BACKGROUND
[0001] Chemical mechanical polishing (CMP), also referred to as chemical mechanical planarization,
refers to a method of removing layers of solid through chemical mechanical polishing
carried out for the purpose of surface planarization. In a typical CMP process, a
rotating polishing pad uses a chemically reactive slurry to polish the outermost surface
of the substrate. The substrate is positioned over the polishing pad and is held in
place by a retaining ring. Typically, the substrate and the retaining ring are mounted
on a carrier or polishing head. A controlled force is exerted on the substrate by
the carrier hear to press the substrate against the polishing pad. The movement of
the polishing pad across the surface of the substrate causes material to be chemically
and mechanically removed from the face of the substrate. The equipment used to perform
CMP processes includes various components that are typically required to be replaced
with some frequency during a polishing process, which can lead to high costs associated
with CMP. One such component is the retaining ring, which as mentioned above, serves
to contain the slurry and maintain the position of the substrate that is being polished.
[0002] Accordingly, there remains a continuing need in the art for an improved retaining
ring for use in chemical mechanical polishing processes.
SUMMARY
[0003] A retaining ring for use in a chemical mechanical polishing process comprises an
annular metal backbone (1); a lower portion (2) having a bottom surface for contacting
a polishing pad during polishing, the lower portion comprising a poly(etherimide)
or a combination of a poly(etherimide) and a poly(aromatic ketone); and an upper portion
(3) comprising a thermoplastic polymer; wherein the annular metal backbone is positioned
between the lower portion and the upper portion.
[0004] A method of manufacturing the retaining ring comprises molding the lower portion
from a poly(etherimide) or a combination of a poly(etherimide) and a poly(aromatic
ketone); molding the upper portion from a thermoplastic polymer; bonding the lower
portion, the upper portion, and the annular metal backbone, such that the annular
metal backbone is positioned between the upper portion and the lower portion.
[0005] A chemical mechanical polishing system comprises the retaining ring.
[0006] The above described and other features are exemplified by the following figures and
detailed description.
BRIEF DESCRIPTION OF THE DRAWINGS
[0007] The following figures represent exemplary aspects wherein like elements are numbered
alike.
FIG. 1 is an illustration of an aspect of the present disclosure.
FIG. 2 is a photograph of an aspect of the present disclosure.
FIG. 3 shows the thickness change for each of Examples 1-6 after immersion of the
samples in a polishing slurry for 48 hours.
FIG. 4 shows scanning electron microscope (SEM) images for Examples 1-6.
DETAILED DESCRIPTION
[0008] The present inventors have unexpectedly discovered an improved retaining ring for
a CMP process can be provided when the retaining ring includes a lower portion comprising
a poly(etherimide) or a combination of a poly(etherimide) and a poly(aromatic ketone).
Advantageously, use of the particular retaining ring described herein can provide
high mechanical and thermal durability as well as chemical resistance.
[0009] Accordingly, an aspect of the present disclose is a retaining ring for use in a chemical
mechanical polishing process. The retaining ring comprises an annular metal backbone,
a lower portion, and an upper portion. The annular metal backbone is positioned between
the lower portion and the upper portion of the retaining ring. For example, the lower
portion and the upper portion can encapsulate the annular metal backbone, for example
as shown in FIG. 1. In an aspect, the annular metal backbone can be sandwiched between
the upper portion and the lower portion, such that an inner and outer edge of the
annular metal backbone are exposed at the inner and outer edges of the retaining ring,
between the upper and lower portions.
[0010] The annular metal backbone can include, for example, aluminum, stainless steel, molybdenum,
a ceramic, zinc, or an alloy or combination thereof.
[0011] The lower portion of the retaining ring has a bottom surface that contacts the polishing
pad during a CMP operation. The lower portion comprises a poly(etherimide) or a combination
of a poly(etherimide) and a poly(aromatic ketone). In an aspect, the lower portion
comprises the poly(etherimide). In an aspect, the lower portion comprises the combination
of the poly(etherimide) and the poly(aromatic ketone).
[0012] Poly(etherimides) comprise more than 1, for example 2 to 1000, or 5 to 500, or 10
to 100 structural units of formula (1)
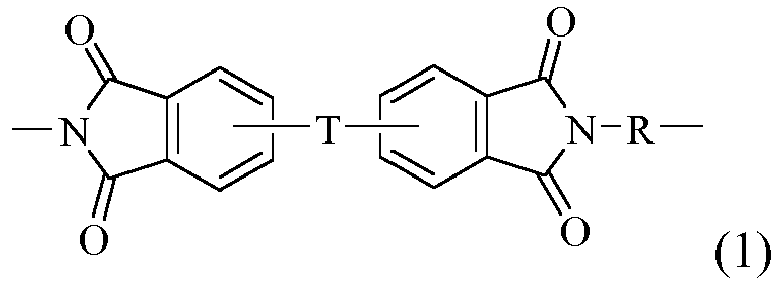
wherein each R is independently the same or different, and is a substituted or unsubstituted
divalent organic group, such as a substituted or unsubstituted C
6-20 aromatic hydrocarbon group, a substituted or unsubstituted straight or branched chain
C
4-20 alkylene group, a substituted or unsubstituted C
3-8 cycloalkylene group, in particular a halogenated derivative of any of the foregoing.
In an aspect R is divalent group of one or more of the following formulas (2)

wherein Q
1 is -O-, -S-, -C(O)-, -SO
2-, -SO-, -P(R
a)(=O)- wherein R
a is a C
1-8 alkyl or C
6-12 aryl,-C
yH
2y- wherein y is an integer from 1 to 5 or a halogenated derivative thereof (which includes
perfluoroalkylene groups), or -(C
6H
10)
z- wherein z is an integer from 1 to 4. In an aspect R is m-phenylene, p-phenylene,
or a diarylene sulfone, in particular bis(4,4'-phenylene)sulfone, bis(3,4'-phenylene)sulfone,
bis(3,3'-phenylene)sulfone, or a combination comprising at least one of the foregoing.
