Field of the Invention
[0001] The invention relates to the field of energetics and can be used in thermal power
plants, boiler houses, etc. to optimize and control the combustion process and ensure
the ignition of boilers and stabilize the burning of fuel, for example, coal dust,
in the process of flaring thereof without the use of additional highly reactive fuel.
Background of the invention
[0002] A technical solution disclosed in patent No.
RU2514534 (F23Q 5/00; published on 27.04.2014) is known, which comprises the following set of
essential features: an air-fuel mixture is fed to an ignition zone, an electric arc
discharge is created in the ignition zone, the air-fuel mixture is ignited, and fuel
flaring is carried out in a combustion chamber.
[0003] All of the above features are common with the proposed technical solution.
[0004] The known method of fuel ignition and flaring is difficult to use in combustion of
low reactive fuels, for example, coal dust, due to the complexity of ensuring the
process of ignition and maintaining the burning of the torch. First of all, this is
due to the relatively high consumption of electric energy, which comprises 2-3% of
the thermal power of the torch being ignited. At the same time, the resource of continuous
operation of devices, in which these methods are implemented, amounts tens of hours,
which makes it difficult to use them in continuous operation to control the burning
mode of the fuel in the process of flaring thereof.
[0005] A method of pulverized coal combustion is known, considered as the closest prior
art, wherein said method is described in patent No.
RU2498159 (F23Q 5/00; published on 10.11.2013), which consists of creating an electric arc discharge
in an ignition zone, feeding an air-fuel mixture to the ignition zone, igniting the
air-fuel mixture in the ignition zone, creating a diffuse electric discharge, and
applying the diffuse electric discharge to a border zone of the flame formation of
the burning fuel torch, and carrying out the fuel flaring.
[0006] A technical solution disclosed in the patent of invention No.
RU2377467C2 (IPC F23D 1/00; published on 27.12.2009) is known, which is a device for fuel flaring.
Said device comprises an ignition chamber, the inner surface of which has a cylindrical
shape, a supply port for feeding an air-fuel mixture to said chamber, and a plasmatron
equipped with rod electrodes. The plasmatron is mounted on the side surface of the
ignition chamber, at entry section of the chamber. The device also comprises a nozzle
of the ignition chamber with plasmatron mounted therein, and a secondary air port.
[0007] The design of this device provides no separation between the ignition chamber and
the cooling chamber, therefore secondary air is supplied directly to the ignition
chamber. This increases the risk of rapid separation of the torch and extinction thereof
in the process of the operation of said device, which is a significant disadvantage
of the known device.
[0008] The technical solution disclosed in the patent of invention No.
RU2059926C1 (IPC F23D 1/00, F23Q 13/00; published on 10.05.1996) is known, which is a device
for fuel flaring. This device comprises an air-fuel mixture supply port, a secondary
air port with a swirler mounted therein, and a plasmatron-igniter with rod electrodes.
Said device is characterized in that the plasmatron-igniter with the rod electrodes
is mounted in the air-fuel mixture supply port, the electrodes are made of graphite
and placed along the entire length of the air-fuel mixture supply port, and the plasmatron-igniter
is equipped with double-flow nozzles and mounted with the possibility of longitudinal
movement between the rod electrodes, wherein the plasmatron nozzles are oriented toward
the ends of the electrodes.
[0009] In regards to operation, this device is characterized by low reliability of the ignition
of pulverized coal fuel, and also a large specific electric power of the burner and
large size thereof. This, in turn, leads to high specific energy consumption in the
process of operation of the known device, which is a significant disadvantage thereof.
In addition, due to the rapid wear of the rod electrodes, it becomes necessary to
replace them, which complicates the known device for fuel flaring maintenance operations.
As the closest prior art, the well-known technical solution disclosed in the patent
of invention No.
RU2410603C1 (IPC F23Q 5/00, F23Q 13/00; published on 27.01.2011) was chosen, which solution is
a device for fuel flaring. This device comprises a housing, rod electrodes connected
to a source of high-frequency alternating current for generating an electric arc,
an air-fuel mixture supply port and a secondary air port, wherein, according to the
invention, the housing is divided into an ignition chamber and a cooling chamber,
wherein a secondary air passage with rod electrodes mounted therein is made within
the cooling chamber. Said features are common with the proposed technical solution.
[0010] A disadvantage of this device is the limited thermal power of the initiated torch
and the impossibility of organizing the optimal process of combustion of the entire
amount of fuel, since the design of the known device is focused only on the generation
of the initiating torch. Supplying the secondary air to the ignition chamber also
limits the amount of flammable pulverized coal due to the need to increase air volumes
and, as a consequence, the values of the flow rate of the air-fuel mixture are unacceptable,
in terms of torch separation. The low reliability of ignition of low reactive fuel
(lean, ballasted, and waterlogged fuels, for example, coal-water fuel) should be counted
as disadvantages of this device. This is primarily due to the subsequent ignition
of the main torch from the torch obtained. When burning fuel with a high degree of
slag formation, slagging of the ignition chamber surfaces can occur, which requires
persistent maintenance. This leads to a decrease in the reliability of the ignition
system operation.
