[0001] The present invention relates to a method of producing a phosphonated acrylic copolymer,
and to the copolymer obtained by the method. Furthermore, the present invention pertains
to the use of the phosphonated acrylic copolymer for hydrophilizing surfaces and to
automatic dish washing and metal cleaning compositions comprising the phosphonated
acrylic copolymer.
[0002] The hydrophilization of surfaces via polymers is a common means in order to improve
water spreading and thus the drain off of water from the surface, especially in cleaning
applications like dishwashing or hard surface cleaning. By hydrophilizing surfaces,
less drying residues appear on reflective and transparent surfaces. Such polymers
often have no specific affinity to the surface and form a hydrophilic layer on the
surface only via drying. Thereby, a rather high amount of polymer is needed. Furthermore,
the effect is not long lasting as the polymer can be washed off.
[0003] Therefore, there is a need for polymers, which can hydrophilize surfaces, especially
metal and SiO
2 surfaces, and have an affinity to the surface to be hydrophilized.
[0004] The present inventors found that the problem can be solved by a novel phosphonated
acrylic copolymer. Furthermore, it has been surprisingly found that with this copolymer
a thicker layer on the surface can be obtained compared to already conventionally
used polymers, when applied in the same amount. Furthermore, the copolymers according
to the present invention form a longer lasting layer and the drain off of water in
view of the initial stainless steel surface is improved. Finally, since phosphonic
groups are employed to obtain the affinity to the surface, no environmental concerns
arise compared with phosphates.
[0005] Therefore, the present invention relates in a first aspect to a method of producing
a phosphonated acrylic copolymer, comprising or consisting of the steps:
reacting
- i) at least one monomer of formula (I)
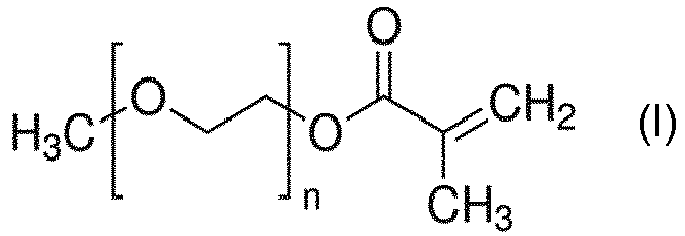
having a number average molecular weight of 250 to 4,000 g/mol with
ii) at least one monomer of formula (II)
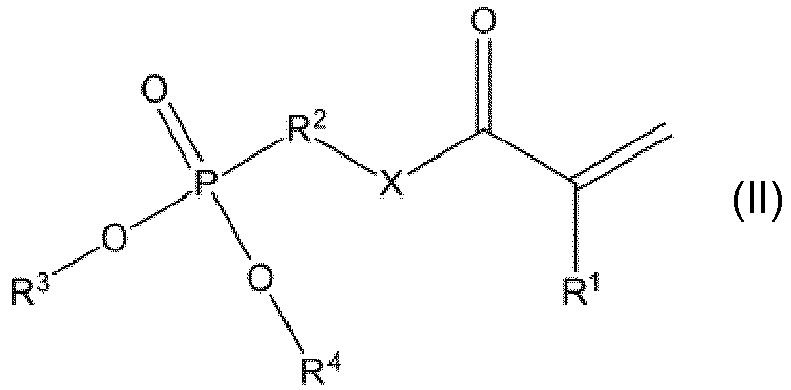
wherein
X is O or NH;
R1 is hydrogen or methyl;
R2 is an aliphatic or aromatic hydrocarbon group having up to 12 carbon atoms;
R3 and R4 are independently selected from hydrogen or an aliphatic or aromatic hydrocarbon
group having up to 6 carbon atoms; and
iii) optionally up to 10 wt.-% of at least one ethylenically unsaturated monomer,
based on the total weight of the monomer mixture; optionally in the presence of a
radical initiator.
[0006] In a second aspect, a phosphonated acrylic copolymer, obtainable by the method according
to the present invention is provided.
[0007] In a third aspect, the invention pertains to the use of the phosphonated acrylic
copolymer according to the present invention for hydrophilizing surfaces, preferably
steel surfaces or silicate containing surfaces.
[0008] Furthermore, in a fourth aspect, the invention refers to a dishwashing composition
comprising the phosphonated acrylic copolymer of the present invention.
[0009] Finally, in a fifth aspect, the invention pertains to a hard surface cleaning composition
comprising the phosphonated acrylic copolymer of the present invention.
[0010] "One or more", as used herein, relates to "at least one" and comprises 1, 2, 3, 4,
5, 6, 7, 8, 9 or more of the referenced species. Similarly, "at least one" means "one
or more", i.e. 1, 2, 3, 4, 5, 6, 7, 8, 9 or more. "At least one", as used herein in
relation to any component, refers to the number of chemically different molecules,
i.e. to the number of different types of the referenced species, but not to the total
number of molecules. For example, "at least one monomer of formula (I)" means that
at least one type of monomer falling within the definition can be used, but that also
two or more different monomers falling within this definition can be used.
[0011] Numeric values specified without decimal places refer to the full value specified
with one decimal place. For example, "99 %" means "99.0 %", if not stated otherwise.
[0012] The expressions "approx." or "about", in conjunction with a numerical value, refer
to a variance of ± 10 % relative to the given numerical value, preferably ± 5 %, more
preferably ± 1 %, if not explicitly stated otherwise.
[0013] These and other aspects, features and advantages of the invention become apparent
to the skilled person in the following detailed description and claims. Each feature
from one aspect of the invention can be used in any other aspect of the invention.
Additionally, each feature from one embodiment can be combined with every other feature
from another embodiment, if not explicitly stated otherwise. Furthermore, the examples
contained herein are intended to describe and illustrate the invention, but do not
restrict it and in particular, the invention is not limited to these examples.
[0014] The phosphonated acrylic copolymer, in the following referred to as copolymer as
well, is obtainable by a method, comprising or consisting of the steps:
reacting
- i) at least one monomer of formula (I)
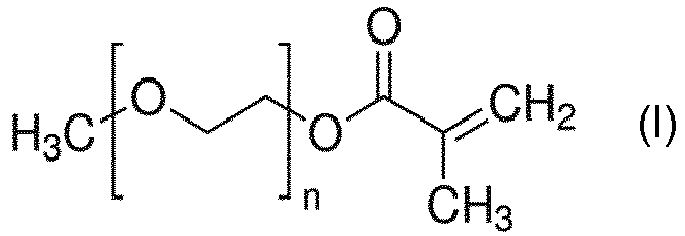
having a number average molecular weight of 250 to 4,000 g/mol with
- ii) at least one monomer of formula (II)
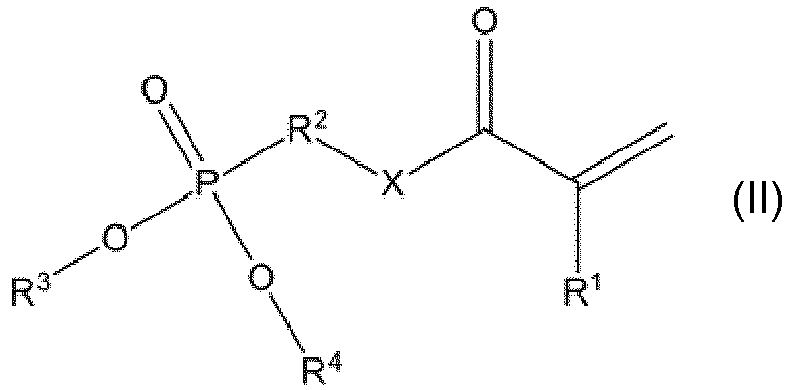
wherein
X is O or NH;
R1 is hydrogen or methyl;
R2 is an aliphatic or aromatic hydrocarbon group having up to 12 carbon atoms;
R3 and R4 are independently selected from hydrogen or an aliphatic or aromatic hydrocarbon
group having up to 6 carbon atoms; and
- iii) optionally up to 10 wt.-% of at least one ethylenically unsaturated monomer,
based on the total weight of the monomer mixture; optionally in the presence of a
radical initiator.
[0015] Aliphatic hydrocarbon groups preferably refer to linear or branched, substituted
or unsubstituted alkyl, alkenyl, alkinly, alkylcycloalkyl, alkenylcycloalkyl, or cycloalkyl
groups which can contain heteroatoms preferably selected from N, S, P, O or Si. In
case at least one substituent is present, the substituent is preferably selected from
-F, -CI, -Br, -CF
3, =O, -OH, -NH
2, -NO
2, -COOH, and -C(=O)H. Aromatic hydrocarbon groups can be substituted or unsubstituted
and can contain heteroatoms preferably selected from -F, -CI, -Br, -CF
3, =O, -OH, -NH
2, -NO
2, -COOH, and -C(=O)H. In case at least one substituent is present, the substituent
is preferably selected from -F, -CI, -Br, -CF
3, =O, -OH, -NH
2, -NO
2, -COOH, and -C(=O)H.
[0016] In one embodiment the at least one monomer of formula (I) has a number average molecular
weight of 300 to 950 g/mol, preferably of 300 to 500 g/mol.
