[0001] The present invention concerns the field of laundry washing techniques.
[0002] In particular, the present invention refers to a method for detecting foam in a laundry
washing machine during a washing cycle.
[0003] Further, the present invention relates to a corresponding laundry washing machine.
BACKGROUND ART
[0004] Nowadays the use of laundry washing machines, both "simple" laundry washing machines
(i.e. laundry washing machines which can only wash and rinse laundry) and laundry
washing-drying machines (i.e. laundry washing machines which can also dry laundry),
is widespread.
[0005] In the present description the term "laundry washing machine" will refer to both
simple laundry washing machines and laundry washing-drying machines.
[0006] Laundry washing machines generally comprise an external casing, or cabinet, provided
with a washing tub which contains a rotatable perforated washing drum where the laundry
is placed. A loading/unloading door ensures access to the washing drum.
[0007] Laundry washing machines typically comprise a water inlet circuit and a products
supply unit for the introduction of water and washing/rinsing products (i.e. detergent,
softener, etc.) into the washing tub.
[0008] Known laundry washing machines are also provided with a draining system for draining
washing liquid from the washing tub. The draining system typically comprises at least
one draining pump, arranged at the bottom of the washing tub, which is operated when
necessary during the washing cycle.
[0009] Usually the draining system drains the washing liquid out of the laundry washing
machine and/or it recirculates the same inside the tub so that the washing liquid
is conveyed again on the laundry.
[0010] According to the known technique, a complete washing cycle typically includes different
phases, or steps, during which the laundry to be washed is subjected to adequate treatments.
[0011] A washing cycle usually comprises an initial phase wherein a proper amount of water
and detergent is introduced in the washing tub which creates the washing liquid for
wetting the laundry.
[0012] The washing cycle then typically comprises a main washing phase during which the
washing drum is rotated and the washing liquid contained therein is heated, typically
by means of an electrical resistor, to a predetermined temperature according to the
washing program selected by the user.
[0013] Successive steps of the washing cycle may comprise rinsing phases with introduction
of clean water and draining steps and a final spinning in which the washing drum is
rotated at high speed and the liquid in the washing tub is drained from the machine.
[0014] When the washing liquid is moved/agitated by the rotating washing drum a certain
amount of foam is typically generated. In particular an high amount of foam can be
very negative during the spinning and draining phase of the washing cycle since the
foam compromises a correct functioning of the drain pump and it obstructs the draining
of the liquid from the machine. The drain pump in presence of foam, then, are noisy.
[0015] Foam is typically generated in the washing cycle due to overdosage of detergent by
the user or due to foaming agents of the detergent itself that facilitates formation
of foam.
[0016] Furthermore, excessive foam may cause overflow involving liquid spillage.
[0017] Some known methods for operating a laundry washing machine are known, for example
as disclosed in
WO2015036166, in which foam is effectively detect and, if necessary, actions for reducing the
amount of foam inside the washing tub and/or in the draining region are taken. The
detection and reduction of foam is carried out in the balancing phase and/or the spinning
phase, i.e. after the main washing phase.
[0018] Nevertheless, already during the initial phases and/or the main washing phase a certain
amount of foam may be generated. If too much foam is generated at such an early stage
of the washing cycle then some phases of the washing cycle cannot be faultlessly performed.
[0019] In particular, for the same reason stated above, an high amount of foam can be very
negative during the spinning and draining phase of the washing cycle, in particular
with reference to the functioning of the pump.
[0020] Furthermore, an high amount of foam can be very negative during the main washing
itself, since the washing efficiency of the washing liquid is notably reduced with
respect normal conditions without foam.
[0021] Foam may also cause detergent accumulation on the laundry. The presence of a quantity
of residual detergent may cause insufficient rinsing. Insufficient rinsing can leave
enough detergent in laundry to affect people with allergies or sensitivity.
[0022] Document
JP 2012 170696 A discloses foam detections performed during several initial washing phases, such as
the water charge and the tumbling of the laundry; each detection is done through the
measure of the water level inside the tub and the subsequent estimation of a water
level abnormality.
[0023] A known method for the detection of foam in a laundry washing machine is known from
EP 1731656 A2. Here, a foam sensor is realized integral with a temperature sensor. However, the
device known from this document is complex.
[0024] This negatively affects size and/or manufacturing costs of the laundry washing machine
and also reliability of the same.
[0025] The object of the present invention is therefore to overcome the drawbacks posed
by the known technique.
[0026] It is a first object of the invention to provide a laundry washing machine that makes
it possible to detect, if necessary, the presence of foam at an early stage of the
washing cycle.
[0027] It is another first object of the invention to provide a laundry washing machine
that makes it possible to reduce residual of detergent on the laundry.
[0028] It is another object of the invention to provide a laundry washing machine which
detects, if necessary, the presence of foam having reduced complexity and/or size
compared to laundry washing machines of known type.
[0029] It is a further object of the invention to provide a laundry washing machine which
detects, if necessary, the presence of foam and having higher reliability compared
to laundry washing machines of known type.
DISCLOSURE OF INVENTION
[0030] The applicant has found that by determining the difference of the liquid level in
a tub of a laundry washing machine between a phase wherein a recirculation pump if
deactivated and a phase wherein the recirculation pump if activated it is possible
to establish the presence of foam in the washing tub.
[0031] The present invention relates, therefore, to a method for determining the presence
of foam in a laundry washing machine during a washing cycle, said laundry washing
machine comprising a washing tub containing a washing drum, a recirculation circuit
comprising a recirculation pump for draining liquid from the bottom of said washing
tub and to re-admit such liquid into an another part of said washing tub, a liquid
level sensor for detecting the liquid level in said washing tub, said washing cycle
comprising at least one phase of introducing a quantity of water and a quantity of
detergent in said washing tub to form a washing liquid, wherein after said at least
one phase of introducing a quantity of water and a quantity of detergent said method
comprises the steps of:
- performing a steady phase wherein said recirculation pump is deactivated and a recirculation
phase wherein said recirculation pump is activated:
- detecting a first level of said washing liquid in said washing tub during said steady
phase;
- detecting a second level of said washing liquid in said washing tub during said recirculation
phase;
- determining the level difference between said second level and said first level;
- comparing the determined level difference with a threshold value and if the determined
level difference is below said threshold value establishing the presence of foam.
