Technical Field
[0001] The present invention relates to a double pipe heat exchanger in which circular pipes
having different pipe diameters are combined to form two channels, and to a refrigeration
cycle device including this double pipe heat exchanger.
US2756032A for instance discloses a double pipe heat exchanger having the features in the preamble
of claim 1.
Background Art
[0002] Examples of conventional double pipe heat exchangers having enhanced heat-transfer
performances include one in which a circular pipe having the smaller diameter (hereafter,
referred to as an inner pipe) is inserted into a circular pipe having the larger diameter
(hereafter, referred to as an outer pipe). In addition, a method is proposed in which
the inside of the inner pipe is defined as a first channel, a channel between the
two circular pipes is defined as a second channel, and a heat transfer area enlargement
pipe that is formed into an undulating shape is inserted into the second channel and
brought into intimate contact with the inner pipe and the outer pipe, so as to enhance
a heat-transfer performance through an effect of increasing heat-transfer area (see,
e.g., Patent Literature 1).
Citation List
Patent Literature
[0003] Patent Literature 1: Japanese Patent Laid-Open No.
2012-63067 (Fig. 1)
Summary of Invention
Technical Problem
[0004] The above-described Patent Literature 1 proposes a double pipe heat exchanger in
which a heat transfer area enlargement pipe is inserted to expand a heat-transfer
area so as to enhance a heat-transfer performance. However, Patent Literature 1 does
not mention a specific measure and the like taken against the heat transfer area enlargement
pipe that can enhance the heat-transfer performance efficiently.
[0005] Thus, the present invention has an object to obtain a double pipe heat exchanger
and a refrigeration cycle device that can enhance a heat-transfer performance efficiently.
Solution to Problem
[0006] A double pipe heat exchanger according to the present invention is described in claim
1. Specifically, it includes an inner pipe inside which a first fluid passes; an outer
pipe that has a diameter larger than a diameter of the inner pipe and that covers
the inner pipe , the inner pipe and the outer pipe configured to allow a second fluid
to pass through a space defined therebetween; and a heat transfer area enlargement
pipe that is provided in the space in which an angle between the heat transfer area
enlargement pipe and the outer wall of the inner pipe at each of inner contact portions
to be contact areas between an outer wall of the inner pipe and the heat transfer
area enlargement pipe is smaller than an angle between the heat transfer area enlargement
pipe and the inner wall of the outer-pipe at each of outer contact portions to be
contact areas between an inner wall of the outer pipe and the heat transfer area enlargement
pipe the heat transfer area enlargement pipe having a projection-depression shape
in a pipe cross section in which fin portions between the inner contact portions and
the outer contact portions that traverse the space in the pipe cross section come
into contact with the outer wall of the inner-pipe and the inner wall of the outer-pipe
in oblique directions, wherein the fin portions each have an arc shape in the pipe
cross section.
Advantageous Effects of Invention
[0007] According to the present invention, a heat transfer area enlargement pipe that is
in contact with an outer pipe and an inner pipe is provided in such a manner that
the length in a pipe-circumferential direction of a contact area with the outer wall
of the inner pipe is made larger than the length of the contact area with the inner
wall of the outer pipe, and it is thus possible to scatter external force applied
to the heat transfer area enlargement pipe in manufacturing, and to expand a heat-transfer
area while suppressing poor contact in particular with the inner pipe, so as to enhance
a heat-transfer performance.
Brief Description of Drawings
[0008]
Fig. 1 is a diagram for illustrating the configuration of a double pipe heat exchanger
according to a first embodiment of the present invention.
Fig. 2 is a diagram showing a cross section of the double pipe heat exchanger according
to the first embodiment of the present invention, in the other direction.
Fig. 3 is a diagram showing a cross section of a double pipe heat exchanger according
to a third embodiment of the present invention.
Fig. 4 is a diagram for illustrating a lift of a heat transfer area enlargement pipe
3.
Fig. 5 is a diagram showing parameters that are set to the double pipe heat exchanger.
Fig. 6 is a diagram showing brazed portions according to a fourth embodiment of the
present invention.
Fig. 7 is a diagram showing refrigeration cycle devices each including the double
pipe heat exchanger according to the present invention.
Description of Embodiments
First embodiment
[0009] Fig. 1 is a diagram for illustrating the configuration of a double pipe heat exchanger
according to a first embodiment of the present invention. Fig. 1 shows a cross sectional
view of the double pipe heat exchanger taken along the direction of flow of refrigerant
(in an inner pipe 2 in particular). The double pipe heat exchanger is formed by inserting
the inner pipe 2 serving as a circular pipe having a smaller diameter into the inside
of an outer pipe 1 serving as a circular pipe having a larger diameter. In addition,
end portions of the heat exchanger having a double cylinder structure is configured
such that an inner-wall portion of the outer pipe 1 (outer-pipe inner wall) comes
into contact with an outer-wall portion of the inner pipe 2 (inner-pipe outer wall)
(such that side-wall portions closing the outer pipe 1 cover the inner pipe 2).
