FIELD
[0001] The present invention relates to a wound yarn body of a water absorbent polyester
fiber and a method for manufacturing the same. More particularly, the present invention
relates to a wound yarn body of a water absorbent polyester fiber capable of rapidly
absorbing perspiration when worn as a result of having semi-permanent water absorbency
without requiring water absorbency processing and due to superior water absorbency,
and can be preferably used in innerwear, sportswear or bedding and the like due to
its superior comfort and softness and favorable feel on the skin.
BACKGROUND
[0002] Although synthetic fibers such as polyester or polyamide fibers are used as general-purpose
materials in innerwear, sportswear and the like, since these synthetic fibers are
hydrophobic fibers, they require water absorbency processing when used in products
around the skin and have the problem of decreased absorbency following repeated washing.
In particular, in the case of washing at high temperatures in the form of so-called
industrial washing that is used to wash uniforms and the like, the loss of water absorbency
processing agent is remarkable thereby requiring a need for improvement of washing
durability.
[0003] Various studies have been conducted on methods for improving the water absorbency
of polyester.
[0004] For example, PTL1 indicated below describes the production of a polyester fiber woven
or knitted fabric having water absorbency by carrying out alkaline processing on polyester
fiber followed by treating with a treatment solution containing a hydrophilic agent.
However, since performance decreases due to repeated washing in the case of ordinary
polyester subjected to alkaline processing and water absorbency processing, water
absorbency having washing durability cannot be imparted.
[0005] In addition, PTL2 and PTL3 indicated below describe that water absorbency having
washing durability can be imparted by carrying out alkaline treatment on a fabric
containing polyester fiber containing 0.005% by weight to 0.5% by weight of elemental
S in the case of PTL2, or carrying out alkaline treatment on a fabric containing polyester
fiber containing 0.5 mol% to 5 mol% of an ester-forming sulfonate compound in the
case of PTL3. However, alkaline treatment cannot be carried out on fabric containing
a blend of materials not having resistance to alkali, and in the case of blending
yarn subjected to water repellency processing, there is the problem of the water repellency
decreasing.
[0006] In addition, although PTL4 indicated below describes a method for using a cheese
dyeing machine as an alkaline treatment method, when alkaline treatment described
in the form of cheese and washing are carried out, the precipitated cyclic oligomer
adheres to the inside of the cheese due to filtration phenomenon resulting in the
formation of a white powder. When yarn having this white powder adhered thereto is
split using a winder for knitting or weaving, the white powder adheres to and accumulates
on the guide or tensioner and the like, thereby increasing tension and disrupting
the wound form resulting in the occurrence of the problems of increased end height
or yarn breakage.
[0007] In addition, since white powder ends up adhering to the yarn guides of knitting machines
or weaving machines when yarn having this white powder adhered thereto is used for
weaving or knitting, frictional resistance value increases resulting in the problem
of the occurrence of fluctuations in tension during knitting. In addition, when this
white powder is introduced into a knitting machine and adheres to and accumulates
on the knitting needle contacts, the movement of the contacts becomes poor thereby
inhibiting the formation of stitches, and when the white powder adheres to and accumulates
on needle grooves of the shuttle of the knitting machine, the movement of the knitting
needle becomes poor resulting in the occurrence of problems such as needle breakage
or pad breakage.
[CITATION LIST]
[PATENT LITERATURE]
[0008]
[PTL1] Japanese Unexamined Patent Publication No. 2005-200799
[PTL2] Japanese Unexamined Patent Publication No. 2014-101598
[PTL3] Japanese Unexamined Patent Publication No. 2014-101599
[PTL4] International Publication No. WO 2015-076412
SUMMARY
[TECHNICAL PROBLEM]
[0009] With the foregoing in view, a problem to be solved by the present invention is to
provide a material that demonstrates semi-permanent water absorbency even in the case
of not subjecting to water absorbency treatment and is free of resistance to alkali,
and a wound yarn body of a water absorbent polyester fiber enabling interknitting
of yarn and the like subjected to water repellency processing, and to inhibit the
generation of white powder that causes problems in processes using the wound yarn
body.
[SOLUTION TO PROBLEM]
[0010] As a result of conducting extensive studies and experimentation to solve the aforementioned
problem, the inventors of the present invention found that the aforementioned problem
can be solved by preventing re-adherence of a cyclic oligomer that is the origin of
a white powder to polyester fiber when alkaline treatment is carried out on a specific
polyester fiber by a specific method, thereby leading to completion of the present
invention.
[0011] Namely, the present invention is as indicated below.
- [1] A wound yarn body of a water absorbent polyester fiber having water absorbency
as determined by the falling-drop method of JIS L1907:2010 after washing 30 times
according to Method 103 C of JIS L0217:1995 of 5 seconds or less, wherein the adhered
amount of a white powder containing a cyclic oligomer that is a decomposition product
of the polyester that composes the water absorbent polyester fiber is less than 0.3%
by weight.
- [2] The wound yarn body described in [1] above, wherein the water absorbent polyester
fiber contains 0.005% by weight to 1% by weight of elemental S and 95 mol% or more
of the repeating units of the polyester is ethylene terephthalate.
- [3] The wound yarn body described in [1] or [2] above, wherein a terminal carboxylic
acid linear oligomer component represented by the following formula (1):

(wherein n is an integer of 3 to 10) is present on the surface of the water absorbent
polyester fiber, and among the terminal carboxylic acid linear oligomer components,
the terminal carboxylic acid linear oligomer component in which n = 4 is contained
in an amount equivalent to the concentration as internal standard of 2 µg/ml to 15
µg/ml.
- [4] The wound yarn body described in any of [1] to [3] above, wherein the wound amount
of the water absorbent polyester fiber is 0.5 kg to 4 kg per single wound yarn body.
- [5] The wound yarn body described in any of [1] to [4] above, wherein the water absorbent
polyester fiber is a false twisted yarn.
- [6] The wound yarn body described in any of [1] to [5] above, wherein the water absorbent
polyester fiber does not have needle loop-shaped crimps.
- [7] A method for manufacturing the wound yarn body described in any of [2] to [6]
above, including a step for carrying out alkali reduction on the polyester fiber containing
0.005% by weight to 1% by weight of elemental S at a reduction rate of 0.6% to 9%
with respect to the polyester fiber.
- [8] The method described in [7] above, wherein a chelating agent is used in combination
in the step for carrying out alkali reduction and an oligomer dispersant is further
used in combination during soaping and neutralization.
[ADVANTAGEOUS EFFECTS OF INVENTION]
[0012] The wound yarn body of a water absorbent polyester fiber of the present invention
can be preferably used in innerwear or sportswear and the like since it absorbs water
semi-permanently even in the case of not subjecting to water absorbency processing
without generating a white powder in the winding and knitting steps of wound yarn,
is able to rapidly absorb perspiration when worn, demonstrates superior comfort and
has a favorable soft feel on the skin.
