Domaine technique
[0001] La présente invention concerne un composant comprenant un alliage d'aluminium et
de lithium revêtu d'un revêtement céramique. Ainsi que le procédé pour former le revêtement.
Etat de la technique
[0002] Les alliages d'aluminium contenant le lithium possèdent des propriétés intéressantes.
Parmi elles on peut mentionner leur légèreté en comparaison aux autres alliages d'aluminium
conventionnels. En effet, le lithium est le plus léger des éléments métallique et,
pour chaque 1% de lithium ajouté à l'alliage d'aluminium permet de réduire de 3 %
la densité de l'aluminium et d'augmenter de 5% son module élastique. Ce type d'alliage
a également une grande résistance à la fatigue et à la corrosion, permettant ainsi
d'allonger la durée de vie du produit. Ces alliages sont 100% recyclables. Les alliages
d'aluminium contenant le lithium trouvent leurs applications dans les domaines de
l'aéronautique, de l'aérospatiale et dans le militaire.
[0003] Cependant, ces alliages présentent une mauvaise résistance à l'usure et à la corrosion.
En effet, malgré l'ajout de lithium, cet alliage, comme tous les alliages d'aluminium
brut, présente des faiblesses à la corrosion et à l'usure et impacts.
[0005] Le document
EP1818428 décrit un procédé de revêtement céramique électrolytique pour un alliage d'aluminium.
Bref résumé de l'invention
[0006] Un but de la présente invention est de proposer un composant revêtu exempt des limitations
des composants connus.
[0007] Selon l'invention, ces buts sont atteints notamment au moyen d'un composant comprenant
un alliage d'aluminium comprenant entre 0.1 et 10 % en poids de lithium, caractérisé
en ce ledit composant est traité à l'aide d'un procédé d'oxydation par micro-arc plasma
permettant d'obtenir un revêtement céramique à la surface de l'alliage d'aluminium
et en ce que le revêtement a une dureté comprise entre 1800 Hv (17.65 GPa) et 2000
Hv (19.61 GPa).
[0008] L'invention concerne également un procédé permettant de croître un revêtement céramique
à la surface du composant, le procédé étant un procédé d'oxydation par micro-arc plasma
et comprenant les étapes d'immerger le composant à revêtir dans un bain électrolytique
composé d'une solution aqueuse d'hydroxyde de métal alcalin, le composant formant
l'une des électrodes; et d'appliquer un courant alternatif ayant une fréquence comprise
entre 10 Hz à 10'000 Hz, de façon à appliquer une tension entre le composant et une
autre électrode variant entre 0 V et une valeur comprise entre 100 V et 1000 V.
[0009] Cette solution présente notamment l'avantage par rapport à l'art antérieur de fournir
un composant ayant une dureté élevée, une excellente résistance à l'usure, aux chocs,
et à la corrosion.
[0010] Le procédé d'oxydation par micro-arc plasma est également une technologie donc l'impact
environnemental est faible, en particulier au vu des techniques d'anodisation conventionnelle
donc les bains acides sont fortement déconseillés pour la protection de l'environnement.
Brève description des figures
[0011] Des exemples de mise en œuvre de l'invention sont indiqués dans la description illustrée
par les figures annexées dans lesquelles :
la figure 1 illustre une installation d'électrolyse;
la figure 2 montre une vue en coupe du composant avec le revêtement formé par le procédé
d'oxydation par micro-arc plasma;
la figure 3 montre un revêtement formé par le procédé d'oxydation de l'invention;
la figure 4 illustre une perspective d'une telle boite de montre;
la figure 5 montre le revêtement formé sur un levier;
la figure 6 montre le revêtement formé sur une lunette;
la figure 7 montre le revêtement formé sur une carrure;
la figure 8 montre le revêtement formé sur la corne de carrure;
la figure 9 montre un vue en coupe d'une portion filetée de la corne de carrure;
la figure 10 est un graphique qui rapporte les épaisseurs mesurée du revêtement formé
sur les différentes parties de la boite de montre;
la figure 11 montre les endroits de mesure d'épaisseur du revêtement;
la figure 12 est un graphique qui rapporte les épaisseurs mesurée du revêtement formé
sur les différentes parties de la boite de montre.
la figure 13 montre l'état de la surface de la carrure de montre en alliage d'aluminium-lithium
sur laquelle le revêtement a été formé, après usure;
la figure 14 montre l'état de la surface de la carrure de montre en alliage d'aluminium-lithium
sur laquelle le revêtement a été formé, après des tests de chocs;
la figure 15 montre l'état de la surface de la carrure de montre en alliage d'aluminium-lithium
sur laquelle le revêtement a été formé, après des tests de corrosion; et
la figure 16 montre une photographie d'un boîtier de montre en alliage aluminium-lithium
ayant subi le procédé d'oxydation de l'invention.
