Technical Field
[0001] The present invention relates to a fiber treatment agent for nonwoven fabrics and
a nonwoven fabric using the same.
Background Art
[0002] Thus far, various base agents have been studied for fiber treatment agents for nonwoven
fabrics; among them, alkyl phosphate ester salts and derivatives thereof are greatly
used for hydrophilicity imparting agents from the viewpoints of high safety, performance,
suitability as process oil agents, etc. (Patent Literatures 1 to 8).
[0003] In the blending design of a chemical agent using an alkyl phosphate ester salt or
a derivative thereof, the hydrophilic capacity is often controlled by the proportion
of the alkyl chain length in the blending base agent; to improve hydrophilic capacity
and processing suitability, it is necessary to blend a large amount of a phosphate
ester salt or the like with a short alkyl chain length.
Citation List
Patent Literature
Summary of Invention
Technical Problem
[0005] However, when a phosphate ester salt with a short alkyl chain length is greatly used,
there has been a problem that the chemical agent applied to a nonwoven fabric often
contaminates (is transferred to) an unintentional part, and the performance and quality
of the article as the end product are impaired, such as significantly impairing the
waterproofness of a gather section of a diaper.
[0006] That is, a phosphate ester salt with a short alkyl chain length is a strong hydrophilizing
base agent, and the action of the phosphate ester salt being held on hydrophobic fibers
is temporary; hence, when the hydrophilizing agent is provided with water, most of
the hydrophilizing agent is typically washed away. Since the holding power on hydrophobic
fibers is thus weak, there has been a problem that, when a nonwoven fabric subjected
to attachment treatment with the chemical agent is processed into an article of the
target use, such as when pieces of a nonwoven fabric are superimposed or bent, are
brought into contact with another material or member or a processing machine, are
mutually adhered and fixed by a method such as hot melt adhesion or thermal adhesion,
or are packaged to manufacture an article, the chemical agent attached by treatment
to fibers is transferred to an unintentional part, and the performance and quality
of the article are impaired.
[0007] In conventional technologies such as Patent Literatures 1 to 8, attention is not
focused on the issue of suppressing the transfer of the chemical agent; and there
has been desired a technology in which conventionally required hydrophilicity and
repeated water permeability are satisfied and yet the transfer of, to an unintentional
part, the chemical agent attached by treatment to fibers is suppressed, particularly
a technology in which, even when a strong hydrophilizing base agent is used, another
place in an article is prevented from being contaminated.
[0008] The present invention has been made in view of the circumstances described above,
and an issue of the present invention is to provide a fiber treatment agent for nonwoven
fabrics by which hydrophilicity and repeated water permeability can be imparted to
a nonwoven fabric and yet the transfer to another part in an article using the nonwoven
fabric can be suppressed.
Solution to Problem
[0009] The present inventor conducted extensive studies in order to solve the issue mentioned
above, and has found out that a fiber treatment agent for nonwoven fabrics excellent
in hydrophilicity and the suppression of transfer by which, even when an alkyl phosphate
ester salt or the like that imparts hydrophilicity, particularly a phosphate ester
salt with a short alkyl chain length, is used, transfer from a nonwoven fabric to
another part is less likely to occur is obtained by using a polyhydric alcohol fatty
acid ester or the like with a melting point of more than or equal to 15°C; thus, has
completed the present invention.
[0010] That is, according to the present invention, a fiber treatment agent for nonwoven
fabrics includes: components (A) and (B) below:
- (A) at least one selected from an alkyl phosphate ester salt and a polyoxyalkylene
alkyl ether phosphate ester salt; and
- (B) at least one selected from a polyhydric alcohol fatty acid ester, a polyoxyalkylene
polyhydric alcohol fatty acid ester, and a naturally derived wax each having a melting
point of more than or equal to 15°C.
[0011] According to the present invention, there is provided a nonwoven fabric, wherein
fibers are subjected to attachment treatment with the fiber treatment agent for nonwoven
fabrics.
Advantageous Effects of Invention
[0012] According to the present invention, hydrophilicity and repeated water permeability
can be imparted to a nonwoven fabric, permeability to fibers is provided, and transfer
to another part in an article using the nonwoven fabric can be suppressed.
Description of Embodiments
[0013] Hereinbelow, the present invention is described in detail.
[0014] For a fiber treatment agent for nonwoven fabrics as a hydrophilizing agent used for
hygienic material uses or the like, the control of the speed of water absorption is
essential in view of quickening surface absorption, causing the fiber treatment agent
to arrive at high-absorbent resin or the like, etc., and also repeated water permeability
(durability) is regarded as important; hence, it is inevitably essential to blend
a hydrophilizing base agent with strong hydrophilicity; however, a mechanism by which
another place is prevented from being contaminated even when such a base agent is
used is needed. Thus, in the present invention, an alkyl phosphate ester salt or the
like of component (A), which is a temporary hydrophilizing agent that is, when used
singly, mostly washed away upon being provided with water, is allowed to be slowly
released by using, as component (B), a polyhydric alcohol fatty acid ester or the
like with a melting point of more than or equal to 15°C. When the fiber treatment
agent for nonwoven fabrics is attached by treatment to fibers, component (A) is oriented
on a surface of the fibers such that a hydrophilic portion of the molecular structure
of component (A) is on the front surface and a hydrophobic portion on the back surface;
it is presumed that component (B) as a hydrophobic wax having a melting point of more
than or equal to a certain degree of temperature holds the hydrophobic portion of
component (A) on the surface of the hydrophobic fibers. Hence, it is presumed that
the fiber treatment agent is, when provided with water, gradually locally washed away
by the action of component (B) holding component (A), therefore acts as a hydrophilizing
agent having light durability, and can thereby suppress transfer to another part in
an article using the nonwoven fabric.
