[0001] The disclosure relates to an austenitic steel alloy, and more particularly to an
austenitic steel alloy for hot work tools. The disclosure also relates to a method
for making an austenitic steel using the alloy, and an austenitic steel made by the
method.
[0002] Martensitic steel is a steel material commonly used for making hot work tools due
to its superior mechanical properties such as hardness and toughness. However, since
the martensitic steel has a relatively low ductility, the hot work tools made therefrom
are liable to cracking.
[0003] AISI H13 steel is an example of the martensitic steel commonly used for making the
hot work tools, and includes carbon in an amount of from 0.32 wt% to 0.45 wt%, silicon
in an amount of from 0.80 wt% to 1.20 wt%, manganese in an amount of from 0.20 wt%
to 0.50 wt%, chromium in an amount of from 4.75 wt% to 5.50 wt%, molybdenum in an
amount of from 1.10 wt% to 1.75 wt%, vanadium in an amount of from 0.80 wt% to 1.20
wt%, phosphorus in an amount of not more than 0.03 wt%, sulfur in an amount of not
more than 0.03 wt%, and a balance of iron. The AISI H13 steel has a room temperature
hardness of from 55 to 58, an elongation at room temperature of from 3% to 5%, an
impact toughness of from 5 Joules (J) to 10 J, and a high temperature Rockwell C hardness
(HRc) of from 33 to 41. Since the AISI H13 steel having a relatively low elongation
is liable to cracking during usage, the room temperature hardness thereof is usually
reduced to a range of from 42 to 50 so as to increase the elongation to a range of
from 5% to 8%.
[0004] QRO 90 steel is another example of the martensitic steel commonly used for making
the hot work tools, and includes carbon in an amount of 0.38 wt%, silicon in an amount
of 0.30 wt%, manganese in an amount of 0.75 wt%, chromium in an amount of 2.60 wt%,
molybdenum in an amount of 2.25 wt%, vanadium in an amount of 0.9 wt%, and a balance
of iron. The QRO 90 steel has a room temperature hardness of 45, an elongation of
about 11 %, an impact toughness of 10 J, and a high temperature Rockwell C hardness
(HRc) of from 26 to 41.
[0005] Alternatively, austenitic Fe-Mn-Al-C steel has been subjected to extensive researches
over the last several decades because of its promising application that is potential
associated with high mechanical strength and high ductility.
[0006] Conventional austenitic Fe-Mn-Al-C steel containing carbon in an amount of greater
than about 1.2 wt% may be deteriorated in terms of ductility and may be even cracked.
Therefore, the amount of carbon in the conventional austenitic Fe-Mn-Al-C steel is
usually controlled within a range of from 0.54 wt% to 1.3 wt% and is added with molybdenum
(Mo), niobium (Nb), and/or tungsten (W) to enhance the mechanical strength thereof.
However, ductility (i.e., elongation) of the conventional austenitic Fe-Mn-Al-C steel
may be undesirably reduced due to precipitation of coarse carbides on the grain boundaries
of the austenitic Fe-Mn-Al-C steel during an aging treatment. Accordingly, the hot
work tools made therefrom are liable to cracking.
[0007] Applicant's
U.S. Patent No. 9,528,177 discloses a Fe-Mn-Al-C quarternary alloy which is essentially consisting of Fe, Mn,
Al, and C in specific amounts. Specifically, the amount of carbon in the Fe-Mn-Al-C
quarternary alloy is controlled within a range of from 1.4 wt% to 2.2 wt%. The Fe-Mn-Al-C
quarternary alloy possesses superior ductility and high mechanical strength due to
formation of a high density of fine
K' carbides within an austenite matrix by a spinodal decomposition phase transition
mechanism during quenching from a solution heat treatment temperature. It is not recommended
to add strong carbide-forming elements such as Cr, Ti, and Mo to the Fe-Mn-Al-C quarternary
alloy because addition of such elements appears to have no beneficial effect in the
formation of the high density of fine
K' carbides within the austenite matrix.
[0008] A first object of the disclosure is to provide an austenitic steel alloy which possesses
superior mechanical properties without compromising ductility at room temperature,
and which also possesses superior mechanical properties at high temperature.
[0009] A second object of the disclosure is to provide a method for making an austenitic
steel using the austenitic steel alloy.
[0010] A third object of the disclosure is to provide an austenitic steel made by the method.
