbildenden Initiatoren, vorzugsweise wässrigen Persulfatlösungen,
besonders bevorzugt Lösungen von Natrium-, Kalium- oder Ammoniumpersulfaten, wie Na2S2O8; und/oder Reduktionsmitteln, bevorzugt NaHSO3-Lösungen, Azo-Initiatoren oder organischen Peroxid-Initiatoren, bevorzugt tert.-Butylhydroperoxid,
oder einer Kombination aus mindestens einer Eisen-Verbindung mit einer H2O2-Lösung bei Temperaturen zwischen 20 bis 150°C, vorzugsweise in einem Temperaturbereich
von 80 bis 120 °C, der radikalischen Polymerisation unterworfen wird.
6. Verfahren nach mindestens einem der Ansprüche 1 bis 5, wobei der Prozessstrom
8 bis 40 Gew.-% |
(Meth)acrylsäure |
0,01 bis 20 Gew.-% |
Formaldehyd und |
jeweils 0,1 bis 10 Gew.-% |
Essigsäure und/oder Ameisensäure |
enthält.
7. Verfahren nach mindestens einem der Ansprüche 1 bis 6, wobei der Prozessstrom vorzugsweise
folgende Zusammensetzung hat:
(Meth)acrylsäure |
8 bis 35 |
Gew.-% |
Formaldehyd |
0,01 bis 5,0 |
Gew.-% |
Essigsäure |
0 bis 5,0 |
Gew.-% |
Maleinsäureanhydrid |
0 bis 3,0 |
Gew.-% |
Ameisensäure |
0 bis 5,0 |
Gew.-% |
Benzoesäure |
0 bis 2,0 |
Gew.-% |
(Meth)acrolein |
0 bis 2,0 |
Gew.-% |
Allylalkohol |
0 bis 0,5 |
Gew.-% |
Hydrochinon |
0 bis 600 |
Gew.-ppm |
Protoanemonin oder dessen Strukturisomere |
0 bis 1000 |
Gew.-ppm |
Wasser |
Rest |
|
8. Verfahren nach mindestens einem der Ansprüche 1 bis 7, wobei der Prozessstrom Aldehyde,
bevorzugt Formaldehyd oder dessen Hydrate, enthält und/oder einer Vorbehandlung, vorzugsweise
mit Harnstoff, unterzogen wird.
9. Verfahren nach mindestens einem der Ansprüche 1 bis 8, wobei die erhaltene Poly(meth)acrylsäure
in Gegenwart der Nebenkomponenten oder deren Folgeprodukte verestert wird und diese
Nebenkomponenten oder deren Folgeprodukte bei der Veresterung zumindest teilweise
thermisch abgetrennt werden.
10. Verfahren nach Anspruch 9, wobei die erhaltene Poly(meth)acrylsäure mit (Methoxy)polyethylenglykol
und/oder mit Alkoholen verestert wird, die Alkylenetherfunktionalität in ihrer Struktur
aufweisen.
11. Verfahren nach Anspruch 9 oder 10, wobei die Veresterung unter Ausschluss eines Katalysators
und/oder in einem Temperaturbereich von 120 bis 250 °C, vorzugsweise von 140 bis 180
°C, durchgeführt wird.
12. Verfahren nach mindestens einem der Ansprüche 1 bis 11, wobei die Poly(meth)acrylsäure
und/oder die funktionalisierte Poly(meth)acrylsäure zumindest teilweise in Lösung
vorliegt und/oder formuliert und/oder isoliert wird, bevorzugt durch Trocknung, Sprühtrocknung
oder Fällung.
13. Verwendung der Poly(meth)acrylsäure und/oder der funktionalisierten Poly(meth)acrylsäure,
die nach dem Verfahren nach mindestens einem der Ansprüche 1 bis 12 herstelltet ist,
als Additiv, Fließverbesserer und Wasserreduktionsmittel, vorzugsweise in der Bauchemie,
bei der Verarbeitung von Zement, Mörtel, Beton, sowie als Additiv bei der Verarbeitung
von Asphalt oder Teer.
14. Verwendung eines Prozessstroms aus der (Meth)acrolein-Synthese, der zwischen 8 und
50 Gew.-% (Meth)acrylsäure enthält, für radikalische Homo- oder Co-Polymerisation.
15. Poly(meth)acrylsäure und/oder funktionalisierte Poly(meth)acrylsäure, die nach dem
Verfahren nach mindestens einem der Ansprüche 1 bis 12 herstelltet ist, und teilweise
oder vollständig gelöst in Wasser vorliegt, das teilweise aus der Oxidationsreaktion
bei der Herstellung von (Meth)acrolein entstanden ist.