TECHNICAL FIELD
[0001] The present invention relates to an induction heating apparatus.
BACKGROUND ART
[0002] Conventional induction heating apparatuses include a first heating coil provided
on an inner circumference side of a single heating port and a second heating coil
provided more on an outer circumference side than the first heating coil. An inverter
circuit that supplies AC currents to the first heating coil and the second heating
coil includes three arm circuits each having two switching elements connected in series
(see, for example, Patent Document 1).
[0003] The three arm circuits are a first arm circuit, a second arm circuit, and a common
arm circuit. The first heating coil is connected between the first arm circuit and
the common arm circuit. The second heating coil is connected between the second arm
circuit and the common arm circuit. The first heating coil and the second heating
coil are each connected in series with a variable capacitor the capacitance of which
can be changed by opening/closing a switch. Switching between opening and closing
the switch has been performed based on whether the heated object placed on the heating
port is made of magnetic metal or nonmagnetic metal.
[0004] The first arm circuit, the second arm circuit, and the common arm circuit are switched
at the same frequency so that AC currents at the same frequency are supplied to the
first heating coil and the second heating coil to inductively heat the heated object.
In a case that the heated object is made of nonmagnetic metal, the switching frequency
of each arm circuit is set to be higher so that AC current at a higher frequency is
supplied to the first heating coil and the second heating coil, compared with a case
that the heated object is made of magnetic metal.
[0005] Inductive heating of a heated object with alternating fluxes at a higher frequency
involves smaller skin depth for making eddy current flow in the heated object by skin
effect, resulting in high electrical resistance in a path in which the eddy current
flows. As a result, even a heated object made of nonmagnetic metal can be inductively
heated efficiently.
PRIOR ART DOCUMENT
PATENT DOCUMENT
SUMMARY OF THE INVENTION
PROBLEMS TO BE SOLVED BY THE INVENTION
[0007] However, the conventional induction heating apparatus described in Patent Document
1 is unable to efficiently inductively heat a heated object made of different materials
formed by joining magnetic metal to the inner circumference side of a bottom section
of the heated object made of nonmagnetic metal, due to the magnetic metal being positioned
on the first heating coil and the nonmagnetic metal being positioned on the second
heating coil. Specifically, the conventional induction heating apparatus supplies
AC currents at the same frequency to the first heating coil and the second heating
coil.
[0008] Thus, when the AC currents are set to be at a frequency suitable for inductively
heating magnetic metal, the inductive heating would be insufficient for the nonmagnetic
metal on the outer circumference side. When the AC currents are set to be at a frequency
suitable for inductively heating nonmagnetic metal, the frequency would be excessively
high for inductively heating the magnetic metal on the inner circumference side. Thus,
the efficiency of inductive heating for the magnetic metal is compromised.
[0009] The present invention has been made to solve the problem described above, and an
object of the present invention is to provide an induction heating apparatus that
can supply AC currents at different frequencies to a first heating coil and a second
heating coil, even when the first heating coil and the second heating coil share a
common arm circuit.
MEANS FOR SOLVING THE PROBLEMS
[0010] An induction heating apparatus according to the present invention includes:
an inverter circuit including a plurality of arm circuits including a first arm circuit,
a second arm circuit, and a common arm circuit each including a first switching element,
a second switching element connected in series with the first switching element, and
an output terminal provided between the first switching element and the second switching
element; a first heating coil electrically connected between the output terminal of
the first arm circuit and the output terminal of the common arm circuit; and a second
heating coil electrically connected between the output terminal of the second arm
circuit and the output terminal of the common arm circuit
[0011] The inverter circuit is configured to switch the first switching element of the common
arm circuit at a predetermined frequency, in a case that AC current at a first frequency
is supplied to the first heating coil, and switch the first switching element of the
common arm circuit at a frequency that is same as the frequency in the case that the
AC current at the first frequency is supplied to the first heating coil, also in a
case that AC current at a second frequency different from the first frequency is supplied
to the second heating coil.
EFFECTS OF THE INVENTION
[0012] With an induction heating apparatus according to the present invention, AC currents
at different frequencies can be supplied to a first heating coil and a second heating
coil, even when the first heating coil and the second heating coil share a common
arm circuit.
BRIEF DESCRIPTION OF THE DRAWINGS
[0013]
- FIG. 1
- is a perspective view of an induction heating apparatus according to a first embodiment
of the present invention.
- FIG. 2
- is a plan view illustrating heating coils according to the first embodiment of the
present invention.
- FIG. 3
- is a circuit diagram illustrating a configuration of an electric circuit of the induction
heating apparatus according to the first embodiment of the present invention.
- FIG. 4
- is a cross-sectional view illustrating cases where a heated object made of a single
material and where a heated object made of different materials are placed on a top
plate of the induction heating apparatus according to the first embodiment of the
present invention.
- FIG. 5
- is a perspective view illustrating a state where the induction heating apparatus according
to the first embodiment of the present invention inductively heats a heated object
made of a single material.
- FIG. 6
- is a perspective view illustrating a state where the induction heating apparatus according
to the first embodiment of the present invention inductively heats a heated object
made of different materials.
- FIG. 7
- illustrates an example of a driving condition for inductively heating the heated object
made of different materials by the induction heating apparatus according to the first
embodiment of the present invention.
- FIG. 8
- is a time chart illustrating gate signals for each switching element forming an inverter
circuit of the induction heating apparatus according to the first embodiment of the
present invention, as well as waveforms of voltage and current output from the inverter
circuit.
- FIG. 9
- is a time chart illustrating gate signals for each switching element forming an inverter
circuit of an induction heating apparatus according to a second embodiment of the
present invention, as well as waveforms of voltage and current output from the inverter
circuit.
- FIG. 10
- is a time chart illustrating gate signals for each switching element forming an inverter
circuit of an induction heating apparatus according to a third embodiment of the present
invention, as well as waveforms of voltage and current output from the inverter circuit.
- FIG. 11
- is a time chart illustrating gate signals for each switching element forming an inverter
circuit of an induction heating apparatus according to a fourth embodiment of the
present invention, as well as waveforms of voltage and current output from the inverter
circuit.
- FIG. 12
- is a time chart illustrating gate signals for each switching element forming an inverter
circuit of an induction heating apparatus according to a fifth embodiment of the present
invention, as well as waveforms of voltage and current output from the inverter circuit.
- FIG. 13
- is a plan view illustrating a position of a heated object placed on a heating coil
to be inductively heated by an induction heating apparatus according to a sixth embodiment
of the present invention.
- FIG. 14
- is a perspective view illustrating a state where an induction heating apparatus according
to a seventh embodiment of the present invention inductively heats two heated objects.
EMBODIMENTS OF THE INVENTION
First Embodiment
[0014] First of all, a configuration of an induction heating apparatus according to a first
embodiment of the present invention will be described. FIG. 1 is a perspective view
of the induction heating apparatus according to the first embodiment of the present
invention.
[0015] In FIG. 1, an induction heating apparatus 100 has an outer form defined by a casing
1 and a top plate 2 provided at an upper portion of the casing 1. The top plate 2
includes an insulating material such as glass, ceramics, or resin, and a heated object
such as pots and frying pans to be inductively heated by the induction heating apparatus
100 is placed on a region of the top plate 2 including the insulating material. The
top plate 2 has placement positions 3a, 3b, and 3c displayed to indicate positions
on the top plate 2 where the heated object is to be placed. When the top plate 2 is
made of a transparent material such as glass, the placement positions 3a, 3b, and
3c may be displayed by printing or the like on a back surface opposite to the front
surface of the top plate 2 serving as a placement surface.
[0016] The placement positions 3a, 3b, and 3c may be implemented by light emitting elements
such as light emitting diodes and a light guiding member provided on the back surface
side of the top plate 2 that enable visual recognition of the positions where the
heated object is to be placed, from the front surface side of the top plate 2. The
placement positions 3a, 3b, and 3c are illustrated as regions in which the heated
object is to be placed in FIG. 1. Alternatively, the placement positions 3a, 3b, and
3c may also be implemented as points each indicating the center of the position where
the heated object is to be placed. The induction heating apparatus 100 inductively
heats the heated object placed on the placement positions 3a, 3b, and 3c, and thus
the placement positions 3a, 3b, and 3c may each be referred to as a heating port.
[0017] The induction heating apparatus 100 includes a grill section 4 with an opening/closing
door that can be pulled toward the forward surface side of the casing 1 to be opened.
The grill section 4 has a heating chamber with a rectangular parallelepiped internal
space provided with a heating unit such as a heater. For example, the grill section
4 is used for grill cooking and the like for grilled fish and the like. The grill
section 4 is not necessarily required, and the induction heating apparatus 100 may
have a configuration without the grill section 4.
[0018] The induction heating apparatus 100 includes an operation unit 5a provided on a forward
side of the top plate 2 and operation units 5b and 5c provided on the front surface
of the casing 1. The operation units 5a, 5b, and 5c are used for starting /stopping
heating or adjusting heating power when a heated object placed on the placement position
3a, 3b, or 3c is inductively heated, and for starting /stopping heating or adjusting
heating power when the grill section 4 is used for the heating. The positions where
the operation units 5a, 5b, and 5c are provided are not limited to those illustrated
in FIG. 1, and may be any positions enabling a user of the induction heating apparatus
100 to easily operate the induction heating apparatus 100.
[0019] A display unit 6 that displays a status of the induction heating apparatus 100 is
provided on the forward side of the top plate 2. The display unit 6 may be a display
device such as a liquid crystal display or an organic electroluminescence (EL) display
for example. The position where the display unit 6 is provided may be any position
that can be easily visually recognized by the user of the induction heating apparatus
100, and thus is not limited to the forward side of the top plate 2. For example,
the display unit 6 may be provided on the front surface of the casing 1. The display
unit 6 displays various types of information in accordance with an operation status
of the induction heating apparatus 100. For example, power input to each heating port
and relative magnitudes of the power may be displayed, or the temperature of the bottom
surface of the heated object placed on each heating port may be displayed. The display
unit 6 may be implemented by a display device with a touch panel, so that the display
unit 6 and the operation unit can be integrally formed.
[0020] Discharge ports 7a, 7b, and 7c are provided on a rear side of the top plate 2. The
discharge ports 7a, 7b, and 7c are for discharging, to the outside of the induction
heating apparatus 100, heat generated by the grill section 4, an electrical circuit
(not illustrated), a heating coil (not illustrated), and the like in the induction
heating apparatus 100, oily smoke generated as a result of cooking in the grill section
4, and the like. The discharge ports 7a, 7b, and 7c provided on the top plate 2 in
FIG. 1 may alternatively be provided on the casing 1. The number of the discharge
ports is not limited to three, and may be any number that is equal to or larger than
1. The induction heating apparatus 100 without the grill section 4 may have a configuration
for emitting heat from the front surface of the casing 1 with the discharge ports
omitted for example.
[0021] The induction heating apparatus 100 incorporates heating coils for inductively heating
a heated object, such as a pot, placed on the top plate 2 and an electric circuit
for supplying high frequency current to the heating coils. The heating coils are provided
on the back surface side of the top plate 2 while facing the respective placement
positions 3a, 3b, and 3c displayed on the top plate 2. The heating coil may be formed
by winding a coated lead wire into a form of a spiral for example. More preferably,
a Litz wire formed by twisting a plurality of coated thin wires (thin wires made of
highly conductive metal such a copper is coated) is used as the lead wire forming
the heating coil, so that increase in electric resistance of the heating coil at high
frequencies such as 20 kHz to 100 kHz can be suppressed. A single heating coil includes
two terminals connected to the electric circuit. Thus, a single heating coil is a
two-terminal circuit part having both ends. If necessary, the heating coil may have
a magnetic body such as a ferrite core provided on a surface opposite to the surface
facing the heated object.
[0022] FIG. 2 is a plan view illustrating heating coils according to the first embodiment
of the present invention. FIGS. 2(a) to 2(d) each illustrate an example of the heating
coil provided inside the induction heating apparatus 100. Thus, the induction heating
apparatus 100 according to the present invention may include a heating coil with a
shape different from those illustrated in FIGS. 2(a) to 2(d). In this description,
the induction heating apparatus 100 illustrated in FIG. 1 has any one of heating coils
illustrated in FIGS. 2(a) to 2(d) provided on the back surface side of the top plate
2 to face the placement region 3a, 3b, and 3c.
[0023] Heating coils with different shapes may be provided to face the respective placement
regions 3a, 3b, and 3c. For example, a heating coil 30c illustrated in FIG. 2(c) may
be provided to face the placement region 3a, a heating coil 30b illustrated in FIG.
2(b) may be provided to face the placement region 3b, and a heating coil 30a illustrated
in FIG. 2(a) may be provided to face the placement region 3c.
[0024] The heating coil 30a illustrated in FIG. 2(a) includes a heating coil 31 that is
obtained by winding a lead wire into a ring shape and a heating coil 32 that is obtained
by winding a lead wire into a ring shape and is arranged adjacent to the heating coil
31. The heating coil 32 is arranged around and apart from the heating coil 31. The
heating coil 31 and the heating coil 32 each have terminals, connected to the electric
circuit, at both ends of the lead wire, and each individually serve as the heating
coil. The heating coil 32 is provided to surround the heating coil 31, so that when
the heated object is placed on the heating coil 30, the heating coil 31 inductively
heats the inner circumference side region of the heated object and the heating coil
32 heats the outer circumference side region of the heated object.
