[0001] Die vorliegende Erfindung bezieht sich auf ein Verfahren zum Bereitstellen eines
Medium-Mangan-Kaltband-Stahlzwischenproduktes mit reduziertem Kohlenstoff-Anteil und
auf Medium-Mangan-Kaltband-Stahlzwischenprodukte mit reduziertem Kohlenstoff-Anteil.
[0002] Sowohl die Zusammensetzung, respektive Legierung als auch die Wärmebehandlung im
Herstellungsprozess haben einen deutlichen Einfluss auf die Eigenschaften von Stahlprodukten.
[0003] Eine bedeutende Komponente heutiger Stahl-Legierungen ist Mangan (Mn). Der Mangan-Anteil
in Gew.% liegt dabei häufig im Bereich zwischen 3 und 12%. Bei diesen Stählen handelt
es sich daher um sogenannte Mittel-Mangan-Stähle, die auch als Medium-Mangan-Stähle
bezeichnet werden.
[0004] Medium-Mangan-Stähle zeichnen sich beispielsweise durch ein Gefüge aus, das aus einer
ferritischen Matrix und Restaustenit besteht. Der Anteil an Ferrit liegt bei Medium-Mangan-Stählen
gewöhnlich bei maximal 90 Vol.%. Der Austenit-Anteil hingegen liegt gewöhnlich im
Bereich von zirka 30 Vol.%.
[0005] Ferrit (auch alpha- oder α-Mischkristall genannt) ist die metallurgische Bezeichnung
eines kubisch raumzentrierten Eisenmischkristalls, in dessen Gitter Kohlenstoff interstitiell
(d.h. in Zwischenpositionen des Gitters) gelöst ist. Ein rein ferritisches Gefüge
besitzt eine geringe Festigkeit, aber eine hohe Duktilität. Durch Zugabe von Kohlenstoff
kann die Festigkeit verbessert werden, wobei das zu Lasten der Duktilität geht.
[0006] Ein Austenit-Gefüge (auch gamma- oder γ-Mischkristall genannt) ist ein kubisch flächenzentrierter
Eisenmischkristall, der sich in einem Stahlprodukt ausbilden kann. Es handelt sich
dabei um eine Hochtemperaturphase, die durch Zugabe von Legierungselementen, wie zum
Beispiel Kohlenstoff, Mangan, Nickel usw. bei Raumtemperatur stabilisiert werden kann.
[0007] Es hat im Laufe der Jahre mehrere Entwicklungsstufen oder -schübe im Bereich der
Medium-Mangan-Stähle gegeben.
[0008] In Fig. 1 ist ein Diagramm gezeigt, in dem die Bruchdehnung A
80 in Prozent über die Zugfestigkeit R
m in MPa aufgetragen ist. Das Diagramm der Fig. 1 gibt eine Übersicht über die Festigkeitsklassen
momentan eingesetzter Stahlwerkstoffe. Generell gilt die folgende Aussage: umso höher
die Zugfestigkeit einer Stahllegierung ist, umso geringer ist die Bruchdehnung dieser
Legierung. Vereinfacht ausgedrückt kann festgestellt werden, dass die Bruchdehnung
mit zunehmender Zugfestigkeit abnimmt und umgekehrt. Es muss also für jede Anwendung
ein optimaler Kompromiss zwischen der Bruchdehnung und der Zugfestigkeit gefunden
werden. Fig. 1 kann man Aussagen über den Zusammenhang zwischen der Festigkeit und
dem Umformvermögen verschiedener Stahlwerkstoffe entnehmen.
[0009] In dem Bereich, der mit dem Bezugszeichen 1 bezeichnet ist, sind die bereits erwähnten
Medium-Mangan-Stähle schematisch zusammengefasst. Der mit Bezugszeichen 1 bezeichnet
Bereich umfasst Medium-Mangan-Stähle mit einem Mn-Anteil zwischen 3 und 12 Gew.%.
[0010] Die sogenannten TRIP Stähle sind mit dem Bezugszeichen 2 bezeichnet und die sogenannten
TRIP baintic ferrite (TBF) und die Quenching and Partitioning (Q&P) Stähle tragen
das Bezugszeichen 3. TRIP steht im Englischen für "TRansformation Induced Plasticity".
[0011] Im Automobilsektor arbeitet man mit einer ganzen Reihe unterschiedlicher kaltumformbarer
Stahllegierungen, die jeweils speziell für ihr jeweiliges Einsatzgebiet am Fahrzeug
optimiert wurden. Bei Innen- und Außenpanelen, strukturellen Teilen und Stoßfängern
kommen Legierungen zum Einsatz, die eine gute Energieabsorption aufweisen. Legierungen
für die Außenhaut eines Fahrzeugs haben eine geringere Streckgrenze und Zugfestigkeit
typischerweise bis 600 MPa und eine höhere Bruchdehnung. Die Stahllegierungen von
Strukturbauteilen haben beispielsweise eine Zugfestigkeit im Bereich zwischen 600
und 1200 MPa. Hierfür eignen sich zum Beispiel die TRIP Stähle (Bezugszeichen 2 in
Fig. 1).
[0012] Mittlerweile gibt es Medium-Mangan-Stähle, die zur 3. Generation der Advanced High
Strength Steels (AHSS) zählen. Diese Stähle zeigen eine gute Kombination von Festigkeit
und Dehnung. Neuere Stähle der 3. Generation erreichen R
mxA
80-Werte von ca. 30.000 MPa% und eignen sich daher z.B. für die Herstellung komplizierter
Tiefziehbauteile, wie sie beispielsweise in der Automobilindustrie eingesetzt werden
(Bezugszeichen 1 in Fig. 1). Zur 3. Generation von höherfesten Stählen werden auch
die bereits genannten TBF und Q&P Stähle gezählt. Diese Stahlgüten sind zum Beispiel
geeignet für den Einsatz als Stahlbarrieren (z.B. für den Seitenaufprallschutz gegen
das Eindringen von Fahrzeugteilen). Sie haben einen Mangan-Anteil im Bereich zwischen
1,5 und 3 Gew.%.
[0013] Auf der Verfahrensseite gibt es zahlreiche verschiedene Wege zur Herstellung solcher
leistungsfähiger Stähle, wobei unter anderem die Temperaturbereiche, die vorgegeben
werden, die Heiz- und Kühlraten und andere Aspekte einen großen Einfluss auf das Gefüge
und somit auf die Qualität und Eigenschaften des Stahlproduktes haben.
[0014] Es besteht der Bedarf Kaltband-Stahlzwischenprodukte bereit zu stellen, die eine
verbesserte Umformbarkeit im Vergleich zu den bekannten Kaltband-Stahlzwischenprodukten
haben. Die Umformbarkeit setzt sich aus einem globalen und einem lokalen Anteil zusammen.
Die globale Umformbarkeit beschreibt vor allem das Verhalten des Materials bei Tiefziehoperationen.
Zur Beschreibung der globalen Umformbarkeit eignet sich die Gleichmaßdehnung A
g, in Englisch uniform elongation (UE). Die lokale Umformbarkeit ist hingegen ein Maß
für das Verhalten des Werkstoffes unter mehrachsigen Spannungszuständen, wie sie zum
Beispiel bei einem Lochaufweitungsversuch auftreten. Der Fracture thickness strain
in Prozent, fts abgekürzt, ist ein entsprechendes Maß für die lokale Umformbarkeit
von Stählen. Eine genaue Beschreibung dieses Kennwertes ist in
P. Larour et al., "Reduction of cross section area at fracture in tensile test: measurement
and applications for flat sheet steels", IDDRG 2017, zu finden.
[0015] Bisher musste meist ein Kompromiss gesucht werden zwischen der lokalen und globalen
Umformbarkeit. DP-Stähle (DP-Stahl steht für Dual-Phasen-Stahl) weisen deutlich niedrigere
fts-Werte auf als CP-Stähle (CP-Stahl steht für Complexphasen oder Komplexphasen-Stahl),
wie dem Diagramm der Fig. 2 zu entnehmen ist. Im Gegensatz dazu haben sie allerdings
eine bessere globale Umformbarkeit, charakterisiert durch den Wert der UE in Prozent.
Die homogenere Mikrostruktur der Komplexphasen-Stähle führt im Vergleich z.B. gegenüber
DP-Stählen zu hervorragenden Eigenschaften bei der lokalen Umformbarkeit und stellt
sich in höheren fts Werten dar.
[0016] Es gibt mehrere Gründe für die unterschiedlichen Eigenschaften von DP-Stählen und
CP-Stählen. Unter anderem liegt ein Grund in den unterschiedlichen Härtekontrasten
zwischen den einzelnen Gefügebestandteilen dieser Materialien. DP-Stähle haben typischerweise
einen hohen Härtekontrast des Gefüges im Vergleich zu den CP-Stählen. Die DP-Stähle
zeigen daher eine hohe Verfestigungsrate und somit eine hohe Dehnung, sprich hohe
UE-Werte. DP-Stähle sind nicht gut lokal umformbar, lassen sich aber gut tiefziehen.
