CROSS REFERENCE TO RELATED APPLICATION
[0001] The present application claims priority to Korean Patent Application No.
10-2019-0058075, filed May 17, 2019, the entire contents of which is incorporated herein for all purposes by this reference.
BACKGROUND OF THE INVENTION
Field of the Invention
[0002] The present invention relates to a bone conduction mount structure for controlling
vibration magnitude by controlling a support position of an actuator and a method
of designing a mount module. More particularly, the present invention relates to a
bone conduction mount structure for controlling vibration magnitude by controlling
a support position of an actuator that reduces sound leakage or noise by controlling
a support position of an actuator that generates vibration and a method of designing
a mount module in a bone conduction technology that enables a user to recognize a
sound signal by transmitting vibration to bones of the user.
Description of the Related Art
[0003] Bone conduction means conduction of sound through bones of the skull, and transmission
of sound by bone conduction can be used for both of non-disabled people and the deaf,
and recently, products, including earphones, which started from the principle of a
hearing aid in the past are being actively developed.
[0004] The method of transmitting sound using bone conduction is implemented by transmitting
vibration to the tympanum through bones of a human using an actuator that generates
vibration with a specific pattern in response to an input signal and the vibration
can be transmitted in any direction around the ear of a human. Accordingly, there
is an advantage in that the usability is high and the actuator can be relatively freely
attached to any positions on bones.
[0005] The actuators that are used for bone conduction usually have a uni-axial vibration
characteristic and generate the same vibration not only in the bones that are supposed
to be vibrated, but also in the opposite direction.
[0006] The vibration generated in the opposite direction is transmitted to a structure such
as glasses through a support that supports the actuators. The vibration transmitted
to the structure generates vibration or sound leakage that exposes a sound signal
to the outside through the vibration. Further, the vibration that is transmitted outside
generates noise that a user can feel in some cases.
[0007] Such sound leakage from earphones that use bone conduction disturbs people at specific
places requiring silence such as a library. Further, sound information that a user
hears is exposed to the outside at places other than such specific places, so it is
difficult to ensure user privacy. Further, a problem with noise and fit that a user
feels due to vibration of a structure by an actuator can also not be overlooked.
[0008] A method for suppressing sound leakage of a bone conduction loudspeaker and a bone
conduction loudspeaker have been disclosed in Korean Patent Application Publication
No.
10-2017-0061188. It is disclosed in the publication document that vibration of a housing accommodating
a vibration plate is induced by forming one or more sound transmission holes in the
housing, sound waves in the housing are transmitted to the outside through the sound
transmission holes, and sound leakage is suppressed by generating interference with
specific leaking sound waves.
[0009] However, it is difficult to achieve accurate offset interference according to vibration
patterns reflecting various sound sources from the structure generating offset interference
in order to prevent sound leakage and it is required to generate specific leaking
sound waves, so there is a defect in that the structure is complicated and energy
efficiency is low.
[0010] Further, a bone conduction output device has been disclosed in Korean Patent No.
10-1603983, which discloses a structure that transmits vibration through a separate bone conduction
transmission member protruding from a case and supposed to come in contact with a
user's body and prevents bone conduction output from being distributed through the
case by preclude interference due to adjacent components when an elastic member vibrates
by defining spaces between a magnetic circuit and the elastic member and between the
elastic member and the bone conduction member.
[0011] However, this patent has a defect in that the vibration of the magnetic circuit is
completely transmitted to a structure for supporting the elastic member and the magnetic
circuit, so the effect of preventing sound leakage is not large.
Documents of Related Art
SUMMARY OF THE INVENTION
[0013] An object of the present invention that has been designed in consideration of the
problems described above is to provide a bone conduction mount structure that reduces
sound leakage and noise by minimizing rotation of an actuator by adjusting the support
position of the actuator that is supported by a support mount, and a method of designing
a mount module.
[0014] In order to achieve the objects of the present invention, a bone conduction mount
structure according to an aspect of the present invention includes: an actuator disposed
in a user's bone direction and generating and transmitting vibration to the bone;
and a support mount disposed to surround a portion of an outer side of the actuator,
supporting the actuator, and being able to be fixed to a structural member.