[0015] In the present invention, the suppression of transfer is based on the following as
a main standard: for example, the rate of decrease in water pressure resistance with
a blank value as a standard being within 30%, particularly within 20%, and most preferably
10% in a measurement method described in Examples, i.e., water pressure resistance
measurement using a measurement apparatus according to Method A (a low water pressure
method) of the water resistance test (the hydrostatic pressure method). Within this
range, on occasions such as when pieces of a nonwoven fabric are superimposed or bent,
are brought into contact with another material or member or a processing machine,
are mutually adhered and fixed by a method such as hot melt adhesion or thermal adhesion,
or are packaged to manufacture an article, the fiber treatment agent is suitable for
the exhibition of the effect of suppressing an event in which the chemical agent attached
by treatment to fibers is transferred to an unintentional part and the performance
and quality of the article are impaired.
[0016] Component (A) used for the fiber treatment agent for nonwoven fabrics of the present
invention is at least one selected from an alkyl phosphate ester salt and a polyoxyalkylene
alkyl ether phosphate ester salt. Component (A) contains, as a main component, a phosphate
monoester salt and/or a phosphate diester salt represented by Formula (I) below, and
is preferably one containing a phosphate monoester salt in a largest amount. As well
as these, component (A) may contain a polyphosphate or the like. Component (A) is
typically a mixture of these.
[Chem. 1]
[RO(AO)
m]
3-nP(=O)(OM)
n (I)
(In the above formula, R represents an alkyl group, AO represents an oxyalkylene group
(A represents an alkylene part), M represents a cation, m represents the average addition
mole number of a polyoxyalkylene, and n represents an integer of 1 or 2. In the case
where there are a plurality of R's and a plurality of M's in each formula, the R's
and the M's may each be the same or mutually different. AOs may be the same or mutually
different.)
[0017] Component (A) that is a mixture of a phosphate monoester salt, a phosphate diester
salt, and the like can be obtained by, for example, reacting together an alkyl alcohol
or a polyoxyalkylene alkyl ether having the corresponding alkyl group and phosphoric
acid anhydride, and neutralizing the resulting alkyl phosphate ester or the resulting
polyoxyalkylene alkyl ether phosphate with an alkali such as potassium hydroxide.
[0018] The number of carbon atoms of the alkyl group in component (A) is not particularly
limited, but is preferably 4 to 22 and more preferably 6 to 18.
[0019] Examples of the alkyl group include a butyl group, a hexyl group, an octyl group,
a 2-ethylhexyl group (an isooctyl group), a nonyl group, a decyl group, an undecyl
group, a dodecyl group (a lauryl group), a tridecyl group, a tetradecyl group, a pentadecyl
group, a hexadecyl group, a heptadecyl group, an octadecyl group (a stearyl group),
a nonadecyl group, an icosyl group, a henicosyl group, a docosyl group, and the like.
Component (A) may be a mixture of compounds having mutually different alkyl groups;
in this case, the number of carbon atoms of the alkyl group mentioned above is the
average number of carbon atoms. Each of the butyl group to the docosyl group mentioned
above includes various isomers such as an n-type, a sec-type, a tert-type, and a multi-branched
type (an isotype).
[0020] The oxyalkylene group in the polyoxyalkylene alkyl ether phosphate ester salt among
a variety of components (A) preferably has 2 to 4 carbon atoms, more preferably 2
to 3 carbon atoms, and still more preferably 2 carbon atoms. Among them, the oxyalkylene
groups may be the same or mutually different. The oxyalkylene groups preferably include
an oxyethylene group as a whole. Among them, one in which all the oxyalkylene groups
are solely oxyethylene groups and one in which an oxyethylene group and an oxypropylene
group coexist are more preferable, and one in which all the oxyalkylene groups are
solely oxyethylene groups is still more preferable. In the case where a plurality
of kinds having different numbers of carbon atoms coexist among the oxyalkylene groups,
for example in the case where an oxyethylene group and an oxypropylene group coexist,
these may coexist in a random manner, or may coexist in a block manner.
[0021] In the polyoxyalkylene alkyl ether phosphate ester salt among a variety of components
(A), in the case where there are a plurality of groups of RO(AO)
m in Formula (I) above, the average addition mole numbers m of the polyoxyalkylenes
are mutually independently more than or equal to 0.25, more than or equal to 0.5,
more than or equal to 1, or more than or equal to 2, for example. Further, the average
addition mole numbers m of the polyoxyalkylenes are mutually independently less than
or equal to 30, less than or equal to 20, less than or equal to 10, or less than or
equal to 6, for example.
[0022] The cation M in component (A) is not particularly limited, and examples include hydrogen,
an alkali metal, an alkaline earth metal, magnesium, an organic ammonium, and the
like. Examples of the alkali metal include lithium, sodium, potassium, and the like.
Examples of the alkaline earth metal include calcium and the like. Examples of the
organic ammonium include one represented by NR
1R
2R
3R
4. Here, R
1 to R
4 mutually independently represent a hydrogen atom, an alkyl group or an alkylene group
optionally having a hydroxy group, or a polyoxyalkylene group. Among these, either
alkali metal selected from sodium and potassium, ammonium, and an organic ammonium
having an alkyl group or a hydroxyalkyl group having less than or equal to 20 carbon
atoms, preferably less than or equal to 10 carbon atoms, and more preferably less
than or equal to 5 carbon atoms are preferable.