BRIEF DESCRIPTION OF DRAWINGS
[0013]
FIG. 1 is a schematic diagram of a wrap reel used when measuring the adhered amount
of a white powder.
FIG. 2 is UV chromatograph (240 nm) obtained during LC/MS measurement.
FIG. 3 is a drawing showing the estimated structures of characteristic peaks in the
UV chromatogram of FIG. 2.
DESCRIPTION OF EMBODIMENTS
[0014] The following provides a detailed explanation of embodiments of the present invention.
[0015] The water absorbent polyester fiber composing the wound yarn body of the present
embodiment has water absorbency (as determined by JIS L1907:2010) after washing 30
times according to Method 103 C of JIS L0217:1995 of 5 seconds or less when producing
a knitted fabric using that fiber and measuring the water absorbency thereof. Water
absorbency after washing 30 times is preferably 3 seconds or less, more preferably
2 seconds or less and even more preferably 1 second or less. Water absorbency after
washing 15 times according to the same method is preferably 5 seconds or less, more
preferably 3 seconds or less, even more preferably 2 seconds or less and particularly
preferably 1 second or less. The polyester fiber that composes the wound yarn body
of the present embodiment is able to retain water absorbency even after washing in
the same manner 50 times or 100 times, and water absorbency after washing 50 times
or 100 times is more preferably 5 seconds or less. Ordinary detergents such as neutral
detergents or weakly alkaline detergents are preferably used for the detergent when
washing.
[0016] In addition, the water absorbent polyester fiber composing the wound yarn body of
the present embodiment also has the superior effect of sustaining water absorbency
effects even during industrial washing. Industrial washing refers to washing under
severe conditions using a home washing machine that is applied to the laundering of
work clothes or uniforms and the like, an example of a method thereof is defined by
the F-2 medium temperature washer method of JIS L1096:2010 8.39.5b) 2.2.2), and an
additive such as hydrogen peroxide or sodium silicate is normally added in addition
to the detergent component. A fabric of the present embodiment preferably has water
absorbency of 5 seconds or less after washing 30 times for 30 minutes at 60°C in accordance
with the F-2 method of JIS L1096:2010.
[0017] In the wound yarn body of the present embodiment, the adhered amount of white powder
is measured using the wrap reel shown in FIG. 1 (Model SSD-3, Daiei Kagaku Seiki Mfg.
Co., Ltd.). White powder adhered to the fiber surface can be collected by rubbing
the yarn surface with a tensioner for applying tension when winding with the wrap
reel. According to this method, although the adhered white powder cannot be completely
collected from the yarn surface, whether or not there is a problem with the level
at which the white powder is collected can be judged in terms of practical use.
[0018] In providing an explanation with reference to FIG. 1, yarn 2 that is drawn out from
a wound yarn body 1 is wound with a bobbin frame 6 (bobbin frame circumference: 1.0
m) after passing through a snail guide 3 (Model A408067-R, Yuasa Yarn Guide Engineering
Co., Ltd.), ring tensioner 4 (Model HRB6-12 Toyo Machine Works Co., Ltd.) and traverse
guide 5 (Model A408132-R, Yuasa Yarn Guide Engineering Co., Ltd.) in that order.
[0019] The height from the floor on which the wound yarn body 1 is placed to the snail guide
3 was set at 800 mm, and the wound yarn body 1 was placed so that a vertical line
extending from the center of the yarn guide hole of the snail guide 3 overlaps with
the central axis of the wound yarn body 1. The height from the snail guide 3 to the
yarn inlet hole of the ring tensioner 4 was set at 400 mm and the angle of the yarn
2 entering the yarn inlet hole of the ring tensioner 4 from the snail guide 3 was
set at 90 degrees. The load applied with the ring tensioner 4 used a total of 6 rings
weighing 1.2 g each. The location of the traverse guide 5 was a location at a horizontal
distance from the yarn outlet hole of the ring tensioner 4 of 250 mm and 50 mm lower
than the height of the yarn outlet hole of the ring tensioner 4. The location of the
bobbin frame 6 was such that the height of the yarn guide hole of the traverse guide
5 and the center of the axis of rotation of the bobbin frame 6 are equal, and the
distance from the traverse guide 5 to the center of the axis of rotation of the bobbin
frame 6 was 533 mm. The oscillating width of the traverse guide 5 was set to 50 mm,
traverse speed was 120 mm/min, winding speed was 120 m/min, and approximately 1000
m of yarn were wound onto the bobbin frame 6.
[0020] Although white powder adheres to the snail guide 3, the ring tensioner 4 and the
traverse guide 5 when winding the yarn, since it is difficult to completely recover
white powder from all of these components and since the adhered white powder ends
up being dispersed in the surrounding area due to friction with the yarn, the amount
of white powder adhered to the yarn was calculated based on the change in weight of
the wound yarn using the following equation:

(wherein A: weight (g) prior to rewinding onto the wound yarn body, B: weight (g)
after rewinding onto the wound yarn body, and C: weight (g) of the rewound yarn).
[0021] The adhered amount of white powder is less than 0.3% by weight, preferably less than
0.2% by weight, and more preferably less than 0.1% by weight. If the adhered amount
of white powder exceeds 0.3% by weight, unwinding becomes poor, adhesion of white
powder to a knitting machine, weaving machine, winder or other guide or yarn path
becomes severe, or the accumulation of white powder causes tension abnormalities and
process problems.
[0022] The polyester fiber composing the wound yarn body of the present embodiment is characterized
by the presence of a linear oligomer component having a carboxyl group on the terminal
thereof (to also be referred to as a "terminal carboxylic acid linear oligomer component"
in the present description) on the fiber surface. Moisture absorbency demonstrates
repeated washing durability due to the presence of the terminal carboxylic acid linear
oligomer component on the fiber surface. Here, an example of a terminal carboxylic
acid linear oligomer component is represented by the following formula (1):

(wherein n = 3 to 10).
[0023] A wound yarn body of a polyester fiber in which a terminal carboxylic acid linear
oligomer component is present in this manner has superior water absorption performance.
[0024] The presence of the oligomer component can be confirmed by qualifying or quantifying
according to the analytical methods described below.
[0025] Among these terminal carboxylic acid linear oligomer components, comparatively low
molecular weight oligomer components can be analyzed by LC-MS (liquid chromatograph-mass
spectrometry) by dissolving in THF. When a typical component is taken to be that in
which n = 4, then the oligomer component in which n=4 present on the fiber surface
can be measured according to the method indicated below.
