Technical Field
[0001] The present invention relates to a raw material for a cold-rolled stainless steel
sheet, the raw material being suitable for manufacturing a cold-rolled ferritic stainless
steel sheet having excellent corrosion resistance, formability, and ridging resistance,
and to a method for manufacturing the raw material.
Background Art
[0002] Ferritic stainless steel sheets are low-cost, excellent price-stable material compared
to austenitic stainless steel sheets since the Ni content is not high, and have been
used in various applications, such as building materials, transportation equipment,
and home electric appliances, due to excellent corrosion resistance. In particular,
unlike austenitic stainless steel sheets, ferritic stainless steel sheets have magnetism,
and, thus, are increasingly used in cooking tools, which are available for induction
heating (IH) systems. Cooking tools such as pots are mostly formed by bulging. Thus,
sufficient elongation is necessary to obtain a desired shape.
[0003] Meanwhile, ferritic stainless steel sheets have a problem in that, during forming,
surface irregularities (ridging) that deteriorate appearance frequently occur on the
surfaces. The surface appearance determines commercial value of cooking tools, therefore
if ridging occurs on their surface, a polishing step for removing the irregularities
must be performed after forming. In other words, there is a problem in that occurrence
of extensive ridging increases the manufacturing cost. In general, extensive ridging
tends to appear when larger strain is applied to the ferritic stainless steel sheet,
in other words, when severe working is performed.
[0004] In recent years, shapes of home cooking tools have become increasingly diverse, and
thus ferritic stainless steel sheets that can be subjected to severer working are
in demand. In other words, ferritic stainless steel sheets with higher elongation
are desirable.
[0005] However, it is also desirable to decrease the manufacturing cost of home cooking
tools. In other words, ferritic stainless steel sheets in which ridging that causes
the increase in manufacturing cost, is decreased are desired.
[0006] In response to these requests, there is a demand for a ferritic stainless steel sheet
that has higher elongation and reduces ridging sufficiently even if strain larger
than conventional one is applied.
[0007] Regarding the aforementioned problem, for example, Patent Literature 1 discloses
a ferritic stainless steel sheet having excellent formability, characterized in containing,
in terms of mass%, C: 0.02 to 0.06%, Si: 1.0% or less, Mn: 1.0% or less, P: 0.05%
or less, S: 0.01% or less, Al: 0.005% or less, Ti: 0.005% or less, Cr: 11 to 30%,
and Ni: 0.7% or less, and satisfying 0.06 ≤ (C + N) ≤ 0.12, 1 ≤ N/C, and 1.5 × 10
-3 ≤ (V × N) ≤ 1.5 × 10
-2 (C, N, and V respectively represents contents of the elements in mass%).
[0008] Patent Literature 2 discloses a method for manufacturing a ferritic stainless steel
sheet having excellent ridging resistance and formability, characterized in that a
hot-rolled sheet of a ferritic stainless steel sheet containing, in terms of weight%,
0.15% or less of C and 13 to 25% of Cr is annealed for 10 minutes or less in a range
of 930 to 990°C where austenite and ferrite phases coexist so as to form a two-phase
structure of a martensite phase and a ferrite phase, the resulting annealed sheet
is cold-rolled, and the resulting cold-rolled sheet is annealed in a range of 750
to 860°C.
[0009] Patent Literature 3 discloses a raw material for a cold-rolled stainless steel sheet,
containing, in terms of mass%, C: 0.007 to 0.05%, Si: 0.02 to 0.50%, Mn: 0.05 to 1.0%,
P: 0.04% or less, S: 0.01% or less, Cr: 15.5 to 18.0%, Al: 0.001 to 0.10%, and N:
0.01 to 0.06% with the balance being Fe and incidental impurities, in which the raw
material has a metal structure containing, in terms of area ratio, 10 to 60% of a
martensite phase and the balance being a ferrite phase, the martensite phase has a
hardness of the ferrite phase constituting the metal structure, and the martensite
phase has a hardness of HV500 or less.
Citation List
Patent Literature
[0010]
PTL 1: Japanese Patent No. 3584881
PTL 2: Japanese Examined Patent Application Publication No. 47-1878
PTL 3: International Publication No. 2015/111403
Summary of Invention
Technical Problem
[0011] In the invention disclosed in Patent Literature 1, ridging evaluation is carried
out on a test piece subjected to a prestrain of 20%, and ridging that occurs due to
severer working is not sufficiently evaluated. The inventors of the present invention
prepared various kinds of steel sheets by methods described in Patent Literature 1,
and the ridging height that occurred when a prestrain of 23% was applied was evaluated
by the method described below. However, none of the steel sheets exhibited excellent
ridging resistance.
[0012] In the invention disclosed in Patent Literature 2, the prestrain applied to evaluate
ridging is not described. The inventors of the present invention prepared various
kinds of steel sheets by methods described in Patent Literature 2, and the ridging
height that occurred when a prestrain of 23% was applied was evaluated by the ridging
evaluation method described below. As a result, none of the steel sheets exhibited
excellent ridging resistance. In addition, in this invention, the shape of the test
piece used for evaluating elongation is not described. It is a well-known fact that
the value of elongation obtained changes depending on the shape of the test piece
used for evaluation.
[0013] The inventors of the present invention prepared various kinds of steel sheets by
methods described in Patent Literature 2, and the elongation after fracture of the
steel sheets was evaluated by the tensile test method described below. As a result,
none of the steel sheets exhibited excellent formability.
[0014] The inventors of the present invention prepared various kinds of steel sheets by
methods described in Patent Literature 3, and the elongation after fracture of the
steel sheets was evaluated by the tensile test method described below. As a result,
none of the steel sheets exhibited excellent formability.
[0015] The present invention has been developed under the current circumstances described
above, and an object thereof is to provide a raw material for a cold-rolled stainless
steel sheet, the raw material being suitable for manufacturing a cold-rolled ferritic
stainless steel sheet having excellent corrosion resistance, formability, and ridging
resistance, and a method for manufacturing the raw material.
[0016] Here, "excellent corrosion resistance" means that the rust area ratio measured by
the method described below is 30% or less. Preferably, the rust area ratio is 20%
or less. The corrosion test for evaluating the corrosion resistance is carried out
in accordance with JASO M609-91. First, in the testing method, a test piece is polished
with an emery paper to #600, washed with water, and ultrasonically degreased in ethanol
for 5 minutes. Subsequently, a three-cycle corrosion test is carried out, each cycle
consisting of salt spraying (5 mass% aqueous NaCl solution, 35°C) 2h → drying (60°C,
relative humidity: 40%) 4h → wetting (50°C, relative humidity: 95% or more) 2h. After
the test, the appearance of the corroded surface is photographed, and a 30 mm × 30
mm region at the center of the test piece in the photographed image is subjected to
image analysis to calculate the rust area ratio.
