[0001] The invention relates to a fiber mat for mounting and/or protecting a component,
that gets exposed to changing temperatures. The invention also relates to a method
of making such a mat.
[0002] Fiber mats for mounting and/or protecting a component that gets exposed to changing
temperatures are for example used in the automotive field as mounting mats for wrapping
and mounting a pollution control element in a casing of a pollution control device.
Such fiber mats get exposed not only to changing but also to high temperatures in
the range of -30 °C to 1050 °C.
[0003] Exhaust gas cleaning systems using a ceramic catalytic converter are known as means
for removing carbon monoxide (CO), hydrocarbons (HC), and nitrogen oxides (NOx) and
the like that are included in exhaust gas from automobile engines. Basically, the
ceramic catalytic converter generally stores a ceramic catalyst carrier with a honeycomb
shape or the like in a metal casing. Other exhaust gas cleaning systems contain ceramic
particulate filters for removing particulates from the exhaust gas of diesel or gasoline
engines.
[0004] There are various types of ceramic catalytic converters, but a general form provides
a catalyst carrier or a filter, a casing that stores the catalyst carrier or the filter,
and a thermal insulation member or mat that fills the gap between the outer surface
of the catalyst carrier or the filter and the inner surface of the casing. The thermal
insulation member or fiber mat mounts the catalyst carrier or the filter and prevents
mechanical shock due to impact and vibration and the like from being inadvertently
applied to the catalyst carrier or the filter. Thereby, moving and breaking of the
catalyst carrier or the filter can be sufficiently suppressed, and thus the desired
effect can be provided over a long period of time. This type of thermal insulation
member is also commonly called a mounting member or fiber mounting mat because the
member also has a function of mounting and holding a pollution control element such
as a catalyst carrier or a filter in a metal shell or the like. The mounting members
or mats used in the exhaust gas cleaning systems are designed such that they reliably
hold the catalytic converter or filter even after a lot of cycles of changing temperatures
in the range of -30 °C to 1050 °C.
[0005] Other uses for fiber mats for mounting and/or protecting a component, that gets exposed
to changing temperatures are thermal or flame barrier applications, spacer applications
or insulation applications. Besides uses in applications in pollution control devices
as described above other uses are possible as well.
[0006] JP 2002 206 421 A2 discloses a holding and sealing material for a catalytic converter, that can sufficiently
maintain the function of retaining the pollution control element in a pollution control
device at high temperatures. The holding and mounting material comprises ceramic fibers.
The fibers comprise an uneven structure consisting of inorganic particles added to
the fibers by sintering.
[0007] WO 2012/106295 A1 discloses a mounting member that can sufficiently suppress scattering of inorganic
fiber material when a pollution control element is assembled in a casing, and that
can maintain sufficiently high contact pressure between the inner surface of the casing
and the pollution control element. The mounting member provides a mat made from inorganic
fiber material and an aggregated substance containing an organic binder and inorganic
fine particles that is impregnated throughout most of the mat.
[0008] US 8,071,040 B2 discloses a mounting mat for an exhaust gas treatment device including high temperature
resistant ceramic fibers containing alumina and/or high temperature resistant biosoluble
inorganic fibers, organic binder which at least partially liquefies at elevated temperature
prior to binder burnout, colloidal inorganic oxide and optionally intumescent material.
The mounting mat can be easily installed and can function across a wide range of inlet
gas temperatures without a significant loss in mat thickness and corresponding shear
strength and holding pressure performance.
[0009] As already laid out above, common requirements for the above described fiber mounting
mats or members are superior holding forces under extreme and changing temperatures.
This property is usually tested with a so called multi-cycle compression test (MCC).
[0010] It now has been found, that a mounting mat according to the invention provides surprisingly
good results in this multi-cycle compression test (MCC).
[0011] The present invention provides a fiber mat for mounting and/or protecting a component
that gets exposed to changing temperatures, the fiber mat comprises:
- processed fibrous material, wherein the processed fibrous material comprises inorganic
fibers as well as inorganic binder and wherein the processed fibrous material is compressed
and fragmented before being used for making the fiber mat, as well as
- optionally inorganic bulk fibers.