In an aspect, at least 10 mole percent or at least 50 mole percent of the R groups
contain sulfone groups, and in other aspects no R groups contain sulfone groups.
[0013] Further in formula (1), T is -O- or a group of the formula -O-Z-O- wherein the divalent
bonds of the -O- or the -O-Z-O- group are in the 3,3', 3,4', 4,3', or the 4,4' positions,
and Z is an aromatic C
6-24 monocyclic or polycyclic moiety optionally substituted with 1 to 6 C
1-8 alkyl groups, 1 to 8 halogen atoms, or a combination comprising at least one of the
foregoing, provided that the valence of Z is not exceeded. Exemplary groups Z include
groups of formula (3)

wherein R
a and R
b are each independently the same or different, and are a halogen atom or a monovalent
C
1-6 alkyl group, for example; p and q are each independently integers of 0 to 4; c is
0 to 4; and X
a is a bridging group connecting the hydroxy-substituted aromatic groups, where the
bridging group and the hydroxy substituent of each C
6 arylene group are disposed ortho, meta, or para (specifically para) to each other
on the C
6 arylene group. The bridging group X
a can be a single bond, -O-, -S-, -S(O)-, -S(O)
2-, -C(O)-, or a C
1-18 organic bridging group. The C
1-18 organic bridging group can be cyclic or acyclic, aromatic or non-aromatic, and can
further comprise heteroatoms such as halogens, oxygen, nitrogen, sulfur, silicon,
or phosphorous. The C
1-18 organic group can be disposed such that the C
6 arylene groups connected thereto are each connected to a common alkylidene carbon
or to different carbons of the C
1-18 organic bridging group. A specific example of a group Z is a divalent group of formula
(3a)
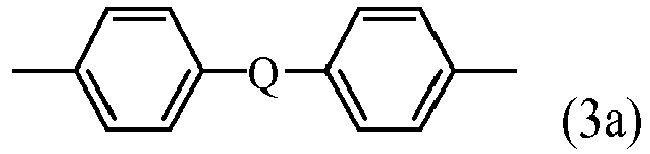
wherein Q is -O-, -S-, -C(O)-, -SO
2-, -SO-, -P(R
a)(=O)- wherein R
a is a C
1-8 alkyl or C
6-12 aryl, or -C
yH
2y- wherein y is an integer from 1 to 5 or a halogenated derivative thereof (including
a perfluoroalkylene group). In an aspect Z is a derived from bisphenol A, such that
Q in formula (3a) is 2,2-isopropylidene.
[0014] In an aspect in formula (1), R is m-phenylene, p-phenylene, or a combination comprising
at least one of the foregoing, and T is -O-Z-O- wherein Z is a divalent group of formula
(3a). Alternatively, R is m-phenylene, p-phenylene, or a combination comprising at
least one of the foregoing, and T is -O-Z-O- wherein Z is a divalent group of formula
(3a) and Q is 2,2-isopropylidene. In an aspect, R is p-phenylene and T is -O-Z-O-
wherein Z is a divalent group of formula (3a) and Q is 2,2-isopropylidene. Such materials
are available under the trade name ULTEM from SABIC.
[0015] In an aspect, the poly(etherimide) is a copolymer that optionally comprises additional
structural imide units that are not poly(etherimide) units, for example imide units
of formula (4)
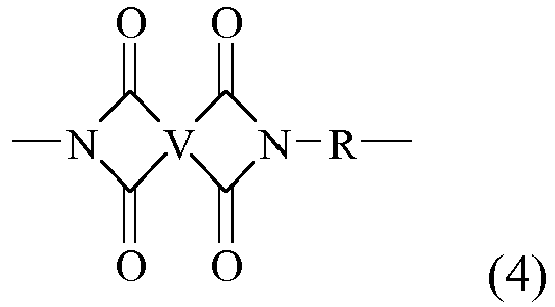
wherein R is as described in formula (1) and each V is the same or different, and
is a substituted or unsubstituted C
6-20 aromatic hydrocarbon group, for example a tetravalent linker of the formulas

wherein W is a single bond, -O-, -S-, -C(O)-, -SO
2-, -SO-, a C
1-18 hydrocarbylene group,-P(R
a)(=O)- wherein R
a is a C
1-8 alkyl or C
6-12 aryl, or -C
yH
2y- wherein y is an integer from 1 to 5 or a halogenated derivative thereof (which includes
perfluoroalkylene groups). These additional structural imide units preferably comprise
less than 20 mol% of the total number of units, and more preferably can be present
in amounts of 0 to 10 mol% of the total number of units, or 0 to 5 mol% of the total
number of units, or 0 to 2 mole % of the total number of units. In an aspect, no additional
imide units are present in the poly(etherimide).
[0016] The poly(imide) or the poly(etherimide) can be prepared by any of the methods known
to those skilled in the art, including the reaction of an aromatic bis(ether anhydride)
of formula (5) or a chemical equivalent thereof, with an organic diamine of formula
(6)
H
2N-R-NH
2 (6)
wherein T and R are defined as described above. Copolymers of the poly(etherimides)
can be manufactured using a combination of an aromatic bis(ether anhydride) of formula
(5) and an additional bis(anhydride) that is not a bis(ether anhydride), for example
pyromellitic dianhydride or bis(3,4-dicarboxyphenyl) sulfone dianhydride.
