FIELD
[0001] The present invention relates to a light source control device that controls a light
source.
BACKGROUND
[0002] In recent years, for a vehicle lighting device such as headlights, a semiconductor
light source such as LEDs (light emitting diodes) which are longer in lifetime and
lower in power consumption is used instead of a halogen lamp having a filament in
a related art. The degree of light emission, that is, the brightness of the LED depends
on the magnitude of a current that is made to flow in the LED. For that reason, when
the LED is used as a light source, there is a need to provide a lighting circuit for
adjusting the current flowing in the LED.
[0003] The present inventors have proposed, in Patent Literature 1, a technique in which
in order to conduct fine light distribution control while making the light distribution
of the headlight variable, an array of the LEDs is applied as the light source, and
the respective LEDs are switched on or off, individually. In the lighting circuit
disclosed in Patent Literature 1, a bypass switch is disposed in parallel to each
of the LEDs, and the bypass switch is turned on/off to realize the individual switch-on/off
of the LED.
[Citation List]
[Patent Literature]
[0005] When a bypass system disclosed in Patent Literature 1 is applied to the lighting
circuit, lines around the LEDs become relatively complicated. When the lines become
complicated, a possibility that a poor continuity such as a contact failure or disconnection
is generated may become high.
SUMMARY
[0007] Exemplary embodiments of the invention provide a light source control device that
can appropriately cope with the poor continuity which is generated in the line around
the light sources or the bypass switches.
[0008] A light source control device (100,700) according to an exemplary embodiment. is
defined in claim 1.
[0009] According to this aspect, if the poor continuity is generated in the connection line,
both of the first bypass switch and the second bypass switch can be forcedly turned
on.
[0010] According to the present invention, there can be provided the light source control
device that can appropriately cope with the poor continuity which is generated in
the line around the light sources or the bypass switches.
BRIEF DESCRIPTION OF THE DRAWINGS
[0011]
FIG. 1 is a circuit diagram illustrating a configuration of a semiconductor light
source control device and members connected to the semiconductor light source control
device according to an embodiment.
FIG. 2 is a circuit diagram illustrating a configuration of a hysteresis width setting
circuit of FIG. 1.
FIG. 3 is a graph illustrating a relationship between an absolute value of a drive
voltage Vout and an offset voltage Voffset.
FIG. 4 is a circuit diagram illustrating a configuration of a downconverter driver
circuit of FIG. 1.
FIG. 5 is a circuit diagram illustrating configurations of a second bypass circuit
and a third bypass circuit of FIG. 1.
FIGS. 6A to 6C illustrate a time variation of a drive current.
FIG. 7 is a timing chart illustrating a change in a second bypass switch drive signal
and a second abnormality detection signal in a PWM dimming state.
FIG. 8 is a circuit diagram illustrating a configuration of a semiconductor light
source lighting circuit according to a comparative example.
FIGS. 9A to 9 C illustrate configurations of semiconductor light source control devices
according to a first to third modified examples.
FIG. 10 is a circuit diagram illustrating a configuration of a semiconductor light
source control device according to a fourth modified example.
FIG. 11 is a circuit diagram illustrating a configuration of a second bypass circuit
in a semiconductor light source control device according to a fifth modified example.
FIG. 12 is a timing chart illustrating a change in the second lighting on/off control
signals when the disconnection is generated in a second LED.
DETAILED DESCRIPTION
[0012] Hereinafter, identical or equivalent elements, members, and signals illustrated in
the respective drawings are indicated by the same numerals or symbols, and their repetitive
description will be appropriately omitted. Also, parts of members which are not important
in description in the respective drawings will be omitted in illustration. Also, symbols
affixed to voltages, currents, or resistances can be used as indications of respective
voltage values, current values, or resistance values as occasion demands.
[0013] In the present specification, "a state in which a member A is connected to a member
B" includes a case in which the member A and the member B are physically directly
connected to each other, as well as a case in which the member A and the member B
are connected indirectly to each other through another member that does not affect
an electric connection state therebetween. Likewise, "a state in which a member C
is disposed between the member A and the member B" includes a case in which the member
A and the member C, or the member B and the member C are connected directly to each
other, as well as a case in which those members are connected indirectly to each other
through another member that does not affect an electric connection state therebetween.
[0014] A semiconductor light source control device according to an embodiment generates
a drive current that flows in a plurality of semiconductor light sources connected
in series, that is, LEDs. A bypass switch is disposed in parallel to each of the LEDs.
When the bypass switch turns on (off), a corresponding LED turns on (off). A bypass
connection line is disposed between a connection node between two adjacent LEDs, and
a connection node between two corresponding bypass switches. The semiconductor light
source control device is configured such that when a disconnection or contact failure
is generated in the bypass connection line, the two bypass switches connected by the
bypass connection line are forcedly turned on. With this configuration, when the poor
continuity is thus generated, the associated LEDs can be turned off.
[0015] FIG. 1 is a circuit diagram illustrating a configuration of a semiconductor light
source control device 100 and members connected to the semiconductor light source
control device 100 according to the embodiment. The semiconductor light source control
device 100 supplies a drive current lout to a plurality (N) of in-vehicle LEDs 2-1
to 2-N which is connected in series with each other, and turns on those LEDs 2-1 to
2-N. N is a natural number of 2 or larger. The semiconductor light source control
device 100 and the N LEDs 2-1 to 2-N are mounted in a vehicle lighting device such
as headlights. The semiconductor light source control device 100 is connected to an
in-vehicle battery 6 and a power switch 8.
[0016] The in-vehicle battery 6 generates a battery voltage (supply voltage) Vbat of 12V
(or 24V) DC. The power switch 8 is a relay switch configured to control the on/off
operation of the overall N LEDs 2-1 to 2-N, and connected in series with the in-vehicle
battery 6. When the power switch 8 turns on, the battery voltage Vbat is applied to
the semiconductor light source control device 100 from a positive terminal of the
in-vehicle battery 6 as an input voltage. A negative terminal of the in-vehicle battery
6 is connected to a fixed voltage terminal, that is, grounded.
[0017] The LEDs 2-1 to 2-N are connected in parallel to electrostatic protection zener diodes
252-1 to 252-N in an opposite direction, respectively. That is, a cathode of the first
electrostatic protection zener diode 252-1 is connected to an anode of the first LED
2-1, and an anode of the first electrostatic protection zener diode 252-1 is connected
to a cathode of the first LED 2-1. The same is applied to the second electrostatic
protection zener diodes 252-2 to the N
th electrostatic protection zener diodes 252-N. The electrostatic protection zener diodes
252-1 to 252-N protect the corresponding LEDs 2-1 to 2-N from being broken down by
static electricity.
[0018] The semiconductor light source control device 100 includes a switching regulator,
that is, a flyback regulator 102, a downconverter 104, a control circuit 106, a current
detection resistor 108, N bypass circuits 270-1 to 270-N, and a bypass driver circuit
112. The control circuit 106 controls the flyback regulator 102 and the downconverter
104, and includes a flyback driver circuit 134, a downconverter driver circuit 136,
and a hysteresis width setting circuit 138. The bypass driver circuit 112 is realized
by a microcomputer.
[0019] The flyback regulator 102 is formed of a voltage regulator, and converts the input
battery voltage Vbat into a target voltage Vt, and outputs the target voltage Vt.
Since an output terminal on a high potential side of the flyback regulator 102 is
on a ground side, the target voltage Vt is a voltage to be applied to the output terminal
on a low potential side of the flyback regulator 102, and has a negative polarity.
The flyback regulator 102 includes an input capacitor 114, a first switching element
116, an input transformer 124, an output diode 126, an output capacitor 128, a voltage
detection diode 130, and a voltage detection capacitor 132.
[0020] The input capacitor 114 is disposed in parallel to the in-vehicle battery 6, and
smooths the battery voltage Vbat. More specifically, the input capacitor 114 is disposed
in the vicinity of the input transformer 124, and performs a function of smoothing
a voltage in the switching operation of the flyback regulator 102.
[0021] A primary winding 118 of the input transformer 124 and the first switching element
116 are connected in series, and the series circuit is connected in parallel to the
input capacitor 114 with respect to the in-vehicle battery 6. For example, the first
switching element 116 is formed of an N-channel MOSFET (metal oxide semiconductor
field effect transistor). One end of a secondary winding 120 of the input transformer
124 is connected to one end of the output capacitor 128, and the other end of the
secondary winding 120 is connected to an anode of the output diode 126. The other
end of the output capacitor 128 is connected to a cathode of the output diode 126.
One end of the output capacitor 128 is connected to the output terminal on a low potential
side of the flyback regulator 102, and is applied with the target voltage Vt. The
other end of the output capacitor 128 is connected to the output terminal on the high
potential side of the flyback regulator 102.
[0022] A control terminal (gate) of the first switching element 116 is supplied with an
upstream control signal S1 having a rectangular waveform which is generated by the
flyback driver circuit 134. The first switching element 116 turns on when the upstream
control signal S1 is asserted, that is, high level, and turns off when the upstream
control signal S1 is negated, that is, low level.
[0023] A voltage detection winding 122 of the input transformer 124, the voltage detection
diode 130, and the voltage detection capacitor 132 configure a positive voltage detector
circuit for detecting a magnitude of the target voltage Vt as a positive voltage.
One end of the voltage detection winding 122 is grounded, and the other end thereof
is connected to an anode of the voltage detection diode 130. A cathode of the voltage
detection diode 130 is connected to one end of the voltage detection capacitor 132.
The other end of the voltage detection capacitor 132 is grounded. One end of the voltage
detection capacitor 132 is applied with a positive voltage corresponding to an absolute
value of the target voltage Vt. This voltage is applied to the flyback driver circuit
134 as a detected voltage Vd.
[0024] The flyback driver circuit 134 conducts a voltage feedback control for keeping a
substantially constant target voltage Vt on the basis of the detected voltage Vd.
The flyback driver circuit 134 adjusts a frequency or a duty ratio of the upstream
control signal S1 so that the target voltage Vt comes close to a set voltage of, for
example, about -100V.
[0025] The downconverter 104 is disposed downstream of the flyback regulator 102, and includes
a second switching element 140, a flywheel diode 142, and an inductor 144, but does
not include an output voltage smoothing capacitor.
[0026] The second switching element 140 is formed of, for example, an N-channel MOSFET.
A control terminal of the second switching element 140 is supplied with a downstream
control signal S2 of a rectangular waveform which is generated by the downconverter
driver circuit 136. The second switching element 140 turns on when the downstream
control signal S2 is high level, and turns off when the downstream control signal
S2 is low level. A drain of the second switching element 140 is connected to the output
terminal on a high potential side of the output capacitor 128, that is, the high potential
side of the flyback regulator 102. A source of the second switching element 140 is
connected to a cathode of the flywheel diode 142.
[0027] An anode of the flywheel diode 142 is connected to one end of the inductor 144. A
connection node between the anode of the flywheel diode 142 and one end of the inductor
144 is connected to the output terminal on the low potential side of the output capacitor
128, that is, on the low potential side of the flyback regulator 102. The other end
of the inductor 144 is connected to the cathode sides of the N LEDs 2-1 to 2-N.
[0028] The current detection resistor 108 is disposed on a route of the drive current lout.
One end of the current detection resistor 108 is connected to a connection node between
the source of the second switching element 140 and the cathode of the flywheel diode
142. The other end of the current detection resistor 108 is grounded, and also connected
to the anode side of the N LEDs 2-1 to 2-N. A voltage drop Vm proportional to the
drive current lout is generated in the current detection resistor 108.
[0029] Since the anode side of the N LEDs 2-1 to 2-N is grounded, the cathode side of the
N LEDs 2-1 to 2-N, that is, the other end of the inductor 144 is applied with a drive
voltage Vout of a negative polarity. In the normal light-up state, the drive voltage
Vout becomes a negative voltage having a magnitude corresponding to (the number of
LEDs that are in a light emitting state (= a state in which corresponding bypass switches
are off)) × (forward drop voltage Vf of one LED).
