[0001] The present invention relates to a steel sheet suitably used for the production of
a reserve tank, an offshore structure and the like. In detail, the present invention
relates to a high strength steel sheet capable of securing a strength of 550 MPa or
more before and even after a post welding heat treatment performed to reduce residual
stress at a welded part after welding.
[0002] When welded structures are produced, such as a reserve tank for crude oil, ethylene,
liquefied petroleum gas (LPG) and the like, and an offshore structure, a post weld
heat treatment (hereinafter sometimes referred to as PWHT) of holding a welded steel
sheet at around 600°C for several hours is sometimes performed to reduce residual
stress at a welded part after welding of a steel sheet. In PWHT, an object is held
at a high temperature for a long period, so that the metallographic structure of the
steel sheet changes to decrease the strength of the steel sheet in some cases.
[0003] Patent Literature 1 discloses a technique for securing the strength after PWHT at
high level. The steel sheet disclosed in Patent Literature 1 is characterized in that
the amounts of particularly Nb, V, Mo and C in component composition are adjusted
to satisfy a predetermined relationship, and the steel sheet has a metallographic
structure in which the bainite fraction is 90 area% or more. Further, Patent Literature
1 describes that a carbide of Nb and Mo is formed in the steel sheet before PWHT to
suppress a decrease in the strength after PWHT. Further, in order to obtain a bainite
structure with an extremely low amount of C, Cr is contained as an essential component
in the range of 0.5 to 2.0%. In examples of Patent Literature 1, PWHT of holding the
steel sheet at 600°C for a period of sheet thickness (inch) × 1 hour is performed
twice, and the holding period is about 8 hours at a maximum.
[0004] Patent Literature 2 describes a hot coil for line pipe and manufacturing method therefore.
Patent Literature 3 discloses a high tempering parameter PWHT embrittlement resistant,
extra thick cryogenic steel plate and manufacture method thereof.
[0006] Along with the growth in size of a welded structure, the thickness of a steel sheet
used as a material has been increased. An increased thickness of the steel sheet prolongs
the period required for a temperature rise to a prescribed temperature according to
the position of a welded structure when a heat treatment is performed. Further, when
adjustment or the like is necessary after welding, PWHT is required again, further
prolonging the heat treatment period. On the other hand, when PWHT is performed at
a high temperature or for a long period, the strength of the steel sheet is significantly
decreased. Therefore, the steel sheet is required to secure predetermined strength
even when PWHT is performed for a long period. Specifically, it is desired to secure
high strength even when PWHT is performed for 15 hours or more.
[0007] In the examples of Patent Literature 1, however, only the margin of change in tensile
strength between before and after the heat treatment is measured for steel sheets
held for about 8 hours at a maximum, and the margin of change in tensile strength
is not measured for a steel sheet when PWHT is performed for 15 hours or more as described
above. Therefore, it is possible that the steel sheets decrease in the strength not
to secure the predetermined strength when prolonged PWHT is performed.
[0008] The present invention has been made with focused attention on the above-described
circumstances, and an object of the present invention is to provide a high strength
steel sheet capable of securing high strength before and even after PWHT is performed
for a long period, for example, of 15 hours or more.
[0009] The invention is defined in the appended claims.
[0010] The present invention also encompasses a high strength welded structure obtained
by subjecting the high strength steel sheet to a heat treatment.
[0011] According to the present invention, there can be provided a high strength steel that
has high strength before and after PWHT, because the component composition and metallographic
structure of the steel sheet are appropriately controlled, so that the strength of
the steel sheet is unlikely to decrease or is rather improved even when PWHT is performed
for a long period, for example, of 15 hours or more.
[0012] Fig. 1 is a graph showing the relationship between the solid solution equivalent
A and the tensile strength (TS) after PWHT.
[0013] As disclosed in Patent Literature 1, strengthening by transformation with use of
a bainite structure is known as means for securing the strength of a steel sheet.
Patent Literature 1, however, is a technique of using dislocations introduced during
transformation, and therefore, when PWHT is performed for about 15 hours or more,
the dislocations may possibly be integrated and annihilated to decrease the strength
of the steel sheet.
[0014] Therefore, the present inventor has studied a method for securing the strength of
a steel sheet even when PWHT is performed for a long period, for example, of 15 hours
or more while setting ferrite as a main structure of the metallographic structure
of the steel sheet. A reason for setting ferrite as a main structure is that the ferrite
has less dislocations introduced, and therefore, a decrease in the strength is considered
to be avoided which is caused by the integration and annihilation of the dislocations,
even when prolonged PWHT is performed.
[0015] Further, the present inventor has focused on carbide dispersion strengthening by
Nb and Mo as means for securing the strength after PWHT. As in Patent Literature 1,
however, a method of precipitating a carbide of Nb and Mo in the steel sheet before
PWHT to improve the strength, the carbide is coarsened and aggregated when PWHT is
performed for a long period, so that the carbide does not contribute to the improvement
in the strength, anyhow leading to a decrease in the strength.
[0016] As a result of further various studies conducted by the present inventor, the present
inventor has found that high strength can be secured before and after PWHT by setting
the ferrite as a main structure of the metallographic structure of the steel sheet,
and appropriately adjusting the chemical component composition so that a carbide containing
at least one selected from the group consisting of Nb and Mo is estimated to be precipitated
in a predetermined amount or more through prolonged PWHT while a predetermined amount
or more of bainite has been generated. Thus, the present invention has been completed.