[0015] When the actuator is inserted into the support mount by external force, a difference
between a center of gravity and a rotational center of the actuator may decrease.
[0016] The support mount may have flexibility, the rotational center may change in accordance
with the degree of insertion of the actuator in the support mount by external force,
and the difference may gradually decrease until the external force reaches a predetermined
reference value.
[0017] When the actuator is inserted in the support mount, the center of gravity and the
rotational center may coincide.
[0018] A method of a mount module, which includes an actuator disposed in a user's bone
direction and generating and transmitting vibration to the bone, and a support mount
having flexibility, disposed to surround a portion of an outer side of the actuator,
supporting the actuator, and being able to be fixed to a structural member, according
to another aspect of the present invention includes: a first calculation step that
calculates a center of gravity of the actuator; a second calculation step that calculates
the degree of support of the actuator by the support mount in accordance with predetermined
external force; a third calculation step that calculates a rotational center of the
actuator on the basis of the degree of support calculated in the second calculation
step; and a position determination step that determines a support position of the
actuator by the support mount such that a difference between the center of gravity
and the rotational center decreases when the predetermined external force is applied
on the basis of the information calculated in the first calculation step to the third
calculation step.
[0019] The position determination step may determine the support position of the actuator
by the support mount according to the external force such that the center of gravity
and the rotational center coincide.
[0020] A method of a mount module, which includes an actuator disposed in a user's bone
direction and generating and transmitting vibration to the bone, and a support mount
having flexibility, disposed to surround a portion of an outer side of the actuator,
supporting the actuator, and being able to be fixed to a structural member, according
to another aspect of the present invention includes: a first calculation step that
calculates a center of gravity of the actuator; a second calculation step that calculates
the degree of support of the actuator by the support mount in accordance with predetermined
external force; a third calculation step that calculates a rotational center of the
actuator on the basis of the degree of support calculated in the second calculation
step; and a property determination step that determines properties of the support
mount such that a difference between the center of gravity and the rotational center
decreases when the predetermined external force is applied on the basis of the information
calculated in the first calculation step to the third calculation step.
[0021] The property determination step may adjust the degree of support of the actuator
by the support mount by determining the properties of the support mount such that
the center of gravity and the rotational center coincide.
[0022] According to the present invention, the difference between the center of gravity
and the rotational center of the actuator is minimized when external force is applied,
so rotational components of the actuator are decreased, whereby it is possible to
reduce sound leakage and noise.
[0023] Further, the structure of the present invention can be used for various bone conduction
devices and has high compatibility.
BRIEF DESCRIPTION OF THE DRAWINGS
[0024] The above and other objects, features and other advantages of the present invention
will be more clearly understood from the following detailed description when taken
in conjunction with the accompanying drawings, in which:
FIG. 1 is a conceptual diagram showing an ideal structure of an actuator and a support
mount;
FIG. 2 is a conceptual diagram showing the structure of a support mount reflecting
a rotational state of an actuator;
FIG. 3 is a graph showing noise due to the difference between the center of gravity
G and a rotational center R when an actuator is rotated;
FIG. 4 is a conceptual diagram showing a bone conduction mount structure for controlling
vibration magnitude by controlling a support position of an actuator according to
an embodiment of the present invention;
FIG. 5 is a flowchart showing a method of designing a mount module according to a
first embodiment of the present invention; and
FIG. 6 is a flowchart showing a method of designing a mount module according to a
second embodiment of the present invention.
DETAILED DESCRIPTION OF THE INVENTION
[0025] In the following description of the present invention, detailed descriptions of well-known
functions or configurations relating to the present invention will not be provided
so as not to obscure the description of the present invention with unnecessary details.
[0026] Embodiments described herein may be changed in various ways and various shapes, so
specific embodiments are shown in the drawings and will be described in detail in
this specification. However, it should be understood that the exemplary embodiments
according to the concept of the present invention are not limited to the embodiments
which will be described hereinbelow with reference to the accompanying drawings, but
all of modifications, equivalents, and substitutions are included in the scope and
spirit of the disclosure.