Exemple(s) de mode de réalisation de l'invention
[0012] Selon l'invention, un composant 1 comprend un alliage d'aluminium comprenant entre
0.1 et 10 % en poids de lithium. Le composant est traité à l'aide d'un procédé d'oxydation
par micro-arc plasma (aussi connu sou le nom anglais de "micro-arc oxydation" et l'acronyme
"MAO") de sorte à obtenir un revêtement céramique 2 à la surface de l'alliage d'aluminium.
[0013] L'alliage d'aluminium contenant du lithium peut être un des alliages commerciaux
disponibles sur le marché. Par exemple, l'alliage d'aluminium-lithium peut comprendre
l'un des alliages mentionnés dans la table 1. Dans la table, la première ligne donne
le nom de l'alliage et la colonne de gauche l'élément ainsi que le contenu de l'élément
en % en poids dans les colonnes successives. Un tel alliage d'aluminium-lithium contiendra
donc jusqu'à 2.45 % en poids de lithium, plus particulièrement entre 0.88 et 2.45
% en poids de lithium.
Table 1
alliage |
2050 |
2090 |
2091 |
2099 |
2195 |
2196 |
2199 |
8090 |
Weldalite 049 |
Cu |
4.3 |
2.7 |
2.1 |
2.4-3.0 |
3.05 |
2.90 |
2.3-2.9 |
1.3 |
5.4 |
Li |
0.88 |
2.2 |
2.0 |
1.6-2.0 |
1.70 |
1.67 |
1.4-1.8 |
2.45 |
1.3 |
Zn |
<0.01 |
- |
- |
0.4-1.0 |
0.01 |
0.01 |
0.2-0.9 |
- |
- |
Mg |
0.58 |
- |
- |
0.1-0.5 |
0.39 |
0.40 |
0.05-0.4 |
0.95 |
0.4 |
Mn |
- |
- |
- |
0.1-0.5 |
0.01 |
0.31 |
0.1-0.5 |
- |
- |
Ag |
0.34 |
- |
- |
- |
0.35 |
0.38 |
- |
- |
0.4 |
Zr |
0.13 |
0.12 |
0.1 |
0.05-0.12 |
0.12 |
0.1 |
0.05-0.12 |
0.12 |
0.14 |
Fe |
0.03 |
- |
- |
0.07 max |
0.05 |
0.04 |
0.07 max |
- |
- |
Si |
0.03 |
- |
- |
0.05 max |
0.03 |
0.03 |
0.05 max |
- |
- |
Ti |
0.04 |
- |
- |
- |
0.03 |
0.03 |
- |
- |
- |
Al |
reste |
reste |
reste |
reste |
reste |
reste |
reste |
reste |
reste |
[0014] La figure 1 illustre un agencement d'une installation, dans laquelle une cuve 3 contient
un bain électrolytique 4. A l'intérieur de l'électrolyte 4 plonge une contre-électrode,
ou cathode, 5 et une anode qui correspond au composant 1 à revêtir. A la figure 1
sont également représentés un bloc d'alimentation en courant 6 apte à générer un courant
alternatif 31.
[0015] Selon un mode de réalisation, le procédé d'oxydation par micro-arc plasma comprend
les étapes d'immerger le composant 1 à revêtir dans l'électrolyte 4 et de faire passer
le courant alternatif 31 de façon à appliquer une tension entre le composant 1 et
la cathode 5.
[0016] L'électrolyte 4 peut comprendre une solution aqueuse d'hydroxyde de métal alcalin,
tel que le potassium ou le sodium, et d'un sel oxyacide d'un métal alcalin. L'électrolyte
4 est typiquement maintenu à une température comprise entre 10°C et 55°C.
[0017] De façon préférée, le courant appliqué comprend des pulses de courant positifs et
négatifs alternant avec une fréquence comprise entre 10 Hz à 10'000 Hz. L'amplitude
des pulses de courant est comprise entre 2 et 200 A/dm
2 de manière à appliquer une tension entre le composant 1 et la cathode 5 de l'ordre
de 100 V à 1000 V. En effet, une tension comprise de 100 et 1000V permet de créer
un plasma électrolytique nécessaire à la formation du revêtement 2 sur le composant
1.