[0011] According to a first aspect of the disclosure, there is provided an austenitic steel
alloy which comprises manganese in an amount of from 25 wt% to 31 wt%, aluminum in
an amount of from 7 wt% to 10 wt%, carbon in an amount of from 1.2 wt% to 1.6 wt%,
molybdenum in an amount of more than 0 wt% and less than 6 wt%, and a balance of iron.
[0012] According to a second aspect of the disclosure, there is provided a method for making
an austenitic steel using the austenitic steel alloy of the first aspect of the disclosure.
[0013] According to a third aspect of the disclosure, there is provided an austenitic steel
made by the method of the second aspect of the disclosure.
[0014] The austenitic steel alloy according to the disclosure possesses superior mechanical
properties both at room temperature and at high temperature (e.g., at about 500°C)
which are achieved by adding molybdenum in an amount of less than 6 wt% into the austenitic
steel alloy including manganese, aluminum, carbon, and iron in specific amounts.
[0015] Other features and advantages of the disclosure will become apparent in the following
detailed description of the embodiment (s) with reference to the accompanying drawings,
of which:
Figure 1 is a flow diagram of an embodiment of a process for making an austenitic
steel according to the disclosure;
Figure 2 is an optical microscope photograph of an austenitic steel of Example 1 after
a hot-working treatment;
Figure 3 is an optical microscope photograph of an austenitic steel of Example 3 after
a hot-working treatment;
Figure 4 is an optical microscope photograph of an austenitic steel of Example 8 after
a hot-working treatment;
Figure 5 is an optical microscope photograph of an austenitic steel of Example 1 after
an aging treatment;
Figure 6 is an optical microscope photograph of an austenitic steel of Example 3 after
an aging treatment;
Figure 7 is an optical microscope photograph of an austenitic steel of Example 8 after
an aging treatment;
Figure 8 is an optical microscope photograph of an austenitic steel of Comparative
Example 1 after a hot-working treatment; and
Figure 9 is an optical microscope photograph of an austenitic steel of Comparative
Example 2 after a hot-working treatment.
[0016] An austenitic steel alloy according to the disclosure comprises manganese (Mn) in
an amount of from 25 wt% to 31 wt%, aluminum (Al) in an amount of from 7 wt% to 10
wt%, carbon (C) in an amount of from 1.2 wt% to 1.6 wt%, molybdenum (Mo) in an amount
of more than 0 wt% and less than 6 wt%, and a balance of iron (Fe). The austenitic
steel alloy according to the disclosure possesses superior mechanical properties and
high ductility, and can be used for making general steel plates such as automobile
steel plates, mechanical parts such as gears, hard work tools, and the like.
[0017] Mn is a strong austenite-stabilizing element. An austenite phase is of face-center-cubic
(FCC) structure with more dislocation slip systems, and thus possesses better ductility
than other crystal structures, such as body-center-cubic (BCC) and hexagonal close
packed (HCP) structures. Therefore, in order to obtain a fully austenite structure
at room temperature, Mn is in an amount of from 25 wt% to 31 wt% in the austenitic
steel alloy according to the disclosure. In certain embodiments, Mn is in an amount
of from 26 wt% to 30 wt% . In certain embodiments, Mn is in an amount of from 27 wt%
to 29 wt%.
[0018] Al not only is a strong ferrite-stabilizing element, but also is one of the primary
elements for forming (Fe,Mn)
3AlC
x carbides (i.e.,

carbides). Al is in an amount of from 7 wt% to 10 wt% in the austenitic steel alloy
according to the disclosure. In certain embodiments, Al is in an amount of from 8
wt% to 10 wt%. In certain embodiments, Al is in an amount of from 8 wt% to 9 wt%.
[0019] C is in an amount of from 1.2 wt% to 1.6 wt% in the austenitic steel alloy according
to the disclosure, which is relatively high as compared to the amount (i.e., up to
1.0 wt%) of C in the conventional austenitic Fe-Mn-Al-C steel, in which molybdenum
(Mo), niobium (Nb), and/or tungsten (W) is added. In certain embodiments, C is in
an amount of from 1.4 wt% to 1.6 wt%.
[0020] Mo is a very strong carbide-forming element. Mo is in an amount of more than 0 wt%
and less than 6 wt% in the austenitic steel alloy according to the disclosure. In
certain embodiments, Mo is in an amount of from 2 wt% to 6 wt%.
[0021] In certain embodiments, the austenitic steel alloy according to the disclosure further
comprises chromium (Cr). Cr is also a very strong carbide-forming element. Cr is in
an amount of less than 6 wt% in the austenitic steel alloy according to the disclosure.