[0017] Illustrative examples of aromatic bis(ether anhydride)s include 2,2-bis[4-(3,4-dicarboxyphenoxy)phenyl]propane
dianhydride (also known as bisphenol A dianhydride or BPADA), 3,3-bis[4-(3,4-dicarboxyphenoxy)phenyl]propane
dianhydride; 4,4'-bis(3,4-dicarboxyphenoxy)diphenyl ether dianhydride; 4,4'-bis(3,4-dicarboxyphenoxy)diphenyl
sulfide dianhydride; 4,4'-bis(3,4-dicarboxyphenoxy)benzophenone dianhydride; 4,4'-bis(3,4-dicarboxyphenoxy)diphenyl
sulfone dianhydride; 4,4'-bis(2,3-dicarboxyphenoxy)diphenyl ether dianhydride; 4,4'-bis(2,3-dicarboxyphenoxy)diphenyl
sulfide dianhydride; 4,4'-bis(2,3-dicarboxyphenoxy)benzophenone dianhydride; 4,4'-bis(2,3-dicarboxyphenoxy)diphenyl
sulfone dianhydride; 4-(2,3-dicarboxyphenoxy)-4'-(3,4-dicarboxyphenoxy)diphenyl-2,2-propane
dianhydride; 4-(2,3-dicarboxyphenoxy)-4'-(3,4-dicarboxyphenoxy)diphenyl ether dianhydride;
4-(2,3-dicarboxyphenoxy)-4'-(3,4-dicarboxyphenoxy)diphenyl sulfide dianhydride; 4-(2,3-dicarboxyphenoxy)-4'-(3,4-dicarboxyphenoxy)benzophenone
dianhydride; 4,4'-(hexafluoroisopropylidene)diphthalic anhydride; and 4-(2,3-dicarboxyphenoxy)-4'-(3,4-dicarboxyphenoxy)diphenyl
sulfone dianhydride. A combination of different aromatic bis(ether anhydride)s can
be used.
[0018] Examples of organic diamines include 1,4-butane diamine, 1,5-pentanediamine, 1,6-hexanediamine,
1,7-heptanediamine, 1,8-octanediamine, 1,9-nonanediamine, 1,10-decanediamine, 1,12-dodecanediamine,
1,18-octadecanediamine, 3-methylheptamethylenediamine, 4,4-dimethylheptamethylenediamine,
4-methylnonamethylenediamine, 5-methylnonamethylenediamine, 2,5-dimethylhexamethylenediamine,
2,5-dimethylheptamethylenediamine, 2, 2-dimethylpropylenediamine, N-methyl-bis(3-aminopropyl)
amine, 3-methoxyhexamethylenediamine, 1,2-bis(3-aminopropoxy) ethane, bis(3-aminopropyl)
sulfide, 1,4-cyclohexanediamine, bis-(4-aminocyclohexyl) methane, m-phenylenediamine,
p-phenylenediamine, 2,4-diaminotoluene, 2,6-diaminotoluene, m-xylylenediamine, p-xylylenediamine,
2-methyl-4,6-diethyl-1,3-phenylene-diamine, 5-methyl-4,6-diethyl-1,3-phenylene-diamine,
benzidine, 3,3'-dimethylbenzidine, 3,3'-dimethoxybenzidine, 1,5-diaminonaphthalene,
bis(4-aminophenyl) methane, bis(2-chloro-4-amino-3,5-diethylphenyl) methane, bis(4-aminophenyl)
propane, 2,4-bis(p-amino-t-butyl) toluene, bis(p-amino-t-butylphenyl) ether, bis(p-methyl-o-aminophenyl)
benzene, bis(p-methyl-o-aminopentyl) benzene, 1, 3-diamino-4-isopropylbenzene, bis(4-aminophenyl)
sulfide, bis-(4-aminophenyl) sulfone (also known as 4,4'-diaminodiphenyl sulfone (DDS)),
and bis(4-aminophenyl) ether. Any regioisomer of the foregoing compounds can be used.
C
1-4 alkylated or poly(C
1-4)alkylated derivatives of any of the foregoing can be used, for example a polymethylated
1,6-hexanediamine. Combinations of these compounds can also be used. In an aspect
the organic diamine is m-phenylenediamine, p-phenylenediamine, 4,4'-diaminodiphenyl
sulfone, 3,4'-diaminodiphenyl sulfone, 3,3'-diaminodiphenyl sulfone, or a combination
comprising at least one of the foregoing.
[0019] The poly(etherimide) can have a melt index of 0.1 to 10 grams per minute (g/min),
as measured by American Society for Testing Materials (ASTM) D1238 at 340 to 370°C,
using a 6.7 kilogram (kg) weight. In an aspect, the poly(etherimide) has a weight
average molecular weight (Mw) of 1,000 to 150,000 grams/mole (Dalton), as measured
by gel permeation chromatography, using poly(styrene) standards. In an aspect the
poly(etherimide) has an Mw of 10,000 to 80,000 Daltons. Such poly(etherimides) typically
have an intrinsic viscosity greater than 0.2 deciliters per gram (dl/g), or, more
specifically, 0.35 to 0.7 dl/g as measured in m-cresol at 25°C.
[0020] The poly(aromatic ketone) comprises repeating units of formula (1)
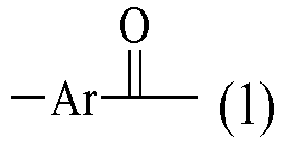
wherein Ar is independently at each occurrence a substituted or unsubstituted, monocyclic
or polycyclic aromatic group having 6-30 carbons. Exemplary Ar groups include, but
are not limited to, substituted or unsubstituted phenyl, tolyl, naphthyl, and biphenyl.
