BACKGROUND
Technical Field
[0001] The present invention relates to a recording apparatus and a recording method.
Discussion of the Background Art
[0002] An ink jet type recording apparatus is known which ejects liquid such as ink through
nozzles included in a recording head and causes the liquid to adhere to a recording
medium such as a paper sheet to form an image according to image information.
[0003] In the ink jet type recording apparatus, when a state where ink is not ejected continues,
the ink inside the recording head is gradually dried from a nozzle portion communicating
with the outside, and ejection abnormality may occur due to rise in ink viscosity
(thickening of ink). To realize stable ejection, it is necessary to appropriately
evaluate the state of the ink inside the recording head and perform restoration operation
such as discharging thickened ink when thickening of ink is found.
[0004] As an apparatus for evaluating the state of the ink in the recording head, an apparatus
is disclosed that captures an image of a liquid level of the ink in a nozzle portion
and an image of a region around the nozzle and compares the images with a reference
image (for example, see
JP-2005-161838-A).
[0005] However, in the apparatus of
JP-2005-161838-A, only information related to the liquid level of the ink in the nozzle portion and
the appearance of the periphery of the nozzle is obtained, so that it may not be possible
to appropriately evaluate the state of the ink inside the recording head, such as
thickening of ink and an uneven distribution state of scattering particles contained
in the ink.
SUMMARY
[0006] The present invention is made in view of the above situation, and an object of the
present invention is to appropriately evaluate the state of the ink inside the recording
head.
[0007] In an aspect of the present invention, there is provided a recording apparatus that
includes a recording head, a light source, an irradiation optical device, a coupling
optical device, a detector, and an arithmetic device. The recording head is configured
to eject liquid containing scattering particles. The light source is configured to
emit light. The irradiation optical device is configured to irradiate the recording
head with an irradiation light being at least a part of the light emitted from the
light source. The coupling optical device is configured to couple reflected or scattered
light with reference light to from a coupled light. The reflected or scattered light
is light obtained by reflecting or scattering the irradiation light by the liquid
inside the recording head. The reference light is at least a part of the light emitted
from the light source and not reflected or scattered by the liquid inside the recording
head. The detector is configured to detect the coupled light formed by the coupling
optical device. The arithmetic device is configured to acquire an optical interference
tomographic image of the liquid inside the recording head based on the coupled light.
[0008] According to the embodiments of the present invention, it is possible to appropriately
evaluate the state of the ink inside the recording head.
BRIEF DESCRIPTION OF THE DRAWINGS
[0009] A more complete appreciation of the disclosure and many of the attendant advantages
and features thereof can be readily obtained and understood from the following detailed
description with reference to the accompanying drawings, wherein:
FIG. 1 is a diagram for explaining an example of a configuration of a tomographic
image acquisition device according to embodiments;
FIG. 2 is a diagram for explaining an example of an optical interference tomographic
image when an ejection function is normal;
FIG. 3 is a diagram for explaining an example of an optical interference tomographic
image when scattering particles are unevenly distributed;
FIG. 4 is a diagram for explaining an example of an optical interference tomographic
image when a concentration of scattering particles is reduced;
FIG. 5 is a diagram for explaining an example of diffusion coefficient value variation
of scattering particles in an ink drying process;
FIG. 6 is a diagram illustrating an example of components of an arithmetic device
according to the embodiments as functional blocks;
FIG. 7 is a flowchart illustrating an example of processing of the arithmetic device
according to the embodiments;
FIG. 8A is a diagram illustrating an example of a configuration of an image forming
apparatus according to a first embodiment;
FIG. 8B is an external view illustrating an example of a configuration of the image
forming apparatus according to the first embodiment;
FIG. 9 is a block diagram illustrating an example of a hardware configuration of a
processing device according to the first embodiment;
FIG. 10 is a diagram illustrating an example of components of the processing device
according to the first embodiment as functional blocks;
FIG. 11 is a diagram for explaining an example of an acquisition method of a discharge
amount according to the first embodiment;
FIG. 12 is a diagram illustrating an example of a correspondence relationship between
a diffusion coefficient value and an execution method of restoration processing according
to the first embodiment;
FIG. 13 (including FIGS. 13A and 13B) is a flowchart illustrating an example of processing
performed by the processing device according to the first embodiment;
FIG. 14 is an external perspective explanatory view of a recording head according
to a second embodiment;
FIG. 15 is a cross-sectional explanatory view in a direction perpendicular to a nozzle
arrangement direction of the recording head according to the second embodiment;
FIG. 16 is a cross-sectional explanatory view in a direction parallel to the nozzle
arrangement direction of the recording head according to the second embodiment;
FIG. 17 is a plan explanatory view of a nozzle plate of the recording head according
to the second embodiment;
FIGS. 18A to 18F are plan explanatory views of members included in a channel member
of the recording head according to the second embodiment;
FIGS. 19A and 19B are plan explanatory views of members included in a common liquid
chamber member of the recording head according to the second embodiment;
FIG. 20 is a block diagram illustrating an ink circulation system according to the
second embodiment;
FIG. 21 is a block diagram illustrating an example of a hardware configuration of
a processing device according to the second embodiment;
FIG. 22 is a diagram illustrating an example of components of the processing device
according to the second embodiment as functional blocks;
FIG. 23 is a diagram for explaining an example of an acquisition method of a circulation
flow rate according to the second embodiment;
FIG. 24 (including FIGS. 24A and 24B) is a flowchart illustrating an example of processing
performed by the processing device according to the second embodiment;
FIG. 25 is a diagram for explaining an example of a configuration around a tomographic
image acquisition device according to a third embodiment; and
FIG. 26 is a diagram for explaining an example of a configuration of a tomographic
image acquisition device according to a fourth embodiment.
[0010] The accompanying drawings are intended to depict embodiments of the present invention
and should not be interpreted to limit the scope thereof. The accompanying drawings
are not to be considered as drawn to scale unless explicitly noted.
DETAILED DESCRIPTION
[0011] The terminology used herein is for the purpose of describing particular embodiments
only and is not intended to be limiting of the present invention. As used herein,
the singular forms "a", "an" and "the" are intended to include the plural forms as
well, unless the context clearly indicates otherwise.
[0012] In describing embodiments illustrated in the drawings, specific terminology is employed
for the sake of clarity. However, the disclosure of this specification is not intended
to be limited to the specific terminology so selected and it is to be understood that
each specific element includes all technical equivalents that have a similar function,
operate in a similar manner, and achieve a similar result.
[0013] Hereinafter, embodiments for carrying out the invention will be described with reference
to the drawings. In the drawings, the same reference numerals are given to the same
components, and redundant description may be omitted.
[0014] A recording apparatus according to the embodiments is an apparatus including a recording
head that ejects liquid containing scattering particles through nozzles. Further,
the recording apparatus is an apparatus that irradiates liquid inside the recording
head with light and evaluates a state of the liquid inside the recording head from
an optical interference tomographic image acquired from light reflected or scattered
by the liquid inside the recording head. The optical interference tomographic image
can be acquired by, for example, optical coherence tomography (OCT).
[0015] In the embodiments, an ink jet type image forming apparatus that ejects ink from
a recording head to a recording medium such as a paper sheet and causes the ink to
adhere to the recording medium is described as an example. The image forming apparatus
is an example of the "recording apparatus" and the ink is an example of the "liquid".
The terms, image forming, recording, and printing in the embodiments are synonyms.
[0016] In the drawings described below, an X direction indicated by a dashed line arrow
indicates a direction in which nozzles included in the recording head are arranged.
A Z direction indicates a direction crossing a surface including the nozzles. The
Z direction is an example of a "depth direction".
Configuration of Tomographic Image Acquisition Device
[0017] First, an example of a configuration of a tomographic image acquisition device included
in an image forming apparatus 250 according to the embodiments will be described with
reference to FIG. 1. FIG. 1 is a diagram for explaining an example of a configuration
of a tomographic image acquisition device 100 according to the embodiments.
[0018] The Z direction in FIG. 1 corresponds to a direction in which ink is ejected from
a recording head 160. FIG. 1 illustrates a perspective diagram of the inside of the
recording head 160 observed from a direction crossing the direction in which ink is
ejected. Ink 163 is filled into the recording head 160 and the ink 163 is in contact
with external air through the nozzle 161 provided to the nozzle plate 162. The ink
163 contains scattering particles 164.
[0019] The tomographic image acquisition device 100 is arranged to face the nozzle 161 included
in the recording head 160. The tomographic image acquisition device 100 has an irradiation
optical device 110, a coupling optical device 120, a detector 130, an arithmetic device
140, and a light source 150. Arrows indicated by solid lines in the irradiation optical
device 110 and the coupling optical device 120 indicates progress of light.
[0020] The irradiation optical device 110 indicated by a dashed-dotted line has a beam splitter
111, a light condensing optical system 112, a mirror 113, and an optical scanning
device 114 and irradiates the recording head 160 with at least a part of light emitted
from the light source 150.
[0021] The beam splitter 111 has a function to split incident light into two beams by reflecting
a part of the incident light and transmitting the rest of the incident light. A part
of the light emitted from the light source 150 is reflected to the mirror 113 by the
beam splitter 111. The mirror 113 reflects the light reflected by the beam splitter
111 to the optical scanning device 114.
[0022] The optical scanning device 114 includes, for example, a galvanometer mirror. The
galvanometer mirror swings according to a drive voltage, so that light reflected by
the galvanometer mirror is reciprocally scanned in the X direction in FIG. 1. The
scanning light scanned by the optical scanning device 114 enters the light condensing
optical system 112.
[0023] The light condensing optical system 112 is separated from the nozzle 161 included
in the recording head 160 and is provided to face the nozzle 161 in an optical axis
direction of light emitted to the recording head 160. The light condensing optical
system 112 condenses the scanning light scanned by the optical scanning device 114
and emits light that converges or scatters toward the nozzle 161. Alternatively, the
light condensing optical system 112 may emit parallel light. When the light condensing
optical system 112 emits light that converges or scatters, it is preferable that the
light condensing optical system 112 emits the light so as to form a light condensing
spot inside the recording head 160 through the nozzle 161. When emitting the parallel
light, it is preferable to emit a light flux that is as narrow as possible in order
to improve spatial resolution of optical interference tomographic image described
later. The light condensing spot or the parallel light as described above is scanned
in the X direction by the optical scanning device 114.
[0024] For example, a condenser lens having a function to condense light can be used as
the light condensing optical system 112. The condenser lens may be a refraction type
lens or may be a diffraction type lens. The light condensing optical system 112 may
be configured by combining a plurality of lenses. The condenser lens can be made smaller
when using a diffraction type lens. An axis passing through the center of the light
condensing optical system 112 along the Z direction is an example of an "optical axis
of irradiation light", and a direction of the axis is an example of an "optical axis
direction of irradiation light".
[0025] The light source 150 is, for example, a super luminescent diode (SLD) that emits
near-infrared light with low coherence. The SLD is a light source that emits light
which is broadband such as light emitted from a light emitting diode (LED) and which
is light of high luminance such as light emitted from a laser diode (LD). However,
the light source 150 is not limited to the light source described above. The light
source 150 may be a light source that emits light in a wavelength band different from
that of near-infrared light or may be an LED, a white lamp, or the like, as long as
the light source 150 emits light with low coherence.
[0026] The light emitted to the recording head 160 is reflected or scattered by the outside
of the recording head 160 or by the ink 163 filled inside the recording head 160.
Light is strongly reflected or scattered by an interface between materials whose refractive
indexes are different. Therefore, the light emitted to the recording head 160 is reflected
or scattered by, for example, an interface between the recording head 160 and the
air, an interface between the ink 163 and the air, an interface between the ink and
163 the recording head 160, or an interface between solvent and a scattering particle
contained in the ink 163.