[0017] In a further embodiment in in the at least one monomer of formula (II) R
1 is methyl; and/or R
2 is an aliphatic hydrocarbon group having up to 6 carbon atoms, preferably C1 to C4
alkyl, more preferably methyl; and/or R
3 and R
4 are hydrogen or methyl; and/or X is O. In a preferred embodiment R
1 is methyl; R
2 is an aliphatic hydrocarbon group having up to 6 carbon atoms, preferably C1 to C4
alkyl, more preferably methyl; R
3 and R
4 are hydrogen or methyl; and X is O. In preferred embodiments R
3 and R
4 are similar.
[0018] The copolymer can contain further ehtylenically unsaturated monomers in up to 10
mol%. If present the at least one ethylenically unsaturated monomer is selected from
C1 to C12 (meth)acrylate, acrylic acid, meth acrylic acid, vinylsulfonic acid, vinyl
pyrrolidon, acrylamide, N-methyl acrylamide, maleic acid, maleic anhydride, itaconic
acid, and cinnamic acid. However, in preferred embodiments only monomers according
to formula (I) and formula (II) are present.
[0019] In various embodiments the at least one monomer of formula (II) is present in 0.1
to 99.9 mol%, preferably 10 to 50 mol% and/or the at least one monomer of formula
(I) is present in 0.1 to 99.9 mol%, preferably 50 to 90 mol%.
[0020] The reaction can be performed in the presence of a radical initiator. Any radical
initiator, which is employed in the field of acrylic polymers is suitable. Preferred
radical initiators are selected from azobisisobutyronitrile, ammonium persulfate,
hydrogen peroxide, and tert.-butyl hydroperoxide. To obtain small molecular weights
in the range of 1000-10000 g/mol chain transfer agents e.g. mercapto acetic acid can
be added in the range of 0.0025-0.25 mol% relative to the total moles of monomers
of the polymerization mixture.
[0021] The reaction can be performed in a solvent or in a mixture of solvents. Any solvents,
which are employed in the field of acrylic polymers are suitable. In preferred embodiments
the reaction is performed in a solvent comprising at least one C1-C5 alcohol and/or
at least one halogenated hydrocarbon solvent, like chloroform or dichloromethane and/or
water.
[0022] In an optional second step the phosphonate groups can be hydrolyzed to the respective
phosphonic acid groups e.g. employing equimolar amounts of trimethylsilyl bromide
under anhydrous conditions.
[0023] The reaction can be performed at elevated temperatures of from 30 to 100°C, preferably
50 to 80°C.
[0024] The obtained phosphonated acrylic copolymer according to the present invention preferably
has a number average molecular weight of 1,000 to 100,000 g/mol, preferably 1,500
to 10,000 g/mol.
[0025] Molecular weights, including the number average molecular weight, are according to
the invention preferably determined via GPC measurement with use of polystyrene standards,
unless explicitly stated otherwise.
[0026] The copolymers according to the present are used for hydrophilizing surfaces, preferably
steel surfaces or silicate containing surfaces.
[0027] Thus, the copolymers according to the present composition can be used in cleaning
compositions.
[0028] The present invention refers to a dishwashing composition, preferably an automatic
dishwashing composition, comprising the phosphonated acrylic copolymer of the present
invention. Furthermore, the present invention refers to a hard surface, preferably
metal, cleaning composition comprising the phosphonated acrylic copolymer of the present
invention.
[0029] The dish washing and hard surface compositions, in the following referred to as compositions,
can further contain further components commonly employed in the respective field.
[0030] In the following compounds, which can be additionally contained are described.
[0031] A composition according to the invention can further comprise a bleach catalyst.
These substances are preferably bleach-boosting transition metal salts or transition
metal complexes such as, for example, manganese-, iron-, cobalt-, ruthenium- or molybdenum-salen
or -carbonyl complexes. Manganese, iron, cobalt, ruthenium, molybdenum, titanium,
vanadium and copper complexes with nitrogen-containing tripod ligands, as well as
cobalt-, iron-, copper- and ruthenium-ammine complexes may also be employed as the
bleach catalysts.
[0032] Complexes of manganese in the valence state II, III, IV or V which preferably comprise
one or a plurality of macrocyclic ligands with the donor functions N, NR, PR, O and/or
S are particularly preferably employed. Ligands having nitrogen donor functions are
preferably employed. In this regard, it is particularly preferred to incorporate bleach
catalyst(s) into the compositions according to the invention, which comprise 1,4,7-trimethyl-1,4,7-triazacyclononane
(Me-TACN), 1,4,7-triazacyclononane (TACN), 1,5, 9-trimethyl-1,5,9-triazacyclododecane
(Me-TACD), 2-methyl-1,4, 7-trimethyl-1,4,7-triazacyclononane (Me/Me-TACN) and/or 2-methyl-1,4,7-triazacyclononane
(Me/TACN) as the macromolecular ligands. Suitable manganese complexes are for example
[Mn
III2(µ-O)
1(µ-OAc)
2(TACN)
2](ClO
4)
2, [Mn
IIIMn
IV(µ-O)
2(µ-OAc)
1(TACN)
2](BPh
4)
2, [Mn
IV4(µ-O)
6(TACN)
4](ClO
4)
4, [Mn
III2(µ-O)
1(µ-OAc)
2(Me-TACN)
2](ClO
4)
2, [Mn
IIIMn
IV(µ-O)
1(µ-OAc)
2(Me-TACN)
2](ClO
4)
3, [Mn
IV2(µ-O)
3(Me-TACN)
2](PF
6)
2 and [Mn
IV2(µ-O)
3(Me-TACN)
2](PF
6)
2(OAc=OC(O)CH
3).
[0033] Compositions, in particular automatic dishwashing compositions, are preferred that
comprise a bleach catalyst selected from the group of the bleach boosting transition
metal salts and transition metal complexes, preferably from the group of the complexes
of manganese with 1,4,7-trimethyl-1,4,7-triazacyclononane (Me-TACN) or 1,2,4,7-tetramethyl-1,4,7-triazacyclononane
(Me/Me-TACN), as these cited bleach catalysts can particularly contribute to a significantly
improved cleaning result.
[0034] The above mentioned bleach boosting transition metal complexes, in particular with
the central atoms Mn and Co, are preferably employed in an amount of up to 5 wt.-%,
particularly from 0.0025 wt.-% to 1 wt.-% and particularly preferably from 0.01 wt.-%
to 0.30 wt.-%, each relative to the total weight of the compositions. However, in
special cases more bleach activator may also be employed.
[0035] A composition according to the invention further preferably comprises a hydrogen
peroxide source.
[0036] These sources concern compounds that supply, or can supply, H
2O
2 in water. The hydrogen peroxide source preferably concerns a bleaching agent, wherein
oxygen bleaching agents are preferred according to present invention.
[0037] Sodium percarbonate, sodium perborate tetrahydrate and sodium perborate monohydrate
are of particular importance among the compounds that serve as bleaching agents and
liberate H
2O
2 in water. Examples of additional bleaching agents that may be used are peroxypyrophosphates,
citrate perhydrates and H
2O
2-liberating peracidic salts or peracids, such as perbenzoates, peroxyphthalates, diperoxyazelaic
acid, phthaloimino peracid or diperoxydodecanedioic acid.
[0038] Moreover, bleaching agents from the group of the organic bleaching agents can also
be employed. Typical organic bleaching agents are the diacyl peroxides, such as e.g.
dibenzoyl peroxide. Further typical organic bleaching agents are the peroxy acids,
wherein the alkylperoxy acids and the arylperoxy acids may be named as examples.
[0039] The hydrogen peroxide source is preferably comprised in an amount of 2-30 wt.-% and
increasingly preferably in 4-25 wt.-%, in 5-20 wt.-% and particularly preferably in
6-15 wt.-% in the dishwashing composition according to the invention, each relative
to the total weight of the dishwashing composition. Preferred dishwashing compositions
are those wherein the dishwashing composition comprises, each relative to the total
weight of the dishwashing composition, 2 to 20 wt.-%, preferably 3 to 18 wt.-% and
particularly 4 to 15 wt.-% of sodium percarbonate.
[0040] Consequently, particularly preferred embodiments of the compositions according to
the invention are those, wherein the bleach catalyst is selected from the group of
the bleach boosting transition metal salts and transition metal complexes, preferably
from the group of the complexes of manganese with 1,4,7-trimethyl-1,4,7-triazacyclononane
Me-TACN) or 1,2,4,7-tetramethyl-1,4,7-triazacyclononane (Me/Me-TACN), and/or the hydrogen
peroxide source is sodium percarbonate, sodium perborate tetrahydrate or sodium perborate
monohydrate or a combination thereof. The bleach catalyst is quite particularly preferably
a complex of manganese with 1,4,7-trimethyl-1,4,7-triazacyclononane (Me-TACN), in
particular [Mn
IV2(µ-O)
3(Me-TACN)
2](PF
6)
2, or 1,2,4,7-tetramethyl-1,4,7-triazacyclononane (Me/Me-TACN) or a mixture therefrom,
and the hydrogen peroxide source sodium percarbonate. The bleach catalyst and the
hydrogen peroxide source in the cited combinations are each preferably present in
of the abovementioned quantities.