[0027] Terms used in the present invention are used only in order to describe specific exemplary
embodiments rather than limiting the present invention. Singular forms are intended
to include plural forms unless the context clearly indicates otherwise. It will be
further understood that the terms "comprises" or "have" used in this specification,
specify the presence of stated features, steps, operations, components, parts, or
a combination thereof, but do not preclude the presence or addition of one or more
other features, numerals, steps, operations, components, parts, or a combination thereof.
[0028] Hereinafter, the present invention is described in detail.
[0029] A bone conduction mount structure for controlling vibration magnitude by controlling
a support position of an actuator according to the present invention includes an actuator
100 and a support mount 200.
[0030] The actuator 100 of the present invention, which is a kind of device that vibrates
in response to an external input signal, converts an electrical signal into mechanical
vibration and then transmits the mechanical vibration to bones of a user. In detail,
the actuator 100 may include a magnet of which the magnetic flux is changed by a current
change of a coil that is supplied with a current from the outside, and may be a magnetic
circuit including the magnet. A yoke that is a path through which magnetic flux lines
pass, a top plate collecting magnetic force, etc. may be additionally included in
the magnetic circuit. In this case, the coil may be disposed inside or outside the
actuator 100.
[0031] A first side of the actuator 100 is disposed in a user's bone direction and a second
side is disposed in a structure direction. The structure comprehends concepts such
as a case surrounding the outer side of the support mount 200 or temples for fixing
to the body of a user and the structure direction may mean other directions except
for the user's bone direction. It is assumed hereafter that the structure direction
is an opposite direction to the user's bone direction.
[0032] The support mount 200 supports the actuator 100 while surrounding a portion, for
example, the second side of the actuator 100. A damper that attenuates vibration transmission
to the structure may be disposed inside or outside the support mount 200.
[0033] The support mount 200 has both of elasticity and flexibility and may have a structure
in a first side of which the actuator 100 is inserted. For example, the support mount
200 may be made of a silicon material. The first side in which the actuator 100 is
inserted may be positioned in the direction to the user's bone, so the first side
of the actuator 100 may be exposed in the user's bone direction with the first side
inserted in the support mount 200.
[0034] In an embodiment, when the actuator 100 is not in contact with a bone of a user,
it partially protrudes out of the support mount 200. When the protruding actuator
100 comes in contact with the body of a user, the degree of protrusion is decreased
by external force that is generated in this case, so the actuator 100 can be partially
or entirely inserted in the support mount 200.
[0035] The support mount 200 may have a compressive portion that is pushed toward the structure
by flexibility when the actuator 100 is inserted, and a flexible portion disposed
outside the compressive portion.
[0036] When the actuator 100 is pushed inward by external force, the compressive portion
increases and the flexible portion decreases in rigidity.
[0037] Such changes in rigidity results in an effect that further pushes the actuator 100
in the user's bone direction, and when the flexible portion of the support mount 200
is connected to the structure, the rigidity decreases and a small amount of vibration
is transmitted, so an effect of preventing sound leakage can be expected.
[0038] In the present invention, when the actuator 100 is inserted into the support mount
200 by external force, the difference E between the center of gravity G and the rotational
center R of the actuator 100 may decrease.
[0039] Further, the rotational center R changes in accordance with the degree of insertion
of the actuator 100 in the support mount 200 by external force, the difference E may
gradually decrease until the external force reaches a predetermined reference value,
and the center of gravity G and the rotational center R may coincide.
[0040] The effect that is achieved by reducing the difference E between the center of gravity
G and the rotational center R is described in detail hereafter with reference to FIGS.
1 to 4.
[0041] FIG. 1 is a conceptual diagram showing an ideal structure of the actuator 100 and
the support mount 200, FIG. 2 is a conceptual diagram showing the structure of the
support mount 200 reflecting a rotational state of the actuator 100, FIG. 3 is a graph
showing noise due to the difference between the center of gravity G and the rotational
center R when an actuator 100 is rotated, and FIG. 4 is a conceptual diagram showing
a bone conduction mount structure for controlling vibration magnitude by controlling
a support position of an actuator according to an embodiment of the present invention.
