[0001] The invention relates to metallurgic engineering, to nickel-based alloys intended
for use in aggressive oxidizing environments.
[0002] A corrosion-resistant alloy Nicrofer 6616 hMo alloy C-4 (No. 2.4610), containing
wt.%: 14.5-17.5 Cr, 14.0-17.0 Mo, ≤3.0 Fe, ≤0.009 C, ≤1.0 Mn, ≤0.05 Si, ≤2.0 Co, ≤0.7
Ti, ≤0.020 P, ≤0.010 S, nickel and other unavoidable impurities is known from the
prior art (
Catalogue "Corrosion-resistant, heat-resistant and high-strength steels and alloys",
M., Prometey-Splav, 2008, pp. 304 - 306).
[0003] The alloy is used for the manufacture of equipment operated in a wide range of chemical
environments, at room and elevated temperatures. In particular, for adsorbers in flue
gas desul-phuring; etching baths and acid recovery plants; acetic acid and agrochemicals
plants.
[0004] The nearest analogue of the given invention is an alloy XH65MB

(

Π760) containing, wt.%: ≤0.02 C, ≤0.1 Si, ≤1.0 Mn, 14.5-16.5 Cr, 15.0-17.0 Mo, 3.0-4.5
W, ≤0.5 Fe, ≤0.012 S, ≤0.015 P, nickel and other unavoidable impurities (GOST 5632-2014
- prototype).
[0005] The alloy is used for the manufacture of welded structures (columns, heat exchangers,
reactors) operating under elevated temperatures in aggressive redox environments,
in the chemical, petrochemical industry (production of acetic acid, epoxy resins,
vinyl acetate, melamine, complex organic compounds) and other industries in the temperature
range -70 to 500°C.
[0006] The XH65MB alloy and its welded joints can be used in KCl - AlCl3 - ZrCl4 media only
up to 500 °C, because at a temperature above this value, the alloy, in addition to
intergranular corrosion and corrosion cracking, sharply decreases the percentage elongation
from 48% to 7.3-13% at 550°C and up to 2.5% at 625°C and the embrittlement of the
metal appears when deformation is applied.
[0007] The objective of the invention is to create an alloy having a high level of corrosion
properties at temperatures up to T = 650°C in the working media of chloride plants
(KCl - AlCl3 - ZrCl4).
[0008] The technical result of the invention is to obtain an alloy with a high level of
plastic properties for the operation in the temperature range 550°C to 625°C and increased
corrosion cracking resistance in chlorides KCl, AlCl3 + (ZrCl4 HfCl4) molten metal,
at temperatures up to 650°C.
[0009] The specified technical result is achieved in that the alloy containing carbon, silicon,
manganese, chromium, molybdenum, phosphorus, sulphur, iron, nickel and unavoidable
impurities, according to the invention additionally contains titanium, aluminium,
niobium, magnesium with the following components ratio, wt.% :
Carbon |
≤0.006 |
Silicon |
≤0.1 |
Manganese |
≤1.0 |
Chromium |
22.8-24.0 |
Iron |
≤0.75 |
Molybdenum |
12.0-14.0 |
Niobium |
0.01-0.03 |
Titanium |
0.01-0.06 |
Aluminium |
0.1-0.2 |
Magnesium |
0.005-0.01 |
Phosphorus |
≤0.015 |
Sulphur |
≤0.012 |
Nickel and unavoidable impurities |
balance |
[0010] To obtain a stable structure and plastic properties, it is preferable that the content
of chromium, molybdenum and iron is related by the ratio:
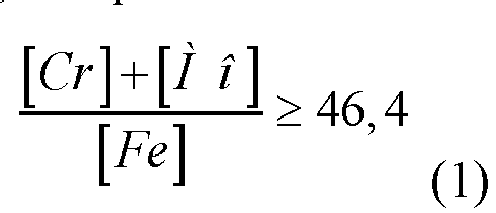
(the ratio of the total weight percentage of chromium and molybdenum to the percentage
of iron is not less than 46.4)
[0011] To obtain a stable structure and high corrosion properties, it is preferable that
the content of niobium and carbon is related by the ratio:
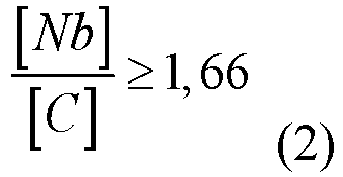
(the ratio of the weight percentage of niobium to the weight percentage of carbon
is not less than 1.66).