Unsubstituted phenyl is preferred. In an aspect, the poly(aromatic ketone) can be
a poly(arylene ether ketone) (PAEK) comprising repeating units of formula (1) and
formula (2)
-Ar-O- (2)
wherein Ar is defined as above. In an aspect the poly(aromatic ketone) comprises a
poly(ether ketone). A poly(ether ketone) comprises repeating units of formula (3)
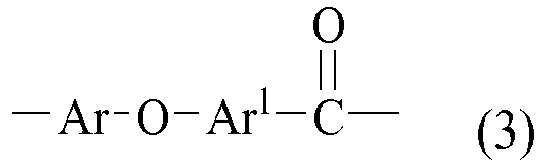
wherein Ar is defined as above and Ar
1 is independently at each occurrence a substituted or unsubstituted, monocyclic or
polycyclic aromatic group having 6-30 carbons. Ar can be the same as or different
from Ar
1. In an aspect Ar and Ar
1 are phenyl groups, preferably unsubstituted phenyl groups.
[0021] In an aspect, the poly(aromatic ketone) comprises a poly(ether ether ketone). A poly(ether
ether ketone) comprises repeating units of formula (4)
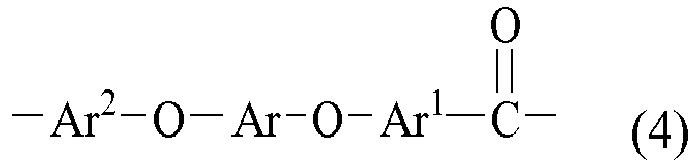
wherein Ar and Ar
1 are defined as above. Ar
2 is independently at each occurrence a substituted or unsubstituted, monocyclic or
polycyclic aromatic group having 6-30 carbons. Ar, Ar
1, and Ar
2 can be the same as or different from each other. Additionally, two of Ar, Ar
1, and Ar
2 can be the same as each other and the third can be different. In an aspect Ar, Ar
1, and Ar
2 are phenyl groups, preferably unsubstituted phenyl groups.
[0022] Poly(arylene ether ketone)s are generally known, with many examples being commercially
available. Examples of commercially available aromatic poly(ketone)s include those
sold under the trade name PEEK™, available from VICTREX.
[0023] In an aspect, the poly(aromatic ketone) comprises a poly(ether ketone), poly(ether
ether ketone), poly(ether ketone ketone), or a combination thereof, preferably a poly(ether
ether ketone) of formula (4).
[0024] In an aspect, the lower portion can include a combination of the poly(etherimide)
and the poly(aromatic ketone), wherein the poly(etherimide) can be present in an amount
of 10 to 90 weight percent, or 20 to 80 weight percent, or 25 to 75 weight percent,
or 25 to 50 weight percent, or 50 to 75 weight percent, and the poly(aromatic ketone)
can be present in an amount of 10 to 90 weight percent, or 20 to 80 weight percent,
or 25 to 75 weight percent or 50 to 75 weight percent, or 25 to 50 weight percent,
wherein weight percent of each component is based on the total weight of the poly(etherimide)
and the poly(aromatic ketone).
[0025] The lower portion of the retaining ring can optionally exclude any polymer other
than the poly(etherimide) and the poly(aromatic ketone).
[0026] In addition to the annular metal backbone and the lower portion, the retaining ring
of the present disclosure further comprises an upper portion comprising a thermoplastic
polymer. Particularly suitable thermoplastic polymers for the upper portion are chemically
stable at a pH of between 2 and 12, have a glass transition temperature (Tg) that
is less than or equal to the glass transition temperature of the composition of the
lower portion of the retaining ring, and have a heat deflection temperature (HDT)
that is less than or equal to the heat deflection temperature of the lower portion.
Thermoplastic polymers can also have a coefficient of thermal expansion (CTE) of 20
to 80 ppm/°C. Tg and HDT can be determined, for example, according to the methods
described in the working examples below. Coefficient of thermal expansion (CTE) can
be determined, for example, with flow by ASTM E831 from -20 to 150°C. The thermoplastic
polymer of the upper portion can be the same or different from the composition of
the lower portion. Preferably, the upper portion of the retaining ring has a composition
that is different from the lower portion of the retaining ring. For example, the upper
portion preferably does not include a poly(etherimide) or a combination of a poly(etherimide)
and a poly(aromatic ketone). In an aspect, the upper portion comprises a poly(aromatic
ketone), a poly(phenylene sulfone), a poly(carbonate), a poly(ethylene terephthalate),
a poly(butylene terephthalate), a poly(ethylene), a poly(propylene), or a combination
thereof.
[0027] In an aspect, the upper portion, the lower portion, or both can each independently
further comprise an additive composition comprising one or more additives selected
to achieve a desired property (e.g., improved adhesion, flowability, processability,
miscibility, and the like), with the proviso that the additive(s) are also selected
so as to not significantly adversely affect a desired property of the thermoplastic
composition. The additive composition or individual additives can be mixed at a suitable
time during the mixing of the components for forming the compositions of the upper
of lower portions. The additive composition can include, for example, an impact modifier,
flow modifier, filler (e.g., a particulate polytetrafluoroethylene (PTFE), glass,
carbon, mineral, or metal), reinforcing agent (e.g., glass fibers), antioxidant, heat
stabilizer, light stabilizer, ultraviolet (UV) light stabilizer, UV absorbing additive,
plasticizer, lubricant, release agent (such as a mold release agent), antistatic agent,
anti-fog agent, antimicrobial agent, colorant (e.g, a dye or pigment), surface effect
additive, radiation stabilizer, flame retardant, anti-drip agent (e.g., a PTFE-encapsulated
styrene-acrylonitrile copolymer (TSAN)), or a combination thereof. The additives can
be used in amounts generally known to be effective. For example, the total amount
of the additive composition (other than any impact modifier, filler, or reinforcing
agent) can be 0.001 to 10.0 weight percent (wt%), or 0.01 to 5 wt%, each based on
the total weight of the composition.