[0042] The rotational center R of the actuator 100 is the same as the center of gravity
G when the actuator 100 is not supported through the support mount 200. However, a
difference from the center of gravity G is generated when the actuator 100 is supported
through the support mount 200. When the actuator 100 is not supported through a specific
structure and there is no external force, the actuator 100 protrudes from the support
mount 200. The rotational center R of the actuator 100 is the center of a rotational
motion of the actuator 100 when it is supported through the support mount 200, and
is the center of the position when it is supported by the support mount 200. For example,
assuming that the actuator 100 is rotated about a Z axis in an X-Y plane, the rotational
center R may mean the center of the area of the actuator 100 supported through the
support mount 200. Alternatively, assuming 3D space coordinates, the rotational center
R may mean the center of the volume of the actuator 100 supported through the support
mount 200.
[0043] The difference E between the rotational center R and the center of gravity G causes
a specific acceleration component, which results in an additional load that is proportioned
to a rotational angular speed. The additional load is a load except for external force
that is generated by contact with the body of a user and is a component that is proportioned
to angular acceleration that is not in a control range. Accordingly, when a user wears
a product having the actuator 100 and the support mount 200 such as a bone conduction
earphone, he/she feels noise type of vibration.
[0044] Referring to FIG. 1, the actuator 100 transmits desired vibration to a bone of a
user by vertically vibrating in the figure and the state of the structural diagram
of FIG. 1 is shown in an ideal case without a rotational motion. In the structure
of FIG. 1, GR indicates a structure adjacent to the support mount 200 supporting the
actuator 100, K
A indicates an equivalent spring of the support mount 200 supporting the actuator 100,
and left and right equivalent springs are not arranged in the acting direction of
external force and arranged in directions different from the vibration direction of
the actuator 100, so their force can be assumed as 0. In this case, the actuator 100
is vertically motioned with force F. In this condition, there is no motion in the
X-axial direction, so a governing equation is derived about the Y-axis as in the following
Equation 1.
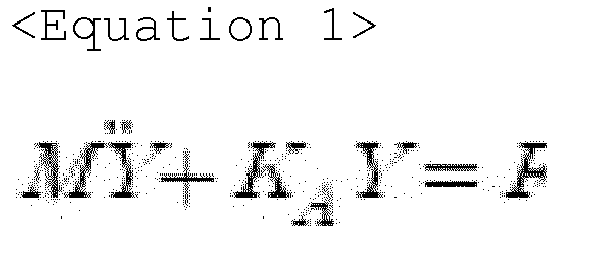
where M is equivalent mass of the actuator 100.
[0045] The effect of K
A can be excepted in an ideal vibration motion of the actuator 100 without a rotational
motion, but the state of the structural diagram shown in FIG. 2 is shown when a rotational
motion is considered.
[0046] Referring to FIGS. 2 and 3, equivalent rigidity of the support mount 200 is shown
by K
X and K
Y in different directions. In this condition, the center of gravity G of the actuator
100 can be expressed as in the following Equations 2 and 3.
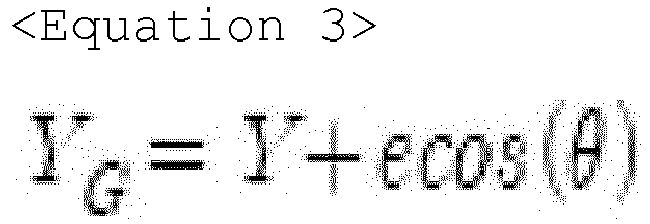
where X
G is the center of gravity G of the actuator 100 in the X-axial direction and Y
G is the center of gravity G of the actuator 100 in the Y-axial direction.
[0047] Equation 2 is expressed as the governing equation of the following Equation 4 and
Equation 3 is expressed as the governing equation of the following Equation 5.

[0048] In the above condition, it is assumed that the X-axial equivalent rigidity KX is
too small, so it can be ignored. The value of the rotational angle θ is so small,
so it has very little influence on a vibration response of the actuator 100 for the
characteristics of the sine function in Equation 4, an X-axial dynamic response can
be ignored.