[0012] It is preferably that the content of chromium, molybdenum, iron, niobium and carbon
is related by the ratios:
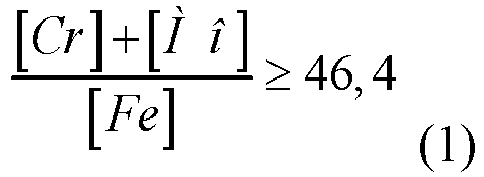
[0013] At
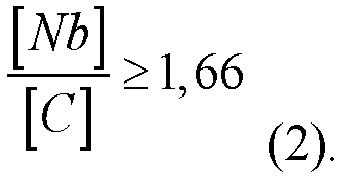
[0014] Comparative analysis with the prototype allows making a conclusion that the claimed
alloy differs from the known one with a lower carbon content (≤0.006% instead of ≤0.02),
molybdenum (12.0-14.0% instead of 15.0-17.0%), increased chromium content (23.0-24.0%
instead of 14.5-16.5%), iron (≤0.75% instead of ≤0.5%) does not contain tungsten,
as well as with the additional introduction of elements such as niobium in an amount
of 0.01-0.03%, titanium in an amount of 0.01-0.06%, aluminium in an amount of 0.1-0.2%
and magnesium in an amount of 0.005-0.01%.
[0015] Moreover, in particular cases of the invention, the claimed ratios of elements are
observed:
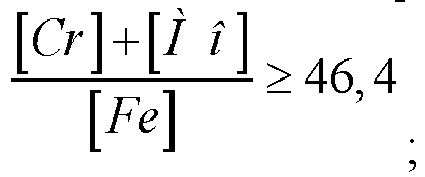
or

[0016] Or
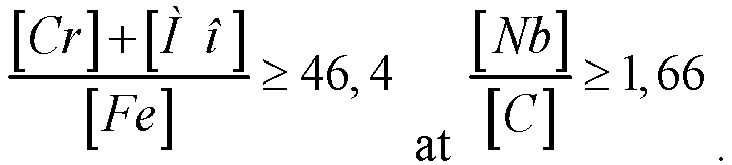
[0017] The limits of the content of alloying elements in the invention alloy are specified
as a result of a study of alloys properties with different composition options.
[0018] Exceeding the carbon content of more than 0.006% leads to a decrease in corrosion
resistance in solutions of zirconium and hafnium salts due to an increase in the carbide
formation process at high temperatures (the appearance of undesirable carbide phases).
[0019] The chromium content was found to be 22.8 - 24.0% to ensure the required heat resistance
in hafnium and zirconium oxides. When chromium is introduced into the alloy in the
amount of less than 22.8%, the required heat resistance is not ensured, and exceeding
the content above 24.0% impairs the heat resistance of the alloy.
[0020] The introduction of molybdenum into nickel alloys increases the recrystallization
temperature of solid solutions, inhibits their softening, increases heat resistance,
and leads to an ductility increase during short and long tests.
[0021] The range of molybdenum content of 12.0-14.0% is selected to provide the required
mechanical properties for both short-term and long-term loads and high temperatures.
With the introduction of less than 12.0% of molybdenum, the mechanical properties
are not met. When the content is above 14.0%, there is a decrease in ductility and,
accordingly, a decrease in the processability of the alloy during metallurgical processing.