[0027] More specifically, the outside of the recording head 160 is, for example, a surface
of the nozzle plate 162, and the light emitted to the recording head 160 is reflected
or scattered by, for example, the surface of the nozzle plate 162.
[0028] The inside of the recording head 160 communicates with the outside through the nozzle
161. Therefore, the light emitted to the recording head 160 is reflected or scattered
by, for example, an interface (meniscus) where the ink 163 filled inside the recording
head 160 is in contact with the air at an opening portion of the nozzle 161.
[0029] Further, the light enters also the inside of the ink 163 through the nozzle 161,
and the ink 163 contains scattering particles 164. Therefore, the light emitted to
the recording head 160 is reflected or scattered by, for example, the scattering particles
existing inside the ink 163 filled inside the recording head 160.
[0030] The ink 163 is, for example, pigment ink. The pigment ink is ink existing in a state
where the pigment, which is a coloring component, is not completely dissolved in a
solvent. The ink 163 may contain particles including metal such as, for example, titanium
oxide. The particles of the pigment and the metal dispersed in the solvent are examples
of the "scattering particles".
[0031] For convenience of description, the light reflected or scattered by the outside of
the recording head 160 or by the ink 163 filled inside the recording head 160 may
be referred to as "probe light".
[0032] The probe light passes through the light condensing optical system 112 in a direction
opposite to that of the light emitted to the recording head 160 and is reflected by
the optical scanning device 114 and the mirror 113. The light reflected by the mirror
113 transmits the beam splitter 111 and enters the detector 130.
[0033] The coupling optical device 120 indicated by a two-dot chain line has the beam splitter
111, a lens 121, and a reference mirror 122. The coupling optical device 120 couples
reference light with light where the irradiation light from the irradiation optical
device 110 is reflected or scattered by the ink 163 inside the recording head 160.
[0034] Among the light emitted from the light source 150, the light that has passed through
the beam splitter 111 enters the lens 121. The lens 121 condenses the light that has
passed through the beam splitter 111 and emits light that converges or scatters toward
the reference mirror 122. Alternatively, the lens 121 may emit parallel light. For
example, a condenser lens having a function to condense light can be used as the lens
121 in the same manner as the light condensing optical system 112.
[0035] Here, it is preferable that the numerical aperture (NA) of the lens 121 is the same
as the NA of the light condensing optical system 112. This is because when the NAs
are the same, for example, an optical wavefront shape of the light condensed by the
lens 121 is substantially coincident with an optical wavefront shape of the light
condensed by the light condensing optical system 112 and it is possible to remove
aberration such as defocus in coupled light described later.
[0036] The reference mirror 122 reflects light emitted by the lens 121. The light reflected
by the reference mirror 122 passes through the lens 121 in a direction opposite to
that of the light emitted by the lens 121, is reflected by the beam splitter 111,
and enters the detector 130. The light reflected by the reference mirror 122 is at
least a part of the light emitted from the light source 150, is light that is not
reflected or scattered by the ink 163 inside the recording head 160, and is an example
of the "reference light".
[0037] The probe light and the reference light are overlapped by the beam splitter 111.
In other words, the probe light and the reference light are coupled by the beam splitter
111. When an optical path length where the probe light passes through and an optical
path length where the reference light passes through are within a coherence length
of the light source 150, both light beams interfere with each other and an interference
fringe occurs. Coupled light containing the interference fringe enters the detector
130.
[0038] The detector 130 has a spectroscope and a line detector. The spectroscope disperses
the light entering the detector 130. The dispersed light reaches a position shifted
in the X direction according to wavelength and forms a line-like pattern on the line
detector. The line-like pattern is detected by the line detector.
[0039] For example, a diffraction grating can be used as the spectroscope. A photo diode
array (PDA) can be used as the line detector. The photo diode array is an element
where photo diodes, each of which outputs a voltage signal according to intensity
of received light, are linearly arranged. Alternatively, as the line detector, a line
sensor where pixels such as a complementary metal oxide semiconductor device (CMOS)
or a charge coupled device (CCD) are linearly arranged may be used. The detector 130
outputs the detected line-like pattern data to the arithmetic device 140.
[0040] The arithmetic device 140 acquires intensity of the probe light for each relative
position of the recording head 160 with respect to the reference mirror 122 by applying
inverse Fourier transformation to the inputted line-like pattern data. In other words,
the relative position of the recording head 160 with respect to the reference mirror
122 is, for example, a position of the recording head 160 in the Z direction without
considering refractive index of the ink.
[0041] The arithmetic device 140 can acquire the intensity of the probe light for each position
(depth) H in the Z direction by converting the relative position of the recording
head 160 with respect to the reference mirror 122 into a distance with the refractive
index of the ink taken into consideration. It is possible to form and acquire a one-dimensional
optical interference tomographic image by connecting intensities of the probe light
at each depth H.
[0042] In the embodiments, the irradiation light to the recording head 160 is scanned in
the X direction by the optical scanning device 114. Therefore, it is possible to acquire
the aforementioned one-dimensional optical interference tomographic image for each
position in the X direction of the irradiation light. It is possible to form and acquire
a two-dimensional optical interference tomographic image by connecting the one-dimensional
optical interference tomographic images in the X direction at each position in the
X direction of the irradiation light. In the embodiments, an example where a two-dimensional
optical interference tomographic image is acquired and used will be described. For
ease of description, the two-dimensional optical interference tomographic image is
simply referred to as an "optical interference tomographic image" in the description
below.
[0043] A pixel in the X direction in the optical interference tomographic image represents
a minimum unit of position in the X direction of the irradiation light, and a pixel
in the Z direction in the optical interference tomographic image represents a minimum
unit of the position H in the Z direction of the irradiation light. In the optical
interference tomographic image, the intensity of the probe light is represented as,
for example, a luminance value of each pixel.
[0044] The arithmetic device 140 can acquire the optical interference tomographic image
for each scanning cycle of the scanning light emitted to the recording head 160. The
arithmetic device 140 may time-average the optical interference tomographic images
acquired every predetermined time longer than the scanning cycle and output the time-averaged
optical interference tomographic image. By the output of the arithmetic device 140,
the tomographic image acquisition device 100 can acquire a time-varying optical interference
tomographic image every scanning cycle or every predetermined time.
[0045] As the arithmetic device 140, for example, wired logic hardware such as an application
specific integrated circuit (ASIC) or a field-programmable gate array (FPGA) can be
used.
[0046] The arithmetic device 140 electrically connects to a storage device 170 and stores
data such as, for example, the inputted line-like pattern data and the optical interference
tomographic image in the storage device 170. The arithmetic device 140 performs an
arithmetic operation while referring to the data stored in the storage device 170
and can realize various functions described later. A processing result of the arithmetic
device 140 is outputted to a processing device 500 and used for control of the image
forming apparatus 250 performed by the processing device 500.
[0047] The storage device 170 is realized by, for example, a random access memory (RAM).
All or an arbitrary part of the functions realized by the arithmetic device 140 may
be realized by a program executed by a central processing unit (CPU).
[0048] In the tomographic image acquisition device 100 according to the embodiments, an
example is illustrated where the optical scanning device 114 scans the irradiation
light outputted from the irradiation optical device 110 in the X direction. However,
the tomographic image acquisition device 100 is not limited by the above. For example,
the tomographic image acquisition device 100 may acquire a three-dimensional optical
interference tomographic image by using an optical scanning device that scans irradiation
light in a Y direction perpendicular to the X direction and the Z direction respectively
instead of the mirror 113.
[0049] The tomographic image acquisition device 100 may acquire a one-dimensional optical
interference tomographic image in the Z direction without scanning the irradiation
light. For example, the tomographic image acquisition device 100 may use fixed mirrors
without scanning function for both the mirror 113 and the optical scanning device
114 and acquire a one-dimensional optical interference tomographic image in the Z
direction without scanning the irradiation light. Alternatively, the tomographic image
acquisition device 100 causes the light reflected by the beam splitter 111 to directly
enter the light condensing optical system 112 without providing the mirror 113 and
the optical scanning device 114. Thereby, the tomographic image acquisition device
100 may acquire a one-dimensional optical interference tomographic image in the Z
direction without scanning the irradiation light.
Optical Interference Tomographic Image
[0050] FIG. 2 is a diagram for explaining an example of an optical interference tomographic
image acquired by the tomographic image acquisition device 100 when an ejection function
is normal.
[0051] The depth of color (blackness) of the optical interference tomographic image illustrated
in FIG. 2 represents light intensity of the probe light scattered by each component
of the recording head 160. It is represented that the deeper (blacker) the color,
the greater the light intensity, and the lighter (whiter) the color, the smaller the
light intensity. The same goes for examples of the optical interference tomographic
image illustrated in FIGS. 2 to 4.
[0052] In FIG. 2, a tomographic image 201 represents a tomographic image formed by the probe
light reflected or scattered by an interface between the air and the recording head
160, for example, the surface of the nozzle plate 162. The nozzle plate 162 is composed
of a metal plate or the like and has high reflectance, so that the light intensity
of the probe light is large and the tomographic image is deeply displayed.
[0053] A tomographic image 202 represents a tomographic image formed by the probe light
reflected or scattered by an interface between the ink 163 inside the recording head
160 and the recording head 160. The interface between the ink 163 inside the recording
head 160 and the recording head 160 is, for example, a surface of a vibration plate
provided inside the recording head 160. The vibration plate is also composed of a
metal plate or the like in the same manner as the nozzle plate 162 and has high reflectance,
so that the light intensity of the probe light is large and the tomographic image
is deeply displayed.
[0054] A tomographic image 203 represents a tomographic image formed by the probe light
reflected or scattered by an interface (meniscus) between the ink 163 inside the recording
head 160 and the air. A liquid surface has high reflectance, so that the light intensity
of the probe light is large and the tomographic image is deeply displayed.
[0055] A tomographic image 204 represents a tomographic image formed by the probe light
reflected or scattered by the ink 163 inside the recording head 160. For example,
the tomographic image 204 is a tomographic image formed by light reflected or scattered
by the scattering particles contained in the ink 163. The probe light is light reflected
or scattered by the scattering particles, so that the light intensity of the probe
light is smaller than that of the other portions. Therefore, the tomographic image
is displayed in a light color.
[0056] When the ejection function is normal, the scattering particles contained in the ink
163 inside the recording head 160 are uniformly dispersed inside the ink 163. Therefore,
the tomographic image 204 is displayed in a uniform color.
[0057] Here, the uniformity of the scattering particles in the ink 163 inside the recording
head 160 largely affects the discharge function of the recording head 160.
[0058] For example, in the vicinity of the interface between the ink 163 and the air, the
scattering particles may be unevenly distributed due to drying of ink, so that a concentration
of the scattering particles may increase or the scattering particles may be mutually
agglomerated. Therefore, an abnormality of the ejection function such as non-ejection
or ejection velocity degradation may occur. The non-ejection is a state where the
ink is not ejected from the nozzle. The ejection velocity degradation is a state where
the speed of the ink ejected from the nozzle is slower than a desired speed.
[0059] There is a case where the concentration of the scattering particles is low in the
vicinity of the interface between the ink 163 and the air due to uneven distribution
of the scattering particles such as sedimentation of the scattering particles and
an image quality degradation such as low image density of an image formed on a paper
sheet occurs. In particular, when the scattering particles are particles containing
metal, the scattering particles are easily unevenly distributed due to sedimentation
or the like.
[0060] FIG. 3 is a diagram for explaining an example of an optical interference tomographic
image when the scattering particles contained in the ink 163 inside the recording
head 160 are unevenly distributed and the concentration of the scattering particles
in the vicinity of the interface between the ink 163 and the air is high. Descriptions
of the same portions as those in FIG. 2 may be omitted.