[0032] According to a preferred embodiment of the invention, the recirculation phase is
performed after the steady phase.
[0033] In a preferred embodiment of the invention, during the steady phase and/or the recirculation
phase, the washing drum is kept motionless.
[0034] According to a preferred embodiment of the invention, the first level is detected
in a predetermined first monitoring period.
[0035] Preferably, the predetermined first monitoring period corresponds to the time duration
of the steady phase.
[0036] According to a preferred embodiment of the invention, the second level is detected
in a predetermined second monitoring period.
[0037] Preferably, the predetermined second monitoring period corresponds to the time duration
of the recirculation phase.
[0038] In a preferred embodiment of the invention, the first level is the average first
level in the predetermined first monitoring period.
[0039] In a preferred embodiment of the invention, the second level is the average second
level in the predetermined second monitoring period.
[0040] According to a preferred embodiment of the invention, the threshold value is between
2 mm and 12 mm, preferably between 4 mm and 10 mm, more preferably equal to 5 mm.
[0041] According to a preferred embodiment of the invention, if presence of foam has been
established then at least one foam reduction action is taken.
[0042] Preferably, the foam reduction action comprises one of the following actions:
- the time reduction of the main washing step with respect to the expected time of the
main washing step for the washing cycle;
- the reduction of the activation time of the heating device with respect to the expected
activation time of the same for the main washing step of the selected cycle;
- the deactivation of a heating device of said laundry washing machine;
- the deactivation of a heating device of said laundry washing machine for a predetermined
time;
- the variation of the washing drum rhythm with respect to the expected rotation time
for the main washing step of the selected cycle;
- the introduction of one or more additional rinsing steps with respect to the expected
rinsing steps for the selected cycle;
- the introduction of a further quantity of water during the main washing step;
- the reduction of the activation time of said recirculation pump with respect to the
expected activation time for the selected cycle;
- the complete deactivation of said recirculation pump.
[0043] Preferably, the foam reduction action comprises sending a warning alarm for the user,
preferably a visual alarm or an acoustic alarm.
[0044] In a further aspect thereof the present invention relates to a laundry washing machine,
wherein the laundry washing machine is provided for the methods described above.
BRIEF DESCRIPTION OF THE DRAWINGS
[0045] Further characteristics and advantages of the present invention will be highlighted
in greater detail in the following detailed description of preferred embodiments of
the invention, provided with reference to the enclosed drawings. In the drawings,
corresponding characteristics and/or components are identified by the same reference
numbers. In such drawings:
- Figure 1 illustrates a perspective view of a laundry washing machine according to
a preferred embodiment of the present invention;
- Figure 2 illustrates a schematic sectional front view of the laundry washing machine
according to the preferred embodiment of the present invention;
- Figure 3 illustrates a schematic flow chart diagram of a method for operating a laundry
washing machine during a washing cycle according to a preferred embodiment of the
present invention;
- Figure 4A illustrates a schematic flow chart diagram of a phase of the method of Figure
3;
- Figure 4B illustrates an alternative schematic flow chart diagram of a phase of the
method of Figure 3;
- Figures 5 to 8 show further preferred embodiments of Figure 3.
DETAILED DESCRIPTION OF THE INVENTION
[0046] The present invention has proved to be particularly advantageous when applied to
laundry washing machines, as described below. It should in any case be underlined
that the present invention is not limited to laundry washing machines. On the contrary,
the present invention can be conveniently applied to laundry washing-drying machines
(i.e. laundry washing machines which can also dry laundry).
[0047] In the present description, therefore, the term "laundry washing machine" will refer
to both simple laundry washing machines and laundry washing-drying machines.
[0048] With reference to Figures 1 and 2 a laundry washing machine 1 according to a preferred
embodiment of the invention is described.
[0049] The laundry washing machine 1 comprises an external casing or cabinet 2, in which
a washing tub 3 is provided that contains a perforated washing drum 4 where the laundry
to be treated can be loaded.
[0050] The cabinet 2 is provided with a front loading/unloading door 8 which allows access
to the washing tub 3 and the washing drum 4.
[0051] The washing tub 3 is preferably suspended in a floating manner inside the cabinet
2, advantageously by means of a number of coil springs and shock-absorbers that are
not illustrated herein.
[0052] The washing drum 4 is advantageously rotated by an electric motor, not visible, which
preferably transmits the rotating motion to the shaft of the washing drum 4, advantageously
by means of a belt/pulley system, not shown. In a different embodiment of the invention,
the motor can be directly associated with the shaft of the washing drum 4.
[0053] A water inlet circuit 5 and a products supply unit 6 are arranged in the upper part
of the laundry washing machine 1 which are suited to supply water and washing/rinsing
products (i.e. detergent, softener, etc.) into the washing tub 3. The water inlet
circuit 5 controls the adduction of cold water coming from an external supply line
E, hereinafter indicated as mains water supply E.
[0054] In a different embodiment, the water inlet circuit may be realized for controlling
adduction of hot water coming from a respective hot water external source.
[0055] The products supply unit 6 preferably comprises a removable drawer 6 provided with
various compartments suited to be filled with washing and/or rinsing products.
[0056] In the embodiment herein described, the water is supplied into the washing tub 3
by making it flow through the drawer 6 and through a supply pipe 9.
[0057] In a preferred embodiment, the water which reaches the washing tub 3 can selectively
contain one of the products contained in the compartments of the drawer 6, or such
water can be clean and in this case it may reach the washing tub 3 directly, bypassing
the compartments of the drawer 6.
[0058] In an alternative embodiment of the invention, a further separate water supply pipe
can be provided, which supplies exclusively clean water into the washing tub 3.
[0059] The water inlet circuit 5 also preferably comprises a water flow sensor, for example
a flow meter, which makes it possible to calculate the quantity of water supplied
into the washing tub 3.
[0060] Laundry washing machine 1 advantageously comprises a water outlet circuit 25 suitable
for withdrawing liquid from the tub 3.
[0061] The water outlet circuit 25 preferably comprises a main pipe 17, a draining pump
26 and an outlet pipe 28 ending outside the cabinet 2.
[0062] The water outlet circuit 25 preferably further comprises a filtering device 12 arranged
between the main pipe 17 and the draining pump 26. The filtering device 12 is adapted
to retain all the undesirable bodies (for example buttons that have come off the laundry,
coins erroneously introduced into the laundry washing machine, etc.).