[0023] Component (A) may use component (A1) below.
(A1) an alkyl phosphate ester salt or a polyoxyalkylene alkyl ether phosphate ester
salt in which the number of carbon atoms of an alkyl group is 6 to 10.
[0024] The fiber treatment agent for nonwoven fabrics of the present invention preferably
contains component (A1). Component (A1) can enhance hydrophilicity, particularly the
initial water permeability, and permeability to fibers necessary for the ensuring
of processing suitability etc. In view of these respects etc., the content amount
of component (A1) is preferably more than or equal to 10 mass%, more preferably more
than or equal to 20 mass%, still more preferably more than or equal to 30 mass%, particularly
preferably more than or equal to 35 mass%, and most preferably more than or equal
to 40 mass% relative to component (A).
[0025] Examples of the alkyl phosphate ester salt among a variety of components (A1) include
a hexyl phosphate ester salt, an octyl phosphate ester salt, a 2-ethylhexyl phosphate
ester salt, a decyl phosphate ester salt, an isodecyl phosphate ester salt, and the
like.
[0026] Examples of the polyoxyalkylene alkyl ether phosphate ester salt among a variety
of components (A1) include a polyoxyethylene hexyl ether phosphate ester salt (POE(1)
to POE(30)), a polyoxyethylene octyl ether phosphate ester salt (POE(1) to POE(30)),
a polyoxyethylene 2-ethylhexyl ether phosphate ester salt (POE(1) to POE(30)), a polyoxyethylene
decyl ether phosphate ester salt (POE(1) to POE(30)), a polyoxyethylene isodecyl ether
phosphate ester salt (POE(1) to POE(30)), and the like. The number in the parentheses
indicates the number of polyoxyethylene (POE) units.
[0027] As the component (A), component (A2) below can be used:
(A2) an alkyl phosphate ester salt or a polyoxyalkylene alkyl ether phosphate ester
salt in which the number of carbon atoms of an alkyl group is more than or equal to
11.
[0028] Component (A2) controls hydrophilicity, enhances repeated water permeability, and
can suppress transfer. In particular, component (A) preferably further contains component
(A2) in addition to (A1), and thereby a fiber treatment agent for nonwoven fabrics
excellent in balance between hydrophilicity, repeated water permeability, permeability
to fibers, and the suppression of transfer can be obtained. In view of these respects
etc., the content amount of component (A2) is preferably less than or equal to 90
mass%, more preferably less than or equal to 80 mass%, still more preferably less
than or equal to 70 mass%, particularly preferably less than or equal to 65 mass%,
and most preferably less than or equal to 60 mass% relative to component (A). Further,
the content amount of component (A2) is preferably more than or equal to 10 mass%,
more preferably more than or equal to 15 mass%, and still more preferably more than
or equal to 20 mass%.
[0029] Examples of the alkyl phosphate ester salt among a variety of components (A2) include
a dodecyl phosphate ester salt (a lauryl phosphate ester salt), a tridecyl phosphate
ester salt, an isotridecyl phosphate ester salt, a tetradecyl phosphate ester salt
(a myristyl phosphate ester salt), a hexadecyl phosphate ester salt (a cetyl phosphate
ester salt), an octadecyl phosphate ester salt (a stearyl phosphate ester salt), an
isooctadecyl phosphate ester salt (an isostearyl phosphate ester salt), and the like.
[0030] Examples of the polyoxyalkylene alkyl ether phosphate ester salt among a variety
of components (A2) include a polyoxyethylene dodecyl ether phosphate ester salt (a
lauryl ether phosphate ester salt) (POE(1) to POE(30)), a polyoxyethylene tridecyl
ether phosphate ester salt (POE(1) to POE(30)), a polyoxyethylene isotridecyl ether
phosphate ester salt (POE(1) to POE(30)), a polyoxyethylene tetradecyl ether phosphate
ester salt (a myristyl ether phosphate ester salt) (POE(1) to POE(30)), a polyoxyethylene
hexadecyl ether phosphate ester salt (a cetyl ether phosphate ester salt) (POE(1)
to POE(30)), a polyoxyethylene octadecyl ether phosphate ester salt (a stearyl ether
phosphate ester salt) (POE(1) to POE(30)), a polyoxyethylene isooctadecyl ether phosphate
ester salt (an isostearyl ether phosphate ester salt) (POE(1) to POE(30)), and the
like. The number in the parentheses indicates the number of polyoxyethylene (POE)
units.
[0031] Component (B) used for the fiber treatment agent for nonwoven fabrics of the present
invention is at least one selected from a polyhydric alcohol fatty acid ester, a polyoxyalkylene
polyhydric alcohol fatty acid ester, and a naturally derived wax each having a melting
point of more than or equal to 15°C (hereinafter, also referred to as a wax component).
[0032] Component (B) suppresses the transfer of component (A). In view of suppressing the
transfer of component (A), the melting point of component (B) is more than or equal
to 15°C, preferably more than or equal to 20°C, more preferably more than or equal
to 25°C, and still more preferably more than or equal to 30°C. Further, in view of
suppressing the transfer of component (A) and enhancing particularly hydrophilicity,
further repeated water permeability, and permeability to fibers necessary for the
ensuring of processing suitability etc., the melting point of component (B) is preferably
less than or equal to 90°C, more preferably less than or equal to 80°C, still more
preferably less than or equal to 70°C, and particularly preferably less than or equal
to 60°C. In the case where component (B1) with a melting point of more than or equal
to 60°C, particularly more than or equal to 80°C, is used, in view of enhancing permeability,
component (B1) is preferably used in combination with component (B2) with a melting
point of less than 60°C, and the mass ratio (B1/B2)
[0033] of component (B1) to component (B2) is preferably less than 1.
