Technical Field
[0001] The present invention relates to a fire-resistant molding material.
Background Art
[0002] Fireproof performance is one of the performances required for fittings, such as windows,
shoji (paper sliding doors),
tobira (i.e., doors),
to (Japanese doors),
fusuma (Japanese sliding screens), and
ramma (transoms), used for the openings of structures, such as houses. In order to enhance
fireproof performance, fire-resistant molding materials are mounted in fittings. In
the frames of fittings placed in openings of structures, thermally expandable materials
were conventionally mounted in the frames so as to prevent the penetration of flames.
[0003] Patent Literature (PTL) 1 discloses a heat-resistant panel using a thermoplastic
elastomer. However, since the material is flexible, such a panel cannot be used for
parts requiring high rigidity.
Citation List
Patent Literature
Summary of Invention
Technical Problem
[0005] As fire-resistant molding materials having fire-resistant functions, flexible materials
that easily conform to the deformation have been used in many cases so as to increase
the airtightness and/or water tightness of openings. However, such materials are not
applicable to parts requiring rigidity.
[0006] An object of the present invention is to provide a fire-resistant molding material
having high rigidity and a high coefficient of thermal expansion.
Solution to Problem
[0007] Co-extrusion, which is a low-cost technique, is the most preferable option to produce
a fire-resistant molding material integrally including a member requiring rigidity
and a fire-resistant expansion part. However, highly rigid members generally require
a high extrusion temperature, and at such a temperature, expansion parts start expanding,
thus causing problems such as shape instability, poor appearance, and reduction in
fire-resistant performance due to inactivation of expandable graphite.
[0008] According to the present invention, it was found that the above problems can be solved
by increasing the viscosity of an expansion part to suppress the expansion of expandable
graphite. Specifically, increase in the viscosity of the expansion part allows co-extrusion,
which makes it possible to produce fire-resistant molding materials having excellent
rigidity. Co-extrusion also enables the production of a fire-resistant molding material
without an adhesive layer or an adhesion step.
[0009] The present invention provides fire-resistant molding materials described below.
Item 1. A fire-resistant molding material comprising a member A having a tensile elastic
modulus rate of 600 MPa or more and a member B having a coefficient of expansion of
10 times or more.
Item 2. The fire-resistant molding material according to Item 1, wherein the member
A has a Rockwell hardness of 70 or more.
Item 3. The fire-resistant molding material according to Item 1 or 2, wherein the
member A has a tensile yield strength of 20 MPa or more.
Item 4. The fire-resistant molding material according to any one of Items 1 to 3,
wherein the member A comprises a thermoplastic resin.
Item 5. The fire-resistant molding material according to any one of Items 1 to 4,
wherein the member B has a residue hardness of 0.3 kgf/cm2 or more.
Item 6. The fire-resistant molding material according to any one of Items 1 to 5,
wherein the member B comprises 3 to 300 parts by mass of a thermally expandable graphite
based on 100 parts by mass of a resin component.
Item 7. The fire-resistant molding material according to any one of Items 1 to 6,
which is produced by co-extrusion.
Advantageous Effects of Invention
[0010] The present invention provides a fire-resistant molding material integrally including
a part having high rigidity and a thermal expansion part.
Brief Description of Drawings
[0011]
Fig. 1 is a sectional view of a fire-resistant molding material according to one embodiment
of the present invention.
Fig. 2 is a perspective view showing another example of a molded article according
to the present invention.
Fig. 3 is a partial sectional view showing a state in which the molded article of
Fig. 2 is used.
Description of Embodiments
[0012] A fire-resistant molding material of the present invention can be used for windows
(including double sliding windows, casement windows, double hung windows, or the like),
tobira (i.e., doors), to (Japanese doors), and like those requiring high rigidity. A member
A provides the fire-resistant molding material with high rigidity and a member B provides
the fire-resistant molding material with fire-resistance.
[0013] The fire-resistant molding material of the present invention comprises a member A
having a tensile elastic modulus rate of 600 MPa or more and a member B having a coefficient
of expansion of 10 times or more. The member A and the member B are integrally formed.
[0014] The tensile elastic modulus rate of the member A is 600 MPa or more, preferably 800
MPa or more, and more preferably 1000 MPa or more. Although the upper limit of the
tensile elastic modulus rate of the member A is not particularly limited, it is 250000
MPa or less.