[0022] In certain embodiments, the austenitic steel alloy according to the disclosure further
comprises cobalt (Co). Co is also a very strong carbide-forming element. Co is in
an amount of less than 5 wt% in the austenitic steel alloy according to the disclosure.
[0023] It should be noted that the amounts of low-melting elements (e.g., Mn and Al) in
the austenitic steel alloy according to the disclosure may be slightly different from
those of the low-melting elements in the austenitic steel made from the alloy due
to the smelting that causes evaporation effect of the low-melting elements. However,
the difference is within an acceptable tolerance. Therefore, the properties of the
austenitic steel made from the alloy will not be affected.
[0024] According to Figure 1, an embodiment of a method for making an austenitic steel according
to the disclosure comprises steps of:
- a) smelting the austenitic steel alloy according to the disclosure in a high-frequency
smelting furnace under an atmosphere to obtain a molten steel alloy;
- b) casting the molten steel alloy to obtain a cast piece;
- c) subjecting the cast piece to a hot-working treatment such as hot-rolling, hot-forging,
and the like at a temperature of from 1100°C to 950°C to obtain a hot-worked body
having a predetermined shape;
- d) subjecting the hot-worked body to an initial water-quenching treatment followed
by cooling to room temperature to obtain a water-quenched body;
- e) subjecting the water-quenched body to an aging treatment at a temperature of from
480°C to 600°C to obtain an aged body; and
- f) subjecting the aged body to a further water-quenching treatment followed by cooling
to room temperature.
[0025] In certain embodiments, in step c), the hot-worked body has a thickness of less than
25% of that of the cast piece.
[0026] In certain embodiments, the temperature for the aging treatment in step e) is from
480°C to 500°C, and the aging treatment is implemented for a period of from 5 hours
to 12 hours.
[0027] In certain embodiments, the temperature for the aging treatment in step e) is larger
than 500 °C and up to 600°C, and the aging treatment is implemented for a period of
from 1 hour to 4 hours.
[0028] The method for making the austenitic steel according to the disclosure is different
from the method for making the conventional austenitic Fe-Mn-Al-C steel having a relatively
low carbon amount and containing strong carbide-forming elements. Specifically, in
the method for making the conventional austenitic Fe-Mn-Al-C steel, a solution heat
treatment is required after the hot-working treatment to dissolve the coarse carbides
precipitated on the grain boundaries into a matrix phase so as to enhance the ductility
of the conventional austenitic Fe-Mn-Al-C steel. In the method for making the austenitic
steel according to the disclosure, although the austenitic steel alloy for making
the austenitic steel has a relatively high carbon amount and contains strong carbide-forming
elements, the temperature for implementing the hot-working treatment is controlled
within a range of from 1100°C to 950°C such that the precipitation of the coarse carbides
on the grain boundaries during the hot-working treatment can be avoided. Therefore,
an austenitic steel having superior mechanical properties and high ductility can be
made without the solution heat treatment, which is required in the method for making
the conventional austenitic Fe-Mn-Al-C steel.
[0029] It should be noted that instead of implementing the further water-quenching treatment
in step f), the aged body can be cooled down naturally to room temperature. In addition,
although the solution heat treatment is not a requisite in the method for making the
austenitic steel according to the disclosure, it may be optionally implemented, if
desired.
[0030] The austenitic steel made by the method according to the disclosure has a fully austenitic
phase, a yield strength at 25°C of from 1200 MPa to 1400 MPa, a Rockwell C hardness
(HRc) at 25°C of from 45 to 55, an ultimate tensile strength at 25°C of from 1200
MPa to 1500 MPa, and an elongation at 25°C of from 20% to 40%. In addition, the austenitic
steel made by the method according to the disclosure has superior yield strength and
ultimate tensile strength at high temperature up to 700°C. Therefore, the austenitic
steel made by the method according to the disclosure can be used for making general
steel plates such as automobile steel plates, mechanical parts such as gears, hard
work tools, and the like.
[0031] In certain embodiments, the austenitic steel alloy according to the disclosure comprises
carbon in an amount of from 1.42 wt% to 1.5 wt% and molybdenum in an amount of from
3.5 wt% to 5 wt%. The austenitic steel made by the austenitic steel alloy according
to the disclosure has an ultimate tensile strength at 25°C of from 1353 MPa to 1386
MPa, a yield strength at 25°C of from 1310 MPa and 1340 MPa, and a HRc at 25°C of
from 47 to 47.7.