Summary of the Invention
[0011] The aim of the claimed invention is to provide a device and method that would be
able to ensure stable ignition and efficient combustion of the entire amount of pulverized
coal fuel fed to the burners of the boiler, with reduced requirements for combustible
fuel (ballasted, lean, and waterlogged coals), and temperature of the fuel and air
fed to the burner, which ensures that the boiler starts up from a cold state with
cold components and with minimal electrical energy consumption without the use of
highly reactive fuel. That ensures the reliability of the boilers operation and the
safety of the processes of kindling and fuel combustion.
[0012] The technical result of the claimed invention is the possibility of flaring of the
fuel, including the low reactive one, and increasing the efficiency of combustion
thereof.
[0013] The efficiency of fuel combustion is understood as the generation of thermal energy
with minimal losses thereof (minimal excessive air, i.e., close to the stoichiometric
value, and also minimal chemical and mechanical underburning of the fuel).
[0014] The reason for the impossibility of achieving the above technical result with known
technical solutions is that in the process of low reactive fuel flaring, for example,
coal dust, when changing technical composition thereof (humidity, ash, etc.), the
intensity of chemoionization processes can decrease with resulting decrease in the
electrostatic potential of the pre-flame zone of the torch, which leads to unstable
burning of the fuel and to the torch extinction.
[0015] Taking into account the characteristics and analysis of the known technical solutions,
it can be concluded that the problem of ensuring sustainable ignition and stabilization
of the burning mode of the fuel in the process of flaring thereof is actual to this
date.
[0016] The technical result provided by the invention is achieved in that the device for
fuel flaring comprises an ignition chamber, an alternating current source, at least
two rod electrodes connected to the alternating current source, an air-fuel mixture
supply port, a secondary air port and a cooling chamber, wherein passages for the
rod electrodes mounting are made between the ignition chamber and cooling chamber.
The inventive device for fuel flaring is characterized in that a constant voltage
source is connected to at least one of the rod electrodes, relative to the shell of
the ignition chamber, and a torch formation chamber with the secondary air port connected
thereto is mounted at the outlet of the ignition chamber. Such design of the device
allows the excitation of a diffuse electric discharge between the electrodes, which
produces ionization and ignition of the air-fuel mixture. Furthermore, due to chemoionization
processes, a highly ionized pre-flame zone of the torch is formed, which is the main
condition for ensuring heterogeneous chemical reactions of oxidation of the air-fuel
mixture to occur, which makes it possible to efficiently combust low reactive fuel,
i.e., the oxidation reaction of which has high chemical reaction rates. The presence
of at least one rod electrode with the constant voltage source connected thereto,
relative to the shell of the ignition chamber, allows to maintain a highly ionized
state of the pre-flame zone of the torch and ensure that the necessary condition is
fulfilled for the complete burning out of the fuel mixture in the process of flaring
thereof. In addition, the presence of the secondary air port connected to the torch
formation chamber ensures the formation and burning of the torch in the furnace by
feeding secondary air to the torch formation chamber through the secondary air port.
Thus, opening the possibility for fuel flaring is achieved, and also increasing the
efficiency of the combustion of the low reactive fuel.
[0017] The rod electrodes are mounted on heat-conductive and electrically conductive racks,
the other end of which is fixed on support plates placed within the cooling chamber,
in isolation from the electrically conductive surfaces of the device. This allows,
on the one hand, to reliably fix the rod electrodes, and on the other hand, to remove
excessive heat from the rod electrodes and base plates. This leads to an increase
in the lifetime of the rod electrodes, increasing the reliability of the operation
of the device for efficient combustion of the low reactive fuel.
[0018] In addition, the cooling chamber is provided with a sealing air supply port, wherein
the secondary air is supplied to the torch formation chamber. This allows to remove
heat from the rod electrodes by supplying sealing air to the cooling chamber, which
leads to efficient heat removal from the electrodes in the device, which increases
the reliability of the operation of the device for the efficient combustion of the
low reactive fuel. Also, supplying the secondary air to the torch formation chamber
ensures optimal torch formation and, as a result, the efficiency of the combustion
of the low reactive fuel using the inventive device for fuel flaring.