[0061] In FIG. 3, a tomographic image 301 represents a tomographic image formed by the probe
light reflected or scattered by the interface between the air and the recording head
160, for example, the surface of the nozzle plate 162. A tomographic image 302 represents
a tomographic image formed by the probe light reflected or scattered by the interface
between the ink 163 inside the recording head 160 and the recording head 160, for
example, the surface of the vibration plate.
[0062] A tomographic image 303 represents a tomographic image formed by the probe light
reflected or scattered by the interface (meniscus) between the ink 163 inside the
recording head 160 and the air. A tomographic image 304 represents a tomographic image
formed by the probe light reflected or scattered by a portion where the scattering
particles are uniformly dispersed in the ink 163 inside the recording head 160.
[0063] On the other hand, a tomographic image 305 represents a tomographic image formed
by the probe light reflected or scattered by a portion where the scattering particles
are unevenly distributed and the concentration of the scattering particles is high
in the ink 163 inside the recording head 160. In the portion where the scattering
particles are unevenly distributed and the concentration of the scattering particles
is high, the light intensity of the probe light reflected or scattered by the scattering
particles is large, so that the tomographic image 305 is more deeply displayed than
the tomographic image 304.
[0064] On the other hand, FIG. 4 is a diagram for explaining an example of an optical interference
tomographic image when the scattering particles are unevenly distributed in the ink
163 inside the recording head 160 and the concentration of the scattering particles
in the vicinity of the interface between the ink 163 and the air is low.
[0065] In FIG. 4, a tomographic image 401 represents a tomographic image formed by the probe
light reflected or scattered by the interface between the air and the recording head
160, for example, the surface of the nozzle plate 162. A tomographic image 402 represents
a tomographic image formed by the probe light reflected or scattered by the interface
between the ink 163 inside the recording head 160 and the recording head 160, for
example, the surface of the vibration plate.
[0066] A tomographic image 403 represents a tomographic image formed by the probe light
reflected or scattered by the interface (meniscus) between the ink 163 inside the
recording head 160 and the air. A tomographic image 404 represents a tomographic image
formed by the probe light reflected or scattered by a portion where the scattering
particles are uniformly dispersed in the ink 163 inside the recording head 160.
[0067] A tomographic image 405 represents a tomographic image formed by the probe light
reflected or scattered by a portion where the concentration of the scattering particles
is low in the vicinity of the interface between the ink 163 and the air. The scattering
particles are reduced due to the low concentration, and the light intensity of the
probe light reflected or scattered by the scattering particles is small, so that the
tomographic image is displayed whitely.
[0068] As illustrated in FIGS. 3 and 4, it is possible to visualize and evaluate the uneven
distribution of the scattering particles in the ink 163 inside the recording head
160 by the optical interference tomographic image acquired by the tomographic image
acquisition device 100. Further, it is possible to acquire a characteristic value
representing an uneven distribution state of the scattering particles based on the
optical interference tomographic image and use the characteristic value to maintain
a stable ejection function as described later.
Diffusion Coefficient of Scattering Particles
[0069] Next, a method of acquiring a diffusion coefficient value of the scattering particles
based on an optical interference tomographic image of the ink 163. Here, the diffusion
coefficient is a coefficient used in a diffusion equation representing a relationship
between the place and time when a material diffuses and a variation of concentration
of the material.
[0070] In the embodiments, the tomographic image acquisition device 100 acquires the diffusion
coefficient value by analyzing light intensity data in the optical interference tomographic
image of the ink 163 based on a photon correlation spectroscopy and a cumulant method
used in a dynamic light scattering method and the like.
[0071] The photon correlation spectroscopy is a method of formulating the magnitude of time
variation of the intensity of probe light for each depth H as an autocorrelation function.
The autocorrelation function represents a correlation of the intensity of probe light
I(t+τ) after τ hours based on the intensity of probe light I(t) at an arbitrary time
t as the following formula (1). Here, in the formula (1), G2 represents a secondary
autocorrelation function.
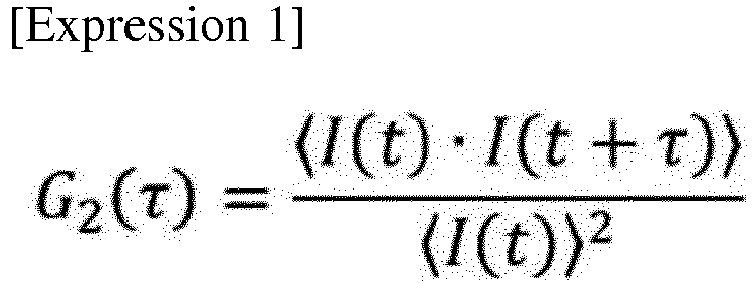
[0072] A diffusion coefficient value D is calculated and acquired by using the cumulant
method from the secondary autocorrelation function obtained by the photon correlation
spectroscopy. In the embodiments, a natural logarithm of a primary autocorrelation
function is approximated by performing secondary series expansion with τ as illustrated
by the following formula (2), and an attenuation constant Γ, which is the coefficient
of the natural logarithm, is obtained. Here, in the formula (2), Γ represents the
attenuation constant, and µ2 represents a polydispersity index.
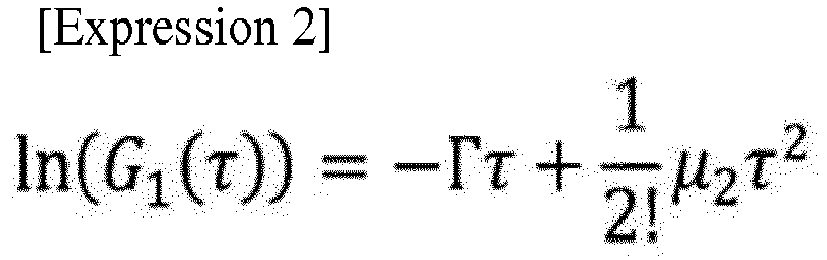
[0073] The diffusion coefficient value D can be calculated and acquired by the following
formula (3) from the attenuation constant Γ. Here, in the formula (3), q represents
a scattering vector.
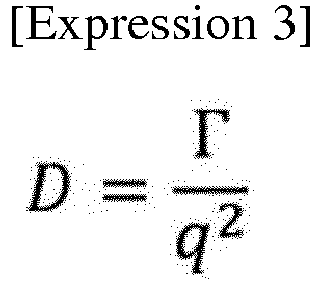
[0074] By these arithmetic operations, the tomographic image acquisition device 100 can
acquire the diffusion coefficient value D of the scattering particles for each depth
H. The diffusion coefficient value D is a value that varies according to the viscosity
of dispersion medium (ink) and the diameters of the scattering particles. Therefore,
it is possible to obtain the time variation of the ink viscosity and the diameters
of the scattering particles in the ink 163 inside the recording head 160 based on
the time variation of the diffusion coefficient value D.
[0075] FIG. 5 is a diagram for explaining an example of the time variation of the diffusion
coefficient value D of the scattering particles in a drying process of the ink 163.
In FIG. 5, the horizontal axis represents the time t, and the vertical axis represents
the depth H. It is illustrated that the smaller the value of the depth H, the closer
to the interface between the ink 163 and the air, and the greater the value of the
depth H, the closer to the vibration plate provided inside the recording head 160.
FIG. 5 illustrates the magnitude of the reciprocal number of the diffusion coefficient
value D of the scattering particles by color density for each time t and depth H.
It is illustrated that the deeper the color, the greater the reciprocal number of
the diffusion coefficient value D, and the lighter the color, the smaller the reciprocal
number of the diffusion coefficient value D.
[0076] In FIG. 5, the reciprocal number of the diffusion coefficient value D is constant
regardless of the depth H in an earlier period of time t. However, as the time elapses,
the reciprocal number of the diffusion coefficient value D gradually changes from
the vicinity of the interface between the ink 163 and the air.
[0077] For example, if the recording head 160 does not eject ink for some time, the ink
163 is dried from the opening portion of the nozzle, and the viscosity of the ink
gradually increases from the interface between the ink 163 and the air toward the
depth direction. The increase of the viscosity of the ink causes abnormality of the
ejection function such as non-ejection or ejection velocity degradation.
[0078] In the embodiments, it is possible to evaluate the increase of the viscosity of the
ink by acquiring the diffusion coefficient value D of the scattering particles based
on the optical interference tomographic image acquired by the tomographic image acquisition
device 100. Information such as the viscosity of the ink is used to maintain a stable
ejection function.
Functional Configuration of Arithmetic Device
[0079] FIG. 6 is a diagram illustrating an example of components of the arithmetic device
140 according to the embodiments as functional blocks. Each functional block of the
arithmetic device 140 illustrated in FIG. 6 is a conceptual block and not necessarily
required to be physically configured as illustrated in FIG. 6. All or a part of the
functional blocks can be configured by functionally or physically dispersed / combined
by arbitrary units. As described above, all or an arbitrary part of the functional
blocks can be realized as wired logic hardware or can be realized by a program executed
by the CPU.
[0080] The arithmetic device 140 has an input unit 141, a tomographic image calculator 142,
a diffusion coefficient value calculator 143, a peak to peak value (P-P) value calculator
144, and an output device 145. The input unit 141 electrically connects to the detector
130, is inputted with line-like pattern data based on coupled light from the detector
130, and outputs the line-like pattern data to the tomographic image calculator 142.
[0081] As described above, the tomographic image calculator 142 applies inverse Fourier
transformation to the inputted line-like pattern data and acquires the light intensity
of the probe light for each relative position of the recording head 160 with respect
to the reference mirror 122. The tomographic image calculator 142 acquires the light
intensity of the probe light for each depth H by converting the relative position
of the recording head 160 with respect to the reference mirror 122 into a distance
with the refractive index of the ink taken into consideration.
[0082] The tomographic image calculator 142 calculates the light intensity of the probe
light for each scanning position in the X direction of the optical scanning device
114 and for each position H in the Z direction and acquires the optical interference
tomographic image by connecting together the light intensities of the probe light.
The tomographic image calculator 142 outputs data representing an acquisition result
to the diffusion coefficient value calculator 143, the P-P value calculator 144, and
the output device 145.
[0083] As described above, the diffusion coefficient value calculator 143 acquires the diffusion
coefficient value D of the scattering particles by analyzing light intensity data
in the inputted optical interference tomographic image based on the photon correlation
spectroscopy and the cumulant method used in the dynamic light scattering method and
the like.
[0084] The diffusion coefficient value calculator 143 may acquire the diffusion coefficient
value D for each depth H based on the light intensity data for each depth H in the
optical interference tomographic image, or may acquire the diffusion coefficient value
D regardless of the depth H by using the entire light intensity data of the optical
interference tomographic image. The diffusion coefficient value calculator 143 outputs
data representing an acquisition result to the output device 145.
[0085] The P-P value calculator 144 acquires a P-P value S of the light intensity by obtaining
the maximum value and the minimum value of the light intensity in the inputted optical
interference tomographic image and calculating a difference between them. The P-P
value S of the light intensity is an example of a "characteristic value representing
a dispersion state of the scattering particles".
[0086] The P-P value calculator 144 may acquire the P-P value S of the light intensity for
each depth H based on the light intensity data for each depth H in the optical interference
tomographic image, or may acquire the P-P value S of the light intensity regardless
of the depth H by using the entire light intensity data of the optical interference
tomographic image. The P-P value calculator 144 outputs data representing an acquisition
result to the output device 145.
[0087] The tomographic image calculator 142, the diffusion coefficient value calculator
143, and the P-P value calculator 144 may temporarily store data such as the optical
interference tomographic image in the storage device 170 and perform arithmetic processing
while referring to the data stored in the storage device 170.
[0088] The output device 145 is inputted with data representing the acquisition results
of the tomographic image and the like acquired by each of the tomographic image calculator
142, the diffusion coefficient value calculator 143, and the P-P value calculator
144 and outputs at least one of the acquisition results to the processing device 500.
