Technical Field
[0001] The present invention relates to an elevator door control device and an elevator
door drive system using the same.
Background Art
[0002] An elevator door control device is mounted to a car side, and an open/close operation
of a door is controlled by sliding a door panel with a power of a motor.
[0003] The door panel is combined with an endless belt (for example, a V belt and a toothed
belt) or a steel wire rope wound around a pulley. When the belt or the steel wire
rope is driven with the power of the motor, the door panel also moves to slide right
and left.
[0004] The door panel is suspended from a door rail disposed on the top of a doorway of
the car. A door shoe disposed on a lower portion of the door panel slidably engages
with a groove of a sill (sill) on a car platform. The door panel is guided by the
door rail and the groove of the sill to slide in a constant direction without deviating
from the doorway.
[0005] While the car is landing floor, a landing door and a car door are engaged with one
another by engagement elements disposed on the respective doors. This drives the landing
door corresponding to driving of the car door, thus causing both doors to open and
close simultaneously.
[0006] In the open/close control of the door that includes the above-described mechanism,
both a speed following performance and a vibration suppression performance are required
at the same time. Since an inferior speed following performance causes a position
error corresponding to a speed error, the door fails to accurately move by a desired
distance corresponding to a speed command. Then, since a deceleration start position
of the door deviates from a predetermined position, the door collides against a door
open end or a door close end, or it takes a longer time for the door to move to the
door open end or the close door end. An inferior vibration suppression performance
causes the door to vibrate to cause a noise, or causes a resonance at a low frequency
to damage a mechanism part.
[0007] Since the speed following performance and the vibration suppression performance
have a trade-off relationship in an ordinary proportional-integral control (PI control),
it is necessary to adjust a control gain and a control command corresponding to a
door mechanism and its operation state for obtaining a desired performance.
[0008] For example, based on a weight of the door or a history of control data at the opening/closing
of the door, the control gain is changed (see PTL 1 and PTL 2), or a pattern of the
speed command is changed (see PTL 3).
[0009] For the open/close control of the door, safety is required. In this regard, by setting
a speed command value such that a kinetic energy at closing the door satisfies a reference
value, an impact when a passenger is caught in the door is reduced (see PTL 4).
Citation List
Patent Literature
[0010]
PTL 1: Japanese Patent Application Laid-Open No. 4-243791
PTL 2: Japanese Patent Application Laid-Open No. 2000-159461
PTL 3: Japanese Patent Application Laid-Open No. 2011-152973
PTL 4: Japanese Patent Application Laid-Open No. 2009-155086
Summary of Invention
Technical Problem
[0011] However, while the change of the control gain improves the speed following capability,
since a response frequency of a controller changes, an overlap of a resonance frequency
of the door mechanism with a response band of the controller causes the vibration
and the noise. Accordingly, the vibration suppression performance is not always satisfied.
[0012] Since the change of the speed command pattern changes the kinetic energy of the door,
the kinetic energy of the door increases depending on the changed pattern. Accordingly,
it becomes difficult to ensure the sufficient safety.
[0013] Simply setting the speed command value such that the kinetic energy satisfies the
reference value can ensure the sufficient safety, but providing both the speed following
performance and the vibration suppression performance at the same time is difficult.
[0014] Therefore, the present invention provides an elevator door control device configured
to provide a plurality of performances at the same time, and an elevator door drive
system using the same.
Solution to Problem
[0015] To solve the above-described problems, an elevator door control device according
to the present invention outputs a control command corresponding to a target command
for a door operation state. The control command is a command to drive a door mechanism
disposed on a car. The elevator door control device includes a controller and an optimal
controller. The controller generates the control command corresponding to a control
input. The optimal controller includes an evaluation index to evaluate the door operation
state and the control input together. The optimal controller computes the control
input to optimize the evaluation index and outputs the computed control input to the
controller.
[0016] To solve the above-described problems, an elevator door drive system according to
the present invention includes a door mechanism and a door control device. The door
mechanism includes a motor, a door driven to be opened and closed by the motor, and
an inverter that drives the motor. The door mechanism is disposed on a car. The door
control device outputs a control command corresponding to a target command for a door
operation state. The control command is provided to the inverter to drive the door
mechanism. The door control device includes a controller and an optimal controller.
The controller generates the control command corresponding to a control input. The
optimal controller includes an evaluation index to evaluate the door operation state
and the control input together. The optimal controller computes the control input
to optimize the evaluation index and outputs the computed control input to the controller.