[0030] The downconverter driver circuit 136 conducts a current feedback control for allowing
the drive current lout to fall within a given current range on the basis of the voltage
drop Vm. The downconverter driver circuit 136 turns off the second switching element
140 if the magnitude of the drive current lout exceeds a given current upper limit
value Ith1. The downconverter driver circuit 136 turns on the second switching element
140 if the magnitude of the drive current lout falls below a current lower limit value
Ith2 smaller than the current upper limit value Ith1. The downconverter driver circuit
136 sets the downstream control signal S2 to the low level if the magnitude of the
drive current lout exceeds the current upper limit value Ith1. The downconverter driver
circuit 136 sets the downstream control signal S2 to the high level if the magnitude
of the drive current lout falls below the current lower limit value Ith2.
[0031] The hysteresis width setting circuit 138 sets a hysteresis width ΔI which is a difference
between the current upper limit value Ith1 and the current lower limit value Ith2,
on the basis of the drive voltage Vout. The hysteresis width setting circuit 138 increases
the hysteresis width ΔI more as an absolute value of the drive voltage Vout becomes
larger if the absolute value of the drive voltage Vout falls below a voltage threshold
value Vth smaller than the absolute value of the target voltage Vt. The hysteresis
width setting circuit 138 decreases the hysteresis width ΔI more as the absolute value
of the drive voltage Vout becomes larger if the absolute value of the drive voltage
Vout exceeds the voltage threshold value Vth.
[0032] FIG. 2 is a circuit diagram illustrating a configuration of the hysteresis width
setting circuit 138. The hysteresis width setting circuit 138 includes a first operational
amplifier 146, a first diode 148, a first resistor 150, a second resistor 152, a third
resistor 154, a fourth resistor 156, a fifth resistor 158, and a reference voltage
source 160. One end of the third resistor 154 is applied with a positive control supply
voltage Vcc. The other end of the third resistor 154 is connected with one end of
the second resistor 152, one end of the fifth resistor 158, and one end of the fourth
resistor 156. The other end of the fourth resistor 156 is grounded. The other end
of the fifth resistor 158 is applied with the drive voltage Vout. The other end of
the second resistor 152 is connected to an inverting input terminal of the first operational
amplifier 146. The inverting input terminal of the first operational amplifier 146
is connected to an anode of the first diode 148 through the first resistor 150. A
cathode of the first diode 148 is connected with an output terminal of the first operational
amplifier 146. A non-inverting input terminal of the first operational amplifier 146
is applied with a reference voltage Vref which is generated by the reference voltage
source 160. A voltage applied to the anode of the first diode 148 is called "offset
voltage Voffset". As will be described later, the offset voltage Voffset corresponds
to the hysteresis width ΔI, and the hysteresis width ΔI becomes larger as the offset
voltage Voffset is higher.
[0033] In resistance values around the first operational amplifier 146, values of the first
resistor 150 and the second resistor 152 which determine a gain are set to be sufficiently
larger than values of the third resistor 154, the fourth resistor 156, and the fifth
resistor 158 which are differentials from the reference voltage Vref so that a feedback
current does not affect the differentials from the reference voltage Vref.
[0034] FIG. 3 is a graph illustrating a relationship between the absolute value of the drive
voltage Vout and the offset voltage Voffset. When the absolute value of the drive
voltage Vout having the negative polarity is small, because a voltage across a common
connection node of the third resistor 154, the fourth resistor 156, and the fifth
resistor 158 is larger than the reference voltage Vref, the first operational amplifier
146 conducts a current sink, and the offset voltage Voffset becomes small. The offset
voltage Voffset becomes maximum when the voltage across the common connection node
becomes equal to the reference voltage Vref.
[0035] In order to realize a control that the hysteresis width ΔI, that is, the offset voltage
Voffset becomes maximum when the absolute value of the drive voltage Vout becomes
the voltage threshold value Vth, the reference voltage Vref is set to the voltage
across the common connection node when the absolute value of the drive voltage Vout
is equal to the voltage threshold value Vth. In particular, when the set value of
the flyback regulator 102 is -100V, the reference voltage Vref is set to the voltage
across the common connection node when the drive voltage Vout=-Vth=-50V is satisfied.
[0036] When the absolute value of the drive voltage Vout becomes larger than the voltage
threshold value Vth, the action of the first operational amplifier 146 is disabled,
and the voltage across the common connection node becomes the offset voltage Voffset
as it is. The hysteresis width setting circuit 138 transmits the offset voltage Voffset
that is changed into an inverted V-shape responsive to the absolute value of the drive
voltage Vout to the downconverter driver circuit 136 to control the hysteresis width
ΔI, and allows a switching frequency of the downconverter 104 to fall within a given
range.
[0037] FIG. 4 is a circuit diagram illustrating a configuration of the downconverter driver
circuit 136. The downconverter driver circuit 136 includes a second operational amplifier
162, a comparator 164, a gate driver 166, a first current mirror circuit 170, a seventh
resistor 172, an eighth resistor 174, a tenth resistor 178, a twelfth resistor 182,
a thirteenth resistor 184, a first npn bipolar transistor 190, a third switching element
202, a fourth switching element 204, and a second current mirror circuit 206.
[0038] A non-inverting input terminal of the second operational amplifier 162 is applied
with the offset voltage Voffset. An output terminal of the second operational amplifier
162 is connected to a base of the first npn bipolar transistor 190, and an inverting
input terminal of the second operational amplifier 162 is connected with an emitter
of the first npn bipolar transistor 190. One end of the eighth resistor 174 is connected
to the emitter of the first npn bipolar transistor 190, and the other end of the eighth
resistor 174 is grounded. A collector of the first npn bipolar transistor 190 is connected
to the first current mirror circuit 170 through the seventh resistor 172.
[0039] The first current mirror circuit 170 includes a sixth resistor 168, a ninth resistor
176, an eleventh resistor 180, a first pnp bipolar transistor 192, a second pnp bipolar
transistor 194, and a third pnp bipolar transistor 196. Those circuit elements are
connected to each other to configure a known current mirror circuit. The first current
mirror circuit 170 receives a current that flows in the seventh resistor 172, and
outputs a current that flows in the tenth resistor 178, and a current that flows in
the third switching element 202, and makes a magnitude of the input current substantially
equal to a magnitude of the output current.
[0040] The second current mirror circuit 206 includes a fourteenth resistor 186, a fifteenth
resistor 188, a second npn bipolar transistor 198, and a third npn bipolar transistor
200. Those circuit elements are connected to each other to configure a known current
mirror circuit. The second current mirror circuit 206 receives a current that flows
in the tenth resistor 178, and outputs a current that flows in the fourth switching
element 204, and makes a magnitude of the input current substantially equal to a magnitude
of the output current.
[0041] The third switching element 202 is formed of, for example, a p-channel MOSFET. The
fourth switching element 204 is formed of, for example, an n-channel MOSFET. A source
of the third switching element 202 is connected to the first current mirror circuit
170. A gate of the third switching element 202 is connected to an inverting output
terminal of the comparator 164. A drain of the third switching element 202 is connected
to a drain of the fourth switching element 204. A gate of the fourth switching element
204 is connected to the inverting output terminal of the comparator 164. A source
of the fourth switching element 204 is connected to the second current mirror circuit
206.
[0042] The twelfth resistor 182 and the thirteenth resistor 184 are connected in series
between the control supply voltage Vcc and the ground potential in the stated order.
A connection node between the twelfth resistor 182 and the thirteenth resistor 184
is connected to a connection node between a drain of the third switching element 202
and a drain of the fourth switching element 204. The connection node between the drain
of the third switching element 202 and the drain of the fourth switching element 204
is connected to the non-inverting input terminal of the comparator 164. The inverting
input terminal of the comparator 164 is applied with a voltage drop Vm.
[0043] A non-inverting output terminal of the comparator 164 is connected to the gate driver
166. The gate driver 166 matches a phase of the downstream control signal S2 with
a phase of a signal that appears in the non-inverting output terminal of the comparator
164. That is, the gate driver 166 sets the downstream control signal S2 to high level
(low level) when the signal appearing in the non-inverting output terminal of the
comparator 164 become high level (low level).
[0044] The second operational amplifier 162 and the first npn bipolar transistor 190 which
receive the offset voltage Voffset output a current of Voffset/(resistance value of
the eighth resistor 174). This current is sunk or sourced into a voltage division
node between the twelfth resistor 182 and the thirteenth resistor 184 by a phase of
an output of the comparator 164 that receives the voltage drop Vm. In the third switching
element 202 and the fourth switching element 204 configuring a bridge, at timing when
a gate of the second switching element 140 is high level (second switching element
140 is on), the third switching element 202 turns on, and a voltage at the voltage
division node between the twelfth resistor 182 and the thirteenth resistor 184 is
raised to set the current upper limit value Ith1. When the drive current lout is raised,
and reaches the current upper limit value Ith1, the fourth switching element 204 turns
on at substantially the same time when the gate of the second switching element 140
becomes low level (the second switching element 140 is off). The voltage at the voltage
division node between the twelfth resistor 182 and the thirteenth resistor 184 is
lowered to set the current lower limit value Ith2.
[0045] A mean value of the drive current lout is set by a divided voltage between the twelfth
resistor 182 and the thirteenth resistor 184. Also, because the sink/source current
becomes larger as the absolute value of the drive voltage Vout is closer to the voltage
threshold value Vth due to the action of the hysteresis width setting circuit 138,
the current upper limit value Ith1 - the current lower limit value Ith2 = the hysteresis
width ΔI becomes larger. The hysteresis width ΔI is smaller as the absolute value
of the drive voltage Vout is farther from the voltage threshold value Vth. As will
be described later, this acts so that the switching frequency of the downconverter
104 falls within a given range.
[0046] Returning to FIG. 1, the semiconductor light source control device 100 is configured
to control the N LEDs 2-1 to 2-N to turn on/off, individually. The bypass driver circuit
112 generates N lighting on/off control signals Sc1 to ScN for controlling the on/off
operation of the respective LEDs 2-1 to 2-N. The bypass driver circuit 112 controls
the levels of the respective N lighting on/off control signals Sc1 to ScN so as to
obtain a desired brightness or light distribution pattern, individually. Specifically,
the bypass driver circuit 112 sets the first lighting on/off control signal Sc1 to
low level when the first LED 2-1 is turned on, and sets the first lighting on/off
control signal Sc1 to high level when the first LED 2-1 is turned off. The same is
applied to the second lighting on/off control signal Sc2 to the N
th lighting on/off control signal ScN. The bypass driver circuit 112 outputs the respective
lighting on/off control signals Sc1 to ScN to the corresponding bypass circuits 270-1
to 270-N.
[0047] The first bypass circuit 270-1 to the N
th bypass circuit 270-N are connected in parallel to the first LED 2-1 to the N
th LED 2-N, respectively. The first bypass circuit 270-1 to the N
th bypass circuit 270-N are connected in series between a high potential side output
terminal and a low potential side output terminal of the downconverter 104 in the
stated order.
[0048] The first bypass circuit 270-1 performs electric continuity between both ends of
the first LED 2-1, that is, connects both ends of the first LED 2-1 to each other
by an impedance lower than that of the first LED 2-1 when the first lighting on/off
control signal Sc1 is high level. With this configuration, the first LED 2-1 is turned
off. Hereinafter, a state of the bypass circuits that turn off the LEDs is called
"bypass-on state". The first bypass circuit 270-1 connects both ends of the first
LED 2-1 to each other by an impedance higher than that of the first LED 2-1 when the
first lighting on/off control signal Sc1 is low level. With this configuration, the
first LED 2-1 turns on. Hereinafter, a state of the bypass circuits that turn on the
LEDs is called "bypass-off state".
[0049] The first bypass circuit 270-1 generates a first abnormality detection signal Sdet1
for detecting the abnormality of the first LED 2-1 and lines around the first LED
2-1, and supplies the first abnormality detection signal Sdet1 to the bypass driver
circuit 112. If the first abnormality detection signal Sdet1 is high level, a voltage
to be applied to the first bypass circuit 270-1 when the first bypass circuit 270-1
is in the bypass-off state is lower than a short-circuit detection voltage, or higher
than a disconnection detection voltage higher than the short-circuit detection voltage.