Alternatively, the output device 145 may electrically connect to an external apparatus
such as a personal computer (PC) and output the data representing the acquisition
result to the external apparatus.
[0089] FIG. 7 is a flowchart illustrating an example of processing of the arithmetic device
140 according to the embodiments.
[0090] First, the input unit 141 is inputted with line-like pattern data from the detector
130 and outputs the line-like pattern data to the tomographic image calculator 142
(step S71).
[0091] Next, the tomographic image calculator 142 calculates the light intensity of the
probe light for each position in the X direction and for each depth H and acquires
the optical interference tomographic image (step S73). The tomographic image calculator
142 outputs data representing an acquisition result to the diffusion coefficient value
calculator 143, the P-P value calculator 144, and the output device 145.
[0092] The diffusion coefficient value calculator 143 acquires the diffusion coefficient
value D of the scattering particles based on the light intensity data of the inputted
optical interference tomographic image and outputs the diffusion coefficient value
D to the output device 145 (step S75). The P-P value calculator 144 acquires the P-P
value S of the light intensity based on the light intensity data of the inputted optical
interference tomographic image and outputs the P-P value S to the output device 145
(step S77). Either of the diffusion coefficient value D of the scattering particles
or the P-P value S may be selected and outputted by the diffusion coefficient value
calculator 143 and the P-P value calculator 144.
[0093] The output device 145 is inputted with inputted data representing the acquisition
results of the tomographic image and the like acquired by each of the tomographic
image calculator 142, the diffusion coefficient value calculator 143, and the P-P
value calculator 144 and outputs at least one of the acquisition results to the processing
device 500 or an external apparatus (step S79).
[0094] In this way, the arithmetic device 140 acquires and outputs the optical interference
tomographic image, the diffusion coefficient value D, and the P-P value S, and the
tomographic image acquisition device 100 can acquire the optical interference tomographic
image, the diffusion coefficient value D, and the P-P value S. For ease of description,
the optical interference tomographic image, the diffusion coefficient value D, and
the P-P value S may be collectively referred to as "the optical interference tomographic
image and the like".
First Embodiment
[0095] Next, the image forming apparatus 250 according to a first embodiment will be described.
The image forming apparatus 250 according to the present embodiment has an abnormal
nozzle detector that detects an abnormal nozzle whose ink ejection function is abnormal
from among a plurality of nozzles included in the recording head 160 based on the
optical interference tomographic image of the ink 163 acquired by the tomographic
image acquisition device 100. Further, the image forming apparatus 250 has a processing
device that controls execution of restoration processing that restores the abnormal
nozzle and a discharge amount acquisition device that acquires a discharge amount
by which the ink inside the recording head 160 is discharged in order to restore the
abnormal nozzle. Configuration of Image Forming Apparatus
[0096] FIG. 8A is a diagram illustrating an example of a configuration of the image forming
apparatus 250 according to the present embodiment. In FIG. 8A, an X2 direction indicated
by an arrow indicates a main scanning direction, and a Y2 direction indicates a sub-scanning
direction crossing the main scanning direction.
[0097] As illustrated in FIG. 8A, the image forming apparatus 250 has a head unit 251, a
carriage device 252, a main scanning motor 253, a gear 254, and a pressure roller
255. Further, the image forming apparatus 250 has a timing belt 256, a guide rod 257,
an encoder sensor 258, an encoder sheet 259, and a platen 260. The image forming apparatus
250 is a multi-scan type image forming apparatus in which the carriage device 252
causes the head unit 251 to scan a plurality of times.
[0098] The head unit 251 includes the recording head 160 and is secured to the carriage
device 252. The main scanning motor 253 transmits a driving force accompanying rotation
to the carriage device 252 through the gear 254, the pressure roller 255, and the
timing belt 256. The carriage device 252 is reciprocated in the main scanning direction
(X2 direction) along the guide rod 257 by the transmitted driving force. The position
of the head unit 251 in the main scanning direction can be changed by the movement
of the carriage device 252 in the main scanning direction.
[0099] The encoder sheet 259 has a linear scale indicating positions in the main scanning
direction. When the carriage device 252 moves in the main scanning direction, the
encoder sensor 258 provided in the carriage device 252 reads the linear scale of the
encoder sheet 259 and detects the position in the main scanning direction.
[0100] On the other hand, a paper sheet 261 is transported in the sub-scanning direction
(Y2 direction) by a driving force accompanying rotation of a sub-scanning motor not
illustrated in the drawings along a predetermined transport path from a supply device
of the image forming apparatus 250, and reaches the position of the platen 260.
[0101] The recording head 160 included in the head unit 251 ejects ink to the paper sheet
261 and attaches the ink to the paper sheet 261 while moving in the main scanning
direction. When one movement of the head unit 251 in the main scanning direction is
completed, the paper sheet 261 is transported a predetermined distance in the sub-scanning
direction. When the transport of the paper sheet 261 in the sub-scanning direction
is completed, once again the recording head 160 included in the head unit 251 ejects
ink to the paper sheet 261 and attaches the ink to the paper sheet 261 while moving
in the main scanning direction.
[0102] The movement of the head unit 251 in the main scanning direction, the transport of
the paper sheet 261 in the sub-scanning direction, and the ejection of ink performed
by the recording head 160 according to the movement and the transport, are repeatedly
performed, so that an image is formed on the paper sheet 261.
[0103] FIG. 8B is an external view illustrating an example of a configuration of the image
forming apparatus 250 according to the present embodiment. As illustrated in FIG.
8B, the image forming apparatus 250 has the tomographic image acquisition device 100,
the processing device 500, and a maintenance mechanism 600.
[0104] The tomographic image acquisition device 100 is installed in a position below the
carriage device 252 so that the light condensing optical system 112 faces the nozzle
161 when the recording head 160 is stopped away from an ink ejection position in the
main scanning direction by moving the carriage device 252.
[0105] It is possible to locate the nozzle 161 above the light condensing optical system
112 by moving the carriage device 252 in the main scanning direction. Further, it
is possible to change the nozzle, which the light condensing optical system 112 faces,
among the plurality of nozzles included in the recording head 160 in the main scanning
direction by moving the carriage device 252 in the main scanning direction. Thereby,
it is possible to change a nozzle to be tested, which is an object to which light
is emitted from the light condensing optical system 112 in order to acquire an optical
interference tomographic image.
[0106] The main scanning motor 253 that moves the carriage device 252 in the main scanning
direction and changes a relative position between the nozzle 161 and the light condensing
optical system 112 in a direction crossing an optical axis direction of emitted light
is an example of a "position adjustment mechanism".
[0107] A stage including a drive device such as a motor may be provided in addition to the
configuration illustrated in FIG. 8B. The nozzle, which the light condensing optical
system 112 faces, among the plurality of nozzles included in the recording head 160
may be changed in the sub-scanning direction by mounting the tomographic image acquisition
device 100 on the stage and moving the stage in the sun-scanning direction. In this
case, the stage that moves the tomographic image acquisition device 100 in the sun-scanning
direction is an example of the "position adjustment mechanism".
[0108] The processing device 500 detects a nozzle whose ejection function is abnormal from
among the plurality of nozzles included in the recording head 160 based on the optical
interference tomographic image and the like inputted from the tomographic image acquisition
device 100. Further, the processing device 500 controls the maintenance mechanism
600 and causes the maintenance mechanism 600 to perform restoration processing that
restores the nozzle whose ejection function is abnormal. The processing device 500
is, for example, a substrate on which electrical circuits and the like are mounted
and is arranged inside the image forming apparatus 250. Details of hardware configuration
and function configuration of the processing device 500 will be described later.
[0109] The maintenance mechanism 600 has a mechanism to perform so-called head cleaning
such as suction and wiping, and performs restoration processing that restores the
nozzle 161 whose ejection function is abnormal under control of the processing device
500. The maintenance mechanism 600 is installed in a position below the carriage device
252 so that the maintenance mechanism 600 faces the nozzle 161 when the recording
head 160 is stopped away from the ink ejection position in the main scanning direction
by moving the carriage device 252.
[0110] For example, when the image forming apparatus 250 started, the image forming apparatus
250 can perform the following inspection process. First, the processing device 500
moves the carriage device 252 to a position where the tomographic image acquisition
device 100 is installed. Then, the processing device 500 detects abnormality of the
ejection function for a part or all of the nozzles 161 included in the recording head
160.
[0111] When detecting abnormality of the ejection function, the tomographic image acquisition
device 100 irradiates the ink 163 inside the recording head 160 with light through
the nozzle 161 and acquires the optical interference tomographic image based of the
probe light reflected or scattered by the outside of the recording head 160 or by
the ink 163 inside the recording head 160. The diffusion coefficient value D or the
P-P value S of the scattering particles in the ink 163 inside the recording head 160
are calculated and acquired from the acquired optical interference tomographic image,
and the optical interference tomographic image and the like are outputted to the processing
device 500.
[0112] The processing device 500 detects abnormality of the ejection function for a part
or all of the nozzles 161 included in the recording head 160 based on the inputted
optical interference tomographic image and the like. The inspection process described
above can be implemented without ejecting ink.
[0113] When there is the nozzle 161 whose ejection function is abnormal, the processing
device 500 moves the carriage device 252 to the position where the maintenance mechanism
600 is installed. The maintenance mechanism 600 performs the restoration processing
under control of the processing device 500. On the other hand, when the ejection functions
of all the nozzles 161 are normal, it is possible to proceed to a printing process.
[0114] By the way, the tomographic image acquisition device 100 may be detachable from the
image forming apparatus 250. Specifically, the tomographic image acquisition device
100 is attachable to and detachable from the image forming apparatus 250 so that the
tomographic image acquisition device 100 can be installed as needed, such as during
maintenance of the image forming apparatus 250.
[0115] In other words, the tomographic image acquisition device 100 can be handled as a
small-sized sensor that can be carried around or can be installed at an arbitrary
place. For example, it is possible to install the tomographic image acquisition device
100 on the image forming apparatus 250 and inspect the ejection function when starting
the image forming apparatus 250 and remove the tomographic image acquisition device
100 from the image forming apparatus 250 after ending the inspection.
[0116] The image forming apparatus 250 may display the optical interference tomographic
image of the ink 163 acquired by the tomographic image acquisition device 100 on an
operation panel included in the image forming apparatus 250 or may output the optical
interference tomographic image to cause an external apparatus connected to the image
forming apparatus 250 to display the optical interference tomographic image. A user
can determine whether the ejection function of the nozzle 161 is normal or abnormal
from the optical interference tomographic image of the ink 163.
[0117] It is possible to cause an external apparatus such as a PC connected to the image
forming apparatus 250 to perform control for performing ejection function abnormality
detection processing, output of processing result, and restoration processing. Configuration
of Processing Device
[0118] FIG. 9 is a block diagram illustrating an example of a hardware configuration of
the processing device 500 according to the present embodiment. The processing device
500 has a CPU 501, a RAM 502, a read-only memory (ROM) 503, an input interface (I/F)
504a, a light source driver 504b, a detector driver 504c, and an optical scanning
device driver 504d. Further, the processing device 500 has a maintenance mechanism
driver 505, a motor driver 506, and a recording head driver 507. These are electrically
connected together through a system bus 508.
[0119] The CPU 501 integrally controls operations such as the restoration processing in
the image forming apparatus 250. The CPU 501 controls the operations such as the restoration
processing in the image forming apparatus 250 and realizes various functions described
later by executing a program stored in the ROM 503 while using the RAM 502 as a work
area (workspace).
[0120] The input I/F 504a is an interface which is electrically connected to the arithmetic
device 140 and through which at least one of the optical interference tomographic
image and the like acquired by the arithmetic device 140 is inputted. The light source
driver 504b is an electrical circuit which is electrically connected to the light
source 150 and outputs a drive voltage to the light source 150.