Particularly, it has been made clear that when Nb and Mo are solid-solved or are dispersed
as extremely fine carbide in a step before PWHT, the carbide can be grown into a size
for contributing to the carbide dispersion strengthening by performing PWHT for a
long period, and high strength can be secured by the carbide dispersion strengthening.
In the present specification, performing PWHT for a long period means performing PWHT
for, for example, 15 hours or more.
[0017] Hereinafter, a high strength steel sheet according to the present invention will
be described in detail.
[0018] The high strength steel sheet according to the present invention has an elemental
composition and microstructure as defined in claim 1.
[0019] First, the high strength steel sheet according to the present invention is described
in terms of the metallographic structure. In the present specification, the high strength
means a tensile strength of 550 MPa or more.
[0020] The metallographic structure of the high strength steel sheet of the present invention
has a proportion of ferrite: 60 area% or more, bainite: 4 area% or more and other
structures (like pearlite, island martensite): 10 area% or less, relative to the entire
structure.
[Ferrite: 60 area% or more]
[0021] With the ferrite accounting for 60 area% or more of the entire structure, high strength
can be secured even when PWHT is performed for a long period. With the amount of the
ferrite decreased and the bainite fraction excessively increased in the entire structure,
excessive dislocations are integrated and annihilated by performing PWHT for a long
period to largely decrease the strength. Therefore, in the present invention, the
ferrite is set to 60 area% or more, preferably 65 area% or more, more preferably 70
area% or more, further preferably 75 area% or more. The upper limit of the ferrite
fraction is 96 area% or less to secure 4 area% or more of the bainite as described
later. The ferrite fraction is preferably 90 area% or less.
[Bainite: 4 area% or more]
[0022] In the metallographic structure of the steel sheet according to the present invention,
the ferrite is 60 area% or more as described above; however, an excessively high ferrite
fraction greatly decreases the strength of the steel sheet. Therefore, in the present
invention, the bainite fraction in the entire structure is set to 4 area% or more,
preferably 5 area% or more, more preferably 10 area% or more, to increase the strength
of the steel sheet. With the bainite fraction excessively increased, however, 60 area%
or more of the ferrite cannot be secured, and the strength after prolonged PWHT is
decreased due to the increased bainite. Therefore, in the present invention, the bainite
fraction is 40 area% or less, preferably 30 area% or less, more preferably 20 area%
or less.
[0023] The metallographic structure of the steel sheet according to the present invention
is basically formed of the ferrite and the bainite, while the metallographic structure
may also contain, for example, pearlite, island martensite (M-A) and the like as other
structure, as long as the effect of the present invention is not inhibited.
[0024] The fraction of the other structure in the entire structure is 10 area% or less,
for example.
[0025] The metallographic structure of the steel sheet according to the present invention
may be exposed in a cross section at a position of t/4, with the thickness of the
steel sheet as t (mm), and subjected to mirror polishing. Then, a test piece may be
collected, etched with a nital solution, and then observed with an optical microscope,
to measure the ferrite fraction and the bainite fraction by image analysis. With the
observation magnification set to 400 times and the number of observation fields set
to 5, the average values of the ferrite fractions and the bainite fractions may be
obtained which are measured in the fields.
[0026] The ferrite fraction in the metallographic structure may be measured by the image
analysis with use of an optical microscope as described above, while a value obtained
by deducting the bainite fraction from 100% may be regarded as the ferrite fraction
as the ferrite and the bainite are basically generated in the high strength steel
sheet of the present invention.
[0027] Next, the estimated precipitation amount P
0 will be described.
[0028] The estimated precipitation amount P
0 indicates a maximum amount of precipitate that can be, on the basis of the amounts
of Mo, Nb and C included in the steel sheet, estimated to be precipitated as a carbide
containing at least one selected from the group consisting of Nb and Mo by, for example,
PWHT.
[0029] The estimated precipitation amount P
0 is a calculated value obtained from the amounts of Nb, Mo and C on the basis of the
following formula (1). The estimated precipitation amount P
0 is to be an index for predicting the strength after PWHT. Such a steel sheet whose
value P
0 is appropriately controlled is subjected to prolonged PWHT to precipitate a carbide
containing at least one selected from the group consisting of Nb and Mo, so that the
strength of the steel sheet can be increased by the carbide dispersion strengthening.
[0030] The carbide containing at least one selected from the group consisting of Nb and
Mo is not particularly limited as long as the carbide includes at least Nb or Mo.
Examples of the carbide include, in addition to a Nb carbide and a Mo carbide, a composite
carbide containing both Nb and Mo. The carbide also includes a carbonitride in which
nitrogen is bonded to a carbide, and the composite carbide also includes a composite
carbonitride in which nitrogen is bonded to a composite carbide.

[0031] The details that the estimated precipitation amount P
0 represented by the formula (1) has been derived are as follows.
[0032] A Mo carbide is represented by MoC and a Nb carbide is represented by NbC, and the
precipitation amount of the MoC and the NbC is represented by the following formula
(a) on the basis of the mass ratio of each element.

[0033] In the formula (a), α, β and γ represent constant numbers, and [ ] represents the
content of each element (mass%).
[0034] In order to determine the constant numbers, the tensile strength after PWHT has
been measured with use of steel sheets obtained by changing only the content of Mo
or Nb while the content of the other element is kept the same. The conditions for
the measurement of the tensile strength are made the same as in examples described
later. A straight line graph has been made with the content of Nb or Mo as a horizontal
axis and the tensile strength after PWHT as a vertical axis, α has been determined
as 340, β as 0.6 and γ as 22 from the ratio of the gradient of the straight line to
determine a parameter x represented by the following formula (b).