[0017] Furthermore, "excellent formability" means that the elongation after fracture of
the steel sheet measured by the method described below is 28% or more. More preferably,
the elongation after fracture is 32% or more. In order to evaluate the elongation
after fracture, first, JIS No. 13B tensile test pieces are taken in accordance with
JIS Z 2241 such that longitudinal directions thereof are, respectively, the rolling
direction (L direction), a direction 45 degrees with respect to the rolling direction
(D direction), and a direction 90 degrees with respect to the rolling direction (C
direction). Subsequently, a tensile test is carried out in accordance with JIS Z 2241,
and the elongation after fracture (El) is measured for each test piece. The three-direction
average ((L + 2D + C)/4, where L, D, and C respectively represent elongation after
fracture (%) in the respective directions) of the obtained elongation after fracture
is calculated, and is determined to be the elongation after fracture of the steel
sheet.
[0018] Furthermore, "excellent ridging resistance" means that the ridging height of the
steel sheet surface measured by the method described below is 3.0 µm or less. More
preferably, the ridging height is 2.5 µm or less. Yet more preferably, the ridging
height is 2.0 µm or less. To measure the ridging height of the steel sheet surface,
first, a JIS No. 5 tensile test piece is taken in a direction parallel to the rolling
direction. Next, after the surface of the test piece is polished with a #600 emery
paper, a tensile strain of 23% is applied. Next, the surface profile is measured with
a laser displacement meter in a direction 90 degrees with respect to the rolling direction
on a polished surface of the parallel portion of the test piece. The measurement length
is 16 mm per line, and the height is measured with 0.05 mm increments. In addition,
the line interval is set to 0.1 mm, and a total of fifty lines are measured. The obtained
profile data of each line is smoothed and subjected to a waviness removal process
by using a Hanning window function-type finite impulse response (FIR) bandpass filter
with a high-cut filter wavelength of 0.8 mm and a low-cut filter wavelength of 8 mm.
[0019] Subsequently, on the basis of the processed profile data of each line, the data corresponding
to 2 mm portions at both ends of each line is eliminated, and the arithmetic mean
waviness Wa prescribed in JIS B 0601 (2001) is measured for each line. The average
value of the values of the arithmetic mean waviness, Wa, of fifty lines is the ridging
height of the steel sheet surface.
[0020] Note that, in the ridging resistance evaluation of the related art, test pieces subjected
to a 15% or 20% tensile strain are mostly used. However, the assumption of the present
invention is that the steel sheet is formed into a shape more complex than that in
the related art. Thus, the tensile strain applied to the test pieces is set to 23%
for evaluation under the assumption that the steel sheet is formed more severely,
in other words, is subjected to higher strain than in the related art.
Solution to Problem
[0021] To address the problems described above, the inventors of the present invention have
investigated a raw material for a cold-rolled stainless steel sheet, the raw material
being suitable for manufacturing a cold-rolled ferritic stainless steel sheet having
excellent corrosion resistance, formability, and ridging resistance, and a method
for manufacturing the raw material. As a result, the following was found.
[0022] A cold-rolled ferritic stainless steel sheet having excellent formability and ridging
resistance is obtained by using a raw material for a cold-rolled stainless steel sheet
prepared by hot-rolling and then annealing a ferritic stainless steel with an appropriate
chemical composition in a preferable temperature region that constitutes a ferrite-austenite
two-phase region before cold-rolling, and then cold-rolling this raw material and
annealing the resulting cold-rolled sheet.
[0023] Specifically, in the steel chemical composition, the C content is set to 0.030% or
less, the Cr content is set to 14.4% or less, and the N content is set to 0.060% or
less. A steel ingot having the aforementioned composition is hot-rolled, and the hot
rolled sheet is annealed at 900 to 1100°C, which is the ferrite-austenite two-phase
region. In this hot-rolled sheet annealing, the steel composition is adjusted so that
the area ratio of the austenite phase is 10 to 90%. Within the steel chemical composition
range of the present invention, nearly all of this austenite phase is transformed
into a martensite phase during the cooling process after the hot-rolled sheet annealing.
Such a hot-rolled and annealed sheet (raw material for a cold-rolled steel sheet)
having a martensite phase is then cold-rolled so as to destroy colonies (crystal grain
groups having similar crystal orientations), that cause ridging, and efficiently apply
the rolling strain to the ferrite/martensite grain boundaries. Since the rolling strain
is efficiently applied as described above and since the Cr content, the C content,
and the N content in the steel are sufficiently low, recrystallization is accelerated
during the cold-rolled sheet annealing. By the recrystallization accelerating effect,
the cold-rolled sheet is recrystallized sufficiently in the temperature range of 780
to 830°C, which is a ferrite single phase region, and a cold-rolled and annealed sheet
(cold-rolled ferritic stainless steel sheet) having excellent formability is obtained.
Furthermore, by the colony destroying effect described above, the cold-rolled and
annealed sheet exhibits excellent ridging resistance.
[0024] The present invention is based on the aforementioned findings, and the features are
summarized as follows.
- [1] A raw material for a cold-rolled stainless steel sheet, the raw material having
a chemical composition containing, in terms of mass%,
C: 0.005 to 0.030%,
Si: 0.05 to 1.00%,
Mn: 0.05 to 1.00%,
P: 0.040% or less,
S: 0.030% or less,
Al: 0.001 to 0.150%,
Cr: 10.8 to 14.4%,
Ni: 0.01 to 2.50%, and
N: 0.005 to 0.060%,
with the balance being Fe and incidental impurities,
in which the raw material has a structure containing 10 to 90% of a martensite phase
in terms of area ratio with the balance being a ferrite phase.
- [2] The raw material for a cold-rolled stainless steel sheet described in [1], in
which the chemical composition further contains, in terms of mass%, one or two or
more selected from
Co: 0.01 to 0.50%,
Cu: 0.01 to 0.80%,
Mo: 0.01 to 0.30%, and
W: 0.01 to 0.50%.
- [3] The raw material for a ferritic stainless steel sheet described in [1] or [2],
in which the chemical composition further contains, in terms of mass%, one or two
or more selected from
Ti: 0.01 to 0.30%,
V: 0.01 to 0.10%,
Zr: 0.01 to 0.10%, and
Nb: 0.01 to 0.30%; and
a value of formula (1) below is 0.0 or less:

where, in formula (1) above, respective element symbols represent contents (mass%)
of respective elements, or represent 0 when corresponding elements are not contained.
- [4] The raw material for a cold-rolled stainless steel sheet described in any one
of [1] to [3], in which the chemical composition further contains, in terms of mass%,
one or two or more selected from
B: 0.0003 to 0.0030%,
Mg: 0.0005 to 0.0100%,
Ca: 0.0003 to 0.0030%,
Y: 0.01 to 0.20%, and
REM (rare earth metal): 0.001 to 0.100%.
- [5] The raw material for a cold-rolled stainless steel sheet described in any one
of [1] to [4], in which the chemical composition further contains, in terms of mass%,
one or two selected from
Sn: 0.001 to 0.500% and
Sb: 0.001 to 0.500%.
- [6] A method for manufacturing the raw material for a cold-rolled stainless steel
sheet described in any one of [1] to [5], the method including:
hot-rolling a steel slab having the chemical composition to prepare a hot-rolled sheet,
and performing hot-rolled sheet annealing that involves holding the hot-rolled sheet
in a temperature range of 900°C or more and 1100°C or less for 5 seconds to 15 minutes.