[0041] Compositions according to the invention, in particular automatic dishwashing compositions,
can further comprise bleach activators, for example in order to achieve an improved
bleach activity when cleaning at temperatures of 60° C and below. Bleach activators,
which can be employed, are compounds which, under perhydrolysis conditions, yield
aliphatic peroxycarboxylic acids having preferably 1 to 10 carbon atoms, in particular
2 to 4 carbon atoms, and/or optionally substituted perbenzoic acid. Substances, which
carry O-acyl and/or N-acyl groups of said number of carbon atoms and/or optionally
substituted benzoyl groups, are suitable. Polyacylated alkylenediamines are preferred,
tetraacetyl ethylenediamine (TAED) having proven to be particularly suitable.
[0042] These bleach activators, especially TAED, are preferably employed in amounts of 0.1-10
wt.-%, particularly 0.1-8 wt.-%, especially 2-8 wt.-% and particularly preferably
2-6 wt.-%, each relative to the total weight of the bleach activator-containing composition.
[0043] In a preferred embodiment of the invention, a dishwashing composition according to
the invention concerns an automatic dishwashing composition. In accordance with this
application, compositions are designated as automatic dishwashing compositions, which
can be employed in an automatic dishwashing process for cleaning soiled dishes. Thus
the automatic dishwashing compositions according to the invention differ for example
from the automatic rinsing agents that are always employed in combination with automatic
dishwashing compositions and develop no inherent cleaning action.
[0044] The compositions, in particular automatic dishwashing compositions, preferably comprise
builders as the essential component for the successful cleaning and rinsing. Firstly,
these builders increase the alkalinity of the cleaning liquor, wherein with an increasing
alkalinity fats and oils are emulsified and saponified, and secondly, reduce the water
hardness of the cleaning liquor by complexing the calcium ions contained in the aqueous
liquor.
[0045] In another embodiment of the invention, the compositions are in solid form. This
is understood to mean all solid presentation forms, for example powders, granulates
or extrudates.
[0046] A powdery composition according to the invention can exist for example as a free-flowing
powder, in particular with a bulk density of 300 g/1 to 1200 g/l, especially 500 g/1
to 900 g/1 or 600 g/1 to 850 g/l.
[0047] The compositions according to the invention, in particular the automatic dishwashing
compositions, are preferably in the form of a molded object, in particular a compacted
material, principally a tablet. For the molded object, however, it can also be a granulate
for example that is comprised in a bag or in a cast shape.
[0048] Compositions according to the invention can be presented as one-phase or multi-phase
products. Compositions, in particular automatic dishwashing compositions, in particular
with one, two, three or four phases, are preferred. Automatic dishwashing compositions
in the form of a prefabricated unit dose with two or more phases are particularly
preferred. In particular, tablets with two or more phases are particularly preferred,
for example two-layer tablets, in particular two-layer tablets with a recess and a
molded object in the recess.
[0049] Automatic dishwashing compositions according to the invention are preferably prefabricated
as unit doses. These unit doses preferably contain the necessary quantity of washing
or cleaning active substances for one cleaning cycle. Preferred unit doses weigh between
12 and 30 g, preferably between 14 and 26 g and especially between 15 and 22 g.
[0050] The volume of the abovementioned unit doses and their three-dimensional shape are
particularly preferably chosen such that the prefabricated units can be dosed by being
placed in the dosing chamber of a dishwasher. Consequently, the volume of the unit
dose is preferably between 10 and 35 ml, preferably between 12 and 30 ml and especially
between 15 and 25 ml. The automatic dishwashing compositions according to the invention,
in particular the prefabricated unit doses, have, in a preferred embodiment, a water-soluble
coating.
[0051] The manufacture of the solid compositions according to the invention presents no
difficulties and can be effected by known methods, for example by spray drying or
granulation, wherein enzymes and possible further heat-sensitive ingredients, such
as, for example bleaching agent are optionally subsequently added separately. For
manufacturing the inventive composition with an increased bulk density, particularly
in the range of 650 g/1 to 950 g/l, a preferred process is one with an extrusion step.
[0052] The manufacture of the molded body according to the invention, in particular in the
form of cleaning composition tablets, is preferably carried in a manner known to the
person skilled in the art by compressing particulate starting materials. To produce
the tablets, the premix is compacted in a so-called die between two punches to form
a solid core. This operation, which hereinafter is abbreviated to tableting, is divided
into four steps: metering, compaction (elastic deformation), plastic deformation,
and ejection. Rotary presses are preferably used for the tableting.
[0053] When tableting with rotary presses, it has been found advantageous to perform tableting
with minimal fluctuations in tablet weight. Fluctuations in tablet hardness can also
be reduced in this way. Minimal fluctuations in weight can be achieved in the following
manner:
- Using plastic inserts with small thickness tolerances
- Low rotational speed of the rotor
- Large feed shoe
- Matching the rpm of the feed shoe impeller to that of the rotor
- Feed shoe with constant powder height
- Decoupling the feed shoe from the powder drum.
[0054] The ingredients intended for tableting can be filled simultaneously into the die
in the form of a common particulate premix or filled sequentially in the form of individual,
separate powders or granulates or simultaneously into the die, wherein the dosing
of a prefabricated particulate premix is preferred.
[0055] In another preferred embodiment, compositions according to the invention, in particular
molded objects, comprise polyvinyl pyrrolidone particles. These particles facilitate
inter alia the disintegration of the molded objects and insofar act as disintegration
auxiliaries or tablet disintegrants. It has proven to be inventively particularly
advantageous to employ polyvinyl pyrrolidone particles with an average particle size
of 100 to 150 µm, in particular with an average particle size of 110 to 130 µm.
[0056] The term "average particle size" or "average size" in the context of the present
invention is understood to mean the volume average D50 particle size that can be measured
using conventional methods. The D50 volume average particle size is that point in
the particle size distribution, at which 50 vol % of the particles have a smaller
diameter and 50 vol % of the particles have a larger diameter. The average particle
size can be measured in particular with the help of dynamic light scattering, which
is usually carried out on dilute suspensions that comprise e.g. 0.01 to 1 wt.-% of
particles.
[0057] It is particularly preferred when the PVP particles not only exhibit an average particles
size of 100 to 150 µm, in particular 110 to 130 µm, but moreover that the particle
size of the added particles is preferably completely within the cited ranges. This
is ensured by employing particle size fractions with the cited particle sizes that
were obtained by a sieving method.
[0058] The PVP particles are comprised in the compositions according to the invention, in
particular in molded objects, preferably in an amount of 0.1 to 5 wt.-%, in particular
in an amount of 0.2 to 3 wt.-%, above all in an amount of 0.3 to 1.8 wt.-%.
[0059] The action of disintegrants generally consists in that their volume increases on
water ingress, wherein firstly they swell, secondly the release of gas can generate
a pressure that causes the tablet to disintegrate into smaller particles. In addition
to, or as an alternative to the PVP particles, other disintegrants, for example carbonate/citric
acid systems or carbonate in combination with other organic acids, synthetic polymers
or naturally occurring polymers or modified natural products such as cellulose and
starch and their derivatives as well as alginates or casein derivatives can also be
comprised in compositions according to the invention, in particular molded objects.
Furthermore, gas-evolving effervescent systems can also be employed as additional
disintegrants. Preferred effervescent systems consist of at least two ingredients
that react together to form a gas, for example alkali metal carbonate and/or -hydrogen
carbonate and an acidifying agent capable of releasing carbon dioxide from the alkali
metal salts in aqueous solution. One acidifying agent that releases carbon dioxide
from the alkali metal salts in aqueous solution is, for example, citric acid.
[0060] The additional disintegration auxiliaries, insofar as they are used, are preferably
employed in quantities of 0.1 to 10 wt.-%, advantageously from 0.2 to 5 wt.-% and
especially from 0.5 to 2 wt.-%, each relative to the total weight of the composition
containing the disintegration aid.
[0061] In another embodiment of the invention, the compositions, in particular the dishwashing
compositions are in the form of a liquid, gel or paste.
[0062] All liquid or free-flowing dosage forms can be used as the liquid composition. In
the context of the present application, "free-flowing" is understood to mean preparations
that are pourable and can have viscosities up to several 10 000 mPas. The viscosity
can be measured using standard methods (for example using a Brookfield-Viscosimeter
LVT-II at 20 rpm and 20° C, spindle 3) and is preferably in the range of 5 to 10 000
mPas. Preferred compositions have viscosities from 10 to 8000 mPas, particularly preferably
from 120 to 3000 mPas. In the context of the present invention, a liquid composition
can therefore also be in gel form or in paste form, it can be a homogenous solution
or suspension, it can be sprayable for example or can be packaged in other usual dosage
forms.
[0063] Liquid or pasty inventive compositions in the form of solutions in standard solvents
are generally prepared by a simple mixing of the ingredients, which can be added as
is or as a solution into an automatic mixer.