[0026] A sample in the form of 100 mg of polyester yarn extracted from a wound yarn body
was placed in a glass sample bottle having a volume of 20 mL (As One Laboran Pack
Screw Tube Bottle 9-852-07 No. 5) followed by the addition of 3 mL of THF. After stirring
for 6 hours at a rotating speed of about 800 rpm using a Yamato Magnetic Stirrer Model
M-41, the sample was allowed to stand undisturbed for 4 days followed by extracting
the sample by carrying out LC/MS on the THF solution and analyzing the components.
When sampling the THF solution, 0.495 mL of solution were sampled while preventing
the entrance of solids followed by the addition of 0.005 mL of internal standard in
the form of methyl benzoate (1 mg/ml) for use as sample. The conditions of LC/MS analysis
are shown in Table 1.
[Table 1]
LC |
Apparatus |
Waters, UPLC |
Column |
Imtakt, Cadenza CD-C18 (2 mm I.D. × 30 mm) |
Column temperature |
40°C |
Detection |
PDA 210-400 nm |
Flow rate |
0.2 mL/min |
Mobile phase |
A = water |
|
B = acetonitrile/THF (20/80) |
Gradient |
Time (min) |
A% |
B% |
|
0 |
90 |
10 |
|
10 |
0 |
100 |
|
10.1 |
90 |
10 |
|
20 |
90 |
10 |
Injection volume |
2 µL |
MS |
Apparatus |
Waters, Synapt G2 |
Ionization |
ESI+, ESI- |
Scan range |
m/z 50-2000 |
[0027] FIG. 2 indicates an example of the chart of a UV chromatogram (240 nm) of the THF
solution. In addition, FIG. 3 indicates the estimated structures of characteristic
peaks in the UV chromatogram of FIG. 2. In FIG. 2, a large number of the aforementioned
terminal carboxylic acid linear oligomer components and cyclic oligomer components
to be subsequently described were detected. Peak x in FIG. 2 is a peak derived from
a linear oligomer component of a terminal carboxylic acid in which n = 3 (molecular
weight: 786.24) shown in formula (1). This is estimated based on the detection of
ions ([M-H]-) having a mass number (m/z) of 785.17 in the ESI-mass spectrum of that
peak (electrospray ionization, negative ion mass spectrum). Components derived from
other peaks were estimated from the mass numbers of ions detected according to the
ESI-mass spectra thereof in the same manner.
[0028] In the UV chromatogram, in cases in which a peak derived from the aforementioned
terminal carboxylic acid linear oligomer component was not well-defined, the mass
spectrogram of a mass number of 785 (vertical axis: detection intensity of specific
mass number, horizontal axis: retention time) is displayed, and whether or not the
oligomer was present was able to be determined according to whether or not a detection
intensity peak of the mass number in the vicinity of the retention time estimated
from the example of the UV spectrum (approx. 4.5 min. in FIG. 2) was present.
[0029] In formula (1), the amount of the terminal carboxylic acid linear oligomer in which
n = 3 can be measured with the value of the peak area in the UV chromatogram, and
that value can be converted to a concentration based on the ratio with the value of
the peak area in the UV chromatogram of methyl benzoate added as internal standard.
The location of peak c corresponding to the internal standard substance is estimated
by detecting the ion of that mass number in an ESI-mass spectrum of that peak. In
the case peak x in the UV chromatogram is not well-defined for reasons such as overlapping
with other peaks, the area of peak z of the sample in question can be converted to
the area of peak x by using the area of peak z in the mass chromatogram having a mass
number of 785 as previously described and determining the intensity ratio between
x and z by measuring a different sample in which both peak x and peak z are clearly
detected under the same conditions. The intensity ratio with peak c can then be calculated
by using the area of peak x of the sample in question determined in this manner.
[0030] The wound yarn body of the present embodiment is such that the amount of the terminal
carboxylic acid linear oligomer in which n=4 shown in formula (1) is preferably equivalent
to a concentration of 2 µg/ml to 15 µg/ml converted from the internal standard, and
is more preferably equivalent to a concentration of 3 µg/ml to 10 µg/ml.
[0031] Although the terminal carboxylic acid oligomer contributes to water absorbency in
this manner, a cyclic oligomer represented by, for example, the following formula
(2):
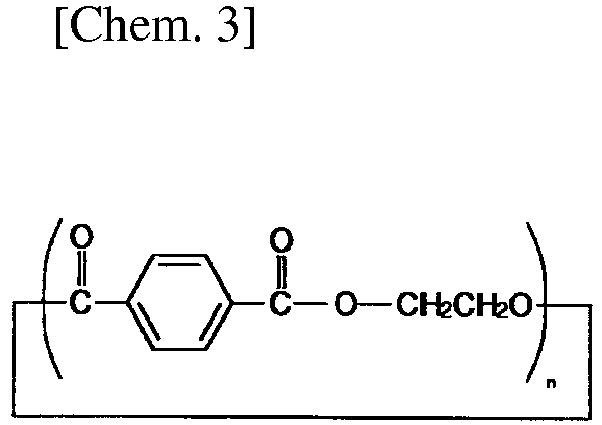
(wherein n = 2 to 10) does not exhibit water absorbency and conversely inhibits water
absorbency. The amount of the cyclic oligomer represented by formula (2) can also
be analyzed by LC-MS (liquid chromatography-mass spectroscopy) by dissolving in THF
with respect to cyclic oligomers having a comparatively low molecular weight, and
the concentration thereof as converted from the internal standard can be determined
from the peak intensity ratio relative to the internal standard. When a typical component
thereof is taken to be that in which n = 3, the amount of cyclic oligomer in which
n = 3 is preferably equivalent to a concentration converted from the internal standard
of 80 µg/ml or less and more preferably equivalent to 70 µg/ml or less.
[0032] More specifically, in the example of the chart of a UV chromatogram (240 nm) shown
in FIG. 2, peak b is a peak of a cyclic oligomer component in which n = 3 shown in
formula (2). Peak b can be confirmed to be derived the cyclic oligomer component (molecular
weight: 576.13) as a result of an ion [(M+NH4)]+) having a mass number of 594.16 being
detected in the ESI-mass spectrum of that peak (electrospray ionization, positive
ion mas spectrum). In cases in which a peak derived from the aforementioned oligomer
cannot be clearly defined in the UV chromatogram, the mass spectrogram of a mass number
of 594.16 is displayed in the same manner as a terminal carboxylic acid linear oligomer
in which n = 4, and whether or not the oligomer is present is able to be determined
according to whether or not a detection intensity peak (peak w) of the mass number
in the vicinity of the retention time estimated from the example of the UV spectrum
(approx. 5.3 min. in FIG. 2) is present. The amount of this oligomer present can be
measured with the value of the peak area in the UV chromatogram, and that value can
be converted to a concentration based on the ratio with the value of the peak area
of peak (peak c) in the UV chromatogram of the methyl benzoate added as internal standard.
