Technical Field
[0001] The present invention relates to an inkjet head, an inkjet recording device, and
a method for producing an inkjet head.
Background Art
[0002] There has been known an inkjet recording device (inkjet printer) that ejects (discharges)
ink droplets from nozzles of inkjet heads, thereby forming an image on a recording
medium. When the inkjet recording device ejects ink droplets, ink may adhere to nozzle
surfaces (around the openings of the nozzles on the ejection side) of the inkjet heads
owing to the influence of ink mist generated in the printer or ink bounced by the
recording medium. It is known that ink adhering to the nozzle surfaces affects ejection
angles of ink droplets when the ink droplets are ejected from the nozzles and changes
the ejection angles.
[0003] In order to prevent adhesion of ink to nozzle surfaces, there is known a method of
forming an ink-repellent layer on nozzle surfaces by coating the nozzle surfaces with
an ink-repellent agent. As the ink-repellent layer, there is known a film formed by
bonding organic functional groups containing fluorine through dehydration-condensation
reactions with silane coupling ([-OH] + [HO-Si-R-F] → [H
2O] + [-O-Si-R-F]) (see Patent Literature 1). Silanol groups in the compound of the
silane coupling agent and hydroxy groups on the surface of a base film form siloxane
bonds. It is desirable that the base film have a strong covalent bonding property.
It is known that a base film having a strong ionic bonding property does not form
siloxane bonds (see Non-Patent literature 1).
[0004] Further, there is proposed a nozzle substrate that has inner walls of nozzle holes
and a plurality of layers of ink resistant protective films (see Patent Literature
2). First, a thermal oxide film having a high coating property is formed. Next, a
metal oxide having ink resistance is formed on the inner walls, the front surface,
and the back surface by a CVD (Chemical Vapor Deposition) method, and then a water-repellent
film is formed on the ejection surface side. As the ink-resistant protective film,
a metal oxide, such as tantalum pentoxide, hafnium oxide, niobium oxide, titanium
oxide, or zirconium oxide, is used. This is because these metal oxides are highly
resistant to alkaline ink (discharging liquid). Also, the water-repellent film preferably
contains a fluorine-containing organosilicon compound as a main component. This is
because hydroxy groups on the surface of the ink-resistant protective film firmly
bond with hydrolyzing groups, such as methoxy groups, of the fluorine-containing organosilicon
compound, so that adhesion between the ink-resistant protective film and the water-repellent
film formed on the surface of the ink-resistant protective film is improved.
[0005] Also, there is known a wiping method of wiping off ink on a liquid-repellent layer
(water-repellent film) of a nozzle substrate of an inkjet head of an inkjet recording
device.
Citation List
Patent literature
Non-Patent literature
[0007]
Non-Patent literature 1: Yoshinobu NAKAMURA, Kazuya NAGATA, et al. "Effects and usage of silane coupling agents
(Silane-coupling-zai no kouka to shiyouhou)", S&T Publishing, November 15, 2012.
Non-Patent literature 2: Takeshi OWAKI, Yasunori TAGA, "Journal of the Surface Finishing Society of Japan",
vol. 49, p. 191-194, 1998
Summary of Invention
Technical Problem
[0008] In Patent Literature 2, metal elements that may be contained in a metal oxide film
used as a protective film, such as tantalum pentoxide, hafnium oxide, niobium oxide,
titanium oxide, and zirconium oxide, are transition metal elements in the group 4
or the group 5. It is known that these metal elements in their oxidation states are
highly stable and their outermost shell orbitals are filled with electrons and their
internal orbitals are unfilled. That is, the bonding of these metal oxide films has
a strong ionic bonding property compared with the bonding of oxide films made of typical
elements, such as SiO
2, as shown in the table I. This leads to low reactivity to the silane coupling agent
(liquid-repellent agent, water-repellent agent).
[Table I]
OXIDE |
IONIC BONDING PROPERTY |
NON-PATENT LITERATURE 1 |
NON-PATENT LITERATURE 2 |
TiO2 |
0.6 |
0.65 |
Ta2O5 |
- |
0.6 |
SiO2 |
0.5 |
0,5 |
SiC |
0.1 |
|
[0009] In addition, in the structure in which the liquid-repellent layer is formed on the
metal oxide film, a liquid repellency (water repellency, ink repellency) is decreased
by wiping.
[0010] Objects of the present invention include improving reactivity with the liquid-repellent
agent and resistance to ink of the nozzle substrate on the ejection surface side,
thereby preventing decrease in liquid repellency of the nozzle substrate on the ejection
surface side.
Solution to Problem
[0011] In order to solve the above problem(s), the present invention described in claim
1 is an inkjet head including a nozzle substrate that includes: a base part in which
a nozzle that ejects ink is formed; a liquid-repellent-layer base film that is formed
on an ejection surface side of the base part and has a silicon carboxide film; and
a liquid-repellent layer that is formed on the ejection surface side of the liquid-repellent-layer
base film.
[0012] The present invention described in claim 2 is the inkjet head according to claim
1, wherein the liquid-repellent-layer base film includes the silicon carboxide film
having a composition, in a triangular diagram showing a ratio of silicon Si, carbon
C, and oxygen O in the number of atoms, within a range enclosed with: a first coordinate
point at which the ratio of Si:C:O in the number of atoms is 1:1:0; a second coordinate
point at which the ratio of SI:C:O in the number of atoms is 3:2:2; a third coordinate
point at which the ratio of SI:C:O in the number of atoms is 1 :2:2; and a fourth
coordinate point at which the ratio of SI:C:O in the number of atoms is 1:2:0, but
not on a line connecting the first coordinate point and the forth coordinate point.
[0013] The present invention described in claim 3 is the inkjet head according to claim
1 or 2, wherein the liquid-repellent-layer base film is formed on the ejection surface
side of the base part and an inner wall of the nozzle.
[0014] The present invention described in claim 4 is the inkjet head according to any one
of claims 1 to 3, further including a flow channel protective film formed inside a
flow channel of the nozzle.
[0015] The present invention described in claim 5 is the inkjet head according to any one
of claims 1 to 4, wherein the liquid-repellent-layer base film has a film thickness
of 50 nm or less.
[0016] The present invention described in claim 6 is the inkjet head according to any one
of claims 1 to 5, wherein the base part is made of silicon, metal material, or resin
material.
[0017] The present invention described in claim 7 is an inkjet recording device including:
the inkjet head according to any one of claims 1 to 6; and a cleaning unit that wipes
off the ink on the ejection surface side of the liquid-repellent layer.
[0018] The present invention described in claim 8 is a method for producing an inkjet head,
including: a liquid-repellent-layer base film forming step of forming a liquid-repellent-layer
base film that includes a silicon carboxide film on an ejection surface side of a
base part; a liquid-repellent layer forming step of forming a liquid-repellent layer
on the ejection surface side of the liquid-repellent-layer base film, thereby producing
a nozzle substrate; a nozzle forming step of forming, in the base part, a nozzle that
ejects ink; and an inkjet head producing step of producing an inkjet head that includes
the nozzle substrate.
[0019] The present invention described in claim 9 is the method for producing an inkjet
head according to claim 8, wherein the liquid-repellent-layer base film includes the
silicon carboxide film having a composition ratio, in a range in a triangular diagram
showing a ratio of silicon Si, carbon C, and oxygen O in the number of atoms, within
a range enclosed with: a first coordinate point at which the ratio of Si:C:O in the
number of atoms is 1:1:0; a second coordinate point at which the ratio of SI:C:O in
the number of atoms is 3:2:2; a third coordinate point at which the ratio of SI:C:O
in the number of atoms is 1:2:2; and a fourth coordinate point at which the ratio
of SI:C:O in the number of atoms is 1:2:0, but not on a line connecting the first
coordinate point and the forth coordinate point.
[0020] The present invention described in claim 10 is the method for producing an inkjet
head according to claim 9, wherein in the liquid-repellent-layer base film forming
step, the liquid-repellent-layer base film of which outermost surface layer has the
composition ratio in the range is formed by additional oxygenation on a silicon carbide
film or the silicon carboxide film.
[0021] The present invention described in claim 11 is the method for producing an inkjet
head according to claim 10, wherein plasma treatment in an atmosphere containing oxygen
gas is used as the oxygenation.
[0022] The present invention described in claim 12 is the method for producing an inkjet
head according to claim 9, wherein in the liquid-repellent-layer base film forming
step, the liquid-repellent-layer base film of which outermost surface layer has the
composition ratio in the range is formed by additional carbon addition on a silicon
oxide film or the silicon carboxide film.
[0023] The present invention described in claim 13 is the method for producing an inkjet
head according to claim 12, wherein plasma treatment in an atmosphere containing hydrocarbon
gas is used as the carbon addition.
[0024] The present invention described in claim 14 is the method for producing an inkjet
head according any one of claims 8 to 13, wherein in the liquid-repellent-layer base
film forming step, the liquid-repellent-layer base film is formed on the ejection
surface side of the base part and an inner wall of the nozzle.
[0025] The present invention described in claim 15 is the method for producing an inkjet
head according to any one of claims 8 to 14, further including a flow channel protective
film forming step of forming a flow channel protective film inside a flow channel
of the nozzle.
[0026] The present invention described in claim 16 is the method for producing an inkjet
head according to any one of claims 8 to 15, wherein in the nozzle forming step, after
the liquid-repellent-layer base film is formed on the base part and the liquid-repellent
layer is formed thereon, the nozzle is formed by excimer laser processing ablating
the base part, the liquid-repellent-layer base film, and the liquid-repellent layer.
[0027] The present invention described in claim 17 is the method for producing an inkjet
head according to any one of claims 8 to 16, wherein in the liquid-repellent-layer
base film forming step, the liquid-repellent-layer base film having a film thickness
of 50 nm or less is formed.
[0028] The present invention described in claim 18 is the method for producing an inkjet
head according to any one of claims 8 to 17, wherein the base part is made of silicon,
metal material, or resin material.
Advantageous Effects of Invention
[0029] The present invention can improve reactivity with the liquid-repellent agent and
resistance to ink of the nozzle substrate on the ejection surface side, and prevent
decrease in liquid repellency of the nozzle substrate on the ejection surface side.
Brief Description of the Drawings
[0030]
FIG. 1 is a schematic view of configuration of an inkjet recording device according
to an embodiment of the present invention viewed from the front side.
FIG. 2A is a schematic configuration diagram of a head unit located above the conveying
surface of an image forming drum viewed from the upstream side in the conveying direction
of recording media.
FIG. 2B is a bottom view of the head unit viewed from the conveying surface side of
the image forming drum.
FIG. 3A is a perspective view of the image forming drum.
FIG. 3B is an illustration behind the image forming drum viewed from the same front
side as FIG. 1, wherein the image forming drum is seen through.
FIG. 4 is a schematic view of a cross-sectional shape of an inkjet head.
FIG. 5 is a schematic cross-sectional view of a first nozzle substrate of the embodiment.