Advantageous Effects of Invention
[0025] The present invention provides a raw material for a cold-rolled stainless steel sheet,
the raw material being suitable for manufacturing a cold-rolled ferritic stainless
steel sheet having excellent corrosion resistance, formability, and ridging resistance,
and a method for manufacturing the raw material.
Description of Embodiments
[0026] The present invention will now be specifically described.
[0027] A raw material for a cold-rolled stainless steel sheet according to the present invention
has a chemical composition containing, in terms of mass%, C: 0.005 to 0.030%, Si:
0.05 to 1.00%, Mn: 0.05 to 1.00%, P: 0.040% or less, S: 0.030% or less, Al: 0.001
to 0.150%, Cr: 10.8 to 14.4%, Ni: 0.01 to 2.50%, and N: 0.005 to 0.060%, with the
balance being Fe and incidental impurities, and has a structure containing 10 to 90%
of a martensite phase on an area ratio basis with the balance being a ferrite phase.
By using the raw material for a cold-rolled stainless steel sheet of the present invention,
a cold-rolled ferritic stainless steel sheet having excellent corrosion resistance,
formability, and ridging resistance can be manufactured.
[0028] First, the reasons for limiting the chemical composition to the aforementioned ranges
in the present invention are described. Note that % indicating the unit of the content
of a composition means mass% unless otherwise noted.
C: 0.005 to 0.030%
[0029] Carbon (C) is an element effective for increasing the strength of the steel. Furthermore,
C is an element that improves ridging resistance since it promotes formation of the
austenite phase during the hot-rolled sheet annealing. This effect is obtained at
a C content of 0.005% or more. However, at a C content exceeding 0.030%, formability
deteriorates due to an increase in the hardness of the steel. Thus, the C content
is set to 0.005 to 0.030%. The C content is preferably 0.007% or more and more preferably
0.010% or more. The C content is preferably 0.020% or less and more preferably 0.015%
or less.
Si: 0.05 to 1.00%
[0030] Silicon (Si) is an element useful as a deoxidant. This effect is obtained at a Si
content of 0.05% or more. However, at a Si content exceeding 1.00%, formability deteriorates
due to an increase in the hardness of the steel. Furthermore, since the amount of
the austenite phase formed during the hot-rolled sheet annealing decreases, the ridging
resistance deteriorates. Thus, the Si content is set to 0.05 to 1.00%. The Si content
is preferably 0.07% or more, more preferably 0.10% or more, and yet more preferably
0.20% or more. The Si content is preferably 0.50% or less, more preferably less than
0.40%, and yet more preferably less than 0.30%.
Mn: 0.05 to 1.00%
[0031] Manganese (Mn) has a deoxidizing effect. Furthermore, Mn is an element that improves
the ridging resistance since it promotes formation of the austenite phase during the
hot-rolled sheet annealing. This effect is obtained at a Mn content of 0.05% or more.
However, at a Mn content exceeding 1.00%, precipitation and coarsening of MnS are
accelerated, and corrosion resistance deteriorates since MnS serves as a starting
point of rust generation. Thus, the Mn content is set to 0.05 to 1.00%. The Mn content
is preferably 0.10% or more and more preferably 0.15% or more. The Mn content is preferably
0.80% or less and more preferably 0.60% or less.
P: 0.040% or less
[0032] Phosphorus (P) is an element that deteriorates corrosion resistance. Moreover, P
segregates in crystal grain boundaries and deteriorates hot workability. Thus, the
P content is preferably as low as possible, and is set to 0.040% or less. Preferably,
the P content is 0.030% or less.
S: 0.030% or less
[0033] Sulfur (S) forms a precipitate, MnS, with Mn. Since this MnS serves as a starting
point of corrosion pitting, corrosion resistance deteriorates. Thus, the S content
is preferably as low as possible, and is set to 0.030% or less. Preferably, the S
content is 0.020% or less.
Al: 0.001 to 0.150%
[0034] Aluminum (Al) is an element effective for deoxidation. This effect is obtained at
an Al content of 0.001% or more. However, at an Al content exceeding 0.150%, the formability
deteriorates due to an increase in the hardness of the steel. Thus, the Al content
is set to 0.001 to 0.150%. The Al content is preferably 0.005% or more and more preferably
0.010% or more. The Al content is preferably 0.100% or less and more preferably 0.050%
or less.
Cr: 10.8 to 14.4%
[0035] Chromium (Cr) is an element that improves corrosion resistance by forming passive
film. At a Cr content less than 10.8%, sufficient corrosion resistance is not obtained.
Meanwhile, at a Cr content exceeding 14.4%, since the austenite phase is not formed
sufficiently in the steel during the hot-rolled sheet annealing process, the ridging
resistance is deteriorated, and the formability deteriorates due to an increase in
hardness of the steel. Thus, the Cr content is set to 10.8 to 14.4%. The Cr content
is preferably 11.0% or more, more preferably 11.5% or more, and yet more preferably
12.0% or more. The Cr content is preferably 14.0% or less, more preferably 13.5% or
less, and yet more preferably 13.0% or less.
Ni: 0.01 to 2.50%
[0036] Nickel (Ni) is an element that suppresses active dissolution in a low pH environment.
In a so-called crevice structure in which steel sheets are overlapped each other,
a low pH environment, that easily causes corrosion, is sometimes formed. Furthermore,
in cases other than the crevice structure formed between the steel sheets as described
above, an aqueous solution containing chloride ions, that cause rusting of steel sheets,
may become condense on the steel sheets, salt may precipitate from the aqueous solution,
and a crevice structure may be formed between the precipitated salt and the steel
sheet such that a low pH environment that easily causes corrosion is formed. Ni suppresses
progress of corrosion in such environments, and improves corrosion resistance of the
steel. In other words, Ni is highly effective for improving the crevice corrosion
resistance, suppresses progress of corrosion in an active dissolution state markedly,
and thereby improves corrosion resistance. Furthermore, Ni is an element that improves
ridging resistance since it promotes formation of the austenite phase during the hot-rolled
sheet annealing.
[0037] This effect is obtained at a Ni content of 0.01% or more. However, at a Ni content
exceeding 2.50%, formability deteriorates due to an increase in the hardness of the
steel. Thus, the Ni content is set to 0.01 to 2.50%. The Ni content is preferably
0.03% or more, more preferably 0.05% or more, and yet more preferably 0.10% or more.
The Ni content is preferably 1.20% or less, more preferably 0.80% or less, and yet
more preferably 0.25% or less.
N: 0.005 to 0.060%
[0038] Nitrogen (N) is an element effective for increasing the strength of the steel. Furthermore,
nitrogen is an element that improves ridging resistance since it promotes formation
of the austenite phase during the hot-rolled sheet annealing. This effect is obtained
at a N content of 0.005% or more. However, at a N content exceeding 0.060%, formability
of the steel deteriorates due to an increase in the hardness of the steel. Thus, the
N content is set to 0.005 to 0.060%. The N content is preferably 0.007% or more and
more preferably 0.010% or more. The N content is preferably 0.020% or less and more
preferably 0.015% or less.