[0033] Among terminal carboxylic acid linear oligomer components, comparatively high molecular
weight oligomer components cannot be detected using the previously described method
due to their poor solubility in THF. The wound yarn body of the present embodiment
preferably retains a comparatively high molecular weight terminal carboxylic acid
linear oligomer that is not extracted with THF on the surface of the polyester fiber
composing the wound yarn body even after having extracted the aforementioned oligomer
components that are soluble in THF. Since this terminal carboxylic acid linear oligomer
demonstrates high adhesiveness with fiber and is resistance to elimination even after
repeated washing, it is thought to demonstrate considerable effectiveness due to its
water absorbency after repeated washing.
[0034] The wound yarn body of the present embodiment demonstrates water absorbency due to
the presence of terminal carboxylic acid linear oligomers in which n = 3 to 10 in
formula (1) that are soluble and insoluble in THF. There are no particular limitations
on the method used to make these oligomers present, and although they may be imparted
by a method such as coating a terminal carboxylic acid linear oligomer component on
a fabric or mixed into an ester polymer, they are preferably imparted to the vicinity
of the fiber surface by subjecting a specific polyester fiber to a specific alkali
treatment.
[0035] The wound yarn body of the present embodiment is preferably characterized by containing
polyester fiber containing 0.005% by weight to 1% by weight of elemental S (elemental
sulfur). A water absorbency effect is obtained by carrying out a specific alkali treatment
on polyester fiber containing 0.005% by weight to 1% by weight of elemental S, resulting
in a line of yarn that exhibits hardly any change in that effect even after repeated
washing. In the case the content of elemental S is less than 0.005% by weight, the
effect of enhancing the durability of water absorbency after alkali treatment diminishes,
while in the case the amount of elemental S contained in the polyester fiber is 1%
by weight or more, fiber strength decreases making spinning difficult. The content
of elemental S in the polyester fiber is more preferably 0.01% by weight to 0.8% by
weight and even more preferably 0.015% by weight to 0.7% by weight. Furthermore, ICP-AES
(inductively coupled plasma-optical emission spectrometry) is used as a method for
quantifying elemental S. An example of a polyester fiber containing 0.005% by weight
to 1% by weight of elemental S is a polyester fiber containing 0.5 mol% to 5 mol%
of an ester-forming sulfonate compound.
[0036] Examples of ester-forming sulfonate compounds contained at 0.5 mol% to 5 mol% in
a polyester fiber include sodium 5-sulfoisophthalate, potassium 5-sulfoisophthalate,
sodium 4-sulfo-2,6-naphthalene dicarboxylic acid, sodium 2-sulfo-4-hydroxybenzoic
acid, 3,5-dicarboxylic acid benzenesulfonic acid tetramethyl phosphonium salt, 3,5-dicarboxylic
acid benzenesulfonic acid tetrabutyl phosphonium salt, 3,5-dicarboxylic acid benzenesulfonic
acid tributylmethyl phosphonium salt, 2,6-dicarboxylic acid naphthalene-4-sulfonic
acid tetrabutyl phosphonium salt, 2,6-dicarboxylic acid naphthalene-4-sulfonic acid
tetramethyl phosphonium salt, 3,5-dicarboxylic acid benzensulfonic acid ammonium salt
and ester derivatives such as methyl esters or dimethyl esters thereof. These ester
derivatives such as methyl esters or dimethyl esters are used preferably from the
viewpoints of obtaining superior polymer whiteness and polymerization rate. The polyester
fiber preferably contains a metal sulfonate group-containing isophthalic acid component
such as sodium 5-sulfoisophthalic acid or potassium 5-sulfoisophthalic acid, and among
these, sodium dimethyl 5-sulfoisophthalate is particularly preferable.
[0037] In addition, another example of polyester fiber containing 0.005% by weight to 1%
by weight of elemental S is polyester fiber containing a non-ester-forming sulfonate
compound. A non-ester-forming sulfonate compound refers to a polyester fiber containing
a sulfonate compound without forming a polyester as a result of a sulfonate compound
undergoing polycondensation by undergoing a direct esterification reaction with polyester,
and examples thereof include polyester fiber obtained by a method consisting of mixing
a master chip incorporating 0.5 mol% to 5 mol% of a sulfonate compound with a polyester
chip in which an ordinary ethylene terephthalate component is 95 mol% or more, and
polyester fiber obtained by adding 0.5 mol% to 5 mol% of a sulfonate compound.
[0038] Examples of a non-ester-forming sulfonate compound include alkaline metal salts of
an alkyl sulfonic acid, and alkaline metal salts of an alkyl benzenesulfonic acid.
Examples of alkaline metal salts of an alkyl sulfonic acid include sodium dodecyl
sulfonate, sodium undecyl sulfonate and sodium tetradecyl sulfonate. In addition,
examples of alkaline metal salts of an alkyl benzenesulfonic acid include sodium dodecyl
benzenesulfonate, sodium undecyl benzenesulfonate and sodium tetradecyl benzenesulfonate.
Sodium dodecyl benzenesulfonate is particularly preferable from the viewpoint of processing
stability.
[0039] The total fineness of the water absorbent polyester fiber is preferably about 8 decitex
(dtex) to about 167 dtex and more preferably about 22 dtex to about 110 dtex. Although
there are no particular limitations on single yarn fineness, it is preferably about
0.5 dtex to about 2.5 dtex from the viewpoints of feel on the skin and texture.
[0040] The water absorbent polyester fiber may also contain a matting agent such as titanium
dioxide, stabilizer such as phosphoric acid, ultraviolet absorber such as a hydroxybenzophenone
derivative, crystallization nucleating agent such as talc, lubricant such as fumed
silica, antioxidant such as a hindered phenol derivative, flame retardant, antistatic
agent, pigment, fluorescent whitening agent, infrared absorber or antifoaming agent.
[0041] The water absorbent polyester fiber is preferably a false twisted yarn. Crimping
of the false twisted yarn is preferably such that the crimp elongation rate is 30%
to 150%. Furthermore, crimp elongation rate is measured under the conditions indicated
below.
[0042] Length (A) is measured after 30 seconds by immobilizing the upper end of the crimped
yarn and applying a load of 1.77 × 10
-3 cN/dtex to the lower end. Next, the load of 1.77 × 10
-3 cN/dtex is removed, a load of 0.088 cN/dtex is applied and length (B) is measured
after 30 seconds followed by determining crimp elongation rate according to equation
(3) indicated below.

[0043] The wound yarn body of the present embodiment is preferably obtained by subjecting
the water absorbent polyester fiber to alkali treatment while in the state of a wound
yarn body. In addition, alkali treatment can be carried out using a cheese dyeing
machine.