FIG. 6A shows a preferable range of a composition ratio of a silicon carboxide film
in a triangular diagram showing a ratio of Si:C:O in the number of atoms.
FIG. 6B shows a coordinate point in the triangular diagram showing the ratio of Si:C:O
in the number of atoms.
FIG. 7 is a flowchart showing a first nozzle substrate producing process.
FIG. 8A is a schematic cross-sectional view of a base part before nozzle processing.
FIG. 8B is a schematic cross-sectional view of the base part with a liquid-repellent-layer
base film formed.
FIG. 8C is a schematic cross-sectional view of the base part with a liquid-repellent
layer formed.
FIG. 8D is a schematic cross-sectional view of the base part with a protective sheet
attached.
FIG. 8E is a schematic cross-sectional view of the base part with nozzles formed.
FIG. 8F is a schematic cross-sectional view of a first nozzle substrate with the protective
sheet removed.
FIG. 9 is a schematic cross-sectional view of a second nozzle substrate.
FIG. 10 is a flowchart showing a second nozzle substrate producing process.
FIG. 11A is a schematic cross-sectional view of a base part with nozzles formed.
FIG. 11B is a schematic cross-sectional view of the base part with a liquid-repellent-layer
base film formed.
FIG. 11C is a schematic cross-sectional view of a second nozzle substrate with a liquid-repellent
layer formed.
FIG. 12 is a schematic cross-sectional view of a third nozzle substrate.
FIG. 13 is a schematic cross-sectional view of a fourth nozzle substrate.
FIG. 14 is a flowchart showing a third nozzle substrate producing process.
FIG. 15A is a schematic cross-sectional view of a base part.
FIG. 15B is a schematic cross-sectional view of the base part with a liquid-repellent-layer
base film formed.
FIG. 15C is a schematic cross-sectional view of the base part with nozzle holes formed.
FIG. 15D is a schematic cross-sectional view of the base part with ink channels formed.
FIG. 15E is a schematic cross-sectional view of the base part with a flow channel
protective film formed.
FIG. 15F is a schematic cross-sectional view of a fourth nozzle substrate with a liquid-repellent
layer formed.
FIG. 16 shows coordinate points of first and second samples in the triangular diagram
showing the ratio of Si:C:O in the number of atoms.
FIG. 17 shows coordinate points and contact angles of third to 11th samples in the triangular diagram showing the ratio of Si:C:O in the number of atoms.
Description of the Embodiment
[0031] With reference to the attached figures, an embodiment, first, second and third modifications,
and first and second examples according to the present invention are described in
detail in order. It should be noted that the present invention is not limited to illustrated
examples. In the following description, components having the same function and configuration
are denoted by the same reference numeral and descriptions thereof are omitted.
(Embodiment)
[0032] With reference to FIGS. 1 to 8F, an embodiment according to the present invention
is described. First, configuration of an inkjet recording device 1 of this embodiment
is described with reference to FIGS. 1 to 3B. FIG. 1 is a schematic view of configuration
of the inkjet recording device 1 of this embodiment viewed from the front.
[0033] The inkjet recording device 1 includes a medium supplying unit 10, an image forming
unit 20, a medium receiving unit 30, and a controller (not illustrated). In the inkjet
recording device 1, recording media R stored in the medium supplying unit 10 are conveyed
to the image forming unit 20 in accordance with control operation performed by the
controller, and, after images are formed, discharged to the medium receiving unit
30.
[0034] The medium supplying unit 10 includes a medium supplying tray 11 and a conveying
unit 12. The medium supplying tray 11 is a plate-shaped member provided so as to be
able to store one or more recording media R. The medium supplying tray 11 moves up
and down according to the amount of recording media R, and the top recording medium
R among the recording media R stored thereon is placed at the conveyance start position
of the conveying unit 12. As recording media R, various types of recording media that
can be held to be curved on the outer circumferential surface of an image forming
drum 21, such as printing paper, cellophane, films and fabrics having various thicknesses,
are used.
[0035] The conveying unit 12 includes a plurality of (for example, two) rollers 121, 122,
a ring-shaped belt 123 supported by the rollers 121, 122 on the inner circumferential
surface, and a supplying unit (not illustrated) that delivers the top recording medium
R among the recording media R stored on the medium supplying tray 11 to the belt 123.
According to the circling movement of the belt 123 driven by the rotation of the rollers
121, 122, the conveying unit 12 conveys and sends the recording medium R, which has
been delivered onto the belt 123 by the supplying unit, to the image forming unit
20.
[0036] The image forming unit 20 includes the image forming drum 21, a first delivering
unit 22, a temperature measuring unit 23, head units 24, a heating unit 25, a second
delivering unit 26, and cleaning units 27 (see FIGS. 3A and 3B).
[0037] The image forming drum 21 has a cylindrical outer circumferential surface. The image
forming drum 21 holds the recording medium R on the outer circumferential surface
(conveying surface) and conveys the recording medium R along a conveying path according
to rotating operation of the image forming drum 21. On the inner surface side of the
image forming drum 21, a heater is provided. The heater can heat the conveying surface
so that the recording medium R placed on the conveying surface has a predetermined
temperature.
[0038] The first delivering unit 22 delivers the recording medium R delivered by the conveying
unit 12 to the image forming drum 21. The first delivering unit 22 is provided at
a position between the conveying unit 12 of the medium supplying unit 10 and the image
forming drum 21. The first delivering unit 22 includes a claw part(s) 221 that grips
one end of the recording medium R conveyed by the conveying unit 12 and a cylindrical
delivering drum 222 that leads the recording medium R gripped by the claw part 221.
The recording medium R that the claw part 221 has received from the conveying unit
12 is sent to the delivering drum 222, moves along the outer circumferential surface
of the rotating delivering drum 222, and is led to and delivered to the outer circumferential
surface of the image forming drum 21.
[0039] The temperature measuring unit 23 is provided at a position between the point where
the recording medium R is placed on the conveying surface of the image forming drum
21 and the point where the recording medium R faces an ink ejection surface (jetting
surface) of a head unit 24 that the recording medium R faces first. The temperature
measuring unit 23 measures temperature of a surface of the recording medium R (temperature
of the surface opposite to the surface contacting the conveying surface) being conveyed.
As a temperature sensor of the temperature measuring unit 23, a radiation thermometer
is used, for example. The radiation thermometer measures the surface temperature of
the recording medium R, which does not contact the temperature measuring unit 23 (radiation
thermometer), by measuring intensity distribution of infrared rays. The temperature
measuring unit 23 has a plurality of sensors arranged along a width direction perpendicular
to the direction in which the recording medium R is conveyed in the image forming
unit 20 (conveying direction), the width direction being perpendicular to the surface
of FIG. 1, so as to be able to measure temperature at a plurality of points. Each
measurement data is output to the controller at an appropriate predetermined timing
to be controlled.
[0040] In accordance with the rotation of the image forming drum 21 holding the recording
medium R, each of the head units 24 ejects (discharges) ink droplets at positions
on the recording medium R from a plurality of nozzle opening parts (nozzle holes)
formed on the ink ejection surface that faces the recording medium R, thereby forming
an image. The inkjet recording device 1 in this embodiment has four head units 24
that are arranged a predetermined distance away from the outer circumferential surface
of the image forming drum 21 and at predetermined intervals from one another. The
four head units 24 output ink of four colors: C (Cyan), M (Magenta), Y (Yellow), and
K (Black), respectively. Herein, the C, M, Y, and K inks are ejected in this order
from the upstream side in the conveying direction of the recording medium R. Although
any ink can be used, a normal liquid ink is herein used. The ink fixes to the recording
medium R when ink evaporates and dries by the operation of the heating unit 25. Each
of the head units 24 has a line scan head that is capable of forming an image over
an image forming width on the recording medium R in combination with the rotation
of the image forming drum 21.
[0041] The heating unit 25 heats the surface of the recording medium R being conveyed. For
example, the heating unit 25 heats the recording medium R by generating heat with
an electric heating wire being energized and heating the air, or by emitting infrared
rays. The heating unit 25 is provided at a position close to the outer circumferential
surface of the image forming drum 21 so as to be able to heat the recording medium
R until the image forming drum 21 delivers the recording medium R to the second delivering
unit 26 after the head units 24 eject ink onto the recording medium R conveyed by
the rotation of the image forming drum 21. The operation of the heating unit 25 dries
the ink ejected from the nozzles of the head units 24 and fixes the ink to the recording
medium R.
[0042] The second delivering unit 26 conveys the recording medium R on which the ink has
been ejected and fixed from the image forming drum 21 to the medium receiving unit
30. The second delivering unit 26 includes a plurality of (for example, two) rollers
261, 262, a ring-shaped belt 263 supported by the rollers 261, 262 on the inner side
surface, and a cylindrical delivery roller 264. The second delivering unit 26 leads
the recording medium R on the image forming drum 21 onto the belt 263 with the delivery
roller 264, moves the recording medium R, which is received, together with the belt
263 that circulates in accordance with the rotation of the rollers 261, 262, and conveys
the recording medium R to the medium receiving unit 30.
[0043] The cleaning units 27 perform cleaning operation of the ink ejection surfaces of
the head units 24. The cleaning units 27 are each provided adjacent to the image forming
drum 21 in the width direction. When the head units 24 move in the width direction,
the ink ejection surfaces of the head units 24 are set at the cleaning positions where
the cleaning units 27 perform cleaning.
[0044] The medium receiving unit 30 stores the recording medium R sent from the image forming
unit 20 after image formation until a user takes out the recording medium R. The medium
receiving unit 30 includes a plate-shaped medium receiving tray 31 on which the recording
medium R conveyed by the second delivering unit 26 is stored.
[0045] FIGS. 2A and 2B are illustrations showing configuration of the head unit 24. FIG.
2A is a schematic structural view of the head unit 24 located above the conveying
surface of the image forming drum 21 viewed from the upstream side in the conveying
direction of the recording medium R. FIG. 2B is a bottom view of the head unit 24
viewed from the conveying surface side of the image forming drum 21.
[0046] The head unit 24 has a plurality of inkjet heads 241. Herein, one head unit 24 has
16 inkjet heads 241, although the present invention is not limited to this. The 16
inkjet heads 241 make eight sets of inkjet modules 242, wherein a pair of inkjet heads
241 are included in one inkjet module 242. Herein, the inkjet modules 242 are fixed
to a fixing member 245 so as to be staggered in appropriate relative positions.
[0047] The fixing member 245 is supported and held by a carriage 246. The carriage 246 also
holds a first sub-tank 243 and second sub-tanks 244 to feed ink to the inkjet heads
241. The carriages 246 of the respective four head units 24 are individually movable
in the width direction over the image forming drum 21.
[0048] As shown in FIG. 2B, each of the inkjet heads 241 has a plurality of nozzles 2411.