[0063] This filtering device 12 can preferably be removed, and then cleaned, through a gate
14 placed advantageously on the front wall of the cabinet 2 of the laundry washing
machine 1, as illustrated in Figure 1.
[0064] In a further embodiment, not illustrated, the filtering device 12 may be provided
directly in the tub 3, preferably obtained in a single piece construction with the
latter. In this case the filtering device 12 is fluidly connected to the outlet of
the tub 3, in such a way that water and washing liquid drained from the tub 3 enters
the filtering device 12.
[0065] Activation of the drain pump 26 drains the liquid, i.e. dirty water or water mixed
with washing and/or rinsing products, from the tub 3 to the outside.
[0066] Laundry washing machine 1 advantageously comprises a recirculation circuit 20 adapted
to drain liquid from the bottom region of the tub 3 and to re-admit such a liquid
into a second region, preferably an upper region, of the tub 3.
[0067] The recirculation circuit 20 preferably comprises a recirculation pump 21, a pipe
22 connecting the filtering device 12 to the recirculation pump 21 and a recirculation
pipe 23, preferably provided with a terminal nozzle 23a arranged preferably at the
upper region of the tub 3. The terminal nozzle 23a is opportunely arranged so that
the liquid is sprayed directly into the drum 4 through its holes.
[0068] The terminal nozzle 23a, therefore, enhances distribution of liquid over the laundry
through the perforated drum 4.
[0069] In different embodiments, the recirculation circuit may be preferably realized as
an independent circuit from the water outlet circuit.
[0070] The liquid from the bottom region of the tub 3 is conveyed towards the upper region
of the tub 3 by activation of the recirculation pump 21.
[0071] The recirculation circuit 20 is therefore advantageously activated in order to improve
wetting of the laundry inside the drum 4.
[0072] Preferably, the recirculation circuit is properly realized for transferring a portion
of liquid from a bottom region of the tub, preferably from the sump, to an upper region
of the tub in order to enhance absorption of the liquid by the laundry.
[0073] Nevertheless, the recirculation circuit may be properly realized for transferring
a portion of liquid from the tub to another region of the tub which allows absorption
of the liquid by the laundry. For example, the recirculation pipe may terminate at
any vertical position of the tub and/or its terminal nozzle may be opportunely shaped
to spray liquid along a direction reaching the laundry inside the washing drum 4.
[0074] Advantageously laundry washing machine 1 comprises a device 19 suited to sense (or
detect) the liquid level inside the washing tub 3.
[0075] The device 19 preferably comprises a pressure sensor which senses the pressure in
the washing tub 3, which value is related to the level of liquid contained in the
washing tub 3. In another embodiment, not illustrated, laundry washing machine 1 comprises
(in addition to or as a replacement of the pressure sensor) a level sensor (for example
mechanical, electro-mechanical, optical, etc.) adapted to sense (or detect) the liquid
level inside the washing tub 3.
[0076] Preferably, the laundry washing machine 1 comprises a heating device 60 adapted to
come into contact with the liquid in the washing tub 3 and to heat it.
[0077] The heating device 60, preferably an electric resistor, is preferably placed in a
suitable seat, not illustrated, obtained at the bottom of the washing tub 3 or in
a draining region thereof.
[0078] In different embodiments, the heating device may be omitted. In a first preferred
embodiment, laundry washing machines without heating device may introduce hot water
coming from a respective hot water external source. In a second preferred embodiment,
laundry washing machines without heating device may perform only washing cycle using
cold water coming from the water external source E.
[0079] Laundry washing machine 1 comprises a control unit 22 connected to the various parts
of the laundry washing machine 1 in order to ensure its operation. The control unit
22 is preferably connected to the water inlet circuit 5, the water outlet circuit
25 (in particular the drain pump 26), the recirculation circuit 20 (in particular
the recirculation pump 21), the electric motor rotating the washing drum 4 and receives
information from the various sensors provided on the laundry washing machine 1, like
the flow meter of the water inlet circuit 5, the level sensor 19 (or pressure sensor),
a temperature sensor, etc.
[0080] In particular, the level detected by the level sensor 19 is preferably continuously
received by the control unit 22 and advantageously used according to the present invention,
as better described below.
[0081] Alternatively, the level detected by the level sensor 19 is acquired by the control
unit 22, when necessary, at a pre-determined time.
[0082] Laundry washing machine 1 advantageously comprises an interface unit 50 connected
to control unit 22, accessible to the user and by means of which the user may select
and set the washing parameters from time to time, in particular the desired washing
program. The washing program selected by the user will correspond to a respective
washing cycle performed by the laundry washing machine. Usually, other parameters
can optionally be inserted by the user, for example the washing temperature, the spinning
speed, the load in terms of weight of the laundry to be washed, etc. The interface
unit 50 preferably comprises a display which displays machine working conditions or
other information.
[0083] Based on the parameters acquired by said interface unit 50, the control unit 22 sets
and controls the various parts of the laundry washing machine 1 in order to carry
out the desired washing cycle.
[0084] According to an advantageous aspect of the present invention, the recirculation pump
21 and the level sensor 19 are utilized to determine the presence and/or amount of
foam in the washing tub 3 and/or the draining region thereof.
[0085] After introduction of water and detergent in the washing tub 3, the washing cycle
performs a foam detection procedure, according to the present invention, comprising
a steady phase wherein the recirculation pump is deactivated and a recirculation phase,
following the steady phase, wherein the recirculation pump is activated.
[0086] Alternatively, the foam detection procedure comprises a recirculation phase wherein
the recirculation pump is activated and a steady phase, following the steady phase,
wherein the recirculation pump is deactivated.
[0087] During the steady phase the level L1 of the liquid is detected by the level sensor
19. During the recirculation phase the level L2 of the liquid is also detected by
the level sensor 19. From the detected values LI, L2 of the liquid it is then determined,
by the control unit 22, the level difference LD between the liquid level L2 in the
recirculation phase, or second liquid level L2, and the liquid level L1 in the steady
phase LI, or first liquid level L1, i.e. LD=L2-L1.
[0088] The presence and/or a high amount of foam in the washing tub 3 and/or in the draining
region thereof is determined, if the determined level difference LD is below a threshold
value TV, i.e. LD=L2-L1<TV.