[0022] Niobium in an amount of 0.01-0.03%, binds residual carbon and nitrogen to carbides,
nitrides and carbonitrides, prevents the formation of chromium carbides and carbonitrides
along the grain boundaries. The addition of niobium in an amount 6 to 10 times higher
than the carbon content in the alloy eliminates intergranular corrosion of the alloys
and protects the welds from destruction. When the niobium content is less than 0.01%,
its interaction with residual carbon is ineffective, and the niobium content above
0.03% is not reasonable for carbide formation.
[0023] Exceeding the silicon content of more than 0.1% negatively affects the processability
of the alloy, as well as leads to embrittlement of the alloy due to an increase of
silicon silicates content in it.
[0024] Increase of manganese content over 1.0% leads to the appearance of a fusible eutectic,
which leads to the destruction of the ingot during pressure processing and reduces
the heat resistance of the alloy, as well as leads to a decrease of local corrosion
resistance.
[0025] Nickel is stable in HCl even at boiling point. However, in the presence of chlorides,
ions of Fe(III) and other oxidizing agents corrosion of nickel and nickelchrome molybdenum
alloys is enhanced, the limitation of the iron content of not more than 0.75% is due
to this.
[0026] The introduction of titanium in an amount of 0.01-0.06% increases the corrosion resistance
in melts of zirconium and hafnium salts, binds residual carbon to carbides and leads
to the formation of a sufficient amount of Ni3Ti type intermetallic compound, which,
at an operating temperature of 500-700C, positively affects the heat resistance of
the alloy. When the titanium content is less than 0.01%, the requirements for corrosion
resistance are not met, and the excess of the titanium content above 0.06% leads to
a decrease in the processability of the alloy and the formation of undesirable phases
due to the reactivity of titanium.
[0027] Aluminium and magnesium in the amount of 0.1-0.2% and 0.005-0.01% are introduced
into the alloy to remove residual oxygen, as well as, with regard to aluminium, to
form an intermetallic compound of the Ni3Al type, which positively affects the heat
resistance of the alloy. When these elements are introduced in amounts less than specified,
the necessary removal of residual oxygen is not achieved. If the content of these
elements is exceeded, gross non-metallic inclusions are formed.
[0028] When the sulphur content exceeds 0.012% and phosphorus exceeds 0.015%, coarse non-metallic
inclusions are formed that adversely affect the ductility of the alloy.
[0029] Under the condition
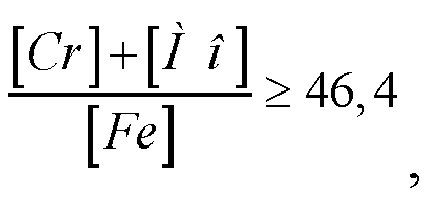
when the ratio decreases below 46.4, the alloy structure becomes less stable (sigma
phase is released), which has a negative effect on plastic characteristics and corrosion
resistance.
[0030] In the condition
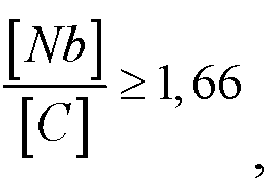
with a ratio of less than 1.66, a decrease in the corrosion resistance of the alloy
occurs.
[0031] The proposed ratio of the elements in the alloy were found experimentally and are
optimal, since they allow obtaining the claimed comprehensive technical result. When
breaking the ratios of the elements, the properties of the alloy deteriorate, their
instability is observed, and the complex effect is not achieved.
[0032] Examples of the invention implementation.
[0033] Alloy ingots were smelted in vacuum induction furnaces. The change in the plastic
properties of the studied alloys under the influence of temperatures of 550°C and
625°C after long exposure in the furnace for more than 1000 hours was controlled by
bending samples to an angle of 90 degrees or more according to GOST 14019-2003. Industrial
corrosion cracking resistance tests of alloys were carried out in molten chlorides
KCl, AlCl3 + (ZrCl4 HfCl4)
[0034] Table 1 shows the chemical composition of alloy ingots with various compositional
options, as well as the prototype alloy. Table 2 shows the results of determining
the plastic properties of the alloys indicated in table 1 by bending at an angle of
90 degrees according to GOST 14019-2003. Table 3 presents the results of industrial
corrosion cracking resistance tests of the alloys indicated in Table 1 in molten chlorides
KCl, AlCl3 + (ZrCl4 HfCl4), 100 hours, at T = 650°C.