The inkjet head 241 ejects ink (droplets) from opening parts (nozzle holes) of nozzles
2411 formed on the bottom surface of the inkjet head 241 (nozzle opening surface 241a),
so that the ink droplets land on the recording medium R held on the conveying surface
of the image forming drum 21. Although each of the inkjet heads 241 shown here has
the opening parts of the nozzles 2411 arranged in two rows in the conveying direction
in a two-dimensional array pattern, the present invention is not limited to this.
The opening parts of the nozzles 2411 may be arranged in an appropriate one-dimensional
or two-dimensional array pattern. The arrangement range of these opening parts of
all the 16 inkjet heads 241 covers, in the width direction, the recordable width of
the recording medium R held on the conveying surface. This enables one-pass image
forming with the head units 24 fixed. The nozzle opening surfaces 241 a of the 16
inkjet heads 241 are covered with a liquid-repellent layer 43 (water-repellent layer,
ink-repellent layer) (see FIG. 5).
[0049] FIGS. 3A and 3B are illustrations to explain configuration of the cleaning unit 27.
FIG. 3A is a perspective view of the image forming drum 21. FIG. 3B is a view behind
the image forming drum 21 viewed from the same front side as FIG. 1, wherein the image
forming drum 21 is seen through.
[0050] The cleaning unit 27 wipes off ink and other impurities (collectively called foreign
elements) adhering to the nozzle opening surfaces 241a of the inkjet heads 241, thereby
removing them after ink is ejected for image formation and/or maintenance is performed.
As shown in FIG. 3A, the cleaning unit 27 is arranged next to the image forming drum
21 in the width direction so that the ink ejection surface can be cleaned when the
head unit 24 moves in the width direction.
[0051] As shown in FIG. 3B, the cleaning unit 27 includes a wiping member 271, an elastic
member 272, an unwinding roller 273, and a winding roller 274. Although this configuration
is provided to each of the head units 24, the configuration may be shared by the head
units 24 by making the cleaning unit 27 movable in the conveying direction.
[0052] The wiping member 271 is a long cloth-like sheet member of which length (width) in
the width direction can cover the ink ejection surface (at least all the nozzle opening
surfaces 241a). A desirable member as the wiping member 271 is the one that easily
absorbs moisture of ink, has lower hardness than the hardness of the material of the
ink ejection surface, and hardly damages the liquid-repellent layer. Examples of such
a member include polyester, acrylic, polyamide, and polyurethane that can form a woven
or non-woven fabric. In particular, a member that has a high water-absorbing property
and can easily absorb liquid with a low pressing force at the time of contact is further
preferable. Alternatively, the wiping member 271 may have a blade-like structure.
[0053] The elastic member 272 faces the ink ejection surface with the wiping member 271
in between. The surface (pressing surface) of the elastic member 272 facing the ink
ejection surface has a size that can cover the entire ink ejection surface. The elastic
member 272 is movable approximately perpendicular to the ink ejection surface. As
a material of the elastic member 272, materials that do not damage nozzles when pressed
against the nozzle opening surfaces 241a, such as a sponge (foamed resin) and rubber,
are used. The wiping member 271 contacts the nozzle opening surfaces 241a (ink ejection
surface) in a state of being approximately parallel to the nozzle opening surfaces
241a as a whole by being moved in a direction to approach the nozzle opening surfaces
241a.
[0054] Herein, the relative positions (distance) of the elastic member 272 and the ink ejection
surface when the wiping member 271 contacts the nozzle opening surfaces 241a are fixed.
This makes the pressing force of the wiping member 271 against the ink ejection surface
the same every time within a range of effects of the liquid-repellent layer that peels
off from the surface of the nozzle opening surfaces 241a. The relative positions of
the elastic member 272 and the ink ejection surface are determined so as to have an
appropriate level of the pressing force for cleaning the ink on the ink ejection surface.
Alternatively, the pressing force may be variable. In such a case, the maximum value
of the pressing force is determined according to a relationship between the surface
shape of the nozzle opening surfaces 241a and the wiping member 271, as described
later.
[0055] The wiping member 271 is unwound from the unwinding roller 273 and wound up by the
winding roller 274 in accordance with winding operation performed by the winding roller
274. During this time, the elastic member 272 presses the wiping member 271 against
the ink ejection surface approximately uniformly. This makes the clean (with no ink
adhered) wiping member 271 contact the ink ejection surface and clean ink or the like
adhering to the nozzle opening surfaces 241a (ink ejection surface). If the whole
wiping member 271 is unwound from the unwinding roller 273, the wiping member 271
can be replaced easily.
[0056] Next, a nozzle substrate 40A provided on the ink ejection surface of the head unit
24 of this embodiment is described in detail. FIG. 4 is a schematic view of a cross-sectional
shape of the inkjet head 241.
[0057] The inkjet heads 241, although not particularly limited, is a bend-mode inkjet head
that is formed with a plurality of plates (substrates) layered as shown in FIG. 4.
More specifically, each of the inkjet heads 241 includes the nozzle substrate 40A,
a pressure chamber substrate 50, an oscillating plate 60, a spacer substrate 70, and
a wiring substrate 80 layered in this order from the side where the nozzle opening
surface 241a (ink ejection surface, lower side) are provided to the upper side.
[0058] Ink supplied from the first sub-tank 243 and the second sub-tanks 244 flows into
the pressure chamber 51 of the pressure chamber substrate 50 through an ink flow channel(s)
that communicates with the wiring substrate 80, the spacer substrate 70, and the oscillating
plate 60. The pressure chamber 51 abuts the piezoelectric element part 71 of the spacer
substrate 70 with the oscillating plate 60 in between, and electrically connects to
the nozzle 2411. When a control signal from the controller of the inkjet recording
device 1 is input to the piezoelectric element part 71 through a wire(s) of the wiring
substrate 80, the piezoelectric element part 71 physically oscillates. This causes
ink in the ink flow channel in the wiring substrate 80 and so forth to flow into the
pressure chamber 51, and causes the ink in the pressure chamber 51 to flow into the
nozzle 2411 of the nozzle substrate 40. Then, the ink in the nozzle 2411 is ejected
as ink droplets from the opening part (nozzle hole) on the side where the nozzle opening
surface 241a (ejection surface) is provided, and the ink droplets land on the recording
medium R.
[0059] There may be provided, between the nozzle substrate 40A and the pressure chamber
substrate 50, an intermediate substrate (intermediate layer) having a flow channel
that connects the pressure chamber 51 and the nozzle 2411.
[0060] Next, configuration of the nozzle substrate 40A is described with reference to FIG.
5. FIG. 5 is a schematic cross-sectional view of the nozzle substrate 40A. In FIG.
5 showing the nozzle substrate 40A, the lower part of the drawing is referred to as
the (ink) ejection surface side (external side of the head), and the upper part of
the drawing is referred to as the flow channel side (internal side of the head, pressure
chamber side). The same applies to cross-sectional views of the other nozzle substrates
and cross-sectional views thereof in producing steps.
[0061] As shown in FIG. 5, the nozzle substrate 40A includes a base part 41, a liquid-repellent-layer
base film 42A, and a liquid-repellent layer 43. Examples of a material of the base
part 41 include silicon; metal, such as SUS (Steel Use Stainless), nickel, and metal
containing nickel; and resin, such as polyimide.
[0062] If silicon is used as the base, processes, such as photolithography used in semiconductor
processing, can be performed for nozzle processing. Using such a process enables highly
precise nozzle processing and production of inkjet heads having few variations in
ejection angles and high quality in image depiction.
[0063] The nozzle 2411 is an ink nozzle formed in the base part 41, and includes an ink
flow channel and a nozzle hole on the ejection surface side. The liquid-repellent-layer
base film 42A is provided on the ejection surface side, where the cleaning unit 27
wipes off ink during maintenance of the base part 41, and is the base layer of the
liquid-repellent layer 43 on the flow channel side (base part 41 side). In this embodiment,
the material of the liquid-repellent-layer base film 42A is silicon carboxide (silicon
carboxide film) Si
aC
bO
c (a, b, c: the number of atoms). The liquid-repellent layer 43 is provided on the
ejection surface side of the liquid-repellent-layer base film 42A, and has, for example,
a structure having perfluorocarbon chains and has ink-repellent properties (water
repellency, ink repellency).
[0064] The reason that the silicon carboxide film is selected as the liquid-repellent-layer
base film 42A in this embodiment is that the silicon carboxide film can achieve alkali
resistance, chemical mechanical polishing (CMP) resistance, and fixability of the
liquid-repellent agent (siloxane bonds can be formed). More specifically, the chemical
mechanical polishing resistance is resistance to film reduction of the liquid-repellent-layer
base film due to ink wiping by the cleaning unit 27. In particular, as a maintenance
of an inkjet recording device using alkaline ink, ink on an ejection surface of a
nozzle substrate is wiped off with a cloth or the like of a cleaning unit. This makes
a liquid-repellent layer of a conventional liquid-repellent-layer base film of the
nozzle substrate to peel off easily. This may result in decrease in ink resistance
of the nozzle substrate. Silicon carbide SiC ranks second to DLC (diamond-like carbon)
in hardness and is known as a material that is hardly alkali-etched. Use of a silicon
carboxide film that is produced by introducing carbon into silicon oxide as the liquid-repellent-layer
base film 42A makes it possible to improve its alkali resistance as well as to maintain
reactivity thereof with the silane coupling agent on the nozzle surface.
[0065] Inkjet printing has been aggressively used in the textile field recently. In comparison
with the conventional textile printing methods, the inkjet printing has merits of:
requiring no plates to be generated; being applicable to small lot production; and
having less ink waste. In a case of using polyester or synthetic fiber as recording
media R, an aqueous ink, such as a disperse dye ink or a sublimation dye ink, is used.
However, an additive to the ink, such as a dispersant, is alkaline. With respect to
ink containing pigment molecules, dispersion of the pigment molecules is controlled
with pH of the ink. The conventional liquid-repellent layer formed by silane coupling
has low reliability because, in an alkaline environment, hydrolysis of the liquid-repellent
layer is accelerated or desorption of the liquid-repellent material is accelerated
by the etching of the liquid-repellent-layer base film. Even if textile-printing ink
itself is neutral or slightly alkaline, a fabric coated with an alkaline pretreatment
agent may be used to improve color development. In an inkjet printer for textile printing,
the alkaline pretreatment agent on the fabric surface may affect reliability of liquid
repellency of the surface of the subsequent inkjet head owing to raising treatment
or the like.
[0066] On the other hand, the silicon carboxide film has high chemical stability and can
improve alkali resistance. With reference to FIGS. 6A and 6B, the composition ratio
of the silicon carboxide film Si
aC
bO
c having high alkali resistance is described. FIG. 6A is a diagram showing a preferable
range of the composition ratio of the silicon carboxide film in a triangular diagram
showing the ratio of Si, C, and O in the number of atoms. FIG. 6B is a diagram showing
a coordinate point P0 in the triangular diagram showing the ratio of SI:C:O in the
number of atoms.