The short-circuit detection voltage is set to be lower than the forward drop voltage
Vf of one LED. The disconnection detection voltage is set to be higher than the forward
drop voltage Vf of the LED, and lower than a sum 2Vf of the forward drop voltages
of two LEDs.
[0050] Similarly, the second bypass circuit 270-2 to the N
th bypass circuit 270-N control the on/off state of the second LEDs 2-2 to the N
th LED 2-N on the basis of the second lighting on/off control signals Sc2 to the N
th lighting on/off control signal ScN, respectively. Also, the second bypass circuit
270-2 to the Nth bypass circuit 270-N generate second abnormality detection signal
Sdet2 to N
th abnormality detection signal SdetN, respectively, and supply those abnormality detection
signals to the bypass driver circuit 112.
[0051] When the brightness of the first LED 2-1 is dimmed in the normal light-up state,
the bypass driver circuit 112 changes the first lighting on/off control signal Sc1
at a dimming frequency f1 of several hundred Hz to several kHz cyclically, that is,
in a rectangular waveform. The first LED 2-1 blinks at the dimming frequency f1 by
the pulse modulation of the first lighting on/off control signal Sc1, and the brightness
visible by human's eyes is dimmed. A duty ratio of the first lighting on/off control
signal Sc1 is set to obtain a desired degree of light mission. In this case, since
a variation in a magnitude of the driver circuit that flows in the first LED 2-1 when
the turning on the first LED 2-1 is suppressed, color shift is suppressed. Similarly,
the bypass driver circuit 112 has a PWM (pulse width modulation) dimming function
for the respective second LED 2-2 to N
th LED 2-N.
[0052] The bypass driver circuit 112 determines whether an abnormality is generated in the
first LED 2-1 and the lines around the first LED 2-1, or not, on the basis of the
first abnormality detection signal Sdet1. The bypass driver circuit 112 determines
that the abnormality is generated when the first abnormality detection signal Sdet1
becomes high level, and forcedly sets the first lighting on/off control signal Sc1
to the high level. For example, the bypass driver circuit 112 keeps the first lighting
on/off control signal Sc1 in the high level, even in a period when the first lighting
on/off control signal Sc1 is to be set to the low level according to the PWM dimming
function. Alternatively, the bypass driver circuit 112 sets the first lighting on/off
control signal Sc1 to the high level, even in a period when the first lighting on/off
control signal Sc1 is to be set to the low level if it is not determined that the
abnormality is generated. The bypass driver circuit 112 also has the same abnormality
detection function for the respective second LED 2-2 to N
th LED 2-N.
[0053] A first bypass connection line 280-1 connects a first bypass side connection node
NB1 between the first bypass circuit 270-1 and the second bypass circuit 270-2, and
a first load side connection node NL1 I between the first LED 2-1 and the second LED
2-2. When the first bypass circuit 270-1 is in the bypass-off state, and the second
bypass circuit 270-2 is in the bypass-on state, the polarity of the drive current
lout flowing in the first bypass connection line 280-1 trends from a load side toward
a bypass side. When the first bypass circuit 270-1 is in the bypass-on state, and
the second bypass circuit 270-2 is in the bypass-off state, the polarity of the drive
current lout flowing in the first bypass connection line 280-1 trends from the bypass
side toward the load side. Therefore, the polarity of the drive current lout flowing
in the first bypass connection line 280-1 in the former case is opposite to the polarity
of the drive current lout flowing in the first bypass connection line 280-1 in the
latter case.
[0054] The same is applied to the second bypass connection line 280-2 to (N-1)
th bypass connection line 280-(N-1).
[0055] If the poor continuity is generated in the bypass connection line, the bypass driver
circuit 112, and the first bypass circuit 270-1 to the N
th bypass circuit 270-N are configured so that both of the two bypass circuits connected
to the bypass connection lines are forcedly brought into the bypass-on state.
[0056] FIG. 5 is a circuit diagram illustrating configurations of the second bypass circuit
270-2 and the third bypass circuit 270-3. The second bypass circuit 270-2 includes
a second switch level shift circuit 254-2, a second bypass/limiter circuit 250-2,
a second disconnection detector circuit 272-2, a second short-circuiting detector
circuit 274-2, a second detection signal level shift circuit 276-2, and a second integrating
circuit 278-2.
[0057] The second switch level shift circuit 254-2 receives the second lighting on/off control
signal Sc2 from the bypass driver circuit 112, and converts the second lighting on/off
control signal Sc2 into a second bypass switch drive signal Sd2 with a voltage across
the cathode of the second LED 2-2 as a standard, that is, a low level. A phase of
the second bypass switch drive signal Sd2 matches a phase of the second lighting on/off
control signal Sc2, and the low level of the second bypass switch drive signal Sd2
becomes the voltage of the cathode of the second LED 2-2. Thus, the second switch
level shift circuit 254-2 shifts the level of the second lighting on/off control signal
Sc2, and supplies the signal to the corresponding second bypass/limiter circuit 250-2.
[0058] The second bypass/limiter circuit 250-2 includes a second bypass switch 110-2 which
is connected in parallel to the second LED 2-2. If the second bypass switch drive
signal Sd2 is high level (low level), the second bypass/limiter circuit 250-2 turns
on (off) the second bypass switch 110-2 to turn on (off) the second LED 2-2. Further,
when the second bypass switch drive signal Sd2 is low level, the second bypass/limiter
circuit 250-2 is configured to limit an upper limit of a voltage between both ends
of the second bypass switch 110-2 with the use of the second bypass switch 110-2.
[0059] The second bypass/limiter circuit 250-2 includes a limiter zener diode 256, a backflow
prevention diode 258, a sixteenth resistor 260, and the second bypass switch 110-2.
The second bypass switch 110-2 is formed of, for example, an N-channel MOSFET.
[0060] A cathode of the limiter zener diode 256 is connected to a drain of the second bypass
switch 110-2. A connection node therebetween is connected to the first bypass connection
line 280-1. An anode of the limiter zener diode 256 is connected to an anode of the
backflow prevention diode 258. The second bypass switch drive signal Sd2 is input
to a gate of the second bypass switch 110-2 through the sixteenth resistor 260. A
source of the second bypass switch 110-2 is connected to the second bypass connection
line 280-2.
[0061] A series circuit of the limiter zener diode 256 and the backflow prevention diode
258 is connected to the gate side of the second bypass switch 110-2 with respect to
the second bypass switch drive signal Sd2 that turns on/off the second bypass switch
110-2. That is, a cathode of the backflow prevention diode 258 is connected between
the sixteenth resistor 260 and the gate of the second bypass switch 110-2.
[0062] If it is assumed that a zener voltage of the limiter zener diode 256 is 6V, the forward
drop voltage Vf of the backflow prevention diode 258 is 0.5V, and a gate threshold
voltage of the second bypass switch 110-2 is 2.5V, when the voltage between both ends
of the second bypass switch 110-2, that is, a drain-source voltage reaches 9V, the
second bypass switch 110-2 starts to turn on. Therefore, an upper limit value of the
voltage between both ends of the second bypass switch 110-2, that is, the disconnection
detection voltage becomes 9V.
[0063] The zener voltage of the limiter zener diode 256 is set so that the disconnection
detection voltage becomes higher than a maximum value of the forward drop voltage
Vf of the second LED 2-2, becomes lower than the zener voltage defined by the second
electrostatic protection zener diodes 252-2, and becomes lower than a sum of the forward
drop voltage Vf of the second LED 2-2, and the forward drop voltage Vf of the third
LED 2-3. For example, if the respective LEDs have substantially the same characteristics,
when the maximum of the forward drop voltage Vf of the LEDs is 6V, and the zener voltage
of the second electrostatic protection zener diodes 252-2 is 20V, the zener voltage
of the limiter zener diode 256 is set to range from 3V to 9V.
[0064] The backflow prevention diode 258 is configured to prevent the second bypass switch
drive signal Sd2 from inhibiting the on/off operation of the second bypass switch
110-2. For example, when the second LED 2-2 that is connected in parallel to the backflow
prevention diode 258 is turned off, or the second bypass switch 110-2 is forcedly
turned on as measures against the disconnection or the contact failure which will
be described later, if there is no backflow prevention diode 258, the gate voltage
of the second bypass switch 110-2 is reduced through the second bypass switch 110-2
which is in the on-state from a forward direction of the limiter zener diode 256.
The backflow prevention diode 258 prevents this status from occurring.
[0065] The second disconnection detector circuit 272-2 determines whether the poor continuity
is generated on a route of the drive current lout that passes through the second LED
2-2, or not, when the second bypass switch 110-2 is off (that is, non-conduction state).
The second short-circuiting detector circuit 274-2 determines whether a short-circuiting
abnormality is generated in the second LED 2-2 or between the lines when the second
bypass switch 110-2 is off, or not. If the abnormality is detected in the second disconnection
detector circuit 272-2 or the second short-circuiting detector circuit 274-2, an integration
capacitor 282 of the second integrating circuit 278-2 is charged by a first time constant
through the second detection signal level shift circuit 276-2. This charging operation
is continued in a period when the second bypass switch drive signal Sd2 is low level,
and the abnormality is detected in the second disconnection detector circuit 272-2
or the second short-circuiting detector circuit 274-2. In other periods, the integration
capacitor 282 is discharged by a second time constant longer than the first time constant.
[0066] The second detection signal level shift circuit 276-2 includes a seventeenth resistor
284, an eighteenth resistor 286, and a fourth pnp bipolar transistor 288. One end
of the seventeenth resistor 284 is connected to an emitter of the fourth pnp bipolar
transistor 288. A connection node therebetween is applied with the control supply
voltage Vcc. The other end of the seventeenth resistor 284 is connected to one end
of the eighteenth resistor 286. A connection node therebetween is connected to a base
of the fourth pnp bipolar transistor 288.
[0067] The second disconnection detector circuit 272-2 includes a 23
rd resistor 210, and a sixth npn bipolar transistor 212. A collector of the sixth npn
bipolar transistor 212 is connected to the other end of the eighteenth resistor 286.
A base of the sixth npn bipolar transistor 212 is connected to the connection node
between the anode of the limiter zener diode 256 and the anode of the backflow prevention
diode 258 through the 23rd resistor 210. An emitter of the sixth npn bipolar transistor
212 is connected to the second bypass connection line 280-2.
[0068] The second short-circuiting detector circuit 274-2 includes a nineteenth resistor
290, a twenty resistor 292, a 21
st resistor 294, a 22
nd resistor 296, a fourth npn bipolar transistor 298, and a fifth npn bipolar transistor
208. The twenty resistor 292 and the 22nd resistor 296 are connected in series between
the first bypass connection line 280-1 and the second bypass connection line 280-2
in the stated order. A connection node between the twenty resistor 292 and the 22
nd resistor 296 is connected to one end of the 21st resistor 294 and a base of the fourth
npn bipolar transistor 298. The other end of the 21
st resistor 294 is connected to the cathode of the backflow prevention diode 258. An
emitter of the fourth npn bipolar transistor 298 is connected to the second bypass
connection line 280-2. A collector of the fourth npn bipolar transistor 298 is connected
to one end of the nineteenth resistor 290. The other end of the nineteenth resistor
290 is applied with the control supply voltage Vcc. A connection node between the
collector of the fourth npn bipolar transistor 298 and the nineteenth resistor 290
is connected to the base of the fifth npn bipolar transistor 208. The emitter of the
fifth npn bipolar transistor 208 is connected to the second bypass connection line
280-2, and a collector of the fifth npn bipolar transistor 208 is connected to the
other end of the eighteenth resistor 286.
[0069] The second integrating circuit 278-2 includes the integration capacitor 282, a 24
th resistor 214, and a 25
th resistor 216. One end of the 24
th resistor 214 is grounded to a ground potential which is substantially equal to a
ground potential of a microcomputer, and the other end of the 24
th resistor 214 is connected to one end of the 25
th resistor 216. A connection node between the 24
th resistor 214 and the 25
th resistor 216 is connected to a collector of the fourth pnp bipolar transistor 288.