CP-Stähle hingegen verfestigen weniger als die DP-Stähle und lassen sich daher besser
lokal umformen.
[0017] Medium-Mangan-Stähle, um die es hier geht, zeigen aufgrund ihres Gefüges einen ähnlich
hohen Härtekontrast wie die DP-Stähle, daher ist hier eine bessere globale Umformbarkeit,
d.h. höhere UE-Werte, zu erwarten. Der hohe Härtekontrast ergibt sich bei Medium-Mangan-Stählen
durch die Umwandlung von Restaustenit in harten Martensit während der Verformung.
Dadurch kommt es zu hohen Härtekontrasten zwischen der weichen ferritischen Matrix
und harten martensitischen Inklusionen.
[0018] Es stellt sich insbesondere die Aufgabe Kaltband-Stahlzwischenprodukte bereit zu
stellen, die eine gute Kombination aus der Zugfestigkeit und der Bruchdehnung haben
und die gleichzeitig eine gute lokale Umformbarkeit zeigen.
[0019] Es stellt sich insbesondere die Aufgabe Kaltband-Stahlzwischenprodukte bereit zu
stellen, die möglichst eine bessere Kombination aus Gleichmaßdehnung (in UE-Werten
ausgedrückt) und lokaler Umformbarkeit (in fts-Werten ausgedrückt) als DP- und CP-Stähle
haben.
[0020] Es wird ein Kaltband-Stahlzwischenprodukt bereit gestellt, dessen Gefüge eine niedrige
Martensitfestigkeit, eine möglichst hohe Ferritfestigkeit und wegen der hohen Stabilität
möglichst sich homogen und langsam umwandelnden Austenit umfasst.
[0021] Es wird ein Verfahren zum Bereitstellen eines Medium-Mangan-Kaltband-Stahlzwischenproduktes
beansprucht, dessen Legierung umfasst:
- einen Kohlenstoffanteil (C) im Bereich 0,003 Gew.% ≤ C ≤ 0,12 Gew.%,
- einen Mangananteil (Mn) im Bereich 3,5 Gew.% ≤ Mn ≤ 12 Gew.%,
- einen Siliziumanteil (Si) und/oder einen Aluminiumanteil (AI) als Legierungsanteile,
mit Si Gew.% + Al Gew.% < 1,
- optional weitere Legierungsanteile,
- optionalen Mikrolegierungsanteilen, insbesondere einen Titananteil (Ti) und/oder einen
Niobanteil (Nb) und/oder Vanadiumanteil (V), und
- wobei der Rest der Legierung Eisen (Fe) und unvermeidbare Verunreinigungen einer Schmelze
umfasst,
wobei das Verfahren den folgenden Schritt umfasst, der nach einem Kaltwalzschritt
ausgeführt wird:
- Durchführen eines interkritischen Hauben-Glühverfahrens mit einer maximalen Glühtemperatur
von 684°C - (517°C * dem Kohlenstoffanteil in Gew.%).
[0022] Bei mindestens einem Teil der Ausführungsformen wird das interkritische Hauben-Glühverfahren
als Teilverfahren eines einstufigen Glühverfahrens so gewählt, dass das Kaltband-Stahlzwischenprodukt
nach diesem Schritt eine Mikrostruktur mit den folgenden Anteilen aufweist:
- einen Restaustenit-Anteil im Bereich ≥ 10 % und ≤ 60 %, und vorzugsweise im Bereich
≥ 10 % und ≤ 40 %,
- einen alpha-Ferrit-Anteil im Bereich ≥ 20 % und ≤ 90 %, und vorzugsweise im Bereich
≥ 50 % und ≤ 80 %, und
- einen Zementit-Anteil im Bereich ≥ 0 % und ≤ 5 %.
Vorzugsweise wird bei diesen Ausführungsformen für das interkritische Hauben-Glühverfahren
eine maximale Glühtemperatur von 648°C - (352°C * dem Kohlenstoffanteil in Gew.%)
vorgegeben.
[0023] Bei mindestens einem Teil der Ausführungsformen wird das interkritische Hauben-Glühverfahren
als Teilverfahren eines zweistufigen Glühverfahrens so gewählt, dass das Kaltband-Stahlzwischenprodukt
nach diesem Schritt eine Mikrostruktur mit den folgenden Anteilen aufweist:
- einen Martensit-Anteil im Bereich ≥ 0 % und ≤ 20 %,%, und vorzugsweise im Bereich
≥ 0 % und ≤ 10 %,
- einen Restaustenit-Anteil im Bereich ≥ 10 % und ≤ 60 %, und vorzugsweise im Bereich
≥ 10 % und ≤ 40 %,
- einen alpha-Ferrit-Anteil im Bereich ≥ 20 % und ≤ 90 %, und vorzugsweise im Bereich
≥ 50 % und ≤ 80 % und
- einen Zementit-Anteil im Bereich ≥ 0 % und ≤ 5 %.
Vorzugsweise wird bei diesen Ausführungsformen vor dem interkritischen Hauben-Glühverfahren
ein vollaustenitisches Glühverfahren durchgeführt.
[0024] Bei mindestens einem Teil der Ausführungsformen wird speziell eine Glühtemperatur
gewählt, die abhängig ist von dem Kohlenstoffanteil in Gew.% und die kleiner ist als
die maximalen Glühtemperatur, um ein Medium-Mangan-Kaltband-Stahlzwischenprodukt zu
erhalten, dass einen fts-Wert aufweist, der mindestens 40% beträgt. Falls ein einstufiges
Glühverfahren zum Einsatz kommt, so wird diese maximale Glühtemperatur durch die Formel
648°C - (352°C * dem Kohlenstoffanteil in Gew.%) definiert. Falls ein zweistufiges
Glühverfahren zum Einsatz kommt, so wird diese maximale Glühtemperatur durch die Formel
684°C - (517°C * dem Kohlenstoffanteil in Gew.%) definiert.
[0025] Gemäß Erfindung wird durch eine Kombination eines Verfahrens- und eines Legierungskonzeptes
ein Stahlzwischenprodukt, vorzugsweise ein Kaltband-Stahlzwischenprodukt, bereitgestellt,
das eine gute lokale und eine gute globale Umformbarkeit aufweist.
[0026] Gemäß Erfindung wird ein Kaltband-Stahlzwischenprodukt bereit gestellt, das eine
gute R
m*A
80 Kombination, wie bei anderen Medium-Mangan-Stählen, und zugleich eine gute lokale
Umformbarkeit, d.h. hohe fts-Werte hat.
[0027] Solche Kaltband-Stahlzwischenprodukte werden durch das erfindungsgemäße Verfahren
bereitgestellt, indem der Kohlenstoffgehalt abgesenkt und die Ferritmorphologie, bzw.
Austenitmorphologie durch speziell angepasstes Glühen gezielt verändert wird. Weiterhin
wird ein Restaustenit mit hoher Stabilität durch das Absenken der interkritischen
Glühtemperatur, die während des Herstellens beim Glühen des Stahlzwischenproduktes
zur Anwendung kommt, eingestellt.
[0028] Obwohl typischerweise auf ein Erhöhen des Kohlenstoffanteils gesetzt wird, wenn man
eine erhöhte Festigkeit eines Stahlzwischenproduktes erzielen möchte, setzt die Erfindung
auf eine deutliche Reduktion des Kohlenstoffanteils. Durch die Reduktion des Kohlenstoffanteils
wird eine niedrigere Martensitfestigkeit erzielt, was einer Reduktion des Härtekontrastes
im Gefüge entspricht.
[0029] Obwohl typischerweise auf relativ hohe Silizium- und Aluminiumanteile gesetzt wird,
setzt die Erfindung auf eine deutliche Reduktion der Silizium- und Aluminiumanteile.
Die Silizium- und Aluminium-Legierungsanteile werden durch die Formel Si Gew.% + Al
Gew.% < 1 begrenzt. Da hier die Silizium- und Aluminium-Legierungsanteile begrenzt
sind, können die Glühverfahren mit veränderten Parametern durchgeführt werden.
[0030] Bei mindestens einem Teil der Ausführungsformen wird speziell auf eine Legierungszusammensetzung
gesetzt, die nur einen geringen Schwefel-Anteil umfasst. Vorzugsweise ist der Schwefel-Anteil
kleiner als 60ppm. Durch eine Reduktion des Schwefel-Anteils bilden sich weniger Sulfide
und die fts-Werte können sich, je nach Ausgestaltung des Glühverfahrens, verbessern.