[0012] According to the invention, the fiber mat comprises processed fibrous material and
optional inorganic bulk fibers. The processed fibrous material comprises inorganic
fibrous material as well as inorganic binder wherein the fibrous material with the
binder has been processed by at least the two following steps:
- compression;
- fragmentation.
[0013] The compression step may be any know compression step used in fiber mat making processes
as listed below. The fragmentation step may be any known fragmentation step used in
fiber mat making processes such as for example a chopping step, a cutting step, a
shredding step, a milling step, a dry or wet opening step, a breaking step or a combination
of any of the before mentioned steps.
[0014] Changing temperatures as mentioned above may be temperatures that quickly change
between for example -30 °C to 1050 °C.
[0015] It is possible to use as processed fibrous material fiber material that already went
through a fiber mat making process, like a dry laid process or a wet laid process.
This could include material that may not be used for mounting mats that are used commercially,
e.g. sold to customers. This could include for example waste material from mounting
mat production processes, like rests of cutting steps that cannot be used because
they do not provide the right geometry or cut mounting mat material that cannot be
used for other reasons.
[0016] The inorganic fibers used for the fiber mat according to the invention - in the processed
fibrous material as well as in the bulk fibers - may comprise fibers selected from
the group of polycrystalline fibers, alumina fibers, alumina-silica fibers, glass
fibers, ceramic fibers, carbon fibers, silicon carbide fibers or boron silicate fibers
or a combination thereof. More specific, the fibrous material may include annealed
melt-formed ceramic fibers, sol-gel formed ceramic fibers, polycrystalline ceramic
fibers, alumina-silica fibers, glass fibers, including annealed glass fibers or non-bio-persistent
fibers. Other fibers are possible as well, if they withstand the high temperatures
and the temperature changes occurring in a pollution control device and the required
holding forces during use of the pollution control device.
[0017] The inorganic binder used for the fiber mat according to the invention may be selected
from the group consisting of metal oxides, metal hydroxides, metal oxide hydroxides,
silicates, clays, nitrides, carbides, sulphides, carbonates and combinations thereof,
for example silica-sol and alumina-sol.
[0018] Surprisingly it has been found, that a fiber mat that was produced through a known
fiber mat making process and that comprises the features mentioned above shows improved
results in a multi-cycle compression test (MCC) without adding any other performance
ingredients, like inorganic binder or other additives. Especially the holding pressure
performance was improved.
[0019] It should be mentioned that in all known fiber mat making processes organic binder
may be added and usually is added. The organic binder is needed to hold the fibers
together and to make the mat manageable during the assembly process. The organic binder
does influence the holding performance only marginal at the mat since it gets burnt
out once the mounting at gets heated above 400 °C. The organic binder may be added
in an amount between 1 and 15 wt. %, preferably between 1 and 10 wt. %. The organic
binder may be an acrylic latex binder, a silicone binder in a wet laid process or
it may be a mono- or bi-component fibers based on PE, PP, PET etc. in a dry laid process
but not limited to that.
[0020] The fiber mat according to the invention may be used as a mounting and/or as an insulation
mat. More specific, it may be used as a mounting mat for exhaust gas treatment devices,
as an insulation mat for example for components of an exhaust gas treatment device
such as for example a catalytic converter or a filter, as a thermal barrier material
in all possible applications or as a flame barrier material in all possible applications.
[0021] According to one embodiment the compression step of the processed fibrous material
includes needling, stich-bonding, thermal bonding, chemical bonding (e.g. vinyl polymers
and copolymers, acrylic ester polymers and copolymers, rubber and synthetic rubber,
and natural binders, principally starch) or a combination thereof. Any other known
compression methods in the field of inorganic fiber mats/members or mounting mats/members
may be used as well.
[0022] According to another embodiment, the inorganic fibers of the processed fibrous material
are the same as the fibers of the bulk fibers. It is also possible that the inorganic
fibers of the processed fibrous material differ from the fibers of the bulk material.
[0023] It is possible that the fiber mat according to the invention comprises processed
fibrous material in an amount of 2 to 100 wt. % based on the total weight of the fiber
mat, preferably 10 to 100 wt. % based on the total weight of the fiber mat, preferably
20 to 100 wt. % on the total weight of the fiber mat, preferably 30 to 100 wt. % on
the total weight of the fiber mat.