[0010] The inside of the inner pipe 2 is defined as an inner channel 4 serving as a first
channel, and a space formed between the inner pipe 2 and the outer pipe 1 is defined
as an outer channel 5 serving as a second channel. An inlet and outlet of the outer
channel 5 for a refrigerant are through holes formed in the wall surface of the outer
pipe 1 and connects contact pipes. In addition, a first fluid and a second fluid are
allowed to flow in the inner channel 4 and the outer channel 5, respectively. The
first fluid and the second fluid having different temperatures flow through the respective
channels, which enables heat exchange between the fluids in the double pipe heat exchanger.
[0011] Fig. 2 is a diagram showing a cross section of the double pipe heat exchanger according
to the first embodiment of the present invention, taken along another direction. Fig.
2 shows an A-A' cross section in Fig. 1 (a pipe cross section. A cross section taken
along a pipe-circumferential direction when viewed in a direction in which the fluids
flow). The double pipe heat exchanger of the present embodiment is configured by further
inserting a heat transfer area enlargement pipe 3 having an undulating shape that
includes projections and depressions, into a space portion of the outer channel 5.
In the heat transfer area enlargement pipe 3, an inner wall (the inner wall of the
heat transfer area enlargement pipe) comes into contact with the inner-pipe outer
wall at the depressed portions, and an outer wall (the outer wall of the heat transfer
area enlargement pipe) comes into contact with the outer-pipe inner wall at the projecting
portions. In addition, a side wall obliquely traverses the outer channel 5 (the space
between the inner pipe 2 and the outer pipe 1) in the pipe cross section, and comes
into contact with the inner-pipe outer wall and the outer-pipe inner wall in oblique
directions.
[0012] Here, the amount of heat exchange Q, a heat-transfer area A, a heat transfer coefficient
K, and a difference dT in temperature between the first fluid and the second fluid
relating to the heat exchange generally have a relationship represented by Expression
(1).
[Expression 1]

[0013] In addition, the heat transfer coefficient K is represented by Expression (2). Here,
α1 is the heat transfer coefficient of the first fluid, d1 is the hydraulic diameter
of the inner channel 4, α2 is the heat transfer coefficient of the second fluid, and
d2 is the hydraulic diameter of the outer channel 5. In addition, λ is the thermal
conductivity of the inner pipe 2, dio is the outer diameter of the inner pipe 2, and
dii is the inner diameter of the inner pipe 2, and R is a thermal resistance.
[Expression 2]

[0014] The heat transfer area enlargement pipe 3 comes into contact with the inner pipe
2 to serve as a fin, enabling the enlargement of the heat-transfer area relating to
the heat exchange, which enables the increase of the amount of heat exchanged between
the first fluid and the second fluid.
[0015] Here, contact areas between the inner-pipe outer wall and the inner wall of the heat
transfer area enlargement pipe are defined as inner contact portions 6 (and the length
of the contact portions in the pipe-circumferential direction is denoted as L1). In
addition, contact areas between the outer-pipe inner wall and the outer wall of the
heat transfer area enlargement pipe are defined as outer contact portions 7 (and the
length of the contact portion in the pipe-circumferential direction is defined as
L2). In addition, portions serving as fins between the inner contact portions 6 and
the outer contact portions 7 (side wall surfaces in the projection-depression shape)
are defined as fin portions 16. From the viewpoint of increasing the heat-transfer
area by the heat transfer area enlargement pipe 3, the double pipe heat exchanger
is preferably formed such that the inner contact portions 6 and the outer contact
portions 7 are each brought into contact at one point (point contact) in the pipe
cross section. The reduction of the contact areas increases, for example, the number
of the fin portions 16 in a pipe circumference, a heat-transfer area per fin portion
16, and the like, increasing the heat-transfer area of the whole double pipe heat
exchanger. Here, "points" as referred below do not mean mathematical points, which
have no area or the like, but mean points that have areas to an extent of securing
reliable contacts between the pipes. Note that the contacts will be described as the
point contacts, but the contact areas are linear in the double pipe heat exchanger
as a whole.
[0016] However, when the inner contact portions 6 are formed to be point contacts, the contact
thermal resistance at each inner contact portions 6 is increased. This reduces the
heat transfer coefficient K in the above-described Expression (2), resulting in the
reduction of the amount of heat exchange Q. In addition, forming the inner contact
portions 6 to be the point contacts may cause spots of poor contact. If there are
spots at which, for example, the inner-pipe outer wall is not in contact with the
inner wall of the heat transfer area enlargement pipe when the inner contact portions
6 are formed to be the point contacts, poor heat transfer occurs, which prevents many
heat-transfer areas from being used efficiently.