[0015] The Rockwell hardness of the member A is preferably 70 or more, more preferably 75
or more, and even more preferably 80 or more. Although the upper limit of the Rockwell
hardness of the member A is not particularly limited, it is 130 or less.
[0016] The tensile yield strength of the member A is preferably 20 MPa or more, more preferably
25 MPa or more, and even more preferably 30 MPa or more. Although the tensile yield
strength of the member A is not particularly limited, it is 3000 MPa or less.
[0017] The "tensile elastic modulus rate" can be calculated as follows. A dumbbell-shaped
specimen according to JIS K7161-2 is cut from the member A, and the dumbbell-shaped
specimen is subjected to a tensile test according to JIS K7161-2. A stress-strain
curve is drawn, and the tensile elastic modulus rate can be calculated according to
formula (I) below based on the first linear part of the stress-strain curve.

[0018] In formula (I), Δσ represents a difference in stress according to an original average
cross-sectional area of two points on a straight line, and Δε represents a difference
in strain between the same two points.
[0019] The "tensile yield strength" can be measured according to JISK7161-2.
[0020] The "Rockwell hardness" can be measured according to JISK7202-2.
[0021] The coefficient of expansion of the member B of the present invention is 10 times
or more, preferably 15 times or more, and more preferably 20 times or more. Although
the upper limit of the coefficient of expansion of the member B is not particularly
limited, it is 50 times or less.
[0022] The residue hardness of the member B of the present invention is 0.3 kgf/cm
2 or more, preferably 0.4 kgf/cm
2 or more, and more preferably 0.5 kgf/cm
2 or more. Although the upper limit of the residue hardness of the member B is not
particularly limited, it is 3.0 kgf/cm
2 or less.
[0023] The material constituting the member A may be, for example, metal, a non-expandable
resin, or a composite material thereof, and is preferably a non-expandable resin.
The non-expandable resin is made of a thermoplastic resin, a thermosetting resin,
an elastomer, rubber, or a combination thereof. A non-expandable resin containing
a thermoplastic resin is preferred. Examples of thermoplastic resins include fluororesin,
polyphenylene ether, modified polyphenylene ether, polyphenylene sulfide, polycarbonate,
polyetherimide, polyetheretherketone, polyarylate, polyamide, polyamideimide, polybutadiene,
polyimide, acrylic resin, polyacetal, polyamide, polyethylene, polyethylene terephthalate,
polycarbonate, polyester, polystyrene, polyphenylene sulfide, polybutylene terephthalate,
polypropylene, polyvinyl chloride, ABS resin, AS resin, and the like. Examples of
thermosetting resins include epoxy resins, phenol resins, melamine resins, urea resins,
unsaturated polyester resins, alkyd resins, polyurethane, thermosetting polyimide,
and the like. Examples of elastomers include olefin-based elastomers, styrene-based
elastomers, ester-based elastomers, amide-based elastomers, vinyl chloride-based elastomers,
and the like. Examples of rubber include natural rubber, silicone rubber, styrene-butadiene
rubber, isoprene rubber, butadiene rubber, chloroprene rubber, acrylonitrile-butadiene
rubber, nitrile butadiene rubber, butyl rubber, ethylene-propylene rubber, ethylene-propylene-diene
rubber, urethane rubber, silicone rubber, fluororubber, and the like.
[0024] In a preferable embodiment of the present invention, the member B is a resin composition
containing a thermally expandable graphite as a resin component.
[0025] A wide range of known resin components may be used as the resin component. Examples
include thermoplastic resins, thermosetting resins, rubber substances, and combinations
thereof.
[0026] Examples of thermoplastic resins include polyolefin resins, such as polypropylene
resins, polyethylene resins, poly(1-)butene resins, and polypentene resins; and synthetic
resins, such as polystyrene resins, acrylonitrile-butadienestyrene (ABS) resins, polycarbonate
resins, polyphenylene ether resins, (meth)acryl-based resins, polyamide resins, polyvinyl
chloride resins, novolac resins, polyurethane resins, polyisobutylene, and ethylene
vinyl acetate resins.
[0027] Examples of thermosetting resins include synthetic resins, such as polyurethane,
polyisocyanate, polyisocyanurate, phenol resins, epoxy resins, urea resins, melamine
resins, unsaturated polyester resins, and polyimide.