[0024] The fiber mat according to the invention may comprise inorganic binder in an amount
of 0.1 to 10 wt. % based on the total weight of the mounting mat, for example in an
amount of 0.5 to 5 wt. %.
[0025] The fiber mat may comprise further additives for improved handling, improved performance
and/or improved protection properties. The fiber mat may also include any material
that provides an expansion of the mat as soon as it gets exposed to higher temperatures.
Such materials may for example be intumescent materials. Useful intumescent materials
for use in making an intumescent mat include, but are not limited to, unexpanded vermiculite
ore, treated unexpanded vermiculite ore, partially dehydrated vermiculite ore, expandable
graphite, mixtures of expandable graphite with treated or untreated unexpanded vermiculite
ore, processed expandable sodium silicate, for example EXPANTROL™ insoluble sodium
silicate, commercially available from 3M Company, St. Paul, Minn., and mixtures thereof.
[0026] The invention also relates to a method of making a fiber mat for mounting and/or
protecting a component that gets exposed to changing temperatures, the method comprising
the steps of:
- providing processed fibrous material, wherein the processed fibrous material comprises
inorganic fibers as well as inorganic binder;
- optionally providing bulk fibers;
- converting the processed fibrous material and optionally the bulk fibers in a known
fiber mat making process into a fiber mat for mounting and/or protecting a component
that gets exposed to changing temperatures.
[0027] The method according to the invention may comprise an additional pre-treatment step,
wherein the pre-treatment step includes the pre heating of the processed fibrous material
and optionally the bulk fiber with a temperature of at least 500 °C.
[0028] The step of converting the processed fibrous material and optionally bulk fibers
may be a wet laid process. A wet laid process is a process that uses a water-based
slurry to mix the ingredients of a fiber mat together. The mixing step may be followed
by a forming and a dewatering step again followed by a drying and a converting step.
[0029] The step of converting the processed fibrous material and optionally the bulk fibers
according to the wet laid process may comprise the steps of:
- preparing a material slurry from the processed fibrous material and optionally the
bulk fibers;
- forming a moulded body having a desired shape using the slurry; and
- drying the moulded body to obtain a fiber mat having the desired shape.
[0030] As an alternative, the step of converting the processed fibrous material and optionally
bulk fibers may be a dry laid process. A dry laid process uses air to mix the ingredients
of a fiber mat together. A forming chamber may be used for this mixing step. The mixing
step may be followed by a laying, compressing and/or a converting step.
[0031] The step of converting the processed fibrous material and optionally the bulk fiber
according to the dry laid process may comprise the steps of:
- supplying processed fibrous material through an inlet of a forming box having an open
bottom positioned over a forming wire to form a mat of fibers on the forming wire,
the forming box having a plurality of fiber separating rollers provided in at least
one row in the housing between the inlet and housing bottom for breaking apart clumps
of fibers and an endless belt screen;
- optionally supplying inorganic bulk fibers through an inlet of the forming box, similar
to the way the processed fibrous material is supplied to the forming box;
- optionally capturing clumps of fibers on a lower run of the endless belt beneath fiber
separating rollers and above the forming wire;
- optionally conveying captured clumps of fibers on the endless belt above fiber separating
rollers to enable captured clumps to release from the belt and to contact and be broken
apart by the rollers;
- transporting the mat of fibers out of the forming box by the forming wire; and
- compressing the mat of fibers and restraining the mat of fibers in its compressed
state thereby obtaining a mounting mat having a desired thickness suitable for mounting
a pollution control element in the housing of a catalytic converter.