[0067] As shown in FIG. 6A, the composition ratio (ratio in the number of atoms) of silicon
Si, carbon C, and oxygen O of the silicon carboxide film is shown in the triangular
diagram that is an equilateral triangle having three vertexes corresponding to Si
only, C only, and O only, respectively. As shown in FIG. 6B, in the triangular diagram
showing composition of Si, C, and O, the vertexes corresponding to only Si, C, and
O are referred to as VSi, VC, and VO, respectively. At an arbitrary coordinate point
P0 in the triangular diagram, the coordinates thereof are represented by a length
α on the side from vertex VO to vertex VSi, a length β on the side from vertex VSi
to vertex VC, and a length γ on the side from vertex VSi to vertex VO. Here, if the
silicon carboxide film at the coordinate point PO has (the number of atoms of) Si:C:O
= a:b:c, α, β, and γ are expressed by the following formulas:
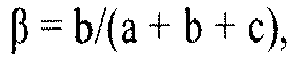
and

wherein α + β + γ = 1.
[0068] With reference to FIG. 6A, the preferable composition ratio of a:b:c of the silicon
carboxide film Si
aC
bO
c as the liquid-repellent-layer base film 42A is described. Firstly, lines L1 to L6
on the triangular diagram showing composition of Si, C, and O are described. In the
triangular diagram, the coordinate point corresponding to silicon dioxide SiO
2 is PSiO
2, the coordinate point corresponding to silicon carbide SiC is PSiC (P1), and the
coordinate point corresponding to silicon dicarbide SiC
2 is PSiC
2 (P4). The line L1 is a line segment connecting the coordinate point PSiO
2 and the coordinate point P1, and composite elements on the line L1 are SiC
1-tO
2t (0 ≤ t ≤ 1). The line L2 is a line segment connecting the coordinate point PSiO
2 and the coordinate point P4, and composite elements on the line L2 are SiC
2(1-s)O
2s (0 ≤ s ≤ 1). The line L3 is a line segment connecting the coordinate point PSiO
2 and the vertex VC. The line L4 is a line segment passing through the vertex VSi and
satisfying b:c = 2:1. The line L5 is a line segment passing through the vertex VSi
and satisfying b:c = 1:1. The line L6 is a line segment passing through vertex VSi
and satisfying b:c = 1:2.
[0069] As described above, in terms of alkali resistance and chemical mechanical polishing
resistance, it is preferable that the proportion of carbon be higher than the proportion
of oxygen (c ≤ b). However, the liquid-repellent-layer base film 42A at least needs
to contain oxygen (c > 0) because hydroxy groups that react with a silane coupling
agent as a liquid-repellent agent need to be present on the surface of the liquid-repellent-layer
base film 42A when the liquid-repellent layer 43 is formed. Therefore, it is preferable
that the ratio of carbon: oxygen (c/b) satisfy 0 < c/b ≤ 1.
[0070] As silicon oxide, silicon monoxide SiO and silicon dioxide SiO
2 are known. Amorphous silicon oxide having an intermediate composition, namely SiO
x where x < 2 stoichiometrically, also exists metastably. On the other hand, SiO
x that satisfies 2 < x does not exist as a film because it is so-called peroxide and
is unstable. Because hydroxy groups, which react with the silane coupling agent, need
to exist on the surface of the liquid-repellent-layer base film 42A when the liquid-repellent
layer 43 is formed, the film at least needs to contain oxygen. Therefore, it is preferable
that the ratio of silicon: oxygen (c/a) satisfy 0 < c/a ≤ 2.
[0071] With respect to the ratio of silicon: carbon, it is preferable that the proportion
of carbon be larger than the line L1, and the proportion of silicon be larger than
the line L2. Because silicon and carbon are both group 14 elements and have the same
valence, substitution in the compound is possible. In terms of alkali resistance and
chemical mechanical polishing resistance, it is preferable that the proportion of
silicon and the proportion of carbon be around the same, or the proportion of carbon
be larger than the proportion of silicon (1 ≤ b/a).
[0072] However, the distance of a covalent bond formed by sp hybridized orbitals of a carbon
atom is shorter than that of a covalent bond formed by sp hybridized orbitals of a
silicon atom because the sp hybridized orbitals of a carbon atom are formed from 2s
and 2p orbitals, whereas these of a silicon atom are formed from 3s and 3p orbitals.
For that reason, the proportion of carbon being too high decreases adhesion between
the base part 41 and the liquid-repellent-layer base film 42A owing to the film stress
of the liquid-repellent-layer base film 42A being larger. With respect to hydroxyl
groups that react with the silane coupling agent when the liquid-repellent layer 43
is formed, because the electronegativity of silicon is smaller than that of carbon,
the hydroxy groups bonded with silicon atoms (≡Si-OH) have more localized charges
than those bonded with carbon atoms (≡C-OH), and hence have higher reactivity with
the silane coupling agent. This is because the electronegativity of silicon is smaller
than that of carbon. Therefore, the proportion of carbon needs to be limited (b/a
≤ 2). In consideration of this, the inventors believe it is preferable that the proportion
of carbon be larger than the line L1 and the proportion of silicon be larger than
the line L2.
[0073] Therefore, as shown in FIG. 6A, the preferable composition ratio of a:b:c of the
silicon carboxide film Si
aC
bO
c as the liquid-repellent-layer base film 42A is, in the triangular diagram, within
a region enclosed with: the coordinate point P1 having the composition ratio of a:b:c
= 1:1:0; the coordinate point P2 having the composition ratio of a:b:c = 3:2:2; the
coordinate point P3 having the composition ratio of a:b:c = 1:2:2; and the coordinate
point P4 having the composition ratio of a:b:c = 1:2:0, but not on a line segment
connecting the coordinate point P1 and the coordinate point P4.
[0074] Next, an example of a method for producing the nozzle substrate 40A in this embodiment
is described with reference to FIGS. 7 to 8F. FIG. 7 is a flowchart showing a first
nozzle substrate producing process. FIG. 8A is a schematic cross-sectional view of
the base part 41 before nozzle processing. FIG. 8B is a schematic cross-sectional
view of the base part 41 with the liquid-repellent-layer base film 42A formed. FIG.
8C is a schematic cross-sectional view of the base part 41 with the liquid-repellent
layer 43 formed. FIG. 8D is a schematic cross-sectional view of the base part 41 with
the protective sheet 45 attached. FIG. 8E is a schematic cross-sectional view of the
base part 41 with nozzles 2411 formed. FIG. 8F is a schematic cross-sectional view
of the nozzle substrate 40A with the protective sheet 45 removed.
[0075] With reference to FIG. 7, the first nozzle substrate producing process for producing
the nozzle substrate 40A is described. First, a manufacturer prepares a base part
41 as a base member as shown in FIG. 8A (Step ST11). Here, the base part 41 is a polyimide
(PI) film. The material of the base part 41 can be resin, such as PET (PolyEthylene
Terephthalate) or PPS (PolyPhenylene Sulfide). More specifically, Kapton film manufactured
by DuPont, Upilex 75S manufactured by Ube Industries, TORELINA manufactured by TORAY,
or the like may be used. Polyimide has high heat resistance, which enables annealing
at a high temperature after the liquid-repellent-layer base film 42A is formed or
after the liquid-repellent layer 43 is formed. PPS has high dimensional stability
and can reduce variation in the length of nozzle rows of the inkjet heads 241.
[0076] As shown in FIG. 8B, the manufacturer forms a silicon carboxide film having a composition
ratio in the preferable range shown in FIG. 6A on the ejection surface side of the
base part 41 prepared in Step ST11, thereby forming the liquid-repellent-layer base
film 42A (Step ST12). Use of the silicon carboxide film can produce the liquid-repellent-layer
base film 42A having high alkali resistance and chemical mechanical polishing resistance.
Because siloxane bonds can be formed, the liquid-repellent-layer base film 42A can
have high fixability with the liquid-repellent agent.
[0077] In Step ST12, the silicon carboxide film can be formed using the following film-forming
methods or the like.
- (1) High-frequency discharge plasma CVD (Chemical Vapor Deposition) or PIG (Penning
Ionization Gauge) plasma CDV using: tetraethyl orthosilicate (TEOS); trimethylsilane
(TMS); silane; hydrocarbon gas, such as methane, ethane, or acetylene; argon; oxygen
gas; or the like
- (2) Sputtering using Si, SiC, or SiO2 as a target in an atmosphere of argon gas, oxygen gas, methane, or the like
- (3) Coating using a solution material containing silica (polysilazane system)
[0078] As pretreatment of film formation of the liquid-repellent-layer base film 42A in
Step ST12, plasma treatment may be performed on the base part 41. The plasma treatment
can be performed with oxygen gas, argon gas, or a mixture of these gases. Performing
the plasma treatment can bring about effects of decontaminating or activating the
surface of the base part 41 and improve adhesion between the liquid-repellent-layer
base film 42A and the base part 41.
[0079] As pretreatment of film formation of the liquid-repellent-layer base film 42A in
Step ST12, reverse sputtering treatment may be performed on the base part 41. As the
reverse sputtering treatment, sputtering is performed on the base part 41 using oxygen
gas, argon gas, or a mixture of these gases. Performing the reverse sputtering treatment
can bring about effects of decontaminating or activating the surface of the base part
41 and improve adhesion between the liquid-repellent-layer base film 42A and the base
part 41.
[0080] In the formation of the silicon carboxide film in Step ST12, the material gas may
be hydrogenated. The hydrogenation may improve the stress, the film hardness, and
the abrasion resistance of the silicon carboxide film.
[0081] In Step ST12, the liquid-repellent-layer base film 42A may be formed by firstly forming
a silicon oxide film or a silicon carboxide film and secondly introducing carbon to
the film surface thereof. As carbon introduction, plasma treatment with hydrocarbon
gas, such as methane or ethane, can be used. As carbon introduction, an ion implantation
method, an ion shower doping method, or the like can be used. When carbon is introduced
to the surface of the liquid-repellent-layer base film, the profile of carbon in the
composition ratio in the depth direction of the liquid-repellent-layer base film shows
a tail from the surface of the base film. However, the composition ratio of the surface
of the liquid-repellent-layer base film (outermost layer) can be controlled by carbonization
to be a desirable composition ratio (within the preferable range shown in FIG. 6A).
[0082] In Step ST12, in order to further improve fixability between the silicon carboxide
film and the liquid-repellent agent, additional treatment, such as oxidation treatment
during or after the film formation, may be performed so as to increase the number
of siloxane bonding sites (-OH groups) on the surface of the silicon carboxide film.
More specifically, examples of the additional treatment include: oxygenating the silicon
carboxide film as the liquid-repellent-layer base film 42A during the film formation
thereof; and, after forming a silicon carbide film or the silicon carboxide film,
oxidizing the surface thereof through oxygen plasma treatment or the like.
[0083] The above-described film formation methods and pretreatment methods of the liquid-repellent-layer
base film 42A may be appropriately combined, and are not limitations of the present
invention.
[0084] It is preferable that the silicon carboxide film in Step ST12 be amorphous or monocrystalline.