[0034] Each of the polyhydric alcohol fatty acid ester and the polyoxyalkylene polyhydric
alcohol fatty acid ester among a variety of components (B) may be a monoester, a diester,
a triester, or the like. The polyhydric alcohol of the polyhydric alcohol fatty acid
ester and the polyoxyalkylene polyhydric alcohol fatty acid ester is a dihydric or
higher alcohol, and is preferably a trihydric or higher alcohol. Further, the polyhydric
alcohol is preferably a decahydric or lower alcohol, and more preferably an octahydric
or lower alcohol. Specific examples include glycerin, polyglycerin such as diglycerin,
sugar alcohol-based compounds such as trimethylolethane, trimethylolpropane, trimethylolbutane,
ditrimethylolpropane, pentaerythritol, dipentaerythritol, sorbitan, erythritol, D-threitol,
L-arabinitol, ribitol, xylitol, sorbitol, mannitol, galactitol, and rhamnitol, monosaccharides
such as arabinose, ribose, xylose, glucose, mannose, galactose, fructose, sorbose,
rhamnose, fucose, and ribodesose, disaccharides such as trehalose, sucrose, maltose,
cellobiose, gentiobiose, lactose, and melibiose, trisaccharides such as raffinose,
gentianose, and melezitose, and the like. The fatty acid of the polyhydric alcohol
fatty acid ester and the polyoxyalkylene polyhydric alcohol fatty acid ester is not
particularly limited; however, in view of the melting point etc., the number of carbon
atoms of the fatty acid is preferably more than or equal to 8, and more preferably
more than or equal to 12. Further, the number of carbon atoms is preferably less than
or equal to 30, more preferably less than or equal to 22, and still more preferably
less than or equal to 18. The fatty acid may be a saturated fatty acid, or may be
an unsaturated fatty acid; among these, in view of enhancing the melting point etc.,
a saturated fatty acid is preferable, and a straight-chain saturated fatty acid is
more preferable. Examples of the saturated fatty acid include caprylic acid, pelargonic
acid, capric acid, lauric acid, myristic acid, palmitic acid, stearic acid, arachidic
acid, behenic acid, and the like.
[0035] The polyhydric alcohol fatty acid ester may be an oil or a fat obtained from nature,
or a hardened oil or fat in which hydrogen is added.
[0036] The average addition mole number of the polyoxyalkylene in the polyoxyalkylene polyhydric
alcohol fatty acid ester among a variety of components (B) is, for example, less than
or equal to 100 or less than or equal to 80 per molar equivalent of the hydroxyl group
of the polyhydric alcohol ester. The oxyalkylene group preferably has 2 to 4 carbon
atoms, and more preferably has 2 carbon atoms (an oxyethylene group) or 3 carbon atoms
(an oxypropylene group). In the case where a plurality of kinds having different numbers
of carbon atoms coexist among the oxyalkylene groups, for example in the case where
an oxyethylene group and an oxypropylene group coexist, these may coexist in a random
manner, or may coexist in a block manner.
[0037] Examples of the naturally derived wax among a variety of components (B) include plant-based
waxes, animal-based waxes, mineral-based waxes, and the like. Examples of the plant-based
wax include carnauba wax, candelilla wax, rice bran wax, sumac wax, jojoba oil, and
the like. Examples of the animal-based wax include lanoline, bees wax, spermaceti
wax, and the like. As the mineral-based wax, paraffin wax, microcrystalline wax, petrolatam,
ozokerite, ceresin, and the like are given. Among these, plant-based waxes are preferable.
Any of these may be used singly, or two or more of these may be used in combination.
[0038] In the fiber treatment agent for nonwoven fabrics of the present invention, the mass
ratio (B)/(A) of component (B) to component (A) is preferably less than 1 in view
of enhancing hydrophilicity. Further, in view of suppressing transfer, the mass ratio
(B)/(A) is preferably more than or equal to 0.1, more preferably more than or equal
to 0.2, and still more preferably more than or equal to 0.3.
[0039] The fiber treatment agent for nonwoven fabrics of the present invention has the effect
of the present invention, that is, hydrophilicity, repeated water permeability, and
permeability to fibers; in view of enabling the suppression of transfer, the total
amount of components (A) and (B) is preferably more than or equal to 50 mass%, more
preferably 60 mass%, still more preferably more than or equal to 70 mass%, particularly
preferably more than or equal to 80 mass%, and most preferably more than or equal
to 85 mass% relative to the solid content of the fiber treatment agent for nonwoven
fabrics. Here, the solid content is the proportion excluding water and volatile components
such as solvent that disappear when the fiber treatment agent is attached by treatment
to fibers.
[0040] In the fiber treatment agent for nonwoven fabrics of the present invention, penetrant
(C) may be blended for the purpose of improving the capacity of permeation to fibers,
in addition to components (A) and (B). As penetrant (C), nonionic surfactants such
as a polyoxyalkylene alkyl ether, anionic surfactants such as a polyoxyalkylene alkyl
ether sulfate and a sulfosuccinic acid ester salt, polyether-modified silicones, and
the like are given. Among these, a polyoxyalkylene alkyl ether, particularly a polyoxyalkylene
branched alkyl ether, is preferably used because permeation capacity can be improved
inexpensively. If the blending amount of the penetrant is increased, bad influence
is given to transfer and durable hydrophilicity; thus, the blending amount of the
penetrant is preferably less than or equal to 20 mass%, more preferably less than
or equal to 15 mass%, and still more preferably less than or equal to 10 mass% relative
to the solid content of the fiber treatment agent for nonwoven fabrics. Any of these
may be used singly, or two or more of these may be used in combination.
