[0001] Embodiments of the present disclosure relate to an MEMS device, to a sound transducer
comprising said MEMS device, and to a manufacturing method of said MEMS device.
[0002] MEMS (microelectromechanical system) devices allow realizing sound transducers, like
loudspeakers or microphones, for example. Such sound transducers typically comprise
a membrane which can be excited to oscillate externally or by means of sound in the
surroundings (microphone), or be excited to oscillate electrically (for realizing
a loudspeaker). These membranes are formed by means of semiconductor technologies
in or on a substrate. Apart from the "MEMS microphone" and "MEMS sound transducer"
applications, there are further MEMS devices, like MEMS-based sensors, for example
pressure sensors or concentration sensors having a functional layer.
[0003] In particular in microphones, an important parameter is the sensitivity of the entire
system. Typically, the sensitivity of the microphone can be improved by reducing the
membrane thickness or by increasing the membrane area (diameter). Both ways have disadvantages.
Increasing the size of a membrane is expensive and with reduction of the membrane
thickness the microphones lose mechanical stability, in particular during manufacturing
and in the application.
[0004] Embodiments of the present disclosure provide an MEMS device comprising a membrane
configured to oscillate (when excited externally or excited electrically). The membrane
comprises an auxetic structure at least in portions thereof. In accordance with embodiments,
an auxetic structure is a structure which, as a consequence of expansion, e.g. expansion
of the membrane in a first (lateral) direction, expands of its own accord in a second,
e.g. orthogonal (lateral) direction, and/or wherein the thickness of the membrane
increases as a consequence of the expansion in the first direction. When reversing
this process, auxetic structures also exhibit comparable characteristics, which means
that, when compressing the membrane in the first (lateral) direction, the membrane
will be compressed of its own accord or due to the auxetic structure in the second,
e.g. orthogonal, (lateral) direction, or the thickness will be changed (reduced) correspondingly.
In accordance with an alternative definition, we speak of an auxetic structure when
the structure or the material has a negative Poisson's ratio. Starting here, the material
or structure considered exemplarily becomes thicker in a direction perpendicular to
the force applied.
[0005] In accordance with embodiments, the auxetic structure comprises a plurality of auxetic
structural elements, like identical or mutually similar structural elements. Each
of these auxetic structural elements may be formed by an area (in parallel to the
membrane) enclosed or defined by four, preferably arched, lateral boundaries (like
profile structures, steps or trenches). In accordance with embodiments, these (preferably
identical) structural elements are arranged in one or several rows (row after row
in order to cover the membrane region at least in an area portion). The plurality
of the auxetic structural elements in one row are mutually adjacent so that a first
and a third one exhibit an identical orientation, wherein a second auxetic structural
element arranged therebetween is rotated compared to the first and third auxetic structural
elements, like rotated by 90°. According to further embodiments, the individual auxetic
structural elements can be different within a membrane. I.e. the auxetic structure
comprises a plurality of auxetic structural elements, wherein at least two auxetic
structural elements differ from each other.
[0006] Assuming that, in accordance with embodiments, each auxetic structural element is
formed by two opposite lateral boundaries (i.e. along the membrane plane) and two
further opposite lateral boundaries, it becomes obvious that each auxetic structural
element forms a kind of quadrangle, for example, wherein, in accordance with embodiments,
the lateral opposite boundaries and the further lateral opposite boundaries are bent
(the result not being a classical quadrangle). In accordance with embodiments, the
arched opposite lateral boundaries may be formed as follows: each auxetic structural
element is confined by two opposite lateral concave and two opposite lateral convex
boundaries so that the auxetic area element of the respective auxetic structural element
is enclosed by the two concave and the two convex boundaries. In this embodiment,
it is obvious that, when assuming the lateral structural elements to be arranged in
a row, wherein the lateral structural element arranged between two other lateral structural
elements is rotated when compared to the other ones, the concave boundary for the
central (rotated) lateral structural element also represents the convex boundary for
the adjacent (non-rotated) structural element. According to further embodiments, the
auxetic structural elements can be also different within a membrane. For example,
the orientation could be rotational symmetric and/or the size can be scaled with respect
to the position inside the membrane.