[0017] Thus, in the double pipe heat exchanger of the first embodiment, the outer contact
portions 7 are formed to be point contacts (the length L2 is reduced to zero) so as
to expand the heat-transfer area. In addition, the inner contact portions 6 are formed
to have a contact length in the pipe cross section (contact areas are to form surfaces
in the double pipe heat exchanger as a whole).
[0018] As seen from the above, according to the double pipe heat exchanger of the first
embodiment, the outer contact portions 7 are formed to be the point contacts so as
to enlarge the heat-transfer area, and the inner contact portions 6 are formed to
have the contact length, which enables the prevention of the poor contact between
the inner-pipe outer wall and the inner wall of the heat transfer area enlargement
pipe. This does not impair but can enhance a heat-transfer performance.
Second embodiment
[0019] The above-described double pipe heat exchanger of the first embodiment includes,
as shown in Fig. 2, the heat transfer area enlargement pipe 3 having the projection-and-depression
(undulating) shape, in the outer channel 5 formed between the outer pipe 1 and the
inner pipe 2. In the heat transfer area enlargement pipe 3, as described in the first
embodiment, the inner wall of the heat transfer area enlargement pipe is in contact
with the inner-pipe outer wall, and the outer wall of the heat transfer area enlargement
pipe is in contact with the outer-pipe inner wall. In addition, the fin portions 16
to be the side walls traverse the outer channel 5 in the pipe cross section.
[0020] To manufacture the double pipe heat exchanger in which the heat transfer area enlargement
pipe 3 is brought into contact with the outer pipe 1 and the inner pipe 2 in such
a manner, a step of expanding the inner pipe 2 or a step of shrinking the outer pipe
1 is performed after the heat transfer area enlargement pipe 3 is inserted into the
outer channel 5.
[0021] Here, if portions of the heat transfer area enlargement pipe 3 to be the fin portions
16 are formed to be perpendicular to the outer pipe 1 and the inner pipe 2, forces
applied to portions to be the inner contact portions 6 or the outer contact portions
7 are applied directly to the fin portions 16, in expanding or shrinking the pipe.
This incurs the risk of forming the fin portions 16 bent into an unexpected shape.
For this reason, the portions to be the fin portions 16 are formed not to be perpendicular,
reducing loads posed on the portions to be the fin portions 16 in expanding or shrinking
the pipe. Then, the fin portions 16 are brought into contact with the inner-pipe outer
wall and the outer-pipe inner wall in oblique directions. For example, when the outer
contact portions 7 are formed to be the point contacts like the above-described first
embodiment, as shown in Fig. 2, an angle α at which the inner-pipe outer wall comes
into contact with the inner wall of the heat transfer area enlargement pipe and an
angle β at which the outer wall of the heat transfer area enlargement pipe comes into
contact with the outer-pipe inner wall are made to be angles less than 90 degrees,
although this is not in particular intended to limit the angles.
[0022] Fig. 3 is a diagram for illustrating a lift of the heat transfer area enlargement
pipe 3. For example, when the step of expanding or shrinking the pipe is performed,
pressures more than necessary act on the inner pipe 2 and the heat transfer area enlargement
pipe 3, the inner contact portions 6 of the heat transfer area enlargement pipe 3
may be deformed, and middle portions thereof, which should be in contact, may be lifted.
The occurrence of the lift may increase, for example, the contact thermal resistance,
which may impair a heat-transfer performance.
[0023] Thus, for example, to prevent this lift, the fin portions 16 are brought into contact
with the inner-pipe outer wall and the outer-pipe inner wall in the oblique directions,
and in addition, the heat transfer area enlargement pipe 3 to be inserted into the
outer channel 5 of the double pipe heat exchanger is made to have a shape in which
the portions to be the fin portions 16, between the portions to be the inner contact
portions 6 (depressed portions) and the portions to be the outer contact portions
7 (projecting portions), are formed into arc shapes in the pipe cross section. Forming
such a shape allows the heat transfer area enlargement pipe 3 to be deformed to bend,
spreading (absorbing) loads on the heat transfer area enlargement pipe 3 even when
the heat transfer area enlargement pipe 3 is pressed excessively against the inner
pipe 2 in expanding the inner pipe 2 or shrinking the outer pipe 1. For this reason,
also in the inner contact portions 6, unreasonable forces are not applied to the heat
transfer area enlargement pipe 3, which can prevent a lift. This does not lose but
can enhance a heat-transfer performance.
[0024] Here, directions in which the portions to be the fin portions 16 are bent through
expanding or shrinking are preferably directions in which the formed fin portions
16 project toward the inner pipe 2 side. By forming the projections toward the inner
pipe 2 side, the fin portions 16 are deformed toward the inner pipe 2 side, increasing
the contact areas between the fin portions 16 and the inner pipe 2, which enlarges
the inner contact portions 6 in length. Heat can be thereby efficiently transmitted
from the inner pipe 2. In addition, for example, as shown in Fig. 2, the angle α <
the angle β is satisfied, which reduces gaps between the heat transfer area enlargement
pipe 3 and the inner pipe 2 in size. Therefore, for example, in brazing the inner
contact portion 6, a brazing material is easy to penetrate. This allows heat to be
further efficiently transmitted from the inner pipe 2. In addition, the increase of
the angle β weakens pressing force in the contact areas between the fin portions 16
and the outer pipe 1, which can suppress the enlargement of the outer contact portions
7 in size.