[0044] In the case of alkali treatment with a cheese dyeing machine, there is susceptibility
to the occurrence of winding collapse in the case of winding crimp-less yarn around
the cheese dyeing tube, and as a result of the occurrence of tightening attributable
to heat shrinkage, liquid passage becomes poor and there is the risk of unevenness
occurring in the reduction rate, thereby making this undesirable.
[0045] The wound yarn body of the present embodiment can be manufactured by a method that
includes a step for carrying out alkali treatment on a polyester fiber containing
0.005% by weight to 1% by weight of elemental S at a reduction rate of 0.6% to 9%
relative to the polyester fiber. In addition, a chelating agent is preferably used
in combination in the step for carrying out alkali treatment, and an oligomer dispersant
is further preferably used in combination during soaping and neutralization.
[0046] A linear oligomer can be formed when a polymer on the surface of the polyester fiber
is subjected to alkali treatment (hydrolysis). Without being bound by a specific theory,
it is presumed that a linear oligomer is formed by hydrolysis of a polymer on the
surface of the polyester fiber on the fiber surface (while adhered to the fiber surface)
without the immediate generation of a white powder component in the form of a cyclic
oligomer due to alkali treatment (hydrolysis), and that the linear oligomer is converted
to the cyclic oligomer by a dehydration-condensation reaction after being eliminated
from the fiber surface. The cyclic oligomer observed on the fiber surface basically
re-adheres to the fiber surface. When the cyclic oligomer is dissolved in a high-temperature
aqueous alkaline solution, chelation is thought to occur to the effect of metal ions,
and a chelating agent is used in combination during alkali reduction to prevent this.
Despite this, cyclic oligomer present in the aqueous alkaline solution that remains
by adhering to the fiber precipitates as a result of having been lowered in temperature
due to rinsing with normal temperature water during soaping, washing and neutralization,
and ends up adhering to the fiber surface. Consequently, the combined use of an oligomer
dispersant during soaping and neutralization removes the adhered oligomer.
[Reduction Rate]
[0047] The reduction rate of the polyester fiber as a condition of alkali treatment for
demonstrating water absorbency is preferably 0.6% to 9%, more preferably 1% to 8%,
and even more preferably 1.5% to 7%. Reduction rate can be calculated from the weight
of the polyester fiber before and after alkali treatment. In the case the reduction
rate is less than 0.6%, water absorbency attributable to alkali treatment is not demonstrated
thereby making this undesirable, while if the reduction rate exceeds 9%, alkali reduction
proceeds excessively resulting in inferior durability of water absorbency, thereby
making this undesirable.
[0048] Polyester fiber containing 0.5 mol% to 5 mol% of an ester-forming sulfonate compound
has a faster rate of alkali reduction in comparison with ordinary polyester fiber,
thereby making this preferable since it is possible carry out treatment by adjusting
the alkali to a lower concentration.
[Alkali Treatment Method]
[0049] A method consisting of forming a fabric by using a portion of a polyester fiber,
obtained by carrying out alkali treatment by a method such as using a cheese dyeing
machine so as to impart a reduction rate of 0.6% to 9% while in the state of a polyester
fiber containing 0.005% by weight to 1% by weight of elemental S, is preferably used
as an alkali treatment method.
[0050] In the case of carrying out alkali treatment using a cheese dyeing machine, it is
necessary to wind the polyester fiber around the perforated tube used for cheese dyeing.
[0051] At that time, the wound amount of the polyester fiber containing 0.005% by weight
to 1% by weight of elemental S is preferably 0.5 kg to 4 kg, more preferably 1 kg
to 3.5 kg and even more preferably 2 kg to 3 kg. If the wound amount is less than
0.5 kg, productivity is inferior, thereby making this undesirable. If the wound amount
exceeds 4 kg, liquid passage through the cheese dyeing machine becomes poor when carrying
out alkali treatment, and in addition to increased susceptibility to variations, winding
diameter also increases, thereby resulting in poor handling.
[Winding Density]
[0052] The winding density of the polyester fiber containing 0.005% by weight to 1% by weight
of elemental S is preferably more than 0.1 g/cm
3 to less than 1.2 g/cm
3, more preferably more than 0.2 g/cm
3 to less than 1.0 g/cm
3, even more preferably more than 0.3 g/cm
3 to less than 0.8 g/cm
3, and particularly preferably more than 0.4 g/cm
3 to less than 0.6 g/cm
3. If winding density is 0.1 g/cm
3 or less, the wound state collapses during alkali treatment with a cheese dyeing machine
and defective unwinding occurs during knitting. In addition, if winding density is
1.2 g/cm
3 or more, liquid passage during alkali treatment becomes poor thereby preventing uniform
treatment and unevenness in water absorbency.
[Knit-Deknit]
[0053] Although knit-deknitting is an example of a technique consisting of first knitting
a polyester containing 0.005% by weight to 1% by weight of elemental S into a knitted
fabric by using knit-deknitting and subjecting to alkali treatment followed by rearranging
to obtain a wound yarn body, crimps in the form of knit loops end up being imparted
to the polyester fiber. Knit loops referred to here refer to crimps in the form of
loops formed in the yarn when rearranging the knitted fabric after having immobilized
stitches formed during knitting by heat treatment, and result in a peculiar texture
when using this yarn to form a knitted fabric or woven fabric, thereby making this
not very desirable.
[Hank Treatment]
[0054] Although an example of hank treatment is a technique consisting of forming the polyester
fiber containing 0.005% by weight to 1% by weight of elemental S into a hank and subjecting
to alkali treatment with a jet dyeing machine and the like followed by rewinding with
a winder to obtain a wound yarn body, not only does this technique require labor and
high costs in the hanking step and rewind step, but since the haniks also contain
alkali treatment solution, crimps of the false twisted yarn end up stretching due
to their own weight, thereby making this undesirable.
[Alkali Reduction Conditions]
[0055] Since unevenness occurs between the inner and outer layers in the case of carrying
out alkali treatment with a cheese dyeing machine, long-term treatment at a low temperature
is preferable, and in order to achieve a reduction rate of 0.6% to 9%, it is preferable
to carry out treatment, for example, for 40 minutes to 100 minutes at a temperature
of 90°C to 100°C and sodium hydroxide concentration if 0.1 g/L to 10 g/L, and more
preferably for 50 minutes to 80 minutes at a temperature of 90°C to 95°C at a sodium
hydroxide concentration of 5 g/L to 10 g/L.