[0064] Therefore, embodiments of the present invention further include all solid, powdery,
liquid, gellified or pasty presentation forms of the compositions which can also optionally
consist of a plurality of phases as well as being in a compressed on non-compressed
form. A composition according to the invention can also be packaged in a container,
preferably an air-permeable container, from which the composition is released shortly
before use or during the cleaning procedure.
[0065] In another embodiment of the invention, a composition, in particular a dishwashing
composition, according to the invention additionally comprises another ingredient
that is selected from the group consisting of builder, surfactant, anionic polymer
as well as combinations hereof. In another embodiment of the invention, a dishwashing
composition according to the invention is essentially phosphate-free, i.e. contains
less than 0.05 wt.-% phosphate compounds or is free from phosphate compounds. Phosphate-free
dishwashing compositions according to the invention are particularly advantageous
with respect to environmental considerations.
[0066] The group of preferred builders includes in particular the citrates as well as the
carbonates and the organic co-builders. The term "citrate" hereby includes both citric
acid as well as its salts, in particular its alkali metal salts. Particularly preferred
dishwashing compositions according to the invention, in particular automatic dishwashing
compositions, comprise citric acid and citrate, preferably sodium citrate, in amounts
of 5 to 60 wt.-%, preferably 10 to 50 wt.-% and particularly 15 to 40 wt.-%.
[0067] Carbonate(s) and/or hydrogen carbonate(s), preferably alkali metal carbonate(s),
particularly preferably sodium carbonate, are particularly preferably added in quantities
of 5 to 50 wt.-%, preferably 10 to 40 wt.-% and especially 15 to 30 wt.-%, each relative
to the weight of the composition.
[0068] Polycarboxylates/polycarboxylic acids and phosphonates may be particularly mentioned
as the organic co-builders. These classes of substances are described below.
[0069] Useful organic builders are, for example, the polycarboxylic acids that can be used
in the form of the free acid and/or their sodium salts, polycarboxylic acids in this
context being understood to be carboxylic acids that carry more than one acid function.
These include, for example, adipic acid, succinic acid, glutaric acid, malic acid,
tartaric acid, maleic acid, fumaric acid, sugar acids, amino carboxylic acids, nitrilotriacetic
acid (NTA) and mixtures thereof. Besides their building effect, the free acids also
typically have the property of an acidifying component and hence also serve to establish
a relatively low and mild pH of the inventive compositions. Succinic acid, glutaric
acid, adipic acid, gluconic acid and any mixtures thereof are particularly to be mentioned
in this regard.
[0070] Besides the 1-hydroxyethane-1,1-diphosphonic acid, the phosphonate complexants include
a series of different compounds such as for example diethylenetriamine penta(methylene
phosphonic acid) (DTPMP). Hydroxyalkane phosphonates or amino alkane phosphonates
are particularly preferred according to the invention. Among the hydroxyalkane phosphonates,
1-hydroxyethane-1,1-diphosphonate (HEDP) is of particular importance as the cobuilder.
It is normally added as the sodium salt, the disodium salt reacting neutral and the
tetrasodium salt reacting alkaline (pH 9). Ethylenediamine tetramethylene phosphonate
(EDTMP), diethylenetriamine pentamethylene phosphonate (DTPMP) and their higher homologs
are preferably chosen as the aminoalkane phosphonates. They are preferably added in
the form of the neutral-reacting sodium salts, e.g. as the hexasodium salt of EDTMP
or as the hepta- and octasodium salt of DTPMP. Of the class of phosphonates, HEDP
is preferably used as the builder. The aminoalkane phosphonates additionally possess
a pronounced ability to complex heavy metals. Accordingly, it can be preferred, particularly
where the compositions also contain bleach, to use amino alkane phosphonates, particularly
DTPMP, or mixtures of the cited phosphonates.
[0071] In the context of this invention, a preferred composition, preferably a dishwashing
composition, in particular an automatic dishwashing composition, comprises one or
more phosphonate(s) from the group
- a) aminotrimethylene phosphonic acid (ATMP) and/or salts thereof;
- b) ethylenediamine tetra(methylene phosphonic acid) (EDTMP) and/or salts thereof;
- c) diethylenetriamine penta(methylene phosphonic acid) (DTPMP) and/or salts thereof;
- d) 1-hydroxyethane-1,1-diphosphonic acid (HEDP) and/or salts thereof;
- e) 2-phosphonobutane-1,2,4-tricarboxylic acid (PBTC) and/or salts thereof;
- f) hexamethylenediamine tetra(methylene phosphonic acid) (HDTMP) and/or salts thereof;
- g) nitrilotri(methylene phosphonic acid) (NTMP) and/or salts thereof.
[0072] Particularly preferred compositions, in particular automatic dishwashing compositions,
comprise 1-hydroxyethane-1,1-diphosphonic acid (HEDP) or diethylenetriamine penta(methylene
phosphonic acid) (DTMP) as the phosphonates.
[0073] The weight fraction of the phosphonates in the total weight of the compositions according
to the invention, in particular the automatic dishwashing composition, is advantageously
1 to 8 wt.-%, preferably 1.2 to 6 wt.-% and especially 1.5 to 4 wt.-%.
[0074] The compositions according to the invention, in particular the automatic dishwashing
compositions, can comprise one or more surfactants, wherein anionic surfactants, non-ionic
surfactants and their mixtures particularly come into question.
[0075] Those preferred anionic surfactants possess at least one sulfate or sulfonate group.
The anionic surfactant with at least one sulfate or sulfonate group is preferably
selected from fatty alcohol sulfates, alkane sulfonates and alkylbenzene sulfonates.
C12-C18 fatty alcohol sulfates (FAS), e.g. Sulfopon K 35 (Cognis, Germany), secondary
C13-C17 alkane sulfonates (SAS), e.g. Hostapur SAS 93 (Clariant, Germany), as well
as linear C8-C18 alkylbenzene sulfonates, in particular dodecylbenzene sulfonate (LAS)
are particularly preferred in this regard.
[0076] According to the invention, the terms "sulfate" and "sulfonate" also include, in
addition to the anionic compounds in question that are present in the form of salts,
the free acids, i.e. the corresponding alkyl sulfur acids or alkyl sulfonic acids.
[0077] The anionic surfactant containing at least one sulfate or sulfonate group is preferably
comprised in compositions according to the invention in an amount of 0.1 to 20 wt.-%,
particularly preferably 0.5 to 15 wt.-%, in particular 2.5 to 10 wt.-%.
[0078] All non-ionic surfactants known to the person skilled in the art can be used as the
non-ionic surfactants. Suitable exemplary non-ionic surfactants are alkyl glycosides
that satisfy the general Formula RO(G)x, in which R means a primary linear or methyl-branched,
particularly 2-methyl-branched, aliphatic group containing 8 to 22 and preferably
12 to 18 carbon atoms and G stands for a glycose unit containing 5 or 6 carbon atoms,
preferably glucose. The degree of oligomerization x, which defines the distribution
of monoglycosides and oligoglycosides, is any number between 1 and 10, preferably
x is 1.2 to 1.4.
[0079] Another class of preferred non-ionic surfactants which may be used, either as the
sole non-ionic surfactant or in combination with other non-ionic surfactants, are
alkoxylated, preferably ethoxylated or ethoxylated and propoxylated fatty acid alkyl
esters preferably containing 1 to 4 carbon atoms in the alkyl chain.
[0080] Non-ionic surfactants of the amine oxide type, for example N-cocoalkyl-N,N-dimethylamine
oxide and N-tallow alkyl-N,N-dihydroxyethylamine oxide, and the fatty acid alkanolamides
may also be suitable. The quantity in which these non-ionic surfactants are used is
preferably no more than the quantity in which the ethoxylated fatty alcohols are used
and, particularly no more than half that quantity.
[0081] Other suitable surfactants are polyhydroxyfatty acid amides corresponding to following
formula
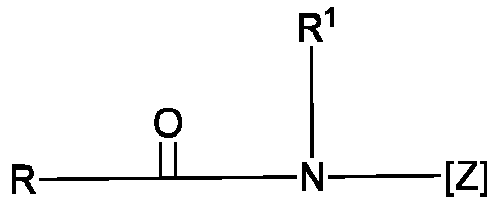
in which R stands for an aliphatic acyl residue with 6 to 22 carbon atoms, R
1 for hydrogen, an alkyl or hydroxyalkyl residue with 1 to 4 carbon atoms and [Z] for
a linear or branched polyhydroxyalkyl residue with 3 to 10 carbon atoms and 3 to 10
hydroxyl groups. The polyhydroxyfatty acid amides are known substances, which may
normally be obtained by reductive amination of a reducing sugar with ammonia, an alkylamine
or an alkanolamine and subsequent acylation with a fatty acid, a fatty acid alkyl
ester or a fatty acid chloride.