Advantageous Effects of Invention
[0017] The present invention can provide a plurality of performances relating to a door
operation state at the same time.
[0018] Problems, configurations, and effects other than ones described above will be made
apparent from the following description of embodiments.
Brief Description of Drawings
[0019]
Figure 1 is an overall configuration diagram illustrating an elevator door control
device as Example 1.
Figure 2 illustrates an exemplary speed pattern.
Figure 3 illustrates an exemplary speed waveform of a door under a Model Predictive
Control in Example 1.
Figure 4 illustrates an exemplary speed waveform under an ordinary proportional-integral
control.
Figure 5 illustrates an exemplary acceleration waveform under the Model Predictive
Control in Example 1 and the proportional-integral control.
Figure 6 is an overall configuration diagram illustrating an elevator door control
device as Example 2.
Figure 7 illustrates a speed command and a speed waveform of a door under a Model
Predictive Control in Example 2.
Description of Embodiments
[0020] The following describes the embodiment of the present invention with Examples 1 and
2 below using the drawings. In the respective drawings, identical reference numerals
are attached to identical components or components having similar functions.
<Example 1>
[0021] Figure 1 is an overall configuration diagram illustrating an elevator door drive
system including a door control device (door control controller) as Example 1 of the
present invention.
[0022] In Figure 1, 103 is a car of an elevator that moves up and down between floors, and
components 101, 102, and 104 to 107 constitute a door mechanism of the car 103. 101
indicates a direct current power supply, 102 indicates a direct current capacitor
charged by the direct current power supply 101, 104 indicates a door motor that opens
and closes a door of the car 103, 105 indicates an inverter that drives the door motor
104, 106 indicates a motor current detector that detects a current flowing to the
door motor 104, and 107 indicates a rotary encoder that detects a rotation speed and
a rotator position of the door motor 104. In this Example 1, a permanent magnet synchronous
motor is applied as the door motor 104.
[0023] As the components of the door mechanism, in addition, for example, an endless belt,
with which a door panel is combined, driven by the door motor 104 is included, but
the door mechanism itself is configured with a known technique and its detailed description
is omitted.
[0024] In Figure 1, 108 to 117 indicate the components of the door controller that controls
the inverter 105. The components will be each described later.
[0025] By charging a DC power of the direct current power supply 101 to the direct current
capacitor 102, a DC input power having a constant voltage to the inverter 105 is obtained.
The DC input power is converted to an AC power by controlling the inverter 105 corresponding
to a control command output from the door control controller. This AC power output
from the inverter 105 rotates the door motor 104, thus controlling the opening and
closing of the door. In Example 1, the control command output from the door controller
is a Pulse Width Modulation (PWM) command to control ON/OFF power semiconductor switching
devices constituting a main circuit of the inverter 105. To the power semiconductor
switching devices, an insulated gate bipolar transistor (IGBT) and a junction bipolar
transistor are applicable.
[0026] Next, the door controller will be described.
[0027] As described in detail below, the door controller in Example 1 outputs the control
command, that is, the above-described PWM command to drive the door mechanism corresponding
to a speed command and an acceleration command as a target command for the door operation
state. Here, the PWM command is output from a current controller 108, and at this
time, a current command (motor current command value) as a control input to the current
controller 108 is generated with application of what is called an optimal control.
[0028] A motor current value detected by the motor current detector 106 is obtained by the
door control controller, and input to the current controller 108. The current controller
108 performs a vector control for controlling the permanent magnet synchronous motor,
and generates a dq-axis voltage command such that the detected motor current has a
desired current value provided by the current command. Furthermore, the current controller
108 converts the dq-axis voltage command to a three-phase voltage command by two-phase
to three-phase coordinate transformation, and outputs the PWM command generated based
on the three-phase voltage command to the power semiconductor switching devices in
the inverter 105.
[0029] The rotary encoder 107 outputs a pulse signal in synchronization with the rotation
of the door motor 104. The pulse signal is input to a speed detection unit 109. The
speed detection unit 109 detects the speed of the door motor 104 from an interval
of the input pulse signals, the number of pulses per unit time, and the like, and
outputs its speed information as a speed feedback value to an optimal controller 113.