[0039] The balance other than the elements described above is Fe and incidental impurities.
Representative examples of the incidental impurities include O (oxygen), Zn, Ga, Ge,
As, Ag, In, Hf, Ta, Re, Os, Ir, Pt, Au, and Pb. Among these elements, O (oxygen) can
be contained in an amount of 0.02% or less. A total of 0.1% or less of other elements
can be contained.
[0040] In the present invention, the following elements may be contained as appropriate
in addition to the basic components described above.
Co: 0.01 to 0.50%
[0041] Cobalt (Co) is an element that improves crevice corrosion resistance of stainless
steel. However, excessively containing Co results in saturated effects and deterioration
of the workability. Thus, if Co is to be contained, the Co content is preferably 0.01
to 0.50%. The Co content is more preferably 0.30% or less and yet more preferably
0.10% or less.
Cu: 0.01 to 0.80%
[0042] Copper (Cu) is an element that improves corrosion resistance by strengthening the
passive film. However, excessively containing Cu results in saturated effects and
deterioration of the workability; furthermore, ε-Cu tends to precipitate and the corrosion
resistance is deteriorated. Thus, if Cu is to be contained, the Cu content is preferably
0.01 to 0.80%. The Cu content is more preferably 0.15% or more and yet more preferably
0.40% or more. The Cu content is more preferably 0.60% or less and yet more preferably
0.45% or less.
Mo: 0.01 to 0.30%
[0043] Molybdenum (Mo) has an effect of improving crevice corrosion resistance of stainless
steel. However, excessively containing Mo results in saturated effects and deterioration
of the workability. Thus, if Mo is to be contained, the Mo content is preferably 0.01
to 0.30%. The Mo content is more preferably 0.20% or less and yet more preferably
0.10% or less.
W: 0.01 to 0.50%
[0044] Tungsten (W) is an element that improves crevice corrosion resistance of stainless
steel. However, excessively containing W results in saturated effects and deterioration
of the workability. Thus, if W is to be contained, the W content is preferably 0.01
to 0.50%. The W content is more preferably 0.03% or more and yet more preferably 0.05%
or more. The W content is more preferably 0.30% or less and yet more preferably 0.10%
or less.
Ti: 0.01 to 0.30%
[0045] Titanium (Ti) is an element that has an effect of improving formability of the cold-rolled
and annealed sheet since its precipitation as carbides or nitrides during hot rolling
due to its high affinity to C and N decreases the amounts of dissolved C and dissolved
N in the base metal. Meanwhile, excessively containing Ti deteriorates the ridging
resistance since it suppresses formation of the austenite phase during the hot-rolled
sheet annealing. Thus, if Ti is to be contained, the Ti content is preferably 0.01
to 0.30%. More preferably, the Ti content is 0.02% or more. The Ti content is more
preferably 0.10% or less and yet more preferably 0.08% or less.
V: 0.01 to 0.10%
[0046] Vanadium (V) is an element that has an effect of improving formability of the cold-rolled
and annealed sheet since its precipitation as carbides or nitrides during hot rolling
due to its high affinity to C and N decreases the amounts of dissolved C and dissolved
N in the base metal. Meanwhile, excessively containing V deteriorates the ridging
resistance since it suppresses formation of the austenite phase during the hot-rolled
sheet annealing. Thus, if V is to be contained, the V content is preferably 0.01 to
0.10%. The V content is more preferably 0.02% or more and yet more preferably 0.03%
or more. The V content is more preferably 0.08% or less and yet more preferably 0.05%
or less.
Zr: 0.01 to 0.10%
[0047] Zirconium (Zr) is an element that has an effect of improving formability of the cold-rolled
and annealed sheet since its precipitation as carbides or nitrides during hot rolling
due to its high affinity to C and N decreases the amounts of dissolved C and dissolved
N in the base metal. Meanwhile, excessively containing Zr deteriorates the ridging
resistance since it suppresses formation of the austenite phase during the hot-rolled
sheet annealing. Thus, if Zr is to be contained, the Zr content is preferably 0.01
to 0.10%. The Zr content is more preferably 0.02% or more and yet more preferably
0.03% or more. The Zr content is more preferably 0.08% or less and yet more preferably
0.05% or less.
Nb: 0.01 to 0.30%
[0048] Niobium (Nb) is an element that has an effect of improving formability of the cold-rolled
and annealed sheet since its precipitation as carbides or nitrides during hot rolling
due to its high affinity to C and N decreases the amounts of dissolved C and dissolved
N in the base metal. Meanwhile, excessively containing Nb deteriorates the ridging
resistance since it suppresses formation of the austenite phase during the hot-rolled
sheet annealing. Thus, if Nb is to be contained, the Nb content is preferably 0.01
to 0.30%. More preferably, the Nb content is 0.02% or more. The Nb content is more
preferably 0.10% or less and yet more preferably 0.08% or less.
[0049] When one or two or more selected from Ti, V, Zr, and Nb is contained, the value of
formula (1) below is 0.0 or less.

In formula (1), respective element symbols represent contents (mass%) of respective
elements, or represent 0 when corresponding elements are not contained.
[0050] In embodying the present invention, when one or two or more selected from Ti, V,
Zr, and Nb is contained, the contents of the respective elements must satisfy the
aforementioned ranges and the value of formula (1) above must be 0.0 or less in order
to obtain excellent ridging resistance.
[0051] As mentioned above, Ti, V, Zr, and Nb have an effect of suppressing formation of
the austenite phase during the hot-rolled sheet annealing process. Meanwhile, even
when these elements are contained, by sufficiently increasing the contents of Mn and
Ni that promote formation of the austenite phase, a sufficient amount of austenite
phase can be formed in the steel during the hot-rolled sheet annealing process.
[0052] In other words, when one or two or more selected from Ti, V, Zr, and Nb is contained,
the steel composition is adjusted so that the value of formula (1) is 0.0 or less.
In this manner, it becomes possible to form a sufficient amount of austenite phase
in the hot-rolled sheet during the hot-rolled sheet annealing and thus a sufficient
amount of martensite phase can exist in the hot-rolled and annealed sheet. Thus, colonies
can be sufficiently destroyed in the cold-rolling process, and excellent ridging resistance
can be given to the cold-rolled and annealed sheet. However, when the value of formula
(1) exceeds 0.0, a sufficient amount of austenite phase is not formed in the hot-rolled
sheet during the hot-rolled sheet annealing, the hot-rolled and annealed sheet does
not include a sufficient amount of martensite phase, destruction of colonies becomes
insufficient during the cold rolling process, and the ridging resistance of the cold-rolled
and annealed sheet deteriorates.
B: 0.0003 to 0.0030%
[0053] Boron (B) is an element effective for preventing low-temperature secondary work embrittlement.
However, excessively containing B results in deterioration of hot workability. Thus,
if B is to be contained, the B content is preferably 0.0003 to 0.0030%. More preferably,
the B content is 0.0005% or more. More preferably, the B content is 0.0020% or less.