[0049] For the Y axis, the rotational angle θ is small, so the angular speed
θ̈ can be ignored, but the angular acceleration
θ̈ cannot be ignored because the rotational angle continuously changes while vertical
vibration is generated. In this condition, Equation 5 can be expressed as the following
approximate formula.
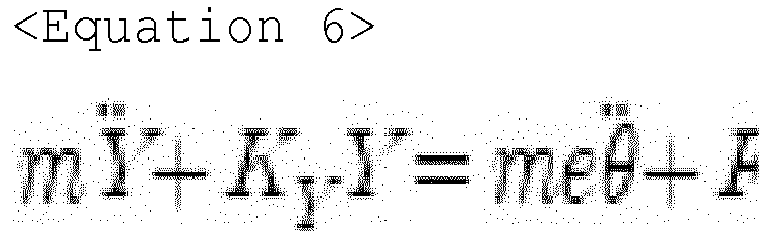
[0050] Referring to Equation 6, there is a value except for the load F that is generated
by the actuator F, so an undesired magnitude of an additional load is determined in
proportion to the difference E between the center of gravity G and the rotational
center R. In particular, a motion in the rotational direction is generated irregularly
with a positive value and a negative value within a very small range by vertical vibration,
so it is possible to remove an additional load due to undesired rotation by adjusting
the position of the actuator 100 supported by the support mount 200 in order to minimize
the difference E.
[0051] Referring to FIG. 4, the support position of the actuator 100 supported by the support
mount 200 is determined to minimize the difference E between the center of gravity
G and the rotational center R. According to the present invention, the actuator 100
is inserted into the support mount 200 by external force that is applied to the actuator
when a user wears the bone conduction device, and when the actuator 100 is inserted
in the support mount 200, the degree and depth of insertion of the actuator 100 can
be adjusted to reduce the difference E. In this case, the external force applied to
the actuator may have predetermined magnitude.
[0052] The rotational center of the actuator 100 depends on the insertion position and depth
of the actuator and the difference E can be gradually reduced until the external force
reached a predetermined reference value. For example, assuming that the value of a
load that is applied to the actuator 100 when a user finishes putting on the bone
conduction device is a reference value, the difference E is the minimum when the user
finishes putting on the bone conduction device, so components due to rotation of the
actuator 100 can be minimized.
[0053] Further, the center of gravity G and the rotational center R can coincide. In this
case, considering the external force that is generated when the bone conduction device
is worn, the difference E between the center of gravity G and the rotational center
R may gradually decrease until the external force reaches the reference value, and
when the external force reaches the reference value, the difference E may be 0.
[0054] Referring to FIG. 3, the red (point 4) indicates amplitude according to the frequency
of the actuator 100 when there is the difference between the center of gravity G and
the rotational center R, and the black (point 2) indicates amplitude according to
the frequency of the actuator 100 when the center of gravity G and the rotational
center R coincide.
[0055] As shown in FIG. 3, it can be seen when there is the difference E, very large amplitude
is shown in a low frequency band and the amplitude gradually decreases in a high frequency
band. This means that, under the same external force, noise is generated at a low
frequency and a required bone conduction effect cannot be effectively achieved at
a high frequency.
[0056] However, it can be seen when the center of gravity G and the rotational center R
coincide in accordance with the present invention, relatively uniform amplitude is
obtained and the bone conduction effect is achieved regardless of the frequency band.
[0057] As described above, since the rotational components due to vibration of the actuator
100 are reduced by minimizing the center of gravity G and the rotational center R
of the actuator 100 that generates vibration in the present invention, there is an
advantage in that noise and sound leakage that a user feels can be reduced.
[0058] Hereafter, a method of designing a mount module according to the present invention
is described.
[0059] The method of designing a mount module according to an embodiment of the present
invention, which is a kind of method of designing a mount module including an actuator
100 that is disposed in a user's bone direction and generates and transmits vibration
to the bone, and a support mount 200 that has flexibility, is disposed to surround
a portion of the outer side of the actuator 100, supports the actuator 100, and can
be fixed to a structural member, is described hereafter with reference to a first
embodiment and a second embodiment.