[0007] In accordance with embodiments, each lateral boundary is formed by a raised profile,
like a dome from the substrate plane, or by a trench profile. Here, the raised profile
or the trench profile divides the plurality of auxetic structural elements among one
another. It is also to be mentioned at this point that, in accordance with embodiments,
the membrane thickness only varies minimally across the profile, i.e. only at the
transitions, wherein, in the region where the profile is formed, the membrane thickness
may exemplarily exhibit the same thickness as the membrane thickness in the region
of the area element (subsequently referred to as auxetic area element, which is enclosed
by the lateral boundaries) of the auxetic structural element. In accordance with embodiments,
the plurality of the auxetic structural elements each comprise an auxetic area element,
wherein the auxetic area elements extend in parallel to or along the membrane plane.
In accordance with embodiments, two of the auxetic area elements are arranged in two
different planes.
[0008] Assuming that each auxetic structural element comprises an auxetic area element enclosed
by the (four) boundaries, in accordance with further embodiments, it would be feasible
for the auxetic area elements to be positioned alternatingly in a top and a bottom
plane. In accordance with embodiments, the lateral boundary here is formed by a step
forming a transition from one auxetic area element of one of the plurality of auxetic
structural elements relative to another auxetic area element of an adjacent one of
the plurality of auxetic structural elements.
[0009] Both in an embodiment where the lateral boundary is formed by a step, and in the
embodiment where the lateral boundary is formed by a profile or a trench profile,
it is to be mentioned that, in accordance with embodiments, the step or profile/trench
is formed by the membrane itself.
[0010] Another embodiment relates to a sound transducer comprising an MEMS device as defined
above. In accordance with further embodiments, the sound transducer may form a microphone
configured to be excited to oscillate when excited by sound from the surroundings
and to output an electrical signal which depends on the sound.
[0011] Further embodiments provide a manufacturing method for forming an MEMS device as
discussed above, wherein the method comprises the step of forming a membrane by means
of depositing, wherein depositing takes place such that the auxetic structure is formed
in the membrane.
[0012] Further developments are defined in the sub-claims. Embodiments of the present disclosure
will be discussed referring to the appended drawings, in which:
- Fig. 1
- shows a schematic illustration of an MEMS device in accordance with a basic embodiment;
- Figs. 2a-h
- show schematic illustrations for illustrating the principle of auxetic structures;
- Figs. 3a-c
- show a schematic illustration of a membrane having an auxetic structure in accordance
with an embodiment;
- Figs. 4a-b
- show schematic illustrations of a membrane having an auxetic structure in accordance
with another embodiment;
- Figs. 5a-b
- show schematic illustrations of simulation results for membranes having auxetic structures
in accordance with embodiments.
[0013] Before discussing embodiments of the present disclosure below referring to the appended
drawings, it is to be pointed out that equal effects and structures are provided with
equal reference numerals so that the description thereof is mutually applicable or
exchangeable.
[0014] Fig. 1 shows an MEMS device 10, like a sound transducer in the form of a loudspeaker
or a microphone, for example. This MEMS device 10 comprises a membrane 12 which is
exemplarily formed in the substrate 14 of the MEMS device 10. The membrane 12 comprises
an auxetic structure 16. This auxetic structure may, for example, be applied onto
the membrane 12, or the membrane 12 may be formed such that the auxetic structure
is formed in the membrane, wherein the latter will be assumed for the following discussion.
[0015] As is illustrated here, the auxetic structure 16 is implemented by the membrane 12
being structured. The structuring 16p is, for example, formed by impressing a profile
16p into the membrane 12. In accordance with embodiments, the structuring is performed
such that the membrane comprises a plurality of profiles extending laterally in two
(crossing) directions, like a grid, along the membrane. In other words, this means
that the profiles 16p on the membrane surface impress elevations or recesses in a
type of grid shape. An auxetic area element 16f each which is enclosed by the profile
16p on four sides is formed in the meshes of the "grid", thereby forming four corners
at the points of contact of the profiles 16p. This means that the profiles 16p border
the auxetic area elements 16f laterally (lateral boundaries along the membrane 12
or along the respective plane). As is illustrated here, the profiles 16p/boundary
lines are preferably (but not necessarily) curved.