[0025] In FIG. 2(a), the heating coil 31 may be referred to as a first heating coil and
the heating coil 32 may be referred to as a second heating coil. Alternatively, these
names (the first heating coil and the second heating coil) may be interchanged so
that the heating coil 32 is referred to as the first heating coil and the heating
coil 31 is referred to as the second heating coil. Although not elaborated in the
description below, the names, that is, the first heating coil and the second heating
coil, may be interchangeably used in the present invention. Specifically, one of a
plurality of heating coils is the first heating coil and one of the plurality of heating
coils excluding the first heating coil is the second heating coil. The first heating
coil and the second heating coil are provided on the back surface side of the top
plate 2 to face the back surface of the top plate 2.
[0026] The heating coil 30b illustrated in FIG. 2(b) includes a heating coil 31a, a heating
coil 31b, and the heating coil 32 that are each formed by winding a lead wire into
a ring form. The heating coil 31a and the heating coil 31b are arranged adjacent to
and apart from each other. The heating coil 31b and the heating coil 32 are arranged
adjacent to and apart from each other. The heating coil 31a, the heating coil 31b,
and the heating coil 32 may each be an individual heating coil having terminals at
both ends of the lead wire. Alternatively, the heating coil 31a and the heating coil
31b may be formed of a continuous lead wire to serve as a single heating coil, for
example. Thus, the first heating coil may include the heating coil 31a and the heating
coil 31b, and the second heating coil may include the heating coil 32.
[0027] The heating coil 30c illustrated in FIG. 2(c) includes a heating coil 31a, a heating
coil 31b, a heating coil 32a, a heating coil 32b, a heating coil 32c, and a heating
coil 32d that are each formed by winding a lead wire into a ring form. As in the case
illustrated in FIG. 2(b), the heating coil 31a and the heating coil 31b may each be
an individual heating coil, or the heating coil 31a and the heating coil 31b may form
a single heating coil. The heating coil 32a, the heating coil 32b, the heating coil
32c, and the heating coil 32d may each also be an individual heating coil, or the
heating coil 32a and the heating coil 32c may be connected to each other to form a
single heating coil and the heating coil 32b and the heating coil 32d may be connected
to each other to form another single heating coil for example. Thus, the first heating
coil may include the heating coil 31a and the heating coil 31b, and the second heating
coil may include the heating coil 32a and the heating coil 32c.
[0028] The heating coil 30d illustrated in FIG. 2(d) includes a heating coil 31a, a heating
coil 32a, a heating coil 32b, a heating coil 32c, a heating coil 32d, a heating coil
32e, a heating coil 32f, a heating coil 32g, and a heating coil 32h that are each
formed by winding a lead wire into a ring form. As in the case illustrated in FIG.
2(c), the heating coils 31a to 31h may each be an individual heating coil, or some
of the heating coils 31a to 31h may be connected to form a single heating coil. For
example, the first heating coil may include the heating coil 32, and the second heating
coil may include the heating coil 32a.
[0029] The first heating coil may include the heating coil 31, the heating coil 32a, the
heating coil 32b, and the heating coil 32h, and the second heating coil may include
the heating coil 32c, the heating coil 32d, the heating coil 32e, and the heating
coil 32g. A switch such as a relay or a semiconductor switching element may be used
to switch between the connections among the plurality of heating coils, so that one
set of the heating coils serves as the first heating coil and another set of the heating
coils serves as the second heating coil, in accordance with what or how to be cooked.
[0030] FIG. 3 is a circuit diagram illustrating a configuration of an electric circuit of
the induction heating apparatus according to the first embodiment of the present invention.
As illustrated in FIG. 3, an electric circuit 8 of the induction heating apparatus
100 includes an inverter circuit 81, a power supply unit 82, a choke coil 83, a DC
part 84, and a control circuit 85. As described above, the electric circuit 8 is provided
in the internal of the induction heating apparatus 100, defined by the casing 1 and
the top plate 2.
[0031] The power supply unit 82 includes a power fuse 12, an input capacitor 13, and a diode
bridge 14. The input capacitor 13 is connected in parallel with an AC side terminal
of the diode bridge 14, and an AC power source 9 that is an external power source
is connected in parallel with the input capacitor 13. The input capacitor 13 functions
as a filter. The AC power source 9 is what is known as a commercial power supply.
The power fuse 12 is provided between the AC power source 9 and the input capacitor
13 to prevent overcurrent from flowing to the induction heating apparatus 100 from
the AC power source 9. The diode bridge 14 rectifies AC power, input to the AC side
terminal, into DC power and outputs the DC power from a DC side terminal of the diode
bridge 14. The power supply unit 82 may have a load detection unit 11 provided at
an input/output terminal, to which the AC power source 9 is connected, to detect a
current value of the input current for detecting a material of the heated object.
The load detection unit 11 will be described more in detail later.
[0032] As illustrated in FIG. 3, the DC part 84 is connected in parallel with the DC side
terminal of the diode bridge 14 through the choke coil 83. For example, the DC part
84 may be a capacitor. When the DC part 84 is a capacitor, the choke coil 83 and the
capacitor forming the DC part 84 may form a filter. The DC part 84 may be formed of
a DC/DC converter such as a step-up chopper, a step-down chopper, or a step-down and
-up chopper, and may be configured to change the voltage value of the DC voltage input
to the inverter circuit 81. The DC part 84 may be a power factor correction converter
for improving the power factor of the AC power input from the AC power source 9.
[0033] When the DC part 84 is a capacitor, the inverter circuit 81 receives pulsating DC
voltage with a voltage value periodically varying, obtained by full wave rectification
of the AC voltage. When the DC part 84 is a DC/DC converter, the inverter circuit
81 receives DC voltage of a substantially constant voltage value. The following description
assumes that DC voltage of a constant voltage value is input to the inverter circuit
81, but the content of the description similarly applies to a case that pulsating
DC voltage is input to the inverter circuit 81.
[0034] As illustrated in FIG. 3, the inverter circuit 81 is connected in parallel with the
DC part 84. The inverter circuit 81 includes a first arm circuit 21, a second arm
circuit 27, and a common arm circuit 24 that are connected in parallel with each other.
Each of the arm circuits is formed by connecting two switching elements, such as an
Insulated Gate Bipolar Transistor (IGBT) and/or a Metal-Oxide-Semiconductor Field-Effect-Transistor
(MOSFET), in series, with an output terminal provided between the two switching elements.
[0035] The first arm circuit 21 includes a first switching element 21a that is electrically
connected to a high voltage side of the DC part 84, a second switching element 21b
that is connected in series with the first switching element 21a and is connected
to a low voltage side of the DC part 84, and an output terminal 23 provided between
the first switching element 21a and the second switching element 21b. A diode 22a
is connected in anti-parallel with the first switching element 21a and a diode 22b
is connected in anti-parallel with the second switching element 21b. When the first
switching element 21a and the second switching element 21b are MOSFETs, the elements
include a body diode and thus may not necessarily include the diode 22a and the diode
22b. A gate signal H1 is input to a gate terminal of the first switching element 21a,
and the first switching element 21a is controlled based on the gate signal H1 to turn
ON or OFF. Similarly, a gate signal L1 is input to a gate terminal of the second switching
element 21b, and the second switching element 21b is controlled based on the gate
signal L1 to turn ON or OFF.
[0036] The second arm circuit 27 includes a first switching element 27a that is electrically
connected to a high voltage side of the DC part 84, a second switching element 27b
that is connected in series with the first switching element 27a and is connected
to a low voltage side of the DC part 84, and an output terminal 29 provided between
the first switching element 27a and the second switching element 27b. A diode 28a
is connected in anti-parallel with the first switching element 27a and a diode 28b
is connected in anti-parallel with the second switching element 27b. A gate signal
H7 is input to a gate terminal of the first switching element 27a, and the first switching
element 27a is controlled based on the gate signal H7 to turn ON or OFF. A gate signal
L7 is input to a gate terminal of the second switching element 27b, and the second
switching element 27b is controlled based on the gate signal L7 to turn ON or OFF.
[0037] The common arm circuit 24 includes a first switching element 24a that is electrically
connected to a high voltage side of the DC part 84, a second switching element 24b
that is connected in series with the first switching element 24a and is connected
to a low voltage side of the DC part 84, and an output terminal 26 provided between
the first switching element 24a and the second switching element 24b. A diode 25a
is connected in anti-parallel with the first switching element 24a and a diode 25b
is connected in anti-parallel with the second switching element 24b. A gate signal
H4 is input to a gate terminal of the first switching element 24a, and the first switching
element 24a is controlled based on the gate signal H4 to turn ON or OFF. Similarly,
a gate signal L4 is input to a gate terminal of the second switching element 24b,
and the second switching element 24b is controlled based on the gate signal L4 to
turn ON or OFF.
[0038] Although FIG. 3 illustrates the configuration with the inverter circuit 81 including
three arm circuits, a configuration with an inverter circuit including four or more
arm circuits with one or a plurality of the arm circuits serving as the common arm
circuit may be employed. Each of the switching elements forming each arm circuit may
be formed of a discrete semiconductor switching element, and may be formed of a power
semiconductor module such as an Intelligent Power Module (IPM) with a plurality of
semiconductor elements incorporated in a single package.
[0039] The power semiconductor module incorporating three arm circuits is widely used for
inverter devices for driving three-phase AC motors, and thus can be used for implementing
the inverter circuit 81 of the induction heating apparatus 100 at a low cost. Each
arm circuit may have a configuration in which a snubber circuit, including a capacitor
and a resistor, is connected in parallel with a switching element so that surge voltage
applied to the switching element can be suppressed.
[0040] The first arm circuit 21 and the common arm circuit 24 form a first full bridge circuit,
and the second arm circuit 27 and the common arm circuit 24 form a second full bridge
circuit. The first heating coil 31 is electrically connected between the output terminal
23 of the first arm circuit 21 and the output terminal 26 of the common arm circuit
24. The second heating coil 32 is electrically connected between the output terminal
29 of the second arm circuit 27 and the output terminal 26 of the common arm circuit
24. A first variable capacitor 41 is connected in series with the first heating coil
31, and a first resonant circuit, including the first heating coil 31 and the first
variable capacitor 41, is connected between the output terminal 23 of the first arm
circuit 21 and the output terminal 26 of the common arm circuit 24.
[0041] A second variable capacitor 45 is connected in series with the second heating coil
32, and a second resonant circuit, including the second heating coil 32 and the second
variable capacitor 45, is connected between the output terminal 29 of the second arm
circuit 27 and the output terminal 26 of the common arm circuit 24. In the present
invention, the first heating coil 31, the second heating coil 32, the first variable
capacitor 41, and the second variable capacitor 45 are not treated as elements of
the inverter circuit 81.
[0042] The first variable capacitor 41 is a capacitor whose capacitance can be changed.
For example, as illustrated in FIG. 3, the first variable capacitor 41 may be implemented
by connecting the capacitor 42 in parallel with a part where the capacitor 43 and
the switch 44 are connected in series. Alternatively, the first variable capacitor
41 may be implemented by connecting the part where the capacitor and the switch are
connected in parallel with another capacitor. The number of capacitors and switches
used for the first variable capacitor 41 can be set as appropriate, and the number
of serial and/or parallel connections may be set as appropriate. The switch may be
a relay or a semiconductor switching element for example. The second variable capacitor
45 is similar to the first variable capacitor 41. The second variable capacitor 45
is formed by connecting the capacitor 46 in parallel with a part where the capacitor
47 and the switch 48 are connected in series. The switch 44 of the first variable
capacitor 41 and the switch 48 of the second variable capacitor 45 are controlled
to be opened or closed by a control signal from the control circuit 85.
[0043] The control circuit 85 outputs a control signal for performing switching control
on the first switching elements 21a, 24a, and 27a and the second switching elements
21b, 24b, and 27b of the arm circuits of the inverter circuit 81, and for performing
open/close control on the switch 44 of the first variable capacitor 41 and the switch
48 of the second variable capacitor 45. In FIG. 3, a signal line connecting the control
circuit 85 with the gate terminal of each switching element and a signal line connecting
the control circuit 85 with the switches 44 and 48 are omitted.
[0044] The control circuit 85 is connected to the load detection unit 11 through a signal
line, and receives a signal from the load detection unit 11. The control circuit 85
is connected to the operation unit 5 and the display unit 6 through signal lines,
and transmits and receives signals, such as an operation signal and a display signal,
to and from the operation unit 5 and the display unit 6. The operation unit 5 is the
operation units 5a, 5b, and 5c illustrated in FIG. 1, and the display unit 6 is the
display unit 6 illustrated in FIG. 1.
[0045] When the DC part 84 is a DC/DC converter, the control circuit 85 may perform switching
control on a switching element in the DC/DC converter. The control circuit 85 may
be implemented by an integrated circuit including an analog circuit and a digital
circuit, or may be implemented by a processing unit such as a microcomputer. Furthermore,
a gate driving circuit for driving each switching element, and a protection circuit
may be provided if necessary.
[0046] The load detection unit 11 determines a material of the heated object placed on the
first heating coil 31 and the second heating coil 32. Impedance measured at both ends
of each heating coil differs between a case that the heated object is magnetic metal
such as iron and a case that the heated object is a nonmagnetic material such as aluminum
and copper. Thus, the material of the heated object placed on the first heating coil
31 or the second heating coil 32 is determined based on this difference in impedance.
As the impedance, a change in resistance may be used for determining the material
of the heated object, or a change in inductance may be used for determining the material
of the heated object. The position where the load detection unit 11 is provided is
not limited to the position illustrated in FIG. 3, and a first load detection unit
may be provided in series with the first heating coil 31, and a second load detection
unit may be provided in series with the second heating coil 32, for example.