[0028] The lower portion of the retaining ring can optionally further comprise a plurality
of channels in the bottom surface extending from an inner edge of the retaining ring
to an outer edge of the retaining ring. The channels can facilitate the transfer of
the slurry in and out of the retaining ring during a polishing process. An illustration
of an aspect wherein the retaining ring includes channels on the bottom surface of
the lower portion of the retaining ring is shown in FIG. 2. The depth of the channels
can be modified (e.g., made deeper or more shallow) to accommodate or modify the flow
of fluid (polishing slurry or other liquid) into and out of the retaining ring, where
the substrate is located. The channel cross section can have a rectangular shape,
a radius shape, or any other suitable shape. The shape of the cross section of the
channel can be chosen to reduce or eliminate low flow areas or dead volumes in the
channels.
[0029] In an aspect, the lower portion of the retaining ring is configured such that it
can be replaced in the event of excessive wear after a polishing process. Advantageously,
the lower portion can be removed and replaced without affecting the annular backbone
or the upper portion.
[0030] The retaining ring of the present disclosure can be made by a method comprising molding
the lower portion from a poly(etherimide) or a combination of a poly(etherimide) and
a poly(aromatic ketone); molding the upper portion from a thermoplastic polymer, and
bonding together the lower portion, the upper portion, and the annular metal backbone,
such that the annular metal backbone is positioned between the upper portion and the
lower portion, as described above. In an aspect, the bonding of the lower portion,
the upper portion, and the annular metal backbone is by an overmolding process wherein
the upper and lower portions are molded in the presence of the annular metal backbone.
Stated another way, the upper and lower portions can be formed or molded directly
over or around the annular metal backbone. This process can also be referred to as
a metal insert molding process. In an aspect, the retaining ring can be made by a
double injection molding process. In an aspect, the upper and lower portions can each
be molded individually, and then can be bonded together with the annular metal backbone
to form the retaining ring.
[0031] The method can further comprise creating a plurality of channels in the bottom surface
of the lower portion of the retaining ring.
[0032] The retaining ring of the present disclosure can be particularly useful in a chemical
mechanical polishing system. Thus, another aspect of the present disclosure is a chemical
mechanical polishing system comprising the above-described retaining ring.
[0033] This disclosure is further illustrated by the following examples, which are nonlimiting.
EXAMPLES
[0034] Materials used in the following examples are summarized in Table 1.
Table 1
Component |
Description |
Supplier |
PEEK |
Polyether ether ketone obtained as VICTREX PEEK 450G |
Victrex PLC |
PEI-1 |
Polyetherimide blend obtained as ULTEM Resin DH1004 |
SABIC |
PEI-2 |
Polyetherimide having a glass transition temperature of 225°C, obtained as ULTEM Resin
CRS5011 |
SABIC |
PEI-3 |
Polyetherimide having a glass transition temperature of 225°C, obtained as ULTEM Resin
CRS5001 |
SABIC |
[0035] Table 2 summarizes the composition of the test samples for Examples 1-6, with Example
1 being a Comparative Example. The amount of each component is given in weight percent
based on the total weight of the composition
Table 2
Component |
1* |
2 |
3 |
4 |
5 |
6 |
PEEK |
100 |
|
|
75 |
50 |
25 |
PEI-1 |
|
100 |
|
|
|
|
PEI-2 |
|
|
100 |
|
|
|
PEI-3 |
|
|
|
25 |
50 |
75 |
[0036] The material properties of each of Examples 1-6 was examined, and the results are
provided in Table 3. Glass transition temperature (Tg) was determined using differential
scanning calorimetry (DSC). Flexural Modulus was determined according to ASTM D732
using a rate of 1.27 mm/min. Heat deflection temperature (HDT) was determined according
to ASTM D648 (1.82 MPa, 3.2 mm). Tensile Modulus was determined according to ASTM
D638 (50 mm/min). Tensile Strength and Tensile Elongation were determined according
to ASTM D638 (50mm/min).
Table 3
Property (units) |
1* |
2 |
3 |
4 |
5 |
6 |
Amorphous/ Crystalline |
Crystalline → Semi crystalline |
Amorphous |
Amorphous |
Crystalline/Amorphous blend |
Crystalline/Amorphous blend |
Crystalline/Amorphous blend |
Tg (°C) |
143 |
216 |
216 |
164 |
165 |
220 |
Flex. Mod. (MPa) |
3.8 |
3.0 |
3.1 |
2.87 |
2.92 |
2.96 |
HDT (°C) |
152 |
204 |
204 |
145 |
148 |
158 |
Tens. Mod. (GPa) |
4 |
2.9 |
2.89 |
2.92 |
2.97 |
3.03 |
Tens. Strength @ yield (MPa) |
98 |
95 |
99 |
83.5 |
86.7 |
90.1 |
Tens. Strength @ brk (MPa) |
- |
- |
- |
58.9 |
70.6 |
68.9 |
Tens. Elong. @ yield (%) |
45 |
85 |
60 |
59 |
62 |
64 |
Tens. Elong. @ brk (%) |
- |
- |
- |
38.4 |
63.1 |
22.6 |
[0037] Round disk test samples for each example were prepared by a mold press process. Each
disk had a diameter of 10 centimeters and a thickness of 3.0 millimeters.
[0038] Each sample was evaluated for chemical resistance after immersing the test sample
into a colloidal silica slurry obtained as COMPOL 80 slurry from Fujimi Corporation
for 48 hours. The thickness of the sample was measured before and after dipping and
the measurements were compared. The thickness change for each sample is shown in FIG.
3, where it is seen that both PEI-1 and PEI-2 of examples 2 and 3, respectively, exhibited
similar change in thickness as the comparative example using PEEK. Example 4 exhibited
the greatest thickness change of 1.5%. Example 5 exhibited a thickness change of 0.75%,
and Example 6 exhibited a thickness change of 0.25%.