[0032] In certain embodiments, the austenitic steel alloy according to the disclosure comprises
carbon in an amount of from 1.42 wt% to 1.45 wt% and molybdenum in an amount of from
3.5 wt% to 4 wt%. The austenitic steel made by the austenitic steel alloy according
to the disclosure has an elongation at 25°C of 25%.
[0033] In certain embodiments, the austenitic steel alloy according to the disclosure comprises
manganese in an amount of from 27.7 wt% to 30 wt% and aluminum in an amount of from
8.2 wt% to 8.5 wt%. The austenitic steel made by the austenitic steel alloy according
to the disclosure has an ultimate tensile strength at 25°C of from 1280 MPa to 1386
MPa, a yield strength at 25°C of from 1250 MPa and 1350 MPa, a hardness (HRc) at 25°C
of from 46.7 to 47.7, and an elongation at 25°C of from 20% to 32%.
[0034] In certain embodiments, the austenitic steel alloy according to the disclosure comprises
manganese in an amount of from 27 wt% to 29 wt%, aluminum in an amount of from 8.0
wt% to 8.5 wt%, and molybdenum in an amount of from 3.0 wt% to 6 wt%. The austenitic
steel made by the austenitic steel alloy according to the disclosure has an elongation
at 25°C of more than 20%, an ultimate tensile strength at 25°C of more than 1280 MPa,
a yield strength at 25°C of more than 1230 MPa, an ultimate tensile strength at 300
°C of more than 1000 MPa, and a yield strength at 300 °C of more than 1000 MPa.
[0035] In certain embodiments, the austenitic steel alloy according to the disclosure comprises
molybdenum in an amount of 3.0 wt%, and further comprises chromium in an amount of
3 wt% or cobalt in an amount of 2 wt%. The austenitic steel made by the austenitic
steel alloy according to the disclosure has an ultimate tensile strength at 25°C of
from 1280 MPa to 1344 MPa, a yield strength at 25°C of from 1230 MPa and 1300 MPa,
a hardness (HRc) at 25°C of from 45 to 46.8, and an elongation at 25°C of from 24%
to 37%.
[0036] Furthermore, the presently available steel for the hot work tools has a density of
from 7.8 g/cm
3 to 7.9 g/cm
3. The austenitic steel made by the method according to the disclosure has a density
of from 6.6 g/cm
3 to 6.8 g/cm
3, which is 14% less than the density of the presently available steel. Therefore,
in addition to superior mechanical properties and high ductility, the austenitic steel
made by the method according to the disclosure has a lightweight advantage.
[0037] The conventional Fe-Mn-Al-C alloy having a relatively high amount of carbon of from
1.4 wt% to 2.2 wt% can possess a fully austenitic phase, form a high density of fine

carbides (i.e., (Fe,Mn)
3AlC
x carbides) within an austenite matrix, and avoid the precipitation of coarse carbides
on the grain boundaries so as to possess superior mechanical strength and high ductility
by controlling the hot-working treatment, the solution heat treatment, and the water-quenching
treatment. However, in the method for making an austenitic steel according to the
disclosure, by adding specific amounts of the strong carbide-forming elements (i.e.,
Mo and optionally Cr and Co) in the austenitic steel alloy and by controlling the
temperature for implementing the hot-working treatment within a specific range (i.e.,
from 1100°C to 950°C), the precipitation of coarse carbides on the grain boundaries
during the hot-working treatment can be avoided. Therefore, an austenitic steel having
superior mechanical properties and high ductility can be made without the solution
heat treatment which is required in the method for making the conventional austenitic
Fe-Mn-Al-C steel.
[0038] Examples of the disclosure will be described hereinafter. It is to be understood
that these examples are exemplary and explanatory and should not be cons trued as
a limitation to the disclosure.
Example 1:
[0039] A steel alloy containing 30 wt% of Mn, 85 wt% of Al, 1.45 wt% of C, 6 wt% of Mo,
and a balance of Fe was smelted in a high-frequency smelting furnace under an atmosphere
to obtain a molten steel alloy, followed by casting the molten steel alloy to obtain
a cast piece having a thickness of 2 cm.
[0040] The cast piece was heated in a furnace at 1100°C, followed by hot-rolling at a temperature
of from 1100°C to 950°C to obtain a test piece having a thickness of less than 25%
of that of the cast piece.
[0041] The test piece was subjected to an initial water-quenching treatment followed by
cooling to room temperature to obtain a water-quenched body.