[0028] Examples of rubber substances include natural rubber, isoprene rubber, butadiene
rubber, 1,2-polybutadiene rubber, styrene-butadiene rubber, chloroprene rubber, nitrile
rubber, butyl rubber, chlorinated butyl rubber, ethylene-propylene rubber, chlorosulfonated
polyethylene, acrylic rubber, epichlorohydrin rubber, highly vulcanized rubber, non-vulcanized
rubber, silicone rubber, fluorine rubber, urethane rubber, thermoplastic olefinic
elastomers (TPOs), and the like.
[0029] One or more kinds of these synthetic resins and/or rubber substances may be used.
[0030] Among these synthetic resins and/or rubber substances, a flexible and rubbery substance
is preferred. Resin components with such properties enable high filling of an inorganic
filler, thereby obtaining a flexible and easily manageable resin composition. To obtain
a more flexible and easily manageable resin composition, a non-vulcanized rubber such
as butyl and a polyethylene-based resin are preferably used.
[0031] In terms of improving the fireproof performance by increasing the flame retardancy
of the resin itself, an epoxy resin is preferred.
[0032] The thermally expandable graphite is a conventionally known substance. The thermally
expandable graphite is a graphite intercalation compound formed by treating a powder,
such as natural flake graphite, pyrolytic graphite, or kish graphite, with an inorganic
acid, such as concentrated sulfuric acid, nitric acid, or selenic acid, and with a
strong oxidizing agent, such as concentrated nitric acid, perchloric acid, perchlorate,
permanganate, dichromate, or hydrogen peroxide. The thermally expandable graphite
is a kind of crystalline compound that retains the layered structure of the carbon.
[0033] The thermally expandable graphite obtained by acid treatment as described above may
be further neutralized with ammonia, an aliphatic lower amine, an alkali metal compound,
an alkaline earth metal compound, or the like. Examples of commercially available
products of thermally expandable graphite include "GREP-EG" produced by Tosoh Corporation,
"GRAFGUARD" produced by GRAFTECH, and the like.
[0034] For example, the member B may comprise 3 to 30 parts by mass of the thermally expandable
graphite, based on 100 parts by mass of the resin component. The member B may further
comprise an inorganic filler.
[0035] When an expandable heat insulating layer is formed, the inorganic filler contained
therein increases heat capacity and suppresses heat transfer, and also functions as
an aggregate, thereby improving the strength of the expandable heat insulating layer.
Examples of inorganic fillers include, but are not particularly limited to, metal
oxides, such as alumina, zinc oxide, titanium oxide, calcium oxide, magnesium oxide,
iron oxide, tin oxide, antimony oxide, and ferrites; hydrated inorganic substances,
such as calcium hydroxide, magnesium hydroxide, aluminum hydroxide, and hydrotalcite;
metal carbonates, such as basic magnesium carbonate, calcium carbonate, magnesium
carbonate, zinc carbonate, strontium carbonate, and barium carbonate; and the like.
[0036] In addition to the above, examples of inorganic fillers also include calcium salts,
such as calcium sulfate, gypsum fiber, and calcium silicate; silica, diatomaceous
earth, dawsonite, barium sulfate, talc, clay, mica, montmorillonite, bentonite, activated
clay, sepiolite, imogolite, sericite, glass fiber, glass bead, silica balloon, aluminum
nitride, boron nitride, silicon nitride, carbon black, graphite, carbon fiber, carbon
balloon, charcoal powder, various types of metal powder, potassium titanate, magnesium
sulfate, lead zirconate titanate, zinc stearate, calcium stearate, aluminum borate,
molybdenum sulfide, silicon carbide, stainless steel fiber, zinc borate, various types
of magnetic powder, slag fiber, fly ash, dehydrated sludge, and the like. These inorganic
fillers may be used singly, or in a combination of two or more.
[0037] The resin composition constituting the member B may comprise 1 to 300 parts by mass
of the inorganic filler, based on 100 parts by mass of the resin component.
[0038] When the member B contains the inorganic filler, the total amount of the thermally
expandable graphite and the inorganic filler is preferably in the range of 3 to 300
parts by mass, based on 100 parts by mass of the resin component.
[0039] The melt viscosity of the resin composition constituting the member B at a temperature
of 160°C and a shear rate of 120 (1/s) is preferably 1000 to 2500 Pa·s, and more preferably
1200 to 2100 Pa·s. Increasing the viscosity of the resin composition of the member
B can suppress the expansion of the member B when the member A and the member B are
co-extruded.