[0016] Generally speaking, the membrane 12 having the auxetic structure 16 allows an extension
of the membrane 12 in a first direction (cf. direction x), resulting in the membrane
to also expand in a second direction (like, for example, direction y, orthogonal to
direction x). Alternatively or additionally, it would also be conceivable for the
membrane 12 to vary, like increase, in its thickness (cf. z direction) as a consequence
of an expansion in the x direction. In accordance with embodiments, this characteristic
which is provided by the auxetic structure 16 results in the membrane 12 being more
flexible. This is due to the fact that, by applying the auxetic structure 16 on the
surface of the membrane 12, for example, or by structuring the membrane 12 in the
form of an auxetic structure, the membrane generally, or in portions, exhibits higher
a flexibility. In case the MEMS device 10 is, for example, used as a microphone, higher
a sensitivity of the microphone 10 is achieved by the increase in flexibility of the
membrane 12. When sticking to the example of a microphone, another positive side effect
is that the membrane 12 is considerably more robust to mechanical overstress, like
in the case of dropping it.
[0017] Subsequently, the principle of auxetic structures will be discussed below referring
to Figs. 2a-h.
[0018] Fig. 2a shows an auxetic structure 16 comprising boundaries 16g bordering the auxetic
area element 16f and extending laterally on the plane.
[0019] The action mechanism of such an auxetic structure will be discussed referring to
Fig. 2b. Reference here is made to the auxetic structural element provided with the
reference numeral 16f*.
[0020] The auxetic structural element 16f* comprises two concave lateral boundaries 16fc*
and two convex boundaries 16fcx*. The deformation, which is illustrated by the arrows,
exemplarily acts on the concave boundaries 16fcx*, resulting in the same to be compressed,
as is illustrated in broken lines. Consequently, the concave boundaries are also compressed
towards the interior by the points of contact of the concave and convex boundaries
16fcx* and 16fc*, as is illustrated in broken lines. When considering the entire auxetic
structure 16, this means that, when compressing in one direction (like y direction),
a compression in the x direction will also result, as is illustrated in Fig. 2c.
[0021] In Fig. 2c, the broken line illustrates the original shape with no external force
applied, wherein the area having the continuous line illustrates compression of the
auxetic structure 16f*. For comparative purposes, reference is made to Fig. 2d where
the identical area is compressed in the y direction, however with no auxetic structure,
the result of this, however, being an expansion in the x direction. It is to be pointed
out here that, with auxetic structures, the same principle also applies in the case
of an expansion, i.e. in the case of a tensile force in the y direction, the result
being an expansion of the area in the x direction. The deformations within the auxetic
structure are illustrated in Fig. 2g for the broken-line area of Fig. 2c in the compressed
state. Expressed generally, auxetic structures also exhibit a negative Poisson's ratio:
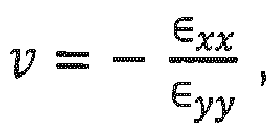
wherein ε
xx is the uniaxial stress in the xx direction and ε
yy is the uniaxial stress in the yy direction.
[0022] Fig. 2g illustrates an auxetic structure 16 which is, for example, employed in the
illustrative example of Fig. 2c. This auxetic structure 16 is basically implemented
to be two-dimensional. However, there are also three-dimensional auxetic structures,
as is, for example, illustrated in Fig. 2h.
[0023] Depending on the application, the membrane discussed referring to Fig. 1 may comprise
either two- or three-dimensional auxetic structures.
[0024] An example of an auxetic structure for a membrane each will be discussed below referring
to Figs. 3 and 4.
[0025] Fig. 3a is a top view of a fourth of a membrane, i.e. a roughly 90° segment of a
circle portion (cf. symmetry lines). The membrane is provided with the reference numeral
12' and comprises an auxetic structure 16'. The suspension or fixed support of the
membrane 12' is provided with the reference numeral 12f' using the arrows.
[0026] The auxetic structure 16' is illustrated in a three-dimensional view in Fig. 3b and
in an enlarged view in Fig. 3c. As can be recognized, the membrane 12' comprises a
membrane plane along which it exemplarily extends at a thickness of 0.5 µm (generally
in a range between 0.1 µm and 1.0 µm or 0.01 µm and 10 µm). The auxetic structure
16' projects from the membrane plane of the membrane 12' as a type of profile or arch.