[0089] If the level difference LD is above, or equal to, the threshold value TV then presence
of only water or a low amount of foam is detected.
[0090] Tests carried out by the applicant have proved that a small difference between the
two liquid levels, i.e. a difference below a threshold value, is indicative of the
presence and/or a high amount of foam in the washing tub 3.
[0091] This is due to the fact that the recirculation pump 21 in presence of foam does not
work properly and is not able to pump liquid and/or foam towards the terminal nozzle
23a and from there above the laundry. Therefore, firstly, the recirculation circuit
20, and in particular its pipes 22, 23, remains empty or substantially empty, and
the liquid level detected by the level sensor 19 is the effective liquid presents
in the washing tub 3.
[0092] Furthermore, being the liquid not sprayed over the laundry there is not absorption
by the laundry during the recirculation phase, when the recirculation pump is activated,
and therefore the liquid level L2 detected by the level sensor 19 in the recirculation
phase does not substantially change with respect to the liquid level L1 detected by
the level sensor 19 in the steady phase.
[0093] According to the invention, therefore, the presence and/or a high amount of foam
in the washing tub 3 is detected by comparing the liquid level in the washing tub
3 while the recirculation pump is deactivated and the liquid level in the washing
tub 3 while the recirculation pump is activated.
[0094] As said above, the recirculation pump may be either deactivated and then activated
or activated and then deactivated.
[0095] Preferably, the first liquid level L1 and/or the second liquid level L2 is detected
while the washing drum 4 is motionless. In such condition, the liquid level inside
the washing drum is not affected by oscillation caused by washing drum rotations.
[0096] More preferably, the first liquid level L1 is detected at the expiring of a first
monitoring period Δt1 while the washing drum 4 is kept motionless and/or the second
liquid level L2 is detected at the expiring of a second monitoring period At2 while
the washing drum 4 is kept motionless.
[0097] In a further preferred embodiment, the first liquid level L1 is the average first
liquid level AL1 of the liquid in the steady phase calculated during a predetermined
first monitoring period Δt1.
[0098] Here again, preferably, during the first monitoring period Δt1 the washing drum 4
is kept motionless.
[0099] In a further preferred embodiment, nevertheless, the average first liquid level AL1
may be calculated during said predetermined first monitoring period Δt1 while the
washing drum 4 is rotating.
[0100] The average first liquid level AL1 is preferably calculated as follows:
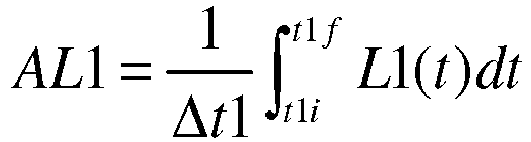
wherein t1i is the initial time of the first monitoring period Δt1 and t1f is the
final time of the first monitoring period Δt1.
[0101] Analogously, in a further preferred embodiment, the second liquid level L2 is the
average second liquid level AL2 of the liquid in the recirculation phase calculated
during a predetermined second monitoring period Δt2.
[0102] Here again, preferably, during the second monitoring period Δt2 the washing drum
4 is kept motionless.
[0103] In a further preferred embodiment, nevertheless, the average second liquid level
AL2 may be calculated during said predetermined second monitoring period Δt2 while
the washing drum 4 is rotating.
[0104] The average first liquid level AL2 is preferably calculated as follows:
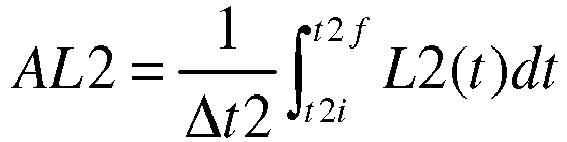
wherein t2i is the initial time of the second monitoring period Δt2 and t2f is the
final time of the second monitoring period Δt2.
[0105] The presence and/or a high amount of foam in the washing tub 3 and/or in the draining
region thereof is then determined if the level difference LD using said average values
is below a threshold value TV, i.e. LD=AL2-AL1<TV.
[0106] In a normal functioning condition of the washing cycle, i.e. substantially without
formation of foam in the washing tub 3, the presence of only water or a low amount
of foam is determined if the level difference LD is above, or equal to, the threshold
value TV, i.e. LD=L2-L1≥TV.
[0107] In different embodiments, the liquid levels may be differently calculated, for example
liquid levels are continuously calculated (instantaneous level).
[0108] Preferably, the first monitoring period Δt1 is preferably set at as the duration
of the steady phase and/or the second monitoring period Δt2 is preferably set at as
the duration of the recirculation phase.
[0109] In different embodiments the predetermined first monitoring periods Δt1 and Δt2 may
have different duration and/or may be differently positioned inside the respective
steady phase and recirculation phase.
[0110] In further preferred embodiments, the first monitoring period Δt1 and/or the second
monitoring period Δt2 are preferably set at a predetermine value, for example 6 sec.
In this case the first monitoring period Δt1 is lower than the duration of the steady
phase and the second monitoring period Δt2 is lower than the duration of the recirculation
phase.
[0111] In further preferred embodiments, the first monitoring period Δt1 is preferably set
at a predetermine value, for example a fixed value of 6 sec.
[0112] In further preferred embodiments, the second monitoring period Δt2 is preferably
set at a predetermine value, for example a fixed value of 14 sec.
[0113] The threshold value TV for the level difference LD is preferably set at a predetermine
value, for example a fixed value of 5 mm.
[0114] Preferably, the threshold value is between 2 mm and 12 mm, more preferably between
4 mm and 10 mm.
[0115] Preferably, the foam detection procedure is carried out one or more times during
the main washing phase of the washing cycle, as will be better described later.
[0116] Nevertheless, the foam detection procedure may be carried out in any other moment
of the washing cycle, obviously after introduction of water and detergent in the washing
tub 3, as will be better described later.
[0117] According to a further advantageous aspect of the present invention, if presence
of foam in the washing tub 3 has been detected, then one or more foam-reducing actions
are preferably taken.
[0118] Hereinafter, possibly foam-reducing actions that can be preferably performed are
described.
[0119] A foam-reducing action that can be performed after detection of foam in the washing
tub 3 preferably comprises the time reduction of the main washing phase with respect
to the expected time of the main washing phase for the washing cycle.