[0047] When the load detection unit 11 is provided to the input terminal of the induction
heating apparatus 100 as illustrated in FIG. 3, the control circuit 85 controls the
first arm circuit 21 and the common arm circuit 24 to supply pulsating current to
the first heating coil 31. Subsequently, the control circuit 85 controls the second
arm circuit 27 and the common arm circuit 24 to supply pulsating current to the second
heating coil 32. Then, based on a change in the input current measured by the load
detection unit 11 during this process, the change in the impedance of the first heating
coil 31 and the second heating coil 32 is detected for determining the material of
the heated object.
[0048] When the second heating coil 32 is arranged to surround the first heating coil 31
as illustrated in FIG. 2(a), the material of the heated object on the inner circumference
side is determined based on the determination result at the first heating coil 31
and the material of the heated object on the outer circumference side is determined
based on the determination result at the second heating coil 32.
[0049] The load detection unit 11 may be provided separately from the control circuit 85
as illustrated in FIG. 3, but may also be integrated with the control circuit 85.
Specifically, a current detector and/or a voltage detector may only be provided to
the input terminal of the induction heating apparatus 100 and input a detected current
value and/or voltage value to the control circuit 85, so that the material of the
heated object is determined based on calculation using the current value and/or voltage
value in the control circuit 85. Thus, the control circuit 85 may have a function
of the load detection unit to serve as the load detection unit.
[0050] The control circuit 85 may serve as the load detection unit similarly in a case that
the control circuit 85 determines the material of the heated object based on a current
value and/or voltage value of the heating coil with the current detector and/or the
voltage detector provided between the output terminal of the arm circuit and the heating
coil.
[0051] Next, an operation of the induction heating apparatus 100 according to the present
invention will be described.
[0052] FIG. 4 is a cross-sectional view illustrating cases where a heated object made of
a single material and where a heated object made of different materials are placed
on the top plate of the induction heating apparatus according to the first embodiment
of the present invention. FIG. 4(a) is a cross-sectional view illustrating a case
that a heated object 110a made of a single material is placed on the top plate 2,
and FIG. 4(b) is a cross-sectional view illustrating a case that a heated object 110b
made of different materials are placed on the top plate 2.
[0053] In the present invention, the heated object 110a with a bottom section 111 made of
a single metal material as illustrated in FIG. 4(a) represents the heated object made
of a single material. The single metal material is magnetic metal such as iron and
ferritic stainless steel or a nonmagnetic metal such as aluminum, copper, and austenitic
stainless steel, and does not mean metal made up of a single element. Thus, the heated
object 110a with the bottom section made of a single alloy such as stainless steel
is the heated object made of a single material.
[0054] On the other hand, the heated object 110b implemented with a magnetic metal section
112, made of metal different from the material of the bottom section 111, joined to
the bottom section 111 as illustrated in FIG. 4(b) represents the heated object made
of different materials. The heated object 110b made of different materials is formed
with an easily inductively heated magnetic metal such as iron and ferritic stainless
steel joined (by attaching and/or coating) to a bottom surface of a pot formed of
a nonmagnetic metal with a low electrical resistance such as aluminum and copper,
for example. The heated object 110b made of different materials can be mainly made
of aluminum, and thus is widely used for the sake of lower cost, lighter weight, and
higher thermal conduction of the heated object 110b.
[0055] As illustrated in FIG. 4(b), the heated object 110b made of different materials usually
has the magnetic metal section 112 provided on the inner circumference side of the
bottom surface of the heated object 110b. Thus, the magnetic metal section 112 is
placed on the first heating coil 31 arranged on the inner circumference side of the
heating port, and the bottom section 111 made of a nonmagnetic metal is placed on
the second heating coil 32 arranged on the outer circumference side of the heating
port.
[0056] FIG. 5 is a perspective view illustrating a state where the induction heating apparatus
according to the first embodiment of the present invention inductively heats a heated
object made of a single material. Note that a distance between the heating coil 30
and the back surface of the top plate 2, which is illustrated to be quite large in
FIG. 5, is about 1 to 10 mm, and thus the heating coil 30 is actually arranged closer
to the back surface of the top plate 2 compared with the state illustrated in FIG.
5, while facing the placement position 3.
[0057] As illustrated in FIG. 5, the heated object 110a, such as a pot or a frying pan,
inductively heated by the induction heating apparatus 100, is placed with the bottom
surface of the heated object 110a positioned on the placement position 3 displayed
on the top plate 2. The bottom surface of the heated object 110a may not be entirely
arranged on the placement position 3, but when the bottom surface of the heated object
110a is not arranged on the placement position 3 at all, the induction heating apparatus
100 determines that no heated object is placed and thus no AC current is supplied
to the heating coil 30.
[0058] When the heated object 110a is placed on the placement position 3 of the top plate
2 as illustrated in FIG. 5 and a user of the induction heating apparatus 100 operates
the operation unit 5 to select an operation of inductively heating the heated object
110a, the control circuit 85 controls the inverter circuit 81 to supply pulsating
current to the heating coil 31 and the heating coil 32.
[0059] For example, first of all, the control circuit 85 outputs a gate signal H1 for turning
ON the first switching element 21a of the first arm circuit 21 of the inverter circuit
81, a gate signal L1 for turning OFF the second switching element 21b, a gate signal
H4 for turning OFF the first switching element 24a of the common arm circuit 24, and
a gate signal L4 for turning ON the second switching element 24b. As a result, current
flows through the first heating coil 31. Then, the control circuit 85 outputs a gate
signal H1 for turning OFF the first switching element 21a of the first arm circuit
21 and a gate signal L1 for turning ON the second switching element 21b, so that the
current stops flowing through the first heating coil 31.
[0060] Next, the control circuit 85 outputs a gate signal H7 to turn ON the first switching
element 27a of the second arm circuit 27 of the inverter circuit 81, a gate signal
L7 for turning OFF the second switching element 27b, a gate signal H4 for turning
OFF the first switching element 24a of the common arm circuit 24, and a gate signal
L4 for turning ON the second switching element 24b. As a result, current flows through
the second heating coil 32. Then, the control circuit 85 outputs a gate signal H7
for turning OFF the first switching element 27a of the second arm circuit 27 and a
gate signal L7 for turning ON the second switching element 27b, so that the current
stops flowing through the second heating coil 32.
[0061] In this process, the load detection unit 11 detects an increase in the input current
to the induction heating apparatus 100 due to the current flowing through the first
heating coil 31 and the second heating coil 32. When the load detection unit is connected
in series with each of the first heating coil 31 and the second heating coil 32, the
load detection unit directly detects the current flowing through the first heating
coil 31 and the second heating coil 32. The load detection unit 11 determines the
material of the heated object 110a placed on the first heating coil 31 and the material
of the heated object 110a placed on the second heating coil 32, based on the current
detected.
[0062] When the load detection unit 11 determines that the material of the heated object
110a on the first heating coil 31 is magnetic metal such as iron, the control circuit
85 closes the switch 44 of the first variable capacitor 41 so that the capacitor 42
and the capacitor 43 are connected in parallel with each other. As a result, the capacitance
of the first variable capacitor 41 increases so that the resonant frequency of the
first resonant circuit including the first heating coil 31 and the first variable
capacitor 41 decreases. On the other hand, when the load detection unit 11 determines
that the material of the heated object 110a on the first heating coil 31 is nonmagnetic
metal such as aluminum or copper, the control circuit 85 opens the switch 44 of the
first variable capacitor 41 so that the capacitor 43 is disconnected from the capacitor
42.
[0063] As a result, the capacitance of the first variable capacitor 41 decreases, so that
the resonant frequency of the first resonant circuit including the first heating coil
31 and the first variable capacitor 41 increases. In this manner, the capacitance
of the first variable capacitor 41 is changed in accordance with the material of the
heated object on the first heating coil 31 determined by the load detection unit 11.
Similarly, the capacitance of the second variable capacitor 45 is changed in accordance
with the material of the heated object on the second heating coil 32 determined by
the load detection unit 11.
[0064] In FIG. 5, the heated object 110a is made of a single material, and thus the load
detection unit 11 determines that the material of the heated object 110a on the first
heating coil 31 is the same as the material of the heated object 110a on the second
heating coil 32. Thus, the inverter circuit 81 supplies the AC current at the same
frequency to the first heating coil 31 and to the second heating coil 32. Thus, the
first switching element 21a of the first arm circuit 21 of the inverter circuit 81,
the first switching element 27a of the second arm circuit 27, and the first switching
element 24a of the common arm circuit 24 are switched at the same frequency. The second
switching elements of the arm circuits are also switched at the same frequency.
[0065] An operation in the case that the heated object is made of different materials can
be performed also in the case that the heated object is made of a single material,
without hindering the inductive heating for the heating object. Thus, even when the
material of the heated object on the first heating coil and the material of the heated
object on the second heating coil are the same, the frequency of the current flowing
through the first heating coil 31 and the frequency of the current flowing through
the second heating coil 32 may be set to be different from each other. The AC current
supplied to the first heating coil and the AC current supplied to the second heating
coil from the inverter circuit may be at different frequencies.
[0066] Next, the operation in the case that the heated object is made of different materials
will be described.
[0067] FIG. 6 is a perspective view illustrating a state where the induction heating apparatus
according to the first embodiment of the present invention inductively heats a heated
object made of different materials. FIG. 6 is the same as FIG. 5 except that the heated
object 110b is made of different materials, and thus the description on the same parts
will be omitted.
[0068] The heated object 110b made of different materials will be described as an object
formed by joining the magnetic metal section 112 made of magnetic metal such as iron
on the inner circumference side of the bottom section 111 made of a nonmagnetic metal
such as aluminum. Alternatively, the heated object made of different materials may
be formed by joining the nonmagnetic metal section on the inner circumference side
of the bottom section of the heated object made of magnetic metal. In this case, the
first heating coil 31 that inductively heats the nonmagnetic metal section on the
inner circumference side may be supplied with AC current at a higher frequency than
that supplied to the second heating coil 32 that inductively heats the magnetic metal
section on the outer circumference side.
[0069] When the heated object 110b is placed on the placement position 3 of the top plate
2 and the load detection unit 11 completes the determination of the material of the
heated object 110b, the control circuit 85 performs open/close control on the switch
44 of the first variable capacitor 41 and the switch 48 of the second variable capacitor
45. The load detection unit 11 determines that the material of the heated object 110b
on the first heating coil 31 is magnetic metal, and thus the switch 44 of the first
variable capacitor 41 is closed. As a result, in the first variable capacitor 41,
the capacitor 42 and the capacitor 43 are connected in parallel with each other, resulting
in a large capacitance. On the other hand, the load detection unit 11 determines that
the material of the heated object 110b on the second heating coil 32 is nonmagnetic
metal, and thus the switch 48 of the second variable capacitor 45 is opened. As a
result, in the second variable capacitor 45, the capacitor 47 is disconnected from
the capacitor 46, resulting in a small capacitance.
[0070] A resonant frequency f2 of the second resonant circuit including the second heating
coil 32 and the second variable capacitor 45 is set to be higher than a resonant frequency
f1 of the first resonant circuit including the first heating coil 31 and the first
variable capacitor 41, when the material of the heated object 110b on the first heating
coil 31 is magnetic metal such as iron and the material of the heated object 110b
on the second heating coil 32 is nonmagnetic metal such as aluminum. Such a configuration
can be set by appropriately selecting the inductance of the first heating coil 31
and the second heating coil 32, the capacitance of the capacitors 42 and 43 in the
first variable capacitor 41, and the capacitance of the capacitors 46 and 47 in the
second variable capacitor 45.
[0071] For example, the inductances of the first heating coil 31 and the second heating
coil 32 are set to be the same, and are set to be 300 µH when the heated object made
of magnetic metal such as iron is placed and are set to be 200 µH when the heated
object such as aluminum is placed. The capacitances of the capacitor 42 of the first
variable capacitor 41 and the capacitor 46 of the second variable capacitor 45 are
set to be 0.024 µF. The capacitances of the capacitor 43 connected in series with
the switch 44 and the capacitor 47 connected in series with the switch 48 are set
to be 0.14 µF. The following description is given assuming that the inductances of
the first heating coil 31 and the second heating coil 32 as well as the capacitances
of the capacitors 42, 43, 46, and 47 are set to be the values described in this paragraph.
[0072] FIG. 7 illustrates an example of a driving condition for inductively heating the
heated object made of different materials by the induction heating apparatus according
to the first embodiment of the present invention. In FIG. 7, the inductively heated
object is the heated object 110b illustrated in FIG. 6, which is formed by joining
the magnetic metal section 112 made of a magnetic body such as iron to the bottom
section 111 of a heated object made of a nonmagnetic body such as aluminum. The load
detection unit 11 determines that the material of the heated object on the first heating
coil 31 is a magnetic body and determines that the material of the heated object on
the second heating coil 32 is a nonmagnetic body, and thus the first switch 44 is
set to be in a "closed" state and the second switch 48 is set to be in an "open" state.
[0073] In this case, as illustrated in FIG. 7, the capacitance of the first variable capacitor
41, which is a sum of the capacitances of the capacitor 42 and the capacitor 43, is
0.164 µF. Thus, the resonant frequency f1 of the first resonant circuit including
the first heating coil 31 and the first variable capacitor 41 is 22.7 kHz. The capacitance
of the second variable capacitor 45 is the capacitance of the capacitor 46 and thus
is 0.024 µF. Thus, the resonant frequency f2 of the second resonant circuit including
the second heating coil 32 and the second variable capacitor 45 is 72.6 kHz. The resonant
frequency f of each serial resonant circuit is represented by the following formula
with L representing the inductance of each heating coil and C representing the capacitance
of each variable capacitor.