The other end of the 25
th resistor 216 is connected to one end of the integration capacitor 282. The other
end of the integration capacitor 282 is grounded to a ground potential which is substantially
equal to the ground potential of the microcomputer. A voltage across one end of the
integration capacitor 282 is applied to the bypass driver circuit 112 as the second
abnormality detection signal Sdet2.
[0070] If the poor continuity is generated on the route of the drive current lout, the voltage
between both ends of the second bypass switch 110-2 is raised over the forward drop
voltage Vf during the off-period of the second bypass switch 110-2. If the voltage
between both ends thereof exceeds the disconnection detection voltage, a current flows
into the limiter zener diode 256. Then, the sixth npn bipolar transistor 212 of the
second disconnection detector circuit 272-2 turns on.
[0071] Also, if the second LED 2-2 is short-circuited, the voltage between both ends of
the second bypass switch 110-2 becomes lower than the forward drop voltage Vf during
the off-period of the second bypass switch 110-2. If the voltage between both ends
thereof becomes lower than a short-circuit detection voltage, the fourth npn bipolar
transistor 298 of the second short-circuiting detector circuit 274-2 turns off, and
the fifth npn bipolar transistor 208 turns on.
[0072] The respective resistance values of the twenty resistor 292, the 21
st resistor 294, and the 22
nd resistor 296 are set to satisfy the following three conditions.
- (1) When the other end of the 21st resistor 294 is supplied with the signal of the high level, the fourth npn bipolar
transistor 298 turns on.
- (2) When the other end of the 21st resistor 294 is supplied with the signal of the low level, and the voltage between
both ends of the second bypass switch 110-2 is the short-circuit detection voltage
or higher, the fourth npn bipolar transistor 298 turns on.
- (3) When the other end of the 21st resistor 294 is supplied with the signal of the low level, and the voltage between
both ends of the second bypass switch 110-2 is lower than the short-circuit detection
voltage, the fourth npn bipolar transistor 298 turns off.
[0073] When any one of the sixth npn bipolar transistor 212 and the fifth npn bipolar transistor
208 turns on, the fourth pnp bipolar transistor 288 of the second detection signal
level shift circuit 276-2 turns on. The control supply voltage Vcc is a positive voltage
with the ground potential of the microcomputer as a standard. If an abnormality is
detected in the second disconnection detector circuit 272-2 or the second short-circuiting
detector circuit 274-2, the control supply voltage Vcc is applied to the second integrating
circuit 278-2. The integration capacitor 282 is charged through the 25th resistor
216, and discharged through the 24
th resistor 214 and the 25
th resistor 216. When a resistance value of the 24
th resistor 214 is set to be larger than a resistance value of the 25
th resistor 216, the abnormality can be detected even in a dimming state where a period
(that is, off-period of the second bypass switch 110-2) for abnormality detection
is short such as a mean current 10% light-up (on state of the second bypass switch
110-2 is 90%, off state thereof is 10%).
[0074] The third bypass circuit 270-3 is configured in the same manner as that of the second
bypass circuit 270-2. The third bypass circuit 270-3 includes a third switch level
shift circuit 254-3 corresponding to the second switch level shift circuit 254-2,
a third bypass/limiter circuit 250-3 corresponding to the second bypass/limiter circuit
250-2, a third disconnection detector circuit 272-3 corresponding to the second disconnection
detector circuit 272-2, a third short-circuiting detector circuit 274-3 corresponding
to the second short-circuiting detector circuit 274-2, a third detection signal level
shift circuit 276-3 corresponding to the second detection signal level shift circuit
276-2, and a third integrating circuit 278-3 corresponding to the second integrating
circuit 278-2.
[0075] The first bypass circuit 270-1, the fourth bypass circuit 270-4 to the N
th bypass circuit 270-N are configured in the same manner as that of the second bypass
circuit 270-2.
[0076] The operation of the semiconductor light source control device 100 configured as
described above will be described.
[0077] FIGS. 6A to 6C are graphs illustrating a time variation of the drive current lout.
Let us consider a status in which only one LED is first turned on, about half of the
LEDs are then turned on, and all of the LEDs are thereafter turned on. In this case,
the PWM dimming is not considered. FIG. 6A illustrates a time variation of the drive
current lout when only one LED is turned on, and the remaining (N-1) LEDs are turned
off by turning on the corresponding bypass switches. FIG. 6B illustrates a time variation
of the drive current lout when about half of the LEDs, that is N/2 LEDs are turned
on, and the remaining LEDs are turned off. FIG. 6C illustrates a time variation of
the drive current lout when all of the LEDs are turned on.
[0078] FIGS. 6A to 6C illustrate a case in which the hysteresis width ΔI is adjusted so
that the switching frequency, that is, a switching cycle Ts of the second switching
element 140 is kept substantially constant, without depending on the number of lighting
of the LEDs and the number of extinction of the LEDs. However, an ordinary skilled
person that reads the present invention would understand that, in this embodiment,
the hysteresis width ΔI is so controlled as to suppress a change in the switching
cycle Ts caused by a change in the number of lighting of the LEDs and the number of
extinction of the LEDs.
[0079] Referring to FIG. 6A, if the number of lighting of the LEDs is small, the drive current
lout is relatively quickly raised in an on-time Ton of the second switching element
140, and the drive current lout is relatively slowly lowered in an off-time Toff of
the second switching element 140. The hysteresis width in this case is expressed as
"ΔI1". An absolute value of the drive voltage Vout is relatively low, and the offset
voltage Voffset generated by the hysteresis width setting circuit 138 is also relatively
low.
[0080] Referring to FIG. 6B, when the number of lighting of the LEDs and the number of
extinction of the LEDs are substantially equal to each other, the drive voltage Vout
is about half of the setting voltage of the flyback regulator 102, and the on-time
Ton and the off-time Toff of the second switching element 140 balance with each other.
A speed of the overall change in the drive current lout is larger than that when the
number of lighting of the LEDs is small.
[0081] The hysteresis width setting circuit 138 allows the higher offset voltage Voffset
to be generated as illustrated in FIG. 3. The downconverter driver circuit 136 receives
the high offset voltage Voffset, and makes a hysteresis width ΔI2 larger than a hysteresis
width ΔI1 when the number of lighting of the LEDs is 1. As a result, an increment
in the speed of the overall change of the drive current lout is offset, and the switching
cycle Ts is kept substantially constant.
[0082] Referring to FIG. 6C, when the number of extinction of the LEDs is small or null,
the drive current lout is relatively slowly raised in the on-time Ton of the second
switching element 140, and the drive current lout is relatively quickly lowered in
the off-time Toff of the second switching element 140. The speed of the overall change
of the drive current lout becomes smaller than that when the number of lighting of
the LEDs and the number of extinction of the LEDs balance with each other. The absolute
value of the drive voltage Vout is relatively high, and the offset voltage Voffset
generated by the hysteresis width setting circuit 138 is also relatively low.
[0083] The downconverter driver circuit 136 receives the low offset voltage Voffset, and
makes a hysteresis width ΔI3 smaller than the hysteresis width ΔI2 when the number
of lighting of the LEDs and the number of extinction of the LEDs balance with each
other. As a result, a decrement in the speed of the overall change of the drive current
lout is offset, and the switching cycle Ts is kept substantially constant.
[0084] FIG. 7 is a timing chart illustrating a change in the second bypass switch drive
signal Sd2 and the second abnormality detection signal Sdet2 in a PWM dimming state.
In this example, the second bypass switch drive signal Sd2 corresponds to the mean
current 20% lighting. That is, the off-time Toff of a period during which the second
bypass switch drive signal Sd2 is low level is about 1/4 of the on-time Ton of a period
during which the second bypass switch drive signal Sd2 is high level.
[0085] If no abnormality is generated, the second abnormality detection signal Sdet2 is
kept constant in the vicinity of the ground potential of the microcomputer, that is,
0V, without depending on a change in the second bypass switch drive signal Sd2. In
this case, it is assumed that the poor continuity or the disconnection is generated
at a time t1 during the period when the second bypass switch drive signal Sd2 is high
level. At the time t1, since the second bypass switch drive signal Sd2 is high level,
that is, the second bypass switch 110-2 is on (that is, conduction state), both of
the sixth npn bipolar transistor 212 and the fifth npn bipolar transistor 208 are
kept off as they are. Therefore, the potential of the second abnormality detection
signal Sdet2 is not substantially changed.
[0086] At a time t2 when the second bypass switch drive signal Sd2 transitions from the
high level to the low level, any one of the sixth npn bipolar transistor 212 and the
fifth npn bipolar transistor 208 is turned on due to the generated abnormality, and
the integration capacitor 282 starts to be charged.
[0087] At a time t3 during a period when the second bypass switch drive signal Sd2 is low
level, the integration capacitor 282 is fully charged. A voltage of the second abnormality
detection signal Sdet2 when the integration capacitor 282 is fully charged is higher
than a level threshold value Vg for determining a level of the second abnormality
detection signal Sdet2 in the bypass driver circuit 112.
[0088] At a time t4 when the second bypass switch drive signal Sd2 transitions from the
low level to the high level, both of the sixth npn bipolar transistor 212 and the
fifth npn bipolar transistor 208 turn off, and the integration capacitor 282 starts
to be discharged.
[0089] After the time t3, although the second abnormality detection signal Sdet2 is higher
than the level threshold value Vg, an operating speed of the bypass driver circuit
112 which is the microcomputer is relatively low. Therefore, the level transition
of the second bypass switch drive signal Sd2 is continued for a while.
[0090] At a t5 when the second bypass switch drive signal Sd2 then transitions from the
high level to the low level, if the generated abnormality is continued, the integration
capacitor 282 starts to be again charged. Therefore, the integration capacitor 282
is again fully charged.
[0091] The second time constant for the discharge of the integration capacitor 282 is set
to be longer than the first time constant for the charge of the integration capacitor
282. Therefore, even in a period between the time t4 when the second bypass switch
drive signal Sd2 is high level, and the time t5, the voltage of the second abnormality
detection signal Sdet2 is kept higher than the level threshold value Vg. Thus, after
the second bypass switch drive signal Sd2 has repeated the level transition several
times, the bypass driver circuit 112 determines that the second abnormality detection
signal Sdet2 has transitioned from the low level to the high level.
[0092] Also, referring to FIG. 7, a case in which the integration capacitor 282 reaches
a fully charged state in one off-period of the second bypass switch 110-2 has been
described. However, the present invention is not limited to this configuration, but
the integration capacitor 282 may come close to the fully charged state every time
the off-period is repeated.
[0093] A description will be given of the operation of the semiconductor light source control
device 100 when the poor continuity is generated in any one of the first bypass connection
line 280-1 to the (N-1)
th bypass connection line 280-(N-1). As an example, let us consider a case in which
the poor continuity is generated in the second bypass connection line 280-2, that
is, a case in which the poor continuity is generated at a portion of a mark "X" indicated
by reference numeral 218 shown in FIG. 5.
[0094] If the poor continuity is generated in the second bypass connection line 280-2, the
potential of the connection node between the source of the second bypass switch 110-2
and the drain of the third bypass switch 110-3 floats. When both of the second bypass
switch 110-2 and the third bypass switch 110-3 are off, the potential of the connection
node comes closer to the potential of the source of the second bypass switch 110-2
or the potential of the drain of the third bypass switch 110-3 due to a difference
in a characteristic between the second bypass switch 110-2 and the third bypass switch
110-3. Then, for example, when the potential of the connection node comes sufficiently
closer to the potential of the drain of the third bypass switch 110-3, it is determined
that short-circuit failure is generated by the third short-circuiting detector circuit
274-3. A third abnormality detection signal Sdet3 becomes high level, and the bypass
driver circuit 112 fixes a third lighting on/off control signals Sc3 to the high level.