[0041] The alkyl portion in the polyoxyalkylene alkyl ether may be a straight-chain alkyl
group or a branched-chain alkyl group, and is preferably an alkyl group having 8 to
14 carbon atoms, and more preferably an alkyl group having 10 to 12 carbon atoms.
Examples of the branched-chain alkyl group include an isooctyl group, an isodecyl
group, an isododecyl group, an isohexadecyl (isocetyl) group, an isooctadecyl (isostearyl)
group, an octyldodecyl group, a decyltetradecyl group, and the like.
[0042] The average addition mole number of the polyoxyalkylene in each of the polyoxyalkylene
straight-chain alkyl ether and the polyoxyalkylene branched alkyl ether is preferably
2 to 12, and more preferably 4 to 8. The oxyalkylene group preferably has 2 to 4 carbon
atoms, and more preferably has 2 carbon atoms (an oxyethylene group) or 3 carbon atoms
(an oxypropylene group). In the case where a plurality of kinds having different numbers
of carbon atoms coexist among the oxyalkylene groups, for example in the case where
an oxyethylene group and an oxypropylene group coexist, these may coexist in a random
manner, or may coexist in a block manner.
[0043] The fiber treatment agent for nonwoven fabrics of the present invention may contain
water or a solvent, and preferably contains water, as necessary. The water used for
the present invention may be any of pure water, distilled water, purified water, soft
water, ion-exchanged water, tap water, and the like. The proportion of the solid content
at the time of manufacturing the fiber treatment agent for nonwoven fabrics of the
present invention is preferably 5 to 90 mass%, and more preferably 10 to 80 mass%.
[0044] The fiber treatment agent for nonwoven fabrics of the present invention may contain
other components as well as the components mentioned above to the extent that the
effect of the present invention is not impaired. Examples of the other component include
a surfactant, an antibacterial agent, an antioxidant, an antiseptic agent, a matting
agent, a pigment, an antirust agent, an aromatic, an antifoaming agent, a perfume,
a pH adjuster, a viscosity adjuster, etc. Examples of the surfactant include nonionic
surfactants such as a polyoxyalkylene alkyl ether, a polyoxyalkylene alkenyl ether,
a polyoxyalkylene fatty acid ester, and a fatty acid alkanolamide, anionic surfactants
such as an alpha-olefin sulfonate, an alkylbenzene sulfonate, an alkyl sulfate, a
polyoxyalkylene alkyl ether sulfate, and a sulfosuccinic acid ester salt, amphoteric
surfactants such as an alkyl betaine, an alkyl sulfobetaine, and an alkylamino fatty
acid salt, cationic surfactants such as an alkyl quaternary ammonium salt, and the
like.
[0045] In the fiber treatment agent for nonwoven fabrics of the present invention, the dynamic
surface tension at the time of a bubble lifetime according to the maximum bubble pressure
method of 100 milliseconds in an aqueous solution prepared such that the solid content
is 2 mass% is preferably less than or equal to 55 mN/m, and more preferably less than
or equal to 50 mN/m. When the dynamic surface tension is in this range, the fiber
treatment agent has good permeability to hydrophobic fibers, does not inhibit process
transitability, and is suitable for the exhibition of the effect of suppressing transfer.
[0046] The method for manufacturing the fiber treatment agent for nonwoven fabrics of the
present invention is not particularly limited; for example, the fiber treatment agent
for nonwoven fabrics of the present invention can be obtained by blending together
components (A) and (B) and water, blending component (C) and other components as necessary,
and uniformly mixing the components at normal temperature or, as necessary, by heating
(for example, 40 to 100°C). The blending order and the blending method of the components
are not particularly limited. The fiber treatment agent for nonwoven fabrics of the
present invention can, for example, be provided to fibers as an emulsion dispersion
liquid, which may be obtained by diluting the fiber treatment agent for nonwoven fabrics
of the present invention with water, as necessary.
[0047] Next, a nonwoven fabric using the fiber treatment agent for nonwoven fabrics of the
present invention is described.
[0048] Examples of the source material fibers of the nonwoven fabric include polyolefin
fibers such as polyethylene and polypropylene, synthetic fibers such as polyester
fibers and polyamide fibers, regenerated fibers such as rayon and cuprammonium rayon,
natural fibers such as cotton, and the like, and mixing fibers, composite fibers,
and the like using two or more of these.
[0049] As the cross-sectional form of the fiber, a circular cross section, a deformed cross
section, and the like are given. Examples of the deformed cross section include a
star shape, an ellipse, a triangle, a quadrangle, a pentagon, a multifoliate shape,
a dumbbell shape, a T-shaped form, a horseshoe shape, and the like.
[0050] Examples of the cross-sectional form of the composite fiber include a sheath-core
form, a parallel form, an eccentric sheath-core form, a multilayer form, a radial
form, a sea-island form, and the like. Examples of the composite fiber include polyolefin
resin/polyolefin resin such as high-density polyethylene/polypropylene, straight-chain-form
low-density polyethylene/polypropylene, low-density polyethylene/polypropylene, a
binary copolymer or a ternary copolymer of propylene and other α-olefins/polypropylene,
straight-chain-form low-density polyethylene/high-density polyethylene, and low-density
polyethylene/high-density polyethylene, polyolefin resin/polyester resin such as polypropylene/polyethylene
terephthalate, high-density polyethylene/polyethylene terephthalate, straight-chain-form
low-density polyethylene/polyethylene terephthalate, and low-density polyethylene/polyethylene
terephthalate, polyester resin/polyester resin such as copolymerized polyester/polyethylene
terephthalate, combinations of polyamide resin/polyester resin and polyolefin resin/polyamide
resin, and the like.