[
Equation 1]
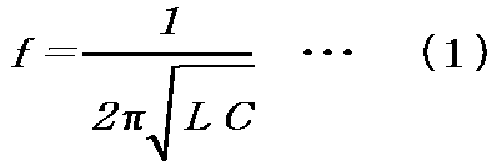
[0074] The induction heating apparatus 100 according to the present invention is formed
with the first heating coil 31 electrically connected between the first arm circuit
21 and the common arm circuit 24, and with the second heating coil 32 electrically
connected between the second arm circuit 27 and the common arm circuit 24. With this
configuration, a first frequency which is the frequency of the AC current flowing
through the first heating coil 31 and a second frequency which is the frequency of
the AC current flowing through the second heating coil 32 can be different from each
other.
[0075] As illustrated in FIG. 7, the inverter circuit 81 of the induction heating apparatus
100 according to the present invention switches each of the first switching element
21a and the second switching element 21b of the first arm circuit 21 at 25 kHz for
example, and switches each of the first switching element 27a and the second switching
element 27b of the second arm circuit 27 at 75 kHz for example. Each of the first
switching element 24a and the second switching element 24b of the common arm circuit
24 is switched at 25 kHz for example.
[0076] Thus, the AC current at the first frequency flowing through the first heating coil
31 and the AC current at the second frequency flowing through the second heating coil
32 are set to be different frequencies, with the switching frequency of the first
arm circuit 21 and the switching frequency of the common arm circuit 24 being the
same frequency and with the switching frequencies of the second arm circuit 27 and
the common arm circuit 24 being different frequencies. Also when the AC current at
the second frequency flows through the second heating coil 32, the inverter circuit
81 switches the first switching element 24a and the second switching element 24b of
the common arm circuit 24 at a frequency that is the same as that in the case that
the AC current at the first frequency flows through the first heating coil 31.
[0077] The first frequency which is the frequency of the AC current flowing through the
first heating coil 31 mainly depends on the resonant frequency f1 of the first resonant
circuit including the first heating coil 31 and the first variable capacitor 41, and
the second frequency which is the frequency of the AC current flowing through the
second heating coil 32 mainly depends on the resonant frequency f2 of the second resonant
circuit including the second heating coil 32 and the second variable capacitor 45.
[0078] Thus, for example, in the case that the first arm circuit 21, the second arm circuit
27, and the common arm circuit 24 are all switched at 25 kHz with the resonant frequency
f1 of the first resonant circuit being 22.7 kHz and with the resonant frequency f2
of the second resonant circuit being 72.6 kHz as illustrated in FIG. 7, the AC current
at 25 kHz close to the resonant frequency 22.7 kHz flows through the first heating
coil 31 and the AC current at a frequency close the resonant frequency 72.6 kHz flows
through the second heating coil 32.
[0079] As described above, the resonant frequency of such a resonant circuit including a
heating coil and a capacitor can be about three times as high as the switching frequency
of the arm circuit, so that AC current at a frequency that is about three times as
high as the switching frequency can be supplied to the heating coils. This is achieved
by the same principle as triple resonant inverters, which are well known to those
skilled in the art. In other words, a triple resonant inverter may be applied to the
induction heating apparatus 100 according to the present invention.
[0080] In FIG. 7, the resonant frequency f1 of the first resonant circuit is 22.7 kHz whereas
the switching frequency of the first arm circuit 21 is 25 kHz, and the resonant frequency
f2 of the second resonant circuit is 72.6 kHz whereas the switching frequency of the
second arm circuit 27 is 75 kHz. Generally, with inverter circuits of induction heating
apparatuses, an arm circuit is switched at a frequency higher than a resonant frequency
of a resonant circuit so that the phase of the AC current flowing through the heating
coil is delayed from the switching of the arm circuit, so as to keep the switching
loss from increasing. This similarly applies to the induction heating apparatus 100
according to the present invention. Thus, the switching frequency of each arm circuit
is preferably selected so that the phase of the AC current flowing through the first
heating coil 31 and the second heating coil 32 is delayed.
[0081] FIG. 8 is a time chart illustrating gate signals for the switching elements forming
the inverter circuit of the induction heating apparatus according to the first embodiment
of the present invention, as well as waveforms of voltage and current output from
the inverter circuit. The gate signals as well as the voltage and current waveforms
in the time chart in FIG. 8 correspond to the conditions illustrated in FIG. 7.
[0082] FIGS. 8(a) to 8(g) illustrate the gate signals for each switching element. The switching
element is ON when the gate signal is ON and is OFF when the gate signal is OFF. The
first switching element and the second switching element of each arm circuit respectively
on the high-voltage side and the low-voltage side are repeatedly switched to alternately
turn ON and OFF, meaning that when one of the switching elements is ON, the other
one of the switching elements is OFF.
[0083] Thus, the first switching element and the second switching element are switched at
the same frequency. Note that with an actual gate signal, deadtime in which the gate
signal for the first switching element and the gate signal for the second switching
element are both OFF is required to prevent the first switching element and the second
switching element of each arm circuit from being ON at the same time, but this is
omitted in FIG. 8.
[0084] FIG. 8(a) illustrates a gate signal H1 for the first switching element 21a of the
first arm circuit 21, and FIG. 8(b) illustrates a gate signal L1 for the second switching
element 21b of the first arm circuit 21. FIG. 8(c) illustrates a gate signal H4 for
the first switching element 24a of the common arm circuit 24. FIG. 8(d) illustrates
a gate signal L4 for the second switching element 24b of the common arm circuit 24.
FIG. 8(e) illustrates a gate signal H7 for the first switching element 27a of the
second arm circuit 27. FIG. 8(f) illustrates a gate signal L7 for the second switching
element 27b of the second arm circuit 27. The gate signals illustrated in FIGS. 8(a)
to 8(f) are gate signals with the duty cycle of the ON time being 50 % relative to
a switching cycle.
[0085] FIG. 8(g) and FIG. 8(i) illustrate the potentials at the output terminal 23 of the
first arm circuit 21 and at the output terminal 29 of the second arm circuit, with
the output terminal 26 of the common arm circuit 24 corresponding to a reference potential.
Vo represents voltage output from the DC part 84 to be applied to each arm circuit.
[0086] FIG. 8(h) illustrates a waveform of the AC current that flows through the first heating
coil 31, with a direction from the output terminal 23 of the first arm circuit 21
toward the first heating coil 31 being the positive direction. FIG. 8(j) is a waveform
of the AC current that flows through the second heating coil 32, with a direction
from the output terminal 29 of the second arm circuit 27 toward the second heating
coil 32 being the positive direction. In FIG. 8(h) and FIG. 8(j), +Io and -Io respectively
represent the maximum value and the minimum value of the current. The maximum value
+Io and the minimum value -Io may not necessarily be the same between the AC current
flowing through the first heating coil 31 in FIG. 8(h) and the AC current flowing
through the second heating coil 32 in FIG. 8(j), and may be different between the
first heating coil 31 and the second heating coil 32.
[0087] The first full bridge circuit including the first arm circuit 21 and the common
arm circuit 24 applies voltage to the first resonant circuit including the first heating
coil 31 and the first variable capacitor 41. As illustrated in FIG. 8(a) and FIG.
8(c), in the first full bridge circuit, the gate signal H1 for the first switching
element 21a of the first arm circuit 21 and the gate signal H4 of the first switching
element 24a of the common arm circuit 24 are at the same frequency of 25 kHz and have
phases shifted from each other by 180°. As a result, square wave voltage alternately
transitioning between +Vo and -Vo is applied to the first resonant circuit as illustrated
in FIG. 8(g), and sinusoidal AC current at 25 kHz flows through the first heating
coil 31 as illustrated in FIG. 8(h). The AC current at the first frequency of 25 kHz,
which is the same as the switching frequency of the first arm circuit 21 and the common
arm circuit 24, flows through the first heating coil 31.
[0088] The second full bridge circuit including the second arm circuit 27 and the common
arm circuit 24 applies voltage to the second resonant circuit including the second
heating coil 32 and the second variable capacitor 45. As illustrated in FIG. 8(e)
and FIG. 8(c), in the second full bridge circuit, the gate signal H7 for the first
switching element 27a of the second arm circuit 27 turns ON, OFF, and ON while the
gate signal H4 for the first switching element 24a of the common arm circuit 24 is
OFF, and the gate signal H7 for the first switching element 27a of the second arm
circuit 27 turns OFF, ON, and OFF while the gate signal H4 for the first switching
element 24a of the common arm circuit 24 is ON.
[0089] The switching frequency of the first switching element 27a of the second arm circuit
27 is 75 kHz, which is three times as high as the switching frequency of the first
switching element 24a of the common arm circuit 24, which is 25 kHz. As a result,
as illustrated in FIG. 8(i), voltage with the waveform transitioning in the sequence
of +Vo, 0, and +Vo and voltage with the waveform transitioning in the sequence of
-Vo, 0, and -Vo are alternately applied to the second resonant circuit, in half a
cycle. The +Vo period, the 0 period, and the -Vo period are each 1/3 of the switching
cycle of the common arm circuit 24. As illustrated in FIG. 8(j), the sinusoidal AC
current at 75 kHz flows through the second heating coil 32. The AC current at the
second frequency of 75 kHz, which is the same as the switching frequency of the second
arm circuit 27, flows through the second heating coil 32.
[0090] As described above, in the second full bridge circuit including the second arm circuit
27 and the common arm circuit 24, the second arm circuit 27 and the common arm circuit
24 are switched at different frequencies, and the AC current at the second frequency
different from the switching frequency of the common arm circuit 24 can be supplied
to the second heating coil 32. With the first full bridge circuit, the AC current
at the first frequency of 25 kHz can be supplied to the first heating coil 31. With
the second full bridge circuit, the AC current at the second frequency of 75 kHz can
be supplied to the second heating coil 32.
[0091] With this configuration, not only the magnetic metal section 112 of the heated object
110b placed on the first heating coil 31 but also the bottom section 111 on the outer
circumference side of the heated object 110b made of nonmagnetic metal can be inductively
heated efficiently. Specifically, alternating fluxes at a higher frequency than on
the inner circumference side are linked on the outer circumference side of the heated
object 110b made of nonmagnetic metal placed on the second heating coil 32, so that
the resistance of a path in which eddy current flows through nonmagnetic metal can
be increased by the skin effect, whereby the bottom section 111 on the outer circumference
side of the heated object 110b made of nonmagnetic metal can be inductively heated
efficiently. Thus, uniformity of the temperature distribution of the bottom section
of the heated object 110b such as a frying pan can be improved.
[0092] In the case described with reference to FIG. 8, the inverter circuit 81 simultaneously
supplies the AC current at the first frequency to the first heating coil 31 and the
AC current at the second frequency to the second heating coil 32. Alternatively, the
AC current at the first frequency and the AC current at the second frequency may be
respectively supplied to the first heating coil 31 and the second heating coil 32
at different timings. Specifically, the inverter circuit 81 may stop supplying the
AC current to the second heating coil 32 when supplying the AC current at the first
frequency of 25 kHz to the first heating coil 31, and may stop supplying the AC current
to the first heating coil 31 when supplying the AC current at the second frequency
of 75 kHz to the second heating coil 32. Then, the operation of supplying the AC current
at the first frequency to the first heating coil 31 and the operation of supplying
the AC current at the second frequency to the second heating coil 32 may be repeated
in an alternating manner.
[0093] As an example of such operations, the common arm circuit 24 may be set to switch
at 25 kHz, and when the AC current at 25 kHz is supplied to the first heating coil
31, the first arm circuit 21 may be switched at 25 kHz and the gate signal H7 and
the gate signal L7 respectively for the first switching element 27a and the second
switching element 27b of the second arm circuit 27 may both be turned OFF, so that
the AC current does not flow through the second heating coil 32. Similarly, when the
AC current at 75 kHz is supplied to the second heating coil 32, the common arm circuit
24 may be set to switch at 25 kHz with no change in the gate signal, the second arm
circuit 27 may be switched at 75 kHz, and the gate signal H1 and the gate signal L1
respectively for the first switching element 21a and the second switching element
21b of the first arm circuit 21 may both be turned OFF, so that the AC current does
not flow through the first heating coil 31.
[0094] In the case described with reference to FIG. 8, the first arm circuit 21 and the
common arm circuit 24 are switched at 25 kHz and the second arm circuit 27 is switched
at 75 kHz. Alternatively, the first arm circuit 21 may be switched at 25 kHz and the
second arm circuit 27 and the common arm circuit 24 may be switched at 75 kHz.
[0095] When the first arm circuit 21 and the common arm circuit 24 are switched at 25 kHz
and the second arm circuit 27 is switched at 75 kHz, as illustrated in FIG. 8(g),
voltage with a square waveform repeatedly and alternately transitioning to +Vo and
-Vo is applied to the first resonant circuit, so that there is no period with 0 voltage
applied to the first resonant circuit, whereby the power input to the first heating
coil 31 can be maximized. On the other hand, as illustrated in FIG. 8(i), the voltage
applied to the second resonant circuit involves a period with 0 voltage as well as
the +Vo and -Vo periods, and thus the power input to the second heating coil 32 is
smaller than that in the case with no period during which 0 voltage is applied to
the second resonant circuit.
[0096] On the other hand, when the first arm circuit 21 is switched at 25 kHz and the second
arm circuit 27 and the common arm circuit 24 are switched at 75 kHz, there is no period
during which 0 voltage is applied to the second resonant circuit, whereby the power
input to the second heating coil 32 can be maximized. Meanwhile, there is a period
during which 0 voltage is applied to the first resonant circuit, and thus the power
input to the first heating coil 31 is smaller than that in the case with no period
during which 0 voltage is applied to the first resonant circuit.