[0040] This resin composition is expanded by heating and forms a fire-resistant heat-insulating
layer. According to this formulation, the fire-resistant molding material can be expanded
by the heating of fire to obtain a necessary coefficient of cubical expansion. The
expanded fire-resistant molding material can form a residue having predetermined heat-insulating
capacity and predetermined strength, and can achieve stable fireproof performance.
[0041] In order to increase the strength of the expandable heat-insulating layer and to
enhance the fireproof performance, the resin composition that constitutes the fire-resistant
molding material may optionally contain, in addition to the above components, the
following components within a range that does not impair the object of the present
invention: red phosphorus; various phosphates, such as triphenyl phosphate, tricresyl
phosphate, trixylenyl phosphate, cresyl diphenyl phosphate, and xylenyl diphenyl phosphate;
metal salts of phosphoric acids, such as sodium phosphate, potassium phosphate, and
magnesium phosphate; ammonium polyphosphates; phosphorus compounds, such as compounds
represented by formula (1) below; and the like.
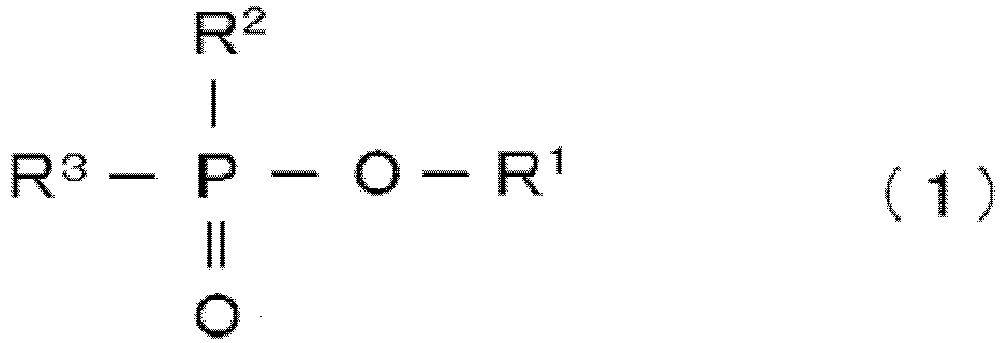
[0042] In formula (1), R
1 and R
3 are the same or different, and each represents hydrogen, a linear or branched alkyl
group having 1 to 16 carbon atoms, or an aryl group having 6 to 16 carbon atoms. R
2 represents a hydroxyl group, a linear or branched alkyl group having 1 to 16 carbon
atoms, a linear or branched alkoxyl group having 1 to 16 carbon atoms, an aryl group
having 6 to 16 carbon atoms, or an aryloxy group having 6 to 16 carbon atoms.
[0043] Furthermore, the resin composition constituting the fire-resistant molding material
may optionally contain, within a range that does not impair the object of the present
invention, an antioxidant, based on phenol, amine, sulfur, or the like, a metal deterioration
inhibitor, an antistatic agent, a stabilizer, a crosslinking agent, a lubricant, a
softening agent, a pigment, a tackifier resin, a molding auxiliary material, and like
additives; a polybutene, a petroleum resin, and a like tackifier.
[0044] The member B is also commercially available. Examples include Fire Barrier produced
by Sumitomo 3M (a fire-resistant molding material comprising a resin composition containing
chloroprene rubber and vermiculite; coefficient of expansion: 3 times, heat conductivity:
0.20 kcal/m·h·°C), Mejihikatto produced by Mitsui Kinzoku Paints & Chemicals Co.,
Ltd. (a fire-resistant molding material comprising a resin composition containing
a polyurethane resin and thermally expandable graphite; coefficient of expansion:
4 times, heat conductivity: 0.21 kcal/m·h·°C), Fi-Block produced by Sekisui Chemical
Co., Ltd.; and the like.
[0045] The fire-resistant molding material of the present invention may further comprise
a coating layer. The coating layer may be made of any material that allows expansion
of the member B upon heating. Combustible materials and noncombustible materials can
be used. When the coating layer is made of a combustible material, the member B can
be more easily expanded, and predetermined fireproof performance can be well exhibited.
[0046] When the fire-resistant molding material comprises a coating layer, the coating layer
may be disposed so that it is in contact with the member B and/or member A.