[0018] Dans un mode de réalisation, les pulses de courants sont séparés par un temps mort
où aucun courant n'est appliqué. La durée du temps mort est de préférence d'environ
10% de la durée totale du pulse de courant. La durée du temps mort est telle que la
tension chute à zéro. Par exemple, chacun des pulses de courant positif et négatif
peut présenter une amplitude maximale suivie d'une décroissance du courant jusqu'à
une valeur nulle. La durée du pulse où la valeur du courant est nulle est d'environ
10% de la durée totale du pulse de courant.
[0019] Autrement dit, lors du temps mort la tension doit chuter à zéro, c'est-à-dire que
la tension est cyclée entre une tension de base (baseline) et une tension plafond,
ou maximale (ceiling line). La tension de base minimale est préférablement ajustée
à une tension comprise entre 0 et 99,9% du pic maximum de la tension plafond. La tension
de base (par exemple 30% de la tension plafond) permettra de favoriser la formation
d'émission de micro arcs électriques visible à l'œil nu, alors qu'une tension de base
plus conséquente (par exemple 60% de la tension plafond), permettra de favoriser la
création d'un plasma continu, également visible à l'œil nu (relatif à la perception
rétinienne de 0.1 à 0.2 secondes). L'influence du choix des tensions moyennes minimales
de base par rapport à la tension maximale et donc du type de micro-arcs obtenus permet
donc de maitriser une couche plus ou moins dense et homogène. La densification de
la couche étant également sujette à la fréquence d'alternance entre les courants anodiques
et cathodiques. En effet dans le premier cas la croissance de la couche nanoporeuse
se réalisera alors que dans le second la densification des nanoporosités opérera.
[0020] La vitesse de croissance du revêtement 1 dépend du type de fréquence et de la forme
du pulse, en particulier du passage entre un courant cathodique et anodique (et vice-versa)
et de l'amplitude de courant (et donc de la tension appliquée). Par exemple, la vitesse
de croissance du revêtement est de l'ordre de 1 micron/ minute pour une tension appliquée
de 100 à 400 V et une fréquence de l'ordre de 1000 Hz.. L'épaisseur du revêtement
ainsi obtenu peut aller de quelques microns, de manière homogène sur la pièce, pour
autant que le posage utilisé pour maintenir le composant dans le bain soit adapté
et ne modifie pas la formation des micro arcs et ne les éteignent pas,) à quelques
centaines de microns. Le procédé d'oxydation par micro-arc plasma est décrit, par
exemple, dans le document
WO03/083181.
[0021] La figure 2 montre une vue en coupe du composant avec le revêtement 1 formé par le
procédé d'oxydation par micro-arc plasma. Le revêtement comprend une couche dure céramique
fonctionnelle 21 épaisse formant environ deux tiers de l'épaisseur totale du revêtement
2, et une couche externe poreuse 22 formant environ un tiers de l'épaisseur totale
du revêtement 2 De plus, lors de sa croissance, le revêtement 2 est formé en partie
par la transformation de la matière substrat 7 et en partie par croissance au-delà
de la surface initiale 8 du composant (représenté par la ligne hachurée dans la figure
2). Dans la figure 2, la surépaisseur du revêtement 2 est représentée par la différence
d'épaisseur entre la surface initiale 8 et la surface supérieure de la couche 22.
[0022] Le revêtement 1 formé par le procédé d'oxydation par micro-arc plasma sur le composant
en alliage aluminium-lithium a une dureté élevée, proche de 2000 Hv. Il a également
une excellente résistance à l'usure, aux chocs, à la corrosion. Le revêtement 1 est
de coloration correspondant à la coloration naturelle de l'aluminium oxydé. Par exemple,
le revêtement 1 a une coloration brun foncée dans le cas de l'alliage aluminium-lithium
2050 (voir table 1).
[0023] Le procédé d'oxydation peut comporter une étape préalable de préparation de la surface
8 du composant 1. Cette étape de préparation peut comprendre le nettoyage et dégraissage
de la surface 8, par exemple à l'eau bouillante ou à un nettoyant alcalin tel qu'une
solution de nettoyant PARCO (produit de Henkel Surface Technologies division de Henkel
Corporation, Madison Heights, Michigan). L'étape de préparation peut être suivie d'une
étape de rinçage, par exemple à l'eau distillée.
[0024] Afin d'obtenir un état de surface optimum et retirer les derniers microns de la couche
poreuse 22 de céramique, une étape de tribofinition peut être réalisée à l'issue de
la formation du revêtement 1 par le procédé d'oxydation. Cette étape de tribofinition
peut comprendre, par exemple, un microsablage.
[0025] La figure 3 montre un revêtement 1 formé par le procédé d'oxydation de l'invention.