[0056] Although neutralization with acid and washing are normally carried out following
alkali treatment, in the case of alkali treatment with a cheese dyeing machine, the
precipitated cyclic oligomer adheres to the inside of the cheese resulting in increased
susceptibility to the occurrence of the problem of unwinding becoming poor when knitting
or weaving using the wound yarn body as well as the problem of the cyclic oligomer
adhering to the knitting machine, weaving machine, yarn path or guides in the form
of a white powder. In order to solve these problems, it is necessary to not allow
the oligomer causing the generation of the white powder to precipitate, not allow
the white powder to adhere to the polyester fiber surface, and remove as much of the
white powder as possible by enhancing washing following alkali treatment.
[0057] As was previously described, a cyclic oligomer in the form of a white powder is generated
when the polyester fiber is hydrolyzed by alkali treatment. The cyclic oligomer is
susceptible to the effects of metal ions present in the washing solution during alkali
treatment, and since it more easily adheres to the fiber surface as a result of chelation,
it is preferable to add a chelating agent. Although the chelating agent is not specified,
examples of chelating agents include polycarboxylic acid, nitrotriacetic acid (NTA),
ethylene diamine tetraacetic acid (EDTA), nitrilotrimethylene phosphonic acid, hydroxyethylidiene
diphosphonic acid (NTMP), phosphonic acid, glutamine diacetate, glutamic acid diacetic
acid and salts thereof. The chelating agent is preferably added at 0.5 g/L to 2.0
g/L in an aqueous solution during alkali treatment.
[0058] Although cyclic oligomer present in an aqueous alkaline solution dissolves in the
case of a high temperature, it precipitates in the case the solution temperature is
lower than 90°C. On the basis thereof, precipitation and adhesion of the cyclic oligomer
can be inhibited by draining the solution at a high temperature of 90°C to 95°C following
alkali treatment.
[Soaping]
[0059] Since the alkaline solution remains in the wound yarn body after draining, it is
necessary to carry out washing. Washing is preferably carried out by injecting water
into the cheese dyeing machine following drainage, adding oligomer dispersant in the
form of sodium hydrosulfite at 0.5 g/L to 2.0 g/L, and washing for 10 minutes at 80°C
followed by washing at normal temperature after having washed twice for 10 minutes
with warm water at 40°C to 60°C.
[0060] Although there are no particular limitations on the oligomer dispersant used, components
such as amino-based ionic compounds, alkylene oxide adducts of fatty acids, polycyclic
nonionic compounds, alkyl sulfonates, polyvalent alcohol fatty acid esters, alkylene
oxide adducts of polyvalent alcohol fatty acids, aromatic polyester resins, carboxylates
or polyaminocarboxylic acids can be used alone or in combination. An amphoteric surfactant
is preferably used to prevent adhesion of oligomer and remove adhered oligomer. The
oligomer dispersant is preferably added at 0.5 g/L to 3.0 g/L during soaping. If added
at less than 0.5 g/L, the effects of preventing adhesion of oligomer and removal of
oligomer become inferior and the adhered amount of white powder cannot be reduced.
In addition, if the added amount of oligomer dispersant exceeds 3.0 g/L, although
the adhered amount of white powder can be reduced, linear oligomer contributing to
water absorbency also ends up being removed from the fiber surface, thereby resulting
in poor water absorbency.
[Neutralization]
[0061] Oxalic acid or acetic acid is preferably used for the acid used in neutralization.
Oligomer precipitation and adhesion can be inhibited when the treatment solution has
become acidic by combining the use of an oligomer dispersant at that time.
[0062] Although there are no particular limitations on the oligomer dispersant used during
neutralization, an amphoteric surfactant is used preferably since adhesion of oligomer
is prevented under alkaline or acidic conditions.
[Cheese Dyeing]
[0063] The wound yarn body of the present embodiment may be dyed. In the case of using in
the form of dyed yarn, cheese dyeing may be carried out directly after having carried
out alkali treatment with a cheese dyeing machine.
[Finishing Agent]
[0064] Although softening treatment for softening texture or oiling treatment for improving
yarn unwinding and knitting organization may be carried out in the bath, it is not
preferable to use that which impairs water absorbency such as a cationic softening
agent or silicon oil.
[Rewinding]
[0065] In addition, the wound yarn body of the present embodiment may be rewound with a
winder after having undergone alkali treatment with a cheese dyeing machine to obtain
a wound yarn body.
EXAMPLES
[0066] The following provides a detailed explanation of the present invention using examples
thereof. The present invention is naturally not limited to these examples.
[0067] Furthermore, wound yarn bodies obtained in the examples were evaluated using the
methods indicated below.
(1) Adhered Amount of White Powder
[0068] The previously described method was used to evaluate the adhered amount of white
powder.
(2) Quantification of Terminal Carboxylic Acid Linear Oligomer in which n=4
[0069] The previously described method was used for evaluation.
(3) Water Absorbency
[0070] Yarn was drawn out from the wound yarn body, a tubular knitted fabric was fabricated
and the resulting tubular knitted fabric was scoured and dried in accordance with
ordinary methods followed by measuring water absorbency of the resulting tubular knitted
fabric using the falling-drop method of JIS L1907:2010 after washing 30 times according
to Method 103 C of JIS L0217:1995. In the present description, the resulting water
absorbency was taken to be the water absorbency of the "water absorbent polyester
fiber".
(4) Washing Treatment
[0071] Yarn was drawn out from the wound yarn body, a tubular knitted fabric was fabricated
and the resulting tubular knitted fabric was scoured and dried in accordance with
ordinary methods followed carrying out washing treatment using a weakly alkaline detergent
(trade name: Attack, Kao Corp.) in accordance with Method 103 C of Attached Table
1 of JIS L0217:1995.
(5) Industrial Washing Treatment
[0072] Yarn was drawn out from the wound yarn body, a tubular knitted fabric was fabricated
and the resulting tubular knitted fabric was scoured and dried in accordance with
ordinary methods followed by carrying out washing treatment on the resulting tubular
knitted fabric using 0.8% owf soap, 0.8% hydrogen peroxide and 0.8% sodium silicate
as detergent under conditions of the F-2 medium temperature washer method of JIS L1096:2010
8.39.5b) 2.2.2) on the assumption of an industrial washing test.
(6) Presence of Absence of Knit Loops
[0073] Yarn was drawn out from the wound yarn body and the state of the yarn was observed
in the state of not applying a load. The presence of loop-shaped crimps originating
in the knitted fabric was confirmed at that time.
[EXAMPLE 1]
[0074] 84 dtex/36 f polyester false twisted yarn having a round cross-section (elemental
S content: 0.14% by weight) and containing 2 mol% sodium dimethyl 5-sulfoisophthalate
was wound around a perforated tube for cheese dyeing at a winding density of 0.5 g/cm
3 and wound amount of 3.0 kg.