[0039] Each sample was also evaluated for abrasion resistance using a Taber abrasion test
(Grinding test) according to ASTM D4060. The load weight used was 500 grams x 2, and
a spin rate of 60 rpm was used with 5000 spins. CS-17 Calibrase abrasive wheels were
used. The abrasion test was conducted on each samples before and after immersing the
sample in COMPOL 80. The results of the abrasion testing are summarized in Table 4.
Table 4
|
1* |
2 |
3 |
4 |
5 |
6 |
Weight change before immersion |
0.0695 |
0.0678 |
0.1022 |
0.0702 |
0.0698 |
0.0698 |
Weight change after immersion |
0.0696 |
0.0681 |
0.1016 |
0.0701 |
0.0700 |
0.0354 |
[0040] After the Taber abrasion testing, abrasion particles and residue left on the Taber
testing machine were collected, and these samples were analyzed by scanning electron
microscopy (SEM) to determined particle size, size distribution, and particle appearance.
[0041] The chipped particle size was 10 micrometers and was in the form of a flake. Example
3 showed the most similar chipping to Comparative Example 1. Significant changes in
the appearance were not noted before and after immersion in the slurry. SEM images
for Examples 1-6 are shown in FIG. 4. The chipped particle size distributions for
Examples 1 and 3 were found to be 6.2 to 8 micrometers, and particle size distribution
for Example 2 was 3.1 to 4 micrometers. Particle size was measured by dynamic light
scattering (DLS) using an Otsuka Photal ELS-8000 DLS.
[0042] The surface hardness of each example was also evaluated using a Rockwell surface
hardness test according to ISO 2039-2. The surface hardness of the samples was compared
before and after immersion in the colloidal silica slurry. Results are summarized
in Table 5, where surface hardness is reported as HRM. The test used a test force
of 980 Newtons, a dwell time of 4 seconds and the indenter used was as ¼" ball.
Table 5
|
1* |
2 |
3 |
4 |
5 |
6 |
Hardness before immersion |
93.60 |
98.53 |
94.87 |
72.83 |
79.90 |
83.23 |
Hardness after immersion |
94.07 |
94.90 |
98.10 |
74.03 |
78.67 |
79.63 |
[0043] As seen in Table 5, the PEI and PEI/PEEK compositions each exhibited similar surface
hardness before and after immersion in the slurry. Examples 1-3 exhibited comparable
surface hardness.
[0044] Surface hardness was also evaluated using a Pencil surface hardness test according
to ASTM D3363. The surface hardness of the samples was compared before and after immersion
in the colloidal silica slurry. Results are summarized in Table 6. The test used a
load cell of 1 kilogram and a stage speed of 25 rpm. The Pencil hardness scale, ranges
from soft to hard: 6B, 5B, 4B, 3B, 2B, B, HB, F, H, 2H, 3H, 4H, 5H, 6H, 7H, 8H, 9H.
Table 6
|
1* |
2 |
3 |
4 |
5 |
6 |
Hardness before immersion |
B |
B |
B |
2B |
B |
B |
Hardness after immersion |
B |
B |
B |
2B |
B |
B |
[0045] This disclosure further encompasses the following aspects.
Aspect 1: A retaining ring for use in a chemical mechanical polishing process, comprising:
an annular metal backbone (1); a lower portion (2) having a bottom surface for contacting
a polishing pad during polishing, the lower portion comprising a poly(etherimide)
or a combination of a poly(etherimide) and a poly(aromatic ketone); and an upper portion
(3) comprising a thermoplastic polymer; wherein the annular metal backbone is positioned
between the lower portion and the upper portion.
Aspect 2: The retaining ring of aspect 1, wherein the thermoplastic polymer of the
upper portion is chemically stable at a pH of greater than 2 and less than 12; has
a coefficient of thermal expansion of 20 to 80 ppm/°C; has a glass transition temperature
that is less than or equal to a glass transition temperature of the lower portion;
and has a heat deflection temperature that is less than or equal to a heat deflection
temperature of the lower portion, wherein HDT is determined according to ASTM D648
at 1.82 MPa and 3.2 mm.
Aspect 3: The retaining ring of aspect 1 or 2, wherein the thermoplastic polymer is
different from the poly(etherimide) or the combination of the poly(etherimide) and
the poly(aromatic ketone).
Aspect 4: The retaining ring of any of aspects 1 to 3, wherein the poly(aromatic ketone)
comprises poly(ether ether ketone).
Aspect 5: The retaining ring of any of aspects 1 to 4, wherein the poly(etherimide)
comprises repeating units derived from bisphenol A dianhydride and para-phenylene
diamine.
Aspect 6: The retaining ring of any of aspects 1 to 5, wherein the lower portion comprises
the poly(etherimide).
Aspect 7: The retaining ring of any of aspects 1 to 4, wherein the lower portion comprises
the combination of the poly(etherimide) and the poly(aromatic ketone).
Aspect 8: The retaining ring of aspect 7, wherein the lower portion comprises 10 to
90 weight percent, or 20 to 80 weight percent, or 25 to 75 weight percent of the poly(etherimide);
and 10 to 90 weight percent, or 20 to 80 weight percent, or 25 to 75 weight percent
of the poly(aromatic ketone); wherein weight percent of each component is based on
the total weight of the poly(etherimide) and the poly(aromatic ketone).
Aspect 9: The retaining ring of any of aspects 1 to 8, wherein the upper portion comprises
a poly(aromatic ketone), a poly(phenylene sulfone), a poly(carbonate), a poly(ethylene
terephthalate), a poly(butylene terephthalate), a poly(ethylene), a poly(propylene),
or a combination thereof.
Aspect 10: The retaining ring of any of aspects 1 to 9, wherein the annular metal
backbone comprises aluminum, stainless steel, molybdenum, a ceramic, or a combination
thereof.