En particulier, les figures 3a et 3c montrent le revêtement 2 vu de face, respectivement
après sa formation (figure 3a) et après l'étape de tribofinition (figure 3c). La figure
3b est une vue en coupe montrant le substrat d'alliage Al-Li 7 et du revêtement 2.
[0026] Le composant 1 à revêtir peut aussi bien être issu d'un procédé de mise en forme
conventionnel de type usinage, décolletage ou mise en forme par procédé de moulage
de l'aluminium liquide (type procédé Cobapress).
[0027] A titre d'exemple, le procédé d'oxydation par micro-arc plasma a été appliqué à différentes
parties d'une boite de montre fabriqué dans un alliage aluminium-lithium. La figure
4 illustre une perspective d'une telle boite de montre 9. En particulier, le revêtement
1 a été formé sur des parties de la boite de montre 9 comprenant une carrure 91, une
corne de carrure 92, un levier 93, un pont de fixation 94, un fond (non visible sur
la figure), une lunette 95 et un cache-couronne 96.
[0028] Les figures 5 à 9 montrent des micrographies de vues d'une coupe métallographique
des revêtements 2 formés par le procédé d'oxydation sur les différentes parties de
la boite de montre 9. En particulier, la figure 5 montre le revêtement 2 formé sur
le levier 93. La figure 6 montre le revêtement 2 formé sur la lunette 95. La figure
7 montre le revêtement 2 formé sur la carrure 91. La figure 8 montre le revêtement
2 formé sur la corne de carrure 92. Dans ces figures, la couche visible en gris pâle
correspond à une couche de cuivrage 10 déposée sur le revêtement à des fins de protection
lors de la préparation de la coupe métallographique.
[0029] Dans le cas où la portion du composant 1 comprend une ou des zones comportant une
structuration fine, par exemple un filetage, des trous ou des taraudages, il peut
être avantageux que ces zones soient revêtues avec le revêtement 2 présentant une
épaisseur plus faible que sur le reste de la surface du composant 1. En effet, la
formation d'un revêtement épais dans les zones structuration fine peut résulter dans
un nivellement de la structuration. Ceci est particulièrement le cas lorsque la structuration
a une dimension inférieure à 100 µm.
[0030] Dans un mode de réalisation, le procédé d'oxydation comprend une étape de former
le revêtement 2 sur la ou les zones ayant la structuration fine. La ou les zones avec
la structuration fine sont ensuite masquées de façon à pouvoir former le revêtement
2 sur le reste du composant 1 sans affecter la ou les zones ayant la structuration
fine. Ensuite, le revêtement est formé sur le reste de la surface du composant 1.
L'épaisseur du revêtement dans la ou les zones avec la structuration fine dépendra
de la dimension de la structuration. Par exemple, le revêtement peut être formé sur
la ou les zones avec la structuration fine avec une épaisseur d'environ 10% de la
dimension de la structuration.
[0031] Dans le cas de l'exemple de la boite de montre 9 ci-dessus, la ou les zones avec
la structuration fine peut comprendre des filetages, trous, taraudage, etc. La figure
9 montre un vue en coupe d'une portion filetée de la corne de carrure 92. Le filetage
a une dimension (distance entre la vallée et le sommet) de quelques dizaines de microns.
La portion filetée, ainsi que le reste de la corne de carrure 92, a d'abord été oxydée
suivant le procédé d'oxydation de l'invention de manière à former le revêtement 2
(couche noire) avec une épaisseur de quelques microns (typiquement entre 1 et 5 µm).
La portion filetée a ensuite été masquée et le reste de la corne de carrure 92 a été
de nouveau oxydée selon le procédé d'oxydation de l'invention, permettant de former
le revêtement 2 avec une épaisseur de plusieurs dizaines à centaines de microns, tel
qu'illustré à la figure 8. La portion filetée étant masquée pendant cette étape, le
revêtement 2 ne croit pas d'avantage à cet endroit et son épaisseur reste inchangée.
Le revêtement 2 ayant une faible épaisseur dans la ou les zones avec la structuration
fine permet de densifier et de durcir ces zones sans toutefois niveler la structuration.
[0032] Le masquage de la ou les zones avec la structuration fine peut être réalisé à l'aide
de joints en silicone ou tout autre moyen de protection résistant au traitement d'oxydation
par micro-arc plasma et pouvant être éliminé à la fin du procédé.