[0082] The group of the polyhydroxyfatty acid amides also includes compounds corresponding
to the following formula
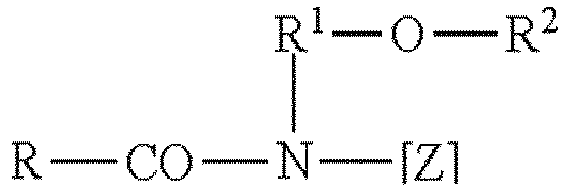
in which R is a linear or branched alkyl or alkenyl group containing 7 to 12 carbon
atoms, R
1 is a linear, branched or cyclic alkyl residue or an aryl residue containing 2 to
8 carbon atoms and R
2 is a linear, branched or cyclic alkyl residue or an aryl residue or an oxyalkyl residue
containing 1 to 8 carbon atoms, C1-4 alkyl- or phenyl residues being preferred, and
[Z] is a linear polyhydroxyalkyl residue, of which the alkyl chain is substituted
by at least two hydroxy groups, or alkoxylated, preferably ethoxylated or propoxylated
derivatives of that group.
[0083] [Z] is preferably obtained by reductive amination of a reducing sugar, for example
glucose, fructose, maltose, lactose, galactose, mannose or xylose. The N-alkoxy- or
N-aryloxy-substituted compounds may then be converted into the required polyhydroxyfatty
acid amides by reaction with fatty acid methyl esters in the presence of an alkoxide
as the catalyst.
[0084] The preferred surfactants are weakly foaming non-ionic surfactants. Compositions,
particularly cleaning compositions for dishwashing and among this preferably for automatic
dishwashers, are especially preferred when they comprise non-ionic surfactants from
the group of the alkoxylated alcohols. Preferred non-ionic surfactants are alkoxylated,
advantageously ethoxylated, particularly primary alcohols preferably containing 8
to 18 carbon atoms and, on average, 1 to 12 moles of ethylene oxide (EO) per mole
of alcohol, in which the alcohol group may be linear or, preferably, methyl-branched
in the 2-position or may contain e.g. linear and methyl-branched residues in the form
of the mixtures typically present in Oxo alcohol residues. Particularly preferred
are, however, alcohol ethoxylates with linear groups from alcohols of natural origin
with 12 to 18 carbon atoms, e.g. from coco-, palm-, tallow- or oleyl alcohol, and
an average of 2 to 8 EO per mole alcohol. Exemplary preferred ethoxylated alcohols
include C12-14 alcohols with 3 EO or 4 EO, C9-11 alcohols with 7 EO, C13-15 alcohols
with 3 EO, 5 EO or 7 EO, C12-18 alcohols with 3 EO, 5 EO or 7 EO and mixtures thereof,
such as mixtures of C12-14 alcohols with 3 EO and C12-18 alcohols with 5 EO. The cited
degrees of ethoxylation constitute statistically average values that can be a whole
or a fractional number for a specific product. Preferred alcohol ethoxylates have
a narrowed homolog distribution (narrow range ethoxylates, NRE). In addition to these
non-ionic surfactants, fatty alcohols with more than 12 EO can also be used. Examples
of these are tallow fatty alcohol with 14 EO, 25 EO, 30 EO or 40 EO.
[0085] Accordingly, ethoxylated non-ionic surfactant(s) prepared from C6-20 monohydroxy
alkanols or C6-20 alkylphenols or C12-20 fatty alcohols and more than 12 mole, preferably
more than 12 mole and especially more than 20 mole ethylene oxide per mole alcohol,
are used with particular preference. A particularly preferred non-ionic surfactant
is obtained from a straight-chain fatty alcohol containing 16 to 20 carbon atoms (C16-20
alcohol), preferably a C18 alcohol, and at least 12 moles, preferably at least 15
moles and more preferably at least 20 moles of ethylene oxide. Of these non-ionic
surfactants, the so-called narrow range ethoxylates are particularly preferred.
[0086] Moreover, surfactant(s) that comprise one or more tallow fat alcohols with 20 to
30 EO in combination with a silicone defoamer are particularly preferably used.
[0087] Non-ionic surfactants that have a melting point above room temperature are used with
particular preference. Non-ionic surfactant(s) with a melting point above 20° C, preferably
above 25° C, particularly preferably between 25 and 60° C and, especially between
26.6 and 43.3° C, are particularly preferred.
[0088] Suitable non-ionic surfactants with a melting and/or softening point in the cited
temperature range are, for example weakly foaming non-ionic surfactants that can be
solid or highly viscous at room temperature. If non-ionic surfactants are used that
are highly viscous at room temperature, then it is preferred that they have a viscosity
greater than 20 Pas, preferably above 35 Pas and especially above 40 Pas. Non-ionic
surfactants that have a waxy consistency at room temperature are also preferred.
[0089] Non-ionic surfactants from the group of the alkoxylated alcohols, particularly preferably
from the group of the mixed alkoxylated alcohols and especially from the group of
the EO-AO-EO-non-ionic surfactants are likewise incorporated with particular preference.
[0090] Preferably, the room temperature solid non-ionic surfactant additionally has propylene
oxide units in the molecule. These PO units preferably make up as much as 25% by weight,
more preferably as much as 20% by weight and, especially up to 15% by weight of the
total molecular weight of the non-ionic surfactant. Particularly preferred non-ionic
surfactants are ethoxylated monohydroxyalkanols or alkylphenols, which have additional
polyoxyethylene-polyoxypropylene block copolymer units. The alcohol or alkylphenol
component of these non-ionic surfactant molecules preferably makes up more than 30
wt.-%, more preferably more than 50 wt.-% and most preferably more than 70 wt.-% of
the total molecular weight of these non-ionic surfactants. Preferred compositions
are characterized in that they comprise ethoxylated and propoxylated non-ionic surfactants,
in which the propylene oxide units in the molecule preferably make up as much as 25%
by weight, more preferably as much as 20% by weight and, especially up to 15% by weight
of the total molecular weight of the non-ionic surfactant.
[0091] Preferred surfactants that are solid at room temperature are used and belong to the
groups of the alkoxylated non-ionic surfactants, more particularly the ethoxylated
primary alcohols, and mixtures of these surfactants with structurally more complex
surfactants, such as polyoxypropylene/polyoxyethylene/polyoxypropylene ((PO/EO/PO)
surfactants). Such (PO/EO/PO) non-ionic surfactants are moreover characterized as
having good foam control.
[0092] Other particularly preferred non-ionic surfactants with melting points above room
temperature comprise 40 to 70% of a polyoxypropylene/polyoxyethylene/polyoxypropylene
block polymer blend, which comprises 75% by weight of an inverted block copolymer
of polyoxyethylene and polyoxypropylene with 17 moles of ethylene oxide and 44 moles
of propylene oxide and 25% by weight of a block copolymer of polyoxyethylene and polyoxypropylene
initiated with trimethylol propane and comprising 24 moles of ethylene oxide and 99
moles of propylene oxide per mole of trimethylol propane.
[0093] Particularly preferred non-ionic surfactants in the context of the present invention
have proved to be weakly foaming non-ionic surfactants, which have alternating ethylene
oxide and alkylene oxide units. Among these, the surfactants with EO-AO-EO-AO blocks
are again preferred, wherein one to ten EO or AO groups respectively are linked together,
before a block of the other groups follows. Here, non-ionic surfactants of the general
formula

are preferred, in which R
1 stands for a linear or branched, saturated or a mono or polyunsaturated C
6-
24 alkyl or -alkenyl group, each group R
2 or R
3 independently of one another is selected from -CH
3, -CH
2CH
3, -CH
2CH
2-CH
3, CH(CH
3)
2, and the indices w, x, y, z independently of one another stand for whole numbers
from 1 to 6.
[0094] The preferred non-ionic surfactants of the previous formula can be manufactured by
known methods from the corresponding alcohols R1-OH and ethylene oxide or alkylene
oxide. The group R1 in the previous Formula can vary depending on the origin of the
alcohol. When natural sources are used, the group R1 has an even number of carbon
atoms and generally is not branched, the linear alcohols of natural origin with 12
to 18 carbon atoms, for example coconut, palm, tallow or oleyl alcohol being preferred.
The alcohols available from synthetic sources are, for example Guerbet alcohols or
mixtures of methyl branched in the 2-position or linear and methyl branched groups,
as are typically present in Oxo alcohols. Independently of the type of alcohol used
for the manufacture of the non-ionic surfactants comprised in the compositions, non-ionic
surfactants are preferred, in which R1 in the previous formula stands for an alkyl
group containing 6 to 24, preferably 8 to 20, particularly preferably 9 to 15 and
particularly 9 to 11 carbon atoms.
[0095] In addition to propylene oxide, especially butylene oxide can be the alkylene oxide
unit that alternates with the ethylene oxide unit in the preferred non-ionic surfactants.
However, also other alkylene oxides are suitable, in which R
2 or R
3 independently of one another are selected from - CH
2CH
2-CH
3 or CH(CH
3)
2. Preferably, non-ionic surfactants of the previous formula are used, in which R
2 or R
3 stand for a group -CH
3, w and x independently of one another stand for values of 3 or 4 and y and z independently
of one another stand for values of 1 or 2.
[0096] In summary, especially non-ionic surfactants are preferred that have a C9-15 alkyl
group with 1 to 4 ethylene oxide units, followed by 1 to 4 propylene oxide units,
followed by 1 to 4 ethylene oxide units, followed by 1 to 4 propylene oxide units.
These surfactants exhibit the required low viscosity in aqueous solution and according
to the invention are used with particular preference.