[0035] Next, in the formula (a), C
1 is a value determined on the basis of the relationship between the amount of C [C]
and the total of the amount of Mo [Mo] and the amount of Nb [Nb] included in the steel.
[0036] That is, when [C] ≥ 12/95 × ([Mo] + [Nb]), the minimum necessary amount of C for
generating the MoC and the NbC is included in the steel, and therefore, C
1 is derived from the following formula (2).

[0037] On the other hand, when [C] < 12/95 × ([Mo] + [Nb]), the amount of C included in
the steel is below the amount of C necessary for generating the MoC and the NbC, and
therefore, C
1 is derived from the following formula (3).

[0038] Here, 12/95 is a coefficient determined in consideration of the atomic weight of
C, Mo and Nb.
[0039] The value P
0 is derived from the formula (1) on the basis of the thus derived parameter x and
C
1.
[0040] In the present invention, the value P
0 is set to 1.50 or more. The threshold 1.50 of the value P
0 is a value determined on the basis of various experimental results. The value P
0 is set to preferably 2 or more, more preferably 3 or more. The upper limit of the
value P
0 is 29.75 or less which is determined on the basis of the maximum value of the amount
of Mo and the maximum value of the amount of Nb. The value P
0 is preferably 25 or less, more preferably 20 or less, further preferably 15 or less,
particularly preferably 10 or less.
[0041] Further, in the high strength steel sheet according to the present invention, a solid
solution equivalent A represented by the following formula (5) satisfies a value of
0.50 or more. Here, when a precipitation amount P
1 is calculated by the following formula (4), from an average interval λ (µm) between
carbides containing at least one selected from the group consisting of Nb and Mo,
the solid solution equivalent A is obtained from the estimated precipitation amount
P
0 and the precipitation amount P
1 by the following formula (5).

[0042] The solid solution equivalent A indicates the total amount of Mo and Nb solid-solved
in the high strength steel sheet, and is an index for predicting the strength of the
steel sheet after PWHT. The threshold 0.50 of the solid solution equivalent A is a
value determined on the basis of various experimental results. With the solid solution
equivalent A set to 0.50 or more, a solid-solved Mo and a solid-solved Nb are precipitated
as a carbide when PWHT is performed for a long period, so that the strength of a welded
structure can be increased by the carbide dispersion strengthening. On the other hand,
with the solid solution equivalent A below 0.50, the amounts of Mo, Nb and C are insufficient
or Mo and Nb are already precipitated as a carbide, and therefore, the carbide is
coarsened or aggregated when PWHT is performed for a long period, so that the strength
of a welded structure is decreased. The solid solution equivalent A is 0.50 or more,
preferably 1 or more, further preferably 2 or more. The upper limit of the solid solution
equivalent A is not particularly limited, and is preferably 15 or less, more preferably
10 or less, for example. The solid solution equivalent A also includes a fine Mo carbide
and a fine Nb carbide that have a particle diameter of 10 nm or less. The fine carbide
having a particle diameter of 10 nm or less exceeds the limits of detection by observation
with use of a transmission electron microscope described later, and is considered
not to contribute to the carbide dispersion strengthening.
[0043] Here, the details that the solid solution equivalent A represented by the formula
(5) has been derived are as follows.
[0044] When the precipitation amount P
1 is calculated, by the formula (4), from an average interval λ (µm) between carbides
containing at least one selected from the group consisting of Nb and Mo, the solid
solution equivalent A is a value obtained by deducting the precipitation amount P
1 from the estimated precipitation amount P
0. The precipitation amount P
1 indicates the amounts of a Nb carbide and a Mo carbide that are actually precipitated
in the steel sheet. Therefore, the total of amounts of Nb and Mo solid-solved in the
steel sheet can be calculated by deducting the precipitation amount P
1 from the estimated precipitation amount P
0. A solid-solved Nb and a solid-solved Mo are precipitated as a carbide by performing
PWHT for a long period, contributing to the improvement in the strength of a welded
structure after PWHT by the carbide dispersion strengthening.
[0045] The precipitation amount P
1 can be calculated by the formula (4).
[0046] In the formula (4), λ can be calculated on the basis of the following formula (c).

[0047] In the formula (c), λ represents an average interval (µm) between carbides containing
at least one selected from the group consisting of Nb and Mo, and f represents an
average volume fraction (volume%) of the carbide, and d represents an average particle
diameter (µm) of the metallographic structure.
[0049] In the formula (c), the average volume fraction f of the carbide can be calculated
on the basis of the area of the carbide and the number of particles of the carbide
measured by observing a cross section at a position of t/4, with the thickness of
the steel sheet as t (mm), with use of, for example, a transmission electron microscope.
The observation magnification may be, for example, 30000 times, and the number of
observation fields may be 10.
[0050] In the formula (c), the average particle diameter d of the metallographic structure
means the average value of circle equivalent diameters of the metallographic structure
that are identified in an observation field. In the observation field, for example,
when a ferrite structure is identified, particle diameters of the ferrite may be measured,
and when a bainite structure is identified, particle diameters of the bainite may
be measured. Then, the average value of the particle diameters may be calculated.
The observation magnification may be, for example, 30000 times, and the number of
observation fields may be 10.
[0051] The particle diameter d of the metallographic structure is considered to be substantially
constant by conducting controlled rolling described later. Thus, the average interval
λ between the carbides can be obtained on the basis of the average volume fraction
f of the carbide and the average particle diameter d of the metallographic structure
by the formula (c).