Mg: 0.0005 to 0.0100%
[0054] Magnesium (Mg) acts as a deoxidant by forming Mg oxides with Al in molten steel.
However, excessively containing Mg results in deterioration of toughness of the steel
and decreases the productivity. Thus, if Mg is to be contained, the Mg content is
preferably 0.0005 to 0.0100%. More preferably, the Mg content is 0.0010% or more.
The Mg content is more preferably 0.0050% or less and yet more preferably 0.0030%
or less.
Ca: 0.0003 to 0.0030%
[0055] Calcium (Ca) is an element that improves hot workability. However, excessively containing
Ca results in deterioration of toughness of the steel, decreases the productivity,
and, furthermore, deteriorates corrosion resistance due to precipitation of CaS. Thus,
if Ca is to be contained, the Ca content is preferably 0.0003 to 0.0030%. More preferably,
the Ca content is 0.0010% or more. More preferably, the Ca content is 0.0020% or less.
Y: 0.01 to 0.20%
[0056] Yttrium (Y) is an element that decreases the viscosity of the molten steel and improves
cleanliness. However, excessively containing Y results in saturated effects and deterioration
of the workability. Thus, if Y is to be contained, the Y content is preferably 0.01
to 0.20%. More preferably, the Y content is 0.10% or less.
Rare earth metal (REM): 0.001 to 0.100%
[0057] Rare earth metals (REM: elements of atomic numbers 57 to 71 such as La, Ce, and Nd)
are elements that improve high-temperature oxidation resistance. However, excessively
containing REM results in saturated effects, causes surface defects during hot-rolling,
and decreases productivity. Thus, if REM is to be contained, the REM content is preferably
0.001 to 0.100%. More preferably, the REM content is 0.005% or more. More preferably,
the REM content is 0.05% or less.
Sn: 0.001 to 0.500%
[0058] Tin (Sn) is effective for improving ridging resistance by promoting formation of
the deformation band during rolling. However, excessively containing Sn results in
saturated effects and deterioration of the formability. Thus, if Sn is to be contained,
the Sn content is preferably 0.001 to 0.500%. More preferably, the Sn content is 0.003%
or more. More preferably, the Sn content is 0.200% or less.
Sb: 0.001 to 0.500%
[0059] Antimony (Sb) is effective for improving ridging resistance by promoting formation
of the deformation band during rolling. However, excessively containing Sb results
in saturated effects and deterioration of the formability. Thus, if Sb is to be contained,
the Sb content is preferably 0.001 to 0.500%. More preferably, the Sb content is 0.003%
or more. More preferably, the Sb content is 0.200% or less.
Structure containing 10 to 90% of martensite phase in terms of area ratio with the
balance being ferrite phase
[0060] In the present invention, it is important that a particular amount of a martensite
phase be present in the structure. In the present invention, a particular amount of
an austenite phase is formed in the steel by performing hot-rolled sheet annealing.
Nearly all of the austenite phase turns into a martensite phase when cooled after
the hot-rolled sheet annealing. Due to the presence of the martensite phase, the colonies
are destroyed in the cool-rolling process, and the ridging resistance of the cold-rolled
and annealed sheet is improved.
[0061] This effect is obtained when the area ratio of the martensite phase after the hot-rolled
sheet annealing is 10% or more. Meanwhile, when the area ratio of the martensite phase
exceeds 90%, the hot-rolled and annealed sheet becomes hard, the rolling load in the
cold-rolling step increases, edge cracking and sheet shape defects occur, and the
productivity is decreased. Thus, the area ratio of the martensite phase is set to
10 to 90%. The area ratio of the martensite phase is preferably 15% or more and more
preferably 20% or more. The area fraction of the martensite phase is preferably 70%
or less and more preferably 50% or less.
[0062] The method for measuring the area ratio of the martensite phase in the present invention
is as follows. First, a test piece for structure observation is taken from near the
width center portion of a raw material for a cold-rolled steel sheet, and after a
section taken in the rolling direction is mirror-polished, the test piece is corroded
(etched) with a Murakami reagent (8 mass% KOH-8 mass% [K
3Fe(CN)
6] aqueous solution). By using an optical microscope, setting a portion of 1.0 mm depth
from the surface layer to the center of the view areas, ten view areas are photographed
at a magnification of 400. The obtained structure images are binarized by image analysis,
and then one of the values is deemed as the martensite phase and the other as the
ferrite phase to identify and separate the martensite phase and the ferrite phase.
Then the area ratio of the martensite phase is measured. The measurements results
of a total of ten view areas are averaged, and the calculated average is used as the
area fraction of the martensite phase.
[0063] Next, a preferable method for manufacturing a raw material for a cold-rolled stainless
steel sheet of the present invention is described. A steel having the above-described
chemical composition is melted by a known method that uses a converter, an electric
furnace, a vacuum melting furnace, or the like, and prepared into a steel (steel slab)
by a continuous casting method or an ingoting-slabbing method. After this slab is
heated to 1000°C or more and 1200°C or less, the heated slab is hot-rolled to a sheet
thickness of 2.0 to 6.0 mm under the condition that the finishing temperature is 700°C
or more and 1000°C or less.
[0064] Next, the hot-rolled sheet is subjected to hot-rolled sheet annealing that involves
holding the hot-rolled sheet in a temperature range of 900°C or more and 1100°C or
less, which is the ferrite-austenite two-phase region, for 5 seconds to 15 minutes.
The hot-rolled sheet annealing is an extremely important step for obtaining the structure
of the present invention.
[0065] At a hot-rolled sheet annealing temperature less than 900°C, annealing is performed
in the ferrite single phase region or a temperature region close thereto, and as a
result a sufficient amount of austenite phase is not formed in the hot-rolled sheet.
At a hot-rolled sheet annealing temperature exceeding 1100°C also, annealing is performed
in the ferrite single phase region or a temperature region close thereto, and as a
result a sufficient amount of austenite phase is not formed in the hot-rolled sheet.
In addition, when the holding time during hot-rolled sheet annealing is less than
5 seconds, a sufficient amount of austenite phase is not formed in the hot-rolled
sheet during the hot-rolled sheet annealing. In contrast, when the holding time in
the hot-rolled sheet annealing exceeds 15 minutes, the crystal grains coarsen during
the hot-rolled sheet annealing, which results in coarsening of crystal grains of a
cold-rolled and annealed sheet obtained by subsequent cold-rolling and annealing for
manufacturing the cold-rolled steel sheet. Such a structure causes surface roughening
known as orange peel, which is different from ridging, during forming.
[0066] Thus, in the present invention, hot-rolled sheet annealing that involves holding
a hot-rolled sheet in a temperature range of 900°C or more and 1100°C or less for
5 seconds to 15 minutes is performed to obtain a hot-rolled and annealed sheet. The
hot-rolled sheet annealing is preferably performed in a temperature range of 950°C
or more. The hot-rolled sheet annealing is preferably performed in a temperature range
of 1050°C or less. The hot-rolled sheet annealing preferably involves holding the
sheet in the aforementioned temperature range for 20 seconds or more.
[0067] The hot-rolled sheet annealing preferably involves holding the sheet in the aforementioned
temperature range for 1 minute or less.