[0097] Thus, the first arm circuit 21 and the common arm circuit 24 may be switched at the
same frequency and the second arm circuit 27 and the common arm circuit 24 may be
switched at different frequencies to inductively heat the magnetic metal section 112
on the inner circumference side with a higher priority, to inductively heat the heated
object 110b formed by joining the magnetic metal section 112 on the inner circumference
side of the bottom section 111 made of nonmagnetic metal as illustrated in FIG. 6.
On the other hand, the second arm circuit 27 and the common arm circuit 24 may be
switched at the same frequency and the first arm circuit 21 and the common arm circuit
24 may be switched at different frequencies, to prioritize inductive heating for the
bottom section 111 made of nonmagnetic metal on the outer circumference side more
than the magnetic metal section 112.
[0098] Which one of the magnetic metal section 112 on the inner circumference side or the
bottom section 111 made of nonmagnetic metal on the outer circumference side is inductively
heated with higher priority may be switched by the control circuit 85 controlling
the switching of each arm circuit based on a signal from the operation unit 5 in response
to an operation on the operation unit 5 by the user for example. Automatic switching
may be implemented by the control circuit 85 of the induction heating apparatus 100
based on what and how to be cooked.
[0099] As described above, in the induction heating apparatus 100 according to the first
embodiment of the present invention, the inverter circuit 81 that includes the first
arm circuit 21, the second arm circuit 27, and the common arm circuit 24 switches
the first switching element 24a of the common arm circuit 24 at a predetermined frequency
when supplying the AC current at the first frequency to the first heating coil 31,
and switches the first switching element 24a of the common arm circuit 24 at the frequency
that is the same as that for supplying the AC current at the first frequency to the
first heating coil 31 also when supplying the AC current at the second frequency different
from the first frequency to the second heating coil 32.
[0100] Thus, the first full bridge circuit and the second full bridge circuit can each include
three arm circuits (the first arm circuit 21, the second arm circuit 27, and the common
arm circuit 24) including one common circuit while enabling the AC currents at different
frequencies to be supplied to the first heating coil 31 electrically connected to
the first full bridge circuit and the second heating coil 32 electrically connected
to the second full bridge circuit. Thus, alternating fluxes at a higher frequency
than in the magnetic metal section can be linked for inductively heating the nonmagnetic
metal section of the heated object made of different materials, without increasing
the number of arm circuits.
[0101] The conventional induction heating apparatus described in Patent Document 1 inductively
heats the heated object made of different materials formed by joining the magnetic
metal section on the inner circumference side of the bottom section of the heated
object made of a nonmagnetic metal, with the first arm circuit, the second arm circuit,
and the common arm circuit switched at the same frequency and with the AC currents
at the same frequency flowing through the first heating coil and the second heating
coil.
[0102] Thus, when the switching frequency of each arm circuit is set to be at a frequency
(25 kHz for example) suitable for inductively heating the magnetic metal section,
the skin effect on the nonmagnetic metal section on the outer circumference side of
the magnetic metal section is limited, resulting in the resistance of the nonmagnetic
metal section being considerably smaller than the resistance of the magnetic metal
section. Thus, overcurrent is likely to flow in the second heating coil on which the
nonmagnetic metal is placed, rendering the power input to the second heating coil
difficult to increase due to limitation by the rated current of the switching element.
Thus, the temperature rise is fast on the inner circumference side of the bottom section
of the heated object made of different materials but is slow on the outer circumference
side. As a result, the uniformity of the temperature of the bottom section of the
heated object is compromised.
[0103] When the switching frequency of each arm circuit is set to be a frequency (75 kHz
for example) suitable for inductively heating the nonmagnetic metal section, the first
arm circuit and the common arm circuit are switched at a frequency that is excessively
high for inductively heating the magnetic metal section, resulting in a high switching
loss. Thus, the efficiency of the inductive heating is compromised. Furthermore, a
higher frequency of the current flowing through the heating coil leads to a higher
resistance of a lead wire forming the heating coil, resulting in a lower efficiency
of the inductive heating.
[0104] On the other hand, in the induction heating apparatus 100 according to the present
invention, the AC current at the first frequency (25 kHz for example) suitable for
inductively heating the magnetic metal flows through the first heating coil 31 that
inductively heats the magnetic metal section on the inner circumference side of the
heated object, and the AC current at the second frequency (75 kHz for example) suitable
for inductively heating the nonmagnetic metal is supplied to the second heating coil
32 that inductively heats the nonmagnetic metal section on the outer circumference
side of the magnetic metal section. Thus, the resistance of the nonmagnetic metal
section on the outer circumference side can be increased by skin effect, whereby larger
power can be input to the nonmagnetic metal section. All things considered, an effect
of improving uniformity of the temperature of the bottom section of the heated object
made of different materials can be obtained.
[0105] In the induction heating apparatus 100 according to the present invention, the AC
current at the first frequency is supplied to the first heating coil 31 and the AC
current at the second frequency is supplied to the second heating coil 32, with the
switching frequency of the first arm circuit 21 and the common arm circuit 24 being
the first frequency and with the switching frequency of the second arm circuit 27
being the second frequency. Thus, the AC currents at different frequencies can be
supplied to the first heating coil 31 and the second heating coil 32 without increasing
the number of arm circuits of the inverter circuit 81, whereby effects of downsizing
and reducing the cost of the inverter circuit 81 can be obtained.
[0106] As described above, the second arm circuit 27 needs to be switched at a frequency
suitable for inductively heating nonmagnetic metal, and thus is required to be switched
at a higher frequency than the first arm circuit 21 that may be switched at a frequency
suitable for inductively heating magnetic metal. Thus, the first switching element
21a and the second switching element 21b of the first arm circuit 21 may be formed
of a silicon semiconductor and the first switching element 27a and the second switching
element 27b of the second arm circuit 27 may be formed of a wide band gap semiconductor
with a larger band gap than silicon. With this configuration, the inverter circuit
81 can be made at a lower cost compared with a case that the switching elements of
both of the first arm circuit 21 and the second arm circuit 27 are formed of a wide
band gap semiconductor. The wide band gap semiconductor may include silicon carbide
(SiC), gallium nitride (GaN), gallium oxide (Ga
2O
3), or diamond, for example.
[0107] The common arm circuit 24 is common between the first full bridge circuit that supplies
the AC current to the first heating coil 31 and the second full bridge circuit that
supplies the AC current to the second heating coil 32, and thus a current larger than
those flowing through the first arm circuit 21 and the second arm circuit 27 flows
through the common arm circuit 24. Thus, the first switching element 24a and the second
switching element 24b of the common arm circuit 24 are preferably switching elements
with a lower ON resistance than those in the first arm circuit 21 and the second arm
circuit 27. In this context, the first switching element 21a and the second switching
element 21b of the first arm circuit 21 are preferably formed of a silicon semiconductor
and the first switching element 24a and the second switching element 24b of the common
arm circuit 24 are preferably formed of a wide band gap semiconductor.
[0108] Similarly, the first switching element 27a and the second switching element 27b of
the second arm circuit 27 are preferably formed of a silicon semiconductor, and the
first switching element 24a and the second switching element 24b of the common arm
circuit 24 are preferably formed of a wide band gap semiconductor. This is because
if the withstand voltage is the same, a switching element formed of a wide band gap
semiconductor can achieve a smaller ON resistance than a switching element formed
of a silicon semiconductor. Thus, the cost of the inverter circuit 81 can be reduced
compared with a case that the switching elements of all the arm circuits are formed
of a wide band gap semiconductor.
[0109] In the example described in this first embodiment, the switching frequency of the
first arm circuit 21 and the common arm circuit 24 is 25 kHz, and the switching frequency
of the second arm circuit 27 is 75 kHz. Thus, in the described example, the switching
frequency of the second arm circuit 27 is three times as high as (integer multiple
of) the switching frequency of the first arm circuit 21 and the common arm circuit
24. Alternatively, for example, the switching frequency of the second arm circuit
27 may be 53 kHz and the switching frequency of the first arm circuit 21 and the common
arm circuit 24 may be 25 kHz. In other words, the switching frequency of the second
arm circuit 27 may not be integer multiple of the switching frequency of the first
arm circuit 21 and the common arm circuit 24.
[0110] The switching frequency of the first arm circuit 21 and the switching frequency of
the common arm circuit 24 may be different from each other, and thus the switching
frequency of the first arm circuit 21, the switching frequency of the second arm circuit
27, and the switching frequency of the common arm circuit 24 may be different from
each other. The frequencies are preferably different from each other by a difference
that is equal to or larger than an audible frequency. This audible frequency is approximately
20 kHz. This is because when the difference between switching frequencies different
from each other is smaller than the audible frequency, the difference in the frequencies
results in interference noise (beat) audible and annoying to the user of the induction
heating apparatus 100.
Second Embodiment
[0111] FIG. 9 is a time chart illustrating gate signals for each switching element of an
inverter circuit of an induction heating apparatus according to a second embodiment
of the present invention, as well as waveforms of voltage and current output from
the inverter circuit. The time chart in FIG. 9 illustrates a state of the induction
heating apparatus 100 described in the first embodiment, and illustrates a power control
method in a case that the input power to the first heating coil 31 and the second
heating coil 32 is reduced from the state in the time chart illustrated in FIG. 8.
In FIG. 9, parts that are the same as the counterparts in FIG. 8 indicate the same
contents, and thus the description thereof will be omitted. The induction heating
apparatus 100 according to the second embodiment has the configuration and the like
that are the same as those in the first embodiment, and the components of the induction
heating apparatus 100 described while being denoted with the same reference numerals
are the same as the counterparts in the first embodiment.
[0112] FIG. 9 is similar to FIG. 8 in that it includes FIGS. 9(a) to 9(f) illustrating waveforms
of gate signals for switching elements of arm circuits, and FIGS. 9(g) to 9(j) illustrating
waveforms of voltage and current output from the inverter circuit 81. In this second
embodiment, a method of controlling the input power to the first heating coil 31 and
the second heating coil 32 based on Pulse Width Modulation (PWM) will be described.
[0113] The control circuit 85 of the induction heating apparatus 100 outputs a control signal
H1 for setting the duty cycle of the ON time of the first switching element 21a of
the first arm circuit 21 to be 25 %, and outputs a control signal L1 for setting the
duty cycle of the ON time of the second switching element 21b of the first arm circuit
21 to be 75 % as illustrated in FIG. 9(a) and FIG. 9(b). Furthermore, the control
circuit 85 of the induction heating apparatus 100 outputs a control signal H7 for
setting the duty cycle of the ON time of the first switching element 27a of the second
arm circuit 27 to be 25 %, and outputs a control signal L7 for setting the duty cycle
of the ON time of the second switching element 27b of the second arm circuit 27 to
be 75 % as illustrated in FIG. 9(e) and FIG. 9(f).
[0114] As described above, the duty cycles of the ON time of the first switching element
21a of the first arm circuit 21 and the second switching element 27a of the second
arm circuit 27 are both set to be 25 % herein. Alternatively, the duty cycles of the
ON time of the first switching element 21a of the first arm circuit 21 and the second
switching element 27a of the second arm circuit 27 can each be independently controlled
and thus may be different from each other. The gate signals for the second switching
elements 27a and 27b of the first arm circuit 21 and the second arm circuit 27 are
uniquely determined based on the gate signals for the first switching elements 21a
and 27a, and thus the description thereof will be omitted.
[0115] As illustrated in FIG. 9(c) and FIG. 9(d), the control circuit 85 of the induction
heating apparatus 100 outputs a control signal H4 for setting the duty cycle of ON
time of the first switching element 24a of the common arm circuit 24 to be 50 %, and
outputs a control signal L4 for setting the duty cycle of ON time of the second switching
element 24b of the common arm circuit 24 to be 50 %.
[0116] As a result, as illustrated in FIG. 9(g), square wave voltage transitioning in the
sequence of +Vo, 0, -Vo, and +Vo is applied to the first resonant circuit including
the first heating coil 31 and the first variable capacitor 41 connected between the
output terminal 23 of the first arm circuit 21 and the output terminal 26 of the common
arm circuit 24. The square wave voltage has the period with the voltage +Vo being
25 % of a single cycle, the period with the voltage -Vo being 50 % of a single cycle,
and the period with 0 voltage being 25 % of a single cycle.
[0117] It is clear that the square wave voltage applied to the first resonant circuit in
FIG. 9(g) has a pulse width of +Vo reduced from that in FIG. 8(g). As illustrated
in FIG. 9(h), the absolute values of the maximum value and the minimum value of the
current flowing through the first heating coil 31 are smaller than Io. As is clear
from the comparison between FIG. 9(h) and FIG. 8(h) that the magnitude of the current
flowing through the first heating coil 31 is smaller in FIG. 9(h). The frequency of
the current flowing through the first heating coil 31 is 25 kHz and thus is unchanged
from the state illustrated in FIG. 8(h).
[0118] The power input to the heated object placed on the first heating coil 31 for inductively
heating the heated object is proportional to the square of the current flowing through
the first heating coil 31. Thus, as illustrated in FIG. 9(a) and FIG. 9(b), the power
input to the heated object placed on the first heating coil 31 can be controlled by
changing the current value of the AC current supplied to the first heating coil 31
by changing the duty cycle of ON time of the first switching element 21a of the first
arm circuit 21.