[0097] Surfactants of the general formula R1-CH(OH)CH
2O-(AO)
w-(A'O)
x-(A"O)
y-(A"'O)
z-R2, in which R1 and R2 independently of one another stands for a linear or branched,
saturated or unsaturated or mono- or polyunsaturated C2-40 alkyl or alkenyl residue;
A, A', A" and A"' independently of one another stands for a residue from the group
-CH
2CH
2, -CH
2CH
2-CH
2, -CH
2CH(CH
3), -CH
2CH
2-CH
2CH
2, -CH
2CH(CH
3)-CH
2-, -CH
2CH(CH
2-CH
3); and w, x, y and z stand for values between 0.5 and 90, wherein x, y and/or z can
also be 0, are preferred.
[0098] Particularly preferred non-ionic surfactants are of the general formula R1-O[CH
2CH(CH
3)O]
x[CH
2CH
2O]
y[CH
2CH(CH
3)O]
zCH
2CH(OH)R2, in which R1 stands for a linear or branched aliphatic hydrocarbon residue
with 4 to 22 carbon atoms, particularly 6 to 18 carbon atoms, or mixtures thereof,
R2 means a linear or branched hydrocarbon residue with 2 to 26 carbon atoms or mixtures
thereof and x and z stand for values between 0 and 40 and y stands for a value of
at least 15, preferably 15 to 120, particularly preferably from 20 to 80.
[0099] In a preferred embodiment, the compositions, in particular the automatic dishwashing
compositions, comprise, relative to its total weight, non-ionic surfactant of the
general formula R1-O[CH
2CH(CH
3)O]
x[CH
2CH
2O]
y[CH
2CH(CH
3)O]
zCH
2CH(OH)R2 in amounts of 0.1 to 15 wt.-%, preferably 0.2 to 10 wt.-%, particularly preferably
0.5 to 8 wt.-% and in particular from 1.0 to 6 wt.-%.
[0100] Those end-blocked poly(oxyalkylated) non-ionic surfactants according to the formula
R1-O[CH
2CH
2O]
yCH
2CH(OH)R2 are particularly preferred, in which R1 stands for a linear or branched aliphatic
hydrocarbon residue with 4 to 22 carbon atoms, particularly 6 to 18 carbon atoms,
or mixtures thereof, R2 means a linear or branched hydrocarbon residue with 2 to 26,
especially 4 to 20 carbon atoms or mixtures thereof and y stands for a value between
15 and 120, preferably 20 to 100, in particular 20 to 80. The group of these non-ionic
surfactants includes for example hydroxy mixed ethers of the general formula C
6-22CH(OH)CH
2O-(EO)
20-120-C
2-26, for example the C
8-12 fatty alcohol-(EO)
22-2-hydroxydecyl ethers and the C
4-22 fatty alcohol-(EO)
40-80-2-hydroxyalkyl ethers.
[0101] A composition according to the invention, in particular an automatic dishwashing
composition, wherein a surfactant is employed as the weakly foaming non-ionic surfactant
of the general Formula R1CH(OH)CH
2O-(CH
2CH
2O)
20-120-R2, wherein R1 and R2 independently of one another stand for a linear or branched
aliphatic hydrocarbon residue with 2 to 20, particularly 4 to 16 carbon atoms, are
particularly preferred.
[0102] Further preferred are surfactants of the formula R1-O[CH
2CH(CH
3)O]
x[CH
2CH
2O]
yCH
2CH(OH)R2, in which R1 stands for a linear or branched aliphatic hydrocarbon residue
with 4 to 22 carbon atoms or mixtures thereof, R2 means a linear or branched hydrocarbon
residue with 2 to 26 carbon atoms or mixtures thereof and x stands for values between
0.5 and 4, preferably 0.5 to 1.5, and y stands for a value of at least 15.
[0103] Further inventively preferred surfactants are also of the general formula R1-O[CH
2CH(CH
3)O]
x[CH
2CH
2O]
y[CH
2CH(OH)R2, in which R1 stands for a linear or branched aliphatic hydrocarbon group
with 4 to 22 carbon atoms or mixtures thereof, R2 means a linear or branched hydrocarbon
group with 2 to 26 carbon atoms or mixtures thereof and x stands for values between
1 and 40 and y stands for a value between 15 and 40, wherein the alkylene units [CH
2CH(CH
3)O] and [CH
2CH
2O] are randomized, i.e. exist in the form of a statistical, random distribution.
[0104] The group of the preferred end-capped poly(oxyalkylated) non-ionic surfactants also
includes non-ionic surfactants of the formula R1-O[CH
2CH
2O]
x[CH
2CH(R3)O]
yCH
2CH(OH)R2, in which R1 and R2 independently of one another stand for linear or branched,
saturated or mono or polyunsaturated hydrocarbon groups containing 2 to 26 carbon
atoms, R3 independently of one other is selected from -CH
3, -CH
2CH
3, -CH
2CH
2-CH
3, -CH(CH
3)
2, preferably, however, stands for-CH
3, and x and y independently of one another stand for values between 1 and 32, wherein
surfactants with R3 = -CH
3 and values for x of 15 to 32 and y of 0.5 and 1.5 are quite particularly preferred.
[0105] Further preferred non-ionic surfactants are the end-capped poly(oxyalkylated) non-ionic
surfactants corresponding to the formula
R1-O[CH
2CH(R3)O]
x[CH
2]
kCH(OH)[CH
2]
jOR2,
in which R1 and R2 stand for linear or branched, saturated or unsaturated, aliphatic
or aromatic hydrocarbon groups containing 1 to 30 carbon atoms, R3 stands for H or
for a methyl, ethyl, n-propyl, isopropyl, n-butyl, 2-butyl or 2-methyl-2-butyl group,
x for values between 1 and 30, k and j have values between 1 and 12, preferably between
1 and 5.
[0106] Each R3 in the above formula R1-O[CH
2CH(R3)O]
x[CH
2]
kCH(OH)[CH
2]
jOR2 can be different for the case where x≧2. R1 and R2 are preferably linear or branched,
saturated or unsaturated, aliphatic or aromatic hydrocarbon groups containing 6 to
22 carbon atoms, groups containing 8 to 18 carbon atoms being particularly preferred.
H, -CH
3 or -CH
2CH
3 are particularly preferred for the group R3. Particularly preferred values for x
are in the range from 1 to 20 and more particularly in the range from 6 to 15.
[0107] As described above, each R3 in the above formula can be different for the case where
x≧2. By this means, the alkylene oxide unit in the straight brackets can be varied.
If, for example, x has a value of 3, then the substituent R3 may be selected to form
ethylene oxide (R3=H) or propylene oxide (R3=CH3) units which may be joined together
in any order, for example (EO)(PO)(EO), (EO)(EO)(PO), (EO)(EO)(EO), (PO)(EO)(PO),
(PO)(PO)(EO) and (PO)(PO)(PO). The value 3 for x was selected by way of example and
may easily be larger, the range of variation increasing with increasing x-values and
including, for example, a large number of (EO) groups combined with a small number
of (PO) groups or vice versa.
[0108] Particularly preferred end-capped poly(oxyalkylated) alcohols corresponding to the
above formula have values for both k and j of 1, so that the above formula can be
simplified to
R1-O[CH
2CH(R3)O]
xCH
2CH(OH)CH
2OR2
[0109] In this last formula, R1, R2 and R3 are as defined above and x stands for numbers
from 1 to 30, preferably 1 to 20 and especially 6 to 18. Surfactants in which the
substituents R and R2 have 9 to 14 carbon atoms, R3 stands for H and x assumes values
of 6 to 15 are particularly preferred.
[0110] Further preferred non-ionic surfactants are non-ionic surfactants of the general
formula R1-O(AlkO)xM(OAlk)yOR2, wherein R1 and R2 independently of one another stand
for a branched or unbranched, saturated or unsaturated, optionally hydroxylated group
with 4 to 22 carbon atoms; Alk stands for a branched or unbranched alkyl group with
2 to 4 carbon atoms; x and y independently of one another stand for values between
1 and 70; and M stands for an alkyl group from the group CH
2, CHR3, CR3R4, CH
2CHR3 and CHR3CHR4, wherein R3 and R4 independently of one another stand for branched
or unbranched, saturated or unsaturated alkyl groups with 1 to 18 carbon atoms.
[0111] In this respect, non-ionic surfactants are preferred with the general formula
R1-CH(OH)CH
2-O(CH
2CH
2O)
xCH
2CHR(OCH
2CH
2)
yO-CH
2CH(OH)-R2,
wherein
R, R1 and R2 independently of each other stand for an alkyl group or alkenyl group
containing 6 to 22 carbon atoms;
x and y independently of one another stand for values between 1 and 40.
[0112] In this regard, particularly compounds of the general formula are preferred:
R1-CH(OH)CH
2-O(CH
2CH
2O)
xCH
2CHR(OCH
2CH
2)
yO-CH
2CH(OH)-R2,
[0113] in which R stands for a linear, saturated alkyl group with 8 to 16 carbon atoms,
preferably 10 to 14 carbon atoms and n and m independently of one another have values
of 20 to 30. Appropriate compounds can be obtained for example by treating alkyl diols
HO-CHR-CH2-OH with ethylene oxide, wherein subsequently the free OH functionalities
are treated with an alkyl epoxide to afford a dihydroxy ether.