[0042] The water-quenched body was polished to remove an oxide layer, followed by an aging
treatment at 500°C to obtain an aged body.
[0043] The aged body was subjected to a further water-quenching treatment followed by cooling
to room temperature.
Examples 2 to 11:
[0044] In each of Examples 2 to 11, the procedure of Example 1 was repeated using the steel
alloy shown in Table 1.
Comparative Examples 1 to 3:
[0045] In each of Comparative Examples 1 to 3, the procedure of Example 1 was repeated using
the steel alloy shown in Table 1.
Table 1:
Steel Alloy |
Fe (wt%) |
Mn (wt%) |
Al (wt%) |
C (wt%) |
Mo (wt%) |
Cr (wt%) |
Co (wt%) |
Ex. 1 |
balance |
30 |
8.5 |
1.45 |
6 |
- |
- |
Ex. 2 |
balance |
30 |
8.5 |
1.45 |
4 |
- |
- |
Ex. 3 |
balance |
30 |
8.5 |
1.50 |
3.5 |
- |
- |
Ex. 4 |
balance |
27 |
8.5 |
1.48 |
6 |
- |
- |
Ex. 5 |
balance |
27.5 |
8.3 |
1.43 |
5 |
- |
- |
Ex. 6 |
balance |
28 |
8.2 |
1.42 |
3.5 |
- |
- |
Ex. 7 |
balance |
28.5 |
8.4 |
1.46 |
2 |
- |
- |
Ex. 8 |
balance |
30 |
8.5 |
1.45 |
3 |
3 |
- |
Ex. 9 |
balance |
28.5 |
8.0 |
1.52 |
3 |
3 |
- |
Ex. 10 |
balance |
30 |
8.5 |
1.45 |
3 |
- |
2 |
Ex. 11 |
balance |
27 |
8.2 |
1.42 |
3 |
- |
2 |
Comp. Ex. 1 |
balance |
28.5 |
8.2 |
1.45 |
9 |
- |
- |
Comp. Ex. 2 |
balance |
28 |
8.3 |
1.53 |
9 |
5 |
- |
Comp. Ex. 3 |
balance |
28.5 |
8.3 |
1.5 |
- |
- |
- |
[0046] Each of the test pieces of Examples 1 to 11 and Comparative Examples 1 to 3 was subjected
to yield strength (YS), ultimate tensile strength (UTS), elongation (El), and Rockwell
C hardness (HRc) measurements at 25°C according to the procedures described below.
The results are shown in Table 2.
[0047] Each of the test pieces of Examples 4, 7, and 9 and Comparative Examples 1 to 3 was
subjected to yield strength (YS) and ultimate tensile strength (UTS) measurements
at 300°C, 500°C, and 700°C according to the procedures described below. The results
are shown in Table 3.
Measurements:
[0048] Each of the test pieces was subjected a tensile test according to the specification
of ASTM E8/E8M using an Instron tensile tester at a strain rate of 10
-3/sec at a desirable temperature (i.e., 25°C, 300°C, 500°C, or 700°C). For each of
the test pieces, a relationship between stress and strain was recorded to obtain a
stress-strain curve at the desirable temperature as that shown below.
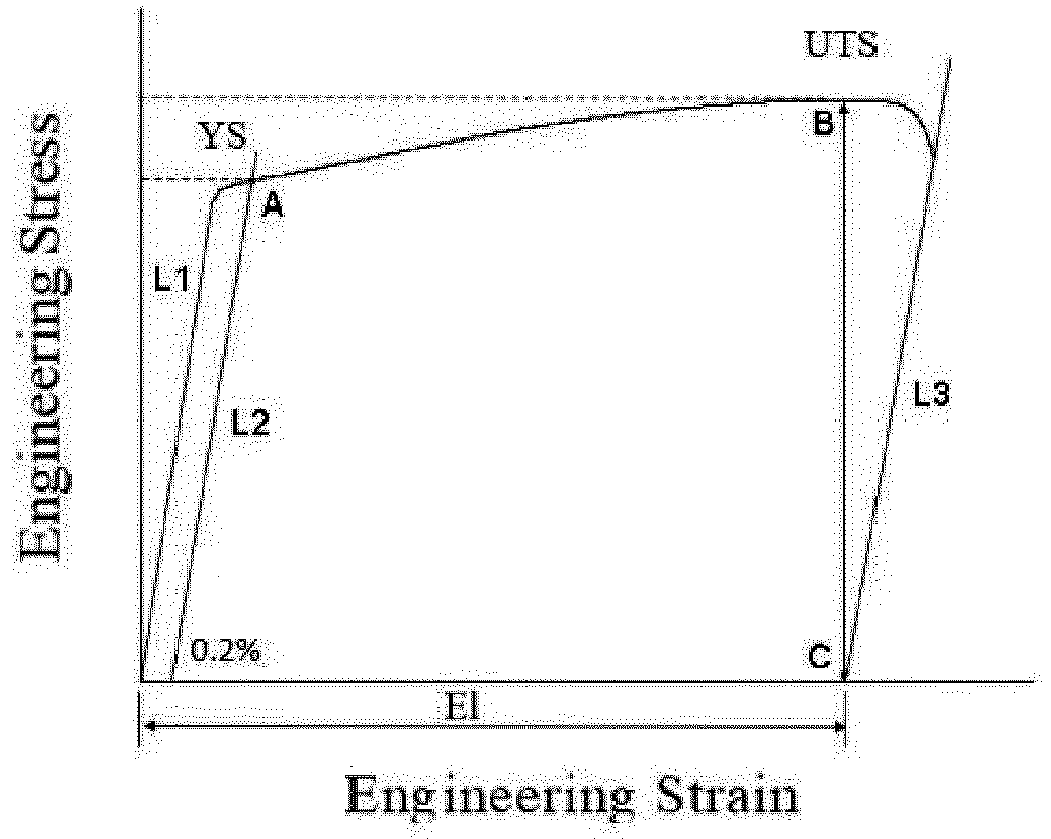
[0049] L2 and L3 are parallel to L1.
1. Yield Strength (YS):
Yield strength is defined as the stress obtained at 0.2% offset strain in the stress-strain
curve, as shown by point A in the stress-strain curve.