This profile is illustrated in an enlarged manner in Fig. 3c and provided with the
reference numeral 16p'. As can be recognized, this profile 16p' is introduced into
the membrane 12' such that the membrane thickness of 0.5 µm remains roughly constant
across the arch. Only in the region of the transition from the membrane area element
(cf. reference numeral 16f') to the raised region 16p', the thickness is not constant.
A step which is provided with the reference numeral 16s' is formed here. The height
of the step is roughly 1 µm, but may vary in the range between 0.1 or 0.5 and 5.0
or 10 or 20 µm, depending on the embodiment. Generally, the step 16s' has a height
of n times the thickness of the membrane, wherein n may vary in a range between 0.5
and 20 (in this case n = 2).
[0027] The profile 16p' extends in curved lines (S-shaped curves) over the entire area so
that an auxetic area element 16f' is enclosed by four curved (90° bends) boundary
lines 16fcx' and 16fc' each. The entire auxetic structure 16' is formed by a plurality
of such area elements 16f' or auxetic structural elements arranged in several rows,
as is illustrated in Fig. 3a. The rows and the structural elements in a row are always
arranged to be directly adjacent to one another so that two area elements 16f1' and
16f2' are separated from each other by a profile 16p' therebetween. The area element
16f2' is rotated by 90° relative to the area element 16f1' so that the convex side
16fcx' of 16f2' forms the concave side 16fc' of 16f1'. The same mechanism for defining
the boundary between the area elements 16f' extends in both lateral dimensions of
the membrane 12'. The radii of all the profile lines 16p' may, for example, be approximately
20 µm (in this case 18 µm or, generally, in a range between 5 µm and 40 µm or between
2 µm and 100 µm). This is dependent on how big the auxetic structure 16' is, which
in this case extends over the entire membrane surface of the membrane 12, having a
radius in the rage from 300 µm up to 1000 µm. The intrinsic stress here is 20, 40
MPa, for example. Apart from the absolute dimensions, each auxetic element 16f may
also be defined by edge-to-edge dimensions (the corner points where the respective
concave boundary line contacts the adjacent convex one). In this embodiment, the dimensions
are 30x30 µm, wherein, depending on the design of the auxetic structure 16', these
dimensions may, of course, also be varied as desired, like in a range between 5 µm
and 500 µm. It is to be pointed out here that, depending on the orientation of the
auxetic structural element 16f', the 30 µm may either represent the width or the height.
[0028] Figs. 4a and 4b illustrate another auxetic structure. In a top view, Fig. 4a shows
a 90° section of a membrane 12" (a quarter of a membrane) having an auxetic structure
16". The membrane 12" is cantilevered fixedly at the points characterized by 12f".
Fig. 4b is a detailed three-dimensional illustration of the auxetic structure 16".
[0029] The auxetic structure 16" comprises a plurality of auxetic area elements 16f". Exemplarily,
two auxetic area elements 16f1" and 16f2" are illustrated here. The auxetic area element
16f1" is located in a different plane (in parallel to the entire membrane) than the
area element 16f2" (also in parallel to the entire membrane). Thus, a step 16s" forms
between the two auxetic area elements 16f1" and 16f2". This step 16s" forms the boundary
of the auxetic areas 16f1" and 16f2" and, as has already been mentioned before, is
arranged such that each auxetic area element 16f" is enclosed by two concave and two
convex boundary lines (lateral boundary lines).
[0030] Like in the embodiment having a profile, the step 16s" here is formed by the structure
of the membrane 12" which exemplarily again has a thickness of 0.5 µm (generally in
a range between 0.01 µm and 5.0 µm), wherein the corrugation height (step height)
is 1 µm each (generally in a range between 0.5 µm and 10 µm).
[0031] In accordance with embodiments, in the structure as discussed before, an auxetic
area element 16f1''' in a lower plane will always alternate with an auxetic area element
16f2" in a higher plane. In accordance with further embodiments, it would, of course,
also be conceivable for the auxetic area elements to be provided in more than two
planes. Generally, the different planes form the surface for the membrane 12".