[0031] Anhand thermodynamischer Modelle kann für eine Stahllegierung die optimale Glühtemperatur
berechnet werden, die man wählt, um den maximalen Restaustenitgehalt und somit eine
ausgezeichnete Kombination aus R
mxA
80 zu erzielen.
[0032] Das Verfahren der Erfindung basiert auf einer speziell optimierten Medium-Mangan-Legierung
und setzt zusätzlich auf eine niedrigere Glühtemperatur, da durch die niedrigere Temperatur
beim Glühen bessere Umformeigenschaften erzielt werden. Durch das Absenken der interkritischen
Glühtemperatur verliert die Medium-Mangan-Legierung der Erfindung etwas an Zugfestigkeit
und Gleichmaßdehnung, gleichzeitig kann aber eine höhere Restaustenitstabilität erreicht
werden, welche zu einer höheren globalen Umformbarkeit (d.h. zu höheren fts-Werten)
führt.
[0033] Um die Ferritmorphologie, bzw. die Austenitmorphologie gezielt zu verändern, kann
bei mindestens einem Teil der Ausführungsformen eine vollaustenitische Glühung, gefolgt
von einer interkritschen Glühung angewendet werden. Dadurch ergeben sich höhere fts-Werte
für die entsprechend geglühten Stahlzwischenprodukte.
[0034] Vorzugsweise wird die Erfindung eingesetzt, um Kaltband-Stahlzwischenprodukte in
Form von kaltgewalztem Flachzeug (z.B. Coils) bereit zu stellen.
ZEICHNUNGEN
[0035] Ausführungsbeispiele der Erfindung werden im Folgenden unter Bezugnahme auf die Zeichnungen
näher beschrieben.
- FIG. 1
- zeigt ein stark schematisiertes Diagramm, bei dem die Bruchdehnung Aso in Prozent
über die Zugfestigkeit Rm in MPa für verschiedene Stähle aufgetragen ist (Stand der Technik);
- FIG. 2
- zeigt ein stark schematisiertes Diagramm, bei dem der fracture thickness strain (fts)
in Prozent über die uniform elongation (UE) in Prozent für DP-Stähle und CP-Stähle
aufgetragen ist (Stand der Technik);
- FIG. 3
- zeigt ein stark schematisiertes Diagramm, bei dem für drei Medium-Mangan-Legierungen
mit unterschiedlichen Kohlenstoffgehalten der Erfindung der fracture thickness strain
(fts) in Prozent über die Temperatur aufgetragen ist, die beim Glühen verwendet wurde;
- FIG. 4
- zeigt ein stark schematisiertes Diagramm, in dem der fracture thickness strain (fts)
in Prozent über die Temperatur aufgetragen ist, wobei die fts-Werte einer Medium-Mangan-Stahl-Legierung
der Erfindung aufgetragen wurden, die einer 1. Glühroute (GR 1) mit einer Einfachglühung
und einer 2. Glühroute (GR 2) mit einer Doppelglühung unterzogen wurden;
- FIG. 5A
- zeigt ein stark schematisiertes Diagramm, bei dem der fracture thickness strain (fts)
in Prozent über die uniform elongation (UE) in Prozent für DP-Stähle, CP-Stähle und
für Medium-Mangan-Stahl-Legierung der Erfindung aufgetragen wurden, die der 1. Glühroute
( GR 1) unterzogen wurden;
- FIG. 5B
- zeigt ein stark schematisiertes Diagramm, bei dem der fracture thickness strain (fts)
in Prozent über die uniform elongation (UE) in Prozent für DP-Stähle, CP-Stähle und
für Medium-Mangan-Stahl-Legierung der Erfindung aufgetragen wurden, die der 2. Glühroute
( GR 2) unterzogen wurden;
- FIG. 6
- zeigt ein stark schematisiertes Diagramm, bei dem die Glühtemperatur über den Kohlenstoff-Anteil
für verschiedene Medium-Mangan-Stahl-Legierung der Erfindung aufgetragen wurde, wobei
konkret die experimentell ermittelten Glühtemperaturen TRAmax beim Erreichen der maximalen Restaustenitmenge als Funktion des Kohlenstoff-Anteils
gezeigt sind; weiterhin finden sich im Diagramm die maximal zulässigen Glühtemperaturen
TANmax für Einfach- und Doppelglühung, um einen erhöhten fts-Wert zu erreichen;
- FIG. 7
- zeigt ein stark schematisiertes Diagramm, bei dem der fracture thickness strain (fts)
in Prozent über verschiedene Festigkeitsklassen Rm in MPa aufgetragen wurde;
- FIG. 8
- zeigt eine schematische Darstellung eines beispielhaften Temperatur-Zeit-Diagramms
für die 1-stufige Temperaturbehandlung (GR 1) eines Stahl(zwischen)produkts der Erfindung;
- FIG. 9
- zeigt eine schematische Darstellung eines beispielhaften Temperatur-Zeit-Diagramms
für die 2-stufige Temperaturbehandlung (GR 2) eines Stahl(zwischen)produkts der Erfindung.
Detaillierte Beschreibung:
[0036] Die Kaltband-Stahlzwischenprodukte der Erfindung werden hergestellt, indem der Kohlenstoffgehalt
der Ausgangslegierung abgesenkt wird. Es hat sich gezeigt, dass sich der fts-Wert
durch das deutliche Reduzieren des Kohlenstoffgehaltes anheben lässt. Durch die Reduktion
des Kohlenstoffgehaltes wird der Härtekontrast im Gefüge reduziert. Dieser Zusammenhang
wurde anhand von Untersuchungen bestätigt und quantifiziert, wobei es sich gezeigt
hat, dass es Grenzen für den Kohlenstoffanteil gibt. Es kommen in Rahmen der Erfindung
daher nur Legierungen zum Einsatz, deren Kohlenstoffanteil kleiner ist als 0,12 Gew.%.
[0037] Der fts-Wert ist an einer geprüften nicht gekerbten Stahl-Flachzugprobe zu ermitteln.
Dabei ist die Ausgangsdicke des Stahlzwischenprodukts d
0 und die Dicke an der Bruchfläche d
1 zu bestimmen. Der fts-Wert berechnet sich folgendermaßen (d
o-d
1)/d
o*100 in %.
[0038] Die Fig. 3 zeigt ein Diagramm in dem die fts-Werte mehrerer Stahl-Legierungen der
Erfindung über die Glühtemperatur aufgetragen sind. Konkret wurden hier mehrere Proben
untersucht, die
- einen Kohlenstoffanteil (C) im Bereich von 0 Gew.% bis 0,12 Gew.% und
- einen Mangananteil (Mn) von 6 Gew.% umfassen,
wobei die Legierung Silizium (Si) und Aluminium (AI) gemäß der folgenden Formel Si
Gew.% + Al Gew.% < 1 enthält und
der Rest der Legierung Eisen (Fe) und unvermeidbare Verunreinigungen der jeweiligen
Schmelze aufweist.
[0039] Der Fig. 3 sind verschiedene Zusammenhänge zu entnehmen, wie folgt. Wenn man z.B.
eine Legierung 1 (Leg. 1 abgekürzt) mit der folgenden Zusammensetzung bei unterschiedlich
hohen Temperaturen glüht, dann sinkt der fts-Wert mit zunehmender Glühtemperatur deutlich
ab:
- einen Kohlenstoffanteil (C) von 0,12 Gew.%,
- einen Mangananteil (Mn) von 6 Gew.%,
- einen Siliziumanteil (Si) und/oder einen Aluminiumanteil (AI) als Legierungsanteile,
mit Si Gew.% + Al Gew.% < 1, und
- dem Rest der Legierung Eisen (Fe) und unvermeidbare Verunreinigungen.
[0040] Entsprechende Beobachtungen konnten auch für die Legierungen 2 und 3 (Leg. 2, Leg.
3 abgekürzt) gemacht werden.
[0041] Außerdem konnte gezeigt werden, dass der fts-Wert mit abnehmendem Kohlenstoffgehalt
deutlich zunimmt. Die Leg. 2 hat die folgende Zusammensetzung:
- einen Kohlenstoffanteil (C) von 0,056 Gew.%,
- einen Mangananteil (Mn) von 6 Gew.%,
- einen Siliziumanteil (Si) und/oder einen Aluminiumanteil (AI) als Legierungsanteile,
mit Si Gew.% + Al Gew.% < 1,
- und
- dem Rest der Legierung Eisen (Fe) und unvermeidbare Verunreinigungen.
[0042] Die Leg. 3 hat die folgende Zusammensetzung:
- einen Kohlenstoffanteil (C) von 0,0 Gew.%,
- einen Mangananteil (Mn) von 6 Gew.%,
- einen Siliziumanteil (Si) und/oder einen Aluminiumanteil (AI) als Legierungsanteile,
mit Si Gew.% + Al Gew.% < 1,
- und
- dem Rest der Legierung Eisen (Fe) und unvermeidbare Verunreinigungen.