[0025] Here, it is assumed in the present embodiment that the shape of the heat transfer
area enlargement pipe 3 is the arc shape, but is not limited to the arc shape, and
a shape having a bent portion at least at one point can bring the advantages of scattering
the loads on the portions to be the fin portions 16 and of preventing a lift in the
inner contact portions 6. In addition, the above description similarly holds in a
double pipe heat exchanger in which, for example, the outer contact portions 7 are
not the point contact, and similar advantages can be brought.
Third embodiment
[0026] Fig. 4 is a diagram showing a double pipe heat exchanger according to a third embodiment
of the present invention. Fig. 4 shows a pipe cross section similar to the A-A' section
in Fig. 1 described in the first embodiment. The double pipe heat exchanger of the
present embodiment is configured such that the length L1 of the inner contact portions
6 between the inner-pipe outer wall and the inner wall of the heat transfer area enlargement
pipe and the length L2 of the outer contact portions 7 between the outer-pipe inner
wall and the outer wall of the heat transfer area enlargement pipe satisfy L1 > L2.
[0027] For example, if the relationship of L1 and L2 is L1 < L2, end points of the inner
contact portion 6 may serve as fulcra to generate deformation when excessive external
forces are applied to the outer pipe 1, the inner pipe 2, and the heat transfer area
enlargement pipe 3. For this reason, as described in the second embodiment, in the
heat transfer area enlargement pipe 3, the middle portion of the inner contact portion
6 may be lifted from the inner pipe 2, resulting in the loss of heat-transfer performance.
[0028] Thus, by satisfying L1 > L2, for example, like the first embodiment, even when external
forces are applied so as to bring the outer pipe 1 into intimate contact with the
heat transfer area enlargement pipe 3 across the outer contact portions 7 each having
a contact length when viewed from the front of the pipe cross section, forces applied
to the outer contact portions 7 are scattered, which prevents the pipes from being
deformed.
[0029] In addition, by satisfying L1 > L2, when external forces are applied so as to bring
the inner pipe 2 into intimate contact with the heat transfer area enlargement pipe
3, and to bring the outer pipe 1 into intimate contact with the heat transfer area
enlargement pipe 3, external forces applied to the inner contact portions 6 are substantially
identical to external forces applied to the outer contact portions 7, and thus the
outer contact portions 7 are first deformed when excessive external forces are applied.
This can prevent the inner contact portions 6, which are most important to reduce
the contact thermal resistance, from being lifted, and does not lose but can enhance
a heat-transfer performance. Even if not apparent from Fig. 4, according to the present
invention as defined in claim 1, the fin portions have an arc shape in the pipe cross
section.
[0030] Next, with respect to the double pipe heat exchanger according to the third embodiment
having such characteristics, conditions of shape parameters to satisfy L1 > L2 will
be considered.
[0031] Fig. 5 is a diagram showing parameters that are set for shape analysis of the double
pipe heat exchanger according to the third embodiment of the present invention. As
shown in Fig. 5, the number of projecting portions (depressed portions) of the heat
transfer area enlargement pipe 3 is denoted by n, and the outer diameter of the inner-pipe
is denoted by dio, and the inner diameter of the outer pipe is denoted by doi. Even
if not apparent from Fig. 5, according to the present invention as defined in claim
1, the fin portions have an arc shape in the pipe cross section.
[0032] In addition, θ0 denotes an angle between the top of a projecting portion of the heat
transfer area enlargement pipe 3 and the top of the next projecting portion, θ1 denotes
an angle that serves as a guide for forming the projecting portions, and θ2 denotes
an angle that serves as a guide for forming the depressed portions. In addition, θ1'
denotes a number b of angles each of which is θ1 divided by a (θ1' = b/a × θ1), and
θ2' denotes a number b of angles each of which is θ2 divided by a (θ2' = b/a × θ2).
Furthermore, a length along which the inner pipe 2 is in contact with the heat transfer
area enlargement pipe 3 is denoted by L1, and a length along which the outer pipe
1 is in contact with the heat transfer area enlargement pipe 3 is denoted by L2. Here,
it is assumed that the shape of the projecting portions and the shape of the depressed
portions are all an identical shape in the heat transfer area enlargement pipe 3.
Then, θ0, θ1, θ2, θ1', and θ2' are geometrically represented by Expressions (3) to
(6).
[Expression 3]

[Expression 4]

[Expression 5]

[Expression 6]

[0033] In addition, the length L1 of the inner contact portions 6 and the length L2 of the
outer contact portions 7 can be represented by Expressions (7) and (8) respectively.