[0047] Although the combustible material is not particularly limited, it is preferable to
use a thermoplastic resin, an elastomer, rubber, or a combination thereof. Examples
of thermoplastic resins include fluororesin, polyphenylene ether, modified polyphenylene
ether, polyphenylene sulfide, polycarbonate, polyetherimide, polyetheretherketone,
polyarylate, polyamide, polyamideimide, polybutadiene, polyimide, acrylic resin, polyacetal,
polyamide, polyethylene, polyethylene terephthalate, polycarbonate, polyester, polystyrene,
polyphenylene sulfide, polybutylene terephthalate, polypropylene, polyvinyl chloride,
ABS resin, AS resin, and the like. Examples of elastomers include olefin-based elastomers,
styrene-based elastomers, ester-based elastomers, amide-based elastomers, vinyl chloride-based
elastomers, and the like. Examples of rubber include natural rubber, silicone rubber,
styrene-butadiene rubber, isoprene rubber, butadiene rubber, chloroprene rubber, acrylonitrile-butadiene
rubber, nitrile butadiene rubber, butyl rubber, ethylene-propylene rubber, ethylene-propylene-diene
rubber, urethane rubber, silicone rubber, fluororubber, and the like. The thickness
of the coating layer made of a thermoplastic resin, an elastomer, rubber, or a combination
thereof is not particularly limited, but is generally 0.5 to 6 mm.
[0048] Moreover, the coating layer may be made of metal, a metal alloy, or a combination
of metal and a combustible material mentioned above.
[0049] The coating layer may have any appearance, and the color and pattern can be determined
depending on the purpose. In one embodiment, the color of the coating layer is similar
to the color of a frame of the fitting to which the fire-resistant molding material
is attached. For example, when the fire-resistant molding material 1 is attached to
an aluminum window frame, the color of the coating layer can be aluminum color. The
term "similar color" means that, among the three elements represented by the characteristics
of color, i.e., hue, brightness, and saturation, the hue is the same or similar. Specifically,
warm colors, cold colors, white and opaque white, transparent and semi-transparent
colors, or the like can be specified as similar colors. Moreover, designability can
be imparted to the coating layer by forming any pattern, such as a wood grain pattern
to give visual warmth. Thus, the designability of the member B having black ash color
can be increased by coating the member B with the coating layer. Furthermore, coating
with the coating layer enhances the weather resistance of the member B, and also increases
the long-term durability of the fire-resistant molding material.
[0050] The kneaded product of resin compositions individually constituting the member A
and the member B can be obtained by mixing and kneading the above components by using
a known kneading apparatus, such as an extruder, a Banbury mixer, a kneader mixer,
or a kneading roll (and further a Raikai mixer, a planetary stirrer, or the like in
the case of a thermosetting resin, such as an epoxy resin). Moreover, in the case
of a two-component thermosetting resin, particularly an epoxy resin, the kneaded product
may be produced by separately producing kneaded products of each of the two components
and a filler by a kneading method mentioned above, supplying each kneaded product
by a plunger pump, a snake pump, a gear pump, or the like, and mixing them by a static
mixer, a dynamic mixer, or the like.
[0051] As the method for molding resin compositions individually constituting the member
A and the member B, the above kneaded product can be molded by a known method, such
as press molding, calender molding, extrusion molding, or injection molding. Moreover,
as the method for molding a two-component thermosetting resin, particularly an epoxy
resin, a known method can be suitably used depending on the shape, such as roll molding
of a sheet molding compound (SMC), coater molding by a roll coater or a blade coater.
[0052] The production method of the fire-resistant molding material 1 is not particularly
limited. The member A and the member B may be co-extruded, or integrally bound to
each other using an adhesion means, such as an adhesion sheet or adhesive. Alternatively,
the member A and the member B may be integrally bound by physical securing. The member
A and the member B are preferably co-extruded.
[0053] The thickness of the member B is not limited, but is preferably 0.1 to 6 mm. When
the thickness of the member B is 0.1 mm or more, sufficient fireproof performance
can be exhibited due to the thickness of the expandable heat-insulating layer formed
by heating. Moreover, when the thickness of the member B is 6 mm or less, insertion
into the hollow can be easy.
[0054] The fire-resistant molding material of the present invention can be mounted in fittings,
such as windows,
shoji (paper sliding doors),
tobira (i.e., doors),
to (Japanese doors),
fusuma (Japanese sliding screens), and
ramma (transoms), used for the openings of structures, such as houses and buildings. The
fire-resistant molding material of the present invention can be also used in
shoji frames or frames of resin sashes.