[0043] Mit anderen Worten ausgedrückt, darf eine solche Medium-Mangan-Legierung nicht zu
hoch geglüht werden und sie sollte möglichst einen geringen Kohlenstoffanteil aufweisen,
wenn man hohe fts-Werte erzielen möchte. Der mit
-C bezeichnete Blockpfeil, der in Fig. 3 nach oben zeigt, soll andeuten, dass ein reduzierter
Kohlenstoffanteil zu einem erhöhten fts-Wert führt.
[0044] Das Absenken der Glühtemperatur führt zu einer höheren chemischen Anreicherung des
Austenits, zu einer kleineren Korngröße und zu einem stabileren Restaustenit. Untersuchungen
haben einen Restaustenit-Anteil ergeben, der bei den Legierungen der Erfindung vorteilhafterweise
im Bereich ≥ 10% und ≤ 60% liegt. Diese Effekte führen zu erhöhten fts-Werten.
[0045] Es wurde weiterhin der Einfluss verschiedener Glühverfahren auf die resultierenden
fts-Werte untersucht. Dabei wurden eine erste Glühroute (GR 1 abgekürzt) mit einem
interkritischen Haubenglühverfahren (Verfahren S.2.1 in Fig. 8) und eine zweite Glühroute
(GR 2 abgekürzt) mit einem vollaustenitischen Glühschritt (erfolgt in Hauben- beziehungsweise
Kontiglühe) gefolgt von einem interkritischen Haubenglühverfahren (Verfahren S.1+S.2.2
in Fig. 9), untersucht.
[0046] Die Fig. 4 zeigt ein Diagramm in dem die fts-Werte einer Stahl-Legierung der Erfindung
über die Glühtemperatur aufgetragen sind, wobei hier der Einfluss der ersten Glühroute
mit dem Einfluss der zweiten Glühroute verglichen wurde. Konkret wurde hier erfindungsgemäße
Stahl-Legierungsproben untersucht, die
- einen Kohlenstoffanteil (C) von 0,1 Gew.% und
- einen Mangananteil (Mn) von 6 Gew.% umfassen,
- einen Siliziumanteil (Si) und/oder einen Aluminiumanteil (AI) als Legierungsanteile,
mit Si Gew.% + Al Gew.% < 1,
wobei der Rest der Legierung Eisen (Fe) und unvermeidbare Verunreinigungen der jeweiligen
Schmelze aufweist.
[0047] Die Legierungsproben, die der ersten Glühroute GR 1 mit nur einer interkritischen
Haubenglühung (Verfahren S.2.1 in Fig. 8) unterzogen wurden, sind in Fig. 4 durch
schwarze Quadrate dargestellt. Hier zeigt sich, wie bereits im Zusammenhang mit Fig.
3 diskutiert, dass eine Reduktion der Glühtemperatur zu einer Zunahme der fts-Werte
führt, falls die Legierungsproben einen Kohlenstoffanteil aufweisen, der geringer
ist als 0,12 Gew.%. In Fig. 4 ist dieser Effekt durch einen schwarzen Blockpfeil dargestellt.
[0048] Die Legierungsproben, die der zweiten Glühroute GR 2 mit einem vollaustenitischen
Glühverfahren gefolgt von einem interkritischen Haubenglühverfahren (Verfahren S.1+S.2.2
in Fig. 9) unterzogen wurden, sind in Fig. 4 durch weiß gefüllte Rauten dargestellt.
Wenn man beispielweise eine erste Legierungsprobe der ersten Glühroute GR 1 unterzieht
und eine zweite, identische zweite Legierungsprobe der zweiten Glühroute GR 2 unterzieht,
dann zeigt die zweite Legierungsprobe einen fts-Wert, der höher ist als der fts-Wert
der ersten Legierungsprobe. In Fig. 4 ist dieser Effekt durch einen weißen Blockpfeil
dargestellt.
[0049] Wenn man eine Doppelglühung GR 2 mit einem vollaustenitischen Glühschritt (Verfahren
S.1 in Fig. 9), gefolgt von einem interkritischen Haubenglühverfahren (Verfahren S.2.2
in Fig. 9), durchführt, so führt dies zu einer Optimierung der Gefügestruktur. Konkret
hat sich gezeigt, dass die Ferritfestigkeit zunimmt und das die Stabilität des Restaustenits
erhöht wird.
[0050] Weitere Untersuchungen dieser Legierungsproben haben ergeben, dass sich im Vergleich
einer ersten Legierungsprobe, welche die erste Glühroute GR 1 durchlaufen hat, und
einer identischen zweiten Legierungsprobe, welche die zweite Glühroute GR 2 durchlaufen
hat, bei der zweiten Glühroute GR 2 auch eine Erhöhung der Uniform Elongation UE ergibt.
D.h., die Wahl der Glühroute und der Parameter (Haltetemperaturen H1 bzw. H2, Haltedauer
Δ1 bzw. Δ2, usw.) der jeweiligen Glührouten haben nicht nur einen Einfluss auf den
fts-Wert sondern auch einen Einfluss auf den UE-Wert.
[0051] Die Fig. 5A zeigt ein Diagramm in dem die fts-Werte verschiedener Stahl-Legierung
der Erfindung über die Uniform Elongation (UE) aufgetragen sind. Es geht hier um Stahl-Legierung
der Erfindung, die der ersten Glühroute GR 1 unterzogen wurden. Ähnlich wie in dem
Diagramm der Fig. 2, sind auch hier Stahllegierungen gezeigt, die entweder zu den
CP-Stählen oder zu den DP-Stähle gehören. Die Stahllegierungen der Erfindung liegen
in diesem Diagramm in einem Bereich, der kreuzschraffiert ist. Man kann anhand dieser
stark schematisierten Darstellung erkennen, dass die Stahllegierungen der Erfindung
im Vergleich zu den CP-Stählen deutlich höhere UE-Werte erreichen. Im Vergleich zu
den DP-Stählen hingegen erreichen sie deutlich höhere fts-Werte.
[0052] Es wurden hier Legierungsproben mit den folgenden Zusammensetzungen hergestellt und
der ersten Glühroute GR 1 unterzogen (siehe Tabelle 1). Für diese Legierungen konnten
Zugfestigkeiten R
m im Bereich zwischen 663 MPa und 873 MPa erzielt werden. Die fts-Werte dieser Legierungsproben
lagen im Bereich von ca. 48% bis 74% und die UE-Werte im Bereich von ca. 14% bis 32%.
Tabelle 1 |
Legierung Nr. |
C |
Mn |
Al |
Si |
Ti |
Fe |
1.1 |
0,1 |
6 |
1 |
0 |
|
Rest |
1.2 |
0,056 |
6 |
|
|
|
Rest |
1.3 |
0,003 |
6 |
|
|
|
Rest |
1.4 |
0,003 |
8 |
|
|
0,11 |
Rest |
1.5 |
0,003 |
10 |
|
|
0,10 |
Rest |
[0053] Die Fig. 5B zeigt ein weiteres Diagramm in dem die fts-Werte verschiedener Stahl-Legierung
der Erfindung über die Uniform Elongation (UE) aufgetragen sind. Es geht hier jedoch
um Stahl-Legierung der Erfindung, die der zweiten Glühroute GR 2 unterzogen wurden.
Die Stahllegierungen der Erfindung liegen in diesem Diagramm in einem Bereich, der
kreuzschraffiert ist. Man kann auch hier erkennen, dass die Stahllegierungen der Erfindung
im Vergleich zu den CP-Stählen deutlich höhere UE-Werte erreichen. Im Vergleich zu
den DP-Stählen hingegen erreichen sie deutlich höhere fts-Werte.
[0054] Es wurden hier Legierungsproben mit den folgenden Zusammensetzungen hergestellt und
der zweiten Glühroute GR 2 unterzogen (siehe Tabelle 2). Für diese Legierungen konnten
Zugfestigkeiten R
m im Bereich zwischen 597 MPa und 996 MPa erzielt werden. Die fts-Werte dieser Legierungsproben
lagen im Bereich von ca. 51% bis 75% und die UE-Werte im Bereich von ca. 10% bis 36%.