[0032] For the sake of completeness, it is to be mentioned here that the intrinsic stress
(tensile) again is 20, 40 MPa. In Fig. 5a, the intrinsic stress is indicated with
no deformation or before deformation. As can be recognized from the hatchings, the
intrinsic stress is distributed very equally over the steps, when there is no external
deformation (0 Pa). With a deformation (10 Pa), the same extends in a radial-symmetrical
manner from the center of symmetry (cf. zero point in the ¼ membrane models of Figs.
3a and 4a) to the edge. As can be recognized from the hatchings, the stress is distributed
homogenously across the membrane, decreasing towards the radius.
[0033] It is to be pointed out here that a compliance in a range of 9.81 nm/Pa was calculated/simulated
in the auxetic structure of Fig. 3a with an externally applied stress of 20 MPa, whereas,
in the auxetic structure of Fig. 4a, a compliance of 6.98 nm/Pa was obtained. For
comparison, the compliance of a simple membrane is 2.5 nm/Pa
In the above embodiments, it has been assumed that the auxetic structures are applied
on membranes, like silicon membranes for SiMic. In accordance with the embodiments
of Figs. 3a and 3b, these membranes are represented to be round. In accordance with
further embodiments, the membrane may also comprise a different shape, like an oval
or quadrangular shape, for example.
[0034] In the above embodiments, it has been assumed that the lateral boundaries of the
auxetic area elements (cf. reference numbers 16f', 16f1', 16f2' and 16f", 16f1", 16f2")
are formed by 90° segments of a circle (formed by a profile 16s' or step 16s") so
that several 90° segments arranged one behind the other and to be curved alternatingly
in opposite directions extend laterally along a direction and a type of grid is formed
in combination with the several boundary lines. In accordance with further embodiments,
the angles of the segments of a circle or the orientation of the boundary lines set
up by the segments of a circle may also vary (45° angle or, generally, in a range
between 15 and 120°, for example). Expressed differently, this means that using the
auxetic structures in combination with the membrane is not restricted to the auxetic
structures as illustrated, but that further auxetic structures are also conceivable.
With regard to the boundaries, it is to be mentioned that two boundary lines next
to each other meandering along one direction are preferably implemented to be symmetrical
among each other, with an interposed axis of symmetry along the direction of propagation.
[0035] In the above embodiments, it has also been assumed that the auxetic structure extends
over the entire membrane area. However, it is to be pointed out here that, in accordance
with further embodiments, it would also be feasible for the auxetic structure to be
located only in portions on the membrane.
[0036] In the above embodiments, it has always been assumed that the boundaries are formed
by steps or raised profiles, wherein it is to be mentioned here that a deformation
by a trench or a combination of profile and trench would, of course, also be conceivable.
[0037] Another embodiment relates to a manufacturing method of a membrane comprising an
auxetic structure. The membrane is manufactured by means of typical semiconductor
manufacturing methods, like by providing a sacrificial layer and applying the membrane
onto the sacrificial layer before removing the sacrificial layer for exposing the
membrane. In accordance with embodiments, before applying the membrane, a sacrificial
layer is structured, for example in order to implement the trenches or positive profiles
in the membrane. The structuring may also be done such that the auxetic structural
areas arranged in different planes are formed with the respective steps therebetween.
[0038] As has already been mentioned in the above embodiments, a preferred field of application
of membranes comprising auxetic structures is manufacturing MEMS microphones or silicon
microphones, like in smart phones, for example. In particular in such cases of application,
it is of advantage for a membrane comprising an auxetic structure to exhibit a higher
sensitivity than a different (silicon) membrane of comparable size or comparable thickness.
This means that the combination of an auxetic structure with a silicon membrane can
achieve signal amplification for microphones, with, at the same time, higher mechanical
stability.
[0039] Although in above embodiments, the auxetic structural elements have been discussed
as elements having an identical or similar function, the elements may be also different
within a membrane. For example, the shape and orientation of each (at least two) auxetic
structural elements could be rotational symmetric and/or the size can be scaled with
respect to the position inside the membrane.