[0068] The prepared hot-rolled and annealed sheet (raw material for a cold-rolled stainless
steel sheet) may be subsequently pickled.
[0069] An example of the method for manufacturing a ferritic stainless steel sheet from
a hot-rolled and annealed sheet (raw material for a cold-rolled stainless steel sheet)
is a method that involves cold-rolling the raw material for a cold-rolled stainless
steel sheet so as to prepare a cold-rolled sheet, and then annealing the cold-rolled
sheet to prepare a cold-rolled and annealed sheet. The cold-rolled and annealed sheet
can be further pickled in a pickling line to remove the scale. The cold-rolled, annealed,
and pickled sheet from which scale is removed may be subjected to skinpass rolling.
The cold rolling conditions are not particularly limited, and a common method may
be employed. For example, in cold-rolling, the total rolling reduction can be 40 to
90%. The cold-rolled sheet annealing is preferably a process of holding the cold-rolled
sheet in a temperature range of 780°C or more and 830°C or less for 5 seconds to 5
minutes. When the cold-rolled sheet annealing temperature is 780°C or more, less unrecrystallized
structure remains in the manufactured cold-rolled ferritic stainless steel sheet,
which can improves formability further. When the cold-rolled sheet annealing temperature
is 830°C or less, since existence of the martensite phase in the structure after annealing
can be suppressed by suppressing formation of the austenite phase in the steel during
annealing, formability can be further improved. Moreover, when the holding time in
cold-rolled sheet annealing is 5 seconds or more, since the martensite phase contained
in the cold-rolled sheet can be sufficiently decomposed during annealing and existence
of the martensite phase in the structure after annealing can be suppressed, formability
can be further improved. When the holding time in cold-rolled sheet annealing is 5
minutes or less, coarsening of the crystal grains during the cold-rolled sheet annealing
can be suppressed with result that it becomes easier to suppress surface roughening
known as orange peel, which is different from ridging, during forming of the manufactured
cold-rolled ferritic stainless steel sheet. Note that the cold-rolled sheet annealing
is preferably performed in a continuous annealing line.
EXAMPLE 1
[0070] Each of ferritic stainless steels having chemical compositions (the balance being
Fe and incidental impurities) indicated in Nos. 1-1 to 1-3 in Table 1 was prepared
into a 100 kg steel ingot, and then hot-rolled under heating at a temperature of 1050°C
so as to obtain a hot-rolled sheet having a thickness of 4.0 mm.
[0071] Each of the hot-rolled sheets was divided into five, and four of these were annealed
in air for 20 seconds at respective temperatures of 830 to 1200°C indicated in Table
1, and top and bottom surfaces were ground to remove scale to prepare a raw material
for a cold-rolled stainless steel sheet. Each of the raw materials for cold-rolled
steel sheets was halved by shearing at the longitudinal center portion, one half was
used for evaluation described below, and the other half was prepared into a cold-rolled,
annealed, and pickled sheet through the steps described below.
[0072] The remaining one of the divided pieces of each hot-rolled sheet was annealed in
an air atmosphere at 800°C for 8 hours, and top and bottom surfaces were ground to
remove scale to prepare a raw material for a cold-rolled stainless steel sheet. Each
of the raw materials for cold-rolled steel sheets was halved by shearing at the longitudinal
center portion, one half was used for evaluation described below, and the other half
was prepared into a cold-rolled, annealed, and pickled sheet through the processes
described below.
[0073] Each of the obtained raw materials for cold-rolled steel sheets was cold-rolled to
prepare a cold-rolled sheet having a thickness of 1.0 mm. The obtained cold-rolled
sheets were annealed in an air atmosphere at 800°C for 20 seconds to obtain cold-rolled
and annealed sheets. The cold-rolled and annealed sheets were pickled by a common
method so as to obtain cold-rolled, annealed, and pickled ferritic stainless steel
sheets.
[0074] The raw materials for cold-rolled stainless steel sheets and the cold-rolled, annealed,
and pickled ferritic stainless steel sheets obtained under the aforementioned manufacturing
conditions were subjected to the following evaluations.
[0075] First, a test piece for structure observation was taken from near the width center
portion of a raw material for a cold-rolled steel sheet, and after a section taken
in the rolling direction was mirror-polished, the test piece was corroded (etched)
with a Murakami reagent (8 mass% KOH-8 mass% [K
3Fe(CN)
6] aqueous solution). By using an optical microscope, setting a portion of 1.0 mm depth
from the surface layer to the center of the view areas, ten view areas were photographed
at a magnification of 400. The obtained structure images were binarized by image analysis
to identify and separate the martensite phase and the ferrite phase, and the area
ratio of the martensite phase was measured. The measurements results of a total of
ten view areas were averaged, and the calculated average was used as the area ratio
of the martensite phase.
<Corrosion resistance>
[0076] From each of the manufactured cold-rolled, annealed, and pickled sheets, a 80 mm
(length) × 60 mm (width) steel sheet was cut out by shearing, the surface thereof
was polished with an emery polishing paper to #600, and, after washing with water,
the steel sheet was ultrasonically degreased for 5 minutes in ethanol to obtain a
test piece. A corrosion test according to JASO M609-91 was performed on the obtained
test piece to evaluate corrosion resistance. After end portions and the rear surface
of a test piece were covered with a vinyl tape, the test piece was placed in a tester
with a slope of 60° and with the lengthwise direction being set in the vertical direction.
A three-cycle corrosion test was carried out, each cycle consisting of salt spraying
(5 mass% aqueous NaCl solution, 35°C) 2h → drying (60°C, relative humidity: 40%) 4h
→ wetting (50°C, relative humidity: 95% or more) 2h. After the test, the appearance
of the corroded surface was photographed, and a 30 mm × 30 mm region at the center
of the test piece in the photographed image was subjected to image analysis to calculate
the rust area ratio. Samples with a rust area ratio of 20% or less were evaluated
as "○" (pass, excellent), samples with a rust area ratio exceeding 20% but not exceeding
30% were evaluated as "□" (pass), and samples with a rust area ratio exceeding 30%
were evaluated as "▲" (fail).
<Formability>
[0077] From each of the cold-rolled, annealed, and pickled sheets manufactured as above,
a JIS No. 13B tensile test piece was taken in accordance with JIS Z 2241 such that
longitudinal directions thereof were, respectively, the rolling direction (L direction),
a direction 45 degrees with respect to the rolling direction (D direction), and a
direction 90 degrees with respect to the rolling direction (C direction), and a tensile
test was performed at room temperature according to the same standard to evaluate
the formability. Samples having a three-direction average ((L + 2D + C)/4 where L,
D, and C represent elongations after fracture (%) of respective directions) of total
elongation after fracture (%) of 32% or more were evaluated as "○" (pass, excellent),
samples with an average of less than 32% but not less than 28% were evaluated as "□"
(pass), and samples with an average of less than 28% were evaluated as "▲" (fail).