[0051] The method for spinning source material fibers may be a known spinning method, and
examples include the melt spinning method, the wet spinning method, the dry spinning,
and the like. The spun fibers may be subjected to processing such as stretching or
crimping.
[0052] In the manufacturing process of a nonwoven fabric, an accumulation layer (web) of
fibers is formed, and next fibers are bonded together.
[0053] Examples of the method for forming an accumulation layer of fibers include the dry
method, the wet method, the spun bonding method, and the like. The dry method is a
method in which short fibers (for example, 15 to 100 mm) are arranged in a fixed direction
or randomly with a carding machine or an air flow called an air lay and an accumulation
layer of fibers is formed. The wet method is a method in which short fibers are dispersed
in water and are fashioned into a thin layer with a paper machine to form an accumulation
layer of fibers. The spun bonding method is a method in which a melted source material
resin is melted out and spun from the tip of a nozzle of a spinning machine and an
accumulation layer of fibers is formed with continuous long fibers. As the method
for manufacturing a nonwoven fabric as it is from a fiber-making (spinning) process,
the melt blowing method, the flash spinning method, and the like are given as well
as the above.
[0054] Examples of the method for bonding fibers together include the thermal bonding method,
the needle punching method, the hydroentanglement method, the chemical bonding method,
and the like. The thermal bonding method is a method in which an accumulation layer
of fibers in which low-melting-point thermal fusion bonding fibers are mixed is passed
between hot rolls to be thermocompression-bonded, or hot air is applied to adhere
fibers together. The needle punching method is a method in which an accumulation layer
of fibers is repeatedly stuck with needles vertically moving at high speed and protrusions
cut in the needles are used to entangle fibers together. The hydroentanglement method
is also called spun lacing, water punching, and water jetting, and is a method in
which high-pressure water flows are jetted to an accumulation layer of fibers to entangle
fibers together. The chemical bonding method is a method in which an emulsion-based
adhesive resin is attached to an accumulation layer of fibers by a method such as
impregnation or spraying, and heating and drying are performed to adhere intersection
points of fibers together.
[0055] The method for performing the attachment treatment of the fiber treatment agent for
nonwoven fabrics of the present invention to fibers is not particularly limited. The
fiber treatment agent for nonwoven fabrics of the present invention may be supplied
as a spinning oil agent or a process oil agent designed for the streamlining, facilitation,
or the like of the manufacturing process, or a finish oil agent designed for an effect
for the end use. In the case where the fiber treatment agent is used as a process
oil agent, also performances such as antistatic capacity, smoothness, durability,
thermal stability, and safety, which suppress the occurrence of static electricity
due to friction caused by a carding machine or the like, the tearing of fibers, the
occurrence of pilling, etc., can be imparted. Examples of the process of attaching
the fiber treatment agent for nonwoven fabrics of the present invention to fibers
include processes such as spinning, stretching, and crimping. As the attachment method,
for example, a method in which the fiber treatment agent for nonwoven fabrics of the
present invention is supplied to fibers by a means such as oil supply with rollers,
immersion, spraying, or foam coating and drying is performed, etc. are given as means
for obtaining the target attachment amount in a uniform way with good efficiency in
accordance with the manufacturing process and the characteristics of fibers. Alternatively,
attachment treatment may be performed by a method in which the fiber treatment agent
for nonwoven fabrics of the present invention is supplied to a nonwoven fabric in
which fibers are bonded together by, for example, a means such as oil supply with
rollers, immersion, spraying, or foam coating and drying is performed.
[0056] The attachment amount of the fiber treatment agent for nonwoven fabrics of the present
invention to fibers is not particularly limited; however, in view of obtaining the
effect of the present invention, performance as a process oil agent, etc., the attachment
amount is preferably 0.05 to 2 mass% and more preferably 0.1 to 1.5 mass% as the solid
content, with the mass of fibers as a standard.
[0057] The nonwoven fabric of the present invention is one in which fibers are subjected
to attachment treatment with the fiber treatment agent for nonwoven fabrics of the
present invention. The nonwoven fabric has hydrophilicity, repeated water permeability,
and permeability to fibers, and can suppress transfer; thus, can be used for various
uses in which such performance is required. Examples of fields in which the nonwoven
fabric of the present invention can be used include hygienic material uses, medical
uses, clothing uses, daily goods, agriculture and public works material uses, matrices
for tapes, filter uses, wrapping material uses, and the like. In particular, the nonwoven
fabric is suitable for fields in which not only the impartment of hydrophilicity etc.
but also the suppression of transfer of the fiber treatment agent for nonwoven fabrics
attached to fibers during processing on an article using the nonwoven fabric, such
as during processing in which a method such as hot melt adhesion or thermal adhesion
is used to perform mutual adhesion and fixing to manufacture a hygienic article, can
be particularly required. Examples of such fields include hygienic material uses such
as paper diapers, sanitary items, masks, bandages, adhesive bandages, disinfecting
cloths, and surgical tapes. In particular, the nonwoven fabric is suitable for a surface
material, for example the top sheet, an intermediate sheet placed between the top
sheet and an absorbent element, or the like, of an absorbent article such as a paper
diaper such as a baby disposable diaper or a disposable diaper for nursing care, or
a sanitary item such as a napkin.