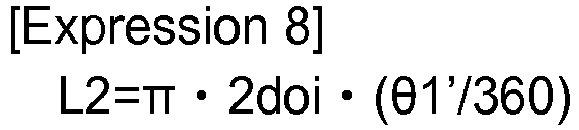
[0034] Based on Expressions (3) to (8), the conditions to satisfy L1 > L2 can be represented
by Expression (9).
[Expression 9]

[0035] As described above, according to the double pipe heat exchanger of the third embodiment,
the length L1 of the inner contact portions 6 between the inner-pipe outer wall and
the inner wall of the heat transfer area enlargement pipe, the length L2 of the outer
contact portions 7 between the outer-pipe inner wall and the outer wall of the heat
transfer area enlargement pipe are made to have the relationship of L1 > L2, and thus
the external forces applied to the outer contact portions 7 can be scattered. In addition,
by making the external forces applied to inner contact portions 6 substantially identical
to the external forces applied to outer contact portions 7, excessive external forces
are not applied only to the inner contact portions 6 but scattered, which can prevent
a lift in the inner contact portions 6. The above enables the prevention of excessive
deformation of each pipe.
Fourth embodiment
[0036] Although not in particular described in the above-described first to third embodiments,
it is preferable that each contact area is brazed with a brazing material 15 so as
to further secure the contact between the inner-pipe outer wall and the inner wall
of the heat transfer area enlargement pipe, and the contact between the outer-pipe
inner wall and the outer wall of the heat transfer area enlargement pipe.
[0037] Fig. 6 is a diagram showing brazed portions according to a fourth embodiment of the
present invention. For example, after assembling the inner pipe 2, the outer pipe
1, and the heat transfer area enlargement pipe 3, a brazing material 15 or the like
is applied, furnace brazing or the like is performed to melt the brazing material
15, brazing contact portions. For example, if the pipes are made of an aluminum or
the like, an Al-Si-based (aluminum-silicon-based) alloy in which an aluminum is alloyed
with a silicon is used as the brazing material 15.
[0038] Here, if it is difficult to apply the brazing material 15 after the assembly, a cladding
material in which the heat transfer area enlargement pipe 3 is clad in (covered with)
the brazing material 15 in advance may be used.
Fifth embodiment
[0039] In a fifth embodiment, there will be described an example of a refrigeration cycle
device to which the double pipe heat exchanger described in the first to fourth embodiments
is applied. Here, four kinds of configurations of the refrigeration cycle device will
be described.
[0040] Fig. 7 is a diagram showing examples of the configurations of the refrigeration cycle
devices according to the fifth embodiment. In each refrigeration cycle device of the
present embodiment, a compressor 8, a condensor 9, an expansion valve 10, an evaporator
11, and a double pipe heat exchanger 12 are connected with pipes to configure a refrigerant
circuit.
[0041] The compressor 8 sucks and compresses a refrigerant, and discharges the refrigerant
at a high temperature and pressure. Here, the compressor 8 may be configured by, for
example, a compressor that controls a rotation speed with an inverter circuit or the
like to adjust the amount of discharged refrigerant. The condensor 9 to be a heat
exchanger is for performing heat exchange between, for example, air supplied from
a blower (not shown) and the refrigerant to condense the refrigerant into a liquid
refrigerant (to condense and liquefy the refrigerant).
[0042] In addition, the expansion valve (pressure-reducing valve or throttle) 10 is for
decompressing and expanding the refrigerant. The expansion valve is configured by,
for example, flow control means such as an electronic expansion valve, and may be
configured by, for example, refrigerant amount adjusting means or the like such as
an expansion valve and a capillary including a temperature sensitive cylinder. The
evaporator 11 is for performing heat exchange between air or the like to evaporate
the refrigerant into a gas refrigerant (to evaporate and gasify).
[0043] In addition, the double pipe heat exchanger 12 of the refrigeration cycle device
in Fig. 7(a) performs heat exchange between a refrigerant at a high temperature and
pressure flowing from the condensor 9 and a refrigerant at a low temperature and pressure
flowing from the evaporator 11. Using the double pipe heat exchanger 12 in such a
manner enables increasing the temperature of the refrigerant in the condensor 9. It
is thereby possible to enhance a capability in heating, and to increase a COP (Coefficient
Of Performance: a value obtained by dividing a capability by an input). In addition,
the refrigerant flowing from the evaporator 11 can be gasified, which can prevent
the liquid refrigerant from returning to the compressor 8.
[0044] The double pipe heat exchanger 12 of a refrigeration cycle device in Fig. 7(b) performs
heat exchange between a high-pressure liquid refrigerant at a refrigerant outlet of
the condensor 9 and a middle-pressure two-phase refrigerant that has passed through
the flow control valve 13. Then, the refrigerant that has been subjected to the heat
exchange and has changed into a middle-pressure gas refrigerant is caused to perform
bypassing to a suction-side pipe to the compressor 8.