[0120] The main washing phase may be defined as the phase of the washing cycle during which
the washing drum is rotated and the washing liquid contained therein is heated and/or
maintained to a predetermined temperature according to the washing program selected
by the user. Furthermore, preferably, during the main washing phase the recirculation
pump 21 is opportunely activated and deactivated for transferring a portion of the
liquid from the bottom region of the tub 3 to an upper region of the tub 3 so that
the liquid is sprayed over the laundry and absorption is facilitated.
[0121] The main washing phase precedes successive steps of the washing cycle such as rinsing
phases, balances phases, spinning phases etc..
[0122] As a consequence of the time reduction of the main washing phase the rotating time
of the washing drum 4 is also reduced, thus avoiding excessive movement/agitation
of the liquid in the washing tub 3. Dissolution of the foam, therefore, is more rapid.
[0123] Another foam-reducing action that can be performed after detection of foam in the
washing tub 3 preferably comprises the reduction of the activation time of the heating
device with respect to the expected activation time of the same for the main washing
phase of the selected cycle. In case, the heating device can be completely deactivated
for the remaining time of the main washing phase. Again, dissolution of the foam is
more rapid.
[0124] Another foam-reducing action that can be performed after detection of foam in the
washing tub 3 preferably comprises the variation of the washing drum rhythm, preferably
the reduction of the rotation time of the washing drum with respect to the expected
rotation time for the main washing phase of the selected cycle.
[0125] The reduction of the rotation time of the washing drum avoids excessive movement/agitation
of the liquid in the washing tub and therefore dissolution of the foam is more rapid.
[0126] Another foam-reducing action that can be performed after detection of foam in the
washing tub 3 preferably comprises the introduction of one or more additional rinsing
phases with respect to the expected rinsing phases for the selected cycle.
[0127] Additional rinsing phases enhances dissolution of the foam and its drainage to the
outside.
[0128] Another foam-reducing action that can be performed after detection of foam in the
washing tub 3 preferably comprises the introduction of a further quantity of water
during the main washing phase.
[0129] The introduction of additional water decreases the concentration of detergent in
the washing tub 3 thus advantageously reducing the possibility of foam generation.
[0130] Another foam-reducing action that can be performed after detection of foam in the
washing tub 3 preferably comprises a drainage phase to remove and discharge the washing
liquid from the bottom of the washing tub to the outside.
[0131] The discharge of washing liquid decreases the concentration of detergent in the washing
tub 3 thus advantageously reducing the possibility of foam generation.
[0132] In a preferred embodiment, one or more introduction phases of water and/or one or
more drainage phases are performed.
[0133] In a preferred embodiment, after a drainage phase an amount of clean water is introduced
in the washing tub 3 to re-instate a sufficient quantity of washing liquid for the
main washing. The introduction of clean water further decreases the concentration
of detergent in the washing tub 3.
[0134] A further foam-reducing action that can be performed after detection of foam in the
washing tub 3 preferably comprises the variation/reduction of the activation time
of the recirculation pump 21 with respect to the expected activation time for the
selected cycle. This enhances a more rapid dissolution of the foam.
[0135] In a further preferred embodiment, the recirculation pump 21 is completely deactivated.
[0136] Another action that can be performed after detection of foam in the washing tub 3
preferably comprises sending a warning alarm for the user, for example a visual alarm
at the display of the interface unit 50 or an acoustic alarm. Since formation of foam
may be caused by an overdose of detergent or a wrong detergent usage, the foam alarm
may be useful for the user because it advises him on how to prevent future laundry
washing cycle with foam formation, for example the choice of a correct detergent.
[0137] Figure 3 illustrates schematic flow chart diagram of a method for operating the laundry
washing machine during a washing cycle according to a preferred embodiment of the
present invention.
[0138] The laundry to be washed is first placed inside the washing drum 4 (step 100).
[0139] By operating on the interface unit 50 the user selects the desired washing program
(step 110).
[0140] In a next step (step 120) the washing cycle according to the washing program selected
by the user is started. As a next step (step 130) the method provides for a phase
wherein a quantity of water Qw and a quantity of detergent Qd are introduced into
the washing tub 3 to form a washing liquid for washing the laundry, preferably by
means of the water inlet circuit 5 and the products supply unit 6. During the phase,
the washing drum 4 is advantageously rotated with a preferred rhythm.
[0141] The washing cycle then proceeds with a main washing phase (step 170).
[0142] In the preferred embodiment herewith illustrated, the main washing phase comprises
cyclical activation (step 172) and deactivation (step 174) of the recirculation pump
21 for transferring a portion of the liquid from the bottom region of the tub 3 to
an upper region of the tub 3 so that the liquid is sprayed over the laundry and absorption
is facilitated.
[0143] During the main washing phase (step 170) the washing drum is then preferably rotated
and the washing liquid contained therein is heated and/or maintained to a predetermined
temperature according to the washing program selected by the user.
[0144] According to the preferred aspect of the present invention, during the main washing
phase (step 170) a foam detection procedure (step 200, 200') is performed.
[0145] In particular, the foam detection procedure (step 200, 200') is preferably performed
after deactivation of the recirculation pump 21 and before the successive activation
of the recirculation pump 21.
[0146] A first preferred embodiment of the foam detection procedure (step 200) is better
described with reference to Figure 4A.
[0147] A second preferred embodiment of the foam detection procedure (step 200') is better
described with reference to Figure 4B.
[0148] The first preferred embodiment of the foam detection procedure (step 200), see Figure
4A, preferably firstly comprises a step wherein the washing drum 4 is stopped (step
210), obviously in case the washing drum 4 was rotating. The stationary condition
with the washing drum 4 motionless is maintained for a predetermined period of time,
for example 6 sec, in order to guarantee a good measurement (step 230) of the first
liquid level L1 in the washing tub 3, preferably detected by the pressure sensor 19.
The predetermined period of time corresponds to the duration of the steady phase and
preferably to the first monitoring period Δt1 as defined above.
[0149] The recirculation pump 21 is then activated (step 240) and after a predetermined
period of time, for example 14 sec, a measurement (step 250) of the second liquid
level L2 in the washing tub 3 is carried out. The predetermined period of time corresponds
to the duration of the recirculation phase and preferably to the second monitoring
period Δt2 as defined above.