2. Ultimate Tensile Strength (UTS):
Ultimate tensile strength is defined as a maximum stress obtained before failure,
as shown by point B in the stress-strain curve.
3. Elongation (El):
Elongation is defined as the strain shown by point C in the stress-strain curve.
4. Rockwell C Hardness (HRc)
Rockwell C hardness of each of the test pieces was measured using a Rockwell hardness
machine at a load of 150 kgf . A diamond conical indenter was used for the measurement.
The results are shown in Table 2.
Table 2
Steel Alloy |
YS (MPa) |
UTS (MPa) |
El (%) |
Rockwell C hardness (HRc) |
Aging time (500°C/h) |
Ex. 1 |
1350 |
1375 |
20 |
47.4 |
12 |
Ex. 2 |
1340 |
1366 |
25 |
47.0 |
12 |
Ex. 3 |
1330 |
1386 |
22 |
47.7 |
6 |
Ex. 4 |
1230 |
1308 |
21 |
46.3 |
12 |
Ex. 5 |
1320 |
1365 |
20 |
47.4 |
12 |
Ex. 6 |
1310 |
1353 |
24 |
47.0 |
6 |
Ex. 7 |
1250 |
1314 |
20 |
46.5 |
12 |
Ex. 8 |
1300 |
1322 |
26 |
45.0 |
12 |
Ex. 9 |
1300 |
1344 |
24 |
46.8 |
12 |
Ex. 10 |
1250 |
1280 |
32 |
46.7 |
5 |
Ex. 11 |
1230 |
1280 |
37 |
46.7 |
5 |
Comp. Ex. 1 |
1400 |
1464 |
7 |
50.2 |
6 |
Comp. Ex. 2 |
1360 |
1410 |
5 |
49.0 |
5 |
Comp. Ex. 3 |
1210 |
1262 |
38 |
45.6 |
2.5 |
Table 3:
Steel Alloy |
300°C |
500°C |
700°C |
YS |
UTS |
YS |
UTS |
YS |
UTS |
Ex. 4 |
1000 |
1033 |
690 |
758 |
410 |
440 |
Ex. 7 |
970 |
1022 |
650 |
719 |
410 |
449 |
Ex. 9 |
1030 |
1070 |
700 |
786 |
420 |
444 |
Comp. Ex. 1 |
1020 |
1047 |
750 |
827 |
420 |
442 |
Comp. Ex. 2 |
1010 |
1068 |
680 |
749 |
400 |
427 |
Comp. Ex. 3 |
850 |
938 |
600 |
670 |
530 |
559 |
[0050] As shown in Table 2, the test pieces of Examples 1 to 11 have a yield strength at
25°C of from 1230 MPa to 1350 MPa, an ultimate tensile strength at 25°C of from 1280
MPa to 1386 MPa, an elongation at 25° of from 20% to 37%, and a Rockwell C hardness
(HRc) of from 45.0 to 47.7. It is demonstrated that the test pieces of Examples 1
to 11 have superior mechanical strength and ductility as compared to the test pieces
of Comparative Examples 1 and 2. Specifically, the austenitic steel alloy of Examples
1 to 11 has superior mechanical strength and ductility at room temperature (i.e.,
25°C) and sufficient mechanical strength at high temperature as well, by controlling
the Mo amount in the steel alloy within a range of from 2 wt% to 6 wt% as compared
to the steel alloy of Comparative Examples 1 to 3 and conventional AISI H13 and QRO
90 alloys. Therefore, when the austenitic steel alloy according to the disclosure
is used to make hot work tools, the cracking problem encountered in the prior art
can be avoided.