[0030] An acceleration sensor 116 detects a door acceleration that indicates a vibration
state of the door. The detected acceleration is input to an acceleration detection
unit 117. The acceleration detection unit 117 performs D/A conversion of an analog
signal of the input acceleration to generate acceleration information, and outputs
the acceleration information as an acceleration feedback value to the optimal controller
113. To the acceleration sensor 116, for example, a three-axis acceleration sensor
using Micro Electro Mechanical Systems (MEMS) is applied.
[0031] While the speed and the acceleration are each performed with sensing in Example 1,
not limiting to this, for example, the speed information may be differentiated to
calculate the acceleration information, or the speed and the acceleration may be estimated
using an observer, a Kalman filter, and the like.
[0032] An acceleration command generation unit 110 generates a command value to a vibration
acceleration of the door, and outputs it to the optimal controller 113. Usually, for
reducing the vibration of the door, the command value is zero.
[0033] A speed command generation unit 111 generates the speed command, that is, a speed
pattern of the door, and outputs it to the optimal controller 113. An exemplary speed
pattern is illustrated in Figure 2. Figure 2 also illustrates a corresponding acceleration
pattern, that is, the acceleration in a door running direction.
[0034] As illustrated in Figure 2, the speed pattern at opening/closing the door is a low
speed at a start of door running and at a stop of the door, that is, open and close
ends of the door, and a maximum speed near the center of a frontage, that is, a door
running range. As illustrated in Figure 2, this speed pattern is a speed pattern of
what is called a hat (hat) type.
[0035] The optimal controller 113 (Figure 1) includes a door model 114 represented by an
equation of motion regarding a mechanism part of the door, and an optimizer 115 as
a solver for solving an optimal control problem. The optimal controller 113 generates
the current command by solving the optimal control problem based on the acceleration
command input from the acceleration command generation unit 110 and the speed pattern
(speed command) input from the speed command generation unit 111 such that the speed
feedback value detected by the speed detection unit 109 follows the speed command
and such that the acceleration feedback value detected by the acceleration detection
unit 117 follows the acceleration command to reduce the door vibration, and the optimal
controller 113 outputs the generated current command to the current controller 108.
[0036] In Example 1, the equation of motion of the door model 114 is expressed by what is
called a state equation that includes the speed and the acceleration as a state quantity.
Furthermore, the equation of motion includes a door driving force. Since the driving
force is provided by a torque of the door motor 104, the driving force depends on
the motor current flowing in the door motor 104. Therefore, in Example 1, the door
driving force is indicated with the current command output from the optimal controller
113 to the current controller 108, and the equation of motion includes the current
command.
[0037] Here, in the optimal controller 113, the speed and the acceleration as the door operation
state and the current command providing the door driving force are comprehensively
evaluated together with a predetermined evaluation index as described later. The optimal
controller 113 computes the current command to optimize the evaluation index, and
provides the computed current command as the control input to the current controller.
In Example 1, the evaluation index is represented by a predetermined function (evaluation
function).
[0038] Here, the speed and the acceleration to be evaluated are a speed response and an
acceleration response of the door mechanism, respectively, computed based on the door
model 114. To evaluate the following capability, in the evaluation index, a difference
between the speed command and the speed response and a difference between the acceleration
command and the acceleration response are defined as evaluation values. In Example
1, to ensure safety, kinetic energies of the door corresponding to the speed response
and the acceleration response are evaluated. Accordingly, the kinetic energy of the
door is also defined as the evaluation value in the evaluation index.
[0039] In Example 1, the evaluation index in the optimal control is represented by predetermined
functions (evaluation functions) having the above-described respective evaluation
values as variables.
[0040] Furthermore, in Example 1, the optimal controller 113 computes the speed response
and the acceleration response in the future for a predetermined time period from the
present time point (hereinafter referred to as a "prediction period") having the acceleration
feedback value and the speed feedback value output from the acceleration detection
unit 117 and the speed detection unit 109, respectively, at the present time point
as initial values using the door model 114. The optimal controller 113 computes the
evaluation value for each computed response, and uses the optimizer 115 to compute
the current command in the case where an integral value for the predetermined time
period in the prediction period becomes optimal (for example, minimum or maximum)
for the evaluation functions including the respective evaluation values including
the current command. Specific computing means will be described later.