[0075] The tube wound with the yarn was placed in a cheese dyeing machine and subjected
to alkali treatment for 60 minutes at a liquid temperature of 95°C with an aqueous
alkaline solution using 10 g/L of sodium hydroxide and 2 g/L of chelating agent in
the form of Marpon A-47 (Matsumoto Yushi-Seiyaku Co., Ltd.) while raising the temperature
of the aqueous alkaline solution under conditions of 2°C/min.
[0076] After draining immediately after alkali treatment at a liquid temperature of 95°C,
water was injected and soaping was carried out for 15 minutes at a liquid temperature
of 80°C using 1 g/L of sodium hydrosulfite and 2 g/L of oligomer dispersant in the
form of Mahon PS-K7 (Matsumoto Yushi-Seiyaku Co., Ltd. incorporating amphoteric surfactant)
followed by draining and washing twice with hot water for 3 minute at a water temperature
of 60°C.
[0077] After washing with hot water, draining and re-supplying with water, neutralization
was carried out using acetic acid after using 1 g/L of oligomer dispersant in the
form of Mahon PS-K7 followed by washing.
[0078] After draining, the tube wound with the yarn was removed from the cheese dyeing machine
and dehydrated with a centrifugal dehydrator followed by drying with a cheese dryer
to obtain a wound yarn body.
[0079] The reduction rate of the water absorbent polyester yarn of the resulting wound yarn
body was 6.0%, water absorbency after washing 30 times in accordance with Method 103
C of Attached Table 1 of JIS L0217:1995 was less than 1 second, and water absorbency
after washing 30 times in accordance with the F-2 medium temperature washer method
of JIS L1096:2010 was 2 seconds. The adhered amount of white powder was 0.10% by weight.
[EXAMPLE 2]
[0080] A wound yarn body was obtained by carrying out treatment using the same method as
Example 1 with the exception of using 1 g/L of a chelating agent in the form of Marpon
A-47 during alkali treatment, using 1 g/L of an oligomer dispersant in the form of
Marpon PS-K7 during soaping, and using 0.5 g/L of an oligomer dispersant in the form
of Marpon PS-K7 during neutralization. The reduction rate of the water absorbent polyester
yarn of the resulting wound yarn body was 6.0%, water absorbency after washing 30
times in accordance with Method 103 C of Attached Table 1 of JIS L0217:1995 was less
than 1 second, and water absorbency after washing 30 times in accordance with the
F-2 medium temperature washer method of JIS L1096:2010 was 2 seconds. The adhered
amount of white powder was 0.23% by weight.
[EXAMPLE 3]
[0081] A wound yarn body was obtained by carrying out treatment using the same method as
Example 1 with the exception of using 2 g/L of oligomer dispersant in the form of
Marpon PS-K7 during neutralization.
[0082] The reduction rate of the water absorbent polyester yarn of the resulting wound yarn
body was 6.0%, water absorbency after washing 30 times in accordance with Method 103
C of Attached Table 1 of JIS L0217:1995 was 4 seconds, and water absorbency after
washing 30 times in accordance with the F-2 medium temperature washer method of JIS
L1096:2010 was 15 seconds. The adhered amount of white powder was 0.05% by weight.
[COMPARATIVE EXAMPLE 1]
[0083] 84 dtex/36 f polyester false twisted yarn having a round cross-section (elemental
S content: 0.14% by weight) and containing 2 mol% sodium dimethyl 5-sulfoisophthalate
was wound around a perforated tube for cheese dyeing at a winding density of 0.5 g/cm
3 and wound amount of 3.0 kg.
[0084] Alkali treatment was carried out for 60 minutes at a liquid temperature of 95°C with
an aqueous alkaline solution using 10 g/L of sodium hydroxide while raising the temperature
of the aqueous alkaline solution under conditions of 2°C/min.
[0085] After draining immediately after alkali treatment at a liquid temperature of 95°C,
soaping was carried out for 15 minutes at a liquid temperature of 80°C followed by
draining and washing twice with hot water for 3 minute at a water temperature of 60°C.
[0086] After washing with hot water, draining and re-supplying with water, neutralization
was carried out using acetic acid followed by washing.
[0087] After draining, the tube wound with the yarn was removed from the cheese dyeing machine
and dehydrated with a centrifugal dehydrator followed by drying with a cheese dryer
to obtain a wound yarn body.
[0088] The reduction rate of the water absorbent polyester yarn of the resulting wound yarn
body was 6.0%, water absorbency after washing 30 times in accordance with Method 103
C of Attached Table 1 of JIS L0217:1995 was 15 seconds, and water absorbency after
washing 30 times in accordance with the F-2 medium temperature washer method of JIS
L1096:2010 was 15 seconds. The adhered amount of white powder was 0.73% by weight.
[COMPARATIVE EXAMPLE 2]
[0089] A wound yarn body was obtained by carrying out treatment using the same method as
Comparative Example 1 with the exception of using 2 g/L of oligomer dispersant in
the form of Marpon A-47 during soaping.
[0090] The reduction rate of the water absorbent polyester yarn of the resulting wound yarn
body was 6.0%, water absorbency after washing 30 times in accordance with Method 103
C of Attached Table 1 of JIS L0217:1995 was less than 1 second, and water absorbency
after washing 30 times in accordance with the F-2 medium temperature washer method
of JIS L1096:2010 was 2 seconds. The adhered amount of white powder was 0.64% by weight.
[COMPARATIVE EXAMPLE 3]
[0091] A wound yarn body was obtained by carrying out treatment using the same method as
Comparative Example 1 with the exception of using 2 g/L of oligomer dispersant in
the form of Marpon A-47 during soaping and using 1 g/L of oligomer dispersant in the
form of Marpon PS-K7 during neutralization.
[0092] The reduction rate of the water absorbent polyester yarn of the resulting wound yarn
body was 6.0%, water absorbency after washing 30 times in accordance with Method 103
C of Attached Table 1 of JIS L0217:1995 was less than 1 second, and water absorbency
after washing 30 times in accordance with the F-2 medium temperature washer method
of JIS L1096:2010 was 2 seconds. The adhered amount of white powder was 0.52% by weight.
[COMPARATIVE EXAMPLE 4]
[0093] A wound yarn body was obtained by carrying out treatment using the same method as
Comparative Example 1 with the exception of using 2 g/L of oligomer dispersant in
the form of Marpon A-47 during alkali treatment.
[0094] The reduction rate of the water absorbent polyester yarn of the resulting wound yarn
body was 6.0%, water absorbency after washing 30 times in accordance with Method 103
C of Attached Table 1 of JIS L0217:1995 was less than 1 second, and water absorbency
after washing 30 times in accordance with the F-2 medium temperature washer method
of JIS L1096:2010 was 2 seconds. The adhered amount of white powder was 0.47% by weight.