[0052] On the other hand, the precipitation amount P
1 of a carbide per unit mass can be represented by the following formula (A) with use
of the average volume fraction of the carbide, the average volume fraction of the
metallographic structure, and the mass per unit volume.

[0053] Here, f is the average volume fraction (volume%) of the carbide, F is the average
volume fraction (volume%) of the metallographic structure, n
1 is specific gravity (kg/m
3) of the carbide, and n
2 is specific gravity (kg/m
3) of the metallographic structure. For the specific gravity n
1 of the carbide, component analysis may be conducted for carbide particles identified
in an observation field, the specific gravity of each of the carbide particles is
obtained, and the average value of the specific gravity may be substituted. For the
specific gravity n
2 of the metallographic structure, the specific gravity of iron may be substituted.
[0054] The average volume fraction F of the metallographic structure is represented by
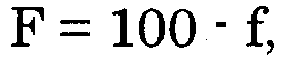
and therefore, the formula (A) can be rewritten as the following formula (B).

[0055] The present inventor has prepared steel sheets obtained by variously changing the
amounts of Mo and Nb and measured the precipitation amount of a carbide to learn that
the formula (B) can be represented by the following formula (4) with use of the interval
λ between carbides.

[0056] In the high strength steel sheet according to the present invention, the value P
0 calculated on the basis of the amounts of Mo, Nb and C included in the steel is 1.50
or more, and it is also necessary to appropriately control the chemical component
composition. Hereinafter, the chemical components of the high strength steel sheet
will be described.
[C: 0.02 to 0.07%]
[0057] C is an element that is necessary for increasing the strength of the steel sheet.
Also, C is an element that is necessary for precipitating a carbide to suppress a
decrease in the strength after PWHT. In the present invention, the amount of C is
0.02% or more, preferably 0.025% or more, more preferably 0.030% or more. Excessive
addition of C, however, is likely to generate the bainite. Excessive generation of
the bainite causes integration and annihilation of dislocations by prolonged PWHT
to largely decrease the strength. In the present invention, the amount of C is 0.07%
or less, preferably 0.065% or less, more preferably 0.06% or less, particularly preferably
0.055% or less.
[Si: 0.1 to 0.4%]
[0058] Si is an element that acts as a deoxidizing agent during smelting of steel and has
an effect of increasing the strength of the steel. For exhibition of such an action,
Si is contained in an amount of 0.1% or more, preferably 0.15% or more, more preferably
0.2% or more in the present invention. An excessive amount of Si, however, deteriorates
HAZ toughness. Therefore, the amount of Si is 0.4% or less, preferably 0.37% or less,
more preferably 0.35% or less in the present invention.
[Mn: 1.2 to 2%]
[0059] Mn is an element that effectively acts for increasing the strength of the steel sheet.
In the present invention, the amount of Mn is 1.2% or more, preferably 1.3% or more,
more preferably 1.4% or more. An excessive amount of Mn, however, excessively generates
the bainite to decrease the strength after PWHT is performed for a long period. In
the present invention, the amount of Mn is 2% or less, preferably 1.8% or less, more
preferably 1.6% or less.
[P: more than 0% and 0.02% or less]
[0060] P is an inevitable impurity and is an element that is segregated in crystal grains
and decreases the ductibility and toughness of the steel sheet. In the present invention,
the amount of P is 0.02 or less, preferably 0.015% or less, more preferably 0.01%
or less, particularly preferably 0.008% or less. It is preferred that the amount of
P is as less as possible; however, it is industrially difficult to realize 0% of the
amount of P.
[S: more than 0% and 0.005% or less]
[0061] S is an inevitable impurity and is an element that forms various inclusions by bonding
to an alloy element in the steel to decrease the ductibility and toughness of the
steel sheet. In the present invention, the amount of S is 0.005% or less, preferably
0.004% or less, more preferably 0.003% or less. It is preferred that the amount of
S is as less as possible; however, it is industrially difficult to realize 0% of the
amount of S.
[Cu: 0.1 to 0.7%]
[0062] Cu is an element that acts for increasing the strength of the steel sheet. In the
present invention, the amount of Cu is 0.1% or more, preferably 0.12% or more, more
preferably 0.15% or more. An excessive amount of Cu, however, easily causes generation
of a crack during hot working. In the present invention, the amount of Cu is 0.7%
or less, preferably 0.65% or less, more preferably 0.5% or less.
[Al: 0.01 to 0.08%]
[0063] Al is an element that acts as a deoxidizing agent during smelting of steel. In the
present invention, the amount of Al is 0.01% or more, preferably 0.015% or more, more
preferably 0.020% or more. An excessive amount of Al, however, inhibits the cleanliness
of the steel sheet to decrease the strength. In the present invention, the amount
of Al is 0.08% or less, preferably 0.06% or less, more preferably 0.04% or less.
[Ni: 0.45 to 0.85%]
[0064] Ni is an element that is necessary for lowering a ferrite transformation start temperature,
accelerating the generation of the bainite, and increasing the strength of the steel
sheet. In the present invention, the amount of Ni is 0.45% or more, preferably 0.5%
or more. An excessive amount of Ni, however, excessively generates the bainite to
suppress the generation of the ferrite, decreasing the strength of the steel sheet
after PWHT is performed for a long period. In the present invention, the amount of
Ni is 0.85% or less, preferably 0.75% or less, more preferably 0.65% or less.