[0121] The detector driver 504c is an electrical circuit which is electrically connected
to the detector 130 and outputs a drive voltage to the detector 130. The optical scanning
device driver 504d is an electrical circuit which is electrically connected to the
optical scanning device 114 and outputs a drive voltage to the optical scanning device
114.
[0122] The maintenance mechanism driver 505 is an electrical circuit which is electrically
connected to the maintenance mechanism 600 and outputs a drive voltage to the maintenance
mechanism 600. The motor driver 506 is an electrical circuit which is electrically
connected to the main scanning motor 253 and outputs a drive voltage to the main scanning
motor 253. The recording head driver 507 is an electrical circuit which is electrically
connected to the recording head 160 and outputs a drive voltage to the recording head
160. The recording head driver 507 is an example of a "drive device that applies a
predetermined drive voltage to a pressure generation device".
[0123] As the maintenance mechanism driver 505, the motor driver 506, and the recording
head driver 507, it is possible to use a maintenance mechanism driver, a motor driver,
and a recording head driver, which are included in the image forming apparatus 250
to form an image.
[0124] FIG. 10 is a diagram illustrating an example of components of the processing device
500 according to the present embodiment as functional blocks. The processing device
500 has a main scanning motor controller 510, a data input unit 511, an abnormal nozzle
detector 512, a discharge amount acquisition unit 513, a restoration processing method
determining unit 514, and a restoration processing controller 515.
[0125] The main scanning motor controller 510 outputs a control signal to the motor driver
506, drives the main scanning motor 253, and reciprocates the carriage device 252
in the main scanning direction. Thereby, the main scanning motor controller 510 controls
the position of the recording head 160 in the main scanning direction. The main scanning
motor controller 510 can move the carriage device 252 to the position where the tomographic
image acquisition device 100 is installed and cause each of the nozzles to be tested
included in the recording head 160 to face the light condensing optical system 112
of the tomographic image acquisition device 100.
[0126] The data input unit 511 is inputted with data representing the optical interference
tomographic image and the like, which the tomographic image acquisition device 100
acquires at the nozzle to be tested, from the arithmetic device 140, and outputs the
data to the abnormal nozzle detector 512, the discharge amount acquisition unit 513,
and the restoration processing method determining unit 514.
[0127] The abnormal nozzle detector 512 detects abnormality of the ejection function of
the nozzle to be tested based on the inputted optical interference tomographic image
and the like. Specifically, for example, when the inputted diffusion coefficient value
D or P-P value S exceeds a predetermined abnormality threshold, the abnormal nozzle
detector 512 detects the nozzle to be tested as an abnormal nozzle whose ejection
function is abnormal. When a time variation amount of the diffusion coefficient value
D or the P-P value S exceeds a predetermined abnormality threshold, the abnormal nozzle
detector 512 may detect the nozzle to be tested as an abnormal nozzle whose ejection
function is abnormal. The abnormality threshold as described above can be determined
by, for example, obtaining the diffusion coefficient value D or the P-P value S when
the ejection function becomes abnormal by simulation, experiment, or the like.
[0128] When the nozzle to be tested is an abnormal nozzle, the abnormal nozzle detector
512 outputs a nozzle number specifying the abnormal nozzle and a corresponding diffusion
coefficient value D or P-P value S in association with each other to the restoration
processing controller 515. Alternatively, the abnormal nozzle detector 512 may store
a nozzle number specifying the abnormal nozzle and a corresponding diffusion coefficient
value D or P-P value S in association with each other in the RAM 502 so that they
can be referred to in other processing.
[0129] The nozzle number is a number assigned to each nozzle in order to specify each nozzle
included in the recording head 160.
[0130] The discharge amount acquisition unit 513 calculates and acquires a discharge amount
of the ink 163 inside the recording head 160 based on the inputted optical interference
tomographic image and the like. Specifically, the discharge amount acquisition unit
513 obtains a depth Hth when the diffusion coefficient value D exceeds a predetermined
discharge amount acquisition threshold value from, for example, the diffusion coefficient
value D of the scattering particles for each depth H. The discharge amount acquisition
unit 513 can acquire the discharge amount by multiplying the depth Hth by the area
of the nozzle 161. By discharging such a discharge amount of ink, a state changes
inside the recording head 160, and only the ink that affects ejection function can
be discharged. Thereby, it is possible to maintain a stable ejection function while
suppressing an amount of ink consumed by discharge.
[0131] FIG. 11 is a diagram for explaining an example of an acquisition method of the discharge
amount based on the diffusion coefficient value D. In FIG. 11, the horizontal axis
represents the depth H and the vertical axis represents the diffusion coefficient
value D. The thick line in FIG. 11 represents a discharge amount acquisition threshold
value Th for the diffusion coefficient value D. The depth Hth represents the depth
H when the diffusion coefficient value D exceeds the discharge amount acquisition
threshold. The discharge amount acquisition unit 513 can acquire the discharge amount
by multiplying the depth Hth obtained in this way by the area of the nozzle 161. The
discharge amount acquisition unit 513 may acquire the discharge amount similarly by
using the P-P value S instead of the diffusion coefficient value D.
[0132] When the abnormal nozzle detector 512 stores a nozzle number specifying the abnormal
nozzle and a corresponding diffusion coefficient value D or P-P value S in association
with each other in the RAM 502, the discharge amount acquisition unit 513 may input
the diffusion coefficient value D or the P-P value S of the abnormal nozzle by referring
to the RAM 502.
[0133] Referring back to FIG. 10, the restoration processing method determining unit 514
determines an execution method of the restoration processing based on the inputted
optical interference tomographic image and the like. As the execution method of the
restoration processing, "dummy ejection", "wiping", and "suction" are assumed.
[0134] The "dummy ejection" is a method of preventing abnormality of the ejection function
by discharging high viscosity ink and the like inside the recording head 160. The
"wiping" is a method of preventing abnormality of the ejection function by wiping
the surface of the nozzle plate 162 of the recording head 160 by a blade or a web.
The "suction" is a method of preventing abnormality of the ejection function by sucking
dried ink and the like in the recording head 160 by air.
[0135] In an ascending order of restoration capability, for example, "dummy ejection", "wiping",
and "suction" are listed. Therefore, when a degree of abnormality of the ejection
function to be restored is lowest, the restoration processing method determining unit
514 determines the "dummy ejection" as the execution method of the restoration processing,
and as the degree of abnormality increases, the restoration processing method determining
unit 514 can determine the "wiping" and the "suction" as the execution method of the
restoration processing. However, the higher the restoration capability, the more the
amount of ink discharged for the restoration processing, so that ink may be discharged
more than necessary to cause waste of ink. Further, it takes a long time to perform
the restoration processing. Therefore, it is preferable to determine an appropriate
execution method of the restoration processing according to the degree of abnormality
of the ejection function.
[0136] The restoration processing method determining unit 514 determines the execution method
of the restoration processing according to at least one of the inputted diffusion
coefficient value D and P-P value S and causes the restoration processing controller
515 to perform appropriate restoration processing.
[0137] FIG. 12 is a diagram illustrating an example of a correspondence relationship between
the diffusion coefficient value D and the execution method of the restoration processing.
According to the correspondence relationship as illustrated in FIG. 12, the restoration
processing method determining unit 514 can determine an appropriate execution method
of the restoration processing for each range of the diffusion coefficient value D.
The restoration processing method determining unit 514 outputs a signal representing
a decision result to the restoration processing controller 515.
[0138] The restoration processing method determining unit 514 may determine the execution
method of the restoration processing in the same way by using the P-P value S instead
of the diffusion coefficient value D.
[0139] When the abnormal nozzle detector 512 stores a nozzle number specifying the abnormal
nozzle and a corresponding diffusion coefficient value D or P-P value S in association
with each other in the RAM 502, the restoration processing method determining unit
514 may input the diffusion coefficient value D or the P-P value S of the abnormal
nozzle by referring to the RAM 502.
[0140] Referring back to FIG. 10, the restoration processing controller 515 outputs a control
signal to the recording head 160 or the maintenance mechanism 600 and causes the recording
head 160 or the maintenance mechanism 600 to perform the restoration processing method
determined by the restoration processing method determining unit 514.
[0141] When the " dummy ejection" is executed, the restoration processing controller 515
causes the recording head 160 to eject ink, the amount of which is the discharge amount
acquired by the discharge amount acquisition unit 513. The "dummy ejection" may be
executed by only the abnormal nozzle specified by the abnormal nozzle detector 512,
or may be executed by all the nozzles included in the recording head 160. When a plurality
of abnormal nozzles is detected, by employing the largest discharge amount among the
discharge amounts acquired for the plurality of abnormal nozzles, the "dummy ejection"
may be executed by the plurality of abnormal nozzles or all the nozzles.
[0142] When the "wiping" is executed, the restoration processing controller 515 causes the
maintenance mechanism 600 to wipe the recording head 160, and when the "suction" is
executed, the restoration processing controller 515 causes the maintenance mechanism
600 to suck the ink inside the recording head 160. It is preferable that the "wiping"
and the "suction" are executed on all the nozzles included in the recording head 160.
[0143] FIG. 13 (including FIGS. 13A and 13B) is a flowchart illustrating an example of processing
performed by the processing device 500 according to the present embodiment.
[0144] First, the main scanning motor controller 510 drives the main scanning motor 253
and moves the carriage device 252 to the position where the tomographic image acquisition
device 100 is installed (step S131).
[0145] Next, the main scanning motor controller 510 moves the carriage device 252 so that
the nozzle to be tested among the plurality of nozzles included in the recording head
160 faces the light condensing optical system 112 of the tomographic image acquisition
device 100 (step S133).
[0146] Next, the tomographic image acquisition device 100 acquires the optical interference
tomographic image and the like, and the data input unit 511 is inputted with data
representing the optical interference tomographic image and the like and outputs the
data to the abnormal nozzle detector 512 (step S135).
[0147] The abnormal nozzle detector 512 determines whether the ejection function of the
nozzle to be tested is normal based on the inputted optical interference tomographic
image and the like (step S137). As described above, for example, when the inputted
diffusion coefficient value D or P-P value S exceeds a predetermined abnormality threshold,
the abnormal nozzle detector 512 determines that the ejection function of the nozzle
to be tested is abnormal.
[0148] When the abnormal nozzle detector 512 determines that the ejection function of the
nozzle to be tested is normal (step S137, Yes), the processing proceeds to step S141.
On the other hand, when the abnormal nozzle detector 512 determines that the ejection
function of the nozzle to be tested is not normal (step S137, No), the abnormal nozzle
detector 512 stores a nozzle number specifying the nozzle to be tested and a corresponding
diffusion coefficient value D or the like in association with each other in the RAM
502 (step S139).
[0149] Next, the processing device 500 determines whether the ejection function is inspected
for all the nozzles to be tested (step S141).
[0150] When the processing device 500 determines that the ejection function is inspected
for not all the nozzles to be tested (step S141, No), the processing returns to step
S133.
[0151] On the other hand, when the processing device 500 determines that the ejection function
is inspected for all the nozzles to be tested (step S141, Yes), the processing device
500 determines whether there is an abnormal nozzle among the nozzles to be tested
by referring to the RAM 502 (step S143).
[0152] When the processing device 500 determines that there is no abnormal nozzle among
the nozzles to be tested (step S143, No), the processing device 500 outputs a signal
indicating that there is no abnormal nozzle among the nozzles to be tested to a printer
controller included in the image forming apparatus 250 and causes the image forming
apparatus 250 to proceeds to a printing process (step S145).
[0153] On the other hand, when the processing device 500 determines that there is an abnormal
nozzle among the nozzles to be tested (step S143, Yes), the main scanning motor controller
510 causes the carriage device 252 to move and causes the recording head 160 to move
to the position of the maintenance mechanism 600 (step S147).