Tabelle 2 |
Legierung Nr. |
C |
Mn |
Al |
Si |
Ti |
Fe |
2.1 |
0,1 |
6 |
1 |
0 |
|
Rest |
2.2 |
0,12 |
6 |
|
|
|
Rest |
2.3 |
0,056 |
6 |
|
|
|
Rest |
2.4 |
0,003 |
6 |
|
|
|
Rest |
2.5 |
0,003 |
10 |
|
|
0,10 |
Rest |
[0055] Tabelle 3 stellt die mechanischen Kennwerte nach verschiedenen Temperaturbehandlungen
dar. Für die angeführten Temperaturbehandlungen sind Zugfestigkeiten im Bereich von
820 MPa und 875 MPa und Gleichmaßdehnungen im Bereich von 27 % und 31 % erreicht worden.
Die erreichten fts-Werte erweisen sich dabei als vorteilhaft. Bevorzugt ist ein vollaustenitisches
Glühen S.1 als Teil eines 2-stufigen Glühverfahrens GR 2 gemäß Fig. 9, bei dem eine
relativ lange Haltezeit von 1000 Minuten ≤ H1 ≤ 6000 Minuten vorgegeben wird. Nach
diesem vollaustenitischen Glühen folgt ein interkritisches Glühen S.2.2, wie in Fig.
9 gezeigt.
Tabelle 3 |
|
Rm |
UE |
fts |
Interkritisches Glühen (S.2.1) |
875 |
27 |
+ |
Vollaustenitisches Glühen (S.1) 10 Sekunden ≤ H1 ≤ 1000 Minuten + interkritisches
Glühen (S.2.2) |
860 |
31 |
++ |
Vollaustenitisches Glühen (S.1) 1000 Minuten ≤ H1 ≤ 6000 Minuten + interkritisches
Glühen (S.2.2) |
820 |
29 |
+++ |
[0056] Zusammenfassend kann für die untersuchten Legierungszusammensetzungen der Erfindung
das Folgende postuliert werden:
- es können mit den erfindungsgemäßen Legierungszusammensetzungen die folgenden charakteristischen
Werte erzielt werden, wenn auch das Glühen gemäß der Verfahrensvorgaben der Erfindung
erfolgt;
- es können Medium-Mangan-Kaltband-Stahlzwischenprodukte hergestellt werden, die fts-Werte
oberhalb von 40% haben;
- insbesondere können Medium-Mangan-Kaltband-Stahlzwischenprodukte mittels Einfachglühung
GR 1 (siehe Fig. 8) hergestellt werden, die fts-Werte im folgenden Bereich haben:
48% ≤ fts ≤ 74% (siehe Fig. 5A);
- insbesondere können Medium-Mangan-Kaltband-Stahlzwischenprodukte mittels Doppelglühung
GR 2 (siehe Fig. 9) hergestellt werden, die fts-Werte im folgenden Bereich haben:
51% ≤ fts ≤ 75% (siehe Fig. 5B);
- es können Medium-Mangan-Kaltband-Stahlzwischenprodukte hergestellt werden, die UE-Werte
oberhalb von 10% haben;
- insbesondere können Medium-Mangan-Kaltband-Stahlzwischenprodukte hergestellt werden,
die UE-Werte im folgenden Bereich haben: 14% ≤ UE ≤ 32% (siehe Fig. 5A);
- insbesondere können Medium-Mangan-Kaltband-Stahlzwischenprodukte hergestellt werden,
die UE-Werte im folgenden Bereich haben: 10% ≤ UE ≤ 36% (siehe Fig. 5A). UE = 10%
wurde hier als Minimalforderung angesetzt.
[0057] Zusammenfassend kann für die untersuchten Legierungszusammensetzungen der Erfindung
das Folgende postuliert werden:
- durch eine Reduktion des Kohlenstoffanteils einer Medium-Mangan-Legierung kann der
fts-Wert gesteigert werden;
- durch eine Reduktion der interkritischen Glühtemperatur T2, die für das Glühen S.2.1
oder S.2.2 einer solchen Medium-Mangan-Legierung verwendet wird, kann der fts-Wert
gesteigert werden;
- durch eine Wahl der Glühroute (Glühroute GR 1 oder GR 2) kann der fts-Wert gesteigert
werden;
- durch eine geeignete Reduktion der Silizium- und Aluminium-Legierungsanteile kann
das Stahlzwischenprodukt weiter optimiert werden;
- durch eine optionale Reduktion des Schwefelanteils kann das Stahlzwischenprodukt weiter
optimiert werden.
[0058] Diese Postulate, die zuvor in vereinfachter und rein schematisierte Form zusammengefasst
wurden, geben dem Entwickler eine Reihe von Freiheitsgraden bei der Definition von
Legierungen an die Hand. Am folgenden Beispiel soll dies veranschaulicht werden.
[0059] Da beim Doppelglühen (GR 2) höhere fts-Werte erzielt werden als beim Einfachglühen
(GR 1), kann man beim Doppelglühen GR 2 z.B. mit Legierungen arbeiten, deren Kohlenstoffanteil
per se etwas höher ist als beim Einfachglühen GR 1.
[0060] In Fig. 6 sind die verschiedenen Effekte, die anhand von erfindungsgemäßen Legierungszusammensetzungen
beobachtet wurden, in einem Diagramm dargestellt. Dieses Diagramm zeigt die Glühtemperatur
auf der Ordinate und den Kohlenstoff-Anteil der Legierungszusammensetzung auf der
Abszisse. Eingetragen sind die experimentell ermittelten maximalen Glühtemperaturen
T
ANmax beim Erreichen der verbesserten fts-Wert als Funktion des Kohlenstoff-Anteils.
[0061] Die gepunktete Linie, die die weißen Rauten verbindet, stellt die experimentell ermittelten
Glühtemperaturen T
ANmax für Legierungen dar, die einem Doppelglühverfahren (GR 2) unterzogen wurden. Die
gestrichelte Linie, die die schwarzen Quadrate verbindet, stellt die experimentell
ermittelten Glühtemperaturen T
ANmax für Legierungen dar, die einem Einfachglühverfahren (GR 1) unterzogen wurden. Die
durchgezogene Linie, die die weißen Kreise verbindet, stellt die experimentell ermittelten
Glühtemperaturen T
RAmax beim Erreichen der maximalen Restaustenitmenge als Funktion des Kohlenstoff-Anteils
dar.
[0062] Es wurden hier Legierungszusammensetzungen untersucht, die 6 Gew.% Anteil an Mangan
(Mn) aufweisen. Der Kohlenstoffanteil wurde, wie auf der Abszisse gezeigt, von 0 Gew.%
bis 0,12 Gew.% variiert.
[0063] Die gepunktete Linie in Fig. 6 kann durch die folgende Gleichung (1) beschrieben
werden, wobei T
ANmax die maximale Glühtemperatur ist. Die Gleichung (1) legt die maximale Glühtemperatur
T2 für das interkritische Glühen S.2.2 der Fig. 9 fest.

[0064] Die gestrichelte Linie in Fig. 6 kann durch die folgende Gleichung (2) beschrieben
werden. Die Gleichung (2) legt die maximale Glühtemperatur T2 für das interkritische
Glühen S.2.1 der Fig. 8 fest.

[0065] Durch die Untersuchungen, deren Ergebnisse in Fig. 6 zusammengefasst sind, wurde
bestätigt, dass man bei geringen Kohlenstoffanteilen mit relativ hohen Glühtemperaturen
arbeiten kann, um verbesserte fts-Werte zu erreichen. Bei höheren Kohlenstoffanteilen
muss entsprechend die Glühtemperatur T2 reduziert werden, um die verbesserten fts-Werte
zu erreichen.
[0066] Aus den in Fig. 6 zusammengefassten Ergebnissen kann man auch ableiten, dass das
Reduzieren des Kohlenstoffanteils auf Werte nahe 0 Gew.% derart wirksam ist, dass
man beim Glühen solcher Legierungszusammensetzungen mit der Glühtemperatur T2 sogar
über die Temperatur T
RAmax hinaus gehen kann, ohne dadurch den fts-Wert zu reduzieren. D.h., das Reduzieren
des Kohlenstoffanteils ist bei den Legierungen der Erfindung eine Einzelmaßnahme,
die besonders wirksam ist.
[0067] Aus den in Fig. 6 zusammengefassten Ergebnissen kann man auch ableiten, dass man
bei höheren Kohlenstoffanteilen, die beispielsweise im Bereich zwischen 0,05 Gew.%
und 0,12 Gew.% liegen, höhere fts-Werte dadurch erzielen kann, dass die Glühtemperatur
T2 reduziert wird. Je höher der Kohlenstoffanteil der erfindungsgemäßen Legierung
ist, umso größer muss die Reduktion der Glühtemperatur T2 sein.
[0068] Wenn man zweifach glüht, wie in Fig. 9 gezeigt, dann braucht die Glühtemperatur T2
erst bei Kohlenstoffanteilen von mehr als 0,056 Gew.% in Bezug auf T
RAmax abgesenkt zu werden.