[0045] In such a manner, the refrigeration cycle device in Fig. 7(b) causes the refrigerant
that has passed through the condensor 9 to diverge before passing through the expansion
valve 10 and to perform bypassing using the double pipe heat exchanger 12, which can
reduce the amount of refrigerant flowing downstream side from the expansion valve
10. It is thereby possible to reduce pressure drop, increasing the COP.
[0046] The double pipe heat exchanger 12 of the refrigeration cycle device in Fig. 7(c)
performs heat exchange between a high-pressure liquid refrigerant at the refrigerant
outlet of the condensor 9 and a middle-pressure two-phase refrigerant that has passed
through the flow control valve 13. Then, the refrigerant that has been subjected to
the heat exchange and has changed into a middle-pressure gas refrigerant is injected
into a middle portion of a compression part of the compressor 8. Here, the compressor
8 of the refrigeration cycle device in Fig. 7(c) is a compressor having a multistage
configuration that can perform the injection.
[0047] In such a manner, the refrigeration cycle device in Fig. 7(c) causes the refrigerant
that has passed through the condensor 9 to diverge before passing through the expansion
valve 10 and to perform bypassing using the double pipe heat exchanger 12, which can
reduce the amount of refrigerant flowing downstream side from the expansion valve
10. In addition, the injection into the middle portion of the compressing part of
the compressor 8 having the multistage configuration can be performed, and thus an
input such as the discharge temperature of the compressor can be reduced, increasing
the COP.
[0048] The refrigeration cycle device in Fig. 7(d), the double pipe heat exchanger 12 is
used as a condensor. Then, a fluid to be subjected to heat exchange with a refrigerant
flowing through a refrigerant circuit is assumed to be water, brine, or the like (hereafter,
the description will be made assuming that the fluid is water).
[0049] In Fig. 7(d), a pump 14 forms the flow of water and supplies the water into the double
pipe heat exchanger 12. In the double pipe heat exchanger 12, the water is heated
through the heat exchange with the refrigerant. Here, the double pipe heat exchanger
12 is used as the condensor, and can be used as an evaporator.
Reference Signs List
[0050]
1 outer pipe 2 inner pipe 3 heat transfer area enlargement pipe
4 inner channel 5 outer channel 6 inner contact portion
7 outer contact portion 8 compressor 9 condensor
10 expansion valve 11 evaporator 12 double pipe heat exchanger 13 flow control valve
14 pump 15 brazing material 16 fin portion.
1. A double pipe heat exchanger (12) comprising:
an inner pipe (2) inside which a first fluid passes;
an outer pipe (1) that has a diameter larger than a diameter of the inner pipe (2)
and that covers the inner pipe (2), the inner pipe (2) and the outer pipe (1) configured
to allow a second fluid to pass through a space defined therebetween; and
a heat transfer area enlargement pipe (3) that is provided in the space and that has
a projection-depression shape in which, in a pipe cross section, an angle between
the heat transfer area enlargement pipe (3) and the outer wall of the inner pipe (2)
at each of inner contact portions (6) to be contact areas between an outer wall of
the inner pipe (2) and the heat transfer area enlargement pipe (3) is smaller than
an angle between the heat transfer area enlargement pipe (3) and the inner wall of
the outer pipe at each of outer contact portions (7) to be contact areas between an
inner wall of the outer pipe (1) and the heat transfer area enlargement pipe (3),
in which, in the pipe cross section, a length in a pipe-circumferential direction
of the inner contact portions (6) to be contact areas with the outer wall of the inner
pipe (2) is made to be larger than a length in a pipe-circumferential direction of
outer contact portions (7) to be contact areas with the inner wall of the outer pipe
(1), and in which, fin portions (16) between the inner contact portions (6) and the
outer contact portions (7) that traverse the space in the pipe cross section come
into contact with the outer wall of the inner pipe and the inner wall of the outer
pipe in oblique directions,
characterised in that the fin portions (16) each have an arc shape in the pipe cross section.
2. The double pipe heat exchanger (12) of claim 1, wherein the fin portions (16) each
have a bent shape that projects toward the inner pipe (2) side in the pipe cross section.
3. The double pipe heat exchanger (12) of claim 1 or 2, wherein the contact portions
are formed such that the outer contact portions (7) are made to be point contacts
in the pipe cross section, and the inner contact portions (6) are made to be line
contacts in the pipe cross section.
4. The double pipe heat exchanger (12) of any one of claims 1 to 3, wherein the heat
transfer area enlargement pipe (3) is formed so as to satisfy

where θ1 is an angle formed between both end portions of the outer contact portion
and the center of the inner pipe (2) and the outer pipe (1), dio is an outer diameter
of the inner pipe (2), doi is an inner diameter of the outer pipe (1), n is a number
of projecting shapes or depressed shapes of the heat transfer area enlargement pipe
(3), and the projecting shapes and the depressed shapes all have an identical shape.