[0150] In a successive step, the level difference LD between the second liquid level L2
and the first liquid level L1 (step 260) is calculated.
[0151] According to the invention, if the level difference LD is below a threshold value
TV (output "Yes" of step 260), the presence of foam is established (step 270) .
[0152] If the level difference LD is above, or equal to, the threshold value TV (output
"No" of step 260), the method normally proceeds without establishing the presence
of foam.
[0153] The second preferred embodiment of the foam detection procedure (step 200'), see
Figure 4B, preferably firstly comprises a step wherein the washing drum 4 is stopped
(step 210), obviously in case the washing drum 4 was rotating.
[0154] The recirculation pump 21 is then activated (step 240') and after a predetermined
period of time, for example 14 sec, a measurement (step 250') of the second liquid
level L2 in the washing tub 3 is carried out. The predetermined period of time corresponds
to the duration of the recirculation phase and preferably to the second monitoring
period At2 as defined above.
[0155] The recirculation pump 21 is then deactivated (step 219') and the stationary condition
with the washing drum 4 motionless is maintained for a predetermined period of time,
for example 6 sec, in order to guarantee a good measurement (step 230') of the first
liquid level L1 in the washing tub 3, preferably detected by the pressure sensor 19.
The predetermined period of time corresponds to the duration of the steady phase and
preferably to the first monitoring period Δt1 as defined above.
[0156] In a successive step, the level difference LD between the second liquid level L2
and the first liquid level L1 (step 260') is calculated.
[0157] According to the invention, if the level difference LD is below a threshold value
TV (output "Yes" of step 260'), the presence of foam is established (step 270') .
[0158] If the level difference LD is above, or equal to, the threshold value TV (output
"No" of step 260'), the method normally proceeds without establishing the presence
of foam.
[0159] Going back to the washing cycle, as illustrated in Figure 3, after the main washing
phase 170 the washing cycle advantageously proceeds with one or more rinsing cycles
(steps 180 and 190) during which clean rinse water is added to the laundry and the
washing drum is rotated to extract water and dirty particles/detergent from the laundry:
the dirty water extracted is drained from the washing tub 3 to the outside.
[0160] The washing cycle terminates with a final spinning phase (step 195).
[0161] Once the washing cycle has been completed, in case of a laundry washing-drying machine,
a drying phase may be also preferably performed.
[0162] It has to be noted that if the presence of foam (step 270, 270') has been established
during the foam detection procedure (step 200, 200'), then the washing cycle as illustrated
in Figure 3 is eventually and properly adapted with execution of one or more foam-reducing
actions of the type previously described. Figure 5 shows a variant of the washing
cycle previously described with reference to Figure 3.
[0163] Corresponding steps of the washing cycle of Figure 3 are identified by the same reference
numbers.
[0164] This washing cycle differs from the washing cycle previously described with reference
to Figure 3 in that the phase of introducing a quantity of water Qw and a quantity
of detergent Qd into the washing tub 3 is replaced by a first phase of introducing
a first quantity of water Q1w (step 135), a procedure for checking correct functioning
of the recirculation pump 21 (step 300) and a phase of introducing a second quantity
of water Q2w and a quantity of detergent Qd into the washing tub 3 (step 140).
[0165] The correct functioning procedure for the recirculation pump 21, not described herein,
allows to obtain information on the correct functioning of the recirculation pump
21 and, in case, taking proper actions.
[0166] An action that can be performed when malfunctioning of the recirculation pump 21
is established is the omission of the foam detection procedure for the washing cycle
or, in other words, the foam detection procedure is performed if it has been established
that the recirculation pump 21 is working correctly.
[0167] In a further preferred embodiment of the washing cycle, not illustrated, after the
phase of introducing a quantity of water Qw and a quantity of detergent Qd into the
washing tub 3 and before the main washing phase (step 170), a step of checking the
liquid level L into the washing tub 3 is performed.
[0168] If the liquid level L is below or equal to a predetermined minimum level Lmin then
the foam detection procedure for the washing cycle is omitted or, in other words,
the foam detection procedure is performed if it has been established that the liquid
level L in the washing tub 3 is above a predetermined minimum level Lmin.
[0169] Figure 6 shows another variant of the washing cycle previously described with reference
to Figure 3.
[0170] This washing cycle simply shows how the foam detection procedure (step 200, 200')
may be advantageously carried out at any proper time during the main washing phase
(step 370), independently of the actions which are performed in the same main washing
phase.
[0171] Analogously, Figure 7 shows a washing cycle wherein the foam detection procedure
(step 200, 200') is advantageously carried after introduction of water and detergent
in the washing tub 3 (step 130) and before a main washing phase (step 470).
[0172] Analogously, Figure 8 shows a washing cycle wherein the foam detection procedure
(step 200, 200') is advantageously carried after a main washing phase (step 470).
[0173] Advantageously, the method according to the invention allows the detection of foam
at different stages of the washing cycle, preferably at an early stage of the washing
cycle.
[0174] It follows that foam-reduction actions may be performed from the very beginning of
the washing cycle. This help to reduce detergent accumulation on the laundry with
respect known methods.
[0175] Furthermore, detection of foam is advantageously carried out by means of a level
sensor which is usually installed in laundry washing machines, without necessity of
installing and controlling a dedicated foam sensor.
[0176] Therefore the method of the invention allows detecting of foam in a laundry washing
machine having reduced complexity and/or size compared to laundry washing machines
which detect foam of known type.
[0177] It follows that the laundry washing machine performing the method of the invention
has higher reliability compared to laundry washing machines which detect foam of known
type.
[0178] Still advantageously, the method according to the invention assures a more correct
functioning of the pumps installed in the laundry washing machine which drain liquid
from the washing tub since presence of foam at their inlets is substantially avoided.
This, in turn, reduces the noise caused by the pump working with foam.
[0179] Advantageously, the method according to the invention reduces or avoids overflow
and liquid spillage from the washing tub.
[0180] It has thus been shown that the present invention allows all the set objects to be
achieved. In particular, it makes it possible to provide a method and a laundry washing
machine with a more effective detection system of foam compared to known systems.
[0181] It is underlined that the laundry washing machine illustrated in the enclosed figures,
and with reference to which some embodiments of the method according to the invention
have been described, is of the front-loading type; however it is clear that the method
according to the invention can be applied as well to a top-loading laundry washing
machine, substantially without any modification.