If the film is polycrystalline, the film may be selectively etched at crystal grain
boundaries as etching sites and thereby have pinholes formed when immersed in an alkaline
solution, and even the base material below may be etched. On the other hand, if the
film is amorphous or monocrystalline, the film is not selectively etched even when
immersed in the alkaline solution because there are no crystal grain boundaries as
etching sites, so that the liquid-repellent-layer base film (flow channel protective
film on the inner wall of nozzles) has higher alkali resistance.
[0085] As shown in FIG. 8C, the manufacturer forms the liquid-repellent layer 43 on the
ejection surface side (front surface) of the liquid-repellent-layer base film 42A
formed in Step ST12 (Step ST13). The liquid-repellent layer 43 may be formed by application
or deposition of a silane coupling agent as the liquid-repellent agent having perfluoro
carbon chains. As the silane coupling agent, OPTOOL manufactured by Daikin Industries,
WR4 manufactured by Merck, FG-5080 and FG-5010 manufactured by FluoroTechnology, or
the like may be used.
[0086] It is preferable that the formation of the liquid-repellent-layer base film 42A in
Step ST12 and the formation of the liquid-repellent layer 43 in Step ST13 be performed
continuously without exposure thereof to air atmosphere. Avoidance of exposure to
air atmosphere makes it possible to avoid decrease in adhesion between the layers,
change in film quality, and so forth due to contamination of the interfaces of the
layers.
[0087] As pretreatment of formation of the liquid-repellent layer 43 in Step ST13, plasma
treatment may be performed. The plasma treatment can be performed with oxygen gas,
argon gas, or a mixture of these gases. Performing the plasma treatment can bring
about effects of decontaminating or activating the surface of the liquid-repellent-layer
base film 42A, improve reactivity and adhesion of the liquid-repellent-layer base
film 42A to the liquid-repellent layer 43, and improve alkali resistance and chemical
mechanical polishing resistance. A primer layer may be formed before the liquid-repellent
layer 43 is formed in Step ST13. The formation of the primer layer can improve adhesion
between the liquid-repellent layer 43 and the liquid-repellent-layer base film 42A.
[0088] As shown in FIG. 8D, the manufacturer attaches a protective sheet 45 to the ejection
surface side (front surface) of the liquid-repellent layer 43 formed in Step ST13
(Step ST14). The protective sheet 45 has a base sheet 45a and an adhesive layer 45b
on the base sheet 45a. As the base sheet 45a, polyimide, PET, PPS, or the like can
be used. The adhesive layer 45b is attached to the ejection surface side of the liquid-repellent
layer 43.
[0089] As shown in FIG. 8E, the manufacturer performs nozzle processing on the flow channel
side (back surface) of the base part 41, the liquid-repellent-layer base film 42A,
and the liquid-repellent layer 43 to which the protective sheet 45 is attached in
Step ST14, thereby forming the nozzles 2411 (Step ST15). In Step ST15, the manufacturer
irradiates the back surface of the base part 41 with laser and forms the nozzles 2411.
Use of the silicon carboxide film as the liquid-repellent-layer base film 42A makes
it possible to accurately perform the laser processing on the liquid-repellent-layer
base film 42A.
[0090] If the nozzle processing is performed using a KrF excimer laser as a laser light
source in Step ST15, the wavelength of the KrF excimer laser is 248 nm, that is, the
photon energy is 5.0 eV. When the silicon carboxide film is used as the liquid-repellent-layer
base film 42A, the band gap of the silicon carboxide film is narrower than that of
SiO
2 owing to the effect of carbon introduction (the band gap of SiO
2 is 8-9 eV, and that of SiC is about 3 eV.). This improves absorption efficiency of
a KrF excimer laser beam, allows the liquid-repellent-layer base film 42A to be ablated
in nozzle processing, and restrains generation of burrs. Thus, processing accuracy
of the edges of the nozzles 2411 is improved.
[0091] The thickness of the liquid-repellent-layer base film 42A is preferably 100 nm or
less, further preferably 50 nm or less, and still further preferably 20 nm or less.
Laser ablation is performed easier on the liquid-repellent-layer base film 42A having
a thinner film thickness, and less burrs are left.
[0092] With respect to the adhesive layer 45b of the protective sheet 45, the adhesive strength
between the protective sheet 45 and the surface of the liquid-repellent layer 43 should
be between 0.1 and 0.7 N per 10 mm inclusive, and further preferably, between 0.15
and 0.64 N per 10 mm inclusive when the protective sheet 45 and the base part 41 are
pulled apart in 180-degree opposite directions. Use of such an adhesive layer 45b
makes it possible to perform nozzle processing without allowing the protective sheet
45 to peel off from the surface of the liquid-repellent layer 43 through handling
of work in laser processing. This can restrain generation of burrs or the like.
[0093] If the base part 41 is made of metal material, such as SUS, and nozzle processing
is performed using laser, it is preferable that a picosecond pulse laser be used as
the laser light source. Use of a picosecond pulse laser makes it possible to prevent
the metal from generating burrs and dross and form the nozzles 2411 having a good
shape.
[0094] Then, as shown in FIG. 8F, the manufacturer removes the protective sheet 45 from
the base part 41, the liquid-repellent-layer base film 42A, the liquid-repellent layer
43, and the protective sheet 45, in which the nozzles 2411 have been formed in Step
ST15, thereby forming the nozzle substrate 40A (Step ST16), and ends the first nozzle
substrate producing method. With respect to the adhesive layer 45b, the adhesive strength
between the protective sheet 45 and the surface of the liquid-repellent layer 43 should
be between 0.1 and 0.7 N per 10 mm inclusive, or further preferably, between 0.15
and 0.64 N per 10 mm inclusive when the protective sheet 45 and the base part 41 are
pulled apart in 180-degree opposite directions. Use of such an adhesive layer 45b
makes it possible to remove the protective sheet 45 without applying a stress, which
can cause distortion of the dimensions of the base part 41, to the base part 41.
[0095] The manufacturer attaches the nozzle substrate 40A, which has been formed by the
first nozzle substrate producing process, to the pressure chamber substrate 50 (or
the intermediate substrate), and forms a substrate in which the nozzle substrate 40A,
the pressure chamber substrate 50, the oscillating plate 60, the spacer substrate
70, and the wiring substrate 80 are layered. The manufacturer then connects the substrate
with a driving circuit, an ink supply channel(s), and so forth, and forms the inkjet
head 241. The inkjet head 241 is used as a part of the inkjet recording device 1.
[0096] As described above, according to this embodiment, the inkjet head 241 includes the
nozzle substrate 40A that includes: the base part 41 in which the nozzles 2411 that
eject ink are formed; the liquid-repellent-layer base film 42A that is formed on the
ejection surface side of the base part 41 and has the silicon carboxide film; and
the liquid-repellent layer 43 that is formed on the ejection surface side of the liquid-repellent-layer
base film 42A.
[0097] The liquid-repellent-layer base film 42A as the silicon carboxide film makes it possible
to improve reactivity with the liquid-repellent agent for forming the liquid-repellent
layer 43 and resistance to ink, particularly alkaline ink, of the nozzle substrate
40A on the ejection surface side, thereby preventing decrease in liquid repellency
of the nozzle substrate 40A on the ejection surface side.
[0098] Furthermore, the liquid-repellent-layer base film 42A has the silicon carboxide film
having a composition, in the triangular diagram showing the ratio of silicon Si, carbon
C, and oxygen O in the number of atoms, within the range enclosed with: the first
coordinate point at which the ratio of Si:C:O in the number of atoms is 1:1:0; the
second coordinate point at which the ratio of SI:C:O in the number of atoms is 3:2:2;
the third coordinate point at which the ratio of SI:C:O in the number of atoms is
1:2:2; and the fourth coordinate point at which the ratio of Si:C:O in the number
of atoms is 1:2:0, but not on the line connecting the first coordinate point and the
forth coordinate point. The liquid-repellent-layer base film 42A makes it possible,
as shown in first and second examples to be described later, to obtain a high etching
rate, greatly improve alkali resistance, and obtain a large contact angle, thereby
improving liquid repellency.
[0099] Furthermore, the liquid-repellent-layer base film 42A has a film thickness of 50
nm or less. This makes it possible to perform laser ablation easily in forming the
nozzles 2411, and prevent burrs from being left on the base part 41 and so forth.
[0100] Furthermore, the base part 41 is made of silicon, metal material, or resin material.
Use of silicon as the base part 41 makes it possible to use photolithography or the
like for nozzle processing. Such processing makes it possible to form the nozzles
2411 highly accurately and produce the inkjet heads 241 having few variations in ejection
angles and high quality in image depiction. Use of polyimide, which is resin material,
as the base part 41 makes it possible to improve heat resistance and perform annealing
at a high temperature after forming the liquid-repellent-layer base film 42A or the
liquid-repellent layer 43. Use of PPS, which is resin material, as the base part 41,
can improve dimensional stability and reduce variations in nozzle length. Use of SUS,
which is metal material, as the base part 41 makes it possible to easily form the
nozzles 2411 by punch processing, laser processing, or electroforming on the SUS film.
[0101] Furthermore, the inkjet recording device 1 includes the inkjet head 241 that has
the nozzle substrate 40A, and the cleaning unit 27 that wipes off ink on the ejection
surface side of the liquid-repellent layer 43. This can restrain effects of chemical
mechanical polishing due to ink wiping by the cleaning unit 27, and realize the inkjet
recording device 1 that prevents decrease in liquid repellency of the nozzle substrate
40A on the ejection surface side.
[0102] Furthermore, the method for producing an inkjet head includes: a nozzle forming step
of forming, in the base part 41, the nozzles 2411 that eject ink; a liquid-repellent-layer
base film forming step of forming the liquid-repellent-layer base film 42A that has
the silicon carboxide film on the ejection surface side of the base part 41; a liquid-repellent
layer forming step of forming the liquid-repellent layer 43 on the ejection surface
side of the liquid-repellent-layer base film 42A, thereby producing the nozzle substrate
40A; and an inkjet head producing step of producing the inkjet head 241 that includes
the nozzle substrate 40A.
[0103] The liquid-repellent-layer base film 42A made of the silicon carboxide film makes
it possible to improve reactivity with the liquid-repellent agent for forming the
liquid-repellent layer 43 and resistance to ink, particularly alkaline ink, of the
nozzle substrate 40A on the ejection surface side, thereby preventing decrease of
liquid repellency.
[0104] In the liquid-repellent-layer base film forming step, the liquid-repellent-layer
base film 42A of which outermost surface layer has a composition ratio in the range
shown in FIG. 6A is formed by additional oxygenation on a silicon carbide film or
a silicon carboxide film. Plasma treatment in an atmosphere containing oxygen gas
is used as the oxygenation. This makes it possible to easily form the liquid-repellent-layer
base film 42A as the silicon carboxide film having a composition ratio in the range
shown in FIG. 6A. Thus, the number of siloxane bonding sites (-OH groups) on the surface
of the silicon carboxide film can be increased, and fixability between the silicon
carboxide film as the liquid-repellent-layer base film 42A and the liquid-repellent
agent as the liquid-repellent layer 43 can be further improved.