[0095] Then, the third bypass switch 110-3 turns on, and a voltage between both ends of
the second bypass switch 110-2 becomes substantially 2Vf. Since the disconnection
detection voltage is lower than 2Vf, the second disconnection detector circuit 272-2
detects that the poor continuity is generated. The second abnormality detection signal
Sdet2 becomes high level, and the bypass driver circuit 112 fixes the second lighting
on/off control signal Sc2 to the high level.
[0096] As a result of the above, both of the second bypass switch 110-2 and the third bypass
switch 110-3 are forcedly turned on to maintain both of the second LED 2-2 and the
third LED 2-3 in an extinction state.
[0097] When the potential of the connection node between the source of the second bypass
switch 110-2 and the drain of the third bypass switch 110-3 comes close to the potential
of the source of the second bypass switch 110-2, the second short-circuiting detector
circuit 274-2 detects the short-circuit abnormality, the third disconnection detector
circuit 272-3 detects the disconnection abnormality, and both of the second bypass
switch 110-2 and the third bypass switch 110-3 are forcedly turned on.
[0098] If the second bypass switch drive signal Sd2 is set to the low level to turn on the
second LED 2-2, and the third bypass switch drive signal Sd3 is set to the high level
to turn off the third LED 2-3 without forcedly turning on both of those two bypass
switches, the third bypass switch 110-3 turns on, and the drive current lout does
not flow into the third bypass switch 110-3, but flows in the third LED 2-3. That
is, the third LED 2-3 cannot be turned off. If the second bypass switch drive signal
Sd2 is set to the high level, and the third bypass switch drive signal Sd3 is set
to the low level, the second bypass switch 110-2 turns on, and the drive current lout
does not flow in the second bypass switch 110-2, but flows in the second LED 2-2.
That is, the second LED 2-2 cannot be turned off.
[0099] Thus, if the poor continuity is generated in the second bypass connection line 280-2,
it is difficult to control the respective lighting on/off states of the second LED
2-2 and the third LED 2-3, individually.
[0100] In the semiconductor light source control device 100 according to this embodiment,
if the poor continuity is generated in any one of the first bypass connection line
280-1 to the (N-1)
th bypass connection line 280-(N-1), both of the two bypass switches connected to the
bypass connection line in which the poor continuity is generated are forcedly turned
on. As a result, both of the two LEDs connected to the bypass connection line are
turned off.
[0101] If the poor continuity is generated in the bypass connection line, it is difficult
to control the respective lighting on/off states of the two LEDs connected to the
bypass connection line, individually, as described above. For example, let us consider
a case in which the semiconductor light source control device 100 is intended for
the high beam of the vehicle headlights, and the semiconductor light source control
device 100 has a function of turning off the appropriate LED so as not to give a preceding
vehicle and an oncoming vehicle glare. In this case, if the poor continuity is generated
in the bypass connection line connected to the appropriate LED, the appropriate LED
cannot be turned off, and the preceding vehicle and the oncoming vehicle may be given
glare. Under the circumstances, in this embodiment, if the poor continuity is generated
in the bypass connection line, both of the two bypass switches connected to the bypass
connection line are forcedly turned on. As a result, the bypass connection line in
which the poor continuity is generated becomes irrelevant to a bypass route of the
drive current lout, and the appropriate LED can be maintained in the extinction state.
As a result, glaring can be avoided.
[0102] Also, the semiconductor light source control device 100 according to this embodiment
has a PWM dimming function of turning on/off the bypass switch at a relative high
speed to adjust the brightness of the corresponding LED. When the bypass switch is
on, the voltage between both ends of the bypass switch comes close to 0V. However,
this is not abnormal, and therefore should not be determined as the short-circuit
abnormality. Under the circumstance, the semiconductor light source control device
100 does not conduct the short-circuit abnormality detection and the disconnection
abnormality detection when the bypass switch is on, and detects the short-circuit
and the disconnection abnormality when the bypass switch is off.
[0103] Therefore, if the abnormality is detected in the PMW dimming LED or the lines, there
is a need to determine the abnormality while a state in which the abnormality appears
when the bypass switch is off, and a state in which the bypass switch turns on regardless
of whether the abnormality is present, or not, are repeated at a high speed. A microcomputer
is frequently used as a main device that controls the on/off operation of the LEDs,
and the PWM dimming function. Since the microcomputer usually operates at relatively
long time intervals such as about several tens msec, the microcomputer is not suited
for picking up only the respective abnormalities of a large number of LEDs at a high
speed for determination. For example, if the dimming frequency f1 is several kHz,
and the LEDs are turned on with the mean current 10%, a length of the off-period of
the bypass switch is several hundred micro second order. Thus, in order to determine
the abnormality/normality in the relatively short period, there is a need to employ
an expensive microcomputer which is relatively high in operating speed.
[0104] Under the circumstance, in the semiconductor light source control device 100 according
to this embodiment, an abnormality detection signal that becomes high level in an
abnormal state, and low level in a normal state is generated without depending on
the PWM dimming, due to the action of the integrating circuit. The bypass driver circuit
112 that is the microcomputer determines the normality or abnormality on the basis
of the abnormality detection signal. As a result, when the PWM dimming function using
the bypass switch is employed, the abnormality of the LEDs or the lines can be detected
even if the expensive microcomputer is not used.
[0105] Also, according to the semiconductor light source control device 100 of this embodiment,
even if the poor continuity such as the contact failure or the disconnection is generated
on the route of the drive current lout, the voltage to be applied to the bypass switch
can be prevented from being raised. For example, let us consider a case in which when,
for example, the first LED 2-1 is in the lighting state, that is, the first bypass
switch 110-1 is off, the contact failure or the disconnection is generated in a line
upstream of the connection node between the anode of the first LED 2-1 and the cathode
of the first electrostatic protection zener diode 252-1, that is, the line of a mark
"X" indicated by reference numeral 262 in the circuit illustrated in FIG. 1.
[0106] When the above contact failure or disconnection is generated, the voltage between
both ends of the first bypass switch is raised, and the first abnormality detection
signal Sdet1 transitions from the low level to the high level. When the bypass driver
circuit 112 detects the above transition of the first abnormality detection signal
Sdet1, the bypass driver circuit 112 determines that the abnormality is generated
in the first LED 2-1, and the circuit illustrated in FIG. 1 takes a countermeasure
to turn on the first bypass switch 110-1 so that the other LEDs can be turned on.
[0107] However, since the operating speed of the bypass driver circuit 112 which is the
microcomputer is relatively low as described above, a time of several tens msec to
several hundred msec is required for the above countermeasure. In this example, if
the semiconductor light source control device has no limiter function of this embodiment,
because no output voltage smoothing capacitor is present, a relatively high voltage
such as several kV (absolute value) determined according to an energy accumulated
in the inductor 144, and a parasitic capacitor of the first bypass switch is output
immediately after the above contact failure or disconnection is generated. This high
voltage is applied to the first bypass switch before the first bypass switch turns
on. Therefore, there is a need to select an element having a withstand voltage of
several kV as the first bypass switch, taking the contact failure or the disconnection
into account, although only a voltage of several V is normally applied in the lighting
state.
[0108] On the contrary, in the semiconductor light source control device 100 having the
limiter function according to this embodiment, when the disconnection or the contact
failure is generated as described above, the drain-source voltage of the first bypass
switch 110-1 is raised. However, a rising of that voltage is limited by the action
of the limiter zener diode 256 and the first bypass switch 110-1 per se. Therefore,
the element having the lower withstand voltage can be selected as the first bypass
switch 110-1 even taking the contact failure or the disconnection into account.
[0109] In this case, when the disconnection or the contact failure is generated, for example,
10V × 1A = about 10 W is applied to the first bypass switch 110-1 for several ten
seconds to several hundred seconds. However, because a device which is small in on-resistance
and large in size to some degree originally needs to be used, an influence on the
device size and the costs is small.
[0110] For example, let us consider a case in which when, for example, the first LED 2-1
is in the lighting state, that is, the first bypass switch 110-1 is off, the contact
failure or the disconnection is generated in a line downstream of the connection node
between the anode of the first LED 2-1 and the cathode of the first electrostatic
protection zener diode 252-1, that is, the line of a mark "X" indicated by reference
numeral 264 in the circuit illustrated in FIG. 1. When the semiconductor light source
control device is equipped with no limiter function of this embodiment, most of an
energy accumulated in the inductor 144 is consumed by the first electrostatic protection
zener diode. As a result, there is a need to select the element that withstands such
a large power consumption as the first electrostatic protection zener diode. Also,
it is conceivable to employ an element having a zener diode higher than a voltage
of several kV which can be generated when the contact failure or the disconnection
is generated as the first electrostatic protection zener diode. However, in general,
if the element has such a high zener voltage, the element cannot perform an original
function of the electrostatic protection.
[0111] On the contrary, in the semiconductor light source control device 100 having the
limiter function of this embodiment, the upper limit value of the voltage between
both ends of the first bypass switch 110-1 is set to be lower than the zener voltage
defined by the first electrostatic protection zener diode 252-1. Therefore, the relatively
small zener diode can be selected as the first electrostatic protection zener diode
252-1.
[0112] Similarly, when the same contact failure or disconnection is generated in any one
of the second LED 2-2 to the N
th LED 2-N, the upper limit of the voltage to be applied to the corresponding bypass
switch or electrostatic protection zener diode is limited. Therefore, the element
having the lower withstand voltage can be employed as the corresponding bypass switch,
and the relatively small zener diode can be employed as the corresponding electrostatic
protection zener diode.
[0113] Also, in the semiconductor light source control device 100 according to this embodiment,
the bypass switches for controlling the on/off operation of the LEDs are also used
as switches for realizing the limiter function for the voltage between both ends of
the LEDs. That is, the bypass switches are shared by the lighting on/off control signal
and the limiter function. As a result, an increase in the number of elements can be
suppressed while realizing the lighting on/off control function and the limiter function.
[0114] In the semiconductor light source control device 100 according to this embodiment,
since no smoothing capacitor is installed on an output stage of the N LEDs 2-1 to
2-N, the following property of the drive current lout to the second switching element
140 becomes excellent. In particular, when the second switching element 140 turns
off, the drive current lout becomes small whereas when the second switching element
140 turns on, the drive current lout becomes large. Then, in order to stabilize the
drive current lout in the vicinity of a target value, the hysteresis control of the
drive current lout is employed instead of smoothing. As a result, a response to a
current feedback can be speeded up. For example, when the number of lighting of the
LEDs is changed by the action of the bypass driver circuit 112 and the bypass switches,
the drive current lout can more rapidly follow a change in the load. In particular,
undershoot of the drive current lout when the number of lighting of the LEDs is increased,
and overshoot of the drive current lout when the number of lighting of the LEDs is
decreased can be suppressed.
[0115] Also, in the semiconductor light source control device 100 according to this embodiment,
the upstream flyback regulator 102 is set as a negative output, and the downstream
downconverter 104 is also set as the negative output. As a result, the N-channel MOSFET
having the more excellent characteristic can be employed as the bypass switch.
[0116] In addition to the above negative outputs, since the inductor 144 is not disposed
between the cathode of the flywheel diode 142 and the output, but disposed between
the anode thereof and the output, the N-channel MOSFET having the more excellent characteristic
can be employed as the second switching element 140 of the downconverter 104. Also,
the drive voltage Vout can be stably detected.
[0117] Also, when the semiconductor light source control device has the positive output,
the drive current is frequently detected on the high side taking a case in which the
LEDs are grounded into account. When the load is changed, since the potential of the
detected portion is also changed, it is difficult to precisely detect the drive current.
Also, the configuration of the detector circuit may be more complicated. Under the
circumstance, in the semiconductor light source control device 100 according to this
embodiment, the negative output is employed, and output on the positive side, that
is, the ground side is equipped with the current detection resistor 108. As a result,
even if the load (drive voltage Vout) is changed, an influence of that change on the
potential of the detected portion of the drive current lout is small, and the drive
current lout can be stably detected. Also, the configuration of the detector circuit
can be simplified.