[0055] The fire-resistant molding material according to one embodiment of the present invention
is explained with reference to Fig. 1.
[0056] As shown in Fig. 1, the fire-resistant molding material 1 includes the member A having
a tensile elastic modulus rate of 600 MPa or more and the member B having a coefficient
of expansion of 10 times or more. The member A and the member B are integrally molded
in a sheet form.
[0057] The upper end of the frame 2 is provided with a pair of opposite rail-like raised
portions 2a and 2b extending along the longitudinal direction of the frame 2. The
raised portions 2a and 2b, and the two projections 3, have an approximately L-shaped
cross-section in the longitudinal direction of the fire-resistant molding material
1. Each of the raised portions 2a and 2b is individually engaged with corresponding
one of the two projections 3.
[0058] Figs. 2 and 3 each show another embodiment of the heat-resistant material of the
present invention. Fig. 2 shows a glazing-channel-type construction gasket 30 that
is mounted in the periphery of a glass panel 38 (refer to Fig. 3). Fig. 3 is a sectional
view describing a state in which the gasket 30 of Fig. 2 is used in the glass panel.
[0059] The gasket 30 comprises a bottom wall 32 oppositely facing an end surface 39 of the
glass panel 38, and side walls 33 that are continuously formed with the bottom wall
32 at both sides of the bottom wall 32 and that cover the glass panel periphery 40
along the longitudinal direction of the glass panel end surface 39. The bottom wall
32 and side walls 33 form the main body 31 of the gasket 30. The main body 31 is made
of the member A.
[0060] A protrusion 34 is formed on the upper end of each side wall 33. Each protrusion
34 has an outside fillet 35 and an inside fillet 36 that are projected toward the
inside, i.e., the side of the glass panel 38.
[0061] Each protrusion 34 includes a groove 37 outside, i.e., a side opposite to the glass
panel side. By inserting the ends of a sash in the grooves 37, the gasket 30 can be
secured to the sash. The protrusions 34 are constituted of the member B. The gasket
30 can be molded by co-extrusion of the main body 31 and the protrusions 34.
Examples
[0062] The present invention is explained in detail below with reference to the Examples.
The present invention is not limited to these Examples.
Examples 1 to 3
[0063] A resin composition containing components of member A in amounts (parts by mass)
shown in Table 1 and a resin composition containing components of member B in amounts
(parts by mass) shown in Table 2 were mixed and kneaded, followed by co-extrusion
to obtain a sheet-like fire-resistant molding material. For the obtained fire-resistant
molding material, the melt viscosity, tensile elastic modulus rate, Rockwell hardness,
tensile yield strength, coefficient of expansion, and residue hardness were measured
under the measurement conditions described in Tables 3, 4, or 5. Measurement conditions
for the coefficient of expansion and residue hardness are described in Items (i) and
(ii) below. Tables 3, 4, and 5 show the results.
(i) Coefficient of expansion
[0064] A sample immersed in a wire sieve with 200 mesh was placed in a box frame made of
SUS. The box frame was placed in an electric furnace that had been heated beforehand
at 600°C, and was heated for 30 minutes. The residue thickness of the extracted sample
was measured with a caliper, and the coefficient of expansion was calculated according
to the following formula:

(ii) Residue hardness
[0065] After the measurement of the coefficient of expansion, the residue was compressed
with an indenter having an area of 0.25 cm
2 at a compression speed of 0.1 cm/min by using a tensile tester (Tensilon RTC, Orientec
Corporation). The maximum load point that appeared first was defined as the residue
hardness.