[0033] Le graphique de la figure 10 rapporte les épaisseurs mesurée du revêtement 2 formé
sur les différentes parties de la boite de montre 9 tel que discuté ci-dessus. La
ligne du bas du graphique donne la valeur de l'épaisseur. Par exemple, le revêtement
2 d'épaisseur de 50 µm est formé sur la carrure 91 et le fond de la boîte 9. Le revêtement
2 a une épaisseur de 45 µm sur le pont de fixation 94 et le cache-couronne 96, ect.
[0034] La table 2 rapporte l'épaisseur mesurée pour le revêtement 2 formé sur les différents
filetages présents sur la boîte de montre 9, par exemple, dans l'axe fileté de la
carrure 91, pour la fixation du levier 93 sur le pont de fixation 94, pour la fixation
du pont de fixation 94 sur la carrure 91. Les trois lignes 1, 2 et 3 dans la table
2 correspondent à l'épaisseur du revêtement 2 mesurée au sommet de trois filets successifs,
comme montré à la figure 11.
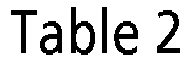
[0035] Le graphique de la figure 12 résume différentes mesures d'épaisseur du revêtement
2 au niveau de trous et filetage des différents éléments de la boîte 9.
[0036] La figure 16a montre une photographie d'un boîtier de montre 9 en alliage aluminium-lithium
ayant subi le procédé d'oxydation de l'invention. La figure 16b montre un détail du
boîtier 9, en particulier une portion du pont de fixation 94, du levier 93 et de la
lunette 95. Ces photographies permettent d'apprécier l'état de surface du composant
avec le revêtement et, dans ce cas, l'étape finale de microsablage.
[0037] Des tests à l'usure réalisés dans des conditions d'usure de billes à une vitesse
de 46 tr/min et avec un mélange de 2 kg de billes céramiques d'un diamètre de 3 mm
dans un-demi litre d'eau et 10 cc de mouillant. La durée du test a été de 36 heures.
Après 6h de ce test, un brillantage de la surface est observé. Après 36 heures de
ce test, aucune évolution ultérieure n'a été observée. Le procédé de céramisation
permet donc une excellente résistance à l'usure. L'état de la surface après usure
du revêtement de céramisation sur un aluminium lithium est montré à la figure 11 dans
le cas d'une surface initiale non usée et après 6h du test, 12h du test et 36h du
test.
[0038] La figure 13 montre l'état de la surface de la carrure de montre en alliage d'aluminium
lithium sur laquelle le revêtement a été formé par le procédé d'oxydation de l'invention,
après 6h d'usure selon le test ci-dessus.
[0039] Des tests de rayures fines ont également été réalisés. Les conditions de ces tests
comprenaient la rotation de l'échantillon à tester à 90 tr/min, dans une boite d'un
volume de 0.6 litre d'un diamètre de 80mm, hauteur de 60mm, paroi en buvard avec 5
à 15 feutres et 10g de poudre de verre « bremor BR 650 ». La durée du test était de
24 heures. La figure 17 montre les tables 3 et 4 qui représentent les observations
faites pour différentes durées de sollicitations de 1 min à 24 heures.
[0040] La figure 14 montre une microphotographie de l'état de la surface de la carrure après
12h de rayures fines. Ces tests montrent que le procédé de céramisation permet également
une excellente résistance aux rayures.
[0041] Des tests de chutes dans lit de gravier ont également été réalisés à l'aide d'une
méthode de tests selon la norme ISO 23160 comprenant des chutes dans un lit de gravier
et chips céramiques de 8 cm sur 500 cm
2 de berlingots céramiques de diamètre 3 mm, d'une longueur de 12 mm et de dureté de
900HV ±100Hv. La hauteur de chute était de 40cm.
[0042] La boite de montre à tester est « chargée » avec une masselotte représentant le poids
du mouvement mécanique normalement intégré dans la tête de montre. On observe après
une dizaine de chutes sur lit de gravier/céramique de très faibles impacts aux niveaux
des arêtes, tels que visibles dans la figure 14 qui montre l'état de surface après
dix de ces tests aux chutes dans lit de gravier hauteur 40cm d'une carrure lestée
avec une masselotte représentant le poids du mouvement mécanique. Ces tests montrent
que le procédé de céramisation permet également une excellente résistance aux chocs
et impacts 40cm sur lit gravier/céramique.
[0043] Des tests de sueur synthétique ont également été réalisés. Ces tests ont été réalisés
selon les conditions des normes NIHS 96-50 et ISO 3160-2, dans lesquelles les pièces
testées sont mises sur un support de coton imbibé de sueur dans un environnement de
40°C±2°C humidité 95 à 100% humidité relative durée du test sur 6 jours.