<Ridging resistance>
[0078] Furthermore, from each of the cold-rolled, annealed, and pickled sheets manufactured
as above, a JIS No. 5 test piece specified in JIS Z 2241 was taken so that the rolling
direction was the longitudinal direction of the test piece, and, after the surface
thereof was polished with a #600 emery paper, a tensile test was performed in accordance
with the same standard to apply a tensile strain of 23%. Subsequently, the surface
profile was measured with a laser displacement meter in a direction 90 degrees with
respect to the rolling direction on a polished surface at the center of the parallel
portion of the test piece. The measurement length was 16 mm per line, and the height
was measured with 0.05 mm increments. The obtained profile data was smoothed and subjected
to a waviness removal process by using a Hanning window function-type finite impulse
response (FIR) bandpass filter with a high-cut filter wavelength of 0.8 mm and a low-cut
filter wavelength of 8 mm. Subsequently, on the basis of the processed profile data
of each line, the data corresponding to 2 mm portions at both ends of each lines was
eliminated, and the arithmetic mean waviness, Wa, specified in JIS B 0601 (2001) was
measured for each line. Note that the line interval was set to 0.1 mm, and a total
of fifty lines were measured. The average of the values of the arithmetic mean waviness,
Wa, of fifty lines was used as the ridging height of the steel sheet surface, and
the ridging resistance was evaluated.
[0079] The case in which the ridging height was 2.0 µm or less was evaluated as "◇" (pass,
particularly excellent), the case in which the ridging height was more than 2.0 µm
but not more than 2.5 µm was evaluated as "○" (pass, excellent), the case in which
the ridging height was more than 2.5 µm but not more than 3.0 µm was evaluated as
"□" (pass), and the case in which the ridging height was more than 3.0 µm was evaluated
as "▲" (fail).
[0080] The obtained results are indicated in Table 1. The cold-rolled, annealed, and pickled
sheets prepared from the raw materials for cold-rolled steel sheets having a martensite
phase area ratio within the range of the present invention, in other words, the raw
materials for cold-rolled steel sheets of the invention examples, were evaluated as
"○" or "□" for corrosion resistance, "○" for formability, and "◇" or "○" for ridging
resistance, indicating excellent corrosion resistance as well as excellent formability
and ridging resistance.
[0081] The cold-rolled, annealed, and pickled sheets prepared from the raw materials for
cold-rolled steel sheets having a martensite phase area ratio outside the range of
the present invention, in other words, the raw materials for cold-rolled steel sheets
of the comparative examples, were evaluated as "▲" for ridging resistance. These cold-rolled,
annealed, and pickled sheets exhibited poor ridging resistance because the amount
of the martensite phase contained in the raw materials for cold-rolled steel sheets
were insufficient and the colonies were not satisfactorily destroyed by cold rolling.
[Table 1]
Test No. |
Chemical composition (mass%) |
Hot-rolled sheet annealing conditions |
Martensite area fraction (%) of raw material for cold-rolled steel sheet |
Evaluation results of cold-rolled, annealed, and pickled sheet |
Remarks |
C |
Si |
Mn |
P |
S |
Al |
Cr |
Ni |
N |
Other elements |
Temperature (°C) |
Time |
Corrosion resistance |
Formability |
Ridging resistance |
1-1 |
0.008 |
0.37 |
0.20 |
0.016 |
0.005 |
0.016 |
13.3 |
0.25 |
0.010 |
- |
800 |
8hr |
0 |
○ |
○ |
▲ |
Comparative Example |
850 |
20S |
7 |
○ |
○ |
▲ |
Comparative Example |
900 |
20S |
28 |
○ |
○ |
○ |
Invention Example |
1000 |
20S |
35 |
○ |
○ |
○ |
Invention Example |
1150 |
20S |
0 |
○ |
○ |
▲ |
Comparative Example |
1-2 |
0.015 |
0.15 |
0.23 |
0.019 |
0.003 |
0.042 |
12.4 |
0.82 |
0.005 |
- |
800 |
8hr |
0 |
○ |
○ |
▲ |
Comparative Example |
830 |
20S |
6 |
○ |
○ |
▲ |
Comparative Example |
900 |
20S |
87 |
○ |
○ |
◇ |
Invention Example |
1050 |
20S |
80 |
○ |
○ |
◇ |
Invention Example |
1200 |
20S |
8 |
○ |
○ |
▲ |
Comparative Example |
1-3 |
0.019 |
0.43 |
0.52 |
0.024 |
0.006 |
0.003 |
11.5 |
0.12 |
0.013 |
- |
800 |
8hr |
0 |
□ |
○ |
▲ |
Comparative Example |
840 |
20S |
9 |
□ |
○ |
▲ |
Comparative Example |
900 |
20S |
84 |
□ |
○ |
◇ |
Invention Example |
1100 |
20S |
70 |
□ |
○ |
◇ |
Invention Example |
1200 |
20S |
3 |
□ |
○ |
▲ |
Comparative Example |
* The balance other than the above-described chemical composition is Fe and incidental
impurities.
*[Hot-rolled sheet annealing time] In examples involving 800°C, annealing was performed
for 8 hours in a batch annealing furnace, and in examples not involving 800°C, annealing
was performed for 20 seconds in a continuous annealing furnace.
*[Corrosion resistance] After three corrosion test cycles, samples with a rust area
ratio of 20% or less were evaluated as "○" (pass, excellent), samples with a rust
area ratio exceeding 20% but not exceeding 30% were evaluated as "□" (pass), and samples
with a rust area ratio exceeding 30% were evaluated as "▲" (fail).
*[Formability] A tensile test was performed at room temperature, and samples having
a three-direction average of total elongation after fracture (%) of 32% or more were
evaluated as "○" (pass, excellent), samples with an average of less than 32% but not
less than 28% were evaluated as "□" (pass), and samples with an average of less than
28% were evaluated as "▲" (fail).
*[Ridging resistance] After 23% tensile strain was applied, the case in which the
ridging height on the surface of the center of the parallel portion of a test specimen
was 2.0 µm or less was evaluated as "◇" (pass, particularly excellent), the case in
which the ridging height was more than 2.0 µm but not more than 2.5 µm was evaluated
as "○" (pass, excellent), the case in which the ridging height was more than 2.5 µm
but not more than 3.0 µm was evaluated as "□" (pass), and the case in which the ridging
height was more than 3.0 µm was evaluated as "▲" (fail).
* Underlines indicate items outside the scope of the present invention. |
EXAMPLE 2
[0082] Raw materials for cold-rolled steel sheets and cold-rolled, annealed, and pickled
sheets having the chemical compositions indicated in Nos. 2-1 to 2-57 in Tables 2-1
and 2-2 were manufactured under the conditions indicated in Example 1. However, for
the hot-rolled sheet annealing conditions, annealing was performed in an air atmosphere
at 1000°C for 20 seconds. These raw materials for cold-rolled steel sheets and the
cold-rolled, annealed, and pickled sheets were subjected to the tests indicated in
Example 1, and the martensite phase area ratio in the structure of the raw material
for a cold-rolled steel sheet, corrosion resistance, formability, and ridging resistance
of the cold-rolled, annealed, and pickled sheet were evaluated.
[0083] The obtained results are indicated in Tables 2-1 and 2-2.