[0114] In another preferred embodiment, the non-ionic surfactant is selected from non-ionic
surfactants of the general formula
R1-O(CH
2CH
2O)xCR3R4(OCH
2CH
2)
yO-R2,
in which
R1 and R2 independently of one another stand for an alkyl group or alkenyl group containing
4 to 22 carbon atoms;
R3 and R4 independently of one another stand for H or an alkyl group or alkenyl group
containing 1 to 18 carbon atoms and
x and y independently of one another stand for values between 1 and 40.
[0115] In this regard, particularly compounds of the general formula are preferred:
R1-O(CH
2CH
2O)xCR3R4(OCH
2CH
2)
yO-R2,
in which R3 and R4 stand for H and the indices x and y independently of one another
assume values of 1 to 40, preferably from 1 to 15.
[0116] In particular, particularly preferred compounds are of the general formula
R1-O(CH
2CH
2O)xCR3R4(OCH
2CH
2)
yO-R2,
in which the R1 and R2 groups independently of one another represent saturated alkyl
groups with 4 to 14 carbon atoms and the indices x and y independently of one another
assume values of 1 to 15 and especially 1 to 12.
[0117] Further preferred compounds are of the general formula
R1-O(CH
2CH
2O)xCR3R4(OCH
2CH
2)
yO-R2,
in which one of the R1 and R2 groups is branched.
[0118] Quite particularly preferred compounds are of the general formula
R1-O(CH
2CH
2O)
xCR3R4(OCH
2CH
2)
yO-R2,
in which the indices x and y independently of one another assume values from 8 to
12.
[0119] The cited carbon chain lengths and degrees of ethoxylation or alkoxylation of the
abovementioned non-ionic surfactants constitute statistically average values that
can be a whole or a fractional number for a specific product. Due to the manufacturing
processes, commercial products of the cited formulas do not consist in the main of
one sole representative, but rather are a mixture, wherein not only the carbon chain
lengths but also the degrees of ethoxylation or alkoxylation can be average values
and thus be fractional numbers.
[0120] Non-ionic surfactants that have a melting point above room temperature are particularly
preferred. Non-ionic surfactant(s) with a melting point above 20°C, preferably above
25°C, particularly preferably between 25 and 60°C and, especially between 26.6 and
43.3°C, is/are particularly preferred.
[0121] In a preferred embodiment, the weight fraction of the non-ionic surfactant in the
total weight of the composition according to the invention, particularly an automatic
dishwashing composition, is 0.1 to 20 wt.-%, particularly preferably 0.5 to 15 wt.-%,
in particular 2.5 to 10 wt.-%.
[0122] In a preferred embodiment, the wt.-% ratio of the anionic surfactant with at least
one sulfate or sulfonate group to the non-ionic surfactant is from 3:1 to 1:3, especially
2:1 to 1:2, particularly preferably 1.5:1 to 1:1.5.
[0123] In another embodiment of the invention, a composition according to the invention
further comprises at least one enzyme, in particular a protease, amylase, cellulase,
pectin-cleaving enzyme, hemicellulase, mannanase, tannase, xylanase, xanthanase, β-glucosidase,
carrageenase, perhydrolase, oxidase, oxidoreductase or a lipase, as well as combinations
hereof, in particular a combination that is selected from protease and amylase, protease
and lipase, protease and cellulase, protease and mannanase, amylase and lipase, amylase
and cellulase, amylase and mannanase, lipase and cellulase, lipase and mannanase,
lipase and cellulase, protease and amylase and lipase, protease and amylase and cellulase,
protease and amylase and mannanase, amylase and lipase and cellulase, amylase and
lipase and mannanase, lipase, cellulase and mannanase, protease and amylase and lipase
and cellulase, protease and amylase and cellulase and mannanase.
[0124] Enzymes of this type are each preferably comprised in the composition in a total
amount of 1×10
-8 to 5 wt.-% based on the active protein. Each additional enzyme is comprised with
increasing preference in compositions according to the invention in an amount of 1×10
-7 to 3 wt.-%, 0.00001 to 1 wt.-%, 0.00005 to 0.5 wt.-%, 0.0001 to 0.1 wt.-% and particularly
preferably 0.0001 to 0.05 wt.-%, based on active protein. In this regard, the active
protein concentration can be determined in a customary manner for hydrolases for example
by titrating the active centers in the presence of a suitable irreversible inhibitor
and measuring the residual activity (see for example
M. Bender et al., J. Am. Chem. Soc. 88, 24 (1966), pp. 5890-5913; the cited reference concerns proteases, wherein the principle of titration of the
active centers is transferable to other hydrolases). The enzymes particularly preferably
exhibit synergistic cleaning powers towards certain soils or stains, i.e. the enzymes
comprised in the composition mutually support each other in their cleaning power.
Such a synergy quite particularly preferably exists between the inventively comprised
protease and another enzyme of a composition according to the invention, in particular
between the inventively comprised protease and an amylase and/or a lipase and/or a
mannanase and/or a cellulase and/or a pectin-cleaving enzyme. Synergistic effects
can not only appear between various enzymes but also between one or more enzymes and
additional ingredients of the composition according to the invention.
[0125] Preferred proteases are those of the subtilisin type. Examples of these are subtilisins
BPN' and Carlsberg, the protease PB92, the subtilisins 147 and 309, the alkaline protease
from Bacillus lentus, subtilisin DY and those enzymes of the subtilases no longer
however classified in the stricter sense as subtilisins thermitase, proteinase K and
the proteases TW3 and TW7. Subtilisin Carlsberg in further developed form is available
under the trade name Alcalase® from Novozymes A/S, Bagsværd, Denmark. The subtilisins
147 and 309 are commercialized under the trade names Esperase® and Savinase® by the
Novozymes company. The protease variants sold under the name BLAP® are derived from
the protease from Bacillus lentus DSM 5483. Additional preferred proteases are furthermore
for example the enzymes sold under the name PUR. Additional proteases are furthermore
the enzymes available with the trade names Durazym®, Relase®, Everlase®, Nafizym®,
Natalase®, Kannase® and Ovozyme® from the Novozymes Company, those under the trade
names Purafect®, Purafect® OxP, Purafect® Prime, Excellase® and Properase® from Genencor,
that under the trade name Protosol® from Advanced Biochemicals Ltd., Thane, India,
that under the trade name Wuxi® from Wuxi Snyder Bioproducts Ltd., China, those under
the trade names Proleather® and Protease P® from Amano Pharmaceuticals Ltd., Nagoya,
Japan, and that under the designation Proteinase K-16 from Kao Corp., Tokyo, Japan.
The proteases from Bacillus gibsonii and Bacillus pumilus which are disclosed in the
international patent applications
WO2008/086916 and
WO2007/131656 are particularly preferably employed.
[0126] Examples of conditionable amylases according to the invention are the α-amylases
from Bacillus licheniformis, from Bacillus amyloliquefaciens or from Bacillus stearothermophilus,
as well as in particular their improved further developments for use in washing or
cleaning compositions. The enzyme from Bacillus licheniformis is available from the
Novozymes Company under the name Termamyl® and from the Danisco/Genencor Company under
the name Purastar®ST. Further development products of this α-amylase are available
from the Novozymes Company under the trade names Duramyl® and Termamyl® ultra, from
the Danisco/Genencor Company under the name Purastar® OxAm and from Daiwa Seiko Inc.,
Tokyo, Japan as Keistase®. The α-amylase from Bacillus amyloliquefaciens is commercialised
by the Novozymes Company under the name BAN®, and derived variants from the α-amylase
from Bacillus stearothermophilus under the names BSG® and Novamyl® also from the Novozymes
Company. Moreover, for this purpose, attention should be drawn to the α-amylase from
Bacillus sp. A 7-7 (DSM 12368) and the cyclodextrin-glucanotransferase (CGTase) from
Bacillus agaradherens (DSM 9948). Fusion products of all the cited molecules can also
be employed. Moreover, further developments of α-amylase from Aspergillus niger and
A. oryzae available from the Company Novozymes under the trade name Fungamyl® are
suitable. Additional commercial products that can be advantageously used are for example
the Amylase-LT® and Stainzyme® or Stainzyme ultra® or Stainzyme plus®, the last also
from the Novozymes company. Variants of these enzymes obtained by point mutations
can also be inventively employed. Particularly preferred amylases are disclosed in
the international applications
WO 00/60060,
WO 03/002711,
WO 03/054177 and
WO 07/079938, to which disclosures reference is therefore expressly made or in this regard their
disclosed content is therefore expressly incorporated into the present patent application.
Inventively conditionable amylases are moreover preferably α-amylases.
[0127] Exemplary inventively conditionable lipases or cutinases that are comprised in particular
due to their triglyceride-cleaving activities, but also to generate peracids in situ
from appropriate precursors, are the lipases that are originally obtainable from Humicola
lanuginose (Thermomyces lanuginosus) or further developed lipases, especially those
with the amino acid exchange D96L. They are commercialized, for example by the Novozymes
Company under the trade names Lipolase®, Lipolase® Ultra, LipoPrime®, Lipozyme® and
Lipex®.