[0044] Après 6 jours, des piqures de corrosion apparaissent sur des zones de mise à nu de
l'aluminium. La couche de céramisation permet de créer une couche de protection de
l'aluminium substrat (voir la figure 15). Ces tests montrent que le procédé de céramisation
permet également une excellente tenue à la corrosion.
[0045] Globalement un aluminium lithium apporte les propriétés suivantes : 25% plus légère
que les matériaux conventionnels, permettant ainsi d'optimiser la conception des pièces
structurelles et de réduire le poids d'une boite de montre, par exemple, Meilleure
résistance à la fatigue et à la corrosion, ce qui permet de fiabiliser et d'allonger
la durée de vie du produit, 100% recyclable, ce qui apporte une contribution majeure
à une industrie horlogère durable.
[0046] Le revêtement 2 obtenu par le procédé de l'invention est avantageux pour les composants
d'une montre mécanique soumis à des frottements ou contraintes mécaniques. Il est
également avantageux pour traiter des composant d'habillage horloger, comme l'exemple
de la boîte de montre 9 ci-dessus, qui sont soumis à des contraintes environnementales
agressives type usure, humidité, taux de salinité (mer, climats tropicaux ou autres).
Bien sûr, le composant 1 comprenant le revêtement 2 n'est pas seulement d'intérêt
dans l'horlogerie mais peut également être également utilisé dans des domaines divers
tels que la lunetterie et les instruments d'écritures.
Numéros de référence employés sur les figures
[0047]
- 1
- composant
- 2
- revêtement
- 21
- couche dure
- 22
- seconde portion
- 3
- cuve
- 31
- courant alternatif
- 4
- bain électrolytique
- 5
- cathode
- 6
- bloc d'alimentation en courant
- 7
- substrat d'aluminium-lithium
- 8
- surface initiale
- 9
- boite de montre
- 91
- carrure
- 92
- corne de carrure
- 93
- levier
- 94
- pont de fixation
- 95
- lunette
- 96
- cache-couronne
- 10
- couche de cuivrage
1. Composant (1) comprenant un alliage d'aluminium comprenant entre 0.1 et 10 % en poids
de lithium, caractérisé en ce ledit composant (1) est traité à l'aide d'un procédé
d'oxydation par micro-arc plasma permettant d'obtenir un revêtement céramique (2)
à la surface de l'alliage d'aluminium, et en ce que le revêtement a une dureté comprise
entre 1800 Hv (17.65 GPa) et 2000 Hv (19.61 GPa).
2. Le composant selon la revendication 1,
dans lequel le revêtement (2) a une épaisseur comprise entre 1 µm et 100 µm.
3. Le composant selon la revendication 2,
comprenant au moins une portion comportant une structuration de surface ayant une
dimension inférieure à 100 µm; et
dans lequel le revêtement a une épaisseur comprise entre 1 µm et 5 µm.
4. Le composant selon la revendication 3,
dans lequel le revêtement a une épaisseur comprise entre 5 µm et 100 µm sur le reste
du composant, et de préférence entre 20 µm et 50 µm sur le reste du composant.
5. Le composant selon l'une des revendications 1 à 4,
comprenant entre 0.88 et 2.45 % en poids de lithium.
6. Le composant selon l'une des revendications 1 à 5,
dans lequel le revêtement est intact après un essai de dix chutes dans lit de gravier
à une hauteur de 40 cm du composant, selon la norme ISO 23160.
7. Le composant selon l'une des revendications 1 à 6,
dans lequel le revêtement montre un état de surface comportant de légères altérations
(indice 4) après 36 heures d'un test selon la norme ISO 23160 .
8. Le composant selon l'une des revendications 1 à 7, étant un composant horloger, notamment
un composant d'habillage ou un composant d'un mouvement, un composant pour la lunetterie
ou un composant pour un instrument d'écriture.
9. Procédé permettant de croître un revêtement céramique (2) à la surface d'un composant
comprenant un alliage d'aluminium comprenant entre 0.1 et 10 % en poids de lithium,
caractérisé en ce que le revêtement a une dureté comprise entre 1800 Hv (17.65 GPa) et 2000 Hv (19.61 GPa),
et
en ce que le procédé est un procédé d'oxydation par micro-arc plasma et comprend:
immerger le composant à revêtir dans un bain électrolytique (3) composé d'une solution
aqueuse d'hydroxyde de métal alcalin, le composant formant l'une des électrodes;
appliquer un courant alternatif ayant une fréquence comprise entre 10 Hz à 10'000
Hz, de façon à appliquer une tension entre le composant et une autre électrode variant
entre 0 V et une valeur comprise entre 100 V et 1000 V.