[0154] The discharge amount acquisition unit 513 acquires a discharge amount by referring
to the RAM 502 and inputting the diffusion coefficient value D or the P-P value S
of the abnormal nozzle, and outputs data representing the discharge amount to the
restoration processing controller 515 (step S149). When there is a plurality of abnormal
nozzles, the discharge amount acquisition unit 513 acquires the discharge amount of
each of the plurality of abnormal nozzles and outputs data representing the greatest
discharge amount to the restoration processing controller 515.
[0155] The restoration processing method determining unit 514 inputs the diffusion coefficient
value D or the P-P value S of the abnormal nozzle by referring to the RAM 502, and
determines the execution method of the restoration processing based on a correspondence
relationship between the diffusion coefficient value D or the P-P value S and the
execution method of the restoration processing (see FIG. 12) (step S151). When there
is a plurality of abnormal nozzles, the restoration processing method determining
unit 514 determines the execution method of the restoration processing according to
the diffusion coefficient value D or the P-P value S, which indicates the highest
degree of abnormality.
[0156] The restoration processing method determining unit 514 may input the discharge amount
acquired by the discharge amount acquisition unit 513 and determine the execution
method of the restoration processing based on the discharge amount. For example, in
the same manner as in FIG. 12, when an acquired discharge amount E satisfies E1 ≤
E < E2, the restoration processing method determining unit 514 determines the "dummy
ejection" as the restoration processing method. When the acquired discharge amount
E satisfies E2 ≤ E < E3, the restoration processing method determining unit 514 determines
the "wiping" as the restoration processing method, and when the acquired discharge
amount E satisfies E3 ≤ E < E4, the restoration processing method determining unit
514 determines the "suction" as the restoration processing method.
[0157] The restoration processing method determining unit 514 outputs a signal representing
the determined execution method of the restoration processing to the restoration processing
controller 515.
[0158] Next, the restoration processing controller 515 outputs a control signal to the recording
head 160 or the maintenance mechanism 600 and causes the recording head 160 or the
maintenance mechanism 600 to perform the restoration processing method determined
by the restoration processing method determining unit 514 (step S153). For example,
the restoration processing controller 515 performs the restoration processing on all
the nozzles included in the recording head 160.
[0159] In this way, the processing device 500 detects an abnormal nozzle from the nozzles
included in the recording head 160, and when an abnormal nozzle is detected, the processing
device 500 performs the restoration processing. Thereby, it is possible to restore
the ejection function of all the nozzles included in the recording head 160 to a normal
state.
[0160] Some or all of the functions realized by the processing device 500 may be realized
by the arithmetic device 140 included in the tomographic image acquisition device
100. Some or all of the functions realized by the arithmetic device 140 may be realized
by the processing device 500. Further, some or all of the functions realized by the
arithmetic device 140 and/or the processing device 500 may be realized by using a
hardware configuration of the printer controller included in the image forming apparatus
250.
[0161] As described above, the image forming apparatus 250 according to the present embodiment
includes the tomographic image acquisition device 100 and acquires the optical interference
tomographic image of the ink 163 inside the recording head 160. It is possible to
acquire the diffusion coefficient, the P-P value, and the like of the scattering particles
by using the optical interference tomographic image and evaluate the viscosity of
the ink, the diameters of the scattering particles, the uneven distribution of the
scattering particles, and the like in the ink 163 inside the recording head 160. Thereby,
it is possible to appropriately evaluate the state of the ink 163 inside the recording
head 160.
[0162] In the present embodiment, when there is a nozzle whose ejection function is abnormal
among the nozzles included in the recording head 160, an appropriate execution method
of the restoration processing is determined based on the optical interference tomographic
image. Thereby, it is possible to reliably restore the abnormal nozzle to a normal
state while suppressing the amount of ink discharged for the restoration processing
and time required for the restoration processing, so that a stable ejection function
can be maintained.
[0163] In the present embodiment, when there is a nozzle whose ejection function is abnormal
among the nozzles included in the recording head 160, based on the optical interference
tomographic image, a discharge amount of ink discharged for the restoration processing
is acquired based on at least one of the diffusion coefficient value and the P-P value
of the scattering particles for each depth H. Thereby, it is possible to reliably
restore the abnormal nozzle to a normal state while suppressing the amount of ink
discharged for the restoration processing, so that a stable ejection function can
be maintained.
Second Embodiment
[0164] Next, an example of an image forming apparatus according to a second embodiment will
be described. Description of the same components as those described in the aforementioned
embodiment will be omitted.
[0165] An image forming apparatus 250a according to the present embodiment has a recording
head including a circulation channel and has a flow rate voltage controller that changes
at least one of a circulation flow rate of ink flowing through the circulation channel
and a drive voltage of the recording head based on the optical interference tomographic
image.
Configuration of Image Forming Apparatus
[0166] First, an example of a recording head 160a according to the present embodiment will
be described with reference to FIGS. 14 to 19. FIG. 14 is an external perspective
explanatory view of the recording head 160a. FIG. 15 is a cross-sectional explanatory
view in a direction perpendicular to a nozzle arrangement direction of the recording
head. FIG. 16 is a cross-sectional explanatory view in a direction parallel to the
nozzle arrangement direction of the recording head. FIG. 17 is a plan explanatory
view of a nozzle plate of the recording head. FIGS. 18A to 18F are plan explanatory
views of members included in a channel member of the recording head. FIGS. 19A and
19B are plan explanatory views of members included in a common liquid chamber member
of the recording head.
[0167] The recording head 160a is formed by laminating and bonding a nozzle plate 1, a channel
plate 2, and a vibration plate member 3 as a wall surface member. The recording head
160a includes a piezoelectric actuator 11 that displaces the vibration plate member
3, a common liquid chamber member 20, and a cover 29. The nozzle plate 1 has a plurality
of nozzles 4 that ejects ink.
[0168] The channel plate 2 forms an individual liquid chamber 6 communicating with the nozzle
4, a fluid resistance portion 7 communicating with the individual liquid chamber 6,
and an ink introduction portion 8 communicating with the fluid resistance portion
7. The channel plate 2 is formed by laminating and bonding a plurality of plate-like
members 41 to 45 from the side of the nozzle plate 1, and a channel member 40 is configured
by laminating and bonding the plate-like members 41 to 45 and the vibration plate
member 3.
[0169] The vibration plate member 3 has a filter portion 9 as an opening communicating with
a common liquid chamber 10 formed by the ink introduction portion 8 and the common
liquid chamber member 20.
[0170] The vibration plate member 3 is a wall surface member that forms a wall surface of
the individual liquid chamber 6 of the channel plate 2. The vibration plate member
3 has a two-layer structure (not limited to two-layer structure), is formed by a first
layer that forms a thin portion from the channel plate 2 and a second layer that forms
a thick portion, and forms a deformable vibration region 30 in a portion corresponding
to the individual liquid chamber 6 in the first layer.
[0171] Here, as illustrated in FIG. 17, a plurality of nozzles 4 is arranged in zigzag in
the nozzle plate 1.
[0172] In the plate-like member 41 included in the channel plate 2, as illustrated in FIG.
18A, a through groove portion (that means a groove-shaped through hole) 6a that forms
the individual liquid chamber 6 and through groove portions 51a and 52a that form
a fluid resistance portion 51 and a circulation channel 52 are formed.
[0173] Similarly, in the plate-like member 42, as illustrated in FIG. 18B, a through groove
portion 6b that forms the individual liquid chamber 6 and a through groove portion
52b that forms the circulation channel 52 are formed.
[0174] Similarly, in the plate-like member 43, as illustrated in FIG. 18C, a through groove
portion 6c that forms the individual liquid chamber 6 and a through groove portion
53a which forms the circulation channel 53 and whose longitudinal direction is the
nozzle arrangement direction are formed.
[0175] Similarly, in the plate-like member 44, as illustrated in FIG. 18D, a through groove
portion 6d that forms the individual liquid chamber 6, a through groove portion 7a
to be the fluid resistance portion 7, a through groove portion 8a that forms the ink
introduction portion 8, and a through groove portion 53b which forms the circulation
channel 53 and whose longitudinal direction is the nozzle arrangement direction are
formed.
[0176] Similarly, in the plate-like member 45, as illustrated in FIG. 18E, a through groove
portion 6e that forms the individual liquid chamber 6, a through groove portion 8b
(to be a filter downstream side liquid chamber) which forms the ink introduction portion
8 and whose longitudinal direction is the nozzle arrangement direction, and a through
groove portion 53c which forms the circulation channel 53 and whose longitudinal direction
is the nozzle arrangement direction are formed.
[0177] In the vibration plate member 3, as illustrated in FIG. 18F, the vibration region
30, the filter portion 9, and a through groove portion 53d which forms the circulation
channel 53 and whose longitudinal direction is the nozzle arrangement direction are
formed.
[0178] In this way, the channel member is configured by laminating and bonding a plurality
of plate-like members, so that it is possible to form a complicated channel with a
simple configuration.
[0179] By the above configuration, in the channel member 40 composed of the channel plate
2 and the vibration plate member 3, the fluid resistance portion 51 along a surface
direction of the channel plate 2 communicating with each individual liquid chamber
6, the circulation channel 52, and the circulation channel 53 in a thickness direction
of the channel member 40 communicating with the circulation channel 52 are formed.
The circulation channel 53 communicates with a circulation common liquid chamber 50
described later.
[0180] On the other hand, in the common liquid chamber member 20, the common liquid chamber
10 and the circulation common liquid chamber 50, to which ink is supplied from a supply/circulation
mechanism 494, are formed.
[0181] In a first common liquid chamber member 21 included in the common liquid chamber
member 20, as illustrated in FIG. 19A, a piezoelectric actuator through hole 25a,
a through groove portion 10a to be a downstream side common liquid chamber 10A, and
a groove portion 50a with a bottom to be the circulation common liquid chamber 50
are formed.
[0182] Similarly, in a second common liquid chamber member 22, as illustrated in FIG. 19B,
a piezoelectric actuator through hole 25b and a groove portion 10b to be an upstream
side common liquid chamber 10B are formed.
[0183] Also referring to FIG. 1, in the second common liquid chamber member 22, a through
hole 71a to be a supply port portion that communicates one end portion in the nozzle
arrangement direction of the common liquid chamber 10 with a supply port 71 is formed.
[0184] Similarly, in the first common liquid chamber member 21 and the second common liquid
chamber member 22, through holes 81a and 81b that communicate the other end portion
(opposite end portion to the through hole 71a) in the nozzle arrangement direction
of the circulation common liquid chamber 50 with a circulation port 81 are formed.
[0185] In FIGS. 19A and 19B, a groove portion with a bottom is shaded (the same goes for
the other drawings).
[0186] In this way, the common liquid chamber member 20 is composed of the first common
liquid chamber member 21 and the second common liquid chamber member 22, the first
common liquid chamber member 21 is bonded to the vibration plate member 3 of the channel
member 40, and the second common liquid chamber member 22 is laminated and bonded
to the first common liquid chamber member 21.
[0187] Here, the first common liquid chamber member 21 forms the downstream side common
liquid chamber 10A that is a part of the common liquid chamber 10 communicating with
the ink introduction portion 8 and the circulation common liquid chamber 50 communicating
with the circulation channel 53. The second common liquid chamber member 22 forms
the upstream side common liquid chamber 10B that is a remaining part of the common
liquid chamber 10.
[0188] At this time, the downstream side common liquid chamber 10A that is a part of the
common liquid chamber 10 and the circulation common liquid chamber 50 are arranged
side by side in a direction perpendicular to the nozzle arrangement direction, and
the circulation common liquid chamber 50 is arranged in a position where the circulation
common liquid chamber 50 is projected in the common liquid chamber 10.