[0041] A constraint condition storage unit 112 stores a constraint condition for the optimal
controller 113 to solve the optimal control problem. Accordingly, the optimal controller
113 reads the constraint condition from the constraint condition storage unit 112,
and executes the optimal control under the read constraint condition. The constraint
condition is, for example, "maximum value and minimum value of speed detection value",
"maximum value and minimum value of current command", "maximum value and minimum value
of inclination of current command", and "maximum value and minimum value of kinetic
energy of door". They are what is called the maximum/minimum value of input/output
and the maximum/minimum value of the inclination of input/output of the optimal controller
113.
[0042] In the optimal control problem, the state quantity (state equation) in the door model
114 may be configured as the constraint condition. For example, when an output part
(output equation) of the equation of motion of the door mechanism part includes the
speed at the door end, the state quantity of the speed at the door end can be configured
as the constraint condition. In this case, since the speed at the door end corresponds
to the kinetic energy of the door, the kinetic energy may be added to the output part
of the equation of motion to add the kinetic energy as a new state quantity to the
door model 114, thus using the deformed constraint condition.
[0043] The following describes the computing means in the optimal controller 113. First,
a description will be given along a general theory of the optimal control problem,
and next, the computing means applied to Example 1 will be described.
[0044] The optimal controller 113 solves the optimal control problem where obtaining a
state feedback control law in a range of a finite time period (prediction period)
is set as a problem, thus determining the output (current command). This control is
generally referred to as a "Model Predictive Control (abbreviated to MPC)" or a "receding
horizon control (abbreviated to RH control)". Here, the state equation of the door
is defined with a formula (1) as time-invariant.
[Math. 1]

[0045] x(t) is a state vector, and the speed, the acceleration, the kinetic energy, and
the like of the door are the state quantity. u(t) is a control input vector, and corresponds
to the current command and the torque command.
[0046] The door model represented by the formula (1) includes, for example, a model that
has one inertia including the motor to the door panel and a model where a spring or
a damper is used for the belt connected to the motor. The model to be applied is appropriately
selected depending on the required control performance (vibration control performance,
following performance, and the like). Typically, since a higher-order model is high
in control performance but high in calculation cost, the model is preferred to be
selected also in consideration of calculation cost.
[0047] In Example 1, regardless of the model to be applied, the kinetic energy of the door
is used for the constraint condition. This ensures opening/closing the door without
an excessive or an excessively low kinetic energy. Furthermore, by setting u(t) such
that a time integration of the evaluation value (for the door speed and the door acceleration,
differences between them and the command value) or a time integration of the evaluation
function including these evaluation values becomes minimum in a range of the constraint
condition, both the speed following capability and the vibration suppression performance
can be improved while the constraint condition is satisfied.
[0048] For the optimal control problem in the Model Predictive Control, it has been known
that an evaluation function J such as a formula (2) is made minimum for optimizing
a response of a system. In the formula (2), the first term of the right side and L
to be integrated are scalar value functions.
[Math. 2]

[0049] Here, t indicates a current time to be controlled, T indicates a length of an evaluation
section as a future time period to be evaluated, and the control input vector u(t)
to make J minimum is computed in this section. This ensures obtaining the optimal
control input up to a finite future time period.
[0050] For obtaining the control input vector u(t), a Hamiltonian H such as a formula (3)
is introduced.
[Math. 3]

[0051] It has been known that by introducing the Hamiltonian H of the formula (3), u(t)
can be obtained from formulas (5) to (7), which are derived from a stationary condition
of the first variation of the evaluation function J, and the state equation (formula
(4)).
[Math. 4]

[Math. 5]
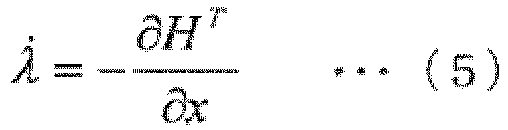
[Math. 6]

[Math. 7]
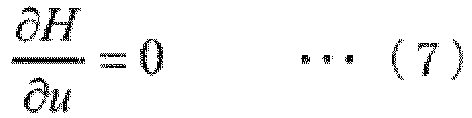
[0052] Here, λ is an adjoint variable vector, and µ is a Lagrange multiplier vector for
a fixed final state quantity. In the Model Predictive Control (MPC), an optimal control
input u
opt that makes the evaluation function J minimum can be obtained by solving the above-described
formulas in a numerical analysis manner having a state quantity x
0 as an initial value at each time. For the method for solving in a numerical analysis
manner, as indirect methods, Newton method, a steepest descent method, and the like
as gradient methods have been known. As direct methods, solutions where conversion
to a nonlinear programming problem is performed, and an active set method and an interior
point method are used have been known.