Aspect 11: The retaining ring of any of aspects 1 to 10, wherein the upper portion,
the lower portion, or both, further comprise an additive composition comprising an
impact modifier, flow modifier, filler, reinforcing agent, antioxidant, heat stabilizer,
light stabilizer, ultraviolet (UV) light stabilizer, UV absorbing additive, plasticizer,
lubricant, release agent, antistatic agent, anti-fog agent, antimicrobial agent, colorant,
surface effect additive, radiation stabilizer, flame retardant, anti-drip agent, or
a combination thereof.
Aspect 12: The retaining ring of any of aspects 1 to 11, wherein the lower portion
further comprises a plurality of channels in the bottom surface extending from an
inner edge of the retaining ring to an outer edge of the retaining ring, wherein the
channels are effective to transfer a slurry during a polishing process.
Aspect 13: A method of manufacturing the retaining ring of any of aspects 1 to 12,
the method comprising, molding the lower portion from a poly(etherimide) or a combination
of a poly(etherimide) and a poly(aromatic ketone); molding the upper portion from
a thermoplastic polymer; bonding the lower portion, the upper portion, and the annular
metal backbone, such that the annular metal backbone is positioned between the upper
portion and the lower portion.
Aspect 14: The method of aspect 13, wherein bonding the lower portion, the upper portion,
and the annular metal backbone is by an overmolding process wherein the upper and
lower portions are bonded in the presence of the annular metal backbone.
Aspect 15: A chemical mechanical polishing system comprising the retaining ring of
any of aspects 1 to 12.
[0046] The compositions, methods, and articles can alternatively comprise, consist of, or
consist essentially of, any appropriate materials, steps, or components herein disclosed.
The compositions, methods, and articles can additionally, or alternatively, be formulated
so as to be devoid, or substantially free, of any materials (or species), steps, or
components, that are otherwise not necessary to the achievement of the function or
objectives of the compositions, methods, and articles.
[0047] All ranges disclosed herein are inclusive of the endpoints, and the endpoints are
independently combinable with each other. "Combinations" is inclusive of blends, mixtures,
alloys, reaction products, and the like. The terms "first," "second," and the like,
do not denote any order, quantity, or importance, but rather are used to distinguish
one element from another. The terms "a" and "an" and "the" do not denote a limitation
of quantity, and are to be construed to cover both the singular and the plural, unless
otherwise indicated herein or clearly contradicted by context. "Or" means "and/or"
unless clearly stated otherwise. Reference throughout the specification to "some aspects",
"an aspect", and so forth, means that a particular element described in connection
with the aspect is included in at least one aspect described herein, and may or may
not be present in other aspects. The term "combination thereof' as used herein includes
one or more of the listed elements, and is open, allowing the presence of one or more
like elements not named. In addition, it is to be understood that the described elements
may be combined in any suitable manner in the various aspects.
[0048] Unless specified to the contrary herein, all test standards are the most recent standard
in effect as of the filing date of this application, or, if priority is claimed, the
filing date of the earliest priority application in which the test standard appears.
[0049] Unless defined otherwise, technical and scientific terms used herein have the same
meaning as is commonly understood by one of skill in the art to which this application
belongs. All cited patents, patent applications, and other references are incorporated
herein by reference in their entirety. However, if a term in the present application
contradicts or conflicts with a term in the incorporated reference, the term from
the present application takes precedence over the conflicting term from the incorporated
reference.
[0050] Compounds are described using standard nomenclature. For example, any position not
substituted by any indicated group is understood to have its valency filled by a bond
as indicated, or a hydrogen atom. A dash ("-") that is not between two letters or
symbols is used to indicate a point of attachment for a substituent. For example,
-CHO is attached through carbon of the carbonyl group.
[0051] As used herein, the term "hydrocarbyl", whether used by itself, or as a prefix, suffix,
or fragment of another term, refers to a residue that contains only carbon and hydrogen.
The residue can be aliphatic or aromatic, straight-chain, cyclic, bicyclic, branched,
saturated, or unsaturated. It can also contain combinations of aliphatic, aromatic,
straight chain, cyclic, bicyclic, branched, saturated, and unsaturated hydrocarbon
moieties. However, when the hydrocarbyl residue is described as substituted, it may,
optionally, contain heteroatoms over and above the carbon and hydrogen members of
the substituent residue. Thus, when specifically described as substituted, the hydrocarbyl
residue can also contain one or more carbonyl groups, amino groups, hydroxyl groups,
or the like, or it can contain heteroatoms within the backbone of the hydrocarbyl
residue. The term "alkyl" means a branched or straight chain, unsaturated aliphatic
hydrocarbon group, e.g., methyl, ethyl, n-propyl, i-propyl, n-butyl, s-butyl, t-butyl,
n-pentyl, s-pentyl, and n- and s-hexyl. "Alkenyl" means a straight or branched chain,
monovalent hydrocarbon group having at least one carbon-carbon double bond (e.g.,
ethenyl (-HC=CH
2)). "Alkoxy" means an alkyl group that is linked via an oxygen (i.e., alkyl-O-), for
example methoxy, ethoxy, and sec-butyloxy groups. "Alkylene" means a straight or branched
chain, saturated, divalent aliphatic hydrocarbon group (e.g., methylene (-CH
2-) or, propylene (-(CH
2)
3-)). "Cycloalkylene" means a divalent cyclic alkylene group, -C
nH
2n-x, wherein x is the number of hydrogens replaced by cyclization(s). "Cycloalkenyl"
means a monovalent group having one or more rings and one or more carbon-carbon double
bonds in the ring, wherein all ring members are carbon (e.g., cyclopentyl and cyclohexyl).