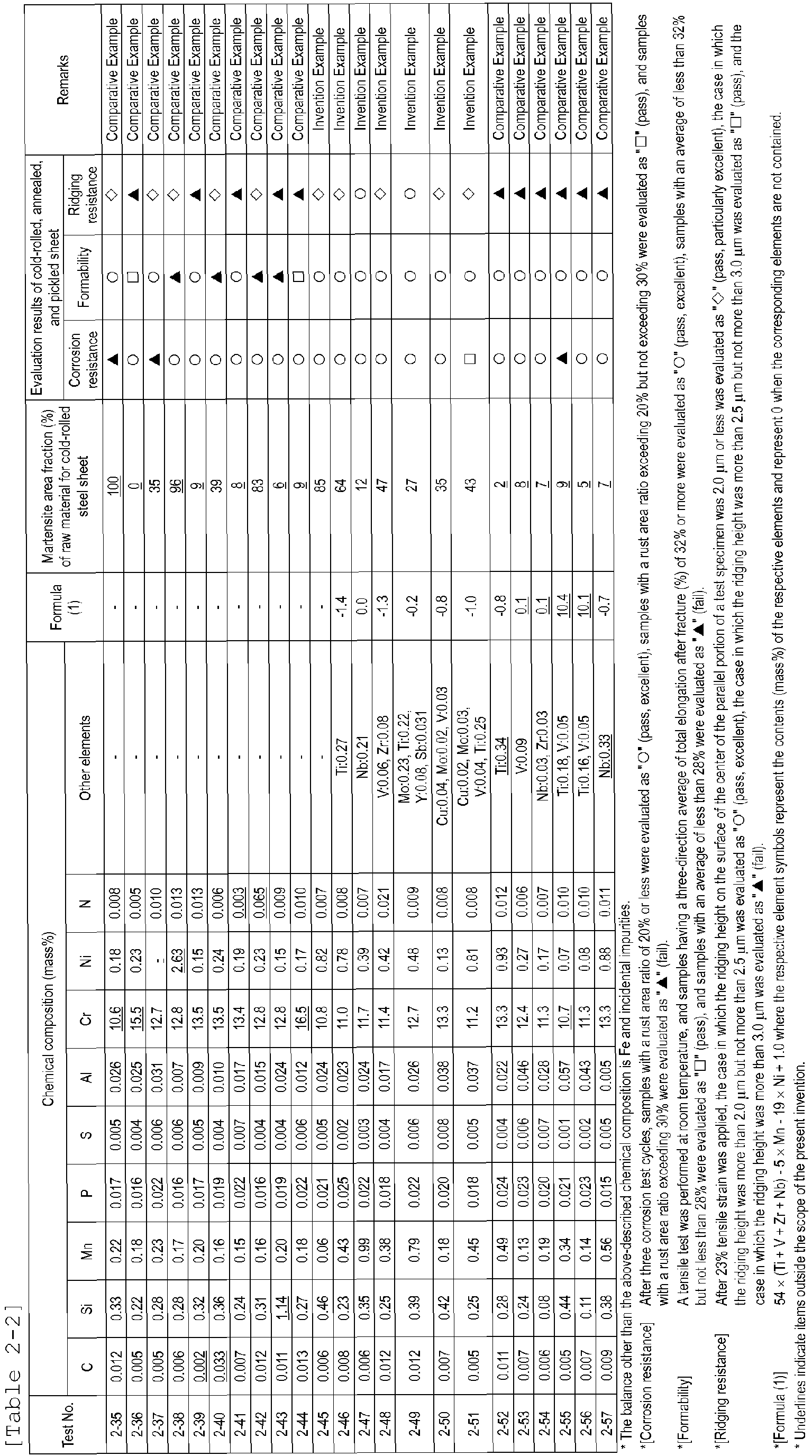
[0084] The cold-rolled, annealed, and pickled sheets prepared from the raw materials for
cold-rolled steel sheets of the invention examples were evaluated as "○" or "□" for
corrosion resistance, "○" or "□" for formability, and "◇", "○", or "□" for ridging
resistance, indicating excellent corrosion resistance as well as excellent formability
and ridging resistance.
[0085] Test No. 2-35 had poor corrosion resistance since it was prepared from a raw material
for a cold-rolled steel sheet of a comparative example in which the Cr content was
lower than the component range of the present invention.
[0086] Test No. 2-36 had poor ridging resistance since it was prepared from a raw material
for a cold-rolled steel sheet of a comparative example in which the Cr content was
higher than the component range of the present invention.
[0087] Test No. 2-37 had poor corrosion resistance since it was prepared from a raw material
for a cold-rolled steel sheet of a comparative example in which the Ni content was
lower than the component range of the present invention.
[0088] Test No. 2-38 had poor formability since it was prepared from a raw material for
a cold-rolled steel sheet of a comparative example in which the Ni content was higher
than the component range of the present invention.
[0089] Test Nos. 2-39 and 2-41 had poor ridging resistance since they were prepared from
raw materials for cold-rolled steel sheets of comparative examples in which the C
content and the N content, respectively, were lower than the component ranges of the
present invention.
[0090] Test Nos. 2-40 and 2-42 had poor formability since they were prepared from raw materials
for cold-rolled steel sheets of comparative examples in which the C content and the
N content, respectively, were higher than the component ranges of the present invention.
[0091] Test No. 2-43 had poor formability and ridging resistance since it was prepared from
a raw material for a cold-rolled steel sheet of a comparative example in which the
Si content was higher than the component range of the present invention.
[0092] Test No. 2-44 had poor ridging resistance since it was prepared from a raw material
for a cold-rolled steel sheet of a comparative example in which the Cr content was
higher than the component range of the present invention.
[0093] Test No. 2-52 had poor ridging resistance since it was prepared from a raw material
for a cold-rolled steel sheet of a comparative example in which the Ti content was
higher than the component range of the present invention.
[0094] Test Nos. 2-53, 2-54, and 2-56 had poor ridging resistance since they were prepared
from raw materials for cold-rolled steel sheets of comparative examples in which the
value of formula (1) exceeded 0.0.
[0095] Test No. 2-55 had poor corrosion resistance and ridging resistance since it was prepared
from a raw material for a cold-rolled steel sheet of a comparative example in which
the Cr content was lower than the component range of the present invention and the
value of formula (1) exceeded 0.0.
[0096] Test No. 2-57 had poor ridging resistance since it was prepared from a raw material
for a cold-rolled steel sheet of a comparative example in which the Nb content was
higher than the component range of the present invention.
Industrial Applicability
[0097] A raw material for a cold-rolled stainless steel sheet of the present invention is
preferable for manufacturing a cold-rolled ferritic stainless steel sheet having excellent
corrosion resistance, formability, and ridging resistance. Since a cold-rolled ferritic
stainless steel sheet manufactured from a raw material for a cold-rolled stainless
steel sheet of the present invention has excellent corrosion resistance, formability,
and ridging resistance, it can be used in home cooking tolls, parts of home electric
appliances, parts of office and stationery supplies, parts of automobile interiors,
pipes for automobile exhaust, building materials, and the like.