5. The double pipe heat exchanger (12) of any one of claims 1 to 4, wherein the outer
contact portions (7) and the inner contact portions (6) are each brazed.
6. The double pipe heat exchanger (12) of claim 5, wherein the heat transfer area enlargement
pipe (3) is formed by a cladding material having a surface covered with a brazing
material.
7. A refrigeration cycle device that performs heat exchange between two kinds of refrigerants
using the double pipe heat exchanger (12) of any one of claims 1 to 6.
8. The refrigeration cycle device of claim 7, wherein at least one of the refrigerants
is water or brine.
1. Doppelrohrwärmetauscher (12), umfassend:
ein Innenrohr (2), in dem ein erstes Fluid strömt;
ein Außenrohr (1), das einen Durchmesser größer als einen Durchmesser des Innenrohrs
(2) aufweist und das das Innenrohr (2) bedeckt, wobei das Innenrohr (2) und das Außenrohr
(1) eingerichtet sind, einem zweiten Fluid zu ermöglichen, einen dazwischen definierten
Raum zu durchströmen; und
ein Wärmeübertragungsflächenvergrößerungsrohr (3), das in dem Raum vorgesehen ist
und eine Vorsprungs-/Vertiefungsform aufweist, in dem, in einem Rohrquerschnitt, ein
Winkel zwischen dem Wärmeübertragungsflächenvergrößerungsrohr (3) und der Außenwand
des Innenrohrs (2) an jedem von inneren Kontaktabschnitten (6), die Kontaktflächen
zwischen einer Außenwand des Innenrohrs (2) und dem Wärmeübertragungsflächenvergrößerungsrohr
(3) sind, kleiner ist als ein Winkel zwischen dem Wärmeübertragungsflächenvergrößerungsrohr
(3) und der Innenwand des Außenrohrs an jedem von äußeren Kontaktabschnitten (7),
die Kontaktflächen zwischen einer Innenwand des Außenrohrs (1) und dem Wärmeübertragungsflächenvergrößerungsrohr
(3) sind, in dem, im Rohrquerschnitt, eine Länge in einer Rohrumfangsrichtung der
inneren Kontaktabschnitte (6), die Kontaktflächen mit der Außenwand des Innenrohrs
(2) sind, größer ausgebildet ist als eine Länge in einer Rohrumfangsrichtung der äußeren
Kontaktabschnitte (7), die Kontaktflächen mit der Innenwand des Außenrohrs (1) sind,
und in dem Rippenabschnitte (16) zwischen den inneren Kontaktabschnitten (6) und den
äußeren Kontaktabschnitten (7), die den Raum im Rohrquerschnitt durchqueren, mit der
Außenwand des Innenrohrs und der Innenwand des Außenrohrs in schrägen Richtungen in
Kontakt kommen,
dadurch gekennzeichnet, dass
die Rippenabschnitte (16) jeweils eine Bogenform im Rohrquerschnitt aufweisen.
2. Doppelrohrwärmetauscher (12) nach Anspruch 1, wobei die Rippenabschnitte (16) jeweils
eine gebogene Form aufweisen, die zur Seite des Innenrohrs (2) im Rohrquerschnitt
vorspringt.
3. Doppelrohrwärmetauscher (12) nach Anspruch 1 oder 2, wobei die Kontaktabschnitte so
ausgebildet sind, dass die äußeren Kontaktabschnitte (7) als Punktkontakte im Rohrquerschnitt
ausgebildet sind und die inneren Kontaktabschnitte (6) als Linienkontakte im Rohrquerschnitt
ausgebildet sind.
4. Doppelrohrwärmetauscher (12) nach einem der Ansprüche 1 bis 3, wobei das Wärmeübertragungsflächenvergrößerungsrohr
(3) gebildet ist, um

zu genügen, wobei θ1 ein Winkel ist, der zwischen beiden Endabschnitten des äußeren
Kontaktabschnitts und der Mitte des Innenrohres (2) und des Außenrohres (1) gebildet
ist, dio ein Außendurchmesser des Innenrohres (2) ist, doi ein Innendurchmesser des
Außenrohres (1) ist, n eine Anzahl von vorspringenden Formen oder vertieften Formen
des Wärmeübertragungsflächenvergrößerungsrohres (3) ist, und die vorspringenden Formen
und die vertieften Formen alle eine identische Form aufweisen.
5. Doppelrohrwärmetauscher (12) nach einem der Ansprüche 1 bis 4, wobei die äußeren Kontaktabschnitte
(7) und die inneren Kontaktabschnitte (6) jeweils verlötet sind.
6. Doppelrohrwärmetauscher (12) nach Anspruch 5, wobei das Wärmeübertragungsflächenvergrößerungsrohr
(3) gebildet ist durch ein Überzugsmaterial, aufweisend eine Oberfläche, die mit einem
Lötmaterial überzogen ist.