[Mo: 0.01 to 0.25%]
[0065] Mo is an element that is necessary for generating the bainite. Also, Mo is an important
element that precipitates a carbide after PWHT is performed for a long period to contribute
to the improvement in the strength of the steel sheet after PWHT. In the present invention,
the amount of Mo is 0.01% or more, preferably 0.1% or more, more preferably 0.15%
or more. An excessive amount of Mo, however, excessively generates the bainite to
suppress the generation of the ferrite, decreasing the strength of the steel sheet
after PWHT is performed for a long period. In the present invention, the amount of
Mo is 0.25% or less, preferably 0.23% or less, more preferably 0.20% or less.
[Nb: 0.015 to 0.05%]
[0066] As with Mo, Nb is an important element that precipitates a carbide after PWHT is
performed for a long period to contribute to the improvement in the strength of the
steel sheet after PWHT. In the present invention, the amount of Nb is 0.015% or more,
preferably 0.020% or more. An excessive amount of Nb, however, deteriorates HAZ toughness.
In the present invention, the amount of Nb is 0.05% or less, preferably 0.048% or
less, more preferably 0.045% or less.
[Ti: 0.005 to 0.025%]
[0067] Ti is an element that is likely to form a nitride and is an element that is necessary
to precipitate fine TiN, so that crystal grains are refined to increase the toughness
of the steel sheet. In the present invention, the amount of Ti is 0.005% or more,
preferably 0.007% or more, more preferably 0.009% or more. An excessive amount of
Ti, however, decreases HAZ toughness. In the present invention, the amount of Ti is
0.025% or less, preferably 0.02% or less, more preferably 0.015% or less.
[Ca: 0.0005 to 0.003%]
[0068] Ca is an element that is necessary for controlling the morphology of an inclusion
in the steel to improve the toughness of the steel sheet. In the present invention,
the amount of Ca is 0.0005% or more, preferably 0.0008% or more, more preferably 0.001%
or more. An excessive amount of Ca, however, causes coarsening of the inclusion to
decrease HAZ toughness. In the present invention, the amount of Ca is 0.003% or less,
preferably 0.0027% or less, more preferably 0.0025% or less.
[N: 0.001 to 0.01%]
[0069] N is an element that is necessary to precipitate fine TiN by bonding to Ti, so that
crystal grains are refined to increase the toughness of the steel sheet. In the present
invention, the amount of N is 0.001% or more, preferably 0.003% or more, more preferably
0.004% or more. An excessive amount of N, however, causes coarsening of the TiN to
deteriorate HAZ toughness. In the present invention, the amount of N is 0.01% or less,
preferably 0.008% or less, more preferably 0.007% or less.
[0070] The chemical components in the steel sheet of the present invention are as described
above, and the balance is iron and inevitable impurities such as O (oxygen).
[0071] The steel sheet of the present invention may contain, in addition to the chemical
components described above, the following elements as necessary.
[At least one selected from the group consisting of Cr: 0.001% or more and 0.2% or
less, V: 0.0001% or more and 0.02% or less, and B: 0.0001% or more and 0.0010% or
less]
[0072] All of Cr, V and B are elements that precipitate a carbonitride to contribute to
the improvement in the strength of the steel sheet. For effective exhibition of such
an action, the amount of Cr is 0.001% or more, preferably 0.005% or more. The amount
of V is 0.0001% or more, preferably 0.0005% or more. The amount of B is 0.0001% or
more, preferably 0.0005% or more. Excessive addition of Cr or V, however, decreases
HAZ toughness. In the present invention, the amount of Cr is 0.2% or less, preferably
0.1% or less, further preferably 0.05% or less. The amount of V is 0.02% or less,
preferably 0.01% or less, further preferably 0.005% or less. An excessive amount of
B excessively generates the bainite to decrease the strength after PWHT is performed
for a long period. In the present invention, the amount of B is 0.001% or less, preferably
0.0005% or less.
[0073] Next, a method for producing a high strength steel sheet according to the present
invention will be described.
[0074] In the steel sheet of the present invention, the component composition is appropriately
controlled as described above, and the production conditions are not particularly
limited, while it is recommended that steel that satisfies the component composition
described above be smelted according to a usual method and a resultant steel ingot
be subjected to controlled rolling and controlled cooling so that the solid solution
equivalent A satisfies the predetermined range. That is, with the solid solution equivalent
A satisfying the predetermined range, the precipitation behavior of Mo and Nb can
be controlled to secure the high strength. Therefore, it is desirable to effectively
make use of the controlled rolling and the controlled cooling. A production technique
that combines the controlled rolling with the controlled cooling is referred to as
a thermo-mechanical control process (hereinafter, sometimes referred to as a TMCP),
and steel that is produced by this production technique is sometimes referred to as
a TMCP steel sheet.
[0075] Specifically, the TMCP steel sheet can be produced by rolling at a cumulative rolling
reduction of 5 to 60% in the temperature range at a position of t/4 of 900 to 800°C,
with the thickness of the steel ingot as t (mm), followed by cooling from a starting
temperature at the position of t/4 of higher than 670°C to room temperature.
[0076] With the cumulative rolling reduction in the temperature range at the position of
t/4 of 900 to 800°C set to 5% or more, a deformation band which is to be a transformation
core of the ferrite can be introduced in austenite grains, so that the generation
of the ferrite can be encouraged. The cumulative rolling reduction is preferably 10%
or more, further preferably 15% or more. A cumulative rolling reduction of more than
60%, however, prolongs the time required for the rolling, leading to a decrease in
the productivity. In the present invention, the cumulative rolling reduction is 60%
or less, preferably 50% or less, further preferably 45% or less.