[0189] Thereby, the dimensions of the circulation common liquid chamber 50 are not restricted
by the dimensions required for the individual liquid chamber 6, the fluid resistance
portion 7, and a channel including the ink introduction portion 8, which are formed
by the channel member 40.
[0190] The circulation common liquid chamber 50 and a part of the common liquid chamber
10 are arranged side by side and the circulation common liquid chamber 50 is arranged
in a position where the circulation common liquid chamber 50 is projected in the common
liquid chamber 10, so that it is possible to suppress the width of the head in a direction
perpendicular to the nozzle arrangement direction and suppress an increase in size
of the head. The common liquid chamber member 20 forms the common liquid chamber 10
and the circulation common liquid chamber 50, to which ink is supplied from a head
tank or an ink cartridge.
[0191] On the other hand, the piezoelectric actuator 11 including an electromechanical conversion
element used as a drive device that deforms the vibration region 30 of the vibration
plate member 3 is arranged on the side opposite to the individual liquid chamber 6
of the vibration plate member 3.
[0192] As illustrated in FIG. 16, the piezoelectric actuator 11 has a piezoelectric member
12 bonded onto a base member 13. Groove processing by half cut dicing is applied to
the piezoelectric member 12 to form a required number of columnar piezoelectric elements
12A and 12B at predetermined intervals in a comb shape in one piezoelectric member
12.
[0193] Here, the piezoelectric elements 12A of the piezoelectric member 12 are used as piezoelectric
elements to which a drive waveform is given and which are driven, and the piezoelectric
elements 12B are not given a drive waveform and are used as mere support columns.
However, all the piezoelectric elements 12A and 12B can be used as piezoelectric elements
to be driven.
[0194] The piezoelectric element 12A is bonded to a protruded portion 30a which is an island-shaped
thick portion formed on the vibration region 30 of the vibration plate member 3. The
piezoelectric element 12B is bonded to a protruded portion 30b which is a thick portion
of the vibration plate member 3.
[0195] The piezoelectric member 12 is a member where piezoelectric layers and internal electrodes
are alternately laminated. Each internal electrode is drawn out to an end face and
an external electrode is provided, and a flexible wiring member 15 is connected to
the external electrode.
[0196] In the recording head 160a configured as described above, for example, when a voltage
applied to the piezoelectric element 12A is lowered from a reference potential, the
piezoelectric element 12A contracts, the vibration region 30 of the vibration plate
member 3 rises, and the volume of the individual liquid chamber 6 expands, so that
ink flows into the individual liquid chamber 6.
[0197] Thereafter, the piezoelectric element 12A is expanded in a lamination direction by
raising the voltage applied to the piezoelectric element 12A, the vibration region
30 of the vibration plate member 3 is deformed toward the nozzle 4, and the volume
of the individual liquid chamber 6 is contracted, so that pressure is applied to the
ink (ink is pressurized) inside the individual liquid chamber 6 and the ink is ejected
from the nozzle 4.
[0198] Then, the voltage applied to the piezoelectric element 12A is restored to the reference
potential, and thereby the vibration region 30 of the vibration plate member 3 is
restored to initial position and the individual liquid chamber 6 is expanded to generate
a negative pressure. Therefore, at this time, ink is filled into the individual liquid
chamber 6 from the common liquid chamber 10. After vibration of the surface of the
meniscus of the nozzle 4 is attenuated and stabilized, an operation for the next ejection
starts.
[0199] The piezoelectric element 12A is an example of a "pressure generation device".
[0200] A drive method of the recording head 160a is not limited to the above example (pull-push
ejection), and pull ejection, push ejection, or the like can be performed according
to how to give a drive waveform. In the embodiment described above, a laminated type
piezoelectric element is used as the "pressure generation device" that gives pressure
variation to the individual liquid chamber 6. However, the "pressure generation device"
is not limited to the laminated type piezoelectric element, and a thin film type piezoelectric
element can also be used. Further, it is possible to use a device where a heating
resistor is arranged in the individual liquid chamber 6 and which generates bubbles
by the heat of the heating resistor to give pressure variation and a device that generates
pressure variation by using electrostatic force.
[0201] Next, an example of an ink circulation system using the recording head 160a according
to the present embodiment will be described with reference to FIG. 20.
[0202] FIG. 20 is a block diagram illustrating the ink circulation system according to the
present embodiment.
[0203] As illustrated in FIG. 20, the ink circulation system is composed of a main tank,
the recording head 160a, a supply tank, a circulation tank, a compressor, a vacuum
pump, a first liquid feed pump 165, a second liquid feed pump, a regulator (R), a
supply side pressure sensor, a circulation side pressure sensor, and the like. The
supply side pressure sensor is connected to a supply channel side connected to the
supply port 71 (see FIG. 14) of the recording head 160a between the supply tank and
the recording head 160a. The circulation side pressure sensor is connected to a circulation
channel side connected to the circulation port 81 (see FIG. 14) of the recording head
160a between the recording head 160a and the circulation tank.
[0204] One of the circulation tanks is connected to the supply tank through the first liquid
feed pump 165, and the other circulation tank is connected to the main tank through
the second liquid feed pump. Thereby, ink flows into the recording head 160a from
the supply tank through the supply port 71, the ink is discharged from the circulation
port and discharged to the circulation tank, and further, the ink is fed from the
circulation tank to the supply tank by the first liquid feed pump 165, so that the
ink is circulated.
[0205] The supply tank is connected with the compressor, and it is controlled so that a
predetermined positive pressure is detected by the supply side pressure sensor. On
the other hand, the circulation tank is connected with the vacuum pump, and it is
controlled so that a predetermined negative pressure is detected by the circulation
side pressure sensor. Thereby, it is possible to keep a negative pressure of the meniscus
constant while circulating ink through the recording head 160a.
[0206] When the ink is ejected from the nozzle of the recording head 160a, the amount of
ink in the supply tank and the circulation tank decreases, so that it is preferable
to properly replenish ink to the circulation tank from the main tank by using the
second liquid feed pump. The timing of replenishing ink to the circulation tank from
the main tank can be controlled by a detection result of a liquid level sensor or
the like provided in the circulation tank. For example, ink is replenished when a
liquid level height of the ink in the circulation tank becomes lower than a predetermined
height.
[0207] Next, the circulation of the ink inside the recording head 160a will be described.
As illustrated in FIG. 14, the supply port 71 communicating with the common liquid
chamber and the circulation port 81 communicating with the circulation common liquid
chamber 50 are formed at an end portion of the common liquid chamber member 20. The
supply port 71 and the circulation port 81 are respectively connected to the supply
tank and the circulation tank (see FIG. 20), which store ink, through tubes. The ink
stored in the supply tank is supplied to the individual liquid chamber 6 through the
supply port 71, the common liquid chamber 10, the ink introduction portion 8, and
the fluid resistance portion 7.
[0208] Further, while the ink in the individual liquid chamber 6 is ejected from the nozzle
4 by the drive of the piezoelectric element 12A, some or all of the ink remaining
in the individual liquid chamber 6 without being ejected is circulated to the circulation
tank through the fluid resistance portion 51, the circulation channels 52 and 53,
the circulation common liquid chamber 50, and the circulation port 81.
[0209] The ink can be circulated not only when the recording head 160a operates, but also
when the recording head 160a stops operation. The ink is circulated when the recording
head 160a stops operation, so that the ink in the individual liquid chamber is refreshed
at all times and it is possible to suppress agglomeration, uneven distribution, and
settling of components contained in the ink, for example, scattering particles such
as pigment. Therefore, the circulation is preferable.
Configuration of Processing Device
[0210] Next, an example of a configuration of a processing device 500a according to the
present embodiment will be described with reference to FIGS. 21 to 24.
[0211] FIG. 21 is a block diagram illustrating an example of a hardware configuration of
the processing device 500a according to the present embodiment. The processing device
500a has a recording head driver 507a and a liquid feed pump driver 509.
[0212] The recording head driver 507a is an electrical circuit which is electrically connected
to the recording head 160a and outputs a drive voltage to the recording head 160a.
The drive voltage outputted to the recording head 160a is applied to the piezoelectric
element 12A. The piezoelectric element 12A contracts or expands according to the applied
voltage, so that ink is ejected from the recording head 160a or the ink inside the
recording head 160a is finely vibrated (finely driven).
[0213] The liquid feed pump driver 509 is an electrical circuit which is electrically connected
to the first liquid feed pump 165 and outputs a drive voltage to the first liquid
feed pump 165. The first liquid feed pump 165 turns ON and OFF the feed of ink according
to the drive voltage. The first liquid feed pump 165 can change the circulation flow
rate of the ink circulating inside the recording head 160a by changing the flow rate
of the fed ink according to the drive voltage.
[0214] FIG. 22 is a diagram illustrating an example of components of the processing device
500a according to the present embodiment as functional blocks. The processing device
500a has a data input unit 511a and a flow rate voltage controller 516.
[0215] The data input unit 511a is inputted with data representing the optical interference
tomographic image and the like, which the tomographic image acquisition device 100
acquires at the nozzle to be tested, from the arithmetic device 140, and outputs the
data to the abnormal nozzle detector 512, the discharge amount acquisition unit 513,
the restoration processing method determining unit 514, and the flow rate voltage
controller 516.
[0216] The flow rate voltage controller 516 changes at least one of a circulation flow rate
Q of the ink circulating inside the recording head 160a and a drive voltage of the
recording head 160a based on at least one of the inputted diffusion coefficient value
D and P-P value S.
[0217] Here, when the circulation flow rate Q is increased, the ink inside the individual
liquid chamber is more readily refreshed. Therefore, the agglomeration, uneven distribution,
and settling of the scattering particles are more suppressed, so that it is possible
to easily prevent the abnormality of the ejection function such as non-ejection or
ejection velocity degradation due to state of the ink inside the recording head 160a.
On the other hand, the flow velocity of the ink flowing inside the recording head
160a increases according to the circulation flow rate Q, so that the stability of
the ejection function may be damaged due to variation of the ejection velocity for
each nozzle. Therefore, it is required to optimize the circulation flow rate Q according
to the state of the ink inside the recording head 160a.
[0218] Thus, the flow rate voltage controller 516 optimizes the circulation flow rate Q
of the ink circulating inside the recording head 160a based on at least one of the
inputted diffusion coefficient value D and P-P value S.
[0219] When the ejection driving voltage of the recording head 160a is increased, an ejection
force is increased, so that it is possible to easily prevent the abnormality of the
ejection function such as non-ejection or ejection velocity degradation due to state
of the ink inside the recording head 160a. On the other hand, characteristic differences
between nozzles easily occur when the ejection force is increased, so that the stability
of the ejection function may be damaged due to variation of the ejection velocity
for each nozzle. Therefore, it is required to apply an appropriate drive voltage according
to the state of the ink inside the recording head 160a.
[0220] On the other hand, during a period in which the recording head 160a does not eject
ink, fine vibration (fine drive) may be applied to the recording head 160a by applying
a small drive voltage, which does not cause the recording head 160a to eject ink,
to the recording head 160a. It is possible to suppress abnormality of the ejection
function by diffusing high viscosity ink inside the individual liquid chamber by the
fine vibration.
[0221] In this case, when a relatively large drive voltage is applied within a range where
the ink is not ejected, vibration amplitude of the ink inside the individual liquid
chamber increases and the high viscosity ink is more diffused, so that suppression
effect of the abnormality of the ejection function increases. However, when the vibration
amplitude is increased more than necessary with respect to the amount of high viscosity
ink inside the individual liquid chamber, the ink may be wrongly ejected during a
period in which the ink is not ejected, or the ejection of the ink may be adversely
affected after the period in which the ink is not ejected. Therefore, it is required
to apply an appropriate drive voltage in order to appropriately finely vibrate the
ink inside the individual liquid chamber.