[0053] In Example 1, to provide both the speed following performance and the vibration
suppression performance at the same time, and simultaneously satisfy the constraint
condition (the kinetic energy), a quadratic form evaluation function J including a
plurality of evaluation values as a formula (8) is set. A formula (9) and a formula
(10) indicate the constraint conditions.
[Math. 8]

[Math. 9]

[Math. 10]

[0054] In the formula (8), v
d is the speed response, v
ref is the speed command value, a
d is the acceleration response, a
ref is the acceleration command value, u is a magnitude of the current command, and V
is the kinetic energy. w
1 to w
4 are weighting factors, and balances among the respective weights are adjusted through
analyses and tests.
[0055] The formula (9) indicates the maximum value and the minimum value of the current
command. The constraint condition of the formula (9) suppresses a rapid change of
the output. The formula (10) indicates the maximum value and the minimum value of
the kinetic energy. With the constraint condition of the formula (10), the kinetic
energy during the move of the door is controlled so as not to become excessive or
excessively low.
[0056] In the formula (8), the first term indicates a following error of the speed, and
the second term indicates a following error of the acceleration. Thus, including these
terms in the evaluation function provides both the speed following performance and
the vibration suppression performance at the same time.
[0057] As described above, using the formulas (3) to (7), the optimal control input u
opt (current command) that makes the evaluation function J of the formula (8) minimum
can be obtained in a numerical analysis manner. At this time, the above-described
computing for the prediction period is repeated at predetermined time intervals, and
u
opt is sequentially set by the computing at each time point.
[0058] Figure 3 illustrates an exemplary speed waveform of the door under the Model Predictive
Control in Example 1. In Figure 3, the speed command (the speed pattern) is also illustrated.
[0059] As illustrated in Figure 3, the shape of the speed waveform substantially matches
the speed pattern. Thus, Example 1 indicates the satisfactory speed following performance.
[0060] Figure 4 illustrates an exemplary speed waveform under an ordinary proportional-integral
control as a comparative example. In the exemplary waveform of Figure 4, different
from Example 1 (Figure 3), there is a deviation from the speed pattern near the peak
of the speed and the like.
[0061] Figure 5 illustrates an exemplary acceleration waveform of the door under the Model
Predictive Control (MPC) and the proportional-integral control (PI control) in Example
1.
[0062] As illustrated in Figure 5, with the Model Predictive Control (MPC) in Example 1,
the door vibration can be reduced while the satisfactory speed following capability
is ensured (Figure 3).
[0063] As described above, according to Example 1, since the current command is set through
the optimal control where the speed and the acceleration of the door are evaluated
together, the speed following capability and the vibration suppression performance
can be provided at the same time. Since the kinetic energy of the door is evaluated
under the constraint condition, the safety is ensured even when a passenger touches
the door, and energy saving is improved.
[0064] Since, in Example 1, the plurality of control performances (speed following capability,
vibration suppression) and the kinetic energy of the door are collectively evaluated
with one evaluation function, this can eliminate the need for complexly adjusting
a control gain or redesigning the control system for balancing the plurality of control
performances and the kinetic energy.
[0065] It is possible that, as Example 1, a current command pattern is preliminarily obtained
by solving the optimal control problem for the predetermined speed pattern as illustrated
in Figure 2 without the sequential computing, and the inverter 105 is controlled corresponding
to the obtained current command pattern.
<Example 2>
[0066] Figure 6 is an overall configuration diagram illustrating an elevator door drive
system including a door control device (door controller) as Example 2 of the present
invention. The following mainly describes differences from Example 1.
[0067] In Example 2, a position pattern (position command) generated by a position command
generation unit 201 is input to the optimal controller 113. A position detection unit
203 integrates the speed information output from the speed detection unit 109 to compute
a position (movement distance) of the door (or the motor). The position information
to be computed is input as the position feedback value to the optimal controller 113.
[0068] The optimal controller 113 generates the speed command by solving the optimal control
problem based on the position command and the acceleration command generated by the
acceleration command generation unit 110 such that the position feedback value follows
the position command and the acceleration as the state quantity in the door model
114 follows the acceleration command to reduce the door vibration, and the optimal
controller 113 outputs the speed command to a speed controller 202.