[0069] In Fig. 7 sind weitere Aspekte der Erfindung in einem Diagramm dargestellt. Auf der
Abszisse sind die Festigkeitsklassen R
m in MPa und auf der Ordinate die fts-Werte in Prozent aufgetragen. Die Mindest-fts-Werte
sind durch eine schräg verlaufende, strichlierte Linie dargestellt, wobei als Randbedingung
von einem UE-Wert ausgegangen wurde, der mindestens 10% beträgt, d.h. UE ≥ 10%. Diese
strichlierte Linie kann mathematisch durch die Gleichung (3) beschrieben werden.

[0070] In Fig. 7 ist durch ein Rechteck, das mit dem Bezugszeichen 4 bezeichnet ist, der
Bereich dargestellt, der die Legierungen der Erfindung umfasst. Für Legierungen, die
innerhalb des Bereichs 4 liegen, ist gewährleistet, dass sie einerseits eine gute
lokale und andererseits eine gute globale Umformbarkeit aufweisen. Die UE-Werte liegen
stets oberhalb von 10% und die fts-Werte liegen stets oberhalb von 40%.
[0071] In der Tabelle 4 sind zusammenfassend einige charakteristische Eigenschaften der
Legierungen der Erfindung zusammengefasst.
Tabelle 4 |
charakteristische Eigenschaften |
|
|
fts [%] |
40 |
ca. 85 |
Rm [MPa] |
980 |
ca. 590 |
UE [%] |
> 10 |
|
[0072] In der Tabelle 5 sind einige Legierungszusammensetzungen und deren charakteristische
Eigenschaften zusammengefasst. Diese Legierungszusammensetzungen kombiniert mit einer
gemäß Erfindung gewählten Glühtemperatur sind bewusst in der Tabelle 5 gezeigt, da
sie außerhalb des Bereiches 4 liegen, der von der Erfindung abgesteckt wurde.
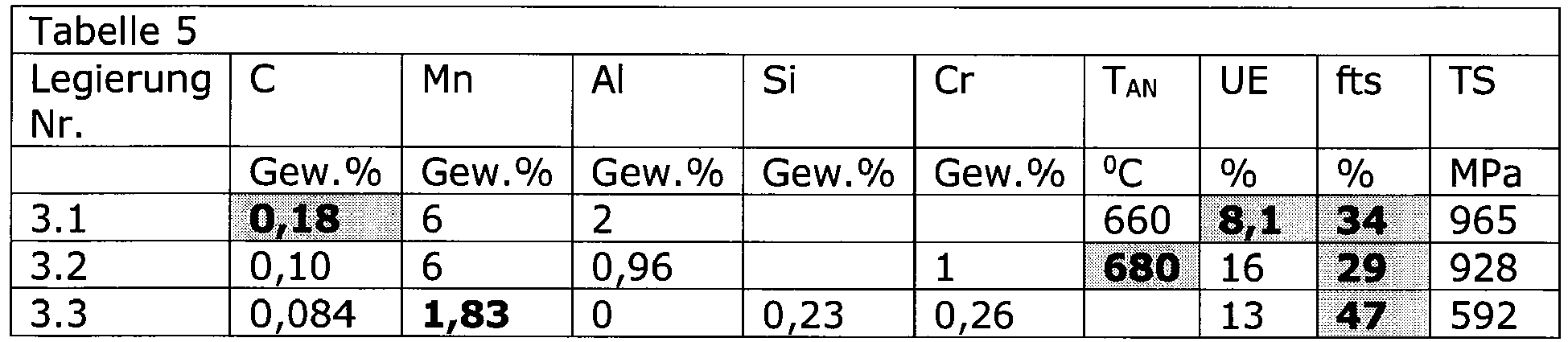
[0073] Die Probe Nr. 3.1 erreicht lediglich einen UE-Wert, der bei 8,1% liegt. Diese 8,1%
sind kleiner als der Mindest-UE-Wert von 10%. Eine der Ursachen für das Nichterreichen
des Mindest-UE-Wertes liegt in dem Kohlenstoffanteil, der mit 0,18 Gew.% oberhalb
der hier gesteckten Obergrenze von 0,12 Gew.% liegt. Weiterhin wird auch die Mindestanforderung
für den fts-Wert von 40% laut Formel 3 unterschritten.
[0074] Die Probe Nr. 3.2 erreicht zwar einen ausreichend hohen UE-Wert, aber der fts-Wert
liegt mit 29% deutlich unterhalb von fts
min= 40%. Aus der Gleichung (2) errechnet sich eine Glühtemperatur T2, die für diese
konkrete Legierung gemäß Erfindung maximal bei 612,8°C liegen sollte. Die Probe Nr.
3.2 wurde jedoch bei relativ hohen 680°C geglüht, was einen zu niedrigen fts-Wert
zur Folge hat.
[0075] Die Probe Nr. 3.3 erreicht zwar einen ausreichend hohen UE-Wert, aber der fts-Wert
liegt mit 47% deutlich unter dem geforderten fts-Wert von 57% nach Formel 3. Eine
der Ursachen für das Nichterreichen des Mindest-fts-Wertes liegt in dem Mangananteil,
der mit 1,83 Gew.% unterhalb der hier gesteckten Untergrenze von 3,5 Gew.% liegt.
[0076] Gemäß Erfindung setzt sich die Legierung somit aus den folgenden Bestandteilen zusammen:
- einen Kohlenstoffanteil (C) im Bereich 0,003 Gew.% ≤ C ≤ 0,12 Gew.%,
- einen Mangananteil (Mn) im Bereich 3,5 Gew.% ≤ Mn ≤ 12 Gew.%,
- einen Siliziumanteil (Si) und/oder einen Aluminiumanteil (AI) als Legierungsanteile,
mit Si Gew.% + Al Gew.% < 1,optional weitere Legierungsanteile,
- optionale Mikrolegierungsanteile, insbesondere einen Titananteil (Ti) und/oder einen
Niobanteil (Nb) und/oder Vanadiumanteil (V), und
- wobei der Rest der Legierung Eisen (Fe) und unvermeidbare Verunreinigungen einer Schmelze
umfasst.
[0077] Bei mindestens einem Teil der Ausführungsformen liegt der Kohlenstoffanteil (C) im
Bereich 0,003 Gew.% ≤ C ≤ 0,08 Gew.%, und/oder der Mangananteil (Mn) im Bereich 4
Gew.% ≤ Mn ≤ 10 Gew.%, insbesondere im Bereich 6 Gew.% ≤ Mn ≤ 10 Gew.%, da in diesem
Fall besonders hohe fts-Werte erzielt werden können.
[0078] Bei mindestens einem Teil der Ausführungsformen liegt der Siliziumanteil (Si) im
Bereich 0 Gew.% ≤ Si ≤ 1 Gew.%. Insbesondere liegt der Siliziumanteil (Si) im Bereich
0,2 Gew.% ≤ Si ≤ 0,9 Gew.%.
[0079] Bei mindestens einem Teil der Ausführungsformen liegt der Aluminiumanteil (AI) im
Bereich 0 Gew.% ≤ Al ≤ 1 Gew.%. Insbesondere liegt Aluminiumanteil (AI) im Bereich
0,01 Gew.% ≤ Al ≤ 0,7 Gew.%.
[0080] Bei mindestens einem Teil der Ausführungsformen umfasst die Legierung einen Schwefelanteil
(S) in Gew.%, der kleiner ist als 60ppm.
[0081] Bei mindestens einem Teil der Ausführungsformen umfasst die Legierung einen Chromanteil
(Cr) im Bereich 0 Gew.% ≤ Cr ≤ 1 Gew.%.
[0082] Bei mindestens einem Teil der Ausführungsformen umfasst die Legierung einen oder
mehr als einen der folgenden Mikrolegierungsanteile:
- Titananteil (Ti),
- Niobanteil (Nb),
- Vanadiumanteil (V).
[0083] Bei mindestens einem Teil der Ausführungsformen liegt der Titananteil (Ti), falls
vorhanden, im Bereich 0 Gew.% < Ti ≤ 0,12 Gew.%.
[0084] Bei mindestens einem Teil der Ausführungsformen haben die Mikrolegierungsanteile
zusammen maximal einen Anteil von 0,15 Gew.% der Legierung.
[0085] Die Angaben, die hier in Bezug auf die Zusammensetzung der Legierung gemacht werden,
verstehen sich jeweils in Gewichtsprozent. Der Rest der Legierung umfasst Eisen (Fe)
sowie Verunreinigungen, die sich in einer solchen Schmelze nicht vermeiden lassen.
Die Angaben in Gewichtsprozent summieren sich immer auf 100 Gew.%.