Examples:
[0032]
The following examples have been prepared:
- fiber mat made from processed fibrous sheet with inorganic binder
- fiber mat made with processed fibrous sheet without inorganic binder
- with and without heat treatment, organic binder is burnt out
[0033] The following equipment has been used:
- Blender, "Rotor GT800 Classic" from Rotor Lips Ltd., CH-3662 Uetendorf, Switzerland
- Container 5000ml
- Mixer RW16 basic from IKA-Werke GmbH & Co. KG, 71219 Staufen, Germany
- Manual hand-sheet maker 8" x 8" [203mm x 203mm] sheet mold equipped with 100 mesh
sieve from Mfg. by Williams Apparatus Co. - Watertown, NY, United States of America
- Convection oven for drying
[0034] The following material has been used:
- Latex A420S, aqueous emulsion 50% solids, commercially available from BASF, Germany
- Flocculant aluminium sulfate solution, commercially available from AppliChem GmbH,
Darmstadt, Germany
- Tap water
- Blotter paper
- Interam™ 1650 HTG, commercially available from 3M Germany GmbH, Germany
- Interam™ 1600 HTE, commercially available from 3M Germany GmbH, Germany
Hand-sheet making process:
[0035] 61.4 g compressed fibrous material has been cut into about 2.5 by 2.5 cm
2 pieces to provide processed fibrous material. The processed fibrous material was
put into the blender (Rotor GT 800 Classic) in 3000 ml tap water. By using the blender
at step 3.5 for 30 sec. the pieces of processed fibrous material were opened or broken
into smaller pieces. The opened fibers together with the 3000 ml water were transferred
into a 5000 ml container. While again agitating the pulp now with a mixer at medium
speed using a propeller blade for at least 1 minute 5.12 g latex binder was added.
After another minute at the same level of blending with the mixer 19 g of a 30 wt.
% aluminum sulfate solution flocculant was added and mixed for another 2 minutes to
coagulate the latex binder. After one more minute the pulp was quickly poured into
a hand-sheet maker and immediately dewatered.
[0036] The hand sheet was manually compressed between blotter paper using a roll and dried
in the oven for 1 h at 140 °C.
Example 1:
[0037] For Example 1 Interam™ 1650 HTG containing 1 % inorganic binder (boehmite) was used
as processed fibrous material for making a hand-sheet according to the above described
process.
Comparative Example 1:
[0038] For Example 2 Interam™ 1600 HTE without inorganic binder was used as processed fibrous
material for making a hand-sheet according to the above described process.
Example 2:
[0039] For Example 3 Interam™ 1650 HTG, containing 1% inorganic binder (boehmite) was pre-treated
by heating it at 600 °C for 30 minutes to remove the organic binder. The burned processed
fibrous material was then cut in pieces and a hand-sheet was made according to the
above described process.
Comparative Example 2:
[0040] For Example 4 Interam™ 1600 HTE without inorganic binder was pre-treated by heating
it at 600 °C for 30 minutes to remove the organic binder. Burned mat was cut in pieces
and a hand-sheet was made according to the above described process.
Table 1: test matrix
Example No. |
Inorganic binder |
Binder burnt out |
1 |
Yes |
No |
2 |
No |
No |
3 |
Yes |
Yes |
4 |
No |
Yes |
Multi-cycle Compression Test MCC:
[0041] A common parameter to characterize the performance of a mounting mat is the so called
multi-cycle test. The Examples were tested at a temperature of 250 °C and 650 °C,
the gap was cycled 1000 times between a closed gap and an open gap density. The open
gap pressure after cycling is recorded.
[0042] For the tests in these examples a material test machine from Zwick/Roell Model Z010
from Zwick GmbH & Co KG, Ulm, Germany was utilized. The test machine was equipped
with a lower fixed heatable stainless steel block and a load cell capable of measuring
forces up to 10 kN and an upper heatable stainless steel block mounted to the movable
crosshead of the test machine. For the tests a sample of each example and comparative
example with 50.8 mm diameter was cut out of the mounting member and placed on the
lower heatable stainless steel block. The crosshead was moved downwards to compress
the mounting member to a defined closed gap, which corresponds to a density of the
mounting member of 0.40 g/cm
3. The maximum pressure at closed and before heating is called peak pressure P0. The
relaxed pressure "P relaxed" is taken after 10 min dwell time after the closed gap
is reached. The temperature of the heatable stainless steel blocks was raised to 650
°C (250 °C) while keeping the gap constant. After reaching the temperature of 650
°C (250 °C), the gap was cycled between the closed gap position corresponding to a
density of the mounting member of 0.40 g/cm
3 and an open gap position corresponding to a density of the mounting member of 0.364
g/cm
3 (0.381 g/cm
3 at 250 °C test temperature). After 1000 cycles the test was stopped and the open
gap pressure after 1000 cycles P1000 was recorded.