[0077] The resultant rolled steel sheet is cooled from a starting temperature at the position
of t/4 of higher than 670°C to room temperature. With the cooling start temperature
set to higher than 670°C, the coarsening of the ferrite can be suppressed. The cooling
start temperature may be preferably higher than 700°C. The upper limit of the cooling
start temperature is the same as a rolling finish temperature, for example, 850°C.
[0078] The cooling rate from the cooling start temperature to room temperature is not particularly
limited, and for example, the steel sheet may be cooled from the cooling start temperature
to the temperature range of higher than 300°C to lower than 500°C at an average cooling
rate of 5 to 30°C/sec and air-cooled from the temperature at which the cooling has
been stopped to room temperature. For example, the steel sheet may be water-cooled
from the cooling start temperature to the temperature range of higher than 300°C to
lower than 500°C.
[0079] The thickness of the steel sheet of the present invention is not particularly limited,
and the thickness may be, for example, 10 mm or more, further 20 mm or more, particularly
30 mm or more. The upper limit of the thickness of the steel sheet is not also particularly
limited, and the thickness may be, for example, 150 mm or less, further 120 mm or
less, particularly 100 mm or less.
[0080] The steel sheet according to the present invention has a high tensile strength of,
for example, 550 MPa or more.
[0081] The present invention also encompasses a welded structure obtained by welding the
steel sheet, and then subjecting the steel sheet to a heat treatment. The welded structure
of the present invention is characterized in that the high strength of the steel sheet
is retained as it is even after a heat treatment. For example, in a case of a steel
sheet having a tensile strength of 550 MPa or more, a welded structure thereof can
also retain the high tensile strength.
Examples
[0082] Hereinafter, the present invention will be described more specifically with reference
to examples. The present invention is not limited by the following examples.
[0083] Steel was smelted which contained the chemical components shown in Table 1 below
with the balance being iron and inevitable impurities, and steel ingots were produced
according to a usual method. Each of the resultant steel ingots was subjected to controlled
rolling and controlled cooling to produce a TMCP steel sheet having a thickness of
64 mm. Specifically, the controlled rolling was performed in the temperature range
at a position of t/4 of 900 to 800°C, with the thickness of the steel ingot as t (mm),
so that the cumulative rolling reduction was as shown in Table 2 below. The controlled
cooling was performed by, after the rolling, starting to cool a resultant steel sheet
from the temperature at the position of t/4 shown in Table 2. The steel sheet was
water-cooled from the cooling start temperature to the temperature range of 380 to
430°C at an average cooling rate of about 7°C/sec, and air-cooled from a cooling stop
temperature in the temperature range of 380 to 430°C to room temperature.
[0084] On the basis of the amounts of Mo and Nb shown in Table 1, a Z value was calculated
by the following formula (e), and the result is shown in Table 2.

[0085] The Z value was compared with the amount of C [C] shown in Table 1, and the Z value
was set for a value C
1 when [C] ≥ Z, and [C] was set for the value C
1 when [C] < Z. The determined value C
1 is shown in Table 2.
[0086] On the basis of the amounts of Mo and Nb shown in Table 1 below and the above value
C
1, a value P
0 was calculated by the following formula (1). The calculation result is shown in Table
2.

[0087] Next, the cross section at a position corresponding to 1/4 the thickness of the resultant
TMCP steel sheet was observed at an observation magnification of 30000 times with
use of a transmission electron microscope. A carbide that was observed in an observation
field and contained at least one selected from the group consisting of Nb and Mo was
measured in terms of the number of the carbide and the area ratio of the carbide to
the area of the observation field. The number of observation fields was 10. In the
present specification, the area ratio of the carbide was recognized as a volume fraction
f (%) of the carbide.
[0088] Next, the resultant TMCP steel sheet was measured in terms of its metallographic
structure.
[0089] The steel sheet was exposed in the cross section at the position corresponding to
1/4 the thickness of the steel sheet and was subjected to mirror polishing. Then,
a test piece was collected and etched with a nital solution. After the etching, the
test piece was observed at an observation magnification of 400 times with use of an
optical microscope, and was subjected to image analysis to measure the bainite fraction.
With the area of the observation field as 100%, a value obtained by deducting the
bainite fraction from 100% was determined as a ferrite fraction. With the number of
observation fields set to 5, the average values of the bainite fractions and the ferrite
fractions which were measured in the each observation fields were obtained, respectively.
The results are shown in Table 2.
[0090] Further, the particle diameter of the ferrite or the bainite that was identified
in the observation field was measured and the average value d (µm) of the particle
diameters in the 5 fields was obtained.
[0091] On the basis of the volume fraction f (%) of the carbide and the average value d
(µm) of the particle diameters, the interval between the carbides was calculated by
the following formula (c).

[0092] A value P
1 calculated by dividing 0.7 by λ is also shown in Table 2.
[0093] On the basis of the values P
0 and P
1, a solid solution equivalent A was obtained by the following formula (5). The results
are shown in Table 2.

[0094] Next, a test piece for a tensile test defined in ASTM A370 was collected from a position
corresponding to 1/4 the thickness of the resultant TMCP steel sheet in a direction
orthogonal to the rolling direction, and the tensile test was conducted to measure
the tensile strength. The measurement result is shown in Table 2 as the tensile strength
before PWHT.
[0095] Next, PWHT heat treatment was performed by heating the test piece to a temperature
of 595°C and then holding the test piece for 19 hours. The tensile strength of the
test piece after the heat treatment was measured in the same procedure as described
above. The measurement result is shown in Table 2 as the tensile strength after PWHT.