[0119] On the other hand, as illustrated in FIG. 9(i), square wave voltage transitioning
in the sequence of +Vo, 0, +Vo, 0, -Vo, 0, -Vo, and +Vo is applied to the second resonant
circuit including the second heating coil 32 and the second variable capacitor 45
connected between the output terminal 29 of the second arm circuit 27 and the output
terminal 26 of the common arm circuit 24. The square wave voltage has a +Vo voltage
period that is 2/12 of the switching cycle of the common arm circuit 24, a -Vo voltage
period that is 5/12 of the switching cycle of the common arm circuit 24, and a 0 voltage
period that is 5/12 of the switching cycle of the common arm circuit 24.
[0120] In FIG. 9(i), the square wave voltage applied to the second resonant circuit has
the pulse width of +Vo reduced by half and 0 voltage and -Vo periods slightly increased,
compared with FIG. 8(i). As illustrated in FIG. 9(j), the absolute values of the maximum
value and the minimum value of the current flowing through the second heating coil
32 are smaller than Io. As is clear from the comparison between FIG. 9(j) and FIG.
8(j), the magnitude of the current flowing through the second heating coil 32 is smaller
in FIG. 9(j). The frequency of the current flowing through the second heating coil
32 is 75 kHz and thus is unchanged from the state illustrated in FIG. 8(j).
[0121] As described above, as illustrated in FIG. 9(e) and FIG. 9(f), the power input to
the heated object placed on the second heating coil 32 can be controlled by changing
the current value of the AC current supplied to the second heating coil 32 by changing
the duty cycle of ON time of the first switching element 27a of the second arm circuit
27.
[0122] The current value of the AC current flowing through the first heating coil 31 and
the current value of the AC current flowing through the second heating coil 32 can
each be independently controlled, by independently controlling each of the duty cycle
of ON time of the first switching element 21a of the first arm circuit 21 and the
duty cycle of ON time of the first switching element 27a of the second arm circuit
27. As a result, the heated object placed on the first heating coil 31 and the heated
object placed on the second heating coil 32 can each be inductively heated by independently
controllable power, whereby the heating temperatures for the inner circumference side
and the outer circumference side of the heated object made of different materials
can each be independently controlled.
[0123] In this second embodiment, the method of controlling the first arm circuit 21 and
the second arm circuit 27 based on PWM to independently control AC current flowing
through each of the first heating coil 31 and the second heating coil 32 is described.
Alternatively, the common arm circuit 24 may be controlled based on PWM to collectively
control the AC current flowing through the first heating coil 31 and the second heating
coil 32. The collective control on the AC current flowing through the first heating
coil 31 and the second heating coil 32 enables the input power to a heated object,
such as a frying pan, made of different materials to be integrally controlled, whereby
the methods may be selectively used in accordance with the purpose of the user to
achieve higher usability.
[0124] Whether the AC current flowing through the first heating coil 31 and the AC current
flowing through the second heating coil 32 are each independently controlled or are
collectively controlled may be determined by the control circuit 85 based on an operation
signal as a result of an operation on the operation unit 5 by the user for example.
[0125] The control on the AC current flowing through the first heating coil 31 and the second
heating coil 32 based on the PWM control described in this second embodiment may be
implemented regardless of the relationship between the first frequency that is the
frequency of the AC current that flows through the first heating coil 31 and the second
frequency that is the frequency of the AC current that flows through the second heating
coil 32. Specifically, although the case that the first frequency is 25 kHz and the
second frequency is 75 kHz is described in this second embodiment, the embodiment
can also be applied to a case that the second frequency is not an integer multiple
of the first frequency such as a case that the first frequency is 25 kHz and the second
frequency is 57 kHz for example.
Third Embodiment
[0126] FIG. 10 is a time chart illustrating gate signals for each switching element of an
inverter circuit of an induction heating apparatus according to a third embodiment
of the present invention, as well as waveforms of voltage and current output from
the inverter circuit. The time chart in FIG. 10 illustrates a state of the induction
heating apparatus 100 described in the first embodiment, and illustrates a power control
method in a case that the input power to the first heating coil 31 and the second
heating coil 32 is reduced from the state in the time chart illustrated in FIG. 8.
[0127] In FIG. 10, parts that are the same as the counterparts in FIGS. 8 and 9 indicate
the same contents, and thus the description thereof will be omitted. The induction
heating apparatus 100 according to the third embodiment has the configuration and
the like that are the same as those in the first embodiment, and the components of
the induction heating apparatus 100 described while being denoted with the same reference
numerals are the same as the counterparts in the first embodiment.
[0128] FIG. 10 is similar to FIG. 8 and FIG. 9 in that it includes FIGS. 10(a) to 10(f)
illustrating waveforms of gate signals for switching elements of arm circuits, and
FIGS. 10(g) to 10(j) illustrating waveforms of voltage and current output from the
inverter circuit 81. In this third embodiment, a method of independently controlling
the input power to each of the first heating coil 31 and the second heating coil 32
by performing phase difference control on the first arm circuit 21 switched at the
same frequency as the common arm circuit 24 and performing PWM control on the second
arm circuit 27 switched at a frequency different from the switching frequency of the
common arm circuit 24.
[0129] As illustrated in FIG. 10(a), the control circuit 85 of the induction heating apparatus
100 outputs a gate signal H1, with which the timing at which the gate signal for the
first switching element 21a of the first arm circuit 21 changes from OFF to ON, that
is, the timing at which the first switching element 21a turns ON is delayed by 90°.
The duty cycle of ON time of the gate signal H1 for the first switching element 21a
is 50 % as in the case illustrated in FIG. 8. The gate signal L1 for the second switching
element 21b of the first arm circuit 21 is uniquely determined based on the gate signal
H1 for the first switching element 21a. Thus, the control circuit 85 outputs the gate
signal L1 for the second switching element 21b with which the timing at which OFF
changes to ON, that is, the timing of turning OFF is delayed by 90°. The duty cycle
of the gate signal L1 for the second switching element 21b is also 50 % as in FIG.
8.
[0130] As illustrated in FIG. 10(c), the switching frequency of the first switching element
24a of the common arm circuit 24 is 25 kHz to be the same as the switching frequency
of the first switching element 21a of the first arm circuit 21, and the duty cycle
of ON time of the first switching element 24a is 50 %. Thus, as illustrated in FIG.
10(a), changing the timing at which the first switching element 21a of the first arm
circuit 21 turns ON results in changing a time period between the timing at which
the first switching element 21a of the first arm circuit 21 turns ON and the timing
at which the first switching element 24a of the common arm circuit 24 turns ON. Such
control is referred to as the phase difference control.
[0131] By delaying the timing at which the first switching element 21a of the first arm
circuit 21 turns ON by 90° as illustrated in FIG. 10(a), the square wave voltage transitioning
in the sequence of +Vo, 0, -Vo, 0, and +Vo is applied to the first resonant circuit
including the first heating coil 31 and the first variable capacitor 41 connected
between the output terminal 23 of the first arm circuit 21 and the output terminal
26 of the common arm circuit 24 as illustrated in FIG. 10(g). The +Vo voltage period
of this square wave voltage is 25 % of a single cycle, and the -Vo voltage period
is 25 % of a single cycle, and the 0 voltage period is 50 % of a single cycle. It
can be seen that square wave voltage applied to the first resonant circuit has the
pulse width of +Vo and the pulse width of -Vo illustrated in FIG. 10(g) reduced from
those illustrated in FIG. 8(g).
[0132] As illustrated in FIG. 10(h), the absolute values of the maximum value and the minimum
value of the current flowing through the first heating coil 31 are smaller than Io.
It can be seen from a comparison between FIG. 10(h) and FIG. 8(h) that the magnitude
of the current flowing through the first heating coil 31 is smaller in the case illustrated
in FIG. 10(h). The frequency of the current flowing through the first heating coil
31 is 25 kHz and thus is unchanged from the state illustrated in FIG. 8(h).
[0133] Thus, control is performed to make the transition from the state illustrated in FIGS.
8(a) and 8(c) to the state illustrated in FIGS. 10(a) and 10(c), that is, the time
period between the timing at which the first switching element 21a of the first arm
circuit 31 turns ON and the timing at which the first switching element 24a of the
common arm circuit 24 turns ON is changed to change the current value of the AC current
supplied to the first heating coil 31, whereby the power input to the heated object
placed on the first heating coil 31 can be controlled.
[0134] The switching elements of the second full bridge circuit including the second arm
circuit 27 and the common arm circuit 24 are controlled in the manner that is same
as that in the second embodiment. Specifically, the second arm circuit 27 switched
at a frequency different from the switching frequency of the common arm circuit 24
changes the duty cycle of ON time of the first switching element 27a to control the
current value of the AC current supplied to the second heating coil 32.
[0135] As described above in this third embodiment, when the switching frequency of the
first arm circuit 21 is the same as the switching frequency of the common arm circuit
24 and the switching frequency of the second arm circuit 27 is different from the
switching frequency of the common arm circuit 24, the phase difference control is
performed on the gate signal H1 for the first switching element 21a of the first arm
circuit 21 and the PWM control is performed on the gate signal H7 for the first switching
element 27a of the second arm circuit 27, whereby the current value of the AC current
flowing through the first heating coil 31 and the current value of the AC current
flowing through the second heating coil 32 can each be independently controlled.
[0136] Similarly, when the switching frequency of the first arm circuit 21 is different
from the switching frequency of the common arm circuit 24 with the switching frequency
of the second arm circuit 27 being the same as the switching frequency of the common
arm circuit 24, the PWM control is performed on the gate signal H1 of the first switching
element 21a of the first arm circuit 21 and the phase difference control is performed
on the gate signal H7 of the first switching element 27a of the second arm circuit
27, whereby the current value of the AC current flowing through the first heating
coil 31 and the current value of the AC current flowing through the second heating
coil 32 can each be independently controlled.
[0137] Note that also in this third embodiment, the switching frequency of the arm circuit
on which the PWM control is performed may be independent from the switching frequency
of the common arm circuit 24, and thus can be set as appropriate.
Fourth Embodiment
[0138] FIG. 11 is a time chart illustrating gate signals for each switching element of an
inverter circuit of an induction heating apparatus according to a fourth embodiment
of the present invention, as well as waveforms of voltage and current output from
the inverter circuit. The time chart in FIG. 11 illustrates a state of the induction
heating apparatus 100 described in the first embodiment, and illustrates a power control
method in a case that the input power to the first heating coil 31 and the second
heating coil 32 is reduced from the state in the time chart illustrated in FIG. 8.
In FIG. 11, parts that are the same as the counterparts in FIGS. 8, 9, and 10 indicate
the same contents, and thus the description thereof will be omitted. The induction
heating apparatus 100 according to the fourth embodiment has the configuration and
the like that are the same as those in the first embodiment, and the components of
the induction heating apparatus 100 described while being denoted with the same reference
numerals are the same as the counterparts in the first embodiment.
[0139] FIG. 11 is similar to FIG. 8, FIG. 9, and FIG. 10 in that it includes FIGS. 11(a)
to 11(f) illustrating waveforms of gate signals for switching elements of arm circuits,
and FIGS. 11(g) to 11(j) illustrating waveforms of voltage and current output from
the inverter circuit 81. In a method described in this fourth embodiment, the phase
difference control is performed on the first arm circuit 21 switched at the same frequency
as the common arm circuit 24 and on the second arm circuit 27 switched at a frequency
different from the switching frequency of the common arm circuit 24, to independently
control input power to each of the first heating coil 31 and the second heating coil
32. The switching frequency of the second arm circuit 27 which is different from the
switching frequency of the common arm circuit 24 is 2n + 1 (n being a natural number
that is equal to or larger than 1) times as high as the switching frequency of the
first arm circuit 21 and the common arm circuit 24.
[0140] The phase difference control as described in the third embodiment is performed to
control the current value of the AC current supplied from the first full bridge circuit
including the first arm circuit 21 and the common arm circuit 24 to the first heating
coil 31 as illustrated in FIGS. 11(a) to 11(d) and in FIGS. 11(g) and 11(h). This
operation is the same as that in the third embodiment, and thus the description thereof
will be omitted.
[0141] As is clear from a comparison with the gate signal H7 in FIG. 8(e), the gate signal
H7 for the first switching element 27a of the second arm circuit 27 illustrated in
FIG. 11(e) has the phase delayed by 90° from the state illustrated in FIG. 8(e). As
is clear from a comparison between FIG. 11(c) and FIG. 8(c), the gate signal H4 for
the first switching element 24a of the common arm circuit 24 is the same between FIG.
11(c) and FIG. 8(c). Thus, in FIG. 11(e), the time period between the timing at which
the first switching element 27a of the second arm circuit 27 turns ON and the timing
at which the first switching element 24a of the common arm circuit 24 turns ON is
changed from the state illustrated in FIG. 8(e). As a result, the 0 voltage period
of the voltage applied to the second resonant circuit including the second heating
coil 32 and the second variable capacitor 45 is increased with the +Vo and -Vo periods
reduced, as is clear from a comparison between FIG. 11(i) and FIG. 8(i). Thus, as
illustrated in FIG. 11(j), the current value of the AC current flowing through the
second heating coil 32 is reduced from the state illustrated in FIG. 8(j).
[0142] As illustrated in FIG. 8(a) in the first embodiment, when the gate signal H7 for
the first switching element 27a of the second arm circuit 27 has no phase difference,
the rate of the period during which the absolute value of the voltage value is Vo
is 4/6 in the waveform of the voltage applied to the second resonant circuit as illustrated
in FIG. 8(i). When the AC current flowing through the second heating coil 32 is reduced
by controlling the phase difference for the second arm circuit 27 with the switching
frequency different from that of the common arm circuit 24 as in the fourth embodiment,
the smallest AC current flowing through the second heating coil 32 is achieved when
the phase difference of gate signal H7 for the first switching element 27a of the
second arm circuit 27 is 180°. In this case, the rate of the period during which the
absolute value of the voltage value in the waveform of the voltage applied to the
second resonant circuit is Vo is 2/6. Thus, with the phase difference control described
in this fourth embodiment, the magnitude of the AC current flowing through the second
heating coil 32 can be halved.