[0105] Furthermore, in the liquid-repellent-layer base film forming step, the liquid-repellent-layer
base film 42A of which outermost surface layer has a composition ratio in the range
shown in FIG. 6A is formed by additional carbon addition on a silicon oxide film or
a silicon carboxide film. Plasma treatment in an atmosphere containing hydrocarbon
gas is used as the carbon addition. This makes it possible to easily form the liquid-repellent-layer
base film 42A as the silicon carboxide film having a composition ratio within the
range shown in FIG. 6A.
[0106] Furthermore, in the nozzle forming step, after the liquid-repellent-layer base film
42A is formed on the base part 41 and the liquid-repellent layer 43 is formed thereon,
the nozzles 2411 are formed by excimer laser processing ablating the base part 41,
the liquid-repellent-layer base film 42A, and the liquid-repellent layer 43. This
makes it possible to perform laser ablation easily in the formation of the nozzles
2411, and prevent burrs from being left on the base part 41 and so forth.
(First modification)
[0107] With reference to FIGS. 9 to 11C, a first modification of the above embodiment is
described. An inkjet recording device in this modification is configured as with the
inkjet recording device I in the above embodiment, except that the nozzle substrate
40A is replaced with a nozzle substrate 40B. The same part as the above embodiment
is not described, and the part different from the above embodiment is mainly described.
[0108] With reference to FIG. 9, configuration of the nozzle substrate 40B is described.
FIG. 9 is a schematic cross-sectional view of the nozzle substrate 40B. As shown in
FIG. 9, the nozzle substrate 40B includes a base part 41, a liquid-repellent-layer
base film 42B, and a liquid-repellent layer 43. The liquid-repellent-layer base film
42B is provided on the ejection surface side of the base part 41 and inside flow channels
of the nozzles 2411. Part of the liquid-repellent-layer base film 42B constitutes
a base layer of the liquid-repellent layer 43 on the base part 41 side. In this modification,
the liquid-repellent-layer base film 42B is a silicon carboxide film having a composition
ratio in the preferable range shown in FIG. 6A.
[0109] Next, with reference to FIGS. 10 to 11C, a method for producing the nozzle substrate
40B is described. FIG. 10 is a flowchart showing a second nozzle substrate producing
process. FIG. 11A is a schematic cross-sectional view of the base part 41 with the
nozzles 2411 formed. FIG. 11B is a schematic cross-sectional view of the base part
41 with the liquid-repellent-layer base film 42B formed. FIG. 11C is a schematic cross-sectional
view of the nozzle substrate 40B with the liquid-repellent layer 43 formed.
[0110] With reference to FIG. 10, the second nozzle substrate producing process for producing
the nozzle substrate 40B is described. First, as shown in FIG. 11, the manufacturer
performs nozzle processing on the flow channel side (back surface) of the base part
41, thereby forming the base part 41 as a base member with the nozzles 2411 formed
(Step ST21). Herein, the base part 41 is made of, for example, metal material (SUS).
The base part 41 with the nozzle 2411 formed can be formed by, for example, forming
on a SUS film depressed portions having a depth larger than the thickness of the SUS
film through punch processing, and smoothing and polishing bulged portions formed
on the back surface of the SUS film. The base part 41 with the nozzles 2411 formed
can be also formed by performing laser processing on the SUS film and forming the
nozzles 2411. The base part 41 made of metal material with the nozzles 2411 formed
can be also formed by electroforming.
[0111] As shown in FIG. 11B. the manufacturer forms a silicon carboxide film having a composition
ratio in the preferable range shown in FIG. 6A on the ejection surface side (front
surface) and the flow channel side (back surface) of the base part 41 formed in Step
ST21, thereby forming the liquid-repellent-layer base film 42B (Step ST22). By using
the silicon carboxide film as the liquid-repellent-layer base film 42B in Step ST22,
the surfaces of the liquid-repellent-layer base film and the flow channel protective
film inside the flow channels can have high alkali resistance and chemical mechanical
polishing resistance. Because siloxane bonds can be formed, the liquid-repellent-layer
base film can have high fixability with the liquid-repellent agent.
[0112] In Step ST22, the silicon carboxide film can be formed, as with Step ST12 in FIG.
7, using the methods (1) to (3) or the like. As pretreatment of film formation of
the liquid-repellent-layer base film 42B in Step ST22, plasma treatment may be performed
on the base part 41 as with Step ST 12 in FIG. 7. Also, as pretreatment of film formation
of the liquid-repellent-layer base film 42B, reverse sputtering treatment may be performed
on the base part 41. As the reverse sputtering treatment, sputtering is performed
on the base using oxygen gas, argon gas, or a mixture of these gases. Performing the
reverse sputtering treatment can bring about effects of decontaminating or activating
the surface of the base part 41 and improve adhesion between the liquid-repellent-layer
base film 42B and the base part 41.
[0113] In the formation of the silicon carboxide film in Step ST22, the material gas may
be hydrogenated. The hydrogenation may improve the stress, the film hardness, and
the abrasion resistance of the liquid-repellent-layer base film 42B. In Step ST22,
the liquid-repellent-layer base film 42A may be formed by firstly forming a silicon
oxide film or a silicon carboxide film and secondly introducing carbon to the film
surface thereof, as with Step ST 12 in FIG. 7. In Step ST22, the liquid-repellent-layer
base film 42B may be formed by: oxygenating a silicon carboxide film during film formation
thereof; or, after forming a silicon carbide film or a silicon carboxide film, oxidizing
the surface thereof as with Step ST 12 in FIG. 7.
[0114] By forming the liquid-repellent-layer base film 42B as a protective film on the inner
walls of the nozzles 2411 and inside the flow channels in Step ST22, the flow channel
protective film can have high alkali resistance and high lyophilic property. The silicon
carboxide film, which has a high covalent bonding property and has hydroxy groups
on the surface, is highly lyophilic (ink-philic, hydrophilic). This allows bubbles
in the flow channels to easily escape when ink is introduced into the inkjet head
241, for example. Also, bubbles hardly adhere to the flow channels during operation
of the inkjet head 241. Thus, ejection defects of the nozzles 2411 or the like are
less likely to occur.
[0115] As shown in FIG. 11C, the manufacturer forms the liquid-repellent layer 43 on the
ejection surface side (front surface) of the base part 41, on which the liquid-repellent-layer
base film 42B has been formed in Step ST22, thereby forming the nozzle substrate 40B
(Step ST23), and ends the second nozzle substrate producing method. In Step ST23,
the liquid-repellent layer 43 is formed as with Step ST13 of FIG. 7. In Step ST23,
it is possible to form the liquid-repellent layer 43 by: firstly forming a liquid-repellent
layer on the ejection surface side (front surface), the inner walls of the nozzles
2411, and the flow channel side (back surface); and secondly removing all or part
of the liquid-repellent layer on the inner walls of the nozzles 2411 and the flow
channel side (back surface). As the removing method, plasma treatment, chemical treatment,
or the like can be used.
[0116] In Step ST23, a liquid-repellent layer may be formed on the ejection surface side
(front surface), the inner walls of the nozzles 2411, and the flow channel side (back
surface). Whereas the front surface of the nozzles 2411 contacts air, the inner walls
of the nozzles 2411 and the inner walls of the flow channels are filled with ink,
and no air is present. Therefore, the ink wettability of the inner walls of the nozzles
2411 and the inner walls of the flow channels may be lower than that of the front
surface of the nozzles 2411.
[0117] As described above, according to this modification, the nozzle substrate 40B of the
inkjet head 241 has the liquid-repellent-layer base film 42B formed on the ejection
surface side of the base part 41 and the inner walls of the nozzles 2411. The liquid-repellent-layer
base film 42B, which has high alkali resistance and high lyophilic property, can protect
the ink flow channels. With the liquid-repellent-layer base film 42B, bubbles in the
flow channels can easily escape when ink is introduced into the inkjet head 241, for
example, and the bubbles hardly adhere to the flow channels during operation of the
inkjet head 241. Thus, ejection defects of the nozzles 2411 or the like are less likely
to occur.
(Second modification)
[0118] With reference to FIG. 12A, a second modification of the above embodiment is described.
An inkjet recording device in this modification is configured as with the inkjet recording
device 1 in the above embodiment, except that the nozzle substrate 40A is replaced
with a nozzle substrate 40Ba. The same part as the above embodiment is not described,
and the part different from the above embodiment is mainly described.
[0119] With reference to FIG. 12, configuration of the nozzle substrate 40Ba is described.
FIG. 12 is a schematic cross-sectional view of the nozzle substrate 40Ba.
[0120] As shown in FIG. 12, the nozzle substrate 40Ba includes a base part 41, a liquid-repellent-layer
base film 42A, a liquid-repellent layer 43, and a flow channel protective film 44B.
The flow channel protective film 44B is provided on the ejection surface side of the
base part 41 and inside the flow channels of the nozzles 2411. Part of the nozzle
substrate 40Ba constitutes a base layer (film) of the liquid-repellent-layer base
film 42A on the base part 41 side. The flow channel protective film 44B is a protective
film having ink resistance.
[0121] Next, a method for producing the nozzle substrate 40Ba is described. The method for
producing the nozzle substrate 40Ba is the same as the producing method of the second
nozzle substrate producing process in FIG. 10. However, after Step ST21 and before
Step ST22 in the second nozzle substrate producing process, the manufacturer forms
the flow channel protective film 44B on the ejection surface side and the flow channel
side of the base part 41 with the nozzles 2411 formed in Step ST21.
[0122] As the flow channel protective film 44B, a metal oxide film containing one or more
kinds of metal elements that are chemically stable in a high oxidation state, such
as tantalum, hafnium, niobium, titanium, and zirconium, may be used. Such a metal
oxide film has high alkali resistance. As the flow channel protective film 44, a metal
silicate film may be used. The metal silicate film is a silicon-containing metal oxide
film containing one or more kinds of metal elements that are chemically stable in
a high oxidation state, such as tantalum, hafnium, niobium, titanium, and zirconium.
Examples of such a metal silicate film include tantalum silicate, hafnium silicate,
niobium silicate, titanium silicate, and zirconium silicate. The metal silicate film
has alkali resistance, and also has a lower ionic bonding property and a higher covalent
bonding property by containing silicon. This increases the number of hydroxy groups
of the flow channel protective film 44B and improves lyophilic property of the surface
of the flow channel protective film 44B. With the improved lyophilic property, bubbles
in the flow channels easily escape when ink is introduced into the inkjet head 241,
for example, and bubbles hardly adhere to the flow channels during operation of the
inkjet head 241. Thus, ejection defects of the nozzles 2411 or the like are less likely
to occur.