[0060] FIG. 5 is a flowchart showing a method of designing a mount module according to a
first embodiment of the present invention and FIG. 6 is a flowchart showing a method
of designing a mount module according to a second embodiment of the present invention.
First Embodiment
[0061] Referring to FIG. 5, a method of designing a mount module according to the first
embodiment includes: a first calculation step (S100) that calculates the center of
gravity G of the actuator 100; a second calculation step (S200) that calculates the
degree of support of the actuator 100 by the support mount 200 in accordance with
predetermined external force; a third calculation step (S300) that calculates the
rotational center R of the actuator 100 on the basis of the degree of support calculated
in the second calculation step (S200); and a position determination step (S400) that
determines a support position of the actuator 100 by the support mount 200 such that
the difference E between the center of gravity G and the rotational center R decreases
when the predetermined external force is applied on the basis of the information calculated
in the first calculation step (S100) to the third calculation step (S300).
[0062] The first calculation step (S100) calculates the center of gravity G of the actuator
100 in consideration of the specifications, volume, mass, structure, etc. of the actuator
100.
[0063] The second calculation step (S200) assumes that a user wears a bone conduction device,
sets external force due to wearing, and the calculates the degree of support of the
actuator 100 by the support mount 200 when the external force is applied to the actuator
100. The degree of support may include a value about the degree of insertion when
the actuator 100 is inserted and supported in the support mount 200. For example,
when external force is applied to the actuator 100 toward the support mount 200 by
elasticity or flexibility of the support mount 200, the degree of support of the actuator
100 changes. The second calculation step (S200) calculates the degree of support under
the assumption that external force is a predetermined value.
[0064] The third calculation step (S300) is a step of calculating the rotational center
R of the actuator 100, in which the rotational center R can be considered in the X-axial,
Y-axial, and Z-axial directions and can be calculated about the Y axis that is a main
element by reflecting the Equations described above.
[0065] The position determination step (S400) determines a support position of the actuator
100 such that the difference E between the center of gravity G and the rotational
center R of the actuator 100 under the assumption that the predetermined external
force is applied.
[0066] For example, when the support mount 200 has a groove in which the actuator 100 is
seated and the actuator 100 is seated in the groove, the degree of support of the
actuator is changed by adjusting the shape, depth, position, etc. of the groove. In
this case, the position determination step (S400) means adjusting the shape, depth,
position, etc. of the groove of the support mount 200 such that the difference E decreases
when the predetermined external force is applied.
[0067] The connection structure of the support mount 200 and the actuator 100 can be achieved
in various ways. In the position determination step (S400), it is possible to determine
the connection structure of the support mount 200 and the actuator 100 such that the
difference E decreases.
[0068] The position determination step (S400) according to an embodiment of the present
invention can determine the support position of the actuator 100 by the support mount
200 according to the external force such that the center of gravity G and the rotational
center R coincide. This case means that when external force is not applied, even though
the difference E somewhat exists, predetermined external force is applied, so the
difference E is removed with the support position or the degree of support of the
actuator changed.
Second Embodiment
[0069] Referring to FIG. 6, a method of designing a mount module according to the second
embodiment includes: a first calculation step (S100) that calculates the center of
gravity G of the actuator 100; a second calculation step (S200) that calculates the
degree of support of the actuator 100 by the support mount 200 in accordance with
predetermined external force; a third calculation step (S300) that calculates the
rotational center R of the actuator 100 on the basis of the degree of support calculated
in the second calculation step (S200); and a property determination step (S500) that
determines properties of the support mount 200 such that the difference E between
the center of gravity G and the rotational center R decreases when the predetermined
external force is applied on the basis of the information calculated in the first
calculation step (S100) to the third calculation step (S300).
[0070] The first calculation step (S100, second calculation step (S200), and third calculation
step (S300) of the second embodiment may be the same as the first calculation step
(S100, second calculation step (S200), and third calculation step (S300) of the first
embodiment.