[0051] In addition, as shown in Table 2, the mechanical strength of each of the test pieces
of Examples 1 to 11 is not significantly affected by the aging time of from 5 hours
to 12 hours. It is demonstrated that the precipitation of coarse carbides on the grain
boundaries of the austenitic steel can be avoided by controlling the temperature during
the hot-working treatment. Therefore, the time period for the aging treatment of the
austenitic steel alloy according to the disclosure can be more flexible, and the problem
of significant precipitation of coarse carbides due to the longer aging time can be
alleviated or even avoided.
[0052] Referring to Figures 2 to 4, there is no precipitation of coarse carbides seen in
each of the test pieces of Examples 1, 3, and 8 after the hot-working treatment at
a temperature of from 1100°C to 950°C. Referring to Figures 5 to 7, there is also
no precipitation of coarse carbides seen in each of the test pieces of Examples 1,
3, and 8 after the hot-working treatment at a temperature of from 1100°C to 950°C,
followed by the aging treatment. Referring to Figures 8 and 9, however, there is significant
precipitation of coarse carbides seen in each of the test pieces of Comparative Examples
1 and 2, in which the strong carbide-forming elements are added in an excess amount.
[0053] Furthermore, as shown in Table 3, the test pieces of Examples 4, 7, and 9 has a yield
strength at 300°C of from 970 MPa to 1030 MPa, an ultimate tensile strength at 300°C
of from 1022 MPa to 1070 MPa, a yield strength at 500°C of from 650 MPa to 700 MPa,
an ultimate tensile strength at 500°C of from 719 MPa to 786 MPa, a yield strength
at 700°C of from 410 MPa to 420 MPa, and an ultimate tensile strength at 700°C of
from 440 MPa to 449 MPa. Although the test piece of Comparative Example 3 has good
ductility at 25°C, the yield strengths and the ultimate tensile strengths at 25°C,
300°C, and 500°C are relatively low as compared to the test pieces of Examples 4,
7, and 9. It is demonstrated that the austenitic steel made by the austenitic steel
alloy according to the disclosure has superior mechanical strength both at room temperature
(i.e., 25°C) and at high temperature, and thus can be used for making a hot work tools.
[0054] In view of the aforesaid, in a conventional austenitic Fe-Mn-Al-C steel containing
carbon in an amount of not more than 1 wt%, the ductility of the austenitic steel
made thereby can be improved by adding relatively low amount (s) of the strong carbide-forming
element (s) such as molybdenum and/or tungsten. However, the mechanical strength of
the austenitic steel cannot be significantly enhanced. On the other hand, in such
austenitic Fe-Mn-Al-C steel, the mechanical strength thereof can be improved by adding
relatively high amount(s) of the strong carbide-forming element(s). However, the ductility
thereof cannot be maintained. In
U. S. Patent No. 9,528, 177, it is not recommended to add the strong carbide-forming elements such as Cr, Ti,
and Mo to the Fe-Mn-Al-C quarternary alloy because addition of the strong carbide-forming
elements appears to have no beneficial effect for forming the high density of fine

carbides within the austenite matrix. In the austenitic steel alloy according to
the disclosure, molybdenum in a specific amount of less than 6 wt% and carbon in a
relatively high amount of from 1.2 wt% to 1.6 wt% are included therein. Therefore,
an austenitic steel possessing superior mechanical strength and high ductility both
at room temperature and at high temperature can be made using the austenitic steel
alloy via a method of this disclosure that includes a hot-working treatment at a temperature
of from 1100°C to 950°C.
[0055] In the description above, for the purposes of explanation, numerous specific details
have been set forth in order to provide a thorough understanding of the embodiment(s).