Examples
[0058] The present invention will now be described in more detail by using Examples; however,
the present invention is not limited to these Examples.
1. Production of fiber treatment agent for nonwoven fabrics and nonwoven fabric for
evaluation
[0059] The components of the blending (parts by mass) of Table 1 were stirred at 80°C for
60 minutes, and a fiber treatment agent for nonwoven fabrics of each of Examples and
Comparative Examples was produced.
[0060] In the following evaluation, a nonwoven fabric for evaluation made of polypropylene
was produced by the following method.
[0061] Each of the fiber treatment agents for nonwoven fabrics of Examples and Comparative
Examples was diluted in water at 40°C such that the solid content was 1 mass%, and
a dilute liquid was obtained. A polypropylene spun-bonded nonwoven fabric with a mass
per unit area of 20 g/m
2 was immersed in the dilute liquid to be supplied with oil, compression was performed
such that the target attachment amount of oil of the nonwoven fabric was 0.6 mass%,
and then drying was performed with a dryer at 80°C for 30 minutes; thus, a nonwoven
fabric was obtained.
[0062] The following were used as alkyl phosphate ester salts or derivatives (A), wax components
(B), and penetrants (C) shown in Table 1. The blending amount described in Table 1
shows the effective content.
Alkyl phosphate ester salt or derivative (A)
1-1: Potassium hexyl phosphate
1-2: Potassium 2-ethylhexyl phosphate
1-3: Ammonium decyl phosphate
1-4: Potassium lauryl phosphate
1-5: Potassium POE(2) lauryl ether phosphate
1-6: Potassium POE(2) stearyl ether phosphate
Wax component (B)
2-1: Sorbitan monostearate (melting point: 53°C)
2-2: Diglycerin laurate (melting point: 34°C)
2-3: Sucrose stearic acid ester (melting point: 48°C)
2-4: Polysorbate 65 (melting point: 33°C)
2-5: POE(50) stearyl ether (melting point: 55°C)
2-6: Carnauba wax (melting point: 85°C)
2-7: Sorbitan monooleate (a liquid form)
2-8: Polyethylene oxide wax (melting point: 105°C)
[0063] The melting point of wax component (B) was measured with a minute amount melting
point measurement apparatus (MP-3S, manufactured by Yanaco Kikikaihatsu Kenkyusho
K.K.).
Penetrant (C)
3-1: POA(4) branched decyl ether
3-2: POE(7) lauryl ether
3-3: Sodium POE(3) lauryl ether sulfate
3-4: Sodium dioctyl sulfosuccinate
3-5: Polyether-modified silicone
2. Evaluation
[0064] The following evaluation was performed using the fiber treatment agents for nonwoven
fabrics and the nonwoven fabrics for evaluation produced in the above.
[0065] In the following description, the chemical agent refers to the fiber treatment agent
for nonwoven fabrics of each of Examples and Comparative Examples, and the attachment
amount refers to the attachment amount of the solid content (the total effective content)
except water of the chemical agent.
[Hydrophilicity (strike-through test)]
[0066] Four sheets of the nonwoven fabric (mass per unit area: 20 g/m
2) produced in the above were sandwiched between two cylindrical measurement instruments
(inner diameter: 40ϕ), and 50 cc of a physiological saline solution was poured into
the upper cylinder out of the measurement instruments. The time until the poured physiological
saline solution caused the volume of the nonwoven fabric for evaluation to be 30 cc
was measured, and the initial water permeation capacity was evaluated.
[0067] As the evaluation, the case where the penetration time of the physiological saline
solution was within 10 seconds was classified as ⊙+, the case where the penetration
time was more than 10 seconds and within 30 seconds as ⊙, the case of more than 30
seconds and within 1 minute as o, the case of more than 1 minute and within 2 minutes
as Δ, and the case of more than 2 minutes as ×.
[Repeated water permeability (waterdrop method)]
[0068] The operation of a strike-through test was performed consecutively 5 times, then
the four sheets of the chemical agent-treated nonwoven fabric immediately after the
test were sandwiched by sheets of filter paper, and water was removed by using rollers.
The sheet of filter paper on the front surface side was removed, and waterdrops of
a physiological saline solution was dropped onto 10 places of the portion of the strike-through
test by using a syringe.
[0069] The evaluation was performed by measuring places where the waterdrop soaked within
3 seconds; the case of more than or equal to 8 places was classified as ⊙, the case
of 7 or 6 places as o, the case of 5 to 2 places as Δ, and the case of less than or
equal to 1 place as ×.
[Permeability (cotton sedimentation method)]
[0070] A 2-mass% aqueous solution (on an effective content basis) of a chemical agent to
be evaluated was prepared, a nonwoven fabric for evaluation made of chemical-agent-untreated
polypropylene cut out in a 10-cm square (mass per unit area: 20 g/m
2) was gently dropped from above the aqueous solution, and the time until the aqueous
solution permeated through the entire nonwoven fabric was measured.
[0071] As the evaluation, the case where the time until the bath liquid permeated through
the entire nonwoven fabric was within 5 seconds was classified as ⊙, the case of more
than 5 seconds and within 10 seconds as o, the case of more than 10 seconds and within
15 seconds as Δ, and the case of more than 15 seconds as ×.