[0128] Moreover, suitable cutinases, for example are those that were originally isolated
from Fusarium solani pisi and Humicola insolens. Suitable lipases or cutinases whose
starting enzymes were originally isolated from Pseudomonas mendocina and Fusarium
solanii are for example available from Genencor Company. Further important commercial
products that may be mentioned are the commercial preparations M1 Lipase® and Lipomax®
originally from Gist-Brocades Company, and the commercial enzymes from the Meito Sangyo
KK Company, Japan under the names Lipase MY-30®, Lipase OF® and Lipase PL® as well
as the product Lumafast® from the Genencor Company.
[0129] Inventively conditionable cellulases (endoglucanases, EG) include for example the
fungal, endoglucanase (EG)-rich cellulase preparation or its further developments
that are offered by the Novozymes Company under the trade name Celluzyme®. The products
Endolase® and Carezyme® based on the 50 kD-EG, respectively 43 kD-EG from Humicola
insolens DSM 1800 are also obtainable from the Novozymes Company. Additional employable
commercial products from this company are Cellusoft®, Renozyme® and Celluclean®. Cellulases,
for example, which are available under the trade names Ecostone® and Biotouch® from
AB Enzymes, Finland can also be used and which are at least partially based on the
20 kD-EG from Melanocarpus. Additional cellulases from the AB Enzymes Company are
Econase® and Ecopulp®. Further suitable cellulases are from Bacillus sp. CBS 670.93
and CBS 669.93, the CBS 670.93 from Bacillus sp. being available under the trade name
Puradax® from the Danisco/Genencor Company. Additional useable commercial products
of the Danisco/Genencor Company are "Genencor detergent cellulase L" and IndiAge®Neutra.
[0130] Variants of these enzymes obtained by point mutations can also be inventively employed.
Particularly preferred cellulases are Thielavia terrestris cellulase variants, which
are disclosed in the international application
WO 98/12307, cellulases from Melanocarpus, in particular Melanocarpus albomyces, which are disclosed
in the international application
WO 97/14804, cellulases of the EGIII type from Trichoderma reesei, which are disclosed in the
European patent application
EP 1 305 432 or variants that can be obtained from them, in particular those that are disclosed
in the European patent applications
EP 1240525 and
EP 1305432, as well as cellulases, which are disclosed in the international patent applications
WO 1992006165,
WO 96/29397 and
WO 02/099091. Reference is therefore expressly made to their respective disclosure or their disclosed
content in this regard is therefore expressly incorporated into the present patent
application.
[0131] In the context of the invention, pectin-cleaving enzymes (pectinases) are enzymes
that cleave pectin and/or other galacturonanes. Pections are polysaccharides, whose
major constituent is α-D-galacturonic acid as the monomer, preferably to at least
50 wt.-% and particularly preferably to at least 65 wt.-%. These galacturonic acid
monomers are linked together though α-1,4-, sometimes also with a minor fraction through
β-1,4-glycosidic bonds, and form the backbone of the pectin molecule that is periodically
interrupted by 1,2-bonds with α-L-rhamnose. Consequently, pectin is a rhamno-galacturonic
acid. Consequently, a pectin-cleaving enzyme is in particular an enzyme that catalyzes
the hydrolysis of 1,4-α-D-galactosiduronic bonds.
[0132] Within the EC Classification of enzymes, in the numerical classification system for
enzymes, the pectin-cleaving enzymes particularly belong to the enzyme classes (Enzyme
Commission number) EC 3.1.1.1 1, EC 3.2.1.15, EC 3.2.1.67 and EC 3.2.1.82, and consequently
fall into the third of the six major classes of enzymes, the hydrolases (E.C.3.-.-.-),
sub-classification glycosylases (E.C. 3.2.-.-) and again sub-classification glycosidases
(E.C. 3.2.1.-), i.e. enzymes that hydrolyse O- and/or S-glycosyl compounds. Consequently,
pectin-cleaving enzymes are effective particularly against residues on dishes which
comprise pectic acid and/or other galacturonanes, and catalyze their hydrolysis.
[0133] In the context of the present invention, the pectin-cleaving enzymes likewise include
enzymes with the names pectinase, pectolyase, pectinesterase, pectindemethoxylase,
pectinmethoxylase, pectinmethylesterase, pectase, pectinmethylesterase, pectinoesterase,
pectinpectylhydrolase, pectindepolymerase, endopolygalacturonase, pectolase, pectinhydrolase,
pectin-polygalacturonase, endo-polygalacturonase, poly-α-1,4-galacturonide glycanohydrolase,
endogalacturonase, endo-D-galacturonase, galacturan 1,4-α-galacturonidase, exopolygalacturonase,
poly(galacturonate) hydrolase, exo-D-galacturonase, exo-D-galacturonanase, exopoly-D-galacturonase,
exo-poly-α-galacturonosidase, exo-polygalacturonosidase or exopolygalacturanosidase.
[0134] Exemplary suitable enzymes are available for example under the names Gamanase®, Pektinex
AR®, X-Pect® or Pectaway® from Novozymes, under the name Rohapect UF®, Rohapect TPL®,
Rohapect PTE100®, Rohapect MPE®, Rohapect MA plus HC, Rohapect DA12L®, Rohapect 10L®,
Rohapect B1 L® from AB Enzymes and under the name Pyrolase® from Diversa Corp., San
Diego, Calif., USA.
[0135] Additional enzymes, which are summarized under the term hemicellulases, can also
be incorporated, especially for removing specific problematic soils. These include
for example mannanases, xanthanlyases, xanthanases, xyloglucanases, xylanases, pullulanases
and β-glucanases. β-Glucanase, extracted from Bacillus subtilis, is available under
the name Cereflo® from the Novozymes Company. Hemicellulases that are inventively
particularly preferred are mannanases, e.g. those that are marketed for example under
the trade names Mannaway® from the Novozymes Company or Purabrite® from the Genencor
Company.
[0136] To increase the bleaching action, a dishwashing composition according to the invention
can also comprise oxidoreductases, for example oxidases, oxygenases, catalases (that
react at lower H
2O
2 concentrations than peroxidase), peroxidases, such as halo-, chloro-, bromo-, lignin-,
glucose- or manganese-peroxidases, dioxygenases or laccases (phenoloxidases, polyphenoloxidases).
Suitable commercial products are Denilite® 1 and 2 from the Novozymes Company. For
an advantageously employable exemplary system for an enzymatic perhydrolysis, reference
may be made to the applications
WO 98/45398 A1,
WO 2005/056782 A2 and
WO 2004/058961 A1. A combined enzymatic bleach system, containing an oxidase and a perhydrolase, is
described in the application
WO 2005/124012. Additional, preferably organic, particularly preferably aromatic compounds are advantageously
added that interact with the enzymes to enhance the activity of the oxidoreductases
in question (enhancers) or to facilitate the electron flow (mediators) between the
oxidizing enzymes and the soils over strongly different redox potentials.
Examples
[0137] Example 1: Adsorption and retention of a polymer according to the present invention
(C1) in comparison with the commercially available polymer Mirapol Surf S 110.
[0138] The following monomers were used for the polymer according to the present invention:
A monomer of formula (I) with a number average molecular weight of 300 g/mol (75 mol%).
A monomer of formula (II) (R1=CH3, R2= CH2, R3 and R4 = H, X = O) (25 mol%).
[0139] The copolymer was obtained by reacting 0.08 mol of the above-mentioned monomer mixture,
0.8 mmol AIBN and 0.02 mmol mercapto acetic acid in 81 mL dry DMF after degassing
with nitrogen at 70 °C until complete conversion. The polymer was precipitated in
cold tert-butyl methyl ether. In a second step the phosphate groups were hydrolyzed
by dissolving the polymer in 73 mL anhydrous DCM and addition of 0.02 mol trimethyl
silyl bromide. The solution was stirred for 24 h at ambient temperature and 50 mL
methanol were added and stirred for another 3 h. The resulting polymer was precipitated
in cold hexane and dried under vacuum.
[0140] The resulting copolymer C1 had a number average molecular weight of 5.000 g/mol.
[0141] Solutions containing 0.3 wt.-% of the copolymer C1 or Mirapol Surf S 110 were obtained
by dissolving the polymer in water (16°dH, pH value 3). The obtained solutions were
tested for their adsorption value against steel (stainless steel) and SiO
2 via a quartz crystal microbalance (QCM). In the retention measurement the same solutions
without polymer were employed to rinse the adsorbates.
Results:
[0142] With the provision of a non-swollen solid polymer layer following values are calculated
for the layer thickness of the plateau of adsorption:
Copolymer C1: 4 nm (stainless steel), 4 nm (SiO2)
Mirapol Surf S 110: 2 nm (stainless steel), 1,5 nm (SiO2)
and for the plateau of retention:
Copolymer C1: 3,5 nm (stainless steel), 4 nm (SiO2)
Mirapol Surf S 110: 1,5 nm (stainless steel), 1 nm (SiO2)