[0069] In Example 2, a controller that generates the PWM command includes the current controller
108 and the speed controller 202. The speed controller 202 generates the current command
through the proportional-integral control and the like such that speed information
feedback value follows the speed command based on the speed command input from the
optimal controller 113 and the speed information feedback value fed back from the
speed detection unit 109, and the speed controller 202 outputs the current command
to the current controller 108. The current controller 108, similarly to Example 1,
generates the PWM command such that the detected motor current has a desired current
value provided by the current command.
[0070] In Example 2, the optimal controller 113 evaluates the position, the acceleration,
the speed command, and the kinetic energy of the door with the evaluation index. Here,
the position and the acceleration to be evaluated are a position response of the door
mechanism and an acceleration as the state quantity, respectively, computed with the
door model 114.
[0071] In Example 2, the optimal controller 113 computes the speed command as an evaluation
index that makes the evaluation function J as a formula (11) minimum. This ensures
obtaining the speed pattern for the fastest opening/closing in the range of the constraint
condition while the door vibration is reduced.
[Math. 11]

[0072] In the formula (11), p
d is the position response, p
ref is a position command value, a
d is an acceleration value as the state quantity, a
ref is the acceleration command value, u is a magnitude of the control input (speed command)
from the optimal controller 113 to the speed controller 202, and V is the kinetic
energy of the door. w
1 to w
4 are weighting factors, and balances among the respective weights are adjusted through
analyses and tests.
[0073] Also, in Example 2, the constraint conditions are represented by the formula (9)
and the formula (10). However, the formula (9) represents the maximum value and the
minimum value of the speed command.
[0074] In the formula (11), the first term indicates a following error of the position,
and the second term indicates a following error of the acceleration. Thus, including
these terms in the evaluation function provides both the position following performance
and the vibration suppression performance at the same time, and making the following
error of the position minimum generates the speed pattern to open/close the door in
the shortest time under the constraint condition.
[0075] Figure 7 illustrates the speed command (speed pattern) and the speed waveform of
the door under a Model Predictive Control in Example 2. In Figure 7, the position
pattern (position command) generated by the position command generation unit 201 is
also illustrated.
[0076] Figure 7 illustrates the speed pattern and the speed waveform during the door opening.
At the door start, to reduce the noise of the door engaging portion, a position A
where engagement elements of the doors on the car side and the landing side mutually
contact is set as the position command, and subsequently, the door open end position
B is set as the position command.
[0077] As illustrated in Figure 7, the speed pattern generated in Example 2 has a shape
different from that of the speed pattern illustrated in Figure 2 to make the opening/closing
time of the door shortest.
[0078] Usually, the opening/closing of the door is often controlled by a speed control system,
and the speed pattern as illustrated in Figure 2 is applied. The speed pattern of
Figure 2 has a low speed period near the open end and the close end, and a high speed
period in the center between both ends. The low speed period is disposed in consideration
of noise reduction at the start of opening/closing and reduction of impact force that
the door receives. The shape of the speed pattern as Figure 2 is empirically obtained.
However, the speed pattern as Figure 2 does not necessarily make the opening/closing
time shortest. In contrast, in Example 2, solving the optimal control problem provides
the shape of the speed pattern that makes the opening/closing speed shortest.
[0079] As described above, according to Example 2, since the speed command is set through
the optimal control where the position and the acceleration of the door are evaluated
together, the door can be opened/closed at the fastest speed while the position following
capability and the vibration suppression performance are provided at the same time.
Since the kinetic energy of the door is evaluated under the constraint condition,
the safety is ensured even when a passenger touches the door, and energy saving is
improved.
[0080] Since, in Example 2, the plurality of control performances (position following capability,
vibration suppression) and the kinetic energy of the door are collectively evaluated
with one evaluation function, this can eliminate the need for complexly adjusting
a control gain or redesigning the control system for balancing the plurality of control
performances and the kinetic energy.
[0081] It is possible that, as Example 2, a speed command pattern is preliminarily obtained
by solving the optimal control problem for the position pattern as illustrated in
Figure 7 without the sequential computing, and the inverter 105 is controlled corresponding
to the obtained speed command pattern.
[0082] The present invention is not limited to the above-described examples and includes
various modifications. For example, the above-described examples have been described
in detail in order to easily understand the present invention, and therefore, it is
not necessarily limited to include all the described configurations. Some of the configurations
of each example can be added to, deleted from, or replaced by other configurations.