1. Verfahren zum Feststellen des Vorhandenseins von Schaum in einer Wäsche-Waschmaschine
(1) während eines Waschzyklus, wobei die Wäsche-Waschmaschine (1) Folgendes umfasst:
einen Waschbottich (3), der eine Waschtrommel (4) enthält, einen Umwälzkreislauf (20),
der eine Umwälzpumpe (21) zum Abführen von Flüssigkeit vom Boden des Wasserbottichs
(3) und zum Rückführen dieser Flüssigkeit in einen anderen Teil des Waschbottichs
(3) enthält, einen Flüssigkeitspegelsensor (19) zum Detektieren des Flüssigkeitspegels
in dem Waschbottich (3), wobei der Waschzyklus wenigstens eine Phase zum Einleiten
einer Menge an Wasser (Qw) und einer Menge an Reinigungsmittel (Qd) in den Waschbottich
(3) zum Bilden einer Waschflüssigkeit umfasst, wobei nach der wenigstens einen Phase
zum Einleiten einer Menge an Wasser (Qw) und einer Menge an Reinigungsmittel (Qd)
das Verfahren die folgenden Schritte umfasst:
- Durchführen einer ruhigen Phase, in der die Umwälzpumpe (21) deaktiviert ist, und
einer Umwälzphase, in der die Umwälzpumpe (21) aktiviert ist, wobei das Verfahren
dadurch gekennzeichnet ist, dass es die folgenden Schritte umfasst:
- Detektieren eines ersten Pegels (L1) von Waschflüssigkeit in dem Waschbottich (3)
während der ruhigen Phase;
- Detektieren eine zweiten Pegels (L2) der Waschflüssigkeit in dem Waschbottich (3)
während der Umwälzphase;
- Feststellen des Pegelunterschieds (LD) zwischen dem zweiten Pegel (L2) und dem ersten
Pegel (L1);
- Vergleichen des festgestellten Pegelunterschieds (LD) mit einem Schwellenwert (TV),
und falls der festgestellte Pegelunterschied (LD) unter dem Schwellenwert (TV) liegt,
Feststellen des Vorhandenseins von Schaum.
2. Verfahren nach Anspruch 1, wobei die Umwälzphase nach der ruhigen Phase durchgeführt
wird.
3. Verfahren nach einem der vorhergehenden Ansprüche, wobei während der ruhigen Phase
und/oder der Umwälzphase die Waschtrommel (4) bewegungslos gehalten wird.
4. Verfahren nach einem der vorhergehenden Ansprüche, wobei der erste Pegel (L1) in einer
festgelegten ersten Überwachungsperiode (Δt1) detektiert wird.
5. Verfahren nach Anspruch 4, wobei die festgelegte erste Überwachungsperiode (Δt1) der
zeitlichen Dauer der ruhigen Phase entspricht.
6. Verfahren nach einem der vorhergehenden Ansprüche, wobei der zweite Pegel (L2) in
einer festgelegten zweiten Überwachungsperiode (Δt2) detektiert wird.
7. Verfahren nach Anspruch 6, wobei die festgelegte zweite Überwachungsperiode (Δt2)
der zeitlichen Dauer der Umwälzphase entspricht.
8. Verfahren nach einem der Ansprüche 4 bis 7, wobei der erste Pegel (L1) der gemittelte
erste Pegel (AL1) in der festgelegten ersten Überwachungsperiode (Δt1) ist.
9. Verfahren nach einem der Ansprüche 6 bis 8, wobei der zweite Pegel (L2) der gemittelte
zweite Pegel (AL2) in der festgelegten zweiten Überwachungsperiode (Δt2) ist.
10. Verfahren nach einem der vorhergehenden Ansprüche, wobei der Schwellenwert (TV) zwischen
2 mm und 12 mm, vorzugsweise zwischen 4 mm und 10 mm liegt, und stärker bevorzugt
5 mm entspricht.
11. Verfahren nach einem der vorhergehenden Ansprüche, wobei dann, wenn des Vorhandenseins
von Schaum festgestellt worden ist, wenigstens eine Aktion zum Reduzieren von Schaum
durchgeführt wird.
12. Verfahren nach Anspruch 11, wobei die Aktion zum Reduzieren von Schaum eine der folgenden
Aktionen umfasst:
- Reduzierung der Zeit des Hauptwaschschritts in Bezug auf die erwartete Zeit des
Hauptwaschschritts für den Waschzyklus;
- Reduzierung der Aktivierungszeit der Heizvorrichtung in Bezug auf die erwartete
Aktivierungszeit für den Hauptwaschschritt des ausgewählten Zyklus;
- Deaktivierung einer Heizvorrichtung der Wäsche-Waschmaschine (1);
- Deaktivierung einer Heizvorrichtung der Wäsche-Waschmaschine (1) für eine festgelegte
Zeitspanne;
- Änderung des Rhythmus der Waschtrommel in Bezug auf die erwartete Rotationszeit
für den Hauptwaschschritt des ausgewählten Zyklus;
- Einleitung eines oder mehrerer zusätzlicher Spülschritte in Bezug auf die erwarteten
Spülschritte für den ausgewählten Zyklus;
- Einleitung einer weiteren Menge an Wasser während des Hauptwaschschritts;
- Reduzierung der Aktivierungszeit der Umwälzpumpe (21) in Bezug auf die erwartete
Aktivierungszeit für den ausgewählten Zyklus;
- vollständige Deaktivierung der Umwälzpumpe (21) .
13. Verfahren nach Anspruch 11 oder 12, wobei die Aktion zum Reduzieren von Schaum das
Senden eines Alarmsignals, vorzugsweise eines optischen Alarms oder eines akustischen
Alarms, an den Benutzer umfasst.
14. Wäsche-Waschmaschine (1), die Folgendes umfasst: ein Außengehäuse (2), das einen Waschbottich
(3), der eine Waschtrommel (4) enthält, umfasst, einen Umwälzkreislauf (20), der eine
Umwälzpumpe (21) zum Abführen von Flüssigkeit von dem Boden des Waschbottichs (3)
und zum erneuten Zuführen dieser Flüssigkeit in einen anderen Teil des Waschbottichs
(3) umfasst, einen Flüssigkeitspegelsensor (19) zum Detektieren des Flüssigkeitspegels
in dem Waschbottich (3), eine Steuereinheit (22), die mit den verschiedenen Teilen
der Wäsche-Waschmaschine (1) verbunden ist, um ihren Betrieb sicherzustellen, wenn
die Wäsche-Waschmaschine (1) für das Verfahren nach einem der Ansprüche 1 bis 13 vorgesehen
ist.