[0096] In the present invention, a steel sheet having a tensile strength of 550 MPa or more
both before and after the heat treatment was determined to be acceptable, and a steel
sheet having a tensile strength of less than 550 MPa even either before or after the
heat treatment was determined to be unacceptable.
[0097] Fig. 1 shows the relationship between the solid solution equivalent A calculated
on the basis of the formula (5) and the tensile strength (TS) after PWHT. In order
to show the significance for specifying the solid solution equivalent A, the results
of the steel sheets Nos. 1 to 8 shown as invention examples in Table 2 are plotted
in Fig. 1, and only the steel sheets Nos. 9 to 11 among the steel sheets Nos. 9 to
15 shown as comparative examples are plotted in Fig.1, whose solid solution equivalent
A fell outside the range recommended in the present invention.
[0098] The following conclusion can be derived from the following Table 2 and Fig. 1.
[0099] Nos. 1 to 8 are invention examples that satisfy the requirements of the present invention.
That is, the predetermined metallographic structure is obtained and the estimated
precipitation amount P
0 also satisfies the predetermined range to achieve a high tensile strength of 550
MPa or more. Further, the steel sheets can secure a tensile strength of 550 MPa or
more even after prolonged PWHT as long as 19 hours.
[0100] In contrast, Nos. 9 to 15 are comparative examples that do not satisfy any of the
requirements specified in the present invention.
[0101] Among the comparative examples, No. 9 is an example that did not contain Mo to excessively
generate the ferrite, not securing the bainite fraction, so that the tensile strength
of the steel sheet could not be secured. In addition, the steel sheet did not contain
Mo and Nb, so that the tensile strength after prolonged PWHT was further smaller than
before PWHT.
[0102] No. 10 is an example that did not contain Nb and did not satisfy the predetermined
range of the estimated precipitation amount P
0. As a result, the tensile strength after prolonged PWHT lowered.
[0103] No. 11 is an example that did not contain Mo to excessively generate the ferrite,
not securing the bainite fraction, so that the tensile strength of the steel sheet
could not be secured. In addition, the steel sheet did not contain Mo and Nb, so that
the tensile strength after prolonged PWHT lowered by performing PWHT for a long period.
[0104] No. 12 was small in the amount of Ni to increase the ferrite transformation start
temperature, excessively generating the ferrite. Therefore, the bainite fraction was
decreased. As a result, the strength before PWHT was near the lower limit of the strength
to be aimed at, and the strength was decreased by performing PWHT for a long period.
[0105] No. 13 was small in the amount of Ni to increase the ferrite transformation start