[0118] In conducting the hysteresis control on the drive current lout, if the input voltage
to the downconverter 104, the drive voltage Vout, or both of those voltages are changed,
since an inclination of the rising or falling of the drive current lout is changed,
the switching frequency of the second switching element 140 can be changed. Under
the circumstance, in the semiconductor light source control device 100 according to
this embodiment, the hysteresis width ΔI is adjusted so that a change in the switching
frequency is suppressed. In particular, a target switching frequency is so set as
to avoid a frequency band of a known radio noise, thereby making it possible to suppress
an adverse effect of the radio noise on the semiconductor light source control device
100.
[0119] Also, in the semiconductor light source control device 100 according to this embodiment,
a variation in the input voltage to the downconverter 104 due to a variation in the
battery voltage Vbat is suppressed by the action of the flyback regulator 102. Therefore,
a change in the switching frequency due to the fluctuation of the input voltage to
the downconverter 104 is suppressed. In other words, there is no need to select the
hysteresis width ΔI by the combination of the input voltage to the downconverter 104
with the drive voltage Vout, and the hysteresis width ΔI can be selected mainly on
the basis of the drive voltage Vout. Therefore, a control for adjusting the hysteresis
width ΔI is simplified. This contributes to a reduction in the scale of the control
signal, and an increase in the processing speed thereof.
[0120] Also, in the semiconductor light source control device 100 according to this embodiment,
the output capacitor 128 is disposed on an output stage of the flyback regulator 102.
If the second switching element 140 is on when the bypass switch turns on, charge
stored in the output capacitor 128 is going to flow in the LEDs at once. However,
since the inductor 144 is disposed on the route of the drive current lout in the semiconductor
light source control device 100, a flow of the charge is smoothed to suppress the
overshoot of the drive current lout. Similarly, when the bypass switch turns off,
the undershoot of the drive current lout is suppressed.
[0121] Let us consider a semiconductor light source lighting circuit 300 according to the
following comparative example which is uniquely created for the purpose of suppressing
the overshoot or the undershoot of the drive current lout at the time of changing
over the bypass switch.
[0122] FIG. 8 is a circuit diagram illustrating a configuration of the semiconductor light
source lighting circuit 300 according to the comparative example. The semiconductor
light source lighting circuit 300 is a forward converter that basically uses no smoothing
capacitor. The semiconductor light source lighting circuit 300 includes a control
circuit 302, an input capacitor 306, a reset circuit 308, a transformer 310, a fifth
switching element 312, a second diode 314, a third diode 316, an inductor 318, and
a current detection resistor 320.
[0123] The control circuit 302 turns off the fifth switching element 312 if a magnitude
of the drive current exceeds a given current upper limit value, and turns on the fifth
switching element 312 if the magnitude of the driver circuit falls below a current
lower limit value.
[0124] In the semiconductor light source lighting circuit 300, when it is assumed that a
winding ratio of the transformer 310 is N
s/p, an inductance of the inductor 318 is Ls', the hysteresis width of the driver circuit
is ΔI', the input voltage is Vin, the output voltage Vout (<0), an on-time of the
fifth switching element 312 is Ton', an off-time of the fifth switching element 312
is Toff', the switching frequency is F', and the forward drop voltage of a rectifier
diode is small and therefore ignored, F' can be obtained by the following expression.
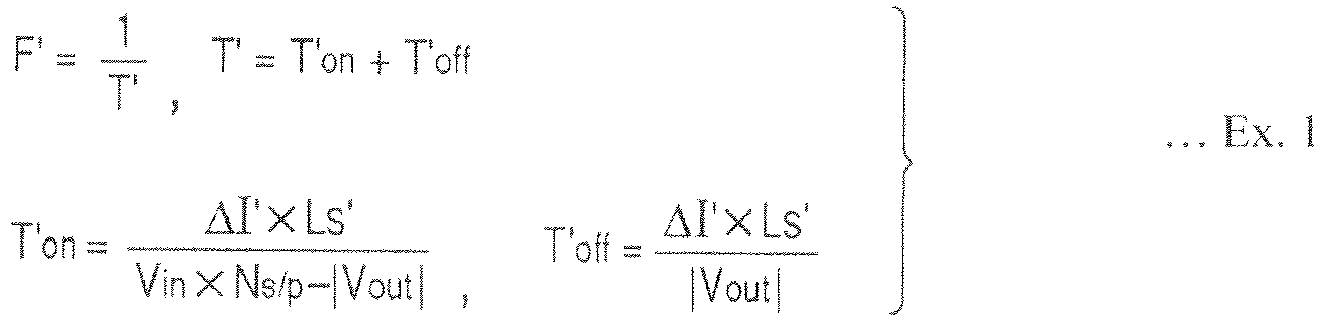
[0125] In the semiconductor light source lighting circuit 300, when it is assumed that the
winding ratio of the transformer 310 is set to 16.7 (convert input = 6V into output
= 100V), the inductance of the inductor 318 is set to 500 µH, the hysteresis width
is set to 0.1A, a relationship between Vin, Vout, and F' obtained from Expression
1 are represented by the following Table 1. In Table 1, it is assumed that an input
voltage variation is 6V to 20V, and an output (load) voltage variation is -4V to -88V
(22 LEDs having Vf = 4V are connected in series).
Table 1
|
|
Vout(V) |
F'(kHz) |
-4 |
-12 |
-28 |
-44 |
-60 |
-72 |
-88 |
Vin(V) |
6 |
76.8 |
211.2 |
403.2 |
492.8 |
480.0 |
403.2 |
211.2 |
9 |
77.9 |
220.8 |
455.5 |
621.9 |
720.0 |
748.8 |
727.5 |
14 |
78.6 |
227.7 |
492.8 |
714.1 |
891.4 |
995.7 |
1096.2 |
16 |
78.8 |
229.2 |
501.2 |
734.8 |
930.0 |
1051.2 |
1179.2 |
20 |
79.0 |
231.4 |
513.0 |
763.8 |
984.0 |
1129.0 |
1295.4 |
[0126] In this case, the switching frequency F' is varied between maximum/minimum by about
17 times. Although this variation range can be suppressed by making the inductance
larger, the circuit is upsized. Also, when a function of suppressing a large variation
of the switching frequency F' within a given range by calculating the input voltage
and the output voltage is realized, the control circuit scale becomes large.
[0127] The same calculation is conducted in the semiconductor light source control device
100 according to this embodiment. In the semiconductor light source lighting circuit
100, when it is assumed that an inductance of the inductor 144 is Ls, the switching
frequency is F, and the forward drop voltage of the flywheel diode 142 is small and
therefore ignored, F can be obtained by the following expression.

[0128] In the semiconductor light source lighting circuit 100, when it is assumed that a
target voltage Vt is set to -100V, the inductance of the inductor 144 is set to 500
µH, and the hysteresis width is set to 0.1A, a relationship between Vt, Vout, and
F obtained from Expression 2 are represented by the following Table 2.
Table 2
|
|
Vout(V) |
|
F'(kHz) |
-4 |
-12 |
-28 |
-44 |
-60 |
-72 |
-88 |
Vin(V) |
-100 |
76.8 |
211.2 |
403.2 |
492.8 |
480.0 |
403.2 |
211.2 |
[0129] In this case, a variation in the switching frequency F is suppressed to about 6.5
times. Also, since a main parameter that causes this variation is the drive voltage
Vout, and the target voltage Vt is substantially fixed, the scale of the control circuit
for adjusting the hysteresis width AI so as to suppress the variation in the switching
frequency F can be relatively reduced.
[0130] When theoretical calculated values of the switching frequency F in Table 2 are viewed,
the switching frequency F increases as the drive voltage Vout decreases from -4V to
-44V, and the switching frequency F decreases as the drive voltage Vout decreases
from -44V to -88V. A boundary between the increase and the decrease of the switching
frequency F is -50V which is about half of the output voltage (input voltage of the
downconverter 104 at a second stage (post stage)) of the flyback regulator 102 at
a first stage (previous stage). Therefore, the control is conducted to increase the
hysteresis width AI more as the drive voltage Vout is lower if Vout > -50V, and to
decrease the hysteresis width ΔI if Vout < -50V, thereby making it possible that the
switching frequency F easily falls within a given range.
[0131] Also, in this embodiment, it is found that the boundary between the increase and
the decrease of the switching frequency F is about half of the output voltage of the
flyback regulator 102. However, in another embodiment having another circuit arrangement,
it is conceivable that this boundary is 1/3 or 1/4 of the output voltage. The common
element between those embodiments resides that the drive voltage Vout that gives the
maximum value of the switching frequency F when the hysteresis width is kept constant
can be present between the maximum value and the minimum value of the drive voltage
Vout. Therefore, when such a drive voltage Vout is found out by experiments or simulations,
and the circuit is configured so that the hysteresis width ΔI becomes minimum at the
drive voltage Vout, the variation in the switching frequency F can be more preferably
suppressed.
[0132] A setting example of the parameters in the semiconductor light source control device
100 according to this embodiment is represented by the following Table 3.
Table 3
Vout (V) |
Voffset |
Lower limit voltage |
Upper limit voltage |
Ith2 |
Ith1 |
Mean Current |
Switching frequency |
-4 |
0.25 |
0.2356 |
0.2456 |
1.178 |
1.228 |
1.203 |
382.2 kHz |
-8 |
0.37 |
0.2332 |
0.2480 |
1.166 |
1.240 |
1.203 |
498.7 kHz |
-12 |
0.48 |
0.2309 |
0.2503 |
1.154 |
1.252 |
1.203 |
542.3 kHz |
-16 |
0.60 |
0.2285 |
0.2527 |
1.143 |
1.264 |
1.203 |
555.8 kHz |
-20 |
0.72 |
0.2262 |
0.2551 |
1.131 |
1.275 |
1.203 |
553.7 kHz |
-24 |
0.83 |
0.2238 |
0.2574 |
1.119 |
1.287 |
1.203 |
542.8 kHz |
-28 |
0.95 |
0.2215 |
0.2598 |
1.107 |
1.299 |
1.203 |
526.1 kHz |
-32 |
1.07 |
0.2191 |
0.2621 |
1.095 |
1.311 |
1.203 |
505.7 kHz |
-36 |
1.18 |
0.2167 |
0.2645 |
1.084 |
1.322 |
1.203 |
482.6 kHz |
-40 |
1.30 |
0.2144 |
0.2668 |
1.072 |
1.334 |
1.203 |
457.6 kHz |
-44 |
1.42 |
0.2120 |
0.2692 |
1.060 |
1.346 |
1.203 |
431.0 kHz |
-48 |
1.54 |
0.2097 |
0.2716 |
1.048 |
1.358 |
1.203 |
403.4 kHz |
-52 |
1.56 |
0.2093 |
0.2720 |
1.046 |
1.360 |
1.203 |
398.2 kHz |
-56 |
1.46 |
0.2113 |
0.2700 |
1.056 |
1.350 |
1.203 |
419.6 kHz |
-60 |
1.36 |
0.2132 |
0.2680 |
1.066 |
1.340 |
1.203 |
438.2 kHz |
-64 |
1.26 |
0.2152 |
0.2660 |
1.076 |
1.330 |
1.203 |
453.4 kHz |
-68 |
1.16 |
0.2172 |
0.2640 |
1.086 |
1.320 |
1.203 |
464.4 kHz |
-72 |
1.06 |
0.2192 |
0.2621 |
1.096 |
1.310 |
1.203 |
469.9 kHz |
-76 |
0.97 |
0.2211 |
0.2601 |
1.106 |
1.300 |
1.203 |
468.4 kHz |
-80 |
0.87 |
0.2231 |
0.2581 |
1.116 |
1.291 |
1.203 |
457.3 kHz |
-84 |
0.77 |
0.2251 |
0.2561 |
1.125 |
1.281 |
1.203 |
433.1 Hz |
-88 |
0.67 |
0.2271 |
0.2542 |
1.135 |
1.271 |
1.203 |
390.0 kHz |
[0133] The offset voltage Voffset is set so that the voltage value becomes high in the vicinity
of Vout=-50V as illustrated by the graph of FIG. 3, by adjusting a circuit constant
of the hysteresis width setting circuit 138 illustrated in FIG. 2. The lower limit
voltage and the upper limit voltage are voltages of the voltage division node between
the twelfth resistor 182 and the thirteenth resistor 184 of the downconverter driver
circuit 136 illustrated in FIG. 4, which correspond to the current lower limit value
Ith2 and the current upper limit value Ith1, respectively. The lower limit voltage
and the upper limit voltage are calculated from the offset voltage Voffset by setting
the respective resistance values of the eighth resistor 174, the twelfth resistor
182, and the thirteenth resistor 184, and the positive control supply voltage Vcc.