[COMPARATIVE EXAMPLE 5]
[0095] A wound yarn body was obtained by carrying out treatment using the same method as
Example 1 with the exception of setting the draining temperature following alkali
reduction to 70°C.
[0096] The reduction rate of the water absorbent polyester yarn of the resulting wound yarn
body was 6.0%, water absorbency after washing 30 times in accordance with Method 103
C of Attached Table 1 of JIS L0217:1995 was 6 seconds, and water absorbency after
washing 30 times in accordance with the F-2 medium temperature washer method of JIS
L1096:2010 was 13 seconds. The adhered amount of white powder was 0.82% by weight.
[COMPARATIVE EXAMPLE 6]
[0097] A wound yarn body was obtained by carrying out treatment using the same method as
Example 1 with the exception of using 6 g/L of oligomer dispersant in the form of
Marpon PS-K7 during neutralization.
[0098] The reduction rate of the water absorbent polyester yarn of the resulting wound yarn
body was 6.0%, water absorbency after washing 30 times in accordance with Method 103
C of Attached Table 1 of JIS L0217:1995 was 7 seconds, and water absorbency after
washing 30 times in accordance with the F-2 medium temperature washer method of JIS
L1096:2010 was 15 seconds. The adhered amount of white powder was 0.03% by weight.
[COMPARATIVE EXAMPLE 7]
[0099] A wound yarn body was obtained by carrying out treatment using the same method as
Example 1 with the exception of using 6 g/L of oligomer dispersant in the form of
Marpon PS-K7 during soaping.
[0100] The reduction rate of the water absorbent polyester yarn of the resulting wound yarn
body was 6.0%, water absorbency after washing 30 times in accordance with Method 103
C of Attached Table 1 of JIS L0217:1995 was 8 seconds, and water absorbency after
washing 30 times in accordance with the F-2 medium temperature washer method of JIS
L1096:2010 was 15 seconds. The adhered amount of white powder was 0.03% by weight.
[COMPARATIVE EXAMPLE 8]
[0101] A wound yarn body was obtained by carrying out treatment using the same method as
Example 1 with the exception of using 84 dtex/36 f polyester false twisted yarn having
a round cross-section and composed of regular polyester not containing sulfonic acid.
[0102] Water absorbency of the water absorbent polyester fiber of the resulting wound yarn
body after washing 30 times in accordance with Method 103 C of Attached Table 1 of
JIS L0217:1995 was 180 seconds or more, and water absorbency after washing 30 times
in accordance with the F-2 medium temperature washer method of JIS L1096:2010 was
180 seconds or more. The adhered amount of white powder was 0.02% by weight.
[0103] The manufacturing conditions, properties and other data relating to the polyester
wound yarn bodies obtained in the aforementioned Examples 1 to 3 and Comparative Examples
1 to 8 are summarized in the following Table 2.
[Table 2]
|
Elemental S content |
Winding density |
Wound amount |
Alkali reduction |
Draining |
Soaping |
Neutralization |
Water absorbency |
Adhered amount of white powder |
Concentration of terminal carboxylic acid linear oligomer (n=4) converted from internal
standard |
Presence of knit loops? |
NaOH concentration |
Chelating agent concentration |
Temp. |
Time |
Reduction rate |
Temp. |
Oligomer dispersant concentration |
Temp. |
Time |
Oligomer dispersant concentration |
After washing 30 times |
After industrial washing 30 times |
wt% |
g/cm3 |
kg |
g/L |
g/L |
°C |
Min |
% |
°C |
g/L |
°C |
Min |
g/L |
Sec |
Sec |
wt% |
Ex.1 |
0.14 |
0.5 |
3.0 |
10 |
2 |
95 |
60 |
6 |
95 |
2 |
80 |
15 |
1 |
<1 |
2 |
0.10 |
4.1 |
No |
Ex.2 |
0.14 |
0.5 |
3.0 |
10 |
1 |
95 |
60 |
6 |
95 |
1 |
80 |
15 |
0.5 |
<1 |
2 |
0.23 |
4.3 |
No |
Ex.3 |
0.14 |
0.5 |
3.0 |
10 |
2 |
95 |
60 |
6 |
95 |
2 |
80 |
15 |
2 |
4 |
4 |
0.05 |
3.1 |
No |
Comp. Ex.1 |
0.14 |
0.5 |
3.0 |
10 |
Absent |
95 |
60 |
6 |
95 |
Absent |
80 |
15 |
Absent |
2 |
4 |
0.73 |
6.0 |
No |
Comp. Ex.2 |
0.14 |
0.5 |
3.0 |
10 |
Absent |
95 |
60 |
6 |
95 |
2 |
80 |
15 |
Absent |
<1 |
2 |
0.64 |
4.2 |
No |
Comp. Ex.3 |
0.14 |
0.5 |
3.0 |
10 |
Absent |
95 |
60 |
6 |
95 |
2 |
80 |
15 |
1 |
<1 |
2 |
0.52 |
3.6 |
No |
Comp. Ex.4 |
0.14 |
0.5 |
3.0 |
10 |
2 |
95 |
60 |
6 |
95 |
Absent |
80 |
15 |
Absent |
<1 |
2 |
0.47 |
4.8 |
No |
Comp. Ex.5 |
0.14 |
0.5 |
3.0 |
10 |
2 |
95 |
60 |
6 |
70 |
2 |
80 |
15 |
1 |
6 |
13 |
0.82 |
4.4 |
No |
Comp. Ex.6 |
0.14 |
0.5 |
3.0 |
10 |
2 |
95 |
60 |
6 |
95 |
2 |
80 |
15 |
6 |
7 |
13 |
0.04 |
2.3 |
No |
Comp. Ex.7 |
0.14 |
0.5 |
3.0 |
10 |
2 |
95 |
60 |
6 |
95 |
6 |
80 |
15 |
1 |
8 |
15 |
0.03 |
2.1 |
No |
Comp. Ex.8 |
0 |
0.5 |
3.0 |
10 |
2 |
95 |
60 |
1.5 |
95 |
2 |
80 |
15 |
1 |
180 or more |
180 or more |
0.02 |
0.0 |
No |
INDUSTRIAL APPLICABILITY
[0104] The wound yarn body of a water absorbent polyester fiber of the present invention
absorbs water semi-permanently even in the case of not subjecting to water absorption
processing without generating white powder in the wound yarn rewinding step and knitting
step, is able to rapidly absorb perspiration when worn, demonstrates superior comfort,
and has a favorable soft feel on the skin, thereby enabling it to be preferably used
in innerwear, sportswear and the like.
REFERENCE SIGNS LIST
[0105]
- 1 Wound yarn body
- 2 Yarn
- 3 Snail guide
- 4 Ring tensioner
- 5 Traverse guide
- 6 Bobbin frame