Table 1
Material name |
Manufacturer and product name |
Example 1 |
Example 2 |
Example 3 |
Polyvinyl chloride |
Shin-Etsu Chemical Co., Ltd., TK-800 |
100 |
100 |
100 |
Epoxy soybean oil |
ADEKA Corporation, O-130P |
0 |
20 |
0 |
Calcium carbonate |
Shiraishi Calcium Kaisha, Ltd., Whiton B |
15 |
15 |
15 |
Ca-Zn heat stabilizer |
Mizusawa Industrial Chemical Ltd., NT-231 |
3 |
3 |
3 |
Calcium stearate |
Sakai Chemical Industry Co., Ltd., SC-100 |
5 |
5 |
5 |
Polymethyl methacrylate |
Mitsubishi Rayon Co., Ltd., P-530A |
0.5 |
0.5 |
0.5 |
Table 2
|
|
Example 1 |
Example 2 |
Example 3 |
Chlorinated vinyl chloride |
Tokuyama Sekisui Co., Ltd., HA53K |
100 |
100 |
100 |
DIDP |
J-PLUS Co., Ltd. |
55 |
55 |
70 |
Expanded graphite |
Tosoh Corporation, GREP-EG |
145 |
110 |
150 |
Calcium carbonate |
Shiraishi Calcium Kaisha, Ltd., Whiton BF300 |
15 |
50 |
15 |
Chlorinated polyethylene |
Weihai Jinhong Chemical Industry Co., Ltd., 135A |
20 |
20 |
20 |
Ca-Zn heat stabilizer |
Mizusawa Industrial Chemicals, Ltd., NT-231 |
3 |
3 |
3 |
Calcium stearate |
Sakai Chemical Industry Co., Ltd., SC-100 |
5 |
5 |
5 |
Polymethyl methacrylate |
Mitsubishi Rayon Co., Ltd., P-530A |
20 |
20 |
20 |
DIDP: Diisodecyl phthalate |
Table 3
Example 1 |
|
Measurement conditions |
Member A, rigid part |
Member B, expansion part |
Determination |
Melt viscosity |
Pa·s |
Capillary type rheometer 160°C, 120(1/s) |
(2310) |
1980 |
A |
Tensile elastic modulus rate |
MPa |
JISK7161-2 |
1590 |
- |
A |
Rockwell hardness |
- |
JISK7202-2 |
94 |
- |
A |
Tensile yield strength |
MPa |
JISK7161-2 |
41.5 |
- |
A |
Coefficient of expansion |
Times |
600°C, 30 min. |
- |
57 |
A |
Residue hardness |
kgf/cm2 |
600°C, 30 min. |
- |
0.60 |
A |
Appearance of member B: Excellent |
Table 4
Example 2 |
|
Measurement conditions |
Member A, rigid part |
Member B, expansion part |
Determination |
Melt viscosity |
Pa·s |
Capillary-type rheometer 160°C, 120(1/s) |
(1810) |
2010 |
A |
Tensile elastic modulus rate |
MPa |
JISK7161-2 |
1100 |
- |
A |
Rockwell hardness |
- |
JISK7202-2 |
80 |
- |
A |
Tensile yield strength |
MPa |
JISK7161-2 |
26.5 |
- |
A |
Coefficient of expansion |
Times |
600°C, 30 min. |
- |
44 |
A |
Residue hardness |
kgf/cm2 |
600°C, 30 min. |
- |
0.78 |
A |
Appearance of member B: Excellent |
Table 5
Example 3 |
|
Measurement conditions |
Member A, rigid part |
Member B, expansion part |
Determination |
Melt viscosity |
Pa·s |
Capillary-type rheometer 160°C, 120(1/s) |
(2310) |
1439 |
A |
Tensile elastic modulus rate |
MPa |
JISK7161-2 |
1100 |
- |
A |
Rockwell hardness |
- |
JISK7202-2 |
80 |
- |
A |
Tensile yield strength |
MPa |
JISK7161-2 |
26.5 |
- |
A |
Coefficient of expansion |
Times |
600°C, 30 min. |
- |
56 |
A |
Residue hardness |
kgf/cm2 |
600°C, 30 min. |
- |
0.62 |
A |
Appearance of member B: Excellent |
[0066] Because the member B had high melt viscosity, expansion was suppressed, and appearance
was excellent. The "determination" criteria of Tables 3, 4, 5, 10, and 11 are shown
below.
- A: Excellent
- B: Poor
Examples 4 to 5
[0067] A resin composition containing components of member A in amounts (parts by mass)
shown in Table 6 or 8 and a resin composition containing components of member B in
amounts (parts by mass) shown in Table 7 or 9 were mixed and kneaded, followed by
co-extrusion to obtain a sheet-like fire-resistant molding material. For the obtained
fire-resistant molding material, the melt viscosity, tensile elastic modulus rate,
Rockwell hardness, tensile yield strength, coefficient of expansion, and residue hardness
were measured under the measurement conditions described in Table 10 or 11. Measurement
conditions for the coefficient of expansion and residue hardness are the same as those
described in Items (i) and (ii) above. Tables 10 and 11 show the results.