[0086] Wie bereits beschrieben, umfasst das Verfahren der Erfindung einen speziellen Glühschritt,
der nach einem Kaltwalzschritt ausgeführt wird: Durchführen eines interkritischen
Hauben-Glühverfahrens S.2.1 oder S.2.2 mit einer maximalen Glühtemperatur T2 von 684°C
- (517°C * dem Kohlenstoffanteil in Gew.%). Der Kohlenstoffanteil in Gew.% wird hier
auch als C% bezeichnet. Falls dieses interkritische Hauben-Glühverfahren Teil eine
einstufigen Glühverfahrens ist, so kann die maximale Glühtemperatur T2 sogar unterhalb
dieser Werte liegen, wie durch die Formel 648°C - (352°C * dem Kohlenstoffanteil in
Gew.%) ausgedrückt.
[0087] Beispielhafte Details eines einstufigen Glühverfahrens GR 1 sind in Fig. 8 gezeigt.
Bei dem interkritischen Hauben-Glühverfahren S.2.1 wird die Legierung auf eine Haltetemperatur
T2 erwärmt. In Fig. 8 ist das Erwärmen mit E2 bezeichnet. Dann wird die Legierung
für eine Haltedauer Δ2 auf der Haltetemperatur T2 gehalten. Anschließend erfolgt das
Abkühlen. In Fig. 8 ist das Abkühlen mit Ab2 bezeichnet. In der folgenden Tabelle
6 sind beispielhafte Parameter für ein einstufiges Glühverfahren GR 1 der Erfindung
angegeben:
Tabelle 6 |
E2 |
T2 |
Δ2 |
Ab2 |
100 Minuten < E2 < 1500 Minuten |
648°C - (352 °C * dem Kohlenstoffanteil in Gew.%) |
1000 Minuten < Δ2 < 6000 Minuten |
100 Minuten < Ab2 < 2500 Minuten |
[0088] Das interkritische Hauben-Glühverfahren wird auch kurz als interkritisches Glühen
bezeichnet, erfolgt mit einer Haltetemperatur T2 im α+γ - Zweiphasengebiet. Der Bereich
zwischen Ac
3 und Ac
1 (siehe Fig. 8 und 9) wird als α+γ - Zweiphasengebiet bezeichnet.
[0089] Das vollaustenitische Glühverfahren S.1 (siehe Fig. 9) erfolgt mit einer Haltetemperatur
T1 oberhalb der Ac
3-Temperatur im einphasigen γ -Gebiet, d.h. T1 > Ac
3.
[0090] Beispielhafte Details eines zweistufigen Glühverfahrens GR 2 sind in Fig. 9 gezeigt.
Bei dem vollaustenitische Glühverfahren S.1 wird die Legierung auf eine Haltetemperatur
T1 erwärmt. In Fig. 9 ist das Erwärmen mit E1 bezeichnet. Dann wird die Legierung
für eine Haltedauer Δ1 auf der Haltetemperatur T1 gehalten. Anschliessend erfolgt
das Abkühlen. In Fig. 9 ist das Abkühlen mit Ab1 bezeichnet. Bei dem anschliessenden
interkritischen Hauben-Glühverfahren S.2.2 wird die Legierung auf eine Haltetemperatur
T2 erwärmt. In Fig. 9 ist das Erwärmen mit E2 bezeichnet. dann wird die Legierung
für eine Haltedauer Δ2 auf der Haltetemperatur T2 gehalten. Anschließend erfolgt das
Abkühlen. In Fig. 9 ist das Abkühlen mit Ab2 bezeichnet. In der folgenden Tabelle
7 sind beispielhafte Parameter für ein zweistufiges Glühverfahren GR 2 der Erfindung
angegeben:
Tabelle 7 |
E1 |
T1 |
Δ1 |
Ab1 |
30 Sekunden < E1 < 1500 Minuten |
T1 > Ac3 |
10 Sekunden < Δ1 < 6000 Minuten |
30 Sekunden < Ab1 < 2500 Minuten |
E2 |
T2 |
Δ2 |
Ab2 |
100 Minuten < E2 < 1500 Minuten |
684°C - (517 °C * dem Kohlenstoffanteil in Gew.%) |
1000 Minuten < Δ2 < 6000 Minuten |
100 Minuten < Ab2 < 2500 Minuten |
[0091] Wie man den verschiedenen Diagrammen und der Beschreibung dieser Diagramme entnehmen
kann, ist es für das Erreichen hoher fts-Werte, die oberhalb von 40% liegen, wichtig,
dass die Glühtemperatur T2 für das interkritischen Hauben-Glühverfahren nicht zu hoch
angesetzt wird. Die maximale Glühtemperatur T2, die für interkritischen Hauben-Glühverfahren
angewendet wird, ist stets kleiner als Ac
3 und sie wird durch die Gleichungen (1) oder (2) nach oben hin begrenzt.
[0092] Die Eigenschaften des Kaltband-Stahlzwischenprodukts der Erfindung werden unter anderem
durch die Wahl der Glühtemperatur T1 und/oder T2 beeinflusst, wobei vor allem die
Temperatur T2 abhängig ist von dem Kohlenstoffanteil in Gew.% und stets kleiner ist
als die maximale Glühtemperatur Ac
3.
[0093] Es ergeben sich für die Kaltband-Stahlzwischenprodukte der Erfindung fts-Werte, die
gemäß Gleichung (3) mindestens 104*e
(-0.001*Rm) bei einer Mindestgleichmaßdehnung (A
g) von 10 % und bei einer Zugfestigkeit (R
m) im Bereich von 590 MPa bis 1350 MPa betragen. Diese fts-Werte wurden an nicht-gekerbten
Flachzugproben der Kaltband-Stahlzwischenprodukte ermittelt.
[0094] Das Kaltband-Stahlzwischenprodukt der Erfindung zeichnet sich unter anderem dadurch
aus, dass es eine Mikrostruktur mit den folgenden Anteilen aufweist, falls ein einstufiges
Glühverfahren GR 1 nach Fig. 8 zur Anwendung kommt:
- einen Restaustenit-Anteil im Bereich ≥ 10 % und ≤ 60 %,
- einen alpha-Ferrit-Anteil im Bereich ≥ 20 % und ≤ 90 % und
- einen Zementit-Anteil ((Fe, Mn)3C) im Bereich ≥ 0 % und ≤ 5 %.
[0095] Das Kaltband-Stahlzwischenprodukt der Erfindung zeichnet sich unter anderem dadurch
aus, dass es eine Mikrostruktur mit den folgenden Anteilen aufweist, falls ein zweistufiges
Glühverfahren GR 2 nach Fig. 9 zur Anwendung kommt:
- einen Martensit-Anteil im Bereich ≥ 0 % und ≤ 20 %,
- einen Restaustenit-Anteil im Bereich ≥ 10 % und ≤ 60 %,
- einen alpha-Ferrit-Anteil im Bereich ≥ 20 % und ≤ 90 % und
- einen Zementit-Anteil ((Fe, Mn)3C) im Bereich ≥ 0 % und ≤ 5 %.
[0096] Diese Mikrostruktur mit einem Martensit-Anteil, einem Restaustenit-Anteil, einem
alpha-Ferrit-Anteil und mit einem Zementit-Anteil sorgt für die speziellen Eigenschaften
des Kaltband-Stahlzwischenprodukts der Erfindung.
Bezugs- und Formelzeichen:
Bereich der Medium-Manqan-Stähle |
1 |
Bereich der TRIP-Stähle |
2 |
Bereich der TBF und Q&P Stähle |
3 |
Bereich |
4 |
austenitische Phase |
γ |
Zweiphasenqebiet |
α+γ |
Bruchdehnung in % |
A |
Abkühlen beim vollaustenitischen Glühen |
Ab1 |
Abkühlen beim interkritischen Glühen |
Ab2 |
Temperatur zu Beginn der Austenitbildung / Austenitstarttemperatur in °C |
Ac1 |
Temperatur zum Ende der Austenitbildung / Austenitendtemperatur in °C |
Ac3 |
Gleichmaßdehnunq in % |
Ag |
Bruchdehnung mit Messlänge 80 mm in % |
A80 |
Kohlenstoffanteil in Gewichtsprozent |
C% |
Erwärmen beim vollaustenitischen Glühen |
E1 |
Erwärmen beim interkritischen Glühen |
E2 |
Ausqanqsdicke des Stahlzwischenprodukts |
d0 |
Dicke an der Bruchfläche des Stahlzwischenprodukts |
d1 |
Zeitdauer des Haltens beim vollaustenitischen Glühen |
Δ1 |
Zeitdauer des Haltens beim interkritischen Glühen |
Δ2 |
fracture thickness strain in % |
fts |
Mindestwert des fracture thickness strain in % |
ftSmin |
ferritische Phase |
α |
Glühroute |
GR |
Halten beim vollaustenitischen Glühen |
H1 |
Halten beim interkritischen Glühen |
H2 |
Zugfestigkeit in MPa |
Rm |
vollaustenitisches Glühen |
S.1 |
interkritisches Glühen |
S.2.1, S2.2 |
Zeit |
t |
Haltetemperatur beim vollaustenitischen Glühen |
T1 |
Haltetemperatur beim interkritischen Glühen |
T2 |
maximale Glühtemperatur in °C |
TANmax |
Glühtemperatur beim Erreichen der maximalen Restaustenitmenge in °C |
TRAmax |
Uniform elongation in % |
UE |
1. Verfahren zum Bereitstellen eines Medium-Mangan-Kaltband-Stahlzwischenproduktes, dessen
Legierung umfasst:
- einen Kohlenstoffanteil (C) im Bereich 0,003 Gew.% ≤ C ≤ 0,12 Gew.%,
- einen Mangananteil (Mn) im Bereich 3,5 Gew.% ≤ Mn ≤ 12 Gew.%,
- einen Siliziumanteil (Si) und/oder einen Aluminiumanteil (AI) als Legierungsanteile,
mit Si Gew.% + Al Gew.% < 1,
- optional weitere Legierungsanteile,
- optionale Mikrolegierungsanteile, insbesondere einen Titananteil (Ti) und/oder einen
Niobanteil (Nb) und/oder Vanadiumanteil (V), und
- wobei der Rest der Legierung Eisen (Fe) und unvermeidbare Verunreinigungen einer
Schmelze umfasst,
wobei das Verfahren den folgenden Schritt umfasst, der nach einem Kaltwalzschritt
ausgeführt wird:
- Durchführen eines interkritischen Hauben-Glühverfahrens (S.2.1, S.2.2)mit einer
maximalen Glühtemperatur (T2) von 684°C - (517°C * dem Kohlenstoffanteil in Gew.%).