It will be apparent, however, to one skilled in the art, that one or more other embodiments
may be practiced without some of these specific details. It should also be appreciated
that reference throughout this specification to "one embodiment," "an embodiment,"
an embodiment with an indication of an ordinal number and so forth means that a particular
feature, structure, or characteristic may be included in the practice of the disclosure.
It should be further appreciated that in the description, various features are sometimes
grouped together in a single embodiment, figure, or description thereof for the purpose
of streamlining the disclosure and aiding in the understanding of various inventive
aspects, and that one or more features or specific details from one embodiment may
be practiced together with one or more features or specific details from another embodiment,
where appropriate, in the practice of the disclosure.
1. An austenitic steel alloy
characterized by:
manganese in an amount of from 25 wt% to 31 wt%;
aluminum in an amount of from 7 wt% to 10 wt%;
carbon in an amount of from 1.2 wt% to 1.6 wt%;
molybdenum in an amount of more than 0 wt% and less than 6 wt%; and
a balance of iron.
2. The austenitic steel alloy according to Claim 1, characterized in that said manganese is in an amount of from 26 wt% to 30 wt% and said aluminum is in an
amount of from 8 wt% to 10 wt%.
3. The austenitic steel alloy according to Claim 2, characterized in that said manganese is in an amount of from 27 wt% to 29 wt% and said molybdenum is in
an amount of from 2 wt% to 6 wt%.
4. The austenitic steel alloy according to Claim 3, characterized in that said aluminum is in an amount of from 8 wt% to 9 wt%.
5. The austenitic steel alloy according to any one of Claims 1 to 4, characterized in that said carbon is in an amount of from 1.4 wt% to 1.6 wt%.
6. The austenitic steel alloy according to any one of Claims 1 to 5, characterized in that said molybdenum is in an amount of from 2 wt% to 6 wt%.
7. The austenitic steel alloy according to any one of Claims 1 to 6, further characterized by chromium in an amount of less than 6 wt%.
8. The austenitic steel alloy according to any one of Claims 1 to 7, further characterized by cobalt in an amount of less than 5 wt%.
9. A method for making an austenitic steel,
characterized by steps of:
a) smelting the austenitic steel alloy of any one of Claims 1 to 8 to obtain a molten
steel alloy;
b) casting the molten steel alloy to obtain a cast piece;
c) subjecting the cast piece to a hot-working treatment at a temperature of from 1100°C
to 950°C to obtain a hot-worked body;
d) subjecting the hot-worked body to an initial water-quenching treatment to obtain
a water-quenched body; and
e) subjecting the water-quenched body to an aging treatment at a temperature of from
480°C to 600°C to obtain an aged body.
10. The method according to Claim 9, characterized in that the temperature for the aging treatment is from 480°C to 500°C, and the aging treatment
is implemented for a period of from 5 hours to 12 hours.
11. The method according to Claim 9 or 10, characterized in that the temperature for the aging treatment is larger than 500°C and up to 600°C, and
the aging treatment is implemented for a period of from 1 hour to 4 hours.
12. The method according to any one of Claims 9 to 11, further characterized by a step of subjecting the aged body to a further water-quenching treatment.
13. The method according to any one of Claims 9 to 12, characterized in that in step c), the hot-worked body has a thickness of less than 25% of that of the cast
piece.
14. An austenitic steel made by the method according to any one of Claims 9 to 13, characterized in that said austenitic steel has a fully austenitic phase, a yield strength at 25°C of from
1200 MPa to 1400 MPa, a Rockwell C hardness at 25°C of from 45 to 55, an ultimate
tensile strength at 25°C of from 1200 MPa to 1500 MPa, and an elongation at 25°C of
from 20% to 40%.
15. The austenitic steel according to Claim 14, characterized in that said austenitic steel has an ultimate tensile strength at 300°C of larger than 1000
MPa.
16. The austenitic steel according to Claim 14 or 15, characterized in that said austenitic steel has a yield strength at 300°C of larger than 970 MPa.
17. The austenitic steel according to any one of Claims 14 to 16, characterized in that said austenitic steel has a yield strength at 500°C of larger than 650 MPa and an
ultimate tensile strength at 500°C of larger than 700 MPa.
18. The austenitic steel according to any one of Claims 14 to 17, characterized in that said austenitic steel has a yield strength at 700°C of from 410 MPa to 420 MPa and
an ultimate tensile strength at 700°C of from 440 MPa to 449 MPa.