The mean current is a mean value of the current upper limit value Ith1 and the current
lower limit value Ith2. The switching frequency is obtained as ΔI = Ith1-Ith2, Vt
= -100V, and Ls = 200µH in the same calculation expression as Expression 2.
[0134] It is found that even if Ls decreases from 500µ H to 200µH, the switching frequency
can fall within a range of from 550 kHz or higher to 500 kHz or lower. That is, in
the semiconductor light source control device 100 according to this embodiment, the
inductance for smoothing the drive current lout can be downsized.
[0135] Also, when the semiconductor light source lighting circuit 300 according to the comparative
example is compared with the semiconductor light source control device 100 according
to this embodiment, in the semiconductor light source control device 100, the output
capacitor 128 of the flyback regulator 102 and the second switching element 140 of
the downconverter 104 are increased, but the reset circuit 308 can be reduced from
the semiconductor light source lighting circuit 300. As a result, the circuit scale
is substantially equal to each other.
[0136] The configuration and the operation of the semiconductor light source control device
according to this embodiment have been described above. This embodiment is exemplary,
and it would be understood by an ordinary skilled person that the combinations of
the respective elements and the respective processing can be variously modified, and
such modifications also fall within the scope of the present invention.
[0137] In this embodiment, as the element arrangement of the downconverter 104, a case in
which the second switching element 140 is arranged on the cathode side of the flywheel
diode 142, and the inductor 144 is arranged on the anode side of the flywheel diode
142 has been described. However, the present invention is not limited to this configuration.
The flywheel diode may be connected in parallel to the output capacitor 128 of the
flyback regulator 102. The second switching element is disposed on the route of the
drive current lout which leads to the LED from one end of the output capacitor 128,
and returns to the other end of the output capacitor 128 from the LED. The second
switching element may be also disposed between the output capacitor 128 and the flywheel
diode. The on/off operation of the second switching element may be controlled on the
basis of the drive current. The inductor 144 may be disposed on the route of the drive
current lout, and disposed between the flywheel diode and the LED.
[0138] FIGS. 9A to 9C are circuit diagrams illustrating the configurations of semiconductor
light source control devices 400, 500, and 600 according to first, second, and third
modified examples. FIG. 9A illustrates the configuration of the semiconductor light
source control device 400 according to the first modified example. One end of a second
switching element 440 is connected to a high potential side output of the flyback
regulator 102, and the other end of the second switching element 440 is connected
to a cathode of a flywheel diode 442. One end of an inductor 444 is connected to a
connection node between the other end of the second switching element 440 and the
cathode of the flywheel diode 442. The other end of the inductor 444 is grounded,
and forms a high potential side output terminal to the LEDs. An anode of the flywheel
diode 442 is connected to a low potential side output of the flyback regulator 102,
and forms a low potential side output terminal to the LEDs.
[0139] FIG. 9B illustrates the configuration of the semiconductor light source control device
500 according to the second modified example. A cathode of a flywheel diode 542 is
connected to a high potential side output of the flyback regulator 102, and grounded,
and forms a high potential side output to the LEDs. One end of a second switching
element 540 is connected to a low potential side output of the flyback regulator 102,
and the other end of the second switching element 540 is connected to an anode of
the flywheel diode 542. One end of an inductor 544 is connected to a connection node
between the other end of the second switching element 540 and the anode of the flywheel
diode 542. The other end of the inductor 544 forms a low potential side output terminal
to the LEDs.
[0140] FIG. 9C illustrates the configuration of the semiconductor light source control device
600 according to the third modified example. One end of a second switching element
640 is connected to a low potential side output of the flyback regulator 102, and
the other end of the second switching element 640 is connected to an anode of a flywheel
diode 642. A connection node between the other end of the second switching element
640 and the anode of the flywheel diode 642 forms a low potential side output to the
LEDs. A cathode of the flywheel diode 642 is connected to one end of an inductor 644.
A connection node between the cathode of the flywheel diode 642 and one end of the
inductor 644 is connected to a high potential side output of the flyback regulator
102. The other end of the inductor 644 is grounded, and forms a high potential side
output terminal to the LEDs.
[0141] According to the respective semiconductor light source control devices 400, 500,
and 600 of the first, second, and third modified examples, the overshoot and the undershoot
of the drive current lout can be reduced as in the semiconductor light source control
device 100 according to the embodiment.
[0142] In the embodiment, there has been described a case in which the high potential side
of the output, that is, the anode side of the plurality of LEDs is grounded to realize
the negative output. However, the present invention is not limited to this configuration,
but, for example, the anode side of the plurality of LEDs may be connected to a terminal
to which a DC voltage such as the battery voltage Vbat is applied.
[0143] In the embodiment, there has been described a case in which the switching frequency
is not measured in real time, but, the relationship between the drive voltage Vout
and the hysteresis width ΔI is determined on the basis of the known relationship between
the drive voltage Vout and the switching frequency instead, and the circuit is configured
so that the hysteresis width AI is changed according to the determined relationship.
However, the present invention is not limited to this configuration. For example,
the semiconductor light source control device may include a circuit for measuring
the switching frequency of the second switching element 140, and adjust the hysteresis
width so that the measured switching frequency falls within a target frequency range.
[0144] In the embodiment, there has been described a case in which the semiconductor light
source control device 100 includes the N bypass switches 110-1 to 110-N. However,
the present invention is not limited to this configuration, but the bypass switches
may be disposed separately from the semiconductor light source control device.
[0145] In the embodiment, there has been described a case in which the hysteresis control
of the driver circuit is conducted. However, the present invention is not limited
to this configuration, but, for example, a duty ratio of the second switching element
140 may be controlled so that a voltage obtained by appropriately filtering the voltage
drop Vm comes closer to a reference voltage corresponding to a target current.
[0146] In the embodiment, there has been described a case in which the driver circuit is
configured to generate the drive current lout by the combination of the flyback regulator
102 and the downconverter 104, and control the magnitude of the drive current lout
to come closer to the target value. However, the present invention is not limited
to this configuration, but, for example, a circuit illustrated in FIG. 8 may be employed
as the above driver circuit, or a flyback regulator that is subjected to a current
feedback control may be employed.
[0147] FIG. 10 is a circuit diagram illustrating a configuration of a semiconductor light
source control device 700 according to a fourth modified example, and members connected
to the semiconductor light source control device 700. The semiconductor light source
control device 700 includes a flyback regulator 702, a current detection resistor
708, the N bypass circuits 270-1 to 270-N, and the bypass driver circuit 112.
[0148] In the semiconductor light source control device 700 according to this modified example,
when a poor continuity is generated in a portion of a mark "X" indicated by reference
numeral 718 in the second bypass connection line 280-2, as in the semiconductor light
source control device 100 according to this embodiment, both of the second bypass
switch and the third bypass switch are forcedly turned on by the actions of the second
bypass circuit 270-2, the third bypass circuit 270-3, and the bypass driver circuit
112.
[0149] Also, a limit value of the maximum voltage output by the flyback regulator 702 is
set to a sum of the forward drop voltages Vf or more, taking a case in which all of
the N LEDs connected in series are turned on into account. For example, when the maximum
value of the forward drop voltage Vf of one LED is set to 6V, and the 30 LEDs are
connected in series to each other, the limit value is set to 180V or higher. In this
example, because the drive current lout does not flow in the LED at the moment when
the contact failure or the disconnection is generated in the line of the mark "X"
indicated by reference numeral 762 in FIG. 10, the output voltage of the flyback regulator
702 is raised toward 180V. When the control circuit (not shown) detects that the drive
current lout is stopped from flowing in the LEDs, the control circuit takes a countermeasure
to inspect in which line or LED the disconnection is generated, and turn on the first
bypass switch 110-1 in the circuit of FIG. 10 so as to turn on the other LEDs. Normally,
a time of several ten msec to several hundred msec is required for this countermeasure.
[0150] In this case, if the semiconductor light source control device does not include
the limiter zener diode 256 and the backflow prevention diode 258, the output voltage
of the flyback regulator 702 reaches 180V before the first bypass switch turns on.
In this situation, when it is assumed that a mean value (at room temperature) of the
forward drop voltages Vf of the used LEDs is 4V, and 3V when a current hardly flows,
a voltage of 180V - 3V × 30 = 90V is applied to the first bypass switch. Therefore,
although only a voltage of several V is usually applied to each of 30 bypass switches,
an element having the withstand voltage of 100V must be selected taking the disconnection
or the contact failure into account.
[0151] Then, when the disconnection or the contact failure is generated in the line of a
mark "X" indicated by reference numeral 764 in FIG. 10, the first electrostatic protection
zener diode is applied with the above 90V when a current hardly flows in the LEDs,
and 180V - 4V × 30 = 60V when a control current flows in the LEDs. In this example,
when it is assumed that the zener voltage of the first electrostatic protection zener
diode is 20V, since the above voltages 90V and 60V are higher than 20V, 20V × 1A =
20W is applied to the first electrostatic protection zener diode for several ten msec
to several hundred msec when the control current is 1A, and the element that withstands
20W needs to be selected. In order to avoid this, the zener voltage of the first electrostatic
protection zener diode needs to be set to 90V or higher, which makes it difficult
to perform the original function of the electrostatic protection.
[0152] Under the circumstance, the semiconductor light source control device 700 according
to this modified example is equipped with a first bypass/limiter circuit 250-1 whereby
even if the contact failure or the disconnection is generated, an upper limit of the
voltage to be applied to the first bypass switch 110-1 is suppressed. Therefore, the
element having the high withstand voltage of 100V or higher may not be selected as
the first bypass switch 110-1. Also, if the limit voltage by the first bypass/limiter
circuit 250-1 is set to the zener voltage or lower of the first electrostatic protection
zener diode 252-1, a small zener diode can be selected.
[0153] In the semiconductor light source control device 100 according to the embodiment,
the withstand voltage of kV order is required for the bypass switch when there is
no limiter function. Therefore, the withstand voltage suppression effect obtained
by provision of the limiter function is more remarkable in the embodiment.
[0154] In this embodiment, a case in which the LEDs and the bypass switches correspond to
each other on a one-to-one basis has been described. However, the present invention
is not limited to this configuration, but the on/off operation of the plurality of
LEDs may be controlled by one bypass switch. For example, when one bypass switch is
connected to two LEDs connected in series, a total maximum value of the forward drop
voltages Vf of the LEDs is 12V, and the zener diode of the electrostatic protection
zener diode is 40V. Therefore, the zener voltage of the limiter zener diode may fall
within a range of from 9V to 21V. When the zener voltage of the limiter zener diode
is set to 20V, the limit value of the voltage between both ends thereof becomes 23V.
Therefore, the element having the withstand voltage of 30V may be selected as the
bypass switch.
[0155] In the embodiment, when the poor continuity is generated not only in the second bypass
connection line 280-2, but also in the portion of the mark "X" indicated by the reference
numeral 220 (refer to FIG. 5) of the third bypass connection line 280-3, all of the
second bypass switch, the third bypass switch, and the fourth bypass switch are forcedly
turned on by the actions of the second bypass circuit 270-2, the third bypass circuit
270-3, the fourth bypass circuit 270-4, and the bypass driver circuit 112.
[0156] In the embodiment, the description has been given of a case in which when the poor
continuity is generated in the bypass connection line, any one of the two bypass switches
connected to the bypass connection line is forcedly turned on by the disconnection
abnormality, and which of the bypass switches is forcedly turned on by the short-circuit
abnormality depends on the characteristic of the bypass switch. However, the present
invention is not limited to this configuration. For example, resistors may be disposed
in parallel to the respective odd-numbered bypass circuits (the first bypass circuit
270-1, the third bypass circuit 270-3, ...). Also, resistors may be disposed in parallel
to the respective even-numbered bypass circuits. In those cases, when the poor continuity
is generated in the bypass connection line, the bypass switch on a side where the
above resistor is provided is forcedly turned on by the short-circuit abnormality,
and the bypass switch on a side where the above resistor is not provided is forcedly
turned on by the disconnection abnormality.