[0035] As can be seen from tables 1, 2, the plastic properties of alloy at 550 and 625C
with the claimed composition (alloys 1, 2) are higher than the properties of the prototype
alloy, alloy 3, not satisfying the claimed composition, has lower plastic characteristics
than alloys 1, 2, which leads to the formation of cracks as a result of bending tests
according to GOST 14019-2003.
[0036] As it can be seen from table 3, the corrosion rate of alloys (alloys 1, 2) that satisfy
the claimed composition is lower than the corrosion rate of the prototype alloy, visual
inspection did not reveal the cracks, unlike the prototype alloy. The corrosion rate
of alloy 3, which does not satisfy the claimed composition, exceeds the corrosion
rate of alloys 1, 2 (however, lower than the corrosion rate of the prototype alloy),
visual inspection revealed a crack in the sample.
Table 1 - Chemical composition of the investigated alloys
Alloy |
C |
Mn |
Si |
Mo |
Cr |
Nb |
S |
P |
Fe |
Ti |
Al |
W |
Ni and unavoidable impurities |
Ratio (1) |
Ratio (2) |
Alloy 1 |
0.0011 |
0.55 |
00.7 |
13.0 |
23.3 |
0.03 |
0.0028 |
0,01 |
0.54 |
≤0.01 |
0.1 |
- |
balance |
67.2 |
27.27 |
Alloy 2 |
0.005 8 |
0.31 |
0,10 |
13.1 |
22.9 |
0.02 |
0.005 |
0.005 |
0.75 |
0.05 |
0.1 |
- |
balance |
48.0 |
3.45 |
Alloy 3 |
0.009 |
0.65 |
0.10 |
12.5 |
23.6 |
0.01 |
0.008 |
0.009 1 |
0.84 |
0.04 |
0.1 |
- |
balance |
42.98 |
1.11 |
Alloy acc.to prototype |
0.017 |
0.63 |
0.08 |
16.2 |
15.6 |
- |
0.006 |
0.009 |
0.45 |
- |
- |
3.7 |
balance |
- |
- |
Table 2 - Results of determining plastic properties by bending at an angle of 90 degrees
according to GOST 14019-2003
Alloy |
Exposure temperature, °C |
550°C |
625°C |
Exposure time, h |
Samples bending result |
Exposure Time, h |
Sample bending result |
Alloy acc.to prototype |
720 |
Sample broken |
720 |
Sample broken |
1000 |
No cracks |
1000 |
Crack |
2065 |
Crack |
2065 |
Crack |
Alloy 1 |
720 |
No cracks |
720 |
No cracks |
1000 |
No cracks |
1000 |
No cracks |
2065 |
No cracks |
2065 |
No cracks |
Alloy 2 |
720 |
No cracks |
720 |
No cracks |
1000 |
No cracks |
1000 |
No cracks |
2065 |
No cracks |
2065 |
No cracks |
Alloy 3 |
720 |
No cracks |
720 |
No cracks |
1000 |
No cracks |
1000 |
Crack |
2065 |
Crack |
2065 |
Crack |
Table 3 - Results of industrial corrosion cracking resistance tests of alloys in chloride
melts
KCl, AlCl3 + (ZrCl4 HfCl4), 100 h, at T = 650 C |
Alloy |
Visual inspection Cracks after testing |
Corrosion rate, mm/year |
Alloy acc.to prototype |
Crack in sample Pit corrosion in a sample up to 0.1-0.2 mm deep |
0.50 |
Alloy 1 |
No cracks Pit corrosion in metal sample up to 0.1-0.2 mm deep |
0.16 |
Alloy 2 |
No cracks Pit corrosion in a sample up to 0.1-0.2 mm deep |
0.21 |
Alloy 3 |
Crack in sample Pit corrosion in a sample up to 0.1-0.2 mm deep |
0.45 |