Table 6
Material name |
Manufacturer and product name |
Example 4 |
Polyvinyl chloride |
Shin-Etsu Chemical Co., Ltd., TK-800 |
100 |
Epoxy soybean oil |
ADEKA Corporation, O-130P |
0 |
Calcium carbonate |
Shiraishi Calcium Kaisha, Ltd., Whiton B |
15 |
Ca-Zn heat stabilizer |
Mizusawa Industrial Chemicals, Ltd., NT-231 |
3 |
Calcium stearate |
Sakai Chemical Industry Co., Ltd., SC-100 |
5 |
Polymethyl methacrylate |
Mitsubishi Rayon Co., Ltd., P-530A |
0.5 |
Table 7
|
Manufacturer and product name |
Example 4 |
Ethylene vinyl acetate resin |
Mitsubishi Chemical Corporation., UF420 |
100 |
Aluminum phosphite |
Taihei Chemical Industrial Co., Ltd., APA100 |
50 |
Expandable graphite |
Air Water Inc., CA-60N |
40 |
Calcium carbonate |
Shiraishi Calcium Kaisha, Ltd., Whiton BF300 |
15 |
PTFE-based auxiliary agent |
Mitsubishi Chemical Corporation., A-3000 |
2 |
Table 8
Material name |
Manufacturer and product name |
Example 5 |
Polypropylene |
Novatec EA9 |
100 |
Hindered phenol-based |
ADEKA Corporation, AO60 |
0.3 |
Calcium carbonate |
Shiraishi Calcium Kaisha, Ltd., Whiton B |
15 |
Phosphoric acid amine salt |
ADEKA Corporation, T1063F |
30 |
Table 9
|
Manufacturer and product name |
Example 5 |
TPO |
Sumitomo Chemical Co., Ltd., Esporex 822 |
100 |
Aluminum phosphite |
Taihei Chemical Industrial Co., Ltd, APA100 |
50 |
Expandable graphite |
Air Water Inc., CA-60N |
40 |
Carbon black |
Asahi Carbon Co., Ltd., #55G |
15 |
PTFE-based auxiliary agent |
Mitsubishi Chemical Corporation., A-3000 |
2 |
Table 10
Example 4 |
|
Measurement conditions |
Member A, rigid part |
Member B, expansion part |
Determination |
Melt viscosity |
Pa·s |
Capillary-type rheometer 195°C, 120(1/s) |
(2280) |
1422 |
A |
Tensile elastic modulus rate |
MPa |
JISK7161-2 |
1590 |
- |
A |
Rockwell hardness |
- |
JISK7202-2 |
94 |
- |
A |
Tensile yield strength |
MPa |
JISK7161-2 |
41.5 |
- |
A |
Coefficient of expansion |
Times |
600°C, 30 min. |
- |
18 |
A |
Residue hardness |
kgf/cm2 |
600°C, 30 min. |
- |
0.38 |
A |
Appearance of member B: Excellent |
Table 11
Example 5 |
|
Measurement conditions |
Member A, rigid part |
Member B, expansion part |
Determination |
Melt viscosity |
Pa·s |
Capillary-type rheometer 195°C, 120(1/s) |
(1632) |
1474 |
A |
Tensile elastic modulus rate |
MPa |
JISK7161-2 |
1250 |
- |
A |
Rockwell hardness |
- |
JISK7202-2 |
95 |
- |
A |
Tensile yield strength |
MPa |
JISK7161-2 |
35 |
- |
A |
Coefficient of expansion |
Times |
600°C, 30 min. |
- |
17 |
A |
Residue hardness |
kgf/cm2 |
600°C, 30 min. |
- |
0.42 |
A |
Appearance of member B: Excellent |
Reference Numerals
[0068]
- 1.
- Fire-resistant molding material
- 2.
- Frame
- 2a.
- Raised portion
- 2b.
- Raised portion
- 3.
- Projection
- 30.
- Gasket
- 31.
- Main body
- 32.
- Bottom wall
- 33.
- Side wall
- 34.
- Protrusion
- 35.
- Outside fillet
- 36.
- Inside fillet
- 37.
- Groove
- 38.
- Glass panel
- 39.
- Glass panel end surface
- 40.
- Glass panel periphery