10. Le procédé selon la revendication 9,
dans lequel la durée du pulse de courant donnant une tension de 0 V est de 10% de
la durée totale du pulse donnant une tension comprise entre 100 V et 1000 V.
11. Le procédé selon la revendication 9 ou 10,
dans lequel la tension moyenne minimale est ajustée de façon à être comprise entre
0 et 99,9% de la tension maximale et de préférence entre 30 % et 60% de la tension
maximale.
12. Le procédé selon l'une des revendications 9 à 11,
dans lequel une zone du composant (1) comporte une structuration fine ayant une dimension
inférieure à 100 µm; et dans lequel le procédé comprend en outre:
croître le revêtement (2) avec une épaisseur comprise entre 1 µm et 5 µm;
masquer ladite zone de sorte que l'application subséquente du procédé n'ait pas d'effet
sur ladite zone; et
croître le revêtement (2) ayant une épaisseur comprise entre 5 µm et 100 µm sur le
reste de la surface du composant (2).
13. Le procédé selon l'une des revendications 9 à 12,
comportant en outre une préparation de surface comprenant une étape de nettoyage et
dégraissage.
14. Le procédé selon l'une des revendications 9 à 13,
comportant en outre une étape de microsablage.
1. Bauteil (1), das eine Aluminiumlegierung umfasst, die zwischen 0,1 und 10 Gew.-% Lithium
umfasst, dadurch gekennzeichnet, dass das Bauteil (1) mithilfe eines Mikrobogen-Plasmaoxidationsverfahrens behandelt wird,
das es ermöglicht, eine keramische Beschichtung (2) auf der Oberfläche der Aluminiumlegierung
zu erhalten, und dass die Beschichtung eine Härte zwischen 1800 HV (17,65 GPa) und
2000 HV (19,61 GPa) hat.
2. Bauteil nach Anspruch 1, bei dem die Beschichtung (2) eine Dicke zwischen 1 µm und
100 µm hat.
3. Bauteil nach Anspruch 2, das mindestens einen Abschnitt umfasst, der eine Oberflächenstrukturierung
mit einem Maß von weniger als 100 µm beinhaltet, und bei dem die Beschichtung eine
Dicke zwischen 1 µm und 5 µm hat.
4. Bauteil nach Anspruch 3, bei dem die Beschichtung eine Dicke zwischen 5 µm und 100
µm über den Rest des Bauteils und bevorzugt zwischen 20 µm und 50 µm über den Rest
des Bauteils hat.
5. Bauteil nach einem der Ansprüche 1 bis 4, das zwischen 0,88 und 2,45 Gew.-% Lithium
umfasst.
6. Bauteil nach einem der Ansprüche 1 bis 5, bei dem die Beschichtung nach einem Fallversuch
am Bauteil aus einer Höhe von 40 cm in ein Kiesbett mit zehn Wiederholungen gemäß
der Norm ISO 23160 unversehrt ist.
7. Bauteil nach einem der Ansprüche 1 bis 6, bei dem die Beschichtung eine Oberflächenbeschaffenheit
aufweist, die 36 Stunden nach einem Versuch gemäß der Norm ISO 23160 leichte Veränderungen
(Index 4) beinhaltet.
8. Bauteil nach einem der Ansprüche 1 bis 7, das ein Uhrenbauteil, insbesondere ein Gehäusebauteil
oder ein Bauteil eines Uhrwerks, ein Bauteil für Brillen oder ein Bauteil für ein
Schreibgerät ist.
9. Verfahren, das es ermöglicht, eine keramische Beschichtung (2) auf der Oberfläche
eines Bauteils wachsen zu lassen, das eine Aluminiumlegierung umfasst, die zwischen
0,1 und 10 Gew.-% Lithium umfasst,
dadurch gekennzeichnet, dass die Beschichtung eine Härte zwischen 1800 HV (17,65 GPa) und 2000 HV (19,61 GPa)
hat und dass das Verfahren ein Mikrobogen-Plasmaoxidationsverfahren ist und Folgendes
umfasst:
Eintauchen des zu beschichtenden Bauteils in ein Elektrolytbad (3), das aus einer
wässrigen Alkalimetallhydroxidlösung besteht, wobei das Bauteil eine der Elektroden
bildet;
Anlegen eines Wechselstroms mit einer Frequenz zwischen 10 Hz und 10.000 Hz, so dass
eine Spannung zwischen dem Bauteil und einer anderen Elektrode angelegt wird, die
zwischen 0 V und einem Wert zwischen 100 V und 1000 V variiert.