[0043] All samples and the comparative example were tested at isothermal temperatures 250
°C, 5 % gap opening, and - another fresh sample - at 650 °C, 10 % gap opening.
Gap Bulk Density GBD (closed gap): 0.40 g/cm3
[0044]
- at 250 °C test GBD (open gap): 0.381 g/cm3 (5 % gap opening)
- at 650 °C test GBD (open gap): 0.3634 g/cm3 (10 % gap opening)
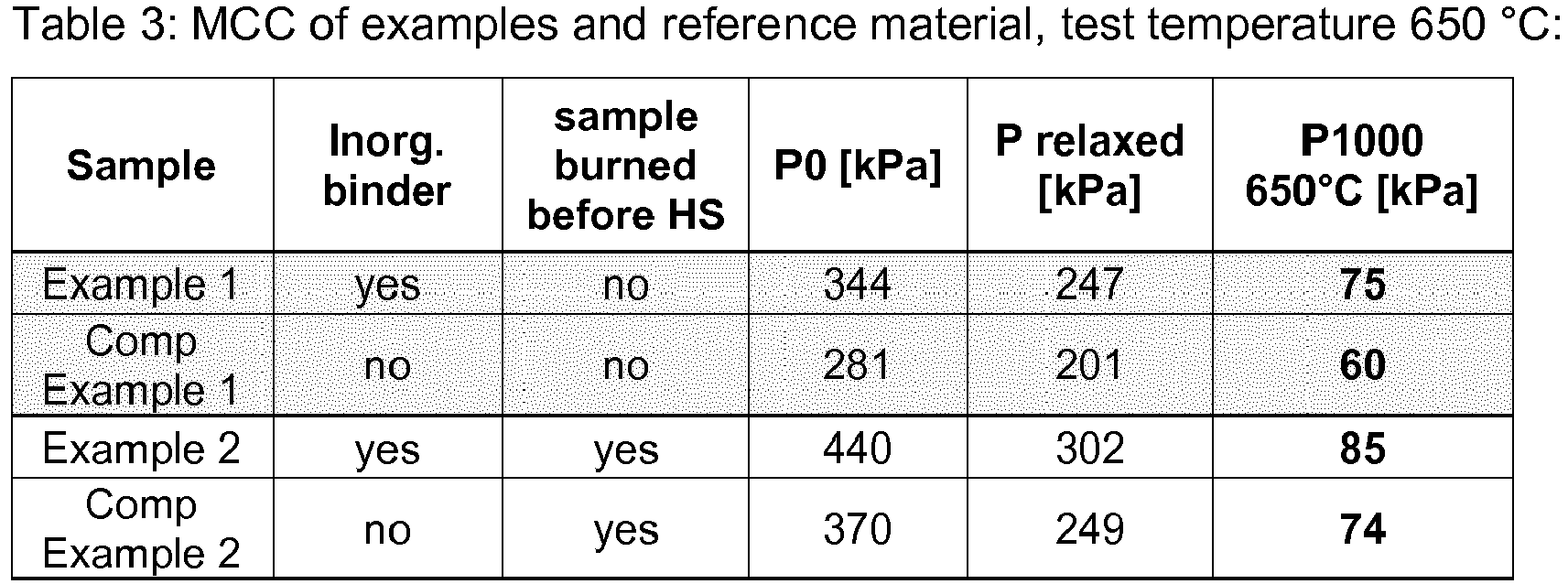
[0045] As can be seen from the Examples, using the processed fibrous material for making
a fiber mounting mat provides improved results in the multi-cycle compression test
in all three values P0, P relaxed and P1000. The values can even be more improved,
when the example gets pre-treated with a heating step like it was done with Example
2.
1. A fiber mat for mounting, and/or protecting a component, that gets exposed to changing
temperatures, the fiber mat comprises:
- processed fibrous material, wherein the processed fibrous material comprises inorganic
fibers as well as inorganic binder and wherein the processed fibrous material is compressed
and fragmented before being used for making the fiber mat, as well as
- optionally inorganic bulk fibers.