[0019] The technical result is achieved using a method of pulverized coal combustion, which
consists of creating an electric arc discharge in an ignition zone, feeding an air-fuel
mixture to the ignition zone, igniting the air-fuel mixture in the ignition zone,
creating a diffuse electric discharge, applying the diffuse electric discharge to
a border zone of flame formation, and carrying out fuel flaring, while setting the
magnitude of the electrostatic potential of the border zone of flame formation at
a predetermined level, which ensures the required parameters of fuel burning in the
process of flaring thereof.
Description of the Drawings
[0020] The implementation of the invention is described hereinafter in accordance with the
accompanying drawings, which are presented to illustrate the essence of the invention
and in no way limit the scope of the invention.
[0021] The following drawings are attached to the application:
FIG. 1 is a basic scheme of a device for fuel flaring;
FIG. 2 is a basic scheme of an ionization unit;
[0022] These figures contain the following positions:
1: an air-fuel mixture supply port;
2: an ionization unit;
3: a torch formation chamber,
4: an alternating current source;
5: a constant voltage source;
6: ignition chambers;
7: cooling chambers;
8: rod electrodes;
9: electrically conductive and heat-conductive racks;
10: insulators;
11: support plates;
12: fasteners;
13: passages for electric cable;
14: passage for cooling air entering;
15: passage for racks.
Detailed Description of the Invention
[0023] Numerous implementation details are set forth in the following detailed description
of the embodiments of the invention to provide a clear understanding of the present
invention. However, it is obvious to a person skilled in the art how to use the present
invention, both with and without these implementation details. In other instances,
well-known methods, procedures, and components have not been described in detail so
as not to obscure the understanding of the features of the present invention.
[0024] Furthermore, it is clear from the foregoing that the invention is not limited to
the above-described implementation. Numerous possible modifications, changes, variations
and substitutions, without departing from the spirit and scope of the present invention,
are obvious to those skilled in the field.
[0025] The present invention is directed to the developing of a device and method that would
be able to ensure stable ignition and efficient combustion of the entire amount of
pulverized coal fed to the burners of the boiler, with reduced requirements for combustible
fuel (ballasted, lean, and waterlogged coals) and for temperature of the fuel and
air fed to the burner, which ensures that the boiler starts up from a cold state with
cold components and with minimal electrical energy consumption without the use of
highly reactive fuel.
[0026] Any known air-fuel mixture can be used as a fuel mixture. Fuel mixture is a mixture
of air or an oxidizing gas, for example, oxygen, and fuel. The fuel used can be in
any aggregate state (solid, liquid or gaseous), however, the necessary condition is
the size of the particles or drops of fuel, if solid or liquid fuel is used as a component
of the fuel mixture, respectively. The particle size for solid fuel should not exceed
60 microns. At the same time, the droplet size for liquid fuel should not exceed 10
microns. Examples of solid fuels that can be used as a component of air-fuel mixture
are coal, peat, wood processing wastes, etc. Examples of liquid fuel that can be used
as a component of air-fuel mixtures are petroleum products, water-coal fuel, etc.
[0027] As an alternating current source 4, an alternating current source of any known design
can be used, for example, a commercially available converter of a power source of
a plasma generator

P


943- 5- 0,4 YX
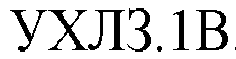
3.1B. As a constant voltage source 5, a constant voltage source of any known design
can be used, for example, a commercially available high voltage source, made according
to the voltage multiplication scheme,

BHP-5/50. An ionization unit 2 comprises an ignition chamber 6, a cooling chamber
7, rod electrodes 8 mounted on electrically conductive and heat-conductive racks 9,
supporting insulators 10 mounted outside the ignition chamber 6, which serve as a
support for the plate 11 that connected to insulators 10 and rack 9 by fasteners 12.
In the cooling chamber 7, which is hermetically sealed, passages are made for an electric
cable 13, passage 14 for cooling air entering and passage 15 for racks 9.
[0028] The air-fuel mixture supply port 1 may be made of any known engineering material,
for example, steel. The ionization unit 2 can be made of any known electrically conductive
engineering material, for example, steel. The rod electrodes 8, racks 9, and the support
plate 11, in turn, can be made of any known electrically conductive and heat-conductive
material, for example, copper or bronze. The torch formation chamber 3 can be made
of any known heat-resistant material. As an example, the torch formation chamber 3
can be made of heat-resistant alloy steel, for example, steel grade X20H35. In addition,
the torch formation chamber 3 may have an internal high-temperature thermal insulation
coating made using any known flame-resistant material, for example, material based
on fireclay powder, fire clay, etc., which is resistant to temperature in the temperature
range with the upper limit reaching 1500 °C - 1700 °C.