temperature, excessively generating the ferrite. Therefore, the bainite fraction was
decreased. As a result, the tensile strength before and after PWHT could not be secured.
[0106] No. 14 is an example in which the amounts of Cu, Ni and Nb were below the ranges
specified in the present invention and which excessively contained Mo. Therefore,
the ferrite was excessively generated and the bainite was not generated. As a result,
the tensile strength was low both before and after PWHT.
[0107] No. 15 is an example in which Ni was below the range specified in the present invention
and which excessively contained Mo but did not contain Nb. Therefore, the ferrite
was excessively generated and the bainite fraction could not be secured. As a result,
the tensile strength after PWHT could not be secured.
[0108] In Nos. 9 to 11, the solid solution equivalent A was below the range recommended
in the present invention to decrease the tensile strength after PWHT.
[Table 1]
No. |
Component composition (mass%) |
C |
Si |
Mn |
P |
S |
Cu |
Al |
Ni |
Cr |
Mo |
V |
Nb |
Ti |
Ca |
N |
1 |
0.034 |
0.29 |
1.49 |
0.003 |
0.002 |
0.18 |
0.026 |
0.54 |
0.01 |
0.22 |
0.001 |
0.023 |
0.011 |
0.0014 |
0.0055 |
2 |
0.034 |
0.29 |
1.49 |
0.003 |
0.002 |
0.18 |
0.026 |
0.54 |
0.01 |
0.22 |
0.001 |
0.023 |
0.011 |
0.0014 |
0.0055 |
3 |
0.036 |
0.31 |
1.57 |
0.004 |
0.002 |
0.30 |
0.028 |
0.56 |
0.01 |
0.25 |
0.001 |
0.025 |
0.013 |
0.0014 |
0.0052 |
4 |
0.040 |
0.30 |
1.50 |
0.005 |
0.001 |
0.65 |
0.030 |
0.55 |
- |
0.01 |
- |
0.045 |
0.012 |
0.0015 |
0.0055 |
5 |
0.034 |
0.29 |
1.49 |
0.003 |
0.002 |
0.18 |
0.026 |
0.54 |
0.01 |
0.22 |
0.001 |
0.023 |
0.011 |
0.0014 |
0.0055 |
6 |
0.040 |
0.30 |
1.50 |
0.005 |
0.001 |
0.20 |
0.030 |
0.55 |
- |
0.01 |
- |
0.045 |
0.012 |
0.0015 |
0.0055 |
7 |
0.040 |
0.30 |
1.50 |
0.005 |
0.001 |
0.65 |
0.030 |
0.55 |
- |
0.01 |
- |
0.045 |
0.012 |
0.0015 |
0.0055 |
8 |
0.041 |
0.31 |
1.56 |
0.004 |
0.002 |
0.32 |
0.023 |
0.55 |
0.01 |
0.13 |
- |
0.023 |
0.012 |
0.0012 |
0.0050 |
9 |
0.036 |
0.31 |
1.56 |
0.004 |
0.002 |
0.67 |
0.027 |
0.54 |
- |
- |
- |
- |
0.013 |
0.0012 |
0.0059 |
10 |
0.039 |
0.31 |
1.55 |
0.004 |
0.003 |
0.64 |
0.027 |
0.55 |
0.01 |
0.20 |
0.001 |
- |
0.013 |
0.0014 |
0.0059 |
11 |
0.039 |
0.30 |
1.50 |
0.005 |
0.001 |
0.67 |
0.032 |
0.54 |
- |
- |
0.051 |
- |
0.013 |
0.0012 |
0.0051 |
12 |
0.040 |
0.31 |
1.54 |
0.004 |
0.002 |
0.32 |
0.029 |
0.40 |
0.01 |
0.21 |
0.001 |
0.026 |
0.013 |
0.0016 |
0.0060 |
13 |
0.041 |
0.31 |
1.55 |
0.004 |
0.002 |
0.31 |
0.030 |
0.20 |
0.01 |
0.20 |
0.001 |
0.025 |
0.012 |
0.0015 |
0.0052 |
14 |
0.040 |
0.30 |
1.56 |
0.004 |
0.002 |
0.01 |
0.026 |
0.01 |
0.01 |
0.40 |
0.001 |
0.001 |
0.012 |
0.0018 |
0.0055 |
15 |
0.040 |
0.31 |
1.57 |
0.004 |
0.002 |
0.24 |
0.029 |
0.25 |
0.01 |
0.59 |
0.001 |
- |
0.013 |
0.0016 |
0.0061 |
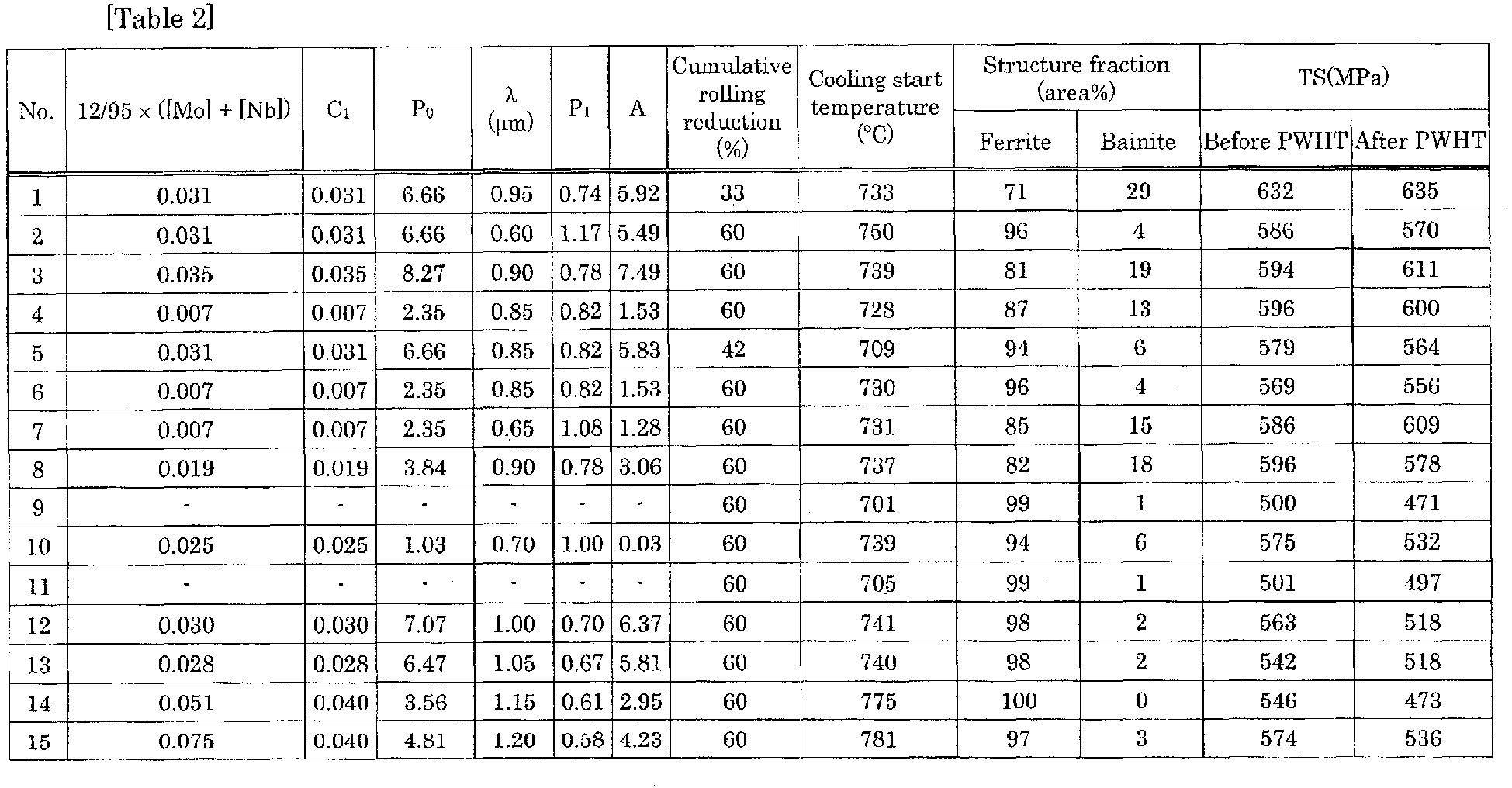