1. Procédé pour déterminer la présence de mousse dans une machine à laver le linge (1)
pendant un cycle de lavage, ladite machine à laver le linge (1) comprenant une cuve
de lavage (3) contenant un tambour de lavage (4), un circuit de recirculation (20)
comprenant une pompe de recirculation (21) pour vider le liquide du fond de ladite
cuve de lavage (3) et pour admettre de nouveau ce liquide dans une autre partie de
ladite cuve de lavage (3), un capteur de niveau de liquide (19) pour détecter le niveau
de liquide dans ladite cuve de lavage (3), ledit cycle de lavage comprenant au moins
une phase consistant à introduire une quantité d'eau (Qw) et une quantité de détergent
(Qd) dans ladite cuve de lavage (3) afin de former un liquide de lavage, ce procédé
comprenant, après ladite au moins une phase consistant à introduire une quantité d'eau
(Qw) et une quantité de détergent (Qd),
les étapes consistant à :
- exécuter une phase stable dans laquelle ladite pompe de recirculation (21) est désactivée
et une phase de recirculation dans laquelle ladite pompe de recirculation (21) est
activée,
ledit procédé étant
caractérisé par les étapes suivantes :
- la détection d'un premier niveau (L1) dudit liquide de lavage dans ladite cuve de
lavage (3) pendant ladite phase stable ;
- la détection d'un deuxième niveau (L2) dudit liquide de lavage dans ladite cuve
de lavage (3) pendant ladite phase de recirculation ;
- la détermination de la différence de niveau (LD) entre ledit deuxième niveau (L2)
et ledit premier niveau (L1) ;
- la comparaison de la différence de niveau déterminée (LD) avec une valeur de seuil
(TV) et, si la différence de niveau déterminée (LD) est en dessous de ladite valeur
de seuil (TV), l'établissement de la présence de mousse.
2. Procédé selon la revendication 1, dans lequel ladite phase de recirculation est exécutée
après ladite phase stable.
3. Procédé selon l'une quelconque des revendications précédentes, dans lequel, pendant
ladite phase stable et/ou ladite phase de recirculation, ledit tambour de lavage (4)
est maintenu immobile.
4. Procédé selon l'une quelconque des revendications précédentes, dans lequel ledit premier
niveau (L1) est détecté lors d'une première période de surveillance prédéterminée
(Δt1).
5. Procédé selon la revendication 4, dans lequel ladite première période de surveillance
prédéterminée (Δt1) correspond à la durée de temps de ladite phase stable.
6. Procédé selon l'une quelconque des revendications précédentes, dans lequel ledit deuxième
niveau (L2) est détecté lors d'une deuxième période de surveillance prédéterminée
(Δt2).
7. Procédé selon la revendication 6, dans lequel ladite deuxième période de surveillance
prédéterminée (Δt2) correspond à la durée de temps de ladite phase de recirculation.
8. Procédé selon l'une quelconque des revendications 4 à 7, dans lequel ledit premier
niveau (L1) est le premier niveau moyen (AL1) dans ladite première période de surveillance
prédéterminée (Δt1).
9. Procédé selon l'une quelconque des revendications 6 à 8, dans lequel ledit deuxième
niveau (L2) est le deuxième niveau moyen (AL2) dans ladite deuxième période de surveillance
prédéterminée (Δt2).
10. Procédé selon l'une quelconque des revendications précédentes, dans lequel ladite
valeur de seuil (TV) est entre 2 mm et 12 mm, de préférence entre 4 mm et 10 mm, idéalement
égale à 5 mm.
11. Procédé selon l'une quelconque des revendications précédentes, dans lequel, si la
présence de mousse a été établie, alors au moins une action de réduction de mousse
est prise.
12. Procédé selon la revendication 11, dans lequel ladite action de réduction de la mousse
consiste en une des actions suivantes :
- la réduction du temps de l'étape de lavage principale par rapport au temps prévu
de l'étape de lavage principale pour le cycle de lavage ;
- la réduction du temps d'activation du dispositif de chauffage par rapport au temps
d'activation prévu de celui-ci pour l'étape de lavage principale du cycle sélectionné
;
- la désactivation d'un dispositif de chauffage de ladite machine à laver le linge
(1) ;
- la désactivation d'un dispositif de chauffage de ladite machine à laver le linge
(1) pendant un temps prédéterminé ;
- la variation du rythme du tambour de lavage par rapport au temps de rotation prévu
pour l'étape de lavage principale du cycle sélectionné ;
- l'introduction d'une ou de plusieurs étapes de rinçage supplémentaires par rapport
aux étapes de rinçage prévues pour le cycle sélectionné ;
- l'introduction d'une quantité supplémentaire d'eau pendant l'étape de lavage principale
;
- la réduction du temps d'activation de ladite pompe de recirculation (21) par rapport
au temps d'activation prévu pour le cycle sélectionné ;
- la désactivation complète de ladite pompe de recirculation (21).
13. Procédé selon l'une quelconque des revendications 11 ou 12, dans lequel ladite action
de réduction de la mousse comprend l'envoi d'une alarme d'avertissement pour l'utilisateur,
de préférence une alarme visuelle ou une alarme acoustique.
14. Machine à laver le linge (1), comprenant une enveloppe externe (2) comprenant une
cuve de lavage (3) contenant un tambour de lavage (4), un circuit de recirculation
(20) comprenant une pompe de recirculation (21) pour vider le liquide du fond de ladite
cuve de lavage (3) et pour admettre de nouveau ce liquide dans une autre partie de
ladite cuve de lavage (3), un capteur de niveau de liquide (19) pour détecter le niveau
du liquide dans ladite cuve de lavage (3), une unité de commande (22) connectée aux
diverses parties de la machine à laver le linge (1) afin d'assurer son bon fonctionnement,
cette machine à laver le linge (1) étant fournie pour le procédé selon l'une quelconque
des revendications 1 à 13.