[0222] For the above requirements, the flow rate voltage controller 516 optimizes the drive
voltage of the recording head 160a when the recording head 160a ejects ink based on
at least one of the inputted diffusion coefficient value D and P-P value S. Alternatively,
the flow rate voltage controller 516 optimizes the drive voltage applied to the recording
head 160a in order to finely vibrate the ink inside the individual liquid chamber
during the period in which the ink is not ejected.
[0223] FIG. 23 is a diagram for explaining an example of an acquisition method of the circulation
flow rate Q based on the diffusion coefficient value D. In FIG. 23, the horizontal
axis represents the diffusion coefficient value D and the vertical axis represents
the circulation flow rate Q appropriate for securing stability of the ejection function
for each diffusion coefficient value D.
[0224] Data representing a correspondence relationship between the diffusion coefficient
value D and the circulation flow rate Q as illustrated in FIG. 23 is acquired in advance
by experiment or simulation, and the data is stored in the ROM 503 or the like. The
flow rate voltage controller 516 acquires the circulation flow rate Q appropriate
for securing stability of the ejection function by referring to the ROM 503 based
on the diffusion coefficient value D acquired by the tomographic image acquisition
device 100.
[0225] The flow rate voltage controller 516 controls the first liquid feed pump 165 so that
the ink inside the recording head 160a circulates at the acquired circulation flow
rate Q. The control of the flow rate can be performed based on a pressure detection
value detected by the supply side pressure sensor or the circulation side pressure
sensor (see FIG. 20) in a state where a relationship between a pressure applied to
the ink and the flow rate is grasped in advance. Alternatively, the flow rate may
be controlled based on a flow rate detection value by providing a flow rate sensor
to the ink circulation system.
[0226] The flow rate voltage controller 516 may secure the stability of the ejection function
in the same manner as described above by controlling the drive voltage of the recording
head 160a instead of the circulation flow rate Q. Alternatively, the flow rate voltage
controller 516 may secure the stability of the ejection function by controlling both
the circulation flow rate Q and the drive voltage of the recording head 160a.
[0227] FIG. 24 (including FIGS. 24A and 24B) is a flowchart illustrating an example of processing
performed by the processing device 500a according to the present embodiment. Steps
S241 to S255 in FIG. 24A are the same as steps S131 to S145 in FIG. 13A, and steps
S261 to S267 in FIG. 24B are the same as steps S147 to S153 in FIG. 13B, so that the
description thereof will be omitted.
[0228] In step S253, when the processing device 500a determines that there is an abnormal
nozzle among the nozzles to be tested (step S253, Yes), the processing device 500a
determines whether to change the circulation flow rate or the drive voltage of the
recording head (step S257). For example, when the diffusion coefficient value D is
smaller than D1 in the table illustrated in FIG. 12, the processing device 500a determines
to change the circulation flow rate or the drive voltage of the recording head. In
other words, when the degree of abnormality is not so high to perform the restoration
processing, the processing device 500a determines to change the circulation flow rate
or the drive voltage of the recording head.
[0229] When the processing device 500a determines to change the circulation flow rate or
the drive voltage of the recording head (step S257, Yes), the flow rate voltage controller
516 changes at least one of the circulation flow rate Q and the drive voltage of the
recording head 160a based on at least one of the diffusion coefficient value D and
the P-P value S.
[0230] On the other hand, when the processing device 500a determines not to change the circulation
flow rate or the drive voltage of the recording head (step S257, No), the restoration
processing and the like of step S261 and subsequent steps are performed.
[0231] In this way, when an abnormal nozzle is detected from the nozzles included in the
recording head 160, the processing device 500a can change at least one of the circulation
flow rate Q and the drive voltage of the recording head 160a based on at least one
of the diffusion coefficient value D and the P-P value S.
[0232] As described above, the image forming apparatus according to the present embodiment
has the recording head including the circulation channel and the flow rate voltage
controller that changes at least one of the circulation flow rate of ink flowing through
the circulation channel and the drive voltage of the recording head. The image forming
apparatus can prevent the abnormality of the ejection function and secure the stability
of the ejection function by changing at least one of the circulation flow rate Q and
a voltage applied to the piezoelectric element 12A based on at least one of the diffusion
coefficient value D and the P-P value S.
[0233] The effects other than those described above are the same as those of the aforementioned
embodiment.
Third Embodiment
[0234] Next, an example of an image forming apparatus according to a third embodiment will
be described. Description of the same components as those described in the aforementioned
embodiments will be omitted.
[0235] In the image forming apparatuses described in the first and the second embodiments,
when light is emitted from the light condensing optical system 112 to the nozzle 161,
light reflected from the interface (the surface of the vibration plate) between the
ink 163 inside the recording head 160 and the recording head 160 may be strong. In
this case, it is difficult to detect the probe light reflected or scattered by the
scattering particles existing near the vibration plate provided inside the recording
head 160.
[0236] Similarly, when light is emitted from the light condensing optical system 112 to
the nozzle 161, light reflected from the interface (meniscus) between the ink 163
inside the recording head 160 and the air may be strong. In this case, it is difficult
to detect the probe light reflected or scattered by the scattering particles existing
near the meniscus inside the recording head 160.
[0237] Therefore, an image forming apparatus 250b according to the present embodiment includes
an angle adjustment mechanism that changes an angle of the optical axis of the light,
which is emitted from the tomographic image acquisition device 100 to the recording
head 160, with respect to the recording head 160. The optical axis of the light emitted
to the nozzle 161 is tilted by an angle adjustment mechanism 182, so that the light
reflected by the surface of the vibration plate and the meniscus is inhibited from
reaching the detector 130.
[0238] FIG. 25 is a diagram for explaining an example of a configuration around the tomographic
image acquisition device 100 included in the image forming apparatus 250b according
to the present embodiment.
[0239] In FIG. 25, the angle adjustment mechanism 182 is a tilting stage that can tilt a
table surface. The tomographic image acquisition device 100 is secured to the table
surface of the angle adjustment mechanism 182. The angle adjustment mechanism 182
can tilt the tomographic image acquisition device 100 with respect to the recording
head 160 by tilting the table surface and can change an angle of the optical axis
183 of the light emitted from the light condensing optical system 112 to the nozzle
161 with respect to the recording head 160. An optical axis 184 represents the optical
axis of the light condensing optical system 112 when the tomographic image acquisition
device 100 is tilted by an angle θ with respect to the Z direction by the angle adjustment
mechanism 182.
[0240] The table surface of the angle adjustment mechanism 182 may be tilted manually or
may be tilted electrically by providing a drive device such as a motor.
[0241] It is preferable that the center (rotation center) of the tilt of the angle adjustment
mechanism 182 is substantially coincident with a light condensing position of the
light condensing optical system 112. When the rotation center is substantially coincident
with the light condensing position, it is possible to prevent the position where the
probe light reflected or scattered from the recording head 160 reaches on the detector
130 of the tomographic image acquisition device 100 from being largely changed according
to the tilt of the angle adjustment mechanism 182. Thereby, the position of the tomographic
image acquisition device 100 can be easily adjusted.
[0242] The tomographic image acquisition device 100 and the angle adjustment mechanism 182
are installed in a position below the carriage device 252 so that the light condensing
optical system 112 faces the nozzle 161 when the recording head 160 is stopped away
from the ink ejection position in the main scanning direction by the movement of the
carriage device 252 in the image forming apparatus 250b.
[0243] As described above, the optical axis of the light emitted to the nozzle 161 is tilted
by the angle adjustment mechanism 182, so that the light reflected by the surface
of the vibration plate and the meniscus is inhibited from reaching the detector 130.
Therefore, it is possible to reduce the intensity of the light reflected in this way.
Thereby, it is possible to detect the probe light reflected or scattered by the scattering
particles in the entire region (portion) inside the recording head 160.
[0244] The effects other than those described above are the same as those of the aforementioned
embodiments.
Fourth Embodiment
[0245] Next, an example of an image forming apparatus according to a fourth embodiment will
be described. Description of the same components as those described in the aforementioned
embodiments will be omitted.
[0246] FIG. 26 is a diagram for explaining an example of a configuration of a tomographic
image acquisition device 100c included in an image forming apparatus 250c according
to the present embodiment. The tomographic image acquisition device 100c has a space
filter 190. The space filter 190 has a lens 191, a pinhole 192, and a lens 193.
[0247] The light emitted from the light source 150 is condensed by the lens 191. The pinhole
192 is arranged at a light condensing position of the lens 191. The pinhole 192 is
an optical element having a circular opening. The pinhole 192 causes light to pass
through only the circular opening and blocks the other light. The light passing through
the pinhole 192 is converted into parallel light or light close to parallel light
by the lens 193, and is used as irradiation light for acquiring the optical interference
tomographic image.
[0248] In the present embodiment, an example is illustrated where the space filter 190 is
provided in an optical path between the light source 150 and the beam splitter 111.
However, the embodiment is not limited to this example. The space filter 190 may be
provided in an optical path between the light source 150 and the recording head 160
such as an optical path between the beam splitter 111 and the mirror 113.
[0249] In the irradiation optical device 110, light reflected or scattered by dust or scratch
of lens becomes noise light and degrades quality of the optical interference tomographic
image to be acquired. In the present embodiment, such noise light is blocked and removed
by the pinhole 192 of the space filter 190. Thereby, it is possible to suppress noise
light and generate correctly shaped irradiation light, so that the quality of the
optical interference tomographic image can be improved.
[0250] The effects other than those described above are the same as those of the aforementioned
embodiments.
[0251] While the recording apparatuses according to the embodiments have been described,
the present invention is not limited to the embodiments described above, but can be
variously modified and improved within the scope of the present invention.
[0252] The embodiments include a recording method. For example, the recording method is
a recording method performed by a recording head in a recording apparatus that ejects
liquid containing scattering particles, and the recording method includes a step of
emitting light from a light source; an irradiation step of irradiating the recording
head with an irradiation light being at least a part of emitted light; an interference
step of coupling reflected or scattered light with reference light to form a coupled
light, the reflected or scattered light being light obtained by reflecting or scattering
the irradiation light by the liquid inside the recording head, the reference light
being at least a part of the light emitted from the light source and not reflected
or scattered by the liquid inside the recording head; a step of detecting the coupled
light coupled in the interference step; and a step of acquiring an optical interference
tomographic image of the liquid inside the recording head based on the coupled light.
The same effect as that of the recording apparatus described above can be obtained
by the recording method.
[0253] The above-described embodiments are illustrative and do not limit the present invention.
Thus, numerous additional modifications and variations are possible in light of the
above teachings. For example, elements and/or features of different illustrative embodiments
may be combined with each other and/or substituted for each other within the scope
of the present invention.
[0254] Any one of the above-described operations may be performed in various other ways,
for example, in an order different from the one described above.
[0255] The present invention can be implemented in any convenient form, for example using
dedicated hardware, or a mixture of dedicated hardware and software. The present invention
may be implemented as computer software implemented by one or more networked processing
apparatuses. The processing apparatuses include any suitably programmed apparatuses
such as a general purpose computer, personal digital assistant, mobile telephone (such
as a WAP or 3G-compliant phone) and so on. Since the present invention can be implemented
as software, each and every aspect of the present invention thus encompasses computer
software implementable on a programmable device. The computer software can be provided
to the programmable device using any conventional carrier medium (carrier means).
The carrier medium includes a transient carrier medium such as an electrical, optical,
microwave, acoustic or radio frequency signal carrying the computer code. An example
of such a transient medium is a TCP/IP signal carrying computer code over an IP network,
such as the Internet. The carrier medium may also include a storage medium for storing
processor readable code such as a floppy disk, hard disk, CD ROM, magnetic tape device
or solid state memory device.