[0143] When the current value of the AC current flowing through the second heating coil
32 is controlled by the phase difference control on the second arm circuit 27 with
the switching frequency different from that of the common arm circuit 24, the switching
frequency of the common arm circuit 24 closer to the switching frequency of the second
arm circuit 27 can achieve a large control amount on the current value. With this
in mind, considering the fact that the switching frequency of the second arm circuit
27 needs to be 2n + 1 (n being a natural number that is equal to or larger than 1)
times as high as the switching frequency of the common arm circuit 24, the switching
frequency of the second arm circuit 27 is most preferably three times as high as the
switching frequency of the common arm circuit 24.
[0144] As described above, in the induction heating apparatus 100 according to the fourth
embodiment, the current value of the AC current flowing through the first heating
coil 31 can be controlled by controlling the phase difference of the first switching
element 21a of the first arm circuit 21, and the current value of the AC current flowing
through the second heating coil 32 can be controlled by controlling the phase difference
of the first switching element 27a of the second arm circuit 27. With the phase difference
control on the first switching element 24a of the common arm circuit 24, the current
value of the AC current flowing through the first heating coil 31 and the current
value of the AC current flowing through the second heating coil 32 can be simultaneously
controlled.
Fifth Embodiment
[0145] FIG. 12 is a time chart illustrating gate signals for each switching element of an
inverter circuit of an induction heating apparatus according to a fifth embodiment
of the present invention, as well as waveforms of voltage and current output from
the inverter circuit. The time chart in FIG. 12 illustrates a state of the induction
heating apparatus 100 described in the first embodiment, and illustrates a power control
method in a case that the input power to the first heating coil 31 and the second
heating coil 32 is reduced from the state in the time chart illustrated in FIG. 8.
[0146] In FIG. 12, parts that are the same as the counterparts in FIGS. 8, 9, 10, and 11
indicate the same contents, and thus the description thereof will be omitted. The
induction heating apparatus 100 according to this fifth embodiment has the configuration
and the like that are the same as those in the first embodiment, and the components
of the induction heating apparatus 100 described while being denoted with the same
reference numerals are the same as the counterparts in the first embodiment.
[0147] FIG. 12 is similar to FIG. 8, FIG. 9, FIG. 10, and FIG. 11 in that it includes FIGS.
12(a) to 12(f) illustrating waveforms of gate signals for switching elements of arm
circuits, and FIGS. 12(g) to 12(j) illustrating waveforms of voltage and current output
from the inverter circuit 81. In the method described in the fifth embodiment, the
input power to each of the first heating coil 31 and the second heating coil 32 is
independently controlled by performing frequency control on the first arm circuit
21 switched at the same frequency as the common arm circuit 24 and on the second arm
circuit 27 switched at a frequency different from the switching frequency of the common
arm circuit 24.
[0148] The gate signals illustrated in FIGS. 12(a) to 12(f) are the same as the gate signals
illustrated in FIGS. 8(a) to 8(f) in that the duty cycle of ON time relative to the
switching cycle is 50 %, but the cycle of the former gate signals is changed to increase
the frequency of these gate signals. FIGS. 12(a) to 12(f) illustrate gate signals
for each switching element after the frequency has been changed according to this
fifth embodiment, from those illustrated in FIGS. 8(a) to 8(f).
[0149] The frequency of the gate signals for each switching element of the first arm circuit
21 and the common arm circuit 24 illustrated in FIGS. 8(a) to 8(d) is 25 kHz before
the frequency change. The frequency of the gate signals for each switching element
of the second arm circuit 27 illustrated in FIGS. 8(e) and 8(f) is 75 kHz before the
frequency change. The frequency of the gate signal for each switching element of the
first arm circuit 21 and the common arm circuit 24 illustrated in FIGS. 12(a) to 12(d)
is 26 kHz after the frequency change. The frequency of the gate signals for each switching
element of the second arm circuit 27 illustrated in FIGS. 12(e) and 12(f) is 78 kHz
after the frequency change.
[0150] As illustrated in FIG. 12(g), voltage with a square waveform transitioning in the
sequence of +Vo and -Vo at a frequency of 26 kHz is applied to the first resonant
circuit including the first heating coil 31 and the first variable capacitor 41 connected
between the output terminal 23 of the first arm circuit 21 and the output terminal
26 of the common arm circuit 24. The frequency of the voltage applied to the first
resonant circuit being 26 kHz means that the frequency of the voltage applied to the
first resonant circuit is more shifted away from the resonant frequency 22.7 kHz of
the first resonant circuit compared with the case that the frequency is 25 kHz. As
a result, the maximum value and the minimum value of the current flowing through the
first heating coil 31 are smaller than Io as illustrated in FIG. 12(h). As is clear
from a comparison between FIG. 12(h) and FIG. 8(h), the current flowing through the
first heating coil 31 is smaller in FIG. 12(h). The frequency of the current flowing
through the first heating coil 31 is 26 kHz and thus has been changed from the frequency
in FIG. 8(h) which is 25 kHz.
[0151] The power input to the heated object placed on the first heating coil 31 for inductively
heating the heated object is proportional to the square of the current flowing through
the first heating coil 31. Thus, as illustrated in FIGS. 12(a) to 12(d), the power
input to the heated object placed on the first heating coil 31 can be controlled by
changing the frequency of the first arm circuit 21 that is switched at the same frequency
as the common arm circuit 24 to change the current value of the AC current supplied
to the first heating coil 31.
[0152] Similarly, as illustrated in FIG. 12(i), the square wave voltage transitioning in
the sequence of +Vo, 0, +Vo, -Vo, 0, and -Vo due to the frequency being 78 kHz and
26 kHz is applied to the second resonant circuit including the second heating coil
32 and the second variable capacitor 45 connected between the output terminal 29 of
the second arm circuit 27 and the output terminal 26 of the common arm circuit 24.
The frequency of the voltage applied to the second resonant circuit being 78 kHz means
that the frequency of the voltage applied to the second resonant circuit is more shifted
away from the resonant frequency 72.6 kHz of the second resonant circuit compared
with the case that the frequency is 75 kHz.
[0153] As a result, the maximum value and the minimum value of the current flowing through
the second heating coil 32 are smaller than Io as illustrated in FIG. 12(j). As is
clear from the comparison between FIG. 12(j) and FIG. 8(j), the magnitude of the current
flowing through the first heating coil 31 is smaller in FIG. 12(j). The frequency
of the current flowing through the first heating coil 31 is 78 kHz, and thus has been
changed from the frequency 75 kHz in FIG. 8(j).
[0154] The power input to the heated object placed on the second heating coil 32 for inductively
heating the heated object is proportional to the square of the current flowing through
the second heating coil 32. Thus, as illustrated in FIG. 12(e) to 12(f), the power
input to the heated object placed on the second heating coil 32 can be controlled
by changing the current value of the AC current supplied to the second heating coil
32 by changing the frequency of the second arm circuit 27.
[0155] Note that in the case that the switching frequency of the common arm circuit 24 switched
at the same switching frequency as the first arm circuit 21 changes, the current flowing
through the second heating coil 32 might change even when the switching frequency
of the second arm circuit 27 remains to be the same, depending on the switching frequency
of the common arm circuit 24 changed. For example, when the switching frequency of
the first arm circuit 21 switched at the same frequency as the common arm circuit
24 is changed from 25 kHz to 26 kHz with the frequency of the second arm circuit 27
maintained at 75 kHz, the magnitude of the current flowing through the first heating
coil 31 decreases and small current flows through the second heating coil 32.
[0156] On the other hand, when the switching frequency of the first arm circuit 21, switched
at the same frequency as the common arm circuit 24, is changed from 25 kHz to 24 kHz
with the frequency of the second arm circuit 27 maintained at 75 kHz, the magnitude
of the current flowing through the first heating coil 31 increases, and large current
flows through the second heating coil 32. The magnitude of the current flowing through
the first heating coil 31 may increase and the magnitude of the current flowing through
the second heating coil 32 may decrease, or the magnitude of the current flowing through
the first heating coil 31 may decrease and the magnitude of the current flowing through
the second heating coil 32 may increase, depending on the changed frequency.
[0157] Thus, the currents flowing through the first heating coil 31 and the second heating
coil 32 may be controlled by changing the frequency of the first arm circuit 21 switched
at the same frequency as the common arm circuit 24 and then changing the frequency
of the second arm circuit 27.
[0158] The control circuit 85 may recognize in advance how the current flowing through the
second heating coil 32 and power increases/decreases due to the change in the frequency
of the common arm circuit 24, and when a certain amount of power is switched in stages,
the frequency of the second arm circuit 27 may be changed while changing the frequency
of the first arm circuit 21 switched at the same frequency as the common arm circuit
24 so that the current flowing through the first heating coil 31 and the current flowing
through the second heating coil 32 are simultaneously controlled.
[0159] In the description of this fifth embodiment, the currents flowing through the first
heating coil 31 and through the second heating coil 32 is reduced with the frequency
of the gate signal shifted away from the resonant frequency. Alternatively, the currents
flowing through the first heating coil 31 and through the second heating coil 32 may
be increased with the frequency shifted toward the resonant frequency.
[0160] As described above, the current value of the AC current flowing through the first
heating coil 31 and the current value of the AC current flowing through the second
heating coil 32 can each be independently controlled, by changing the switching frequency
of the first arm circuit 21 switched at the same frequency as the common arm circuit
24 and by changing the switching frequency of the second arm circuit 27. As a result,
the heated object placed on the first heating coil 31 and the heated object placed
on the second heating coil 32 can each be inductively heated by independently controllable
power, whereby the heating temperatures for the inner circumference side and the outer
circumference side of the heated object made of different materials can each be independently
controlled.
[0161] Similarly, when the switching frequency of the first arm circuit 21 is different
from the switching frequency of the common arm circuit 24 and the switching frequency
of the second arm circuit 27 is the same as the switching frequency of the common
arm circuit 24, the switching frequency of the first arm circuit 21 is changed and
the switching frequency of the second arm circuit 27 switched at the same frequency
as the common arm circuit 24 is changed so that the current value of the AC current
flowing through the first heating coil 31 and the current value of the AC current
flowing through the second heating coil 32 can each be independently controlled.
[0162] Note that also in this fifth embodiment, the switching frequency of the first arm
circuit 21 or the second arm circuit 27 switched at different frequencies may be independent
from the switching frequency of the common arm circuit 24, and thus can be set as
appropriate.
[0163] Next, controlling the frequency in a case that the switching frequency of each switching
element is shifted toward the resonant frequency will be described. As described above,
generally, an inverter circuit of induction heating apparatuses switches an arm circuit
at a frequency higher than a resonant frequency of a resonant circuit so that the
phase of AC current flowing through a heating coil is delayed from the switching of
the arm circuit, whereby switching loss can be kept from increasing.
[0164] While the induction heating is in progress, a full resonance or a leading phase might
be achieved due to a change in the impedance of the resonant circuit as a result of
a cooking action such as pan flipping for example. When this happens, the current
flowing through a switching element or surge voltage may become large, and thus may
even result in breakage of a switching element of each arm circuit and the like. Thus,
when the frequency of the gate signal is shifted toward the resonant frequency, the
switching frequency is preferably controlled at a frequency higher than the resonant
frequency to guarantee prevention of leading phase.
[0165] To achieve this, for example, a threshold of a frequency and an error of the resonance
frequency of a load may be set in the control circuit 85 in advance, and the switching
frequency may be controlled to achieve the difference between the resonant frequency
and the switching frequency that is equal to or larger than the threshold of the frequency.
The control circuit 85 may constantly detect the resonant frequency of the load, control
the frequency of the gate signal by feedbacking the difference between the resonant
frequency and the switching frequency, and control the switching frequency to be equal
to or larger than the threshold of the frequency constantly.
[0166] The control circuit 85 may detect the voltage and the current output from the inverter
circuit 81, and feedback the phase difference between the voltage and the current
to control the switching frequency, so that the delay phase is constantly achieved.
When a leading phase is achieved with the switching frequency falling below the resonant
frequency, the control circuit 85 may perform a protective operation of stopping the
switching of each switching element to stop the inductive heating.
[0167] In the method described in this fifth embodiment, both of the input power to the
first heating coil 31 and the input power to the second heating coil 32 are controlled
by the frequency control. Note that the input power to one of the first heating coil
31 and the second heating coil 32 may be controlled by the PWM control or the phase
difference control described in the second or the third embodiment, and the other
one of the first heating coil 31 and the second heating coil 32 may be controlled
by the frequency control according to this fifth embodiment. The PWM control and the
frequency control may be combined, so that the frequency control is performed while
the PWM control is being performed.
Sixth Embodiment
[0168] FIG. 13 is a plan view illustrating a position of a heated object placed on a heating
coil to be inductively heated by an induction heating apparatus according to a sixth
embodiment of the present invention. FIG. 13(a) is a plan view illustrating a state
where a heated object 110b made of different materials is placed with the center of
the heated object 110b matching the center of the heating coil 30. FIG. 13(b) is a
plan view illustrating a state where the heated object 110b made of different materials
is placed with the center of the heated object 110b shifted from the center of the
heating coil 30.