[Dynamic surface tension]
[0072] A 2-mass% aqueous solution (on an effective content basis) of a chemical agent to
be evaluated was prepared, the measurement of the maximum bubble pressure method was
performed by using a commercially available dynamic surface tension measurement apparatus
(BP-D5, manufactured by Kyowa Interface Science Co., Ltd), and the surface tension
(mN/m) at the time of a bubble lifetime of 100 milliseconds (msec) was recorded as
a measurement value.
[Suppression of transfer (rate of decrease in water pressure resistance)]
[0073] A nonwoven fabric (mass per unit area: 20 g/m
2) produced in the above manner and a chemical-agent-untreated nonwoven fabric in a
15-cm square likewise were superimposed together, a load of 0.49 kPa was applied,
and still standing was performed for 30 days. After the period elapsed, the chemical-agent-untreated
nonwoven fabric was taken out to be used as a test piece, and water pressure resistance
measurement was performed by using a measurement apparatus according to Method A (a
low water pressure method) of the water resistance test (the hydrostatic pressure
method) described in JIS L 1092:2009, "Testing methods for water resistance of textiles".
The test piece was placed in the measurement apparatus such that the contact surface
with the chemical-agent-treated nonwoven fabric was located on the side of the water-contact
surface. As a control test, the water pressure resistance measurement of a chemical-agent-untreated
nonwoven fabric was performed before the test, and the measurement value was used
as a blank value.
[0074] As the evaluation, the case where the rate of decrease in water pressure resistance
of the test piece was within 10% of the blank value was classified as ⊚+, the case
of more than 10% and within 20% as ⊚, the case of more than 20% and within 30% as
o, the case of more than 30% and within 50% as Δ, and the case of more than 50% as
×.
[0075] The results of the above evaluation are shown in Table 1.
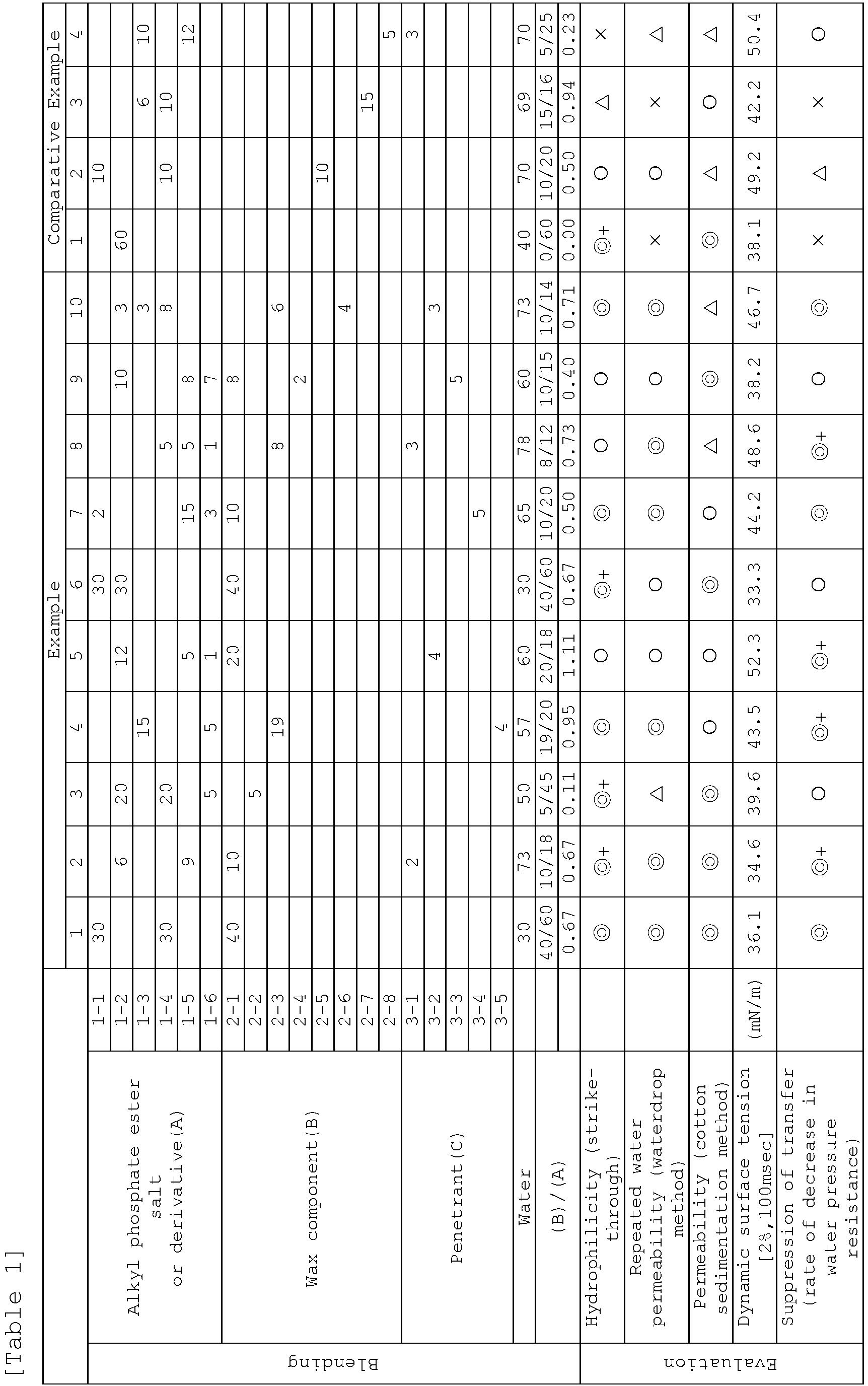