[0040] The embodiments described above merely represent an illustration of principles of
the present disclosure. Modifications and variations of the arrangements described
herein and details will be obvious for others skilled in the art. Therefore, the disclosure
is intended to be restricted solely by the scope of the following claims, but not
by the specific details having been presented herein using the description and discussion
of embodiments.
1. An MEMS device (10) comprising:
a membrane (12, 12', 12") configured to oscillate and comprising an auxetic structure
(16, 16', 16") at least in portions thereof.
2. The MEMS device (10) according to claim 1, wherein the membrane (12, 12', 12") is
configured to expand, when oscillating, in at least a first lateral direction,
wherein the auxetic structure (16, 16', 16") is configured to expand the membrane
(12, 12', 12") in a second direction as a consequence of the expansion of the membrane
(12, 12', 12") in the first direction, and/or wherein the auxetic structure (16, 16',
16") is configured to increase a thickness of the membrane (12, 12', 12") as a consequence
of the expansion in the first direction.
3. The MEMS device (10) in accordance with any of the preceding claims, wherein the auxetic
structure (16, 16', 16") is formed by a plurality of auxetic structural elements (16f*,
16f', 16f").
4. The MEMS device (10) in accordance with claim 3, wherein each auxetic structural element
(16f*, 16f', 16f") is identical.
5. The MEMS device (10) in accordance with claim 3 or 4, wherein at least three of the
plurality of auxetic structural elements (16f*, 16f', 16f") are arranged in a row
to be mutually adjacent so that a first and a third of the auxetic structural elements
(16f*, 16f', 16f", 16f1') exhibit an identical orientation, wherein a second auxetic
structural element (16f*, 16f', 16f") arranged between the first and third auxetic
structural elements (16f2') is rotated compared to the first and second auxetic structural
elements (16f*, 16f', 16f", 16f2').
6. The MEMS device (10) in accordance with any of claims 3 to 5, wherein each auxetic
structural element (16f*, 16f', 16f") is enclosed by two opposite lateral and two
further opposite lateral boundaries (16fcx*, 16fc, 16fc', 16fcx').
7. The MEMS device (10) in accordance with any of claims 3 to 5, wherein each auxetic
structural element (16f*, 16f', 16f") is enclosed by two opposite lateral concave
and two opposite lateral convex boundaries.
8. The MEMS device (10) in accordance with claim 6 or 7, wherein each lateral boundary
(16fcx*, 16fc, 16fc', 16fcx') is formed by a raised profile (16p') or a trench profile
which borders one of the plurality of auxetic structural elements (16f*, 16f', 16f")
from an adjacent one of the plurality of auxetic structural elements (16f*, 16f',
16f").
9. The MEMS device (10) in accordance with any of claims 6, 7 or 8, wherein the membrane
(12, 12', 12") forms the raised profile (16p') or the trench profile.
10. The MEMS device (10) in accordance with any of claims 3 to 7, wherein the plurality
of auxetic structural elements (16f*, 16f', 16f") each comprise auxetic area elements
(16f', 16f") extending along the membrane plane, and wherein the auxetic area elements
(16f', 16f") of the plurality of auxetic structural elements (16f*, 16f', 16f") are
arranged in at least two different planes.
11. The MEMS device (10) in accordance with any of claims 6, 7 or 10, wherein each lateral
boundary (16fcx*, 16fc, 16fc', 16fcx') is formed by a step (16s") forming a transition
from one auxetic area element (16f', 16f") of one of the plurality of auxetic structural
elements (16f*, 16f', 16f") to an auxetic area element (16f', 16f") of an adjacent
one of the plurality of auxetic structural elements (16f*, 16f', 16f").
12. The MEMS device (10) in accordance with claim 11, wherein the step (16s") is formed
by the membrane (12, 12', 12").
13. A sound transducer comprising an MEMS device (10) in accordance with any of the preceding
claims.
14. The sound transducer in accordance with claim 13, the sound transducer forming a microphone
configured to output, when excited to oscillate by sound from the surroundings, an
electrical signal which is dependent on the sound.
15. A method for manufacturing an MEMS device (10) in accordance with any of claims 1
to 12, the method comprising the step of:
forming a membrane (12, 12', 12") by means of depositing, depositing taking place
such that the auxetic structure (16, 16', 16") is formed in the membrane (12, 12',
12").