[0071] The property determination step (S500) determines properties of the support mount
200 such that the difference E between the center of gravity G and the rotational
center R of the actuator 200 under the assumption that the predetermined external
force is applied.
[0072] For example, the support mount 200 can have various properties such as strength,
shape, flexibility, and elasticity and the degree of support of the actuator 100 depends
on the properties of the support mount 200 when the external force is applied. In
this case, the property determination step (S500) determines rigidity, elasticity,
shape, etc. of the support mount 200 such that the difference E decreases when the
predetermined external force is applied. When the external force is applied to the
actuator 100 and the difference E is somewhat large because the degree of support
of the actuator is small, it is possible to increase the degree of support 100 when
the same external force is applied by somewhat reducing the flexibility and rigidity
at the contact position with the actuator 100 on the support mount 200.
[0073] The property determination step (S500) according to an embodiment of the present
invention can adjust the degree of support of the actuator 100 by the support mount
200 by determining the properties of the support mount 200 such that the center of
gravity G and the rotational center R coincide. This case means that when external
force is not applied, even though the difference E somewhat exists, predetermined
external force is applied, so the difference E is removed with the support position
or the degree of support of the actuator changed.
[0074] It is possible to prevent noise and sound leakage by designing a mount module through
the steps that are sequentially performed, as in the first embodiment and the second
embodiment. Further, a mount module designed by the method can be easily applied to
existing device or device that will be manufactured in future, so the usability is
large.
1. A bone conduction mount structure for controlling vibration magnitude by controlling
a support position of an actuator, the bone conduction mount structure comprising:
an actuator disposed in a user's bone direction and generating and transmitting vibration
to the bone; and
a support mount disposed to surround a portion of an outer side of the actuator, supporting
the actuator, and being able to be fixed to a structural member,
wherein when the actuator is inserted into the support mount by external force, a
difference between a center of gravity and a rotational center of the actuator decreases.
2. The bone conduction mount structure of claim 1, wherein the support mount has flexibility,
the rotational center changes in accordance with the degree of insertion of the actuator
in the support mount by external force, and the difference gradually decreases until
the external force reaches a predetermined reference value.
3. The bone conduction mount structure of claim 2, wherein when the actuator is inserted
in the support mount, the center of gravity and the rotational center coincide.
4. A method of designing a mount module that includes an actuator disposed in a user's
bone direction and generating and transmitting vibration to the bone, and a support
mount having flexibility, disposed to surround a portion of an outer side of the actuator,
supporting the actuator, and being able to be fixed to a structural member, the method
comprising:
a first calculation step that calculates a center of gravity of the actuator;
a second calculation step that calculates the degree of support of the actuator by
the support mount in accordance with predetermined external force;
a third calculation step that calculates a rotational center of the actuator on the
basis of the degree of support calculated in the second calculation step; and
a position determination step that determines a support position of the actuator by
the support mount such that a difference between the center of gravity and the rotational
center decreases when the predetermined external force is applied on the basis of
the information calculated in the first calculation step to the third calculation
step.
5. The method of claim 4, wherein the position determination step determines the support
position of the actuator by the support mount according to the external force such
that the center of gravity and the rotational center coincide.
6. A method of a mount module that includes an actuator disposed in a user's bone direction
and generating and transmitting vibration to the bone, and a support mount having
flexibility, disposed to surround a portion of an outer side of the actuator, supporting
the actuator, and being able to be fixed to a structural member, the method comprising:
a first calculation step that calculates a center of gravity of the actuator;
a second calculation step that calculates the degree of support of the actuator by
an inside of the support mount in accordance with predetermined external force;
a third calculation step that calculates a rotational center of the actuator on the
basis of the degree of support calculated in the second calculation step; and
a property determination step that determines properties of the support mount such
that a difference between the center of gravity and the rotational center decreases
when the predetermined external force is applied on the basis of the information calculated
in the first calculation step to the third calculation step.
7. The method of claim 6, wherein the property determination step adjusts the degree
of support of the actuator by the support mount by determining the properties of the
support mount such that the center of gravity and the rotational center coincide.