7. Kältekreislaufeinrichtung, die Wärmeaustausch zwischen zwei Arten von Kältemitteln
unter Verwendung des Doppelrohrwärmetauschers (12) nach einem der Ansprüche 1 bis
6 durchführt.
8. Kältekreislaufeinrichtung nach Anspruch 7, wobei zumindest eines der Kältemittel Wasser
oder Salzlösung ist.
1. Echangeur de chaleur à deux tuyaux (12) comprenant :
un tuyau intérieur (2) à l'intérieur duquel un premier fluide passe ;
un tuyau extérieur (1) qui a un diamètre plus grand qu'un diamètre du tuyau intérieur
(2) et qui recouvre le tuyau intérieur (2), le tuyau intérieur (2) et le tuyau extérieur
(1) étant configurés pour permettre à un deuxième fluide de passer à travers un espace
défini entre eux ; et
un tuyau d'agrandissement d'aire de transfert de chaleur (3) qui est prévu dans l'espace
et qui a une forme saillante-en creux dans laquelle, en section transversale du tuyau,
un angle entre le tuyau d'agrandissement d'aire de transfert de chaleur (3) et la
paroi extérieure du tuyau intérieur (2) au niveau de chacune des parties de contact
intérieures (6) destinées à être des zones de contact entre une paroi extérieure du
tuyau intérieur (2) et le tuyau d'agrandissement d'aire de transfert de chaleur (3)
est plus petit qu'un angle entre le tuyau d'agrandissement d'aire de transfert de
chaleur (3) et la paroi intérieure du tuyau extérieur au niveau de chacune des parties
de contact extérieures (7) destinées à être des zones de contact entre une paroi intérieure
du tuyau extérieur (1) et le tuyau d'agrandissement d'aire de transfert de chaleur
(3), dans lequel, en section transversale du tuyau, une longueur dans une direction
circonférentielle de tuyau des parties de contact intérieures (6) destinées à être
des zones de contact avec la paroi extérieure du tuyau intérieur (2) est réalisée
de manière à être plus grande qu'une longueur dans une direction circonférentielle
de tuyau des parties de contact extérieures (7) destinées à être des zones de contact
avec la paroi intérieure du tuyau extérieur (1), et dans lequel les parties d'ailette
(16) entre les parties de contact intérieures (6) et les parties de contact extérieures
(7) qui traversent l'espace en section transversale du tuyau viennent en contact avec
la paroi extérieure du tuyau intérieur et la paroi intérieure du tuyau extérieur dans
les directions obliques,
caractérisé en ce que
les parties d'ailette (16) ont chacune une forme d'arc en section transversale du
tuyau.
2. Echangeur de chaleur à deux tuyaux (12) selon la revendication 1, dans lequel les
parties d'ailette (16) ont chacune une forme pliée qui se projette vers le côté de
tuyau intérieur (2) en section transversale du tuyau.
3. Echangeur de chaleur à deux tuyaux (12) selon la revendication 1 ou 2, dans lequel
les parties de contact sont formées de sorte que les parties de contact extérieures
(7) soient réalisées de manière à être des contacts ponctuels en section transversale
du tuyau, et les parties de contact intérieures (6) sont réalisées de manière à être
des contacts linéaires en section transversale du tuyau.
4. Echangeur de chaleur à deux tuyaux (12) selon l'une quelconque des revendications
1 à 3, dans lequel le tuyau d'agrandissement d'aire de transfert de chaleur (3) est
formé de manière à satisfaire à

où θ1 est un angle formé entre les deux parties d'extrémité de la partie de contact
extérieure et le centre du tuyau intérieur (2) et du tuyau extérieur (1), dio est
un diamètre extérieur du tuyau intérieur (2), doi est un diamètre intérieur du tuyau
extérieur (1), n est un nombre de formes saillantes ou de formes en creux du tuyau
d'agrandissement d'aire de transfert de chaleur (3), et les formes saillantes et les
formes en creux ont toutes une forme identique.
5. Echangeur de chaleur à deux tuyaux (12) selon l'une quelconque des revendications
1 à 4, dans lequel les parties de contact extérieures (7) et les parties de contact
intérieures (6) sont chacune brasées.
6. Echangeur de chaleur à deux tuyaux (12) selon la revendication 5, dans lequel le tuyau
d'agrandissement d'aire de transfert de chaleur (3) est formé par un matériau de revêtement
ayant une surface recouverte d'un matériau de brasage.
7. Dispositif à cycle de réfrigération qui effectue un échange de chaleur entre deux
types de fluides frigorigènes en utilisant l'échangeur de chaleur à deux tuyaux (12)
de l'une quelconque des revendications 1 à 6.
8. Dispositif à cycle de réfrigération selon la revendication 7, dans lequel au moins
l'un des fluides frigorigènes est de l'eau ou de la saumure.