[0157] In the embodiment, a description has been given of a case in which the poor continuity
of the bypass connection line is treated by the disconnection detection function and
the short-circuit detection function of the bypass circuit and the bypass driver circuit.
However, the present invention is not limited to this configuration. For example,
a unit for detecting the poor continuity of the bypass connection line such as a current
measurement unit may be disposed in the bypass connection line, and the unit may be
used to determine whether the poor continuity is generated in the bypass connection
line, or not. If it is determined that the poor continuity is generated, the bypass
driver circuit may forcedly turn on the corresponding two bypass switches.
[0158] In the embodiment, a description has been given of a case in which the integration
capacitor is charged in a case where the poor continuity or the short-circuit abnormality
is detected when the bypass switch is off, and the integrating capacitor is discharged
in the other cases. However, the present invention is not limited to this configuration.
For example, the integration capacitor may be discharged by the first time constant
if the poor continuity or the short-circuit abnormality is detected when the bypass
switch is off, and the integration capacitor may be charged by the second time constant
in the other cases.
[0159] In the semiconductor light source control device 100 according to the embodiment,
the PWM dimming function is employed. During the PWM dimming operation, the bypass
driver circuit 112 cyclically changes the voltage level of the lighting on/off control
signal at the dimming frequency f1. If no abnormality is generated, the corresponding
bypass switch is turned off when the lighting on/off control signal is low level,
and the corresponding bypass switch is turned on when the lighting on/off control
signal is high level. Therefore, the low level of the lighting on/off control signal
corresponds to an off state of the corresponding bypass switch, and the high level
of the lighting on/off control signal corresponds to an on state of the corresponding
bypass switch.
[0160] Also, the bypass driver circuit 112 is a microcomputer, and operates at relatively
long time intervals. In particular, the bypass driver circuit 112 monitors the abnormality
detection signal over a given abnormality determination period for the respective
LEDs to determine whether the abnormality is generated, or not. Then, if it is determined
that the abnormality is generated in a certain LED, the bypass driver circuit 112
fixes the lighting on/off control signal corresponding to that LED to the high level.
This will be described with a concept of certainty and uncertainty of the abnormality.
When the bypass driver circuit 112 continuously detects the abnormal state for the
abnormality determination period, the bypass driver circuit 112 decides the abnormal
state as abnormality, and subjects the bypass switch to on-latch control.
[0161] In general, since the abnormality determination period is longer than a cycle (=1/f1)
of the PWM dimming, the semiconductor light source control device 100 according to
the embodiment introduces the integrating circuit, to thereby enable more accurate
short-circuit abnormality/disconnection abnormality detection which is little in misdetection
even if the PWM dimming is conducted.
[0162] A case in which the disconnection abnormality is generated in the LED normally-on
(bypass switch = normally-off) control where the PWM dimming is not conducted will
be studied. In a period since the disconnection is generated in a certain LED until
a bypass switch corresponding to the LED is subjected to the on-latch control, the
bypass switch operates as a switch for realizing the limiter function by the action
of, particularly, the limiter zener diode of the bypass/limiter circuit corresponding
to the LED. As a result, routes of the current to the other LEDs can be maintained.
However, in this case, since the bypass switch basically operates in a linear area,
the bypass switch is continuously supplied with an electric power of "disconnection
detection voltage × drive current lout" with the result that a power loss becomes
large in the bypass switch. In this case, the switching element large in size and
large in tolerated dose is required as the bypass switch, resulting in an upsized
circuit and an increase in the costs. If the on-latch control is conducted on the
bypass switch immediately after the detection of the disconnection abnormality, the
power loss is reduced. However, in this case, the number of determinations in the
bypass driver circuit 112 is decreased (determination time is short), and in particular,
a possibility of the misdetection (malfunction) of the disconnection abnormality in
a PWM dimming mode becomes high.
[0163] Even if the disconnection is generated when the PWM dimming is conducted, the bypass
switch operates as a switch for realizing the limiter function when the lighting on/off
control signal is low level. For that reason, there is a risk that the power loss
is increased in the bypass switch, likewise. A ratio of the on-period (=extinction
period of the LED) of the bypass switch to one cycle (= 1/f1) of the PWM dimming is
called "on-duty ratio". The power loss caused by the disconnection is increased more
as the on-duty ratio is smaller.
[0164] Also, the power loss in the bypass switch when the bypass switch is turned on is
mainly caused by the on-resistance of the bypass switch, and slight, and extremely
smaller than the power loss particularly when the bypass switch basically operates
in the linear area.
[0165] FIG. 11 is a circuit diagram illustrating a configuration of a second bypass circuit
870-2 in a semiconductor light source control device according to a fifth modified
example. The other bypass circuits are configured in the same manner as that of the
second bypass circuit 870-2.
[0166] A difference between the second bypass circuit 270-2 illustrated in FIG. 5 and the
second bypass circuit 870-2 illustrated in FIG. 11 mainly resides in the configuration
of the second switch level shift circuit. A second switch level shift circuit 854-2
of the second bypass circuit 870-2 receives a second lighting on/off control signal
Sc2' from a bypass driver circuit 812, and converts the second lighting on/off control
signal Sc2' into the second bypass switch drive signal Sd2. In particular, the second
switch level shift circuit 854-2 sets the second bypass switch drive signal Sd2 to
the low level if the second lighting on/off control signal Sc2' is high level, and
sets the second bypass switch drive signal Sd2 to the high level if the second lighting
on/off control signal Sc2' is low level.
[0167] A second bypass/limiter circuit 850-2 of the second bypass circuit 870-2 may not
have a resistor corresponding to the sixteenth resistor 260.
[0168] The second switch level shift circuit 854-2 includes a 26
th resistor 822, a 27
th resistor 814, a 28
th resistor 816, a 29
th resistor 818, and a fifth pnp bipolar transistor 820. One end of the 26th resistor
822 is connected to a terminal of the bypass driver circuit 812. The second lighting
on/off control signal Sc2' is output from the terminal of the bypass driver circuit
812. The other end of the 26
th resistor 822 is connected to a base of the fifth pnp bipolar transistor 820. One
end of the 27
th resistor 814 is connected to a connection node between the other end of the 26
th resistor 822 and the base of the fifth pnp bipolar transistor 820. A positive control
supply voltage Vcc is applied to the other end of the 27
th resistor 814, and an emitter of the fifth pnp bipolar transistor 820. A collector
of the fifth pnp bipolar transistor 820 is connected to one end of the 28
th resistor 816. The other end of the 28
th resistor 816 is connected to one end of the 29
th resistor 818. The other end of the 29
th resistor 818 is connected to the cathode of the second LED 2-2.
[0169] A connection node between the 28
th resistor 816 and one end of the 29
th resistor 818 is connected to the gate of the second bypass switch 110-2. A signal
generated in the connection node forms the second bypass switch drive signal Sd2.
[0170] When the second lighting on/off control signal Sc2' is high level, the second bypass
switch drive signal Sd2 becomes low level, and the second bypass switch 110-2 turns
off (the second LED 2-2 turns on). When the second lighting on/off control signal
Sc2' is low level, the second bypass switch drive signal Sd2 becomes high level, and
the second bypass switch 110-2 turns on (the second LED 2-2 turns off). When the PWM
dimming is conducted, the bypass driver circuit 812 sets the second lighting on/off
control signal Sc2' as a high level/low level repetitive signal having a cycle of
several msec.
[0171] If the voltage between both ends of the integration capacitor 282 exceeds a given
threshold voltage, the bypass driver circuit 812 increases the on-duty ratio and the
cycle of a signal to be supplied to the control input terminal, that is, the gate
of the second bypass switch 110-2 larger than those of the normal PWM dimming in synchronization
with the second lighting on/off control signal Sc2'. In particular, if the voltage
of the second abnormality detection signal Sdet2 exceeds the level threshold value
Vg, the bypass driver circuit 812 starts the abnormality determination period for
the second LED 2-2, and increases the ratio of a duration of the low level to one
cycle of the second lighting on/off control signal Sc2'. In an example, the cycle
of the second lighting on/off control signal Sc2' increases to several hundred msec,
and the on-duty ratio increases to 90% or higher.
[0172] FIG. 12 is a timing chart illustrating a change in the second lighting on/off control
signals Sc2 and Sc2' when the disconnection is generated in the second LED 2-2. A
waveform represented on an upper stage of FIG. 12 represents the second lighting on/off
control signal Sc2' when the semiconductor light source control device according to
the fifth modified example conducts the PWM dimming in a first cycle PT1 of about
several msec in the normal lighting state. A waveform represented in a middle stage
of FIG. 12 represents the second lighting on/off control signal Sc2 when the semiconductor
light source control device 100 according to the embodiment always conducts lighting
in the normal lighting state. A waveform represented on a lower stage of FIG. 12 represents
the second lighting on/off control signal Sc2 when the semiconductor light source
control device 100 according to the embodiment conducts the PWM dimming in the first
cycle PT1 in the normal lighting state.
[0173] When the disconnection is generated in the second LED 2-2 in the fifth modified example,
a cycle of the second lighting on/off control signal Sc2' becomes a second cycle PT2
of about several hundred msec larger than the first cycle PT1. In particular, the
bypass driver circuit 812 lengthens the duration of the low level while maintaining
a length of the duration of the high level in one cycle of the second lighting on/off
control signal Sc2', to thereby realize an increase in the cycle. The second cycle
PT2 may be smaller than the second time constant for the discharge of the second integrating
circuit 278-2.
[0174] In abnormality determination period PT3 of about several seconds, the bypass driver
circuit 812 keeps the increased on-duty ratio and cycle of the signal to be supplied
to the gate of the second bypass switch 110-2 in synchronization with the second lighting
on/off control signal Sc2' if the voltage of the second abnormality detection signal
Sdet2 when the second lighting on/off control signal Sc2' is set to the high level
is higher than the level threshold value Vg. If the voltage of the second abnormality
detection signal Sdet2 falls below the level threshold value Vg, the bypass driver
circuit 812 returns the second lighting on/off control signal Sc2' to a state having
the first cycle PT1. The bypass driver circuit 812 determines that the abnormality
is generated (that is, abnormality certainty) if a state in which the voltage of the
second abnormality detection signal Sdet2 is higher than the level threshold value
Vg is continued until the abnormality determination period PT3 is expired. Then, the
bypass driver circuit 812 fixes the second lighting on/off control signal Sc2' to
the low level.
[0175] When the disconnection is generated in the second LED 2-2 in the embodiment, the
state of the second lighting on/off control signal Sc2 remains in the same state as
that before the abnormality is generated, during the abnormality determination period
PT3. Then, if the abnormality determination period PT3 is expired, it is determined
that the abnormality is generated, and the second lighting on/off control signal Sc2
is fixed to the high level.
[0176] Thus, according to the semiconductor light source control device of the fifth modified
example, as compared with the semiconductor light source control device 100 according
to the embodiment, a total length of the off-periods of the bypass switch in the abnormality
determination period can be shortened even in the always-on state or even in the PWM
dimming. Since the off-period corresponds to a period during which the bypass switch
operates in the linear area when the disconnection is generated, the power loss in
the bypass switch can be reduced in the fifth modified example. As a result, the switching
element low in withstand can be employed as the bypass switch, so that the circuit
can be downsized, and the costs can be reduced.
[0177] In particular, for the convenience of the PMW dimming, in a status where it is improper
to determine that the abnormality is generated immediately with the level transition
of the abnormality detection signal, according to the fifth modified example, it can
be more precisely determined whether the abnormality is generated, or not, by monitoring
the abnormality detection signal over the abnormality determination period, and the
power loss of the bypass switch in the abnormality determination period can be reduced.