10. Verfahren nach Anspruch 9, bei dem die Dauer des Strompulses, der eine Spannung von
0 V ergibt, 10 % der Gesamtdauer des Pulses beträgt, der eine Spannung zwischen 100
V und 1000 V ergibt.
11. Verfahren nach Anspruch 9 oder 10, bei dem die mittlere Mindestspannung so eingestellt
wird, dass sie zwischen 0 und 99,9 % der Höchstspannung und bevorzugt zwischen 30
% und 60 % der Höchstspannung beträgt.
12. Verfahren nach einem der Ansprüche 9 bis 11, bei dem ein Bereich des Bauteils (1)
eine Feinstrukturierung mit einem Maß von weniger als 100 µm beinhaltet und bei dem
das Verfahren ferner umfasst:
Wachsenlassen der Beschichtung (2) mit einer Dicke zwischen 1 µm und 5 µm;
Maskieren des Bereichs derart, dass die nachfolgende Anwendung des Verfahrens keine
Auswirkung auf den Bereich hat; und
Wachsenlassen der Beschichtung (2) mit einer Dicke zwischen 5 µm und 100 µm über den
Rest der Oberfläche des Bauteils (2).
13. Verfahren nach einem der Ansprüche 9 bis 12, das ferner eine Oberflächenvorbereitung
beinhaltet, die einen Reinigungs- und Entfettungsschritt umfasst.
14. Verfahren nach einem der Ansprüche 9 bis 13, das ferner einen Mikrosandstrahlschritt
beinhaltet.
1. Component (1) comprising an aluminium alloy comprising between 0.1% and 10% by weight
of lithium, characterized in that the said component (1) is treated using a plasma microarc oxidation process which
makes it possible to obtain a ceramic coating (2) at the surface of the aluminium
alloy and in that the coating has a hardness of between 1800 Hv (17.65 GPa) and 2000 Hv (19.61 GPa).
2. Component according to Claim 1,
in which the coating (2) has a thickness of between 1 µm and 100 µm.
3. Component according to Claim 2,
comprising at least one portion comprising a surface structuring having a dimension
of less than 100 µm; and
in which the coating has a thickness of between 1 µm and 5 µm.
4. Component according to Claim 3,
in which the coating has a thickness of between 5 µm and 100 µm over the remainder
of the component and preferably between 20 µm and 50 µm over the remainder of the
component.
5. Component according to one of Claims 1 to 4, comprising between 0.88% and 2.45% by
weight of lithium.
6. Component according to one of Claims 1 to 5,
in which the coating is intact after a test of ten drops of the component into a gravel
bed at a height of 40 cm, according to Standard ISO 23160.
7. Component according to one of Claims 1 to 6,
in which the coating shows a surface state comprising slight detrimental changes (index
4) after 36 hours of a test according to Standard ISO 23160.
8. Component according to one of Claims 1 to 7, being a watchmaking component, in particular
a casing component or a component of a movement, a component for the spectacle trade
or a component for a writing implement.
9. Process which makes it possible to grow a ceramic coating (2) at the surface of a
component comprising an aluminium alloy comprising between 0.1% and 10% by weight
of lithium,
characterized in that the coating has a hardness of between 1800 Hv (17.65 GPa) and 2000 Hv (19.61 GPa)
and
in that the process is a plasma microarc oxidation process and comprises:
immersing the component to be coated in an electrolytic bath (3) composed of an aqueous
alkali metal hydroxide solution, the component forming one of the electrodes;
applying an alternating current having a frequency of between 10 Hz and 10 000 Hz,
so as to apply a voltage between the component and another electrode varying between
0 V and a value of between 100 V and 1000 V.
10. Process according to Claim 9,
in which the duration of the current pulse giving a voltage of 0 V is 10% of the total
duration of the pulse giving a voltage of between 100 V and 1000 V.
11. Process according to Claim 9 or 10,
in which the minimum mean voltage is adjusted so as to be between 0% and 99.9% of
the maximum voltage and preferably between 30% and 60% of the maximum voltage.
12. Process according to one of Claims 9 to 11,
in which a zone of the component (1) comprises a fine structuring having a dimension
of less than 100 µm; and in which the process additionally comprises:
growing the coating (2) with a thickness of between 1 µm and 5 µm;
masking the said zone so that the subsequent application of the process does not have
an effect on the said zone; and
growing the coating (2) having a thickness of between 5 µm and 100 µm on the remainder
of the surface of the component (2).
13. Process according to one of Claims 9 to 12, additionally comprising a surface preparation
comprising a cleaning and degreasing stage.
14. Process according to one of Claims 9 to 13, additionally comprising a microsanding
stage.