[0123] In Step ST22, instead of the liquid-repellent-layer base film 42B, a liquid-repellent-layer
base film 42A is formed on the ejection surface side of the base part 41 with the
flow channel protective film 44B formed. For example, the liquid-repellent-layer base
film 42A is formed by: forming a liquid-repellent-layer base film on the ejection
surface side and the flow channel side of the base part 41 with the flow channel protective
film 44B formed; attaching a protective sheet on the ejection surface side of the
base part 41 with the liquid-repellent-layer base film formed; removing the liquid-repellent-layer
base film on the flow channel side through etching treatment or plasma treatment;
and removing the protective sheet. Then, Step ST23 is performed and the nozzle substrate
40Ba is produced.
(Third modification)
[0124] With reference to FIGS. 13 to 15F, a third modification of the above embodiment is
described. An inkjet recording device in this modification is configured as with the
inkjet recording device 1 in the above embodiment, except that the nozzle substrate
40A is replaced with a nozzle substrate 40C. The same part as the above embodiment
is not described, and the part different from the above embodiment is mainly described.
[0125] With reference to FIG. 13, configuration of the nozzle substrate 40C is described.
FIG. 13 is a schematic cross-sectional view of the nozzle substrate 40C. As shown
in FIG. 13, the nozzle substrate 40C includes a base part 41, a liquid-repellent-layer
base film 42A, a liquid-repellent layer 43, and a flow channel protective film 44.
The flow channel protective film 44 is provided on the ejection surface side of the
base part 41 and inside the flow channels of the nozzles 2411. Part of the flow channel
protective film 44 constitutes a base layer (film) of the liquid-repellent-layer base
film 42A on the base part 41 side. The flow channel protective film 44 is a protective
film having ink resistance.
[0126] Next, with reference to FIGS. 14 to 15F, a method for producing the nozzle substrate
40C is described. FIG. 14 is a flowchart showing a third nozzle substrate producing
process. FIG. 15A is a schematic cross-sectional view of the base part 41C. FIG. 15B
is a schematic cross-sectional view of the base part 41C with the liquid-repellent-layer
base film 42A formed. FIG. 15C is a schematic cross-sectional view of the base part
41C with nozzle holes 2411a formed. FIG. 15D is a schematic cross-sectional view of
the base part 41C with ink channels 2411b formed. FIG. 15E is a schematic cross-sectional
view of the base part 41C with the flow channel protective film 44 formed. FIG. 15F
is a schematic cross-sectional view of the nozzle substrate 40C with the liquid-repellent
layer 43 formed.
[0127] With reference to FIG. 14, a third nozzle substrate producing process for producing
the nozzle substrate 40C is described. In the producing process of the nozzle substrate
40C to be described as an example, the base part 41 is the base part 41C as an SOI
(Silicon On insulator) substrate, and the nozzles 2411 are nozzles 2411C having nozzle
holes and ink channels.
[0128] First, as shown in FIG. 15A, the manufacturer prepares the base part 41C as an SOI
substrate (Step ST31). The base part 41C has a supporting substrate 41a, a BOX (Buried
Oxide) layer 41b, and an SOI layer 41c that are layered in this order. The base part
41C as the SOI substrate can be formed using a substrate bonding method, an SIMOX
(Separation by IMplantation of OXygen) method, an ELTRAN (Epitaxial Layer TRANsfer),
or the like. The film thickness of the SOI layer 41c should be between 10 and 100
µm inclusive, and the film thickness of the BOX layer 41b should be between 50 and
200 nm inclusive. A silicon oxide film or the like may be formed on the surface of
the base part 41C, the surface being positioned on the SOI layer 41c side.
[0129] The thickness of the supporting substrate 41a should be between 50 and 1,000 µm inclusive.
Silicon may be used as the material of the supporting substrate 41a, although this
is not a limitation. Quartz, glass, sapphire, SiC, GaN, YSZ, or the like may be used.
Use of the base part 41C having the supporting substrate 41a made of an ink-resistant
material makes it possible to produce the inkjet head 241 of which nozzles 2411C have
highly ink-resistant inner walls and ink flow channels can be produced.
[0130] As shown in FIG. 15B, the manufacturer forms a silicon carboxide film having a composition
ratio in the preferable range shown in FIG. 6A on the ejection surface side (front
surface) of the SOI layer 41c of the base part 41C, which has been prepared in Step
ST31, thereby forming the liquid-repellent-layer base film 42A (Step ST32). In Step
ST32, the silicon carboxide film can be formed, as with Step ST 12 in FIG. 7, using
the methods (1) to (3) or the like.
[0131] As pretreatment of film formation of the liquid-repellent-layer base film 42B in
Step ST32, plasma treatment may be performed on the base part 41 as with Step ST 12
in FIG. 7. Also, as pretreatment of film formation of the liquid-repellent-layer base
film 42B, reverse sputtering treatment may be performed on the base part 41. In the
formation of the silicon carboxide film in Step ST32, the material gas may be hydrogenated.
In Step ST32, the liquid-repellent-layer base film 42B may be formed by firstly forming
a silicon oxide film or a silicon carboxide film and secondly introducing carbon to
the film surface thereof, as with Step ST12 in FIG. 7. In Step ST32, the liquid-repellent-layer
base film 42B may be formed by: oxygenating a silicon carboxide film during film formation
thereof; or, after forming a silicon carbide film or a silicon carboxide film, oxidizing
the surface thereof as with Step ST 12 in FIG. 7. The above-described film formation
methods and pretreatment methods may be appropriately combined, and are not limitations
of the present invention.
[0132] As shown in FIG. 15C, the manufacturer performs nozzle hole processing on the ejection
surface side (front surface) of the liquid-repellent-layer base film 42A formed in
Step ST32 and the SOI layer 41c of the base part 41C, thereby forming nozzle holes
2411a (Step ST33). In Step ST33, nozzle holes 2411a are formed by, for example, applying
a resist to the surface of the liquid-repellent-layer base film 42A, forming a resist
pattern by exposure, and performing dry etching. As the dry etching, Bosch process
or the like can be used. It is preferable that the nozzle holes 2411a be reversely
tapered as viewed from the SOI layer surface side. Such a reversely tapered shape
becomes a normally tapered shape as viewed from the flow channel side when nozzles
are finished, and stabilizes meniscus vibration when ink droplets are ejected. This
realizes the inkjet head 241 having excellent ejection characteristics.
[0133] As shown in FIG. 15D, the manufacturer performs ink channel processing on the flow
channel side (back surface) of the supporting substrate 41a and the BOX layer 41b
of the base part 41C, in which the nozzle holes 2411a have been formed in Step ST33
(Step ST34). In Step ST34, the ink channels 2411b are formed by, for example, applying
a resist to the back surface of the supporting substrate 41a, forming a resist pattern
by exposure, and performing dry etching. Before the ink channels 2411b are formed,
the supporting substrate 41 a may be polished to make it thin so as to have the supporting
substrate 41a of a desired size.
[0134] As shown in FIG. 15E, the manufacturer forms a flow channel protective film 44 on
the flow channel side (back surface) of the base part 41C with the ink channels 2411b
(nozzles 2411C) formed in Step ST34 (Step ST35). As the flow channel protective film
44, a metal oxide film containing one or more kinds of metal elements that are chemically
stable in a high oxidation state, such as tantalum, hafnium, niobium, titanium, and
zirconium, may be used. Such a metal oxide film has high alkali resistance. As the
flow channel protective film 44, a metal silicate film may be used. The metal silicate
film is a silicon-containing metal oxide film containing one or more kinds of metal
elements that are chemically stable in a high oxidation state, such as tantalum, hafnium,
niobium, titanium, and zirconium. Examples of such a metal silicate film include tantalum
silicate, hafnium silicate, niobium silicate, titanium silicate, and zirconium silicate.
Containing silicon, the metal silicate film, which has alkali resistance, has a low
ionic bonding property and a high covalent bonding property. This increases the number
of hydroxy groups of the flow channel protective film 44B and improves lyophilic property
of the surface of the flow channel protective film 44B. With the improved lyophilic
property, bubbles in the flow channels easily escape when ink is introduced into the
inkjet head 241, for example, and bubbles hardly adhere to the flow channels during
operation of the inkjet head 241. Thus, ejection defects of the nozzles 2411 or the
like are less likely to occur.
[0135] A silicon carboxide film may be used as the flow channel protective film 44. Use
of the silicon carboxide film as the flow channel protective film 44 can produce the
flow channel protective film having high alkali resistance and high lyophilic property.
The silicon carboxide film, which has a high covalent bonding property and has hydroxy
groups on the surface, is highly lyophilic. This allows bubbles in the flow channels
to easily escape when ink is introduced into the inkjet head 241, for example. Also,
bubbles hardly adhere to the flow channels during operation of the inkjet head 241.
Thus, ejection defects of the nozzles or the like are less likely to occur. A silicon
carboxide film may be additionally layered on the whole of or part of the upper layer
of the flow channel protective film 44 made of the metal oxide or the metal silicate
film. The nozzle substrate 40C may not have the flow channel protective film 44.
[0136] As shown in FIG. 15F, the manufacturer forms a liquid-repellent layer on the ejection
surface side (front surface) of the base part 41C, on which the flow channel protective
film 44 has been formed in Step ST35, and the liquid-repellent-layer base film 42A,
thereby forming the nozzle substrate 40C (Step ST36), and ends the third nozzle substrate
producing method. In Step ST36, the liquid-repellent layer 43 is formed as with Step
ST13 of FIG. 7. In Step ST36, it is possible to form the liquid-repellent layer 43
by: firstly forming a liquid-repellent layer on the ejection surface side (front surface),
the inner walls of the nozzles 2411C, and the flow channel side (back surface); and
secondly removing all or part of the liquid-repellent layer on the inner walls of
the nozzles 2411C and the flow channel side (back surface). As the removing method,
plasma treatment, chemical treatment, or the like can be used.
[0137] In Step ST36, a liquid-repellent layer may be formed on the ejection surface side
(front surface), the inner walls of the nozzles 2411C, and the flow channel side (back
surface). Whereas the front surface of the nozzles 2411C contacts air, the inner walls
of the nozzles 2411C and the inner walls of the flow channels are filled with ink,
and no air is present. Therefore, the ink wettability of the inner walls of the nozzles
2411C and the inner walls of the flow channels may be lower than that of the front
surface of the nozzles 2411C.
[0138] As described above, according to this modification, the nozzle substrate 40C of the
inkjet head 241 includes the flow channel protective film 44 formed inside the flow
channels of the nozzles 2411. The flow channel protective film 44 can protect the
ink flow channels. Further, use of the silicon carboxide film as the flow channel
protective film 44 allows bubbles in the flow channel to easily escape when ink is
introduced into the inkjet head 241, for example. Also, bubbles hardly adhere to the
flow channels during operation of the inkjet head 241. Thus, ejection defects of the
nozzles 2411 or the like are less likely to occur.
(First example)
[0139] With reference to FIG. 16, (i) samples of silicon carboxide as a first example used
as the liquid-repellent-layer base films 42A, 42B in the above embodiment and the
first and second modifications and (ii) evaluation of the samples are described. FIG.