[0083] For example, the door may be any of a single slide type and a double slide type.
The number of the door panels to be opened/closed may be any number. The driving force
of the door motor may be transmitted to the door via a link mechanism. The model of
the door mechanism is not limited to the equation of state, but may be represented
by a differential equation and the like.
Reference Signs List
[0084]
- 101...
- direct current power supply,
- 102...
- direct current capacitor,
- 103...
- car,
- 104...
- door motor,
- 105...
- inverter,
- 106...
- motor current detector,
- 107...
- rotary encoder,
- 108...
- current controller,
- 109...
- speed detection unit,
- 110...
- acceleration command generation unit,
- 111...
- speed command generation unit,
- 112...
- constraint condition storage unit,
- 113...
- optimal controller,
- 114...
- door model,
- 115...
- optimizer,
- 116...
- acceleration sensor,
- 117...
- acceleration detection unit,
- 201...
- position command generation unit,
- 202...
- speed controller,
- 203...
- position detection unit
1. An elevator door control device that outputs a control command corresponding to a
target command for a door operation state, the control command being a command to
drive a door mechanism disposed on a car, the elevator door control device comprising:
a controller that generates the control command corresponding to a control input;
and
an optimal controller that has an evaluation index to evaluate the door operation
state and the control input together, and the optimal controller computing the control
input to optimize the evaluation index and outputting the computed control input to
the controller.
2. The elevator door control device according to claim 1,
wherein the optimal controller has a model of the door mechanism, and computes the
door operation state based on the model, and
wherein the optimal controller computes the control input to optimize the evaluation
index based on the computed door operation state.
3. The elevator door control device according to claim 2,
wherein the optimal controller computes the door operation state in a prediction section
from a current time to a predetermined time based on the model, and computes the control
input to optimize the evaluation index in the prediction section based on the computed
door operation state.
4. The elevator door control device according to claim 3, comprising a detection unit
that detects the door operation state of the door mechanism,
wherein the optimal controller computes the door operation state having a feedback
value of the door operation state from the detection unit as an initial value.
5. The elevator door control device according to claim 3,
wherein the optimal controller computes the control input under a predetermined constraint
condition.
6. The elevator door control device according to claim 5,
wherein the constraint condition is a kinetic energy of a door, and
the evaluation index evaluates the kinetic energy with the door operation state and
the control input.
7. The elevator door control device according to claim 3,
wherein the evaluation index evaluates the door operation state based on a difference
between the door operation state and the target command.
8. The elevator door control device according to claim 1,
wherein the evaluation index is an integral of a function that includes the door operation
state and the control input as variables, and
the optimal controller computes the control input that makes the integral minimum.
9. The elevator door control device according to claim 3,
wherein the evaluation index is an integral of a function that includes the door operation
state and the control input as variables, and
the optimal controller computes the control input that makes the integral in the prediction
section minimum.
10. The elevator door control device according to claim 8 or 9,
wherein the function has a quadratic form.
11. The elevator door control device according to claim 1 or 3,
wherein the door operation state includes a door acceleration of the door mechanism.
12. The elevator door control device according to claim 1 or 3,
wherein the door operation state is a speed and an acceleration of the door of the
door mechanism, and
the control input is a current command.
13. The elevator door control device according to claim 1 or 3,
wherein the door operation state is a position and an acceleration of the door of
the door mechanism, and
the control input is a speed command.
14. An elevator door drive system comprising:
a door mechanism that includes a motor, a door driven to be opened and closed by the
motor, and an inverter that drives the motor, the door mechanism disposed on a car;
and
a door control device that outputs a control command corresponding to a target command
for a door operation state, the control command being provided to the inverter to
drive the door mechanism,
wherein the door control device includes:
a controller that generates the control command corresponding to a control input;
and
an optimal controller that has an evaluation index to evaluate the door operation
state and the control input together, and the optimal controller computing the control
input to optimize the evaluation index and outputting the computed control input to
the controller.
15. The elevator door drive system according to claim 14,
wherein the optimal controller has a model of the door mechanism, and computes the
door operation state in a prediction section from a current time to a predetermined
time based on the model, and
wherein the optimal controller computes the control input to optimize the evaluation
index in the prediction section based on the computed door operation state.