2. The fiber mat according to claim 1, wherein the fiber mat can be used as a mounting
and/or insulation mat.
3. The fiber mat according to any of the preceding claims, wherein the compression step
of the processed fibrous material includes needling, stich-bonding, thermal bonding,
chemical bonding or a combination thereof.
4. The fiber mat according to any of the preceding claims, wherein the inorganic fibers
of the processed fibrous material and/or the inorganic fibers of the bulk material
comprise inorganic fibers such as polycrystalline fibers, alumina fibers, alumina-silica
fibers, glass fibers, ceramic fibers, alkaline and alkaline earth silicate fibers,
carbon fibers, silicon carbide fibers or boron silicate fibers or a combination thereof.
5. The fiber mat according to any of the preceding claims, wherein the inorganic fibers
of the processed fibrous material are the same as the fibers of the bulk fibers.
6. The fiber mat according to any of the preceding claims, wherein the fiber mat comprises
processed fibrous material in an amount of 2 to 100 wt. % based on the total weight
of the fiber mat, preferably 10 to 100 wt. % based on the total weight of the fiber
mat, preferably 20 to 100 wt. % on the total weight of the fiber mat, preferably 30
to 100 wt. % on the total weight of the fiber mat.
7. The fiber mat according to any of the preceding claims, wherein the fiber mat comprises
inorganic binder in an amount of 0.1 to 10 wt. % based on the total weight of the
fiber mat, for example 0.5 to 5 wt. % based on the total weight of the fiber mat.
8. The fiber mat according to any of the preceding claims, wherein the fiber mat comprises
organic binder in an amount between 1 to 15 wt. %, preferably between 1 and 10 wt.
%.
9. The fiber mat according to any of the preceding claims, wherein the fiber mat comprises
further additives for improved handling, improved performance and/or improved protection
properties.
10. Method of making a fiber mat for mounting and/or protecting a component, that gets
exposed to changing temperatures, the method comprising the steps of:
- providing processed fibrous material, wherein the processed fibrous material comprises
inorganic fibers as well as inorganic binder;
- optionally providing bulk fibers;
- converting the processed fibrous material and optionally the bulk fibers in a known
fiber mat making process into a fiber mat for mounting and/or protecting a component
that gets exposed to changing temperatures.
11. Method according to claim 10, wherein the method comprises an additional pre-treatment
step, wherein the pre-treatment step includes the preheating of the processed fibrous
material and optionally the bulk fiber with a temperature of at least 500 °C.
12. Method according to claim 10 or 11, wherein the step of converting the processed fibrous
material and optionally the bulk fibers into a fiber mat is a wet laid process.
13. Method according to any of the claims 10 to 12, wherein the step of converting the
processed fibrous material and optionally the bulk fibers into a fiber mat comprises
the steps of:
- preparing a material slurry from the processed fibrous material and optionally the
bulk fibers;
- forming a moulded body having a desired shape using the slurry; and
- drying the moulded body to obtain a fiber mat having the desired shape.
14. Method according to claim 10 or 11, wherein the step of converting the processed fibrous
material and optionally the bulk fibers into a mat is a dry laid process.
15. Method according to claim 10 or 14, wherein the step of converting the processed fibrous
material and optionally the bulk fibers into a mat comprises the steps of
- supplying processed fibrous material through an inlet of a forming box having an
open bottom positioned over a forming wire to form a mat of fibers on the forming
wire, the forming box having a plurality of fiber separating rollers provided in at
least one row in the housing between the inlet and housing bottom for breaking apart
clumps of fibers and an endless belt screen;
- optionally supplying inorganic bulk fibers through an inlet of the forming box,
similar to the way the processed fibrous material is supplied to the forming box;
- optionally capturing clumps of fibers on a lower run of the endless belt beneath
fiber separating rollers and above the forming wire;
- optionally conveying captured clumps of fibers on the endless belt above fiber separating
rollers to enable captured clumps to release from the belt and to contact and be broken
apart by the rollers;
- transporting the mat of fibers out of the forming box by the forming wire; and
- compressing the mat of fibers and restraining the mat of fibers in its compressed
state thereby obtaining a mounting mat having a desired thickness suitable for mounting
a pollution control element in the housing of a catalytic converter.