2. Verfahren nach Anspruch 1, dadurch gekennzeichnet, dass das interkritische Hauben-Glühverfahren (S.2.1, S.2.2) einen Erwärmungsschritt (E2),
eine Haltephase (H2) mit einer Haltedauer (Δ2) und einem Abkühlvorgang (Ab2) umfasst,
wobei die Haltedauer (Δ2) mehr als 1000 und weniger als 6000 Minuten und vorzugsweise
weniger als 5000 Minuten dauert.
3. Verfahren nach Anspruch 1 oder 2, dadurch gekennzeichnet, dass das Kaltband-Stahlzwischenprodukt, durch die Wahl einer Glühtemperatur (T2), die
abhängig ist von dem Kohlenstoffanteil in Gew.% und die kleiner ist als die maximalen
Glühtemperatur, einen fts-Wert aufweist, der mindestens 40% beträgt.
4. Verfahren nach Anspruch 1, 2 oder 3, dadurch gekennzeichnet, dass das Kaltband-Stahlzwischenprodukt, durch die Wahl einer Glühtemperatur (T2), die
abhängig ist von dem Kohlenstoffanteil in Gew.% und die kleiner ist als die maximalen
Glühtemperatur, einen fts-Wert aufweist, der mindestens 104*e(-0.001*Rm) bei einer Mindestgleichmaßdehnung (Ag) von 10 % und bei einer Zugfestigkeit (Rm) im Bereich von 590 MPa bis 1350 MPa beträgt, wobei dieser fts-Wert an einer nicht-gekerbten
Flachzugprobe des Kaltband-Stahlzwischenproduktes ermittelt wird.
5. Verfahren nach einem der Ansprüche 1 bis 4, dadurch gekennzeichnet, dass ein einstufiges Glühverfahren (GR 1) zur Anwendung kommt, bei dem nur das erwähnte
Hauben-Glühverfahren (S.2.1) mit einer interkritischen Glühtemperatur (T2) durchgeführt
wird, die oberhalb der Ac1-Temperatur und unterhalb einer maximalen Glühtemperatur liegt, die durch die Gleichung
648°C - (352°C * dem Kohlenstoffanteil in Gew.%) definiert ist.
6. Verfahren nach einem der Ansprüche 1 bis 4, dadurch gekennzeichnet, dass ein zweistufiges Glühverfahren (GR 2) zur Anwendung kommt, bei dem vor dem interkritischen
Hauben-Glühverfahren (S.2.2) ein vollaustenitisches Glühverfahren (S.1) angewendet
wird.
7. Verfahren nach Anspruch 6, dadurch gekennzeichnet, dass das vollaustenitische Glühverfahren (S.1) mit einer Glühtemperatur (T1) durchgeführt
wird, die oberhalb der Ac3-Temperatur liegt, wobei die Glühtemperatur (T1) vorzugsweise während einer Haltedauer
(Δ1) gehalten wird, die mindestens 10 Sekunden und vorzugsweise zwischen 10 Sekunden
und 6000 Minuten beträgt.
8. Verfahren nach einem der Ansprüche 6 bis 7, dadurch gekennzeichnet, dass ein zweistufiges Glühverfahren (GR 2) zur Anwendung kommt, bei dem zuerst ein vollaustenitisches
Glühen (S.1) oberhalb der Ac3-Temperatur und anschließend das interkritischen Hauben-Glühverfahren (S.2.2) mit
einer interkritischen Glühtemperatur durchgeführt wird, die oberhalb der Ac1-Temperatur und unterhalb der maximalen Glühtemperatur liegt.
9. Verfahren nach einem der Ansprüche 1 bis 8, dadurch gekennzeichnet, dass der Kohlenstoffanteil (C) im Bereich 0,003 Gew.% ≤ C ≤ 0,08 Gew.% liegt.
10. Verfahren nach einem der Ansprüche 1 bis 9, dadurch gekennzeichnet, dass der Mangananteil (Mn) im Bereich 4 Gew.% ≤ Mn ≤ 10 Gew.%, insbesondere im Bereich
5 Gew.% ≤ Mn ≤ 8 Gew.%, liegt.
11. Verfahren nach einem der Ansprüche 1 bis 10, dadurch gekennzeichnet, dass die Legierung einen Siliziumanteil (Si) im Bereich 0 Gew.% ≤ Si < 1 Gew.%, insbesondere
im Bereich 0,2 Gew.% ≤ Si ≤ 0,9 Gew.% umfasst.
12. Verfahren nach einem der Ansprüche 1 bis 11, dadurch gekennzeichnet, dass die Legierung einen Aluminiumanteil (AI) im Bereich 0 Gew.% ≤ Al < 1 Gew.%, insbesondere
im Bereich 0,01 Gew.% ≤ Al ≤ 0,7 Gew.% umfasst.
13. Verfahren nach einem der Ansprüche 1 bis 12, dadurch gekennzeichnet, dass die Legierung einen Chromanteil (Cr) im Bereich 0 Gew.% ≤ Cr ≤ 1 Gew.% umfasst.
14. Verfahren nach einem der Ansprüche 1 bis 13, dadurch gekennzeichnet, dass die Legierung einen Schwefelanteil (S) umfasst, der weniger als 60ppm beträgt.
15. Verfahren nach einem der Ansprüche 1 bis 14,
dadurch gekennzeichnet, dass die Legierung einen oder mehr als einen der folgenden Mikrolegierungsanteile umfasst:
- Titananteil (Ti),
- Niobanteil (Nb),
- Vanadiumanteil (V).
16. Verfahren nach Anspruch 15, dadurch gekennzeichnet, dass die Mikrolegierungsanteile zusammen maximal einen Anteil von 0,15 Gew.% haben.
17. Stahlzwischenprodukt, das nach einem Verfahren der Ansprüche 1-5 bereitgestellt wurde,
dadurch gekennzeichnet, dass es eine Mikrostruktur mit den folgenden Anteilen aufweist:
- einen Restaustenit-Anteil im Bereich ≥ 10 % und ≤ 60 %, %, und vorzugsweise im Bereich
≥ 10 % und ≤ 40 %,
- einen alpha-Ferrit-Anteil im Bereich ≥ 20 % und ≤ 90 %, und vorzugsweise im Bereich
≥ 50 % und ≤ 80 %, und
- einen Zementit-Anteil im Bereich ≥ 0 % und ≤ 5 %.
18. Stahlzwischenprodukt, das nach einem Verfahren der Ansprüche 6-8 bereitgestellt wurde,
dadurch gekennzeichnet, dass es eine Mikrostruktur mit den folgenden Anteilen aufweist:
- einen Martensit-Anteil im Bereich ≥ 0 % und ≤ 20 %, und vorzugsweise im Bereich
≥ 0 % und ≤ 10 %,
- einen Restaustenit-Anteil im Bereich ≥ 10 % und ≤ 60 %, und vorzugsweise im Bereich
≥ 10 % und ≤ 40 %,
- einen alpha-Ferrit-Anteil im Bereich ≥ 20 % und ≤ 90 %, und vorzugsweise im Bereich
≥ 50 % und ≤ 80 %, und
- einen Zementit-Anteil im Bereich ≥ 0 % und ≤ 5 %.