[0169] The induction heating apparatus 100 according to this sixth embodiment has the configuration
and the like that are the same as those in the first embodiment, and the components
of the induction heating apparatus 100 described while being denoted with the same
reference numerals are the same as the counterparts in the first embodiment. In this
sixth embodiment, a difference from the induction heating apparatus 100 according
to the first embodiment will be described.
[0170] The induction heating apparatus 100 according to this sixth embodiment periodically
performs load detection to determine the material of the heated object placed on the
top plate 2. The load detection unit 11 of the induction heating apparatus 100 determines
the material of the heated object placed on each of the first heating coil 31 and
the second heating coil 32 and transmits the determination result to the control circuit
85, at an interval such as once in every few seconds for example. Based on the determination
result periodically transmitted from the load detection unit 11, the control circuit
85 controls the switching of the first arm circuit 21, the common arm circuit 24,
and the second arm circuit 27 of the inverter circuit 81, and the inverter circuit
81 supplies the AC currents to the first heating coil 31 and the second heating coil
32.
[0171] As illustrated in FIG. 3, the load detection unit 11 may be provided to the power
supply unit 82 through which the AC power source 9 is connected to the induction heating
apparatus 100. However, load detection performed by detecting the current input from
the AC power source 9 to the induction heating apparatus 100 is unable to determine
the material of the heated object placed on the first heating coil 31 and the material
of the heated object placed on the second heating coil 32 simultaneously, meaning
that a long period of time is required for the load detection and thus is not preferably
performed as the periodical load detection.
[0172] The load detection unit 11 preferably has a configuration capable of performing load
detection simultaneously on the heated object on the first heating coil 31 and on
the heated object on the second heating coil 32, with a current detection unit connected
in series with the first heating coil 31 and a current detection unit connected in
series with the second heating coil 32. When the current detection unit is connected
in series with each of the first heating coil 31 and the second heating coil 32, the
load detection unit 11 may determine the material of the heated object from the current
flowing through each of the heating coils inductively heating the heated object, and
periodically transmit the determination result to the control circuit 85.
[0173] A case is described below where the load detection unit 11 determines the material
of the heated object based on the currents flowing through the heating coils detected
by the current detection unit connected in series with the first heating coil 31 and
the current detection unit connected in series with the second heating coil 32. Note
that the configuration of the load detection unit 11 is not limited to this, and a
configuration of determining the material of the heated object based on the current
input from the AC power source 9 as illustrated in FIG. 3 may be employed.
[0174] In FIG. 13, the heating coil 30 includes the first heating coil 31 that inductively
heats the inner circumference side of the bottom section of the heated object 110b
and the second heating coil 32 that inductively heats the outer circumference side
of the bottom section of the heated object 110b. The heated object 110b is formed
by joining the magnetic metal section 112 made of magnetic metal such as iron on the
bottom section 111 of a pot such as a frying pan made of nonmagnetic metal such as
aluminum.
[0175] When the user operates the operation unit 5 of the induction heating apparatus 100,
with the heated object 110b placed on the heating coil 30 with the center of the heated
object 110b matching the center of the heating coil 30 as illustrated in FIG. 13(a),
to start the inductive heating for the heated object, the induction heating apparatus
100 determines the materials of the heated object on the first heating coil 31 and
the second heating coil 32, with the pulsating current flowing through the first heating
coil 31 and the second heating coil 32 as described in the first embodiment. Then,
based on the result of the determination by the load detection unit 11, the inverter
circuit 81 supplies the AC currents at the same frequency or different frequencies
to the first heating coil 31 and the second heating coil 32.
[0176] In the case illustrated in FIG. 13(a), the material of the heated object 110b placed
on the first heating coil 31 is magnetic metal and the material of the heated object
110b placed on the second heating coil 32 is also magnetic metal, and thus the inverter
circuit 81 supplies the AC currents at the same frequency to the first heating coil
31 and the second heating coil 32. In such a case, the control circuit 85 closes the
switch 44 of the first variable capacitor 41 so that the capacitor 42 and the capacitor
43 are connected in parallel with each other, and closes the switch 48 of the second
variable capacitor 45 so that the capacitor 46 and the capacitor 47 are connected
in parallel with each other, in the circuit diagram in FIG. 3.
[0177] When the inductances of the heating coils and the capacitances of the capacitors
are of values described as an example in the first embodiment, the resonant frequency
of the first resonant circuit including the first heating coil 31 and the first variable
capacitor 41 is 22.7 kHz and the resonant frequency of the second resonant circuit
including the second heating coil 32 and the second variable capacitor 45 is also
22.7 kHz in the state illustrated in FIG. 13(a). Thus, the inverter circuit 81 switches
the first arm circuit 21, the common arm circuit 24, and the second arm circuit 27
at 25 kHz to supply the AC current at 25 kHz to each of the first heating coil 31
and the second heating coil 32.
[0178] The load detection unit 11 detects each of the AC current at 25 kHz flowing through
the first heating coil 31 and the AC current at 25 kHz flowing through the second
heating coil 32 with the current detection unit, and determines that the material
of each of the heated objects placed on the first heating coil 31 and the second heating
coil 32 is magnetic metal. This determination result is a result of the determination
performed when the inductive heating for the heated object has started, and thus the
induction heating apparatus 100 continues to supply the AC current at 25 kHz to each
of the first heating coil 31 and the second heating coil 32.
[0179] Now, it is assumed that the positional shift has occurred with the center of the
heated object 110b shifted from the center of the heating coil 30 as illustrated in
FIG. 13(b), due to pan flipping or the other like action by the user. In this state,
the magnetic metal section 112 of the heated object 110b is placed on the first heating
coil 31, and thus the magnitude of the AC current flowing through the first heating
coil 31 remains unchanged. The magnetic metal section 112 of the heated object 110b
and the bottom section 111 made of nonmagnetic metal provided on the outer circumference
side of the magnetic metal section 112 are placed on the second heating coil 32, and
thus the inductance of the second heating coil 32 decreases, and the resistance of
the heated object on the second heating coil 32 also decreases.
[0180] As a result, the current flowing through the second heating coil 32 changes, and
thus the load detection unit 11 detects the change in the load on the second heating
coil 32. In this process, when the rate of the part of the heated object placed on
the second heating coil 32 made of nonmagnetic metal exceeds a predetermined amount,
the load detection unit 11 determines that the material of the heated object placed
on the second heating coil 32 is nonmagnetic metal.
[0181] The load detection unit 11 periodically determines the material of the heated object
on the first heating coil 31 and the material of the heated object on the second heating
coil 32 and transmits the determination result to the control circuit 85. Thus, when
the control circuit 85 recognizes that the material of the heated object on the second
heating coil 32 has changed from magnetic metal to nonmagnetic metal, the control
circuit 85 changes the capacitance of the second variable capacitor 45.
[0182] Specifically, the control circuit 85 opens the switch 48 of the second variable capacitor
45 to disconnect the capacitor 47 from the capacitor 46, resulting in the capacitance
of the second variable capacitor 45 being 0.024 µF. As illustrated in FIG. 13(b),
the heated object on the second heating coil 32 is not completely made of nonmagnetic
metal, and thus the inductance of the second heating coil 32 is larger than 200 µH
but is smaller than 300 µH. As a result, the resonant frequency of the second resonant
circuit including the second heating coil 32 and the second variable capacitor 45
becomes high.
[0183] The control circuit 85 outputs a gate signal for the switching element of each arm
circuit so that the inverter circuit 81 switches the second arm circuit 27 at a frequency
higher than the switching frequencies of the first arm circuit 21 and the common arm
circuit 24. The gate signal for the switching element of each arm circuit in such
a case is as described above in the first to the fourth embodiments. Thus, the bottom
section 111 made of nonmagnetic metal on the outer circumference side of the magnetic
metal section 112 of the heated object 110b can be inductively heated efficiently,
with the AC current at the first frequency supplied to the first heating coil 31 and
the AC current at the second frequency, higher than the first frequency, supplied
to the second heating coil 32. As a result, uniformity of the temperature of the bottom
section of the heated object can be improved even when the positional shift of the
heated object occurs.
Seventh Embodiment
[0184] FIG. 14 is a perspective view illustrating a state where an induction heating apparatus
according to a seventh embodiment of the present invention inductively heats two heated
objects. In FIG. 14, parts that are the same as the counterparts in FIG. 5 for the
first embodiment indicate the same or corresponding configurations, and thus the description
thereof will be omitted. The induction heating apparatus 100 according to this seventh
embodiment has the configuration and the like that are the same as those in the first
embodiment, and the components of the induction heating apparatus 100 described while
being denoted with the same reference numerals are the same as the counterparts in
the first embodiment. This seventh embodiment is different from the first embodiment
in a configuration where the first heating coil 31 and the second heating coil 32
are provided to different heating ports.
[0185] As illustrated in FIG. 13, the induction heating apparatus 100 has the first heating
coil 31 and the second heating coil 32 provided to respectively face the placement
position 3a and the placement position 3c displayed on the top plate 2. The first
variable capacitor 41 is connected in series with the first heating coil 31, so that
the first heating coil 31 and the first variable capacitor 41 form a first resonant
circuit. The second variable capacitor 45 is connected in series with the second heating
coil 32 so that the second heating coil 32 and the second variable capacitor 45 form
a second resonant circuit.
[0186] The inverter circuit 81 illustrated in the circuit diagram in FIG. 3 in the first
embodiment supplies AC currents to the first heating coil 31 and the second heating
coil 32. Thus, the first heating coil 31 is electrically connected between the output
terminal 23 of the first arm circuit 21 and the output terminal 26 of the common arm
circuit 24, and the second heating coil 32 is electrically connected between the output
terminal 29 of the second arm circuit 27 and the output terminal 26 of the common
arm circuit 24.
[0187] As illustrated in FIG. 14, a first heated object 110a inductively heated by the AC
current flowing through the first heating coil 31 is placed on the first heating coil
31 and a second heated object 110c inductively heated by the AC current flowing through
the second heating coil 32 is placed on the second heating coil 32. When the user
operates the operation unit 5 of the induction heating apparatus 100 to perform an
operation for inductively heating the first heated object 110a and the second heated
object 110c, the load detection unit 11 determines the material of the heated object
110a placed on the first heating coil 31 and the material of the heated object 110c
placed on the second heating coil 32.
[0188] When the load detection unit 11 determines that the material of the heated object
110a on the first heating coil 31 is magnetic metal such as iron and that the material
of the heated object 110c on the second heating coil 32 is nonmagnetic metal such
as aluminum, the control circuit 85 closes the switch 44 of the first variable capacitor
41 to connect the capacitor 42 and the capacitor 43 in parallel with each other, and
opens the switch 48 of the second variable capacitor 45 to disconnect the capacitor
47 from the capacitor 46. As described in the first embodiment, the first arm circuit
21 and the common arm circuit 24 are switched at the first frequency and the second
arm circuit 27 is switched at the second frequency.
[0189] The first frequency may be 25 kHz for example, and the second frequency may be 75
kHz for example. As a result, the AC current at 25 kHz flows through the first heating
coil 31 and the first heated object 110a made of magnetic metal is inductively heated
by alternating fluxes at 25 kHz. The AC current at 75 kHz flows through the second
heating coil 32 and the second heated object 110c made of nonmagnetic metal is inductively
heated by alternating fluxes at 75 kHz.
[0190] When the first heated object 110a and the second heated object 110c are both made
of magnetic metal or nonmagnetic metal, the switching frequencies of the first arm
circuit 21, the common arm circuit 24, and the second arm circuit 27 may be set to
be the same, so that the frequencies of the AC current flowing through the first heating
coil 31 and of the AC current flowing through the second heating coil 32 are set to
be the same.
[0191] The first variable capacitor 41 and the second variable capacitor 45 may not necessarily
be variable capacitors and may be capacitors with a fixed capacitance. In such a case,
for example, the heating port provided with the first heating coil 31 serves as the
heating port for inductively heating the heated object made of magnetic metal and
the heating port provided with the second heating coil 32 serves as the heating port
for inductively heating the heated object made of nonmagnetic metal. The capacitor
connected in series with the first heating coil 31 is formed by connecting the capacitor
42 and the capacitor 43 in parallel with each other with the switch 44 omitted from
the first variable capacitor 41, and the capacitor connected in series with the second
heating coil 32 is formed to include the capacitor 46 only, with the switch 48 and
the capacitor 47 omitted from the second variable capacitor 45. The first arm circuit
21 and the common arm circuit 24 may be switched at the first frequency and the second
arm circuit 27 may be switched at the second frequency to supply the AC current at
the first frequency to the first heating coil 31 and to supply the AC current at the
second frequency to the second heating coil 32.
[0192] The first to the seventh embodiments of the present invention are described above.
The configurations described in these first to the seventh embodiments of the present
invention can be combined with each other.
DESCRIPTION OF REFERENCE SYMBOLS
[0193]
- 11
- LOAD DETECTION UNIT
- 21
- FIRST ARM CIRCUIT
- 21a
- FIRST SWITCHING ELEMENT
- 23
- OUTPUT TERMINAL
- 24
- COMMON ARM CIRCUIT
- 24a
- FIRST SWITCHING ELEMENT
- 26
- OUTPUT TERMINAL
- 27
- SECOND ARM CIRCUIT
- 21a
- SECOND SWITCHING ELEMENT
- 29
- OUTPUT TERMINAL
- 31
- FIRST HEATING COIL
- 32
- SECOND HEATING COIL
- 41
- FIRST VARIABLE CAPACITOR
- 45
- SECOND VARIABLE CAPACITOR
- 81
- INVERTER CIRCUIT
- 100
- INDUCTION HEATING APPARATUS