16 is a diagram showing coordinate points PSA and PSB of samples SA and SB, respectively,
in the triangular diagram showing the ratio of Si:C:O in the number of atoms.
[0140] Firstly, the sample SA as an example of the silicon carboxide film Si
aC
bO
c was produced. As pretreatment of film formation of the sample SA, O
2 plasma treatment was performed on a base (Si wafer) by RIE-10NR manufactured by Samco.
Conditions of the O
2 plasma treatment were as follows: RF (Radio Frequency) power = 100 W; O
2 flow rate = 60 sccm; and time = 20 sec.
[0141] As the sample SA, a silicon carboxide film was formed on the base (Si wafer) using
TEOS (TEtraethOxySilane) by a film forming apparatus (Plasma CVD apparatus PD-200ST
manufactured by Samco). Conditions of the film formation were as follows: RF power
= 500 W; RF frequency = 13.56 MHz; film formation pressure = 53 Pa; film formation
temperature = 300°C; TEOS gas flow rate = 3 sccm; and Ar flow rate = 100 sccm.
[0142] As an example of the silicon carboxide film Si
aC
bO
c, the sample SB being a silicon oxide film was also produced. As with the sample SA,
film formation pretreatment was performed on the base (Si wafer) of the sample SB.
Then, a silicon carboxide film as the sample SB was formed on the base (Si wafer)
using TEOS by the film forming apparatus (Plasma CVD apparatus PD-200ST manufactured
by Samco). Conditions of the film formation were as follows: RF power = 400 W; RF
frequency = 13.56 MHz; film formation pressure = 53 Pa; film formation temperature
= room temperature; TEOS gas flow rate = 12 sccm; and O
2 flow rate = 400 sccm.
[0143] The composition ratio of Si, C, and O of each of the samples SA and SB was evaluated
by an X-ray photoelectron spectrometer (QuanteraSXM manufactured by ULVAC-PHI). The
composition ratio of the silicon carboxide film Si
aC
bO
c as the sample SA was a:b:c = 32.5:39.7:27.8. The composition ratio of the silicon
carboxide film Si
aC
bO
c (silicon oxide film) as the sample SB was a:b:c = 58:0:42. As shown in FIG. 16, the
coordinate points PSA and PSB corresponding to the samples SA and SB, respectively,
are plotted in the triangular diagram showing the ratio of Si, C, and O in the number
of atoms. The coordinate point PSA of the sample SA is included in the preferable
range of the composition ratio of Si:C:O shown in FIG. 6A. The sample SB is a silicon
oxide film, and the coordinate point PSB is not included in the same preferable range
of composition ratio.
[0144] Next, the wet etching rate of each of the samples SA and SB that were immersed in
an alkaline solution (aqueous potassium hydroxide solution) was evaluated. Followings
are conditions of the evaluation experiment. As the etching conditions, 40% aqueous
potassium hydroxide solution was used at 80°C. The etching rates were as shown in
the table II below.
[Table II]
SAMPLE NAME |
ETCHING RATE [nm/min] |
SAMPLE SA |
0.11 |
SAMPLE SB |
30.5 |
[0145] As shown in the table II, the etching rate of the silicon carboxide film as the sample
SA was about 1/300 of the etching rate of the silicon oxide film as the sample SB.
This shows that the use of a silicon carboxide film like the sample SA as the liquid-repellent-layer
base films 42A, 42B greatly improves alkali resistance of the liquid-repellent-layer
base films 42A, 42B.
(Second example)
[0146] With reference to FIG. 17, a second example of the above embodiment and the first
and second modifications are described. More specifically, (i) samples of silicon
carboxide used as the liquid-repellent-layer base films 42A, 42B and a liquid-repellent
layer, and (ii) evaluations of the samples are described. FIG. 17 is a diagram showing
coordinate points and contact angles of samples S1 to S9, respectively, in the triangular
diagram showing the ratio of Si:C:O in the number of atoms.
[0147] As with the first example, samples S1, S2, S3, S4, S5, S6, S7, S8, and S9 of the
silicon carboxide film Si
aC
bO
c having composition ratios shown in the table III below were produced.
[Table III]
SAMPLE NAME |
COMPOSITION RATIO OF LIQUID-REPELLENT-LAYER BASE FILM |
CONTACT ANGLE [°] |
Si |
C |
O |
STATIC |
RECEDING |
SAMPLE S1 |
1.00 |
0.00 |
0.00 |
SOAKED |
SOAKED |
SAMPLE S2 |
0.33 |
0.00 |
0.67 |
SOAKED |
SOAKED |
SAMPLE S3 |
0.58 |
0.00 |
0.42 |
37.9 |
9.2 |
SAMPLE S4 |
0.39 |
0.61 |
0.00 |
40.9 |
18.8 |
SAMPLE S5 |
0.39 |
0.59 |
0.02 |
63.7 |
44.5 |
SAMPLE S6 |
0.23 |
0.73 |
0.04 |
6.5 |
6.65 |
SAMPLE S7 |
0.38 |
0.56 |
0.06 |
70.6 |
52.4 |
SAMPLE S8 |
0.26 |
0.72 |
0.03 |
11.8 |
0 |
SAMPLE S9 |
0.28 |
0.42 |
0.30 |
77.8 |
63.1 |
[0148] The sample S1 is silicon, the samples S2 and S3 are silicon oxide films, and the
sample S4 is a silicon carbide film. As shown in FIG. 17, coordinate points PS1, PS2,
PS3, PS4, PS5, PS6, PS7, PS7, PS8, and PS9 corresponding to the samples S1, S2, S3,
S4, S5, S6, S7, S8, and S9, respectively, are plotted in the triangular diagram showing
the ratio of SI:C:O in the number of atoms.
[0149] On each of the samples S1 to S9 as the liquid-repellent-layer base films 42A, 42B,
a liquid-repellent layer was formed as the liquid-repellent layer 43 by application.
Conditions of the application were as follows: the samples S1 to S9 were dipped in
0.1% OPTOOL solution for three minutes, and pulled up at a low speed (10 mm/sec);
and ultrasonic cleaning (ultrasonic frequency 950 kHz for 20 minutes) was performed.
[0150] Next, each of the samples S1 to S9 with the liquid-repellent layer formed was immersed
in an aqueous alkaline dummy ink having a pH of 11. Contact angles (static contact
angle, receding contact angle) of the dummy ink were then measured to evaluate change
in contact angles. The aqueous alkaline dummy ink having a pH of 11 was an aqueous
solution in which a buffer solution of sodium carbonate, potassium carbonate, or the
like was mixed with polypropylene glycol alkyl ether, dipolypropylene glycol alkyl
ether, tripolypropylene glycol alkyl ether, or the like to adjust its pH to between
10 and 11 inclusive. The dummy ink to measure the contact angles was: diethylene glycol
alkyl ether; triethylene glycol alkyl ether; tetraethylene glycol alkyl ether; polypropylene
glycol alkyl ether; dipolypropylene glycol alkyl ether; tripolypropylene glycol alkyl
ether; or a mixture of a plurality of solvents selected from these.
[0151] The static contact angle and the receding contact angle of the dummy ink on each
of the samples S1 to S9 with the liquid-repellent layer formed were as shown in the
table III. In FIG. 17, the contact angles of each of the samples S1 to S9 are expressed
by the size (diameter) of a circle centered at each of the coordinate points PS1 to
PS9. Among the samples S1 to S9, the samples S5, S7, and S9 each having a composition
ratio in the preferable range shown in FIG. 6A obtained preferable contact angles
even in a deteriorated state after being immersed in the alkaline ink, and obtained
preferable liquid repellency.
[0152] As the reasons why the resistance to alkaline ink increased, the following two reasons
are considered.
[0153] Firstly, it is considered that the increase in the number of hydroxy groups on the
surface of the liquid-repellent-layer base film increased density of Si-O bonds formed
between the compound forming the liquid-repellent layer and the liquid-repellent-layer
base film, and consequently restrained the liquid-repellent material from desorbing
from the liquid-repellent-layer base film, which is caused by alkaline hydrolysis.
[0154] Secondly, it is considered that the improvement of alkali resistance of the liquid-repellent-layer
base film restrained the liquid-repellent-layer base film from being etched during
immersion in alkaline ink, and consequently restrained the liquid-repellent material
from desorbing from the liquid-repellent-layer base film.
[0155] The descriptions on the above embodiment and modifications are examples of a preferable
inkjet head, an inkjet recording device, and a method for producing an inkjet head
according to the present invention, and are not intended to limit the present invention.
[0156] For example, at least two of the above embodiment and the modifications may be combined
appropriately.
[0157] Although the nozzle substrate described in the above embodiments and modifications
is the nozzle substrate for a bend-mode inkjet head in which a plurality of substrates
are layered, the present invention is not limited to this. For example, the nozzle
substrate in the above embodiment and the modifications may be applied to a nozzle
substrate of a shear-mode inkjet head that presses ink in channels by applying an
electric field in a direction perpendicular to the poling direction of a piezoelectric
element and shearing the piezoelectric element.
[0158] Further, it is possible to appropriately change the detailed configuration and the
detailed operation of the components constituting the inkjet recording device 1 in
the above-described embodiment and modifications without departing from the scope
of the present invention.
Industrial Applicability
[0159] As described above, an inkjet head, an inkjet recording device, and a method for
producing an inkjet head in the present invention can be applied to image recording
using ink.
Reference Signs list
[0160]
- 1
- inkjet recording device
- 10
- medium supplying unit
- 11
- medium supplying tray
- 12
- conveying unit
- 121,122
- roller
- 123
- belt
- 20
- image forming unit
- 21
- image forming drum
- 221
- claw part
- 222
- drum
- 22
- first delivering unit
- 23
- temperature measuring unit
- 24
- head unit
- 241
- inkjet head
- 241a
- nozzle opening surface
- 2411, 2411
- Cnozzle
- 2411
- a nozzle hole
- 2411
- b ink channel
- 242
- inkjet module
- 243
- first sub-tank
- 244
- second sub-tank
- 245
- fixing member
- 246
- carriage
- 25
- heating unit
- 26
- second delivering unit
- 261,262,264
- roller
- 263
- belt
- 27
- cleaning unit
- 271
- wiping member
- 272
- elastic member
- 273
- unwinding roller
- 274
- winding roller
- 30
- medium receiving unit
- 31
- medium receiving tray
- P
- recording medium
- 40A, 40B, 40Ba, 40C
- nozzle substrate
- 41, 41C
- base part
- 41a
- supporting substrate
- 41b
- BOX layer
- 41c
- SOI layer
- 42A, 42B
- liquid-repellent-layer base film
- 43
- liquid-repellent layer
- 44, 44B
- flow channel protective film
- 45
- protective sheet
- 45a
- base sheet
- 45b
- adhesive layer
- 50
- pressure chamber substrate
- 51
- pressure chamber
- 60
- oscillating plate
- 70
- spacer substrate
- 71
- piezoelectric element part
- 80
- wiring substrate
- R
- recording medium