"Aryl" means an aromatic hydrocarbon group containing the specified number of carbon
atoms, such as phenyl, tropone, indanyl, or naphthyl. "Arylene" means a divalent aryl
group. "Alkylarylene" means an arylene group substituted with an alkyl group. "Arylalkylene"
means an alkylene group substituted with an aryl group (e.g., benzyl). The prefix
"halo" means a group or compound including one more of a fluoro, chloro, bromo, or
iodo substituent. A combination of different halo groups (e.g., bromo and fluoro),
or only chloro groups can be present. The prefix "hetero" means that the compound
or group includes at least one ring member that is a heteroatom (e.g., 1, 2, or 3
heteroatom(s)), wherein the heteroatom(s) is each independently N, O, S, Si, or P.
"Substituted" means that the compound or group is substituted with at least one (e.g.,
1, 2, 3, or 4) substituents that can each independently be a C
1-9 alkoxy, a C
1-9 haloalkoxy, a nitro (-NO
2), a cyano (-CN), a C
1-6 alkyl sulfonyl (-S(=O)
2-alkyl), a C
6-12 aryl sulfonyl (-S(=O)
2-aryl), a thiol (-SH), a thiocyano (-SCN), a tosyl (CH
3C
6H
4SO
2-), a C
3-12 cycloalkyl, a C
2-12 alkenyl, a C
5-12 cycloalkenyl, a C
6-12 aryl, a C
7-13 arylalkylene, a C
4-12 heterocycloalkyl, and a C
3-12 heteroaryl instead of hydrogen, provided that the substituted atom's normal valence
is not exceeded. The number of carbon atoms indicated in a group is exclusive of any
substituents. For example -CH
2CH
2CN is a C
2 alkyl group substituted with a nitrile.
[0052] While particular aspects have been described, alternatives, modifications, variations,
improvements, and substantial equivalents that are or may be presently unforeseen
may arise to applicants or others skilled in the art. Accordingly, the appended claims
as filed and as they may be amended are intended to embrace all such alternatives,
modifications variations, improvements, and substantial equivalents.
1. A retaining ring for use in a chemical mechanical polishing process, comprising:
an annular metal backbone (1);
a lower portion (2) having a bottom surface for contacting a polishing pad during
polishing, the lower portion comprising a poly(etherimide) or a combination of a poly(etherimide)
and a poly(aromatic ketone); and
an upper portion (3) comprising a thermoplastic polymer;
wherein the annular metal backbone is positioned between the lower portion and the
upper portion.
2. The retaining ring of claim 1, wherein the thermoplastic polymer of the upper portion
is chemically stable at a pH of greater than 2 and less than 12;
has a coefficient of thermal expansion of 20 to 80 ppm/°C, determined with flow by
ASTM E831 from -20 to 150°C;
has a glass transition temperature that is less than or equal to a glass transition
temperature of the lower portion, wherein glass transition temperature is determined
by differential scanning calorimetry; and
has a heat deflection temperature that is less than or equal to a heat deflection
temperature of the lower portion, wherein HDT is determined according to ASTM D648
at 1.82 MPa and 3.2 mm.
3. The retaining ring of claim 1, wherein the thermoplastic polymer is different from
the poly(etherimide) or the combination of the poly(etherimide) and the poly(aromatic
ketone).
4. The retaining ring of any of claims 1 to 3, wherein the poly(aromatic ketone) comprises
poly(ether ether ketone).
5. The retaining ring of any of claims 1 to 4, wherein the poly(etherimide) comprises
repeating units derived from bisphenol A dianhydride and para-phenylene diamine.
6. The retaining ring of any of claims 1 to 5, wherein the lower portion comprises the
poly(etherimide).
7. The retaining ring of any of claims 1 to 4, wherein the lower portion comprises the
combination of the poly(etherimide) and the poly(aromatic ketone).
8. The retaining ring of claim 7, wherein the lower portion comprises
10 to 90 weight percent, or 20 to 80 weight percent, or 25 to 75 weight percent of
the poly(etherimide); and
10 to 90 weight percent, or 20 to 80 weight percent, or 25 to 75 weight percent of
the poly(aromatic ketone);
wherein weight percent of each component is based on the total weight of the poly(etherimide)
and the poly(aromatic ketone).
9. The retaining ring of any of claims 1 to 8, wherein the upper portion comprises a
poly(aromatic ketone), a poly(phenylene sulfone), a poly(carbonate), a poly(ethylene
terephthalate), a poly(butylene terephthalate), a poly(ethylene), a poly(propylene),
or a combination thereof.
10. The retaining ring of any of claims 1 to 9, wherein the annular metal backbone comprises
aluminum, stainless steel, molybdenum, a ceramic, or a combination thereof.
11. The retaining ring of any of claims 1 to 10, wherein the upper portion, the lower
portion, or both, further comprise an additive composition comprising an impact modifier,
flow modifier, filler, reinforcing agent, antioxidant, heat stabilizer, light stabilizer,
ultraviolet (UV) light stabilizer, UV absorbing additive, plasticizer, lubricant,
release agent, antistatic agent, anti-fog agent, antimicrobial agent, colorant, surface
effect additive, radiation stabilizer, flame retardant, anti-drip agent, or a combination
thereof.
12. The retaining ring of any of claims 1 to 11, wherein the lower portion further comprises
a plurality of channels in the bottom surface extending from an inner edge of the
retaining ring to an outer edge of the retaining ring, wherein the channels are effective
to transfer a slurry during a polishing process.
13. A method of manufacturing the retaining ring of any of claims 1 to 12, the method
comprising,
molding the lower portion from a poly(etherimide) or a combination of a poly(etherimide)
and a poly(aromatic ketone);
molding the upper portion from a thermoplastic polymer;
bonding the lower portion, the upper portion, and the annular metal backbone, such
that the annular metal backbone is positioned between the upper portion and the lower
portion.
14. The method of claim 13, wherein bonding the lower portion, the upper portion, and
the annular metal backbone is by an overmolding process wherein the upper and lower
portions are bonded in the presence of the annular metal backbone.
15. A chemical mechanical polishing system comprising the retaining ring of any of claims
1 to 12.