[0029] The operation of the device and the implementation of the method of plasma fuel flaring
are as follows:
an electric arc discharge is created in the ignition zone, the air-fuel mixture is
fed to the ignition zone, the air-fuel mixture in the ignition zone is ignited, a
diffuse electric discharge is created, the diffuse electric discharge is applied to
the border zone of flame formation, and fuel flaring is carrying out, while maintaining
the electrostatic potential of the border zone of flame formation at a given level.
[0030] It is known, [
Lauton D., Weinberg F. Electrical aspects of burning. / Transl. from English under
the editorship of V. A. Popov. M.: Energy, 1976. - 296 p.], that the process of flame formation, the stability and intensity of burning of
the entire torch depend on the state of the pre-flame zone, which is especially important
when burning low-reactive fuel (coal dust, coal-water fuel), which cannot be burned
in usual conditions so that the use of additional measures is required, for example,
pre-heating of the fuel and oxidizer.
[0031] The prepared air-fuel mixture is fed through the air-fuel mixture supply port 1 to
the ignition chamber 6. From the alternating current source 4, alternating current
voltage is supplied to the rod electrodes 8 in the frequency range 1-30 kHz, the breakdown
of the interelectrode space occurs, as a result of which the electrical circuit is
closed. As a result, a diffuse electric discharge is excited, which produces ionization
and ignition of the air-fuel mixture. At the same time, due to chemoionization processes,
a highly ionized pre-flame zone of the torch is formed, which is the main condition
for ensuring heterogeneous chemical reactions of oxidation of the entire amount of
the air-fuel mixture to occur. Due to the relatively high electrical conductivity,
the diffusion discharge acquires an equal electrostatic potential, which provides
the required electrostatic potential in the pre-flame zone. With a change in this
potential, a change in the intensity of the ionic wind taking the combustion products
of the torch into the ignition zone and supporting the processes of fuel ignition
occurs, along with chemical processes in the highly ionized regions of the diffuse
discharge and the pre-flame zone of the torch. With a decrease in the voltage of the
constant voltage source, the potential of the pre-flame zone of ignition decreases,
upon that the concentration of charges in the pre-flame zone of the torch, the amount
of ionic wind and, as a result, the intensity of the torch burning decrease up to
the extinction of the torch. Ensuring the occurrence of heterogeneous chemical processes
is the main condition for the combustion of low reactive fuels, including coal-water
fuel. To ensure the highly ionized state of the pre-flame zone of the torch, at least
one rod electrode 8 is supplied with an electrostatic potential from the constant
voltage source 5, relative to the electrically conductive surface of the ignition
chamber 6. The ignition chamber 6 can be made as part of the air-fuel mixture supply
port 1. The ignited air-fuel mixture enters the torch formation chamber 3, where the
main chemical processes take place. Further, the formed torch containing highly activated
components of the fuel and oxidizer enters the furnace of the boiler, in which the
complete combustion of the fuel is carried out. When changing the parameters of the
fuel, its amount, etc., the value of the potential of the pre-flame zone is corrected,
providing the required parameters of the torch burning. The range of variation of
the electric potential is from 0.1 to 5 kV.
[0032] To ensure the forming and burning of the torch in the furnace, the secondary air
is supplied through the secondary air port to the torch formation chamber 3. Excessive
air in the torch formation chamber 3 is set taking into account the arrangement of
the fuel burning in the furnace.
[0033] The heat generated on the rod electrodes 8 is removed through the electrically conductive
racks 9 to the support plate 11, which is cooled by the sealing air entering under
the shell of the ionization unit 2. After that, the heat is discharged into the torch
ignition chamber 3 through the passages 15 for the electrically conductive racks 9
made in the torch ignition chamber 3. Part of the thermal energy from the rod electrodes
8 and racks 9 is removed by the flow of the air-fuel mixture, which ensures the durability
of the operation of the rod electrodes 8.
[0034] At the outlet of the torch formation chamber 3, the fuel mixture is obtained with
a temperature above 700 °C. and a combustible content of up to 50% in the gas phase.
Such a mixture burns steadily, which makes it possible to increase the reliability
of the torch burning even in the cold furnace, which makes it possible to use this
device for ignition of boilers without the use of highly reactive fuel, providing
a high degree of fuel burn-off.
[0035] The frequency of operation of the alternating current source 4 is selected from the
conditions needed for ensuring a stable diffuse discharge and technical limitations
associated with the technical implementation, and is in the range of 3-50 kHz. To
limit the erosion of the rod electrodes 8, the amplitude current should be in the
range of 0.1-2 A, which ensures the durability of the operation of the rod electrodes
8 without replacing them.
[0036] The embodiments of the sequence of operations in the method and device described
in the text of this application are confirmed by tests, but are not the only ones
possible and are presented for most clearly disclosing the essence of the invention.
[0037] The claimed invention is technologically advanced and easy to use and manufacture.